- Artificial Intelligence
- Generative AI
- Business Operations
- Cloud Computing
- Data Center
- Data Management
- Emerging Technology
- Enterprise Applications
- IT Leadership
- Digital Transformation
- IT Strategy
- IT Management
- Diversity and Inclusion
- IT Operations
- Project Management
- Software Development
- Vendors and Providers
- Enterprise Buyer’s Guides
- United States
- Middle East
- España (Spain)
- Italia (Italy)
- Netherlands
- United Kingdom
- New Zealand
- Data Analytics & AI
- Newsletters
- Foundry Careers
- Terms of Service
- Privacy Policy
- Cookie Policy
- Copyright Notice
- Member Preferences
- About AdChoices
- Your California Privacy Rights
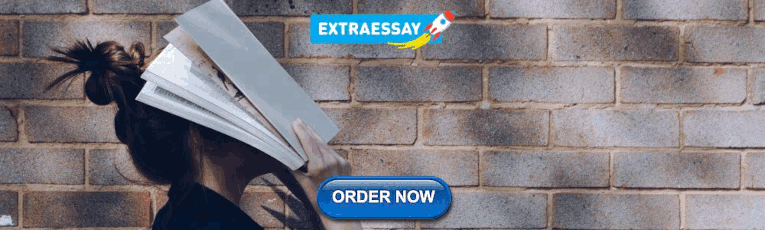
Our Network
- Computerworld
- Network World
Nestlé’s Enterprise Resource Planning (ERP) Odyssey
In June 2000, Nestlé SA signed a much publicized $200 million contract with SAP—and threw in an additional $80 million for consulting and maintenance—to install an ERP system for its global enterprise. The Switzerland-based consumer goods giant intends to use the SAP system to help centralize a conglomerate that owns 200 operating companies and subsidiaries in 80 countries.
Not surprisingly, a move of this magnitude sparked skepticism. Anne Alexandre, an analyst who covers Nestlé for HSBC Securities in London (the company is traded only in Europe), downgraded her recommendation on Nestlé stock a year after the project was announced. While she says that the ERP system will likely have long-term benefits, she is wary of what the project will do to the company along the way. “It touches the corporate culture, which is decentralized, and tries to centralize it,” she says. “That’s risky. It’s always a risk when you touch the corporate culture.”
It is a risk that Jeri Dunn, vice president and CIO of Nestlé USA, the $8.1 billion U.S. subsidiary, knows all too well. In 1997, the Glendale, Calif.-based company embarked on an SAP project code-named Best (business excellence through systems technology). By the time it reaches the finish line, Best will have gobbled up six years and more than $200 million (the same amount its global parent intends to spend). Dunn now says she sees the light at the end of the tunnel. The last rollouts will take place in the first quarter of 2003. But the implementation has been fraught with dead ends and costly mistakes. It is a cautionary tale, full of lessons not only for its Swiss parent but for any Fortune 1000 company intent on an enterprisewide software implementation.
“I took eight or nine autonomous divisions and said we are going to use common processes, systems and organization structures,” says Dunn. “[Nestlé SA is] looking at 80 autonomous countries and saying the same thing. They’re just taking it up a notch. If they go in with an attitude that there’s not going to be resistance and pain, they’re going to be disappointed.”
Nestlé’s global SAP project, which is tied in to a larger $500 million hardware and software data center rehaul, will be integrated with its American subsidiary’s soon-to-be completed ERP. And Dunn is even lending 70 of her own staffers for the global initiative, as well as some of her hard-won expertise. But while the verdict is still out on the global project, the pain?angry employees, costly reengineering and long periods when it seemed the project would never end?was worth it for Nestlé USA, Dunn says. To date, she claims, the Best project has saved the company $325 million. (Because Nestl&#eacute; is headquartered outside the United States, it doesn’t have to disclose its financial information to the SEC.)
Regardless of the project’s exact ROI, the lessons learned are real. The primary lesson Dunn says she has taken away from the project is this: No major software implementation is really about the software. It’s about change management. “If you weren’t concerned with how the business ran, you could probably [install the ERP software] in 18 to 24 months,” she says. Then “you would probably be in the unemployment line in 19 to 25 months.”
Nestlé learned the hard way that an enterprisewide rollout involves much more than simply installing software. “When you move to SAP, you are changing the way people work,” Dunn says. “You are challenging their principles, their beliefs and the way they have done things for many, many years.”
The Problem: 29 Brands of Vanilla
Vanilla may be the world’s least exciting ingredient?the word is even a synonym for bland. But that wasn’t the case at Nestlé USA, where vanilla represented a piquant plethora of inefficiencies and missed opportunities.
Before 1991, Nestlé was simply a collection of independently operating brands, such as Stouffer’s and Carnation, owned by the Swiss-based parent. In 1991, the brands were unified and reorganized into Nestlé USA. Even so, the new company continued to function more like a holding corporation than a single entity. Divisions still had geographically dispersed headquarters and were free to make their own business decisions, although they now reported to corporate Nestlé USA executives in Glendale rather than in Vevey, Switzerland. The new company was trying to introduce economies of scale and common practices, but years of autonomous operation proved an almost insurmountable hurdle.
In 1997, a team examining the various systems across the company found, among many other troubling redundancies, that Nestlé USA’s brands were paying 29 different prices for vanilla?to the same vendor. “Every plant would buy vanilla from the vendor, and the vendor would just get whatever it thought it could get,” Dunn says. “And the reason we couldn’t even check is because every division and every factory got to name vanilla whatever they wanted to. So you could call it 1234, and it might have a whole specification behind it, and I might call it 7778. We had no way of comparing.”
While the American brands were willing to go about their business as autonomous companies?headaches be damned?the Swiss parent knew that similar problems would continue. In 1991, the same year that Nestlé USA was created, Dunn, then associate director for application systems of Stouffer’s Hotels, one of the many Nestlé brands, went to Switzerland to help implement a common methodology for Nestlé projects worldwide. In 1995, she was promoted to assistant vice president of technology and standards for Nestlé SA, where she came up with technology standards for every Nestlé company to follow. Dunn figured that common systems across the Nestlé empire would create savings through group buying power and facilitate data sharing between subsidiaries.
Yet when Dunn returned stateside to take the more hands-on CIO job at Nestlé USA in 1997, she found that few of her recommendations had been acted on. “My team could name the standards, but the implementation rollout was at the whim of the businesses,” she says during a recent interview in her sparsely decorated fourth floor office in Glendale. Dunn takes cigarette breaks at every possible opportunity and isn’t afraid to dress in a leopard-print skirt and blouse. At 47, she is a survivor who is refreshingly open about her mistakes and is respected throughout the company. Her staff speaks of her in almost reverential tones.
The Proposal: One Nestlé, Under SAP
Dunn’s arrival in spring 1997 came a few months after Nestlé USA Chairman and CEO Joe Weller coined the term One Nestlé to re-flect his goal of transforming the separate brands into one highly integrated company. In June, Dunn joined with executives in charge of finance, supply chain, distribution and purchasing to form a key stakeholders team and study what was right and wrong with the company. When the time came, the key stakeholders were initially allotted a little over two hours to present their findings to Weller and other top Nestlé officials.
The team balked at the time limit. “I told them that they would either throw me out in the first 15 minutes or they would cancel the rest of the day, and we would really have a great discussion,” says Dick Ramage, Nestlé USA’s vice president of supply chain and a member of the team. “It took them an hour, but they canceled the rest of the day.”
“I don’t think they knew how ugly it was,” says Dunn, referring to the company’s condition. “We had nine different general ledgers and 28 points of customer entry. We had multiple purchasing systems. We had no clue how much volume we were doing with a particular vendor because every factory set up their own vendor masters and purchased on their own.”
Soon the stakeholders team presented Weller with a blueprint for major changes they thought could be made in three to five years. While the cornerstone of the recommendation was an SAP package, Dunn says, “We made it very clear that this would be a business process reorganization and that you couldn’t do it without changing the way you did business. There was going to be pain involved, it was going to be a slow process, and this was not a software project.”
Despite that warning, it would later become apparent that neither Weller nor the key stakeholders really understood the degree to which the Best project would change the business processes at Nestlé or the amount of pain it would cause. “They still thought that it was just about software,” Dunn says.
By October 1997, a team of 50 top business executives and 10 senior IT professionals had been assembled to implement the SAP project. The team’s goal was to come up with a set of best practices that would become common work procedures for every Nestlé division. All the divisional functions?manufacturing, purchasing, accounting and sales?would have to give up their old approaches and accept the new pan-Nestlé way.
On the technical side, a smaller team spent 18 months examining every bit of item data in each division in order to implement a common structure across the company. From now on, vanilla would be code 1234 in every division. The SAP system would be customized around the uniform business processes. In the case of the supply chain, the team decided not to use SAP because the ERP company’s supply chain module, Ad-vanced Planner and Optimizer or APO, was brand-new and therefore risky. Instead, Nestlé turned to Manugistics?at that time an SAP partner. Manugistics’ supply chain module followed all the SAP standards and could easily be integrated.
By March 1998 the key stakeholders had a plan in place. Nestlé would implement five SAP modules?purchasing, financials, sales and distribution, accounts payable and accounts receivable?and the Manugistics’ supply chain module. Each would be deployed across every Nestlé division. For instance, the purchasing group for confections would follow the same best practices and data as the purchasing group for beverages.
Development work began in July 1998. The deadline for four of the modules was Y2K. The new systems would have to double as code fixes and be in place for the millennial change. Nestlé USA made the deadline. But its haste created almost as many problems as it solved.
The Process: Nestlé’s Crunch
Even before three of the SAP and the Manugistics modules were rolled out in late 1999, there was rebellion in the ranks. Much of the employee resistance could be traced to a mistake that dated back to the project’s inception: None of the groups that were going to be directly affected by the new processes and systems were represented on the key stakeholders team. Consequently, Dunn says, “We were always surprising [the heads of sales and the divisions] because we would bring something up to the executive steering committee that they weren’t privy to.” Dunn calls that her near fatal mistake.
By the beginning of 2000, the rollout had collapsed into chaos. Not only did workers not understand how to use the new system, they didn’t even understand the new pro-cesses. And the divisional executives, who were just as confused as their employees?and even angrier?didn’t go out of their way to help. Dunn says her help desk calls reached 300 a day. “We were really naive in the respect that these changes had to be managed,” she admits now.
Nobody wanted to learn the new way of doing things. Morale tumbled. Turnover among the employees who forecast demand for Nestlé products reached 77 percent; the planners simply were loath or unable to abandon their familiar spreadsheets for the complex models of Manugistics.
A technical problem soon emerged as well. In the rush to beat the Y2K deadline, the Best project team had overlooked the integration points between the modules. All the purchasing departments now used common names and systems, and followed a common process, but their system was not integrated with the financial, planning or sales groups. A salesperson, for example, may have given a valuable customer a discount rate and entered it into the new system, but the accounts receivable department wouldn’t know about it. So when the customer paid the discounted rate, it would appear to the accounts receivable operative as though the invoice were only partially paid. In its haste to unify the company’s separate brands, the project team had essentially replaced divisional silos with process silos.
In June 2000, the project was reorganized. Project leader Mark Richenderfer was promoted to a new job in Switzerland, working on Nestlé’s global SAP implementation and business process improvement initiatives. Dunn given full responsibility for the project. It was time for self-examination. In October 2000, Dunn gathered 19 Nestlé USA key stakeholders and business executives for a three-day offsite at the DoubleTree Hotel in Pasadena, Calif., about 10 miles from Nestlé headquarters.
Jose Iglesias, director of information systems, says the retreat started off as a gripe session. The time constraints necessitated by Y2K had put too much pressure on the people in charge of executing the changes. The project team had lost the big picture of how the various components would work together. And there was still work to be done. The existing modules had to be integrated and the team still needed to roll out two more SAP modules?sales and distribution on the domestic side, and accounts receivable?as well as a new module for the supply chain. Since Dunn had rejected the SAP supply chain module two years before, it had improved and been named a Nestlé global standard by Dunn’s old standards group in Switzerland. So she decided to replace all but a couple of parts of the Manugistics system with APO. Dunn estimates that last-minute switcheroo accounted for 5 percent of Best’s $210 million cost.
The offsite group members eventually decided that to finish the project they would need to begin at the beginning, starting with the business requirements then reaching an end date, rather than trying to fit the project into a mold shaped by a predetermined end date. They also concluded they had to do a better job of making sure that they had support from key divisional heads and that all the employees knew exactly what changes were taking place, when, why and how.
The End Game: Sadder But Wiser
By April 2001, the end-state design was complete, giving the project team a highly detailed road map to follow. A month later, Tom James came on board as director of process change for the Best project, having the sole responsibility of acting as a liaison between the divisions and the project team. James says that he was shocked by the still poor relationship between the divisions and the project team. He and Dunn began meeting with more of the division heads. They also started conducting regular surveys of how the employees affected by the new systems were dealing with the changes.
They were not afraid to react to what they found. Dunn says that Nestlé recently delayed the rollout of a new comanufacturing package for six months based on feedback indicating that the would-be users were not prepared to make the process changes that were involved.
ERP projects are notorious for taking a long time and a lot of money. Jennifer Chew, an analyst at Cambridge, Mass.-based Forrester Research, found that 54 percent of respondents to a recent survey said that their project lasted more than two years (the other 46 percent brought theirs to fruition in less than two years). Nestlé USA’s project “sounds on the high side” for both time and money, says Chew. Still, success is ultimately measured by what the project accomplishes. Chew points out that Kmart had to write off $130 million for an ERP project that was never completed.
Dunn herself is not ashamed of the length of the project or the numerous dead ends. She insists that slow and steady wins the race. Nestlé USA has already achieved significant ROI, she says, with the largest chunk of savings from better demand forecasting. “The old process involved a sales guy giving a number to the demand planner, who says, ’Those guys don’t know what the hell they are talking about; I’m going to give them this number,’’’ Dunn says. “The demand planner turns [that number] over to factory, and the factory says the demand planner doesn’t know what the hell he’s talking about.” Then the factory changes the number again.
With SAP in place, common databases and business processes lead to more trustworthy demand forecasts for the various Nestlé products. Furthermore, because all of Nestlé USA is using the same data, Ramage says, Nestlé can forecast down to the distribution center level. That allows the company to reduce inventory and the redistribution expenses that occur when too much of a product is sent to one place and not enough to another. Ramage says that supply chain improvements accounted for a major chunk of the $325 million Nestlé says it has saved from SAP.
If Dunn were to do it over again, she’d focus first on changing business processes and achieving universal buy-in, and then and only then on installing the software. “If you try to do it with a system first, you will have an installation, not an implementation,” she says. “And there is a big difference between installing software and implementing a solution.”
More on ERP:
- 11 tips for selecting and implementing an ERP system
- 12 famous ERP disasters, dustups and disappointments
- 10 most powerful ERP vendors today
- 5 top ERP trends — and their implications for IT leaders
- 7 things you need to know about maintaining your ERP system
Related content
Automated order management: is it worth the hype, sap ai pact with aws offers customers more gen ai options, accenture’s cloud migration sets standard for other large businesses, ex-open ai researcher jan leike joins anthropic amid ai safety concerns, from our editors straight to your inbox, show me more, 3 things cios can do to make gen ai synch with sustainability.

