Got any suggestions?
We want to hear from you! Send us a message and help improve Slidesgo
Top searches
Trending searches
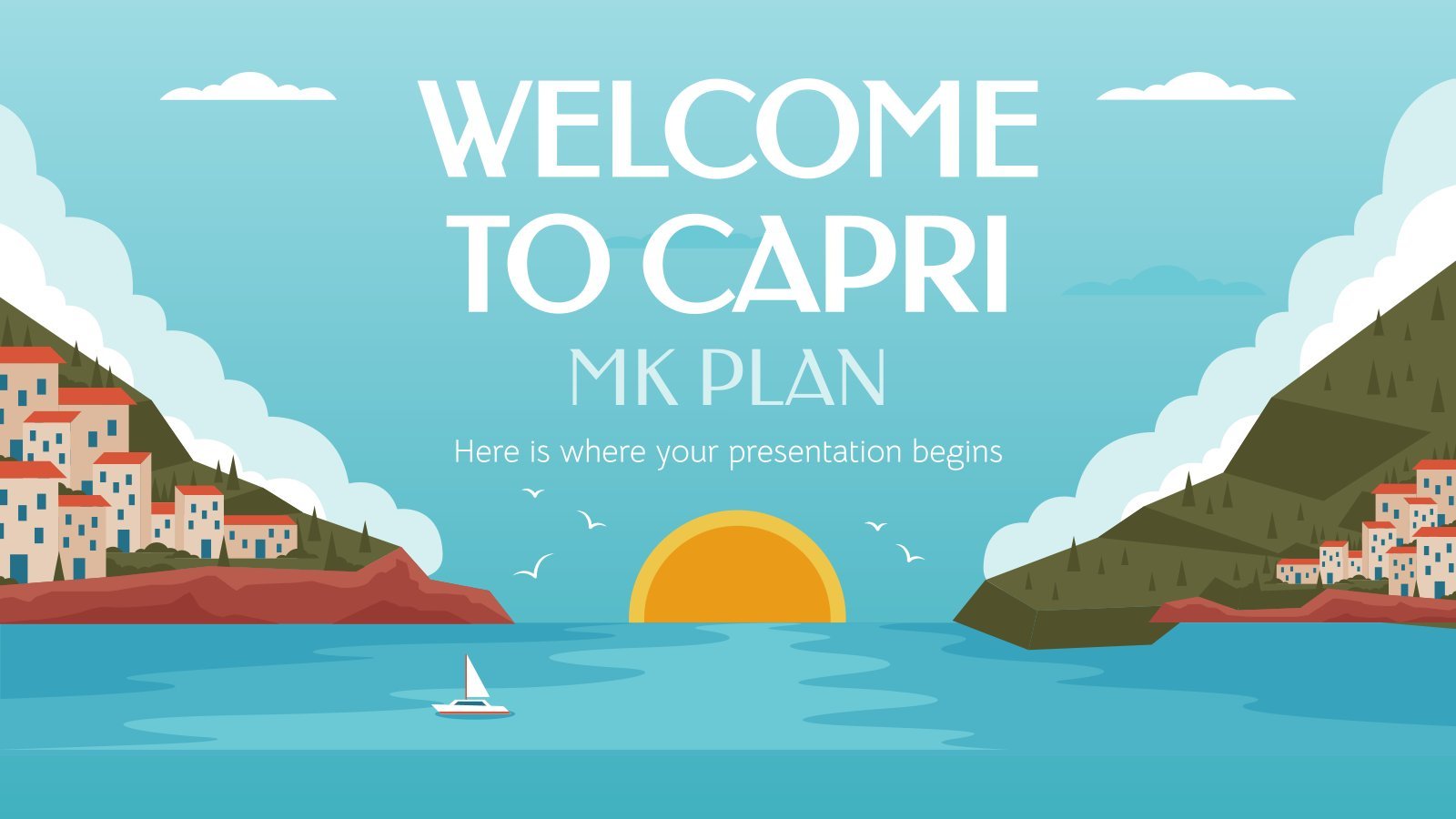
11 templates
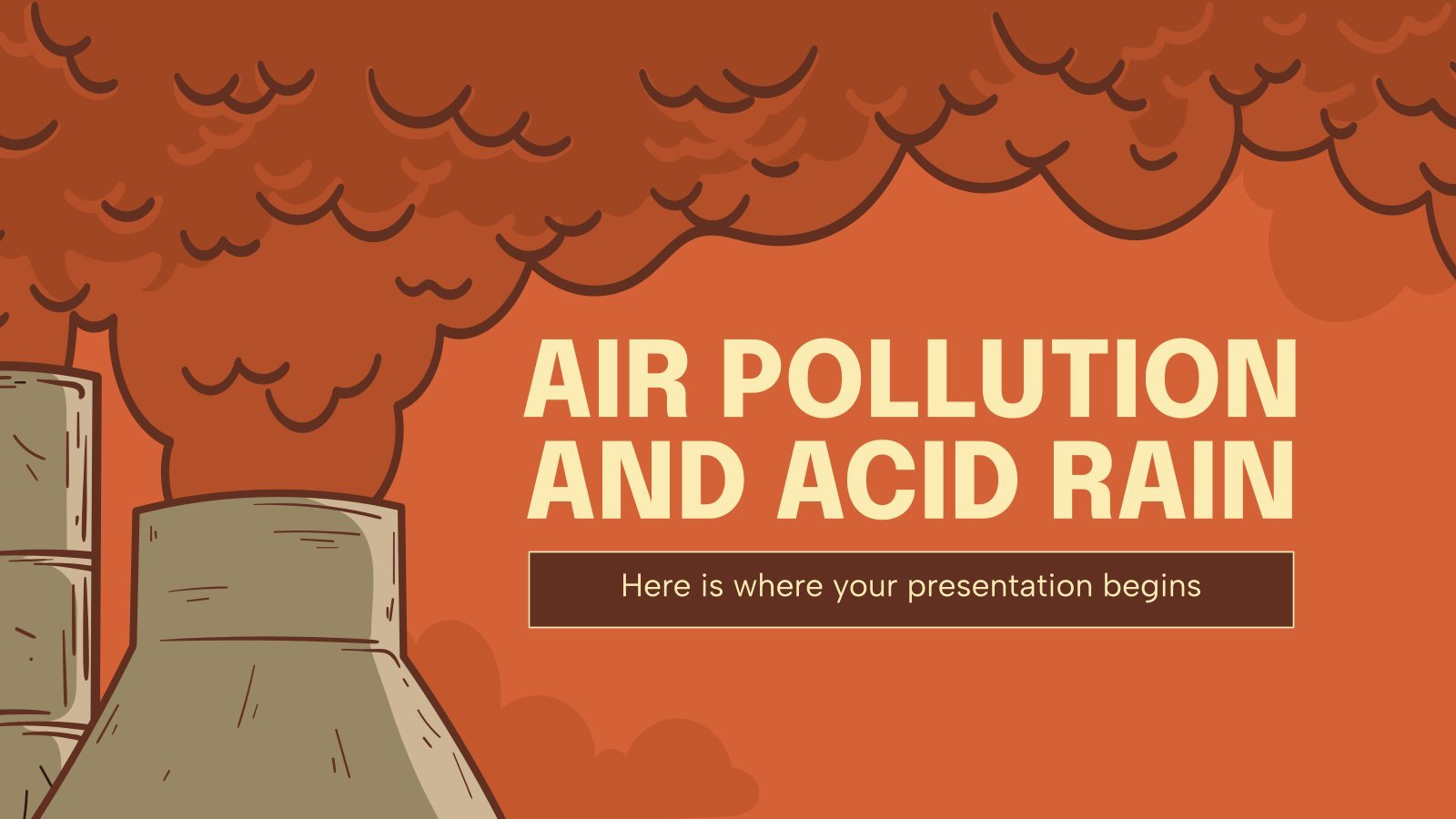
8 templates
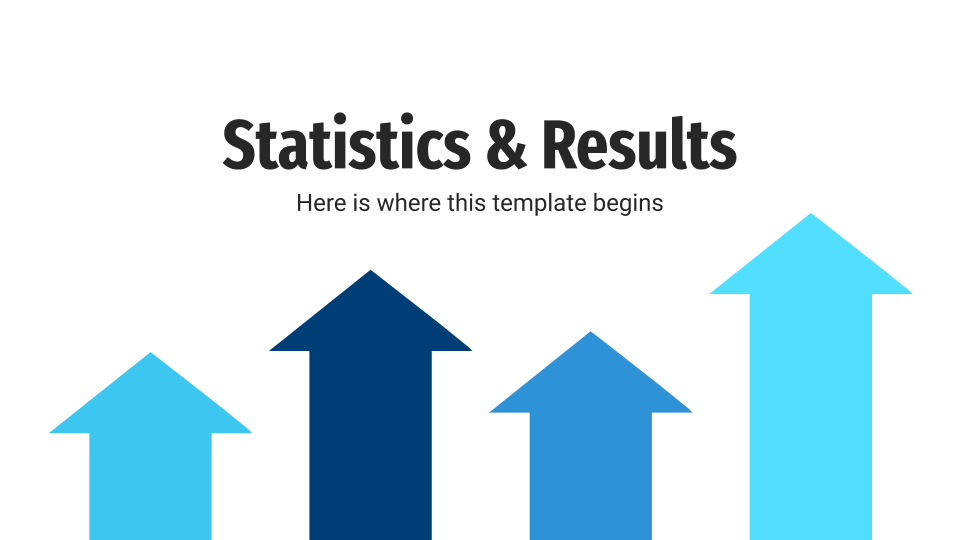
25 templates
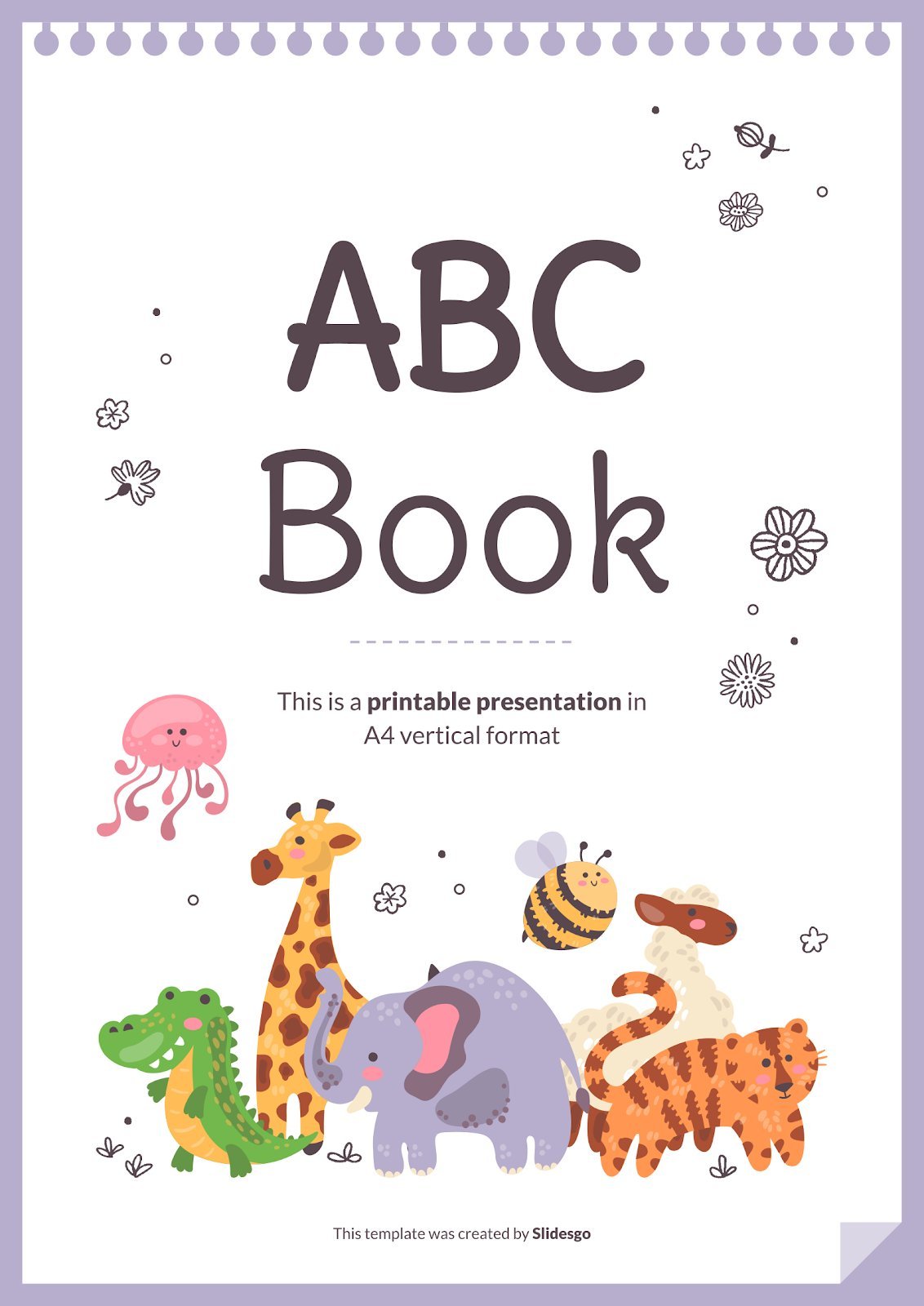
9 templates
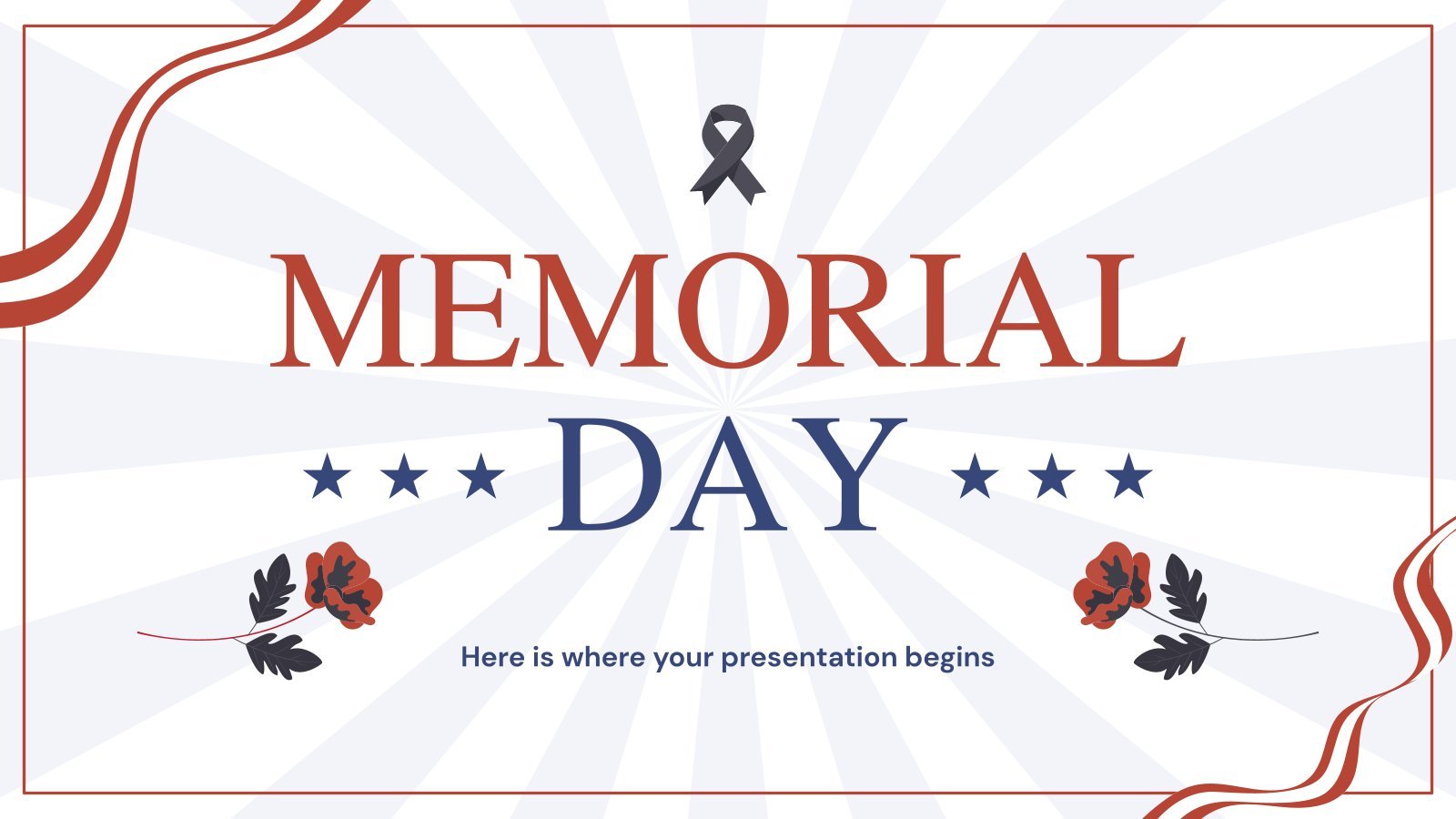
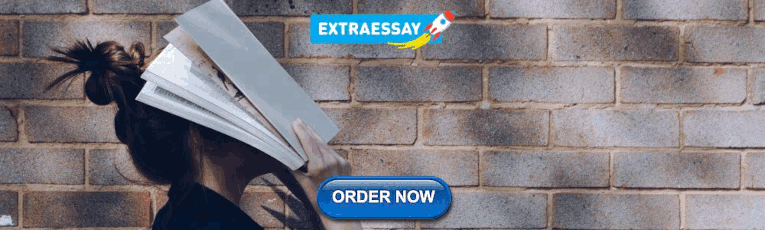
memorial day
12 templates
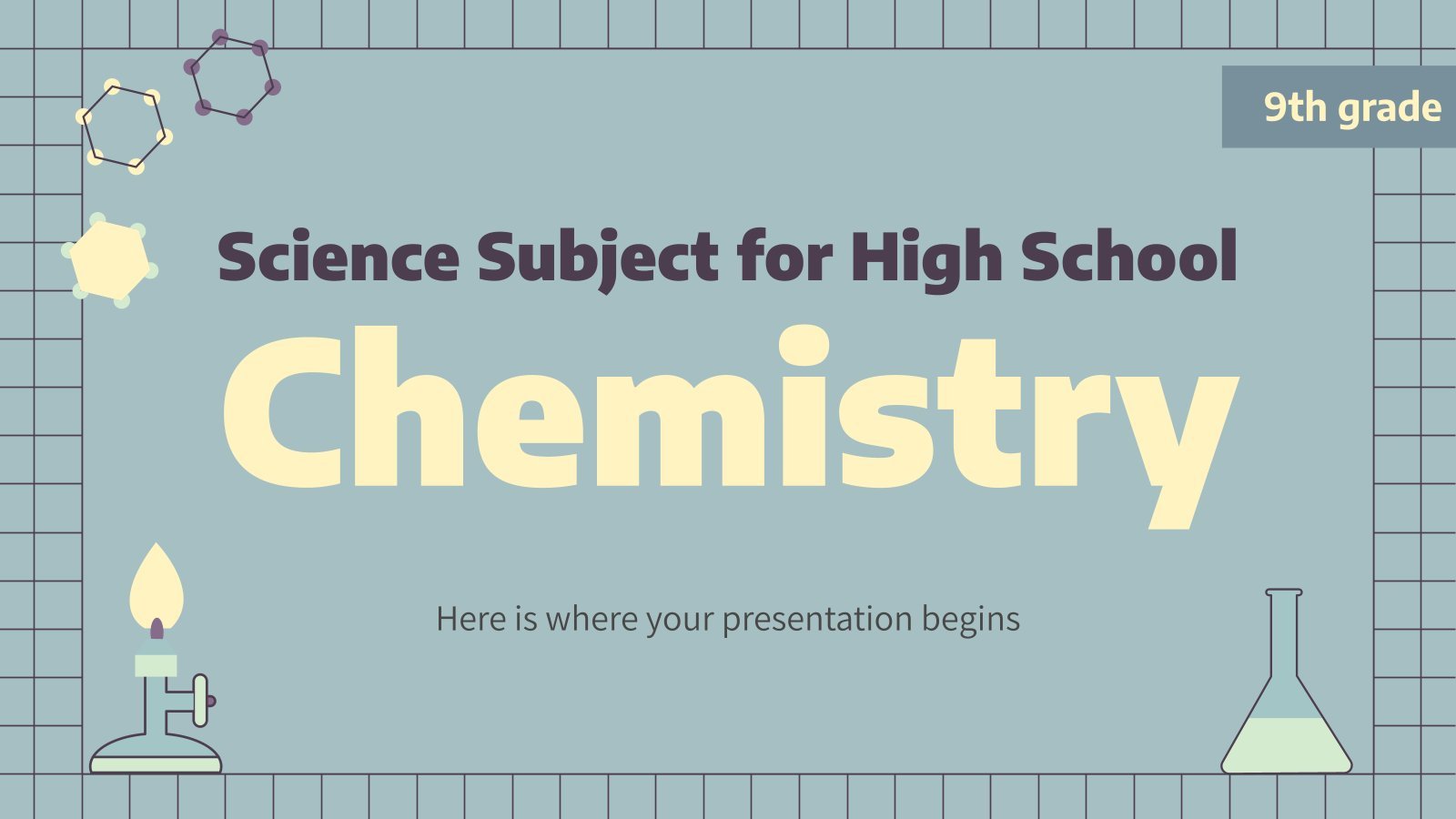
39 templates
Quality Control Required Documentation
Quality control required documentation presentation, free google slides theme and powerpoint template.
Whenever we purchase a product, we want it to last long, and arrive in perfect condition. Quality control ensures that. What about the required documentation in order to be given the "OK"? It's an important topic in businesses, so make sure to have a clear slideshow that explains everything. You might want to use this template, because its design is great! You may define it as abstract, but that's not bad! That, for us, means "eye-catching". Check out the slides and think of the ways you could customize their elements so that your audience is satisfied with your speech.
Features of this template
- 100% editable and easy to modify
- 35 different slides to impress your audience
- Contains easy-to-edit graphics such as graphs, maps, tables, timelines and mockups
- Includes 500+ icons and Flaticon’s extension for customizing your slides
- Designed to be used in Google Slides and Microsoft PowerPoint
- 16:9 widescreen format suitable for all types of screens
- Includes information about fonts, colors, and credits of the resources used
How can I use the template?
Am I free to use the templates?
How to attribute?
Attribution required If you are a free user, you must attribute Slidesgo by keeping the slide where the credits appear. How to attribute?
Related posts on our blog.
