Chapter 3: Process Cost System
3.3 process costing (weighted average).
Process Costing consists of the following steps:
- Physical flow of units
- Equivalent Units of Production
- Cost per Equivalent Unit
- Assign Costs to Units completed and Ending work in process inventory
- Reconcile Costs
Keep in mind, there are no Generally Accepted Accounting Principles (GAAP) that mandate how we must do a process cost report. We will focus on the calculations involved and show you an example of a process cost summary report but know there are several ways to present the information, but the calculations are all the same.
In the previous page, we discussed the physical flow of units (step 1) and how to calculate equivalent units of production (step 2) under the weighted average method. We will continue the discussion under the weighted average method and calculate a cost per equivalent unit.
Step 3: Cost per Equivalent Unit
The formula we will use is notice we are primarily using the dollar costs and not units for this section (except we will use TOTAL equivalent units we calculated in the previous section):
We will calculate a cost per equivalent unit for each cost element (direct materials and conversion costs (or direct labor and overhead).
Example – Jax Company
To continue with our previous example, we were given the following information:
We calculated total equivalent units of 11,000 units for materials and 9,800 for conversion.
To calculate cost per equivalent unit by taking the total costs (both beginning work in process and costs added this period) and divide by the total equivalent units.
In this example, beginning work in process is zero. This will not always be the case. The problem will provide the information related to beginning work in process inventory costs and units.
Step 4: Assign Costs
In this next section, we will combine the equivalent units (from step 2) and the cost per equivalent units (step 3) to assign costs to units completed and transferred out (also called cost of goods manufactured) and costs of units remaining ending work in process inventory. The basic formula to assign costs is:
Using the example company, Jax Company, we have the following information:
We would assign costs as follows:
For costs of units completed and transferred, we take the equivalent units for units completed x cost per equivalent unit. We do the same of ending work in process but using the equivalent units for ending work in process .
Step 5: Cost Reconciliation
Finally, we can check our work. We want to make sure that we have assigned all the costs from beginning work in process and costs incurred or added this period to units completed and transferred and ending work in process inventory.
First, we need to know our total costs for the period (or total costs to account for) by adding beginning work in process costs to the costs incurred or added this period. Then, we compare the total to the cost assignment in step 4 for units completed and transferred and ending work in process to get total units accounted for. Both totals should agree.
For Jax Company, the cost reconciliation would be:
The full process cost report can be found by clicking Jax_process cost ).
- Accounting Principles: A Business Perspective.. Authored by : James Don Edwards, University of Georgia & Roger H. Hermanson, Georgia State University.. Provided by : Endeavour International Corporation. Project : The Global Text Project.. License : CC BY: Attribution
- Cost Per Equivalent Unit (weighted average method) . Authored by : Education Unlocked. Located at : https://youtu.be/Txv05196CWs . License : All Rights Reserved . License Terms : Standard YouTube License
The global body for professional accountants
- Search jobs
- Find an accountant
- Technical activities
- Help & support
Can't find your location/region listed? Please visit our global website instead
- Middle East
- Cayman Islands
- Trinidad & Tobago
- Virgin Islands (British)
- United Kingdom
- Czech Republic
- United Arab Emirates
- Saudi Arabia
- State of Palestine
- Syrian Arab Republic
- South Africa
- Africa (other)
- Hong Kong SAR of China
- New Zealand
- Our qualifications
- Getting started
- Your career
- Apply to become an ACCA student
- Why choose to study ACCA?
- ACCA accountancy qualifications
- Getting started with ACCA
- ACCA Learning
- Register your interest in ACCA
- Learn why you should hire ACCA members
- Why train your staff with ACCA?
- Recruit finance staff
- Train and develop finance talent
- Approved Employer programme
- Employer support
- Resources to help your organisation stay one step ahead
- Support for Approved Learning Partners
- Becoming an ACCA Approved Learning Partner
- Tutor support
- Computer-Based Exam (CBE) centres
- Content providers
- Registered Learning Partner
- Exemption accreditation
- University partnerships
- Find tuition
- Virtual classroom support for learning partners
- Find CPD resources
- Your membership
- Member networks
- AB magazine
- Sectors and industries
- Regulation and standards
- Advocacy and mentoring
- Council, elections and AGM
- Tuition and study options
- Study support resources
- Practical experience
- Our ethics modules
- Student Accountant
- Regulation and standards for students
- Your 2024 subscription
- Completing your EPSM
- Completing your PER
- Apply for membership
- Skills webinars
- Finding a great supervisor
- Choosing the right objectives for you
- Regularly recording your PER
- The next phase of your journey
- Your future once qualified
- Mentoring and networks
- Advance e-magazine
- Affiliate video support
- An introduction to professional insights
- Meet the team
- Global economics
- Professional accountants - the future
- Supporting the global profession
- Download the insights app
Can't find your location listed? Please visit our global website instead
- Process costing
- Study resources
- Management Accounting (MA)
- Technical articles
Process costing is a method of costing used mainly in manufacturing where units are continuously mass-produced through one or more processes. Examples of this include the manufacture of erasers, chemicals or processed food. In process costing it is the process that is costed (unlike job costing where each job is costed separately). The method used is to take the total cost of the process and average it over the units of production.
