- Grundfos USA
- All courses
- 75 - The Extended Basic Hyd...
- An introduction to basic hy...
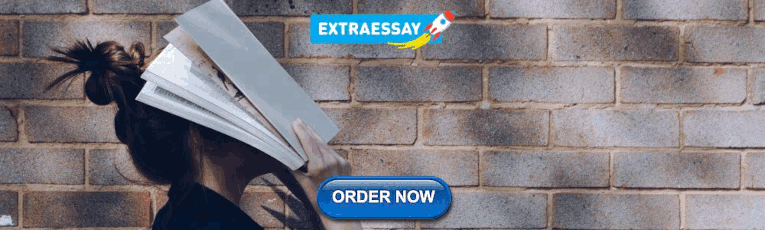
An introduction to basic hydraulic fundamentals
Learn about the most basic hydraulic fundamentals including terms such as flow and head.
When it comes to hydraulics in water pumping systems, we need to consider three major parameters: Flow, head and power – or Q, H and P.
In this short module, we’re going to introduce you to these basic parameters and what they mean for each other. Let’s get started.
Flow (Q) is typically measured in ft3/h. Simply put, the flow describes the amount of water that a pump moves through pipes within a given time period.
This is exactly why it is measured in ft3/h. The head (H) of a pump is the pressure that it is able to provide. It describes the height to which the pump can elevate water. So, if a pump’s head is, say, 60 feet, it means that it can lift water 60 feet in the air.
Finally, there’s the power (P). As the name suggests, power denotes the force and speed at which the water is moved. The power is measured in kilowatt.
As the power is dependent on the aforementioned flow (Q) and head (H), you can measure it by using the following formula: P = Q x H x c. In this calculation, c is a constant which depends on your pump’s efficiency, the level of gravity, and the fluid you are pumping.
Keep in mind that if you double the pump’s flow or head, you automatically double the pump’s power. And if you double both the flow and the head, you quadruple the energy usage.
That just about covers our introduction to the fundamentals of basic hydraulics. Thanks for tuning in.
Course overview
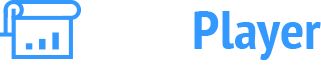
- My presentations
Auth with social network:
Download presentation
We think you have liked this presentation. If you wish to download it, please recommend it to your friends in any social system. Share buttons are a little bit lower. Thank you!
Presentation is loading. Please wait.
Principles, Components & Advantages Hydraulic System Created by : Aamir Shaikh Er No.-130050119501.
Published by Kory Jones Modified over 7 years ago
Similar presentations
Presentation on theme: "Principles, Components & Advantages Hydraulic System Created by : Aamir Shaikh Er No.-130050119501."— Presentation transcript:
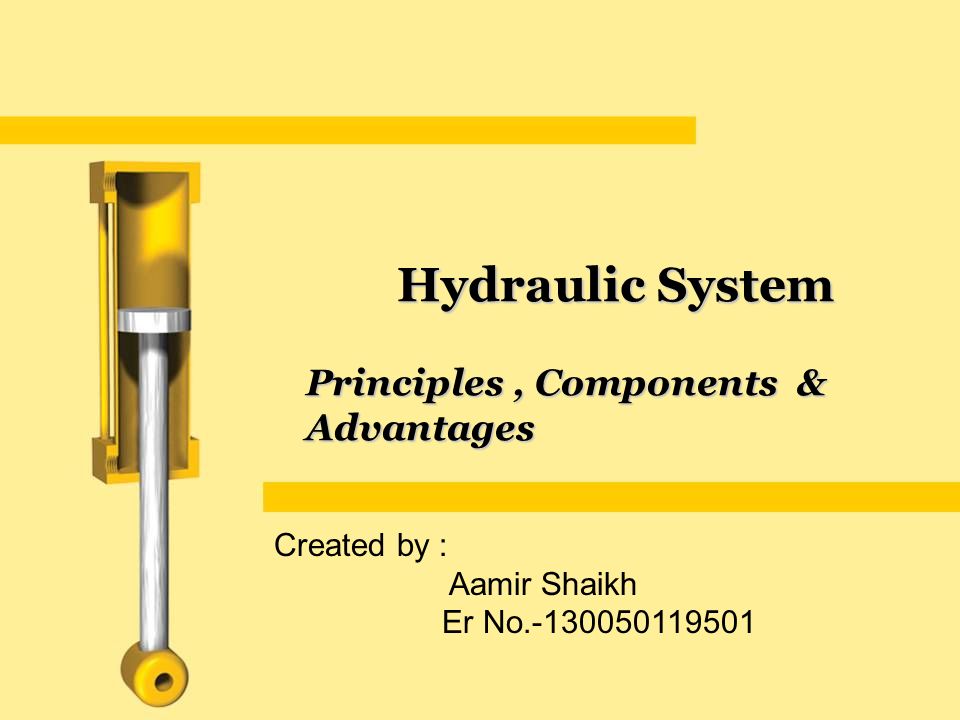
Landstown High School Governors STEM & Technology Academy
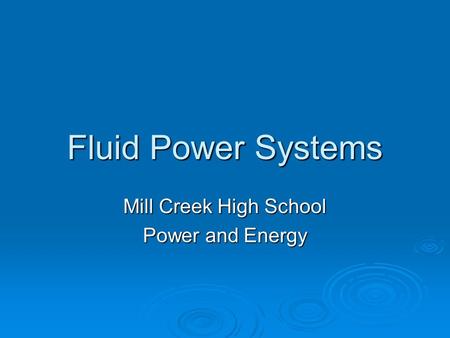
Fluid Power Systems Mill Creek High School Power and Energy.
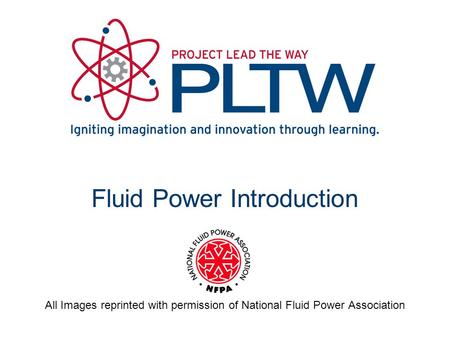
Fluid Power Introduction
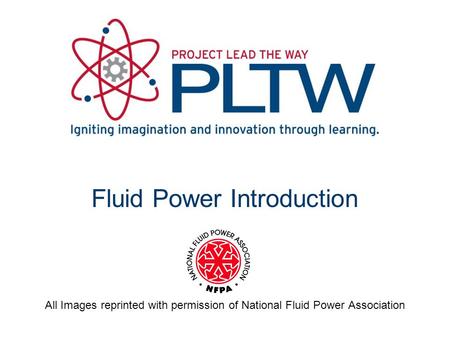
Hydraulics.
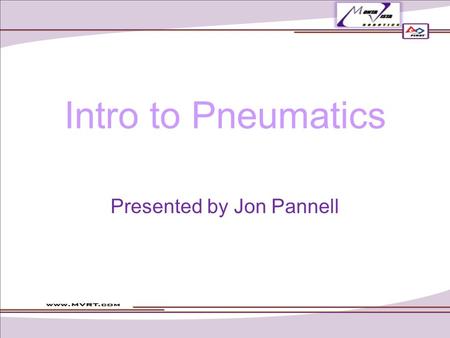
Presented by Jon Pannell

Using Hydraulic Systems. NEXT GENERATION / COMMON CORE STANDARDS ADDRESSED! CCSS.ELA Literacy RST Cite specific textual evidence to support analysis.
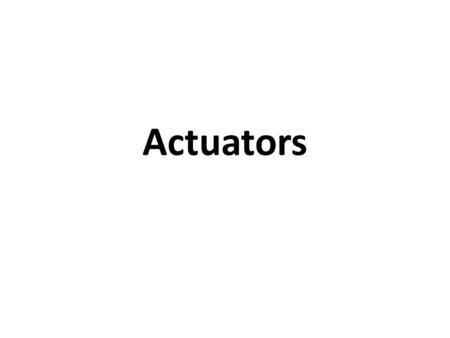
AIRCRAFTS HYDRAULIC SYSTEM
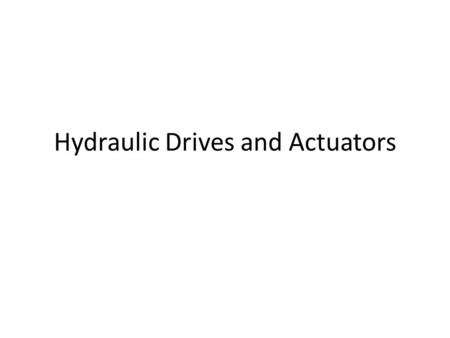
Hydraulic Drives and Actuators. Description A hydraulic drive consists of three major parts: The generator (such as a hydraulic pump) driven by an electric.
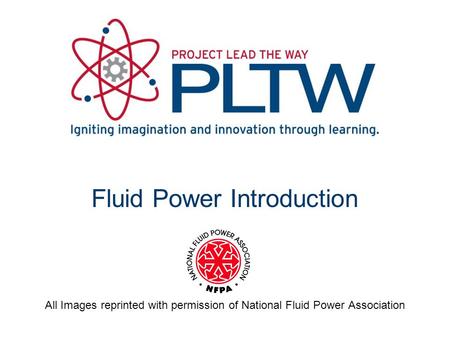
Intro to Fluid Power Topics What is fluid power? Where is it used?
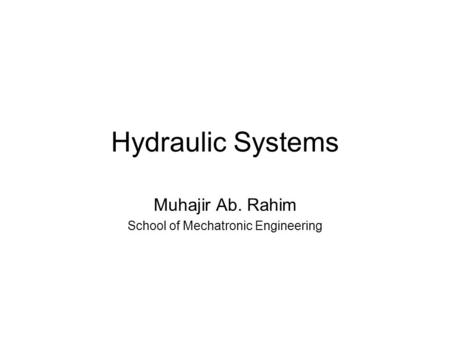
Muhajir Ab. Rahim School of Mechatronic Engineering
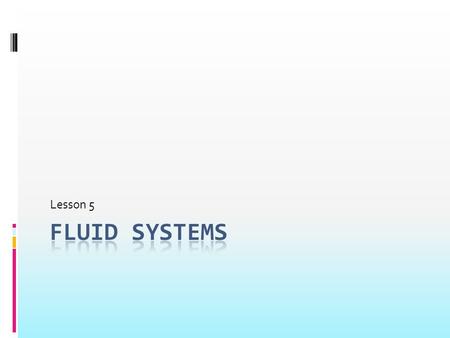
Lesson 5 Fluid Systems.