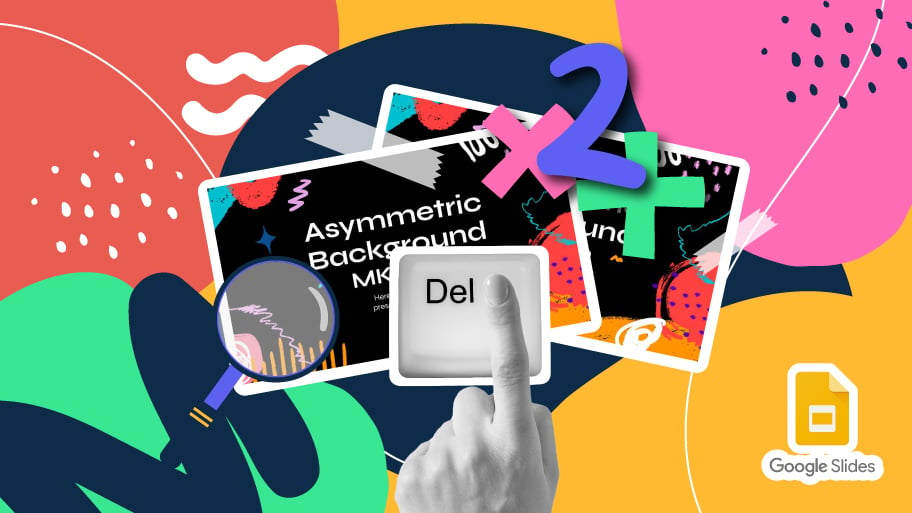
How to Add, Duplicate, Move, Delete or Hide Slides in Google Slides
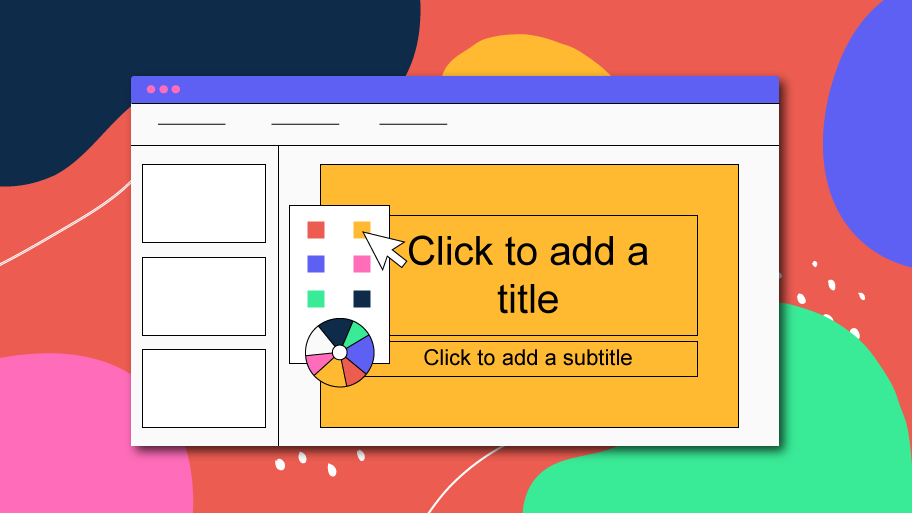
How to Change Layouts in PowerPoint
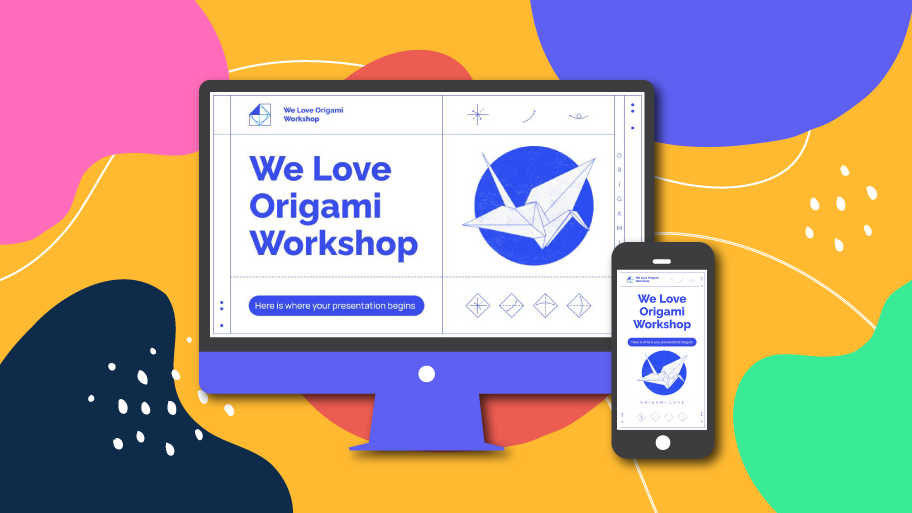
How to Change the Slide Size in Google Slides
Related presentations.

Premium template
Unlock this template and gain unlimited access


- Customer Favourites
Quality Control
Powerpoint Templates
Icon Bundle
Kpi Dashboard
Professional
Business Plans
Swot Analysis
Gantt Chart
Business Proposal
Marketing Plan
Project Management
Business Case
Business Model
Cyber Security
Business PPT
Digital Marketing
Digital Transformation
Human Resources
Product Management
Artificial Intelligence
Company Profile
Acknowledgement PPT
PPT Presentation
Reports Brochures
One Page Pitch
Interview PPT
All Categories

- You're currently reading page 1

Stages // require(['jquery'], function ($) { $(document).ready(function () { //removes paginator if items are less than selected items per page var paginator = $("#limiter :selected").text(); var itemsPerPage = parseInt(paginator); var itemsCount = $(".products.list.items.product-items.sli_container").children().length; if (itemsCount ? ’Stages’ here means the number of divisions or graphic elements in the slide. For example, if you want a 4 piece puzzle slide, you can search for the word ‘puzzles’ and then select 4 ‘Stages’ here. We have categorized all our content according to the number of ‘Stages’ to make it easier for you to refine the results.
Category // require(['jquery'], function ($) { $(document).ready(function () { //removes paginator if items are less than selected items per page var paginator = $("#limiter :selected").text(); var itemsperpage = parseint(paginator); var itemscount = $(".products.list.items.product-items.sli_container").children().length; if (itemscount.
- 3D Man (104)
- Anatomy (34)
- Block Chain (10)
- Branding (38)
- Brochures Layout (2)
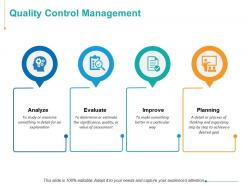
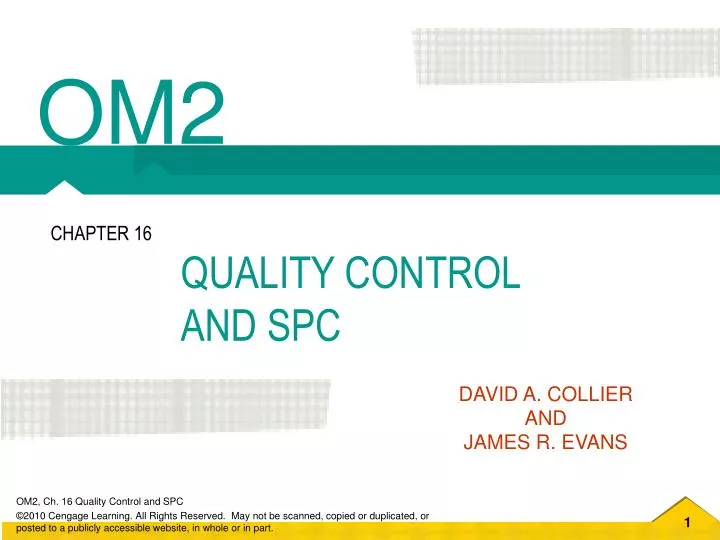
QUALITY CONTROL AND SPC
Nov 12, 2014
820 likes | 1.39k Views
OM2. CHAPTER 16. QUALITY CONTROL AND SPC. DAVID A. COLLIER AND JAMES R. EVANS. Chapter 16 Learning Outcomes. l e a r n i n g o u t c o m e s. LO1 Describe quality control system and key issues in manufacturing and service.
Share Presentation
- quality control
- control limits
- process capability
- meets customer requirements
- statistical process control spc

Presentation Transcript
OM2 CHAPTER 16 QUALITY CONTROL AND SPC DAVID A. COLLIER AND JAMES R. EVANS
Chapter 16 Learning Outcomes l e a r n i n g o u t c o m e s LO1Describe quality control system and key issues in manufacturing and service. LO2Explain types of variation and the role of statistical process control. LO3Describe how to construct and interpret simple control charts for both continuous and discrete data. LO4Describe practical issues in implementing SPC. LO5Explain process capability and calculate process capability indexes.