Important terms to understand In a manufacturing process the number of units of output may not necessarily be the same as the number of units of inputs. There may be a loss. Normal loss This is the term used to describe normal expected wastage under usual operating conditions. This may be due to reasons such as evaporation, testing or rejects. Abnormal loss This is when a loss occurs over and above the normal expected loss. This may be due to reasons such as faulty machinery or errors by labourers. Abnormal gain This occurs when the actual loss is lower than the normal loss. This could, for example, be due to greater efficiency from newly-purchased machinery. Work in progress (WIP) This is the term used to describe units that are not yet complete at the end of the period. Opening WIP is the number of incomplete units at the start of a process and closing WIP is the number at the end of the process. Scrap value Sometimes the outcome of a loss can be sold for a small value. For example, in the production of screws there may be a loss such as metal wastage. This may be sold to a scrap merchant for a fee. Equivalent units This refers to a conversion of part-completed units into an equivalent number of wholly-completed units. For example, if 1,000 cars are 40% complete then the equivalent number of completed cars would be 1,000 x 40% = 400 cars. Note: If 1,000 cars are 60% complete on the painting, but 40% complete on the testing, then equivalent units will need to be established for each type of cost. (See numerical example later.) How to approach process accounting questions
Note: Although this proforma includes both losses and WIP, the Paper F2/FMA syllabus specifically excludes situations where both occur in the same process. Therefore, don’t expect to have to complete all of the steps in the questions. Normal loss example Mr Bean’s chocolate Wiggly bars pass through two processes. The data for the month just ended are:
Mr Bean allows the staff to eat 5% of the chocolate as they work on Process 1. There was no work in progress at the month end. Prepare the two process accounts and calculate the cost per kg.
- The staff normally eat 5% of the chocolate, so the normal loss is 4,000 x 5% = 200kg There is no work in progress or scrap value or abnormal losses or gains, so we can now balance the account to obtain the amounts transferred to Process 2.
- Number of kg transferred = kg input less normal loss = 4,000 – 200 = 3,800kg
Abnormal gain example There is a heat wave and staff have eaten less chocolate. At the end of Process 1, 3,810 units are transferred to Process 2.
Cost of units transferred to Process 2 = $2.89 x 3,810 = $11,029 (using $2.894736842 to avoid rounding differences). Cost of abnormal gain = $2.89 x 10 = $29. [Remember to open an abnormal gain T account and credit it with $29]
Scrap value example Mr Bean can no longer afford to give his staff 5% of the bars. He decides to offer the bars to his staff at a discount. They pay 40c for every kg that they eat. As a result of this, there is another abnormal gain of 10kg, so 3,810 units are transferred to Process 2.
Workings Here we need to calculate the scrap value. The value of units transferred to Process 2 is a balancing figure.
- Number of kg of normal loss scrap amount per kg = 200 x 0.4 = $80 [Dr Scrap A / C $80, Cr Process A / C $80]
Be careful here! The scrap value also affects the abnormal gain or loss accounts. Since the staff didn’t eat the number of bars that they were entitled to, the scrap value (the 40c per bar) is lower than 200 40c. In fact, it is 10 x 40c = $4 lower (the abnormal gain). This needs to be reflected in the scrap account and the abnormal gain account.
Work in progress example Assuming at the month end there are now part-completed bars (work- in-progress). Assuming also that he stopped charging staff for the bars that they had eaten. The data for Process 2 was as follows:
For questions that include WIP, we need to calculate equivalent units. First, we need to choose the method of valuing WIP. In an exam, use the first in first out (FIFO) method if the percentage completion of each element of opening WIP is given. Use the weighted average (WA) method if the value of each element of opening WIP is given. [Note that the two methods give different valuations for the closing WIP.] In the weighted average method, no distinction is made between units of opening inventory and new units introduced to the process during the accounting period.
Heather Freer is management accounting technical author at BPP Learning Media
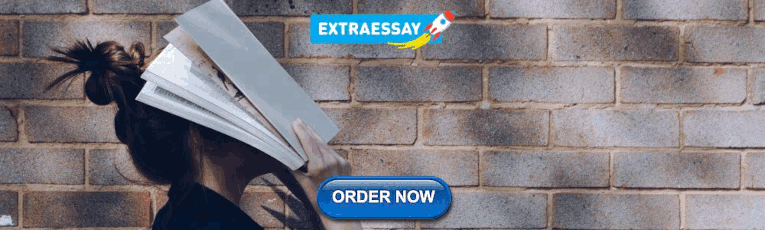
Related Links
- Student Accountant hub
Advertisement
- ACCA Careers
- ACCA Career Navigator
- ACCA Learning Community
Useful links
- Make a payment
- ACCA-X online courses
- ACCA Rulebook
- Work for us
Most popular
- Professional insights
- ACCA Qualification
- Member events and CPD
- Supporting Ukraine
- Past exam papers
Connect with us
Planned system updates.
- Accessibility
- Legal policies
- Data protection & cookies
- Advertising
ACCOUNTING PRINCIPLES: Problem Solving Survival Guide, Volume 2: Chapters 13-26, 10th Edition by
Get full access to ACCOUNTING PRINCIPLES: Problem Solving Survival Guide, Volume 2: Chapters 13-26, 10th Edition and 60K+ other titles, with a free 10-day trial of O'Reilly.
There are also live events, courses curated by job role, and more.
P ROCESS COSTING
Some products are produced in such a manner that individual units are not identifiable throughout the process. Examples include the manufacture of paint, the refining of oil, and the canning of food. The cost of a completed gallon of paint or oil or can of vegetables is determined by a series of calculations as the product moves through the various production processes. Costs are accumulated for each production department (or manufacturing process) each period and are allocated to the production units processed during that period in each department. The costs accumulated for production units that are transferred out of one department are considered to be costs of materials added to the subsequent manufacturing process. Costs accumulated for production units that are transferred out of the final department are considered to be costs of items added to finished goods inventory. The procedures for accounting for the flow of costs in a process cost system and the related equivalent units of production are discussed in this chapter.