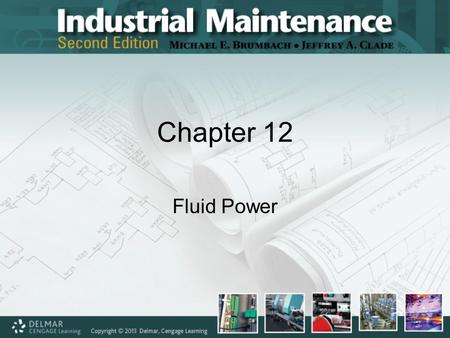
Chapter 12 Fluid Power. Objectives Upon completing this chapter, you should be able to: –Discuss some fluid power fundamentals –Explain psi, psig, psia,
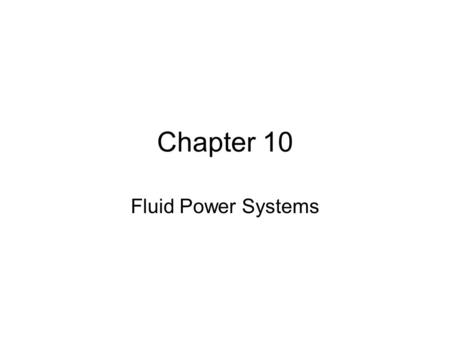
Chapter 10 Fluid Power Systems.
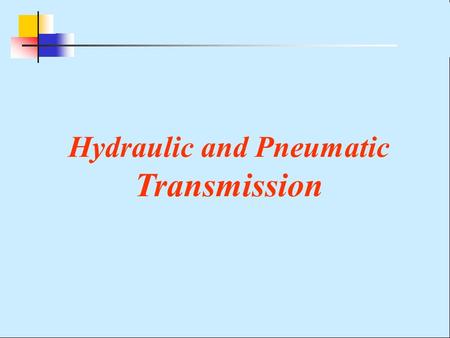
Hydraulic and Pneumatic Transmission
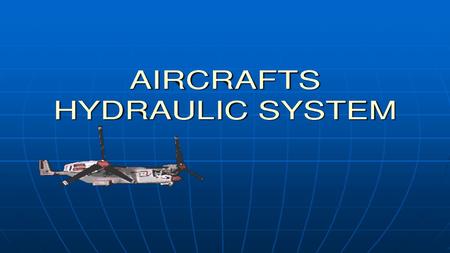
INTRODUCTION Hydraulics is based on the fact that liquids are incompressible Hydraulic system is a system where liquid under pressure is used to transmit.
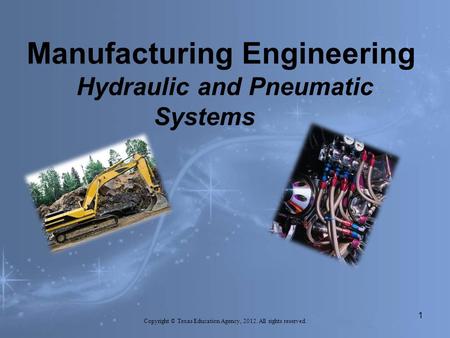
Manufacturing Engineering Hydraulic and Pneumatic Systems
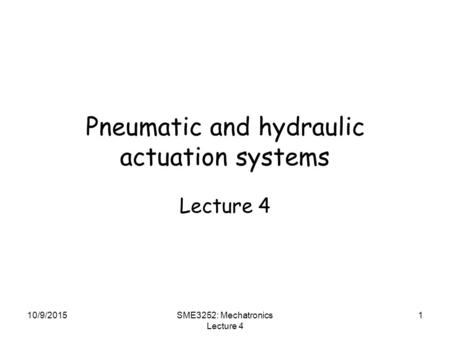
Pneumatic and hydraulic actuation systems
About project
© 2024 SlidePlayer.com Inc. All rights reserved.
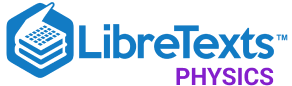
- school Campus Bookshelves
- menu_book Bookshelves
- perm_media Learning Objects
- login Login
- how_to_reg Request Instructor Account
- hub Instructor Commons
Margin Size
- Download Page (PDF)
- Download Full Book (PDF)
- Periodic Table
- Physics Constants
- Scientific Calculator
- Reference & Cite
- Tools expand_more
- Readability
selected template will load here
This action is not available.
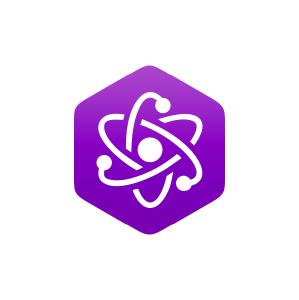
14.5: Pascal's Principle and Hydraulics
- Last updated
- Save as PDF
- Page ID 4057
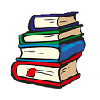
\( \newcommand{\vecs}[1]{\overset { \scriptstyle \rightharpoonup} {\mathbf{#1}} } \)
\( \newcommand{\vecd}[1]{\overset{-\!-\!\rightharpoonup}{\vphantom{a}\smash {#1}}} \)
\( \newcommand{\id}{\mathrm{id}}\) \( \newcommand{\Span}{\mathrm{span}}\)
( \newcommand{\kernel}{\mathrm{null}\,}\) \( \newcommand{\range}{\mathrm{range}\,}\)
\( \newcommand{\RealPart}{\mathrm{Re}}\) \( \newcommand{\ImaginaryPart}{\mathrm{Im}}\)
\( \newcommand{\Argument}{\mathrm{Arg}}\) \( \newcommand{\norm}[1]{\| #1 \|}\)
\( \newcommand{\inner}[2]{\langle #1, #2 \rangle}\)
\( \newcommand{\Span}{\mathrm{span}}\)
\( \newcommand{\id}{\mathrm{id}}\)
\( \newcommand{\kernel}{\mathrm{null}\,}\)
\( \newcommand{\range}{\mathrm{range}\,}\)
\( \newcommand{\RealPart}{\mathrm{Re}}\)
\( \newcommand{\ImaginaryPart}{\mathrm{Im}}\)
\( \newcommand{\Argument}{\mathrm{Arg}}\)
\( \newcommand{\norm}[1]{\| #1 \|}\)
\( \newcommand{\Span}{\mathrm{span}}\) \( \newcommand{\AA}{\unicode[.8,0]{x212B}}\)
\( \newcommand{\vectorA}[1]{\vec{#1}} % arrow\)
\( \newcommand{\vectorAt}[1]{\vec{\text{#1}}} % arrow\)
\( \newcommand{\vectorB}[1]{\overset { \scriptstyle \rightharpoonup} {\mathbf{#1}} } \)
\( \newcommand{\vectorC}[1]{\textbf{#1}} \)
\( \newcommand{\vectorD}[1]{\overrightarrow{#1}} \)
\( \newcommand{\vectorDt}[1]{\overrightarrow{\text{#1}}} \)
\( \newcommand{\vectE}[1]{\overset{-\!-\!\rightharpoonup}{\vphantom{a}\smash{\mathbf {#1}}}} \)
Learning Objectives
- State Pascal’s principle
- Describe applications of Pascal’s principle
- Derive relationships between forces in a hydraulic system
In 1653, the French philosopher and scientist Blaise Pascal published his Treatise on the Equilibrium of Liquids , in which he discussed principles of static fluids. A static fluid is a fluid that is not in motion. When a fluid is not flowing, we say that the fluid is in static equilibrium. If the fluid is water, we say it is in hydrostatic equilibrium . For a fluid in static equilibrium, the net force on any part of the fluid must be zero; otherwise the fluid will start to flow.
Pascal’s observations—since proven experimentally—provide the foundation for hydraulics, one of the most important developments in modern mechanical technology. Pascal observed that a change in pressure applied to an enclosed fluid is transmitted undiminished throughout the fluid and to the walls of its container. Because of this, we often know more about pressure than other physical quantities in fluids. Moreover, Pascal’s principle implies that the total pressure in a fluid is the sum of the pressures from different sources. A good example is the fluid at a depth depends on the depth of the fluid and the pressure of the atmosphere.
Pascal’s Principle
Pascal’s principle (also known as Pascal’s law) states that when a change in pressure is applied to an enclosed fluid, it is transmitted undiminished to all portions of the fluid and to the walls of its container. In an enclosed fluid, since atoms of the fluid are free to move about, they transmit pressure to all parts of the fluid and to the walls of the container. Any change in pressure is transmitted undiminished.
Note that this principle does not say that the pressure is the same at all points of a fluid—which is not true, since the pressure in a fluid near Earth varies with height. Rather, this principle applies to the change in pressure. Suppose you place some water in a cylindrical container of height H and cross-sectional area A that has a movable piston of mass m (Figure \(\PageIndex{1}\)). Adding weight Mg at the top of the piston increases the pressure at the top by \(\frac{Mg}{A}\), since the additional weight also acts over area A of the lid:
\[\Delta p_{top} = \frac{Mg}{A} \ldotp\]
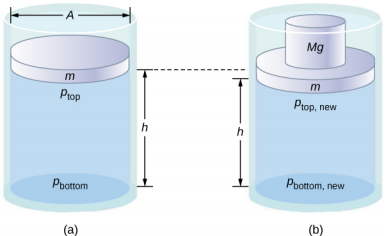
According to Pascal’s principle, the pressure at all points in the water changes by the same amount, \(\frac{Mg}{A}\). Thus, the pressure at the bottom also increases by \(\frac{Mg}{A}\). The pressure at the bottom of the container is equal to the sum of the atmospheric pressure, the pressure due the fluid, and the pressure supplied by the mass. The change in pressure at the bottom of the container due to the mass is
\[\Delta p_{bottom} = \frac{Mg}{A} \ldotp\]
Since the pressure changes are the same everywhere in the fluid, we no longer need subscripts to designate the pressure change for top or bottom:
\[\Delta p = \Delta p_{top} = \Delta p_{bottom} = \Delta p_{everywhere} \ldotp\]
Pascal’s Barrel is a great demonstration of Pascal’s principle. Watch a simulation of Pascal’s 1646 experiment, in which he demonstrated the effects of changing pressure in a fluid.
Applications of Pascal’s Principle and Hydraulic Systems
Hydraulic systems are used to operate automotive brakes, hydraulic jacks, and numerous other mechanical systems (Figure \(\PageIndex{2}\)).
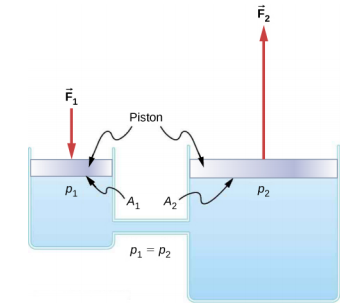
We can derive a relationship between the forces in this simple hydraulic system by applying Pascal’s principle. Note first that the two pistons in the system are at the same height, so there is no difference in pressure due to a difference in depth. The pressure due to F 1 acting on area A 1 is simply
\(p_{1} = \frac{F_{1}}{A_{1}}\), as defined by \(p = \frac{F}{A}\).
