07912631891

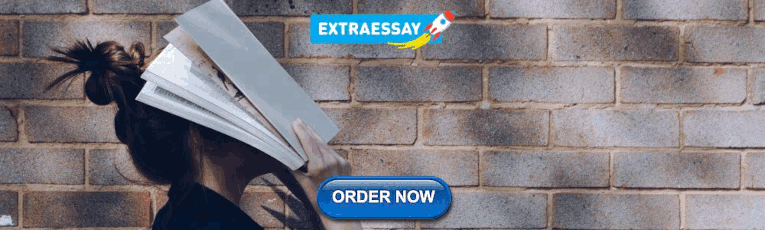
The Problem Solving Power of CAD Design

With the ever evolving landscape of design and engineering, Computer Aided Design (CAD) has emerged as a dominant force, moulding the way we conceptualise and solve complex problems. This blog dives into the overwhelming impact of CAD, both in 2D and 3D realms, resolving the intricacies of its problem solving abilities and exploring its real world applications.
The Evolution of CAD Design
CAD Design has undertaken an astonishing journey over the years. From rudimentary 2D sketches to detailed complex 3D models, CAD has continually evolved. Embracing technological advancements to keep pushing against the boundaries of creativity and innovation.
The Power of Problem Solving Using CAD
At the heart of all innovation lies a solution to a problem. In the area of engineering design, this challenge often involves intricate solutions that are not always visible in your mind’s eye. At its centre, CAD is a tool that provides problem solving super powers. This complex tool empowers our design engineers to visualise, analyse and refine their ideas in a virtual environment.
One of the most potent aspects of the CAD Design process is its ability to bring concepts to life in a virtual environment. In a traditional design process translating mental images into tangible prototypes was a formidable task. CAD has reduced this barrier by providing our engineers with a digital canvas to work from where ideas can be tried and tested before manufacture. Using this technique we can explore diverse concepts effortlessly.
Understanding 2D CAD Design
2D CAD design involves creating detailed flat drawings showing the dimensions and specifications of a component or assembly. Depending on the application, this is a foundational step in the design process, providing a clear blueprint for further development of the product.
2D CAD provides a digital drawing board for design engineers to meticulously plan and analyse their concepts. The simplicity and precision lay the groundwork for more complex 3D models ensuring a smoother process for problem solving endeavours.
The key software that Twenty20 Engineering uses for 2D CAD are, AutoCAD and Draftsight. We also use the 2D draughting tools within SolidWorks and SMAP3D, depending on the nature of the project and industry sector.
What Are The Benefits Of 2D CAD Design?
There are several key benefits to 2D CAD Design.
- Precision and Accuracy
- Speed and Efficiency
- Cost reduction
- Easy Collaboration & Communication
What Are The Real-World Applications For 2D CAD Design?
There are several key industries that use 2D CAD design for their product and applications, these include:
- Architectural Planning and Design – Architects harness 2D CAD extensively to create precise floor plans, elevations and blueprints, to aid them with their planning application process.
- Electrical and Electronics Design – In the electrical engineering sector, 2D CAD is indispensable. It is used to design and create circuit diagrams, schematics and wiring layouts, ensuring the seamless integration of systems and components.
- Building Services & Industrial Plant Design – All (MEP) Mechanical, Electrical and Plumbing design work for new buildings will be carried out in 2D CAD to create accurate and reliable PID drawings to be used for installation and maintenance of building services.
- Mechanical Engineering – Twenty20 Engineering’s design engineers use the 2D draughting tools within Solidworks and SMAP3D to create detailed part, assembly and fabrication drawings for our projects.
Transitioning To 3D CAD Design
What is 3d cad design.
Three dimensional CAD provides realistic virtual models that increase the power of our design engineers problem solving abilities. 3D models represent the physical attributes of objects and structures, providing a comprehensive view of their form and function.
What Is The Advantage Of 3D CAD Design?
The design team can immerse itself in the virtual 3D realm allowing better visualisation of the components and assemblies that make up a project. The 3D environment makes it easier to solve design problems and helps to identify manufacturing issues and streamline the design process. For example, the complex relationship between multiple parts can be explored and refined, avoiding unforeseen component clashes and misaligned holes.
Twenty20 Engineering makes use of several types of software that utilise 3D CAD. Depending on the project requirements and industry sector we use the following:
- Tekla Structures – For all structural steel detailing projects
- SolidWorks – For all fabrication projects (not requiring structural steel)
- SMAP3D – for all MEP / PID projects
What Are The Benefits Of 3D CAD Design?
There are several key benefits to 3D CAD Design including:
- Realistic Visualisation – all components of a project, large and small can be viewed as they would be in the real world
- Enhanced Collaboration – 3D CAD enhances the collaboration between the different stakeholders of a project, for example, the relationship between different assemblies, designed by 2 different teams to go on a new car.
- Simulation and Analysis – Simulation Tools integrated into the 3D software packages enable our engineers to optimise the design of our products
- Rapid Prototyping – the CAD model can be easily transformed into a working prototype, using 3D Printing Technology.
What Are The Real-World Applications For 3D CAD?
There are several industries that make use of 3D CAD for their projects
- Product Design and Development – in the sector of product design 3D CAD is supreme. Designers create detailed and accurate 3D Models of products and appliances, iterating and optimising the design as they go. This is achieved by running real world simulations and user feedback, helping to develop innovative and user friendly products.
- Aerospace and Automotive Industries – the aerospace and automotive industries rely heavily on 3D CAD for the design of all aspects of the aeroplane or vehicle. 3D CAD is not just used to design the car but also for tooling design for injection moulding or press forming for example.
- Medical and Health Care Sectors – in the medical sector 3D CAD has been a game changer. Medical devices, implants and even human organ models have been created. 3D CAD has been instrumental in developing lifesaving medical machines and alleviating the suffering of thousands who need joint replacement surgery.
- Construction – 3D CAD has fundamentally improved construction times on major infrastructure projects, allowing for better communication between different trades and designers. For example, clash detection and avoidance between structural steel frames and MEP (Mechanical Electrical and Plumbing) building services.
Integrating 2D and 3D CAD Design
Both 2D and 3D CAD are usually used in some form at different stages of different projects, both have their place and are in dispensable to our design engineers. 2 examples of this are:
- Structural Steel Detailing – Twenty20 Engineering uses Tekla Structures to create a 3D model of the structural steel item, such as a gantry, mezzanine floor or staircase. The model will contain all of the parts, assemblies and connection details. All of this 3D information will be presented in a 2D format for fabrication and installation.
- MEP Design – Twenty20 Engineering uses SMAP3D to produce detailed 2D PID drawings for our MEP projects, before progressing to a 3D CAD Model for pipe routing and clash detection. This enables us to validate our MEP design before progressing with the necessary fabrication and installation drawings.
Combining the best of both worlds with 2D and 3D CAD harnesses the strengths of both systems. 2D CAD provides us with the precision and ease of documentation for a project as 3D CAD offers immersive visualisations, problem solving and analysis. Combining these efforts results in a comprehensive and efficient design process for multi-faceted problems.
In conclusion, the power of 2D and 3D CAD cannot be overstated, it empowers problem solving engineers to be creative and innovative in their solutions. Enabling them to visualise, analyse and optimise their solutions with remarkable precision and accuracy. By continuing to harness the technology designers and engineers can navigate the complexities of the modern world, generating solutions for the future.
As we move forward the integration of AI and machine learning will continue to empower problem solvers, whether by helping to optimise a design solution or by automating repetitive modelling tasks. Increasing the output of future design engineers. Contact our expert engineers to discuss your CAD design requirements today!

The Role of Sheet Metal Fabrication in Modern Engineering

Balancing Creativity and Technology in CAD Design

Sustainability Matters: Eco-Friendly Practices in Engineering

A Behind The Scenes Look At Our CAD Process
3 Ideas for Design Challenges Using a 3D Printer
Thomas schwartz thomasschwartz, news on september 26 2018.

You’ve purchased a 3D printer. You’ve had your students complete tutorials on CAD software. Now what? What’s the best way to built your students’ abilities on the software, and get them ready to create on their own? A great way to begin a 3D printing unit is to start a design challenge using a 3D printer.
Design Challenge 101 (a quick refresher)
A design challenge is an open-ended project that encourages students to ask questions, take the initiative, and think creatively. With a design challenge, teachers can engage students in problem-solving, collaboration, and technology tools – and it encourages a deeper connection to the learning process. Design challenges guide students through the engineering design process . A design challenge is often shaped by specific parameters that students must adhere to (for instance, the final size of the object, or the amount of material being used), and is an excellent tool to expose students to a new way of thinking. Rather than being defined by yes/no answers and strict steps, the engineering design process is flexible, without a specific starting and stopping point, and adapts to the needs of the project.
Three Design Challenges Using a 3D Printer
How do we bring design challenges into the classroom in a way that is relevant for students? Here are three simple ideas for design challenges using a 3D printer that are open-ended, creative, and get your students working hands-on with each other – and the 3D printer.
1. Start with the basics: Custom Keyring
This simple project allows students to creatively express themselves – and engage in the design and printing process – by customizing their own keyring. Students can design and print a keyring with their initials, their favorite sports team, and anything in between. This project encourages students to create an original design, and to think about scale and functionality when they’re designing. Most importantly, this project teaches students the basics of a design challenge and gets them comfortable with how 3D printing works.
2. Put on Your Thinking Cap: Identify a Problem, Create the Solution
A design challenge is the perfect way to engage students in problem-solving. Turn your students into detectives! Have them identify a common problem around your school and then have students create a design to solve it. Most likely, this will come in the form of a simple machine. Door won’t stay open? Create a door stopper. Windows too heavy to lift? Make a lever. Whatever the application, encourage your students to come up with creative ideas that can be printed and tested. The design can be tweaked and reiterated until it solves the problem; this is the engineering design process at work!
3. Master Level: Design a Scale Model
This may be the most difficult of the design challenges presented here. It will test your students’ skills and have them fully engaged in the engineering design process. Designing a scale model is a great way to incorporate Math and Engineering into your 3D printing, as this project will require that students take and convert measurements to ensure that their model is accurate and built to scale. While it may seem nearly impossible to reconstruct something like the White House, students can start with a more simple structure, or perhaps their own house or school building.
We’ve Got Resources!
We hope these ideas help you get the ball rolling with 3D printing in your classroom. If you’re looking for more information around design challenges, check out our Online PD courses or download our eBook “Why 3D Print in the Classroom?” for great info and ideas. Other resources we love for 3D printing project ideas are YouMagine.com and Thingiverse.com .
0 thoughts on “ 3 Ideas for Design Challenges Using a 3D Printer ”
Leave a reply cancel reply.
You must be logged in to post a comment.
Related Articles & Other Recommended Reading

Introducing the iRobot Root By now, iRobot has become a household name that many people will recognize. Maybe you have one of their products in your house right now, such as the Roomba, the robotic vacuum. With just the push of a button, you can program your Roomba to clean at a specific time. It can map out the […]

Elevate Your Teaching with Updates to SMART Notebook SMART Notebook has recently updated to its latest version, 23.1! There are some amazing new features designed for higher-level teaching. SMART’s cloud platform, Lumio has become more popular but, many teachers continue to stick with what they know, which is SMART Notebook. In order to satisfy users who continue to utilize Notebook, SMART has made […]

Thanking Community Helpers with Cricut Reflecting on our lives and what we are thankful for can be a wonderful way to help students practice gratitude and gain new perspectives that can improve their overall mental health. We may choose to think about our homes, families, friends, and other things that we are fortunate to have. These types of exercises can […]
- Higher Education
- ***Blog****
- Customer Stories
- Help Center
- Khamis Studio x Gravity Sketch
We use third party cookies in order to personalise your site experience.
How 3D sketching stimulates a more creative workflow
Designers are spending a lot less time ideating with 2D mediums in favour of working with immersive technology. 3D sketching has enabled a faster and more creative design pipeline. Designers are creating more unique and compelling designs through the use of Gravity Sketch at the early stages of their process.