SUMMARY OF STUDY OBJECTIVES
- Understand who uses process costs systems. Companies that mass-produce similar products in a continuous fashion use process cost systems. Once production begins, it continues until the finished product emerges. Each unit of finished product is indistinguishable from every other unit.
- Explain the similarities and differences between job order cost and process cost systems. Job order cost systems ...
Get ACCOUNTING PRINCIPLES: Problem Solving Survival Guide, Volume 2: Chapters 13-26, 10th Edition now with the O’Reilly learning platform.
O’Reilly members experience books, live events, courses curated by job role, and more from O’Reilly and nearly 200 top publishers.
Don’t leave empty-handed
Get Mark Richards’s Software Architecture Patterns ebook to better understand how to design components—and how they should interact.
It’s yours, free.
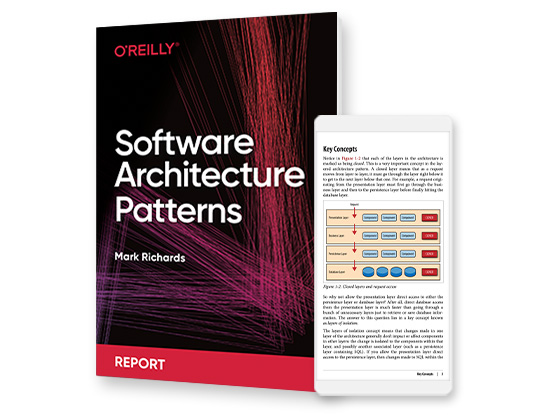
Check it out now on O’Reilly
Dive in for free with a 10-day trial of the O’Reilly learning platform—then explore all the other resources our members count on to build skills and solve problems every day.
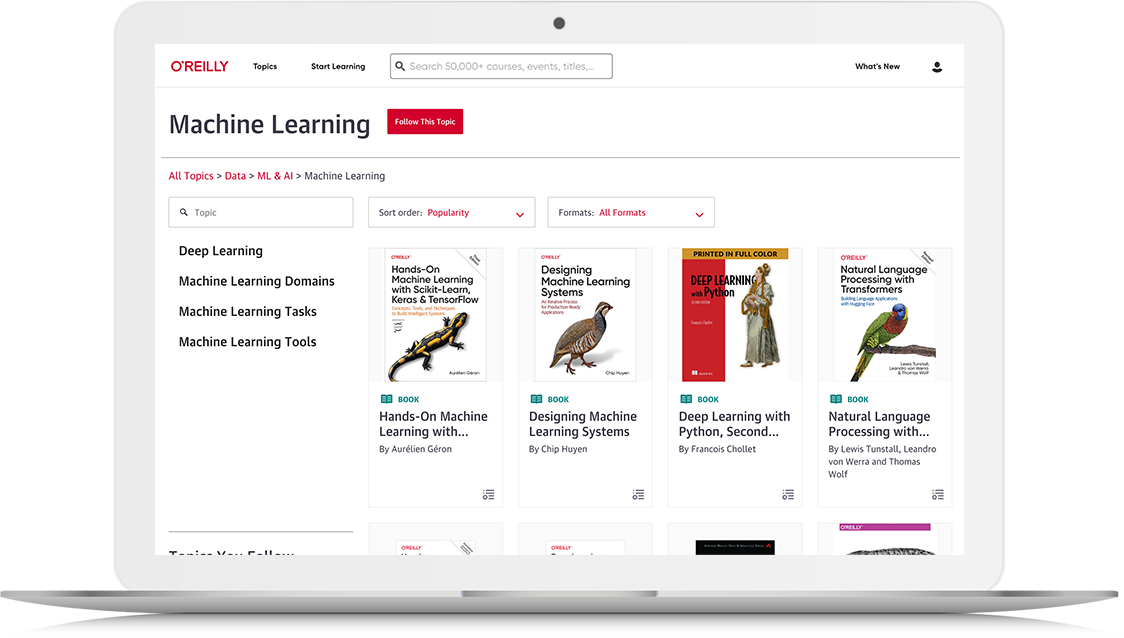
Accountinguide
Simple and Easy
Process Costing
Process Costing is the cost accounting method in which production overhead is equally allocated to each product due to their similarity and mass production. The company assumes that each product requires the same overhead cost. It is hard to separate the overhead cost base on actual consumption. Moreover, raw material needs to pass through multiple stages of production before turning into finished goods. And it is very complicated to assign the overhead cost individual unit.
All production costs will be accumulated and allocate equally to all products by assuming that they are consumed the same resource. Accountants will calculate the total overhead cost of each month and separate them to each finished product at the month-end.
Process costing is suitable for some businesses, which produces similar products, such as a footwear manufacturing. Besides that, It is also applicable to manufacturing that has many processes which cannot identify the cost of each production process.
Feature of Process Costing
- The production has more than two processes.
- Raw material goes through many processes, the output of one process will become the input of another process.
- The output of the last process will become finished goods.
- The final products are similar and hard to separate from each other.
- The production cycle will operate continuously.
- The output may result in a joint product or by-product.
- The wastage also takes into account while calculating the cost.
- The unfinished product at the end of the month will be estimated by the percentage of completion, which known as Equivalent units (EU = number of unfinished product x percentage of completion).
