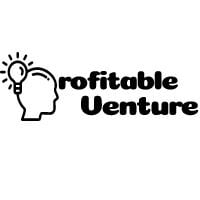
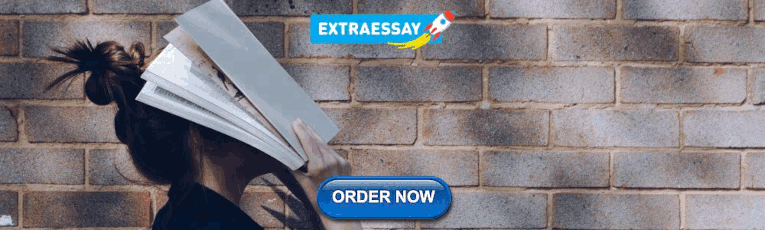
Wheat Flour Mill Business Plan [Sample Template]
By: Author Tony Martins Ajaero
Home » Business Plans » Agriculture Sector » Agro Processing
Are you about starting a wheat flour mill? If YES, here is a complete sample wheat flour production business plan template & feasibility report you can use for FREE .
Okay, so we have considered all the requirements for starting a wheat flour production business. We also took it further by analyzing and drafting a sample wheat flour mill marketing plan template backed up by actionable guerrilla marketing ideas for wheat flour production businesses. So let’s proceed to the business planning section.
As an aspiring entrepreneur who is looking towards starting a business and becoming your own boss, one of the businesses that you can successfully start if you have the financial requirement and of course business expose is to open a wheat flour production mill.
Although this type of business is not a business that you can start making profits from instantly, but a you are sure going to make good profits in the long run if you are determined and proactive in running the business. The reason is not far – fetched; you will require huge capital to set – up a standard wheat flour production mill. This type of business can somewhat be capital intensive.
Beyond every reasonable doubt, wheat flour is consumed in all parts of the world either as flour or the flour is used in the production of bread and other baked foods.
This goes to show that there is indeed a large market both locally and internationally for wheat flour production companies. Below is a sample wheat flour production mill business plan template that can help you to successfully write your own.
A Sample Wheat Flour Production Mill Business Plan Template
1. industry overview.
Wheat flour production companies in basically engaging in milling wheat grains into flour and then package and sell them to wholesale distributors, grocery wholesalers or other food-related business. They purchase wheat grain inputs from wholesalers or directly from growers.
The main fact that wheat flour mills provide goods that are considered diet staples, the industry will remain relevant in the years to come. The revenue and profit generated from this industry will depend on the price and production of wheat. As companies vertically integrate and merge operations to take advantage of economies of scale, revenue will rise.
According to a report released by IBISWORLD, the Flour Milling industry of which Wheat Flour Mill Production line of business is a part of is characterized by a low level of market share concentration. The report stated that in 2016, the top three players are expected to account for less than 31.0 percent of industry revenue.
While the industry exhibits low concentration, the industry is expected to approach moderate concentration over the next five years in line with the entrance of larger flour milling companies.
The report also stated that, in 2014, Ardent Mills entered the industry, as a result of ConAgra Mills and Horizon Milling, which is a joint venture between Cargill and CHS, combining their flour milling operations. Overall, larger operations will enable flour milling companies to use their large size to leverage lower costs for input commodities, such as wheat and grains
The Flour Production Mill industry of which wheat flour mill production line of business is subset of is a thriving sector of the economy of the united states of America and they generates a whooping sum of well over billion annually from more than 403 registered and licensed wheat flour mill production companies scattered all around the United States of America.
The industry is responsible for the employment of well over 24,938 people. Experts project the wheat flour mill production industry to grow at a -1.2 percent annual rate. Archer Daniels Midland Company, Ardent Mills, ConAgra Mills and Horizon Milling are the market leaders in the wheat flour production mill industry; they have the lion market share in the United States of America.
With this kind of business, if you want to start on a small scale, you can choose to start servicing your local community. All you would need is contacts, packaging, networking and good marketing and customer service skills. However, if you intend starting it on a large scale, then you should consider spreading beyond your local community to state level and even national level.
Over and above, the wheat flour production mill line of business is a profitable industry and it is open for any aspiring entrepreneur to come in and establish his or her business; you can chose to start on a small scale servicing a community or you can chose to start on a large scale with several distribution outlets in key cities all around the United States of America.
2. Executive Summary
Sammy Jay® Wheat Flour Production Company is a licensed and standard wheat flour mill production company that will be located in an industrial area in Springfield – Illinois. We have been able to secure a long term lease for a facility in a strategic location close to a big wheat farm with an option of a long term renewal on an agreed terms and conditions that is favorable to us.
The facility has government approval for the kind of business we want to run and it is easily accessible and we are deliberate about that to facilitate easy movement of raw materials (wheat grains and packaging materials et al) and finished products (well packaged wheat flour).
We are in the wheat flour mill production business to engage in processing, packaging and retailing wheat flour. We are also in business to make profits at the same to give our customers value for their money; we want to give people and businesses who patronize our well – packaged wheat flour the opportunity to be part of the success story of Sammy Jay® Wheat Flour Production Company.
We are aware that there are several big scale and small scale wheat flour mill production companies scattered all around the United States and Canada whose products can be found in every nooks and crannies of The United States and Canada.
Which is why we spent time and resources to conduct our feasibility studies and market survey so as to enable us locate the business in an area that will support the growth of the business and also for us to be able offer much more than our competitors will be offering.
We ensured that our facility is easy to locate and we have mapped out plans to develop a wide distribution network for wholesalers all around Springfield – Illinois and throughout the United States of America.
Much more than producing healthy, well processed and well packaged wheat flour, our customer care is going to be second to none. We know that our customers are the reason why we are in business which is why we will go the extra mile to get them satisfied when they visit purchase our wheat flour warehouse and also to become our loyal customers and ambassadors.
Sammy Jay® Wheat Flour Production Company will ensure that all her customers (wholesale distributors) are given first class treatment whenever they visit our flour mill or warehouse.
We have a CRM software that will enable us manage a one on one relationship with our customers (wholesale distributors) no matter how large the numbers of our customer base may grow to. We will ensure that we get our customers involved when making some business decisions that will directly or indirectly affect them.
Sammy Jay® Wheat Flour Production Company is family business that will be owned and managed by Sammy Jay and his immediate family members. Sammy Jay who is the Chief Executive Officer of the Company is Graduate of MicroBiology (B.Sc.) and he holds a Master’s Degree in Business Management (MBA).
He has well over 10 years of experience working in related industry as a senior manager prior to starting Sammy Jay® Wheat Flour Production Company. He will be working with a team of professionals to build the business and grow it to enviably height.
3. Our Products and Services
Sammy Jay® Wheat Flour Production Company is going to operate a standard and licensed wheat flour mill production company whose products will not only be sold in Springfield – Illinois but also throughout the United States of America.
We are in this line of business to make profits and also to give our customers value for their money. We are going to do all that is permitted by the law of the United States to achieve our business aim and ambition. Our product offering will be;
- Processing, packaging and retailing wheat flour in commercial quantities
4. Our Mission and Vision Statement
- Our vision is to establish standard Wheat Flour Production Company whose products will not only be sold in Springfield – Illinois, but also throughout the United States of America and Canada.
- Our mission is to establish a standard and world class Wheat Flour Mill Production Company that in our own capacity will favorably compete with leaders in the industry. We want to build a wheat flour mill production business that will be listed amongst the top 10 wheat flour mill brands in the United States of America and Canada
Our Business Structure
Sammy Jay® Wheat Flour Production Company is a business that is established with the aim of competing favorably with other leading wheat flour brands in the United States of America and Canada. This is why we will ensure that we put the right structure in place that will support the kind of growth that we have in mind while setting up the business.
We will ensure that we only hire people that are qualified, honest, hardworking, customer centric and are ready to work to help us build a prosperous business that will benefit all the stakeholders (the owners, workforce, and customers).
As a matter of fact, profit-sharing arrangement will be made available to all our senior management staff and it will be based on their performance for a period of five years or more depending how fast we meet our set target. In view of that, we have decided to hire qualified and competent hands to occupy the following positions;
- Chief Executive Officer (Owner)
Plant Manager
Human Resources and Admin Manager
Merchandize Manager
Sales and Marketing Manager
- Machine Operators
- Accountants / Cashiers
Distribution Truck Drivers
5. Job Roles and Responsibilities
Chief Executive Officer – CEO (Owner):
- Increases management’s effectiveness by recruiting, selecting, orienting, training, coaching, counseling, and disciplining managers; communicating values, strategies, and objectives; assigning accountabilities; planning, monitoring, and appraising job results; developing incentives; developing a climate for offering information and opinions; providing educational opportunities.
- Creates, communicates, and implements the organization’s vision, mission, and overall direction – i.e. leading the development and implementation of the overall organization’s strategy.
- Responsible for fixing prices and signing business deals
- Responsible for providing direction for the business
- Responsible for signing checks and documents on behalf of the company
- Evaluates the success of the organization
- Responsible for overseeing the smooth running of the wheat flour mill
- Part of the team that determines the quantity of wheat flour bags that are to be produced
- Maps out strategy that will lead to efficiency amongst workers in the plant
- Responsible for training, evaluation and assessment of plant workers
- Ensures that the steady flow of both raw materials to the plant and easy flow of finished products through wholesale distributors to the market
- Ensures operation of equipment by completing preventive maintenance requirements; calling for repairs.
- Ensures that the plant meets the expected safety and health standard at all times.
- Responsible for overseeing the smooth running of HR and administrative tasks for the organization
- Updates job knowledge by participating in educational opportunities; reading professional publications; maintaining personal networks; participating in professional organizations.
- Enhances department and organization reputation by accepting ownership for accomplishing new and different requests; exploring opportunities to add value to job accomplishments.
- Defines job positions for recruitment and managing interviewing process
- Carries out staff induction for new team members
- Responsible for training, evaluation and assessment of employees
- Oversees the smooth running of the daily office and factory activities.
- Manages vendor relations, market visits, and the ongoing education and development of the organizations’ buying teams
- Helps to ensure consistent quality of wheat grains and packaging materials are purchased
- Responsible for the purchase of raw materials and packaging materials (wheat grains and packaging materials et al)
- Responsible for planning sales, monitoring inventory, selecting the merchandise, and writing and pricing orders to vendors
- Ensures that the organization operates within stipulated budget.
- Manages external research and coordinate all the internal sources of information to retain the organizations’ best customers and attract new ones
- Models demographic information and analyze the volumes of transactional data generated by customer purchases
- Identifies, prioritizes, and reaches out to new partners, and business opportunities et al
- Responsible for supervising implementation, advocate for the customer’s needs, and communicate with clients
- Develops, executes and evaluates new plans for expanding increase sales
- Documents all customer contact and information
- Represents the company in strategic meetings
- Helps to increase sales and growth for the company
Accountant / Cashier
- Responsible for preparing financial reports, budgets, and financial statements for the organization
- Provides managements with financial analyses, development budgets, and accounting reports; analyzes financial feasibility for the most complex proposed projects; conducts market research to forecast trends and business conditions.
- Responsible for financial forecasting and risks analysis.
- Performs cash management, general ledger accounting, and financial reporting
- Responsible for developing and managing financial systems and policies
- Responsible for administering payrolls
- Ensuring compliance with taxation legislation
- Handles all financial transactions for the organization
- Serves as internal auditor for the organization
Client Service Executive
- Ensures that all contacts with customer (e-mail, walk-In center, SMS or phone) provides the client with a personalized customer service experience of the highest level
- Through interaction with customers on the phone, uses every opportunity to build client’s interest in the company’s products and services
- Manages administrative duties assigned by the store manager in an effective and timely manner
- Consistently stays abreast of any new information on Sammy Jay® Wheat Flour Production Company products, promotional campaigns etc. to ensure accurate and helpful information is supplied to clients when they make enquiries
Production Workers / Machine Operators:
- Responsible for processing and packaging (bagging) wheat flour
- Assists in packaging and loading wheat flour (bags) into distribution trucks
- Any other duty as assigned by the plant manager.
- Assists in loading and unloading wheat grains and wheat flour (bags)
- Maintains a logbook of their driving activities to ensure compliance with federal regulations governing the rest and work periods for operators.
- Keeps a record of vehicle inspections and make sure the truck is equipped with safety equipment
- Assists the transport and logistics manager in planning their route according to a delivery schedule.
- Local-delivery drivers may be required to sell products or services to stores and businesses on their route, obtain signatures from recipients and collect cash.
- Transports finished goods and raw materials over land to and from manufacturing plants or retail and distribution centers
- Inspects vehicles for mechanical items and safety issues and perform preventative maintenance
- Complies with truck driving rules and regulations (size, weight, route designations, parking, break periods etc.) as well as with company policies and procedures
- Collects and verifies delivery instructions
- Reports defects, accidents or violations
6. SWOT Analysis
We are well informed that there are several wheat flour mill production companies both large and small in the United States of America and Canada which is why we are following the due process of establishing a business so as to compete favorable with them.
We know that if a proper SWOT analysis is conducted for our business, we will be able to position our business to maximize our strength, leverage on the opportunities that will be available to us, mitigate our risks and be welled equipped to confront our threats.
Sammy Jay® Wheat Flour Production Company employed the services of an expert HR and Business Analyst with bias in start – up business to help us conduct a thorough SWOT analysis and to help us create a Business model that will help us achieve our business goals and objectives. This is the summary of the SWOT analysis that was conducted for Sammy Jay® Wheat Flour Production Company;
Part of what is going to count as positives for Sammy Jay® Wheat Flour Production Company is the vast experience of our management team, we have people on board who are highly experienced and understands how to grow business from the scratch to becoming a national phenomenon.
So also, proximity to one of the largest wheat grain farms in Springfield – Illinois, our large national distribution network and of course our excellent customer service culture will definitely count as a strong strength for the business.
A major weakness that may count against us is the fact that we are a new wheat flour mill production company and we don’t have the financial capacity to engage in the kind of publicity that we intend giving the business.
- Opportunities:
The fact that wheat flour is stable food in the United States and in all the countries of the world means that the opportunity available to us is enormous.
As a result of that, we were able to conduct a thorough market survey and feasibility studies so as to enable us properly position our business to take advantage of the existing market for wheat flour and also to create our own new market. We know that it is going to requires hard work, and we are well prepared to achieve it.
We are quite aware that just like any other business, one of the major threats that we are likely going to face is economic downturn and unfavorable government policies . It is a fact that economic downturn affects purchasing power.
Another threat that may likely confront us is the arrival of a new wheat flour mill production company in same location where ours is located. Changing diet preference may also pose a threat to wheat flour mill production companies.
7. MARKET ANALYSIS
- Market Trends
IBISWORLD published a report that stated that the Flour Milling industry of which Wheat Flour Mill Production line of business is a part of is characterized by a low level of market share concentration.
The report stated that in 2016, the top three players are expected to account for less than 31.0 percent of industry revenue. While the industry exhibits low concentration, the industry is expected to approach moderate concentration over the next five years in line with the entrance of larger flour milling companies.
The report also stated that, in 2014, Ardent Mills entered the industry, as a result of ConAgra Mills and Horizon Milling, which is a joint venture between Cargill and CHS, combining their flour milling operations.
Overall, larger operations will enable flour milling companies to use their large size to leverage lower costs for input commodities, such as wheat and grains.
If you are conversant with the trends in amongst wheat flour mill production companies, you will realize that in the bid to expanding their brand and generate enough income, they do not just settle for just the production of wheat flour, they also engage in related activities such as producing flour from corn, producing flour mixes from a variety of grain crops, milling rough rice, producing malt from a variety of cereal grains, and producing meal and animal feed
They are able to achieve this because the processes and machine involved are same as that required for milling wheat grains into fine wheat flour. With this, they are able to maximize their capacity and make good profits from the business.
8. Our Target Market
When it comes to selling wheat flour, there is indeed a wide range of available customers. In essence, our target market can’t be restricted to just a group of people, but all those who resides in our target market locations. In view of that, we have conducted our market research and we have ideas of what our target market would be expecting from us.
We are in business to engage in wholesale distribution and to retail well – packaged wheat flour in different sizes to the following groups of people;
- Restaurants and Canteens
- Event Planners and Caterers
- Everybody in our target market location
Our Competitive Advantage
A close study of the wheat flour mill production industry reveals that the market has become much more intensely competitive over the last decade. As a matter of fact, you have to be highly creative, customer centric and proactive if you must survive in this industry.
We are aware of the stiffer competition and we are well prepared to compete favorably with other wheat flour mill production companies in Springfield – Illinois and throughout the United States and Canada.
Sammy Jay® Wheat Flour Production Company is launching a standard wheat flour brand that will indeed become the preferred choice of residence of Springfield – Illinois and every city where our well – packaged wheat flour will be distributed and retailed.
Part of what is going to count as competitive advantage for Sammy Jay® Wheat Flour Production Company is the vast experience of our management team, we have people on board who are highly experienced and understands how to grow business from the scratch to becoming a national phenomenon.
So also proximity to one of the largest wheat grain farms in Springfield – Illinois, our large national distribution network and of course our excellent customer service culture will definitely count as a strong strength for the business.
Lastly, our employees will be well taken care of, and their welfare package will be among the best within our category (startups wheat flour mill production companies) in the industry, meaning that they will be more than willing to build the business with us and help deliver our set goals and achieve all our aims and objectives.
We will also give good working conditions and commissions to freelance sales agents that we will recruit from time to time.
9. SALES AND MARKETING STRATEGY
- Sources of Income
Sammy Jay® Wheat Flour Production Company is established with the aim of maximizing profits in the wheat flour mill production industry in both the United States of America and Canada and we are going to go all the way to ensure that we do all it takes to sell our well processed and well – bagged wheat flour to a wide range of customers.
Sammy Jay® Wheat Flour Production Company will generate income by processing, packaging, distributing and retailing wheat flour.
10. Sales Forecast
One thing is certain when it comes to wheat flour production business, if your wheat flour are well – packaged and branded and if your production mill is centrally positioned and easily accessible, you will always attract customers cum sales and that will sure translate to increase in revenue generation for the business.
We are well positioned to take on the available market in Springfield – Illinois and every city where our well processed and well – packaged wheat flour will be distributed and retailed and we are quite optimistic that we will meet our set target of generating enough income / profits from the first six month of operations and grow the business and our clientele base.
We have been able to critically examine the wheat flour mill production industry and we have analyzed our chances in the industry and we have been able to come up with the following sales forecast. The sales projections are based on information gathered on the field and some assumptions that are peculiar to startups in Springfield – Illinois.
Below are the sales projection for Sammy Jay® Wheat Flour Production Company, it is based on the location of our business and other factors as it relates to small scale and medium scale wheat flour production company start – ups in the United States;
- First Fiscal Year-: $240,000
- Second Fiscal Year-: $450,000
- Third Fiscal Year-: $950,000
N.B : This projection is done based on what is obtainable in the industry and with the assumption that there won’t be any major economic meltdown and there won’t be any major competitor offering same products and customer care services as we do within same location. Please note that the above projection might be lower and at the same time it might be higher.
- Marketing Strategy and Sales Strategy
Before choosing a location for Sammy Jay® Wheat Flour Production Company we conduct a thorough market survey and feasibility studies in order for us to be able to be able to penetrate the available market in our target market locations.
We have detailed information and data that we were able to utilize to structure our business to attract the numbers of customers we want to attract per time and also for our products to favorable compete with other leading wheat flour brands in the United States of America and Canada.
We hired experts who have good understanding of the wheat flour production industry to help us develop In other to continue to be in business and grow, we must continue to sell our well – bagged wheat flour to the available market which is why we will go all out to empower or sales and marketing team to deliver our corporate sales goals.
In summary, Sammy Jay® Wheat Flour Production Company will adopt the following sales and marketing approach to sell our wheat flour;
- Introduce our wheat flour brand by sending introductory letters to residence, wheat flour merchants and other stakeholders in Springfield – Illinois and other cities both in the United States of America and Canada
- Open our wheat flour production company with a party so as to capture the attention of residence who are our first targets
- Engage in road show in targeted communities from time to time to sell our wheat flour
- Advertise our wheat flour in community based newspapers, local TV and radio stations
- List our business and products on yellow pages ads (local directories)
- Leverage on the internet to promote our wheat flour brands
- Engage in direct marketing and sales
- Encourage the use of Word of mouth marketing (referrals)
11. Publicity and Advertising Strategy
In as much as our wheat flour mill is a standard one with well processed and well packaged wheat flour that can favorably compete with other leading brands, we will still go ahead to intensify publicity for all our products and brand. We are going to explore all available means to promote Sammy Jay® Wheat Flour Production Company.
Sammy Jay® Wheat Flour Production Company has a long term plan of distributing our wheat flour in various locations all around the United States of America and Canada which is why we will deliberately build our brand to be well accepted in Springfield – Illinois before venturing out.
As a matter of fact, our publicity and advertising strategy is not solely for selling our products but to also effectively communicate our brand. Here are the platforms we intend leveraging on to promote and advertise Sammy Jay® Wheat Flour Production Company;
- Place adverts on both print (community based newspapers and magazines) and electronic media platforms
- Sponsor relevant community programs
- Leverage on the internet and social media platforms like; Instagram, Facebook , twitter, et al to promote our wheat flour brand
- Install our Billboards on strategic locations all around major cities in the United States of America and Canada
- Engage in road show from time to time in targeted communities
- Distribute our fliers and handbills in target areas
- Position our Flexi Banners at strategic positions in the location where we intend getting customers to start patronizing our products.
- Ensure that our wheat flour bags are well branded and that all our staff members wear our customized clothes, and all our official cars and distribution vans are customized and well branded.
12. Our Pricing Strategy
When it comes to pricing for products such as wheat flour, there are two sides to the coin. We are aware of the pricing trend in the wheat flour mill production industry which is why we have decided to produce various bags – sizes of wheat flour.
In view of that, our prices will conform to what is obtainable in the industry but will ensure that within the first 6 to 12 months our products are sold a little bit below the average prices of various wheat flour brands in the United States of America.
We have put in place business strategies that will help us run on low profits for a period of 6 months; it is a way of encouraging people to buy into our wheat flour brands.
- Payment Options
The payment policy adopted by Sammy Jay® Wheat Flour Production Company is all inclusive because we are quite aware that different customers prefer different payment options as it suits them but at the same time, we will ensure that we abide by the financial rules and regulation of the United States of America.
Here are the payment options that Sammy Jay® Wheat Flour Production Company will make available to her clients;
- Payment via bank transfer
- Payment with cash
- Payment via Point of Sale Machine (POS)
- Payment via online bank transfer
- Payment via check
- Payment via bank draft
In view of the above, we have chosen banking platforms that will enable our client make payment for farm produces purchase without any stress on their part. Our bank account numbers will be made available on our website and promotional materials to clients who may want to deposit cash or make online transfer for the purchase of our products.
13. Startup Expenditure (Budget)
Starting a standard wheat flour mill production company is indeed a capital intensive business. This is so because the amount required setting – up a flour mill is not a piecemeal. The bulk of the start – up capital will be spent on leasing or acquiring a facility and also in purchasing grain milling machines, and packaging equipment.
Aside from that, you are not expected to spend much except for purchase and servicing of distribution trucks, paying of your employees and utility bills. This is the key areas where we will spend our start – up capital;
- The Total Fee for Registering the Business in the United States of America – $750.
- Legal expenses for obtaining licenses and permits as well as the accounting services (software, P.O.S machines and other software) – $1,300.
- Marketing promotion expenses for the grand opening of Sammy Jay® Wheat Flour Production Company in the amount of $3,500 and as well as flyer printing (2,000 flyers at $0.04 per copy) for the total amount of – $3,580.
- Cost for hiring Business Consultant – $2,500.
- Insurance (general liability, workers’ compensation and property casualty) coverage at a total premium – $2,400.
- Cost for payment of rent for 12 month at $1.76 per square feet in the total amount of $105,600.
- Cost for construction of a standard wheat flour mill – $100,000.
- Other start-up expenses including stationery ( $500 ) and phone and utility deposits ( $2,500 ).
- Operational cost for the first 3 months (salaries of employees, payments of bills et al) – $100,000
- The cost for Start-up inventory (raw materials and packaging materials et al) – $80,000
- The cost for counter area equipment (counter top, sink, ice machine, etc.) – $9,500
- Cost for grain milling machines and packaging equipment – $100,000
- Cost for store equipment (cash register, security, ventilation, signage) – $13,750
- Cost of purchase of 3 distribution vans – $30,000
- The cost for the purchase of furniture and gadgets (Computers, Printers, Telephone, Fax Machines, tables and chairs et al) – $4,000.
- The cost of Launching a Website – $600
- The cost for our opening party – $10,000
- Miscellaneous – $10,000
We would need an estimate of $500,000 to successfully set up our wheat flour mill in Springfield – Illinois. Please note that this amount includes the salaries of all the staff for the first 3 month of operation.
Generating Funds / Startup Sammy Jay® Wheat Flour Production Company
Sammy Jay® Wheat Flour Production Company is a family business that is owned and financed by Sammy Jay and his immediate family members. They do not intend to welcome any external business partner which is why he has decided to restrict the sourcing of the start – up capital to 3 major sources. These are the areas we intend generating our start – up capital;
- Generate part of the start – up capital from personal savings and sell of stocks
- Source for soft loans from family members and friends
- Apply for loan from my Bank
N.B: We have been able to generate about $200,000 (Personal savings $150,000 and soft loan from family members $50,000) and we are at the final stages of obtaining a loan facility of $300,000 from our bank. All the papers and document have been signed and submitted, the loan has been approved and any moment from now our account will be credited with the amount.
14. Sustainability and Expansion Strategy
The future of a business lies in the numbers of loyal customers that they have the capacity and competence of the employees, their investment strategy and the business structure. If all of these factors are missing from a business (company), then it won’t be too long before the business close shop.
One of our major goals of starting Sammy Jay® Wheat Flour Production Company is to build a business that will survive off its own cash flow without the need for injecting finance from external sources once the business is officially running.
We know that one of the ways of gaining approval and winning customers over is to retail our well processed and well bagged wheat flour a little bit cheaper than what is obtainable in the market and we are well prepared to survive on lower profit margin for a while.
Sammy Jay® Wheat Flour Production Company will make sure that the right foundation, structures and processes are put in place to ensure that our staff welfare are well taken of. Our company’s corporate culture is designed to drive our business to greater heights and training and retraining of our workforce is at the top burner.
As a matter of fact, profit-sharing arrangement will be made available to all our management staff and it will be based on their performance for a period of three years or more. We know that if that is put in place, we will be able to successfully hire and retain the best hands we can get in the industry; they will be more committed to help us build the business of our dreams.
Check List / Milestone
- Business Name Availability Check : Completed
- Business Registration: Completed
- Opening of Corporate Bank Accounts: Completed
- Securing Point of Sales (POS) Machines: Completed
- Opening Mobile Money Accounts: Completed
- Opening Online Payment Platforms: Completed
- Application and Obtaining Tax Payer’s ID: In Progress
- Application for business license and permit: Completed
- Purchase of Insurance for the Business: Completed
- Leasing of facility and construction of standard wheat flour mill: In Progress
- Conducting Feasibility Studies: Completed
- Generating capital from family members and friends: Completed
- Applications for Loan from the bank: In Progress
- Writing of business plan: Completed
- Drafting of Employee’s Handbook: Completed
- Drafting of Contract Documents and other relevant Legal Documents: In Progress
- Design of The Company’s Logo: Completed
- Graphic Designs and Printing of Packaging Marketing / Promotional Materials: In Progress
- Recruitment of employees: In Progress
- Purchase of the Needed furniture, racks, shelves, computers, electronic appliances, office appliances and CCTV: In progress
- Creating Official Website for the Company: In Progress
- Creating Awareness for the business both online and around the community: In Progress
- Health and Safety and Fire Safety Arrangement (License): Secured
- Opening party / launching party planning: In Progress
- Establishing business relationship with vendors – wholesale suppliers / merchants: In Progress.
Related Posts:
- Chicken Processing Plant Business Plan [Sample Template]
- Tomato Processing Plant Business Plan [Sample Template]
- Vegetable Oil Production Business Plan [Sample Template]
- Shea Butter Processing Business Plan [Sample Template]
- Sunflower Oil Business Plan [Sample Template]