January 11, 2021

This is the 1st blog in the series where we’ll be looking at the various ways designers are implementing Gravity Sketch into their process. Each blog will focus on one of the four benefits we have identified across all of the designers and design studios we have engaged with over the past year. With this blog we will first focus on how, with project deadlines seeming to tighten throughout the industry and clients demanding ever more, 3D sketching can help designers work more creatively, while maintaining and often shortening the time to delivery. We overwhelmingly hear that designers are under a great deal of pressure to deliver high quality work at dramatically shortened time frames; this is a key theme we picked up on from designers, especially at consultancies. However, with the competitive nature of in-house design studios, this challenge exists there as well and can be felt throughout the industry.
A more efficient workflow preserves time for ideation and the deeper development of concepts which are often left on the table due to time and feasibility constraints. The more concepts developed the stronger end result. In addition to this we have also heard that through 3D sketching designers are able to realise concepts which are extremely challenging to visualize and iterate using traditional industry tools. Sean O’Shea, Anta’s LA Studio Director sums this up well:
“I never realised how limiting drawing in 2D was until I started using Gravity Sketch. The freedom and creativity are clearly the most enjoyable parts for me. Also the end result is shockingly impressive when compared to other 2D programmes I had been using”
We’ll share some insights from users and explain how designers are getting more compelling outcomes by bringing 3D earlier in their design process.

Time pressure on ideation
With several teams we spoke to there is an expectation for designers to produce work at the ideation phase which can be used much further downstream in the development process. Across the industry both clients and various stakeholders are requesting design reviews with digital 3D data at all stages of the pipeline. It appears the inductsy is tightening the design window and as a result, there is very little time left for designers to explore, ideate, and imagine. This reduction of time spent on ideation with pen and paper or digital sketching results in a series of compromises and in turn drastically affects the final outcome. This exploration and imagination phase is starting to become a second class citizen in the pipeline. The larger impact this has had is the transition to CAD, designers are moving into CAD programs much earlier in the process when they are still in the exploration stages. These tools are not fit for purpose, once a designer gets into the digital 3D realm with traditional CAD software, the process becomes more rigid and the ability to iterate becomes much harder due to the time needed to operate the software. These tools fail to capture the fluidity of hand sketching but rather generate seamlessly lifeless proposals.
The current version of Gravity Sketch is designed for this early stage ideation, and enables designers to use their gestural styles to generate 3D sketches and early sketch models in a free-form environment. With a typical onboarding time of only eight hours, the tool combines the fluidity of sketching with a digital 3D output that conveys proportions, volumetric information, and a more accurate iteration of the initial idea. Rather than spending hours behind a computer screen, or sketching multiple 2D views of a product, one 3D sketch/model created with Gravity Sketch captures any desired angle of the design. The 3D data, or screenshots of the model can be shared instantly with external stakeholders or management.
The major advantage of sharing this work as 3D data is the ability for others to visualize the earliest sketches in 3D with 1:1 accuracy, comment in real time, and export like for like to traditional CAD programmes for use later in the pipeline. This increased speed of exploration of ideas allows designers to spend less time stuck behind a computer screen and frees up time to explore multiple ideas. With more time spent concepting, designers unlock a more compelling output and less time on the development of a single compromised concept.

Uncompromised creativity
Design is a competitive sport. Whether it’s in competition with his/her peers or with themselves, designers often look to leverage emerging technology to elevate the quality of their work. Gravity Sketch has provided a new way to iterate on ideas and push designs forward at every stage of the process. Visualizing ideas in 3D in real time helps elevate creativity and eliminates the 2D-3D transition which has been the industry norm for forever. Often designs look great in 2D, but don’t credibly translate into 3D, which causes a lot of back and forth between designers and modelers or engineers; this is especially a challenge for designers who are early on in their journey.
Creating with gestures and free form editing SubDivision geometry in a limitless immersive environment provides an unrestricted experience when it comes to expressing organic forms. Users can better solve aesthetic or usability challenges, in turn making more informed decisions about which ideas to progress. With this method, designers can explore forms that would be difficult to produce with traditional tools.
In no way are designers we spoke with knocking transitional 2D sketching, the medium provides the fastest way of getting an idea out of your brain. However to fully express an idea designers must work through a series of sketches and 2D renders. This ability to immediately understand an idea and fully visualise a design in 3D early helps designers identify challenging areas in their concept. This opens an opportunity to immediately start problem solving in real time as the design is coming into focus.

VR provides a limitless blank canvas to design within, allowing the visualisation of multiple concepts at once in 3D. Create image mood boards, a virtual studio set-up, or copy multiple instances of similar designs to compare closely. The power of this digital setup provides a new way of evaluating concepts at the early stages of the process and empowers designers to create more compelling products.

It’s fantastic to see creatives liberated and free to push their ideas in a new way. We have learned so much from users who have fully integrated Gravity Sketch into their workflow. We aim to increase the potential of the tool in the key areas from above. We also want to unlock unexplored ways of working which this medium supports. The most rewarding part of building this product is seeing the way designers are able to step up their game and work in a totally unrestricted way. If you’re using the tool to elevate the quality of work and depth of creativity we would love to hear about your process.
Get in touch

Evolving Gravity Sketch’s screen creation tools

Capturing Gravity Sketch workflows in augmented reality

Gravity Sketch Student Ambassadors 2022 – 2023

3D Modelling and printing applied to elementary and secondary schools
3d modeling and printing, enhancing creativity and problem-solving skills.
Learn how 3D modeling and printing foster creativity and problem-solving skills among students. By engaging in hands-on design projects, students can unleash their imagination, iterate designs, and develop innovative solutions to real-world problems. This section showcases inspiring examples of how students can bring their ideas to life using 3D modeling and printing.
Accessible Tools and Resources for Schools
Discover user-friendly software, affordable 3D printers, and online platforms that support educators in delivering engaging 3D design projects. Learn about successful case studies where schools have successfully implemented these technologies, and gain insights on how to overcome common challenges associated with 3D modeling and printing in an educational setting.
Integrating 3D Modeling and Printing into the Curriculum
Explore the various ways 3D modeling and printing can be integrated into the curriculum across different subjects. From designing prototypes in science experiments to creating historical artifacts in social studies, these technologies offer interdisciplinary opportunities for students to apply their knowledge and deepen their understanding of various concepts. Discover practical examples and lesson ideas for incorporating 3D modeling and printing into the classroom.
Fostering Collaboration and Future-Ready Skills
How students can work together in teams to design and create 3D-printed projects, promoting communication, teamwork, and problem-solving abilities. Additionally, discover how the skills acquired through 3D modeling and printing, such as digital literacy and design thinking, prepare students for future careers in fields such as engineering, architecture, and product design.
3D Models, Modeling software and 3D Printers
3D printing allows product/industrial designers to create prototypes in a few hours instead of weeks using traditional methods. The cost to create a prototype can exceed €10,000 when we consider the use of tools necessary for processes such as injection molding. with the impression 3D prototypes can be achieved at a fraction of the cost.
Work sessions in the Professional Computer Courses (Secondary)
The workshops that took place within the Professional Computer Science and Computer Courses involved 3 high school classes (see Figure 12 below). Within the scope of these courses the following projects were carried out:
– Development of 3D scenarios for games (with Blender); – Implementation of the Farmbot Control System with RaspberriPy; – Construction of a programmable DIY clock; – Drone construction and programming; – Construction of arcade game console; – Construction of Robot with ultrasonic sensors.
1st vegetable garden set up at the school
During almost the whole day of Friday, all classes of the school participated in the STEAM activities organized by InovLabs. The component of Electronics, Robotics and implementation of sensors in the garden space were the most worked activities in this school. The project “Oeiras Innovation Labs” also supported the activities of the project “Aqui há horta”, and the vegetables produced in the school space allow today to recurrently supply the canteen with fresh vegetables to feed the students.
3D PRINTING MANUAL PDF