Process Costing Example
Company ABC is manufacturing which specializes in shoe production, they mainly focus on the local market. The production needs to go through multiple processes which they called the departments.
First, they start from the Designing and Cutting department where shoes are designed to fit with the trending market, and fabric will be cut to fit with each design. In March 200X, the Design and Cutting department incur the cost of direct material USD 100,000, direct labor cost of USD 150,000 and USD 80,000 of overhead cost. During month, this department has finished 10,000 pairs of shoes and passes them to next stage.
Second, Sewing department where all parts of the shoes are attached. In March 202X, this department has incurred a cost of direct labor USD 50,000, overhead cost USD 30,000. As a result, they have completed 8,000 pairs of shoes and pass the next stage.
Finally, the Packaging department, the place where shoes are matched by size and put into a retail box. They are ready for delivery to customers. The cost of direct labor in this department during March has only USD 30,000 and they complete the work for 12,000 pairs of shoes.
Calculate the process costing in each department.
Design and Cutting department
- Direct material cost per unit: 100,000 /10,000 units = $ 10 per unit
- Direct Labor cost per unit: 150,000/10,000 units = $ 15 per units
- Overhead cost per unit: 80,000/10,000 units = $ 8 per unit
Sewing department
- Direct labor per unit: 50,000/8,000 units = $ 6.25 per unit
- Overhead cost per unit: 30,000/8,000 units = $ 3.75 per unit
Packaging department
- Direct Labor per unit: 30,000/12,000 units = $ 2.5 per unit
What are the Advantages of Process Costing?
What are the disadvantages of process costing.
Although process costing has several benefits, it still has some disadvantages as included in the table below:
Related posts:
- Absorption Costing
- Activity-Based Costing
- Accounts Payable Process
- Audit Process
- Direct Cost and Indirect Cost
Your Article Library
Top 5 problems on process costing (with solution).
ADVERTISEMENTS:
In this article we will discuss about the top five problems on process costing with their relevant solutions.
- Process Costing Problem 5 with Solution
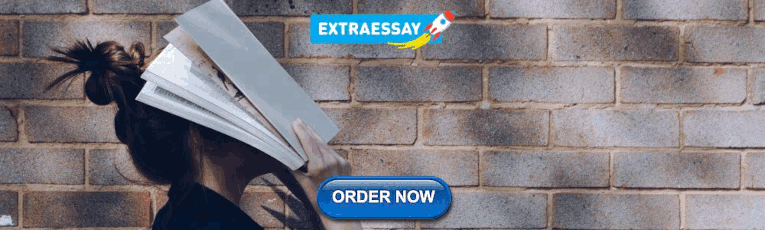
Process Costing Problem 1:
The Bharat Manufacturing Company’s product passes through two distinct processes, X and Y, and then to the finished stock. It is known from the past experience that wastage occurs in the process as under:
In Process X, 5% of the units entering the process.
In Process Y, 10% of the units entering the process.
The scrap value of the wastages in process X is Rs.8 per 100 units and in process Y is Rs.10 per 100 units.
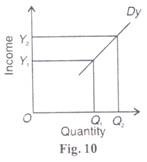

Process Costing Cost Accounting : Study Notes, Problems Solutions, Question Answers
Study notes.
- Process Costing - Characteristics, Features, Application in Industry
- Process Costing - Elements/Components of Cost, Recording/Accounting Methodology
- Process Costing - Collection of information, Cost ledgers, integrated accounting
- Process Account - Input, Output, Cost of Production
- Process Account - Gross/Net Input/Output, Normal/Abnormal Loss/Gain, Cost of Production
- Normal/Abnormal Loss - Valuation