According to Pascal’s principle, this pressure is transmitted undiminished throughout the fluid and to all walls of the container. Thus, a pressure p 2 is felt at the other piston that is equal to p 1 . That is, p 1 = p 2 . However, since p 2 = \(\frac{F_{2}}{A_{2}}\), we see that
\[\frac{F_{1}}{A_{1}} = \frac{F_{2}}{A_{2}} \ldotp \label{14.12}\]
This equation relates the ratios of force to area in any hydraulic system, provided that the pistons are at the same vertical height and that friction in the system is negligible.
Hydraulic systems can increase or decrease the force applied to them. To make the force larger, the pressure is applied to a larger area. For example, if a 100-N force is applied to the left cylinder in Figure 14.16 and the right cylinder has an area five times greater, then the output force is 500 N. Hydraulic systems are analogous to simple levers, but they have the advantage that pressure can be sent through tortuously curved lines to several places at once.
The hydraulic jack is such a hydraulic system. A hydraulic jack is used to lift heavy loads, such as the ones used by auto mechanics to raise an automobile. It consists of an incompressible fluid in a U-tube fitted with a movable piston on each side. One side of the U-tube is narrower than the other. A small force applied over a small area can balance a much larger force on the other side over a larger area (Figure \(\PageIndex{3}\)).
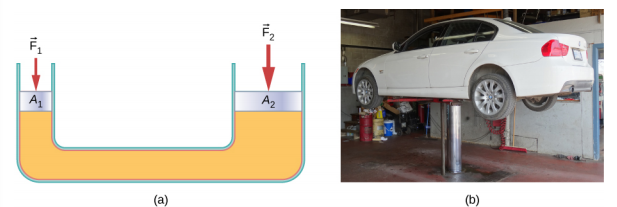
From Pascal’s principle, it can be shown that the force needed to lift the car is less than the weight of the car:
\[F_{1} = \frac{A_{1}}{A_{2}} F_{2},\]
where F 1 is the force applied to lift the car, A 1 is the cross-sectional area of the smaller piston, A 2 is the cross sectional area of the larger piston, and F 2 is the weight of the car.
Example \(\PageIndex{1}\): Calculating Force on Wheel Cylinders: Pascal Puts on the Brakes
Consider the automobile hydraulic system shown in Figure \(\PageIndex{4}\). Suppose a force of 100 N is applied to the brake pedal, which acts on the pedal cylinder (acting as a “master” cylinder) through a lever. A force of 500 N is exerted on the pedal cylinder. Pressure created in the pedal cylinder is transmitted to the four wheel cylinders. The pedal cylinder has a diameter of 0.500 cm and each wheel cylinder has a diameter of 2.50 cm. Calculate the magnitude of the force F 2 created at each of the wheel cylinders.
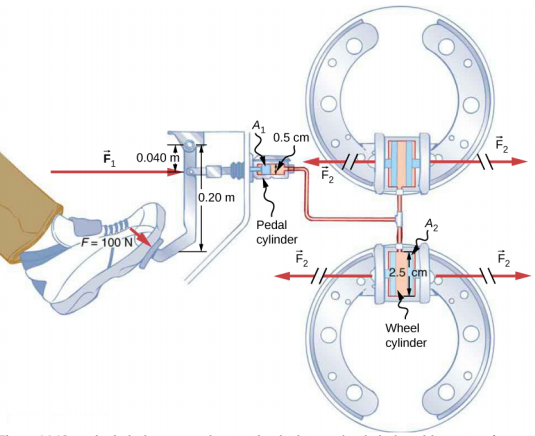
We are given the force F 1 applied to the pedal cylinder. The cross-sectional areas A 1 and A 2 can be calculated from their given diameters. Then we can use the following relationship to find the force F 2 :
\[\frac{F_{1}}{A_{1}} = \frac{F_{2}}{A_{2}} \ldotp\]
Manipulate this algebraically to get F 2 on one side and substitute known values.
Pascal’s principle applied to hydraulic systems is given by \(\frac{F_{1}}{A_{1}} = \frac{F_{2}}{A_{2}}\):
\[\begin{split} F_{2} & = \frac{A_{2}}{A_{1}} F_{1} = \frac{\pi r_{2}^{2}}{\pi r_{1}^{2}} F_{1} \\ & = \frac{(1.25\; cm)^{2}}{(0.250\; cm)^{2}} \times 500\; N = 1.25 \times 10^{4}\; N \ldotp \end{split}\]
Significance
This value is the force exerted by each of the four wheel cylinders. Note that we can add as many wheel cylinders as we wish. If each has a 2.50-cm diameter, each will exert 1.25 x 10 4 N. A simple hydraulic system, as an example of a simple machine, can increase force but cannot do more work than is done on it. Work is force times distance moved, and the wheel cylinder moves through a smaller distance than the pedal cylinder. Furthermore, the more wheels added, the smaller the distance each one moves. Many hydraulic systems—such as power brakes and those in bulldozers—have a motorized pump that actually does most of the work in the system.
Exercise \(\PageIndex{1}\)
Would a hydraulic press still operate properly if a gas is used instead of a liquid?
Solutions for
Educator & Staff Training
Improve compliance and deliver critical professional development with online courses and management system
Safety & Compliance
Inclusive Instruction & Interventions
Diversity & Inclusion
School Bus Driver
Cybersecurity Awareness
Facilities Maintenance
Child Sexual Abuse Prevention
Student Safety & Wellness Program NEW
Student Safety & Wellness Program
Keep students safe and healthy with safety, well-being, and social and emotional learning courses and lessons
Substance Misuse Prevention Courses
Mental Health & Well-Being Courses
Healthy Relationships Courses
Personal & Community Safety Courses
Career Readiness & Life Skills NEW
Professional Growth Management
Integrated software to manage and track evaluations and professional development and deliver online training
Professional Development Management
Evaluations Management
Anonymous Reporting & Safety Communications
Empower your school community to ask for help to improve school safety and prevent crises before they occur
Incident & EHS Management
Streamline safety incident reporting and management to improve safety, reduce risk, and increase compliance
Higher Education
Student Training
Increase safety, well-being, and belonging with proven-effective training on critical prevention topics
Sexual Assault Prevention
Alcohol & Drug Misuse Prevention
Diversity, Inclusion, & Belonging
Wellness & Safety
Career & Personal Development NEW
Fraternity & Sorority Life
Faculty & Staff Training
Create a safe, healthy, and welcoming campus environment and improve compliance with online training courses
Harassment, Discrimination, & Sexual Assault Prevention
IT & Campus Security
Health & Safety
Human Resources & Workforce Management
Environmental Health & Facilities Management
Campus Climate Surveys
Simplify VAWA compliance with easy, scalable survey deployment, tracking, and reporting
Empower your faculty, staff, and students to take an active role in protecting themselves and others
Manufacturing
Safety Training NEW
Safety Training
Elevate performance and productivity while reducing risk across your entire organization with online training.
MSHA Training
Industrial Skills Training NEW
Industrial Skills Training
Close skills gap, maximize production, and drive consistency with online training
Core Industrial Skills
Preventative Maintenance
Electrical Maintenance
Continuous Improvement
Power Generation
Paper Manufacturing Training
Enhance worker expertise and problem-solving skills while ensuring optimal production efficiency.
HR & Compliance
Provide role-specific knowledge, develop skills, and improve employee retention with career development training.
Professional Development NEW
DEI Training NEW
Anti Harassment Training NEW
Learning Management System (LMS)
Assign, track, and report role-based skills and compliance training for the entire workforce
Competency Assessments NEW
EHS Management
Track, Analyze, Report Health and Safety Activities and Data for the Industrial Workforce
Incident Management
Inspections & Audits
Real-TIme Safety Metrics and Reports
Behavior-Based Safety
Hazard Reporting
Job Safety Analysis
SDS & Chemical Management
Safety Communication
Enhance the safety for the industrial workforce with two-way risk communications, tools, and resources
Fire Departments
Training Management
A training management system tailored for the fire service--track all training, EMS recerts, skill evaluations, ISO, and more in one place
Training Management System
Skill Evaluations
Firefighter Continuing Education
Online EMS Recertification Training
Fire Academy Automation
Fire Standards and Training
Crew Shift Scheduling
Simplify 24/7 staffing and give firefighters the convenience of accepting callbacks and shifts from a mobile device
Checks & Inventory Management
Streamline truck checks, PPE inspections, controlled substance tracking, and equipment maintenance with a convenient mobile app
Controlled Substance Tracking
Exposure and Critical Incident Monitoring NEW
Exposure and Critical Incident Monitoring
Document exposures and critical incidents and protect your personnels’ mental and physical wellness
Training Management and Recertification
A training management system tailored for EMS services—EMS online courses for recerts, mobile-enabled skill evaluations, and more
EMS Skill Evaluations
EMS Shift Scheduling
Simplify 24/7 staffing and give medics the convenience of managing their schedules from a mobile device
Inventory Management
Streamline vehicle checks, controlled substance tracking, and equipment maintenance with a convenient mobile app
Wellness Monitoring & Exposure Tracking NEW
Wellness Monitoring & Exposure Tracking
Law Enforcement
Training and FTO Management
Increase performance, reduce risk, and ensure compliance with a training management system tailored for your FTO/PTO and in-service training
Training Management System & FTO
Law Enforcement Online Training
Academy Automation
POST and Regulatory Management
Early Intervention & Performance Management
Equip leaders with a tool for performance management and early intervention that helps build positive agency culture
Officer Shift Scheduling
Simplify 24/7 staffing and give officers the convenience of managing their schedules from a mobile device
Asset Mangagement & Inspections
Streamline equipment checks and vehicle maintenance to ensure everything is working correctly and serviced regularly
Energy Skills Training
Empower your team with skills and safety training to ensure compliance and continuous advancement.
Track, analyze, report health and safety activities and data for the industrial workforce
Lone Worker Safety
Enhance lone worker safety with two way risk communications, tools, and resources
Federal Training Management
Lower training costs and increase readiness with a unified system designed for high-risk, complex training and compliance operations.
Military Training Management
Increase mission-readiness and operational efficiency with a unified system that optimizes military training and certification operations.
Local Government Training Management
Technology to train, prepare, and retain your people
Fire Marshall Training & Compliance
Improve fire service certification and renewal operations to ensure compliance and a get a comprehensive single source of truth.
Elevate fire academy training with automation software, enhancing efficiency and compliance.
POST Training & Compliance
Streamline your training and standards operations to ensure compliance and put an end to siloed data.
Law Enforcement Academy Automation
Modernize law enforcement training with automation software that optimizing processes and centralizes academy information in one system.
Simplify incident reporting to OSHA and reduce risk with detailed investigation management.
Architecture, Engineering & Construction
Ensure licensed professionals receive compliance and CE training via online courses and learning management.
