Academia.edu no longer supports Internet Explorer.
To browse Academia.edu and the wider internet faster and more securely, please take a few seconds to upgrade your browser .
Enter the email address you signed up with and we'll email you a reset link.
- We're Hiring!
- Help Center
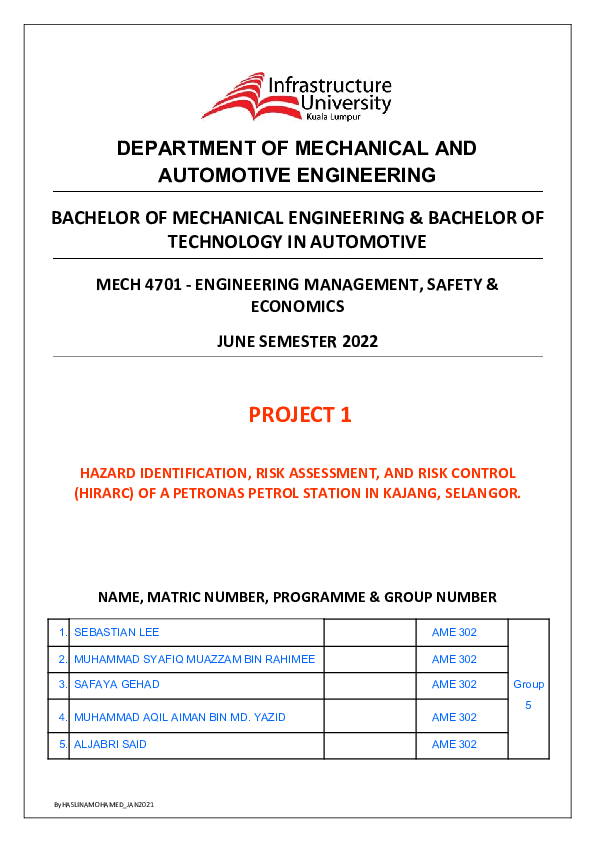
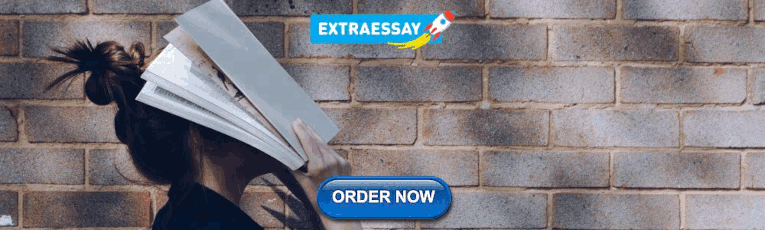
HAZARD IDENTIFICATION, RISK ASSESSMENT, AND RISK CONTROL (HIRARC) OF A PETRONAS PETROL STATION IN KAJANG, SELANGOR.

HIRARC, which stands for Hazard Identification, Risk Assessment, and Risk Control, is simply a strategy or tool deployed to identify hazards, probe and evaluate risks, establish risk management, and implement risk control. HIRARC is developed under the Occupational Safety and Health Act 1994 (OSHA 1994), specifically Section 15 (2a & 2b) and it is mandatory under the OSH Management Systems – Malaysian Standard (MS) 1722, Occupational Health and Safety Standard (OHSAS) 18000, among other management systems.
Related Papers
Sebastian Lee
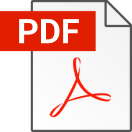
2011 National Postgraduate Conference
DR MOHD FARIS KHAMIDI
Adam Burgess
This case study examines the alleged hazard associated with mobile phone use at petrol stations and suggests that it is a phantom risk. Understanding its persistence in the absence of evidence, a number of factors are outlined. A precautionary safety regime enforced by oil companies in the UK established a restriction on mobile use on station forecourts that had the effect of confirming a danger. Warning signs in mobile phone handbooks had a similar effect and led to further restrictions at petrol stations. Among a number of problematic consequences, most ironic has been to distract from the real cause of the increased number of petrol stations fires at, particularly, American petrol stations. Investigations have identified the real cause; body static generated through vehicle re-entry while refuelling. This episode suggests the need for clarity about the precise reasons behind any restrictions on the use of a popular device that is already established as a potential, but invariably unconfirmed, health hazard.
Ikhwanul Muslimin
Lecture Notes in Computer Science
Do Thanh Dong
raeesa moolla
IOSR Journals
The presence of gas stations in residential areas is very dangerous for what can happen in case of accidents, fires, fuel leaks from tanks or even among vehicles when filling, refueling, in addition to the risk of toxic gases due to lead in gasoline. The article evaluates disaster management in the operational reality of gas stations in urban areas. It also analyzes the reality of occupational diseases and accidents at work of employees in those infrastructures. On this basis, appropriate recommendations and proposals are put forward to serve in the drafting of legislation regulating the distribution of hydrocarbon fuel and disaster management.
Arif Hanafi
RELATED PAPERS
Journal of Environmental & Earth Sciences
Wisdom Chukwuemeke
Wishal Kurnia
Safety Science
Sameek Bhattacharya
Asian Journal of Applied Sciences
Nooh Abu Bakar
F. Markert , Nijs Duijm
HAKIM MULINDWA
THE INTERNATIONAL JOURNAL OF HUMANITIES & SOCIAL STUDIES
Sophia Dauda
International Journal of Engineering & Technology
Mohammad Hussaini Wahab
Advances in Science, Technology and Engineering Systems Journal
Dieudonné Bitondo
masrur tanjil
IAEME Publication
Cogent Environmental Science
Francis Attiogbe
Jeremy Smallwood
Kwanele Qonono
allizon flores
Journal of Environmental and Occupational Science
Asantewa Gyamfi
International Journal of Environmental Research and Public Health
Bożena Kukfisz
Divyanshu Singh
Zeszyty Naukowe SGSP
Norbert Tuśnio
Mir Aftab Hussain Talpur
Editor IJERMS
International Journal of Preventive, Curative & Community Medicine
Akshaya Naik
JOURNAL ASRO
Sukmo Hadi Nugroho
June Mellawati
Current Journal of Applied Science and Technology
Prince Mmom
VF-Report 12/2007
Otto Andersen
Faridah Wahab
Argonne, Illinois, ANL/ESD-TM-160
Steven Plotkin
www.researchgate.net
Dr Yehia F Khalil
Jaakko Paasi
Ecotoxicology and environmental safety
Mahmoud Mohammadyan
Carl Rivkin
Journal of Building Construction and Planning Research
Ismail Wadembere
Process Safety Progress
International Journal for Research in Applied Science and Engineering Technology
Sachin Vasudevaiah
James Mutua
RELATED TOPICS
- We're Hiring!
- Help Center
- Find new research papers in:
- Health Sciences
- Earth Sciences
- Cognitive Science
- Mathematics
- Computer Science
- Academia ©2024

What is a HIRARC Document and How to Use It
HIRARC stands for Hazard Identification, Risk Assessment, and Risk Control. It is a systematic approach to managing occupational safety and health in workplaces. This methodology is developed by the Department of Occupational Safety and Health (DOSH) Malaysia to identify potential hazards, assess the associated risks, and implement control measures to mitigate or eliminate those risks at the workplace. The full document on HIRARC is released under the name of Guidelines for Hazard Identification, Risk Assessment and Risk Control (HIRARC) published in 2008.
What is the Purpose of HIRARC?
The guideline aims to offer a structured and impartial method for evaluating hazards and the risks linked to them. The goal is to establish an unbiased assessment of identified hazards and to present a strategy for managing the associated risks.
It should be noted that compliance with the guideline is part of the overall responsibilities outlined in the Occupational Safety and Health Act 1994 (Act 514) , wherein employers are obligated to ensure the safety of workplaces for both their employees and other relevant individuals.
Kindly note that the methodology of HIRARC as proposed in this Guidelines is intended for the assessment of physical hazards . Those who intend to assess health hazards in their workplaces, should make use of other risk assessment guidelines designed specifically for such purposes.
What Does a HIRARC Look Like?
In common practice, HIRARC is presented in a table format which is called a HIRARC Form, like below. Note that you can use your own version as long as it contains the important contents as shown here.