A major tech tune-up at Camping World gives customers a smooth ride

The Right Networking Solution Lies Not in What You Choose, But Why You Choose It

CIO Leadership Live India with Partha Protim Mondal, CIO, Berger Paints

CIO Leadership Live Middle East with Nani M. Butti, ahrain Supreme Council for Youth & Sports

CIO Leadership Live NZ with Avinash de Silva, Head of Technology at Alvarium

Aras Innovator weaves a digital thread through a product lifecycle

Sponsored Links
- Everybody's ready for AI except your data. Unlock the power of AI with Informatica
ERP Implementation at Nestle
Derek S. Dieringer
Enterprise Resource Planning Systems
June 24, 2004
Introduction
At first glance, Enterprise Resource Planning (ERP) systems seem to be the silver bullet for every company’s problems. In one fell swoop, implementation of an ERP system offers a company the chance to re-engineer business processes, coordinate the systems of geographically dispersed locations, consolidate data, and empower users by giving them access to all the company’s data in real time. Of course, these opportunities come at a high price in terms of financial cost, implementation nightmares, and human issues. Often these implementations fail miserably as they run behind schedule and over budget; other times they are successful. Regardless of the outcome, each ERP implementation holds valuable lessons to be learned for companies considering their own ERP implementation.
The Business Case for an ERP
The business case for implementing an ERP system can be seen by examining any one of three Nestle stories. Nestle SA is the parent company of the candy-making giant and is headquartered in Switzerland ( Konicki , pg 185). In 2000 Nestle SA decided that it wanted to leverage its size and begin acting like the giant it is. To do so, it signed a $200 million contract with SAP to roll out an ERP system to its 230,000 employees in 80 countries around the world (Olson, pg. 53). In addition to this sum, Nestle SA also committed to an additional $80 million to be spent on consulting, maintenance, and upgrades ( Konicki , pg. 185). Executives at Nestle SA realized that the company needed to standardize its business processes if it wanted to be competitive. The rollout was scheduled to take three years for Nestle SA’s largest sites with the others to follow. Included in the implementation were the mySAP.com financials, accounts payable, accounts receivable, planning, production management, procurement, direct procurement, supply-chain, demand planning, fulfillment, and business-intelligence modules ( Konicki , pg. 185).
Prior to the Nestle SA ERP decision, Nestle UK had already implemented an ERP system. The British subsidiary of Nestle SA implemented SAP R/3 over a period of five years in 18 UK manufacturing sites (Glick, 7 Days, pg. 4). This implementation wrapped up in 1999 and was the one of the UK ’s largest ERP systems with over 6,000 users (Glick, Enterprise , pg. 24). As with the Nestle SA deployment, the goals of the Nestle UK implementation were centered on leveraging the size of the organization as well as tightening up the supply chain and re-engineering work practices and processes (Glick, 7 Days, pg. 4).
The third Nestle ERP implementation story involves Nestle USA . Nestle USA is the $8.1 billion U.S. subsidiary of Nestle SA. In 1997, Nestle USA began its own ERP project known as Best (Business Excellence through Systems Technology) ( Worthen , pg. 1). Scheduled to run over the course of six years ending in the first quarter of 2003, this project was budgeted at well over $200 million and would implement five SAP modules: purchasing, financials, sales and distribution, accounts payable, and accounts receivable ( Worthen , pg. 1-3). Similar to the other two Nestle divisions, the goal behind this ERP implementation was unification. Additionally, the project would solve Nestle USA ’s Y2K woes ( Worthen , pg. 3). In the case of Nestle USA , the ERP was part of the vision Nestle USA Chairman and CEO Joe Weller referred to as “One Nestle” that would be responsible for “transforming the separate brands into one highly integrated company” ( Worthen , pg. 2). Prior to the implementation, Nestle USA had nine different general ledgers and 28 points of customer entry ( Worthen , pg. 2). The goal of the ERP project was to bring these numbers down to one. One of the most interesting views on the Nestle USA problem is the story of vanilla. Prior to the ERP implementation, Nestle USA did not act as one company. Instead, each location acted on its own behalf and was free to make its own business decisions. “In 1997, a team examining the various systems across the company found, among many other troubling redundancies, that Nestle USA’s brands were paying 29 different prices for vanilla – to the same vendor” ( Worthen , pg. 2). This situation arose from the fact that each factory negotiated their own deals with the vendor and the vendor adjusted the price per factory based on what they thought the factory would pay. The situation was only worsened by the fact that each factory referred to vanilla in a different way. While one factory might have referred to vanilla as 1234, another factory referred to it as 7890. This made it nearly impossible for individuals at the corporate headquarters to do comparisons across plants to see manufacturing costs ( Worthen , pg. 2).
Regardless which Nestle case is examined, the goals behind all three ERP implementations were similar for all the divisions. That is, in each instance, there was a driving goal to consolidate the operations of the different locations so that Nestle could truly leverage their size and buying power. Additionally, there was a need to centralize and control data so that the financial, reporting, and forecasting numbers were more consistent and accurate. As each factory acted as an autonomous unit, Nestle was at a severe competitive disadvantage and realized that it needed one system used by all in order to be more efficient and survive in the global economy.
Implementation Strategy
The term ‘ERP implementation’ has become synonymous with ‘nightmare’ in recent years. High profile failures dot the headlines and companies are often intimidated not only by the high price but also the negative effect implementations can have on their business. Vendors such as SAP are working diligently on shaking this reputation and have made great strides in meeting their goals. “In 1996, a user could expect to pay six to 10 times the license cost in consulting charges. These days the external consulting cost has dropped to typically one to two-and-a-half times the software costs, depending on how much process re-engineering the user does” ( Adshead , pg. 26). Fortunately for companies considering an ERP implementation there have been enough done in the past that there are opportunities to learn from the successes and failures of others. One of the key factors of a successful implementation is “don’t try to make the product fit exactly the way you would ideally like to work or on the other hand assume that people will completely change their processes to meet the package. The first takes many years and costs loads, the second meets big resistance” ( Adshead , pg. 26). For most businesses there needs to be a middle-of-the-road approach where individuals realize that the software will not solve every organizational problem and not every process in the company can be re-engineered to fit the software. Regardless, savvy project leaders with prior ERP implementation experience will tell you that there are several pitfalls to avoid during ERP projects. The first is not to select an ERP package based on a demo. Choose your package wisely, ask questions, get references, and do your homework. An ERP package is a costly investment and you need to be sure you are choosing the package that best fits the needs of your organization. The second is get management commitment. Not securing top management buy-in results in an automatic project failure. Management commitment is often high at the beginning of a project but begins to wane as the project wears on. It is vital to keep management interested, involved, and positioned squarely behind the project. The third is to avoid heavy customization. It is both easy and tempting to customize ERP packages to fit your exact needs. Unfortunately excessive customization will haunt you by lengthening the project timeline and by driving up maintenance costs in the future. The final pitfall to avoid in ERP implementations is not to underestimate the importance of training. It is not uncommon that users receive several days of training on the new system and then do not see the system again for months. Users need in-depth and on-going training and should even be involved with system testing if at all possible ( Adshead , pg. 27).
Unfortunately for Nestle USA , they did not heed the failures of others. Throughout the implementation, Nestle USA made several large mistakes that almost doomed the project. When the project began a team of 50 top executives and 10 senior IT professionals was assembled to develop a set of best practices for all Nestle USA divisions. The goal was to develop these best practices for all functions of the organization. Each function from manufacturing to sales would eventually be forced to retire their old approaches and adopt the new best practice that had been developed. Concurrently, a technical team was charged with the task of implementing a common data structure across the company ( Worthen , pg. 2). By the time the implementation began in 1999 Nestle already had problems with its employees’ acceptance of the system. Most of the resistance met by the project team was traced back to the fact that “none of the groups that were going to be directly affected by the new processes and systems were represented on the key stakeholders team” ( Worthen , pg. 3). This was only the start of Nestle USA ’s problems. By early 2000, the implementation had turned into a disaster. Employees did not understand how to use the new system and did not understand the new work processes they were being forced to adopt. Divisional executives were just as confused as their employees as they had been left out of the planning and development of the new system and were less than willing to assist in straightening out the mess that had developed ( Worthen , pg. 3). The result of this was that morale plummeted and turnover skyrocketed. In fact, “turnover among the employees who forecast demand for Nestle products reached 77 percent” ( Worthen , pg. 3).
Nestle USA ’s implementation problems did not stop with employee issues. Technical difficulties began to emerge as well during the rollout. In the rush to beat the Y2K deadline the project team had overlooked the integration points between the modules. This meant that the different modules could not talk to each other. So if a salesperson gave a discount to a customer and entered it in the system, the accounts receivable portion of the system did not know of the discount. The result was that the customer would pay their bill but invoice appeared as though it were only partially paid ( Worthen , pg. 3).
