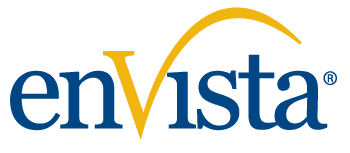
- 877-684-7700
- Inventory Optimization
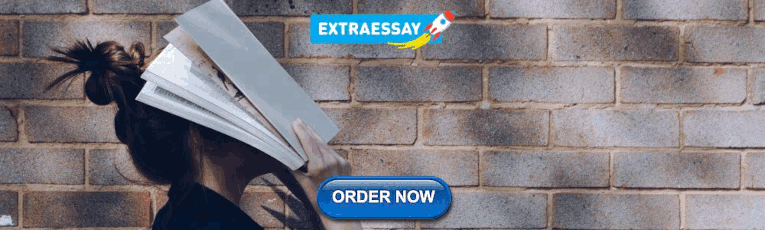
Supply Chain Systems
Retail systems, it managed services, microsoft application management, design build services, material handling, robotics integration, warehouse control systems, slam line automation.
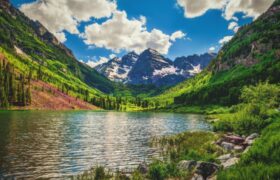
Big Rock Sports Implements New WMS for Greater Efficiency and Scalability
Big Rock Sports leverages enVista’s WMS implementation services to improve inventory and picking accuracy and lower labor costs.
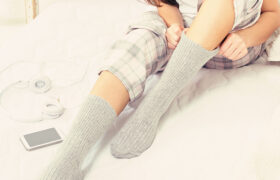
Leading Sock and Legwear Designer and Manufacturer Improves S&OP Strategy Program
Sock and legwear manufacturer reduces inventory costs and significantly improves service levels with enVista’s S&OP strategy program.
Distribution
Manufacturing
Third-Party Logistics
Private Equity
Food & Beverage
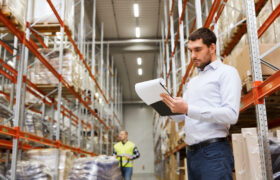
Hidden Treasures of Advanced Warehousing
Make the most of Microsoft Dynamics 365’s Advanced Warehousing module and gain insight into the hidden treasures to unlock value.
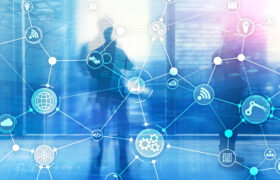
What Is Supply Chain Execution and How Can Supply Chain Execution Software Help Your Company?
Learn about supply chain execution and how supply chain execution software can help your company streamline processes and lower costs.
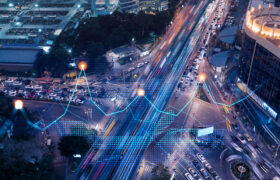
Get Rates Right: How You Need to Think About Strategic and Tactical Sourcing
Gain insight into strategic vs. tactical sourcing and how placing transportation procurement into these categories can reduce the complexity.
- Company Overview
Associate Experience
Client Experience
Community Impact
- Honors & Awards
Home > 4 Warehouse Management System Case Studies
4 Warehouse Management System Case Studies
- July 23, 2020
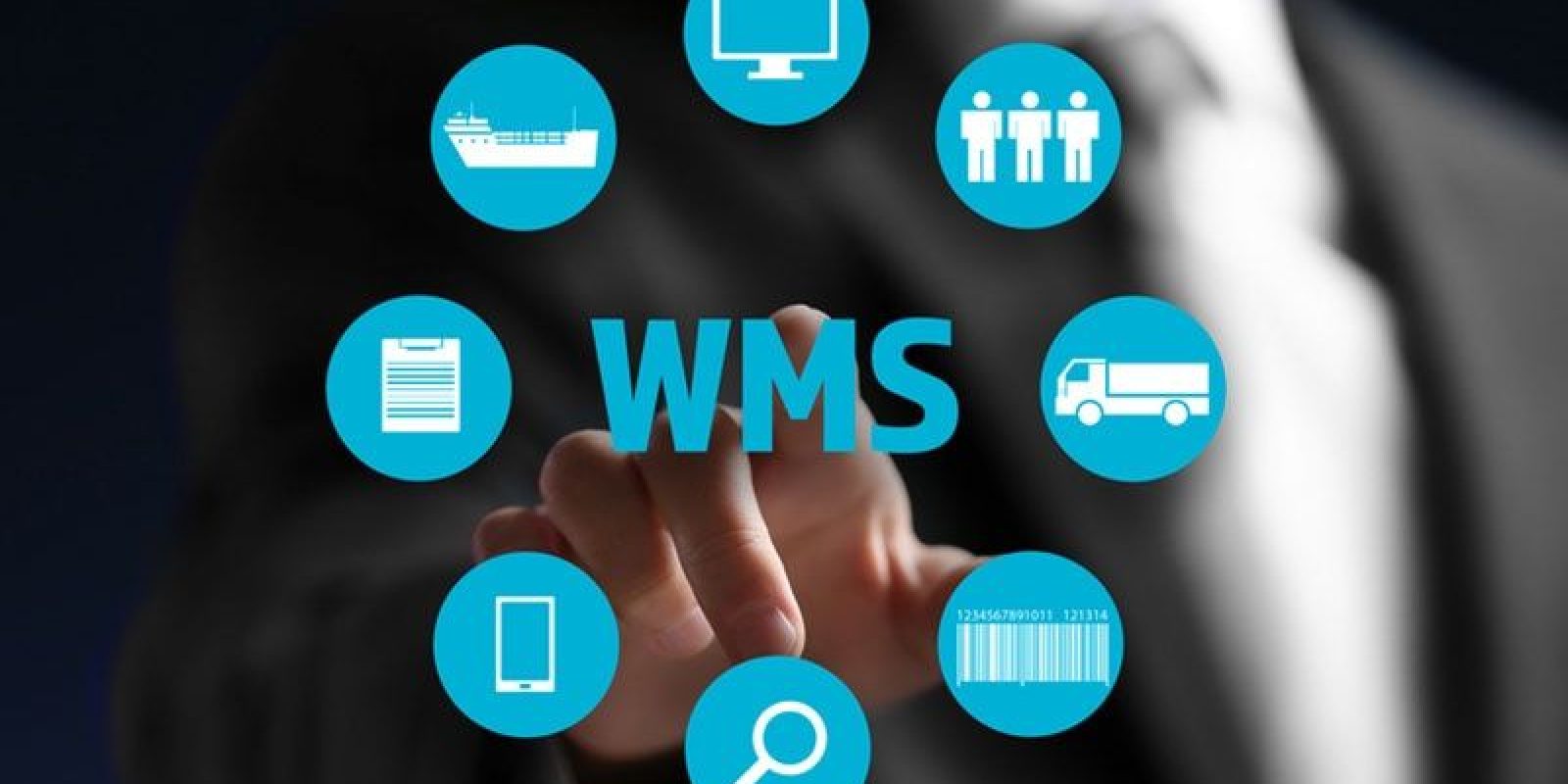
Successful WMS Implementation Case Studies
Warehouse Management Systems (WMS) represent a major investment in your supply chain and operational efficiency. While it can be difficult to gauge your estimated time to value, these four cases featuring enVista clients provide a warehouse management system business case and showcase outcomes after successful WMS implementations.
In this post, we’ll cover four examples of WMS implementations and how they helped companies to optimize warehouse operations :
- Nature’s Best
- Performance Bike
- Bradshaw International
- Men’s Wearhouse
Four WMS Implementation Examples
1. nature’s best.
*Note: Since project completion, Nature’s Best has been acquired by KeHE.*
Leading the market of health and natural foods distribution, Nature’s Best serves Certified Organic products in over twelve states. Nature’s Best was experiencing high labor costs based on time and manpower to transport temperature-controlled food products between four buildings on its DC campus. The company’s zones were organized to suit either small or large clients – a key competitive differentiator. Because of the facility layout, the overall distribution process was inefficient; each product was touched 18 times on its way to the customer. Nature’s Best technology, distribution processes and buildings also needed updating to keep pace with growth projections.
enVista was called upon to address and resolve the challenges Nature’s Best was facing and did so using its consult, implement and operate (CIO) methodology to create a customized solution.
Phase One: Consult
A supply chain strategy that met Nature’s Best’s business goals was developed. enVista conducted a material flow analysis and redesigned the internal flow processes to increase efficiencies. As a result, a global WMS was selected that addressed all of Nature’s Best’s concerns and determined construction needs for the distribution center (DC). Operations would be consolidated to one DC, and enVista designed the new facility with various temperature-controlled zones.
Phase Two: Implement
As Nature’s Best began construction, enVista supervised the integration and implemented a Manhattan Associates WMS including interface design, configuration, training, facility preparation and labor standards among other features. Nature’s Best shifted from a mechanized to non-mechanized system and from paper to radio-frequency (RF) devices with voice-based technology. enVista managed the move of $25 million of inventory and trained the company team on new system processes.
Phase Three: Operate
During go-live, enVista ensured a seamless transition into Nature’s Best new facility, systems and processes. Throughout the Consult, Implement, and Operate phases, sales were steady – even growing – and upon completion, the project was delivered on time and within budget. The chosen system required few modifications for Nature’s Best’s business model, which would lower costs and allow for easier upgrades in the future.
The new system reduced labor costs by over 30 percent and more than doubled productivity. Ninety-seven percent of full-time employees were retained, and temporary and non-value-added positions were eliminated. Nature’s Best went consultant-free only four weeks after go-live.
Download Nature’s Best Case Study
Example 2: Performance Bike
Performance Bike is a privately-held, specialty retailer focused on bicycles and accessories. The company had expanded to over 110 retail locations since its founding in 1982. Performance Bike had a DC in Chapel Hill, NC, with over 60 associates and partners with a 3PL in Long Beach, CA.
Due to compliance issues with the U.S. Postal Service barcodes, Performance Bike had to make system changes to its Manhattan PkMS WMS. The company’s experience with Manhattan Associates gave it a flexible approach when considering an upgrade. enVista’s enABLE methodology was used for the upgrade, and many of the roles typically filled by software or consulting companies were completed by Performance Bike.
Because of the prior experience and flexibility of Performance Bike and enVista, the WMS implementation was under budget and on time. Team members from both enVista and Performance Bike worked together to complete and implement the WMS. The vice president of warehouse operations for Performance Bike noted enVista’s customer-centric approach and flexibility.
The WMS upgrade was implemented in less than 6 months. There were very minor changes to the user experience, so trainings were seamless and increased productivity. Performance Bike experienced a pick per hour increase of 50 to 100 units per hour, exceeding the company’s executives’ expectations.
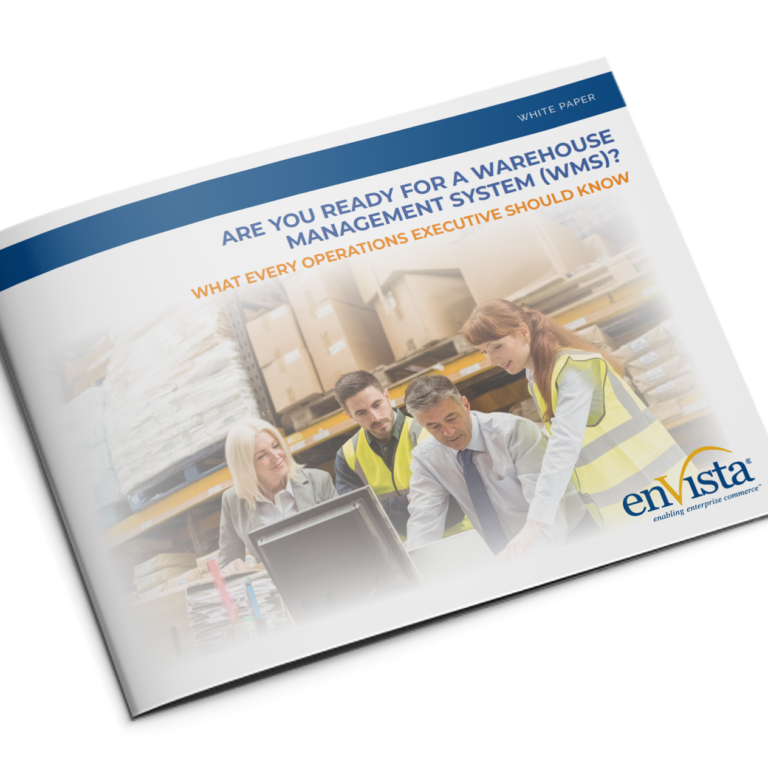
Are you Ready for a Warehouse Management System?
Discover what every operations executive should know about selecting a WMS to ensure a positive ROI, and improved operations.
Example 3: Bradshaw International
Bradshaw International’s Good Cook™ brand is sold in over 30,000 U.S. retail stores. Bradshaw is a leading marketer of kitchenware products and launched Good Cook to incorporate quality, value and service into every product. This philosophy has allowed Good Cook to achieve the best position for kitchen tools and gadgets with 43 percent of the market.
Bradshaw was asked to participate in Wal-Mart’s direct store delivery consolidation (DSDC) program as Good Cook is distributed in the stores. The program was designed to allow shippers to directly replenish Wal-Mart stores in less-than-case-pack quantities. To do so, Bradshaw had to make changes to several parts of its current distribution systems.
Changes to electric data interchange (EDI), order management, and a pick/pack operation integrated with a new WMS would be required to handle the new variable volumes. enVista was asked to help design and integrate the DSDC program. To meet Walmart’s DSDC objectives, the team had to design and build a new pick/pack module, select the technology to be used by the picking team, and integrate it with the WMS. The order management software , EDI software and billing system had to be modified to accommodate the structures required by Walmart’s DSDC program.
The team profiled SKU movements, identified pick and storage mediums to model replenishment rates, and formulated labor plans and proper work flows. Bradshaw IT and enVista worked together to make configuration changes to the RedPrairie WMS and integrate it with the Pick from Light System and EDI software. The joint team also specified data maps from order capture to order management to WMS through EDI transmissions to move the infrastructure to industry standards.
With enVista’s help, Bradshaw successfully integrated the DSDC program into operations. Shipping volumes increased beyond expectations, but the new WMS has allowed Bradshaw to keep up with demand. The program was implemented with almost no customer disruption.
Example 4: Men’s Wearhouse
Founded in 1973, Men’s Wearhouse is one of the country’s largest specialty retailers of men’s apparel with over 700 stores. The stores carry a full selection of high-end men’s clothing and accessories.
Men’s Warehouse’s main DC was a 1.1-million square foot facility in Houston, Texas. It is the core retail distribution center for Men’s Warehouse retail stores, as well as 60 percent of merchandise from K&G Retail stores, acquired in 1999. A significant percentage of its garment-on-hanger merchandise is shipped by dedicated fleet to regional hubs across the country. enVista’s main objective was to consolidate retail and e-commerce systems to run all operations on a single platform and a central material handling equipment (MHE) integration point.
enVista acted as the program management role for supply chain execution and MHE software functions for all facilities. The implementation of the new systems platform occurred in two distinct phases.
The first phase focused on using the new systems platform to more efficiently meet Men’s Wearhouse’s growing e-commerce business needs. A new WMS and distributed order management system were implemented and integrated to an e-commerce web platform. These systems allowed strategic decision making regarding e-commerce order fulfillment and room for growth, along with the accuracy and flexibility necessary for seamless execution and delivery.
Phase two focused on implementing the new WMS and a consolidated warehouse control system (WCS) in Men’s Wearhouse’s Retail Distribution Operation. The WMS replaced the retailer’s legacy system, and the WCS consolidated the management of several operations into one system. Men’s Wearhouse now has the ability to dynamically change product flow, unit allocation, and achieve more effective utilization of Case Level ASN receiving with the new WMS. The system’s ability to recognize and execute on cross-docking opportunities created improved throughput and lower overall processing costs.
With the implementation of a common WMS and standardized processes, Men’s Wearhouse was able to share recourses across operations and respond to seasonal increases in workload more effectively. The implementation of WMS and WCS gives the company the ability to consolidate its distinct Men’s Wearhouse and K&G distribution operations to reduce costs and increase overall processing efficiency.
Download Men’s Wearhouse Case Study
Conclusion: enVista’s WMS Expertise
Getting your WMS right and making sure it’s integrated properly across your supply chain technology stack is critical to realizing quick ROI and improved operational efficiencies.
enVista has completed hundreds of WMS implementation projects in its nearly two decades of experience, and our vendor agnostic approach to consulting and implementation ensures you get objective help for your most critical projects. We’re passionate about supply chains and delivering solutions that are the right fit for our clients and would love to help you optimize your supply chain.
If you have a WMS project on the horizon or want to learn more about how we can help you, let’s have a conversation .
About the Author
enVista Thought Leadership
Related posts.
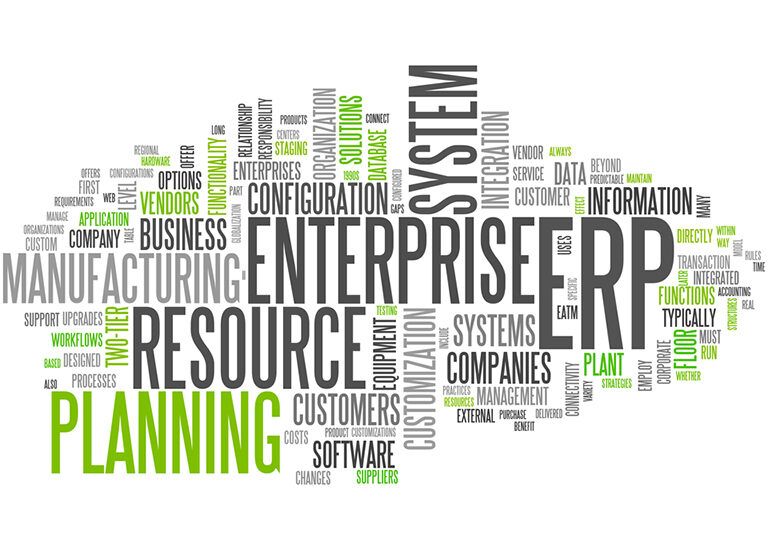
Why Supply Chain Management Features are Crucial for an ERP System
Bridging the gap between an ERP system and supply chain management allows businesses to maximize IT dollars and resources.
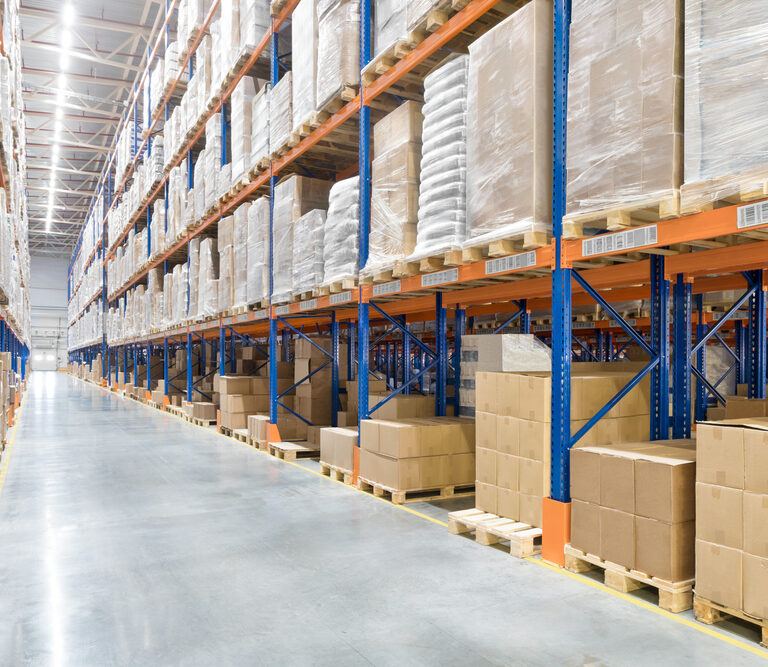
Increase ROI Through Successful Warehouse Slotting
A well-thought-out slotting strategy also enables businesses to minimize wasted space and maximize storage capacity within the warehouse. Increase ROI using the right tools, strategy and management plan with successful warehouse slotting.
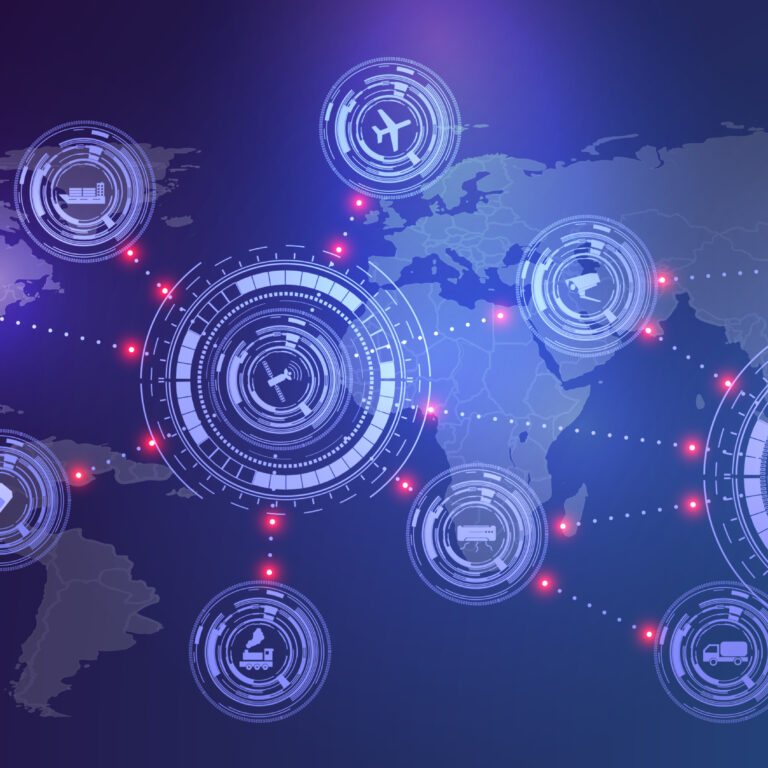
The Cost-Saving Power of Artificial Intelligence in Supply Chains
There are endless tactical opportunities for leveraging AI in your supply chain operations to increase efficiency, profitability and customer service levels. Beginning your AI journey within the areas of the supply chain that are costing your organization the most – network design, inventory and warehousing – will multiply your cost savings.
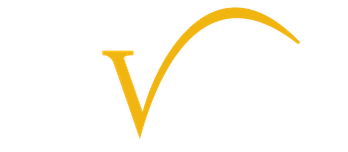
Subscribe to Our Insights
Why envista.
- Diversity, Equity, & Inclusion
About enVista
- Cookie Policy
- Privacy Policy
- Privacy Notice for CA Residents
- Terms of Use
We support your right to privacy and transparency about how we collect and use your personal data.
Privacy overview, contact envista.
Improving warehouse operations—digitally
Warehouse operations are increasing in complexity with time. The growth of e-commerce has led to a proliferation of SKUs, and there’s an ever-growing need to delight customers by offering super-fast fulfillment. Technology is a factor as well: as new automation systems come onto the market, operations leaders must face the challenge of keeping pace and understanding which technologies apply and what kind of impact they can generate.
Worldwide, companies spend an estimated $350 billion a year on warehousing, and that number grows each year as pick sizes shrink and costs balloon, raising pressure not just on margins but also on service levels.
The need to improve both sides of the equation may be obvious, but the question is how. Trial-and-error is not an option: companies cannot simply shut down a warehouse so they can tinker with new layouts and workflows to see what works best.
But the better news is that they don’t have to. A few companies are already able to design and visualize their warehouse operations virtually via “digital twin” simulations. The simulations allow companies to create virtual models of their existing facilities, and then test different scenarios—no shutdowns required.
This digital warehouse-design approach lets companies experiment with different floor plans, workflows, and other variables to assess the overall impact virtually. Operations leaders can see the impact of changes in a wide range of factors, including the SKU mix, order and shipment profiles, seasonal demand spikes, productivity initiatives, automation options, and a host of other issues that impact warehouse performance. This level of detail allows warehouse designs to be optimized in advance, before anyone starts moving physical assets.
The process typically takes six to ten weeks. The revamped warehouse designs that result can help companies improve efficiency by 20 to 25 percent, before spending the money to test or pilot the changes (exhibit).
Would you like to learn more about our Operations Practice ?
The power of digital simulations.
Digital warehouse design has a wide range of applications, from productivity initiatives at existing facilities to mergers, warehouse consolidations, and new warehouse construction. Across all applications, however, the benefits are reasonably consistent: sizable savings in operating expenses from productivity improvement, as well as in capital expenses from optimizing the deployment of material-handling equipment, storage assets, and targeted, right-sized automation systems.
The approach removes bottlenecks to improve efficiency and effectiveness, and enables optimal slotting and product flows to meet service requirements at the lowest possible cost. Most important, digital warehouse design identifies the full potential of a given facility, rather than forcing companies to settle for incremental improvements to the as-is layout.
Critically, the process also enables companies to gauge the potential impact of mechanization and automation options across the entire spectrum of vendors and products on the market. These technologies can be powerful tools to reduce space and increase efficiency. But in some cases, incorrect or inappropriate automation can actually create more problems than it solves. Digital modeling lets companies see what is possible from a range of technologies and applications, before they make any investment decisions.
Transcending traditional improvements
Of course, most companies know they need to improve their warehouse operations. But they struggle to identify and make the needed upgrades, due to limited data and internal expertise. Quite simply, many companies lack the full set of capabilities needed to assess various warehouse improvement options and create a business case that incorporates capex investments and running costs.
Some rely on third-party logistics providers, but even those vendors often lack the breadth of expertise to see what is truly possible with alternative warehouse designs and operations. A related problem is that most traditional methods to design or revamp warehouses use computer-aided design software (CAD)—which is resource-heavy and time-consuming, and doesn’t allow companies to calculate the impact of new changes or anticipate second-order effects. Digital warehouse design, by contrast, offers a low-risk way to visualize and optimize layouts, allowing companies to rapidly identify real, feasible solutions that deliver quick impact.
For example, a North American manufacturer decided to consolidate several regional manufacturing and warehouse locations into a single campus, with separate buildings dedicated to manufacturing and warehousing. However, it faced several challenges, including capital constraints, insufficient warehouse space, and a need to move fast.
Instead of relying on traditional tools, the company used a digital warehouse-design approach to simulate various options across warehousing, kitting (assembly of related items into a single “kit” for shipment), and value-added operations. The digital tools allowed the company to develop detailed OPEX and CAPEX estimates for both manual and automated solutions, making it far easier to evaluate various business cases. In all, the company reduced planned capex by approximately 10 percent and operating expenses by more than 30 percent.
Digital warehouse design can also help companies rethink existing facilities. For example, another company deployed digital warehouse-design and simulation tools to optimize and revamp its operations in a warehouse currently in operation. It built models to test various layouts, material-handling-flow scenarios, picking methods, and targeted automation solutions.