Chapter 16 Quality Control and SPC arriott has become infamous for its obsessively detailed standard operating procedures (SOPs), which result in hotels that travelers either love for their consistent good quality or hate for their bland uniformity. “This is a company that has more controls, more systems, and more procedural manuals than anyone—except the government,” says one industry veteran. “And they actually comply with them.” Housekeepers work with a 114-point checklist. One SOP: Server knocks three times. After knocking, the associate should immediately identify themselves in a clear voice, saying, “Room Service!” The guest’s name is never mentioned outside the door. Although people love to make fun of such procedures, they are a serious part of Marriott’s business, and SOPs are designed to protect the brand. Recently, Marriott has removed some of the rigid guidelines for owners of hotels it manages, empowering them to make some of their own decisions on details. What do you think?What opportunities for improved quality control or use of SOPs can you think of at your college or university (e.g., bookstore, cafeteria)?
Chapter 16 Quality Control and SPC Quality Control Systems The task of quality control is to ensure that a good or service conforms to specifications and meets customer requirements by monitoring and measuring processes and making any necessary adjustments to maintain a specified level of performance.
Chapter 16 Quality Control and SPC • Quality Control Systems • Quality Control Systems have three components: • A performance standard or goal, • A means of measuring actual performance, and • Comparison of actual performance with the standard to form the basis for corrective action.
Chapter 16 Quality Control and SPC 1:10:100 Rule: If a defect or service error is identified and corrected in the design stage, it might cost $1 to fix. If it is first detected during the production process, it might cost $10 to fix. However, if the defect is not discovered until it reaches the customer, it might cost $100 to correct.
Chapter 16 Quality Control and SPC Quality at the sourcemeansthe people responsible for the work control the quality of their processes by identifying and correcting any defects or errors when they first are recognized or occur.
Chapter 16 Quality Control and SPC • Quality Control Practices in Manufacturing • Supplier Certification and Management: ensures conformance to requirements before value-adding operations begin. • In-process control: ensures that defective outputs do not leave the process and prevents defects in the first place. • Finished goods control: verifies that product meets customer requirements.
Chapter 16 Quality Control and SPC • Quality Control Practices in Services • Prevent sources of errors and mistakes in the first place by using poka-yoke approaches. • Customer satisfaction measurement with actionableresults (responses that are tied directly to key business processes). • Many quality control tools and practices apply to both goods and services.
Chapter 16 Quality Control and SPC QualityControl for Medical Prescriptions Poor doctor handwriting is the number one root cause of medication errors. Often the wrong drug is prescribed, or the wrong dosage is used, or drug interactions cause adverse reactions. Mr. J. Lyle Bootman, the dean of the College of Pharmacy at the University of Arizona noted that “The economic consequences of medication errors are as costly as the entire cost of diabetes, and close to cancer and heart disease. It is a silent disease in America.” The Institute of Medicine estimates that a U.S. hospital patient is subject to at least one medication error daily. They estimate that more than 7,000 people die from medication errors every year. The solution is to streamline related processes, build quality control checks into every stage of each process, and use electronic prescription systems to eliminate handwritten prescriptions.
Chapter 16 Quality Control and SPC • Statistical Process Control and Variation • Statistical process control (SPC)isa methodology for monitoring quality of manufacturing and service delivery processes to help identify and eliminate unwanted causes of variation.
Chapter 16 Quality Control and SPC • Statistical Process Control and Variation • Common cause variationis the result of complex interactions of variations in materials, tools, machines, information, workers, and the environment. • Common cause variation accounts for 80 to 95 percent of the observed variation in a process. • Only management has the power to change systems and infrastructure that cause common cause variation.
Chapter 16 Quality Control and SPC • Statistical Process Control and Variation • Special (assignable) cause variationarises from external sources that are not inherent in the process, appear sporadically, and disrupt the random pattern of common causes. • Special cause variation accounts for 15 to 20 percent of observed variation. • Front-line employees and supervisors have the power to identify and solve special causes of variation.
Chapter 16 Quality Control and SPC • Foundations of Statistical Process Control • Stable system: a system governed only by common causes. • In control:if no special causes affect the output of the process. • Out of control:when special causes are present in the process.
Chapter 16 Quality Control and SPC • Constructing Control Charts • Steps 1 through 4 focus on setting up an initial chart; in step 5, the charts are used for ongoing monitoring; and finally, in step 6, the data are used for process capability analysis. • Preparation • Choose the metric to be monitored. • Determine the basis, size, and frequency of sampling. • Set up the control chart.
Chapter 16 Quality Control and SPC • Constructing Control Charts • Data collection • Record the data. • Calculate relevant statistics: averages, ranges, proportions, and so on. • Plot the statistics on the chart. • Determination of trial control limits • Draw the center line (process average) on the chart. • Compute the upper and lower control limits.
Chapter 16 Quality Control and SPC • Constructing Control Charts • Analysis and interpretation • Investigate the chart for lack of control. • Eliminate out-of-control points. • Recompute control limits if necessary. • Use as a problem-solving tool • Continue data collection and plotting. • Identify out-of-control situations and take corrective action. • 6.Determination of process capability using the control chart data
Chapter 16 Quality Control and SPC • Foundations of Statistical Process Control • A continuous metricis one that is calculated from data that are measured as the degree of conformance to a specification on a continuous scale of measurement. • A discrete metricisone that is calculated from data that are counted.
Foundations of Statistical Process Control SPC uses control charts, run charts to which two horizontal lines, called control limits, are added: the upper control limit (UCL) and lower control limit (LCL). Control limits are chosen statistically to provide a high probability (generally greater than 0.99) that points will fall between these limits if the process is in control. Chapter 16 Quality Control and SPC
Foundations of Statistical Process Control As a problem-solving tool, control charts allow employees to identify quality problems as they occur. Of course, control charts alone cannot determine the source of the problem. Chapter 16 Quality Control and SPC
Chapter 16 Constructing x-bar and R-Charts [16.1] [16.2] [16.3]
Chapter 16 Quality Control and SPC Solved Problem Goodman Tire periodically tests its tires for tread wear under simulated road conditions using x- and R-charts. Company collects twenty samples, each containing three radial tires from different shifts over several days of operations. x-bar Control Limits: UCL = 31.88 + 1.02(10.8) = 42.9 LCL = 31.88 – 1.02(10.8) = 20.8
Excel Template for Goodman Tire x-bar and R-Charts Exhibit 16.1
R-Chart for Goodman Tire Example Exhibit 16.2
x-Chart for Goodman Tire Example Exhibit 16.3
Chapter 16 Quality Control and SPC • Interpreting Patterns in Control Charts • A process is said to be “in control” when the control chart has the following characteristics: • No points are outside the control limits (the traditional and most popular SPC chart guideline). • The number of points above and below the center line is about the same. • The points seem to fall randomly above and below the center line. • Most points, but not all, are near the center line, and only a few are close to the control limits.
Interpreting Patterns in Control Charts A more in-depth understanding of SPC charts includes evaluating the patterns in the sample data using guidelines, such as: 8 points in a row above or below the center line 10 of 11 consecutive points above or below the center line 12 of 14 consecutive points above or below the center line 2 of 3 consecutive points in the outer one-third region between the center line and one of the control limits 4 of 5 consecutive points in the outer two-thirds region between the center line and one of the control limits Chapter 16 Quality Control and SPC
Illustration of Some Rules for Identifying Out-of-Control Conditions Exhibit Extra
Chapter 16 Constructing p-charts [16.4] [16.5] [16.6]
Data and Calculations for p-Chart Solved Problem Exhibit 16.4
p-Chart for ZIP Code Reader Solved Problem withConstant Sample Size Exhibit 16.5
UCLc= c + 3 √ √ c c LCLc= c - 3 Chapter 16 Constructing c-charts • Constructing c-charts • Where p-chart monitors the proportion of nonconforming items, a c-chart monitors the “number of nonconformances” per unit (i.e., a count of the number of defects, errors, failures, etc.). • Example: one customer’s purchase order may have several errors, such as wrong items, order quantity, or wrong price. [16.7]
UCLc= c + 3 √ √ c c LCLc= c - 3 Chapter 16 Constructing c-charts • Constructing c-charts • These charts are used extensively in service organizations. • To use a c-chart, the size of the sampling unit or the number of opportunities for errors remains constant. • Examples of c-chart applications: a fender or windshield on a certain automobile model, ceramic coffee cups all of same size and shape, etc. [16.7]
Exhibit 16.6 Machine Failure Data for c-Chart Solved Problem
c-Chart for Machine Failures Exhibit 16.7
Chapter 16 Control Chart Design • Control Chart Design • Sample size: small sample size keeps costs lower; however, large sample sizes provide greater degrees of statistical accuracy in estimating the true state of control. • Sampling frequency: samples should be close enough to provide an opportunity to detect changes in process characteristics as soon as possible and reduce the chances of producing a large amount of nonconforming output.