In an Organization, Who Should Do the HIRARC?
HIRARC is not a solitary endeavor! It is a common misconception for organizations to assume that the responsibility of conducting and establishing HIRARC documentation solely lies with the ‘Safety Personnel.’ In reality, the HIRARC process demands a collaborative effort involving the process owner(s) or person(s) in charge who possess a comprehensive understanding of the entire process.
Simultaneously, the Safety Personnel should be integral members of the team, contributing to coordination and providing relevant safety concepts and insights throughout the development process. The synergy between these parties is crucial to ensure comprehensive coverage of all associated risks.
However, when it comes to producing and writing the final HIRARC documentation, a different approach is necessary. Following the brainstorming session outlined above, organizations must decide which party will compile all the inputs and formalize them into a legally binding document. It’s essential to keep this in mind!
What is Risk?
In simple terms, risk is the possibility or chance of something bad happening. It’s about the potential for harm, damage, loss, or any negative outcome. When we talk about risk in different contexts, like in finance or safety, it’s about understanding and managing the likelihood and impact of undesirable events.
Let’s simplify the concept with following situation. Imagine you’re planning to go on a picnic with friends. There are a few risks involved in this simple scenario:
So there you go! In everyday life, we naturally assess and manage risks to make informed decisions. Developing an awareness and thoughtful consideration of risks in our daily lives empowers us to make informed choices that contribute to our overall well-being while reducing the likelihood of undesirable outcomes.
This principle seamlessly extends to our workplace environment , where the assessment of risks involves careful consideration of multiple factors to ensure a safe and conducive work setting. By embracing a proactive approach to risk evaluation, we pave the way for a healthier, more secure, safer and more productive work experience.
Can We Calculate Risk?
Yes! In fact, this article will explain in detail how to do so. The formula to calculate risk is as follows:
Risk = Likelihood x Severity
But you may be wondering how do we assign values to that Likelihood and Severity. Let’s continue with the next topic.
How Do We Assign Values to Likelihood and Severity?
In simpler terms, ‘Likelihood’ value tells us how likely it is that a certain event will happen. To figure this out, we can ask questions like “ Has this happened before, and how often? ” Assessing likelihood involves looking at past experiences, analyzing data, or using measurements. The likelihood levels are on a scale from “most likely” to “inconceivable.”
Let’s break it down with an example. Imagine a small spill of bleach from a container when filling a spray bottle. This is something that is considered most likely to happen, and it might occur every time someone does this task during their shift given that he or she has to do the refill a few times per day.
On the other hand, think about a leak of diesel fuel from a securely sealed tank. This is less likely to happen compared to the bleach spill. So, the likelihood is lower for the diesel fuel leak.
In summary, when we talk about likelihood, we’re trying to estimate how probable it is for something to occur based on past experiences or careful analysis, and it can range from very likely to almost impossible.
Therefore, the guideline provides a simplified Likelihood table shown below for our reference. Note that you can define any suitable ‘Quantitative Approach’ that suits to the nature of your workplace.
Let’s now define the ‘Severity’ table as per guidelines.
Without further ado, let’s create our HIRARC document.
HIRARC Worked Example: Wood panel cutting process
Here is the scenario,
A team of two workers operates a cross-cut saw machine. Their work includes loading wood panel onto the machine, cutting the wood and unloading the cut wood. They also need to repair and maintain the machine regularly as well as to change the blades of the machine.
Caution: This example may not be applicable to similar work in your workplace
To simplify things, let’s break down the HIRARC development into 3 vital stages that are:
- Hazard Identification
- Risk Analysis
- Risk Control
1. Hazard Identification
Before we can pinpoint the hazards associated with each step of the wood panel cutting activity, it’s essential to first identify the critical job steps within the entire process.
What is Hazard?
Exercise caution when identifying each job step, avoiding excessive detail on trivial tasks . The goal is to ensure the inclusion of all critical steps necessary to complete the entire process.
2. Risk Analysis
After completing the Hazard Identification phase, we can proceed to analyze the risks as outlined below. It’s essential to note that as the number of your ‘Existing Risk Controls’ increases, the ‘Likelihood’ should decrease. In other words, they are inversely proportional.
Envision a new worker operating the cutting machine. Initially, there might be a few ‘mistakes,’ but by actively ‘controlling’ his works through peer-to-peer guiding and instructing the worker through training, he will undoubtedly improve in his tasks, leading to a reduction in ‘mistakes.’ The same principle applies to the likelihood of hazard realization.
Now, what about the Severity rating? In many instances, the Severity rating linked to a specific hazard remains constant. However, it’s crucial to carefully examine each case to ensure accurate assessment.
3. Risk Control
Before delving into recommending additional risk controls to our hazards, let’s familiarize ourselves with the concept of priority. While the ideal scenario would involve entirely risk-free work activities, the practical world presents a different reality due to various organisational factors such as cost of implementation and resources allocation.
What is Risk Controls?
The objective of the risk controls is to bring down the risk to a level that is “ reasonably practicable ” to the organization.
Nevertheless, we can effectively prioritize based on the level of risk. To aid us in this process, the guidelines have furnished us with the following Risk Matrix.
To further enhance our decision-making process, the guidelines provide us with the ‘Action Priority’ table, depicted below.
Let’s proceed with the final section of the HIRARC documentation, focusing on assigning additional risk controls.
Lastly, all you need to do now is piece all the 3 parts together into a comprehensive HIRARC form.
There you have it! We’ve successfully created HIRARC documentation for one specific work activity among many. Now, you can proceed with addressing the remaining work activities within your workplace.
As a reminder, don’t forget to incorporate non-routine work activities into the HIRARC development process. The inclusion of non-routine activities is essential, and their specifics should be determined and defined based on the unique nature of your workplace.
When Should You Revise a HIRARC?
There isn’t a predetermined schedule for revising a HIRARC, but it is advisable to conduct timely reviews, such as annually or once every three years. As a general guideline, you should contemplate a review if any of the following conditions occur in the workplace:
- Substantial alterations to the work process, encompassing changes in terms of personnel, machinery, methodologies, materials, or measurement.
- Introduction of new processes, materials, or machinery into the work environment.
- Occurrence of accidents or injuries related to the specific work process in question.
Read HIRARC Guidelines by DOSH
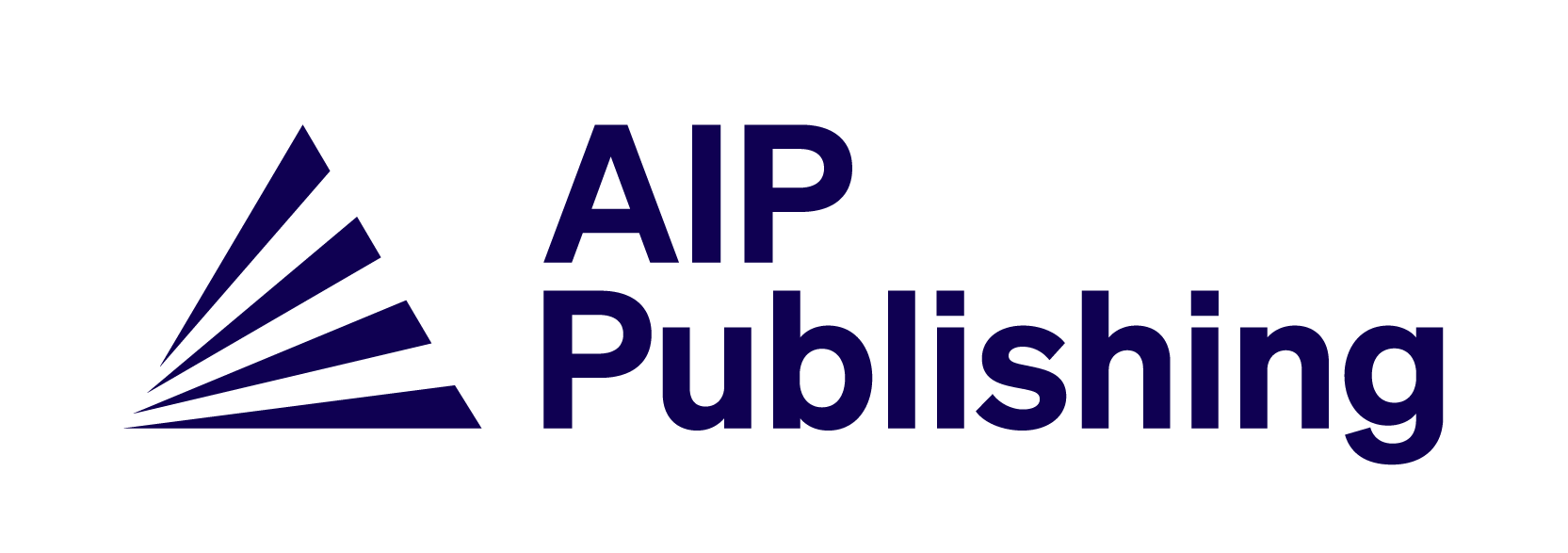
HIRARC evaluation on chemical factories in Malaysia
- Article contents
- Figures & tables
- Supplementary Data
- Peer Review
- Reprints and Permissions
- Cite Icon Cite
- Search Site
M. Fathullah , N. R. Nik Yusoff , Vertic Eridani Budi Darmawan , L. X. Yin , T. W. Yee , T. S. Teng , T. H. Jui , Y. N. Fong; HIRARC evaluation on chemical factories in Malaysia. AIP Conf. Proc. 3 May 2021; 2339 (1): 020203. https://doi.org/10.1063/5.0045231
Download citation file:
- Ris (Zotero)
- Reference Manager
This paper reports on case studies of safety incidents in chemical factories in Malaysia. The processes used for identifying and evaluating both existing and potential hazards in a palm-oil work site and the way of controlling it is hazard identification, risk assessment and risk control or known as HIRARC. Many that have already done risk assessments have recorded successful changes to their working procedures, and conditions of work in establishing and taking the appropriate effective actions. An ergonomic, physical and chemical hazards is a main factor in occurred in this study that could cause damage to humans, systems and environments. The assessment was done in estate area, involving the process of oil palm harvesting and collecting operation, oil palm manuring, and oil palm field upkeep and maintenance. The overall methodologies in this study consist of fishbone concept, HIRARC and PARETO analysis towards the working procedures at loading ramp station in palm factory. At the end of this paper, a list of recommendations is made to ensure the risk assessed can be minimzed in future.
Sign in via your Institution
Citing articles via, publish with us - request a quote.
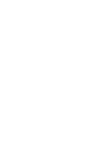
Sign up for alerts
- Online ISSN 1551-7616
- Print ISSN 0094-243X
- For Researchers
- For Librarians
- For Advertisers
- Our Publishing Partners
- Physics Today
- Conference Proceedings
- Special Topics
pubs.aip.org
- Privacy Policy
- Terms of Use
Connect with AIP Publishing
This feature is available to subscribers only.
Sign In or Create an Account

