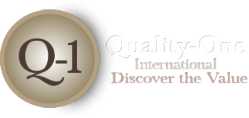
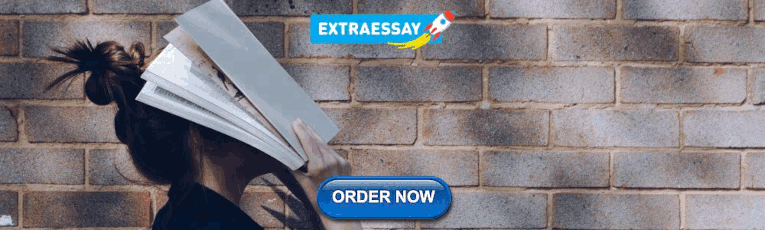
Eight Disciplines of Problem Solving (8D)
– Eight Disciplines of Problem Solving –
⇓ Introduction to 8D
⇓ What is 8D
⇓ Why Apply 8D
⇓ When to Apply 8D
⇓ How to Apply 8D
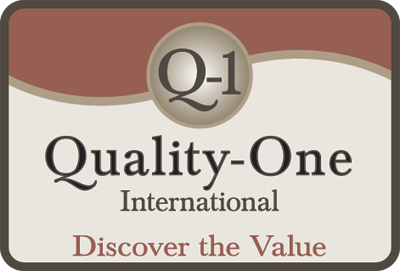
Introduction to Eight Disciplines of Problem Solving (8D)
The Eight Disciplines of Problem Solving (8D) is a problem solving methodology designed to find the root cause of a problem, devise a short-term fix and implement a long-term solution to prevent recurring problems. When it’s clear that your product is defective or isn’t satisfying your customers, an 8D is an excellent first step to improving Quality and Reliability.
Ford Motor Company developed this problem solving methodology, then known as Team Oriented Problem Solving (TOPS), in the 1980s. The early usage of 8D proved so effective that it was adopted by Ford as the primary method of documenting problem solving efforts, and the company continues to use 8D today.
8D has become very popular among manufacturers because it is effective and reasonably easy to teach. Below you’ll find the benefits of an 8D, when it is appropriate to perform and how it is performed.
What is Eight Disciplines of Problem Solving (8D)
The 8D problem solving process is a detailed, team oriented approach to solving critical problems in the production process. The goals of this method are to find the root cause of a problem, develop containment actions to protect customers and take corrective action to prevent similar problems in the future.
The strength of the 8D process lies in its structure, discipline and methodology. 8D uses a composite methodology, utilizing best practices from various existing approaches. It is a problem solving method that drives systemic change, improving an entire process in order to avoid not only the problem at hand but also other issues that may stem from a systemic failure.
8D has grown to be one of the most popular problem solving methodologies used for Manufacturing, Assembly and Services around the globe. Read on to learn about the reasons why the Eight Disciplines of Problem Solving may be a good fit for your company.
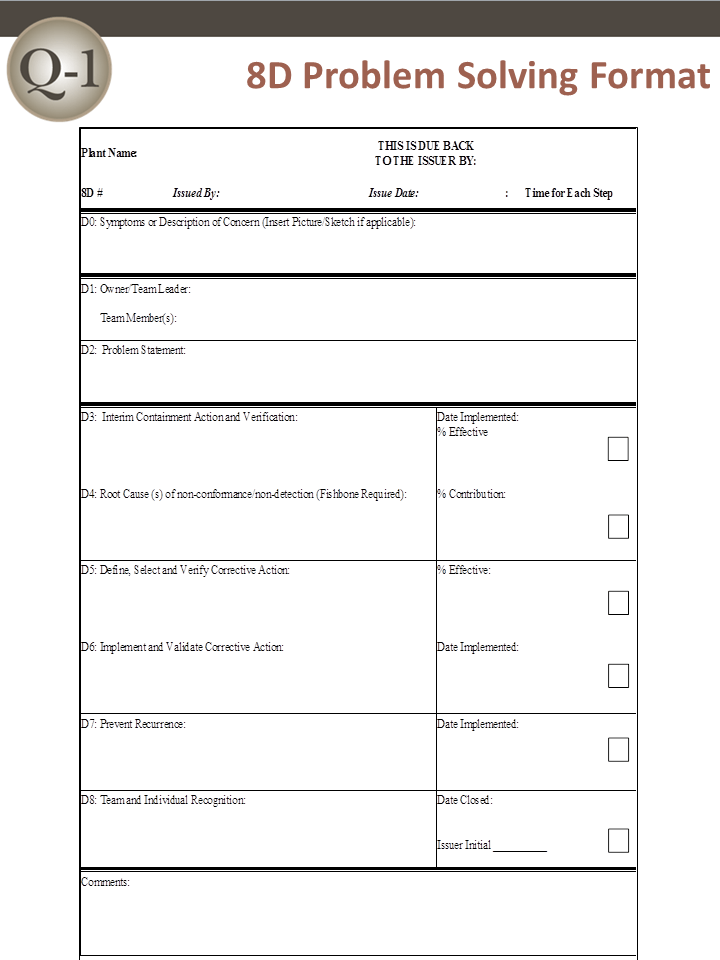
Why Apply Eight Disciplines of Problem Solving (8D)
The 8D methodology is so popular in part because it offers your engineering team a consistent, easy-to-learn and thorough approach to solving whatever problems might arise at various stages in your production process. When properly applied, you can expect the following benefits:
- Improved team oriented problem solving skills rather than reliance on the individual
- Increased familiarity with a structure for problem solving
- Creation and expansion of a database of past failures and lessons learned to prevent problems in the future
- Better understanding of how to use basic statistical tools required for problem solving
- Improved effectiveness and efficiency at problem solving
- A practical understanding of Root Cause Analysis (RCA)
- Problem solving effort may be adopted into the processes and methods of the organization
- Improved skills for implementing corrective action
- Better ability to identify necessary systemic changes and subsequent inputs for change
- More candid and open communication in problem solving discussion, increasing effectiveness
- An improvement in management’s understanding of problems and problem resolution
8D was created to represent the best practices in problem solving. When performed correctly, this methodology not only improves the Quality and Reliability of your products but also prepares your engineering team for future problems.
When to Apply Eight Disciplines of Problem Solving (8D)
The 8D problem solving process is typically required when:
- Safety or Regulatory issues has been discovered
- Customer complaints are received
- Warranty Concerns have indicated greater-than-expected failure rates
- Internal rejects, waste, scrap, poor performance or test failures are present at unacceptable levels
How to Apply Eight Disciplines of Problem Solving (8D)
The 8D process alternates inductive and deductive problem solving tools to relentlessly move forward toward a solution. The Quality-One approach uses a core team of three individuals for inductive activities with data driven tools and then a larger Subject Matter Expert (SME) group for the deductive activities through brainstorming, data-gathering and experimentation.
D0: Prepare and Plan for the 8D
Proper planning will always translate to a better start. Thus, before 8D analysis begins, it is always a good idea to ask an expert first for their impressions. After receiving feedback, the following criterion should be applied prior to forming a team:
Collect information on the symptoms
Use a Symptoms Checklist to ask the correct questions
Identify the need for an Emergency Response Action (ERA), which protects the customer from further exposure to the undesired symptoms
D1: Form a Team
A Cross Functional Team (CFT) is made up of members from many disciplines. Quality-One takes this principle one step further by having two levels of CFT:
- The Core Team Structure should involve three people on the respective subjects: product, process and data
- Additional Subject Matter Experts are brought in at various times to assist with brainstorming, data collection and analysis
Teams require proper preparation. Setting the ground rules is paramount. Implementation of disciplines like checklists, forms and techniques will ensure steady progress. 8D must always have two key members: a Leader and a Champion / Sponsor:
- The Leader is the person who knows the 8D process and can lead the team through it (although not always the most knowledgeable about the problem being studied)
- The Champion or Sponsor is the one person who can affect change by agreeing with the findings and can provide final approval on such changes
D2: Describe the Problem
The 8D method’s initial focus is to properly describe the problem utilizing the known data and placing it into specific categories for future comparisons. The “Is” data supports the facts whereas the “Is Not” data does not. As the “Is Not” data is collected, many possible reasons for failure are able to be eliminated. This approach utilizes the following tools:
- Problem Statement
- Affinity Diagram (Deductive tool)
- Fishbone/Ishikawa Diagram (Deductive tool)
- Problem Description
D3: Interim Containment Action
In the interim, before the permanent corrective action has been determined, an action to protect the customer can be taken. The Interim Containment Action (ICA) is temporary and is typically removed after the Permanent Correct Action (PCA) is taken.
- Verification of effectiveness of the ICA is always recommended to prevent any additional customer dissatisfaction calls
D4: Root Cause Analysis (RCA) and Escape Point
The root cause must be identified to take permanent action to eliminate it. The root cause definition requires that it can be turned on or off, at will. Activities in D4 include:
- Comparative Analysis listing differences and changes between “Is” and “Is Not”
- Development of Root Cause Theories based on remaining items
- Verification of the Root Cause through data collection
- Review Process Flow Diagram for location of the root cause
- Determine Escape Point, which is the closest point in the process where the root cause could have been found but was not
D5: Permanent Corrective Action (PCA)
The PCA is directed toward the root cause and removes / changes the conditions of the product or process that was responsible for the problem. Activities in D5 include:
- Establish the Acceptance Criteria which include Mandatory Requirements and Wants
- Perform a Risk Assessment / Failure Mode and Effects Analysis (FMEA) on the PCA choices
- Based on risk assessment, make a balanced choice for PCA
- Select control-point improvement for the Escape Point
- Verification of Effectiveness for both the PCA and the Escape Point are required
D6: Implement and Validate the Permanent Corrective Action
To successfully implement a permanent change, proper planning is essential. A project plan should encompass: communication, steps to complete, measurement of success and lessons learned. Activities in D6 include:
- Develop Project Plan for Implementation
- Communicate the plan to all stakeholders
- Validation of improvements using measurement
D7: Prevent Recurrence
D7 affords the opportunity to preserve and share the knowledge, preventing problems on similar products, processes, locations or families. Updating documents and procedures / work instructions are expected at this step to improve future use. Activities in D7 include:
- Review Similar Products and Processes for problem prevention
- Develop / Update Procedures and Work Instructions for Systems Prevention
- Capture Standard Work / Practice and reuse
- Assure FMEA updates have been completed
- Assure Control Plans have been updated
D8: Closure and Team Celebration
Teams require feedback to allow for satisfactory closure. Recognizing both team and individual efforts and allowing the team to see the previous and new state solidifies the value of the 8D process. Activities in D8 include:
- Archive the 8D Documents for future reference
- Document Lessons Learned on how to make problem solving better
- Before and After Comparison of issue
- Celebrate Successful Completion
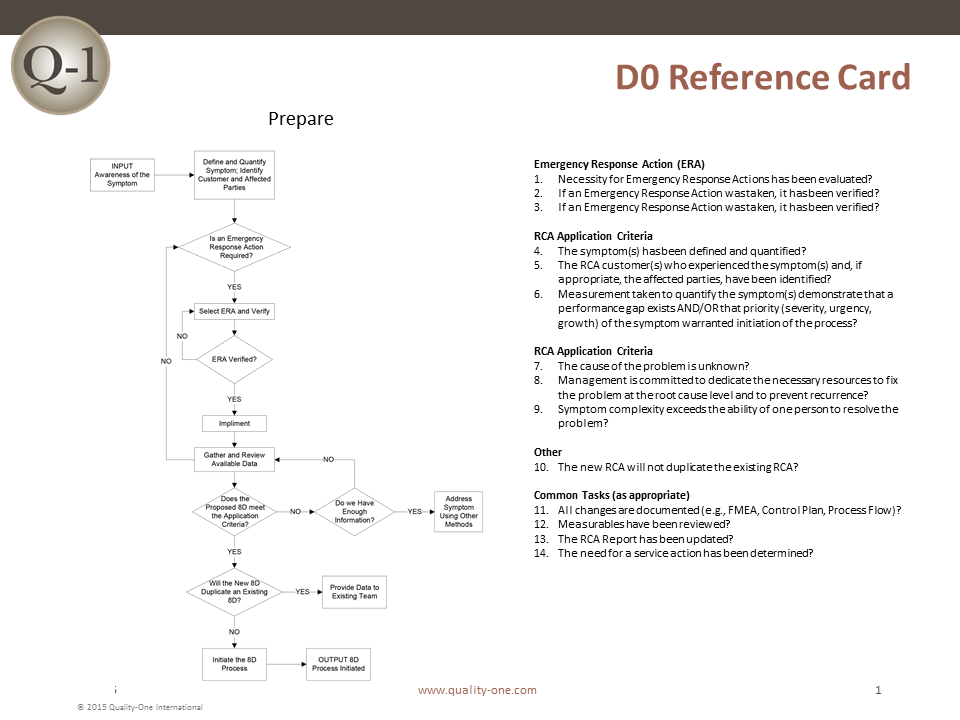
8D and Root Cause Analysis (RCA)
The 8D process has Root Cause Analysis (RCA) imbedded within it. All problem solving techniques include RCA within their structure. The steps and techniques within 8D which correspond to Root Cause Analysis are as follows:
- Problem Symptom is quantified and converted to “Object and Defect”
- Problem Symptom is converted to Problem Statement using Repeated Whys
- Possible and Potential Causes are collected using deductive tools (i.e. Fishbone or Affinity Diagram)
- Problem Statement is converted into Problem Description using Is / Is Not
- Problem Description reduces the number of items on the deductive tool (from step 3)
- Comparative Analysis between the Is and Is Not items (note changes and time)
- Root Cause theories are developed from remaining possible causes on deductive tool and coupled with changes from Is / Is Not
- Compare theories with current data and develop experiments for Root Cause Verification
- Test and confirm the Root Causes
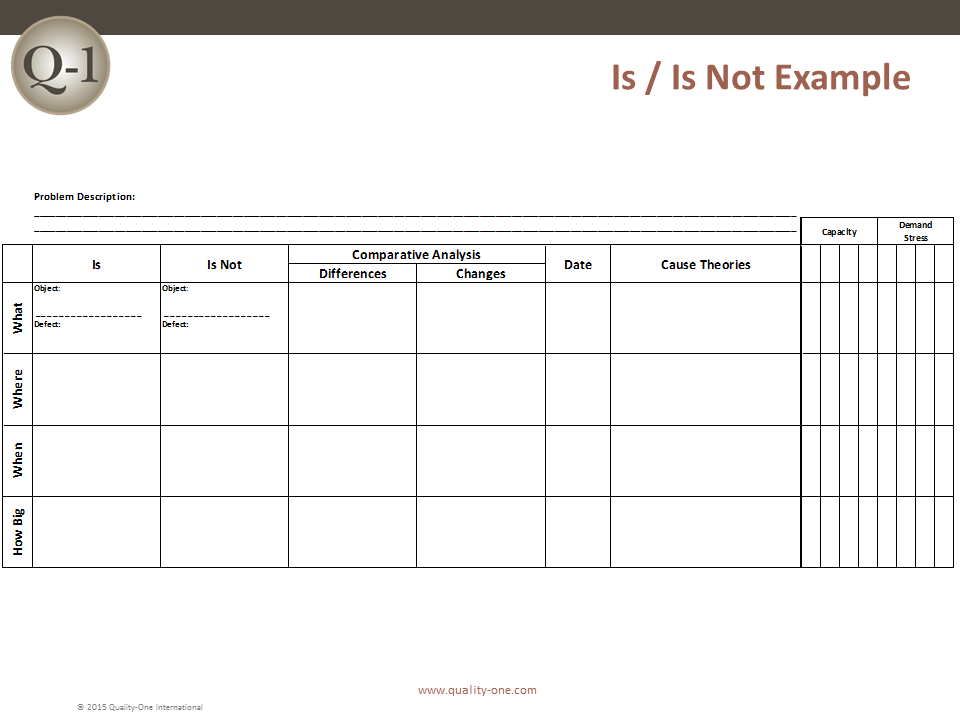
Example: Multiple Why Technique
The Multiple / Repeated Why (Similar to 5 Why) is an inductive tool, which means facts are required to proceed to a more detailed level. The steps required to determine problem statement are:
- Problem Symptom is defined as an Object and Defect i.e. “Passenger Injury”
- Why? In every case “SUV’s Roll Over”
- Why? In every case, it was preceded by a “Blown Tire”
- Why? Many explanations may be applied, therefore the team cannot continue with another repeated why past “Blown Tire”
- Therefore, the Problem Statement is “Blown Tire”
- Why? Low (Air) Pressure, Tire Defect (Degradation of an Interface) and High (Ambient) Temperature
- Counter measures assigned to low pressure and tire defect
This example uses only 4 of the 5 Whys to determine the root causes without going further into the systemic reasons that supported the failure. The Repeated Why is one way to depict this failure chain. Fault Tree Analysis (FTA) could also be used.
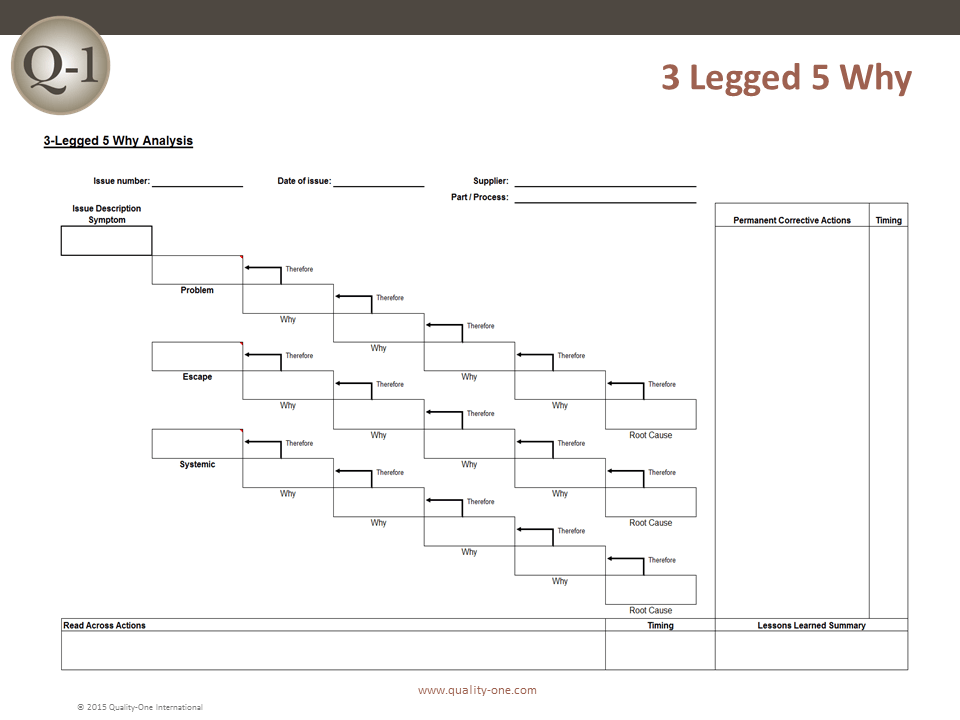
Learn More About Eight Disciplines of Problem Solving (8D)
Quality-One offers Quality and Reliability Support for Product and Process Development through Consulting, Training and Project Support. Quality-One provides Knowledge, Guidance and Direction in Quality and Reliability activities, tailored to your unique wants, needs and desires. Let us help you Discover the Value of 8D Consulting , 8D Training or 8D Project Support .
Contact Us | Discover the Value!
(248) 280-4800 | [email protected]
Remember Me
- Don't have an account? Register
- Lost your password? Click here
- Already have an account? Log in