- Normal Loss - Accounting Treatment
- Process Account - Normal Loss - Illustration
- Abnormal Loss - Accounting Treatment
- Process Account - Normal/Abnormal Loss - Illustration
- Abnormal Gain - Valuation and Accounting Treatment
- Process Account - Abnormal Gain - Illustration
- Closing Stock in Process Account - Raw Material, Finished Goods, Work in Progress
- Closing Stock of Raw Material in Process Account
- Stock of Raw Material in Process Account - Illustration
- Closing Stock of Finished Goods/Stock in Process Account
- Closing Stock of Finished Goods/Stock in Process Account - Illustration
- Inter Process Profits and Closing stock of Finished Goods
- Closing Stock of Work-in-Progress in Process Account
- Statement of Equivalent Production, Statement of Cost, Statement of Evaluation
- Only closing Stock of Work-in-Progress in Process Account - illustration
- Weighted Average, FIFO methods for valuation of work-in-progress in Process Accounts
- Both opening and closing Stocks of Work-in-Progress in Process Account - illustration
- Only opening Stock of Work-in-Progress in Process Account - illustration
Problems Solutions
- Simple Process Accounts
- Simple Process Accounts involving Overhead Distribution
- Normal Loss - Wastage, Scrap - Cost Sheet
- Part Production sold - Income Statement, Cost Sheet
- Reverse Calculations - Finding input, Wastage Percentage
- Normal Abnormal Losses - Process Accounts
- Normal Losses and Abnormal Gains - Process Accounts
- Normal Loss, Abnormal Loss, Abnormal Gain - Process Accounts, Income Statement
- Stocks at Raw Material Stage and Normal losses
- Stocks at Finished Goods Stage and Normal losses
- Inter Process Profits only closing Finished Goods
- Inter Process Profits both opening and closing Finished Goods
- Only Closing Work in Progress
- Only Closing Work in Progress - Normal Loss, Abnormal Loss/Gain
- Opening and Closing Work in Progress - FIFO and Weighted Average Methods
- Opening Closing Work in Progress - Normal/Abnormal Loss/Gain
- Only Opening Work in Progress
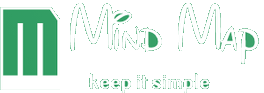
Process Costing – steps with examples
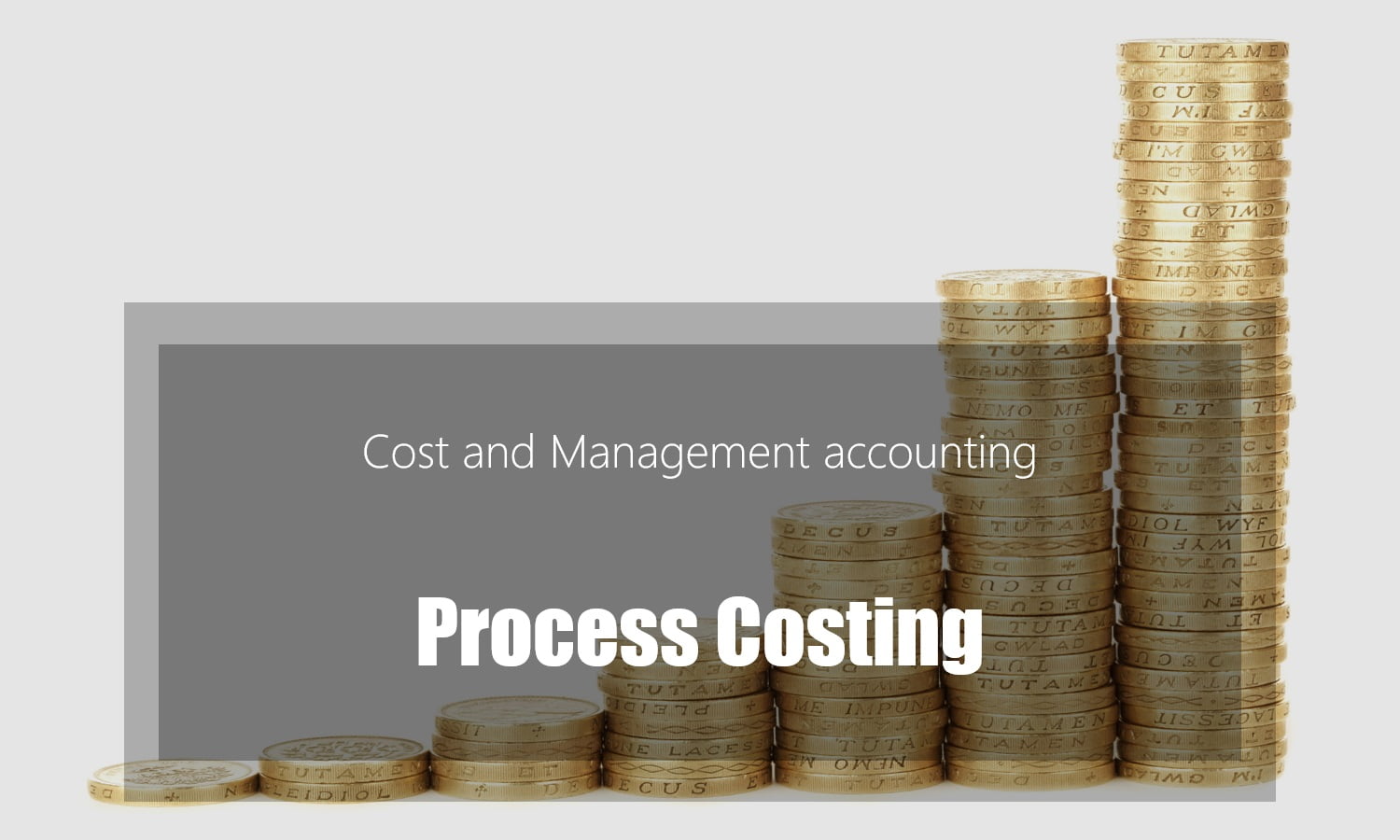
- Introduction to Cost and Management Accounting
- High/Low and Linear Regression Analysis
- Inventory Management
- Accounting for Inventory
- Accounting for overheads
- Absorption Costing
- Marginal Costing
- Job Batch and Service costing
- Process Costing
- Target Costing
- Standard Costing
- Cost Volume Profit analysis
- Relevant costing and Decision-Making Techniques
- Time Value of Money (TVM)
Process Costing Overview
- Process costing is used when output is produced in a continuous process system and it is difficult to separate individual units of output.
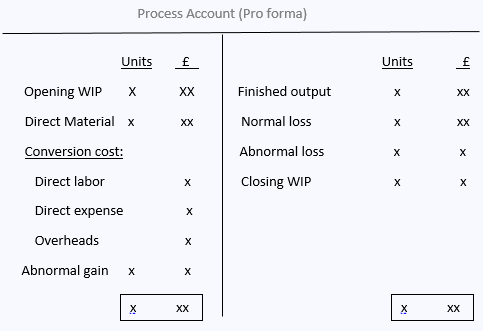
- It is not possible to have abnormal loss and gain on the same account in the same period.
- Whatever the complications, the task that sits at the heart of process costing is always to allocate the costs collected on the debit side of the account to possible output on the credit side.
- Basically we will need to:
- Identify the losses and output units.
- Calculate the cost of good output, losses and WIP.
- Use the costs calculated to assign to good output, losses and WIP (i,e units x cost)
- Complete the process account.