Flour Mill Business Plan
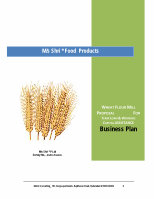
S B A P_ Business plan_V.01
Matrix Consulting_ 101, Durga apartments, Rajbhavan Road, Hyderabad 0 9989 040404 1
M/s Shri * P.Ltd Survey No, , Andhra Pradesh.
WHEAT FLOUR MILL PROPOSAL FOR
TERM LOAN & WORKING CAPITAL ASSISTANCE
Business Plan
M/s Shri * Food Products
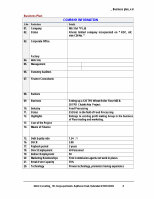
Matrix Consulting_ 101, Durga apartments, Rajbhavan Road, Hyderabad 0 9989 040404 2
Business Plan COMPANY INFORMATION
S.No Particulars Details 01. Company M/s Shri * P.Ltd 02. Status Private limited company incorporated on * ROC, AP,
vide CIN No. *
03. Corporate Office Factory
04. Web Site 05. Management
06. Statutory Auditors
07. Finance Consultants
08. Bankers
09. Business Setting up a 120 TPD Wheat Roller Flour Mill & 30 TPD Chakki Atta Project
10. Industry Food Processing 11. Status SSI Unit in the field of Food Processing 12. Highlights Belongs to existing profit making Group in the business
of Flour trading and marketing. 13 Cost of the Project Project Cost: Rs 578.00 lakhs 14. Means of Finance Term Loan Rs 350.00 lakhs
Equity Capital Rs 228.00 lakhs Working Capital Rs 240.00 lakhs
15. Debt Equity ratio 1.54 : 1 16. DSCR 3.08 17. Payback period 3 years 18. Direct Employment 49 Personnel 19. Indirect Employment 50 20 Marketing Relationships Firm Commission agents net work in places 21. Break Even Capacity 35% 20. Technology Proven technology, promoters having experience
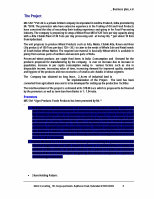
Matrix Consulting_ 101, Durga apartments, Rajbhavan Road, Hyderabad 0 9989 040404 3
The Project M/s Shri * Pvt Ltd is a private limited company incorporated in Andhra Pradesh, India promoted by Mr. *2010. The promoters who have extensive experience in the Trading of Oil and Food Products have conceived the idea of encashing their trading experience and going in for Food Processing industry. The company is proposing to setup a Wheat Flour Mill of 120 Tons per day capacity along with a Atta Chakki Plant of 30 Tons per day processing unit at Survey No, * just about 10 Kms from Hyderabad.
The unit proposes to produce Wheat Products such as Atta, Maida, Chakki Atta, Ravva and Bran ( By product ) of 150 Tons per day ( 120 + 30 ) to cater to the needs of Whole Sale and Retail needs of South Indian Wheat Market. The required raw material is basically Wheat which is available in plenty from various parts of northern and western parts of India.
Processed wheat products are staple food items in India .Consumption and Demand for the products proposed for manufacturing by the company, is ever on increase due to increase in population, increase in per capita consumption owing to various factors such as rise in disposable income, increasing value of time, increasing demand for improved quality standard and hygiene of the products and non-economics of small-scale chakkis in wheat segment.
The Company has obtained on long lease, 2_Acres of industrial land in Nadigama Village, Patancheru Mandal, Medak district, for implementation of the Project. The land has been converted from agricultural area and is to be developed for setting up the production facilities
The total Investment of the project is estimated at Rs 578.00 Lacs which is proposed to be financed by the promoters as well as term loan from Banks in 1 : 1.54 ratio.
PPrroommootteerrss
M/S Shri * Agro Products Foods Products has been promoted by Mr. * .
• Mr.Kamal Kumar Mundada (Director)- S/o Late Sri Kishan Mundada started his career in the year 1991 after his school education. He entered the family business run by his father viz., M/s Mundada brokers who are commission agents for supply of crude edible oil to oil refineries till 2006. Currently the business is handled by his cousins. For a couple of years he assisted his young nephew who owns a proprietary concern ‘Anand Agencies’, distributors of wheat products viz., Atta, Chikki Atta, Maida etc. He gained rich experience assisting his nephew in the wheat products business. With this background, he started his own business in 2007viz., ‘Shubham Agro Industries’, a partnership firm to manufacture Chakki Atta at Kattedan industrial area. Presently the firm is clocking a turnover of Rs 6.00 Cr to Rs. 7.00 Cr per annum.
• Ashish Mundada S/o Sri Kamal Kumar Mundada after completing his graduation (B Tech in Electrical Engg) in the year 2006, started his career as a channel partner to market the products of Idea Cellular. He did this business for a period of 2 years and achieved a turnover of Rs 12 Cr each per year. He gave up this business and joined as a partner of ‘Shubham Agro Industries’.
• Share Holding Pattern:
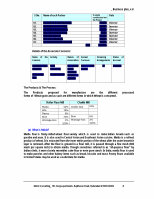
Matrix Consulting_ 101, Durga apartments, Rajbhavan Road, Hyderabad 0 9989 040404 4
S.No. Name of each Partner % equity contribution into the Project
01. Mr. Ashish Kumar Mundada 15.00% Director 02. Mr.Radha Kirshna Bajaj 25.00% Investor 03. Mr. Ashish Kumar Bung 12.50% Director 04. Mrs. Chandrakala Bung 5.00% Investor 05. Mr.Rohit Agarwal 17.50% Investor 06. Mrs.Indra Mundada 10.00% Director 07. Mr. Kamal Kishore Mundada 15.00% Director total 100.00%
Details of the Associate Concerns:
Name of the Concern
Activity Nature of Association
Annual Turnover
Financing Arrangements
Status of Account
Shubham Agro Industries
(Partnership firm)
Food Processing
Chakki Atta Mill
Sri Kamal Kumar Mundada-Director is a partner
Rs 7.00 Crores.
Nil Standard
The Products & The Process:
The Products proposed for manufacture are the different processed forms of Wheat grain and as such are different forms in which Wheat is consumed.
Roller Flour Mill Chakki Mill Maida 52% Chakki Atta 92%
Atta 15% Ravva 8% Bran 23% Bran 6% Wastage-loss 2% Wastage-loss 2% 100% 100%
(a) What is Maida?
Maida flour is finely-milled wheat flour variety which is used to make Indian breads such as paratha and naan. It is also used in Central Asian and Southeast Asian cuisine. Maida is a refined product of wheat. It is extracted from the inner white portion of the wheat after the outer brownish layer is removed. After the flour is ground in a flour mill, it is passed through a fine mesh (600 mesh per square inch) to obtain maida. Though sometimes referred to as "all-purpose flour" by Indian chefs, it more closely resembles cake flour or even pure starch. In India, maida flour is used to make pastries and other bakery items such as bread, biscuits and toast. Pastry flours available in United States may be used as a substitute for maida.
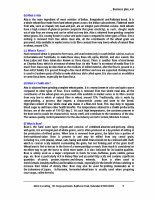
Matrix Consulting_ 101, Durga apartments, Rajbhavan Road, Hyderabad 0 9989 040404 5
(b) What is Atta
Atta is the main ingredient of most varieties of Indian, Bangladeshi and Pakistani bread. It is a whole wheat-flour made from hard wheat grown across the Indian subcontinent. Flatbread made from atta, such as chapati, roti, naan and puri, are an integral part of Indian cuisine. Hard wheats have a high content of gluten (a protein composite that gives elasticity), as such, doughs made out of atta flour are strong and can be rolled out very thin. Atta is obtained from grinding complete wheat grains. It is creamy brown in colour and quite coarse compared to other types of flour. Since nothing is removed from true whole meal atta, all the constituents of the wheat grain are preserved. Atta available in market varies in its fibre content from very low to whole of natural fiber in wheat, around 12%.
(c) What is Ravva ? Husk removed wheat is ground to form rava, and used extensively in south Indian cuisine, such as in Karnataka and Tamilnadu, to make Rava dosa, Rava idli, upma, khichdi, and also sweets like Rava Ladoo and Rava halwa also known as Rava Kesari. There is another form of rava known as Chamba Rava, which is an extract of wheat flour. As this "Rava" is an extract of maida flour it is much finer. Rava may be described as the residues of milled material, after the flour is ground in a flour mill (Chakki). It is passed through a fine mesh till flour and rava are separated. Bombay Rava is used in Southern parts of India to make delicious dish called upma. It is also used as an additive in some Dosa items, especially the Rava Dosa. (d) What is Chakki atta ?
Atta is obtained from grinding complete wheat grains. It is creamy brown in color and quite coarse compared to other types of flour. Since nothing is removed from true whole meal atta, all the constituents of the wheat grain are preserved. Atta available in market varies in its fibre content from very low to whole of natural fibre in wheat, around 12%. Traditionally, atta is made by stone grinding, a process that imparts a characteristic aroma and taste to the bread. High bran content of true whole meal atta makes it a fiber-rich food. This may help to regulate blood sugar as well have other health benefits. The temperatures attained in a chakki produced by friction, are of the order of 110-125 deg C. At such high temperatures, the carotenes present in the bran tend to exude the characteristic roasty smell, and contribute to the sweetness of the atta. The various quality control parameters for the atta industry are Ash Content, Moisture Content, (f) What is Bran? Bran is the hard outer layer of grain and consists of combined aleurone and pericarp. Along with germ, it is an integral part of whole grains, and is often produced as a by-product of milling in the production of refined grains. When bran is removed from grains, the latter lose a portion of their nutritional value. Bran is present in and may be milled from any cereal grain, including rice, corn (maize), wheat, oats, barley and millet. Bran should not be confused with chaff, which is coarser scaly material surrounding the grain, but not forming part of the grain itself. Wheat bran is fed to horses in the form of a warm porridge or mash. Bran mash is considered an excellent way to get the horse to drink more water. It is also indicated for its laxative qualities. Bran is widely used as a major component in foods for cows, buffaloes, goats, rabbits, guinea pigs, etc. Bran is particularly rich in dietary fiber and essential fatty acids and contains significant quantities of starch, protein, vitamins and dietary minerals. Bran is often used to enrich breads (notably muffins) and breakfast cereals, especially for the benefit of those wishing to increase their intake of dietary fiber. Bran may also be used for pickling (nukazuke) as in the tsukemono of Japan. In Romania, fermented wheat bran is usually used when preparing sour soups, called borscht.
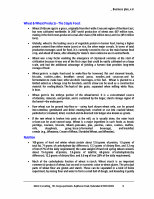
Matrix Consulting_ 101, Durga apartments, Rajbhavan Road, Hyderabad 0 9989 040404 6
Wheat & Wheat Products– The Staple Food:
• Wheat (Triticum spp) is a grass, originally from the Fertile Crescent region of the Near East, but now cultivated worldwide. In 2007 world production of wheat was 607 million tons, making it the third most-produced cereal after maize (784 million tons) and rice (651 million tons).
• Globally, wheat is the leading source of vegetable protein in human food, having a higher protein content than either maize (corn) or rice, the other major cereals. In terms of total production tonnages used for food, it is currently second to rice as the main human food crop, and ahead of maize, after allowing for maize's more extensive use in animal feeds.
• Wheat was a key factor enabling the emergence of city-based societies at the start of civilization because it was one of the first crops that could be easily cultivated on a large scale, and had the additional advantage of yielding a harvest that provides long-term storage of food.
• Wheat grain is a staple food used to make flour for leavened, flat and steamed breads, biscuits, cookies, cakes, breakfast cereal, pasta, noodles, and couscous and for fermentation to make beer, other alcoholic beverages, or bio fuel. Wheat is planted to a limited extent as a forage crop for livestock, and its straw can be used as a construction material for roofing thatch. The husk of the grain, separated when milling white flour, is bran.
• Wheat germ is the embryo portion of the wheat kernel. It is a concentrated source of vitamins, minerals, and protein, and is sustained by the larger, starch storage region of the kernel—the endosperm.
• Raw wheat can be ground into flour or - using hard durum wheat only, can be ground into semolina; germinated and dried creating malt; crushed or cut into cracked wheat; parboiled (or steamed), dried, crushed and de-branned into bulgur also known as groats.
• If the raw wheat is broken into parts at the mill, as is usually done, the outer husk or bran can be used several ways. Wheat is a major ingredient in such foods as bread, porridge, crackers, biscuits, Muesli, pancakes, pies, pastries, cakes, cookies, muffins, rolls, doughnuts, gravy, boza (a fermented beverage), and breakfast cereals (e.g., Wheatena, Cream of Wheat, Shredded Wheat, and Wheaties).
• 100 grams of hard red winter wheat contain about 12.6 grams of protein, 1.5 grams of total fat, 71 grams of carbohydrate (by difference), 12.2 grams of dietary fiber, and 3.2 mg of iron (17% of the daily requirement); the same weight of hard red spring wheat contains about 15.4 grams of protein, 1.9 grams of total fat, 68 grams of carbohydrate (by difference), 12.2 grams of dietary fiber, and 3.6 mg of iron (20% of the daily requirement).
• Much of the carbohydrate fraction of wheat is starch. Wheat starch is an important commercial product of wheat, but second in economic value to wheat gluten. The principal parts of wheat flour are gluten and starch. These can be separated in a kind of home experiment, by mixing flour and water to form a small ball of dough, and kneading it gently
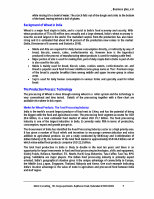
Matrix Consulting_ 101, Durga apartments, Rajbhavan Road, Hyderabad 0 9989 040404 7
while rinsing it in a bowl of water. The starch falls out of the dough and sinks to the bottom of the bowl, leaving behind a ball of gluten.
Background of Wheat in India
Wheat is a major food staple in India, and is crucial to India’s food economy and security. With wheat production of 75 to 85 million tons annually and a large demand, India’s wheat economy is now the second largest in the world. The marketed surplus from the production has also been rising and it is estimated that about 60-70 percent of the production now comes to the market (India, Directorate of Economic and Statistics 2010).
• Maida and Atta are required for daily human consumption directly, or indirectly by way of bread, biscuits, sweets, cakes, confectioneries etc. However bran is the byproduct produced in the process of manufacturing wheat products is used for making cattle feed.
• Major portion of atta is used for making Roti, part of daily staple diet in India. A part of atta is also used for biscuits.
• Maida is mainly used for bread, biscuit, cakes, cookies sweets, confectionaries etc. and Bread is popular snack food for lower middle-income group name as ‘Pav’. Premium range of the bread is popular breakfast item among middle and upper income group in urban areas
• Suji is used for daily human consumption in various forms and specially used for infant foods
TThhee PPrroodduuccttiioonn PPrroocceessss:: TTeecchhnnoollooggyy
The processing of Wheat is done through running wheat in a roller system and the technology is very conventional and time tested. Details of the processing together with a flow chart are available else where in this report. Market for Wheat Products: The Food Processing Industry:
India is the world's second largest producer of food next to China, and has the potential of being the biggest with the food and agricultural sector. The processing food segment accounts for USD 29.4 billion, in a total estimated food market of about USD 91.7 billion. The food processing industry is one of the largest industries in India. It currently ranks fifth in terms of production, consumption, export and growth prospects.
The Government of India has identified the Food Processing Industry sector as a high priority area. It has given a number of fiscal reliefs and incentives to encourage commercialization and value addition to agricultural produce. As per a study conducted by McKinsey and Confederation of Indian Industry (CII), the turnover of the total food market is approximately USD 69.4 billion out of which value-added food products comprise USD 22.2 billion.
The total food production in India is likely to double in the next ten years and there is an opportunity for large investments in food and food processing technologies, skills and equipment. Godrej Foods, Reliance, Namdhari, ITC, Nestle, Ruchi Soya Industries, Tata Coffee, Tata Tea, RPG group, Subhiksha are major players. The Indian food processing industry is primarily export oriented. India’s geographical situation gives it the unique advantage of connectivity to Europe, the Middle East, Japan, Singapore, Thailand, Malaysia and Korea. One such example indicating India’s location advantage is the value of trade in agriculture and processed food between India and Gulf region.
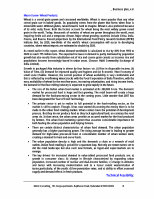
Matrix Consulting_ 101, Durga apartments, Rajbhavan Road, Hyderabad 0 9989 040404 8
Macro-Scene- Wheat Products:
Wheat is a cereal grain grown and consumed worldwide. Wheat is more popular than any other cereal grain use in baked goods. Its popularity stems from the gluten that forms when flour is mixed with water. Without gluten, raised bread is hard to imagine. Wheat is also preferred because of its mild, nutty flavor. Both the factors account for wheat being the most widely grown cereal grain in the world. Today, thousands of varieties of wheat are grown throughout the world, most requiring fertile soil and a temperate climate. Major wheat growing countries include China, India, France, and Russia. Recent projections by the International Food Policy research Institute (IFPRI) indicate that, by 2020, two-thirds of the world’s wheat consumption will occur in developing countries, where wheat imports are estimated to double by 2020.
As noted earlier in this report, wheat demand worldwide is calculated to rise by 40% from 1993 to 2020 to reach 775 million tons. The expected increase in demand is partly motivated by population growth but also results from substitution out of rice and coarse grain cereals as incomes rise and populations become increasingly based in urban areas. (Source: Multi Commodity Exchange of India Limited) .
Growth in packaged Atta industry is driven by four factors viz. (i) Rise in disposable income, (ii) Value of Time, (iii) Demand for improved quality and hygiene and (iv) Economic / Non Economy of small scale Chakkis. However, the current position of wheat availability is very comfortable and this is reflected by overflowing wheat stocks with the Food Corporation of India Therefore, with the easy availability of wheat for the next few years, increasing urbanization, and rising income levels, the demand for the flour milling industry is expected to grow rapidly in the future.
• The size of the Indian urban food market is estimated at Rs 350,000 Crore. The domestic market for processed food is huge and fast growing. The retail boom will create a huge demand for the food-processing sector in the coming years. Little wonder that 2007 has been designated the Year of Food Technology.
• The private sector is yet to realize its full potential in the food-retailing sector, as the market is still to explore. Though, it has now started discovering the money there is to be made in the urban food retailing market. Urban centers have the potential of development process. But they do not produce food as they lack agricultural land; on contrary the rural areas do. In that sense, the urban areas provide an assured market for the food produced by farmers. The urban food marketing system thus assumes considerable importance for both feeding the urban population and helping farmers.
• There are certain distinct characteristics of urban food demand. The urban population generally has a higher purchasing power. The rising average income is leading to greater demand for high-value processed food. A considerable number of urban women work, creating a demand for heat-and-serve foods.
• The urban population density is high and this demands a chain or a network of retail outlets. Indian food retailing is poised for a quantum leap. Not only are newer names set to dot the retail landscape but also such new formats, as hyper-and super-markets are to emerge.
• The key drivers for increased demand in value-added processed food products are: a) growth in consumer class; b) change in lifestyle characterized by expanding urban population, increased number of nuclear and dual-income families; c) change in attitudes and tastes with increasing modernization and to a lesser extent westernization of tastes,particularly, of the youth; d) low penetration rates; and e) ability to offset seasonal supply-and-demand effects in fresh products.
Technical Feasibility:
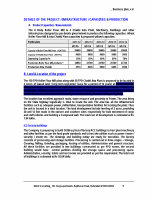
Matrix Consulting_ 101, Durga apartments, Rajbhavan Road, Hyderabad 0 9989 040404 9
DETAILS OF THE PROJECT / INFRASTRUCTURE / CAPASITIES & PRODUCTION
AA.. PPrroodduucctt CCaappaacciittiieess // RRaaww mmaatteerriiaallss
The 8 Body Roller Flour Mill & 4 Chakki Atta Plant, Machinery, Buildings and other Infrastructure designed (as per details given below) to produce the following capacities. Wheat Roller Flour Mill & Atta Chakki Plant capacities & proposed utilized capacities:
Particulars 2011-12 2012-13 2013-14 2014-15 2015-16 MT/ PA MT/ PA MT/ PA MT/ PA MT/ PA Capacity of Roller Flour Mill Plant ( 120 TPD ) 39600 39600 39600 39600 39600 Capacity of Chakki Atta Plant ( 30 TPD ) 9900 9900 9900 9900 9900 Operating Capacity % 50% 55% 60% 65% 70% Production Roller flour Mill products * 14850 21780 23760 25740 27720 Production Atta Chakki 3713 5445 5940 6435 6930
B. Land & Location of the project The 120 TPD Roller Flour Mill plant along with 30 TPD Chakki Atta Plant is proposed to be located in 2_Acres of leased land ( long term registered lease for a period of 12 years) at Survey No,31/A, Nadigama Village, Patancheru Mandal, Medak district, Andhra Pradesh just about 10 Kms from Hyderabad. Patancheru also known as Patan Choru, is a census town and mandal headquarters in Medak district located about 10 km from Hyderabad on the Hyderabad-Sholapur highway.
The location has excellent approach roads, water resource and proximity to Power. The area being on the State highway logistically is ideal to locate the unit. The area has all the infrastructure facilities such as adequate power, skilled labor, transportation facilities for locating the plant. Thus the unit is located in a ideal location. The land development include leveling of 2 acres, providing 20 and 12 feet roads in the eastern and southern sides respectively for bulk movement of cargo and staff vehicles and building a Compound wall. The total cost of development is estimated at Rs 1.94 lakhs. (C) Factory buildings
The Company is proposing to build 24356 sq feet of factory RCC buildings to host plant machinery and other facilities as per the food grade standards and to host the utilities such as power / water / security / steam etc. The drawings and building outlay are ready for execution. The factory consists of processing and storage facilities. Processing is carried out in three stages – Storage, Cleaning, Milling, Grinding, packaging, hosting of utilities, Administration and general structure. All these facilities are provided in two buildings constructed as per FPO norms, the second building would have central partition dividing the storage space and processing space. Administrative, security, toilets and rest rooms are provided as per the requirement. The total cost of buildings is estimated at Rs 92.64 lakhs
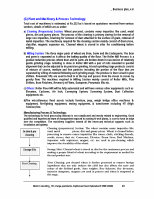
Matrix Consulting_ 101, Durga apartments, Rajbhavan Road, Hyderabad 0 9989 040404 10
(G) Plant and Machinery & Process Technology:
Total cost of machinery is estimated, at Rs.232 lac’s based on quotations received from various vendors, details of which are as under:
a) Cleaning (Preparatory) Section: Wheat procured, contains many impurities like sand, metal pieces, dirt and gunny pieces. The process of the cleaning is primary sieving for the removal of large size impurities, brushing for removal of dust attached to the surface of grain, removal of metal impurities. The machinery required for the cleaning section mainly consist of drum sieve, classifier, magnets separator etc. Cleaned wheat is stored in silos for conditioning before milling.
b) Milling Section: The three major parts of wheat are Bran, Germ and the Endosperm. The bran and germ is separated as it affects the baking quality of the flour. The Roller Mill Process is a gradual reduction process where bran and its parts are broken down in succession of relatively gentle grinding stage. Grinding is done in Roller Mill with a pair of rolls mounted in parallel alignment that can be adjusted to do precision grinding. At each grinding stage products consist of mixture of coarse, medium and fine particles including the portion of the flour that are separated by sifting of material following each grinding stage. The produce is then sieved in plan shifters. Pneumatic lifts are used to feed in at the top and passes from the sieves to sieves by gravity flow. The machines required in Milling Section mainly consist of Roller Mills, Plan Shifters, Bran Finishers, Reverse Jet Filters, Dampener, Pneumatic lifts etc.
c) Others: Roller Flour Mill will be fully automated and will have various other equipments such as Elevators, Cyclones, Air lock, Conveying System, Screening System, Dust Collection equipments etc.
d)The miscellaneous fixed assets include furniture, jeep, weigh bridge office machines & equipment, fire-fighting equipment, testing equipment, & transformer including HT (High Tension) line.
Manufacturing Process & Technology: The technology for food processing industry is not complicated and mostly related to engineering. Good qualified and experienced team of management exposed to running hi-tech plants, is sure to have an edge over the competitors. The machinery suppliers extend all the necessary technical supports such as installation and upkeep.
Cleaning (preparatory) Section: The wheat contains many impurities like sand, metal pieces, dirt and gunny pieces. Wheat is cleaned before processing to remove coarse impurities like stones, chafe, stitching threads, woods, straws, dust etc. Conveyors, Elevator, Drum Sieve, Reel Machine, Separator with aspirators, magnet, etc. are used in pre-cleaning which improves the storability of the wheat.
Storage Silos: Cleaned wheat is stored in silos for the continuous process and making a proper blend of wheat according to the requirement as needed for the end product mix.
First Cleaning: pre cleaned wheat is further processed to remove foreign ingredients that not only reduces the yield but also affects the taste and colour of the finished goods. Auto weigher, flow balancer, Dry de-stoner, intensive dampener, magnets are used in process and wheat is tempered at this stage.
In take & pre cleaning
Storage Silo
First Cleaning
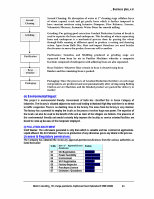
Matrix Consulting_ 101, Durga apartments, Rajbhavan Road, Hyderabad 0 9989 040404 11
Second Cleaning: By absorption of water at 1st cleaning stage cellulose layer of wheat expand, crack and get partly loose which is further tempered to have constant moisture using Intensive Dampner, Flow Balancer, Scourer, Volumetric Measure, Automatic Water Doser for smooth milling. Grinding: For getting good extraction Gradual Reduction System of break is used to separate the bran and endosperm. This breaking of wheat separating bran and endosperm is a mechanical process done by passing the wheat through Rolls running at different speed to produce a cutting and shearing action. Apart from Rolls Disc, Beat and impact Detachers are used besides the elevators to move the product from one roll to another
Purification: Semolina and Middling produced at grinding stage are separated from bran by air in Purifier Machines whereby a composite fractions composed of endosperm with adhering bran are also separated.
Bran Finisher: Whatever flour remain in bran is cleaned using bran finisher and the remaining bran is packed.
Packaging: Since the process is of Gradual Reduction therefore at each stage end products are produced and sent pneumatically after sieving using Bolting Cloth in service Machines and the finished product are packed for delivery in market
((HH)) EEnnvviirroonnmmeennttaall IImmppaacctt This project is environmental friendly. Government of India has classified this in Green Category of industries. The factory is situated adjacent to main road leading to National High Way and there is no threat to traffic congestion. There is no dwelling close to the factory. The noise from the factory is very minimal. The factory has a potential to employ the locals as the process involves huge man power. The expertise of the locals can also be used to the benefit of the unit as most of the villagers are farmers. The presence of this environmental friendly unit would certainly help improve the locality as service oriented facilities are bound to come up because of the manpower employed.
(I) POLLUTION ABATEMENT Solid Wastes: The solid waste generated is only bran which is saleable and has commercial applications. Liquid effluent: Nil, Air Pollution: There is no production of any obnoxious gases any where in the process. Licenses & Regulatory permissions: The Company has obtained the necessary approvals/permissions/licenses from the various authorities as listed hereunder:
S.No. Item of Approval/License /Permission
01 SSI Registration Received 02 Power Feasibility Under process 03 Environment Under process 04 VAT Registration Received 05 Factory Inspector Under process 06 Panchayat License Received 07 Estimates / Quotations Received
Second Cleaning
Grinding
Purification
Bran Finisher
Packaging
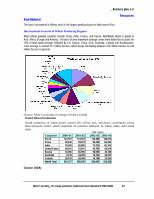
Matrix Consulting_ 101, Durga apartments, Rajbhavan Road, Hyderabad 0 9989 040404 12
Resources Raw Material:
The basic raw material is Wheat and it is the largest produced grain in India next to Rice. International Scenario of Wheat Producing Regions
Major wheat growing countries include China, India, France, and Russia. Worldwide wheat is grown in Asia, Africa, Europe and America. On basis of area maximum acreage comes from India that accounts for 13% of total world average, followed by EU, Russia, China, USA, Australia, Canada and Kazhakastan. Total average is around 217 million hectare, which keeps fluctuating between 210 million hectare to 230 million hectare in general.
(Source: Multi Commodity Exchange of India Limited) World Wheat Production
World production of wheat hovers around 585 million tons. Maximum contribution comes from European Union, which comprises 25 countries followed, by China, India, and United states.
(000 Tonnes) Countries 2000-01 2001-02 2002-03 2003-04EU-25 124,197 113,553 124,483 106,615China 99,640 93,873 90,290 86,490 India 76,369 69,680 71,810 65,100 United States 60,641 53,001 43,705 63,814Russia 34,450 46,900 50,550 34,100Australia 22,18 24,299 10,132 26,231Canada 26,519 20,568 16,198 23,552World Total 581,377 580,930 566,963 552,828
(Source: USDA)