Online Continuing Education
Keep AEC staff licensed in all 50 states for 100+ certifications with online training
Architecture
Engineering
Construction
Project Management
Drive organizational success with training that grows skills and aligns with the latest codes and standards
Heath & Safety
Construction and Trades
Track, Analyze, Report Health and Safety Activities and Data for AEC Worksites
Inspections and Audits
Real-Time Safety Metrics and Reports
Enhance AEC workforce safety with two-way risk communications, tools, and resources
Anti-Money Laundering Training
Reduce risk in casino operations with Title 31 and Anti-Money Laundering training compliance
Employee Training
Deliver our leading AML and casino-specific online courses to stay compliant with national and state standards
Streamline training operations, increase employee effectiveness, and reduce liability with our LMS for casinos
Simplify incident reporting to OSHA and reduce risk with detailed investigation management
Employee Scheduling
Equip your employees with a mobile app to manage their schedules and simplify your 24/7 staff scheduling

Career & Technical Education NEW
Industrial Manufacturing
Chemical Processing
Pulp & Paper
Food & Beverage NEW
Utilities NEW
Renewables NEW
Distribution & Logistics
Distribution & Warehousing NEW
Public Safety
EMS Agencies
911 Emergency Communications
State Government - Fire Departments
State Government - Law Enforcement
Local Government
Architecture & Engineering
Facilities Management
Course Center
Success Stories
Speak to an Expert

Resource Center
Expert insights to boost training
Resource type
Course Catalogs
Whitepapers/Guides
Product Brochures
Acquisitions
Vector Cares
Executive Team
Industry Honors

Elevate Training, Elevate Success
Firefighter
See All Industrial Courses
See All AEC Courses
See All Facilities Courses
See All Casino Courses
What Is a Hydraulic System? Definition, Design, and Components
October 23, 2023 14 min read
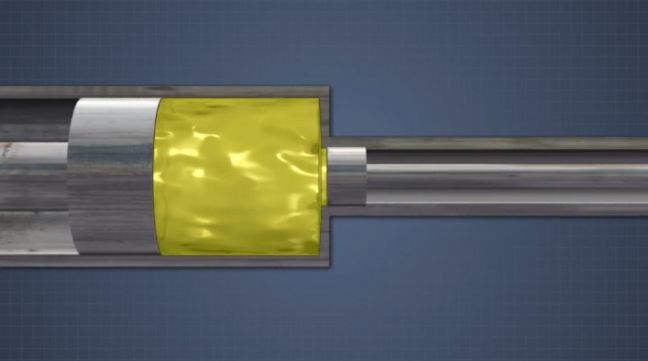
With a variety of applications, hydraulic systems are used in all kinds of large and small industrial settings, as well as buildings, construction equipment, and vehicles. Paper mills, logging, manufacturing, robotics, and steel processing are leading users of hydraulic equipment.
As an efficient and cost-effective way to create movement or repetition, hydraulic system-based equipment is hard to top. It’s likely your company has hydraulics in use in one or more applications for these reasons.
We’ll provide more information about hydraulic systems in this article, including covering the definition and basic designs and components.
An Overview of Hydraulic Systems
The purpose of a specific hydraulic system may vary, but all hydraulic systems work through the same basic concept. Defined simply, hydraulic systems function and perform tasks through using a fluid that is pressurized. Another way to put this is the pressurized fluid makes things work.
The power of liquid fuel in hydraulics is significant and as a result, hydraulic are commonly used in heavy equipment. In a hydraulic system, pressure, applied to a contained fluid at any point, is transmitted undiminished. That pressurized fluid acts upon every part of the section of a containing vessel and creates force or power. Due to the use of this force, and depending on how it’s applied, operators can lift heavy loads, and precise repetitive tasks can be easily done.
This online hydraulics systems training course illustrates this point.
Marvelously versatile, hydraulic systems are dynamic, yet relatively straightforward in how they work.
Let’s look at some applications and a few basic components found in hydraulic systems. This short sample from our online hydraulic systems and components course sets the scene nicely.
Hydraulic Circuits
Transporting liquid through a set of interconnected discrete components, a hydraulic circuit is a system that can control where fluid flows (such as thermodynamic systems), as well as control fluid pressure (such as hydraulic amplifiers).
The system of a hydraulic circuit works similar to electric circuit theory, using linear and discrete elements. Hydraulic circuits are often applied in chemical processing (flow systems).
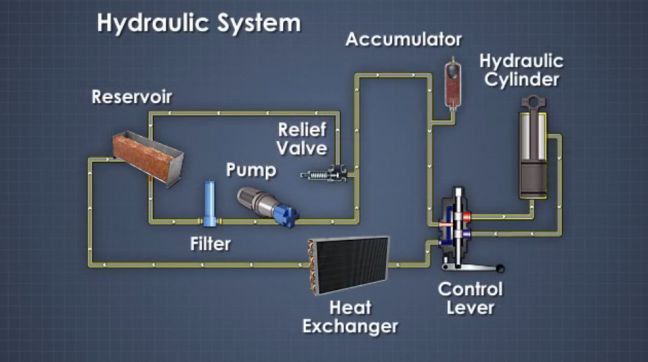
Hydraulic Pumps
Mechanical power is converted into hydraulic energy using the flow and pressure of a hydraulic pump. Hydraulic pumps operate by creating a vacuum at a pump inlet, forcing liquid from a reservoir into an inlet line, and to the pump. Mechanical action sends the liquid to the pump outlet, and as it does, forces it into the hydraulic system.
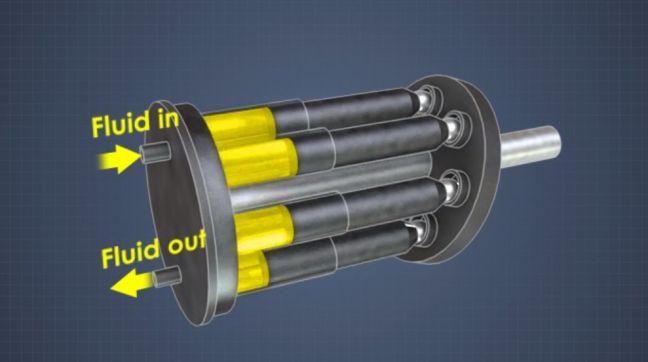
This is an example of Pascal’s Law , which is foundational to the principle of hydraulics. According to Pascal’s Law, “A pressure change occurring anywhere in a confined incompressible fluid is transmitted throughout the fluid such that the same change occurs everywhere.”
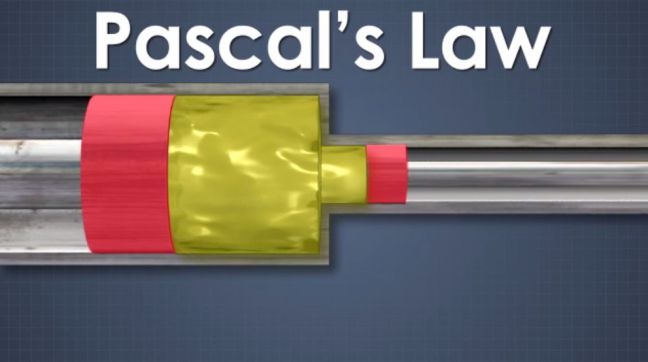
Hydraulic Motors
The conversion of hydraulic pressure and flow into torque (or a twisting force) and then rotation is the function of a hydraulic motor, which is a mechanical actuator.
The use of these is quite adaptable. Along with hydraulic cylinders and hydraulic pumps, hydraulic motors can be united in a hydraulic drive system. Combined with hydraulic pumps, the hydraulic motors can create hydraulic transmissions. While some hydraulic motors run on water, the majority in today’s business operations are powered by hydraulic fluid, as the ones in your business likely are.
Hydraulic Cylinders
A hydraulic cylinder is a mechanism that converts energy stored in the hydraulic fluid into a force used to move the cylinder in a linear direction. It too has many applications and can be either single acting or double acting. As part of the complete hydraulic system, the cylinders initiate the pressure of the fluid, the flow of which is regulated by a hydraulic motor.
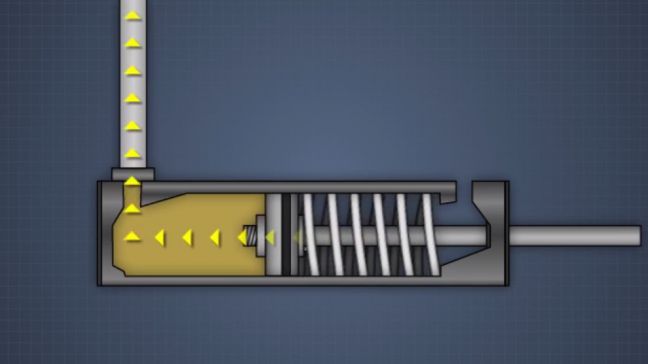
Hydraulic Energy and Safety
Hydraulics present a set of hazards to be aware of, and for that reason safety training is required.
For example, this short sample from our online hydraulic safety training course explains some of the ways the fluids in a hydraulic system can be hazardous.
Remember, the purpose of hydraulic systems is to create motion or force. It’s a power source, generating energy.
Don’t underestimate hydraulic energy in your safety program. It is small but mighty in force. And like any force, it can do great good or great harm.
In the workplace, that translates to a potential hazard source, especially if uncontrolled. Hydraulic energy is subject to OSHA’s Lockout/Tagout rules , along with electrical energy and other similar hazard sources. Be sure to train workers about the hazards of uncontrolled hydraulic energy, especially during maintenance, and the need for lockout/tagout, as illustrated by this still image from one of our online lockout/tagout training courses .
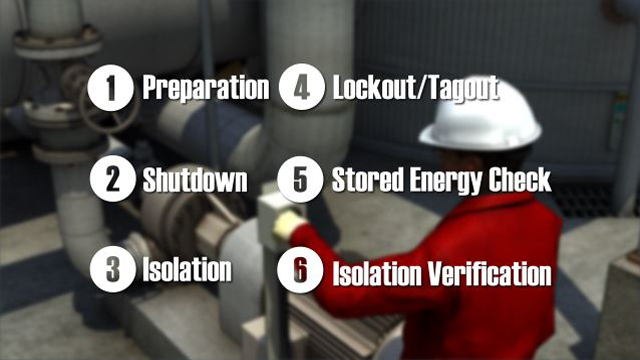
If neglected in procedures or forgotten when servicing equipment, uncontrolled hydraulic energy can have devastating results. Failure to control hydraulic energy frequently causes crushing events, amputations, and lacerations to exposed workers.
Therefore, like other energy sources, hydraulic energy must be controlled, using an appropriate energy isolating device that prevents a physical release of energy. There are also systems that require the release of stored hydraulic energy to relieve pressure. And also, those engaged in lockout/tagout, must also verify the release of stored hydraulic energy/pressure (usually indicated by zero pressure on gauges) prior to working on equipment.