By June 2000, Nestle USA was forced to halt the rollout and the project manager was removed from the project and reassigned to Switzerland ( Worthen , pg. 3). Nestle USA gathered 19 key stakeholders and executives went on a three-day offsite retreat to discuss the future of the project. Out of this meeting came the revelation that they would need to redefine the business requirements of the project and then shape the project timeline around the requirements rather than to shape the timeline around a predetermined end date ( Worthen , pg. 3-4). This process took until April 2001 and resulted in a detailed blueprint for the project team to follow. A director of process change was hired to act as a liaison between the project team and the different functional divisions ( Worthen , pg. 4). With all of these items finally resolved, the project was able to continue. The last rollouts were scheduled to be completed in the first quarter of 2003 ( Worthen , pg. 1).
Although there were bumps in the road for Nestle USA ’s ERP implementation, it certainly seems to be paying for itself. As of 2002, Nestle USA claimed they had already realized a savings of over $325 million ( Worthen , pg. 1). Most of these savings came in the area of supply chain improvements, specifically demand forecasting. “The old process involved a sales guy giving a number to the demand planner, who says, ‘Those guys don’t know what the hell they are talking about; I’m going to give them this number’. The demand planner turns [that number] over to factory, and the factory says the demand planner doesn’t know what the hell he’s talking about. Then the factory changes the number again. With SAP in place, common databases and business processes lead to more trustworthy demand forecasts for the various Nestle products. Furthermore, because all of Nestle USA is using the same data, Nestle can forecast down to the distribution center level” ( Worthen , pg. 4).
In addition to saving money, Nestle USA has also been able to come together as one organization. The problem of 29 different brands of vanilla has been solved and now with common databases each factory refers to vanilla in the same manner. They also use common processes that simplify operating procedures and allow for the centralization of functions such as developing training procedures. Training no longer needs to be customized for each factory. Since each location follows the same procedures, training materials only need to be developed once. Additionally, any Nestle USA employee could relocate to another factory and not have to adjust to local processes.
Nestle UK experienced similar successes with their ERP implementation. They were able to recoup the money spent on the system in only two years (Glick, 7 Days, pg. 4). Further, like their American counterpart, Nestle UK has experienced reduced inventory levels, tighter control on inventory, and a more disciplined attitude toward business processes (Glick, 7 Days, pg. 4). Most importantly, the ERP implementation at Nestle UK helped to foster a “culture of continuous improvement” (Glick, Enterprise , pg. 24). “Improvement priorities are clear: first, the internal opportunities; second, business-to-business; and third, business to consumer” (Glick, Enterprise , pg. 24). This attitude is embodied by the fact that following the ERP rollout they hired a process development manager. This person’s sole responsibility is to act as a bridge between business and the Information Technology department and to make sure that employees stay focused on continuous improvement rather than simply trying to maintain existing systems (Glick, Enterprise , pg. 24).
Recommendations
The Nestle USA case is an excellent case study for ERP implementations because it contains both successes and failures. There were obviously breakdowns during the planning phases of the project yet the overall result can be considered successful due to the consolidated system they now have in place and the amount of money that they are saving due to the ERP rollout. By examining the experiences of Nestle USA other companies can learn valuable lessons that can be applied to their own rollouts. Some of these lessons come straight from the mouths of Nestle USA executives while others are observations made from studying the case.
The first lesson that can be learned from the Nestle USA scenario is that in order for an ERP implementation to be successful the right individuals need to be involved in the process from the beginning. Nestle learned this lesson the hard way and eventually was forced to halt their rollout. It is simply impossible to redesign work processes without involving some of the people that actually do the work. While an argument could be made for “too many cooks in the kitchen” regarding ERP implementations, it is certainly better to have more people than needed rather then not enough when the future of the company is on the line. It is easier on the project schedule to trim the project team during the project than it is to bring new people into the fold and then have to spend time bringing them up to speed on all of the intricacies of the project.
Another lesson that can be gleaned from the Nestle USA case is that an ERP implementation is not the project that companies should attempt to force into a specific timeline. There is no better way to miss things and have components completed shoddily than to force the project timeline to fit a specified end date. Again, with the future of the company on the line, it is important to completely define the business goals of the project and then create a timeline that will accomplish those goals.
A third recommendation for companies considering an ERP implementation is to place a large focus on training. Training is one of the key elements of any ERP implementation because without it employees that will be using the system and the new business processes on a day-to-day basis will not be prepared to do so. As with most software projects, training is often an afterthought and typically one of the first items to be cut or reduced when the project timeline begins slipping. Organizations must resist the urge to do this on ERP projects. It is crucial that employees receive training early and often throughout the project. If at all possible, end-users should also be involved in the testing of the new system.
Fourth, organizations should spend time evaluating the business process re-engineering that will be done in conjunction with an ERP implementation. Companies often take the opportunity presented by an ERP rollout to either redesign business processes or adopt best practices throughout the organization. Caution should be exercised during this phase as re-engineering processes just for the sake of re-engineer the process is often not necessarily a wise business decision. There are times where processes should be left alone. There are also instances where best practices may vary from location to location. Attempting to force a new or revised process on every facility in the organization is an excellent way to breed contempt and resistance within the organization. ERP implementations do offer a great opportunity to re-engineer processes but great care should be taken when selecting which processes are actually modified.
The fifth general recommendation for ERP projects is to limit the number of customizations that are done to the system. As the number of customizations requested increase so does the cost, timeline, and likelihood of bugs in the system. Since ERP systems are sold by vendors rather than developed in-house, they need to be generic enough to be resold to multiple organizations. This means that either the software needs to be customized to fit an organization’s needs or the organization’s processes need to be redesigned to fit the software. As mentioned earlier, it is important to choose which processes are re-designed wisely. Combined with this recommendation, it becomes clear that making the determination as to which processes are re-engineered and which pieces of software are customized is a balancing act.
The final recommendation for ERP implementations is to obtain universal buy-in for the project. Traditionally, much emphasis has been placed on securing buy-in for the project by top level executives. Unfortunately this is only half the battle. Everyone in the organization needs to support the project if it is to be successful. In the case of Nestle, if they “were to do it over again, [they’d] focus first on changing business processes and achieving universal buy-in, and then and only then on installing the software. If you try to do it with a system first, you will have an installation, not an implementation. And there is a big difference between installing software and implementing a solution” ( Worthen , pg. 4). The end-users are the ones that will be using the system and the processes. If they are not behind the system there will be morale and turnover issues.
In summary, ERP implementations are unlike any other system implementation that a company will ever experience. Despite the bad press that ERP systems and their corresponding rollouts receive, it is possible to experience a successful rollout. Often, as in the case of Nestle USA , organizations will encounter major setbacks and difficulties during the implementation yet still be able to salvage a successful project. The important point to take away is that the plans must be flexible enough to change mid-stream to overcome obstacles that appear during the project and organizations must do their homework prior to beginning an ERP project. Enough companies have gone through implementations that there are plenty of lessons to be learned if organizations are willing to accept the advice of others. ERP implementations combine disparate data sources, re-engineer processes, and involve large numbers of users and locations. It is nearly impossible to plan for every contingency in projects of this size. The difference between success and failure is an organization’s ability to rally and work together during difficult times to reach an end goal that will eventually make everyone’s job easier and the company more competitive.
- Adshead , Antony . SAP: The Climb Gets Easier. Computer Weekly , Dec 12, 2002 ; pg. 26-27.
- Glick, Bryan. 7 Days: SAP Software Gives Nestle Sweet Returns. Computing , Apr 12, 2001 ; pg. 4.
- Glick, Bryan. Enterprise : Nestle Points the Way Forward from ERP. Computing , Apr 12, 2001 ; pg. 24.
- Konicki , Steve. Nestle Taps SAP for E-Business. InformationWeek , Jun 26, 2000 ; pg. 185.
- Olson, David L. Managerial Issues of Enterprise Resource Planning Systems . McGraw Hill/Irwin, New York , 2004.
- Worthen, Ben. Nestle’s ERP Odyssey. CIO , May 15, 2002 . [Online]. Available: http://www.cio.com/archive/051502/nestle.html ( Jun 18, 2004 ).
0800/5 34 34 24
United States
+1-800-872-1727
Or see our complete list of local country numbers
Chat Unavailable
Allow Functional Cookies to enable chat
Send us your comments, questions, or feedback.
- Customer Stories
Nestlé S.A.: Achieving a global cloud transformation