Matrix Consulting_ 101, Durga apartments, Rajbhavan Road, Hyderabad 0 9989 040404 13
World wheat consumption is consistently growing. Long-term trend supports the fact that is evident from above chart. Wheat being one of the major staple foods all across the world demand seems to remain strong owing to increasing population. Two major consuming countries of wheat are EU, China, India, Russia, USA and Pakistan.
Wheat has made the largest contribution to the growth of food grain production in India. This is shown by the growth rates: wheat production has grown at a much faster pace compared to other food grains. During 1974 – 2010, when total food grain production grew at an annual rate of 3.68 per cent, wheat production grew at 5.36 per cent. Even in the last decade, wheat production is showing the fastest growth. The growth in wheat production has come from increase in yield as well as expansion of area. The increase in area sown has come at the expense of coarse cereals and pulses area, and from an increase in cropping intensity through multiple cropping. WHEAT ALL INDIA PRODUCTION IN MILLION TONS – 1974 - 2010
WHEAT - ALL INDIA PRODUCTION
MILLION TONNES
ACTUAL PRODUCTION PRODUCTION TREND
Nationally about 18 per cent of the net cropped area is planted to wheat. Figure 1 shows the shares of different states in the national wheat production. Uttar Pradesh (U.P.) contributes the largest share with 36 per cent of production, followed by Punjab with 19 per cent and Haryana with 11 per cent. These three northern states together contribute two-thirds of the production of wheat. These are followed by Madhya Pradesh (M.P.) 11 per cent, Rajasthan 10 per cent, Bihar 6 per cent and Gujarat 3 per cent. All the rest contribute only 4 per cent. As expected, the major wheat growing states are all in the north.
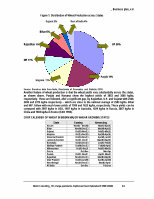
Matrix Consulting_ 101, Durga apartments, Rajbhavan Road, Hyderabad 0 9989 040404 14
Figure 1: Distribution of Wheat Production across States
Gujarat 3% Rest of India 4%
BBiihhaarr 66%% RRaajjaasstthhaann 1100%% UUPP 3366%% MMPP 1111%%
PPuunnjjaabb 1199%% Haryana 11%
Source: Based on data from India, Directorate of Economics and Statistics 2010 Another feature of wheat production is that the wheat yields vary substantially across the states, as shown above. Punjab and Haryana show the highest yields of 3853 and 3660 kg/ha, respectively. These are followed, after a significant gap, by Rajasthan, U.P. and Gujarat with 2500, 2498 and 2373 kg/ha respectively – which are close to the national average of 2583 kg/ha. Bihar and M.P. follow with much lower yields of 1999 and 1625 kg/ha, respectively. These yields can be compared with 2907 kg/ha in USA, 1907 kg/ha in Australia, 1029 kg/ha in Russia, 3667 kg/ha in China and 7603 kg/ha in France (FAO 1998). CROP CALENDER OF WHEAT IN INDIAN MAJOR WHEAR GROWING STATES
State Sowing Harvesting Assam Nov(B) - Dec(M) Mar(B)-Apr(E) Bihar Nov(M)-Dec(E) Mar(M)-Apr(E) Gujarat Oct(B)-Nov(E) Feb(B)-Mar(E) Haryana Oct(E)-Dec(B) Apr(M)-Apr(E) Himachal Pradesh Oct(B)-Nov(E) Apr(M)-Jun(E) Jammu & Kashmir Oct(B)-Dec(E) May(B)-May(E) Karnataka Oct(B)-Dec(E) Jan(B)-Feb(E) Madhya Pradesh Oct(M)-Dec(E) Feb(M)-Apr(E Maharashtra Oct(B)-Dec(E Feb(B)-Mar(E) Orissa Oct-Nov Mar-Apr Punjab Oct(B)-Nov(E) Apr(B)-May(E Rajasthan Nov(B)-Dec(E) Mar(B)-May(E) Uttar Pradesh Oct(B)-Jan(M) Apr(B)-Apr(M) West Bengal Nov(B)-Dec(E) Mar(B)-Apr(E All India Oct-Dec Feb-Jun
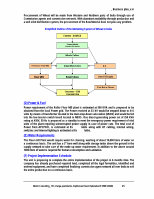
Matrix Consulting_ 101, Durga apartments, Rajbhavan Road, Hyderabad 0 9989 040404 15
Procurement of Wheat will be made from Western and Northern parts of India through use of Commission agents and commission net work. With abundant availability through production and a well oiled distribution system, the procurement of the Raw Material does not pose any problem.
Simplified Outline of the Marketing System of Wheat in India
(D) Power & Fuel
Power requirement of the Roller Flour Mill plant is estimated at 500 KVA and is proposed to be obtained from the local Power grid. The Power received at 33 KV would be stepped down to 415 volts by means of transformer located in the main step-down sub-station (MSDS) and would be fed into the low tension switch board located in MSDS. One diesel-generating power set of 250 KVA rating at 430V, 50 Hz is proposed as a standby to meet the emergency power requirement of vital units of the plant requiring uninterrupted power supply in case of power cuts. The total cost of Power from APCPDCL is estimated at Rs 15.00 lakhs along with HT cabling, internal wiring, switches and internal lighting is estimated at Rs 16.74 lakhs.
(E) Water Requirements
The Flour mill Plant would require water for cleaning, washing of about 10,000 liters of water on a continuous basis. The unit has a 3” bore well along with storage tanks above the ground in the supply network to take care of the make up water requirement. In addition to the above around 1000 liters of water is required for human consumption and sanitation.
(F) Project Implementation Schedule:
The unit is proposing to complete the entire implementation of the project in 6 months time. The company has already purchased required land, completed all the legal formalities, identified and ordered equipment, and have completed finalizing commission agent network all over India to sell the entire production on a continuous basis.
Farmers - SOURCE
Primary Market Commission Agents
Whole Sellers
Processors / Flour Mills F C I Urban Whole Sellers
State Civil Supply Flour Mills Retail Shops
Fair Price Shops Consumers – END
CONSUMPTION
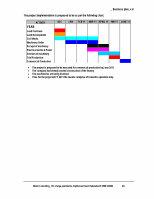
Matrix Consulting_ 101, Durga apartments, Rajbhavan Road, Hyderabad 0 9989 040404 16
The project implementation is proposed to be as per the following chart.
• The project is proposed to be executed for commercial production by June 2011 • The company had already started construction of the factory • The machineries are being finalized. • Thus for the projected FY 2011 the results comprise of 6 months operation only.
ACTIVITY DEC JAN FEB 11 MAR 11 APRIL 11 MAY !! JUNE 11
YEAR Land Purchase
Land Development Civil Works Machinery Order Receipt of machinery Electrical works & Power Erection of machinery Trial Production Commercial Production
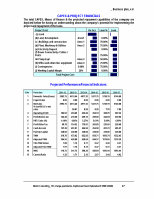
Matrix Consulting_ 101, Durga apartments, Rajbhavan Road, Hyderabad 0 9989 040404 17
CAPEX & PROJECT FINANCIALS The total CAPEX, Means of finance & the projected repayment capabilities of the company are depicted below for having an understanding about the company’s potential for implementing the project and repayment of the loans.
Project Cost Rs lacs Loan % Loan (a) Land on lease (b) Land, Development Anex1 1.94 0.00% 0.00 (c ) Buildings and construction Anex 1 132.37 70.00% 92.64 (d) Plant, Machinery & Utilities Anex 2 309.29 75.00% 231.97 (e) Electricity Deposit 15.00 0.00% 0.00 (f) Power Connectivity / Cables / Pole's 10.00 75.00% 7.50 (g) Preop Exp) Anex 3 14.14 50.00% 7.07 (h) Office and other misc equipment Anex 4 2.00 75.00% 1.50 (i) Contingencies 3.00% 13.25 75.00% 9.94 (j) Working Capital Margin 25% 80.00 0.00% 0.00
Total Project Cost 578.00 350.62
Projected Performance/Financial Indicators:
S.No Particulars 2011-12 2012-13 2013-14 2014-15 2015-16 2016-17
1 Domestic Sales(Gross) 2992.75 4513.46 4917.32 5327.75 5738.19 5746.08 2 Export Sales 0.00 0.00 0.00 0.00 0.00 0.00 3 Net Sales 2992.75 4513.46 4917.32 5327.75 5738.19 5746.08
% rise/fall (-) in net sales 50.81 8.95 8.35 7.70 7.85
4 Operating Profit 184.92 294.65 324.60 354.74 388.79 387.24 5 Profit Before tax 124.38 219.40 259.15 299.09 342.94 349.96 6 PBT/ Sales (%) 4.16% 4.86% 5.27% 5.61% 5.98% 6.09% 7 Profit After Tax 90.70 154.32 179.81 205.89 235.03 238.68 8 Cash Accrual 137.39 201.01 226.50 252.58 281.73 285.37 9 Paid Up Capital 228.00 228.00 228.00 228.00 228.00 228.00
10 TNW 318.70 473.02 652.83 858.71 1093.74 1332.43 11 Adjusted TNW 304.56 458.88 638.69 844.57 1079.60 1318.29 12 TOL/TNW (times) 1.89 1.13 0.71 0.47 0.30 0.21 13 Adjusted TOL/TNW 1.97 1.16 0.73 0.47 0.31 0.21 14 NWC 110.75 241.75 398.26 580.84 1095.44 1095.44 15 Current Ratio 1.33 1.71 2.16 2.67 3.44 4.92
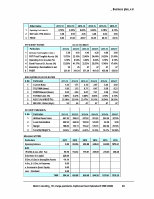
Matrix Consulting_ 101, Durga apartments, Rajbhavan Road, Hyderabad 0 9989 040404 18
Other Ratios 2011-12 2012-13 2013-14 2014-15 2015-16 2016-17 1 Operating Cost/ sales % 6.18% 6.53% 6.60% 6.66% 6.78% 6.74% 2 Net Sales /TTA (times) 3.30 4.55 4.45 4.28 4.06 3.60 3 PBDIT 8.03 21.68 48.07 66.35 66.35 66.35
EFFICIENCY RATIOS As on 31st March Particulars 2011-12 2012-13 2013-14 2014-15 2015-16 2016-17
1 Net Sales/ Total Tangible ( times ) 3.30 4.55 4.45 4.28 4.06 3.60 2 PBT/ Total Tangible Assets (%) 13.73% 22.10% 23.45% 24.04% 24.29% 21.90% 3 Operating Cost to sales (%) 6.18% 6.53% 6.60% 6.66% 6.78% 6.74% 4 Bank Finance/ Ct. Assets (%) 53.39% 41.17% 32.33% 25.87% 17.45% 17.45% 5 Inventory+ Receivables to net 53 45 47 47 47 47 6 PBDIT 231.61 341.34 371.29 401.43 435.48 433.93
RISK RATING RELATED RATIOS S.No Particulars 2011-12 2012-13 2013-14 2014-15 2015-16 2016-17
1 Current Ratio 1.33 1.71 2.16 2.67 3.44 4.92 2 TOL/TNW (times) 1.89 1.13 0.71 0.47 0.30 0.21 3 PBDIT/Interest (times) 3.83 4.54 5.67 7.21 9.50 11.64 4 PAT/Net Sales (%) 3.03% 3.42% 3.66% 3.86% 4.10% 4.15% 5 ROCE (%) (PBDIT/TA) 25.18% 33.91% 33.17% 31.91% 30.54% 26.92% 6 INV+REC./Sales (days) 53 45 47 47 47 47
SECURITY MARGIN % S.No Particulars 2011-12 2012-13 2013-14 2014-15 2015-16 2016-17
1 Written Down Value 441.30 394.61 347.92 301.23 254.54 207.85 2 Loan Outstanding 332.50 262.50 192.50 122.50 52.50 0.00 3 Margin 108.80 132.11 155.42 178.73 202.04 207.85 4 Security Margin % 24.66% 33.48% 44.67% 59.33% 79.37% 100.00%
Movement of TNW
Particulars 2011 2012 2013 2014 2015 2015 Opening balance 0.00 304.56 458.88 638.69 844.58 1079.61 Add. i Profit/(-)Loss after Tax 90.70 154.32 179.81 205.89 235.03 238.68 ii Increase in Capital 228.00 iii Dec./(-) Inc.in Intangible Assets -14.14 iv Inc../(-) \ Dec.in Reserves 0.00 v. Increase in Quasi Equity 0.00 Less : Dividend 0.00
TNW 304.56 458.88 638.69 844.58 1079.61 1318.29
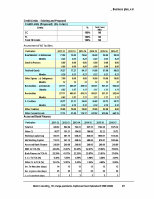
Matrix Consulting_ 101, Durga apartments, Rajbhavan Road, Hyderabad 0 9989 040404 19
Credit Limits – Existing and Proposed
Assessment of WC facilities:
Particulars 2011-12 2012-13 2013-14 2014-15 2015-16 2016-17 Raw Material : a) Indigenous 71.92 73.02 79.66 86.30 92.94 92.94 Months 0.25 0.23 0.23 0.23 0.23 0.23 Stock in Process 0.00 0.00 0.00 0.00 0.00 0.00 0.00 0.00 0.00 0.00 0.00 0.00 Finished Goods 76.37 77.27 84.17 91.08 97.98 98.03 Months 0.26 0.23 0.23 0.23 0.23 0.23 Other Spares : a) Indigenous 7.00 8.00 9.00 10.00 10.00 10.00 Months 12 13 13 13 12 12 Receivables : a) Domestic 277.11 403.67 455.31 493.31 531.31 532.04 Months 0.83 1.07 1.11 1.11 1.11 1.11 Receivables 277.11 403.67 455.31 493.31 531.31 532.04 Months 0.83 1.07 1.11 1.11 1.11 1.11 S. Creditors 28.77 31.21 34.05 36.89 39.72 39.72 Months 0.10 0.10 0.10 0.10 0.10 0.10 Other Creditors 70.00 70.00 70.00 70.00 52.50 0.00 Other Current Assets 17.12 21.00 114.17 247.03 410.05 642.15
Assessed Bank Finance:
Particulars 2011-12 2012-13 2013-14 2014-15 2015-16 2016-17
Total CA 449.52 582.96 742.31 927.72 1142.29 1375.16
Other CL 98.77 101.21 104.05 106.88 92.22 39.72
Working Capital Gap 350.75 481.75 638.26 820.84 1050.07 1335.44
Net Working Capital 110.75 241.75 398.26 580.84 810.07 1095.44
Assessed Bank Finance 240.00 240.00 240.00 240.00 240.00 240.00
NWC to TCA (%) 24.64% 41.47% 53.65% 62.61% 70.92% 79.66%
Bank Finance to TCA % 53.39% 41.17% 32.33% 25.87% 21.01% 17.45%
S. Cr. To TCA (%) 6.40% 5.35% 4.59% 3.98% 3.48% 2.89%
Other CL to TCA (%) 15.57% 12.01% 9.43% 7.55% 4.60% 0.00%
Inv. To Net sales (days) 14 13 13 13 13 13
Rec. to gross sales (days) 25 33 34 34 34 34
S. Cr. To purchases (days) 3 3 3 3 3 3
Credit Limits (Proposed): (Rs. in lacs) Limits State Bank of Hyderabad % Total Cons/
MBA CC 240.00 100% Nil TL 350.00 100% Nil Total FB Limits 590.00 100% Nil