An official website of the United States government
The .gov means it’s official. Federal government websites often end in .gov or .mil. Before sharing sensitive information, make sure you’re on a federal government site.
The site is secure. The https:// ensures that you are connecting to the official website and that any information you provide is encrypted and transmitted securely.
- Publications
- Account settings
Preview improvements coming to the PMC website in October 2024. Learn More or Try it out now .
- Advanced Search
- Journal List
- Indian J Occup Environ Med
- v.21(2); May-Aug 2017
Hazard Identification, Risk Assessment, and Control Measures as an Effective Tool of Occupational Health Assessment of Hazardous Process in an Iron Ore Pelletizing Industry
Assistant General Manager (Medical), Jindal Stainless limited, Jaipur, Rajasthan, India
B. K. Sikdar
1 Deputy Chief Inspector of Factories (Med) and Certifying Surgeon, West Bengal, India
Background:
With the growing numbers of iron ore pelletization industries in India, various impacts on environment and health in relation to the workplace will rise. Therefore, understanding the hazardous process is crucial in the development of effective control measures. Hazard Identification, Risk Assessment, and Control measures (HIRAC) acts as an effective tool of Occupational Health Assessment.
The aim of the study was to identify all the possible hazards at different workplaces of an iron ore pelletizing industry, to conduct an occupational health risk assessment, to calculate the risk rating based on the risk matrix, and to compare the risk rating before and after the control measures.
Materials and Methods:
The research was a cross-sectional study done from March to December 2015 in an iron ore pelletizing industry located in Odisha, India. Data from the survey were collected by inspecting the workplace, responses of employees regarding possible hazards in their workplace, reviewing department procedure manual, work instructions, standard operating procedure, previous incident reports, material safety data sheet, first aid/injury register, and health record of employees.
A total of 116 hazards were identified. Results of the paired-sample's t -test showed that mean risk rating differs before taking control measures (M = 9.13, SD = 5.99) and after taking control measures (M = 2.80, SD = 1.38) at the 0.0001 level of significance ( t = 12.6428, df = 115, N = 116, P < 0.0001, 95% CI for mean difference 5.34 to 7.32). On an average, risk reduction was about 6.33 points lower after taking control measures.
Conclusion:
The hazards having high-risk rating and above were reduced to a level considered As Low as Reasonably Practicable (ALARP) when the control measures were applied, thereby reducing the occurrence of injury or disease in the workplace.
I NTRODUCTION
India has the fourth largest iron ore reserves in the world after Russia, Brazil, and Australia.[ 1 ] As per the survey conducted by the Indian Bureau of Mines (IBM) in April 2000, India had 9919 million tonnes of recoverable reserves of haematite and 3546 million tonnes of magnetite.[ 1 ]
As good quality iron ore deposits are depleting very fast, beneficiation technologies have to be adopted to meet iron ore demand. Agglomeration technologies such as pelletization/sintering have to be added to steel plant so that concentrates can be used as feed material.[ 1 ]
Pelletization plants beneficiate fines and transform the unusable low grade fines into an easily consumable feed for blast furnaces.[ 1 ] The present production capacity of pelletization in eastern region is 28.7 MMT, which will increase to 40.7 MMT in the coming time after commissioning of about 9 number of units, which are at various stages of commissioning.[ 1 ] With the growing numbers of pelletization plants, various impacts on environment and health will rise.
A critical part of any Occupational Health and Safety program is the identification, assessment, elimination and/or the control of hazards in the workplace. Risk assessment is the process of evaluation of the risks arising from a hazard, taking into account the adequacy of any existing controls and deciding whether or not the risks is acceptable.[ 2 ] It is impossible to eliminate all hazards, so the goal is to eliminate and/or control the hazards with critical and high potential risk to the lowest reasonable risk level so as to protect workers from harm.
Section 2 (cb) of the Indian Factories Act, 1948, defines hazardous process as follows:
“Hazardous process” means any process or activity in relation to an industry specified in the First Schedule where, unless special care is taken, raw materials used therein or the intermediate or finished products, by-products, wastes, or effluents thereof would:
- Cause material impairment to the health of the persons engaged in or connected therewith, or
- Result in the pollution of the general environment.[ 3 ]
Hazard means a source or a situation with a potential for harm in terms of human injury or ill health, damage to property, damage to the environment, or a combination of these.[ 4 ]
Hazard identification means the identification of undesired events that lead to the materialization of the hazard and the mechanism by which those undesired events could occur.[ 4 ]
Risk is, at minimum, a two-dimensional concept involving (1) the possibility of an adverse outcome, and (2) uncertainty over the occurrence, timing, or magnitude of that adverse outcome.[ 5 ] If either attribute is absent, then there is no risk.[ 5 ]
Risk assessment is a systematic process for describing and quantifying the risks associated with hazardous substances, processes, actions, or events.[ 5 ]
Risk assessment method can be defined as any self-contained systematic procedure conducted as part of a risk assessment – that is, any procedure that can be used to help generate a probability distribution for health or environmental consequences.[ 5 ]
Hazard Identification Risk Assessment (HIRA) is a process of defining and describing hazards by characterizing their probability, frequency, and severity and evaluating adverse consequences, including potential losses and injuries. A risk assessment that provides the factual basis for activities proposed in the strategy to reduce losses from identified hazards.[ 6 ] The ISO Risk Management Principles and Guidelines standardize risk assessment in four parts: risk identification, risk analysis, risk evaluation, and risk treatment. The first step — risk identification — is achieved by identifying all hazards and their subsequent consequences.[ 7 ] Local risk assessments must provide sufficient information to enable the jurisdiction to identify and prioritize appropriate mitigation actions to reduce losses from identified hazards.[ 6 ]
Hazard control means the process of implementing measures to reduce the risk associated with a hazard.[ 4 ]
Scope of the study
The occupational health risk assessment shall address the following:
- The hazards of the process involved in different activities
- Semi-quantitative evaluation of the possible health and safety effects of failure of controls
- Engineering and administrative controls applicable to the hazards and their interrelationships, such as appropriate application of detection methodologies to provide early warning of release.
M ATERIALS AND M ETHODS
Study design.
The study was cross-sectional in design and involved semi-quantitative methods of data collection. Primary data was obtained by inspecting the work place, interacting with employees regarding the possibility of hazards, reviewing the department procedure manual, work instructions, standard operating procedure, and incident report, whereas secondary data was collected using Material Safety Data Sheet (MSDS), first aid/injury register, health record of employees, journals, and literatures.
Study settings
The study was carried out in a 4-m tonne iron ore pelletizing industry located in Odisha, India from March to December 2015. The pellet plant used travelling grate technology to convert low grade fines into value-added pellets.
The slurry was received at the pellet plant from the beneficiation plant through a 220-km pipe line. It was stored in the holding tanks before being fed through pressure filters and mixed with the additives. The purpose of the additives - limestone, bentonite, coke, and anthracite – was to improve the physical and metallurgical properties of the pellets during processing and in final use. A disc pelletizer was then used to ball the mixture into “green balls” about the size of a marble.
A roller screening mechanism was used to remove any undersized material before the green balls enter the final stage of production, the induration furnace. The induration process used travelling grate technology and a series of updrafts and downdrafts to dry and gradually heat the green balls to remove moisture before entering the combustion zone where they were first preheated to minimize thermal shock, then fired, and ultimately cooled in various sections of the furnace. After screening out oversized and undersized pellets, the final product – which had the required properties for charging a blast furnace and ready to withstand handling and transportation – were transferred by conveyor to a stockpile.
Methodology
The different steps of methodology are mentioned in the Figure 1 .