GxP Lifeline
Solving quality issues and problems: go beyond root cause to ‘real’ cause.
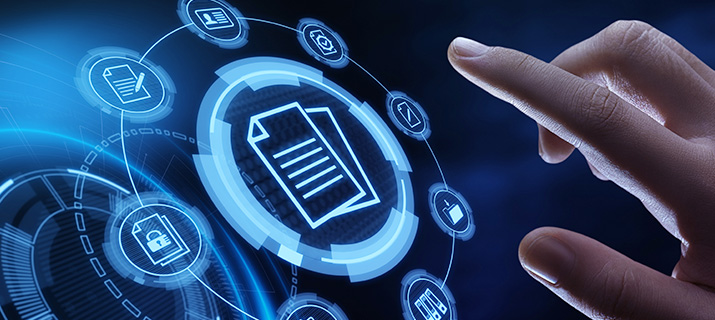
There is a tendency in the quality management field to confuse the root cause of a problem with the problem’s real cause. A root cause is objective evidence of a quality problem. The real cause of a quality problem, however, is the actual finding or nonconformance .
Uncovering real causes of quality issues and problems requires different, deeper scrutiny than identifying root causes. Mistaking one for the other can lead to the perpetuation of cycles such as this one:
- A severe quality problem occurs at a production facility after a change is made.
- A team of stakeholders and possibly consultants convene to investigate the problem.
- A root cause is found.
- A corrective action / preventive action (CAPA) is implemented.
- The problem goes away.
- When another change occurs, the cycle repeats itself with a different yet related issue.
If you’re a quality professional who has been with the same organization for multiple years, this recursive pattern is likely to sound familiar. When multiple change-related root causes arise, it soon becomes evident that they are symptomatic of a deeper-seated cause.
Six Real Causes of Quality Issues Problems
In his foundational book on management audits, Allan Sayle concluded that there are just six real causes of all quality problems. (1) For each of the six causes, Sayle outlined specific sub-cause indicators, the identification of which can enable an auditor to properly assign a real cause for a quality problem. Attributing a quality problem to one or more of the sub-causes listed below can help your company identify the real cause and devise a change to mitigate or eliminate it.
#1. Lack of Organization
- Undetermined responsibilities and authorities (i.e., confusion about who is supposed to perform and be responsible for specific jobs that result in a product that is fit for purpose).
- Undefined management systems (i.e., the methods and means of communication between departments and individuals doesn’t form a complete and continuous chain).
- Inadequate communication, especially as it pertains to information generated by a particular department that is needed by specialists.
#2. Lack of Training
- Personnel are not trained in the systems/methods in place or are not told with whom they are supposed to interface.
- Inadequate company training (e.g., managers produce and distribute a quality assurance manual but users aren’t trained on its contents).
#3. Lack of Discipline
- Workers follow bad examples set by supervisors and managers.
- Quality campaigns do not extend across the enterprise and subsequently build up frictions, become demotivators, and lead to disillusionment.
- Personal attributes that prevent employees from following the agreed upon methods.
- Inflexible systems that stifle innovation, quick thinking, and human problem-solving creativity.
- Demotivating environments.
#4. Lack of Resources
- Overly complex management systems that drain valuable resources.
- Irresponsible attitudes (i.e., resources are always completely used up in proportion with their allocation).
- Uneven allocation.
- Unrealistic estimates.
- Inadequate reinvestment (e.g., resource allocations are based on previous years’ budgets without taking market changes into account).
- Failure to modernize and seek potential applications for new technologies.
#5. Lack of Time
- Overly complex systems that waste time and/or create needless tasks.
- Irresponsible attitudes (e.g., personnel whose work always expands to fill the allotted time).
- Unrealistic commitments that are promised to customers without consideration for the time it takes to properly deliver a quality product.
- Selfishness that increasingly piles on pressures downline as a product gets closer to delivery.
- Excessive workloads.
#6. Lack of Top Management Support
- Attitude/motivation (i.e., a corporate culture that does not prioritize quality and assumes it is automatic).
- Managers who are inadequately educated to the importance of quality and the means of achieving it.
- Time management (e.g., quality managers spend more time fighting fires than proactively addressing quality, which typically results in a self-defeating cycle).
- “Cancer of complacency” (i.e., the false belief that reputation and past performance will always outweigh any quality issues that may arise).
Now that you know what problems to look for, the next step is ensuring your personnel have the right tools and skillsets to identify and rectify them.
Quality Problem Identification Certifications
Quality practices can vary widely across different industries and countries. That being the case, there is not a blanket quality problem identification certification that applies globally to all business sectors. However, there are a variety of specialized certifications, such as those offered by the American Society for Quality ( ASQ ), that formally recognize an individual’s proficiency within, and comprehension of, specific quality knowledge.
ASQ offers professional certifications in the following areas:
- Management (i.e., organizational excellence and supplier quality).
- Foundational quality (i.e., quality improvement and process analysis).
- Inspections (including equipment calibration).
- Engineering (including software development, implementation, testing, verification, and validation).
- Auditing (including certifications specific to quality practices for food safety, pharmaceutical, and medical device industries).
- Six Sigma techniques for process improvement.
For professionals seeking quality problem identification programs, ASQ offers Certified Quality Inspector (CQI) training. CQI certification ensures an inspector has learned proven techniques for inspecting products, measuring process performance, recording data, evaluating hardware documentation, performing laboratory procedures, and preparing formal reports.
Real Cause Identification Requires Tools Built for the Job
Unearthing and correcting real causes can dramatically reduce the occurrence and severity of quality problems. Determining real causes also helps diminish the dysfunctions caused by CAPA overload. But you need the right set of tools to identify real causes efficiently and effectively.
A digital, fully integrated quality management system (QMS) simplifies real cause discovery. It’s much easier to identify the real causes of problems when you can rely on a unified platform that connects quality data across your products’ life cycles and within a common architecture. A connected QMS platform gives you greater real-time visibility into quality data, which pushes real problems to the fore.
To learn how your organization can identify real causes with greater speed and accuracy, visit MasterControl’s product life cycle managementplatform page .
- “ Management Audits: The Assessment of Quality Management Systems ,” Sayle, Allan J., 1988, McGraw-Hill, pp. 18.21-34.

James Jardine is the editor of the GxP Lifeline blog and the marketing content team manager at MasterControl, Inc., a leading provider of cloud-based quality, manufacturing, and compliance software solutions. He has covered life sciences, technology and regulatory matters for MasterControl and various industry publications since 2007. He has a bachelor’s degree in communications with an emphasis in journalism from the University of Utah. Prior to joining MasterControl, James held several senior communications, operations, and development positions. Working for more than a decade in the non-profit sector, he served as the Utah/Idaho director of communications for the American Cancer Society and as the Utah Food Bank’s grants and contracts manager.

By using this site you agree to our use of cookies. Please refer to our privacy policy for more information. Close

7 Powerful Problem-Solving Root Cause Analysis Tools
The first step to solving a problem is to define the problem precisely. It is the heart of problem-solving.
Root cause analysis is the second important element of problem-solving in quality management. The reason is if you don't know what the problem is, you can never solve the exact problem that is hurting the quality.
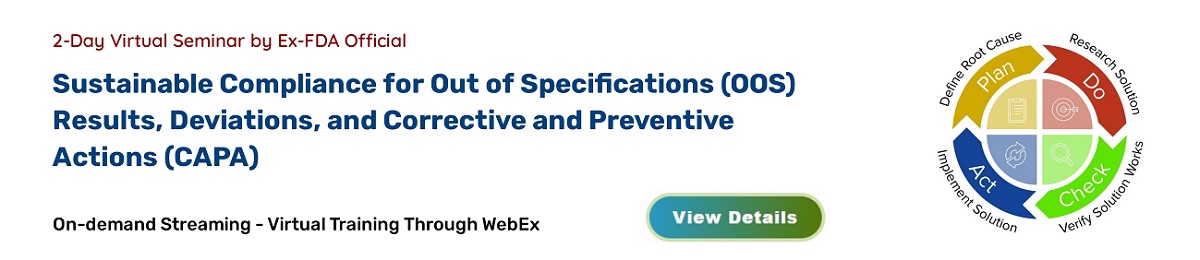
Manufacturers have a variety of problem-solving tools at hand. However, they need to know when to use which tool in a manner that is appropriate for the situation. In this article, we discuss 7 tools including:
- The Ishikawa Fishbone Diagram (IFD)
- Pareto Chart
- Failure Mode and Effects Analysis (FMEA)
- Scatter Diagram
- Affinity Diagram
- Fault Tree Analysis (FTA)
1. The Ishikawa Fishbone Diagram IFD
The model introduced by Ishikawa (also known as the fishbone diagram) is considered one of the most robust methods for conducting root cause analysis. This model uses the assessment of the 6Ms as a methodology for identifying the true or most probable root cause to determine corrective and preventive actions. The 6Ms include:
- Measurement,
- Mother Nature- i.e., Environment
Related Training: Fishbone Diagramming
2. Pareto Chart
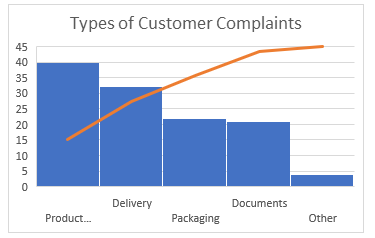
The Pareto Chart is a series of bars whose heights reflect the frequency or impact of problems. On the Chart, bars are arranged in descending order of height from left to right, which means the categories represented by the tall bars on the left are relatively more frequent than those on the right.
Related Training: EFFECTIVE INVESTIGATIONS AND CORRECTIVE ACTIONS (CAPA) Establishing and resolving the root causes of deviations, problems and failures
This model uses the 5 Why by asking why 5 times to find the root cause of the problem. It generally takes five iterations of the questioning process to arrive at the root cause of the problem and that's why this model got its name as 5 Whys. But it is perfectly fine for a facilitator to ask less or more questions depending on the needs.
Related training: Accident/Incident Investigation and Root Cause Analysis
4. Failure Mode and Effects Analysis (FMEA)
FMEA is a technique used to identify process and product problems before they occur. It focuses on how and when a system will fail, not if it will fail. In this model, each failure mode is assessed for:
- Severity (S)
- Occurrence (O)
- Detection (D)
A combination of the three scores produces a risk priority number (RPN). The RPN is then provided a ranking system to prioritize which problem must gain more attention first.
Related Training: Failure Mode Effects Analysis
5. Scatter Diagram
A scatter diagram also known as a scatter plot is a graph in which the values of two variables are plotted along two axes, the pattern of the resulting points revealing any correlation present.
To use scatter plots in root cause analysis, an independent variable or suspected cause is plotted on the x-axis and the dependent variable (the effect) is plotted on the y-axis. If the pattern reflects a clear curve or line, it means they are correlated. If required, more sophisticated correlation analyses can be continued.
Related Training: Excel Charting Basics - Produce Professional-Looking Excel Charts
6. Affinity Diagram
Also known as KJ Diagram, this model is used to represent the structure of big and complex factors that impact a problem or a situation. It divides these factors into small classifications according to their similarity to assist in identifying the major causes of the problem.
7. Fault Tree Analysis (FTA)
The Fault Tree Analysis uses Boolean logic to arrive at the cause of a problem. It begins with a defined problem and works backward to identify what factors contributed to the problem using a graphical representation called the Fault Tree. It takes a top-down approach starting with the problem and evaluating the factors that caused the problem.
Finding the root cause isn't an easy because there is not always one root cause. You may have to repeat your experiment several times to arrive at it to eliminate the encountered problem. Using a scientific approach to solving problem works. So, its important to learn the several problem-solving tools and techniques at your fingertips so you can use the ones appropriate for different situations.
ComplianceOnline Trainings on Root Cause Analysis
P&PC, SPC/6Sigma, Failure Investigation, Root Cause Analysis, PDCA, DMAIC, A3 This webinar will define what are the US FDA's expectation for Production and Process Control / Product Realization, the use of statistical tehniques, 6 sigma, SPC, for establishing, controlling , and verifying the acceptability of process capability and product characteristics, product acceptance or validation and other studies. Non-conformance, OOS, deviations Failure Investigations, and Root Cause Analysis, PDCA, DMAIC, and similar project drivers to improvement, A# and similar dash boards.
Accident/Incident Investigation and Root Cause Analysis If a major workplace injury or illness occurred, what would you do? How would you properly investigate it? What could be done to prevent it from happening again? A properly executed accident/incident investigation drives to the root causes of the workplace accident to prevent a repeat occurrence. A good accident/incident investigation process includes identifying the investigation team, establishing/reviewing written procedures, identifying root causes and tracking of all safety hazards found to completion.
Root Cause Analysis - The Heart of Corrective Action This presentation will explain the importance of root cause analysis and how it fits into an effective corrective and preventive action system. It will cover where else in your quality management system root cause analysis can be used and will give examples of some of the techniques for doing an effective root cause analysis. Attendees will learn how root cause analysis can be used in process control.
Addressing Non-Conformances using Root Cause Analysis (RCA) RCA assumes that systems and events are interrelated. An action in one area triggers an action in another, and another, and so on. By tracing back these actions, you can discover where the issue started and how it grew into the problem you're now facing.
Risk Management Under ISO 14971 ISO 14971:2019 is the definitive standard for risk management for medical devices and IVDs. The standard lays out a comprehensive approach to managing risks in the life sciences. The course will discuss practical approaches to complying with the standard.
Introduction to Root Cause Investigation for CAPA If you have reoccurring problems showing up in your quality systems, your CAPA system is not effective and you have not performed an in-depth root cause analysis to be able to detect through proper problem solving tools and quality data sources, the true root cause of your problem. Unless you can get to the true root cause of a failure, nonconformity, defect or other undesirable situation, your CAPA system will not be successful.
Root Cause Analysis and CAPA Controls for a Compliant Quality System In this CAPA webinar, learn various regulations governing Corrective and Preventive Actions (CAPA) and how organization should collect information, analyze information, identify, investigate product and quality problems, and take appropriate and effective corrective and/or preventive action to prevent their recurrence.
How to Design and Implement a Dynamic Control Plan This webinar training will discuss how to design a dynamic control plan that combines FMEA and the control plan by extending the FMEA to encompass the elements of the control plan and create a living document that helps to drive continual improvement.
An Easy to Implement Integrated Risk Management Approach Compliant with ISO 14971 This integrated risk management training for medical devices will discuss how to incorporate risk management as per ISO 14971 guidelines in all phases of medical device development. It will highlight the documentation needed to support the decisions made as part of the risk management process.
The Use and Mis-use of FMEA in Medical Device Risk Management The presentation will discuss the proper use of FMEA in risk management and how to recognize and avoid the traps associated with this tool in order to have a more efficient risk management process. Most medical device manufacturers use FMEA as a part of their risk management system. Most medical device manufacturers use FMEA as a part of their risk management system.
Root Cause Analysis for CAPA Management (Shutting Down the Alligator Farm) Emphasis will be placed on realizing system interactions and cultural environment that often lies at the root of the problem and prevents true root cause analysis. This webinar will benefit any organization that wants to improve the effectiveness of their CAPA and failure investigation processes.
Root Cause Analysis for Corrective and Preventive Action (CAPA) The Quality Systems Regulation (21 CFR 820) and the Quality Management Standard for Medical Devices (ISO 13485:2003), require medical device companies to establish and maintain procedures for implementing corrective and preventive action (CAPA) as an integral part of the quality system.
Strategies for an Effective Root Cause Analysis and CAPA Program This webinar will provide valuable assistance to all regulated companies, a CAPA program is a requirement across the Medical Device, Diagnostic, Pharmaceutical, and Biologics fields. This session will discuss the importance, requirements, and elements of a root cause-based CAPA program, as well as detailing the most effective ways to determine root cause and describing the uses of CAPA data.
Legal Disclaimer
This piece of content and any of its enclosures, attachments or appendices, references are created to provide solely for information purpose. ComplianceOnline has made all effort to provide accurate information concerning the subject matter covered. This content is created from interpretation, and understanding of relevant and applicable information and it is not all inclusive. It can be best used in conjunction with your professional judgment and discretion.
However, this piece of content and any other ancillary items disseminated in connection with same are not necessarily prepared by a person licensed to practice law in a particular jurisdiction. This piece of content is not a substitute for the advice of an attorney. If you require legal or other expert advice, you should seek the services of a competent attorney or other professional.
ComplianceOnline necessarily is not, cannot and will not be liable for any claims, damages, or regulatory legal proceedings initiated as a consequence of you using whole or any part of the content present in this document. If any action, claim for damages, or regulatory proceedings is commenced against ComplianceOnline as a consequence of your use of this document, then and in that event, you agree to indemnify ComplianceOnline for such claims, and for any attorney's fees expended by ComplianceOnline in connection with defense of same.