Matrix Consulting_ 101, Durga apartments, Rajbhavan Road, Hyderabad 0 9989 040404 20
Present Proposal with State Bank of Hyderabad
Facility Present Limit Proposed Limit CC limit (Hypothecation of Receivables) Nil Rs 240.00 Lacs Term Loan Nii Rs 350.00 Lacs Securities 40% collateral security apart from primary assets Repayment of Term loans.
• The Project implementation has commenced and is proposed to be completed for commercial production by June 2011.
• The term loan is thus proposed to be repayable in 5 years i.e 60 monthly installments along
with interest with a initial holiday of 12 months. i.e first 6 months for project implementation and the balance 6 months for stabilizing the cash flows.
PROJECTED OPERATIONAL RESULTS Detailed data on operational expenses and profits for the forthcoming 6 years of projected operations have been worked out and given in the statement annexed. While working out estimates, prices of inputs and selling prices of outputs have been kept at constant rates assuming that any increase in inputs cost would be effect by proportionate increase in the selling price. Marginal increase has been provided in other operational cost to cover effects of possible inflation. CASH GENERATION & REPAYMENT SCHEDULE Based on the estimates of cash generation from the operations and considerations the need to retain certain funds for meeting any other contingent situations, plans for repayment of the loan has been worked out and enclosed as annexes. By the end of the third year the company shall be self sufficient to meet the enhanced working capital limits /or /for expansion or diversification PROJECTED CASH FLOWS A projected cash flow statement of the company at the end of the projected 6 years of working has been drawn up and given in the statement enclosed. The pictures emerges from a glance of the date, spread for the 6 years i.e. Increasing levels of reserve accumulation and decreasing borrowings on the one hand and increasing levels of current assets on the other with comparatively very less amount blocked in fixed capital. The data also reveals a comparatively high ratio of equity to debt depicting a growing strong capital base of the unit over loan funds in the business.
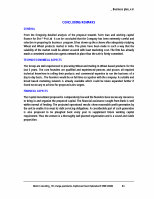
Matrix Consulting_ 101, Durga apartments, Rajbhavan Road, Hyderabad 0 9989 040404 21
CONCLUDING REMARKS
From the foregoing detailed analysis of the proposal towards Term loan and working capital finance for Shri * Pvt Ltd it can be concluded that the Company has been extremely careful and selective in preparing its business program. It has drawn up the scheme after adequately studying Wheat and Wheal products market in india. The plans have been made in such a way that the salability of the market could be almost assured with least marketing cost. The firm has already made a committed commission agents network in place thus the sale is firmly committed.
TECHNO ECONOMICAL ASPECTS
The Group are well experienced in procuring Wheat and trading in Wheat based products for the last 5 years. The core founders are qualified and experienced persons and posses all required technical know-how in selling their products and commercial expertise to run the business of a day to day basis.. The founders would be on full time occupation with the company. A suitable and broad based marketing network is already available which could be taken expanded further if found necessary to achieve for proposed sales targets.
FINANCIAL ASPECTS
The Capital investment proposed is comparatively low and the founders have necessary resources to bring in and organize the proposed capital. The financial assistance sought from Bank is well within normal of lending. The projected operational results show reasonable profit generation by the unit to enable it to meet its debt servicing obligations. A considerable part of cash generation is also proposed to be ploughed back every year to supplement future working capital requirement. Thus the venture is a thoroughly well planned organization and is a sound and viable proposition.

SMEDA Mini Flour Mill

Business Plan on Small Scale Flour Mill

ORIGINAL FLOUR MILL REMEMBERED AT THE AUSTRALIA DAY ... · ORIGINAL FLOUR MILL REMEMBERED AT ... Canfield, Cliffe Hannah and Lance Ward. The full story of the flour Mill will be in

Solar Powered Flour Mill Energy Storage Leh –Ladakh · and weather-based disaster resilient flour mill in the villages: solar powered flour mill energy storage. The deployment of

Flour mill by Gaurang enterprise

Flour Mill Instruction Sheet

Flour Mill Project

Roller Flour Mill (Atta, Maida & Suji) - Market Survey cum ... Flour Mill... · 2 Introduction Roller Flour mill serve the purpose of processing wheat to convert it into flour. The

The Need Of Using Flour Mill for Top Quality Flour

Engineering

Flour Mill Manufacturer in India

Rathore & Company, New Delhi, Flour Mill

Maize mill wheat flour mill hongdefa machinery tony 008618330112982

Dangote flour mill annual report 2010
Investor Relations

Sulluoglu flour mill catalogue

Indian Flour Mill Final (1)

Dangote Flour Mill annual report 2011

production on kisaan flour mill, jammu
Academia.edu no longer supports Internet Explorer.
To browse Academia.edu and the wider internet faster and more securely, please take a few seconds to upgrade your browser .
Enter the email address you signed up with and we'll email you a reset link.
- We're Hiring!
- Help Center
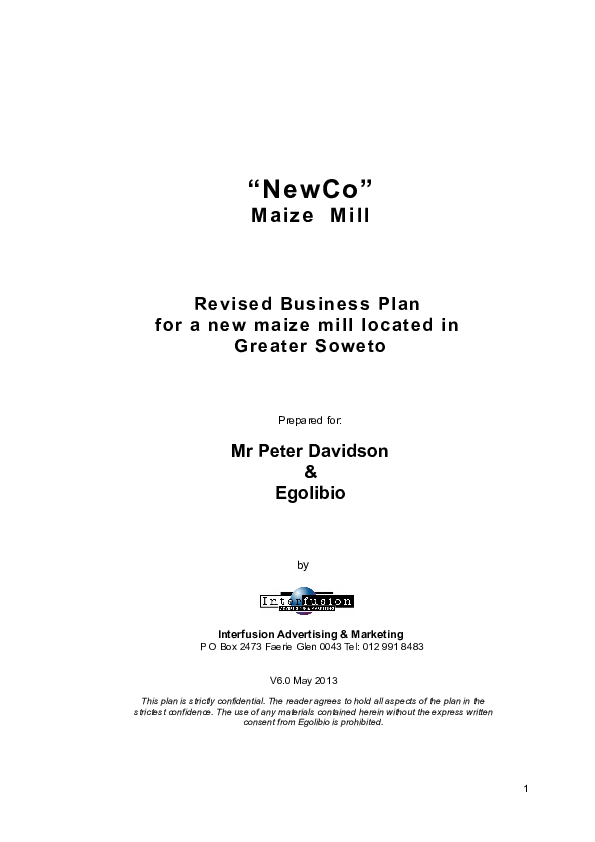
REVISED NewCo Maize Mill BUSINESS PLAN V6.3 Sept