Flow chart of methodology of hazard identification, risk assessment, and control measures
Classification of work activities
Identification of hazard.
All the work activities pertaining to various departments were minutely examined to identify all the possible hazards inherent to the nature of work or work environment [ Table 1 ]. The following methods were used to identify the hazards in the workplace:
Department-wise work activities of pellet plant

- Walking around the workplace to inspect what is in the general area
- Employee participation by interacting with them regarding their work place, working hours, and the possible hazards they noticed [ Annexure 1 ]
- Reviewing of Department Procedure Manual (DPM), Work Instruction, and Standard Operating Procedure (SOP) and comparing it with the regular practice
- Reviewing previous Incident Reports
- Reviewing Material Safety Data Sheet (MSDS)
- Reviewing first aid/injury records
- Reviewing health records of employees.
Identification of risk
After all the possible hazards were identified, the occupational health risk that could be associated with the hazard was identified by studying previous incident reports, MSDS, first aid/injury records, and health records of the employees.
Assessment of risk
Risk assessment was done using semi quantitative method [ 8 ] based on two key factors [ Table 2 ]:
Semi quantitative method of risk assessment

- The likelihood that the injury (or illness) may actually occur
- The severity of the injury (or illness) resulting from the hazard.
Control of risk
Risk rating can prioritize hazards with the highest potential to cause an injury so that they can be eliminated first [Tables [Tables3 3 and and4 4 ].
Control measures and its effectiveness

Control measures based on risk rating

The following steps were taken for the control of risk:
- Quick attention to critical or high-risk hazards
- Effective temporary solutions until permanent fixes were applied
- Long-term solutions for those risks which can cause long-term illness
- Long-term solutions for those risks with the worst consequences
- Training of workers on the risks, which continue to remain and its control measures
- Regular monitoring to check whether control measures are intact or not.
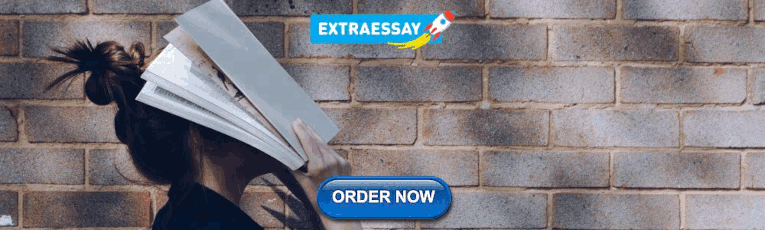
Documentation of procedure
Documenting the process helps to ensure that the identified risk control measures are implemented in the way they were intended. It will also assist in managing other hazards and risks that may be in some way similar to ones already identified. Adequate record keeping of the risk management process should show that the process has been conducted properly. This information should include:
- Hazards identified
- Assessment of the risks associated with those hazards
- Decision on control measures to manage exposure to the risks
- How and when the control measures are implemented
- Evidence of monitoring and reviewing of the effectiveness of the controls.
Monitoring and review
It involves reassessment of the risk to see whether there is a reduction of risk rating from critical and high risk to a level considered As Low as Reasonably Practicable (ALARP).
In this plant, 116 hazards were identified and their analysis was performed. They have been classified into five major categories [ Figure 2 ].