Also, workers need training which must explain the hazard potential and clearly detail methods to prevent injury. According to OSHA:
“All employees who are authorized to lockout machines or equipment and perform the service and maintenance operations need to be trained in recognition of applicable hazardous energy sources in the workplace, the type and magnitude of energy found in the workplace, and the means and methods of isolating and/or controlling the energy.”
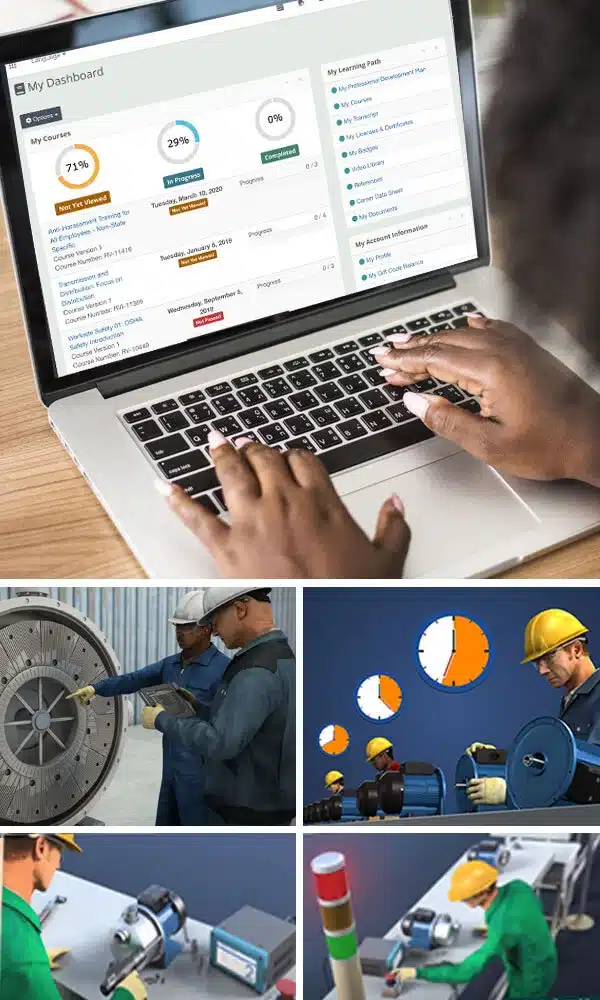
Vector EHS Management Software empowers organizations – from global leaders to local businesses – to improve workplace safety and comply with environmental, health, and safety regulations.
Learn more about how our software can save you valuable time and effort in recording, tracking, and analyzing your EHS activities.
Learn more about how we can help:
- Incident Management Software →
- EHS Inspection Software →
- Key Safety Metrics Dashboard →
- Learning Management System (LMS) and Online Training Courses →
- Mobile Risk Communication Platform
Download our EHS Management Software Buyer’s Guide .
You should be very familiar with any equipment in your business that creates hydraulic energy to ensure your workers are adequately protected through well-detailed procedures and training. And of course, your LO/TO program should echo your procedures, and list sources of workplace hydraulic energy devices. (Don’t forget to perform at least annual reviews of the program and procedures to ensure you catch any changes or deficiencies.)
Again, it’s critical anyone involved with hydraulic systems is properly trained. Don’t neglect that aspect.
If you’d like to dig deeper into this topic, we have several courses on hydraulic systems, including Hydraulic System Basics , which outlines the essentials of hydraulic theory, common components, what mechanical advantage is, and how hydraulic fluid is contaminated. In addition, we have two others which provide vital in-depth information, Hydraulic System Valves and Components and Hydraulic System Equipment .
It’s important to understand the principles of these systems, not only for servicing and maintenance, but also to understand the ways the hydraulic systems function to avoid injuries and accidents.
Conclusion: Hydraulics Are Common in the Modern Workplace
Having a working understanding of hydraulics of the type we’ve covered in this article will help you better understand a modern workplace and will make you or your company more efficient, productive, and safe.
Before you go, feel free to download the free guide to manufacturing training below.
Manufacturing Training Guide
Tech, tools, tips, and more!
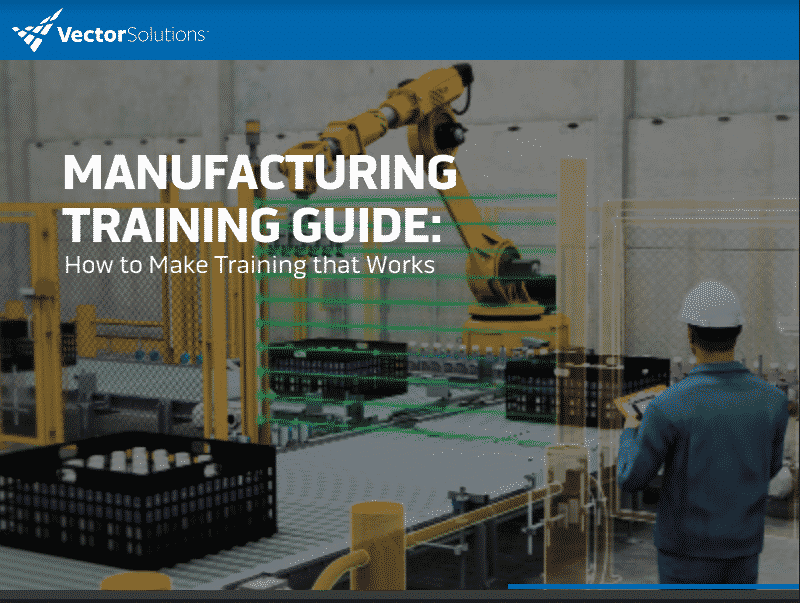
How to Operate a Forklift: Pre-Operation, Traveling, Load Handling, and Maintenance
OSHA Recordkeeping Assistance in 2024
Related Resources

Complete Guide to Construction Fall Protection
May 16, 2024 10 min read