Explore Nestlé’s journey with SAP
With sales of more than one billion products a day, Nestlé S.A. is one of the world’s largest food and beverage companies. And with over 2,000 brands in 188 countries, the company’s operations are as large as they are complex. Nestlé’s journey with SAP began 20 years ago when it standardized its global ERP systems. Today, cloud solutions from SAP help support the digitization of everything from advanced analytics, customer experience, sustainability tracking to workforce and talent management.
Employees worldwide have a single point-of-entry to all SAP applications.
Increased system availability with a simplified global IT infrastructure.
Terabytes of data moved to the cloud.
The Challenge
Strengthen the core: building an it infrastructure fit for global scale and complexity.
To stay in the hearts and minds of consumers for 156 years as Nestlé has, you need to embrace change. But when your company sells more than a billion products each day and employs more than 275,000 people who manage over 2,000 brands in 188 countries, that’s easier said than done.
Nestlé’s business models and routes to market are changing as constantly as the world around us. Consumer expectations have shifted, and digital commerce is accelerating quickly. Supporting a future ready workforce with great employee experiences and efficiency at scale.
Nestlé knew that at the core of every successful company is a solid IT infrastructure built to utilize data and provide the business insights that guide decision-making. And so it began its digital transformation journey.
The Solution
Transforming with a seamless journey to the cloud.
To ensure a smooth, disruption-free transition to a more dynamic, reliable, and scalable infrastructure, Nestlé selected the RISE with SAP solution—a complete offering of ERP software, industry practices and outcome-driven services designed to help companies take advantage of cloud computing in their mission-critical, core systems. With its global cloud transformation, Nestlé is now able to automate business processes across its operations, create innovative business models at global scale and achieve greater agility and resilience.
All of Nestlé’s cloud solutions are integrated and feed into its analytics tools allowing 275,000 employees worldwide to have a single point-of-entry to all SAP applications. This is a major game-changer, reducing the time and effort to manage IT systems.
With help from SAP Services and Support , including SAP MaxAttention services and the SAP Solution Delivery Center group, Nestlé shut down nine data centers and more than 10,000 servers. This enabled the company to migrate thousands of applications, 300 instances of SAP software, and a total of 1,200 terabytes of data to the cloud. Despite the size and complexity of the project, it was delivered on time, on budget, and without disruption to the business.
“What we have between the Nestlé IT teams and the SAP Services and Support team is a true partnership that delivered on an ambitious transformation program—one that’s critical to Nestlé’s future success in the marketplace,” Chris Wright, CIO.
Optimizing recruitment to retirement processes
One of the first areas of Nestlé’s digital transformation was the transformation of HR systems. The company used SAP SuccessFactors to standardize and automate HR processes that support everything from recruitment to retirement. Nestlé also uses SAP Business Technology Platform (SAP BTP) to develop custom extensions of SAP SuccessFactors for situations such as high-volume hiring during seasonal surges.
By creating a hiring application that allows for batch handling and validation of employment data, Nestlé sped up the hiring process and made it much less cumbersome. Additionally, Nestlé now has a chatbot that speaks over 20 languages and answers simple and common questions from thousands of candidates each week without input (interactions) from HR professionals, providing a more seamless experience to the candidates and allowing the Nestlé team to focus on other work.
Giancarlo Pala Head of IT HR / Nestlé S.A.
Transforming Customer Experience with One-Stop Shop
Nestlé is enhancing the customer experience for its business customers by streamlining the ordering, tracking, and invoicing processes. The existing approach relied on frequent telephone contact, resulting in time-consuming processes and potential errors. To overcome these challenges and adapt to the "Consumerization of Commerce," Nestlé implemented a global platform based on SAP Commerce Cloud. This platform eliminates the need for telephone contact by providing real-time insights into orders, invoices, and delivery information.
By offering a digital self-service portal, Nestlé improves the ordering and payment process, making it easier, quicker, and more efficient for retailers, wholesalers, supermarkets, and distributors. The unified one-stop shop built on SAP Commerce Cloud has revolutionized the previous customer service approach, reducing waiting times, enhancing flexibility, and ensuring transparency. This transition aligns with Nestlé's recognition of the importance of offering a seamless digital customer experience to stay competitive and meet evolving consumer expectations. The implementation of the platform not only benefits customers but also optimizes internal processes, increases flexibility, and supports Nestlé's sustainability efforts through paperless invoicing and better insights into orders, deliveries, and transportation.
Pablo Nill Sr. Product Group Manager Customer Service Information Technology / Nestlé S.A.
Better IT infrastructure means better business efficiency and agility
Nestlé has seen a range of benefits from its implementation of RISE with SAP, which has enabled a rapid and cost-effective cloud transformation, reducing costs, and improving the security and compliance of its applications. In simplifying its global IT infrastructure, the company has increased systems availability to 99.97% with outage times reduced from six hours to seven minutes. With SAP BTP, the company can now deploy digital assets 10 times faster than before, increasing business agility and reducing time spent managing IT.
Business units such as human resources have seen improvements in their operations, too. Not only do they benefit from innovative applications like the multilingual chatbot, but increased automation has helped streamline and automate processes. Nestlé has also standardized the annual bonus and salary review processes across the company. Instead of taking a different approach in each country, 15,000 managers in more than 100 countries now use one common solution that has automated 95% of review processes.
The transition to a customer-oriented approach and improved customer experience has yielded significant benefits. The reliance on the internal ERP system has diminished with the implementation of SAP Commerce Cloud, enabling easier connections and freeing the company from IT system constraints. This enhanced flexibility has led to smoother processes and better visibility of ongoing activities. Customers can now manage orders and inquiries independently, allowing the customer service team to focus on more complex customer questions or provide additional support to the sales force teams.
Nestlé has strong commitments when it comes to sustainability and is using the information architecture of SAP to understand how its processes, supply chain, and manufacturing practices can be optimized to achieve these.
Future Plans
Improving the consumer experience.
With Nestlé’s direct-to-consumer business increasing by more than 14% in the last year, the company is piloting SAP Commerce Cloud-based applications and portals to ensure that the customer has the same shopping experience buying directly from Nestlé as they do from a retailer.
Nestlé plans to continue its journey to migrate its entire business operations to SAP S/4HANA Cloud, private edition , with finance and procurement already live.
Nestlé’s digital transformation with SAP is helping to achieve their mission to unlock the power of food to enhance quality of life for everyone. And with SAP cloud solutions at the core, there is nothing stopping the company from fulfilling its purpose to be a force for good.
SAP helps Nestlé S.A. run better
Key business outcomes and benefits
- Reduced time spent on IT, allowing the company to quickly adjust business models and enter new markets
- Increased reliability, resilience, and performance of the platform
- Enhanced visibility and transparency
- 70% of hiring tasks now automated, improving data quality and cutting processing time by up to 90% in some markets
Featured solutions and services
- RISE with SAP can transition your current ERP data and processes to the cloud with less risk and without compromise. The bundle of tailor-made ERP software, transformation services, business analytics, and partner expertise guides you along a personalized path to the cloud.
- SAP S/4HANA Cloud, private edition is a ready-to-run cloud ERP that delivers the latest industry best practices and continuous innovation.
- SAP Business Technology Platform is a unified, business-centric platform that helps companies decide confidently, act with integrity, connect processes, data, and experiences, and achieve continued business innovation
- SAP SuccessFactors HXM Suite offers individualized experiences and strategic solutions – with mobile self-services available anytime, anywhere that empower employees to reach their full potential.
- SAP MaxAttention can help you realize the full potential of your intelligent enterprise vision with on-site, premium access to trusted SAP experts, tools, and methodologies that can help deliver your expected outcomes successfully with SAP solutions.
- SAP Commerce Cloud solution provides a trusted e-commerce platform to help you innovate at scale and tap enterprise-wide data to boost profits and customer satisfaction.
About Nestlé S.A.
Nestlé S.A. is a Swiss multinational food and drink processing conglomerate corporation. It is the largest publicly held food company in the world, measured by revenue and other metrics, since 2014.
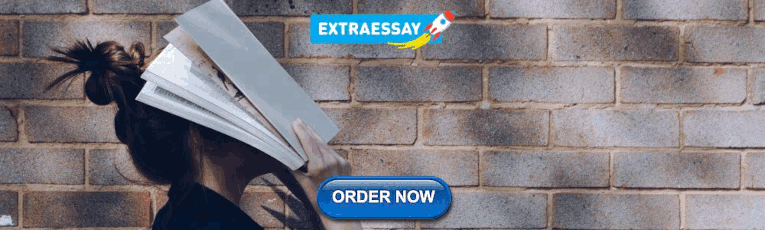
Explore more customer stories
Learn how Cirque du Soleil...
See how Microsoft set up a core HR...
With SAP, the Mercedes-AMG...
Discover how Versuni became an...
- Find customer stories relevant to your business