Starting from an optimized slotting design, the digital twin analyzed historical orders to estimate the exact labor and equipment requirements by day of the week and by hour of the day. With accurate labor-staffing models, the company was able to choose the most optimal, modular design to implement during the transition. In addition, the company could define precise, engineered standards for each operation of the warehouse, and it could monitor daily labor and equipment performance once the new system was in place. This enabled the company to reduce annual operating expenses by 18 percent.
Similarly, one business had a central regional warehouse in Eastern Europe, with annual costs of several million dollars. By constructing a digital twin, the company analyzed the potential improvements from a proposed layout change (specifically, a picking zone that enabled one-step picking). Looking at both high-season and low-season volume, the company determined that it could reduce input costs by more than 25 percent.

Supply chain risk management is back
Foundational capabilities.
As with most technology, digital warehouse design is not a turnkey solution. To capture its full potential, companies must understand their strategy not only for today and tomorrow, but also well into the future—in terms of product portfolio, customer-order profiles, and other factors. Leadership teams must assess the implications of design changes on the supply-chain network as well. And success requires new capabilities in warehouse design—typically engineers who understand the range of variations and permutations for a space. Most organizations do not yet have internal people ready for these roles, and thus need to source that expertise externally.
As a practical matter, the simulation process must involve operations and warehouse managers—those with the deep day-to-day knowledge and real-world insights that can only come from direct experience. Because these experts will be tasked with implementing any changes to the warehouse after the simulation ends, their buy-in will be essential. The more they contribute during the early stages of the process, the more willing they are likely to be to forego old habits and work in new ways.
Last, companies need to plan for repeated changes over time. Optimizing warehouse performance is a process without a finish line—it must happen again and again, as market forces, technology, and consumer preferences continue to evolve. In fact, digital warehouse-simulation tools could become a new way of setting performance expectations, with the tools embedded as part of the day-to-day management of each distribution center. Estimating daily performance targets based on daily volume, mix, and staffing can help warehouse managers manage the shift’s performance more precisely than any other traditional, static approach to setting goals.
Companies face a growing need to improve their warehouse operations. Digital warehouse design is one clear means to help them do so. The process may be virtual, but the results generate a real impact on performance, providing an edge in an ever-more-complex warehousing landscape.
Stay current on your favorite topics
Felipe Bustamante is a consultant in McKinsey’s Miami office, Ashutosh Dekhne is a partner in the Dallas office, Jörn Herrmann is a senior expert in the Zürich office, and Vedang Singh is a consultant in the New Jersey office.
The authors wish to thank Aditi Brodie for her contribution to this article.
Explore a career with us
Related articles.

Digital supply-chain transformation with a human face
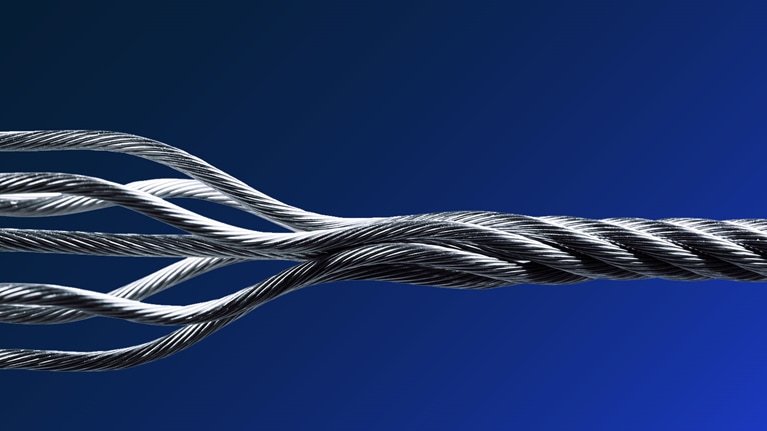
Industry’s fast-mover advantage: Enterprise value from digital factories
We and our partners use cookies to give you the best online experience, including to personalize content, advertising, and web analytics. You can reject cookies by changing your browser settings. To learn more about the cookies we use see our Cookie Policy .
- Supply Chains
- Manufacturing
- Transportation
- Warehouse Operations
- Rail Logistics
- Ports & Terminals
- Road Traffic
- Passenger Terminals
- Business Processes
- Asset Management
- Social Processes
- Why simulation
- AnyLogic Timeline
- Artificial Intelligence
- Digital Twin
- Enterprise Simulation
- Get started
- White papers
Case studies
- Training and events
- AnyLogic Conference
- Documentation
- For academia
- Academic articles
- Clients & Testimonials
- --> Supply Chains
- --> Manufacturing
- --> Transportation
- --> Warehouse Operations
- --> Rail Logistics
- --> Oil & Gas
- --> Ports & Terminals
- --> Road Traffic
- --> Passenger Terminals
- --> Healthcare
- --> Business Processes
- --> Asset Management
- --> Marketing
- --> Social Processes
- --> Defense
Walmart’s Alphabot: Designing Material Handling System with Simulation
Walmart, the world’s largest retailer by revenue, was looking for an automation technology that would help complete orders faster and at a lower cost in the company’s fast-growing online grocery business. They wanted to evaluate Alert Innovation’s Goods-to-Person (GTP) concept, Alphabot (an AGV or robot-based system), which could automate the grocery pickup process by using autonomous mobile carts capable of operating in all three dimensions within a multilevel storage structure.
Optimizing E-Commerce Warehouse Operations
The global e-commerce sector has seen 320% growth in five years, and demand is increasing following the COVID-19 pandemic. To reduce costs and remain competitive, DHL Supply Chain ran a warehouse operations optimization project. The project involved developing a smart and robust warehouse simulation tool for testing wave picking strategies.
Optimizing Warehouse Operations for Pharmaceutical Distribution Company
Cardinal Health, a billion-dollar pharmaceutical distribution and logistics firm, manages multiple products from brand name pharmaceuticals and generic drugs to over the counter drugs, health & beauty items and their own private label. They face a multitude of typical distribution warehouse challenges that are further complicated by the nature of pharmaceutical products. Brian Heath, Director of Advanced Analytics at Cardinal Health, and an experienced user of AnyLogic software, employed agent based modeling to solve various business problems, saving Cardinal Health over $3 Million annually.
Warehouse Simulation for Choosing Optimal Picking Algorithm
Kuehne+Nagel, a leading global provider of logistics solutions, was involved in planning a new warehouse for one of their clients. The warehouse would process 13K order lines or 750 picking cartons per day. The project included the development of the best algorithm for multi-order picking. It was planned that the orders in the warehouse would be served by workers with trolleys (or fangos). Workers with trolleys would pick the goods and put them in cartons by order.
Warehouse Cluster Pick Optimization
How DHL optimized warehouse order picking and improved efficiency. Analysis using simulation-based modeling increased picking speed and reducing order completion times. The tool integrates with warehouse management systems.
Developing a Forecasting Simulation Model for Efficient Warehouse Operations
A warehouse in Thailand was encountering difficulties because of a number of complicated processes involved in their logistics and storage systems. In order to overcome these and achieve more efficient warehouse operations, EPIC InnoLabs was contracted to develop a forecasting simulation model. This model would be used to predict system behavior based on a number of inputs as well as retrieve the expected values of selected KPIs.
Large-Scale Logistics Network Planning and Optimization
For a delivery network processing 15 billion parcels annually, simulation modeling provided significant saving across key metrics in a package easily accessible to all stakeholders. Find out how in this case study and presentation from Pitney Bowes.
Creating a Workforce Optimization Model for a Micro-Fulfillment Center
Micro-fulfillment centers are small, sometimes highly automated facilities that can fulfill online orders for delivery as well as click-and-collect in-store pickups. They use a combination of automated picking technology and manual picking. Dematic wanted to create a workforce optimization model that they would be able to present to retailers. It would help them understand the staffing required to operate their micro-fulfillment centers and how different scenarios could impact their ability to fulfill orders.
Evaluating Introduction of Warehouse Automation Systems
Symbotic is a warehouse automation solutions provider. Its systems are based on mobile robots that can travel freely throughout a dense storage structure, accessing products in all locations and handling them at a very high throughput rate. The company needed a tool to help their customers learn the impact of warehouse reorganization and compare capital investments against expected operational savings before the actual introduction of automation systems.
Cold Store Warehouse Operations Optimization
Phoenix Analytics is a Turkish consulting company and provider of simulation solutions for various industries. They were involved in developing a warehouse optimization project for one of the biggest ice-cream and frozen desserts manufacturers in Europe and Asia.
Get a brochure with industry case studies
Logistics and Supply Chain Case Studies
Review our case studies to see how we’ve helped major corporations turn logistical ideas into a reality., leading beverage distributor, penske logistics helps beverage distributor rapidly establish new warehousing operations.
When this distributor had to expand its operation quickly to counter a competitor, they turned to Penske to deploy a customized solution.
Baby2Baby Donation Transportation
Coordination and planning lead to successful transport of $3 million clothing donation.
Penske Logistics worked with Baby2Baby, a nonprofit that provides basic essentials to impoverished children, and Old Navy to transport $3M of clothing donations.
Luxury Product Manufacturer
Penske logistics reduces inventory shrinkage, improves overall inventory management.
A leading producer of fine luxury products required a partner who could improve their warehouse and distribution operations and reduce the theft.
Poultry Supplier
Transporting food items requires extra care and expertise.
Poultry producers, navigate a complex array of supply and delivery challenges to ensure their food arrives fresh, wholesome, and on-time.
Building Products Manufacturer
Customized fleet technology solution.
A leading building products manufacturer sought to streamline its supply chain operations and expand its fleet while improving visibility through the implementation of fleet management technology.
National Wholesale Distributor
A national wholesale distributor case study.
A national wholesale distributor of heating and air conditioning supplies was struggling to manage its complex supply chain and maintain high levels of customer service, which is a top priority.
Looping Process Ensures Continuous Production
Penske collaborated with Novelis to create a closed-loop recycling network that moves finished aluminum coils and transports scrap for new production.
A Global Manufacturer
Optimizing activities in the distribution center.
Penske worked with this global manufacturer to optimize its inventory routing and mode selection and to improve visibility to its supply chain.
Quick Service Restaurant
Food and beverage in-store delivery and warehousing.
Penske helped this restaurant chain get its supply chain fundamentals in place with the right logistics tools, truck driver training and warehousing solutions.
Tier 1 Automotive Component Supplier
Managing the inbound supply chain.
Penske helped this supplier minimize supply chain disruptions by designing a network that optimized mode selection, routing and analysis.
- Supply Chain Management
- Lead Logistics Provider
- Consulting Services
- Network Design
- Dedicated Contract Carriage
- Shared Dedicated Transportation
- Freight Management
- ClearChain ® Control
- Transportation Services
- Transportation Management Solutions
- Truckload Shipping Services
- Warehousing and Distribution
- Warehouse Design
- Warehouse Operations
- Multi-Client Warehousing
- Freight Brokerage
- Freight Forwarding
- Become a Carrier for Penske
Contact Penske Logistics about our services.
Case Studies
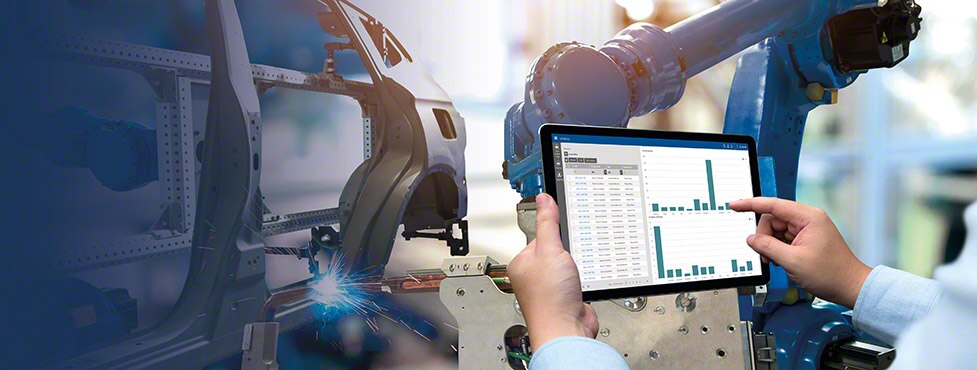
The automotive maker Renault has installed the Easy WMS warehouse management system by Mecalux in its production warehouse in Seville (Spain). The manufacturing centre in this city focuses on the assembly of transmissions and the warehouse supplies manufacturing ...
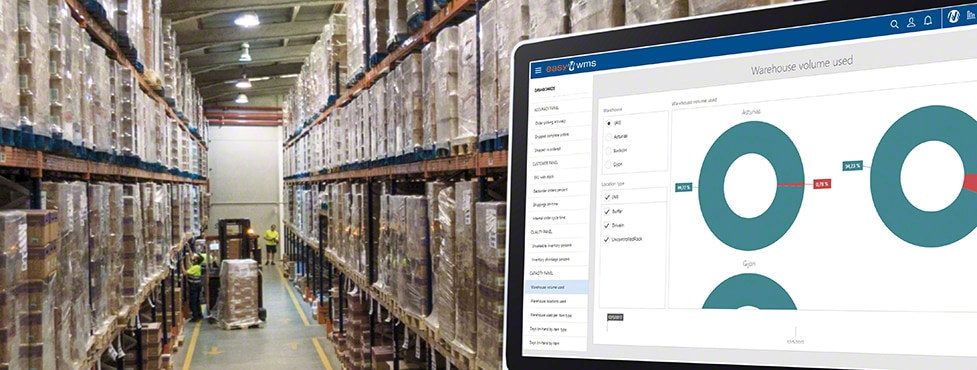
Danone’s distribution centre in Valdemoro (Spain) must cope with a very high-paced daily work rhythm: managing between 500 and 600 SKUs and preparing up to 700 orders. It is an all-in-one omnichannel warehouse, i.e. orders are sent to retailers, wholesalers and c...
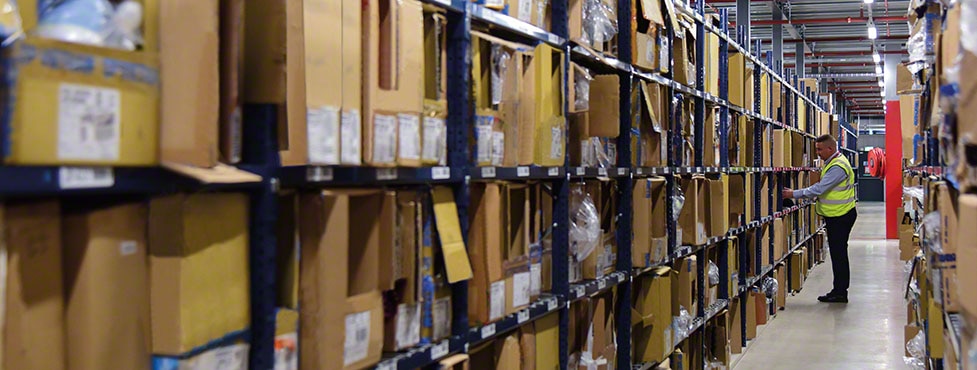
Decathlon has chosen Mecalux’s shelving for picking once again to manage its omnichannel logistics. After equipping its warehouses in France, Germany, Italy and Poland, it is Northampton’s (UK) turn. With 35,000 SKUs, the warehouse preps and ships out 3,000 order...
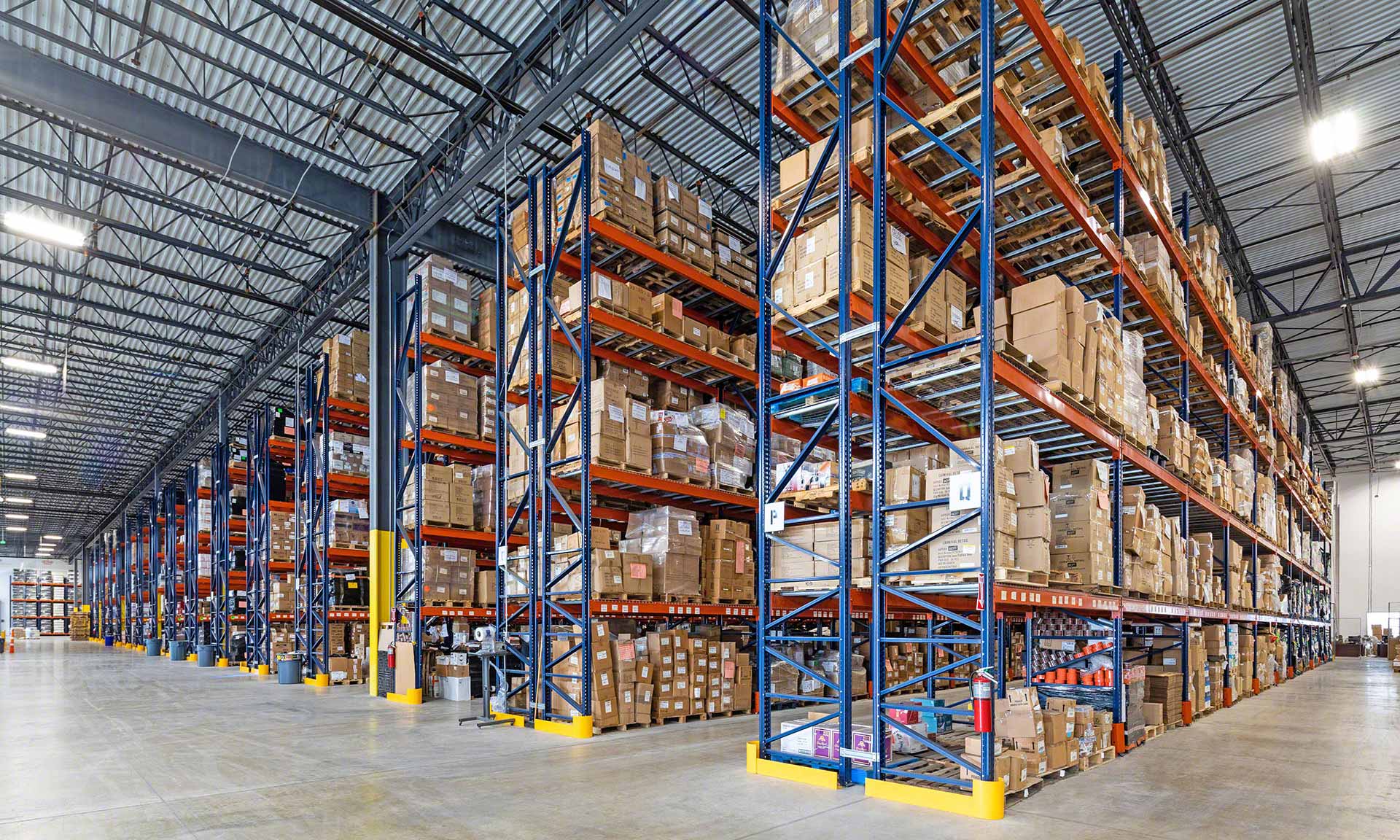
Interlake Mecalux and partner Andersen Material Handling have equipped a 13,935 m 2 warehouse in Miami, Florida, for Dufry, a travel retailer. The project includes adjustable pallet racks and the high-density push-back racking system. Overall, the syste...
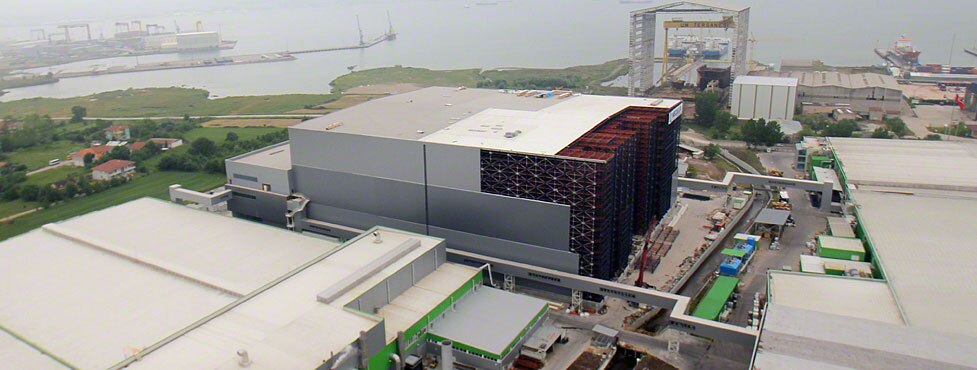
Hayat Kimya
Hayat Kimya is a leading manufacturer in the Eurasian fast-moving consumer goods market, specifically in the sector for hygiene and cleaning products. Founded in 1937, with its headquarters in Turkey, the company currently has 5,200 employees and exports to 101 c...
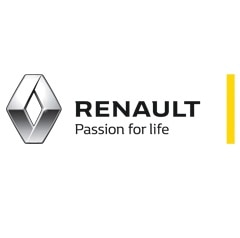
Here you can see some real solutions that Mecalux has developed. Contact us so we can assess the ideal solution for your company.
See our case studies for:
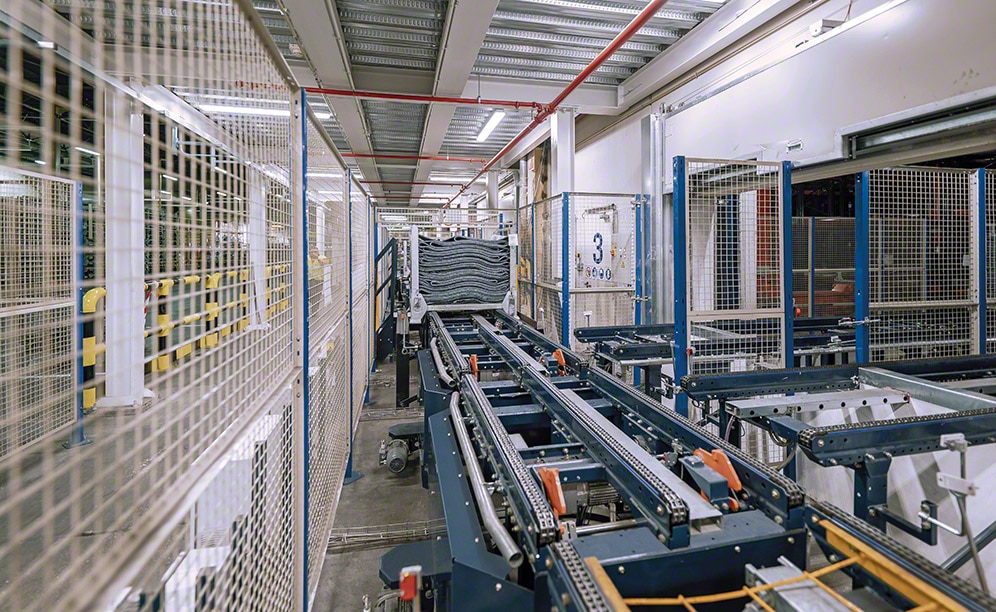
Automated clad-rack warehouse of Michelin integrated with manufacturing
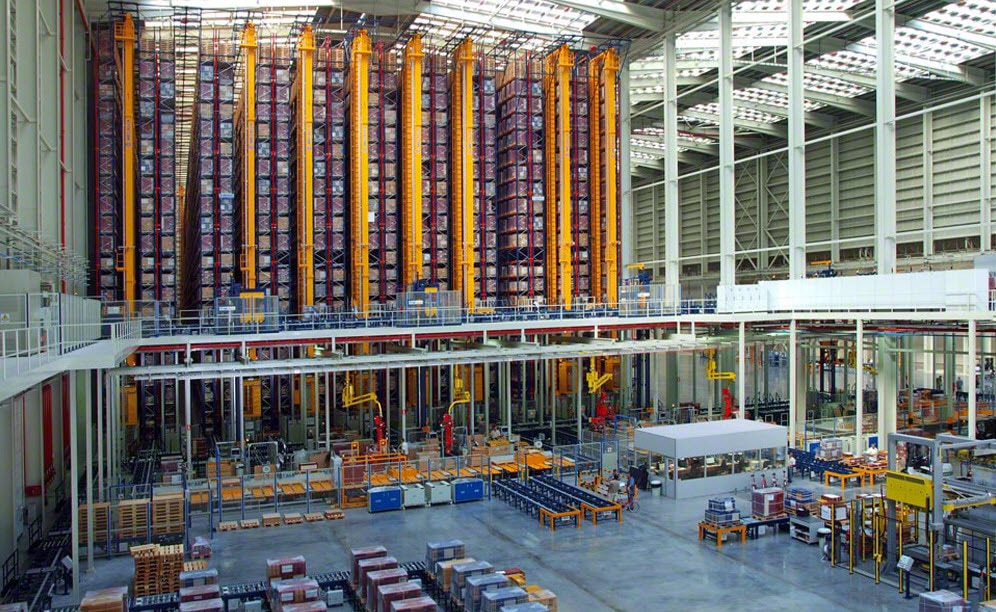
Porcelanosa
Mecalux completes the process of automating the porcelanosa group’s warehouses in castellón, spain.