Related Papers
Mainul Islam
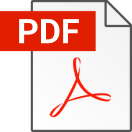
Lwando Elvis
Anthropology of Agriculture & Nutrition eJournal
Predrag Vuković
The purpose of this paper is to consider the possibilities of branding agri-food products from Serbia, which contributes to their recognition and competitiveness increase. Development of sustainable competitive advantage refers to a logical understanding of advantages and flaws of a firm in regard to possibilities and threats on the market. Research on behaviour of buyers and appropriate targeting of the real segment provides input values for development of a special marketing mix. The essential connection of the consumers’ needs with the firm’s possibilities constitutes brand development. This process enables a firm to develop a special distinctive identity and to position itself on the market so as to differ from its competitors. The traditional economic theory is based on the assumptions of perfect competitive markets, on which numerous salesmen offer identical products for sale. It is assumed that all the products are perfectly replaceable; thus, by competition process, the pric...
Esperienze D Impresa Dipartimento Di Studi E Ricerche Aziendali Universita Di Salerno
Maria Palazzo
Interdisciplinary Social Studies
choirul hamidah
Background: Branding is an identity created by marketing people to make it easier for consumers to choose products. The role and obstacles faced by home industry owners and the strategies carried out by home industry voters in facing existing obstacles. Aim: This study aims to determine the role of branding in the home industry to increase sales potential and community income. Method: This study uses qualitative descriptive research. The source of data was taken in Bringinan Village, Jambon District, Ponorogo Regency, which was raised from the results of the Ormawa Capacity Building Program Fund Grant of the Ministry of Education, Culture, Research, and Technology. Findings: To overcome current challenges, sellers might employ a number of tactics. The Ponorogo Regency Department of Trade, Cooperatives, and MSMEs provides assistance with branding socialization and training so that residents of Bringinan Village in Jambon District are more informed about the significance of branding i...
Hari Sreekumar
Kouk Qing Yuan
Eliot T Masters
International Journal of Managerial Studies and Research
Kesia M O U X E L L A Marengo
RELATED PAPERS
The Astrophysical Journal
Marek Sarna
Anais Do Cbmfc
Marcello Giffoni
Journal of Applied Biosciences
paulo roberto de albuquerque leal
082214297187 , Tempat kegiatan produksi sandal jepit desain sendiri Pelabuhan Ratu , Penyedia jasa produksi sandal jepit pakai desain sendiri di Pelabuhan Ratu
sandaljepit customPR
International Petroleum Technology Conference
Nader Ghadami
world comedy
Sara Azevedo Cardoso
Proceedings of the International Conference of CELSciTech 2019 - Science and Technology track (ICCELST-ST 2019)
Bambang Sugiantoro
Academic Pediatrics
Janet Serwint
Palaeogeography, Palaeoclimatology, Palaeoecology
Kirsten Kennedy
Tibor Ördögh
Annals of cardiac anaesthesia
ramya gnanasekar
Mohamed Rashed
IEEE Microwave and Wireless Components Letters
Maulik Bhavsar
Research, Society and Development
Gynecologic Oncology
Carleton Garrett
renato possebon
Journal of advanced simulation in science and engineering
NORZAIDAH MD NOH
WA/CALL : 0822-3006-6162, Pembuatan Box Motor Fiberglass Surabaya, Harga Box Fiberglass, Harga Box Fiberglass Motor
gamal imron khoirudin
Oldenbourg eBooks
abdi scheybani
Bangladesh Heart Journal
MD monir Khan
ghfkfg fdgdsf
Toxicological & Environmental Chemistry
OMOTAYO OLUTOLA DOSUMU
- We're Hiring!
- Help Center
- Find new research papers in:
- Health Sciences
- Earth Sciences
- Cognitive Science
- Mathematics
- Computer Science
- Academia ©2024
Hire Bizvestor for business research & planning, content writing, digital advertising, or to create a similar website for you → Contact Us
Flour Mill Business Plan Sample (With Financial Template)
Share this Post:
- Share on Facebook
- Share on Telegram
- Share on LinkedIn
- Share on WhatsApp
This is a sample business plan for a flour mill business based in Nigeria. The sample business name of the flour mill is Kachi Mills.
The flour mill is based in Lagos state and produces yam flour, wheat flour and corn flour.
This business plan outline used follows a standard business summary template and is usable for applying for loans, grants, and equity funding.
You can use this business plan sample as a guide to develop a business plan for your flour mill business.
Introduction
Kachi Mills is a modern standard flour mill based in Lagos state, Nigeria.
We produce edible flours used for staple foods in Nigeria. Our flour types include yam flour, corn flour, and wheat flour.
We source raw materials directly from the best farms, produce our flours following industry standards of quality, and package for delivery.
The brand name for our product packages in Kachmills. Kachmills yam flour, Kachmills wheat flour, and Kachmills corn flour.
Business Analysis
We are focused on producing the finest flours for direct consumption.
Not only are our production facilities certified by the NAFDAC, our flour quality has been tested and satisfactorily passed the tests of the SON.
We are targeting specific markets with our range of products and our pricing is very competitive.
We are looking to keep improving our product quality based on consumer feedback, and making our production process more efficient.
Product Pricing
Our products are priced according to category and packaging.
Our flours are packaged in 600g and 10kg bags.
The corn flour is priced at 400 Naira for the 600g packaging and 5,500 for the 10kg packaging.
The yam flour is priced at 350 Naira for the 600g packaging and 4,800 Naira for the 10kg packaging.
The wheat flour is priced at 800 Naira for the 600g packaging and 7,500 for the 10kg packaging.
We offer discounts on all these packages for wholesale buyers and distributors in our network.
Business Model & Profitability
Business model.
Our business model involves large scale production, packaging and distribution of our range of flour products via our distribution network in and around Lagos state.
We also have partnerships with retail shops and supermarkets that market our products on their shelves.
Expected Annual Customers
Through our distribution network, we expect to reach 5,000 retail shops annually.
But this number can be boosted via marketing campaigns and promos which are run directly with retail customers in areas where our distribution hasn’t covered.
Estimated Annual Revenue
We expect to distribute at least 30 bags of our large package and 300 packs of our smaller package annually to 5,000 retail shops.
That means we could make around 1.5 billion Naira annually in wholesale revenue.
Production & Distribution Cost
Our production costs include sourcing of raw materials, branded packaging materials, power supply, distribution, wages and other production costs.
Ideally, we spend about 2,500 Naira to produce a bag of flour.
Profit Margin
Currently, our profit margin stands at 38% but we are looking to scale that up to about 55% once we improve on our production efficiency.
Kachi Mills is owned by Kachi Solomon, who is currently the CEO of the business.
He has a background in agric economics and grew up in a family that owned a flour processing mill.
He works with Hazzan Mar who is the quality control manager, Chioma Ude the resource manager, Jane Menno the business development manager, and James Gigi the distribution coordinator.
Business Journey
The flour mill business was inherited by Kachi Solomon from his family in 2012, and has undergone major rebranding since then.
With a 5 million loan facility, the company acquired new flour mill machines a company distribution vehicle, and new staff.
In 2018, we also launched our 600g flour packaging which is aimed at meeting demands for retail customers.
We have since grown our wholesale customer base from just under 1,000 to over 5,000.
Market Analysis
Market size/target audience.
According to World-grain, Nigeria’s 3.2-million-tonne flour market is valued at $2 billion, and growing at 3.5% a year.
We expect Lagos to have at least 10% share of that market, which would be valued at $200 million.
We are mostly looking to address this market via capturing processed food retailers and wholesalers in and around Lagos.
If we can address about 10% of the Lagos market, we’ll be able to make $20 million per year.
Marketing Plan
Our marketing plan involves reaching out to consumers, retailers, and wholesalers, and trying to address their needs.
The first plan is to deliver exceptional quality with all our flour products in order to meet the demands of our customers.
Also, we are incorprating a reward program that helps wholesalers and retailers make more profit if they sell more of our products over that of our competitors.
SWOT Analysis
Strength: Our strength lies in having a superior product that is easily the most affordable in the market.
Weakness: Our brand is still relatively unknown with products sold in only a section of the country.
Opportunity: We have a plan to expand our customer base by reaching markets in other states in Nigeria. With a few additional distributors we can achieve this.
Threat: We could be heading into a price war with any of our big competitors if they niche down to our flour categories.
Business Needs
Our plan right now is to grow big as fast as possible.
We are looking to add more packaging options to our range of products and also increase our distributorship.
To achieve this, we are already making plans to expand our production facility while acquiring warehousing in strategic locations around the country.
We require funding of 150 million Naira to help us quickly scale these plans in order to achieve our business and financial goals.
Future Plans
We plan to triple our production capacity in the next five years, which would help us to at least double our revenue.
We are also looking at outsourcing our packaging through industry partnerships to help us speed our distribution and compete favorably in the market.
Cash Flow Projection
To create a cash flow Projection for your poultry farm business plan, click here to use our Simple Financial Template .
- Poultry Farm Business Plan Sample (With Financial Template)
- Real Estate Services Business Plan (Sample + Template)
- Fashion Boutique Store Business Plan (Sample + Template)
- How to Create Financial Projection for Business Plan (With Free Template)
- Business Plan Template for Creating your Business Roadmap
Chijioke Solomon
Share This Post:
- Email this Page
- Share on Reddit
- Buying Guide
How to Start a Flour Mill Business – Complete Guide
- Next What Business Research Team
- January 3, 2024
A flour mill is an easy business to start. You can start this business in both city and rural areas. Furthermore, a flour mill offers a wide range of manufacturing opportunities for entrepreneurs.
What is a Flour Mill Business?
A flour mill business involves the processing of wheat and other grains to produce flour, a fundamental ingredient in various food products. The primary objective of a flour mill is to transform raw wheat kernels into flour through milling processes.
How a Flour Mill Works
Here are key aspects of a flour mill business:
Raw Material Processing
Flour mills source raw materials, mainly wheat, from agricultural regions. The quality of wheat is crucial for producing high-quality flour. The Milling Process starts with the cleaning and conditioning of Raw wheat. It undergoes cleaning to remove impurities and conditioning to optimize moisture content.
Milling Machines
The cleaned wheat is then milled using specialized machinery to separate the bran, germ, and endosperm. This process results in different types of flour, including whole wheat flour and refined flour. Flour mills implement quality control measures by conducting laboratory tests on the flour produced. This includes assessments of protein content, moisture levels, and other factors.
Packaging and Distribution
Packaging: The processed flour is packaged in various quantities, from small consumer packages to bulk packaging for industrial clients. Flour mills distribute their products through various channels, including wholesalers, retailers, and, in some cases, directly to consumers.
Market Segmentation
Flour mills may produce different varieties of flour, such as all-purpose flour, whole wheat flour, speciality flour, and even organic or gluten-free options. It caters to diverse markets, including households, bakeries, food manufacturers, and industrial users.
Regulatory Compliance
Flour mills must comply with local and national regulations related to food safety and quality. This involves obtaining the necessary licenses and certifications. Maintaining high hygiene standards throughout the milling process is essential for regulatory compliance.
Technological Innovation
Flour mills often invest in advanced milling machinery to improve efficiency and product quality. Some mills incorporate automation to streamline processes and reduce labour requirements.
Business Models
Flour mills may adopt various business models, such as traditional milling, speciality flour production, organic flour milling, or industrial-scale milling.
Market Trends
Adaptation: Flour mills monitor market trends and adapt their processes to meet changing consumer preferences. This may include producing gluten-free products or emphasizing sustainable and organic practices.
Supply Chain Management
Flour mills establish reliable supply chains for wheat, often collaborating with farmers or agricultural cooperatives. Efficient logistics are crucial for timely sourcing of raw materials and distribution of finished products.
Is the Flour Business Profitable
Flour remains a staple in various food products, contributing to consistent consumer demand. Data from market research indicates sustained consumer interest in home baking and cooking, driving flour consumption. According to a report by Statista, the global flour market was valued at approximately $245 billion in 2020. The market is projected to witness a compound annual growth rate (CAGR) of around 3.7% from 2021 to 2028.
15 Steps to Start a Flour Mill Business
Starting a flour mill business can be a rewarding venture, providing a staple product that is in constant demand. Here’s a step-by-step guide to help you navigate the process of establishing a successful flour milling business:
1. Conduct Market Research
Identify the target market by determining the demand for flour in your target market. Consider factors such as population size, dietary habits, and the presence of competitors.
2. Select your Niche
Below we list down the Most Profitable Flour Mill Business Ideas:
- Bran: The bran is the skin of the grains. Also, bran is used as a dietary fibre.
- Cornflour: Cornflour is an essential item in the food processing industry. Corn milling or maize milling is a highly profitable business. However, you must establish the mill in a location where you can source the corn easily.
- Gram Flour: The most common name for gram flour is besan. And the product has a great demand in our country.
- Sooji: Sooji is another trendy grocery item in our country. You can produce sooji from the same manufacturing unit.
- Wheat Flour (Atta): Atta is one of the most essential items for the domestic kitchen.
- Wheat Flour (Maida): Maida has comparatively more demand than atta.
3. Select the Business Model
The business models of flour mills can vary based on factors such as scale, target market, and value proposition. Here are several common business models adopted by flour mills:
⇒ Traditional Flour Milling Model
Traditional flour mills follow a conventional model of sourcing wheat, milling it into flour, and distributing the product to local markets.
⇒ Specialty Flour Milling Model
Speciality flour mills focus on producing unique and high-quality flours tailored to specific consumer preferences or dietary requirements.
⇒ Organic Flour Milling Model
Organic flour mills exclusively source and process organic wheat, catering to the growing demand for organic and sustainable food products.
⇒ Industrial Flour Milling Model
Industrial flour mills operate on a large scale, producing massive quantities of flour for commercial and industrial use.
⇒ Vertical Integration Model
Flour mills employing vertical integration control various stages of the supply chain, from wheat cultivation to retail distribution.
⇒ Direct-to-Consumer Model
Flour mills adopting a direct-to-consumer model sell their products directly to end consumers through online platforms, farmer’s markets, or on-site stores.
⇒ Contract Milling Model
Contract milling involves milling wheat on behalf of other businesses, allowing them to focus on their core activities.
⇒ Export-Oriented Model
Flour mills following this model focus on exporting their products to international markets, capitalizing on global demand.
⇒ Cooperative Flour Milling Model
Cooperative flour mills are owned and operated by a group of farmers or community members who share in the management and profits.
Read: Home Based Manufacturing Business Ideas
4. Create a Business Plan
Clearly outline your business goals, including the scale of production, target market, and financial projections. Conduct a thorough cost analysis covering equipment, raw materials, labour, and operational expenses.
5. Choose a Suitable Location
Select a location close to wheat-producing regions to minimize transportation costs. Ensure access to essential infrastructure, including water and electricity.
6. Obtain Necessary Licenses and Permits:
You need to understand and comply with local and national regulations governing flour milling. Obtain the necessary licenses and permits required to operate a flour mill.
Here we put a list of basic requirements.
- First of all, determine the form of the organization and register your business with ROC.
- Apply for the Trade License from the local municipal authority.
- Furthermore, apply for Udyog Aadhaar MSME Online Registration
- Apply for FSSAI registration.
- You have to apply for AGMARK .
- Apply for BIS certification
- Check the tax liabilities.
- This business doesn’t demand any pollution clearance. However, check it with the State Pollution Control Board of your area.
- Apply for the GST registration number.
7. Secure Funding
Determine the initial investment required for land, equipment, and working capital. Consider loans, grants, or partnerships to secure the necessary funds.
8. Flour Mill Business Plant Setup & Machinery
First of all, you have to secure a location for manufacturing operations. Check the available transportation facility, electricity, water, semi-skilled manpower, and drainage facility. For setting up a small-scale unit with the entire product range, you will need to have 3000 Sq Ft built-up areas at least.
Related: Things To Consider in Selecting Factory Location
Here are some basic requirements for plant & machinery:
- Bucket elevator
- Reel machine (3 segments)
- Rotary separator with aspiration channel
- Scourer machine with aspiration channel
- Intensive dampener
- Indent cylinder
- Screw conveyor
- V-Groove, Pulleys, Couplings, V-Belts, etc
- Weighing scale
- Dust cyclone
- L.P fan for cleaning
- Roller Mill body
- Roll Grooving & spindle cutting
- Supper cyclone
9. Set Up the Milling Unit
Design an efficient layout for the milling unit, considering workflow and safety. Set up and install the milling equipment, ensuring proper calibration and maintenance.
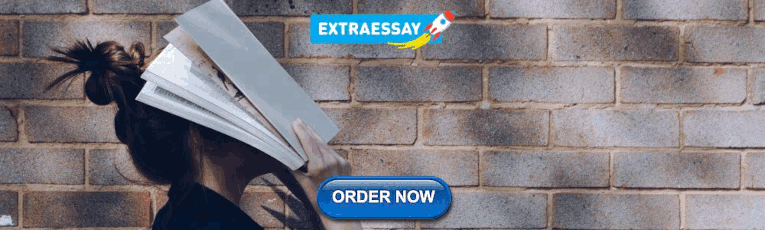
10. Quality Control Measures
Implement regular testing procedures to ensure the quality of the flour produced. Adhere to strict hygiene standards in the milling process to meet regulatory requirements.
11. Employ Skilled Workforce
Hire experienced millers for operating machinery, quality control, and overall production management. Conduct training programs to enhance the skills of your workforce.
12. Develop Distribution Channels
Build relationships with distributors, wholesalers, and retailers for efficient distribution. Consider export options to expand your market reach.
13. Implement Marketing Strategies
Develop a strong brand identity for your flour. Highlight any unique qualities or milling processes. Utilize online platforms to create awareness and reach a wider audience.
14. Monitor Wheat Market Trends
Keep abreast of wheat market trends, including price fluctuations and supply-demand dynamics. Implement strategies to manage risks associated with market volatility.
15. Build Relationships with Suppliers
Negotiate favourable contracts with wheat suppliers to ensure a steady and cost-effective supply. Work closely with suppliers to maintain consistent quality standards.
Related: Questions To Ask Before Starting a Manufacturing Business
Frequently Asked Questions
What is the cost of setting up a flour mill.
The flour milling business generally demands two different types of investments. One is a fixed capital investment. It includes land (if you purchase the land), building, machinery, registration, and licensing fees. If you start the business with a rental premise then fixed capital includes the security deposit amount for the area of land.
Another is the working capital investment. It includes raw materials, staffing, rent, transportation, marketing, distribution, and administration costs. There are different types of small business loan-providing companies in our country. Loan providers also offer various customized schemes for your specific requirements.
Related: Best Small Business Loans in India
4. What is the profit margin of flour mills?
You can earn an inspiring profit margin from a flour milling business. However, the percentage of profit depends on several aspects. To enhance the profit, you will need to reduce the production cost.
Also, you must consider enhancing the sales volume and penetrating new areas. Remember, you will only expect a good profit when you sell the product as a brand.
What Types of Flour Can Be Produced by a Flour Mill?
Flour mills can produce various types of flour, including all-purpose flour, whole wheat flour, speciality flour (such as gluten-free or organic), and customized blends based on consumer preferences.
What are the Key Factors Influencing Flour Business Profitability?
Key factors include market demand, product diversification, operational efficiency, raw material costs, and adherence to quality and safety standards.
What are the Market Trends in the Flour Industry?
Market trends include increased demand for speciality and organic flour, the rise of e-commerce and direct-to-consumer sales, and a focus on healthier flour options.
Can Flour Mills Export Their Products?
Yes, flour mills often explore export opportunities. Understanding international trade regulations, market demand, and quality standards is essential for successful exports.
What Certifications are Important for Flour Mills?
Answer: Certifications such as ISO 9001 (Quality Management), ISO 22000 (Food Safety Management), and relevant organic certifications contribute to ensuring quality and compliance with industry standards.
What Challenges Might Flour Mill Businesses Face?
Challenges can include fluctuating raw material costs, market competition, regulatory changes, and the need for ongoing investments in technology and quality control.
The Editorial Staff at NextWhatBusiness is a team of Business Consultants having years of experience in small and medium-scale businesses.
Sample Flour Mill Business Plan
Flour mill business plan sample.
If you have been worried about how to start a flour mill business, then you are warmly welcomed. I am ready to take your hands and show you how well you can do it. But wait for a moment, have you ever asked yourself these questions?
One, is the flour mill business lucrative? Two, is the demand for flour that high? And lastly, are the raw materials to produce the flowers readily available?
It might interest you to know that ‘yes’ is the answer to all these questions!
However, you might ask? Why do I have to find answers to these questions? The answer is simple. Positive or negative answers to these questions will either stimulate your arousal or kill the passion to start a flour mill business.
Scan through what happens all around you with the daily demand and usage of flour. Bakery, food processing and pharmaceutical companies are the largest consumers of flour and we get to see their end product each passing day.
Not exempting the local use in your vicinity for pastry as well.
Additionally, the raw materials for the production of flowers which could either be corn, wheat or millet are readily available. All these gives a high demand for flour and promise a high Return on Investment (ROI).
The next step is knowing what how to start a flour mill. Although there is a caution. The steps might seem similar to any steps for beginning a business, but the processes involved are quite different. Therefore, do not quickly dismiss that you have known a point and thus jump to other. Read carefully!
Steps Involved in Starting a Flour Mill Business
- Get Trained to Handle Factory Machinery or Equipment
If you are a newbie with zero knowledge about how the machines works in the factory, then you should not take this step with levity. You must have a solid foundation.
If your case is a lot different, possibly you have handled or worked at a flour mill company before, you will still need to get acquainted with the machines. There might be new development you have not heard of. Yearn to have basic training on the grinding process in achieving the final product.
To accomplish this will demand that you make visit to flour mill companies so you can be trained. There is an opportunity to make research on the Internet to boost your experience on effective machines you can use and how to handle them.
- Register Your Flour Mill Business
There is no hard and play rule here. Get your business registered. Seek help from the local authority in your location or the location where you intend to choose on how you can register your business. You will earn real freedom and operate your business like a king.
- Write a Flour Business Plan
Your flour mill startup plan is not limited to the size of the business you are operating. Therefore, it is a must to write a decent and well explanatory plan if you want to start a flour mill business. If you will need loan to fund your business, you must write a catchy business plan so as to attract investors.
- Acquire a Location
You might have to rent or buy a space for your flour mill industry. Getting a location for the business is a must. That is where you will have your machinery installed and the company’s office.
The size of the location primarily will be influenced by the size of machines you are to run and the number of workers to employ. It is also important to bear in mind that the location of the flour mill industry should be easily located by customers and easy delivery of raw materials for the production of flours.
- Buy Flour Mill Machinery and Raw Materials
The space you have acquired for your business would not function without the installation of machines and buying of raw materials to start the flour mill. It is then required that you buy the machines you have surveyed during your training and visit cost effective locations to buy the machines. If you lack fund, you can rent but make it a goal to buy as soon as possible.
Getting raw materials does not require an extensive search. You can contact Companies that stores grains in large quantities for sale.
Also, you can meet mechanized farmers too who stores grains at large quantities majorly for commercial purpose.
- Source for Customers
Every business products needs customers, and your flour mill business is not an exemption. Endeavour to get customers and retain a solid relationship with them. Write companies and inform them about your flour mill company.
Keep to whatever promise you will make. Be optimistic that as your business grows, you will get more customers.
- Keep On Improving
This final phase is not the final stage to start a flour mill business operation. Constantly, you will need to keep improving your products, customer’s relation, modes of advertisement and utilizing new technological equipment.
Have good relationship with your employees and maintain an honest dealing with them. If you try all possible best to keep on improving, you will succeed on the quest to start a flour mill business.
I am well convinced that if these points are applied correctly, you will start a flour mill that will be profitable and at the same time gain the approval of most companies that will be buying your final products.
FLOUR MILL BUSINESS PLAN EXAMPLE
Here is a sample business plan for starting a flour mill.
I will go straight to the point that is, the business plan sample because it is expected that you already know the basics of the business, the requirements and skills since you are about to start it.
BUSINESS NAME: Sammy Jay Wheat Flour Production Company
Executive Summary
Business Overview
Product Offering
Vision Statement
Mission Statement
Business Structure
Target Market
Sales Forecast
Sammy Jay Wheat Flour Production Company is a standard and licensed wheat flour mill production company that will be located in an industrial area, Springfield-Illinois. We have secured a long term lease of the facility in this area which is close to a wheat farm and there is an option of renewal of the lease on agreed terms and conditions which seems favorable to us.
It has been approved by the government to use the facility for this type of business and the facility has easy accessibility and easy movement of raw materials and finished products.
Sammy Jay Wheat Flour Production Company is a business that will engage in processing, packaging and retailing wheat flour. We are in the business to give well packaged wheat flour to customers so they can have the value of their money as well as to make profits.
Feasibility studies and market surveys has been done to find the most suitable location for our business due to the fact that there are several wheat flour mill companies scattered all around the United States and Canada.
Plans have been made to have a wide distribution network for wholesalers in Illinois and the United States.
Apart from producing healthy and well packaged wheat flour, our greatest concern is customers’ care because we know that they are the ones keeping us in business and they are determinants of the success or otherwise of the business. We are ready to go extra miles in satisfying our customers so they can become loyal customers to our business.
There is a CRM software that will make it possible to have a one on one relationship with our customers and also involve our customers when making decisions that directly or indirectly affect them.
Sammy Jay Wheat Flour Production Company is a family business that is owned and managed by Sammy Jay and the immediate family. He is a graduate of micro biology (B. Sc) and also has a Master’s degree in Business Management.
Wheat flour mill business basically has to do with milling wheat grains into flour then package and sell to wholesale distributors, grocery stores and other food related business. The wheat grains are purchased directly from growers or wholesalers.
It is a fact that wheat flour industry will remain relevant in years to come. The profit and revenue generated from the business depends on the price and production of wheat flour. The flour production mill industry under which wheat flour production is a subset, is a sector that thrives regardless of the economy and other kinds of situation.
This type of business is a business that can either be started on a large or small scale; serving your local community is a form of small scale wheat flour business while it becomes large scale once you go beyond your local environment.
Therefore, the wheat flour production company is a profitable business open for anyone to start either on a large scale or small scale.
Sammy Jay Wheat Flour Production Company will operate a standard and licensed wheat flour company that will offer its products not only in Springfield-Illinois but throughout the United States of America.
Our product offering will be processing, packaging and distributing wheat flour in commercial quantities.
The Sammy Jay Wheat Flour Production Company’s vision is to establish a wheat flour production company whose product will be the best and be sold on a large scale.
Our mission is to establish a company that will be world class and favorably compete with leaders in the industry, a company that will be listed among the first ten best wheat flour companies in the United States and Canada.
Sammy Jay Wheat Flour Production Company aims to have a right structure put in place to support the setting up and growth of the company.
Our aim is to hire qualified, hardworking, honest and customer centric people that are ready to work and help achieve the vision of the company. There will be a profit sharing arrangement for all senior management staff which we will be based on their performance for five years or more than based on how quick the set target is met.
Therefore, we will be hiring people to occupy the following positions:
Chief Executive Officer (Owner) Plant Manager Human Resources and Admin Manager Merchandize Manager Sales and Marketing Manager Machine Operators Accountants / Cashiers Distribution Truck Drivers
There is a wide range of customers for wheat flour so our target market cannot be restricted to a group of people but includes everyone who resides in our target locations. Market research has been done to know what the target market is expecting from us.
Our business will be extended to the following group of people:
• Hotels • Restaurants and Canteens. • Event Planners and Caterers. • Households. • Students. • Everybody in our target market location
One certain thing about wheat flour production is that once it is healthy and well packaged and the production mill is easily accessible, you will sure have customers which will lead to an increase in generating revenue.
Sammy Jae Wheat Flour Production Company is in a good position to take on the available market in Illinois by producing well packaged and well-branded wheat flour. We have analyzed our chances in the industry and came up with the following sales forecast:
• First Fiscal Year-: $240,000 • Second Fiscal Year-: $450,000 • Third Fiscal Year-: $950,000
This is done with the assumption that there will be no economic meltdown and there won’t be any competitor in the same location with us offering the same quality of same products and customer care service. Share this wheat flour mill business plan , thanks.
Leave a Reply Cancel reply
Your email address will not be published. Required fields are marked *
- Business Performance Improvement
- Legal Compliances
- Market Linkage
- Newsletters
- Professional Services
- Proposal Creation & Funding
- Research & Policy advocacy
- Yashaswi Udyojak
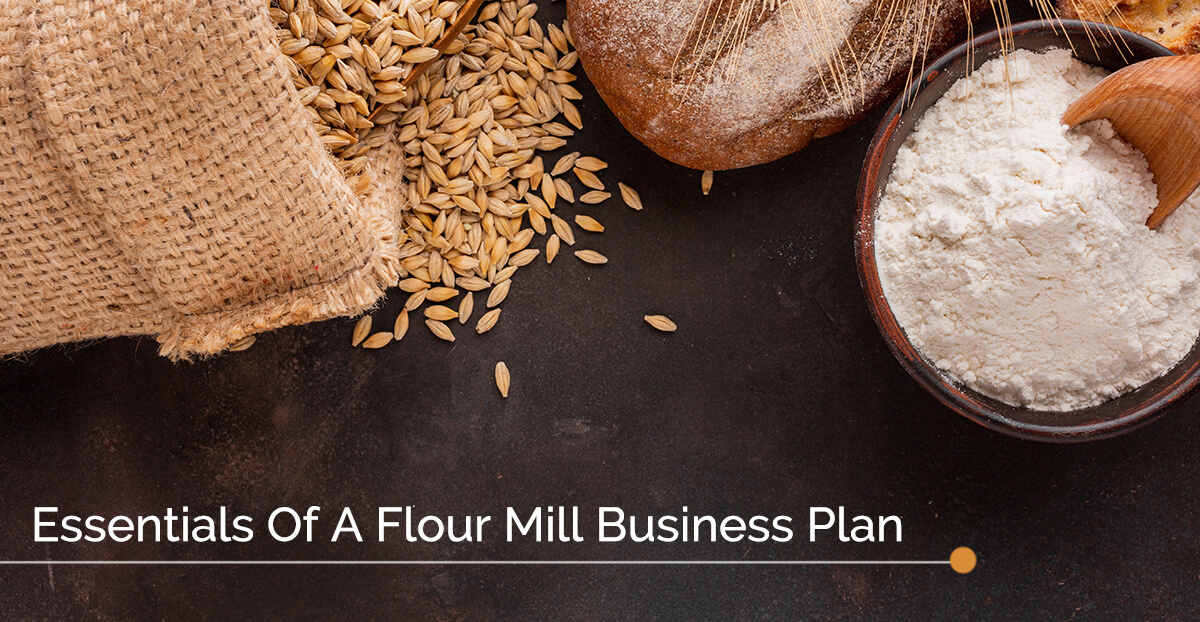
Essentials Of A Flour Mill Business Plan
For an aspiring business entrepreneur, a flour mill business plan is a good idea as it comes under the category of ‘essentials’. Roti, chapati is a daily requirement. Thus, your flour mill business will never be out of business. During the time of festivals, this business is in demand as everyone wants to prepare homemade snacks and sweets.
During Ganpati everyone needs rice flour for those yummy modaks and during Diwali there is a rise in mix dal flour for the tasty chaklis. These are just a few instances of why a flour mill business is absolutely essential.
Besides, one cannot stress enough on the fact that everyone needs homemade snacks and these homemade snacks require a flour mill. And what does a flour mill need? Well, for starters (and most importantly) it needs a flour mill business plan.
Your atta chakki business plan will be your permanent guide. So make sure you work on it diligently and with concentration. To draft a flour mill business plan you need to consider ALL the factors of your business.
Your flour mill business plan should have answers to the why’s, how’s, when’s, where’s of your business. At any point in your business, if you feel stuck or lost, you should know where to seek help from and that is your atta chakki business plan.
Starting a food business requires extra efforts because it’s not just the quantity that matter, but it also includes other factors like quality, hygiene and delivery. Be sure to include all these factors in your atta chakki business plan.
Let’s get to the point, so how to start an atta chakki business ? You need to take care of some technicalities of your business like the legal licenses, the procedure and the capital.
Here’s a detailed breakdown of atta chakki business plan –
The length of business plans may vary depending on how extensively you draft it but it usually contains the same sections. Now you know why a business plan is important. Your atta chakki business plan is like a road map of your business. To make an amazing business plan you need to know what all should be included in a business plan.
Flour Mill Business Plan
Executive summary.
As the word suggests, it should be an ‘executive’ summary of your business. The key points of your atta chakki business plan should find a place here. The sales, the goal, action items and more. You need to remember that your business plan plays a dual role. It will help you incur funds from banks but also act as your guide.
Usually, it can be one to four pages long. Treat as a separate document in the business plan so that you can refer to it and tick your goals and benchmarks as and when required. Your executive summary can be updated and is prone to change as and when you seem fit depending on the progress of your business.
For more details, you can check this business plan checklist that includes the important factors of a business plan.