- Implementation
3 successful ERP implementation case studies to learn from
Because of the high degree of complexity associated with large-scale ERP implementations, over time the proportion of successful outcomes tends to become fifty-fifty propositions from a business case perspective.
ERP case study #1: Cadbury – A Sweet Success
Our first successful ERP implementation case study focuses on Cadbury, a 123-year-old confectioner currently owned by American snack foods conglomerate Mondelēz International. The company was on an accelerated growth track while facing problems meeting its production and distribution requirements.
Subsequently, SAP was engaged to resolve these concerns. Along with other significant changes triggered by the ERP implementation, multi-node resources management was extended throughout its supply chain, along with a complete revamping of existing warehouse and distribution processes.
The consequent impacts allowed Cadbury to reduce overall operating costs, while its newly engaged supply chain produced significantly better production efficiencies throughout its manufacturing chain.
Key takeaway: For an ERP implementation to really pay off, you'll need to see improvements in key areas. A thorough ERP requirements gathering effort during the selection phase is therefore essential.
GET ERP RESEARCH & KNOWLEDGE RIGHT TO YOUR INBOX
Covering the key issues faced by businesses selecting and implementing ERP.
ERP case study #2: Nestle SA – Integration Excellence
As an enormous international candy-maker, Nestle SA headquartered in Konicki Switzerland, had harbored a goal of integrating ERP across all three of its operating companies; Nestle SA, Nestle UK, and Nestle USA.
The latter operation had been working toward complete integration of a set of ERP solutions since the late 90s, but various requirements, organizational, and policy problems had plagued the complete initiation.
By the turn of the millennium, its management finally decided that a holistic re-approach to its business requirements was in order. Consequently, this effort paid dividends that allowed SAP to finally get the $200 million job done.
Ultimately, positive business impacts included the consolidation of an outdated accounting structure, better and more efficient communications throughout its supply chain, and a much more confident workforce.
Key takeaway: Integration across different sites requires a lot of upfront effort - but it pays off in the long run.
Guide: ERP Implementation: 11 steps to success
ERP case study #3: ABC Compounding – A Timely Switch
ABC Compounding, based in Atlanta, Georgia in the United States, provides industrial cleaning supplies to businesses around the world. Most of the products are private-labeled and they are sold through regional and national distributors.
They had a legacy ERP that was no longer a good fit and that lacked essential tools such as planning, scheduling, and MRP. The solution for ABC Compounding was Sage ERP X3.
ABC Compounding employs about 150 people and presents an interesting study as most examples use much larger multinational companies.
ABC is a process manufacturing business. Some of their customers are in food processing and other industries that require FDA and similar control systems.
Myra Hager, chief information officer, had used Sage ERP X3 in a prior position and was familiar with its comprehensive manufacturing capabilities. “The time was right, and the pricing to make the switch was very competitive,” she says. A common thread among companies using ERP at the time.
New Sage functions
ABC lets the MRP function create work orders for us based on orders and stocking levels. Previously they printed reports, did separate calculations, and manually entered the work orders. There were often several hundred work orders active at once, each with dozens of items. Eliminating the manual data entry tasks has been an enormous time saver.
Step-Saving Tools
Intercompany transfers of inventory are common, as are transfers between site locations within each company. Using Sage ERP X3, such transfers are straightforward and easily traceable. Previously, ABC Compounding had to enter separate buy and sell transactions to transfer ownership of the material.
Sales and customer service staff appreciate the software’s easy and intuitive navigation. Six staff members that enter more than 200 orders each day. Speed is of the essence, and Sage ERP X3 provides the tools they need to quickly enter orders and answer any customers’ questions that arise throughout the work day.
Quick Access to Actionable Data
The single biggest benefit of Sage ERP X3 to ABC Compounding is the easy access to critical information. The ability to drill down and tunnel around following a transaction is invaluable.
They have access to relevant documents and data with just a few clicks. The staff loves what they call the Left List, a display of tasks and data related to the screen they’re working on. It’s a quick way to navigate and uncover all the information we need.
Hager says it is still too early to accurately measure the actual return on investment ABC Compounding will realize with the switch to Sage ERP X3, but many dividends became obvious from the start.
“We have only been live for a short time, but already our team is positive about the contribution of Sage ERP X3,” she concludes. “It is a powerful ERP solution with strong manufacturing capabilities.
We have been able to abandon several third-party applications that we had needed, because the functionality they provided is part of Sage ERP X3. That saves us money and effort. In addition, the comfort level of relying on a software solution that uses a modern, industry-standard database and platform can’t be underestimated.”
Key takeaway: Success in ERP implementation can lead to significant efficiency gains, cost savings, and improved customer service, as evidenced by ABC Compounding's experience with Sage ERP X3.
To read about ERP implementations that didn’t go nearly as smoothly, click here .

Free white paper

ERP Implementation: 9 steps to success
The 9 proven steps you should follow when implementing ERP
- I would like to receive free ERP resources via email

Click here if your download doesn’t start automatically .
Featured white papers

ERP Implementation Checklist
Over 120 actionable steps to implementing a new ERP successfully

Manufacturing ERP Implementation Checklist
Over 70 actionable steps to rolling out new manufacturing ERP software
Sign up to our newsletter Sign up
Your first ERP newsletter should arrive in your inbox soon.
Related articles

ERP implementation plan (ERP implementation process guide)
Everything you need to know about running a successful ERP implementation - and we mean everything

Why a food specific ERP system is a must-have
Key features and requirements food companies should consider when searching for an ERP

Calculating ERP implementation costs of top ERP systems
Where your ERP implementation budget should be allocated, and pricing models of top ERP

- A Comprehensive View of Supermarket Operations
- An Exploration of Business Process Maturity in Polish Organisations
- Demystifying MDA: A Response to Misconceptions
- Empowering Business Operations with EG Work Manager
- Navigating the Evolving Landscape of Process Modeling in the 21st Century
- The Evolution and Impact of Business Process Management in Organizations
- The State of Business Process Management
- Best Gold IRA Companies
- Best Precious Metals Companies
- Best Precious Metals Storage Companies
- Advantage Gold Review
- American Coin Co. Review
- American Hartford Gold Review
- APMEX Review
Augusta Precious Metals Review
- Beverly Hills Precious Metals Review
- Birch Gold Group Review
- Bishop Gold Group Review
- BlueVault San Diego Review
- BullionMax Review
- Capital Gold Group Review
- Colorado Gold Review
- Fidelity Review
- Gold Alliance Review
- Gold Avenue Review
- Goldco Review
- GoldDealer.com Review
- Golden State Mint Review
- Goldmoney.com Review
- Guidance Corporation Review
- Hard Assets Alliance Review
- IRA Financial Group Review
- iTrustCapital Review
- JM Bullion Review
- Lear Capital Review
- Lexi Capital Review
- Miles Franklin Precious Metals
- Monetary Gold Review
- Money Metals Exchange Review
- Nationwide Coin & Bullion Reserve Review
- Noble Gold Review
- Orion Metal Exchange Review
- Oxford Gold Group Review
- Patriot Gold Review
- Pimbex Review
- Red Rock Secured Review
- Rosland Capital Review
- SD Bullion Review
- U.S. Gold Bureau Review
- U.S. Money Reserve Review
- APMEX vs JM Bullion
- Birch Gold Group vs Augusta Precious Metals
- Birch Gold Group vs Noble Gold
- Goldco vs American Hartford Gold
- Goldco vs Augusta Precious Metals
- Goldco vs Noble Gold
- Are Gold IRAs a Safe Investment?
- Benefits of Diversifying a Retirement Portfolio With Gold
- Best Precious Metal to Buy or Invest in
- Bullion Investment Advice
- Can I Borrow From My IRA?
- Can I Set Up a Home Storage Gold IRA?
- Different Ways to Invest in Gold
- Gold IRA Investing Guide
- Gold IRA Tax Rules
- Gold IRA vs Gold ETF
- Gold IRA vs Physical Gold
- Gold IRA vs Roth IRA
- Gold IRA Withdrawal Rules
- Gold vs Platinum
- Gold vs Silver
- How to Buy Gold in an IRA
- How to Convert Your IRA into a Gold IRA
- How to Execute a 401k to Gold IRA Rollover
- How to Hold Physical Gold in an IRA
- How to Move 401k to Gold Without Penalty
- How to Start a Gold IRA
- Platinum vs Palladium
- Tips to Avoid Gold IRA Scams
- What are the Pros and Cons of a Gold IRA?
- What Gold is IRS Approved?
- What is a Gold IRA?
- What is a Gold IRA Rollover?
- Who Holds My Gold in a Gold IRA?
- Why Gold Has Intrinsic Value for Investors
- Why Invest in a Gold IRA?
Nestle USA installs SAP

Publications
by Grant HEnson
*The owners of this website may be paid to recommend some precious metals companies. The content on this website, including any positive reviews of these companies and other reviews, may not be neutral or independent.