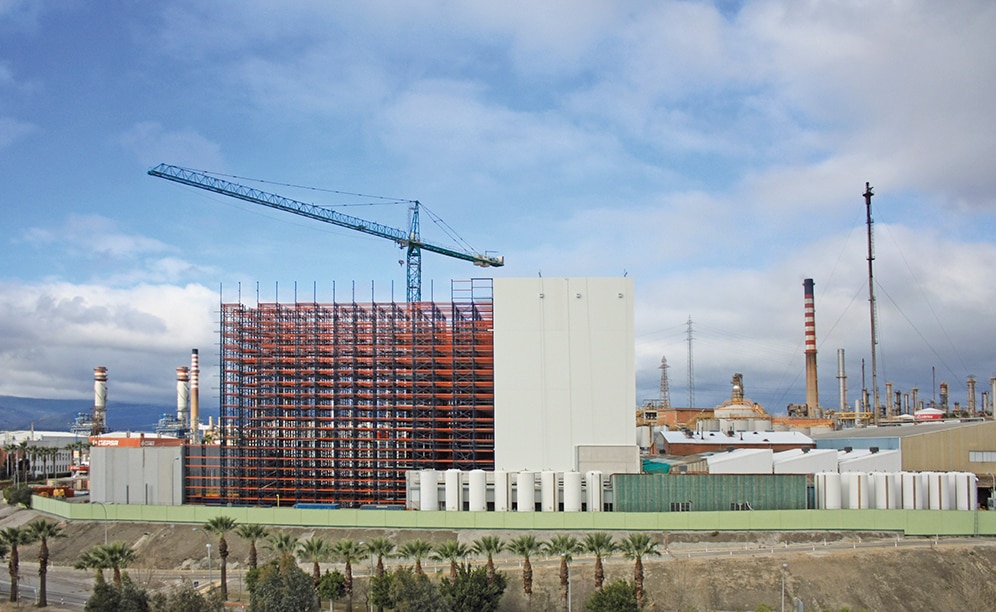
Next-generation automated clad-rack warehouse: a sure bet to streamline of logistics processes at Cepsa
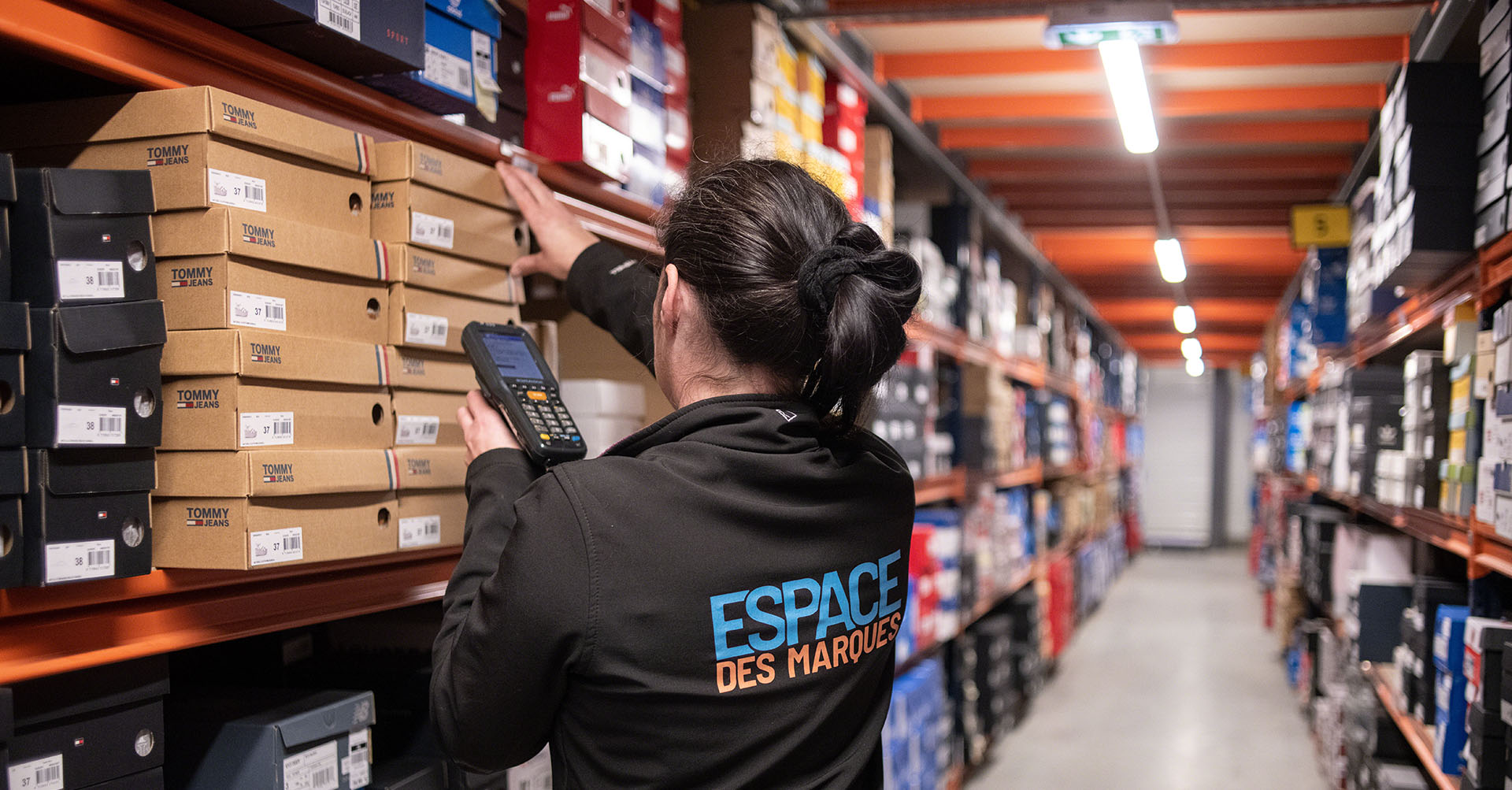
Espace des Marques
Omnichannel warehouses with 70,000 skus.
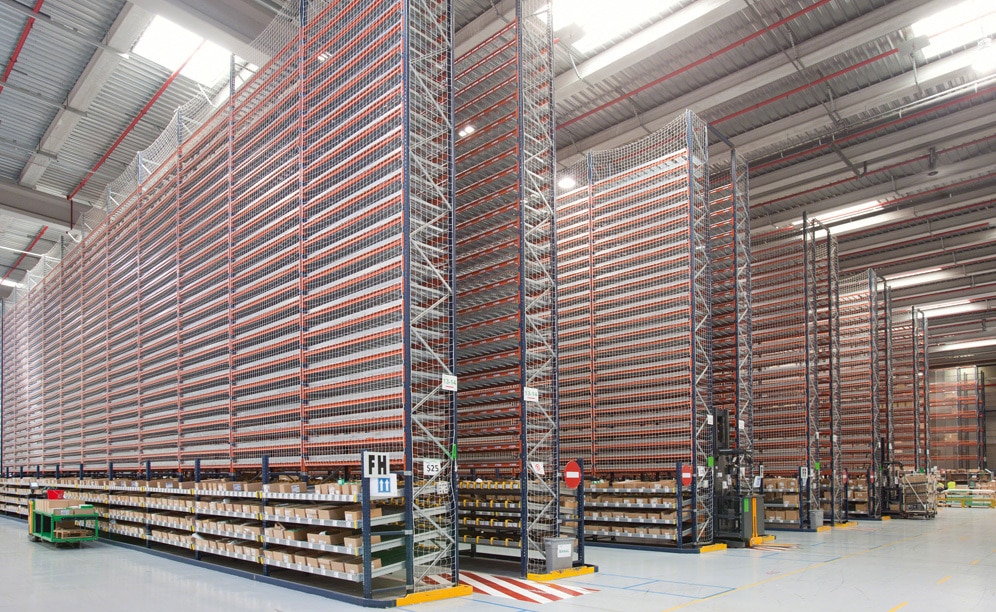
Schneider Electric
How to achieve the ideal balance between speedy picking and storage capacity.
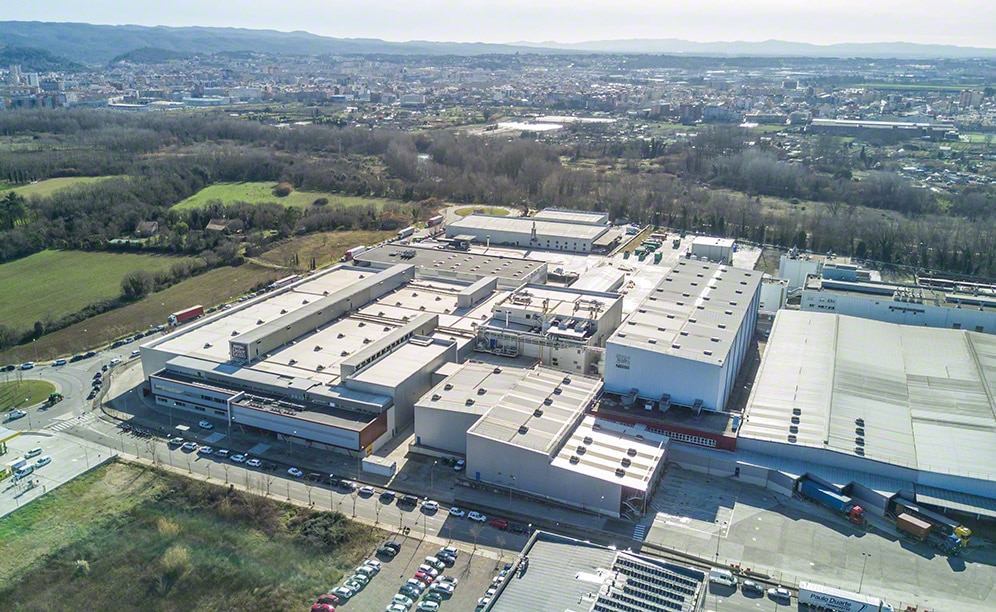
Efficient conveyors improve storage at Nestlé in Girona
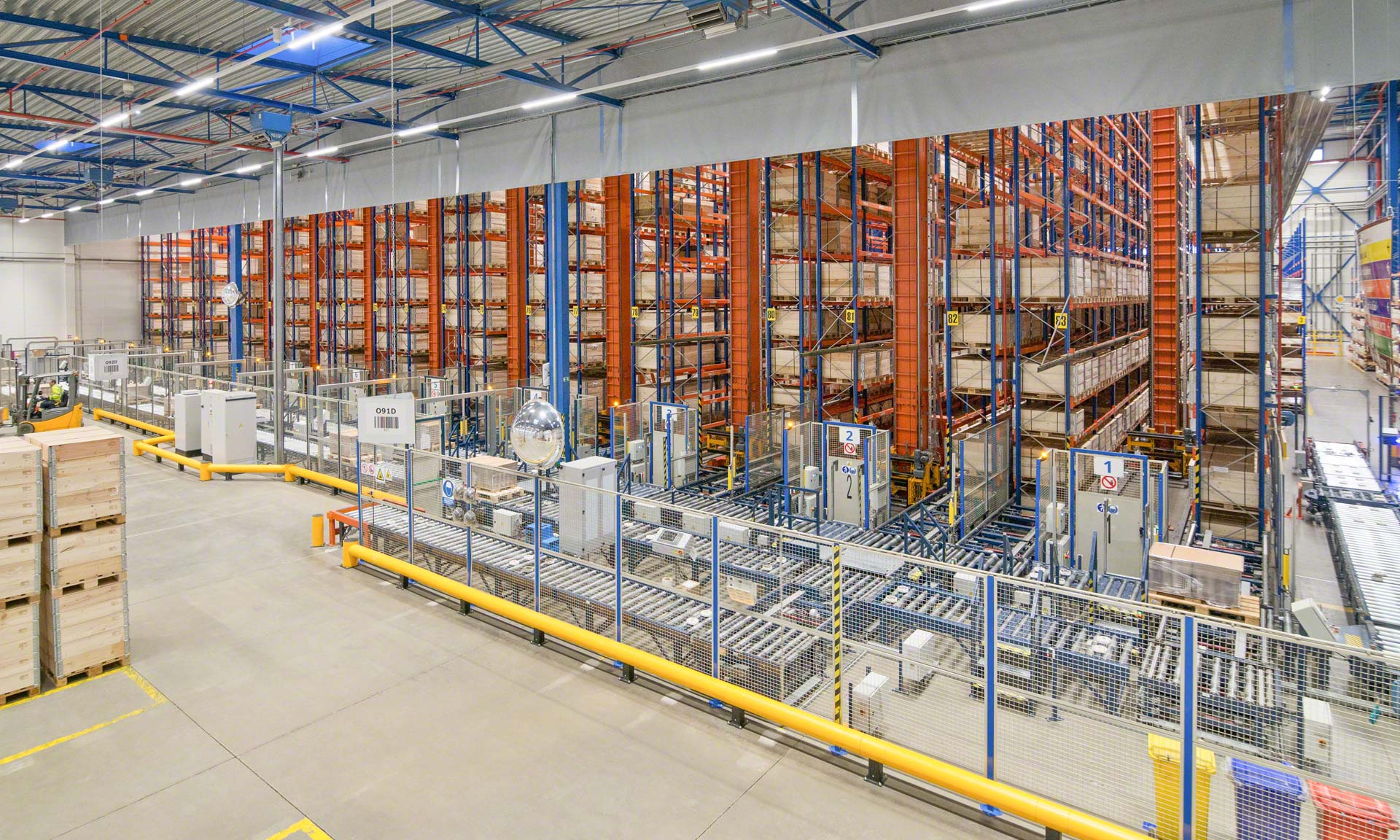
IKEA Components
Ikea components automates its warehouse in malacky without disrupting operations.
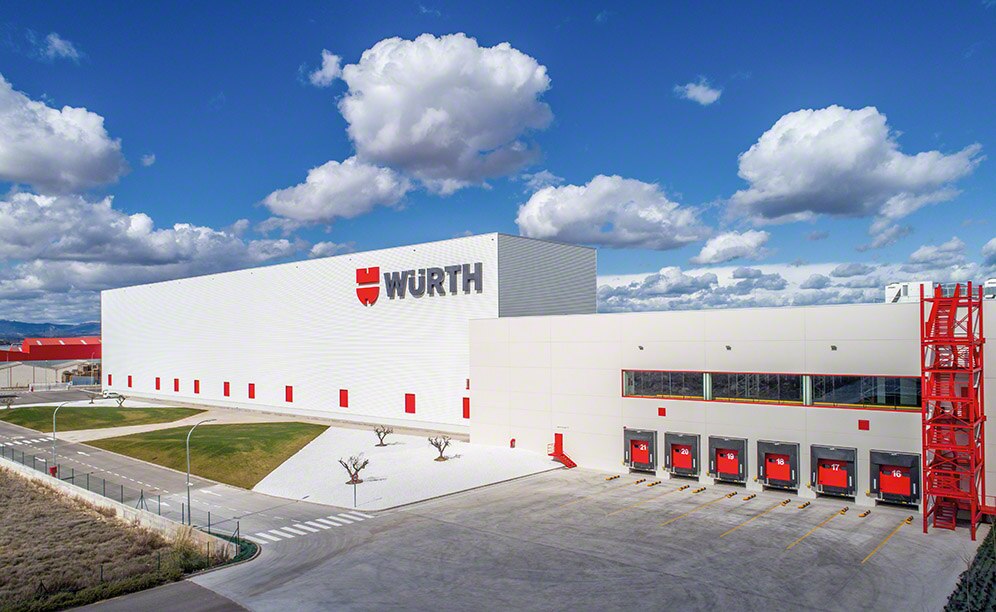
A 100% automated, turnkey warehouse for Würth in La Rioja
Easy WMS of Mecalux runs the warehouse of the car maker Renault
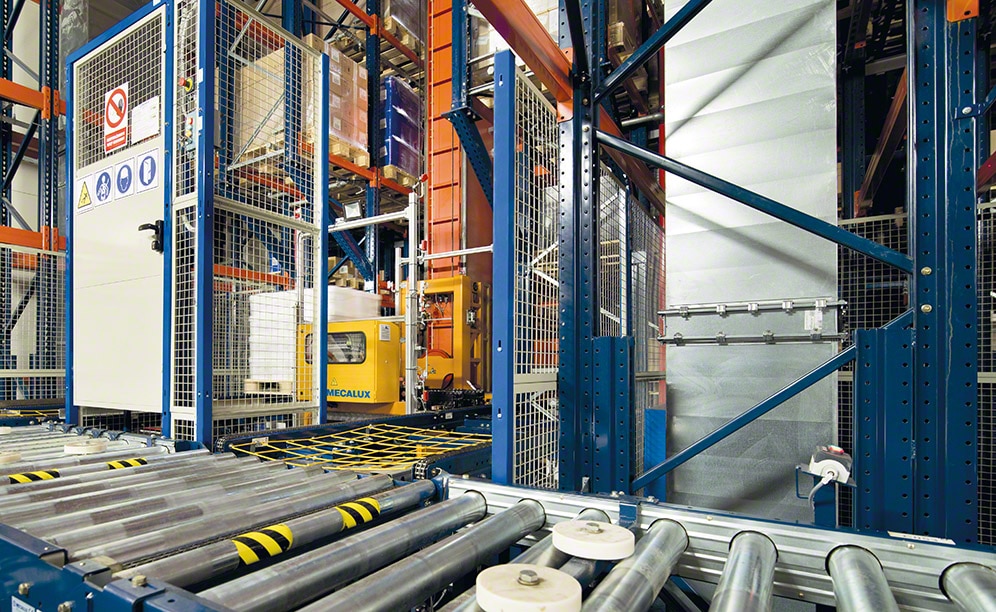
Novartis automates its supply chain in Poland
Coca-Cola Refrescos Bandeirantes
Warehouse with coca-cola soft drinks of refrescos bandeirantes in brazil.
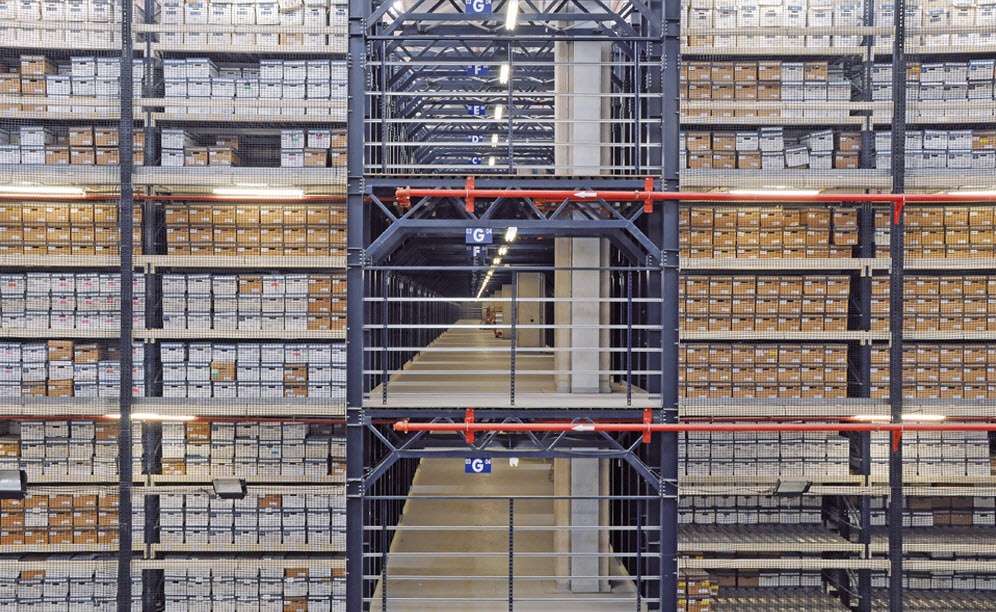
Iron Mountain
Earthquake-proof racking: warehouse with mecalux conventional racking on the pacific rim.
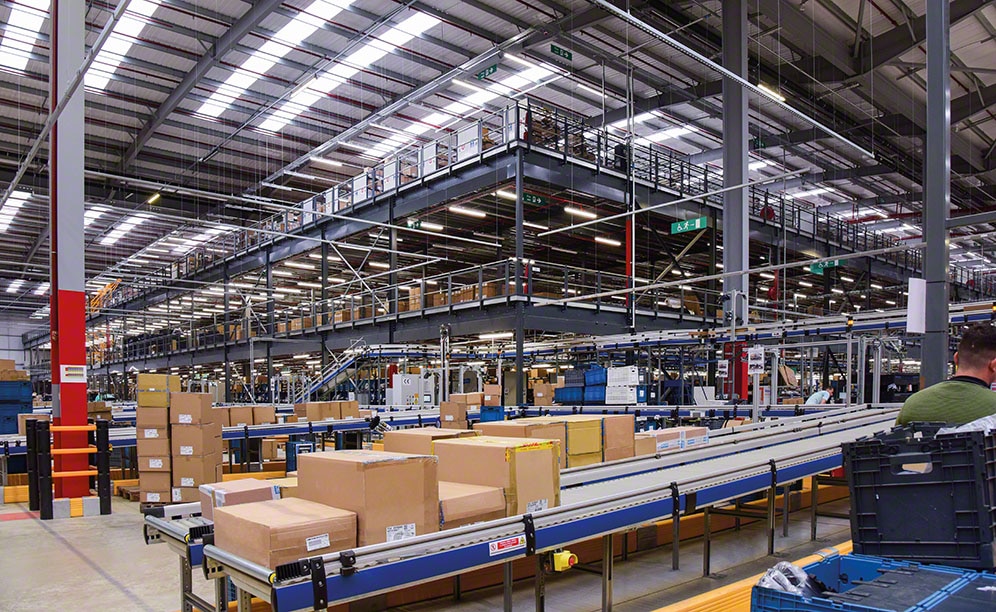
Decathlon has opened a new omnichannel warehouse in Northampton (United Kingdom)
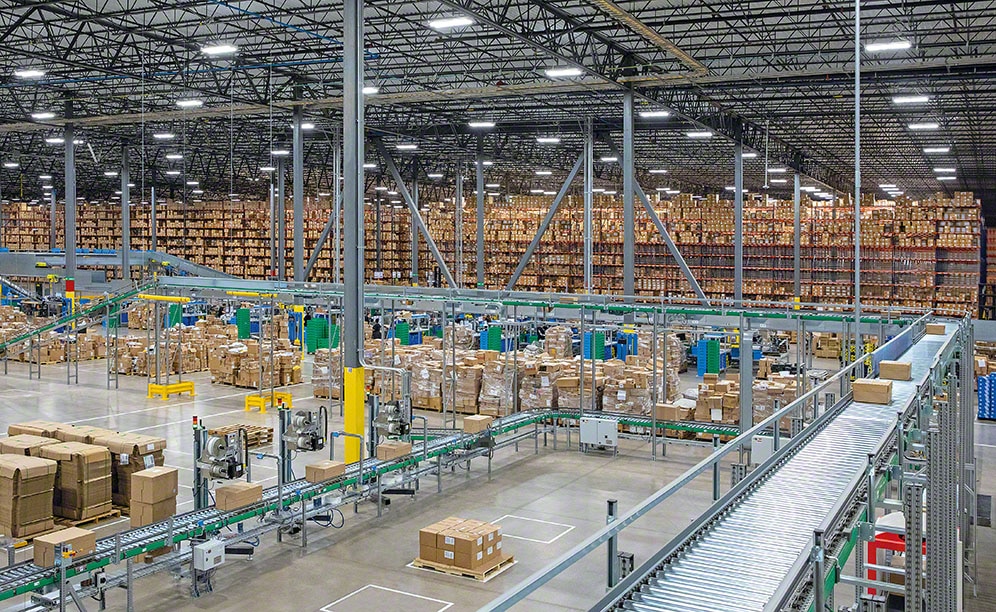
The Adidas sportswear and footwear store in Pennsylvania, USA
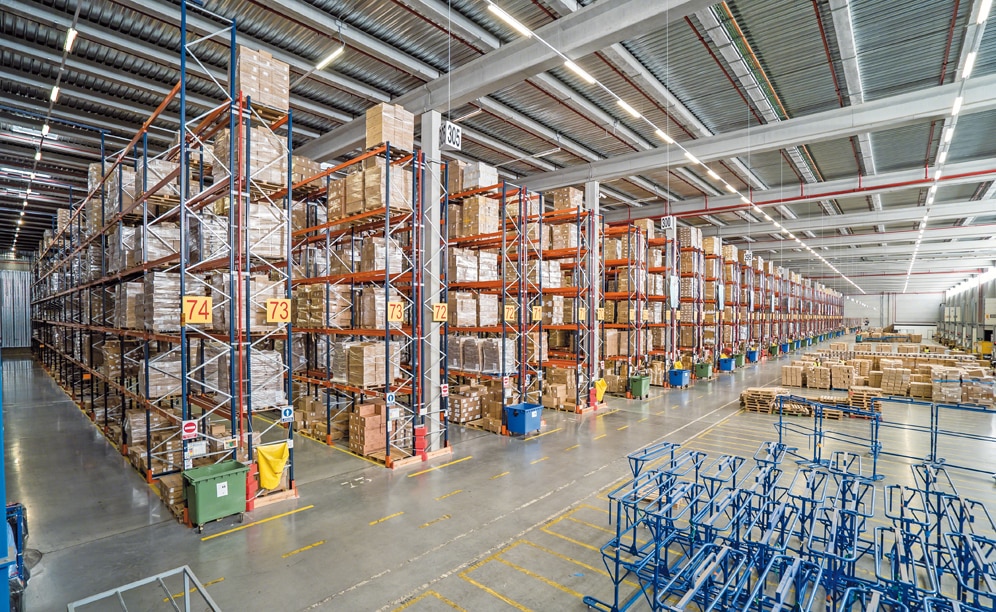
Mecalux installs a new logistics centre for DHL on the outskirts of Madrid
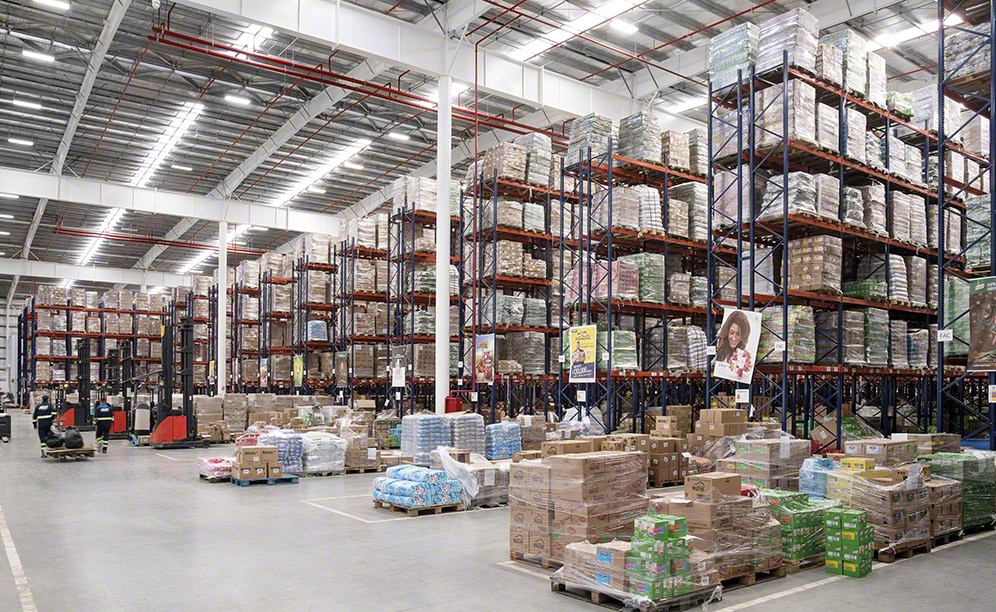
Mecalux has equipped the new Unilever distribution centre with pallet racking
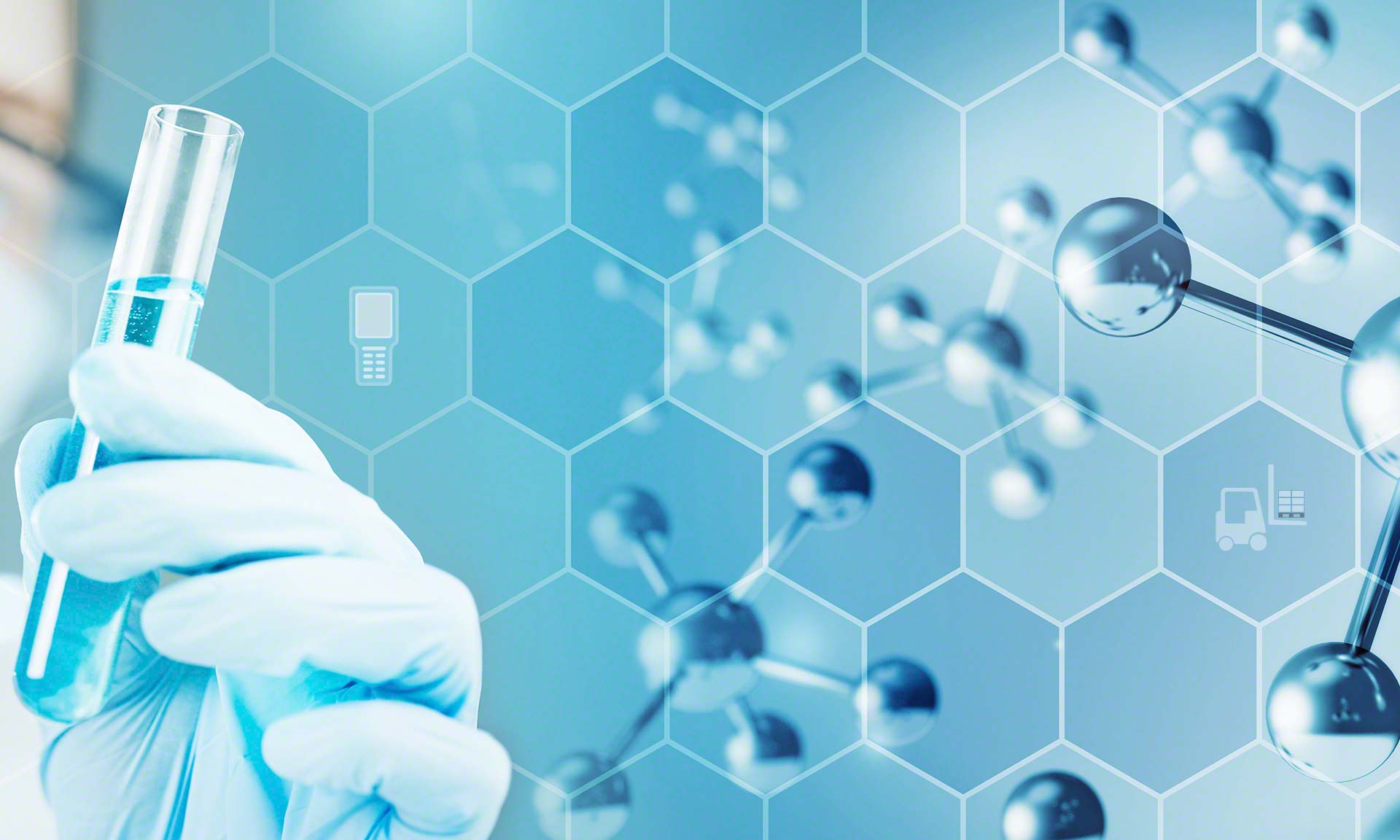
BASF: digitisation for just-in-time production
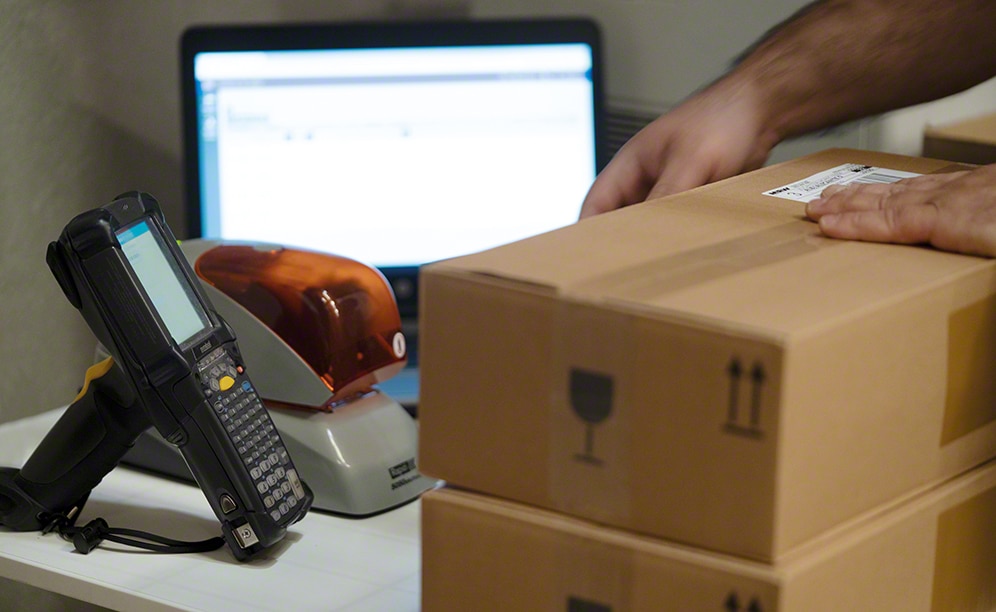
Danone’s warehouse for the infant and medical nutrition product line in Madrid
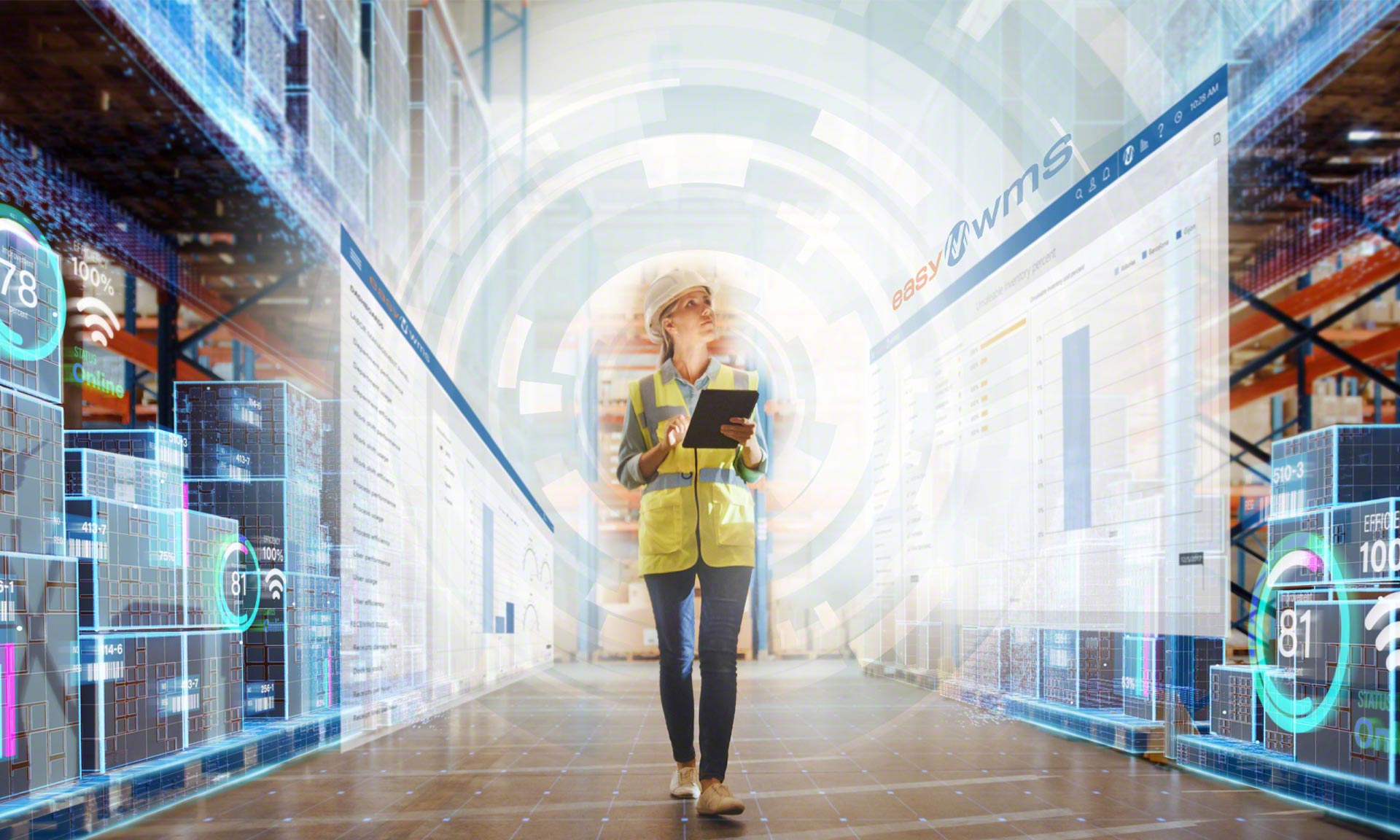
Digitisation transforms the supply chain
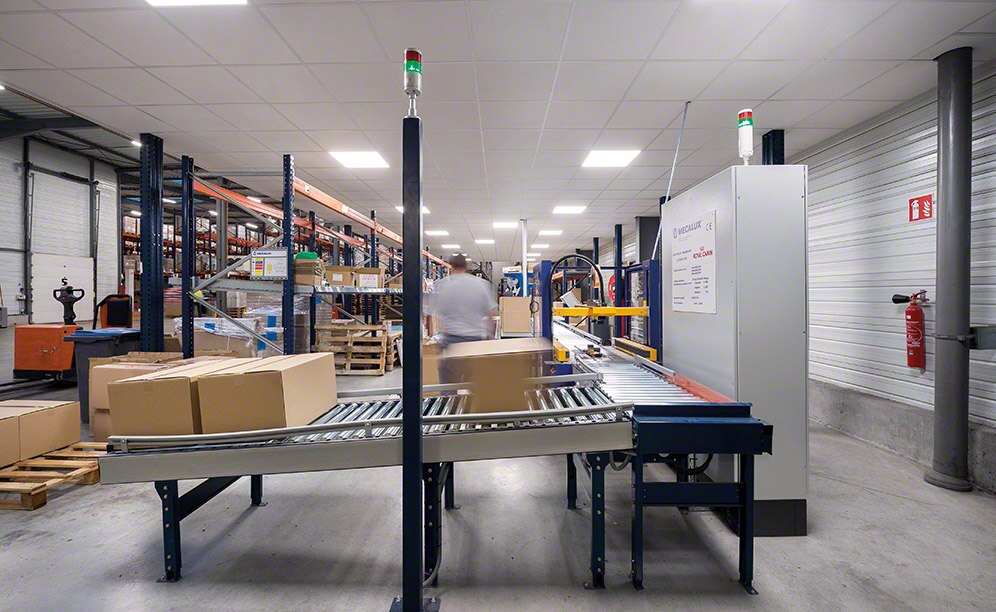
Royal Canin
Multiple solutions to manage pet food products, {{reference.name}}, {{reference.pcase.name}}.
Know more about our vision & mission at Zenkins.
Learn more about our process and how we work?
Contact today! Ready to help you with all tech challenges.
Stay updated with latest technologies and tools.
SAAS Product Development
Empowering Your Vision with Expert SAAS Product Development Services
IT Staff Augmentation
Boosting Your IT Capabilities with Staff Augmentation Solutions
Product Engineering
Crafting Innovation Through Product Engineering Services
Platform and Infrastructure
Elevating Your Digital Foundation: Our Platform and Infrastructure Expertise
Digital Transformation
Unlocking Your Digital Potential: Transformation Services for the Modern Age
Data Engineering
Unlocking the Power of Data: Our Expert Data Engineering Services
IT Consulting
Navigating IT Excellence: Our Comprehensive Consulting Services
- Maintenance And Support
Safeguarding Your Success: Exceptional Maintenance and Support Services
Core Expertise
- .NET Development
- ASP.NET MVC Web Dev.
- ASP.NET Core Web Dev.
- ASP.NET Web Form Dev.
- .NET Windows App Dev.
- .NET WPF Application Dev.
- .NET Core API Development
- .NET WCF Services
- .NET CMS Development
- C# Development
- .NET Core Development
- Full-Stack Web App Dev.
- Agile, Scrum & DevOps
- Integration Services
- Mobile App Development
- AI ML Development
- Legacy .NET App Modernization
- E-Commerce Solutions
- Enterprise Application Dev.
- Database Design And Mgmt
- Cloud Integration
- Azure / AWS / GCP
- Migration Services
- Third-Party Integrations
- UI/ UX Design
- Quality Assurance & Testing
- Security And Compliance
- Consulting And Strategy
- Content Management
- Performance Optimization
- IoT Hardware & Software
- .NET Developers
- C# Developers
- VB.NET Developers
- .NET Core Developers
- Windows Desktop Application Developers
- Azure Developers
- SQL Server Developers
- ASP.NET MVC Developers
- Blazor Developers
- Angular Developers
- Full-Stack .NET Developers
- HTML / CSS Developers
- JavaScript Developers
- Xamarin Developers
- Kentico CMS Developers
- Sitecore Developers
- Umbraco Developers
- Orchard CMS Developers
- DNN (DotNetNuke) Developers
- Sitefinity Developers
- NopCommerce Developers
- mojoPortal Developers
- DevOps Engineers
- UI/UX Designers
- Quality Assurance (QA) Testers
- Security Experts
Build Your Team
We help companies transform, scale, and gain a competitive edge with robust, customized, and innovative digital solutions.
- Technologies
- Entity Framework
- Razor Pages
- Razor Views
- Microservices
- IdentityServer
- Visual Studio
- Visual Studio Code
- Azure DevOps
- SQL Server Management Studio (SSMS)
- AWS (Amazon Web Services)
- GCP (Google Cloud Platform)
- Azure Functions
- Distributed Platforms
Our expertise spans all major technologies and platforms, and advances to innovative technology trends.
Can't find what you need?
- Case Studies
Warehouse Management Software: A Case Study
- Post author: Maryliya M J
- Post published: January 11, 2024
- Reading time: 12 mins read
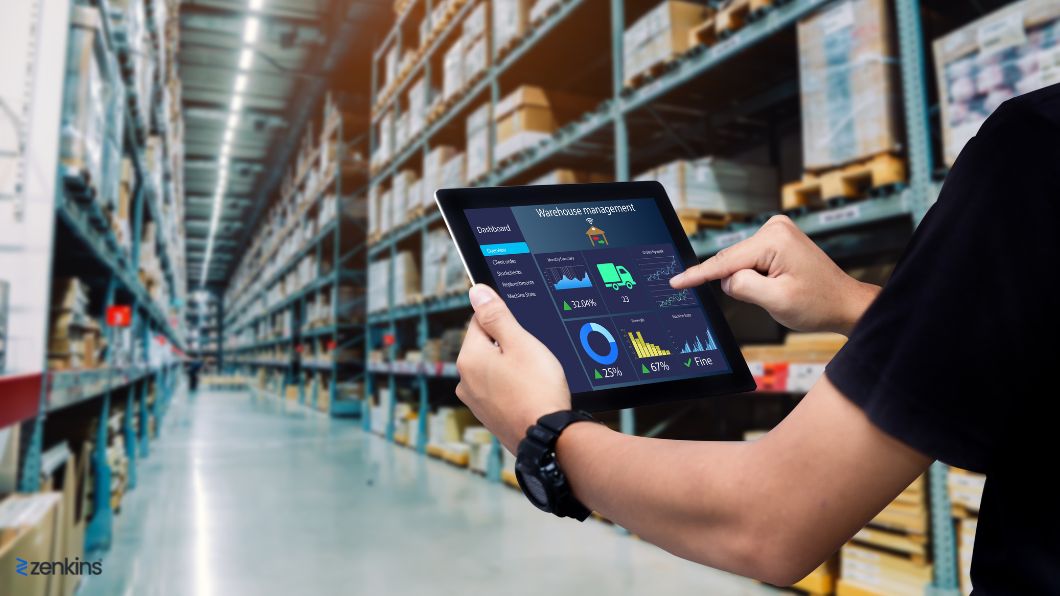
Warehouse Management Software (WMS): A Case Study
Table of contents.
Warehouse management software (WMS) has become an integral tool for modern businesses seeking to optimize their supply chain operations. With the ever-increasing complexity of managing inventory, orders, and logistics, implementing an effective WMS solution can provide significant advantages.
Introduction to Warehouse Management Software (WMS)
Understanding warehouse management systems (wms).
Warehouse Management Software ( WMS ) is like your personal assistant for managing the chaos of a warehouse. It’s a fancy computer program that helps keep track of inventory, streamline processes, and make your life a whole lot easier. Think of it as the Hermione Granger of your warehouse – organized, efficient, and always on top of things.
Evolution and Advancements in WMS
Gone are the days of scribbling inventory numbers on a piece of paper and playing detective to find that missing box of widgets. WMS has come a long way since then. It has evolved from simple spreadsheets to sophisticated systems that can handle complex tasks like inventory tracking, order processing, and even automated picking and packing. It’s like upgrading from a flip phone to the latest iPhone – everything just works better.
Benefits of Implementing WMS
Implementing a WMS might sound like a hassle, but trust me, the benefits are totally worth it. With a WMS by your side, you can say goodbye to inventory nightmares, reduce errors, and improve overall efficiency. It’s like having a superpower that makes your warehouse run smoother than a freshly oiled machine. From enhanced inventory visibility to streamlined order fulfillment, WMS has your back.
About the Client
Our client, a prominent e-commerce company, faced challenges in efficiently managing its warehouse operations. With a growing inventory and increasing order volume, they recognized the need for a robust Warehouse Management Software (WMS) to streamline inventory tracking, order fulfillment, and overall warehouse efficiency.
Project Overview
The project involved developing a .NET-based Warehouse Management Software that seamlessly integrated with the client’s existing systems. The primary objectives were to provide real-time visibility into stock levels, automate order processing, and optimize the warehouse layout for improved picking and packing processes.
The Challenges
- Inefficient Inventory Tracking: The existing systems lacked real-time visibility, leading to inaccuracies in inventory tracking.