Management Details
Your flour mill business plan should include the detail of management. The details like how much do you plan to deliver, when do you plan to expand your business and more. This should include the steps of your business.
Marketing Your Business
Before stepping into a business venture, you need to do thorough research. A background study is a must before you start your business. Know your competitors well, know where they are located so as to understand the immediate competition and learn their marketing strategies.
After evaluative research, create a plan and highlight the good points of your business and spread it through online and offline marketing methods. There are many ways of marketing your business. Apart from the digital way of marketing, you can also choose some traditional ways of marketing your business.
You can consider distributing flyers in the immediate vicinity of your business. This way, you can let people in the area know about your business and also this can trigger immediate footfall into your business.
Define Your Service
Give a detailed description of your products and services. Make a consolidated list of all the dals and grains you will be grinding in your flour mill. Even though it is the same obvious list, creating a list will help them locate their needs easily.
Also, you can provide a home delivery service in the vicinity of your business. For example, if you can appoint additional helping staff, you can ask customers to leave the packages and instead of having to wait in the queue, you can deliver it to their home. You can leverage this service while promoting your business as there are not many atta chakki businesses who provide this kind of service.
The Hygiene Factor
This might sound a little obvious, but do not ignore the hygiene factor in your business. Especially a food business needs to take extra precautions to make sure that the location of their business is hygienic and clean. Even the staff should take the necessary precautions like wearing hand gloves or caps.
This will help in building trust in your customers as nothing is more appealing in a food business that cleanliness and hygiene. The caps and gloves will earn you extra stars from your customers. Tiny things like these trigger the ‘word of mouth’ promotion and before you know, you will have a loyal and a long customer base.
The Flour Mill Equipment
Obviously, you need the soul of your business and that is the flour mill equipment. When you are done managing the aforementioned factors, the entrepreneur should ask the most important question and that is which, how and where to get the flour mill machinery from. All these questions have majorly depended upon the capital that you are going to invest in the machinery, the capacity of your production, availability of raw material and the overall investment.
Therefore, this decision cannot be made in a haste and it will definitely not be an overnight process. It will take a considerable time to choose the aptest and reliable flour milling equipment supplier. This carefully taken decision will help you avoid any unseen problems in the operation and installation of the flour milling factory and also help in minimising the cost of machinery purchases.
The Legal Support
Any business is incomplete without strong legal support. Your business needs to be compliant with all the necessary legal licenses. It is important that you safeguard your business with these legal formalities. Your atta chakki business will need to be compliant with the following legal licenses –
Any food business is incomplete without FSSAI license. Your atta chakki has to comply with all the regulation set by the Food Safety and Standards Authority of India. FSSAI Certification in your premise adds to the trust quotient in your customers. It is not a difficult procedure, you just got to keep the right documents ready.
Udyog Aadhar
An flour mill is considered as a small or micro business and hence it needs to be registered under Udyog Aadhaar which is a registration and recognition for micro, small, and medium enterprises (MSMEs).
You need to check the state-specific licenses depending on the location of your business. In Maharashtra, your atta chakki business will require a Shop Act License from the local municipal authorities for the purpose of carrying out the business operations.
This licence helps in regulating the management of the business and takes care of factors like working conditions, working hours, holidays, wages, leaves, etc. of the employees and helps in running your business efficiently.
GST Registration
Goods and Service Tax enables entrepreneurs to avail government scheme benefits and only GST compliant businesses are allowed to charge GST on their products and services. All businesses, including the flour mill, has to consider the tax system at one point or the other. To be able to and handle a unified, single and uniform taxation method, the business needs to be registered under the common GST scheme/ the Goods and Service Tax.
Your atta chakki business plan should be inclusive of the status of all the mentioned legal licenses.
So above are the essentials of a flour mill business plan. Hope that you find all the necessary information under this one roof. Agreed that business plan is a meticulous process but once you get through with it, it will help your business. If you need further help with your plan, you can avail deAsra’s business plan services which will help you in creating a successful business plan.

If you have any entrepreneurial questions, please reach out to deAsra Foundation . With a wide range of resources, deAsra will be able to help you in your entrepreneurial journey.
Are Paid Ads Effective for Small Businesses? Find Out Why You Should Consider Them
In today’s cutthroat market, small businesses must be adept at navigating the digital landscape. In today's digital age, a significant 69% of small businesses harness digital marketing to attra...
From Wardrobe to Worldwide: 8 Expert Tips for Selling Clothes on E-commerce Platforms
Taking the leap from a local clothing line to a vibrant online store can seem daunting, but with the right tools and a sprinkle of creativity, your fashion brand can thrive in the vast world of e-comm...
Why ONDC is the Ideal Cost-Effective Solution for Small Business Owners
The Open Network for Digital Commerce (ONDC) is rapidly expanding its digital footprint, now reaching over 482 cities, offering a diverse and dynamic marketplace across 10 distinct domains. With 90 ac...
A Guide to Registering Your Restaurant on ONDC
Welcome to the digital revolution, restaurateurs! Are you ready to take your mouth-watering menu online with the Open Network for Digital Commerce (ONDC)? It’s not just a platform; it’s a banquet ...
Girija Oak: “You Are Your Own Brand”
In the vibrant tapestry of entrepreneurship, the ability to distinguish oneself through a unique brand is invaluable. The Entrepreneur Excellence Awards, a beacon of innovation and entrepreneurship, p...
Leave a Reply Cancel reply
Your email address will not be published. Required fields are marked *
Step 1 of 2
All fields marked* are mandatory
To continue reading further, please provide us the below details
- Name * First Last
- Country Code *
- Facilitator Email
- External Handholder Email
- Selected Service
- EHH Engaged Consent Stay Engaged with EHH only
- LS Response
- Business Rule
- Response Message
- UTM Campaign

wrong OTP try again!!
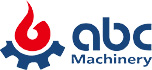
- Crafting a Comprehensive Wheat Flour Mill Business Plan in Ethiopia
Are you thinking about starting a wheat flour mill business in Ethiopia? Do you want to invest in a profitable and successful business?
Ethiopia is a country with a rich agricultural heritage and a growing population. Wheat is widely consumed in various forms as one of the main crops, making wheat flour an important commodity. At the same time, the Ethiopian government recognizes the importance of the flour mill industry, promoting investment and supporting local wheat flour production.
Therefore, setting up a wheat flour mill plant in Ethiopia can be a lucrative business. However, to ensure the success of your venture, you need a solid wheat flour mill business plan .
Relaetd Posts: Setting up a flour mill in Pakistan>>
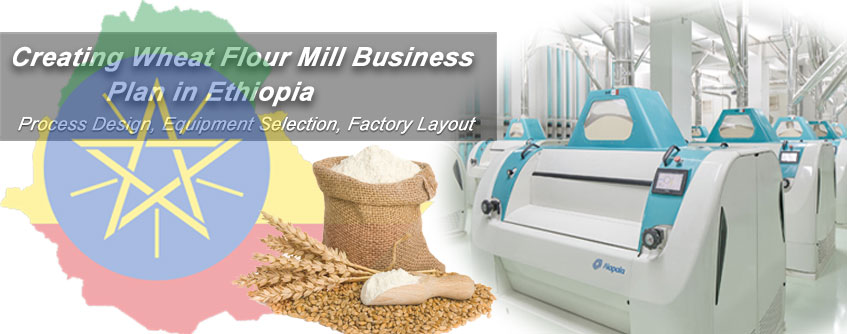
In this article, we will cover the steps to customize a wheat flour mill business plan for the Ethiopian market , to help you achieve your business goals. If you have any questions while reading, don't be shy about consulting us for professional answers!