- It is the expected loss in processing and is usually expressed as a percentage of input units of materials.
- It is inherent in the process and is unavoidable.
Normal loss = material input – expected output
Normal loss with recovery/scrap value
- when losses in a process has scrap value then the company is able to recover some of input costs.
- The scrap value reduces overall cost of the process.
- In process account Normal loss is measured at scrap value.
Cost of output = Total process cost – scrap value Expected output Expected output = material input – normal loss
Normal loss without recovery/scrap value
- The cost of lost units is part of the cost of obtaining the good output.
- All of the cost should be assigned to the good output and none to the normal loss.
- It is given a NIL value when the loss has no scrap value.
- Disposal cost of normal loss is an addition to costs to the process and debited to process account. It is added to total process costs when calculating cost of good output.
Cost of output = Total process cost – scrap value Expected output
Abnormal Losses
- The difference between total actual loss and normal loss is ‘abnormal loss’.
- Abnormal loss is not expected and given a cost.
- If it is assumed that losses occur at the end of process, units of abnormal loss are costed exactly as finished output units i,e cost per units of abnormal loss is same as cost of units of good output
Cost of output = Total process cost – scrap value Expected output
- Abnormal loss is treated as an expense and charged in Income Statement.
Abnormal Gain

- The difference between normal loss and the total actual loss, where the actual loss is less then normal loss.
Abnormal Gain = Normal loss – Actual loss
- Abnormal gain is a benefit rather than a cost.
- Abnormal gain is an adjustment the increases the profit for the period.
- It is recorded as a debit entry.
- If it is assumed that all losses occur at the end of the process, the cost per unit of finished output and the value/cost of abnormal gain is calculated as the cost per expected unit of output.
- The cost per unit of abnormal gain is therefore the same as the cost of units of good output.
Abnormal Gain where loss has a scrap value
- When loss has a scrap value, the value of abnormal gain is actually less than the amount shown in the process account. As the balance on the abnormal gain account is netted off by the scrap value.
- The balance is transferred as a net benefit to the Income Statement.
Losses and Gains at different stages in the Process
- If it is assumed that losses occur at the end of the production process, units of abnormal loss or gain are given a cost or value as if they are fully completed units and so one equivalent unit each. But is no relevant for normal loss .
- However, if losses occur at a different stage in the process, this assumption of differing degrees of completion is used for direct material and conversion , instead the concept of equivalent unit is used to decide the cost of abnormal loss/gain.
When loss occurs part-way through a process, the cost of any abnormal loss is calculated:
- establishing the equivalent units of direct material and conversion costs for loss.
- calculating a cost per equivalent units.
- using the calculations of equivalent units and cost per equivalent units to obtain a cost for finished output and abnormal loss in period.
of Abnormal Gain
The same principles apply to the valuation of abnormal gain, where the gain occur part-way through the process as abnormal loss.
However there is one important difference, equivalent units of abnormal gain are given a Negative value and subtracted from the total equivalent units of output in the period.
Work in Progress Balance
- When there is opening WIP there are two types of costs on the debit side. The opening WIP and the cost incurred in current period.
- The issue is whether these type of costs should be treated together or separately. The question is addressed in the accounting policy adopted for opening WIP. The following are two policies adopted:
weighted average cost method
- When this is used the assumption is that all units produced during the period and all units in closing inventory should be valued at the same cost per equivalent units for materials and conversion i,e an average cost per equivalent unit is calculated for all units of output and closing inventory.
- A three stage calculation is used:
- Prepare statement of equivalent units.
- Prepare statement of cost per unit equivalent units
- Prepare statement of evaluation.
FIFO cost method
- Based on the assumption that the opening WIP are the first units completed. It is necessary to calculate the number of equivalent units for:
- WIP opening
- Finished output
- WIP closing
- The three stage calculation is used for equivalent units and cost allocation.
- The three stage calculation is similar as weighted average with the exception that in statement of evaluation finished output consists of:
- The finished cost of opening WIP is the sum of: costs in opening WIP value at start of period PLUS cost incurred in current period to complete these units PLUS the cost of finished output started and finished in the period.
Closing Work in Progress
- Closing WIP means some units have been started and finished in the year and others have been started but not finished.
- It stands to reason that cost/value of an unfinished unit is less than the cost of a completed unit . The cost of the process must be shared between finished output and unfinished WIP . In order to do this the concept of equivalent is used.
- A three stage calculation:
- Prepare statement of cost per unit equivalent units.
Joint Products and By-Products
Process costing.
Joint products are two or more products generated simultaneously, by a singe manufacturing process, using common input , and being substantially equal in value.
Apportioning common processing costs
- The costs of the common process that produces the Joint products are common costs. They must be apportioned between Joint products.
One of the following methods is used:
Units Basis
Common costs are apportioned on basis of total number of units produced.
Sales value at split-off point
Common costs are apportioned on basis of the sales value of Joint product produced when they are separated in process.
Net realizable value
By-Products
When two or more different products are produced. Any product that does not have a substantial sales value and relatively minor in quantity is called a by-product.
Treatment of By-Product
Any of following method is used:
- Adding it to revenue from sales. No cost is allocated to by-product.
- As other income. No cost is allocated to by-product.
- As a deduction from Joint process costs (the most common method used).
- By-product is measured at scrap value, similar to normal loss.