Explained: 8 Disciplines of Problem Solving for Improved Product Quality
Table of content.
1 What Exactly is an 8D Problem-Solving Method?
2 Benefits of Implementing 8D Problem-Solving Approach
3 Steps Involved in 8 Disciplines of Problem Solving for Improved Product Quality
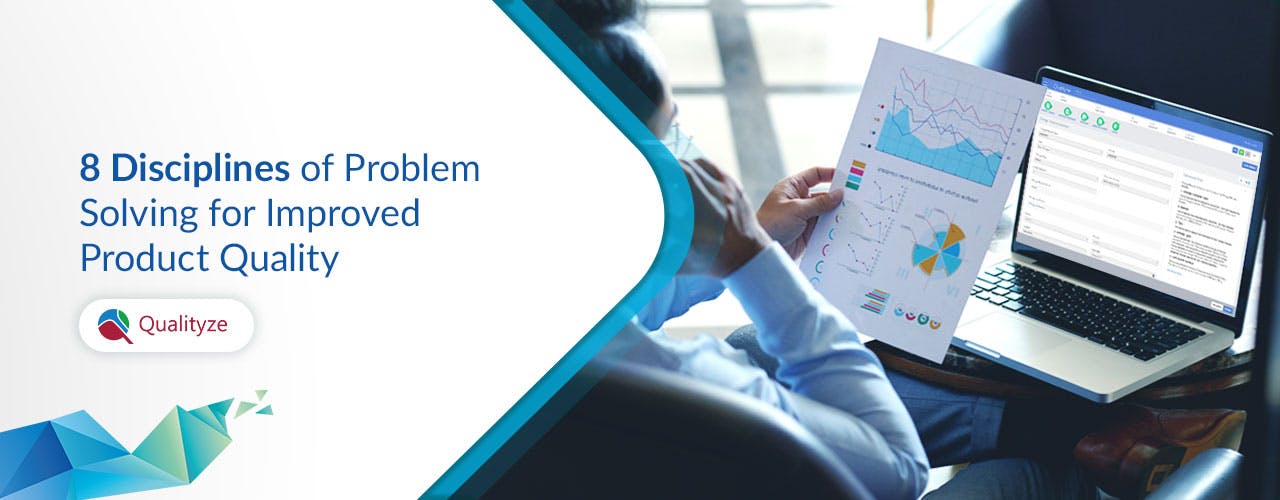
7 Basic Tools of Quality for Process Improvement