Other Practical Issues in SPC Implementation SPC is a useful methodology for processes that operate at a low sigma level (less than or equal to 3-sigma). However, when the rate of defects is extremely low, standard control limits are not so effective. For processes with a high sigma level (greater than 3-sigma), few defects will be discovered even with large sample sizes. Chapter 16 Quality Control and SPC
Chapter 16 Quality Control and SPC IBM At one IBM branch, pre-employment physical examinations took too long and taxed the medical staff assigned to conduct them. Such examinations are vital for assuring that employees can perform certain jobs without excess stress and that they pose no health threat to other employees. Therefore, the challenge IBM faced was to maintain the quality of the exam while reducing the time needed to perform it by identifying and eliminating waiting periods between the various parts of it. Preliminary control charts revealed that the average time required for the examination was 74 minutes, but the range varied greatly. New equipment and additional training of the medical staff were suggested as means of shortening the average time. Initial charts indicated that the process was out of control, but continued monitoring and process improvements lowered the average time to 40 minutes, and both the average and range were brought into statistical control with the help of x and R-charts.
Chapter 16 Quality Control and SPC • Process Capability • Process capabilityis the natural variation in a process that results from common causes. • Cp = (UTL – LTL)[16.9] • 6σ • Where: • UTL = upper tolerance limit • LTL = lower tolerance limit • σ = standard deviation of the process (or an estimate based on the sample standard deviation, s)
Chapter 16 Quality Control and SPC • Process Capability • Process capabilityis the natural variation in a process that results from common causes. • When Cp = 1, the natural variation is the same as the design specification width, as in Exhibit 16.8(b). • When Cp< 1, a significant percentage of output will not conform to the specifications as in Exhibit 16.8(a).
Process Capability versus Design Specifications Exhibit 16.8
Chapter 16 Quality Control and SPC • Process Capability • Cp> 1, indicates good capability as in Exhibit 16.8(c); in fact, many firms require Cp values of 1.66 or greater from their suppliers, which equates to a tolerance range of about 10 standard deviations. • The value of Cp does not depend on the mean of the process; thus, a process may be off-center, such as in Exhibit 16.8(d), and still show an acceptable value of Cp.
Process Capability Versus Design Specifications Exhibit 16.8
Chapter 16 Quality Control and SPC • One-sided capability indices that consider off- centered processes • Cpu = (UTL – µ)/3σ[16.10] • Cpl= (µ – LTL)/3σ[16.11] • Cpk = min (Cpl, Cpu) [16.12] • where • UTL = upper tolerance limit • LTL = lower tolerance limit • µ = the mean performance of the process • σ = standard deviation of the process (or an estimate based on the sample standard deviation, s)
Chapter 16 Quality Control and SPC SolvedProblem A controlled process shows an overall mean of 2.50 and an average range of 0.42. Samples of size 4 were used to construct the control charts. Part A: What is the process capability? From Appendix B, d2 = 2.059, σ = R/d2 = 0.42/2.059 = 0.20. Thus, the process capability is 2.50 3(.020), or 1.90 to 3.10. Part B: If specifications are 2.60 ± 0.25, how well can this process meet them? Because the specification range is 2.35 to 2.85 with a target of 2.60, we may conclude that the observed natural variation exceeds the specifications by a large amount. In addition, the process is off-center (see Exhibit 16.9).
Comparison of Observed Variation and Design Specifications for Solved Problem Exhibit 16.9
Chapter 16 Quality Control and SPC DeanDoor Corporation Case Study 1. Interpret the data in Exhibit 16.13, establish a state of statistical control, and evaluate the capability of the process to meet specifications. 2. What do the initial control charts tell you? Do any out-of-control conditions exist? 3. If the process is not in control, what might be the likely causes, based on the information that is available? 4. What is the process capability? What do the process capability indexes tell the company? 5. Is DDC facing a serious problem that it needs to address? How might the company eliminate the problems found by Walker Homes?
- More by User
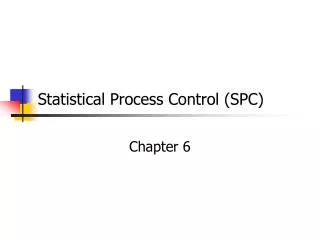
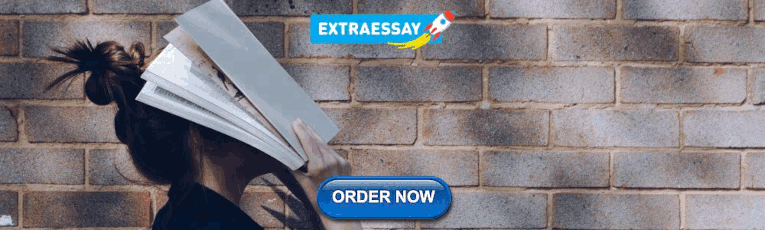
Statistical Process Control (SPC)
Statistical Process Control (SPC). Chapter 6. MGMT 326. Capacity and Facilities. Products & Processes. Quality Assurance. Planning & Control. Foundations of Operations. Managing Projects. Managing Quality. Introduction. Strategy. Product Design. Statistical Process Control.
1.13k views • 42 slides
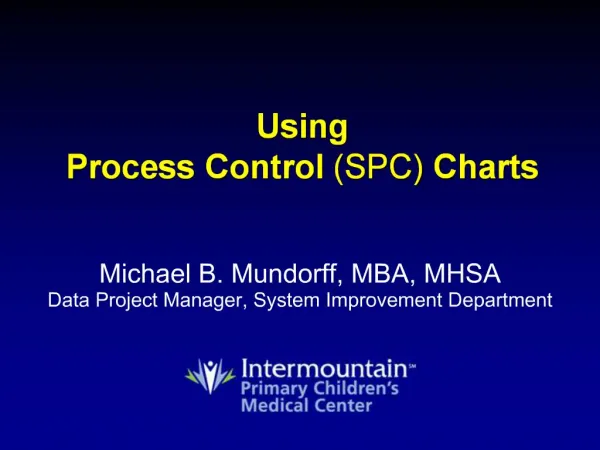
Using Process Control SPC Charts
9/18/2012. Intermountain Healthcare. 2. Random variation. represents the sum of many small variations, arising from real but small causes that are inherent in and part of a processfollows the laws of probability behaves statistically as a random probability functionBecause random variation
701 views • 30 slides
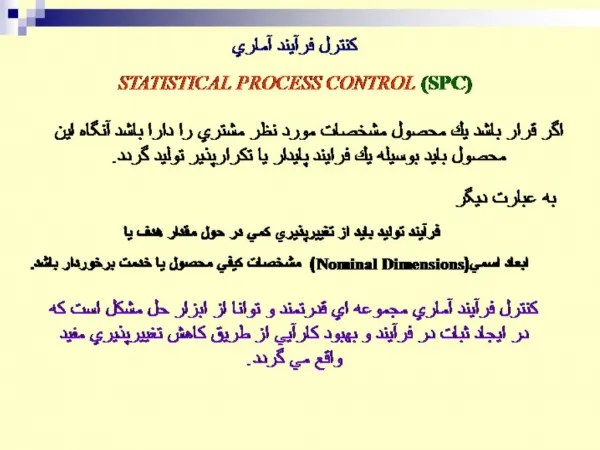
STATISTICAL PROCESS CONTROL SPC
?? ?? ?????? ????? ???? ?????????? ?? ??? ???? ???? ????. ??? ?????????? ???? ?? ??? ??????? ??? ?????? ????? ?? ???????? ???? ? ??????? ?????? ?? ???? ?? ???. ?? ????? ????? ????? ??? ?????????? ?? ?????? ?? ????? ?? ????? ?????? ?? ??????. ??????? ?? ??? ?? ???? ???????? ?????? ???