OSHA’s “Fatal Four” In Construction: Leading Causes of Fatalities in Construction
May 14, 2024 12 min read

How to Create a Safety Program for Construction Workers
May 13, 2024 6 min read
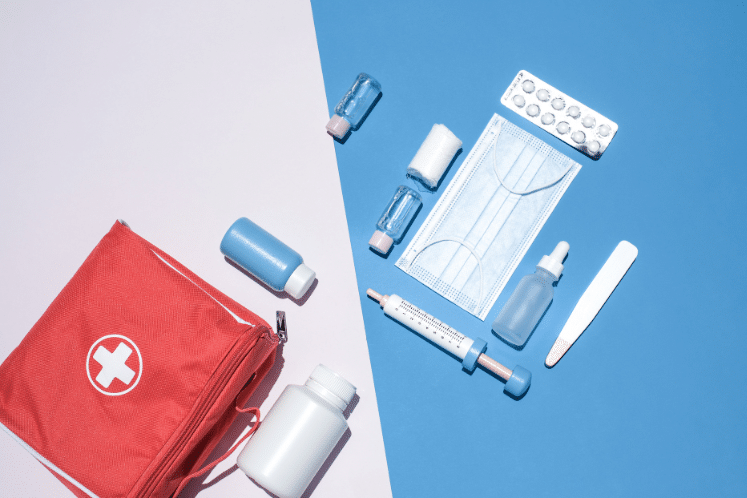
First Aid Training Tips to Improve Workplace Health & Safety
May 9, 2024 6 min read
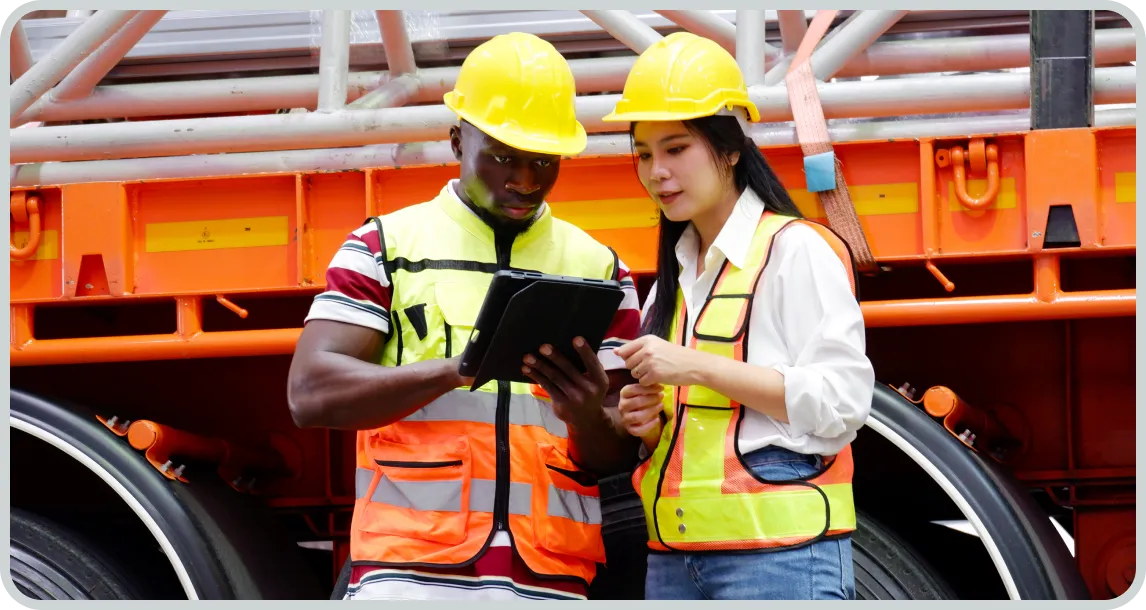
The Three Phases of Risk Assessment: Risk Management Basics
May 7, 2024 4 min read

GHS Label Requirements, Symbols, and Classifications
March 1, 2024 9 min read
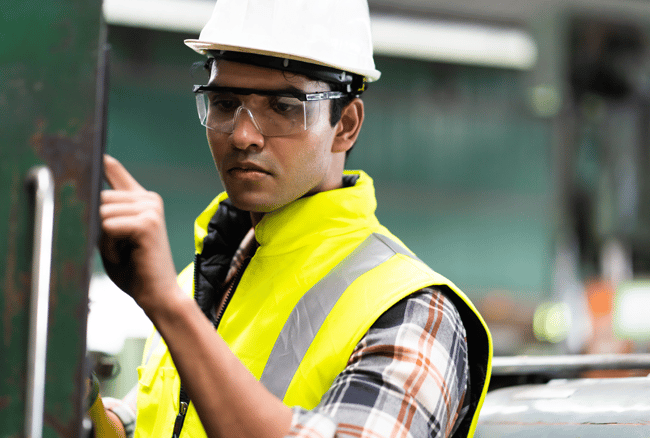
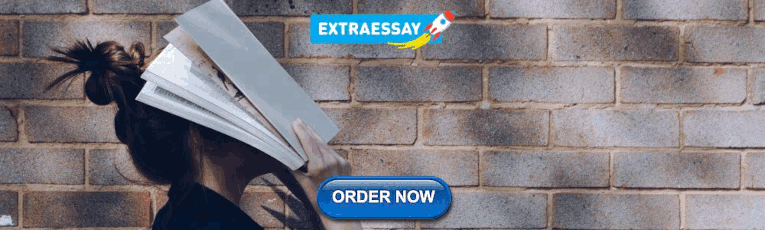
AE Learning Paths: The Secret to Retaining Architects & Engineers
January 26, 2024 min read
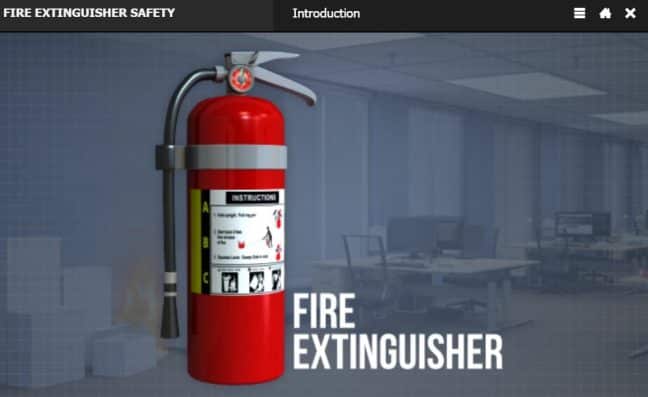
OSHA Fire Extinguisher Mounting Height, Placement & Signage Requirements
May 17, 2024 9 min read
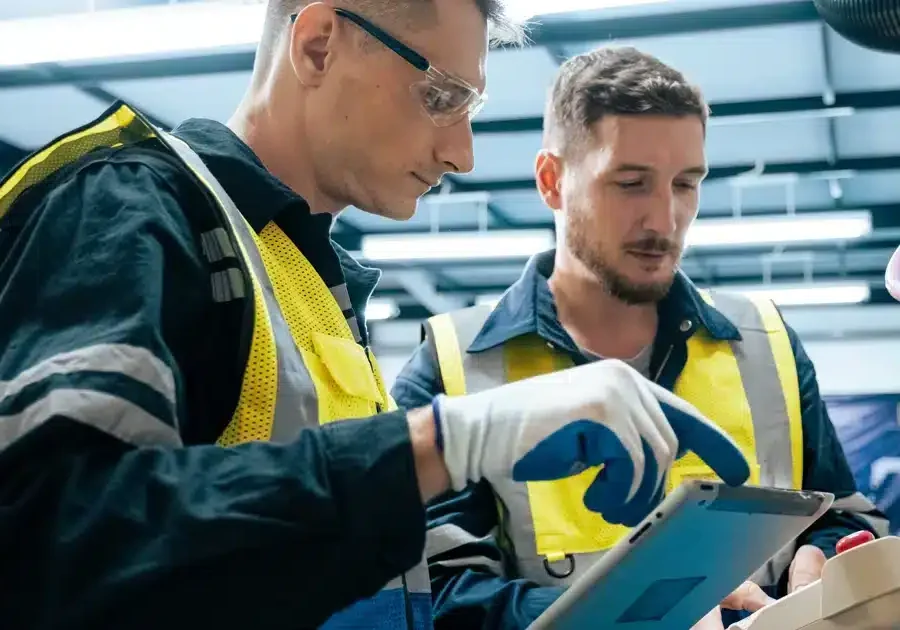
Developing Skilled Maintenance Teams through Targeted Learning Paths
May 29, 2024

Guide to Fleet Safety: Ensuring Safe Operations Across Various Industries
May 16, 2024 8 min read
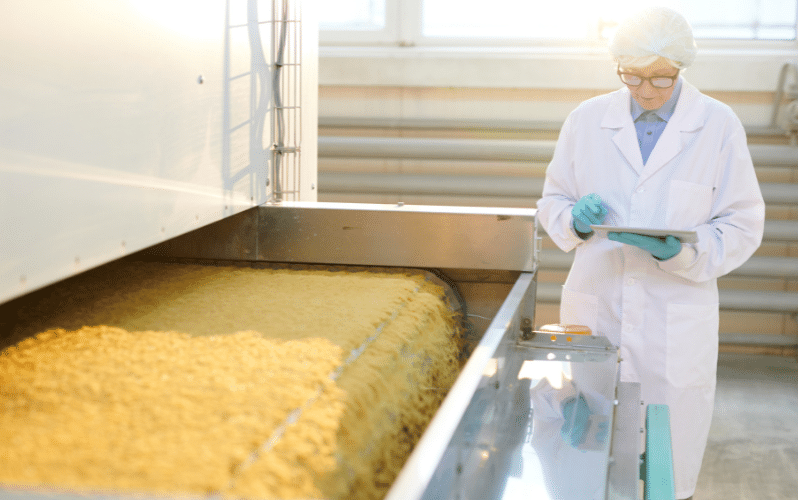
Food Manufacturing Safety: Tips to Create a Safety Culture
May 10, 2024 8 min read
Explore our software solutions designed to help your organization succeed
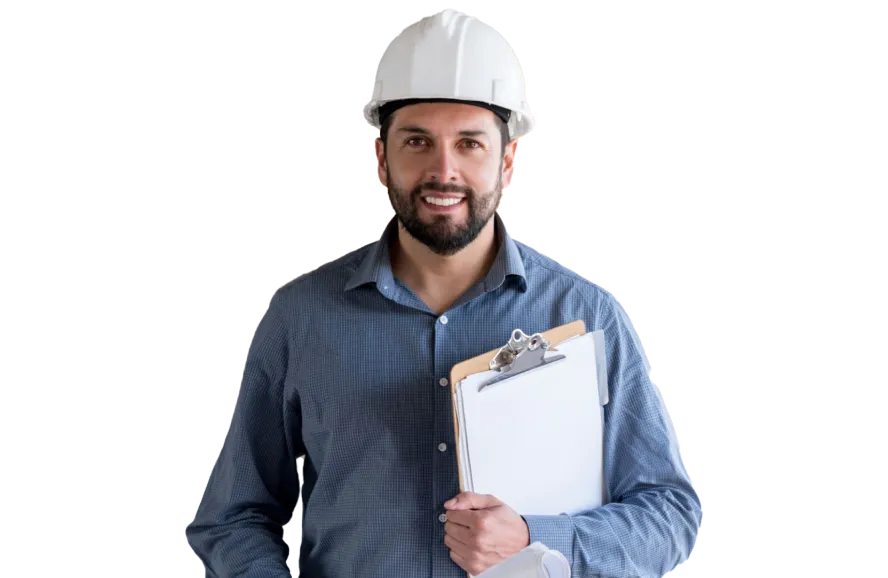
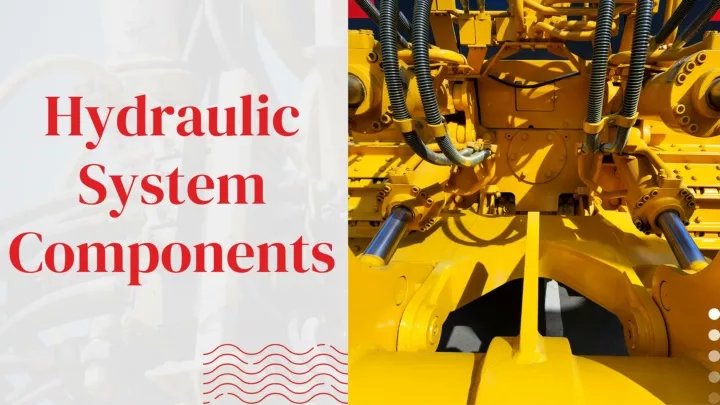
Hydraulic System Component
Apr 11, 2022
60 likes | 75 Views
A hydraulic system is a drive technique in which energy is transferred from an electric motor to an actuator, such as a hydraulic cylinder by using a fluid. Hydraulic systems are usually used in that situations where a high power density is required or load needs to change frequently. The reservoir, pump, valve, and actuator are the main components of a hydraulic system. Vtech Hydraulic is the manufacturer of hydraulic equipment/ hydraulic tools. In order to get more knowledge about Hydraulic Tools, Visit: https://www.vtechhydraulic.com/products.php
Share Presentation

Presentation Transcript
In order to get more knowledge about Hydraulic Tools, Visit: www.vtechhydraulic.com.
- More by User
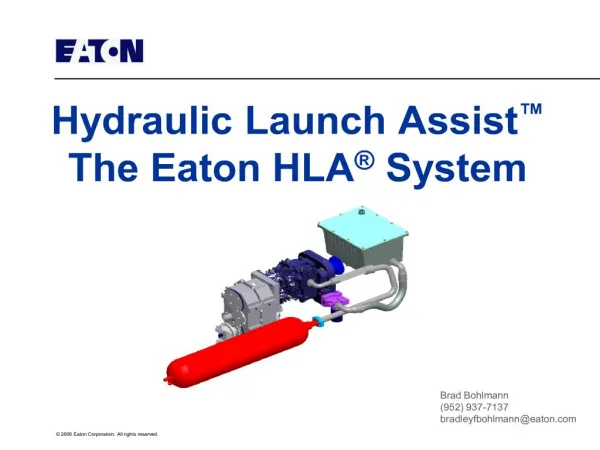
hydraulic launch assist the eaton hla system
What is the Eaton HLA System?. The Eaton HLA system is a parallel hybrid hydraulic regenerative braking system.The HLA system recovers the majority of the energy normally wasted as heat during braking and uses it to supplement the engine's power during acceleration.The HLA system provides the greatest benefit when the vehicle's driving cycle involves stop and go driving..
1.19k views • 11 slides
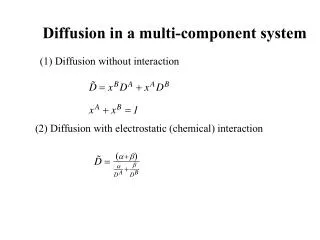
Diffusion in a multi-component system
Diffusion in a multi-component system. (1) Diffusion without interaction. (2) Diffusion with electrostatic (chemical) interaction. Which D? Which species (Mg,, Si or O)? 2. Diffusion through grains or diffusion along grain-boundaries? (m=2 or 3). diffusion in olivine (volume diffusion).