Japan is known worldwide for its quality products and services. One of the many reasons for this is its excellent quality management. How did it become so? Japan has Dr. Kaoru Ishikawa to thank for that.
Postwar Japan underwent a major quality revolution. Companies were focused on training their employees in statistical quality control. But soon they realized that the complexity of the subject itself could intimidate most of the workers; so they wanted more basic tools.
Dr. Kaoru Ishikawa, a member of the Japanese Union of Scientists and Engineers (JUSE), took it to his hands to make quality control easier for everyone – even those with little knowledge of statistics – to understand. He introduced the 7 basic tools of quality. They were soon adopted by most companies and became the foundation of Japan’s astonishing industrial resurgence after World War 2.
This post will describe the 7 basic quality tools, how to use them and give you access to templates that you can use right away.
Quality Tools: What Are They?
How can teams and organizations use the 7 basic quality tools, cause and effect diagram, scatter diagram, check sheets.
- Control chart
- Pareto chart
The 7 basic tools of quality, sometimes also referred to as 7 QC tools – represent a fixed set of graphical tools used for troubleshooting issues that are related to quality.
They are called basic quality tools because they can be easily learned by anyone even without any formal training in statistics. Dr. Kaoru Ishikawa played the leading role in the development and advocacy of using the 7 quality tools in organizations for problem-solving and process improvement.
The 7 basic quality tools include;
- Cause-and-effect diagram
- Scatter diagram
- Check sheet
The 7 quality tools were first emphasized by Kaoru Ishikawa a professor of engineering at the University of Tokyo, who is also known as the father of “Quality Circles” for the role he played in launching Japan’s quality movement in the 1960s. During this time, companies were focused on training their employees in statistical quality control realized that the complexity of the subject could intimidate most of the workers; hence they opted for simpler methods that are easy to learn and use. 7 basic tools of quality were thus incorporated company-wide.
Quality tools are used to collect data, analyze data, identify root causes, and measure results in problem-solving and process improvement. The use of these tools helps people involved easily generate new ideas, solve problems, and do proper planning.
- Structured approach: They provide a systematic approach to problem-solving and process improvement, ensuring that efforts are well-organized and focused.
- Data-driven decision making: The tools enable data collection, analysis, and visualization, empowering teams to make informed decisions based on evidence.
- Improved communication and collaboration: Visual representations and structured tools facilitate effective communication and collaboration among team members, leading to shared understanding and alignment.
- Problem identification and prioritization: The tools help identify and prioritize problems or improvement opportunities, enabling teams to allocate resources efficiently and address critical issues first.
- Continuous improvement: By using these tools, teams can establish a culture of continuous improvement, as they provide a framework for ongoing monitoring, analysis, and refinement of processes.
7 Basic Quality Tools Explained with Templates
The 7 quality tools can be applied across any industry. They help teams and individuals analyze and interpret the data they gather and derive maximum information from it.
Flowcharts are perhaps the most popular out of the 7 quality tools. This tool is used to visualize the sequence of steps in a process, event, workflow, system, etc. In addition to showing the process as a whole, a flowchart also highlights the relationship between steps and the process boundaries (start and end).
Flowcharts use a standard set of symbols, and it’s important to standardize the use of these symbols so anyone can understand and use them easily. Here’s a roundup of all the key flowchart symbols .
- To build a common understanding of a process.
- To analyze processes and discover areas of issues, inefficiencies, blockers, etc.
- To standardize processes by leading everyone to follow the same steps.
Real-world examples of usage
- Documenting and analyzing the steps involved in a customer order fulfillment process.
- Mapping out the workflow of a software development lifecycle.
- Visualizing the process flow of patient admissions in a hospital.
Enhances process understanding, highlights bottlenecks or inefficiencies, and supports process optimization and standardization efforts.
How to use a flowchart
- Gather a team of employees involved in carrying out the process for analyzing it.
- List down the steps involved in the process from its start to end.
- If you are using an online tool like Creately , you can first write down the process steps and rearrange them later on the canvas as you identify the flow.
- Identify the sequence of steps; when representing the flow with your flowchart, show it from left to write or from top to bottom.
- Connect the shapes with arrows to indicate the flow.
Who can use it?
- Process improvement teams mapping and documenting existing processes for analysis.
- Business analysts or consultants analyzing workflow and process optimization opportunities.
- Software developers or system designers documenting the flow of information or interactions in a system.
To learn more about flowcharts, refer to our Ultimate Flowchart Tutorial .
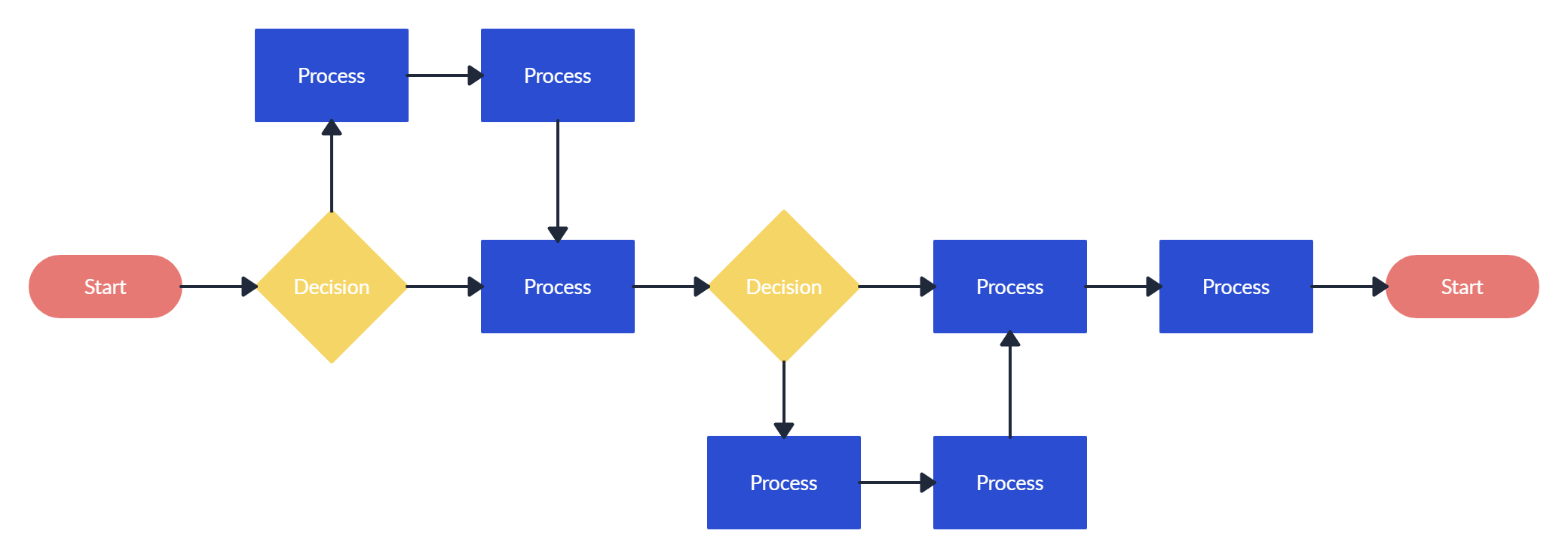
A histogram is a type of bar chart that visualizes the distribution of numerical data. It groups numbers into ranges and the height of the bar indicates how many fall into each range.
It’s a powerful quality planning and control tool that helps you understand preventive and corrective actions.
- To easily interpret a large amount of data and identify patterns.
- To make predictions of process performance.
- To identify the different causes of a quality problem.
- Analyzing the distribution of call wait times in a call center.
- Assessing the distribution of product weights in a manufacturing process.
- Examining the variation in delivery times for an e-commerce business.
Provides insights into process performance and variation, enabling teams to target areas for improvement and make data-driven decisions.
How to make a histogram
- Collect data for analysis. Record occurrences of specific ranges using a tally chart.
- Analyze the data at hand and split the data into intervals or bins.
- Count how many values fall into each bin.
- On the graph, indicate the frequency of occurrences for each bin with the area (height) of the bar.
- Process engineers or data analysts examining process performance metrics.
- Financial analysts analyzing expenditure patterns or budget variances.
- Supply chain managers assessing supplier performance or delivery times.
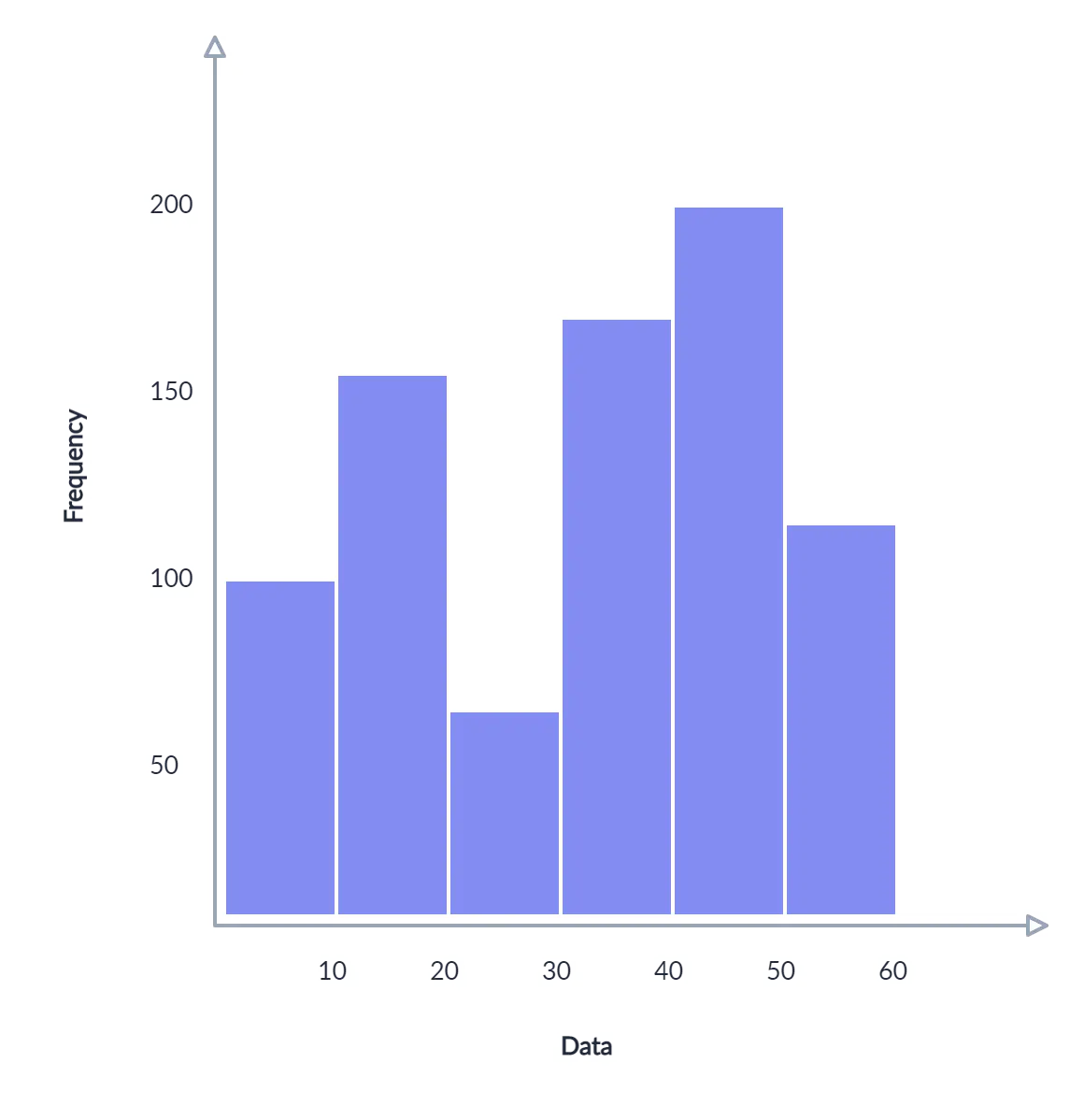
Here’s a useful article to learn more about using a histogram for quality improvement in more detail.
This tool is devised by Kaoru Ishikawa himself and is also known as the fishbone diagram (for it’s shaped like the skeleton of a fish) and Ishikawa diagram.
They are used for identifying the various factors (causes) leading to an issue (effect). It ultimately helps discover the root cause of the problem allowing you to find the correct solution effectively.
- Problem-solving; finding root causes of a problem.
- Uncovering the relationships between different causes leading to a problem.
- During group brainstorming sessions to gather different perspectives on the matter.
- Investigating the potential causes of low employee morale or high turnover rates.
- Analyzing the factors contributing to product defects in a manufacturing process.
- Identifying the root causes of customer complaints in a service industry.
Enhances problem-solving by systematically identifying and organizing possible causes, allowing teams to address root causes rather than symptoms.
How to use the cause and effect diagram
- Identify the problem area that needs to be analyzed and write it down at the head of the diagram.