Recent Posts
- Externally oriented Cost Management Techniques
- Pricing decisions and Pricing strategies
- Multi-product Break-even (CVP) analysis
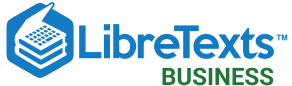
- school Campus Bookshelves
- menu_book Bookshelves
- perm_media Learning Objects
- login Login
- how_to_reg Request Instructor Account
- hub Instructor Commons
Margin Size
- Download Page (PDF)
- Download Full Book (PDF)
- Periodic Table
- Physics Constants
- Scientific Calculator
- Reference & Cite
- Tools expand_more
- Readability
selected template will load here
This action is not available.
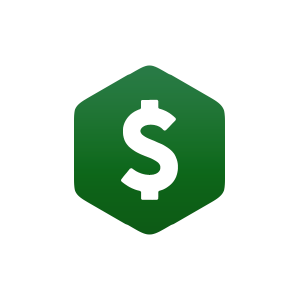
7: Costing Methods
- Last updated
- Save as PDF
- Page ID 45732
\( \newcommand{\vecs}[1]{\overset { \scriptstyle \rightharpoonup} {\mathbf{#1}} } \)
\( \newcommand{\vecd}[1]{\overset{-\!-\!\rightharpoonup}{\vphantom{a}\smash {#1}}} \)
\( \newcommand{\id}{\mathrm{id}}\) \( \newcommand{\Span}{\mathrm{span}}\)
( \newcommand{\kernel}{\mathrm{null}\,}\) \( \newcommand{\range}{\mathrm{range}\,}\)
\( \newcommand{\RealPart}{\mathrm{Re}}\) \( \newcommand{\ImaginaryPart}{\mathrm{Im}}\)
\( \newcommand{\Argument}{\mathrm{Arg}}\) \( \newcommand{\norm}[1]{\| #1 \|}\)
\( \newcommand{\inner}[2]{\langle #1, #2 \rangle}\)
\( \newcommand{\Span}{\mathrm{span}}\)
\( \newcommand{\id}{\mathrm{id}}\)
\( \newcommand{\kernel}{\mathrm{null}\,}\)
\( \newcommand{\range}{\mathrm{range}\,}\)
\( \newcommand{\RealPart}{\mathrm{Re}}\)
\( \newcommand{\ImaginaryPart}{\mathrm{Im}}\)
\( \newcommand{\Argument}{\mathrm{Arg}}\)
\( \newcommand{\norm}[1]{\| #1 \|}\)
\( \newcommand{\Span}{\mathrm{span}}\) \( \newcommand{\AA}{\unicode[.8,0]{x212B}}\)
\( \newcommand{\vectorA}[1]{\vec{#1}} % arrow\)
\( \newcommand{\vectorAt}[1]{\vec{\text{#1}}} % arrow\)
\( \newcommand{\vectorB}[1]{\overset { \scriptstyle \rightharpoonup} {\mathbf{#1}} } \)
\( \newcommand{\vectorC}[1]{\textbf{#1}} \)
\( \newcommand{\vectorD}[1]{\overrightarrow{#1}} \)
\( \newcommand{\vectorDt}[1]{\overrightarrow{\text{#1}}} \)
\( \newcommand{\vectE}[1]{\overset{-\!-\!\rightharpoonup}{\vphantom{a}\smash{\mathbf {#1}}}} \)
- 7.1: Introduction to Process Costing
- 7.2: Job Order Costing vs Process Costing
- 7.3: Flow of Costs (Process Costing)
- 7.4: Equivalent Unit Calculations
- 7.5: Cost Reconciliation
- 7.6: Direct and Step-Down Methods
- 7.7: Introduction to Cost Accounting Methods
- 7.8: Activity-Based Costing
- 7.9: Traditional Costing vs. ABC
- 7.10: Putting It Together- Costing Methods
- 7.11: Why It Matters- Costing Methods
- 7.12: Assignment- Costing Methods
- 7.13: Introduction to Cost Management
- 7.14: Value Chain
- 7.15: Direct and Indirect Costs
- 7.16: Introduction to Job Order Costing
- 7.17: Job Order Costing
- 7.18: Calculating Costs
- 7.19: Flow of Costs (Job Order Costing)
- 7.20: Recording Job Order Costs
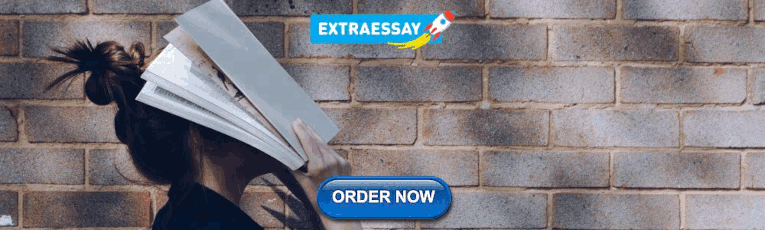
IMAGES
VIDEO
COMMENTS
Problem # 1: The Zee manufacturing company produces a single product which goes through one process only. The manufacturing cycle takes a month. The company started its manufacturing operation on 1 st February, 2018 and costs of production for this month were as follows: Material Rs. 41,412; Labor Rs. 32,054; FOH Rs. 23,870.
Direct labor cost. $ 2,880. Applied overhead cost. $ 8,880. We calculated total equivalent units of 11,000 units for materials and 9,800 for conversion. To calculate cost per equivalent unit by taking the total costs (both beginning work in process and costs added this period) and divide by the total equivalent units.