Top 10 Problem-Solving Lesson Ideas with Fairy Tales & 3D Design (Worksheets)
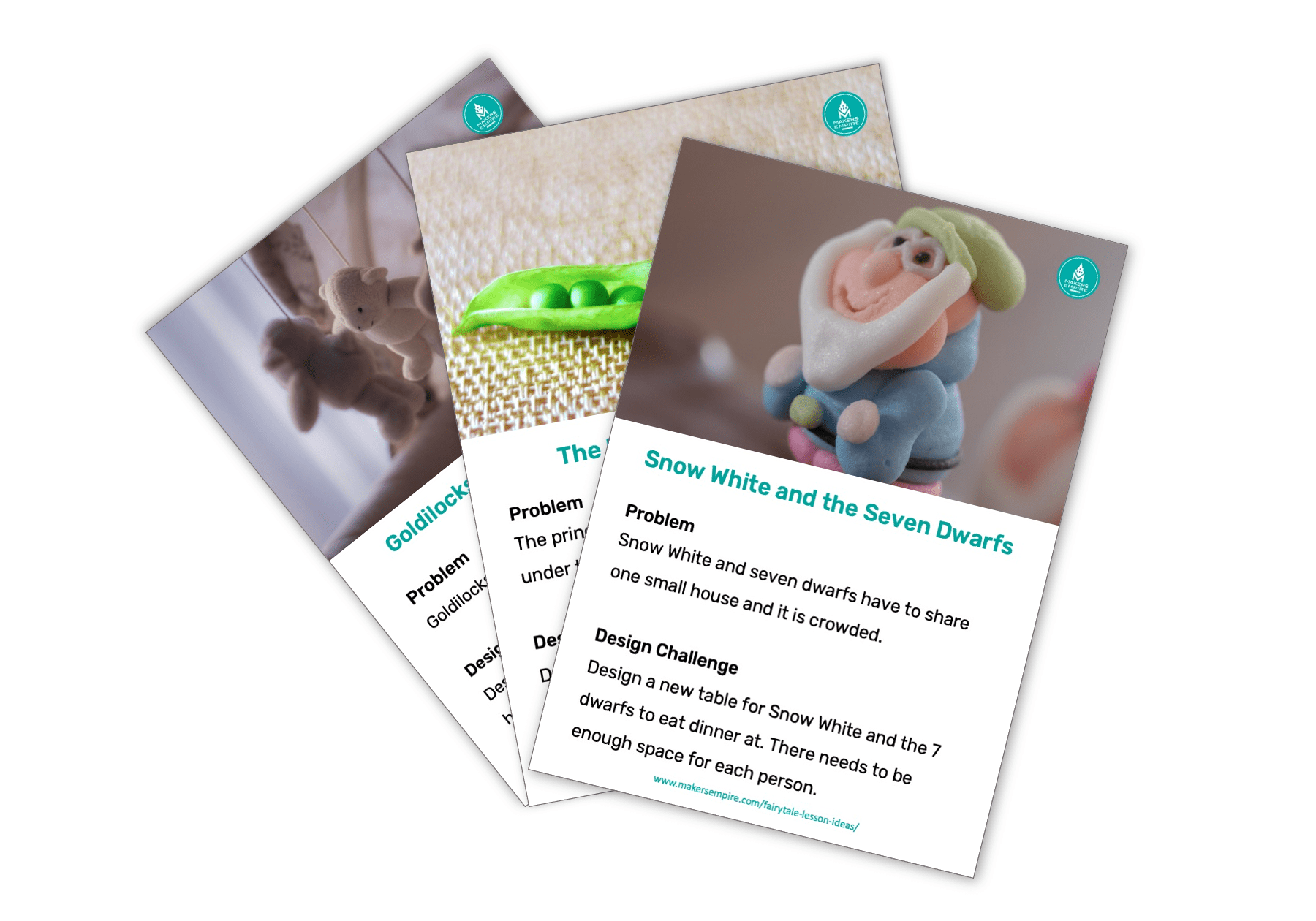
We all love a great story and a happy ending. Fairy tales have both of these elements, and also make great starting points for engaging students in many different learning activities. They can be used to explore the narrative genre and develop writing skills, provide examples of numeracy concepts, and open opportunities to discuss values, morals, and social skills.
Fairy tales can also provide a great context for students to practice creative, critical, and design thinking, and develop STEM skills by identifying and solving problems.
Fairy tales generally present some kind of problem or conflict that the characters try to solve. The characters often make several attempts to solve the problem before they are successful, making them great examples of iterative design thinking and persistence in developing solutions.
In this article I share ten examples of putting Makers Empire together with a fairy tale to make a great problem-solving lesson that requires very little preparation.
These activities are ideal if you have an hour or one lesson a week to devote to Makers Empire. Fairy tales can be used with any age group. These ideas have been written with students in grades K- 4 in mind.
Each example can be implemented using a simple lesson plan structure that can become a consistent routine for students to follow in your STEM lessons.
- Step 1: Read the fairy tale with your class (10 minutes)
- Step 2: Class discussion to identify and define a problem (5 minutes)
- Step 3: Brainstorm possible ideas for solving the problem (5 minutes)
- Step 4: Design a solution for the problem using Makers Empire (30 minutes)
- Step 5: Students share their designed solutions and give each other feedback. (10 minutes)
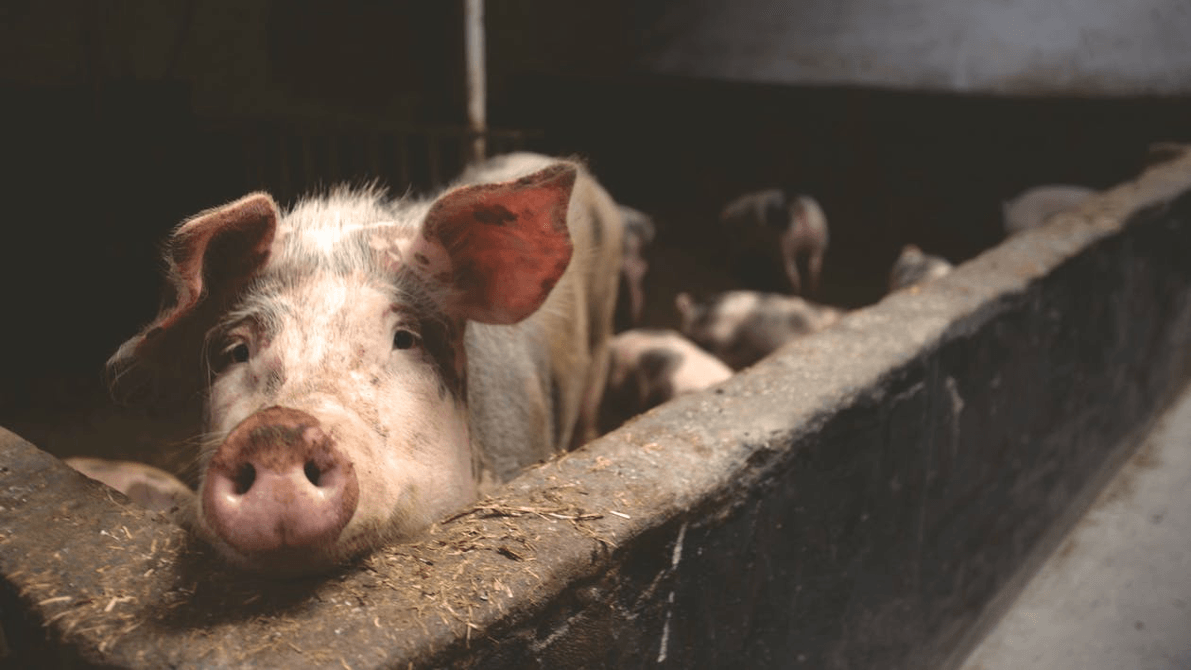