- Identify the main causes of the problem. These are the labels for the main branches of the fishbone diagram. These main categories can include methods, material, machinery, people, policies, procedures, etc.
- Identify plausible sub-causes of the main causes and attach them as sub-branches to the main branches.
- Referring to the diagram you have created, do a deeper investigation of the major and minor causes.
- Once you have identified the root cause, create an action plan outlining your strategy to overcome the problem.
- Cross-functional improvement teams working on complex problems or process improvement projects.
- Quality engineers investigating the root causes of quality issues.
- Product designers or engineers seeking to understand the factors affecting product performance.
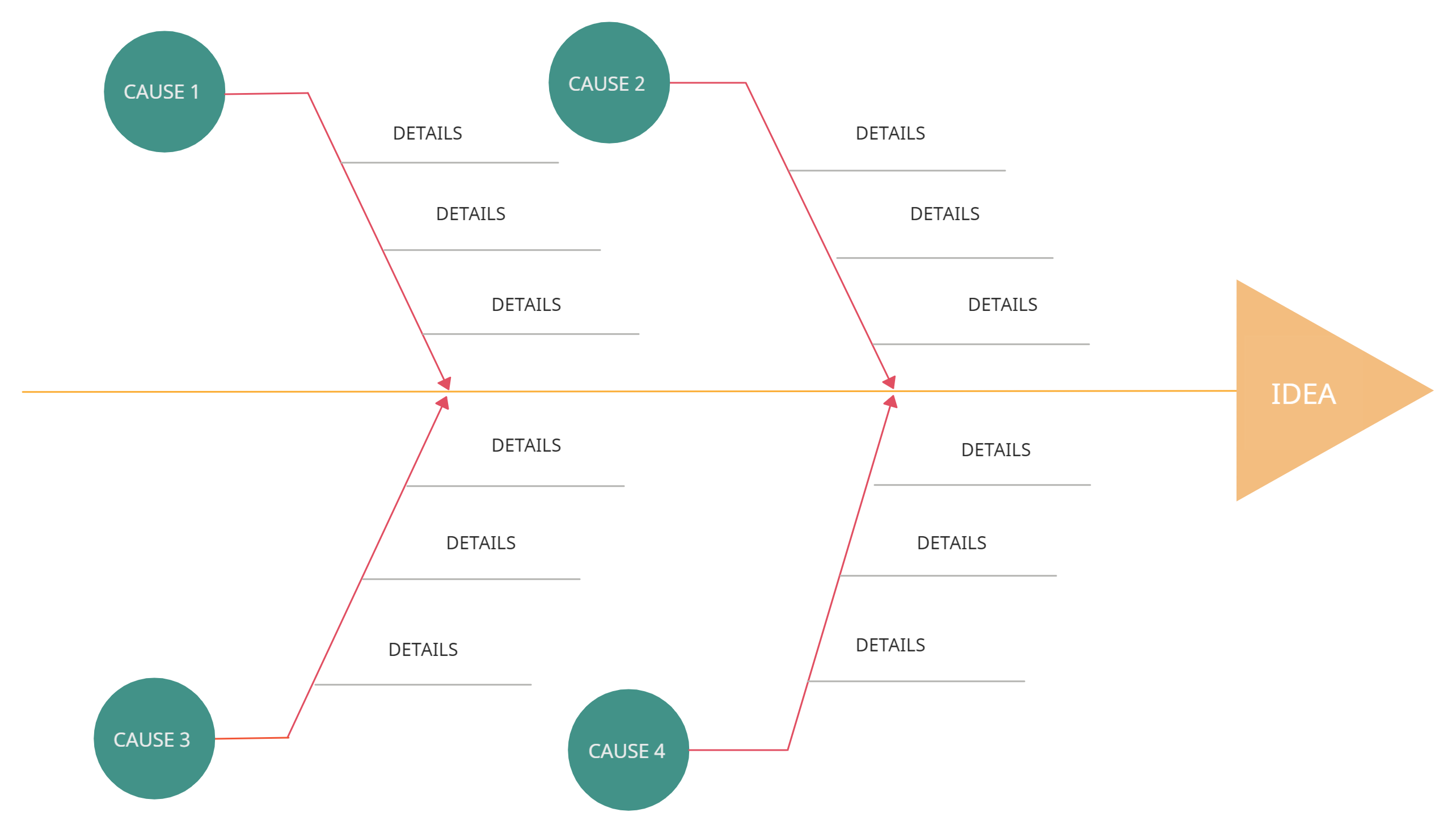
The scatter diagram (scatter charts, scatter plots, scattergrams, scatter graphs) is a chart that helps you identify how two variables are related.
The scatter diagram shows the values of the two variables plotted along the two axes of the graph. The pattern of the resulting points will reveal the correlation.
- To validate the relationship between causes and effects.
- To understand the causes of poor performance.
- To understand the influence of the independent variable over the dependent variable.
- Exploring the relationship between advertising expenditure and sales revenue.
- Analyzing the correlation between employee training hours and performance metrics.
- Investigating the connection between temperature and product quality in a production line.
Helps identify correlations or patterns between variables, facilitating the understanding of cause-and-effect relationships and aiding in decision-making.
How to make a scatter diagram
- Start with collecting data needed for validation. Understand the cause and effect relationship between the two variables.
- Identify dependent and independent variables. The dependent variable plotted along the vertical axis is called the measures parameter. The independent variable plotted along the horizontal axis is called the control parameter.
- Draw the graph based on the collected data. Add horizontal axis and vertical axis name and draw the trend line.
- Based on the trend line, analyze the diagram to understand the correlation which can be categorized as Strong, Moderate and No Relation.
- Data analysts exploring relationships between variables in research or analytics projects.
- Manufacturing engineers investigating the correlation between process parameters and product quality.
- Sales or marketing teams analyzing the relationship between marketing efforts and sales performance.
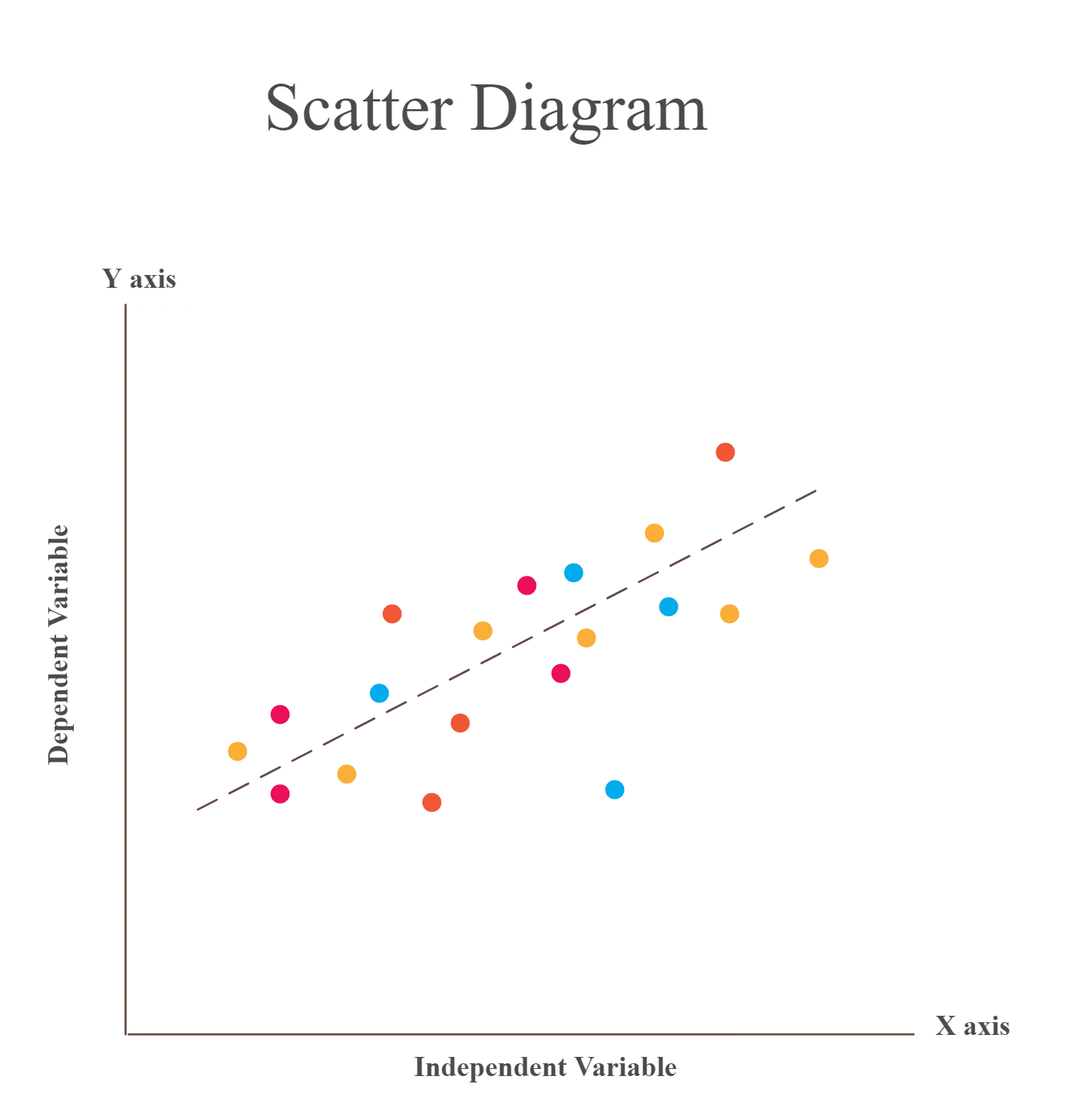
Check sheets provide a systematic way to collect, record and present quantitative and qualitative data about quality problems. A check sheet used to collect quantitative data is known as a tally sheet.
It is one of the most popular QC tools and it makes data gathering much simpler.
- To check the shape of the probability distribution of a process
- To quantify defects by type, by location or by cause
- To keep track of the completion of steps in a multistep procedure (as a checklist )
- Tracking the number of defects or errors in a manufacturing process.
- Recording customer complaints or inquiries to identify common issues.
- Monitoring the frequency of equipment breakdowns or maintenance needs.
Provides a structured approach for data collection, making it easier to identify trends, patterns, and areas for improvement.
How to make a checksheet
- Identify the needed information.
- Why do you need to collect the data?
- What type of information should you collect?
- Where should you collect the data from?
- Who should collect the data?
- When should you collect the data?
- How should you measure the data?
- How much data is essential?
Construct your sheet based on the title, source information and content information (refer to the example below).
Test the sheets. Make sure that all the rows and columns in it are required and relevant and that the sheet is easy to refer to and use. Test it with other collectors and make adjustments based on feedback.
- Quality inspectors or auditors who need to collect data on defects or issues.
- Process operators or technicians responsible for tracking process parameters or measurements.
- Customer service representatives who record customer complaints or inquiries.
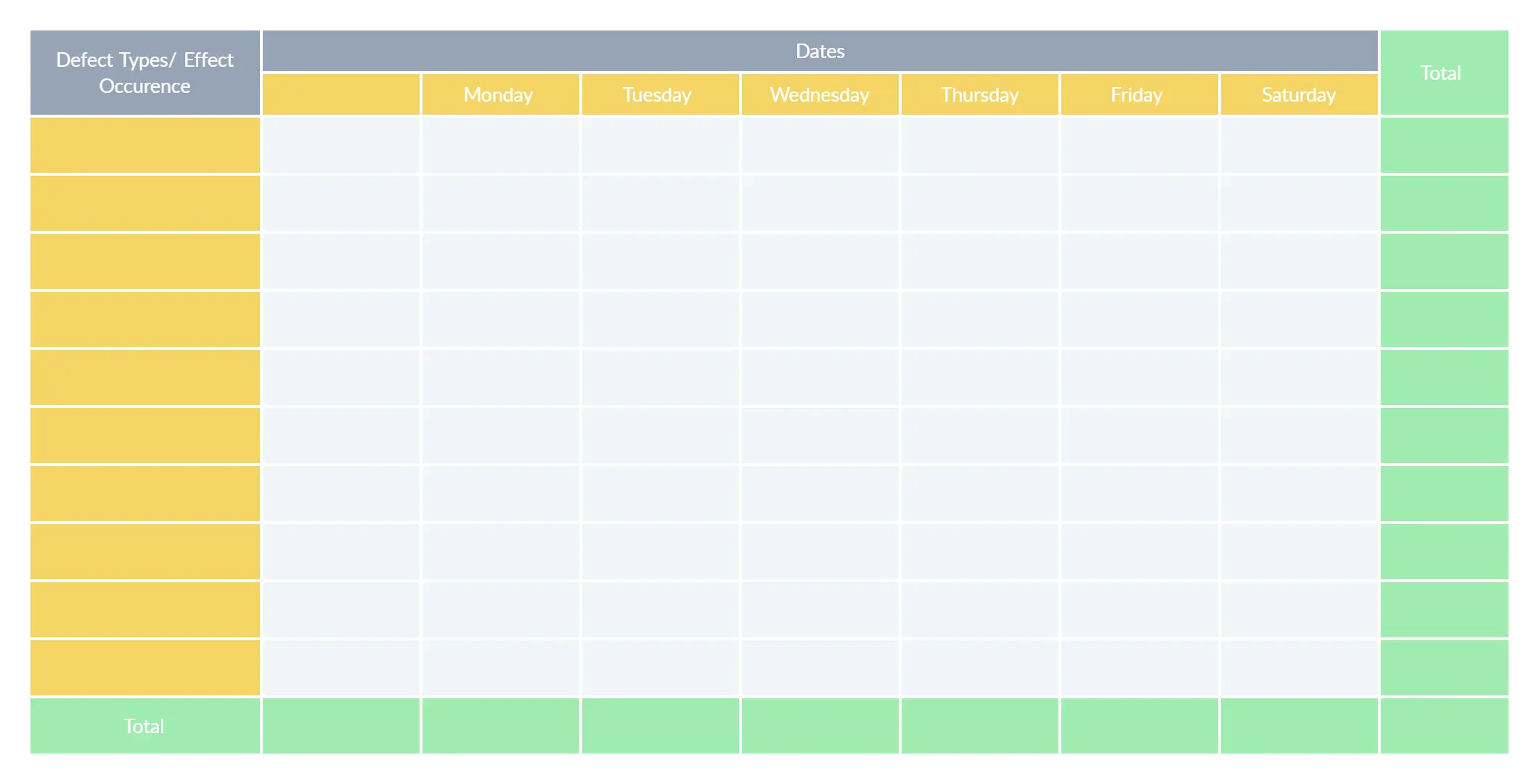
Control Chart
The control chart is a type of run chart used to observe and study process variation resulting from a common or special cause over a period of time.
The chart helps measure the variations and visualize it to show whether the change is within an acceptable limit or not. It helps track metrics such as defects, cost per unit, production time, inventory on hand , etc.
Control charts are generally used in manufacturing, process improvement methodologies like Six Sigma and stock trading algorithms.
- To determine whether a process is stable.
- To monitor processes and learn how to improve poor performance.
- To recognize abnormal changes in a process.
- Monitoring the variation in product dimensions during a manufacturing process.
- Tracking the number of customer complaints received per day.
- Monitoring the average response time of a customer support team.
Enables real-time monitoring of process stability, early detection of deviations or abnormalities, and prompt corrective actions to maintain consistent quality.
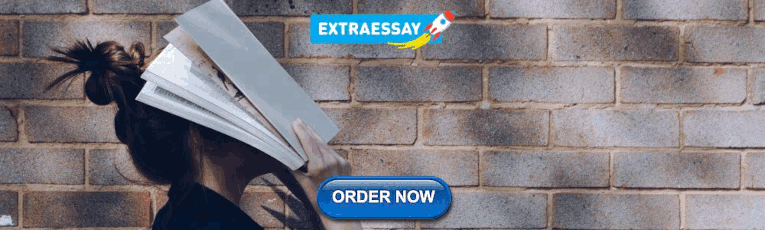
How to create a control chart
- Gather data on the characteristic of interest.
- Calculate mean and upper/lower control limits.
- Create a graph and plot the collected data.
- Add lines representing the mean and control limits to the graph.
- Look for patterns, trends, or points beyond control limits.
- Determine if the process is in control or out of control.
- Investigate and address causes of out-of-control points.
- Regularly update the chart with new data and analyze for ongoing improvement.
- Production supervisors or operators monitoring process performance on the shop floor.
- Quality control or assurance personnel tracking variation in product quality over time.
- Service managers observing customer satisfaction levels and service performance metrics.
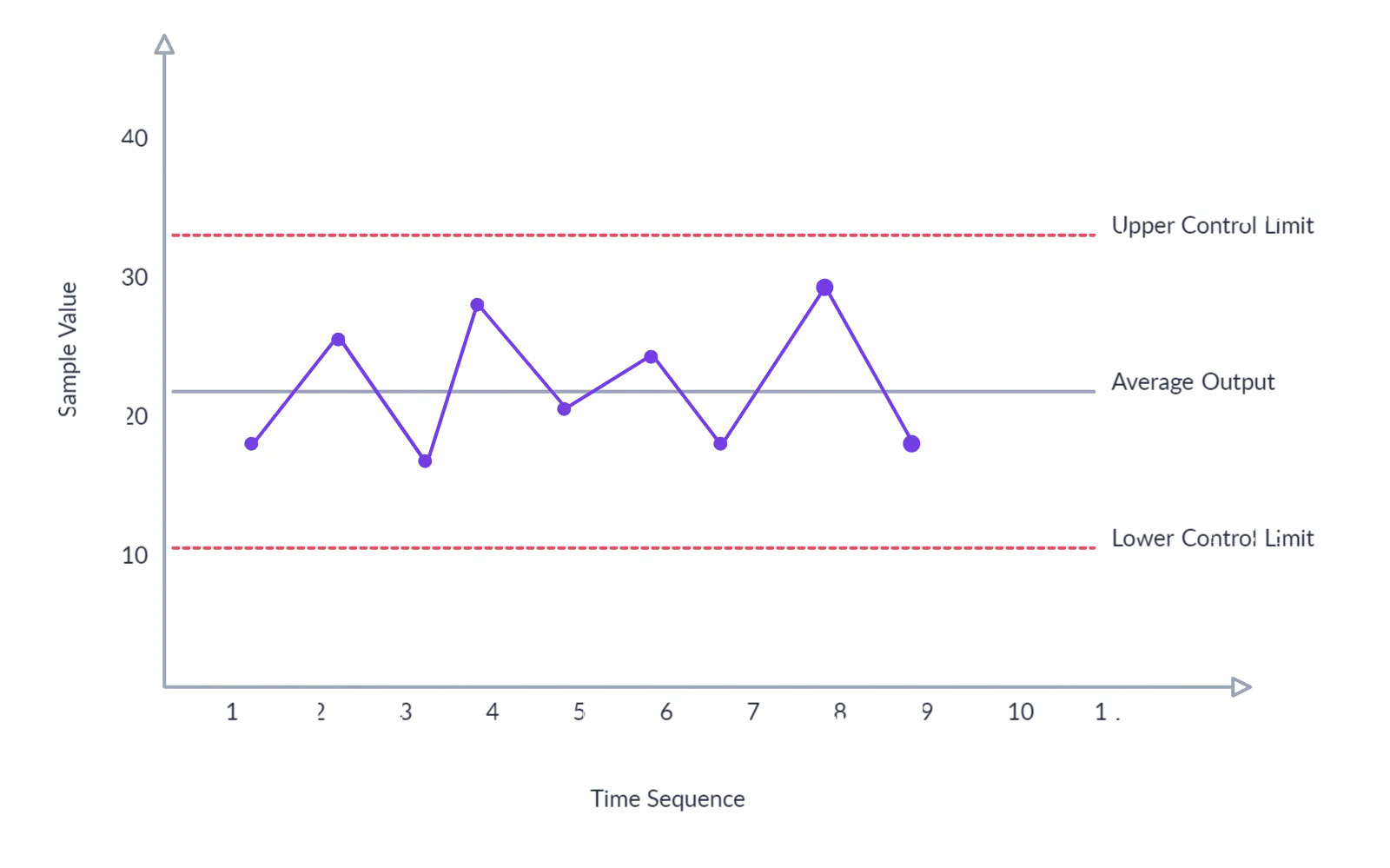
Pareto Chart
The Pareto chart is a combination of a bar graph and a line graph. It helps identify the facts needed to set priorities.
The Pareto chart organizes and presents information in such a way that makes it easier to understand the relative importance of various problems or causes of problems. It comes in the shape of a vertical bar chart and displays the defects in order (from the highest to the lowest) while the line graph shows the cumulative percentage of the defect.
- To identify the relative importance of the causes of a problem.
- To help teams identify the causes that will have the highest impact when solved.
- To easily calculate the impact of a defect on the production.
- Analyzing customer feedback to identify the most common product or service issues.
- Prioritizing improvement efforts based on the frequency of quality incidents.
- Identifying the major causes of delays in project management.
Helps focus improvement efforts on the most significant factors or problems, leading to effective allocation of resources and improved outcomes.
How to create a Pareto chart
- Select the problem for investigation. Also, select a method and time for collecting information. If necessary create a check sheet for recording information.
- Once you have collected the data, go through them and sort them out to calculate the cumulative percentage.
- Draw the graph, bars, cumulative percentage line and add labels (refer to the example below).
- Analyze the chart to identify the vital few problems from the trivial many by using the 80/20 rule . Plan further actions to eliminate the identified defects by finding their root causes.
- Quality managers or improvement teams looking to prioritize improvement initiatives.
- Project managers seeking to identify and address the most critical project risks.
- Sales or marketing teams analyzing customer feedback or product issues.