Nestle USA, the U.S. subsidiary of the Swiss food conglomerate Nestle SA, embarked on a transformative journey to reorganize its business processes through the implementation of ERP packages.
The Need for Change
In the late 1980s and early 1990s, Nestle USA underwent a series of acquisitions, resulting in seven divisions that collectively offered popular brands such as Nescafe, Nestle Toll House, Lean Cuisine, and Baby Ruth. However, the lack of standardized systems and processes hindered efficiency and led to redundant practices.
For example, Nestle USA was purchasing vanilla at 29 different prices from the same vendor. This inefficiency was unacceptable for a company of Nestle USA's size and scale.
The ERP Solution
In 1997, Nestle USA decided to implement an ERP (enterprise resource planning) system to standardize its business processes across all divisions. ERP systems are designed to integrate all aspects of an organization's operations, from accounting and finance to manufacturing and sales.
Nestle USA chose SAP, the world's leading provider of ERP software, as its ERP platform. SAP offers a wide range of modules that can be customized to meet the specific needs of any organization.
The Benefits of ERP
The implementation of SAP ERP at Nestle USA resulted in a number of benefits, including:
- Increased efficiency: Standardized processes and procedures led to significant improvements in efficiency across all divisions.
- Reduced costs: The elimination of redundancies and the optimization of processes helped Nestle USA to reduce its costs.
- Improved decision-making: The availability of real-time data and insights from SAP ERP enabled Nestle USA to make better decisions about its business.
- Enhanced customer service: The improved efficiency and accuracy of Nestle USA's operations led to better customer service.
The Success of the Transformation
The ERP transformation at Nestle USA was a success. The company achieved its goals of standardization, efficiency, and cost reduction. Additionally, the ERP system helped Nestle USA to improve its decision-making and customer service.
This case study demonstrates the power of ERP systems to transform businesses. By standardizing processes and procedures, ERP systems can help organizations to improve their efficiency, reduce their costs, and make better decisions.
Nestle USA's ERP transformation is an inspiring example of how a strategic IT investment can lead to sustainable growth and success. By implementing SAP ERP, Nestle USA was able to streamline its operations, improve its efficiency, and enhance its competitiveness. This case study provides valuable insights for other organizations that are considering an ERP implementation.
Related Articles
Best gold ira companies, best precious metals company 2024.
Academia.edu no longer supports Internet Explorer.
To browse Academia.edu and the wider internet faster and more securely, please take a few seconds to upgrade your browser .
Enter the email address you signed up with and we'll email you a reset link.
- We're Hiring!
- Help Center
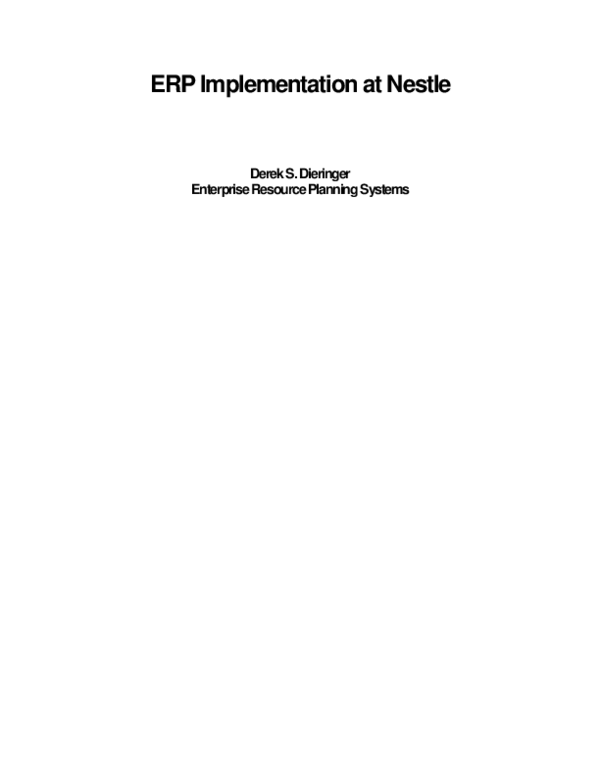
ERP Implementation at Nestle