Fairy Tale 1: The Three Little Pigs
Problem: The Big Bad Wolf can blow down houses.
Makers Empire Design Challenge: Design a new house for the 3 little pigs to live in. The house needs to be strong so that it can’t be easily blown down.
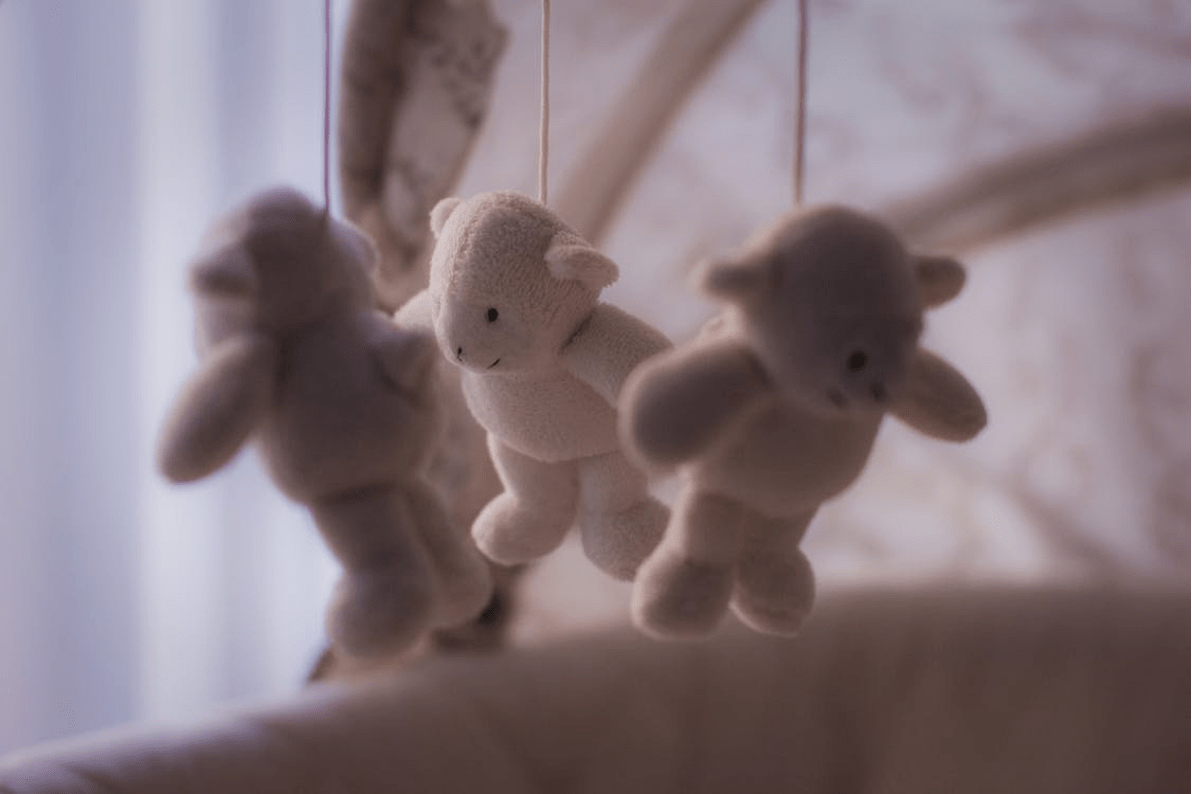
Fairy Tale 2: Goldilocks and the 3 Bears
Problem: Goldilocks has broken Baby Bear’s chair.
Design Challenge: Design a new chair for baby bear. Think about how you can design a chair that won’t break if Goldilocks sits on it again.
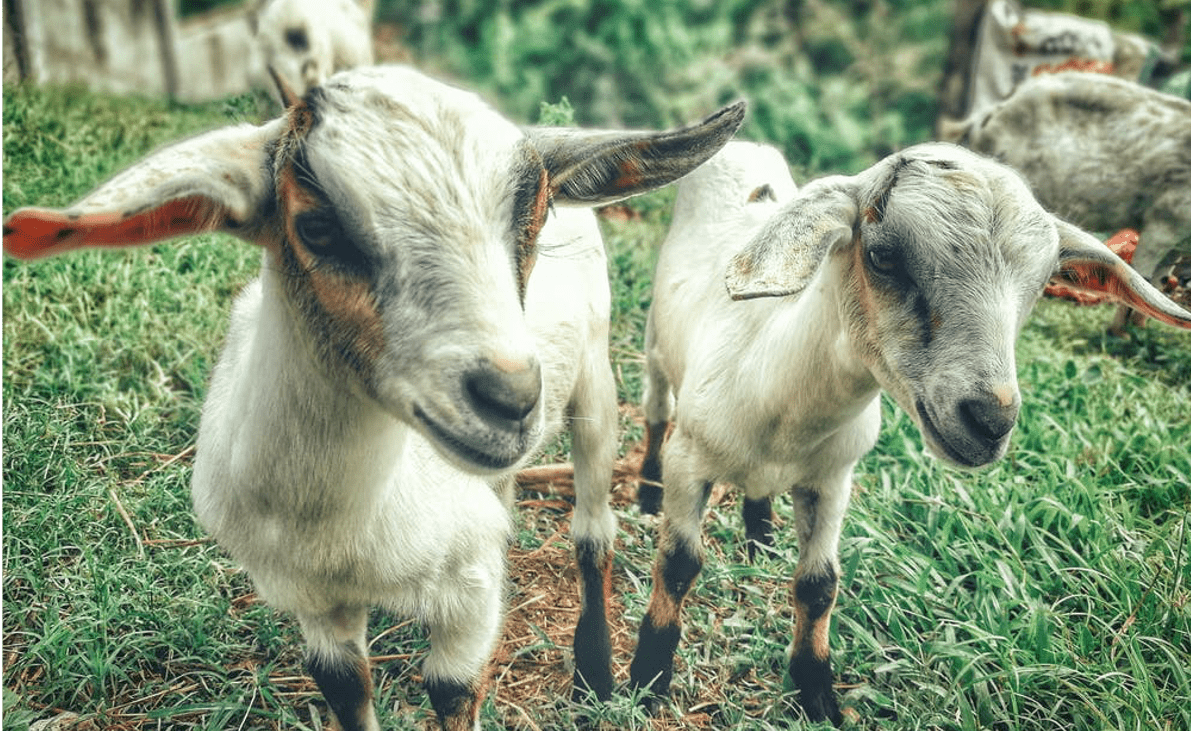
Fairy Tale 3: The 3 Billy Goats Gruff
Problem: The goats cannot cross the bridge because they are scared of the troll who lives underneath it
Design Challenge: Design a new way for the 3 goats to cross the stream to get to the grass on the other side.
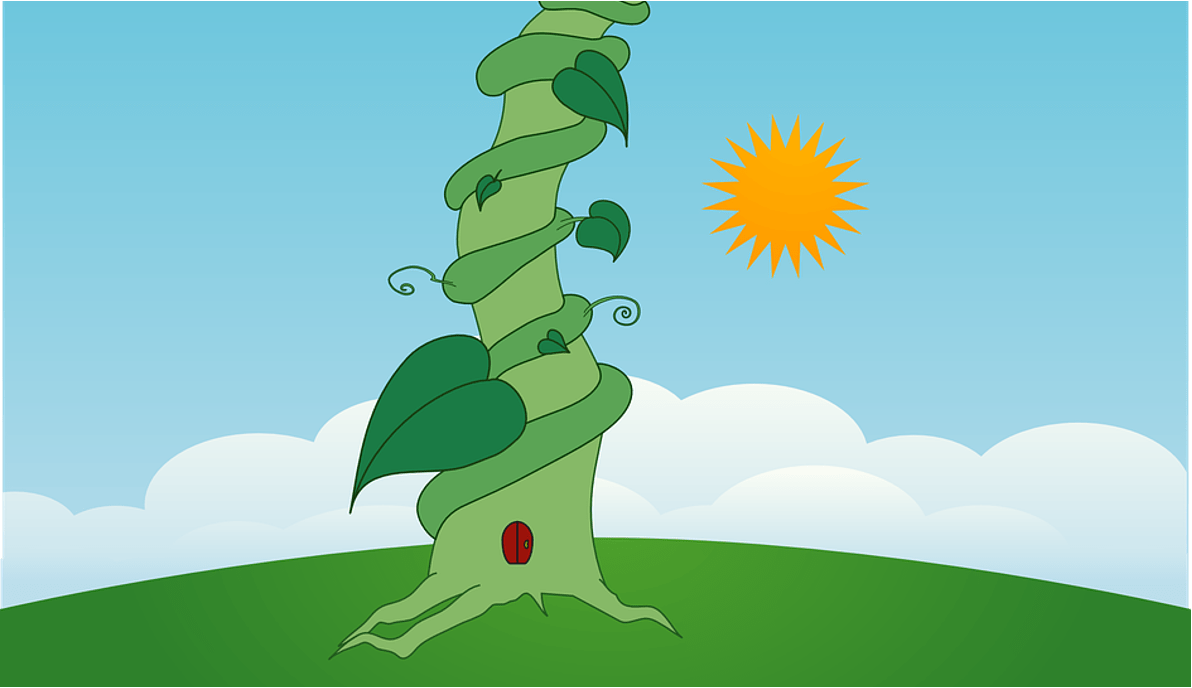
Fairy Tale 4: Jack and the Beanstalk
Problem: The only way to reach the castle is by climbing the beanstalk.
Design Challenge: Design a new way for Jack to reach the castle in the sky. He needs to be able to get to the castle without disturbing the giant.
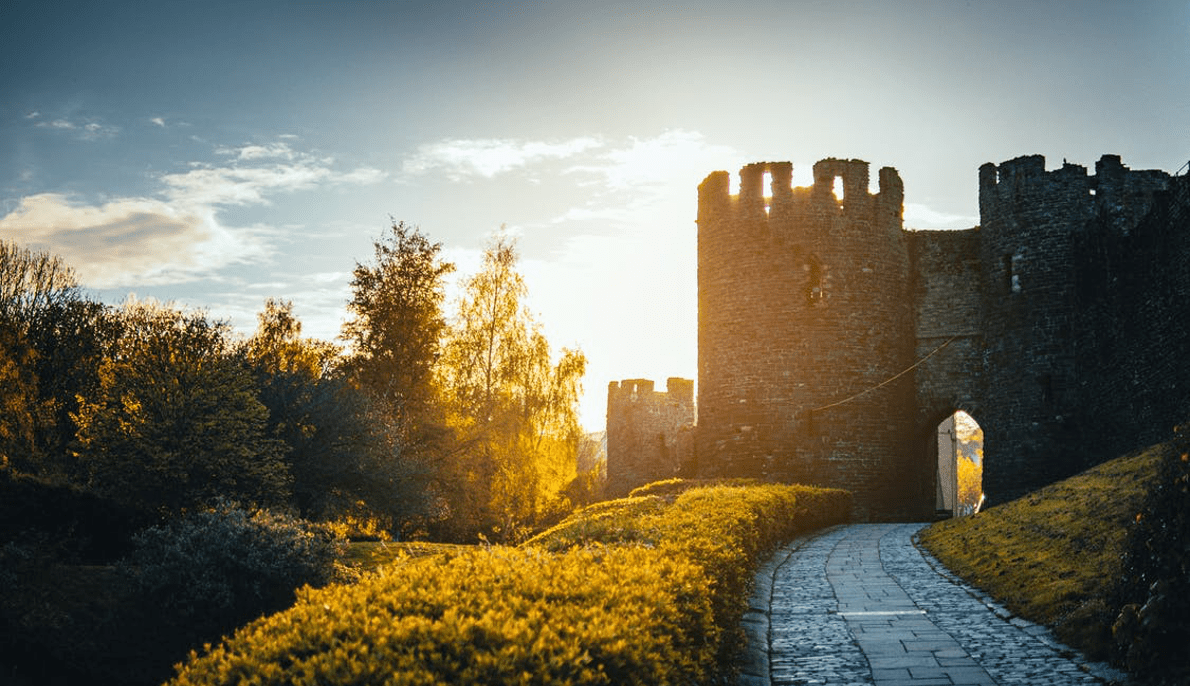
Fairy Tale 5: Rapunzel
Problem: Rapunzel is locked in the castle and can’t get out.
Design Challenge: Design a new castle for Rapunzel. She needs to be able to come and go as she pleases without using her hair as a rope.
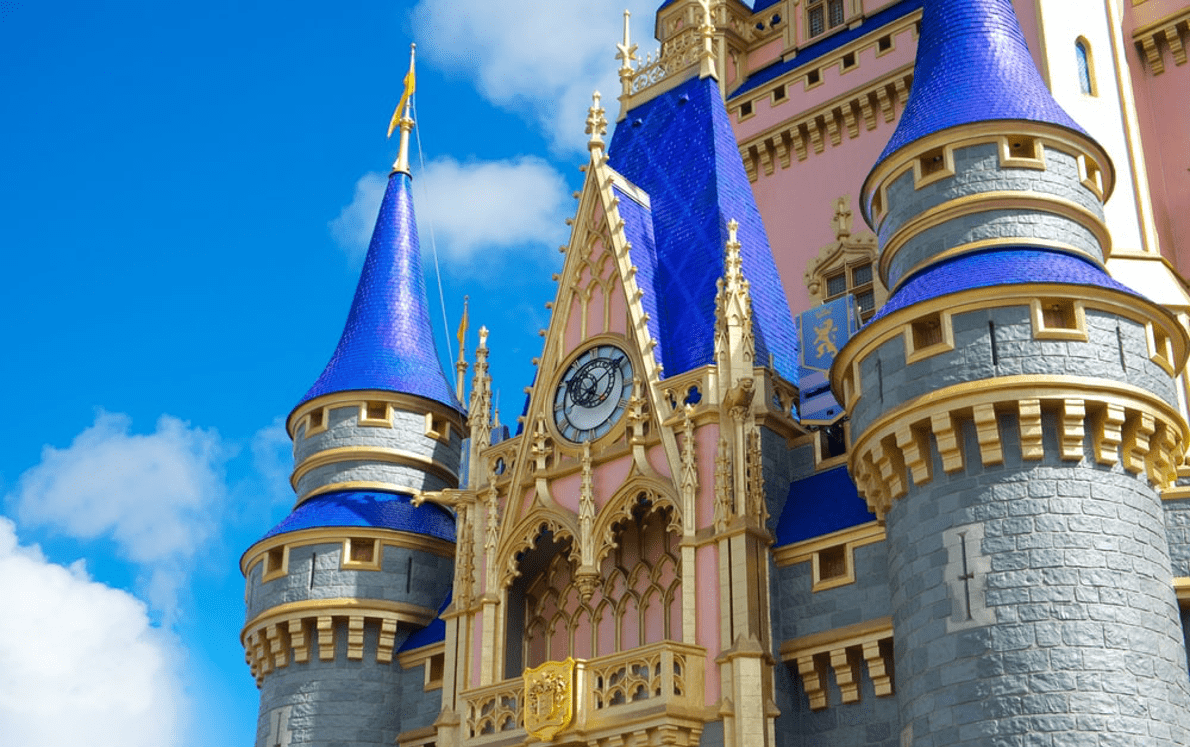
Fairy Tale 6: Cinderella
Problem: Cinderella has lost her glass slipper.
Design Challenge: Design a new pair of shoes for Cinderella. Make sure to design the shoes so that they can’t easily fall off if Cinderella needs to run somewhere in a hurry.
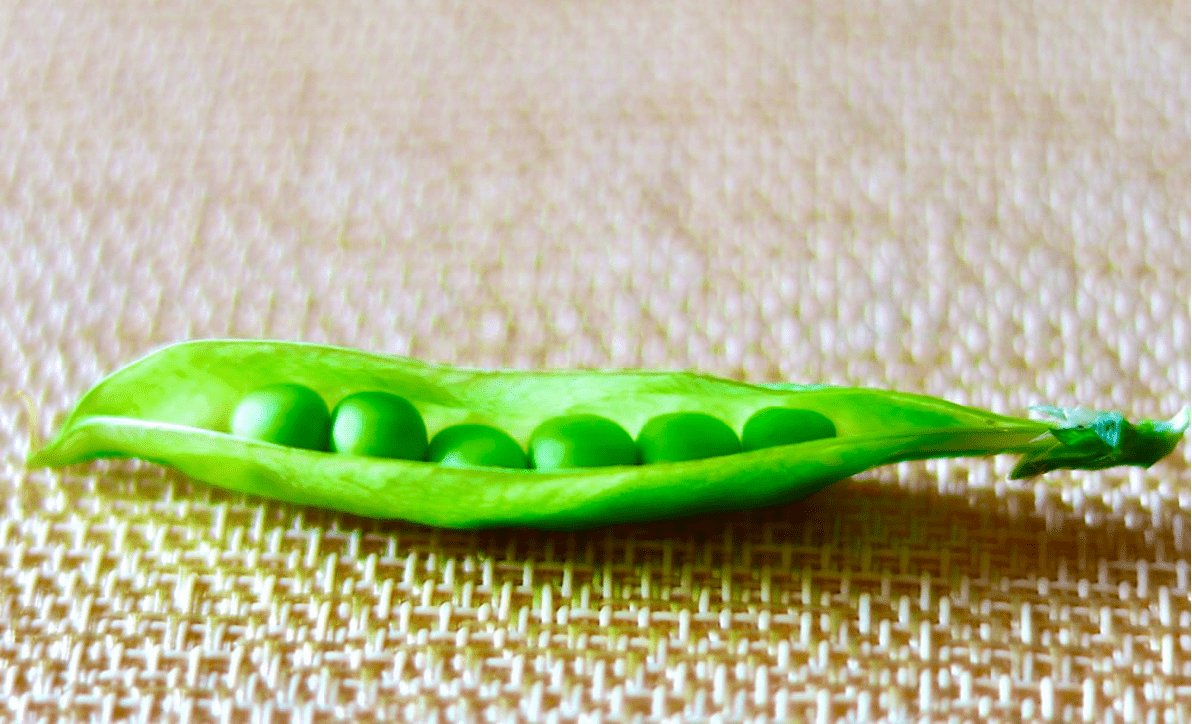
Fairy Tale 7: The Princess & The Pea
Problem: The princess can’t sleep because there is a pea under the mattresses.