What’s Your Favorite Out of the 7 Basic Quality Tools?
You can use these 7 basic quality tools individually or together to effectively investigate processes and identify areas for improvement. According to Ishikawa, it’s important that all employees learn how to use these tools to ensure the achievement of excellent performance throughout the organization.
Got anything to add to our guide? Let us know in the comments section below.
Join over thousands of organizations that use Creately to brainstorm, plan, analyze, and execute their projects successfully.
FAQs about 7 Basic Quality Tools
Quality problems in an organization can manifest in various forms and affect different areas of operations.
- Product defects: Products may have defects or non-conformities that deviate from quality specifications, leading to customer dissatisfaction, returns, or warranty claims.
- Service errors: Service errors can occur when services do not meet customer expectations, such as incorrect billing, delays in delivery, or inadequate customer support.
- Process inefficiencies: Inefficient processes can lead to delays, errors, or rework, resulting in increased costs, decreased productivity, and customer dissatisfaction.
- Poor design or innovation: Inadequate product design or lack of innovation can lead to products that do not meet customer needs, lack competitive features, or have usability issues.
- Supplier quality issues: Poor quality materials or components from suppliers can affect the overall quality of the final product or service.
- Ineffective quality management systems: Inadequate quality management systems, such as lack of quality standards, processes, or documentation, can contribute to quality problems throughout the organization.
The basic quality improvement steps typically follow a systematic approach to identify, analyze, implement, and monitor improvements in processes or products.
- Clearly articulate the problem or identify the area for improvement.
- Collect relevant data and information related to the problem.
- Analyze the collected data to identify patterns, root causes, and opportunities for improvement.
- Brainstorm and generate potential improvement ideas or solutions.
- Assess the feasibility, impact, and effectiveness of the generated improvement ideas.
- Develop an action plan to implement the chosen solution.
- Continuously monitor and measure the results of the implemented solution.
- Based on the monitoring results, evaluate the effectiveness of the implemented solution.
- Once the improvement is successful, document the new processes, best practices, or standard operating procedures (SOPs).
- Iterate through the steps to continuously improve processes and products.
More Related Articles
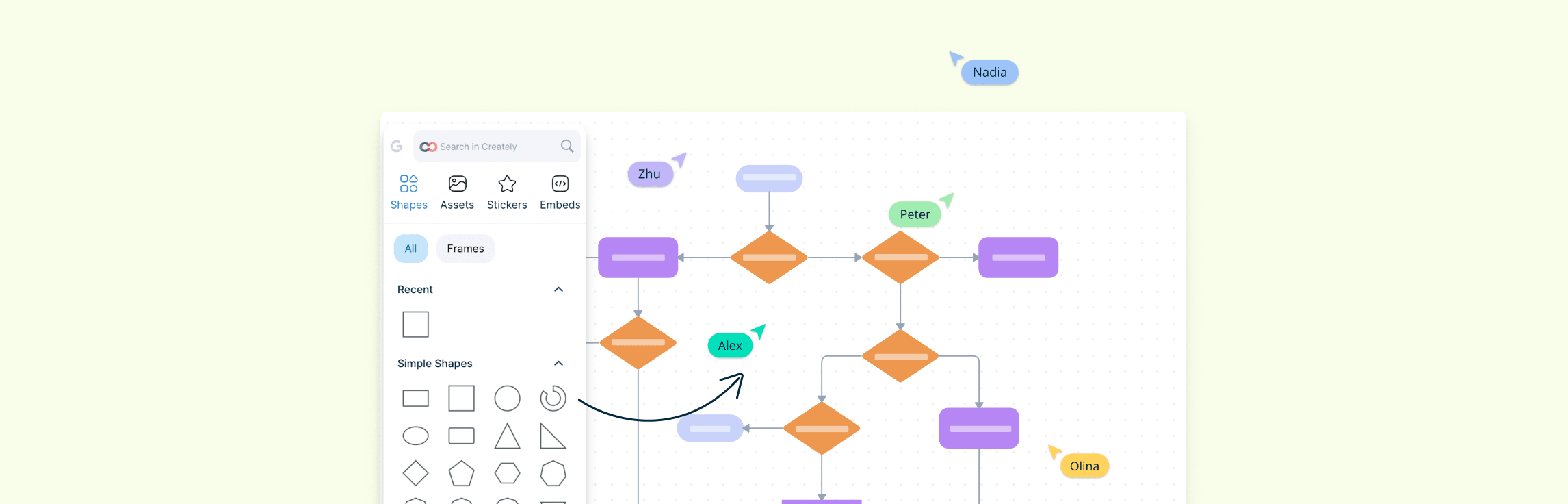
Amanda Athuraliya is the communication specialist/content writer at Creately, online diagramming and collaboration tool. She is an avid reader, a budding writer and a passionate researcher who loves to write about all kinds of topics.
Are you a ComplianceQuest Customer?
8D Management (8 Disciplines Management)

8D Management & The 8D of Problem Solving
Problems are a part of life and a business is no exception. Even with the best of intentions and systems, some errors can creep in and be hard to detect. It may be nothing serious or can have serious repercussions such as reputation damage, heavy fines, product recall, property loss, and so on. It becomes essential to identify the problem, its consequences on the one hand, and causes on the other to be able to not only resolve it for now but also ensure prevention of its recurrence. One of the methodologies, popular amongst engineers and professionals mainly in the automotive industry but now applied across several industries is the eight disciplines (8D) model. It helps to identify, correct, and eliminate recurring problems, affecting improvement in product and process.
Related Assets
Whenever organizations tackle problems and generate solutions based out of root cause analysis, they tend to generate a lot of…
Key Highlights: 8D is an extremely effective, proven problem-solving framework, especially in the manufacturing and automotive sector. However, to truly…
From a quality management standpoint, a problem may be reported in an organization from one of the following processes: Complaints…
What is 8D?
The 8D is a systematic, holistic and proven methodology designed to identify the root cause of a problem, plan a quick fix, and implement corrective actions and preventive actions to avoid their recurrence. If your product is defective or not meeting your customer requirements, then 8D is an excellent first step to improve Quality and Reliability.
One of the core parts of introducing 8D problem solving, greatly accepted by most disciplines of industries, and having huge effectiveness levels in improving product and process quality, would be 8D (Eight Disciplines). Key steps in the 8D methodology are forming a team, defining the problem, identifying and implementing interim containment, identifying the root causes, implementing and verifying permanent corrective actions, and avoiding future recurrence of problems. The 8D process for root cause analysis concludes by highlighting that the team members not only play a vital role but also recognizes them, hence reinforcing that this approach is a collaborative one. 8D has become very popular among manufacturers, assembly, and services around the globe because it is effective and comparatively easy to teach.

Why to Apply 8D Problem Solving Methodology?
The 8D methodology, developed to represent the best practices in problem solving, provides the engineering teams with an effective and efficient team-oriented problem solving skill, a better understanding of Root Cause Analysis (RCA) and how to use basic statistical tools required for problem solving. 8D helps the management understand and resolve problems better, identify necessary systemic changes and inputs for change , and facilitate a more candid and open communication in problem solving discussions.
8D improves the Quality and Reliability of your products, and if performed correctly, prepares the engineering team for future problems.
When to Apply 8D Problem Solving Process?
The 8D problem solving process is used to solve major, critical, chronic, and recurring problems. The 8D is typically required during safety or regulatory issues, customer complaints , warranty concerns, poor performance or test failures, internal rejects, and to minimize waste and scrap.

How to Use Root Cause Analysis to Transform Your Safety Program
8d problem solving approach.
The 8D is a systematic process for the introduction and improvement of quality, and elimination of problems. Here we will show you the step by step approach of the problem solving tools that can make you proficient at identifying causes of problems, defining problems, and errors. Additionally, it helps identify root causes and take actions to solve and prevent identified problems in processes. So, let’s take a peep inside:

D0: Planning and preparing for the 8D
Proper planning and preparation are always a good start before taking any action. So, you need to consider the following before forming a team:
- Problem description
- Timeframe for the resolution
- The number of resources to accomplish this

D1: Team establishment
Create a team with people who varied backgrounds and experiences which will lead to the best quality inputs and a complete solution. For the team to function smoothly, define clear roles, and responsibilities for your people, and have a team leader.

D2: Problem description
The 8D method’s primary focus is to describe the problem appropriately and objectively such that it captures all the vital information. During this analysis, repeated 5W1H (why, what, who, where, when, and how) are required to be asked to develop a clear description.

D3: Problem containment plan
A temporary problem containment plan is sometimes needed to minimize the impact of the problem until you develop permanent solutions. On developing the plan based on the hypothetical cases, the resources for addressing the main problem can be released. At times, new processes may be required to work around the problem until you have a permanent fix.

D4: Root Cause Analysis (RCA)
With the problem temporarily contained, you can now turn to identify all of the root causes of the nonconformance . There are several tools to identify the actual root cause of an issue including the 5W1H to understand the problem in-depth, Fishbone diagrams to visually categorize causes, and Pareto charts to identify the vital causes.

D5: Permanent Corrective Action
Once the root cause of the problem is determined, the team can start brainstorming permanent corrections to identify what the best long-term solution will be. Brainstorming sessions combined with tools such as affinity diagrams help organize ideas based on their relationships and determine the best course of action.

D6: Implement and Validate the Permanent Corrective Action
Once the solution is identified, the management needs to implement and verify the corrective action using the PDCA (plan-do-check-act) approach for small-scale testing before large-scale rollout. Thus, the outcomes and corrective actions are tracked to ensure expected results. To successfully implement a permanent change, a project plan should incorporate:
- Development of the project plan for implementation
- Communicating the plan to all stakeholders
- Validating improvements using measurement

D7: Prevent Recurrence
A complete solution of problems means preventing them from occurring. Besides, preventative measures should also be implemented for corrective actions in the 8D methodology. This requires reviewing management processes, operating procedures, and training manuals to ensure that best practices are followed.
At this stage, organizations should consider actions including updating process audit questions and regularly verifying them based on corrective actions to reduce risk in other processes, presenting poka-yoke or error-proofing devices to big-risk processes, and conducting red rabbit tests to see how long it takes poka-yoke devices to detect defective product.

D8: Verification and Team Celebration
Once the problem is solved, the ultimate step is to congratulate the team. It’s important to recognize their efforts and share their success across the organization because teams require feedback to allow for satisfactory closure. This facilitates motivation and employee engagement while helping you improve quality control, execute process improvements, and aid change management as you grow.

Create a team with people who are having varied backgrounds and experiences which will lead to the best quality inputs and a complete solution. For the team to function smoothly, define clear roles, and responsibilities for your people, and have a team leader.

A complete solution of problems means preventing them from occurring initially. Besides, preventative measures should also be implemented for corrective actions in the 8D methodology. This requires reviewing management processes, operating procedures, and training manuals to ensure that best practices are followed.
8D Root Cause Analysis (RCA) and 8D Corrective Action Process
The 8D Root Cause Analysis, as well as the 8D Corrective Action process, is a widely systematic approach in quality management, especially concerning 8D in quality control. This method includes eight comprehensive steps that are devised to problem solving by dealing with root causes of the problems comprehensively. The steps of the 8D process start with the formation of a team, a clear definition of the problem, and move on to interim containment actions. This is then followed by detailed root-cause analysis using the 8D RCA process, development and verification of permanent corrective actions, implementation, and recurrence preventing efforts. Encouraging details in the analysis: the 8D methodology steps encompass collaborative efforts and documentation that ensure durable solutions and continuous improvement in organizational processes. Root Cause Analysis (RCA) is embedded within the 8D process and includes the following steps and techniques:

Problem Symptom is measured and transformed to “Object and Defect”

Problem Symptom is reformed to Problem Statement using the 5W1H process

Potential Causes are gathered using the tools like Fishbone or Affinity Diagram

Problem Statement should fit using both the “is” and the “isn’t” sections of the question

Root Cause concepts are developed from remaining possible causes on the tool and related changes from is/is not

Compare theories with recent data and develop experiments for Root Cause Verification

Test and confirm the Root Causes

Customer Success
3 Women Leaders Making a Powerful Impact in Global Quality and Safety Management
How to use the 8d approach.
8D portrays 8 steps of a structured approach to solve difficult, recurring, or critical problems by providing transparency, driving a team approach, and increasing the chances of solving the problem.
Proper plan for solving the problem and identify the prerequisites.
Team creation
Gather a cross-functional team with product/process knowledge.
Problem description and definition
Use the data and information to specify the problem by identifying in quantifiable terms the who, what, where, when, why, how, and how many (the 5W1H) for the problem.
Problem Containment Plan development
Develop and implement interim actions to eliminate the problem from any customer in the future.
Specify and assess Root Causes
Identify and review all relevant causes and sources of variation that analyze why the problem has occurred and figure out why the problem was not noticed at first using 5W1H or diagrams.
Verify Permanent Solutions
After collecting data confirm that the possible solutions will actually resolve the problem.
Implement and Validate Corrective Actions
Discuss and review results and develop plans to implement the best solutions or countermeasures.
Preventive measures
Transform the operation systems, management systems, procedures, and practices to avoid the recurrence of similar problems.
Compliment your team
Recognize the collective efforts of your team and formally thank them for their involvement.
8D Problem Solving Tools and Techniques
The 8D problem solving methodology is the set of tools and methods aiming for complex quality issues. 8D problem solving techniques are basically comprised of a fishbone diagram, 5 Whys analysis, Pareto charts, process flowcharts, and Failure Mode and Effects Analysis (FMEA) to come to terms with the 8D framework. Integration with statistical tools and data analysis in every step of 8D analysis is sure to make the most accurate identification of the root cause.
This approach would ensure that cross-functional teams' participation would not only be present in the brainstorming sessions but also in the 8D problem solving process at the problem solving stage.

Training in 8D Methodology
8D training is an inevitable imperative that makes its deployment in organizations effective. The 8D methodology provides all the necessary details that the teams could apply to the skills and knowledge required at every step in 8D of quality control . Training the workforce on 8D methodology will make them able to apply these aspects when dealing with real-world problems, which will better off the quality and efficiency of the entire organization. It ensures that all these measures and strategies have been inducted to make sure that 8D problem solving approaches are not just tools for problem solution but have been inducted to lay down the base for sustainable quality improvement and prevention practices in the organizational processes.
Great product, support, and people to work with!
We have rolled-out CQ across our company to automate various elements of QMS requirements such as Document Management, Complaints, Non-conformances, Corrective Action (8D and A3), Supplier Management and Audit Management. We have been using the software for more than 2 years. We are glad to see how well the system is being used across the company. We have several thousand users on the system currently and working to scale the usage further. CQ solution has been configured to meet our needs, works elegantly across languages, across time zones, and business verticals. With integration between CQ and SAP to exchange critical data, the process automation provides a lot of productivity.
CQ configuration team and support have worked hard to ensure that our needs continue to be met. They consistently go above and beyond. We cannot be more pleased with our use of CQ QMS capabilities and would definitely recommend to anyone who is looking for a modern cloud based EQMS solution especially if you want a scalable EQMS solution.
Lia Budiman, Continental Contitech

8D Problem Solving Report
8D problem solving reports and templates are useful tools to initiate a problem solving process. These reports are used to explain what 8D is and including information about each step so that one will know what needs to be done by attempting this to solve problems. Keeping these reports easily available can avoid repeating work on the same problems over and over again.
8D reports must be detailed and incorporate information at every step within the 8D process. Those who are working on the problem should provide sufficient information when completing a report so that someone who was not on the current 8D team can pull it out and understand what the problem was and what solutions were implemented.

Who Can 8D Help?
The 8D methodology is universally applicable for every organization that needs solving. Although, there are a few industries and sectors where this 8D approach is successfully used such as manufacturing, the automotive industry , engineering companies that manufacture products or parts, and medium and large-scale enterprises.
Improve quality, eliminate problems and identify the root cause of a problem with 8d Methodology
Related checklists.

Quality Assurance Checklist – Part A (Project Management)
Checklist | September 7th, 2022

Quality Assurance Checklist – Part B (Project Deliverables)

Quality Control Area Safety Audit Checklist for Pharmaceutical Companies
Checklist | April 22nd, 2022
Quality-centric Companies Rely on CQ QMS

Frequently Asked Questions
The 8D methodology is often used since it provides a consistent, simple, and thorough approach to solving raised problems at various stages. If properly applied, it gives several advantages such as:
A systematic approach for improving team-oriented problem solving skills
A clear understanding of basic statistical tools needed for problem solving
A practical understanding of the ‘ root cause analysis’ tool
Creating and expanding relative information about past failures and lessons learned to avoid future problems in the organization
Improving skills for corrective action deployment
When the team is trying to find the root cause of the problem and deploy corrective actions, some defective products will continue to be manufactured. To prevent these defective parts from reaching the customer, interim containment ensures that the defects are contained in the facility till the problem is completely solved. If defective parts reach the customer, it may result in warranty claims, field failures, and customer complaints.
To implement the 8D process successfully, the following factors are crucial:
The right team
An accurate description of the problem
Avoiding skipping through steps
Ensuring cooperation within the team and management support
Understanding the difference between real causes and possible causes
Related Insights

5 Dos and Don’ts When Choosing a QMS Solution for Your Enterprise
Every investment a business makes should have a measurable impact. In the case of an EQMS, the ROI is based…
Root Cause Analysis – Definition, Benefits and Process
All Quality and Safety Management Standards emphasize the importance of…
5 Why vs. Pareto Chart vs. Fishbone Diagram – Pros and Cons of Each of These RCA Techniques
All Quality Management Standards emphasize the importance of identifying the…
Automated CAPA with RCA and 5 Why to Make Your Workplace Healthy and Safe
PGT Innovations (PGT), pioneers in the impact-resistant window and door…
Connect with a CQ Expert
Learn about all features of our Product, Quality, Safety, and Supplier suites. Please fill the form below to access our comprehensive demo video.