Related Papers
Mohammad Anisur Rahman
Evolving in early 1990s, Enterprise Resource Planning (ERP) has become a global standard for the premier business firms for maintain their operations. ERP automates and streamlines business processes, reduces the complexity of collaboration, optimizes the operations that helps to gain superior control over business. However, ERP implementation success rate is meager in the world due to its complex nature of implementation and cost. This paper shows how to access the success of ERP implementation through a case study of a leading pharmaceutical company of Bangladesh. This study identified the causes of preliminary success in pre-implementation phase and the causes of delay in the implementation phase of ERP.
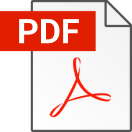
Trupti Dave
Introduction The evolution of ERP took place slowly and gradually from the 1960s. In the 1960s, very few companies could afford to own a computer. Therefore, both manufacturing and inventories were handled on the basis that companies must hold enough stocks to satisfy customer demand, and that customers would order what they had ordered in the past. In the 1970s and 1980s, when computers became small and affordable, attention was focused on Material Requirements Planning (MRP) and Master Production Schedule (MPS). MRP started as a system for planning raw material requirements based on the MPS. Soon it developed into Manufacturing Requirements Planning (MRP II), which used the MRP system as the basis and added scheduling and capacity planning activities. In the early 1990s MRPII was further extended into Enterprise Resource Planning (ERP), incorporating all the MRPII functionality, in addition to Finance, Supply Chain, Human Resources and Project Management functionality. What is ERP...
Information Technology and Management
Marc Schniederjans
Springer Series in Advanced Manufacturing
Jonas Hedman
Fatima Badr Omer Borham
Fatima Borham
This study aims to highlight on the effect of Enterprise Resource Planning System. Enterprise Resource Planning (ERP) system consists of different sets of software that are used to integrate the business functions in a company or organization. Given that these solutions provide an integrated solution to the needs of an organization, these systems are in high demand by all organizations. The full potential of these systems can only be realized only if they are successfully implemented. However, the implementation process is costly and time consuming, and thus requires careful planning and organization. If successfully implemented, ERP systems provide many benefits to those organizations that adopt them. On the other hand, if the implementation process is not successful, the venture can prove costly. By examining the existing literature on this topic, this paper focuses on how ERP systems can be successfully implemented in organization and the critical success factors. The information provided in this paper may be used to guide organizations in the implementation of ERP systems.
British Food Journal
Harry Kogetsidis
Proceedings of the 29th IRIS
International Journal of Enterprise Information Systems
Norita Ahmad
Transforming Enterprise Operations with Nexer and K3: A Case Study of The Regatta Group
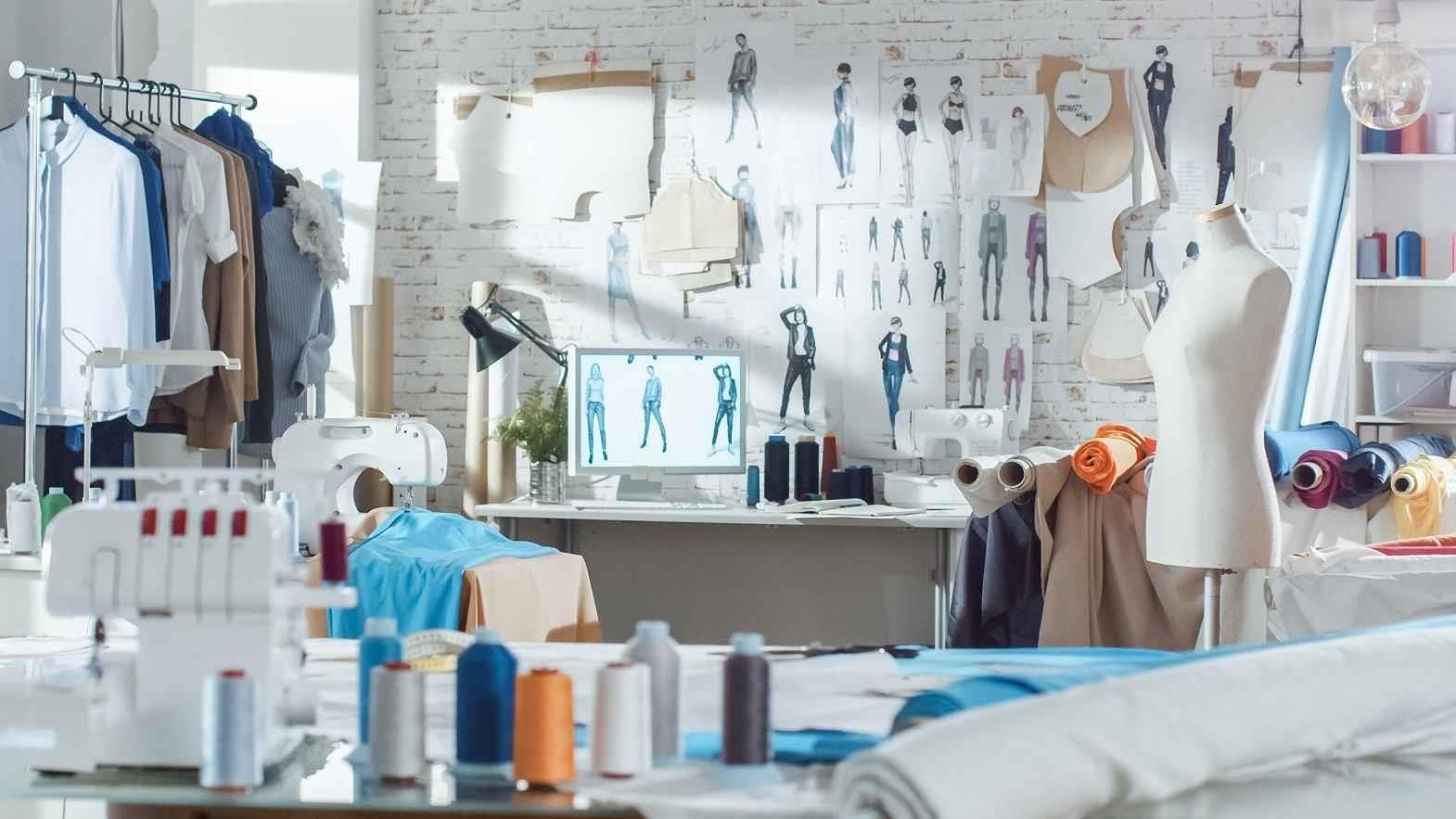
Fashion and apparel operate in a complicated environment, often creating and managing hundreds of thousands of Stock Keeping Units (SKUs) per year, or sometimes per season. Such work demands a robust Enterprise Resource Planning (ERP) but few in the market support the specific nuances of fashion.
Dynamics 365 is one of the leading ERPs available to fashion brands, and while the platforms are incredibly powerful, they can be tailored further through Microsoft Dynamics 365 Partners and Independent Software Vendors like Nexer and K3 respectively.
Who are Nexer and K3?
Nexer Enterprise Applications (formerly Sigma) is a leading global digital transformation expert specialising in Microsoft Dynamics 365. As a strategic advisor with more than 500 business experts in the Americas, Europe and Asia, Nexer helps its clients’ transition their operations to the cloud. With 24/7 proactive support, brands all over the world choose Nexer as their implementation partner.
The K3 Fashion Portfolio, on the other hand, provides fashion-specific solutions that are natively embedded in the D365 technical landscape to enable brands to handle their entire operations from concept to consumer.
Together, Nexer and K3 have revolutionised ERP environments for countless clients… like The Regatta Group. Speaking on the collaboration between Nexer and K3, Colin Crow, Managing Director, Nexer Enterprise Applications UK, said:
“The partnership with K3 and specifically its retail ISV add-on to Dynamics has brought significant benefits to Regatta who can, for the first time, run their entire business on one integrated system. This gives them visibility of their business from all angles making buying, selling, stock quantity, and pricing decisions in a much more effective way. Nexer really values the partnership with K3 and Regatta as a client. ”
Sunsetting an Esoteric System
The Regatta Group has over 2,500 employees across 16 countries, and offices and distribution centres across the world. In recent years, it set out to level up its mission-critical IT infrastructure to match its status as an industry leader and elevate its business operations.
The business first embarked on its multi-million-pound digital transformation project with Nexer five years ago. After investing in a new distribution centre and head office, the business turned its attention to enhancing its ERP systems.
Prior to this, the business had been operating with a legacy system that was developed and managed by a small group of colleagues.
The historic system had gradually expanded, with new functionalities being built onto it to accommodate the evolving needs of the business. But as the Group continued to go from strength to strength, this patchwork system began to bring its own set of challenges.
To prevent the esoteric system from stalling business operations and inhibiting growth, it quickly became clear to The Regatta Group that it needed to overhaul its IT operations entirely and implement a system fit for the future of the thriving business. But with the Group operating on both a wholesale and direct-to-consumer basis, and changes needing to be adopted across 16 different countries, this was set to be a complex undertaking.
Engaging Nexer and K3
The Regatta Group commissioned Nexer in 2019 to business solution, managing the analysis, build, testing, and project management stages of software implementation. It was the Group’s first time working with external consultants on a transformation project, but the team was assured by Nexer’s global expertise and reputation.
Nexer implemented Microsoft Dynamics 365 Finance & Operations, providing Regatta with a trusted, industry-standard solution that they could build upon and tailor to their unique business needs. The software delivered integrated ERP and CRM functionalities to help streamline and simplify Regatta’s processes across sales, customer service, marketing, finance, and operations. Nexer also introduced Microsoft Business Intelligence systems to facilitate cloud-to-cloud migration and align with Microsoft’s integrated software ecosystem.
Meanwhile, K3 Fashion was chosen to support Regatta’s outdoor clothing line as a concept-to-consumer solution seamlessly embedded in D365 Finance & Operations. With comprehensive support across the full fashion lifecycle, paired with its intuitive nature and ‘One Microsoft’ approach, it made sense to adopt a best-in-suite solution that would scale with Regatta.
Following the initial implementation, Nexer provided post-live support to The Regatta Group. Amid the peak of the 2023’s retail ‘golden quarter’, the Group chose to transition to Nexer’s Care365 service to receive seamless ongoing support and ensure they were maximising the new systems to their full potential.
Care365 takes a customised, people-first approach to delivering Microsoft Dynamics 365 post-live support, maintenance, and optimisation, helping to meet evolving operational needs and leverage new features to generate business benefits. By accessing the service, The Regatta Group can raise queries for quick resolutions, and Nexer also speaks directly to Microsoft on the Group’s behalf to handle more complex technical issues.
Doing More with Less
In the spirit of living up to Microsoft’s adage of “do more with less”, both Nexer and K3 firmly believe in empowering fashion brands with technology that facilitates smarter working – not harder.
Following the successful rollout of D365 Finance & Operations and K3 Fashion, legacy systems that limit access to valuable business insights and inhibit growth are a thing of the past for The Regatta Group. As a result of long-term collaboration with Nexer, the Group has successfully overhauled its IT ecosystem and transformed its operations to meet future demands.
Chris Bulmer, Consultant Director (AI and Automation) and former Group IT Director at The Regatta Group, who oversaw the project, commented:
“The Microsoft implementation project was a major milestone for The Regatta Group. Implementing Microsoft solutions has enabled us to consolidate our international operations, access more detailed reporting, and work smarter.
“We knew that Nexer had the expertise to execute the job, and working with the technical team in recent years has proven we made the right choice. It's clear that the team genuinely care and is invested in our business – they know our operations inside out and clearly want the best for us.”
Through Care365, Microsoft Dynamics 365 and Power BI will continue to work hard for the Group and empower its employees to work smarter. The group is now also exploring other functionalities as part of the integrated freedom it now enjoys through the Microsoft ecosystem.
Speaking on the decision to choose K3, Chris added:
“The Regatta-centric positioning of K3 highlighted how the new system would benefit us, with particular focus on K3 Fashion’s purpose-built nature for fashion and apparel. K3 has a strong track record in the outdoor fashion market, and it was clear to us that there was only choice – especially with the solution being fully embedded in D365.”
Discover more about how Nexer and K3 can overhaul your brand’s IT infrastructure at www.k3btg.com
- Ground Reports
- 50-Word Edit
- National Interest
- Campus Voice
- Security Code
- Off The Cuff
- Democracy Wall
- Around Town
- PastForward
- In Pictures
- Last Laughs
- ThePrint Essential

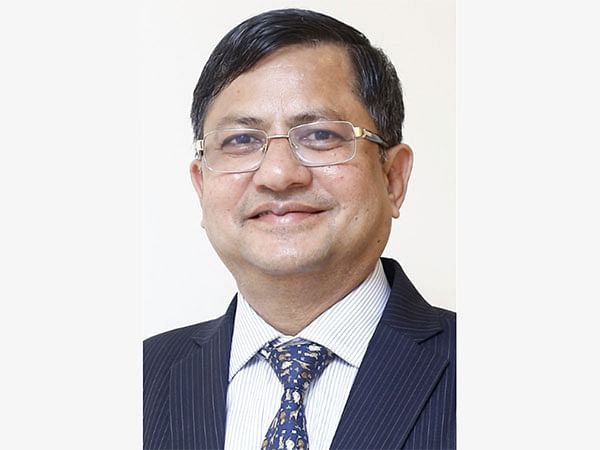
Pune (Maharashtra) [India], May 28: In the ever-evolving landscape of the construction industry, the shift towards digital transformation is not just a trend–it’s a necessity. As a AECO software & services company at the forefront of innovation, we understand the pivotal role technology plays in not just enhancing operational efficiency but also in driving significant cost savings. Among the myriad of technological advancements, cloud-based Construction ERP (Enterprise Resource Planning) systems stand out as a game-changer for businesses in the construction sector.
The Financial Edge of Cloud-Based Construction ERP:
Reduced IT Infrastructure and Maintenance Costs
Traditional ERP systems necessitate substantial upfront investment in IT infrastructure, including servers, storage, and an in-house IT team to manage and maintain this hardware. Cloud-based ERP solutions, on the other hand, eliminate these expenses. Hosted on the provider’s servers and accessed via the internet, they significantly reduce the need for physical hardware and the costs associated with its upkeep. This shift not only cuts down capital expenditure but also converts it into a predictable operational expense.
Enhanced Scalability and Flexibility
The construction industry is characterized by its dynamic nature, with the scale of operations constantly changing. Cloud-based ERP systems offer unparalleled scalability, allowing businesses to easily adjust their usage based on current needs without the need for physical hardware changes. This scalability ensures that companies pay only for what they use, optimizing expenses and improving financial flexibility.
Improved Data Accuracy and Decision-Making
Data is the lifeblood of decision-making in the construction industry. Cloud-based ERP systems provide real-time data access and analytics, empowering businesses with accurate information for timely decision-making. This immediacy not only improves project outcomes but also reduces costly delays and rework, directly impacting the bottom line.
Streamlined Processes and Increased Productivity
By integrating various business processes, from project management to finance and HR, cloud-based ERP systems create a cohesive workflow. This integration eliminates data silos, streamlines processes, and significantly enhances productivity. The efficiency gained translates into faster project completion times and reduced labor costs, contributing to overall financial health.
Enhanced Security and Compliance
Data security and regulatory compliance are critical concerns for the construction industry. Cloud-based ERP providers invest heavily in security measures, including data encryption and regular backups, ensuring that sensitive information is well-protected. Additionally, these systems are updated regularly to comply with the latest regulations, reducing the risk of costly legal penalties and protecting your company’s reputation.
The adoption of cloud-based Construction ERP systems is more than just a step towards digital transformation; it’s a strategic move that promises significant financial benefits. From slashing IT-related expenses to enhancing operational efficiency, the financial advantages are compelling. As a construction software company, we are committed to empowering our clients with solutions that not only meet the demands of today but also pave the way for a more profitable and efficient future. Embracing cloud-based ERP is not just an investment in technology–it’s an investment in your company’s financial health and competitive edge.
https://softtechglobal.com/
(ADVERTORIAL DISCLAIMER: The above press release has been provided by PNN. ANI will not be responsible in any way for the content of the same)
This story is auto-generated from a syndicated feed. ThePrint holds no responsibility for its content.
Subscribe to our channels on YouTube , Telegram & WhatsApp
Support Our Journalism
India needs fair, non-hyphenated and questioning journalism, packed with on-ground reporting. ThePrint – with exceptional reporters, columnists and editors – is doing just that.
Sustaining this needs support from wonderful readers like you.
Whether you live in India or overseas, you can take a paid subscription by clicking here .
LEAVE A REPLY Cancel
Save my name, email, and website in this browser for the next time I comment.
Most Popular
Mullaperiyar row flares up again as kerala seeks to proceed with dam study, tn warns of legal action, patanjali case has changed ad regulations. sc mandate only causes more trouble, pune porsche case: can the 17-yr-old accused be treated as an adult here’s what the law says.