Design Challenge: Design a new bed for the princess. Her bed should be comfortable, even if someone hides a pea under the mattress.
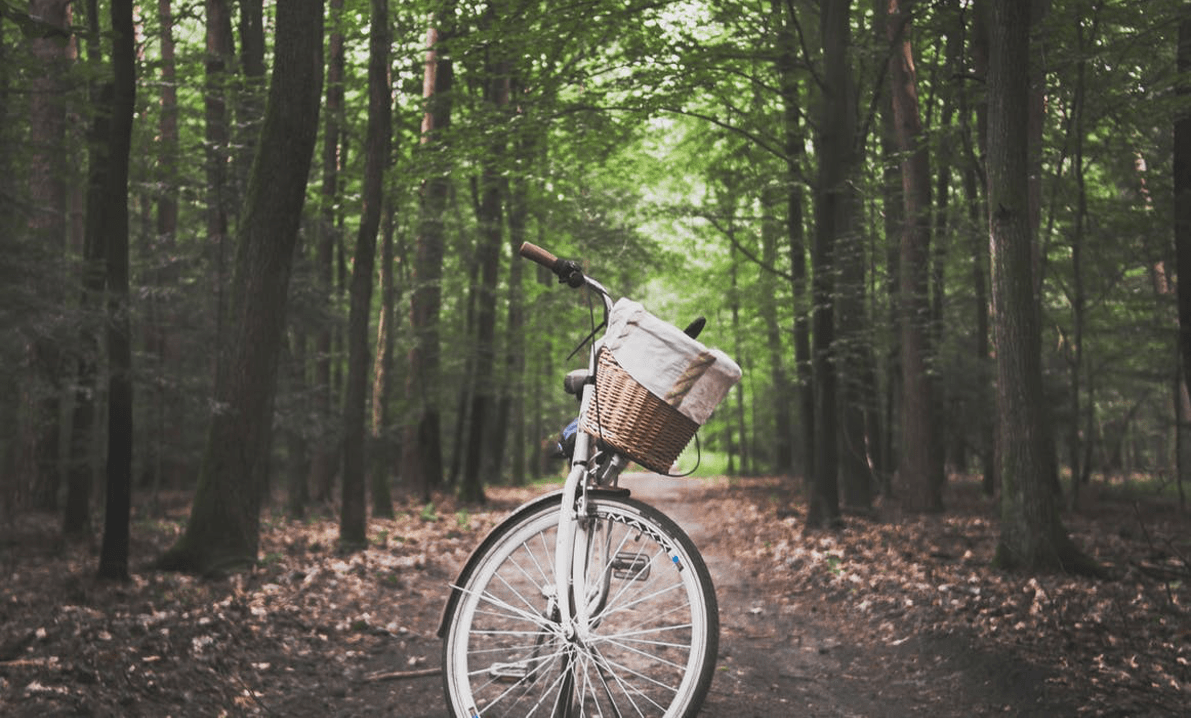
Fairy Tale 8: Little Red Riding Hood
Problem: Little Red Riding Hood is in danger when she tries to deliver food to her sick grandmother.
Design Challenge: Design something Little Red Riding Hood can use to travel easily through the woods carrying her basket.
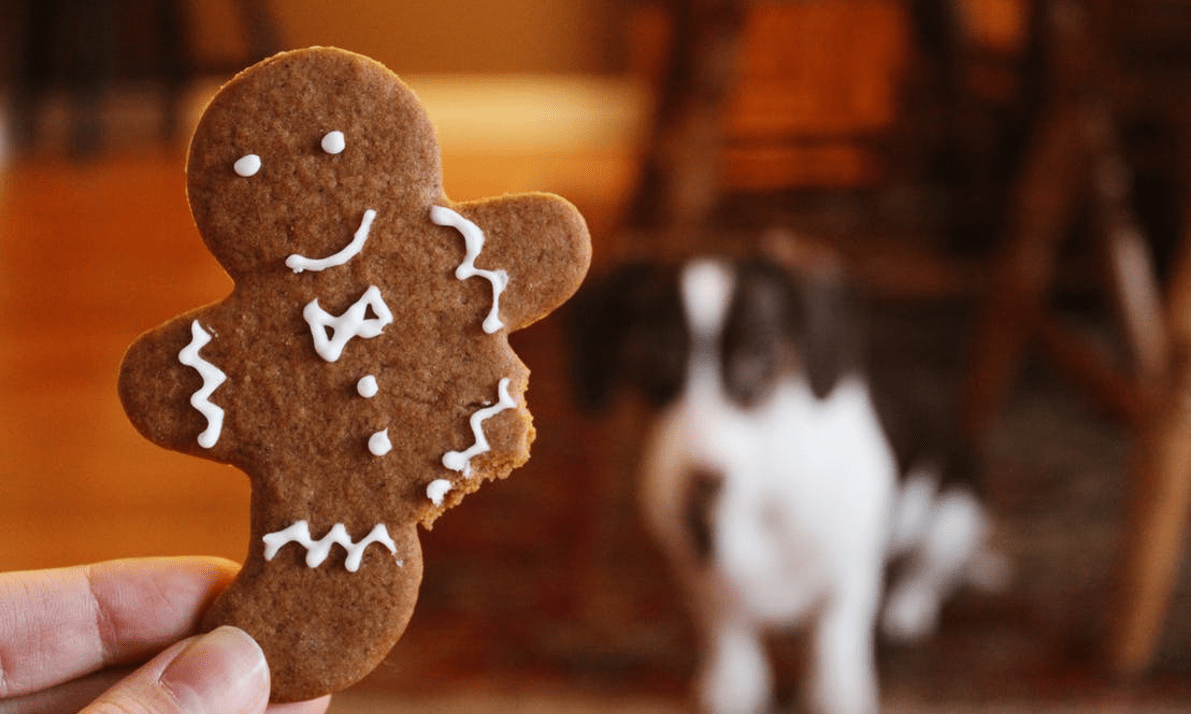
Fairy Tale 9: The Gingerbread Man
Problem: The gingerbread man cannot cross the river because the water will make him soggy and fall apart.
Design Challenge: Design a boat for the gingerbread man. The gingerbread man needs to stay dry and away from the fox while he is in his boat.
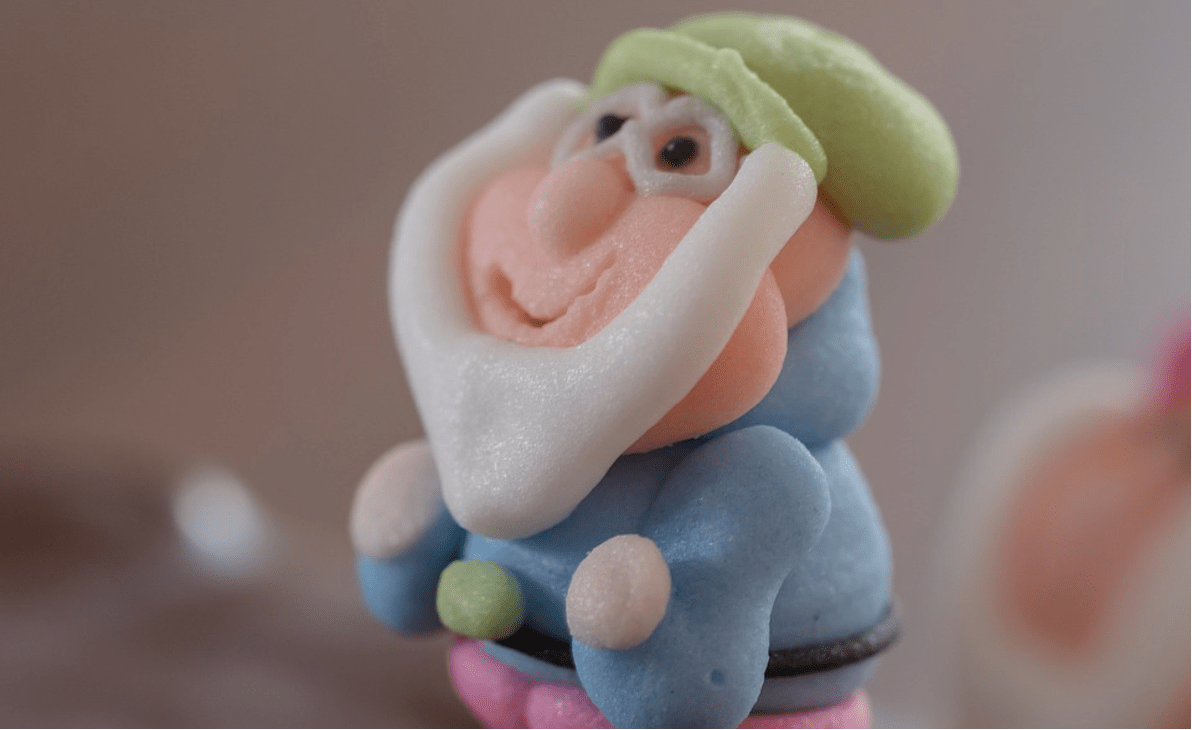
Fairy Tale 10: Snow White & The Seven Dwarfs
Problem: Snow White and seven dwarfs have to share one small house and it is crowded.
Design Challenge: Design a new table for Snow White and the 7 dwarfs to eat dinner at. There needs to be enough space for each person.
Keen to use these lesson ideas with your students? Why not use our downloadable Fairy Tale Lesson Ideas worksheets and our downloadable Design Thinking Cycle worksheets together?
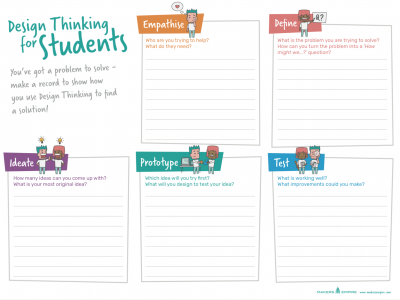
Mandi Dimitriadis
Mandi Dimitriadis, DipT. is the award-winning, highly regarded and passionate Director of Learning at Makers Empire. She is an experienced classroom teacher who recognises the power of technology to enhance teaching and improve educational outcomes. Mandi has extensive experience with curriculum development and learning, having previously developed programs for the Australian Government’s Department of Education, and having created custom curriculum for Makers Empire schools in the USA, China and the UAE. She is passionate about Design Thinking and how best to prepare today’s students for the future.
Share this:

New STEM Publication Calls for a United Effort to Encourage Students to Develop an Interest in STEM
In an era characterised by rapid technological advancements and glo…
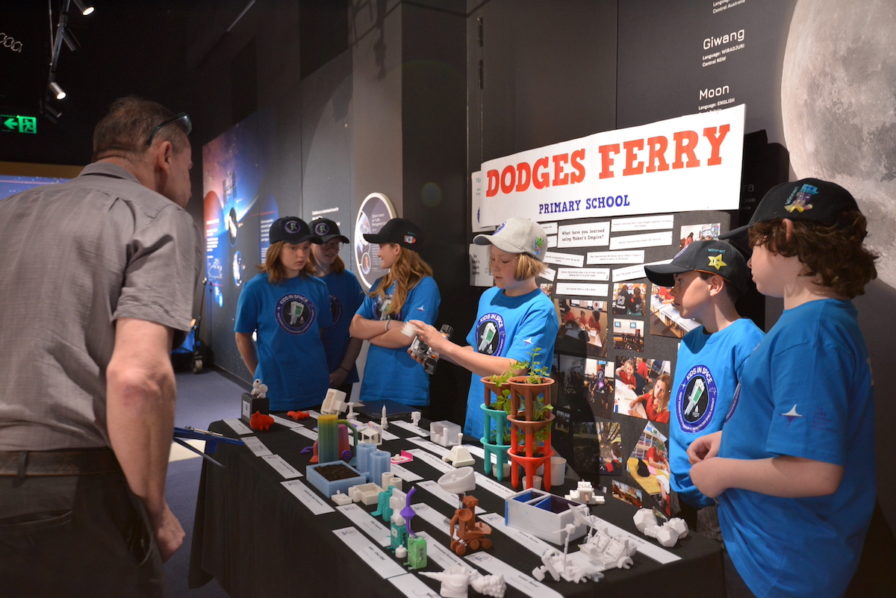
Kids in Space expanding in 2024 to 100+ Schools Across Australia
The Andy Thomas Space Foundation and Makers Empire are delighted to…
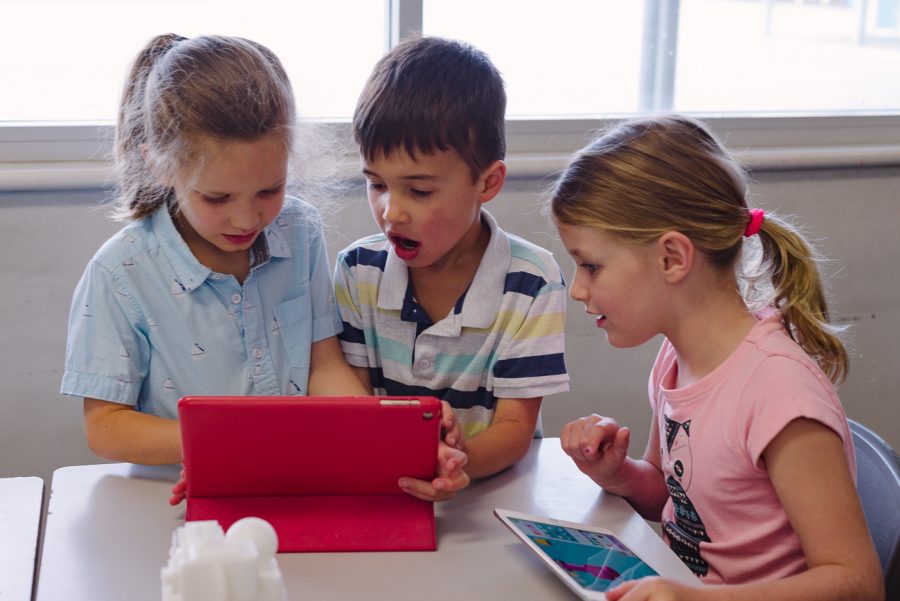
7 Ways Makers Empire Supports Neuro Affirming Learning for Students With Varying Support Needs
Over the years, Makers Empire has received feedback from teachers i…
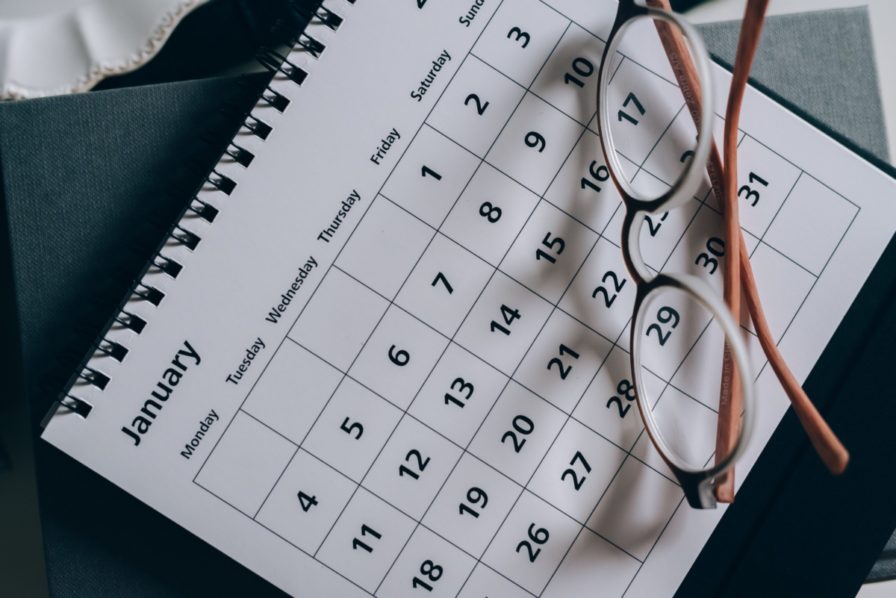
2024 Design Thinking 3D Design Competitions Planner
Makers Empire’s in-app, monthly Design Thinking competitions …
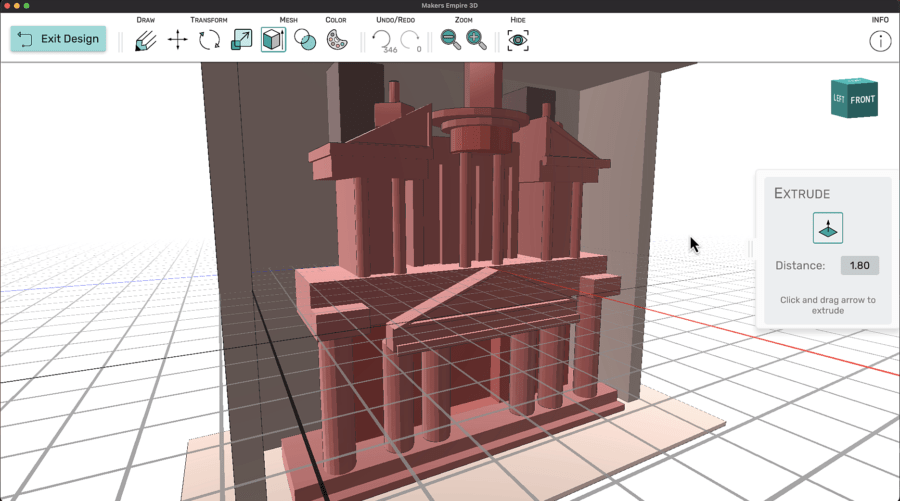
5 Ways To Engage Students in Real-World Problem Solving Across the Curriculum with Makers Empire’s Advanced Module
Students can design in 3D in Makers Empire using one of three desig…
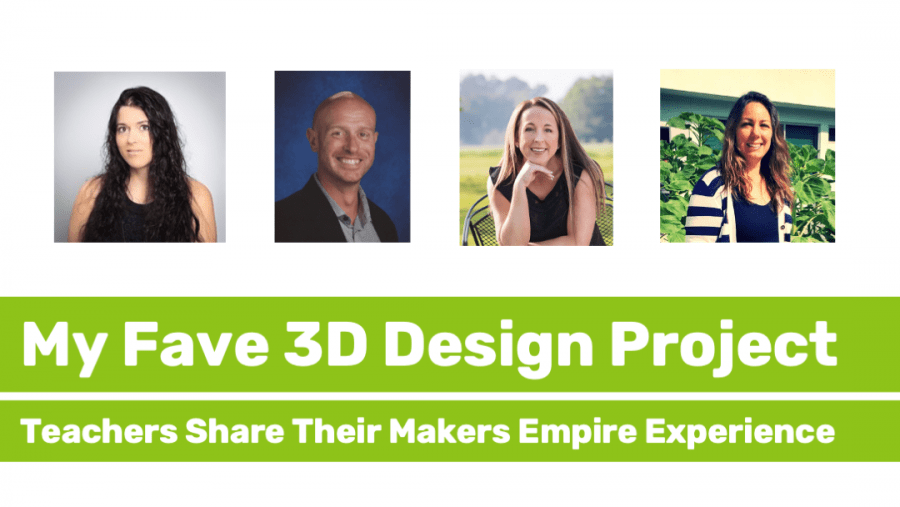
[Videos] American Teachers Share Their Fave Makers Empire Projects, Aha! Moments & Tips
We recently asked some of our American elementary and middle school…
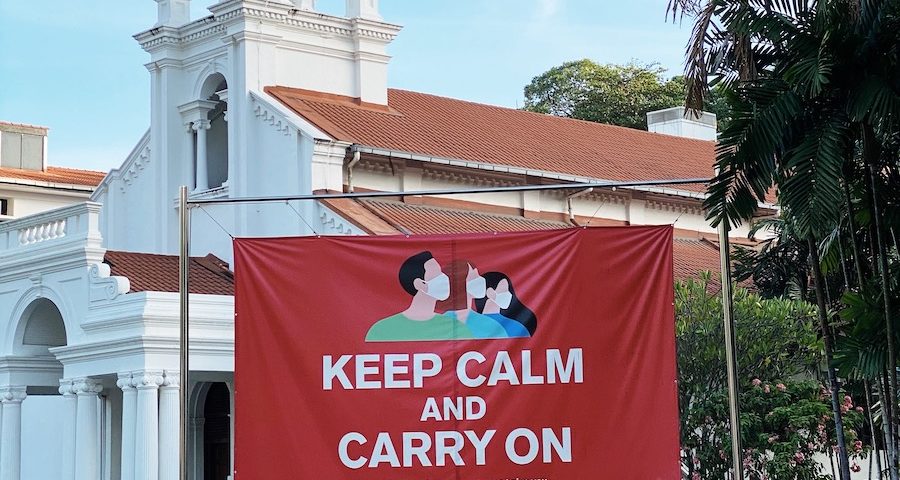
10 Coronavirus 3D Design Challenges For Students | Help People Affected By COVID-19
We’ve seen a recent surge of activity around the world as health au…
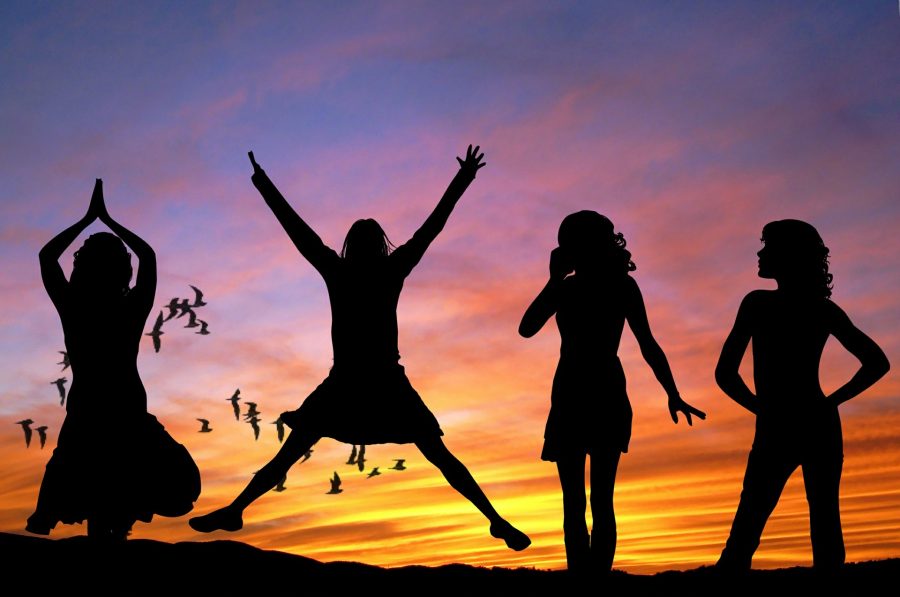
10 Design Challenges for Children To Help Create Positive Feelings During COVID-19
We are all navigating unchartered territory as we learn to cope wit…
Try Makers Empire for free!
Start learning 3D design in minutes. Make teaching design and technology fun and effective!
- USA (415) 652 0206
- AUS 61 (0)8 8120 3150
- Contact Makers Empire
- Get Tech Support
- Search Knowledgebase / FAQs
- Share Your Makers Empire Story
- 3D Design Software
- Class & School Subscriptions
- Learning by Design Course
- Custom Solutions
- Shop Makers Empire
- Knowledgebase
- Safety & Privacy
- Accessibility & Equity
- Free Printables
- Grants for Schools
- Makers Empire Blog
- Gallery of Designs
- Our Teachers
- Teacher Interviews
- Monthly Competitions
- Our Partners & Awards
- In the News
- Testimonials
- Major Milestones
- Terms of Service | Privacy
We acknowledge and pay our respects to the Kaurna people, the traditional custodians whose ancestral lands we gather on. We acknowledge the deep feelings of attachment and relationship of the Kaurna people to country and we respect and value their past, present and ongoing connection to the land and cultural beliefs.
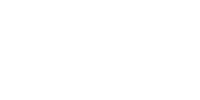
Please wait while you are redirected to the right page...
Prototype Problem Solving Activities Increasing Creative Learning Opportunities Using Computer Modeling and 3D Printing
- First Online: 04 September 2018
Cite this chapter
- Antonia Szymanski 5
Part of the book series: Mathematics Education in the Digital Era ((MEDE,volume 10))
1653 Accesses
3 Citations
This chapter explores the use of Prototype Problem-Solving Activities and 3D printing (PPSA) as a curricular tool to develop mathematical understanding, creativity, and technological literacy. Prototype Problem Solving Activities (PPSA) are teaching and learning activities that have been designed for students to create artifacts that demonstrate their understanding and to find unique solutions to authentic problems. They represent an outgrowth of the maker movement and attempt to involve students in authentic problem-solving exploration. The thesis of this chapter is that by using PPSA as a teaching strategy teachers can (1) provide students with opportunities to develop mathematical and creative thinking, (2) encourage students who may not perceive themselves as talented in mathematics by providing new ways in which to demonstrate mathematical thinking, and (3) use authentic problems and interdisciplinary approaches to problem solving that simulates real-life behavior by practitioners in the STEM fields. PPSA emphasizes communication and problem solving which are two principles that are stressed in education and by business leaders as being critical for life-long success. A description is provided of the creative processes that are nurtured through the use of PPSA, as well as the instructional design principles, and specific connections to technological literacy that moves students beyond being mere consumers of information to generating ideas and reflecting on thinking. The use of authentic problems requiring a generation of prototype products allows learners to self-assess and reflect on their understanding. The process of using PPSA allows the students to develop higher order thinking skills of analysis and synthesis in their mathematical understanding.
This is a preview of subscription content, log in via an institution to check access.
Access this chapter
- Available as EPUB and PDF
- Read on any device
- Instant download
- Own it forever
- Compact, lightweight edition
- Dispatched in 3 to 5 business days
- Free shipping worldwide - see info
- Durable hardcover edition
Tax calculation will be finalised at checkout
Purchases are for personal use only
Institutional subscriptions
Bronfenbrenner, U. (1986). Ecology of the family as a context for human development: Research perspectives. Developmental Psychology, 22 (6), 723–742.
Article Google Scholar
Chamberlin, S., & Moon, S. (2005). Model-eliciting activities as a tool to develop and identify creatively gifted mathematicians. The Journal of Secondary Gifted Education, 17 (1), 37–47.
Chu, S. L., Quek, F., Bhangaonkar, S., Ging, A. B., & Sridharamurthy, K. (2015). Making the maker: A means-to-an-ends approach to nurturing the maker mindset in elementary-aged children. International Journal of Child-Computer Interaction, 5, 11–19.