- Manual Order Processing: Order fulfillment processes were time-consuming and prone to errors due to manual interventions.
- Suboptimal Warehouse Layout: The warehouse layout needed optimization to enhance picking and packing efficiency.
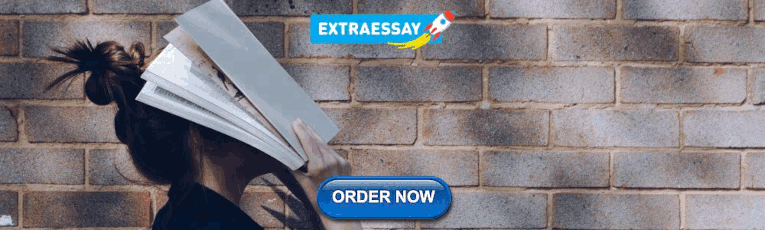
The Solution
Our team, comprising skilled developers and project managers, collaborated to design and implement a comprehensive Warehouse Management Software. Technologies such as .NET, SQL Server, and REST APIs were employed to ensure a robust and scalable solution.
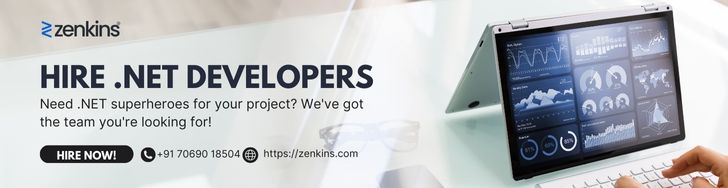
Are you struggling to keep up with your software development needs? Are you looking for a team of dedicated developers who can work on your project full-time and deliver high-quality results? So why wait? Contact us today to learn more about our services and to start the process of hiring your own dedicated development team. Let us help you take your project to the next level! Contact Now!
Key features of the wms.
- Real-time Stock Visibility: The WMS provided instant visibility into stock levels, reducing the risk of stockouts and overstock situations.
- Automated Order Processing: Orders were processed seamlessly, minimizing errors and accelerating the fulfillment process.
- Optimized Warehouse Layout: The software employed intelligent algorithms to optimize the warehouse layout, resulting in improved picking and packing efficiency.
The Outcome
The Warehouse Management Software was successfully deployed, leading to significant improvements in warehouse operations. The client reported enhanced efficiency in inventory management, reduced order processing times, and improved overall warehouse productivity.
By leveraging the benefits of WMS, such as enhanced inventory visibility, streamlined order fulfillment processes, and improved accuracy and efficiency, the company was able to overcome their warehouse management challenges and achieve remarkable results. The lessons learned from this case study provide valuable insights for businesses considering the adoption of WMS, emphasizing the importance of careful selection, thorough implementation planning, and seamless integration with existing systems. Ultimately, the successful implementation of WMS opens doors to increased productivity, cost savings, and improved customer satisfaction, making it a strategic investment for any organization looking to optimize their warehouse operations.
Our team’s expertise in developing a tailored Warehouse Management Software using cutting-edge technologies resulted in a solution that addressed the client’s challenges effectively. The implementation of real-time visibility, automated order processing, and warehouse layout optimization contributed to a more streamlined and efficient warehouse operation.
Are you facing similar challenges in warehouse management? Contact us today to explore how our expertise in WMS development can transform your warehouse operations and drive efficiency.
What is Warehouse Management Software (WMS) and why is it important?
Warehouse Management Software (WMS) is a software solution designed to efficiently manage and control various aspects of warehouse operations, including inventory management, order fulfillment, and logistics. It is important because it helps businesses optimize their warehouse processes, improve inventory accuracy, streamline operations, enhance productivity, and ultimately deliver better customer service.
How does a WMS solution benefit businesses?
A WMS solution offers numerous benefits to businesses. It provides real-time visibility into inventory levels and locations, enabling effective inventory management and reducing stockouts. It automates and streamlines order fulfillment processes, improving speed and accuracy while reducing errors. WMS also optimizes warehouse layout, resource allocation, and workflow, leading to increased operational efficiency, productivity, and cost savings.
What considerations should businesses keep in mind when selecting a WMS solution?
When selecting a WMS solution, businesses should consider factors such as scalability, ease of integration with existing systems, customization options, vendor support, and cost. It is crucial to assess specific business requirements, evaluate the software’s functionality, and determine whether it aligns with the organization’s long-term goals. Conducting thorough research, seeking recommendations, and requesting demos or trials can help make an informed decision.
Is it challenging to integrate WMS with existing systems and processes?
Integrating WMS with existing systems and processes can present challenges, mainly due to differences in data structures, formats, and compatibility. It requires careful planning, data migration, and coordination between the WMS provider and internal IT teams. However, with proper communication, collaboration, and expert guidance, businesses can overcome integration challenges and achieve seamless connectivity between WMS and other enterprise systems.
Get 50% off on your first project with us! Join our community of satisfied customers and experience the power of our software team today. Contact now and get 50% off your first software project/ product. Don’t miss out on this exclusive offer! Your Name * Your Email * Contact Number * Brief Your Requirement * 0 / 500 Claim Your Discount Please do not fill in this field.
You might also like.
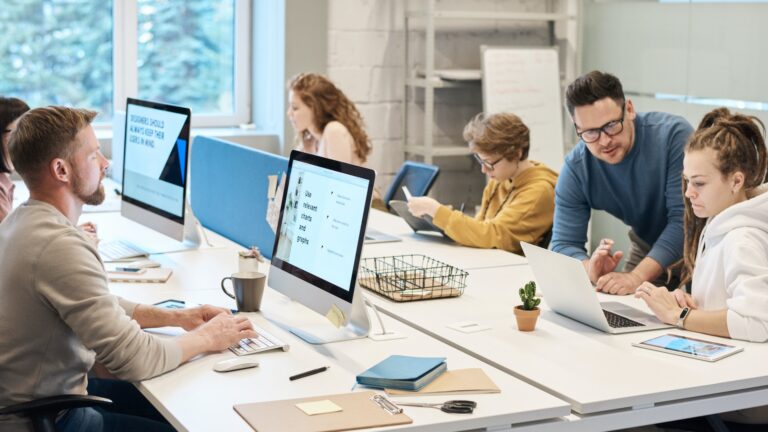
Employee Engagement Portal: Our approach to help the Human Resource department
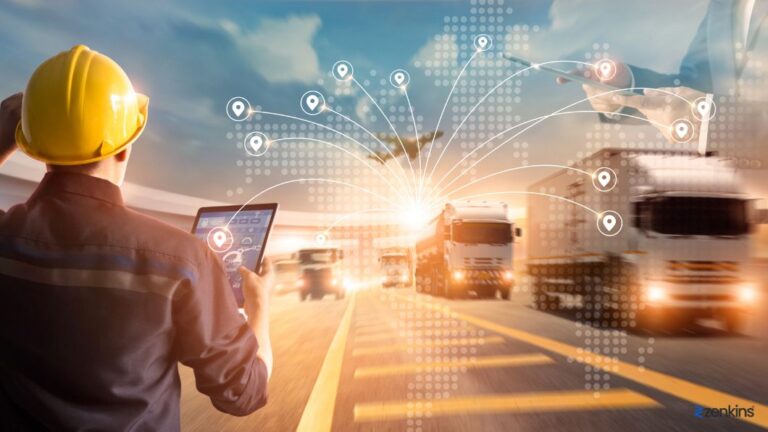
Transport Management Software: A Case Study
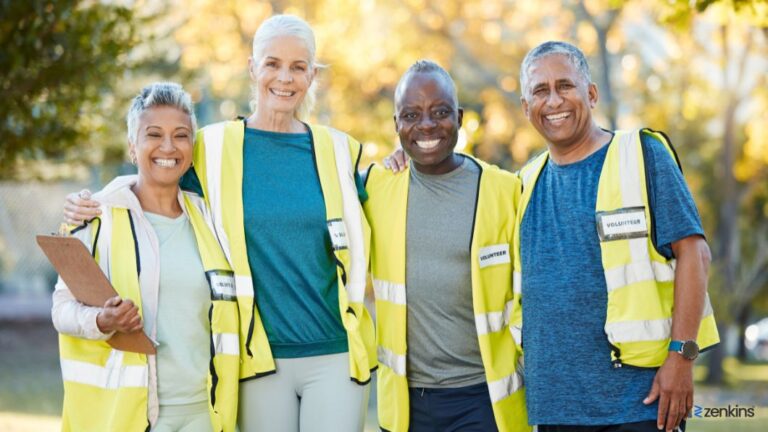
Nonprofit Donor Management Software: A Case Study
Book a free consultation.
Tailored Solutions, Expert Advice, and Project Estimates Await.
Expect a Prompt Call from one of our Account Managers.
- Elite IT Professionals
- Time Zone Aligned
- Experienced Team
At Zenkins, we bring together a curated network of elite IT professionals ready to elevate your projects to new heights. From seasoned developers to innovative designers, our handpicked talent pool is here to turn your visions into reality. Experience unparalleled expertise, reliability, and dedication to excellence with our team of Elite IT Professionals.
At Zenkins, we understand the importance of global collaboration. That’s why our team is strategically aligned across time zones, ensuring seamless communication and productivity no matter where you are. From brainstorming sessions to project updates, our time zone-aligned approach guarantees that deadlines are met and progress never stalls. Experience the convenience of working with a team that’s always in sync.
At Zenkins, we pride ourselves on our experienced team of professionals who bring years of industry knowledge and skill to every project. From seasoned developers to seasoned project managers, our team has the expertise to tackle even the most complex challenges. With a proven track record of success, we deliver results that exceed expectations.
+91 70690 18504
[email protected]
Zenkins is a leading software development company based in India, specializing in SAAS Product Development, Digital Transformation, and Product Engineering. With a dedicated team of professionals and a commitment to excellence, we deliver innovative solutions that drive business growth and success. Partner with Zenkins for all your software development needs and experience the difference firsthand.