Process A. The other direct expenses were as follows: PROCESS-A PROCESS-B PROCESS-C Sundry materials Direct labour Direct expenses The wastage of process 'A' was 5% and in process 'B' 4% I ,500 4,500 I ,OOO I 8,000 I ,OOO I ,500 6,500 I ,503 The wastage of process 'A' was sold at 0.25 per unit and that of 'B' at 0.50 per unit and that of C at 1.00.
Process costing is used when there is mass production of similar products, where the costs associated with individual units of output cannot be differentiated from each other. In other words, the cost of each product produced is assumed to be the same as the cost of every other product. Under this concept, costs are accumulated over a fixed ...
Process 1 involved preparing the raw materials for printing, process 2 is the actual printing, and process 3 is packaging the planners to be moved to finished goods inventory. Costing is simpler in this system because rather than having to prepare a costing sheet for many products, we only need to do costing for three departments or processes.
2.6: Process Costing (FIFO Method) Another acceptable method for determining unit cost under process costing is the first-in, first-out (FIFO) cost method. Under the FIFO method, we assume any units that were not completed last period (beginning work in process) are finished before anything else is started.
Learning Outcomes. The flow of costs in the process costing system is similar to in a job-costing system, but let's review with our Ultimate Planner example: In the process planning we will cost by process. Process 1 involved preparing the raw materials for printing, process 2 is the actual printing, and process 3 is packaging the planners to ...
The continuous flow of products makes job costing impractical. Instead, accountants compute the cost per unit by first accumulating costs for the entire period (usually a month) for each process or department. Second, they divide the accumulated costs by the number of units produced (tons, pounds, gallons, or feet) in that process or department.
Process costing is a method of costing used mainly in manufacturing where units are continuously mass-produced through one or more processes. Examples of this include the manufacture of erasers, chemicals or processed food. In process costing it is the process that is costed (unlike job costing where each job is costed separately).
Process Costing consists of the following steps: Physical flow of units; Equivalent Units of Production; ... The problem will provide the information related to beginning work in process inventory costs and units. Step 4: Assign Costs. In this next section, we will combine the equivalent units (from step 2) and the cost per equivalent units ...
Process costing is a method of costing used mainly in manufacturing where units are continuously mass-produced through one or more processes. Examples of this include the manufacture of erasers, chemicals or processed food. In process costing it is the process that is costed (unlike job costing where each job is costed separately).
CHAPTER 21 PROCESS COSTING OVERVIEW Some products are produced in such a manner that individual units are not identifiable throughout the process. Examples include the manufacture of paint, the … - Selection from ACCOUNTING PRINCIPLES: Problem Solving Survival Guide, Volume 2: Chapters 13-26, 10th Edition [Book]
Process Costing is the cost accounting method in which production overhead is equally allocated to each product due to their similarity and mass production. The company assumes that each product requires the same overhead cost. It is hard to separate the overhead cost base on actual consumption. Moreover, raw material needs to pass through ...
Process costing . Process costing is a costing method used when mass production of many identical products takes place, for example, the production of bars of chocolate, cans of soup or tins of paint. It is an example of continuous operation costing. One of the distinguishing features of process costing is that all the products in a process are identical and indistinguishable from each other.
Work in Process Dept. I 20% 50% 2/3 Work in Process Dept. II 4/5 2/4 ¼ Report form production control department shows as follows: Description Department I Department II Units put in the process 8,000 Units completed and transfer 6,500 4,500 Units still in process 1,500 2,000
Dear Students, To follow all the lectures of "Cost Accounting" subject, please follow the given link:https://www.youtube.com/watch?v=ESqO8sFgQa0&list=PLLhSIF...
In Process X, 5% of the units entering the process. In Process Y, 10% of the units entering the process. The scrap value of the wastages in process X is Rs.8 per 100 units and in process Y is Rs.10 per 100 units. Process Costing Problem 2: ABC Ltd. is producing the product "P" required to be processed in three continuous processes.
Problems Solutions. Simple Process Accounts. Simple Process Accounts involving Overhead Distribution. Normal Loss - Wastage, Scrap - Cost Sheet. Part Production sold - Income Statement, Cost Sheet. Reverse Calculations - Finding input, Wastage Percentage. Normal Abnormal Losses - Process Accounts.
Process costing refers to a cost accounting method that is used for assigning production costs to mass-produced goods. For instance, large manufacturing companies that mass-produce inventory might use process costing to calculate the total amount of direct and indirect costs associated with products that are completed and left in-process at the ...
Whatever the complications, the task that sits at the heart of process costing is always to allocate the costs collected on the debit side of the account to possible output on the credit side. Identify the losses and output units. Calculate the cost of good output, losses and WIP. Complete the process account.
PROCESS COSTING PROBLEM 1. Dover Corporation's production cycle starts in the Mixing Department. The following information is available for April: Units Work in process, April 1 (50% complete) 40, Started in April 240, Work in process, April 30 (60% complete) 25, Materials are added at the beginning of the process in the Mixing Department.
7.1: Introduction to Process Costing; 7.2: Job Order Costing vs Process Costing; 7.3: Flow of Costs (Process Costing) 7.4: Equivalent Unit Calculations; 7.5: Cost Reconciliation; 7.6: Direct and Step-Down Methods; 7.7: Introduction to Cost Accounting Methods; 7.8: Activity-Based Costing; 7.9: Traditional Costing vs. ABC; 7.10: Putting It ...
Process Costing (Problem Solving 2) Beginning WIP - 0. Units started and completed - 1,500. Ending WIP - 500. EUP materials - 2,000. Click the card to flip 👆. ABC Company uses the FIFO method in its process costing system. The following data are for the first processing department for a recent month: Beginning inventory (30% complete as to ...