Required fields are marked *
Copyright © 2024 Printline Media Pvt. Ltd. All rights reserved.
- Terms of Use
- Privacy Policy
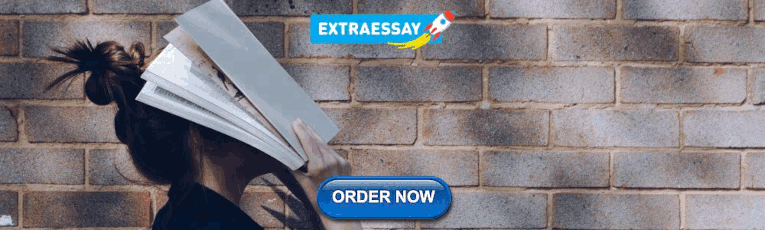
IMAGES
VIDEO
COMMENTS
Nestlé's Enterprise Resource Planning (ERP) Odyssey. News. May 15, 200215 mins. ERP Systems. In June 2000, Nestlé SA signed a much publicized $200 million contract with SAP—and threw in an ...
The Nestle USA case is an excellent case study for ERP implementations because it contains both successes and failures. There were obviously breakdowns during the planning phases of the project yet the overall result can be considered successful due to the consolidated system they now have in place and the amount of money that they are saving ...
To ensure a smooth, disruption-free transition to a more dynamic, reliable, and scalable infrastructure, Nestlé selected the RISE with SAP solution—a complete offering of ERP software, industry practices and outcome-driven services designed to help companies take advantage of cloud computing in their mission-critical, core systems. With its global cloud transformation, Nestlé is now able ...
Its annual revenue is around $8.1 billion with 16,000 employees. The ERP implementation at Nestlé, code-named BEST (Business Excellence through Systems Technology), had an estimated cost of $210 ...
The ERP system implementation literature contains many case studies of organizations that have implemented ERP system successfully. However, many Malaysian facing difficulties and challenges in ...
ERP case study #2: Nestle SA - Integration Excellence. As an enormous international candy-maker, Nestle SA headquartered in Konicki Switzerland, had harbored a goal of integrating ERP across all three of its operating companies; Nestle SA, Nestle UK, and Nestle USA. The latter operation had been working toward complete integration of a set of ...
In the case of Nestle USA, the ERP was part of the vision Nestle USA Chairman and CEO Joe Weller referred to as "One Nestle" that would be responsible for "transforming the separate brands into one highly integrated company" (Worthen, pg. 2). ... Recommendations The Nestle USA case is an excellent case study for ERP implementations ...
on a worldwide basis. An inductive case study (Yin 2003) approach was adopted for this study. Narrative contributed by the second author who was a key player in the ERP implementation in Nestlé formed the central plank on which the story was structured. The four facets of supply chain
Using a case study approach informed by documents, and accounts of key personnel involved in the development of single all encompassing ERP system in Nestlé a critical assessment of the supply ...
Application and Benefits of ERP - Case study on Nestle - Free download as Word Doc (.doc / .docx), PDF File (.pdf), Text File (.txt) or read online for free. The document summarizes an academic paper about Nestle's implementation of an ERP system across various divisions. It discusses how Nestle implemented SAP systems in its UK, Swiss, and US divisions to standardize processes and leverage ...
The ERP transformation at Nestle USA was a success. The company achieved its goals of standardization, efficiency, and cost reduction. Additionally, the ERP system helped Nestle USA to improve its decision-making and customer service. This case study demonstrates the power of ERP systems to transform businesses.
Nestle Erp Case Study Summary. 1327 Words6 Pages. Introduction: Nestle, which is the largest Food &Beverage company in the world, have an estimated 8,500 brands, manufactures around 10,000 various products in nearly 500 factories in 83 countries and employs some 250,00 people. The company markets its products in 130 countries across the world ...
The last rollouts will take place in the first quarter of 2003. and costly mistakes. It is a cautionary tale, full of lessons. Nestle's ERP Odyssey - An ERP implementation fraught with costly mistakes; hard-won lessons gleaned from this SAP project; why Nestle's CIO thinks pain was worth it - ….
Sreekumar Menon. This exploratory qualitative single case study discusses the benefits and process improvements pertinent to enterprise resource and planning (ERP) projects. The study was conducted in a Canadian case organization in the oil and gas industry that includes twenty participants from four project role groups of senior leaders ...
ERP Case Study #1: Fulton & Roark. Fulton & Roark, a retailer of men's grooming products, is an example of a successful ERP implementation. Prior to upgrading to full-featured ERP, the North Carolina-based business tracked its inventory in a spreadsheet and its financial data in desktop accounting software, Sage Live. When the company began ...
Approximate, during the third and fourth quarters of 1999, Hershey lost about 0.5% market share. The Hershey's failure to implement the ERP software on time led to the loss of $150 million in ...
Nestle is one of the largest food and beverage companies in the world. The company has adopted a comprehensive supply chain strategy as part of its business strategy. This strategy covers all areas of its operations, from sourcing raw materials to delivering finished products to customers. Nestle's supply chain strategy is focused on ensuring ...
Case Study: Nestle ERP implementation Background Nestle is a multinational company based on Switzerland, was establish long ago in 1866 by Henri nestle which supplies different kinds of food products. Over the period nestle has grown as one of the big company. Nestle USA is a part of nestle company, having seven business divisions: beverage ...
In the case of Nestle USA, the ERP was part of the vision Nestle USA Chairman and CEO Joe Weller referred to as "One Nestle" that would be responsible for "transforming the separate brands into one highly integrated company" (Worthen, pg. 2). ... Recommendations The Nestle USA case is an excellent case study for ERP implementations ...
View ERP Case Study-Nestle.pptx from MANAGEMENT 105 at Nirma Institute Of Management. SAP Implementation at Nestlé Case Study submitted for EDP-OM by ANKIT KUMAR NAYAN (195306) ANUBHAV BOSE AI Homework Help
2 must even prove effective. Increasing ERP specification is special, independently with their result. Businesses preparing that initial ERP deployment will benefit a lot from this case study.
Nexer Enterprise Applications (formerly Sigma) is a leading global digital transformation expert specialising in Microsoft Dynamics 365. As a strategic advisor with more than 500 business experts ...
Case Studies Of SaaS ERP Models. Oracle ERP Cloud offers a range of services within its ERP suite, such as financial management, procurement, project management and manufacturing processes.
An Analysis of ERP Systems Implementations. February 2020. DOI: 10.13140/RG.2.2.32309.22249. License. CC BY 4.0. Authors: Bienvenido Bartido Abad Jr. Institute of Business Studies, Papua New ...
Customer Case Study HENDRICKSON The Company: QAD DEVELOPS INNOVATIVE AUTOMATION SOLUTIONS TO MEET COMPANY'S NEEDS. Hendrickson is a leading global manufacturer and supplier for the commercial transportation industry.They produce medium and heavy-duty mechanical, elastomeric and air suspensions; integrated and non-integrated axle systems; auxiliary lift axle systems; parabolic and multi-leaf ...
BDO's ERP solution consultants support many leading cloud applications. The enterprise resource planning (ERP) lifecycle requires support. BDO's ERP solution consultants support many leading cloud applications. ... Enterprise Resource Planning Case Studies. Enterprise Resource Planning Insights. Explore our most recent resources and thought ...
Data is the lifeblood of decision-making in the construction industry. Cloud-based ERP systems provide real-time data access and analytics, empowering businesses with accurate information for timely decision-making. This immediacy not only improves project outcomes but also reduces costly delays and rework, directly impacting the bottom line.
Manufacturing ☁️ ERP | MES | Thought Leadership| Business Consulting l · First and foremost, I love manufacturing. Ever since being involved in the commissioning and operations of Aluminum smelter machines, I have been obsessed with the idea of manufacturing.<br><br>Previously, I have enjoyed many key positions throughout my career in Production, PPC, Quality, Maintenance, Process control ...
The present study examined how decision-making is affected by first (L1) and second languages (L2), emotion, and cognitive load. In a cross-task study, 30 Chinese-English bilinguals were asked to implement lexical-semantic judgment and gambling task. The results showed that after lexical decisions under high cognitive load, P3 was more positive for negative words than for neutral words in L1.
DYSON CASE STUDY INDIVIDUAL REPORT Information resources - a source of sustainable competitive advantage After the 'Knowledge Economy' in the 1990s; the business world, presently, is in the era of 'Intangible Economy'. Eustace (2003) discusses about the shift of corporate value system from the physical assets towards the intangible assets. . In the present era, sustainable ...