Clapp, E. P., & Jimenez, R. L. (2016). Implementing STEAM in maker-centered learning. Psychology of Aesthetics, Creativity, and the Arts, 10 (4), 481–491. http://doi.org/10.1037/aca0000066 .
Cosgrove, P. (2014). Making it real: 3D printing as a library service. Educause Review . Retrieved from http://er.educause.edu/articles/2014/10/making-it-real-3d-printing-as-a-library-service .
Coxbill, E., Chamberlin, S., & Weatherford, J. (2013). Using model-eliciting activities as a way to identify and develop mathematically creative students. Journal for the Education of the Gifted, 36 (2), 176–197.
Deci, E. L., & Ryan, R. M. (2000). The ‘what’ and ‘why’ of goal pursuits: Human needs and the self-determination of behavior. Psychological Inquiry, 11 (4), 227–268.
Doorley, S., Witthoft, S., & Kelly, D. (2012). Make space: How to set the stage for creative collaboration . Hoboken, NJ: Wiley.
Google Scholar
Eisenberg, M. (2013). 3D printing for children: What to build next? International Journal of Child-Computer Interaction, 1, 7–13.
Flores, C., & Springer, T. (2013). Authentic learning and assessment in the self-directed environment of a middle school maker space. In Proceedings from the Interaction Children and Design Conference , New York, NY.
Fonseca, D., Valls, F., Redondo, E., & Villagrassa, S. (2016). Informal interactions in 3D education: Citizenship participation and assessment of virtual urban proposals. Computer in Human Behavior, 55, 504–518.
Glas, E. (2002). Klein’s model of mathematical creativity. Science & Education, 11, 95–104.
Hobson, S. M., Trundle, K. C., & Sackes, M. (2010). Using a planetarium software program to promote conceptual change with young children. Journal of Science Education Technology, 19, 165–176.
Jaakkola, T., & Nurmi, S. (2008). Fostering elementary school students’ understanding of simple electricity by combining simulation and laboratory activities. Journal of Computer Assisted Learning, 24, 271–283.
Kaufmann, H., & Schmalsteig, D. (2003). Mathematics and geometry education with collaborative augmented reality. Computers and Graphics, 27 , 339–345.
Kim, S. H., & Kim, S. (2010). The effects of mathematical modeling on creative production ability and self-directed learning attitude. Asia Pacific Educational Review, 11, 109–120.
Kostakis, V., Niaros, V., & Giotitsas, C. (2015). Open source 3D printing as a means of learning: An educational experiment in two high schools in Greece. Telematics and Informatics, 32, 118–128.
Kroll, E., & Artzi, D. (2011). Enhancing aerospace engineering students’ learning with 3-D printing wind-tunnel models. Rapid Prototyping Journal, 17 (5), 393–402.
Kűcukozer, H. (2013). Designing a powerful learning environment to promote durable conceptual change. Computers & Education, 68, 482–494.
Kwan, O. N., Park, J. H., & Park, J. S. (2014). Providing students authentic learning experiences through 3D printing technology. In Learning experiences to promote mathematics learning yearbook 2014 . Singapore, Singapore: World Scientific Publishing Company.
Lesh, R., & Doerr, H. (2003). Beyond constructivism: Models and modeling perspectives on mathematical problem solving, learning, and teaching . Mahawah, NJ: Lawrence Erlbaum Associates.
Makermedia. (2013). Makerspace playbook school edition . Retrieved from https://makered.org/wp-content/uploads/2014/09/Makerspace-Playbook-Feb-2013.pdf .
Mann, E. (2006). Creativity: The essence of mathematics. Journal for the Education of the Gifted, 30 (2), 236–260.
Martinez, S. L., & Stager, G. S. (2013a, December). Invent to learn: Makers in the classroom. Educational Digest , 11–15.
Martinez, S. L., & Stager, G. S. (2013b). Invent to learn: Making, tinkering, and engineering in the classroom . Torrance, CA: Constructing Modern Knowledge Press.
Matthews, D., & Geist, E. (2002). Technological applications to support children’s development of spatial awareness . Information Technology in Childhood Education Annual , 321–336.
Novak, G. M., Patterson, E. T., Gavrin, A. D., & Christian, W. (1999). Just-in-time teaching: Blending active learning with web technology . Upper Saddle River, NJ: Prentice-Hall Inc.
Parpet, S., & Harel, I. (1991). Situating constructionism. In I. Harel & S. Papert (Eds.), Constructionism . Norwood, NJ: Ablex Publishing Corporation.
Peppler, K., & Bender, S. (2013, November). Maker movement spreads innovation one project at a time. Kaplan , 22–27.
Plucker, J. A., Beghetto, R. A., & Dow, G. T. (2004). Why isn’t creativity more important to educational psychologists? Potentials, pitfalls, and future directions in creativity research. Educational Psychologist, 39 (2), 83–96.
Sawyer, K. (2012). Explaining creativity: The science of human innovation (2nd ed.). New York, NY: Oxford University Press.
Schelly, C., Anazlone, G., Wijnen, B., & Pearce, J. (2015). Open-source 3D printing technologies for education: Bringing additive manufacturing to the classroom. Journal of Visual Languages and Computing, 28, 226–237.
Sheridan, K. M., Halverson, E. R., Litts, B. K., Brahm, L., Jacobs-Priebe, L., & Owens, T. (2014). Learning in the making: A comparative case study of three makerspaces. Harvard Educational Review, 84 (4), 505–531.
Silverman, L. K. (2002). Upside-down brilliance: The visual-spatial learner . Denver, CO: DeLeon Publishing.
Snow, R. E. (1992). Aptitude theory: Yesterday, today, and tomorrow. Education Psychologist, 27 , 5–32.
Sriraman, B. (2005). Are giftedness and creativity synonyms in math education? Journal of Secondary Gifted Education, 17 (1), 20–26.