764 views • 36 slides
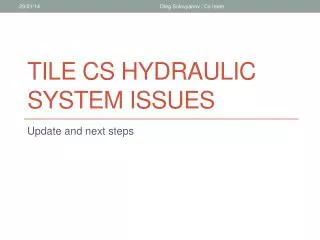
Tile Cs hydraulic system issues
Tile Cs hydraulic system issues. Update and next steps. The leak. 26 November 2013 a water leak from Tile Cs calibration system had occurred during the dummy capsule tests
316 views • 18 slides
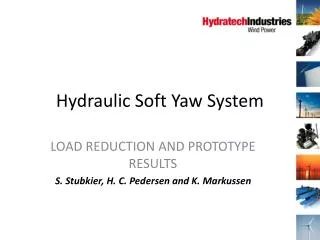
Hydraulic Soft Yaw System
Hydraulic Soft Yaw System. LOAD REDUCTION AND PROTOTYPE RESULTS S. Stubkier, H. C. Pedersen and K. Markussen. Agenda. Introduction System description Simulation setup Load reduction Results of controlled slippage Test rig presentation Measurement results Conclusion and Future prospects.
503 views • 24 slides
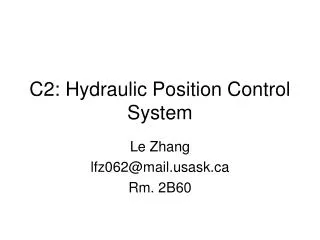
C2: Hydraulic Position Control System
C2: Hydraulic Position Control System. Le Zhang [email protected] Rm. 2B60. Objectives. Study the open-loop performance of an electro-hydraulic position control system.
445 views • 25 slides
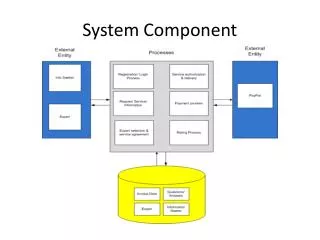
System Component
System Component.
81 views • 1 slides
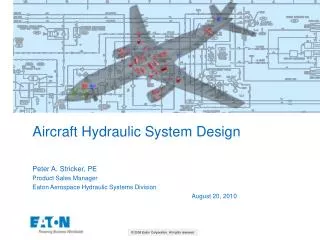
Aircraft Hydraulic System Design
Aircraft Hydraulic System Design. Peter A. Stricker, PE Product Sales Manager Eaton Aerospace Hydraulic Systems Division August 20, 2010. Purpose. Acquaint participants with hydraulic system design principles for civil aircraft
6.22k views • 27 slides
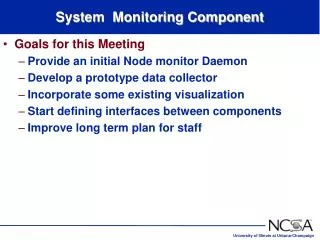
System Monitoring Component
System Monitoring Component. Goals for this Meeting Provide an initial Node monitor Daemon Develop a prototype data collector Incorporate some existing visualization Start defining interfaces between components Improve long term plan for staff. Components Developed.
169 views • 4 slides
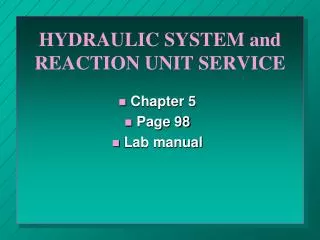
HYDRAULIC SYSTEM and REACTION UNIT SERVICE
HYDRAULIC SYSTEM and REACTION UNIT SERVICE. Chapter 5 Page 98 Lab manual. DIAGNOSE HYDRAULIC and VACUUM CONTROL SYSTEMS. The best way to identify the exact cause of transmission problems is to use the results of a road test: Logic
536 views • 36 slides
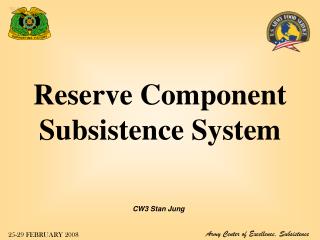
Reserve Component Subsistence System
Reserve Component Subsistence System. CW3 Stan Jung. Discuss Reserve Component Subsistence System Explain the Proper Procedure in Preparing the Forms Answer Questions. Purpose.
444 views • 21 slides
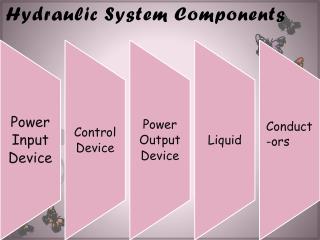
Hydraulic System Components
Hydraulic System Components. Conduct-ors. Power Input Device :
2.47k views • 17 slides
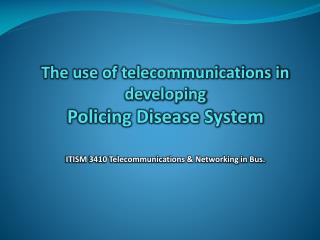
Component of Policing Diseases System
The use of telecommunications in developing Policing Disease System ITISM 3410 Telecommunications & Networking in Bus. Component of Policing Diseases System. MIIDSS : Major Incident Investigation and Disaster Support System ( 重大事件調查及災難支援工作系統 ) CMS : Clinical Management System.
530 views • 35 slides
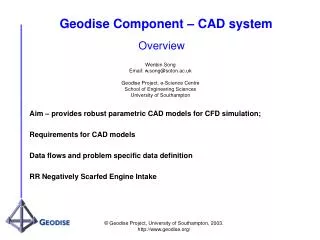
Geodise Component – CAD system
Aim – provides robust parametric CAD models for CFD simulation; Requirements for CAD models Data flows and problem specific data definition RR Negatively Scarfed Engine Intake. Geodise Component – CAD system. Overview. Wenbin Song Email: [email protected] Geodise Project, e-Science Centre
169 views • 5 slides
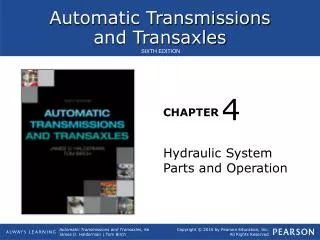
Hydraulic System Parts and Operation
4. Hydraulic System Parts and Operation. FIGURE 4–1 Fluid pressure is used to apply clutches and bands. The pressure and calculated volume index readings of the fluid in the unit can be monitored using a scan tool.
603 views • 38 slides
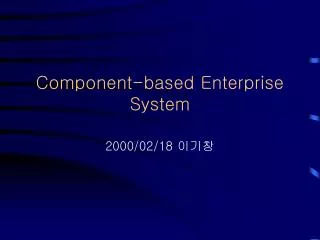
Component-based Enterprise System
Component-based Enterprise System. 2000/02/18 이기창. An application of CIMOSA concepts in the development of change capable manufacturing cells. R.P. Monfared, R.H. Weston MSI Research Institute, Loughborough University, UK Computers in Industry 40(1999) 243-257.
463 views • 36 slides
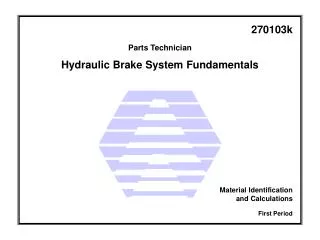
Hydraulic Brake System Fundamentals
270103k. Parts Technician. Hydraulic Brake System Fundamentals. Material Identification and Calculations. First Period. Figure 1 - Maximum stopping distances allowed under the conditions indicated. Figure 2 - Braking levels. Figure 3 - Energy conversion during braking.
3.49k views • 48 slides
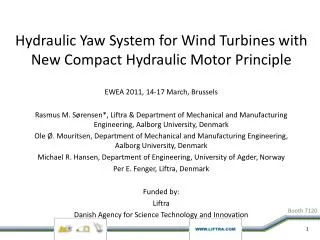
Hydraulic Yaw System for Wind Turbines with New Compact Hydraulic Motor Principle
Hydraulic Yaw System for Wind Turbines with New Compact Hydraulic Motor Principle. EWEA 2011, 14-17 March, Brussels Rasmus M. Sørensen*, Liftra & Department of Mechanical and Manufacturing Engineering, Aalborg University, Denmark
485 views • 14 slides
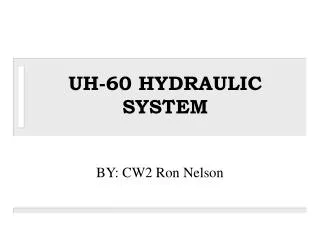
UH-60 HYDRAULIC SYSTEM
UH-60 HYDRAULIC SYSTEM. BY: CW2 Ron Nelson. TERMINAL LEARNING OBJECTIVE. To develop the student Instructor Pilot’s understanding of the components and functions of the UH-60 Hydraulic System. Ref: UH-60 Operator’s Manual (-10) C Co. 1-223d Flight Line Supplement
2.53k views • 18 slides
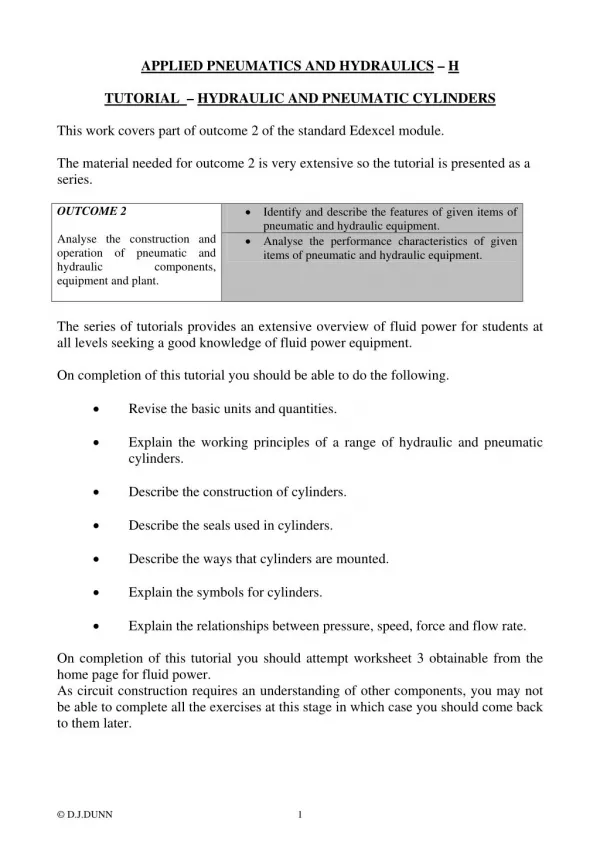
HYDRAULIC SYSTEM-CYLINDERS
Hydraulic control system.Understanding cylinders
830 views • 14 slides
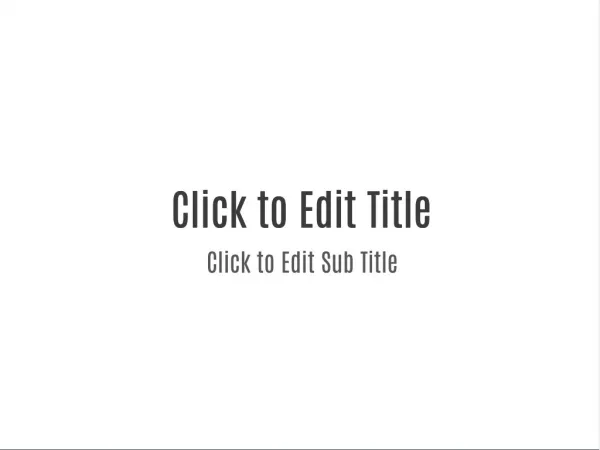
hydraulic of pipelines
89 views • 3 slides
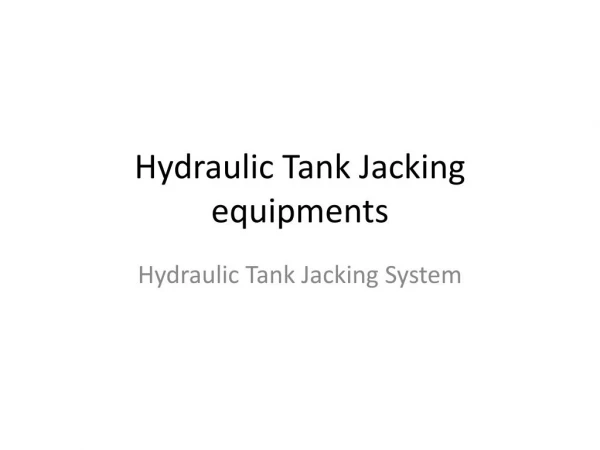
Hydraulic Tank Jacking System Manufacturer, Exporter
https://asthagroup.in/ Astha Group Jack system,Hydraulic jack system, Hydraulic Jacking system, Above ground storage tanks,Hydraulic Jacking system for tank erection, Hydraulic Jacking system for tank lifting, hydraulic jacks, Hydraulic jacks and power pack for storage tank erection, Hydraulic Jack-up system, Jack up system,Jacking Equipment
138 views • 3 slides
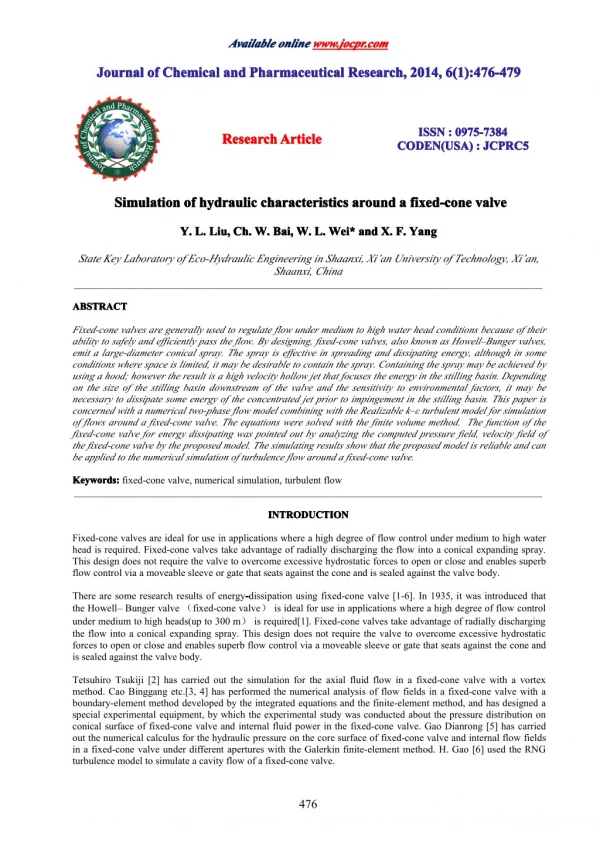
Simulation of hydraulic hydraulic hydraulic hydraulic characteristics characteristics characteristics characteristics a
Fixed-cone valves are generally used to regulate flow under medium to high water head conditions because of their ability to safely and efficiently pass the flow. By designing, fixed-cone valves, also known as Howell–Bunger valves, emit a large-diameter conical spray. The spray is effective in spreading and dissipating energy, although in some conditions where space is limited, it may be desirable to contain the spray. Containing the spray may be achieved by using a hood; however the result is a high velocity hollow jet that focuses the energy in the stilling basin. Depending on the size of the stilling basin downstream of the valve and the sensitivity to environmental factors, it may be necessary to dissipate some energy of the concentrated jet prior to impingement in the stilling basin. This paper is concerned with a numerical two-phase flow model combining with the Realizable k–ε turbulent model for simulation of flows around a fixed-cone valve. The equations were solved with the finite volume method. The function of the fixed-cone valve for energy dissipating was pointed out by analyzing the computed pressure field, velocity field of the fixed-cone valve by the proposed model. The simulating results show that the proposed model is reliable and can be applied to the numerical simulation of turbulence flow around a fixed-cone valve.