How to Create a Wheat Flour Business Plan in Ethiopia: A Complete Guide
Developing a business plan for your wheat flour processing business is critical to ensuring the success of operation. It provides direction and goals for setting up a wheat flour mill and is a guide for entrepreneurs to ensure the success and sustainability of the business.
Here are the key components and writing points of a wheat flour business plan:
1 Executive Summary
Your business plan should begin with a concise executive summary that provides a high-level view of your business . This section should capture the essence of your flour mill business, including its vision, mission, and goals.
2 Company Description
In this section, provide a detailed overview of your wheat flour mill factory . Describe the history and background of your flour mill company, its location, and legal structure. Potential investors or partners will use this information to assess the viability of your business.
3 Market Research and Analysis
Thorough market research is the cornerstone of your business plan. You must gain an in-depth understanding of the Ethiopia wheat flour market , including its size, demand, and competition. Gather data on wheat production, consumption, and trends, and consider factors such as regional differences in consumption, the quality of wheat produced, and local consumer preferences. (Read More: Flour mill market analysis column>> )
4 Products & Services
What types of wheat flour mill products do you plan to produce? These may include different grades of flour for a variety of uses, such as bread, pastries, or traditional Ethiopian dishes such as injera. In addition, please consider value-added services, such as packaging or distribution.
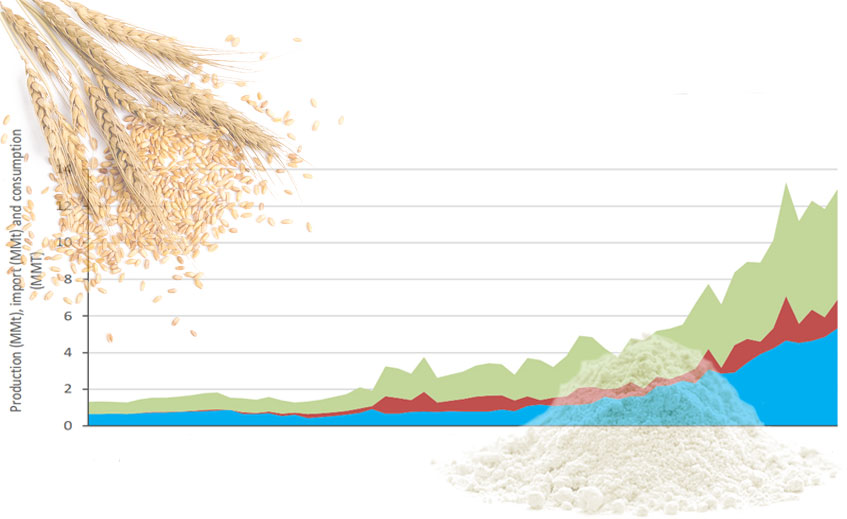
5 Sales and Distribution
How will you sell your products? Describe your sales strategy in this section, whether you plan to sell directly to consumers, wholesalers, or retailers. Discuss the distribution channels you will use to ensure that your flour products reach the right place at the right time.
6 Management and Organization
Introduce your management team and their role in the organization. Explain the organizational structure of your wheat flour mill business, showing how responsibilities are divided.
7 Capital Requirements
Setting up a wheat flour mill plant requires capital for commercial wheat flour mill machine , facilities, and operating expenses. Estimate the capital you will need and explain how you plan to obtain it. Whether through personal savings, loans, or investors, define your financial requirements. (Related Posts: Wheat flour mill plant cost>> )
It should be noted that investment in starting a wheat flour mill mainly includes the following aspects: Wheat flour mill machinery and equipment cost Raw materials-wheat purchase cost Labor costs Infrastructure and land plant costs Other costs and expenses
8 Risk Analysis and Mitigation
Identify potential risks your business may face and describe strategies to mitigate them. Address issues related to market volatility, competition, or operational challenges.
9 Appendices
Include any additional information that supports your business plan for wheat flour production. This could be market research data, resumes of key team members, legal documents, or any other relevant information.
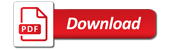
Promising Investment Prospects in Ethiopian Wheat Flour Milling Industry
Ethiopia, a nation with a rich agricultural heritage and a burgeoning economy, presents compelling investment prospects in its milling industry. There are mainly these advantages conducting wheat flour milling business in Ethiopia:
- Abundant wheat resources: Wheat production and consumption have both increased in Ethiopia despite the existence of strong markets for potential substitute grains.
- Government support: The Ethiopian government has played an active role in wheat markets, such as making large investments in extension programs and adopting protectionist policies to ensure government control of all commercial grain imports.
- Low labor costs: With a relatively low labor cost environment, businesses can maintain competitive pricing structures.
- Development opportunities: As a developing country, Ethiopia is undergoing rapid economic growth, providing development opportunities across various industries, including the food processing sector.
Project Report for Wheat Flour Mill Business in Ethiopia-ABC Machinery
Click on the image to view details of the Wheat Flour Mill Plant Project in Ethiopia.
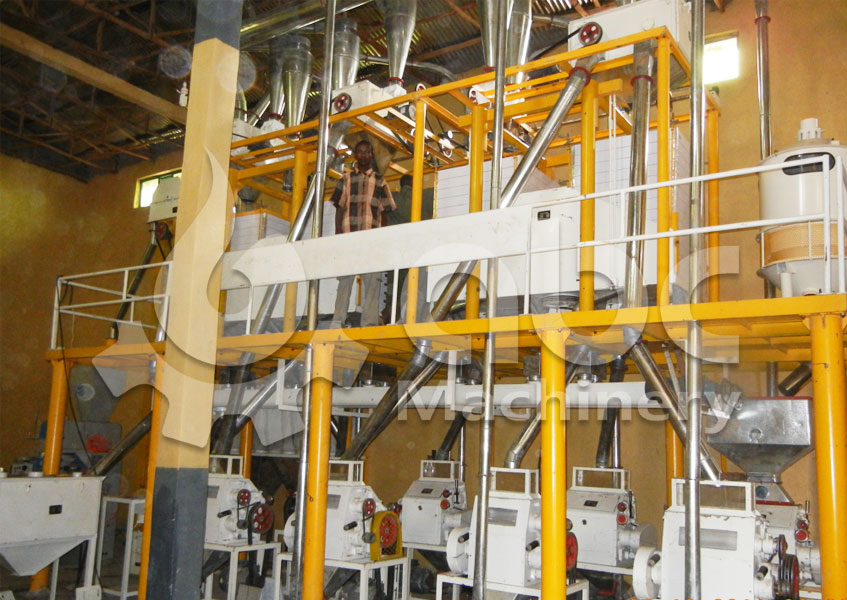
FAQs of Starting Wheat Flour Processing Business in Ethiopia
- How much does it cost to set up wheat flour mill plant in Ethiopia?
- If you are planning to start a small flour mill business, you will need about 50,000 to 60,000 Ethiopian Birr. A large wheat flour mill will cost around 140,000 Ethiopian birr or more, with a variable ceiling. It also depends on the type of flour mill machine required for the business and the complexity of the wheat milling process .
- What licenses are required to start a flour mill in Ethiopia?
- The specific licenses and permits you will need may vary depending on the size and location of your flour mill company. You may need these licenses and permits: Business Registration, Environmental Permit, Food Processing License, Tax Identification Number (TIN), Health and Safety Permits, etc.
- 10-20TPD Wheat Flour Mill
- 30-60 TPD Wheat Flour Mill
- 70-200TPD Wheat Flour Mill
- 200-500 TPD Wheat Flour Mill
- 500-1000TPD Wheat Flour Mill
- 10-20TPD Maize Flour Mill
- 30-100TPD Maize Flour Mill
- 100-200TPD Maize Flour Mill
- bean peeling plant
- chili powder making machine
- Cassava Starch Production Plant
- Soy Protein Isolate Production Line
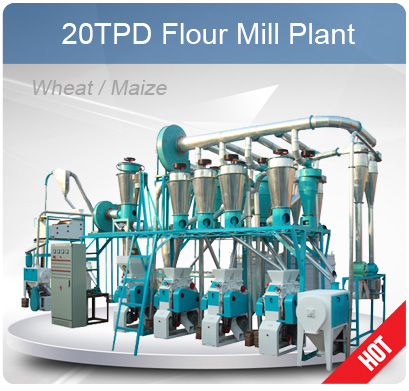
40 TPD Maize Flour Mill Plant Project Setup in Uganda
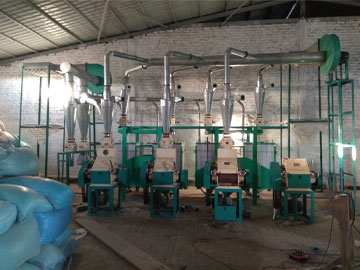
30TPD Maize Flour Milling Plant Setup in Chad
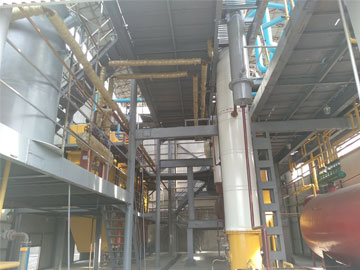
100TPD Soybean Protein Isolate Plant Project Built in Uzbekistan
- Launch Your Maize Flour Mill Business with Proven Strategies
- Buying Flour Mill Machine for Home: What You Need to Know
- Guide to Flour Mill Machine Price in India | Considerations Before Buying
Recently, the mayor of a city in Zimbabwe visited a local maize processing plant project. The plant is the latest cooperation project between ABC Machinery and our Zimbabwean client. All the highly efficient maize mill machines for the maiz...
Zambia 2024 is coming up with AGRITECH EXPO ZAMBIA exhibition at GART Research Centre, Chisamba (April 18th to April 20th) . ABC Machinery will be participating in this years Exhibition. We cordially invite you to visit our booth (A19) and...
Recently, our Ethiopia client ordered a 60TPD Wheat Flour Plant to produce wheat flour. The main equipment of the wheat flour manufacturing plant includes a combined cleaning sieve, wheat washing machine, wheat scourer, rotary sieve classif...
Download Wheat Flour Mill Business Plan Sample
Considering all the requirements for starting or expanding your wheat flour production business, we put together this Wheat flour Mill business plan template.
Wheat Flour is consumed all across Nigeria for its delicious taste and health benefits . There is a strong demand for the product, so market entry is not as difficult as most would think.
So let’s proceed to the business planning section.
READ -Download Cassava Processing Business Plan with 3 Years Financial Analysis
A Sample Wheat Flour Production Mill Business Plan Template
TABLE OF CONTENTS
1.0. Wheat Flour Mill Business Plan Executive Summary
Labake Wheat Flour Production Company is a standard wheat flour mill production company that will be located in an industrial area in Lagos State. We have been able to secure a long term lease for a facility in a strategic location, this location is strategic as it is close to a big wheat farm with an option of a long term renewal on agreed terms and conditions that is favourable to us. We have sought and acquired government approval for the kind of business we want to run and it is easy to access this reason was deliberate as it would facilitate easy movement of raw materials (wheat grains and packaging materials e.t.c) and finished products (well-packaged wheat flour). We are in the wheat flour mill production business to engage in processing, packaging and retailing wheat flour. We are also in business to make profits at the same to give our customers value for their money; we want to give people and businesses who patronize our well – packaged wheat flour the opportunity to be part of the success story of Labake Wheat Flour Production Company.
We are aware that there are several big scale and small scale wheat flour mill production companies scattered all around Nigeria whose products can be found in every corner of the country, which is why we spent time and resources to conduct our feasibility studies and survey the market so as to enable us to situate the business in an area that will ensure the support of the ascent of the business and also for us to be able to add much more value more than our market rivals will be offering. Our facility is easy to locate as we ensured that, and we have designed plans to create a wide distribution network for wholesalers all around Lagos and across Nigeria.
Much more than producing healthy, well processed and well-packaged wheat flour, our customer care is going to be second to none. We know that our customers are the reason why we are in business which is why we will go the extra mile to get them satisfied when they visit to purchase our wheat flour warehouse and also to become our loyal customers and ambassadors. Labake Wheat Flour Production Company will ensure that all her customers (wholesale distributors) are given first class treatment whenever they visit our flour mill or warehouse. We have a CRM software that will ease the task of managing a one on one relationship with our customers (wholesale distributors) no matter how large the numbers of our customer base may grow to. We will ensure that we get our customers involved when making some business decisions that may affect them directly or indirectly. Labake Wheat Flour Production Company will be owned and managed by Labake and his immediate family members, it may be tagged as a family business.
Labake who is the Chief Executive Officer of the Company is Graduate of Micro Biology (B.Sc.) and he holds a Master’s Degree in Business Management (MBA). She has well over 15 years of experience working in related industry as a senior manager prior to starting Labake Wheat Flour Production Company. She will be working with a team of professionals to build the business and grow it to enviable heights.
2.0. Our Product Offering
Labake Wheat Flour Production Company is going to operate a standard and licensed wheat flour mill production company whose products will not only be sold locally but also across the federation. We are in this line of business to generate profits and also to give our customers value, not only in form of goods, in exchange for the money. We are going to do all that is permitted by the law of the land to achieve our business aim and ambition. Our product offering will be;
Processing, packaging and retailing wheat flour in commercial quantities
3.0. Our Vision Statement
Our vision is to create a standard Wheat Flour Production Company whose products will not only be sold in Lagos but also throughout the Country.
4.0. Our Mission Statement
Our mission is to establish a standard and world-class Wheat Flour Mill Production Company that in our own capacity will favourably compete with leaders in the industry. We want to build a wheat flour mill production business that will be listed amongst the top 10 wheat flour mill brands in West Africa
5.0. Our Business Structure
Labake Wheat Flour Production Company is a business that is established with the aim of competing favourably with other leading wheat flour brands in the country. This is why we will ensure that we put the right structure in place that will support the kind of growth that we have in mind while setting up the business.
We will ensure that we hire qualified individuals, that are defined by honesty and hard work, that are concerned about the customers and are willing to work to help us put together a prosperous business that will benefit all the stakeholders (the owners, workforce, and customers). As a matter of fact, a profit-sharing arrangement will be made exclusively for all senior management staff and it will be based on their performance and attitude to work for a stipulated period, maybe of five years or more, depending on how fast we meet our set target. In view of that, we have decided to hire qualified and competent hands to be on deck for the following positions;
- Chief Executive Officer (Owner)
- Plant Manager
- Human Resources and Admin Manager
- Merchandise Manager
- Sales and Marketing Manager
- Machine Operators
- Accountants / Cashiers
- Distribution Truck Drivers
READ –
How To Download The Full Wheat Flour Mill Business Plan Template PDF (with financial analysis)
Above is a part of the wheat flour mill business plan template in Nigerian. IF you need the complete business plan, follow the procedures to download it.
Pay the sum of N8000 ( eight thousand naira only) to the account detail below: Bank: GTBank Name: Oyewole Abidemi (I am putting my name and not our company account so you know we are real people and you can trust us) Ac/No: 0238933625 Type: Saving
Thereafter, send us your email address through text message to +234 701 754 2853 . The text must contain the title of the wheat flour mill business plan you want and also your email address. Immediately after the confirmation of your payment, we will send the business plan in Nigeria to your email address where you can easily download it.
Dr. Abi Demi is a skilled technical writer and author with specialties in the martech and fintech space. Featured on Tekedia, Coin Review, Business Insider, Fintechna, Cryptocoin.news, Date 360 and several other sterling online publications, Demi is an astute technical writer that specializes in finance, marketing and technology - with over 500 published pieces across the internet ecosystem. Contact Abi Demi - [email protected]
Download Logistics and Transport Business Plan in Nigeria
How to start a wheat flour mill business in nigeria, you may also like, feasibility study sample for private school, private school business plan sample, feasibility study template for zobo production, business plan sample for zobo production, ict feasibility study sample, download ict business plan sample, download snailery feasibility study sample, download snailery business plan sample business, 8 farming & agriculture business ideas in nigeria, 5 investment apps for saving, growing your money....
Fascinating information! I cant believe Ive finally found the information Ive been searching for for so long. Thank you!
Leave a Comment Cancel Reply
Save my name, email, and website in this browser for the next time I comment.
Chat With Us
Schedule A Call Back
Our Experts are ready to assist you, Let's Connect with Us By submit your enquiry.
Welcome to Corpseed. Please type your query, and we shall provide immediate assistance.
Didn't receive code? Resend OTP
Your Enquiry has been received !!
Our legal advisor will contact you shortly.., how to start a flour manufacturing company in india.

- Importance of Flour Mill in India
Flour is an important aspect of the Indian diet because it is used in almost all of our cuisines. As a result, flour is an item that almost every household purchases on a regular basis, making flour manufacturing a viable business opportunity. Flour milling enterprises have sprouted up all throughout India, owing to the tremendous opportunities they bring in both rural and urban areas. So, how do you establish a flour production business, and what permits are required? We'll look at all you need to know about beginning a flour mill business in India in this article.
Table of Contents
Why Start a Flour Manufacturing Company in India
Business registration, fssai license, udyog aadhar registration, gst registration, shop license, trade license, bis certification, what are the steps involved in starting a flour mill company in india.
--------------Blog Contact Form-------------
The flour mill can grind a variety of grains, including maize, rice, spices, and nuts, in addition to wheat. It saves a lot of time and allows you to grind wheat finely or coarsely depending on your needs. Packed flour contains preservatives and may lack critical elements, but you can ground fresh flour rich in nutrients and vitamins with the help of grinding mills.
The majority of Indians consume flour on a regular basis because all of our primary recipes require it in some way or another. As a result, retail establishments, households, and even restaurants require a steady supply of flour, making a flour milling firm an attractive investment option in India. A flour manufacturing firm can be a good idea if you want to start a small-scale food business in India. Furthermore, because of the great demand for the goods, this is the type of business that requires little capital but guarantees high returns. Depending on the size of your operation, you can start one of two types of flour mill businesses.
- Small-scale: On a smaller scale, charge cash for milling grains for personal use. While the profit margins aren't particularly large in this situation, it takes very little money to get started.
- Large-scale: On a large scale, Process flour from raw ingredients you've sourced and sell it to merchants or other consumers.
Licenses Are Required To Start a Flour Manufacturing
A flour mill falls under the category of a food production firm, it will necessitate the acquisition of specific licenses. Here's a quick rundown of the numerous licenses and registrations you'll need to start a business like this in India.
- Udyog Aadhaar Registration
- GST registration
In order to start an Atta Chakki business in India, each potential owner must first register his or her company. Furthermore, the Sole Proprietorship Firm is the best business structure for starting a Basic Mill. However, the finest type of business format for starting a flour manufacturing company in India is a Private Limited Company Registration .
A Flour Mill or Atta Chakki business is classified as a food business in India. As a result, the owner must get an FSSAI License or FSSAI Certificate from India's Food Safety and Standards Authority.
The Ministry of MSME issues Udyog Aadhaar (also known as Aadhaar for Business) to small and medium-sized firms who want to register as MSME. A sole proprietor company owner, unlike other business entities, does not have formal recognition of his business. Udyog Aadhaar is highly recommended for sole proprietors who do not have official government recognition since it allows the alone owner to obtain a unique identity and official registration with the Government of India, which verifies the existence of his business.
GST stands for goods and service tax, introduced in India on 1st July 2017 and replaced around 15 other cascading taxes levied by the Central and State governments. Under GST, goods and services are taxed at different rates as per the categories defined by the Indian Government. Various tax slabs are 0%, 5%, 12%, 18% and 28%. There is a special rate of 0.25% on rough precious and semi-precious stones and 3% on gold. In addition to this, a CESS of 22% on top of 28% GST applies to luxury items like aerated drinks, luxury cars, and tobacco products.
GST replaced other indirect taxes and is thus set to dramatically reshape the country's 2.274 trillion-dollar economy. GST registration is compulsory for all businesses involved in the buying/selling of products or providing services or both within India.
The owner of a basic mill must get a Shop License or a Shop and Establishment License from the authorities since both ensure that the rights and interests of those employed are properly protected.
In the event of a flour mill, the proprietor must get a Trade License from the appropriate state's Municipal Corporation. A trade license is a certificate/ document that permits a company to carry on the business or trade activities in a particular municipal limit for which it is issued.
BIS Certification is a way of providing a third-party guarantee of reliability, safety, and quality of products to the customer. The government of India has made BIS certification compulsory for a few products taking into consideration public health & safety and flour is one of them.
BIS CRS Certification is issued in India by the Bureau of Indian Standards. BIS has been successfully promoting and maintaining International standards within the country since 1987. Bureau of Indian Standards is involved in different activities like standards formulation, certification of products, system certifications, hallmarking, laboratory services, registration scheme, and more.
- First and foremost, you must register your flour production business as a legal corporation. The majority of small and medium businesses are organized as a sole proprietorship or a partnership.
- Once you've decided what type of legal company entity you wish to register, you'll need to gather the necessary documents.
- Entrepreneurs must then select a suitable location for their firm and have the necessary equipment installed in order to begin operations.
- You'll also need to hire a lawyer to draught your company's Memorandums and Articles of Association.
- Then, go to the Registrar of Companies or Registrar of Firms and file for incorporation.
- After you've received your Certificate of Incorporation, you'll need to open a bank account for your business.
- After that, you must register for GST and obtain a PAN and TAN for your business.
- After that, you must obtain the necessary trade and food business permits from the FSSAI.
- Companies interested in exporting flour must register with the DGFT and apply for an IEC code.
Private Limited Company Registration
Private Limited Company registration is the legal process of incorporating a company as a private limited entity under the Companies Act, 2013 in India. A Private Limited Company is a type of company that is privately held and has limited liability for its shareholders.
Business Plan
A business plan is an engraved sketch of your business's prospect, a document that describes the step to step process on what a business owner plan to do and how to execute the plan.
Bureau of Indian Standards is involved in different activities like standards formulation, certification of products, system certifications, hallmarking, laboratory services, registration scheme and more
This portion of the site is for informational purposes only. The content is not legal advice. The statements and opinions are the expression of author, not corpseed, and have not been evaluated by corpseed for accuracy, completeness, or changes in the law.
BOOK A FREE CONSULTATION
Get help from an experienced legal adviser. Schedule your consultation at a time that works for you and it's absolutely FREE.
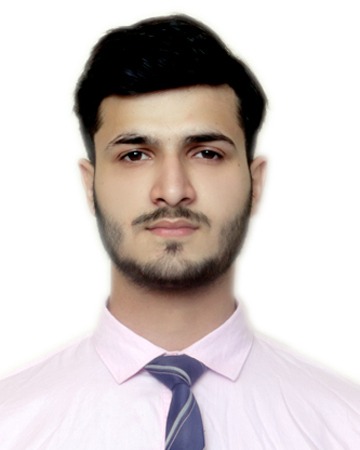
Surbhit Sharma
I have worked for many internet blog pages and news portals. currently, I am working as a content writer for Corpseed Pvt. Ltd. I like to write blogs and articles in the field of different services.
Latest Articles
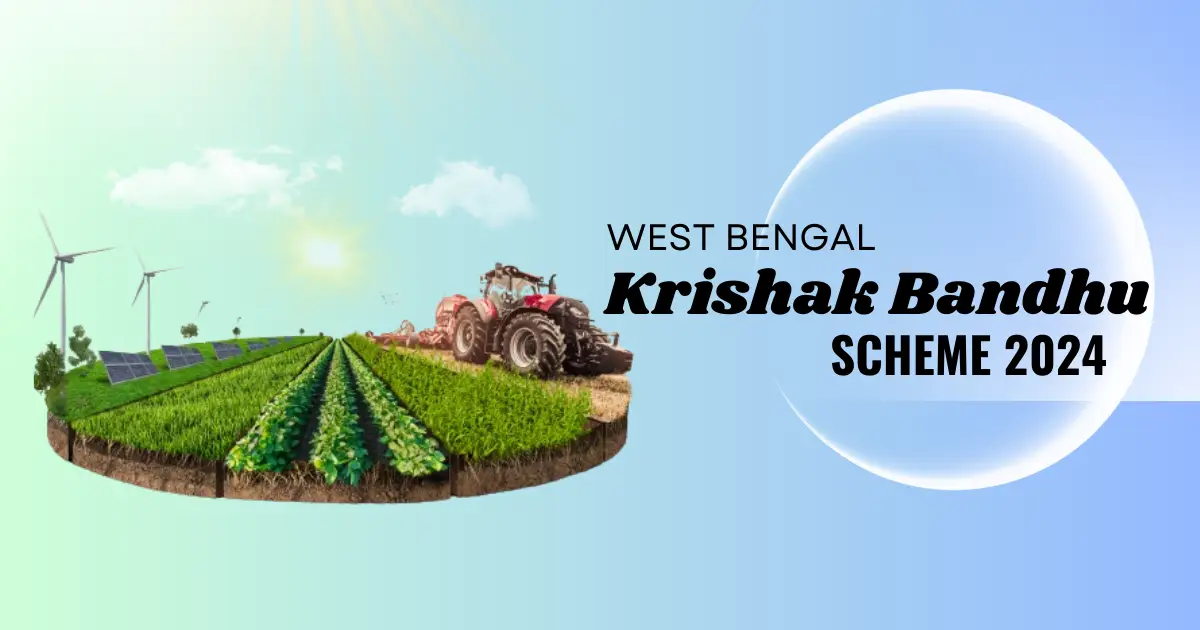
Thank you for your vote! Would you have any suggestions for improvements?
Thanks so much for sharing your experience with us , we hope to see you again soon. .
Business Ideas
Investment Ideas
Make Money at Home
- Bitcoin and Xcoins
- Earn On Social Networking
- Freelancing
- Make a Website
- Money Making Apps
- Affiliate Marketing
- Online Surveys
- Start a Blog
- Web Hosting
Startup Ideas
- Your Passion Your Money
Make Money Online
Flour Mill Business Plan in India: Cost, Profits, License, and Requirements
Table of contents, market for flour mill products in india, production process of flour milling, business model of a flour mill in india, financials of a flour mill business in india, risks and challenges associated with starting a flour mill business in india, flour mill business plan in india, is flour mill profitable in india, how much does it cost to set up a flour mill in india, is an fssai license mandatory for flour mills, how to choose your flour mill machine.
Are you looking to start a flour mill business in India? If so, you’ll need a flour mill business plan. This guide to help you get started. The Indian flour milling industry is highly competitive, with many large and small players vying for market share. Therefore, you’ll need a well-thought-out business plan that gives you a competitive edge. Let’s check out more information about flour mill business plan in India below.