Frequency of different hazards in an iron ore pelletizing industry
- Fire and explosion
- Dust, chemicals, and toxic substances
- Ergonomical
- Psychosocial
The major hazards, risk assessment, and the reduction of risk after taking appropriate control measures are tabulated below [ Table 5 and Figure 3 ].
Hazard identification, occupational health risk assessment before and after control measures

Reduction of extreme and high risk rating to acceptable risk rating after control measures
Statistical analysis
Statistical analysis involves the calculation of the mean of a set of values in a sample used for observational study.[ 9 ] Hypothesis testing is used to make an inference about a population that is under study.[ 9 ] The null hypothesis is the assumption that the mean will be equal to zero.[ 9 ] The paired t -test is a type of hypothesis testing that is used when two sets of data are being observed.[ 9 ] The data in a paired t -test are dependent, because each value in the first sample is paired with a value in the second sample.[ 9 ] The parameter used to make the inference is the difference of the means of both data sets.[ 9 ]
Statistical analysis was done using GraphPad's website.[ 10 ] A value of P < 0.05 was considered significant [ Table 6 ].
Statistical analysis of risk reduction after control measures

Results of the paired-samples t -test show that mean risk rating differs before taking control measures (M = 9.13, SD = 5.99) and after taking control measures (M = 2.80, SD = 1.38) at the 0.0001 level of significance ( t = 12.6428, df = 115, n = 116, P < .0001, 95% CI for mean difference 5.34 to 7.32). On an average, risk reduction was about 6.33 points lower after taking control measures.
D ISCUSSION
In this cross-sectional study, it was found out that by applying control measures, hazards having high risk rating and above was reduced to a level considered ALARP. The findings suggest that Hazard Identification, Risk Assessment, and Control measures (HIRAC) study on a routine basis can serve as a tool to reduce occurrence of injury or disease in any manufacturing industries.
Health, Safety, and Environment (HSE) department is the core pillar of any manufacturing industry. Other departments such as manufacturing, engineering services, commercial, and human resources are strongly linked with the HSE department [ Figure 4 ].

Integrity of health safety and environment (HSE) department with other departments
HSE department has a lot of common functions and they play a great role in identifying hazards, risk assessment studies, and their control measures through monthly Safety Committee meeting.
In tough economic times, it is important to remember that poor workplace safety and health costs money. What's more, case studies show that good Occupational Safety and Health management in a business is linked to improved performance and profitability.[ 11 ]
The various steps of occupational health assessment of hazardous process in an iron ore pelletizing industry are as follows:
Process description
The concentrate slurry is received at pellet plant and stored in slurry tanks [ Figure 5 ]. The concentrate slurry is fed to the filtration process where it is de-watered by pressure filters. The product comes out is called filter cake (moisture 9%), which is stored in bin for further process of mixing. The filtrate water so generated is sent to process reservoirs via thickener for storage and internal plant consumption.

Process flow chart of iron ore pelletizing industry
Pellet plant is facilitated with additives grinding unit as the process of pelletization requires binder and additives. Bentonite is used as a binder for proper balling of the filter cake particles in to spherical shaped balls with certain compression strength. The bentonite is stored and ground in a Vertical mill by dry grinding process to desired fineness (−200 mesh, 80%). The powdered bentonite is stored for further mixing process. Limestone is used as a fluxing agent and to get strength to the pellet by heat hardening. Coke dust is used as a compensatory fuel and to improve physical strength of the pellets by uniform firing of each pellet up to the core. Both limestone and coke are ground in a definite lime to coke ratio in a ball mill by dry grinding process. The product is lime + coke powder mix of desired fineness (−200 mesh, 80%) is stored for subsequent mixing process.
In mixing and baling building, bentonite, lime + coke mix are added to the concentrate filter cake at a definite rate of addition and is thoroughly mixed in a vertical mixer. The so-mixed concentrate is called mixed material, which is fed to a rotating inclined disc pelletizer. Fine ore particles are agglomerated in to spherical-shaped balls due to the rotating action of the disc. The so-formed balls are called green balls which are further screened and fed to an induration machine.
In induration building, the green balls are fed to the induration machine which forms endless chain of pallets, are slowly brought through different zones of the induration furnace by the horizontal movement of the pallets. These green balls are subjected to drying (280–340°C), preheating (350–900°C), firing (900–1330°C), and cooling (1330–100°C) in the induration furnace where pellets are in directly heated in a controlled manner by circulation of hot gases with the help of process fans. Heat energy is supplied by oil fired burners. LSHS/FO is used as fuel and source of heat energy, which is stored and pumped to burners. Critical parts of the induration furnace are cooled by water circulation. The fired and cooled pellets with good physical strength is conveyed and stored in pellet stock pile. The pellets are dispatched to the customers as a feed to blast furnace and/or Direct Reduced Iron production.
Material safety data sheet
A Material Safety Data Sheet (MSDS) provides basic information on a material or chemical product. It contains information on the properties and potential hazards of the material, how to use it safely, and what to do if there is an emergency.[ 12 ]
The MSDS is an essential starting point for the development of a complete health and safety program for the material.[ 12 ]
MSDS deals with the following:[ 12 ]
- Chemical product and company identification
- Composition/Information on ingredients
- Hazards identification
- First aid measures
- Fire-fighting measures
- Accidental release measures
- Handling and storage
- Exposure controls/Personal protection
- Physical and chemical properties
- Stability and reactivity
- Toxicological information
- Ecological information
- Disposal considerations
- Transport information
- Regulatory information
- Other information.
The following MSDS were collected to study the hazardous process and its control measures in the iron ore pelletizing industries:
- Material Safety Data Sheet (MSDS) Iron ore; Cliffs Natural Resources [ 13 ]
- Material Safety Data Sheet (MSDS) Bentonite; Sciencelab.com, Inc [ 14 ]
- Material Safety Data Sheet (MSDS) Lime [ 15 ]
- Material Safety Data Sheet (MSDS) Furnace Oil.[ 16 ]
Hazard identification
- Fugitive dusts
- Particulate matter
- Iron Oxide, Silica, Crystalline Silica as Quartz, Crystalline Silica as Cristobalite, Al 2 O 3 , CaO, MgO.
- Metals – Iron
- Chemicals – acid, alkali
- Fumes (sulphur dioxide, oxides of nitrogen).
- Psychosocial.
Risk assessment
Risk assessment can be done in three ways:
- Qualitative
- Quantitative
- Semi-quantitative.
However, semi-quantitative risk assessments are currently widely used to overcome some of the shortcomings associated with qualitative approaches.
Semi-quantitative method
Semi-quantitative risk assessment takes the qualitative approach a step further by attributing values or multipliers to the likelihood and consequence groupings. It may also involve multiplication of frequency levels.
All risks cannot be eliminated. Urgent action is required for risks assessed as critical or high which may include instructions for immediate cessation of the work and/or isolation of the hazard until permanent measures can be implemented. Documented control plans with responsibilities and completion dates need to be developed for moderate risks.
Acceptable risk
Risk that is acceptable to regulatory agency and to the public is called acceptable risk. There are no formally recognized regulatory criteria for risk to personnel in the mining industry. Individual organizations have developed criteria for employee risk and the concepts originally arising from chemical process industries and oil and gas industries.
Because of the uncertainties linked with probabilistic risk analysis used for quantification of the risk levels the general guiding principle is that the risk be reduced to a level considered ALARP.
Preventive measures
The aim of implementation of prevention measures is to reduce the likelihood of work accident or occupational disease occurrence.[ 3 ] The measures used are as follows:

Hierarchy of control measures
- Remove – during the workspace designing phase, any equipment not meeting the occupational health standards should not be used
- Reduce – levels of hazardous substances can be reduced by proper ventilation through exhaust fans
- Replace – high-risk equipment or substances should be replaced by low risk ones.
- Training of employees – Workers must know the risks they are exposed to, the harm they might cause, and precautions that could prevent these harmful effects
- Work instructions for every activity.
Protection measures
Enclose or isolate the risk through the use of guards, protection of machinery parts etc
Use of physical barriers such as acoustic, thermal, electrical, etc.
Use of Personal Protective Equipment (PPE) as shown in Figure 6 to protect the worker from the residual risk. Workers must be trained regarding the selection and use of PPE.
Mitigation measures
When prevention and protective measures fail, a work accident or an occupational disease could happen. The company needs to be prepared (emergency preparedness) and to have mitigation measures implemented. The aim of mitigation measures is to reduce the severity of any damage to facilities and harm to employees and public.[ 18 ]
Environmental monitoring and measures
There are three main objectives of assessment of exposure:
- To determine the level of exposure of workers to harmful agents,
- To assess the need for control measures, and
- To ensure the efficiency of control measures in use.
The list of air pollution control measures are shown in Table 7 .
Air pollution control measures

Gas flow through stack is done by two fans 42 and 32 connected to ESP. The ESP 42 and ESP 32 are designed to blow 400,000 m 3 /h and 1400,000 m 3 /h of air, respectively.
The main raw material for the pellet plant is iron ore, which comes as slurry from the beneficiation plant through the pipe line. Hence, there are no fugitive emissions in raw materials handling area.
Water sprinkling is done by the water tanker on the roads and work zone areas to minimize the fugitive emissions. Fixed water sprinklers are installed in product yard area and product conveyer area.
In product area (HLSB), wet scrubbers are used to minimize particulate matter emissions and water sprinkling is done to decrease fugitive emissions.
Despite all the control measures, continuous monitoring of suspended particles is essential to ensure that it is below the permissible exposure limit.
The waste water from iron ore slurry is separated through filtration system and treated in the thickener. In the thickener, all de-dusting/scrubber return water is passed and the underflow is reused in the process. The pellet plant has a goal to achieve zero discharge norms with a comprehensive water and waste water management.
Solid waste
The iron ore dust collected by ESP is recycled into the thickener for its reuse in the process. Any fugitive dust generated is extracted, collected through bag filters, scrubbers, and reused in the process. Thus, no solid waste is generated.
Noise control
Continuous monitoring of high noise area is done by sound meter to ensure that it is within the permissible exposure limit. Low noise generating equipments are used in the pellet plant. The equipment producing high noise are surrounded by baffles and covered with noise-absorbing material. Workers are provided with personal protective equipment to protect from noise (like ear muffs, ear plugs).
Trees are important sinks for air pollutants and absorb the noise. They enhance the green cover, improve the ecology and aesthetics and affect the local micrometeorology. Trees also have major long-term impacts on soil quality and the ground water table. A total of 19,525 trees were planted in the plant premises on an area of 12.193 Ha.
Housekeeping
Proper housekeeping is an essential part of sound environmental management, which keeps the industry free from dusts.
Health monitoring
Health examinations are designed to ensure that the worker is fit for employment and that he remains in that state of fitness throughout his period of employment. Any deviation from good health must be detected early and managed appropriately. Health examinations of workers frequently reveal the existence of health hazards in workplace, thus necessitating environmental evaluation and control.
Preplacement health examination (baseline records)
This examination is carried out before employment of a worker in the workplace with potential health hazards. This helps in obtaining the baseline data. It also enables the management to place workers in jobs suited to their capacities and limitations. It includes physical examination of the various organs of the body, blood and urine analysis, radiographic examination, eye examination, audiometry, and spirometry.
Periodic health examination
This examination is carried out at regular intervals after the initial examination. Emphasis is given on exposure. Periodicity depends on the nature and extent of the risk involved.
Trend analysis
Workplace Injury and Illness Trend Analysis Program strives to identify unhealthy behaviors or hazardous conditions by tracking work-related injuries and illnesses.[ 19 ] This information is used to target occupational health and safety education activities to prevent or reduce future employee work-related injuries and illnesses.[ 19 ] Workplace Injury and Illness Trend Analysis includes the following:
- Tracking and monitoring workplace injuries and illnesses on an on-going basis [ 19 ]
- Grouping injuries and illnesses by nature, body part affected, event or exposure, source, etc [ 19 ]
- Determining if any trends in workplace injuries or illnesses exist and graphing those trends, if possible [ 19 ]
- Identifying any equipment, materials, or environmental factors that may be commonly involved in workplace injury or illness incidents [ 19 ]
- Identifying possible solutions and suggesting improvements to reduce or prevent the likelihood of future workplace injuries or illnesses.[ 19 ]
Monitor and review
Whichever method of eliminating and/or controlling the hazard is used, it is essential that an evaluation of its impact on the use of the equipment, substance, system, or environment is carried out to ensure that the control does not contribute to the existing hazard or introduce a new hazard.
It is also essential that all people involved are informed about the changes and, when necessary, provided with the appropriate information, instruction, training, and supervision to ensure that each worker is safe from injury and risk to health. It is also recommended that after a period of time, the area supervisor carry out a review of the system or control to determine its ongoing suitability.
C ONCLUSION
The first step for protection of workers against occupational diseases and maintaining a safe workplace is defining and analyzing hazards. There is a need for HIRAC study as a routine practice in all manufacturing industries. This helps in achieving two objectives; first is identifying the critical and high-risk hazards, which need to be addressed on priority basis, and second, by applying control measures at the earliest, it reduces the risk to a level considered ALARP.
Financial support and sponsorship
Conflicts of interest.
There are no conflicts of interest.
Acknowledgment
I would like to express my deepest appreciation to the Managing Director of the Pellet Plant for encouraging me to conduct this study. I would like to thank the employees and the workers of the Pellet Plant for participating in the study. Finally, I take this opportunity to express my deep sense of gratitude and indebtedness to my beloved teacher and guide Dr. Barun Kumar Sikdar, Deputy Chief Inspector of Factories (Med) and Certifying Surgeon, West Bengal for his encouragement and support.
A NNEXURE 1: Questionnaire
- Do you think there are any hazards in your work place?
- If your answer to question 1 is yes then how would you rate the consequence of the hazard in a scale of 1 to 5 with 1 being the least consequence causing a near miss and 5 being the maximum consequence causing fatality or permanent disability?
- If your answer to question 1 is yes then how would you rate the likelihood of the hazard in a scale of 1 to 5 with 1 being the least likelihood occurring very rarely or practically impossible and 5 being the maximum likelihood occurring continuously?
- Are there any control measures in your workplace for the hazard identified?
- Is there any administrative control over the hazard in your work place?
- Is sufficient Personal Protective Equipment (PPE) available in your work place where hazard is identified?
- If your answer to question 6 is yes then are you provided training regarding the type of PPE to use and the procedure of using PPE?
- Is there any facility for Pre employment and Periodical Health Checkup of employees in your organization?
- If your answer to question 8 is yes then what is the periodicity of health checkup in years?
- Are training provided regarding the Material Safety Data Sheet (MSDS) of the materials that are used in the workplace?
R EFERENCES
Log in using your username and password
- Search More Search for this keyword Advanced search
- Latest content
- Current issue
- BMJ Journals More You are viewing from: Google Indexer
You are here
- Online First
- Bad news: how the media reported on an observational study about cardiovascular outcomes of COVID-19
- Article Text
- Article info
- Citation Tools
- Rapid Responses
- Article metrics