145 views • 4 slides
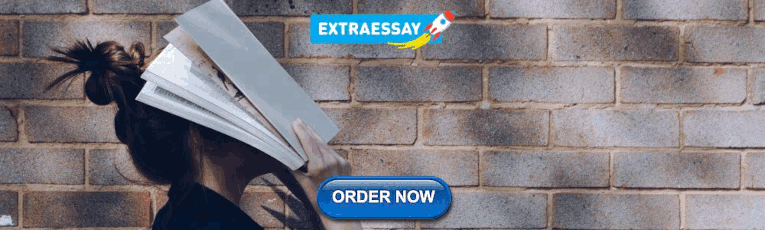
IMAGES
VIDEO
COMMENTS
The term hydraulics. Necessity of hydraulics: 1.To. Pascal's Law Pressure exerted. Pressure applied to. Pascal's Law Pressure. Important Properties: "Shapelessness" . Components of hydraulics: 1.Reservoir 2.Hydraulic pump 3.Hydraulic cylinder 4.Hydraulic piston 5.Control. Hydraulic circuit: A hydraulic. Pump Functions in a.
18 Conductors: The conductors are the pipes or hoses needed to transmit the oil between the hydraulic components. Download ppt "Introduction to hydraulics". Objectives Identify the common uses of hydraulic systems. Determine that liquids are incompressible. Identify the fundamental parts of a hydraulic system.
Unit 1 - Introduction to Hydraulic System - Free download as Powerpoint Presentation (.ppt), PDF File (.pdf), Text File (.txt) or view presentation slides online. This document provides an introduction to hydraulic systems. It defines hydraulics as technology that generates, controls, and transmits power using pressurized liquid. The main advantages of hydraulic systems are easy control, force ...
Hydraulic Mid Inlets 29. Power Beyond 30. Open Center Schematic 31. Closed Center LS Schematic 32. Horse Power Consumption 33. Hydraulic Cylinders 34. Single Acting Double Acting Cylinders 35. Bleeding Air 36. Hydraulic Motor Types 37. How Motors Work 38. Filtration 39. How Filters are Selected 40. PTO Types 41. Manual PTO's 42
1.6 -Basic Construction of Hydraulic Systems, 37 1.7- Advantages and Limitations of Hydraulic Systems, 40 1.7.1- Use of Hydraulic Fluids, 40 1.7.2- Power Transmission, 41 1.7.3- Controllability and System Design, 42 1.8- Industry Standards for Hydraulic Systems, 43
Pump Power. Hydraulic power is the product of pressure and flow rate. Across a circuit with the same flow in as out, the power change: Ph = Q∆p / 60 Where Ph = hydraulic power, kW Q = flow through device, L/min ∆p = pressure rise or drop across device or circuit, MPa.
Hydraulic • Two Greek word, hudro (Water) + aulos (Pipe) → hudraulikos • hudraulikos (Greek) → hydraulic (Latin) early 17th century • Hydraulics is the science of forces and movements transmitted by means of liquids. • Pressurized liquid act as a medium of power transmission. • Hydraulic fluids are incompressible.
An introduction to basic hydraulic fundamentals. Learn about the most basic hydraulic fundamentals including terms such as flow and head. When it comes to hydraulics in water pumping systems, we need to consider three major parameters: Flow, head and power - or Q, H and P.
3 3 Basic Principle Basic principle of a hydraulic system are: -Prime mover to power the system -Pump to move fluid -Reservoir to store fluid -Relief valve or pump compensator to control maximum system pressure -Filter to clean the fluid -Plumbing to transport fluid to components. 4 4 Basic Principle. 5 Basic Components The major ...
Figure 14.5.4 14.5. 4: Hydraulic brakes use Pascal's principle. The driver pushes the brake pedal, exerting a force that is increased by the simple lever and again by the hydraulic system. Each of the identical wheel cylinders receives the same pressure and, therefore, creates the same force output F 2.
In this lesson we'll define fluid power systems and identify critical fluid power properties, pressure, flow rate, and valve position, and discuss how these ...
Presentation Transcript. Introduction to hydraulics Module 1. Objectives • Identify the three main methods of transmitting power. • Identify the common uses of hydraulic systems. • Determine that liquids are incompressible. • Identify the fundamental parts of a hydraulic system. • Identify the main components of the hydraulic work ...
Hydraulics has many advantages not always found in electrical and mechanical type drives. Hydraulic cylinders and motors can be operated at variable speeds. By varying the volume flowing into the actuator (cylinder or motor) the speed is changed. The hydraulic cylinder or motor can be stalled under a load. Hydraulic systems use relief valves or ...
A hydraulic system uses pressurized liquid to generate, control, and transmit power. It has several advantages over mechanical and electrical systems including easy control, force multiplication, constant force regardless of speed changes, and compact construction. The key components are a pump, reservoir, valves, actuator, and piping. Pascal's law states that pressure in a confined fluid is ...
this chapter, we shall discuss a structure of hydraulic systems and pneumatic systems. We will also discuss the advantages and disadvantages and compare hydraulic, pneumatic, electrical and mechanical systems. 1.2 Fluid Power and Its Scope Fluid power is the technology that deals with the generation, control and transmission of ...
Hydraulic pumps operate by creating a vacuum at a pump inlet, forcing liquid from a reservoir into an inlet line, and to the pump. Mechanical action sends the liquid to the pump outlet, and as it does, forces it into the hydraulic system. This is an example of Pascal's Law, which is foundational to the principle of hydraulics.
Presentation Transcript. A hydraulic system is a drive technique in which energy is transferred from an electric motor to an actuator, such as a hydraulic cylinder by using a fluid. Hydraulic systems are usually used in that situations where a high power density is required or load needs to change frequently.
3.1 Hydraulic power pack. The hydraulic power pack combines the pump, the motor, and the tank. The hydraulic power pack unit provides the energy required for the hydraulic system. The parts of the hydraulic power pack unit are shown in Fig. 1.6. Locate the power pack unit and identify its parts.
The hydraulic systems consists a number of parts for its proper functioning. These. include storage tank, filter, hydraulic pump, pressure regulator, control valve, hydraulic. cylinder, piston and ...
For more and related videos :https://www.youtube.com/channel/UCpdWMqUKAErpyRt6IBY2GKA?sub_confirmation=1