The Flour mill business in India is a highly profitable industry with enormous growth potential. The Indian flour mill market is estimated to be worth Rs. 15,000 crores and is growing at a CAGR of 5%. The market is segmented by type of flour, end-use, distribution channel, and region. There are two types of flour mills in India – small-scale mills and large-scale mills.
The small-scale mills cater to the local market’s needs, while the large-scale mills export their products to other countries. The large-scale flour mills have a capacity of more than 200 tons per day, and they are located mainly in the states of Uttar Pradesh, Punjab, Haryana, Madhya Pradesh, and Maharashtra. The Indian flour mill market is segmented by type of flour as follows: Atta (wheat), Maida (refined wheat), Suji (semolina), Dal flour, and bran.
Atta is the most popular type of flour used in India, accounting for about 60% of the total flour production in India. Maida is primarily used in the bakery industry for making cakes, biscuits, and pastries. Suji is used in making noodles, pasta, and vermicelli. Finally, bran is used as livestock feed. The Indian flour mill market is segmented by end-use: domestic, institutional, and commercial. Domestic consumption accounts for about 85% of India’s total flour demand.
The flour milling process is lengthy and complex, involving several different steps. First, the wheat kernels must be cleaned and separated from other foreign matter. Next, they are crushed and ground into coarse flour, which is then sifted to remove any remaining larger pieces.
In case you missed it: Boat Rental Business Plan: How to Start, Cost, Profit, License, and Requirements

The resulting flour is then milled to a finer consistency before blended with desired additives (such as salt, sugar, or malt) and finally packaged for sale. Depending on the type of flour being produced, the process may vary slightly, but each stage is essential to have a high-quality product.
The business model of a flour mill in India depends on the following factors:
- The cost of raw materials : The cost of wheat or other grains used to produce flour will directly impact the business.
- The price of flour : This is determined by the demand and supply in the market, as well as the quality of the flour.
- The capacity of the mill : A bigger mill will be able to produce more flour and therefore command a higher price.
- The mill’s efficiency will determine how much wheat can be converted into flour and how much profit can be made.
Numerous flour mills in India are helping the country’s economy by providing employment and producing quality flour for the citizens. However, the Indian flour milling industry is highly competitive with many established brands. As a result of this, the competition among the brands is intense, and the government controls the pricing of products. The financials of a flour mill business in India vary depending on the size and scale of operation.
In case you missed it: RV Rental Business Plan: How to Start for Profits, Insurance, and Cost .

The investment required for setting up a small-scale flour mill business can range from Rs. 2 lakhs to 20 lakhs. On the other hand, the costs incurred in setting up a large-scale flour mill business can go up to Rs. 1 crore or more. The profitability of a flour mill business in India depends on several factors, such as the type of wheat used, production capacity, operating efficiencies, marketing strategies, etc. However, a well-managed and efficiently operated flour mill can generate good profits even in a low-margin environment.
Numerous risks and challenges are associated with starting a flour mill business in India. The most significant challenge is the high cost of setting up the business. This is due to the expensive machinery and equipment required for milling. Additionally, the cost of transportation and storage of flour can be pretty high. Other risks and challenges include:
- Theft or vandalism of milling equipment
- Dearth of qualified personnel to operate the mill
- Inadequate supply of raw materials
- Fluctuations in market demand
You should remember a few things when making a flour mill business plan in India. The first is the location of your mill. You want to ensure that you have a good location for your business. There are many different types of flour mills in India, so you must research the different types and choose the one that will be best for your business. The second thing to remember is the type of flour you will be milling. You must ensure that you have a good variety of flours to offer your customers.
In case you missed it: Free Personal Loan Eligibility Calculator – Plan Comprehensively Before Taking Loan

There are different types of wheat and other grains that can be milled, so you need to ensure that you provide various products. The third thing to keep in mind is the price of your product. You must ensure that you are competitive with the other mills in the area. You also need to ensure you charge a fair price for your product. The fourth thing to keep in mind is the marketing of your business. Make sure that you have a good marketing strategy so that people will know about your business and what you have to offer them.
Here are important points to remember:
- Know your target market. To whom will you be selling your flour? What are their needs and wants?
- Research the competition. What are they doing right? What are they doing wrong? How can you do better?
- Choose the correct location. Your mill should be close to your target market and have good transportation access.
- Invest in the best equipment. You’ll need high-quality machinery to produce quality flour.
- Create a strong marketing strategy. How will you let people know about your flour mill? Make sure you have a plan for getting the word out.
- Have a solid financial plan. This is critical for any business but is especially important.
There are key factors to consider when determining if a flour mill is profitable in India. The first factor is the cost of wheat. Wheat prices can fluctuate greatly, so keeping an eye on the market is essential. The second factor is the cost of labor. Labor costs in India are relatively low, so that a flour mill can be profitable even with a small staff. The third factor is the cost of transportation.
Because India is such a large country, transportation costs can be high. The fourth factor is the price of flour. Flour prices also fluctuate but tend to be more stable than wheat prices. Assuming all other costs remain constant, a flour mill will be most profitable when wheat prices are low, and flour prices are high. Conversely, a flour mill will be least profitable when wheat prices are high, and flour prices are low. Therefore, it is important to watch both wheat and flour prices when deciding whether or not to operate a flour mill in India.
In case you missed it: Dog Breeding Business Plan in India: Requirements, Cost, Profit, and License

Setting up a flour mill in India is a relatively easy task. You can easily find a large number of flour mills in the country. However, it is key to select the right one for your business. Here are some tips and ideas that can help you select the best flour mill for your business:
- Do your research : It is essential to do your research before selecting a flour mill. You should consider various factors such as price, quality, reputation, customer service, etc.
- Consider your needs : Before selecting a flour mill, you should consider your specific needs and requirements. This will help you choose the suitable flour mill for your business.
- Compare prices: Once you have shortlisted some potential options, you should compare the prices of each option. This will help you get the best deal possible.
- Check reviews : It is always helpful to check online reviews before purchasing. This will give you some kind of an idea about the quality of the product and the company’s customer service.
The FSSAI license is not mandatory for flour mill business in India, but it is highly recommended. The license ensures that the flour mill adheres to food safety and quality standards set by India’s Food Safety and Standards Authority. It also gives the customers a sense of assurance that the product they are buying is safe and of good quality.
There are several different types of flour mill machines available on the market today. Each type of machine has its own unique set of features and benefits. Choosing the suitable flour mill machine for your business can be daunting. However, there are certain things you should keep in mind when selecting a flour mill machine for your business:
In case you missed it: Herbal Soap Manufacturing Business Plan: Steps, Cost, Benefits, and Equipment

- The wheat you will be grinding : There are two main types of wheat, hard wheat, and soft wheat. Hard wheat is typically used to make bread, while soft wheat is used to make pastry and cakes. Depending on the wheat you will be grinding, you will need to choose a flour mill machine designed for that specific type of wheat.
- The capacity of the flour mill machine: Another important consideration when choosing a flour mill machine is the capacity of the machine. Select a machine that can accommodate the grain you plan to process.
- The flour mill machine’s price is always important when purchasing equipment. Make sure to compare prices from different suppliers before making your final decision.
Opening a flour mill in India is a great business idea. Not only will you be able to serve the needs of your local community, but you’ll also be able to tap into the massive demand for flour from all over the country. With some planning and research, you can set up a successful flour milling business that will provide you with a steady income for years.
Handicraft Making at Home: A Small Profitable Business Idea
Pet-tech startups: innovations for animal lovers, tech repair services: meeting the demand for gadget maintenance, maximizing rewards: smart credit card habits for cashback and points, ultimate guide to making money from goat milk business, how to start an agricultural value added product business.
- Value-Added Business Ideas for Greenhouse: The Best Ways to Make Profits with Greenhouse Farming
How to Make Profits with Organic Country Chicken: Best Strategies for Beginners
10 value-added business ideas for millets: low-investment and highly profitable, why cleaning service business becoming more profitable in metro cities in india, 10 best businesses to start in ayodhya for profits, top drone business ideas in india: unlocking aerial innovation & opportunities, top 10 service businesses you can start with no money, ultimate guide to starting a home-based advertising agency business.
- Starting a Nail Salon Near Your Location: Check List, Business Plan, Licensing, and Opening Instructions
Construction Company Name Ideas: Guide to Create New Construction Company Names
8 best small businesses to start in hyderabad: low-cost and profitable, 10 best small businesses to start in massachusetts: low-cost and profitable, 10 best small businesses to start in maryland: low-investment and profitable, 10 best small businesses to start in delaware: low-investment and profitable.
- 10 Best Small Businesses to Start in Connecticut: Low-Investment and Profitable
- Top 10 Best Online Pet Business Ideas: Exploring Cats to Dogs
- 10 Best Small Businesses to Start in Colorado: Low-Investment and Profitable
- Top 10 Profitable Small Business Ideas in California: Low-Investment Tips
- From Little Rock to Fayetteville: Top 10 Profitable Small Business Ideas in Arkansas
- Top 10 Profitable Small Business Ideas in Alabama: Discover Opportunities in Alabama’s Growing Cities
- Top 10 Profitable Small Business Ideas in Arizona: Discover Opportunities in Arizona’s Growing Cities
- Golf Business Ideas: Exploring Golf Course Money Making Ideas
- Low Capital Profitable Small Farm Ideas: Farming Ideas to Make Money
- How to Write a Business Plan for Daycare: Exploring from Financial Projections to Risk Management
- Home Daycare License Requirements: Exploring State-wise In-home Daycare Requirements
- How Profitable is Day Care Business: How Much Does a Daycare Owner Make a Month or Year?
- How to Open a Daycare Center in Toronto, Canada: Business Plan, Licenses and Permits
- How to Start Meal Prep and Delivery Services: A Popular Business Idea
- How to Start a Milk Chilling Plant Business
- How to Start Coconut Shell Charcoal Business: Business Plan for Maximizing Profits
LEAVE A REPLY Cancel reply
Save my name and email in this browser for the next time I comment.
Value-Added Business Ideas for Greenhouse: The Best Ways to Make Profits with...
Starting a nail salon near your location: check list, business plan, licensing,..., ideas to make money in india – a full guide, mudra yojana loan scheme, eligibility, how to apply, profit in dry fruit business (cost to start), how to make money from rice mill business in india, profitable agriculture business ideas in india, government loans for women entrepreneurs in india.
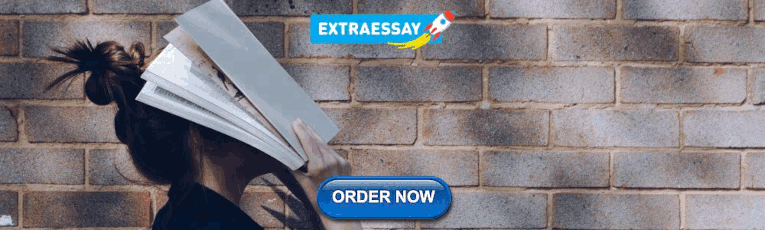
IMAGES
VIDEO
COMMENTS
Cost for hiring Business Consultant - $2,500. Insurance (general liability, workers' compensation and property casualty) coverage at a total premium - $2,400. Cost for payment of rent for 12 month at $1.76 per square feet in the total amount of $105,600. Cost for construction of a standard wheat flour mill - $100,000.
Flour Mill project Business Plan - Free download as Word Doc (.doc / .docx), PDF File (.pdf), Text File (.txt) or read online for free.
S B A P_ Business plan_V.01. Matrix Consulting_ 101, Durga apartments, Rajbhavan Road, Hyderabad 0 9989 040404 7. while rinsing it in a bowl of water. The starch falls out of the dough and sinks to the bottom of the bowl, leaving behind a ball of gluten. Background of Wheat in India.
Business Plan for Flour Mill Plant - Free download as Word Doc (.doc), PDF File (.pdf), Text File (.txt) or read online for free.
Mozambique has built a post-war economy with one of the highest growth rates in Africa. From 2003-2008, the country experienced an average annual growth rate of approximately 8%, with projections for 2009 at 4% to 4.5%.1 Nonetheless, Mozambique continues to experience extremely high levels of poverty.
BUSINESS PLAN FOR LOREL FLOUR MILL This business plan is written to start the production of yam flour by LOREL Flour Mill Plc. This cover page provides the contents of the business plan. Name of Business: LOREL Flour Mill Plc Type of business: Yam flour production Location of Business (Factory): No 15, Akinyele Street, Moniya, Ibadan. Oyo State.
To achieve total revenues of R34,383,900 in 2011/12 (Super Maize Meal accounting for R29,127,600) increasing to R 73,663,759 in 2015/2016. To improve net realisations by +3% in Years 1-3 and +5% in Years 4-5 of the Plan. To achieve an Operating Profit (PBIT) of R 1,637,189 in Year 1 and R 8,755,719 in Year 5 of the Plan.
This is a sample business plan for a flour mill business based in Nigeria. The sample business name of the flour mill is Kachi Mills. The flour mill is based in Lagos state and produces yam flour, wheat flour and corn flour. This business plan outline used follows a standard business summary template and is usable for applying for loans, grants ...
Here's a step-by-step guide to help you navigate the process of establishing a successful flour milling business: 1. Conduct Market Research. Identify the target market by determining the demand for flour in your target market. Consider factors such as population size, dietary habits, and the presence of competitors. 2.
A business plan proposal to establish and operate a flour mill in Arsi zone in Oromia - Free download as Word Doc (.doc / .docx), PDF File (.pdf), Text File (.txt) or read online for free.
Here is a sample business plan for starting a flour mill. I will go straight to the point that is, the business plan sample because it is expected that you already know the basics of the business, the requirements and skills since you are about to start it. BUSINESS NAME: Sammy Jay Wheat Flour Production Company.
Flour Mill Business Plan Executive Summary. As the word suggests, it should be an 'executive' summary of your business. The key points of your atta chakki business plan should find a place here. The sales, the goal, action items and more. You need to remember that your business plan plays a dual role. It will help you incur funds from banks ...
If you are planning to start a small flour mill business, you will need about 50,000 to 60,000 Ethiopian Birr. A large wheat flour mill will cost around 140,000 Ethiopian birr or more, with a variable ceiling. It also depends on the type of flour mill machine required for the business and the complexity of the wheat milling process .
India's packaged wheat flour market is rising by almost 21% at a whooping CAGR . If the growth trend stays the same, by the end of the current fiscal year (2020-21) itself, the market could be likely to hit a new height of Rs 20,000 Cr. The numerous micro- and macroeconomic variables pave the way for the growth of the market.
How To Download The Full Wheat Flour Mill Business Plan Template PDF (with financial analysis) Above is a part of the wheat flour mill business plan template in Nigerian. IF you need the complete business plan, follow the procedures to download it. Pay the sum of N8000 (eight thousand naira only) to the account detail below: Bank: GTBank
Furthermore, the Sole Proprietorship Firm is the best business structure for starting a Basic Mill. However, the finest type of business format for starting a flour manufacturing company in India is a Private Limited Company Registration. FSSAI License. A Flour Mill or Atta Chakki business is classified as a food business in India.
2. Career Point Cares INTRODUCTION • This project includes the survey of the village (Gandi Phali) and draft the Business plan according to the resources available in the village and using the human resource of the village, if possible. • Whether the proposed business is suitable according to the environment of the area and the resources is available or not and everything is in favorable ...
Abrham Flour Mill Project b.plan - Free download as Word Doc (.doc / .docx), PDF File (.pdf), Text File (.txt) or read online for free. project
The cost of raw materials: The cost of wheat or other grains used to produce flour will directly impact the business.; The price of flour: This is determined by the demand and supply in the market, as well as the quality of the flour.; The capacity of the mill: A bigger mill will be able to produce more flour and therefore command a higher price.; The mill's efficiency will determine how ...
flour factory_proposal_study11 - Free download as Word Doc (.doc / .docx), PDF File (.pdf), Text File (.txt) or read online for free. 1. The document proposes establishing a wheat flour factory in Ethiopia with a capacity to produce 85,000 quintals annually. 2. The total investment cost is 10,080,009.80 ETB and will create 92 jobs. 3. The flour will be sold locally and in surrounding areas to ...
e AG (%) - 7 - - Wheat Flour Commodity Study, March, 2009 As per the business plan submitted by the promoter report; the company has created employment opportunity about 16 employees at varies level of the project activity. Of these, about 15 are skilled and semi skilled while the rest are non skilled employees. 7.
Wheat Flour Bussines Plan 2 - Free download as Word Doc (.doc), PDF File (.pdf), Text File (.txt) or read online for free. This business plan is submitted by PAKANA Food Processing PLC to the Ethiopian Competitiveness Facility (ECF) grant support program. PAKANA produces blended food products in Bishoftu and seeks to enhance efficiency and productivity through capacity development activities ...