Please confirm your details
By submitting this form you agree that we can store and process your personal data as per our Privacy Statement. We will never sell your personal information to any third party.
In Need of Smarter Ways Forward? Get in Touch.
Got questions we can help.
Chat with a CQ expert, we will answer all your questions.
Critical Challenges faced by Quality Departments and Recommended Actions
Each organization’s challenges may stack up differently based on considerations like industry sector, product/service type, customer base and culture..
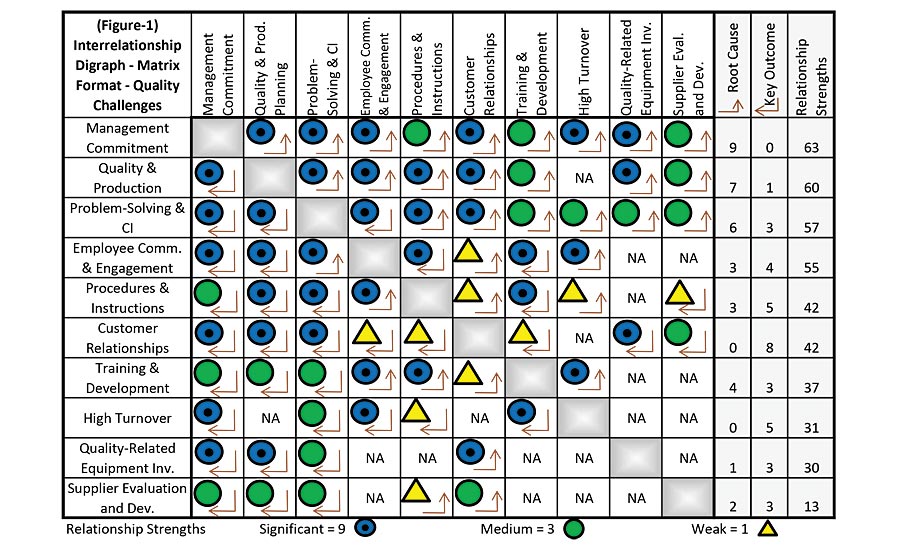
Figure 1. An interrelationship digraph in a matrix format was created to rate the relative importance of the priority quality challenges.
Successful management and leadership of the quality department for an organization involves an integrated approach that includes a communication network that extends both horizontally and vertically within the organization as well as outward to customers and suppliers.
The top 10 challenges identified below are the primary constraints to achieving effective quality assurance. Each challenge is defined, concerns indicated and successful resolution identified. Most of these challenges are interrelated; therefore, one will often affect others.
These challenges are especially critical in a new or turnaround operation where quality has either not been established or otherwise ignored for an extended amount of time. An organization may also experience multiple challenges in the same timeframe as well as high turnover, primarily in the quality department.
An interrelationship digraph in a matrix format was created to rate the relative importance of the priority quality challenges (Figure 1). Most notable are the top three challenges (management commitment, inadequate quality and production planning and problem-solving CI teams) which share in common a high number of root causes in addition to the relationship strengths. My interpretation of this result based on these three challenges is that risk analysis is critical for an organization. The high outcome rating for “customer relationships” in the matrix is not surprising in that many internal processes ultimately affect customers.
Ratings for these challenges are based on the organizations I have worked for as well as various customer and supplier interactions. My primary experience has been in the automotive part manufacturing sector.
1. Management Commitment – All the challenges listed here connect to management commitment. Failure to communicate the appropriate details for management will almost certainly lead to a lack of support. Identifying and determining the details, cost and justification, setting a timeline and getting approval for completing all necessary activities is an essential first step in a plan to successfully address challenges and reduce risk. Providing management with updated status on these challenges is also important.
2. Inadequate Quality & Production Planning – It is critical for the sales function to have the technical and logistical capability as well as team support to produce reasonable quotes. Without a proper team feasibility review with all relevant stakeholders before committing to a price and subsequent PO, sales may underquote. This deficiency can lead to compromises in quality. The feasibility review should also include risk analysis to stay ahead of any potential technical or logistical issues. Make sure all customer requirements derived from drawings and specifications are clearly understood by all internal and external stakeholders. If the organization needs other specifications to further clarify “grey areas” or otherwise protect them, include those as well. Do not assume you cannot negotiate existing or new specifications. Negotiating specifications could increase the organization’s capability to produce the required product as well as minimize cost for the customer and organization.
3. Quality Support for Problem-Solving and Continuous Improvement Project Teams – Ongoing efforts to resolve problems and otherwise continue to make improvements based on the importance of issues is imperative to maximize the effectiveness of an organization as well as stay ahead of the competition. Failure to form and maintain these project teams as well as include the appropriate team members will lead to higher scrap rates, decreased customer satisfaction and increased risk for the organization. Team leaders that maintain priority-based action item lists with firm completion dates should drive these teams. Team leaders should keep top management in the loop to sustain their commitment to the resources needed to address the challenges.
4. Employee Communication and Engagement – Keeping all employees in the loop is essential to productivity and quality as well as the morale of the organization and can drive a positive culture. This approach is a two-way street that includes communicating with the employees as well as getting input from employees. Failure to make these connections will lead to gaps in information shared both ways that will cause a decline in quality and productivity as well as employees’ willingness to contribute. Methods to communicate to employees include monthly meetings, posting (current) results, newsletters, etc. On the other side, maximizing engagement includes involving employees in corrective actions, continuous improvement initiatives, training needs assessments, etc. Communication and engagement also involve managers visiting work areas on a regular basis to facilitate informal two-way conversations.
5. Procedures and Instructions not Written or Updated – This is one of the most common findings in ISO-9001 QMS third-party audits for organizations that certify to this standard. Some organizations rely too much on verbal communications and partially retained memories. The extent of documentation should be determined based on the complexity and interactions of the various processes as well as the scope of training for the employee. A guideline to use for developing a work instruction set is to have a basic version visible at the point of use for those who perform the task regularly. Also, have a more detailed version taken from the training documentation available at the point of use accessible by recently trained employees or employees that have not run the process for a while. There should also be a system of tracking documents to assure the most current version is available.
6. Breakdown in Customer Relationships – This is usually a result of poor or declining quality or delivery and related communications. Accompanying this is poor follow-up on issues or otherwise no substantial progress to resolve issues. It is critical to maintain ongoing communications on the status of any issues that includes an action plan with identified dates of completion. Depending on the significance of the issue, you may communicate by email or phone. Use the phone when speed and clarity are essential. Document calls by following up with emails to primary stakeholders.
7. Training and Development – This is a systemic issue for the majority of organizations at some level. There is a tendency to get new employees to the work areas as soon as possible. Managers that interact regularly with new employees in their work areas indicate that employees often express concern about training for their job. Employees are afraid to approach their supervisor for fear of criticism for not retaining all the information communicated to them during their brief training session and that it is not available at the point of use. The ideal training program should consist of an approved documented program that considers past experience and entails the level of complexity depending on the type of job. This hands-on approach should include describing the job, show them how to do the job, and then letting them do the job to validate their training. The trainee should also be comfortable asking follow-up questions, and there should be a mentor assigned to the trainee for a designated amount of time, depending on the level of complexity.
8. High Turnover and Shortage in Quality and Production Employees – High turnover rates can have a substantial effect throughout all levels of the organization. Reasons for high turnover can include inadequate pay, lack of appreciation or being mistreated by the supervisor, and insufficient training related to performance issues (employee leaves or is terminated). As the popular phrase goes, “people are your best resource.” This should always be on the minds of management. Ongoing and adequate training and development, praise for a good job done, and appropriate pay for a given job will go a long way to retain employees at all levels of seniority as well as affect the bottom line.
9. Lack of Investment in Quality Equipment or Quality-Related Production Equipment – After setting priorities for equipment repair, refurbishment or replacement through problem-solving or continuous improvement teams, management needs to plan ahead to have the financing available to address the challenges. Many companies have great expectations on the front end of problem-solving and continuous improvement initiatives but stall out due to declining or shifting priorities. Return on investment for many capital projects is typically one to three years based on quantifiable and qualifiable considerations. Management must have the strategic vision to maintain the commitment to move forward with these investments.
10. Supplier Evaluation and Development – Suppliers are an important part of the quality equation. All too often, suppliers fall off the radar until they have issues. Frequently, these issues are only taken seriously when reject supplier material reaches the organization’s customer. Suppliers providing material with critical characteristics should be high on a priority list for evaluation and development. Purchasing and quality should thoroughly assess all critical suppliers before their approval for use. In some cases, dual sourcing could also be considered as a contingency when a supplier is unable to provide an acceptable material.
Of course, each organization’s challenges may stack up differently based on considerations like industry sector, product/service type, customer base and culture.
Accurately identifying the challenges your organization faces along with getting management commitment are critical first steps in effectively working toward a successful resolution.
This approach aims to move an organization from a reactive (firefighting) position to a proactive (best in class) position. Q
Share This Story
Don Goolsby has worked for over 25 years in manufacturing management, primarily in quality. His academic background includes a B.S. degree in engineering technology and manufacturing from Tennessee Technological University in Cookeville, TN, an MBA from The University of Phoenix, a Lean Six Sigma Black Belt Certification, and a Baldrige examiner. Find him on LinkedIn at www.linkedin.com/in/dgoolsby .
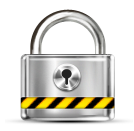
Restricted Content
You must have JavaScript enabled to enjoy a limited number of articles over the next 30 days.
Related Articles
Quality test & inspection: change solves navy's quality challenges, quality management: more pay, more challenges, quality innovations: address metrology challenges, get our new emagazine delivered to your inbox every month., stay in the know with quality’s comprehensive coverage of the manufacturing and metrology industries..
Copyright ©2024. All Rights Reserved BNP Media.
Design, CMS, Hosting & Web Development :: ePublishing
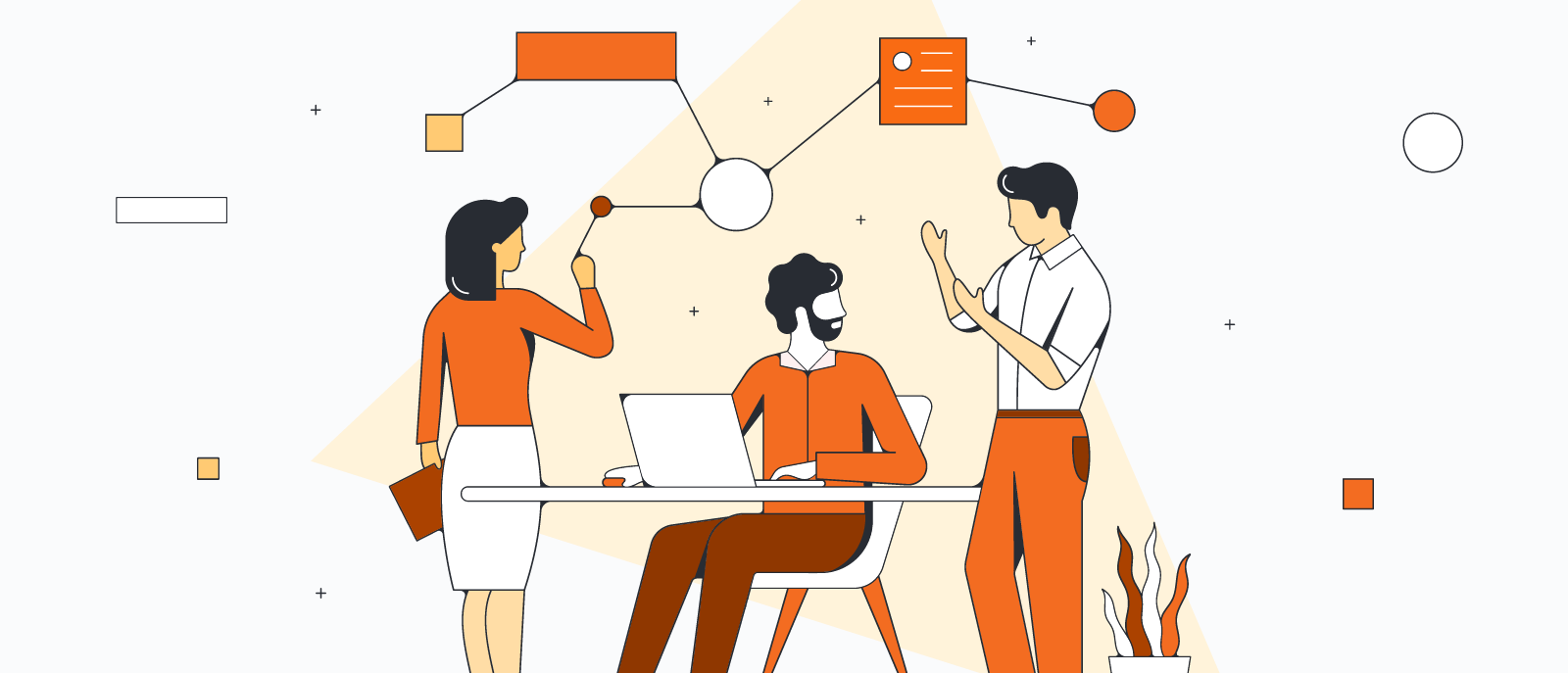
What are the 7 basic quality tools, and how can they change your business for the better?
Reading time: about 6 min
What are the 7 basic quality tools?
- Stratification
- Check sheet (tally sheet)
- Cause and effect diagram (fishbone or Ishikawa diagram)
- Pareto chart (80-20 rule)
- Scatter diagram
- Control chart (Shewhart chart)
The ability to identify and resolve quality-related issues quickly and efficiently is essential to anyone working in quality assurance or process improvement. But statistical quality control can quickly get complex and unwieldy for the average person, making training and quality assurance more difficult to scale.
Thankfully, engineers have discovered that most quality control problems can be solved by following a few key fundamentals. These fundamentals are called the seven basic tools of quality.
With these basic quality tools in your arsenal, you can easily manage the quality of your product or process, no matter what industry you serve.
Learn about these quality management tools and find templates to start using them quickly.
Where did the quality tools originate?
Kaoru Ishikawa, a Japanese professor of engineering, originally developed the seven quality tools (sometimes called the 7 QC tools) in the 1950s to help workers of various technical backgrounds implement effective quality control measures.
At the time, training programs in statistical quality control were complex and intimidating to workers with non-technical backgrounds. This made it difficult to standardize effective quality control across operations. Companies found that simplifying the training to user-friendly fundamentals—or seven quality tools—ensured better performance at scale
7 quality tools
1. stratification.
Stratification analysis is a quality assurance tool used to sort data, objects, and people into separate and distinct groups. Separating your data using stratification can help you determine its meaning, revealing patterns that might not otherwise be visible when it’s been lumped together.
Whether you’re looking at equipment, products, shifts, materials, or even days of the week, stratification analysis lets you make sense of your data before, during, and after its collection.
To get the most out of the stratification process, consider which information about your data’s sources may affect the end results of your data analysis. Make sure to set up your data collection so that that information is included.
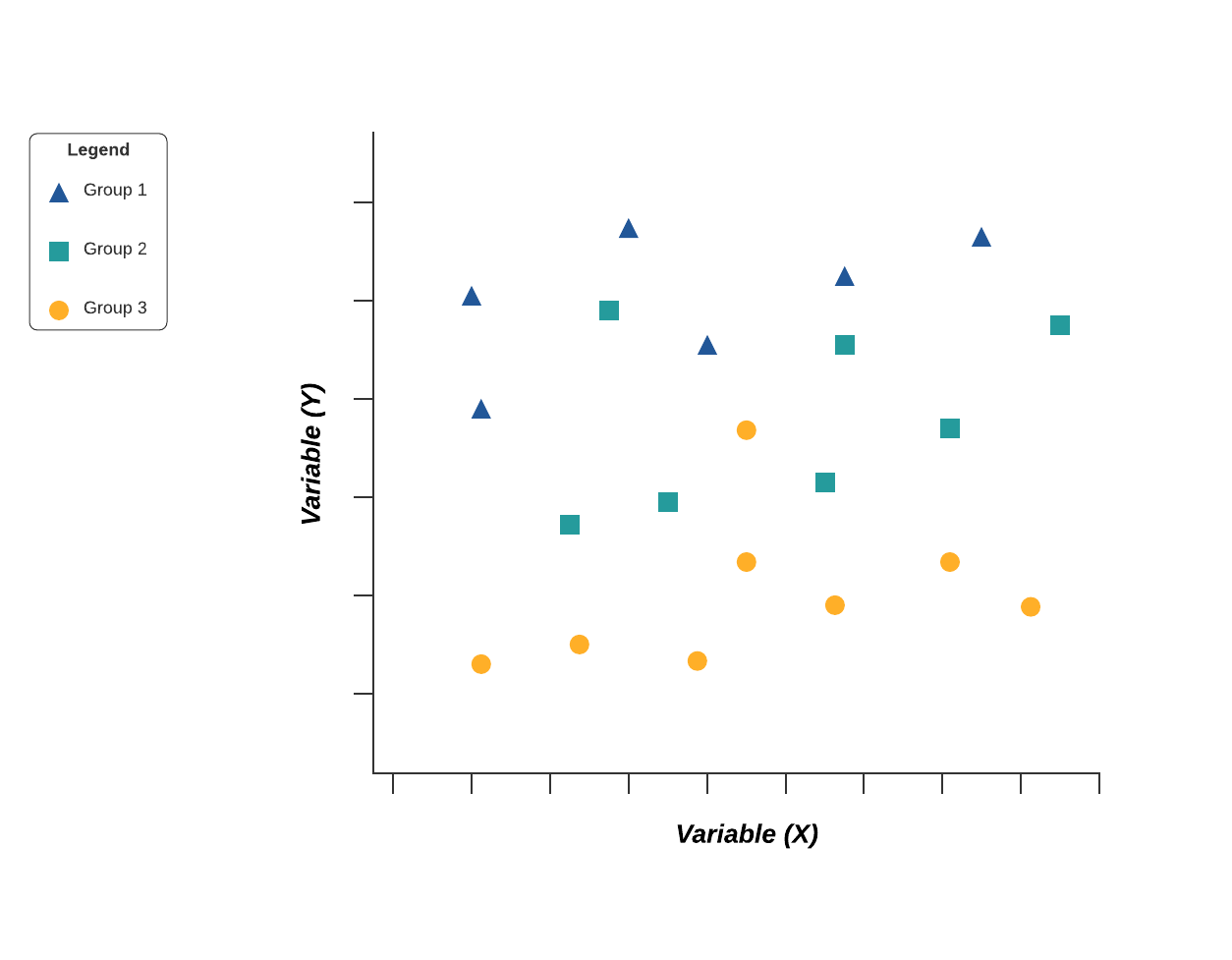
2. Histogram
Quality professionals are often tasked with analyzing and interpreting the behavior of different groups of data in an effort to manage quality. This is where quality control tools like the histogram come into play.
The histogram represents frequency distribution of data clearly and concisely amongst different groups of a sample, allowing you to quickly and easily identify areas of improvement within your processes. With a structure similar to a bar graph, each bar within a histogram represents a group, while the height of the bar represents the frequency of data within that group.
Histograms are particularly helpful when breaking down the frequency of your data into categories such as age, days of the week, physical measurements, or any other category that can be listed in chronological or numerical order.
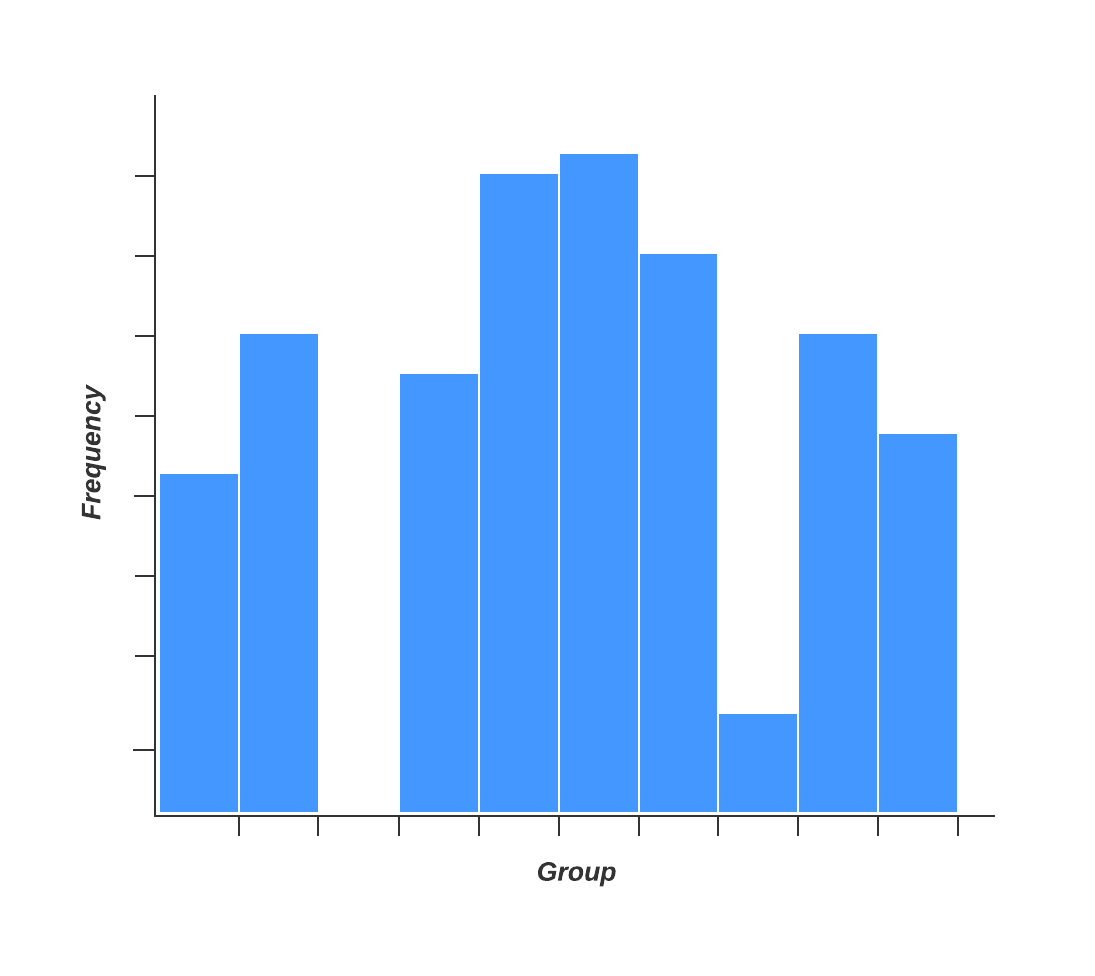
3. Check sheet (or tally sheet)
Check sheets can be used to collect quantitative or qualitative data. When used to collect quantitative data, they can be called a tally sheet. A check sheet collects data in the form of check or tally marks that indicate how many times a particular value has occurred, allowing you to quickly zero in on defects or errors within your process or product, defect patterns, and even causes of specific defects.
With its simple setup and easy-to-read graphics, check sheets make it easy to record preliminary frequency distribution data when measuring out processes. This particular graphic can be used as a preliminary data collection tool when creating histograms, bar graphs, and other quality tools.