- Methodologies
- Our Services
- IT Staffing Services
- Software Outsourcing
- Careers @Zenkins
- Current Openings
- Technology Insights
- Careers Insights
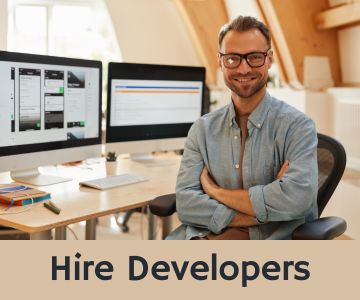
326, Naroda Business Point, Vasant Vihar 2, Nava Naroda, Ahmedabad, Gujarat 382330
Opening soon in Pune Baner, Pune, Maharashtra 411045 - India
Opening soon in Bangalore Vasanth Nagar, Bengaluru, Karnataka, 560020 - India
Privacy Overview
Get 50% off your first project with us.
Join our community of satisfied customers and experience the power of our software team today. Contact now and get 50% off your first software project/ product. Don’t miss out on this exclusive offer!

Read our customer success stories
Read on to understand how Hopstack's customers improved its warehousing and fulfillment activities, and grew their businesses while minimizing operational costs.
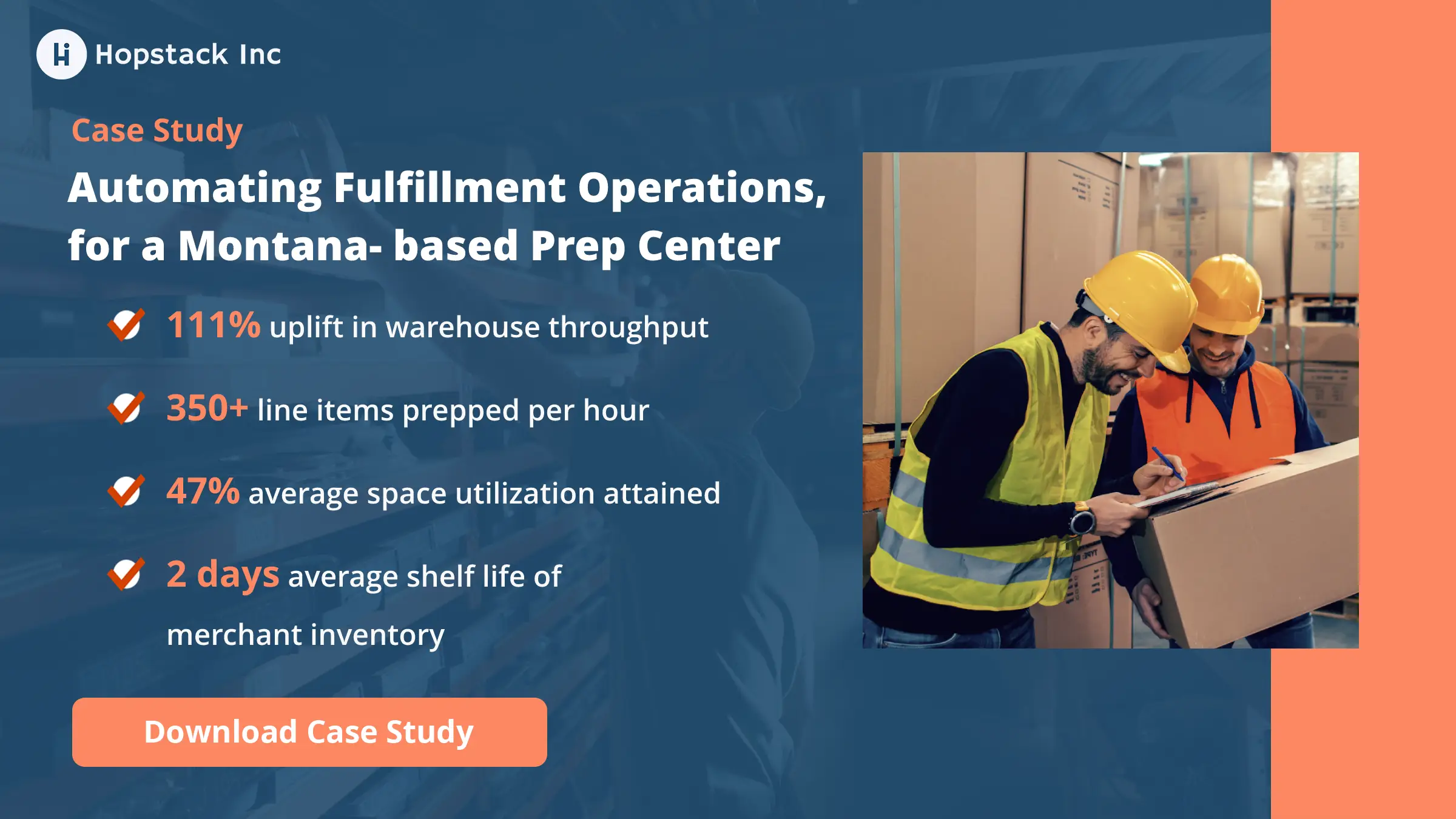
Automating Fulfillment Operations, for a Montana-based Prep Center
Here's how Hopstack transformed this Prep Center's inbound, prepping, and outbound operations and helped improve the merchant experience.
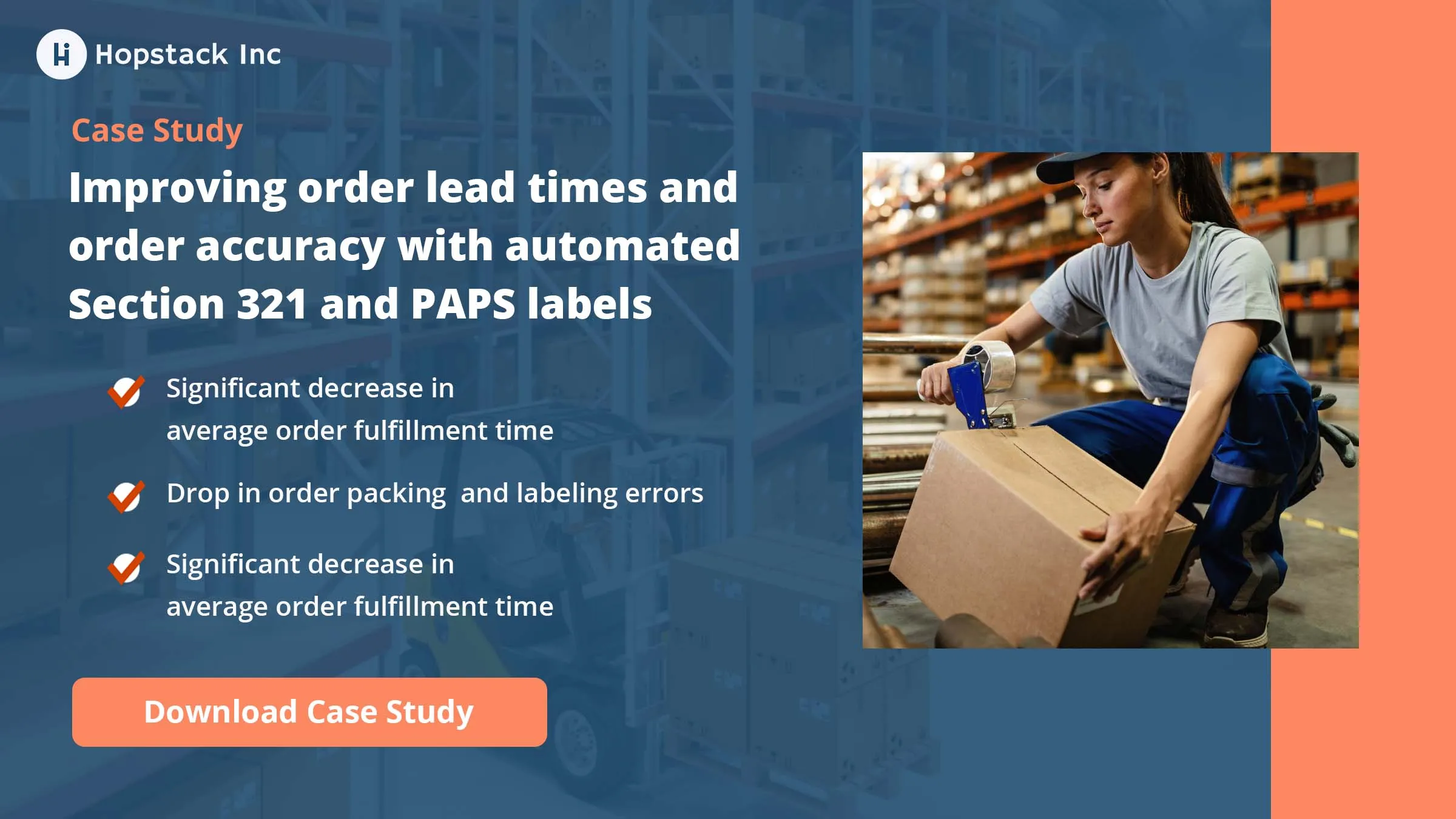
Enabling Section 321 and PAPS for North American Brands for International Fulfillment
Here’s how Hopstack enabled this North American consumer retail brand to automate the packing and labeling process around Section 321 and PAPS and make its cross-border fulfillment more efficient.
.webp)
Solving Combined Orders for North America’s Brands and Fulfillment Providers
Here's how Hopstack's algorithmic and highly flexible 'Combined Orders' functionality helped this North American luxury consumer goods seller cut down packaging and shipping costs and improve order lead time.
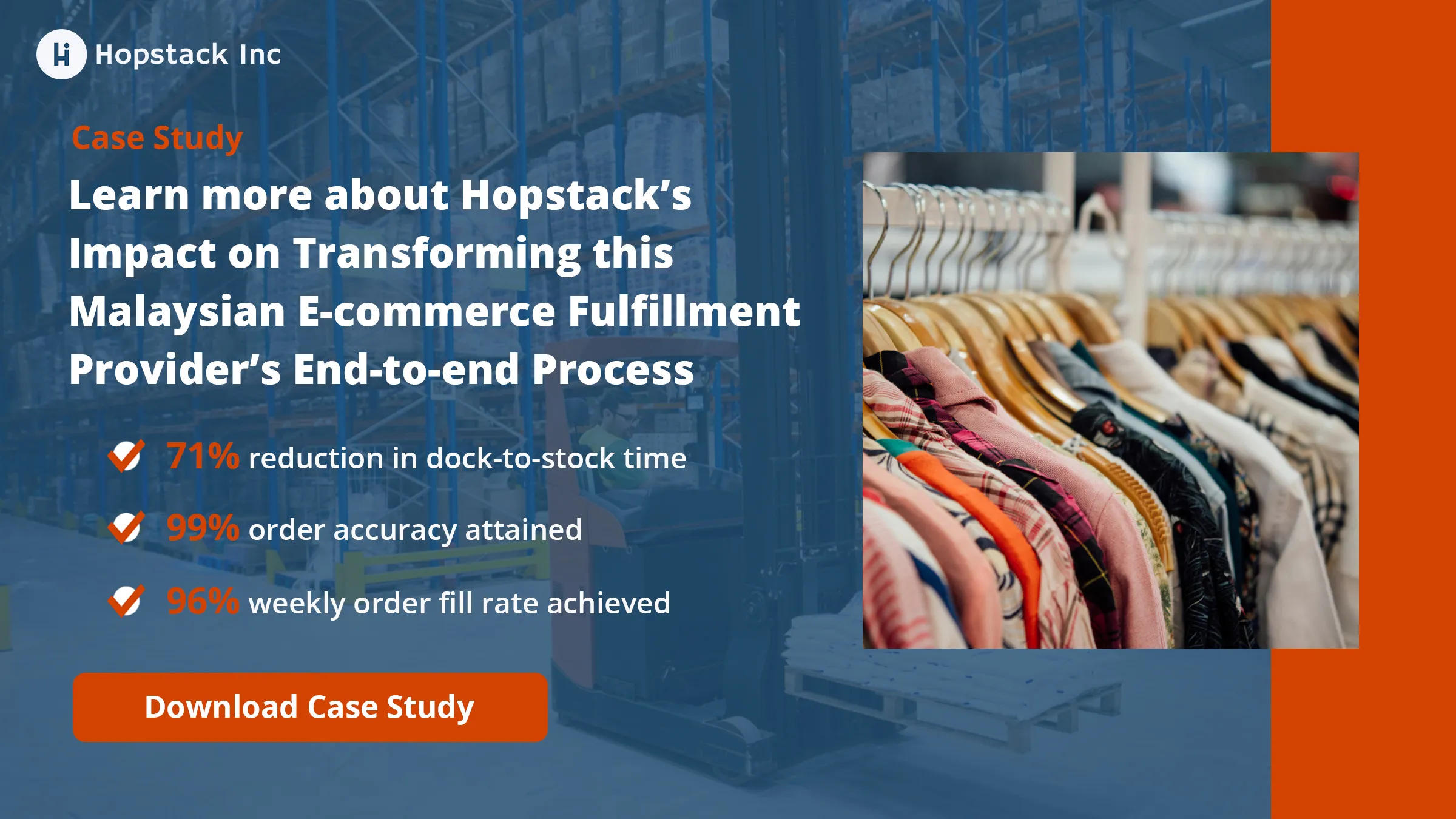
How this Apparel-Focused Malaysian Ecommerce Fulfillment Provider Transformed its End-to-End Process using Hopstack
How one of the fastest growing 3PLs in Malaysia improved performance visibility and transformed its end-to-end inbound and outbound processes to better serve its fast-fashion customers.
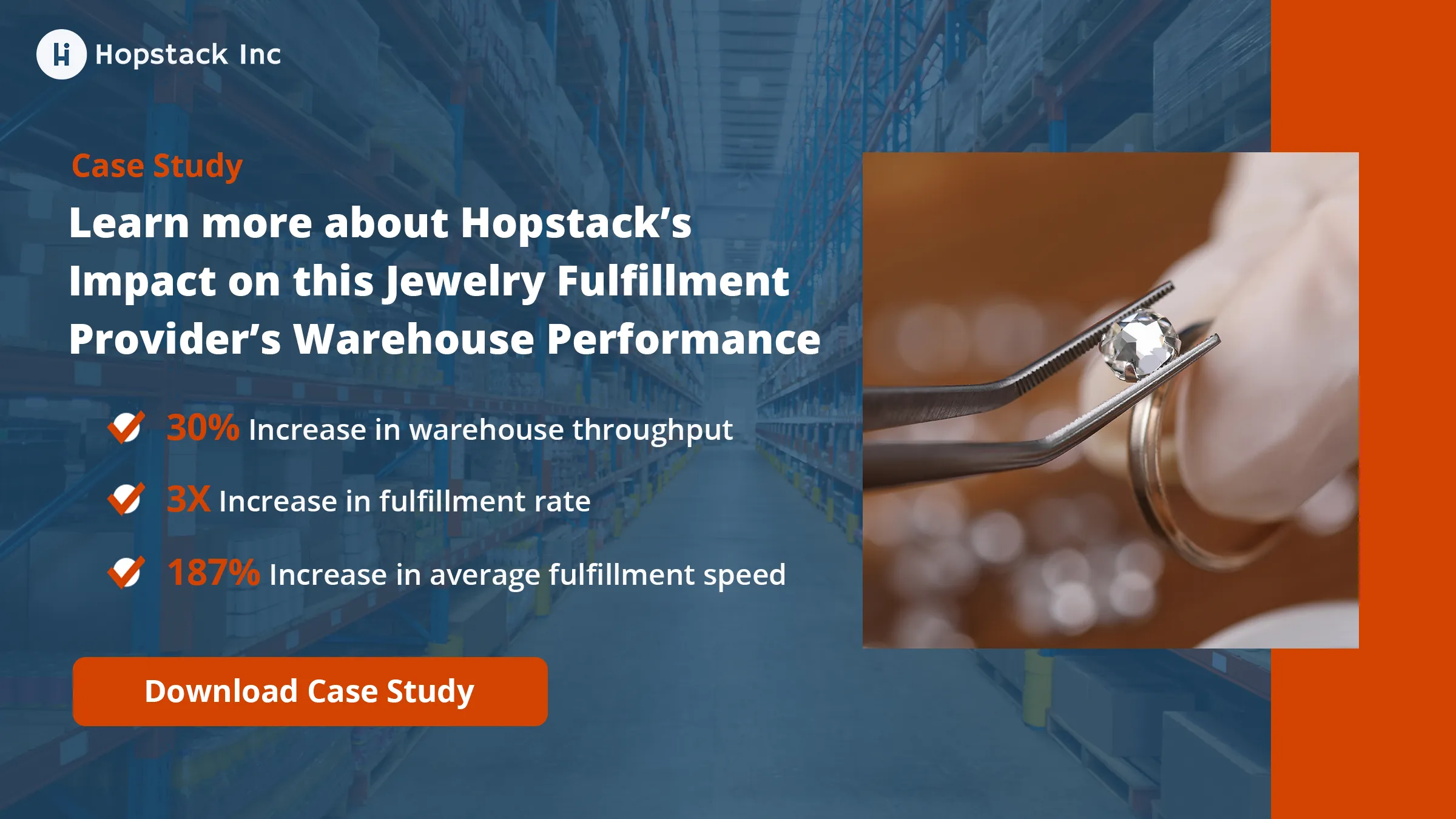
How this Jewelry Fulfilment Provider Grew its Warehouse Throughput by 30%
How one of the leading jewelry fulfilment providers solved the challenge of peak seasonal demand by replacing manual processes with Hopstack's warehouse automation and execution system.
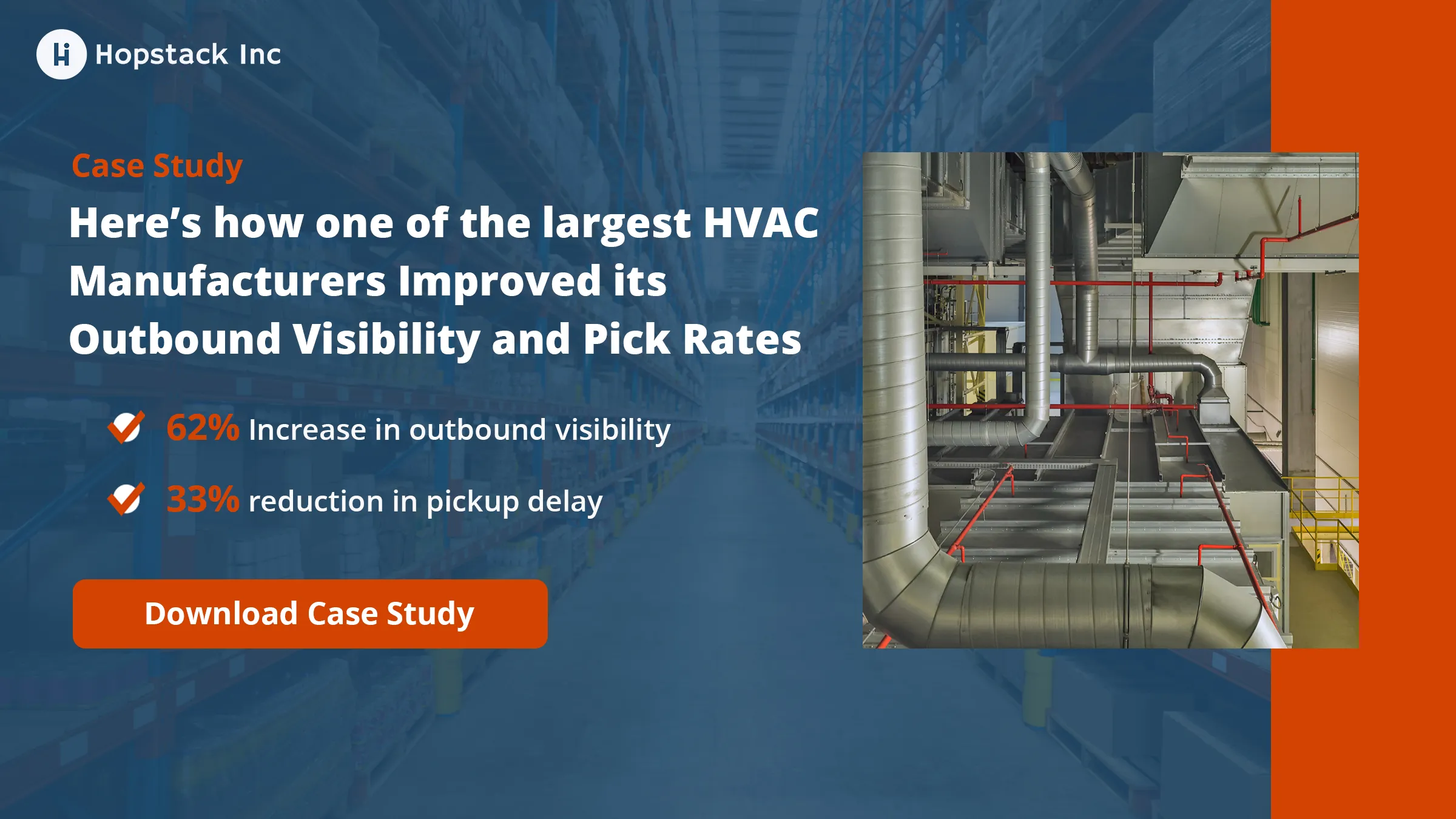
How Hopstack Helped this HVAC Manufacturer in Increasing the Outbound Visibility by 62%
How one of the world's largest HVAC (Heating, Ventilation, and Air Conditioning) manufacturers adopted Hopstack's Digital Warehouse platform leading to 62% increase in outbound visibility and 25% reduction in pickup delay.
Warehouse Case Studies
The warehouse case studies below explore how our portfolio of warehouse technology solutions and services helped companies overcome their challenges. Each case study discusses the challenges faced, solutions implemented, and results attained by our clients.
A Major 3PL Achieved Warehouse Modernization with Cyzerg’s Custom In-Transit Software
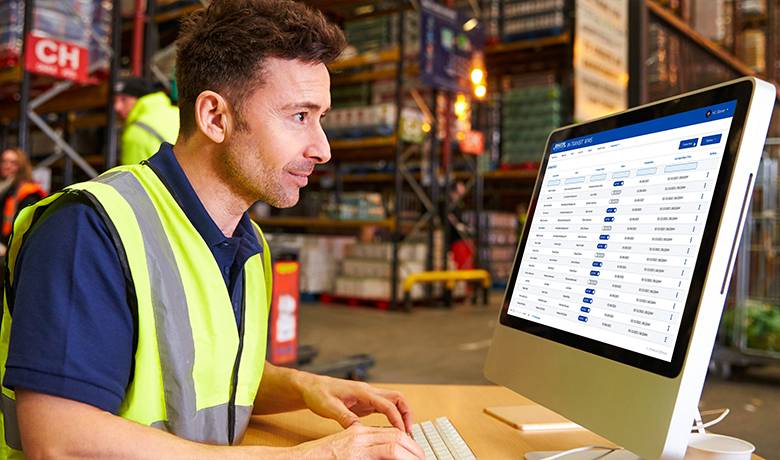
A major 3PL has been experiencing inefficiencies and errors due to manual processes and a lack of system integration. After working with Cyzerg, the 3PL modernized its warehouse via a custom WMS and automation, boosting productivity and profitability.
How a 3PL Reduced Inefficiencies & Walking Time with a Custom Warehouse Management System Mobile App
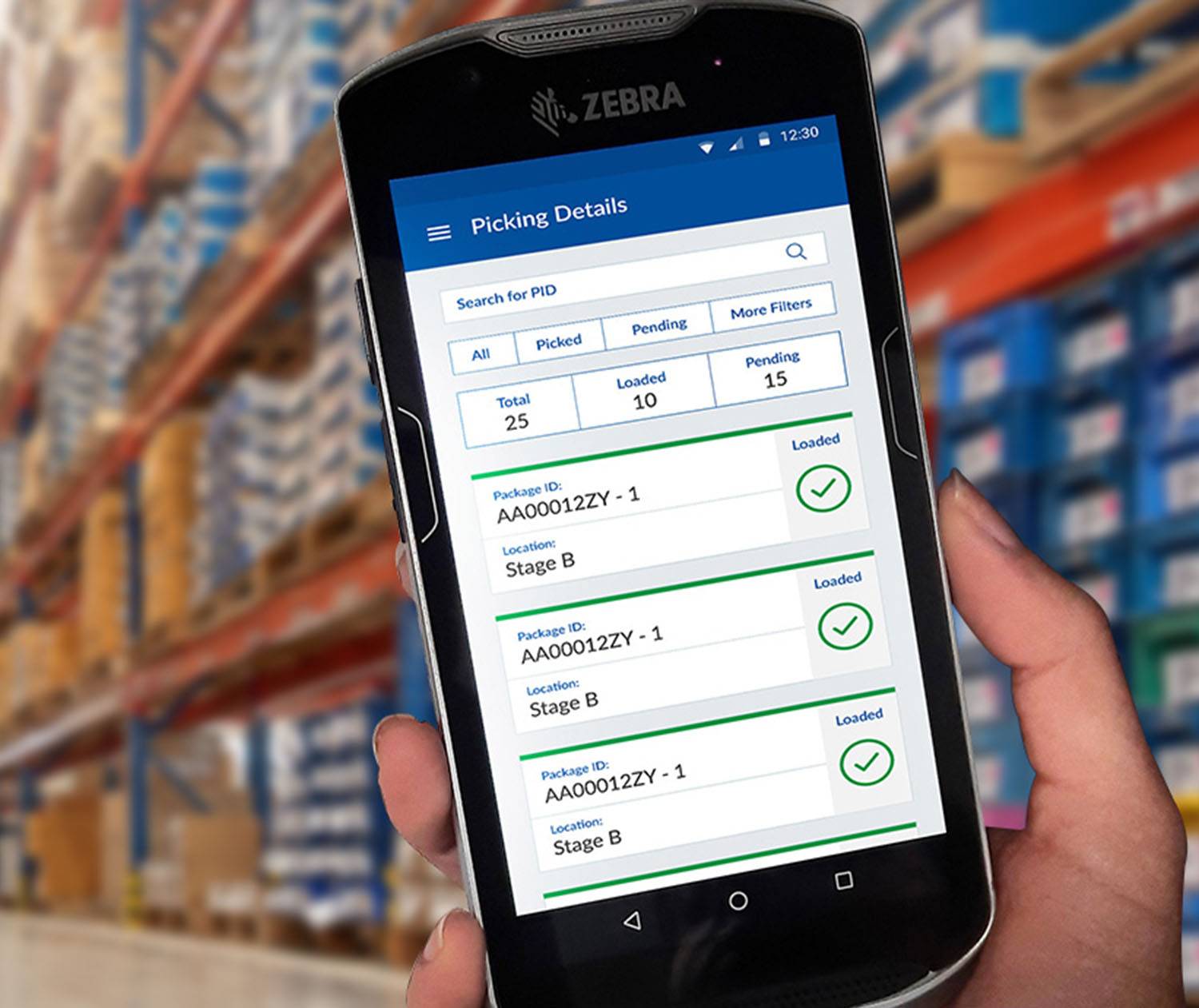
A 3PL faced operational inefficiencies and delayed decision-making due to high walking time and data collection latency. Through Cyzerg, the 3PL addressed these challenges with a custom warehouse management system mobile app.