- http://orcid.org/0000-0002-4166-5450 Camilla Alderighi 1 , 2 ,
- Raffaele Rasoini 1 , 2 ,
- Rebecca De Fiore 2 , 3 ,
- Fabio Ambrosino 2 , 3 ,
- Steven Woloshin 1 , 4
- 1 Lisa Schwartz Foundation for Truth in Medicine , Norwich , Vermont , USA
- 2 Alessandro Liberati Association - Cochrane Affiliate Centre , Potenza , Italy
- 3 Pensiero Scientifico Editore s.r.l , Roma , Italy
- 4 Center for Medicine and the Media, The Dartmouth Institute for Health Policy and Clinical Practice , Dartmouth University , Lebanon , New Hampshire , USA
- Correspondence to Dr Camilla Alderighi, Lisa Schwartz Foundation for Truth in Medicine, Norwich, Vermont, USA; camilla.alderighi{at}gmail.com
https://doi.org/10.1136/bmjebm-2023-112814
Statistics from Altmetric.com
Request permissions.
If you wish to reuse any or all of this article please use the link below which will take you to the Copyright Clearance Center’s RightsLink service. You will be able to get a quick price and instant permission to reuse the content in many different ways.
- Cardiovascular Diseases
- PUBLIC HEALTH
- Cardiovascular Abnormalities
Medical research gets plenty of media attention. Unfortunately, the attention is often problematic, frequently failing to provide readers with information needed to understand findings or decide whether to believe them. 1 Unless journalists highlight study cautions and limitations, avoid spin 2 and overinterpretation of findings, the public may draw erroneous conclusions about the reliability and actionability of the research. Coverage of observational research may be especially challenging given inherent difficulty in inferring causation, a limitation that is rarely mentioned in medical journals articles or corresponding news. 3 We used news coverage of a retrospective cohort study, published in Nature Medicine in 2022, 4 as a case study to assess news reporting quality. The index study used national data from US Department of Veteran Affairs to characterise the post-acute cardiovascular manifestations of COVID-19. We chose this study because of its potential public health impact (ie, reporting increased cardiovascular diseases after even mild COVID-19 infection) and its enormous media attention: one of the highest Altmetric scores ever (>20 k, coverage in over 600 news outlets and 40 000 tweets). Our study supplements a previous analysis limited to Italian news. 5
Supplemental material
Using Altmetric news page, we collected the news stories released in the first month after index study publication. We excluded duplicate articles, articles where the index study was not the main topic, articles<150 words or with unreachable link, paywalled articles and articles aimed at healthcare professionals. We translated articles not in English or Italian into Italian using Google Translate. Four raters (two physicians and two scientific journalists) independently analysed the included news articles using the coding scheme in online supplemental appendix 1 . Outcome was the proportion of news articles failing to meet each of the quality measures. Inter-rater agreement across all items was substantial (Fleiss’ kappa=0.78). Coder disagreements were resolved through discussion.
Almost all news stories (95 of 96, 99%) failed to mention the causal inference limitation or used causal language (eg, “Covid causes substantial long-term cardiovascular risks.”). 69 of 96 (72%) made unsupported recommendations (eg, “Based on the results of this study, I recommend that everyone who has been infected with Covid-19 […] get a cardiovascular workup within 12 months.”). 62 of 88 (70%) employed spin, for example, by reporting only relative risks (eg, “Overall, for all cardiovascular diseases combined, the risk after Covid-19 infection increased by 55%.”). 84 of 96 (87%) employed fear mongering (eg, “The results of the paper have shocked other researchers.”). 75 of 96 (78%) failed to undertake a basic critical evaluation of the study (eg, mention population characteristics and study context). More quality measure details and examples from the news are given in table 1 .
- View inline
Quality measures investigated in the analysis and examples from the news
This case study highlights how uncritical reporting of observational research in the news can result in dissemination of poor-quality information to the public. In this case, a high-impact study described an increased incidence of cardiovascular diseases after COVID-19, including coronary disease, myocarditis, pericarditis, heart failure, dysrhythmias, cerebrovascular disease and thromboembolic disease. Because they were based on observational analyses of US Veterans cohorts, these findings should be interpreted cautiously. Nevertheless, many of the subsequent news reports used inappropriate causal language and made recommendations unsupported by the research.
In this analysis, we focused on issues about reporting, that is what people eventually read. However, upstream sources are part of the problem 8 : for instance, the quality of reporting in the case study press release 9 reflects what we have observed in the news (eg, from an investigator quoted in the press release: “Because of the chronic nature of these conditions, they will likely have long-lasting consequences for patients and health systems and also have broad implications on economic productivity and life expectancy”).
The Nature Medicine paper was timely and of great interest to a public concerned about the sequelae of COVID-19. Not surprisingly, it received extraordinary coverage in the media. Careful, balanced news coverage could have helped the public understand that there might be long-term harms of COVID-19. Unfortunately, instead, as documented in our analysis, most media tended to overstate the certainty of results, likely generating substantial public anxiety about an inevitable epidemic of post-COVID-19 cardiovascular disease, and that is bad news.
Our analysis has limitations, such as, being restricted to a single study, unpaywalled articles and using a subjective selection of quality measures—albeit consistent with minimum quality standards used to judge reporting on observational research. 6 7
Ethics statements
Patient consent for publication.
Not applicable.
Ethics approval
- Pérez Gaxiola G , et al
- Boutron I ,
- Bolland MJ ,
- Bowe B , et al
- Rasoini R ,
- Ambrosino F ,
- De Fiore R , et al
- von Elm E ,
- Altman DG ,
- Egger M , et al
- Schwitzer G
- Schwartz LM ,
- Woloshin S ,
- Andrews A , et al
- Nordemberg T
Supplementary materials
Supplementary data.
This web only file has been produced by the BMJ Publishing Group from an electronic file supplied by the author(s) and has not been edited for content.
- Data supplement 1
- Data supplement 2
X @camialderighi
Contributors All authors contributed to conception, planning, design and conduct; acquisition, analysis and interpretation of data; drafting of the manuscript; critical revision of the manuscript for important intellectual content; and administrative, technical or material support and had full access to all the data in the study. CA, FA, RDF and RR: contributed to statistical analysis and take responsibility for the integrity of the data and the accuracy of the data analysis. CA and RR contributed equally to the creation of this manuscript; the order of their authorship is entirely arbitrary. CA, RR and SW: contributed to supervision.
Funding The authors have not declared a specific grant for this research from any funding agency in the public, commercial or not-for-profit sectors.
Competing interests None declared.
Provenance and peer review Not commissioned; externally peer reviewed.