855 views • 59 slides
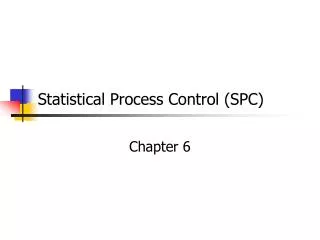
Statistical Process Control (SPC). Chapter 6. MGMT 326. Capacity, Facilities, & Work Design. Products & Processes. Quality Assurance. Planning & Control. Foundations of Operations. Project Manage- ment. Managing Quality. Introduction. Strategy. Statistical Process Control.
753 views • 38 slides
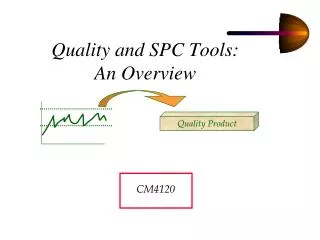
Quality and SPC Tools: An Overview
Quality and SPC Tools: An Overview. Quality Product. CM4120. Topics. Quality Advocates Quality Improvement Methodologies Six Sigma Quantitative Tools -Statistical Process Control (SPC) Tools. Process is “in control”?. Pause and Ponder?. What does “quality” mean?
1.14k views • 73 slides
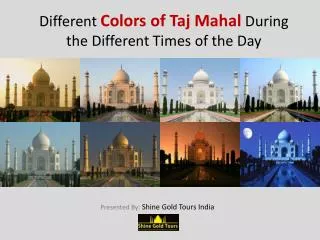
Webinar On Statistical Process Control (SPC)
All companies want to improve the quality of their products. Attempts to improve product quality need to be structured in such a way that they have a reasonable chance of success and the cost/benefit ratio is appropriate.
221 views • 10 slides
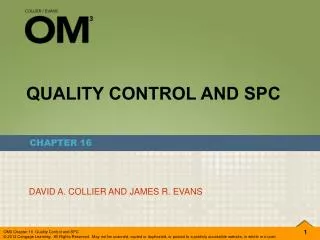
QUALITY CONTROL AND SPC. CHAPTER 16. DAVID A. COLLIER AND JAMES R. EVANS. Statistical Process Control and Variation
469 views • 38 slides

Quality management: SPC - I
Quality management: SPC - I. Presented by: Dr. Husam Arman. Quality Control (QC). Control – the activity of ensuring conformance to requirements and taking corrective action when necessary to correct problems Importance Daily management of processes Prerequisite to longer-term improvements.
760 views • 58 slides
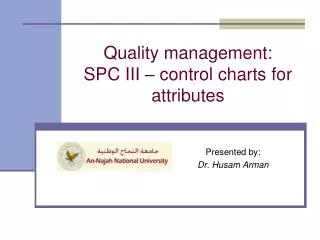
Quality management: SPC III – control charts for attributes
Quality management: SPC III – control charts for attributes . Presented by: Dr. Husam Arman. Control charts for attributes . Control charts for nonconforming (defective): p (percentage of defective units) np (number of defective units)
692 views • 36 slides
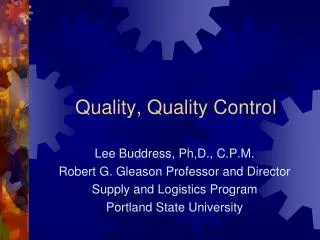
Quality, Quality Control
Quality, Quality Control. Lee Buddress, Ph,D ., C.P.M. Robert G. Gleason Professor and Director Supply and Logistics Program Portland State University. Control Charts. Processes Have Natural Variation Fundamental Question: Natural Variation or Process Change?
1.27k views • 19 slides
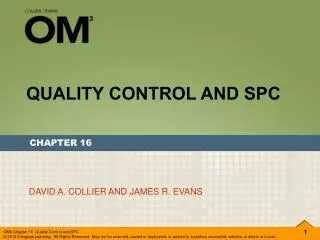
QUALITY CONTROL AND SPC. CHAPTER 16. DAVID A. COLLIER AND JAMES R. EVANS. LO1 Describe quality control system and key issues in manufacturing and service. LO2 Explain types of variation and the role of statistical process control .
799 views • 53 slides
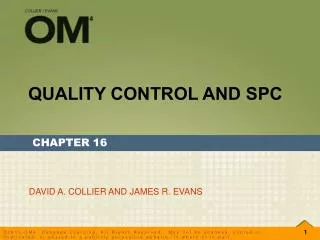
QUALITY CONTROL AND SPC. CHAPTER 16. DAVID A. COLLIER AND JAMES R. EVANS. 16-1 Describe quality control system and key issues in manufacturing and service. 16-2 Explain types of variation and the role of statistical process control (SPC).
816 views • 53 slides
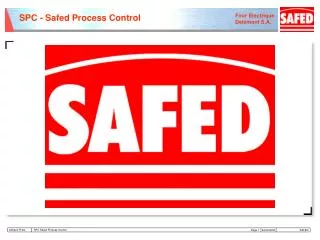
SPC - Safed Process Control
SPC - Safed Process Control. SPC - Safed Process Control. Data Recording. Heat Treatment Process Parameters. Receipt Management. Data Display Mode. Equipment Monitoring. Charge Data. Bar Code. Setting Process Values. SPC Safed Process Control. Quality Reports. Alarms.
469 views • 26 slides
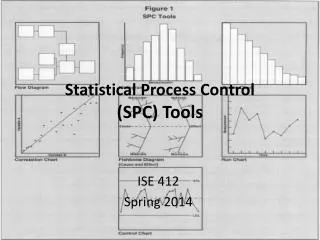
Statistical Process Control (SPC) Tools
Statistical Process Control (SPC) Tools. ISE 412 Spring 2014. Why do we need SPC tools?. We need Quality! With SPC, the process is monitored through sampling. Considering the results of the sample, we can prevent or improve the our week point in production lines. What do SPC tools monitor?.
2.01k views • 24 slides
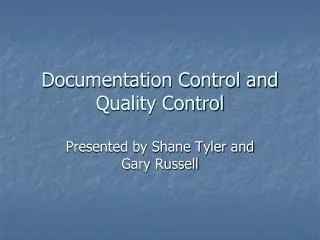
Documentation Control and Quality Control
Documentation Control and Quality Control. Presented by Shane Tyler and Gary Russell. Maintaining ATEX Certification on the Sage Rio Mass Flow Meter. Procedures and Documentation ATEX NIST Traceability Weekly Quality Meetings
268 views • 7 slides
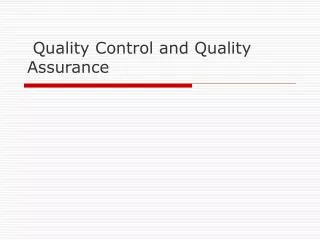
Quality Control and Quality Assurance
Quality Control and Quality Assurance. Quality. Why is Quality a Concern?. Gives competitive advantage Encourages return purchases Provides customer with information and builds consumer confidence in the brand Reduces costs incurred in solving post sales problems Helps improve efficiency.
504 views • 10 slides
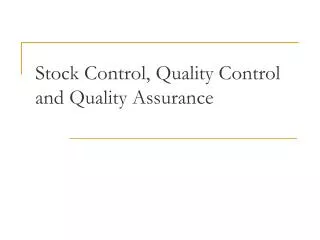
Stock Control, Quality Control and Quality Assurance
Stock Control, Quality Control and Quality Assurance. Stock Control, Quality Control and Quality Assurance. Stock Control. Stock Control. Costs: Storage costs – warehousing, etc. Depreciation costs – wear and tear, perishability, shelf-life, etc.