A Freight Forwarder Addressed Its Server Challenges Through the Utilization of Cyzerg’s Cloud Servers
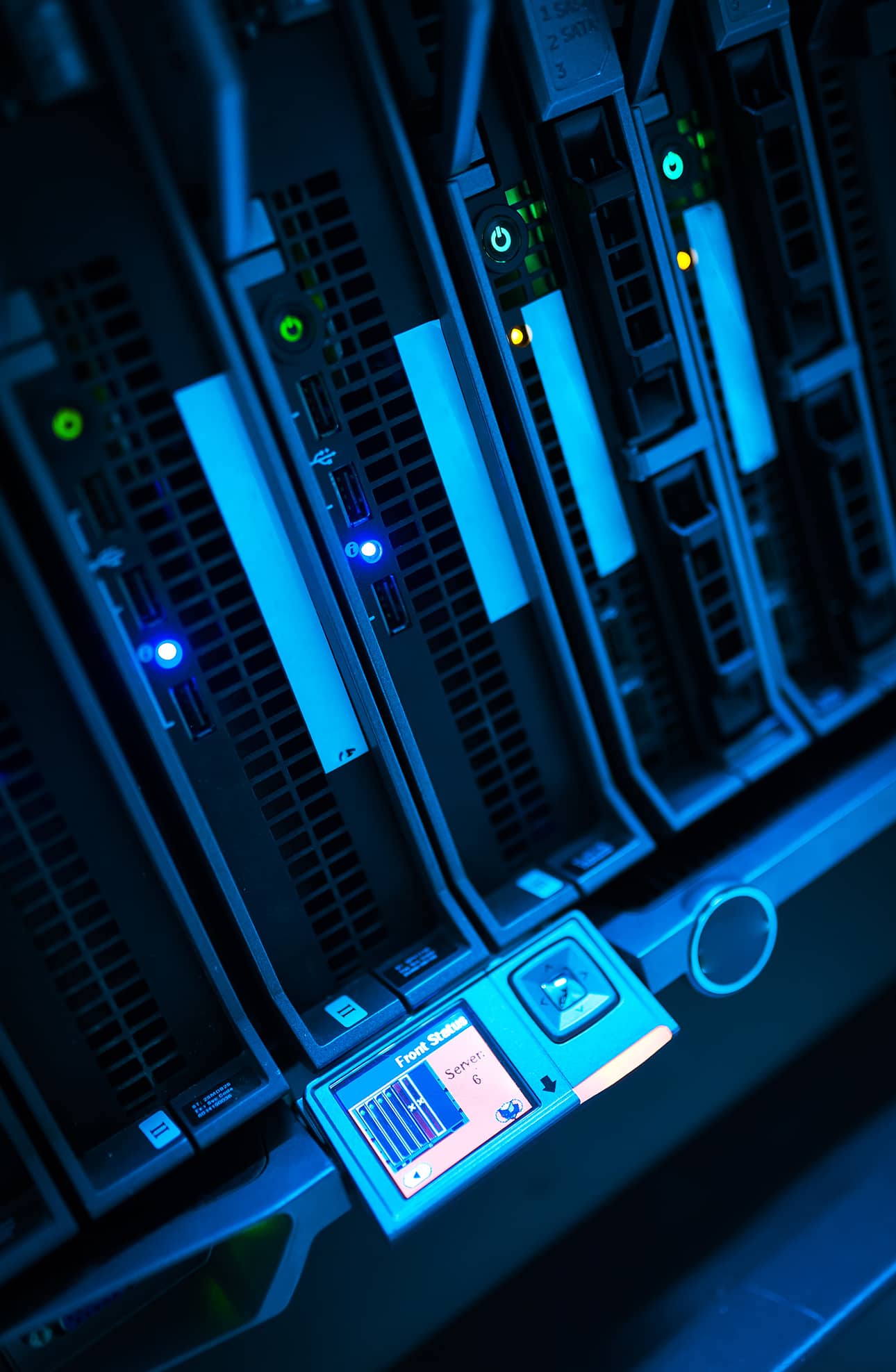
A company faced inefficiencies and downtimes due to its servers being scattered across numerous branches. Through Cyzerg, the company addressed its challenges by utilizing cloud servers and increasing uptimes and productivity.
A Cruise Ship Increased Its Receiving Process Efficiency Through Cyzerg’s Custom Warehouse Mobile App
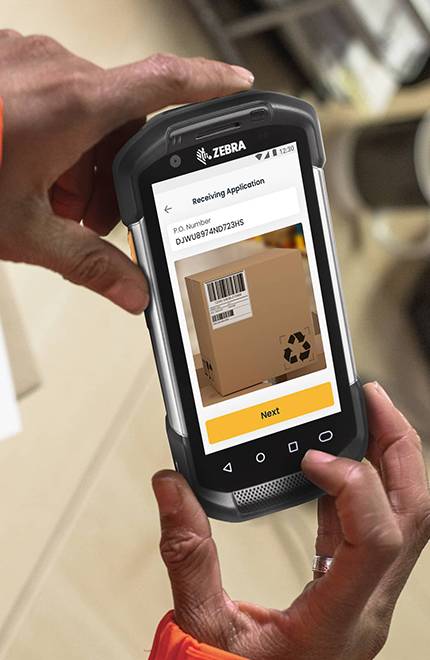
A cruise ship experienced warehouse receiving process inefficiencies due to manual tasks. Through Cyzerg, the company addressed its challenges with a custom warehouse mobile app, increasing its productivity and cost savings.
A DC Increased Its Efficiency Through Cyzerg’s Warehouse Wireless Network Solution
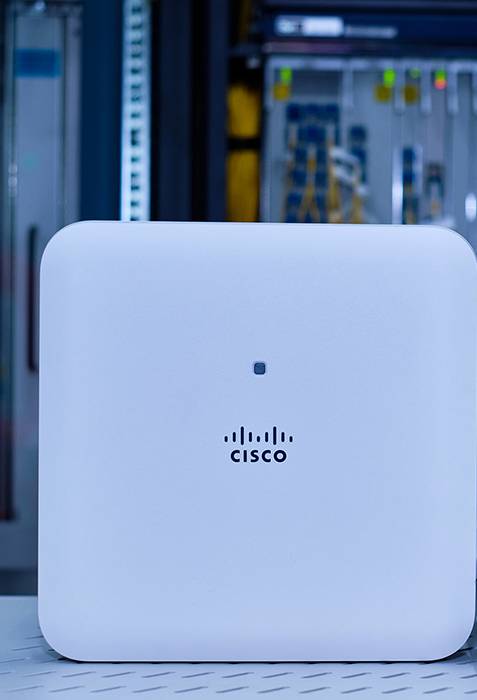
A distribution center's operational efficiency was impacted by the unreliability of its wireless network. The DC contacted Cyzerg to resolve the constant wireless issues and implement a reliable warehouse wireless network solution.
Improved Customer Satisfaction Through Cyzerg’s 3PL Customer Portal
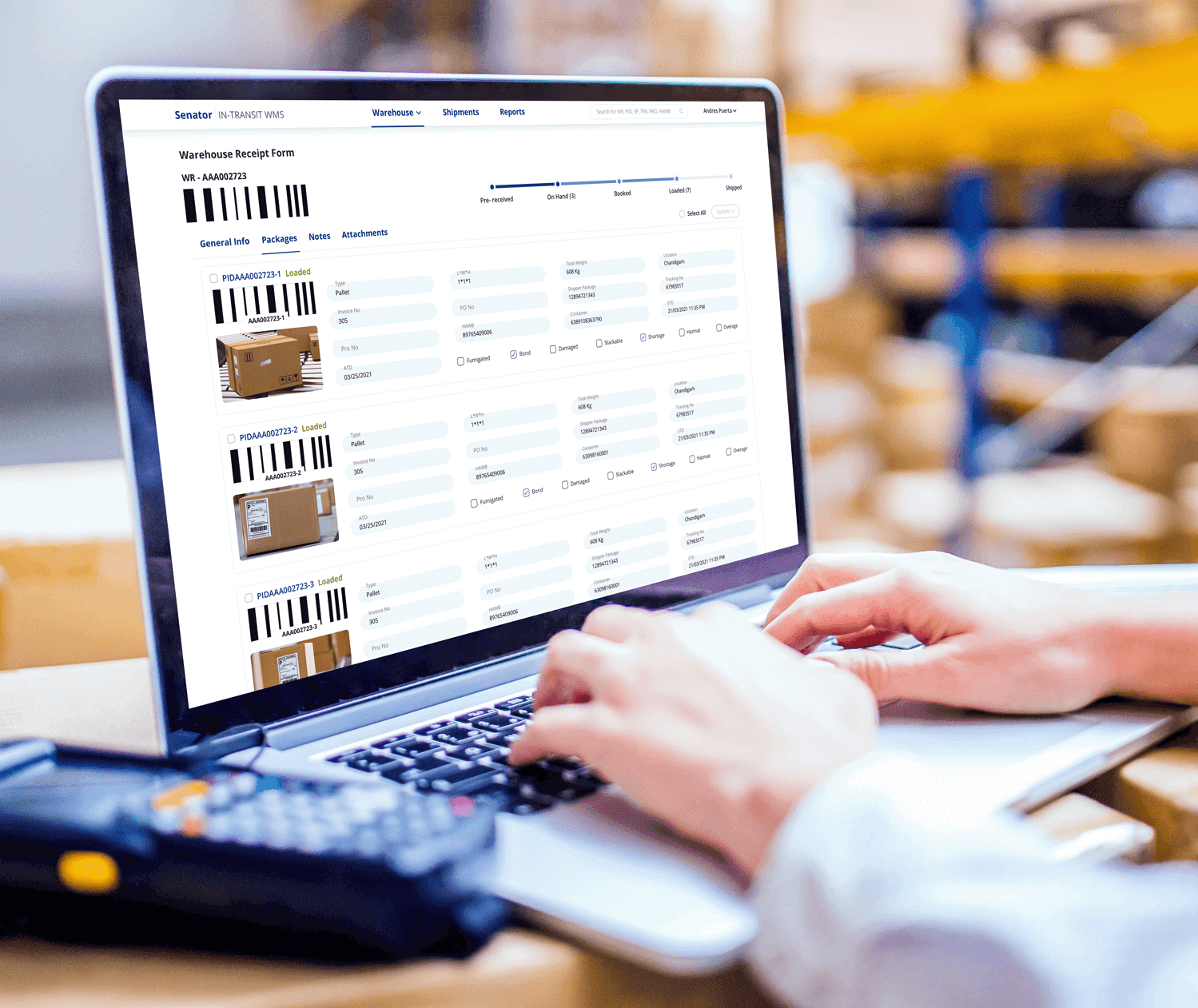
A 3PL faced recurrent customer complaints due to its inability to provide real-time inventory visibility and cargo control. After working with Cyzerg, the client resolved its customer challenges through a 3PL portal.
Reduced Costs and Overcame Technology Challenges by Outsourcing IT Operations to Cyzerg’s Managed IT Services
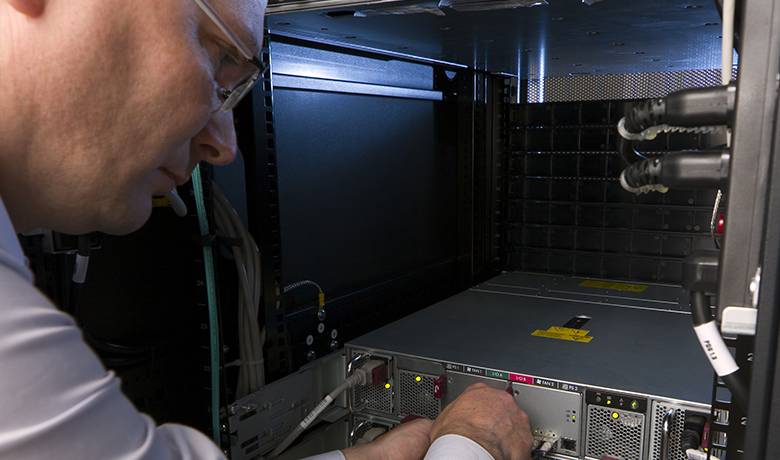
An NVOCC faced a significant increase in technology management costs as it scaled from small to mid-size. By outsourcing its IT operations to Cyzerg, the customer overcame its rising IT management costs.
A Freight Forwarder Automated Its Warehouse Pallet & Parcel Dimensioning and Image Capture
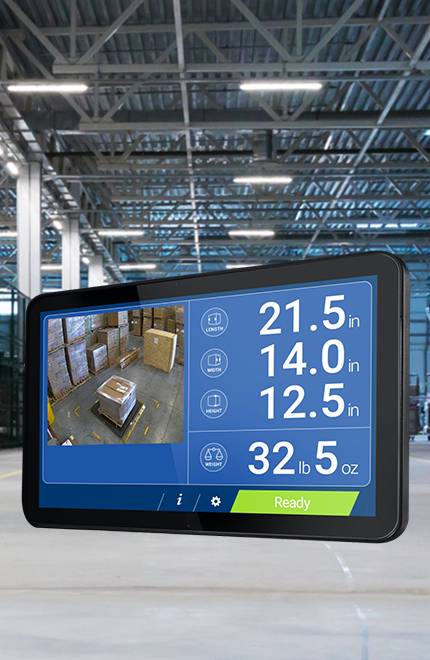
A company has been dimensioning and capturing cargo images manually, thus limiting its processing capacity and increasing costs. With Cyzerg, the company automated its warehouse pallet and parcel dimensioning process.
A 3PL Reduced Communication Costs Through Cyzerg’s VoIP Enterprise Phone System
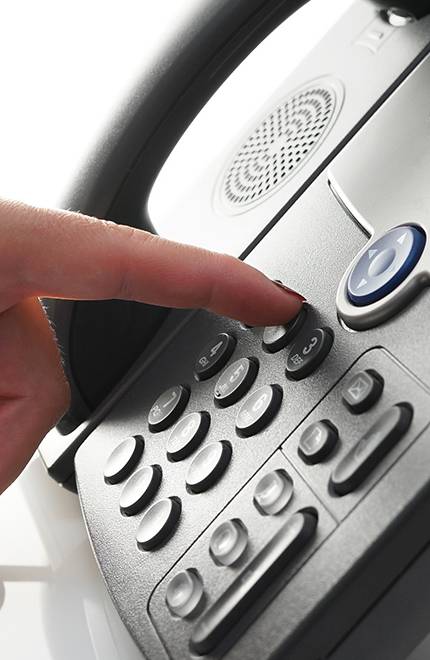
A 3PL with multiple branches across Latin America faced communication challenges and high costs. After working with Cyzerg, the customer increased its cost-efficiency and productivity via a VoIP enterprise phone system.
A Manufacturer Protected Systems and Data from Cyberattacks Through Cyzerg’s Security and Data Protection Strategy
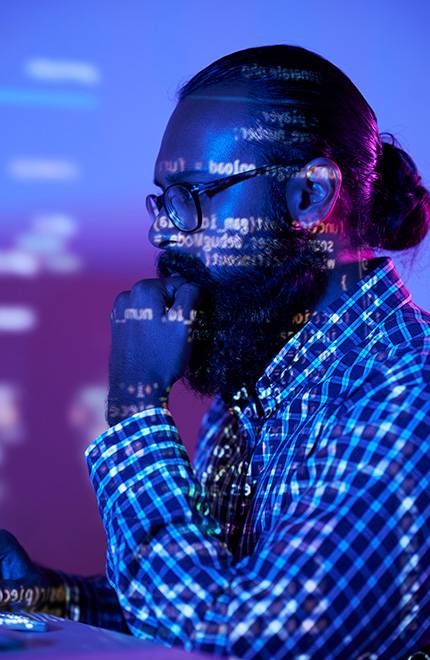
A manufacturer experienced system security exploits and continuous business downtimes that slowly affected its reputation. After working with Cyzerg, the company addressed its challenges by implementing a security and data protection strategy.
- Back to Blog
Case Studies of Successful Custom WMS Implementations
Commonly, we study the success stories of others to get inspiration and find new ideas for improving our business or personal efficiency. As a custom WMS development partner, we at HQSofware, also follow best practices and trends to deliver top-notch solutions to our clients. However, based on our WMS development experience, we can already share our own examples of winning warehouse management systems.
In this article, we’ll take a look at 5 successful examples of WMS software to understand how to implement such a system to enhance warehouse productivity.
What is a Custom WMS?
Developing an E-3PL System for Warehouse Automation
Implementing Predictive Analytics for Smart Inventory Management
Providing Warehouse Navigation to Speed Up Order Picking
Improving Supply Management with a WMS
Developing a WMS Module to Boost Marketplace Operations
How to Maximize WMS Efficiency?
A warehouse management system (WMS) is a powerful tool that optimizes and streamlines warehouse operations, including inventory management, picking and packing processes, shipping management, etc. A custom WMS, designed according to your unique workflow, eliminates unnecessary features and offers a user-friendly interface. With custom WMS development , you can prioritize factors that are crucial for your organization, ensuring that the system aligns perfectly with your unique business needs.
Let’s take a look at some custom WMS examples and how they’ve helped to overcome warehouse challenges for their respective owners.
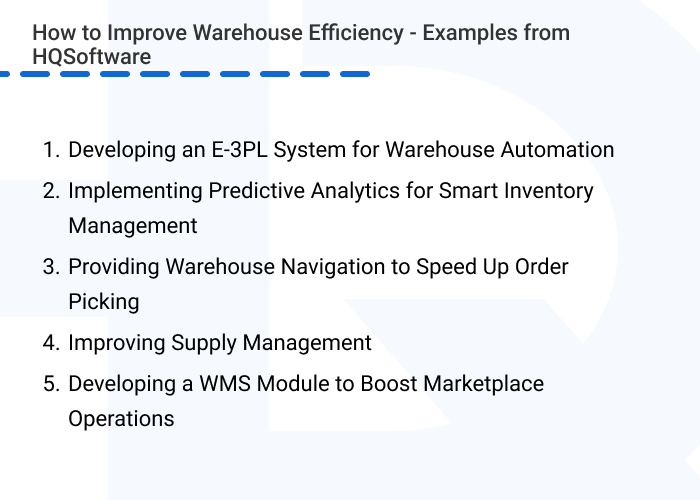
It’s no longer enough for a modern warehouse management system to merely provide inventory visibility and assist in order picking and packing. Companies are now striving to maximize operational efficiency by choosing smart systems with advanced features that can simultaneously address a wide range of issues.
In line with this trend, a US-based startup embarked on the development of comprehensive WMS software that adheres to modern requirements. A large international team of developers, including HQSoftware specialists, was involved in the project.
The main goal was to create an advanced system that can automate and optimize many logistics processes and perform some of them autonomously. For example: automatically generate replenishment orders based on customer demand forecasts, or update goods availability and price for buyers in real-time.
In addition, the system facilitates warehouse audits, provides enhanced navigation, integrates with numerous third-party systems, and enables express picking and receiving. With all its innovative features, the E-3PL platform boasts an impressive 99.9% order accuracy and 99.4% same-day order delivery.
This WMS implementation case study highlights the potential for comprehensive software to enhance virtually any warehouse operation. Achieving this requires a thorough analysis of every process within your warehouse and careful consideration of how advanced technology can drive improvements. This is especially beneficial if you decide to turn to custom WMS software development , as this allows you to build a system that meets your business needs in the best possible way.
Not wasting financial resources and being able to meet changing customer demand are deeply desired by every business and a must-have feature of modern WMS software.
Our client approached us with just such a request. They needed to upgrade a legacy WMS and implement predictive analytics capabilities to optimize warehouse inventory.
To accomplish this, our development team carefully selected the most suitable Machine Learning models capable of analyzing both historical and real-time operational data. The system provides data-driven replenishment recommendations tailored to specific parameters such as supplier delivery terms and minimum stock quantities. As a result, the client was able to reduce inventory costs by 15%.
The power of predictive analytics lies in its ability to learn and adapt to your unique business characteristics, offering personalized recommendations on how to improve it. So, you can benefit from optimal stock levels, excess-cost elimination, efficient space utilization, and a proactive response to customer needs, gaining a strong competitive edge in the market.
Since goods in a warehouse are not arranged as in a supermarket but are stored in boxes with numerical location identifiers, finding the right item can be a daunting task for pickers.
To address this WMS challenge and streamline order picking, our client — a retail company from Germany — decided to implement enhanced warehouse navigation . The feature creates optimized picking routes according to the picker and other items’ location and warehouse configuration.
The solution is delivered as a cross-platform mobile app that provides a map with a picking route and offers voice and visual guidance. With the app, pickers now spend 25% less time on order picking .
Even if you have many large warehouses with different layouts, this is no reason to overlook such a feature. Our developers can create an intuitive graphical interface that allows you to create any warehouse layout, as was implemented in this WMS case study.
Want to create a WMS solution to improve your warehouse operations? We’re ready to help! HQSoftware has a team of skilled professionals ready to tackle the project. Let’s talk! Anna Halias Business Development Manager Get a Free Quote
In an ideal world, all suppliers would have compatible systems that seamlessly integrate with your WMS. However, in reality, you may encounter scenarios where a vendor relies on Google Spreadsheets for inventory tracking or where having a large number of suppliers makes collaboration within a single WMS challenging.
Well, we know several examples of WMSs that include a separate platform for onboarding and communicating with suppliers. We’ve developed such a platform as well . It enables a US retailer to connect with all suppliers in a single interface. Here, suppliers can upload product catalogs, manage item availability, and set prices, while the customer can place purchase orders and establish collaborative agreements.
An important feature of this platform is its ability to handle various data formats, enabling suppliers to post catalogs in their preferred format, which was quite a challenge for our development team. We also ensured system scalability, enabling the customer to expand their network of suppliers.
With this platform, the customer now enjoys seamless order placement, improved supply management, and a 37% reduction in product delivery delays.
The process of publishing and updating items on a single marketplace is relatively straightforward. You fill out the product details, add images, and configure display settings. This is true for several products or catalogs hosted on a single platform. But when you’re a 3PL provider responsible for hosting hundreds of clients with thousands of items on multiple marketplaces, it’s more like a nightmare.
Therefore, for one of the 3PL providers, the HQSoftware team has developed a module for the company’s custom supply chain software system that can automatically publish and update catalogs on several marketplaces and allows for manual item updates within one interface. By synchronizing with the customer’s system, the module ensures consistent and accurate data across platforms.
Within the module, the customer can also customize the display of different products according to specific parameters, such as particular display times, different prices for different times of the day, etc. With robust data exchange mechanisms implemented by our team, the module seamlessly uploads files with all data, speeding up product management tasks by 30%.
Even if you’re not a 3PL provider, such a feature can greatly simplify marketplace management. You no longer have to manually navigate through each product listing on every platform to make changes. All this can be done with a few clicks through a user-friendly interface.
Based on the expertise we’ve gained from our WMS implementation case studies, we understand that leveraging the advantages of WMS software takes more than simply finding or developing a suitable system. It’s also important to focus on proper WMS implementation . Consider the following actions.
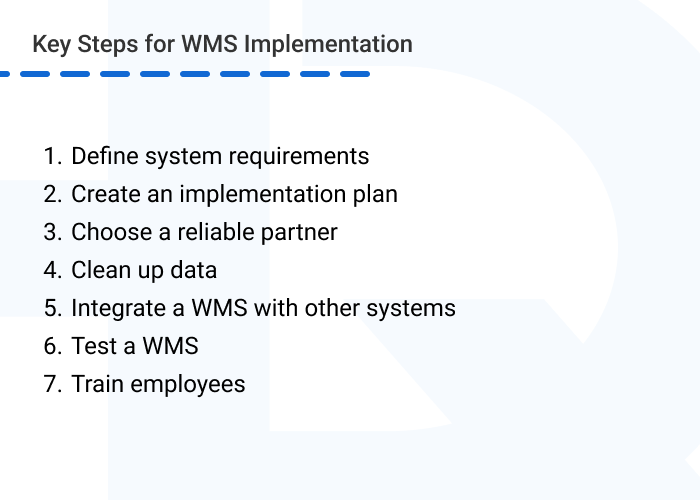
- Define system requirements . Conduct a thorough analysis of your warehouse operations to understand how a new system can automate and improve established processes. This analysis will help you define the specific requirements for your WMS.
- Create an implementation plan. The step-by-step plan will help you overview the whole cycle of WMS implementation and control the progress. A common WMS implementation project plan example includes several key phases, starting with planning, then analysis, then implementation, testing, training, and finally, deployment.
- Clean up data. It’s a good idea to get rid of outdated or duplicate information that can lead to errors and slow down the process of migrating data to the new WMS.
- Integrate a WMS with other systems. This greatly enriches WMS functionality and allows you to get valuable insights from both internal and external platforms.
- Test a WMS. Verify that the system can process all your data smoothly without any interruptions or delays. It is important to test the system’s interaction with third-party systems and ensure it meets the needs of end-users.
- Train employees. Comprehensive training ensures that your employees know how to use the system effectively and helps overcome potential resistance to change. Create visual and interactive manuals and step-by-step tutorials that employees can refer to when they encounter difficulties.
But one of the most important factors in successfully implementing a WMS is choosing a reliable and trusted WMS provider, especially if you opt for a custom WMS. The capabilities of your system and its successful implementation will depend directly on the expertise of your development partner.
At HQSoftware, we have extensive experience not only in creating comprehensive WMS systems but also in working with cutting-edge technologies that can enhance WMS functionality, such as Artificial Intelligence , Machine Learning , IoT , etc. Contact us to learn more about our WMS development services.
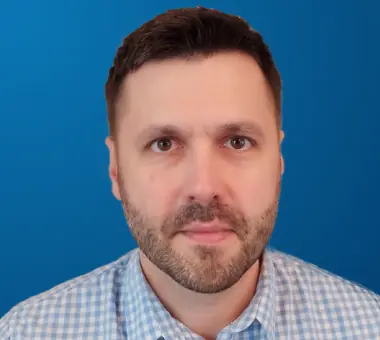
Head of Production
To ensure the outstanding quality of HQSoftware’s solutions and services, I took the position of Head of Production and manager of the Quality Assurance department. Turn to me with any questions regarding our tech expertise.
Related Posts
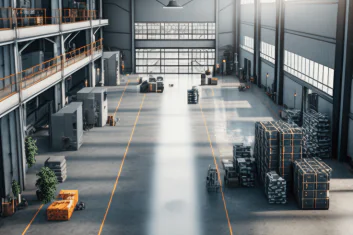
Your Name *
Your Email *
How Can We Help You? *
* Required Fields
Attach File
NDA required
I accept your privacy policy *
We are open to seeing your business needs and determining the best solution. Complete this form, and receive a free personalized proposal from your dedicated manager.
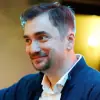
Sergei Vardomatski
We use cookies to analyze traffic, personalize site content, and for social media features. We share this data with our ad and social media partners. You can change your cookie settings and learn more here. By browsing the website you consent to our rules.