4. Cause-and-effect diagram (also known as a fishbone or Ishikawa diagram)
Introduced by Kaoru Ishikawa, the fishbone diagram helps users identify the various factors (or causes) leading to an effect, usually depicted as a problem to be solved. Named for its resemblance to a fishbone, this quality management tool works by defining a quality-related problem on the right-hand side of the diagram, with individual root causes and sub-causes branching off to its left.
A fishbone diagram’s causes and subcauses are usually grouped into six main groups, including measurements, materials, personnel, environment, methods, and machines. These categories can help you identify the probable source of your problem while keeping your diagram structured and orderly.
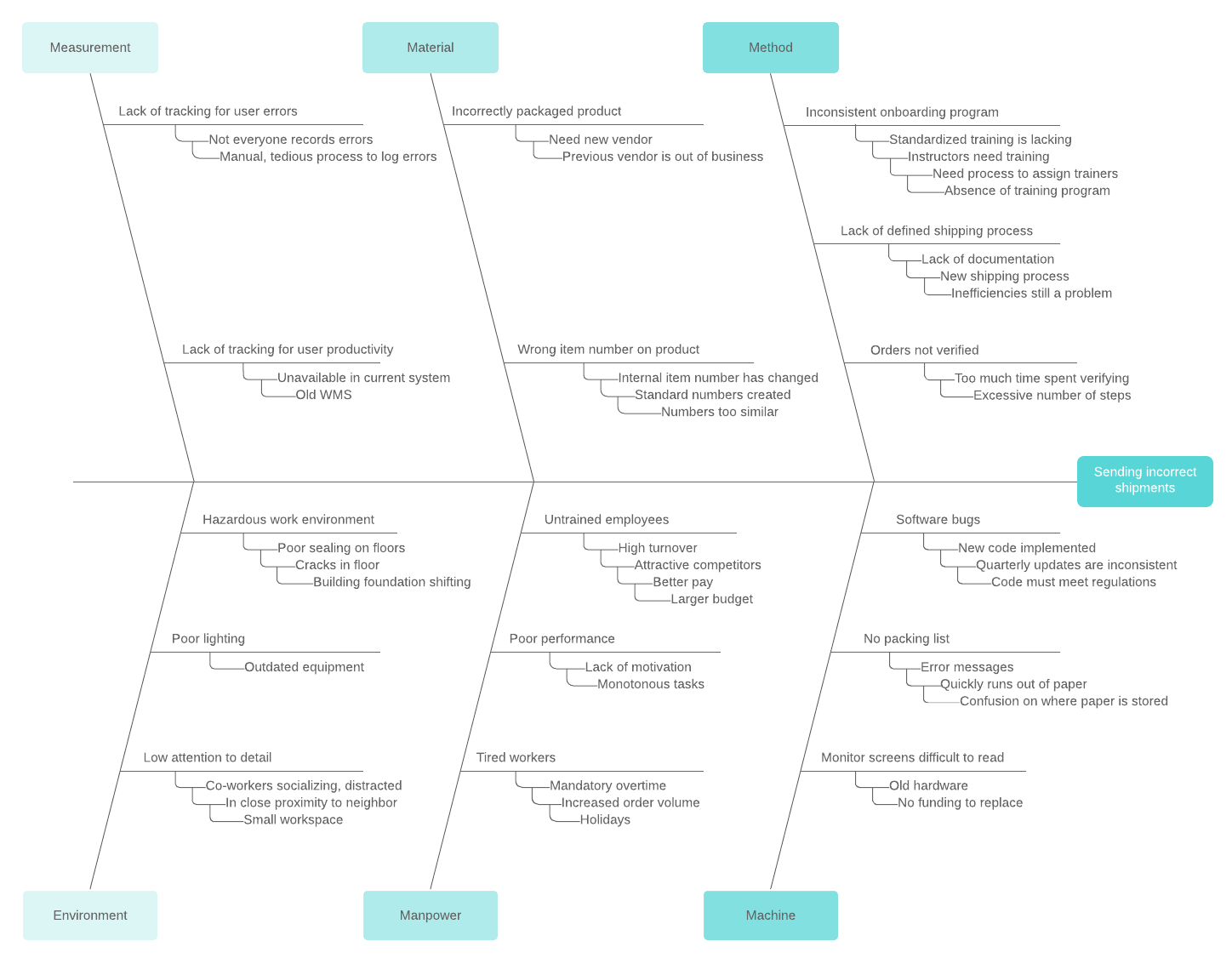
5. Pareto chart (80-20 rule)
As a quality control tool, the Pareto chart operates according to the 80-20 rule. This rule assumes that in any process, 80% of a process’s or system’s problems are caused by 20% of major factors, often referred to as the “vital few.” The remaining 20% of problems are caused by 80% of minor factors.
A combination of a bar and line graph, the Pareto chart depicts individual values in descending order using bars, while the cumulative total is represented by the line.
The goal of the Pareto chart is to highlight the relative importance of a variety of parameters, allowing you to identify and focus your efforts on the factors with the biggest impact on a specific part of a process or system.
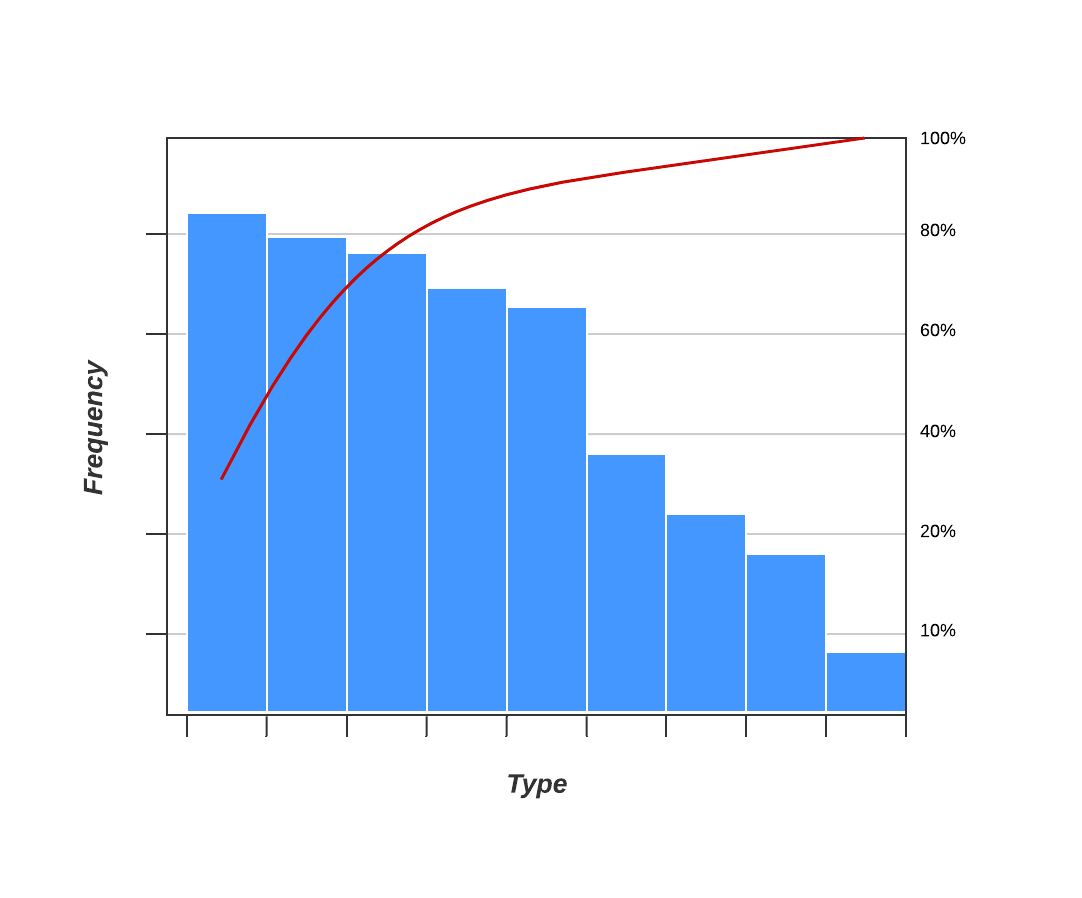
6. Scatter diagram
Out of the seven quality tools, the scatter diagram is most useful in depicting the relationship between two variables, which is ideal for quality assurance professionals trying to identify cause and effect relationships.
With dependent values on the diagram’s Y-axis and independent values on the X-axis, each dot represents a common intersection point. When joined, these dots can highlight the relationship between the two variables. The stronger the correlation in your diagram, the stronger the relationship between variables.
Scatter diagrams can prove useful as a quality control tool when used to define relationships between quality defects and possible causes such as environment, activity, personnel, and other variables. Once the relationship between a particular defect and its cause has been established, you can implement focused solutions with (hopefully) better outcomes.
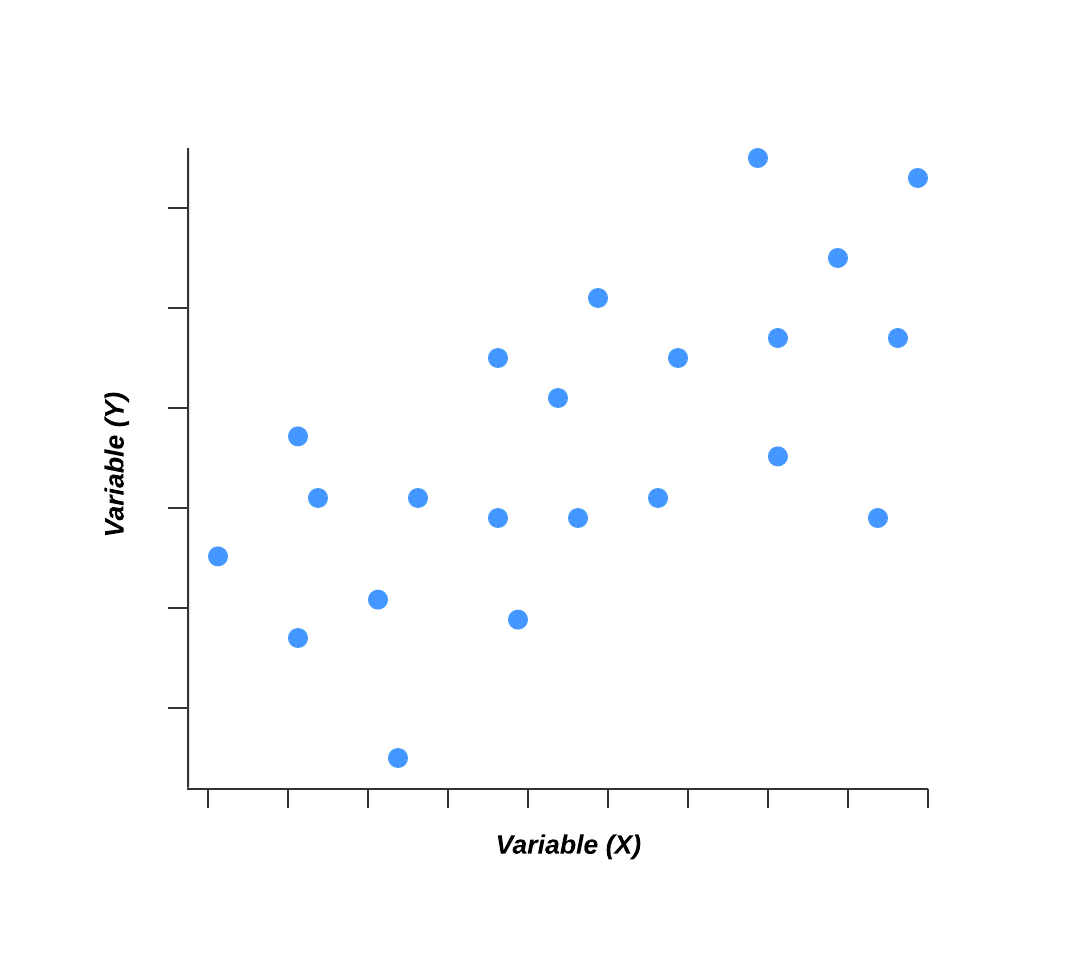
7. Control chart (also called a Shewhart chart)
Named after Walter A. Shewhart, this quality improvement tool can help quality assurance professionals determine whether or not a process is stable and predictable, making it easy for you to identify factors that might lead to variations or defects.
Control charts use a central line to depict an average or mean, as well as an upper and lower line to depict upper and lower control limits based on historical data. By comparing historical data to data collected from your current process, you can determine whether your current process is controlled or affected by specific variations.
Using a control chart can save your organization time and money by predicting process performance, particularly in terms of what your customer or organization expects in your final product.
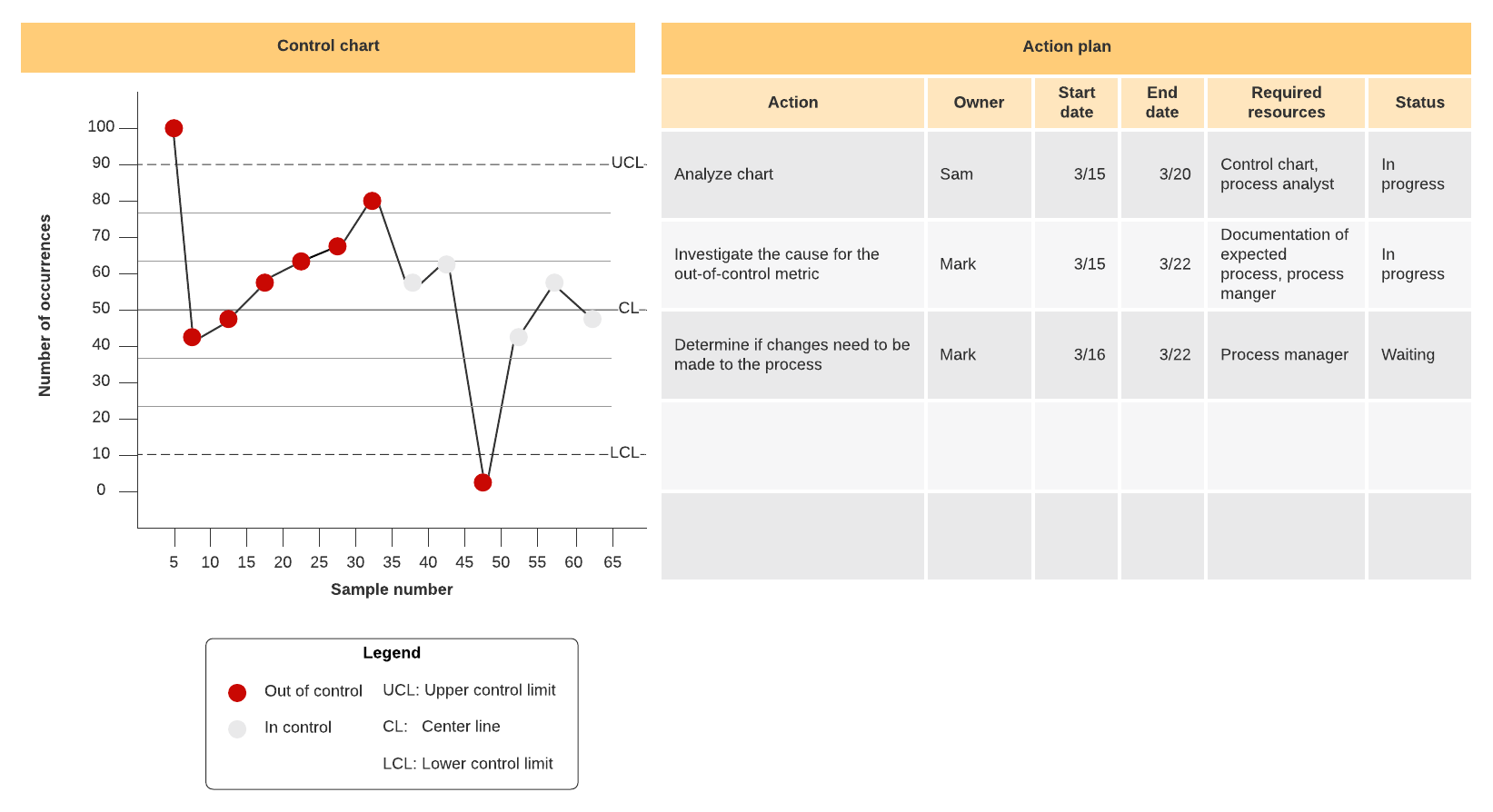
Bonus: Flowcharts
Some sources will swap out stratification to instead include flowcharts as one of the seven basic QC tools. Flowcharts are most commonly used to document organizational structures and process flows, making them ideal for identifying bottlenecks and unnecessary steps within your process or system.
Mapping out your current process can help you to more effectively pinpoint which activities are completed when and by whom, how processes flow from one department or task to another, and which steps can be eliminated to streamline your process.
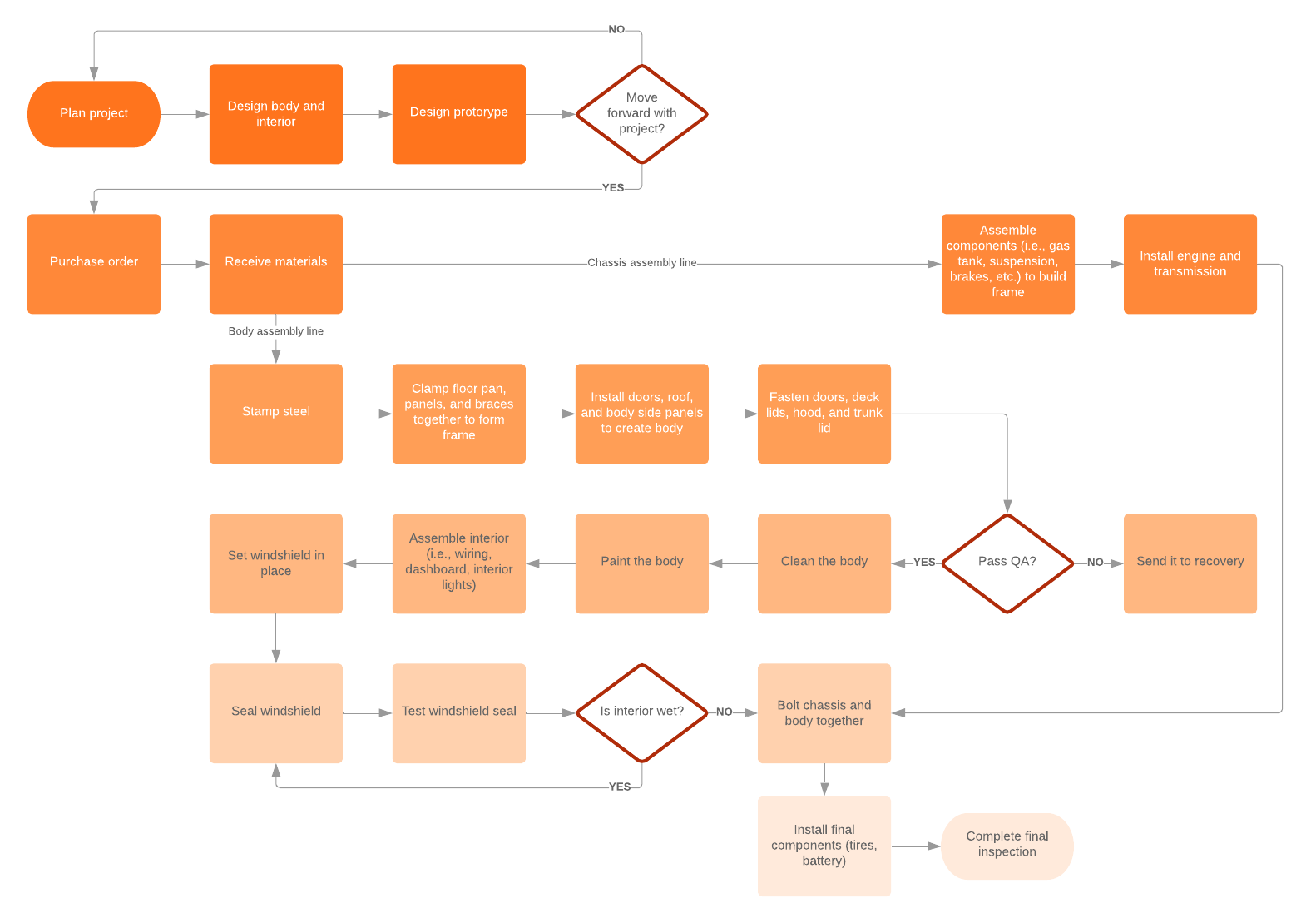
Learn how to create a process improvement plan in seven steps.
About Lucidchart
Lucidchart, a cloud-based intelligent diagramming application, is a core component of Lucid Software's Visual Collaboration Suite. This intuitive, cloud-based solution empowers teams to collaborate in real-time to build flowcharts, mockups, UML diagrams, customer journey maps, and more. Lucidchart propels teams forward to build the future faster. Lucid is proud to serve top businesses around the world, including customers such as Google, GE, and NBC Universal, and 99% of the Fortune 500. Lucid partners with industry leaders, including Google, Atlassian, and Microsoft. Since its founding, Lucid has received numerous awards for its products, business, and workplace culture. For more information, visit lucidchart.com.
Related articles
How to improve process visualization.
In this article we’ll talk about how to improve visualization, even if you are not a visual presentation expert.
Which process improvement methodology should you use?
Struggling to decide which process improvement methodology to use? Learn about the top approaches—Six Sigma, Lean, TQM, Just-in-time, and others—and the diagrams that can help you implement these techniques starting today.
Bring your bright ideas to life.
or continue with
By registering, you agree to our Terms of Service and you acknowledge that you have read and understand our Privacy Policy .
Troubleshooting Tips: How QC Analysts Identify and Resolve Quality Issues
Quality control analysts play a crucial role in ensuring that products meet the highest standards of quality. As part of their job, they are responsible for identifying any issues with product quality. They then find ways to resolve them.
This requires a thorough understanding of the manufacturing process. It also entails strong analytical and problem-solving skills.
In this document, we will discuss some valuable tips and techniques that a QC analyst can use to troubleshoot quality issues effectively. So, read further!
Understanding Specifications and Requirements
One of the essential tasks of a QC analyst is to understand the product specifications and requirements thoroughly. This helps them identify any discrepancies in the final product quickly.
Understanding these details will help an analyst during their inspection process. This is because every product has specific guidelines.
It would be challenging to identify if there are any deviations from the expected product quality. This happens if there is no clear understanding of the specifications.
Furthermore, it is essential to communicate with the production team and gather all necessary information before beginning an inspection.
Root Cause Analysis
Conducting a root cause analysis helps QC analysts identify the underlying cause of a problem. They do this rather than just addressing its symptoms. By determining the root cause, they can effectively resolve the issue. Thus, further prevent it from happening again in the future.
Root cause analysis involves:
- collecting data
- analyzing it
- identifying patterns or trends
All these could be causing the problem. It also involves looking at all possible factors that could contribute to the issue, such as:
- equipment malfunction
- human error
- raw material defects
QC analysts can develop effective solutions to prevent or resolve product quality issues. This comes along with a clear understanding of the root cause.
Utilizing Inspection Services
In addition to having in-house quality control processes, QC analysts may also benefit from utilizing an inspection service . These services offer a third-party perspective. They can provide valuable insights into identifying and resolving quality issues.
Inspection services often have advanced equipment and techniques. They can use these to detect defects or deviations that may be difficult to identify otherwise.
They can also provide a detailed report on the product quality. This can help QC analysts propose and implement appropriate solutions.
Process Evaluation and Improvement
A QC analyst should continuously evaluate the quality control process. They must look for ways to improve it too. This involves gathering feedback from various stakeholders, including:
- production teams
Analysts can identify any gaps or inefficiencies that may be causing quality issues. They can do this by regularly evaluating the QC process. They can then propose solutions such as implementing new procedures or updating equipment to improve overall product quality.
Learn How a QC Analyst Identifies and Resolve Quality Issues
Troubleshooting quality issues requires a combination of the right resources. A QC analyst can effectively identify and resolve quality issues. They can do this while maintaining a high standard for product quality.
So, keep these strategies in mind during your next inspection to achieve optimal results!
Should you wish to read more topics, visit our blog. We’ve got more!
This article is published by NYTech in collaboration with Syndication Cloud.
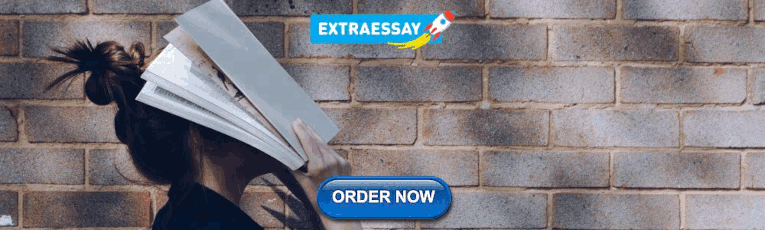
IMAGES
VIDEO
COMMENTS
Whatever the urgency, effective problem-solvers have the self-discipline to develop a complete description of the problem. Diagnostic Quality Problem Solving: A Conceptual Framework And Six Strategies (Quality Management Journal) This paper contributes a conceptual framework for the generic process of diagnosis in quality problem solving by ...
Quality Glossary Definition: Eight disciplines (8D) model. The eight disciplines (8D) model is a problem solving approach typically employed by quality engineers or other professionals, and is most commonly used by the automotive industry but has also been successfully applied in healthcare, retail, finance, government, and manufacturing. The ...
The 8D problem solving process is a detailed, team oriented approach to solving critical problems in the production process. The goals of this method are to find the root cause of a problem, develop containment actions to protect customers and take corrective action to prevent similar problems in the future. The strength of the 8D process lies ...
DMAIC: The define, measure, analyze, improve, and control process is a data-driven quality strategy used to improve processes. It is an integral part of a Six Sigma initiative, ... Sometimes, project leaders or sponsors don't feel a formal approach is necessary, but most problem-solving efforts benefit from a disciplined method.
Solving Quality Issues and Problems: Go Beyond Root Cause to 'Real' Cause. There is a tendency in the quality management field to confuse the root cause of a problem with the problem's real cause. A root cause is objective evidence of a quality problem. The real cause of a quality problem, however, is the actual finding or nonconformance.
Quality professionals are frequently required to engage in two areas that are as certain as death and taxes. The first is involvement in activities intended to result in continuous improvement, and the second is problem-solving. There are numerous models, approaches, tools and techniques available to help quality professionals solve problems ...
Reacting faster with a systematic approach to problem-solving. No matter how robust your planning phase is, problems and defects will occur. When an unexpected issue arises that can impact product quality, it's essential to react immediately. However, reacting fast is only effective if we deeply analyze the root causes and implement measures ...
ISO 9001:2015, Clause 5.1.1, emphasises the importance of engaging, directing and supporting people to contribute to the effectiveness of the quality management system. Using the six thinking hats technique fosters this engagement and enables a 360-degree perspective and input from those involved in the process.
The first step to solving a problem is to define the problem precisely. It is the heart of problem-solving. Root cause analysis is the second important element of problem-solving in quality management. The reason is if you don't know what the problem is, you can never solve the exact problem that is hurting the quality.
CQI and IRCA Certified Training. Level. Foundation. This course provides understanding of the fundamental tools, techniques and structured methodologies for problem solving and the capability to participate as a member of a problem-solving team in the application of the key tools to support the development of robust and sustainable solutions.
7 QC Tools are also known as Seven Basic Quality Tools and Quality Management Tools.These graphical and statistical tools are used to analyze and solve work-related problems effectively. The 7 Quality Tools are widely applied by many industries for product and process improvements, and to solve critical quality problems.. 7QC tools are extensively used in various Problem Solving Techniques ...
Then, you can proceed to define the relevant corrective actions. The most commonly used method is 5M1E. These 6 elements are reevaluated every time a disturbance in the product quality is observed. The six elements are Man, Machine, Material, Method, Measurement, and Environment. However, you can use multiple tools in the process of identifying ...
4) Develop and verify a solution. The more challenging the problem, the more demand for an in-depth analysis and synthesis of ideas into concepts that deliver value. The key to effective problem solving comes down to becoming more innovative. That is, including psychological factors, valuing idealistic thinking, becoming more resourceful ...
Quality Glossary Definition: Seven tools of quality "The Old Seven." "The First Seven." "The Basic Seven." Quality pros have many names for these seven basic tools of quality, first emphasized by Kaoru Ishikawa, a professor of engineering at Tokyo University and the father of "quality circles."Start your quality journey by mastering these tools, and you'll have a name for them too: indispensable.
quality management approaches used in the United States, Europe, Canada, and some Latin American and Asian countries, with lessons ... monitoring quality, and 3) solving quality problems and improving processes. The following are the 10 steps of the QA process: Designing for Quality 1. Planning for Quality Assurance: Develop a vision and ...
Various industries employ RCA for a wide range of problem-solving scenarios, from quality control and safety incident analysis to healthcare and software systems. Effective RCA requires a cross-functional team approach and may incorporate multiple tools and methods, such as Ishikawa diagrams and the 5 Whys technique, to systematically dissect ...
They are called basic quality tools because they can be easily learned by anyone even without any formal training in statistics. Dr. Kaoru Ishikawa played the leading role in the development and advocacy of using the 7 quality tools in organizations for problem-solving and process improvement. The 7 basic quality tools include; Flowchart; Histogram
The 8D Root Cause Analysis, as well as the 8D Corrective Action process, is a widely systematic approach in quality management, especially concerning 8D in quality control. This method includes eight comprehensive steps that are devised to problem solving by dealing with root causes of the problems comprehensively.
9. Lack of Investment in Quality Equipment or Quality-Related Production Equipment - After setting priorities for equipment repair, refurbishment or replacement through problem-solving or continuous improvement teams, management needs to plan ahead to have the financing available to address the challenges. Many companies have great ...
4. Cause-and-effect diagram (also known as a fishbone or Ishikawa diagram) Introduced by Kaoru Ishikawa, the fishbone diagram helps users identify the various factors (or causes) leading to an effect, usually depicted as a problem to be solved. Named for its resemblance to a fishbone, this quality management tool works by defining a quality-related problem on the right-hand side of the diagram ...
Diagnostic Quality Problem Solving: A Conceptual Framework And Six Strategies (Quality Management Journal) This paper contributes a conceptual framework for the generic process of diagnosis in quality problem solving by identifying its activities and how they are related. It then presents six strategies that structure the diagnostic process by ...
Here's how you can apply problem solving skills to address service quality issues in service operations. Powered by AI and the LinkedIn community. 1. Identify Issues. 2. Analyze Causes. Be the ...
It also entails strong analytical and problem-solving skills. In this document, we will discuss some valuable tips and techniques that a QC analyst can use to troubleshoot quality issues ...
QC Circles were organized in Japan as a way of getting operators to participate in quality control activities. In order to be efficient and effective in their problem-solving activities, members ...
Root cause analysis can be traced to the broader field of total quality management (TQM). TQM has developed in different directions, including a number of problem analysis, problem solving, and root cause analysis. Root cause analysis is part of a more general problem-solving process and an integral part of continuous improvement. Because of ...