Supplemental material This content has been supplied by the author(s). It has not been vetted by BMJ Publishing Group Limited (BMJ) and may not have been peer-reviewed. Any opinions or recommendations discussed are solely those of the author(s) and are not endorsed by BMJ. BMJ disclaims all liability and responsibility arising from any reliance placed on the content. Where the content includes any translated material, BMJ does not warrant the accuracy and reliability of the translations (including but not limited to local regulations, clinical guidelines, terminology, drug names and drug dosages), and is not responsible for any error and/or omissions arising from translation and adaptation or otherwise.
Read the full text or download the PDF:
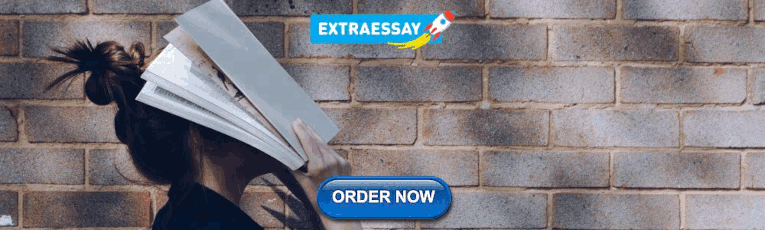
IMAGES
VIDEO
COMMENTS
Conclusion Hirarc - Free download as Word Doc (.doc / .docx), PDF File (.pdf), Text File (.txt) or read online for free. Conclusih Hiracr
The case study o f the Mengkuang . ... (HIRARC) Method (Case Study in PT Barokah Galangan Perkasa) ... As a conclusion, this study promotes evidence-base risk informed decision making for ...
Control (HIRARC), an effective safety management system has been implemented to control risks and minimize hazards at the construction sites. HIRARC risk management is a fundamental to the business operation, planning and management. The study by Asma lia [2] cited that hazard identification and risk assessment are processes
This case study examines the alleged hazard associated with mobile phone use at petrol stations and suggests that it is a phantom risk. Understanding its persistence in the absence of evidence, a number of factors are outlined. ... . CONCLUSION/OVERALL FINDINGS FROM THE HIRARC STUDY CONDUCTED Hazard identification is a proactive way of ...
This report analyses case studies on construction sites, construction sector is chosen to be the scope of studies due to the high frequency of accidents occurrence in this sector. Occupational Safety and Health Department's (DOSH), Malaysia's statistics recorded 169 deaths and 3,911 accidents in the construction sector in the year of 2018 [5].
There are many formal techniques for the systematic analysis of occupational safety and health in general, and risk analysis in particular, for power generation plants at hydroelectric power stations.This study was initiated in order to create a HIRARC model for the evaluation of environmental safety and health at a hydroelectric power generation plant at Cameron Highlands in Pahang, Malaysia.
This methodology is developed by the Department of Occupational Safety and Health (DOSH) Malaysia to identify potential hazards, assess the associated risks, and implement control measures to mitigate or eliminate those risks at the workplace. The full document on HIRARC is released under the name of Guidelines for Hazard Identification, Risk ...
As a conclusion, by doing this research, it gives a lot of information about the HIRARC process of safety. The objectives of this project were achieved after a couple of months, several studies and
need to be implemented to make sure the risk level can be reduced in the future. In conclusion, the HIRARC method used in this study is a useful method to identify the potential hazard in order to minimised the accident rate. Keywords: Hazard Identification, Risk Assessment, HIRARC
for each case study. The process of breaking down each cause from this tool, is analyzed until the root causes to the problem is identified [12]. The methodology of this HIRARC analysis is based on the guideline for Hazard Identification, Risk Assessment and Risk Control (HIRARC) from the Department of Occupation Safety and Health (2008) [13].
Hazard and safety evaluation in construction sites in Malaysia: A case study. Conference Paper. May 2021. Mohd Fathullah. Nik Raihan Nik Yusoff. Vertic Eridani Budi Darmawan. W. Q. Hui. View. Show ...
Conclusion. The request of quantitative risk assessment is needed nowadays in most of the regulatory documentation which will help in eliminating the risk or pre-planning can be done to avoid the risk. ... A Case Study Analysis of Hazard Identification, Risk Assessment, and Risk Control Implementation. 2023, E3S Web of Conferences ...
Shows the relation between system failure. a specific undesirable event in the system, and failures of the components of the system. Technique based on deductive logic, using "AND" and "OR" gates. An undesirable event is first defined and casual relationships of the failures leading to that event are then identified.
This paper reports on case studies of safety incidents in chemical factories in Malaysia. The processes used for identifying and evaluating both existing and potential hazards in a palm-oil work site and the way of controlling it is hazard identification, risk assessment and risk control or known as HIRARC. Many that have already done risk ...
2 INTRODUCTION: -This paper reports on case studies of safety incidents in Malaysia. The processes used for identifying and evaluating both existing and potential hazards in work site and the way of controlling it are hazard identification, risk assessment and risk control or known as hirarc were addressed.-HIRARC is a compound word which is made up of three consecutive activities running one ...
implementation of HIRARC in reducing accidents on construction sites, based on 10 different projects that implemented HIRARC. From structured interviews conducted to 10 safety personnel who implemented HIRARC in their projects, it has been found that the basic process of HIRARC was 100 % implemented and carried out. The study also revealed that
indicate that the HIRARC method enables prioritization of improvement efforts for activities with high-risk levels. Therefore, the HIRARC method is utilized in this study, which focuses on a case study conducted at PT Barokah Galangan Perkasa, one of the shipping companies located in East Kalimantan. 2. LITERATURE REVIEW
based on HIRA RC (Hazard I dentification, Risk Assessment and Risk Control) process. The data were collected at. two coal-fired powe r plant located in Malay sia. The finding of the study ...
CASE STUDY 1 : HAZARD IDENTIFICATION, RISK ASSESMENT AND RISK CONTROL (HIRARC) PROGRAM DKM CLASS DKM1E LECTURER MADAM NOOR LIZAWATI ... Identification / 5 marks Risk Assessment / 5 marks Risk Control / 5 marks Discussion 1. Photo (5 marks) 2. HIRARC Forms (10 marks) / 15 marks. Conclusion / 5 marks References / 5 marks TOTAL /50 marks. 1. ...
The aim of the study was to identify all the possible hazards at different workplaces of an iron ore pelletizing industry, to conduct an occupational health risk assessment, to calculate the risk rating based on the risk matrix, and to compare the risk rating before and after the control measures. ... Conclusion: The hazards having high-risk ...
circumstances of a particular case and the possible severity that could come from it (the risks); and c. to enable employers to plan, introduce and monitor preventive measures to ensure that the risks are adequately controlled at all times. 4.2 Planning of HIRARC Activities HIRARC activities shall be plan and conducted - a. for situation - i.
This study was initiated in order to create a HIRARC model for the evaluation of environmental safety and health at a hydroelectric power generation plant at Cameron Highlands in Pahang, Malaysia.
Medical research gets plenty of media attention. Unfortunately, the attention is often problematic, frequently failing to provide readers with information needed to understand findings or decide whether to believe them.1 Unless journalists highlight study cautions and limitations, avoid spin2 and overinterpretation of findings, the public may draw erroneous conclusions about the reliability ...