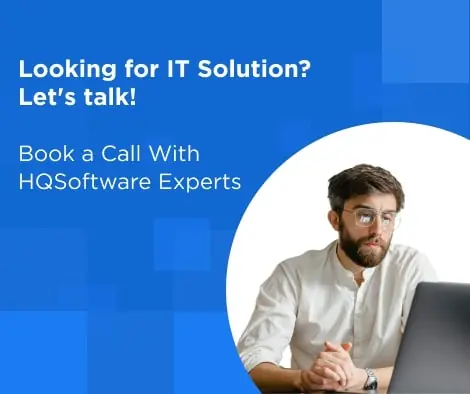
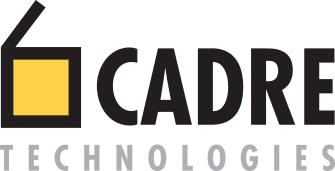
White Papers/Case Studies
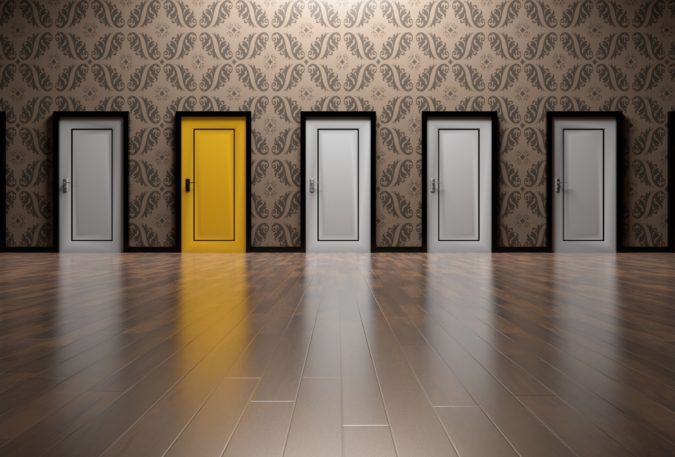
White Paper: Tips for Choosing the Best WMS Software for Your Business
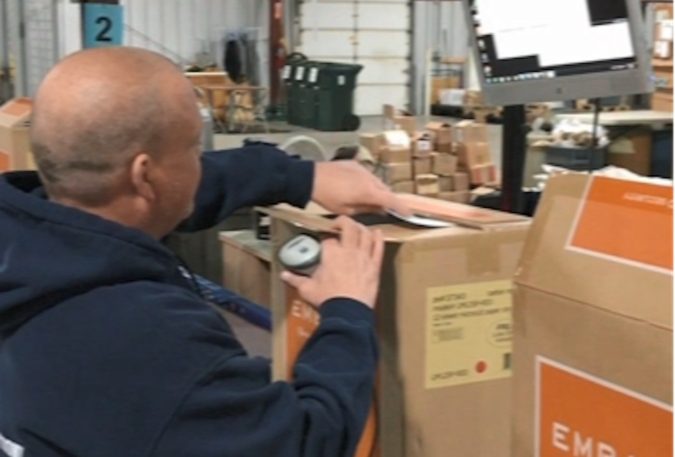
Case Study: IMG
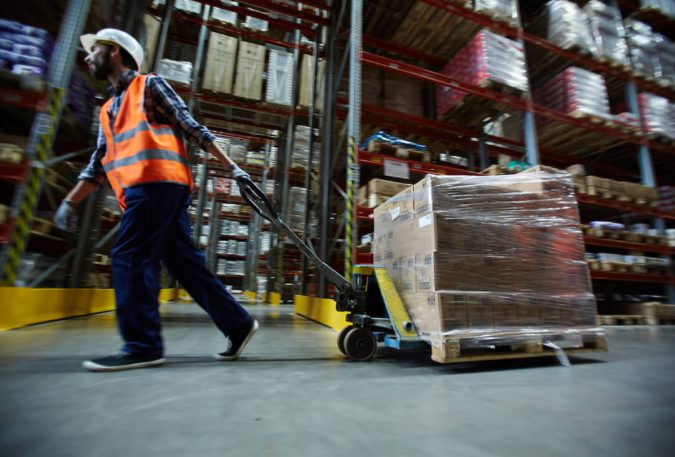
White Paper: Best Practices for Warehouse Management
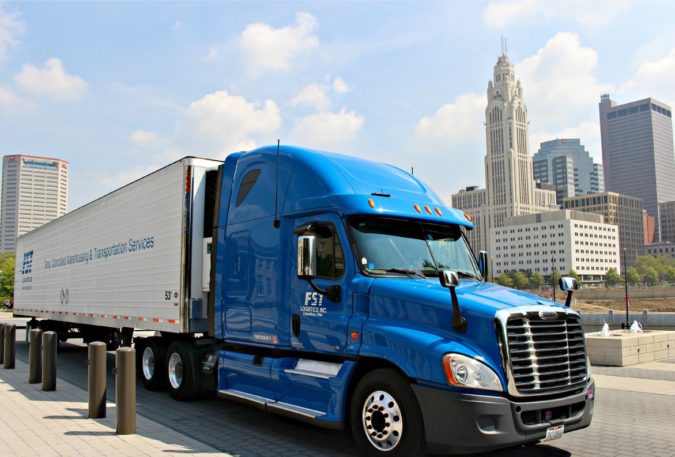
Case Study: FST
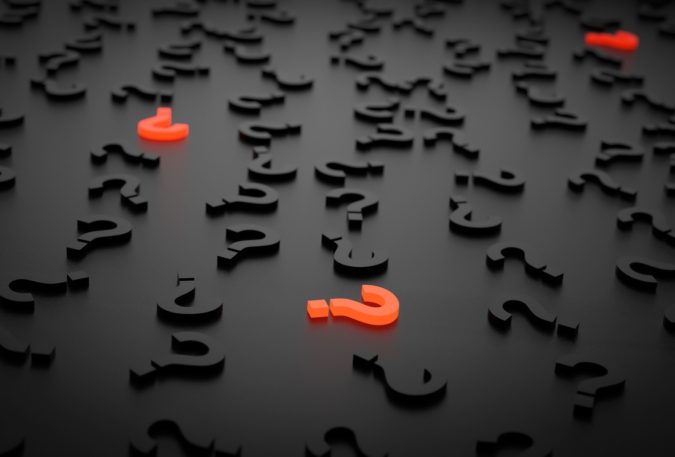
White Paper: How to Choose the Right WMS
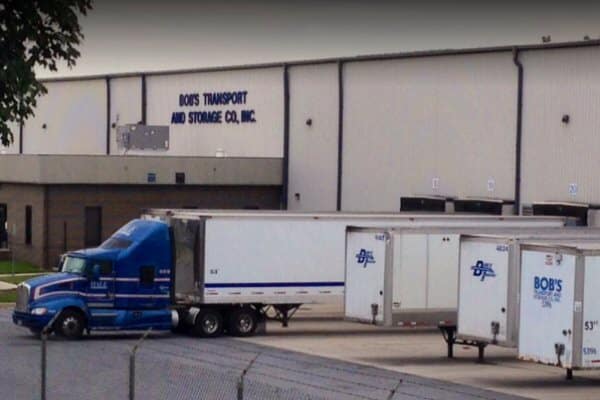
Case Study: BTS
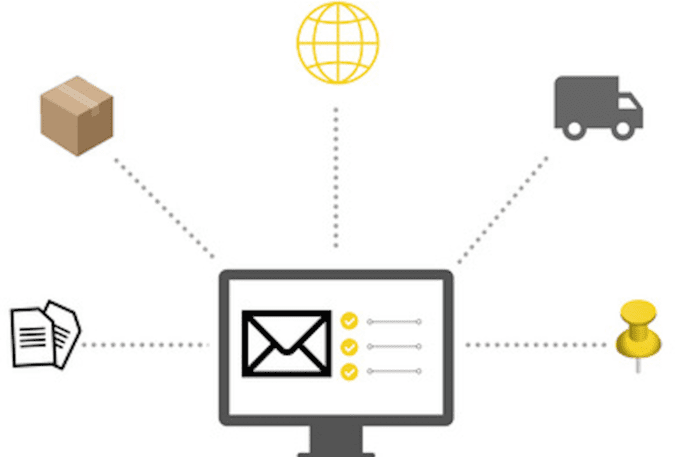
White Paper: Why Wave Pre-Planning Will Improve Your Warehouse Management
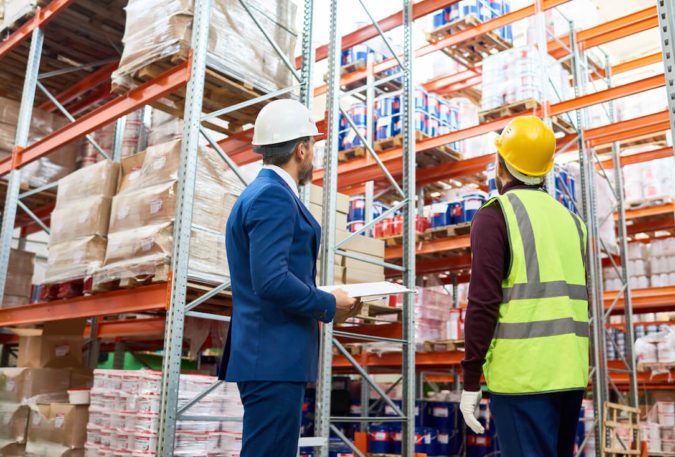
Case Study: Axis Global
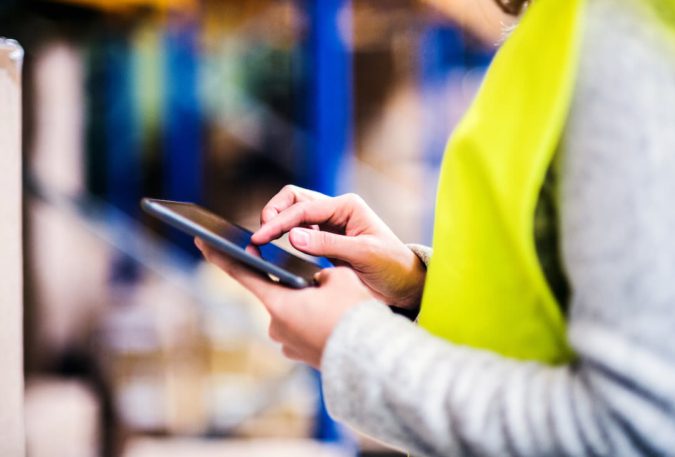
Case Study: TAGG Logistics
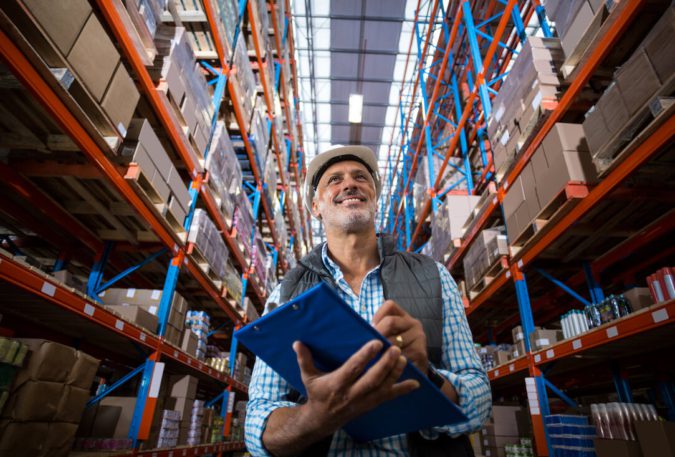
Case Study: Bonded Logistics
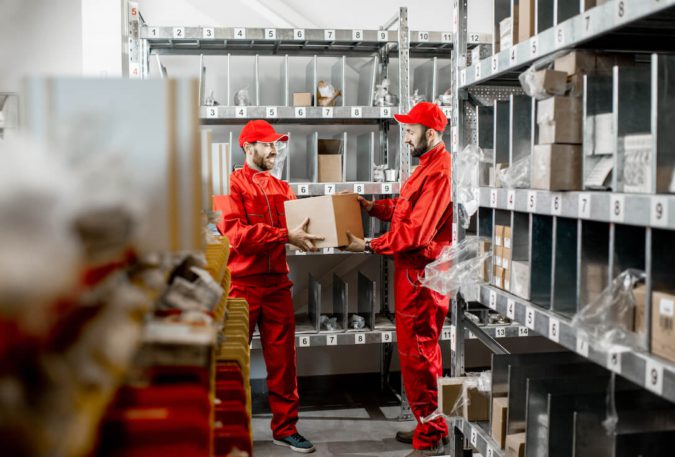
White Paper: Guide for Implementing WMS Software
Are you looking for a Warehouse Management System? Request a demo today
Ready to Learn More About Cadre’s WMS Solutions? Request a demo today
Success Stories
“Cadence WMS provides us real time data to allow us to monitor our daily activities in all of our warehouses. It has provided us the visibility to flex our staff across our network and also provides our clients the transparency they want into our daily operations.”
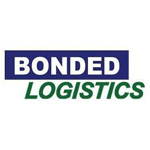
“We’ve used Cadre products for quite some time now. Their willingness to work with us to customize and connect to other systems and provide seamless solutions for our customers through their online tools has been invaluable. Logiview has been a cornerstone of our logistics platform for many years. ”
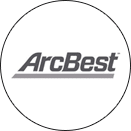
“Cadre’s software allows us to meet the changing requirements of our warehouse clients and helps us remain competitive with new opportunities. The people are great to work with because they are responsive and understand our business.”
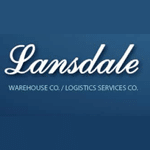
Recent Articles
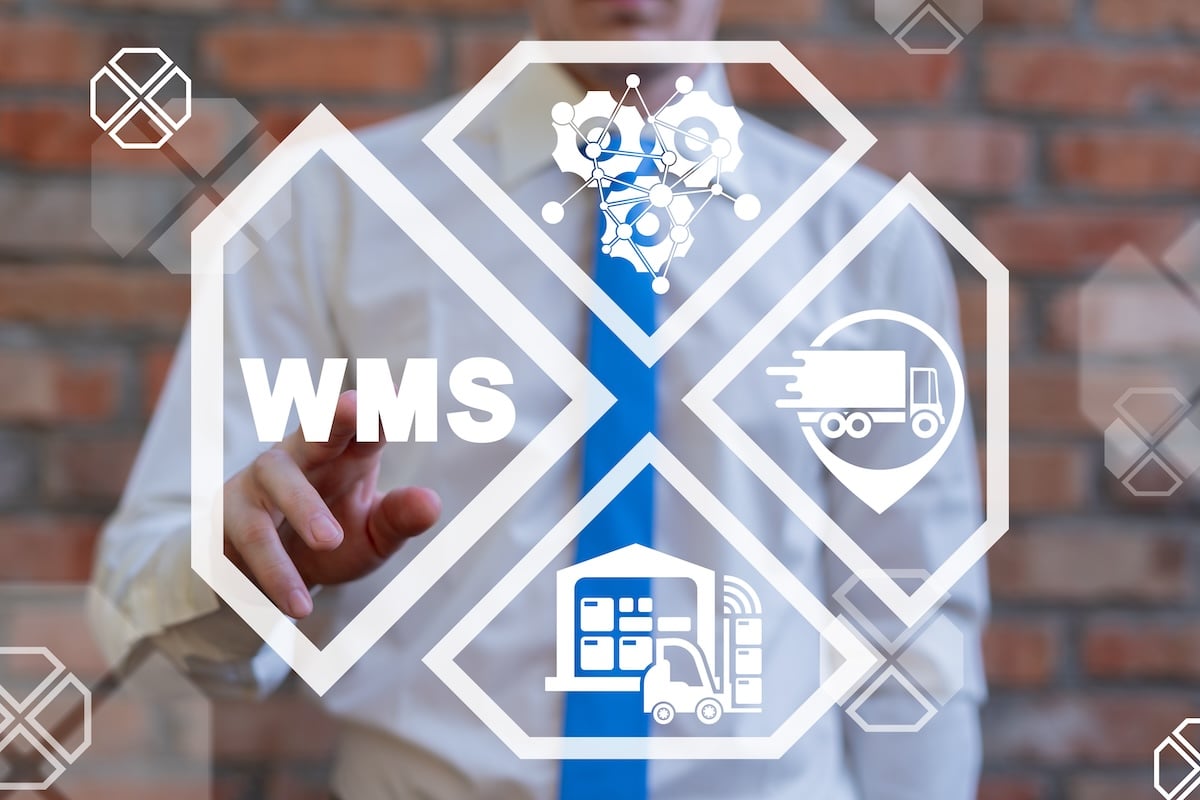
Efficient WMS Integration: Streamlining Your Warehouse Operations
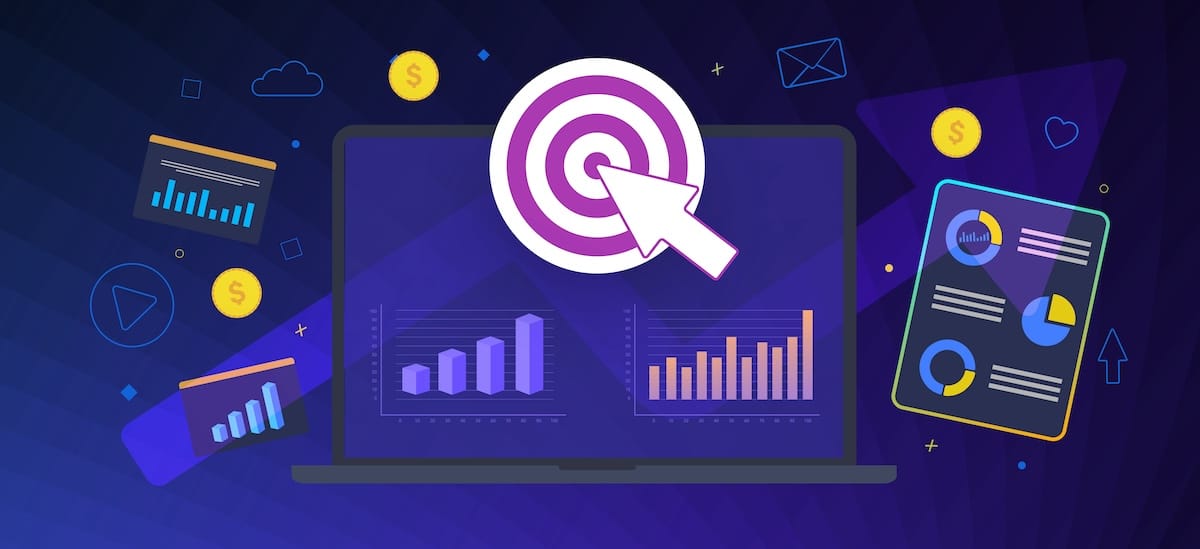
Key Performance Indicators (KPIs) for Ecommerce Fulfillment
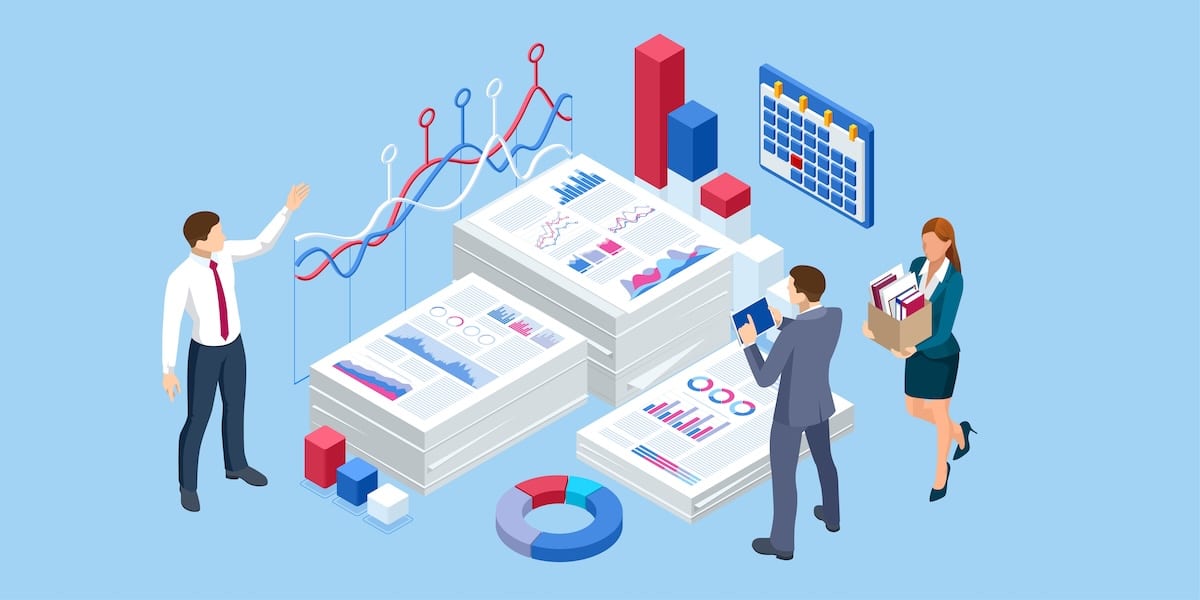
Supply Chain KPIs: A Guide to Mastering SCM Efficiency
Denver Office 7900 East Union Avenue Suite 1007 Denver, CO 80237 303-217-7030
Lenexa Office 8371 Melrose Drive Lenexa, KS 66214 913-492-5700
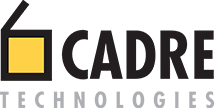
- By Job Role
Privacy Policy | Cookie Policy | Terms and Conditions |© 2024 Cadre Technologies. All rights reserved.

Facilities Management Advisor
Practical Facilities Tips, News & Advice.
Design and Construction, Human Resources, Sustainability/Business Continuity
Amazon: a case study in how strategic warehouse placement can drastically reduce shipping times.
Updated: Apr 27, 2022
Few businesses can compete with Amazon—not just as a retailer, but also in shipping, data management, and even warehousing. To become the juggernaut it is today, Amazon has evolved to provide many of its necessary service needs.
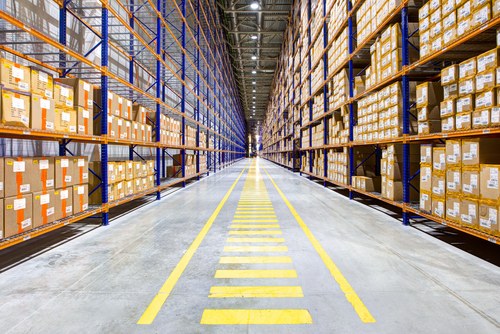
For its warehousing needs alone, for example, Amazon reportedly owns nearly 319 million square feet of fulfillment center floor space in the United States. Though that is a massive number, consider that Amazon’s warehouse placement is designed to keep shipping times as low as possible. In other words, Amazon warehouses have been strategically placed all over the country.
Strategic warehousing allows Amazon to ensure that goods are already nearby when a customer places an order. It also enables the company to focus on efficiency and cost-effectiveness for shipping. This is how Amazon can offer free next-day or two-day shipping.
With these facts in mind, let’s look at how strategic warehouse placement can help other companies reduce their shipping times.
Less Time on the Road
Transportation occupations are some of the most dangerous jobs . In 2018 alone, workers’ injuries and illnesses in transportation and material moving accounted for 20% of all injuries. These statistics also include related transportation roles, such as mechanics and transport-related warehouse jobs.
Strategic warehouse placement reduces the time that trucks and other transport options need to be used. Shorter travel periods can also decrease the time that vehicles are on the road and, thus, can help with driver fatigue. Furthermore, using strategic warehouse placement in high-volume areas will:
- Ensure the fastest shipping times by decreasing the hindrance of supply bottlenecks.
- Keep high-volume items well-stocked, eliminating unplanned shipments.
- Benefit from courier usage to deliver goods where larger delivery options may struggle (such as residential or historic areas).
Additionally, warehouses built in strategic locations can reduce the load of other warehouses. Not only does this decrease shipping times in the area, but it also increases the efficiency of the once-beleaguered warehouse.
Optimization In, Optimization Out
A strategically placed warehouse is optimized inside and out. Shipping costs and speeds are affected by more than the distance. Without optimized functions and employees, warehouses and shipping will suffer.
No matter the industry, however, warehouse safety is essential. Injured workers won’t be working, and could be costing money. Perhaps more importantly, a poorly managed warehouse will drag down morale, handling speeds, and efficiency. Mistakes will pile up, just like the hazards that surround the workers.
To achieve an optimized and safe warehouse, the following guidelines must be followed:
- Rigid daily protocols, especially around safety, awareness, and internal assistance.
- Incentivize safe efficiency, not bottom-line numbers. Breakneck speed is only temporarily sustainable.
- Storage and organization pipelines must always be adhered to.
- Use optimized scheduling to keep shipping and receiving on different shifts.
Each of the above-mentioned tips not only ensures smooth operations, but also keeps the employees and their safety in mind. Unless the warehouse is entirely automated, optimization must consider the humans within.
Technology and automation should still be used, but focus on systems that work with the human element in mind. Use machine learning and logic-oriented technologies to study your warehouse statistics. Optimize how the team at hand works, instead of forcing them into a “pre-optimized mold.”
In short, if the warehouse and its employees are optimized, then shipping times too will be optimized.
Strategic Location Keeps the Goods Close By
Today’s supply chain management goals are meant to ensure customer satisfaction . Two-day or next-day shipping is no longer a leg up over other services. Rapid shipping is now the expected offering. Larger fleets or faster processing lines alone won’t speed up shipping times if the warehouse is located across the country.
Therefore, strategically placing warehouses ensures that goods are always within your customers’ desired shipping times. Amazon’s vast number of warehouses allow for same-day shipping in some areas. Often, within hours of an online order, the purchased item is at the customer’s door. It doesn’t get much faster than that. This is achieved by the vast amount of strategic square footage Amazon devotes to customer satisfaction.
Of course, not every business can afford millions of feet of storage space. Still, a company can decide where best to locate the storage it can afford. For example, warehouses next to major shipping hubs can take better advantage of increased shipping options. Major metropolitan areas benefit from having warehouses nearby, especially in high-volume areas.
Large metropolitan areas also provide other strategic benefits, including:
- Better access to existing infrastructure.
- A more significant potential labor pool.
- A greater area of serviceable customers, plus the ability to offer reduced shipping times to a major section of customers.
Keeping warehouses close to the manufacturing locations can reduce shipping times on the back end. However, strategically located warehouses next to major shipping hubs can benefit from nearly the same back-end fulfillment, and provide customers with even quicker delivery times.
Final Thoughts
Warehouses use massive amounts of capital, both in start-up mode and during normal operations. They can be dangerous, especially with a high-velocity mix of employees and machinery. Warehouse use and placement must therefore be strategic to maximize efficiency at all levels. From employee safety to customer satisfaction, where you place a warehouse has long-existing ramifications.
Companies have found success working backward with the customer as the end goal. Strategically located warehouses allow logistics to focus on the fastest route to the customer. Be it extra stock for a high-volume item, or simply shorter shipping times from the warehouse to the customer’s door, warehouse placement is critical.