346 views • 16 slides
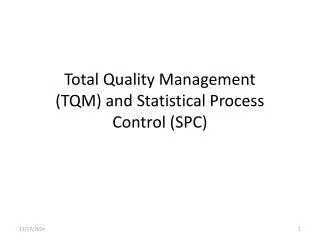
Total Quality Management (TQM) and Statistical Process Control (SPC)
Total Quality Management (TQM) and Statistical Process Control (SPC). TQM. Quality: a powerful competitive weapon Importance evidenced by variety of industrial awards (e.g., Baldrige Award, Deming Prize) Complex and multifaceted concept
789 views • 20 slides
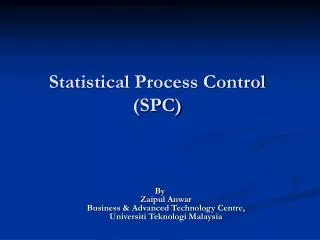
Statistical Process Control (SPC). By Zaipul Anwar Business & Advanced Technology Centre, Universiti Teknologi Malaysia. Aims and objectives. Explain the concept of SPC Understand variation and why it is important Manage variation in our work using SPC Learn how to do a control chart
928 views • 45 slides
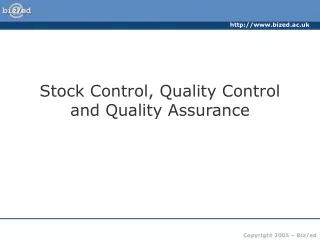
211 views • 16 slides
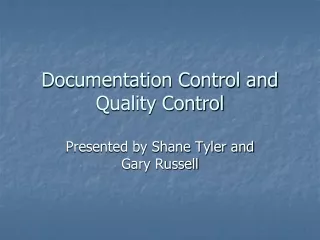
145 views • 7 slides
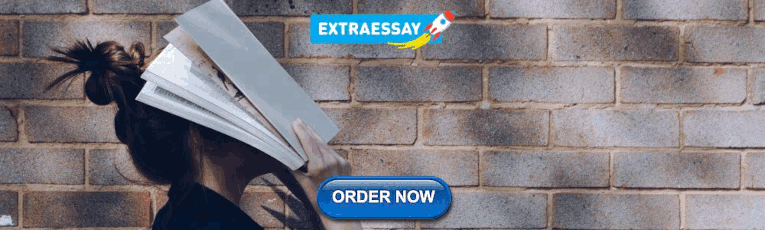
IMAGES
VIDEO
COMMENTS
Features: The organization gets the total man Humanize the work i.e. Quality of work life is stressed and improved Brings out extra-ordinary qualities from ordinary people To display the human capabilities fully and eventually draw out infinite possibilities Prepares the employer and employees to meet the challenges of the changing time and condition Quality control circle presentation
Free Google Slides theme, PowerPoint template, and Canva presentation template. A quality control lab is a must-have for any organization looking to ensure their production line meets the highest standards. This template offers a creative and professional approach to presenting quality control data. It features an illustrated background with a ...
Slide 1: This slide introduces Quality Management System .State Your Company Name and begin. Slide 2: This slide showcases Content with these points- Introduction, Principles & Certification, Tools of Quality Management, Data Analysis, Quality Control, Cost of Quality. Slide 3: This slide presents Introduction with these following parameters- TQM Pyramid, TQM Model, Elements of Quality ...
This is a quality control chart ppt powerpoint presentation infographic template slide portrait. This is a three stage process. The stages in this process are upper control limit, center line, unstable trend, process change, process improvement, lower control limit. Slide 1 of 5.
Get ignited with all new occurrences with our most appealing PPT template, quality control PowerPoint presentation slides and forget about disappointments. Click on the download button and proceed. Advocate a healthy jog with our Quality Control Powerpoint Presentation Slides. Elaborate on the innumerable benefits. « »
Quality control (QC) is a procedure or set of procedures intended to ensure that a manufactured product or performed service adheres to a defined set of quality criteria or meets the requirements of the client or customer. QC is similar to, but not identical with, quality assurance (QA). QC IN clinical biochemistry labs and hospitals. Read more.
Deliver an informational PPT on various topics by using this Manual Testing Strategies For Quality Control Powerpoint Presentation Slides. This deck focuses and implements best industry practices, thus providing a birds-eye view of the topic. Encompassed with forty seven slides, designed using high-quality visuals and graphics, this deck is a ...
Free Google Slides theme, PowerPoint template, and Canva presentation template. The Kaizen method is a philosophy of continuous improvement that has gained popularity in the business world. The concept is simple yet powerful: small, incremental changes lead to significant progress over time. Slidesgo wasn't built in one day—it's been a ...
This is a quality control ppt powerpoint presentation styles tips. This is a three stage process. The stages in this process are control chart, quality maintenance check sheet, quality maintenance check list, business, icons. Slide 1 of 5 Quality Control Ppt PowerPoint Presentation Ideas Icon.
Apr 19, 2015 •. 19 likes • 20,838 views. Sneha J Chouhan. This presentation breifs about the quality control sector, its ojectives, benefits. The various departments which monitor the quality in India are also mentioned. Read more. Leadership & Management. 1 of 20. Quality Control - Download as a PDF or view online for free.
The 18 slides for the quality control presentation allow you to showcase the Quality Control process that ensures products or services meet specific standards by monitoring and testing them throughout the production or delivery process. For this, SlideBazaar designers have compiled a sequence of concepts as follows: You can utilize the quality ...
Grab our presentation template to depict the 7 Quality Control Tools and how they are crucial for identifying issues, analyzing data, and finding solutions in quality management. 100% compatible with MS PowerPoint and Google Slides, this deck features visuals that can be used to ensure accurate and faster interpretation of content.
Free Google Slides theme and PowerPoint template. Whenever we purchase a product, we want it to last long, and arrive in perfect condition. Quality control ensures that. What about the required documentation in order to be given the "OK"? It's an important topic in businesses, so make sure to have a clear slideshow that explains everything.
Solve critical quality related issues using Tools Of Quality Control PowerPoint Presentation Slides. Incorporate this professionally designed tools of quality control PPT slideshow and apply these quality check tools from product development phase till delivery. This content-ready QC tools PowerPoint complete deck has pareto chart, flow chart ...
Presentation Transcript. The word 'quality control' comprises of two words i.e. • 'Quality' & 'Control' • Quality isthe reflection of your commitment to your customer. It is the sum of various characteristics of the product such as: • Shape • Dimension • Composition • Strength and durability • Finish and colour etc ...
QUALITY CONTROL (QC) is a tool / concept for objectively determining , analyzing and solving quality problem and for maintaining better quality. QC has two main activities :. Download Presentation. quality. actual facts.
Definitions (1) • Quality Control - QC refers to the measures that must be included during each assay run to verify that the test is working properly. • Quality Assurance - QA is defined as the overall program that ensures that the final results reported by the laboratory are correct. • "The aim of quality control is simply to ensure ...
Quality analysts, quality technicians, and quality assurance managers can capitalize on these memorable PowerPoint slides to exhibit that quality control is used to produce products and services that match the set quality standards. However, inspection is an examination tool to analyze whether the goods have the expected quality or not.
Click here to download this PowerPoint Presentation. Quality Control . Up next, we delve into Quality Control (QC) — a suite of procedures aimed at guaranteeing the excellence of a product or service. The objective of QC is to ensure that the processes outlined in the QA strategy are executed.
Our Quality Control PowerPoint template comprises of a wide range of HD vectors that will make your job a whole lot easier. It is an essential set for every QC, auditor, tester, manager, or almost every other professional who is associated with quality management and testing. It doesn't matter if you belong to manufacturing or a service-based ...
Control Charts • Purpose: • Using the samples collected from the process, and calculating the required statistics to construct a time sequence chart to detect the process variation. • Process control with variablemeasurements: • For each sample, we measure the weight, volume, length, or other variable measurements.
Slide 1 of 10. Quality Control Techniques In Powerpoint And Google Slides Cpb. Slide 1 of 2. Purchasing inventory and quality control vendor business planning actionable steps ppt graphics. Slide 1 of 2. Companys franchise success cycle and quality control creating culture digital transformation ppt grid. Slide 1 of 5.
Chapter 16 Quality Control and SPC • Constructing Control Charts • Steps 1 through 4 focus on setting up an initial chart; in step 5, the charts are used for ongoing monitoring; and finally, in step 6, the data are used for process capability analysis. • Preparation • Choose the metric to be monitored.