Rachel Perez is an Outreach Associate with North Star Inbound and wrote this piece working in tandem with BigRentz . An honors graduate of New York University, she is passionate about writing about business, e-commerce, construction, and travel. When not writing, she enjoys spending time in the Florida sunshine.
Leave a Reply Cancel reply
Your email address will not be published. Required fields are marked *
Save my name, email, and website in this browser for the next time I comment.
- Other Items...
- Back to Top
- Go to "Contact Us" Page
Warehouse Logistics Challenges? UWB Says, “Hold My Beer”
May 16, 2024
The Challenge
Logistics can be a challenge for any company, but the Budweiser Budvar Brewery had recently found itself facing a particular puzzle. Crafted exclusively in České Budějovice (Budweis) in the Czech Republic, the brewery produced ten different beer varieties, each with labels in dozens of languages, and shipped to 76 countries. This diversity created an intimidating 360 product combinations and the warehouse had to accommodate more than 20,000 pallets of two different container sizes for both indoor and outdoor facilities.
Before exploring Ultra-Wideband solutions, Budweiser Budvar had relied on a passive RFID system. The RFID anchors were mounted on forklifts with about ten tags per tracking position. It worked for a while, but it eventually fell short in some critical aspects:
- Dependability: The system experienced reliability issues, leading to disruptions in operations.
- Maintenance Cost: Maintaining and scaling the RFID infrastructure was expensive.
- Efficiencies: The system's limitations resulted in operational waste and delays.
- Lack of Precision: It did not consistently provide accurate, real-time location data for goods. The brewery struggled to leverage data for analytics.
The Solution
Budweiser Budvar Brewery looked for a game-changing solution and found it in Sewio's UWB-based Real-Time Location System (RTLS). UWB uses time of flight (ToF) to measure the distance to a tag. Multiple methods for ToF improve the accuracy of measurement and reduce infrastructure costs.
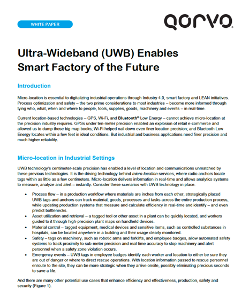
Learn How UWB enables micro-location to transform factories so manufacturers can optimize processes and safety.
Read the White Paper
Two-way ranging (TWR) and time difference of arrival (TDoA) eliminate the impacts that reflections from walls and machinery (multi-path) have on signal strength. Other ranging methodologies in UWB include phase difference of arrival (PDoA) and reversed TDoA (RTDoA), offering benefits for various types of deployments. These different ranging techniques can be used to identify the distance and direction (vector) of an object.

Here's how this technology transformed the Budvar warehouse management:
- Efficient Deployment: Installing Sewio's UWB-based system took about a month. Afterward, engineers took about six months for seamless integration into their existing enterprise resource planning (ERP) systems.
- Comprehensive Coverage: To cover a sprawling 15,000 square meters (17,940 square yards) across the indoor and outdoor warehouse facilities, Budweiser Budvar deployed 70 UWB anchors and equipped 15 forklifts with tags, achieving an impressive positional accuracy of 30 centimeters.
Results and Benefits
The installation and integration of Sewio's UWB-based RTLS yielded substantial improvements:
- 19 Percent Better Uptime: Compared to the legacy RFID system, the UWB solution delivered a 19 percent increase in uptime, minimizing disruptions in warehouse operations.
- 19 Percent Better Warehouse Operations: Budweiser Budvar Brewery optimized its warehouse space more effectively, resulting in a 19 percent increase in overall warehouse utilization.
The adoption of UWB technology marked a significant turning point for Budweiser Budvar Brewery's warehouse management. By overcoming the limitations of their legacy RFID system and embracing UWB-based RTLS, they not only improved operational efficiency but also gained the real-time, high-precision location data needed for advanced analytics. This success story underscores the power of UWB technology in enhancing business operations, and as the ecosystem of UWB Technology , and solution providers expands, we can expect even more groundbreaking micro-location services to shape the future of various industries.
Have another topic that you would like Qorvo experts to cover? Email your suggestions to the Qorvo Blog team and it could be featured in an upcoming post. Please include your contact information in the body of the email.
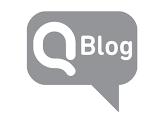
About the Author
Qorvo blog team.
One part technical, one part content, and one part strategic, our small team is dedicated to connecting you with helpful, timely insights from some of the bright minds at Qorvo.
Related Content
Ultra-wideband and ccc® digital key - enabling a better driving experience, noccela and ultra-wideband take industry and sports to the next level, ultra-whatband ultra-wideband, bringing the bible to life with ultra-wideband, how does ultra-wideband work learn from qorvo experts, ultra-wideband and contact tracing 101, lights, camera, action uwb is the star supporter in le premier royaume, location, location, location: the road to ultra-wideband, ultra-wideband for dummies, qorvo acquires uwb software provider 7hugs labs sas, qorvo ultra-wideband helps the world get back to work, qorvo acquisition of decawave named deal of the year by the irish times, qorvo completes acquisition of decawave, qorvo online design summit: ultra-wideband (uwb) use cases & benefits, the future is uwb, ultra-wideband (uwb) enables smart factory of the future, getting back to basics with ultra-wideband (uwb).
Qorvo uses cookies and other technologies to enhance your experience, display customized content, secure our website and help us understand how our website is used. For details, please see our Privacy Notice .
COVID-19 Update
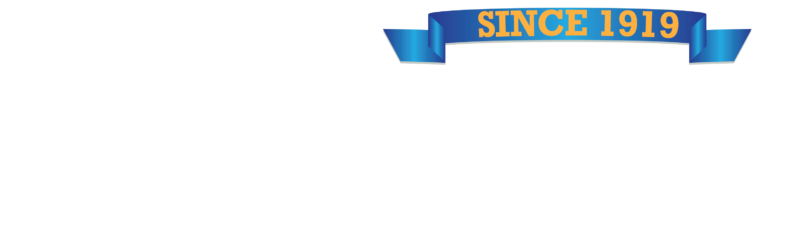
Santa Clarita Valley's #1 Local News Source
Reducing errors and increasing speed: the ocr advantage in warehousing, sponsored post.
- May 14, 2024
Introduction to OCR Technology in Warehousing
Step into the future of warehouse operations where errors vanish, and efficiency soars. Imagine a world where technology seamlessly integrates with logistics to revolutionize the way we work. Enter OCR technology – a game-changer in the realm of warehousing. Today, we delve into how Optical Character Recognition (OCR) is transforming warehouses by reducing errors and increasing operational speed like never before. Let’s explore this cutting-edge innovation together!
Impact of OCR on Error Reduction
Imagine a warehouse where human errors in data entry lead to misplaced items, delayed shipments, and frustrated customers. This is where OCR software technology steps in as a game-changer. By automatically scanning and deciphering text from labels, invoices, and documents with near-perfect accuracy, OCR drastically reduces the risk of manual mistakes. With OCR seamlessly integrated into warehouse operations, the likelihood of picking the wrong item or shipping to the incorrect address diminishes significantly. Every barcode scanned or text recognized by OCR becomes a step towards error prevention. The result? Improved inventory management, enhanced order fulfillment accuracy, and ultimately higher customer satisfaction levels. By harnessing the power of OCR to streamline processes traditionally prone to errors caused by human intervention, warehouses can operate more efficiently and effectively than ever before. The impact is not just about reducing mistakes; it’s about elevating operational excellence to new heights through automation and digitization.
Enhancing Operational Speed with OCR
In the fast-paced world of warehousing, efficiency is key to success. One technology that has revolutionized operational speed is Optical Character Recognition (OCR). By digitizing and automating data entry processes, OCR reduces manual errors and speeds up information processing. By scanning and interpreting text from various documents like shipping labels or packing slips, OCR eliminates the need for manual data input. This not only saves time but also minimizes human error, leading to smoother operations. With OCR, warehouses can streamline inventory management, order processing, and shipment tracking. The ability to quickly extract and analyze crucial information accelerates decision-making processes. Moreover, by integrating OCR with other warehouse technologies such as barcode scanners or RFID systems, companies can further enhance their operational speed and accuracy. As a result, businesses can meet customer demands more efficiently while maintaining high levels of productivity in their operations.
Case Studies and Success Stories of OCR Implementation
Picture this: a bustling warehouse where efficiency is key. Thanks to OCR technology, inventory management has been revolutionized. Take Company X, for example. By implementing OCR in their warehousing operations, they saw a significant decrease in errors and an increase in operational speed. Company Y also jumped on the OCR bandwagon with impressive results. Their order processing time was cut in half, leading to happier customers and improved overall productivity. Let’s not forget about Company Z, who used OCR to streamline their receiving process. This allowed them to accurately track shipments and reduce manual data entry errors. These success stories highlight the transformative power of OCR in warehouses across different industries. The future looks bright as more businesses embrace this technology for enhanced efficiency and accuracy in their operations.
Future Trends in OCR and Warehouse Automation
As technology continues to evolve at a rapid pace, the future of OCR and warehouse automation looks promising. One emerging trend is the integration of artificial intelligence into OCR systems, allowing for more advanced data processing and analysis capabilities. This will enhance accuracy and efficiency in warehouse operations. Another exciting development is the use of robotics alongside OCR technology to automate tasks like inventory management and order fulfillment. These collaborative systems can significantly increase productivity while reducing human error. Furthermore, we can expect to see continued advancements in cloud-based OCR solutions, enabling real-time data access across multiple devices and locations. This will streamline communication within warehouses and improve overall operational visibility. The future holds endless possibilities for OCR and warehouse automation as businesses strive to stay competitive in an increasingly digital world.
Best Practices for Implementing OCR in Warehousing Operations
Implementing OCR technology in warehousing operations can revolutionize the way businesses handle inventory management, reduce errors, and increase operational speed. By following best practices such as conducting a thorough assessment of current processes, selecting the right OCR software provider, providing adequate training to employees, and continually monitoring and optimizing the system for maximum efficiency, companies can truly unlock the full potential of OCR in their warehouses. As technology continues to advance and automation becomes more prevalent in supply chain management, incorporating OCR into warehousing operations will be crucial for staying competitive in today’s fast-paced business environment. Embracing these best practices will not only streamline operations but also pave the way for future growth and success. The time is now to harness the power of OCR and reap its benefits in your warehouse operations.
Related To This Story
Navigating the golden state: essential riverside moving tips for a smooth transition, future outlook: innovations in venture capital portfolio management, making sense of electronic health records (ehrs) with nlp, five benefits of hiring a moving company, optimizing user experience (ux) for e-commerce websites, how to combine loan affiliate marketing and finance tips to make money online, latest news.
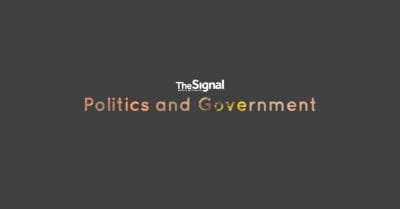
Garcia applauds House passage of bipartisan Israel bill
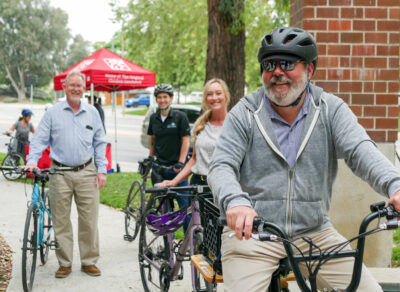
Pedal to the metal: Santa Clarita hosts annual Bike to Work Challange
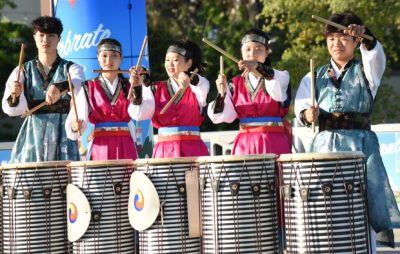
Celebrate Series: South Korea
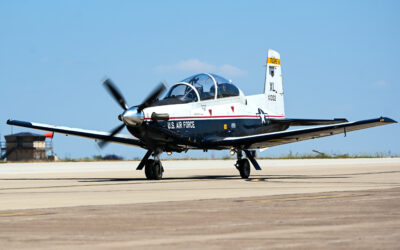
Air Force instructor pilot dies after ejection seat activates during ground operations
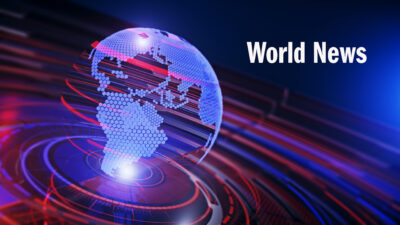
Slovak prime minister shot, in life-threatening condition
Sign up for the, morning rundown.
Filled with the top stories to start your day, and emergency news alerts.
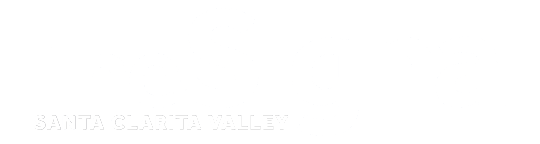
25060 Avenue Stanford, St. 141
Valencia, CA, 91355
Main Desk: 661-259-1234
Newsroom: 661-255-1234
Advertising: 661-287-5564
Have a news tip? Let us know!
News Sections
- Coronavirus
- Environment
- Politics & Government
More Sections
- Video + Podcasts
- Sunday Signal
- Subscribe to Print
- Classified Ads
- Event Calendar
Post comment
or continue as guest
- Today's news
- Reviews and deals
- Climate change
- 2024 election
- Fall allergies
- Health news
- Mental health
- Sexual health
- Family health
- So mini ways
- Unapologetically
- Buying guides
Entertainment
- How to Watch
- My watchlist
- Stock market
- Biden economy
- Personal finance
- Stocks: most active
- Stocks: gainers
- Stocks: losers
- Trending tickers
- World indices
- US Treasury bonds
- Top mutual funds
- Highest open interest
- Highest implied volatility
- Currency converter
- Basic materials
- Communication services
- Consumer cyclical
- Consumer defensive
- Financial services
- Industrials
- Real estate
- Mutual funds
- Credit cards
- Balance transfer cards
- Cash back cards
- Rewards cards
- Travel cards
- Online checking
- High-yield savings
- Money market
- Home equity loan
- Personal loans
- Student loans
- Options pit
- Fantasy football
- Pro Pick 'Em
- College Pick 'Em
- Fantasy baseball
- Fantasy hockey
- Fantasy basketball
- Download the app
- Daily fantasy
- Scores and schedules
- GameChannel
- World Baseball Classic
- Premier League
- CONCACAF League
- Champions League
- Motorsports
- Horse racing
- Newsletters
New on Yahoo
- Privacy Dashboard
Moscow missile plant ablaze in apparent drone attack
Tomilinsky Electronic Plant research and production enterprise in Lyubertsy, Moscow Oblast, is reportedly ablaze after a drone attack on Sep. 1, according to our sister publication, Ukrainska Pravda .
The Tomilinsky plant is under sanctions by the Ukrainian government as it manufactures electronics for Russian missile systems.
The plant was attacked in an operation directed by Ukraine’s Main Intelligence Directorate (HUR), who believe they have achieved their aim, a well-informed source told Ukrainska Pravda.
The HUR has thus far refused to publicly confirm or deny its involvement. The agency’s spokesman, Andriy Yusov, commented that Russian state media had issued "a mountain" of lies about the attack and said that "cotton has really blossomed" at the plant in Lyubertsy on Friday.
Explosions in Russia or Russian-held territory far behind the frontlines are popularly referred to in Ukraine as “bavovna”, or “cotton” in English.
Drones tried to attack the Russian capital on Sept. 1 , said Moscow mayor Serhiy Sobyanin, adding that one drone was allegedly shot down near Lyubertsy.
We’re bringing the voice of Ukraine to the world. Support us with a one-time donation, or become a Patron !
Read the original article on The New Voice of Ukraine
Recommended Stories
Dolphins owner stephen ross reportedly declined $10 billion for team, stadium and f1 race.
The value of the Dolphins and Formula One racing is enormous.
Welcome to the WNBA: Caitlin Clark's regular-season debut is anything but easy
Clark set the Indiana Fever’s franchise record for turnovers (10), shot 5-of-15 from the floor and struggled with the Connecticut Sun’s physical defense.
2024 NBA Mock Draft 7.0: Who will the Hawks take at No. 1? Our projections for every pick with lottery order now set
With the lottery order set, here's a look at Yahoo Sports' projections for both rounds of the 2024 NBA Draft.
What scouts think of Bronny James' NBA prospects
The biggest question looming over the NBA draft combine this week: How will Bronny James do?
2024 NFL schedule: Everything you need to know about this season's slate of games
Here's what you need to know about the 2024 NFL schedule after Wednesday night's announcement.
NFL schedule release: The top 10 must watch games of the regular season
What are the most anticipated games for this NFL season?
Fox Sports host Doug Gottlieb hired as Green Bay's coach, will reportedly still host radio show
Gottlieb's repeatedly courted controversy in his media role and will reportedly continue to host his nationally syndicated radio show while coaching Green Bay.
Fantasy Baseball Numbers Do Lie: Luck evening out will change fortunes for these 5 players
Dalton Del Don puts some fraudulent stats under the magnifying glass as we move through Week 7 of the fantasy baseball season.
Rory McIlroy files for divorce from wife Erica after seven years of marriage
On the eve of the PGA Championship, Rory McIlroy has filed for divorce from his wife, Erica.
Lionel Messi's salary, Inter Miami's payroll are MLS record highs
Even without his Apple deal and his equity in Inter Miami, Lionel Messi is making more money than all but a few MLS teams.
The Spin: Making a call on 5 slumping fantasy baseball stars
All five of these hitters were drafted highly in fantasy baseball leagues. So far, they have not lived up to their ADPs — and that's an understatement. Scott Pianowski analyzes.
Top 25 MLB free-agent rankings: Are Juan Soto, Alex Bregman and Pete Alonso helping or hurting their future paydays?
Free agency is more than 5 months away, but today's performances will shape this winter's contracts.
Where does Jared Goff’s $212M extension leave Dak Prescott and Cowboys?
In one scenario, Dallas makes Prescott the highest paid player in NFL history. In another, the Cowboys decline that commitment, at which point another team will make him the top paid player in NFL history.
Memorial Day sales 2024: Everything we know, including early deals you can shop now
Mark your calendar: The holiday weekend runs May 24-27, but you don't have to wait to save.
Why the Premier League should adopt playoffs to crown a champion
Manchester City could potentially win a fourth straight EPL title Sunday without having beaten either of its two top challengers this season.
Utility stocks are on fire — here are Wall Street analysts' top picks
Utility stocks are outperforming the broader markets. Here's a look at three top picks from analysts.
MLB Power Rankings: Phillies lead Dodgers, Braves as trio of NL contenders top this week's list
Here's a look at the rookies who have stood out on each team through the first quarter of the 2024 season.
Former MLB infielder, Little League World Series star Sean Burroughs dies at 43
The seven-year major leaguer collapsed while coaching his son's Little League game on Thursday.
Cleveland Cavaliers 2024 NBA offseason preview: There are some questions to address
The Cavaliers have some questions about frontcourt fit and the future of star scorer Donovan Mitchell.
Fantasy Baseball Weekend Preview: Substantial streaming should send you to success
Fantasy baseball analyst Fred Zinkie delivers his full-scale blueprint to finishing Week 7 on a high note.
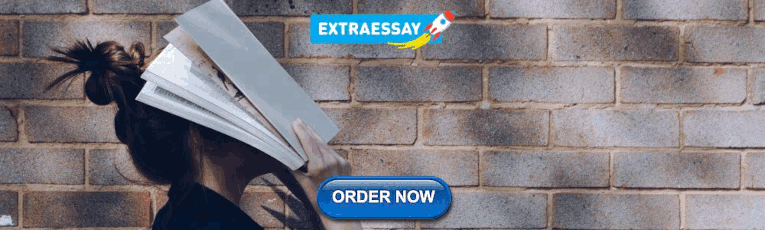
COMMENTS
Successful WMS Implementation Case Studies. Warehouse Management Systems (WMS) represent a major investment in your supply chain and operational efficiency. While it can be difficult to gauge your estimated time to value, these four cases featuring enVista clients provide a warehouse management system business case and showcase outcomes after successful WMS implementations.
BUILDING THE NO.1 LOGISTICS INFRASTRUCTURE IN THE 'SELECT-SHOP' INDUSTRY. Founded in 1977 in Yoyogi, Shibuya-ku in Tokyo, Baycrew's is a leading 'select-shop' company which provides products purchased domestically and abroad alongside its original items. Since their launch they've grown to an organization with over 5,500 employees ...
This digital warehouse-design approach lets companies experiment with different floor plans, workflows, and other variables to assess the overall impact virtually. Operations leaders can see the impact of changes in a wide range of factors, including the SKU mix, order and shipment profiles, seasonal demand spikes, productivity initiatives ...
2 | Warehousing and Logistics Case Study Warehouse and Distribution Practices Among States During COVID-19 In the 21st century, public organizations have increasingly shifted to an on-demand just-in-time model of procurement and supply chain management.This model has been useful for shrinking bud-
The comparative analysis of the individual warehouse processes' duration is also visible in this chapter. Finally, everything is rounded off with the observed conclusions of the research. 2. Overview of warehouse process optimization methods Logistics costs take an important part of the overall production costs.
Warehouse Simulation for Choosing Optimal Picking Algorithm. Kuehne+Nagel, a leading global provider of logistics solutions, was involved in planning a new warehouse for one of their clients. The warehouse would process 13K order lines or 750 picking cartons per day. The project included the development of the best algorithm for multi-order ...
Managing the Inbound Supply Chain. Penske helped this supplier minimize supply chain disruptions by designing a network that optimized mode selection, routing and analysis. Read supply chain case studies about our work with customers to create supply chain management solutions that support long-term growth and profitability.
With 35,000 SKUs, the warehouse preps and ships out 3,000 order... View case study. Dufry. Interlake Mecalux and partner Andersen Material Handling have equipped a 13,935 m warehouse in Miami, Florida, for Dufry, a travel retailer. The project includes adjustable pallet racks and the high-density push-back racking system.
Warehouse Management Software ( WMS) is like your personal assistant for managing the chaos of a warehouse. It's a fancy computer program that helps keep track of inventory, streamline processes, and make your life a whole lot easier. Think of it as the Hermione Granger of your warehouse - organized, efficient, and always on top of things.
Warehouse Automation Case Studies; Customer success stories: Over 2,000 implemented projects worldwide . As a long-term partner, we help future-proof warehouses by introducing a new era of robotic, data-driven and flexible automated solutions that deliver exceptional customer value. Our global presence and local service means we are close to ...
How one of the world's largest HVAC (Heating, Ventilation, and Air Conditioning) manufacturers adopted Hopstack's Digital Warehouse platform leading to 62% increase in outbound visibility and 25% reduction in pickup delay. Read Case Study. Here's a small glimpse of our latest case studies of Warehouse, Inventory & Order Management Solutions.
Case Studies of Successful Warehouse Optimization. Some sources consider these types of WMS, but they are not comparable to the types discussed previously. On-premise and cloud WMS are infrastructure options with corresponding pros and cons. Let's compare the two. A Major 3PL Achieved Warehouse Modernization with Cyzerg's Custom In-Transit ...
The warehouse case studies below explore how our portfolio of warehouse technology solutions and services helped companies overcome their challenges. Each case study discusses the challenges faced, solutions implemented, and results attained by our clients.
The Amazon Fulfillment Technologies (AFT) team builds and maintains the company's Warehouse Management Systems. Among these are Inventory Management Services (IMS), which facilitate warehouse processes, including inbound and outbound shipments, item picking, sorting, packaging, and inventory storage. These are essential for on-time delivery ...
Case Study Overview. In this case study, Company X, a leading logistics provider, embarked on a cloud transformation journey to modernize its warehouse management operations. The company ...
This WMS implementation case study highlights the potential for comprehensive software to enhance virtually any warehouse operation. Achieving this requires a thorough analysis of every process within your warehouse and careful consideration of how advanced technology can drive improvements. This is especially beneficial if you decide to turn ...
WMS Case Studies offers insightful information to help you with all your warehouse management systems (WMS) and software needs. Client Login; ... Increase Warehouse Accuracy and Efficiency with Cadence Warehouse Management Case Study for 3PL Bob's Transport and Storage (BTS) For more than 40 years, life has been sweet for Bob's Transport...
The aim of this paper is to study the problem areas in GI and provide solutions to increase the performance of warehousing operations. First, a conceptual framework has been developed to improve the effectiveness of warehousing operations. Second, a case study has been conducted with the help of the model to minimize the through‐put time in ...
Unless the warehouse is entirely automated, optimization must consider the humans within. Technology and automation should still be used, but focus on systems that work with the human element in mind. Use machine learning and logic-oriented technologies to study your warehouse statistics. Optimize how the team at hand works, instead of forcing ...
May 16, 2024. The Challenge. Logistics can be a challenge for any company, but the Budweiser Budvar Brewery had recently found itself facing a particular puzzle. Crafted exclusively in České Budějovice (Budweis) in the Czech Republic, the brewery produced ten different beer varieties, each with labels in dozens of languages, and shipped to ...
The hidden costs of delaying warehouse automation decisions. Warehouse automation introduces efficiencies that enable organizations to increase productivity, respond faster to orders, and increase storage density. However, securing the capital required to support these initiatives is a hurdle some organizations struggle to overcome.
The WES is the "brain" of the system, sequencing and regulating the release and flow of orders into the facility. FlexSim's Process Flow tool was used to replicate the WES logic—Bastian Solutions created an algorithm using Process Flow activity blocks to evaluate the system's capacity against the orders sitting in the pool, and then ...
Case Studies and Success Stories of OCR Implementation. Picture this: a bustling warehouse where efficiency is key. Thanks to OCR technology, inventory management has been revolutionized.
Climate warming is a common concern around the world. Achieving carbon reduction within the warehouse is a problem that needs to be addressed in the layout of the green warehouse. This paper builds a soft path model to study the impact of the improved systematic layout planning method on carbon reduction in warehouses from a low carbon economy perspective. This paper considers two main ...
Main page; Contents; Current events; Random article; About Wikipedia; Contact us; Donate
A residential and industrial region in the south-east of Mocsow. It was founded on the spot of two villages: Chagino (what is now the Moscow Oil Refinery) and Ryazantsevo (demolished in 1979). in 1960 the town was incorporated into the City of Moscow as a district. Population - 45,000 people (2002). The district is one of the most polluted residential areas in Moscow, due to the Moscow Oil ...
Tomilinsky Electronic Plant research and production enterprise in Lyubertsy, Moscow Oblast, is reportedly ablaze after a drone attack on Sep. 1, according to our sister publication, Ukrainska Pravda. The Tomilinsky plant is under sanctions by the Ukrainian government as it manufactures electronics for Russian missile systems.
Kasimovskoye shosse, 3Ж, Malakhovka Township, Lubertsy City District, Moscow Region, 140030