Download references
Author information
Authors and affiliations.
Western Kentucky University, Bowling Green, KY, USA
Antonia Szymanski
You can also search for this author in PubMed Google Scholar
Corresponding author
Correspondence to Antonia Szymanski .
Editor information
Editors and affiliations.
Université de Moncton, Moncton, NB, Canada
Viktor Freiman
Janet Lynne Tassell
Rights and permissions
Reprints and permissions
Copyright information
© 2018 Springer International Publishing AG, part of Springer Nature
About this chapter
Szymanski, A. (2018). Prototype Problem Solving Activities Increasing Creative Learning Opportunities Using Computer Modeling and 3D Printing. In: Freiman, V., Tassell, J. (eds) Creativity and Technology in Mathematics Education. Mathematics Education in the Digital Era, vol 10. Springer, Cham. https://doi.org/10.1007/978-3-319-72381-5_13
Download citation
DOI : https://doi.org/10.1007/978-3-319-72381-5_13
Published : 04 September 2018
Publisher Name : Springer, Cham
Print ISBN : 978-3-319-72379-2
Online ISBN : 978-3-319-72381-5
eBook Packages : Education Education (R0)
Share this chapter
Anyone you share the following link with will be able to read this content:
Sorry, a shareable link is not currently available for this article.
Provided by the Springer Nature SharedIt content-sharing initiative
- Publish with us
Policies and ethics
- Find a journal
- Track your research
- Reviews / Why join our community?
- For companies
- Frequently asked questions
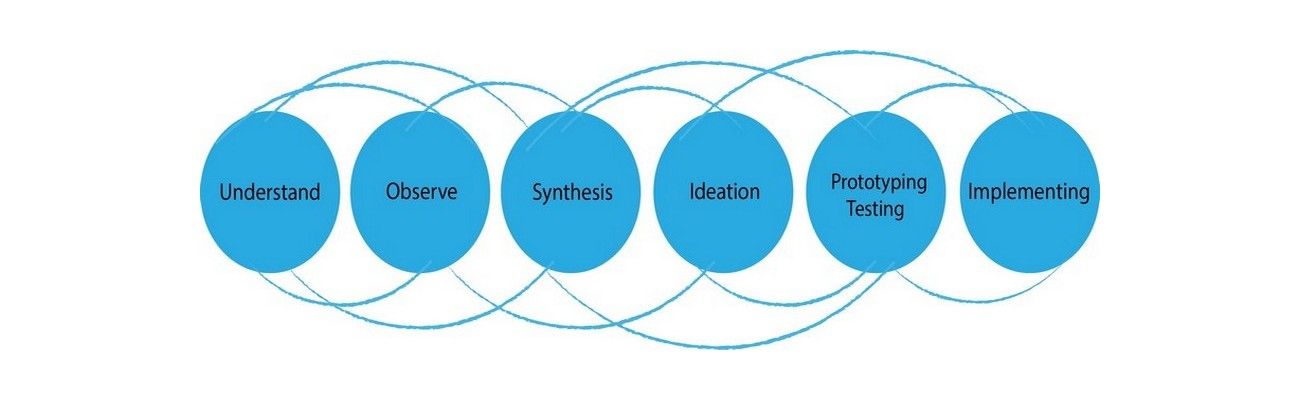
Design Thinking, Essential Problem Solving 101- It’s More Than Scientific
The term “ Design Thinking ” dates back to the 1987 book by Peter Rowe; “Design Thinking.” In that book he describes the way that architects and urban planners would approach design problems. However, the idea that there was a specific pattern of problem solving in “design thought” came much earlier in Herbert A Simon’s book, “The Science of the Artificial” which was published in 1969. The concept was popularized in the early 1990s by Richard Buchanan in his article “ Wicked Problems in Design Thinking”.
Ralph Caplan, the design consultant, sums up the need for design thinking with; “Thinking about design is hard, but not thinking about it can be disastrous.”
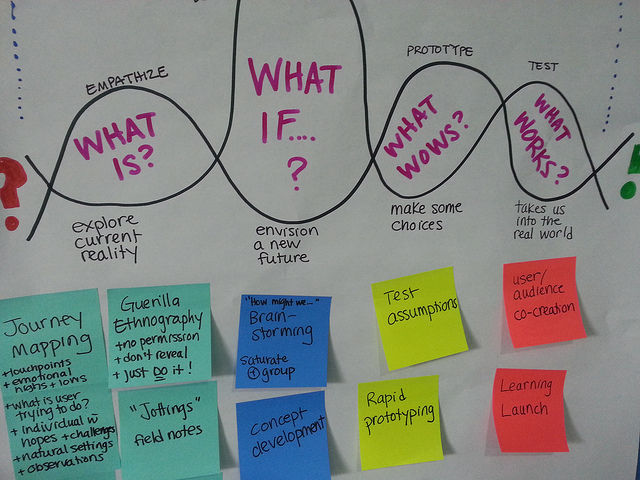
Author/Copyright holder: Christine Prefontaine. Copyright terms and licence: CC BY-SA 2.0
A simple overview of design thinking as a problem solving process.
Problem-Solving and Two Schools of Thought
Design thinking is concerned with solving problems through design. The idea being that the future output of the process will provide a better answer than the one already available or if nothing is available – something entirely new.
It is an unconstrained methodology where it is possible that the designer (or design team) will work on many possible solutions at once. It enables designers to consider the problem in many different ways and speculate on both the past and future of the problem too.
This is in contrast to the scientific method of problem solving which requires a highly-defined problem which focuses on delivering a single solution.
This difference was first noted by Brian Lawson, a psychologist, in 1972. He conducted an experiment in which scientists and architects were asked to build a structure from colored blocks. He provided some basic rules for the project and observed how they approached it. The scientists looked to move through a simple series of solutions based on the outcome and entire rule set. The architects, in contrast, simply focused on the desired end-state and then tested to see if the solution they had found met the rules.
This led to the idea that scientists solve problems by a process of analysis, whilst designers solve problems by synthesis. However, later evidence suggests that designers apply both forms of problem solving to attain “design thinking”.
They do this via a process of divergent thinking . A designer will examine as many possible solutions at the beginning of a process as they can think of – then they will apply the scientific side ( convergent thinking ) to narrow these solutions down to the best output.
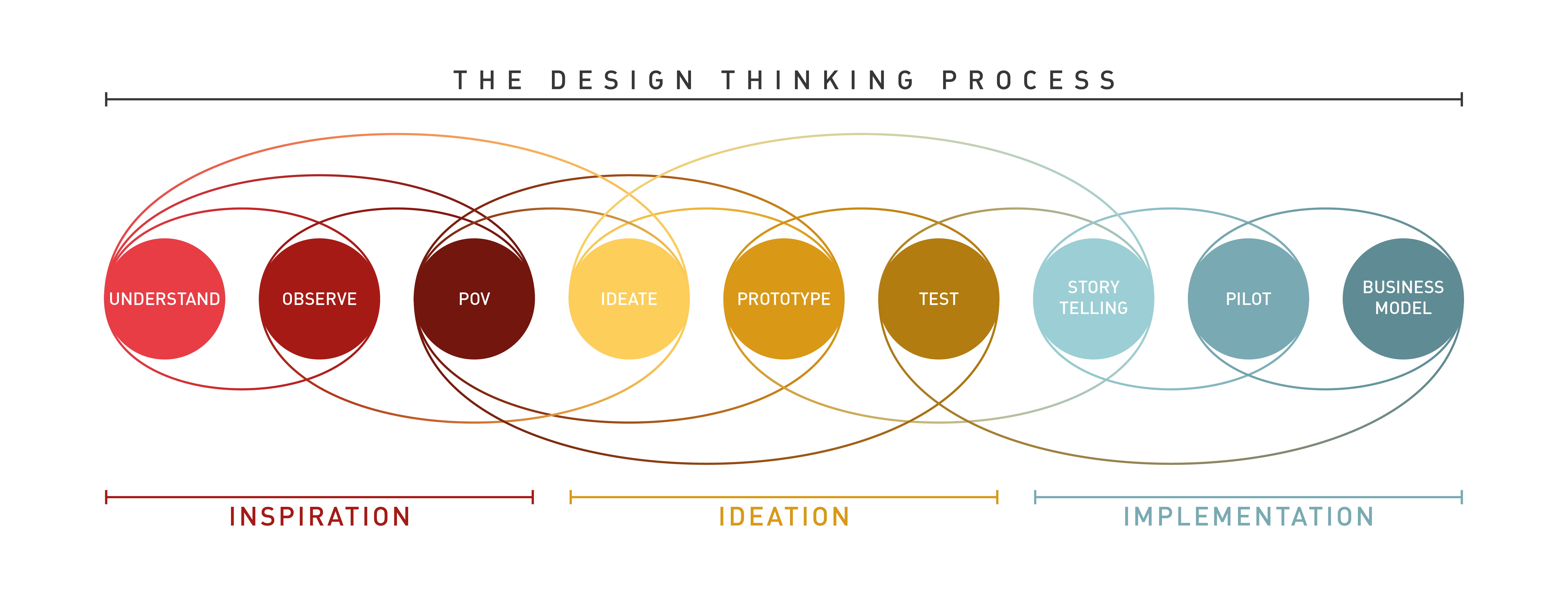
Design thinking can be as simple or as complex as the business and users require. This IDEO process can be seen as a 3 part process or a 9 part process .
The Design Thinking Process
Design thinking is essentially a process which moves from problem to solution via some clear intermediate points. The classic approach, as proposed by Herbert A Simon, is offered here:
- Definition – where the problem is defined as best as possible prior to solving it
- Research – where the designers examine as much data as they feel necessary to be able to fully contribute to the problem solving process
- Ideation – where the designer commences creating possible solutions without examining their practicality until a large number of solutions has been proposed. Once this is done, impractical solutions are eliminated or played with until they become practical.
- Prototyping – where the best ideas are simulated in some means so that their value can be explored with users
- Choosing – where the best idea is selected from the multiple prototypes
- Implementing – where that idea is built and delivered as a product
- Testing – where the product is tested with the user in order to ensure that it solves the original problem in an effective manner
There are many other design thinking processes outlined in literature – most of which are a truncated version of the above process combining or skipping stages.
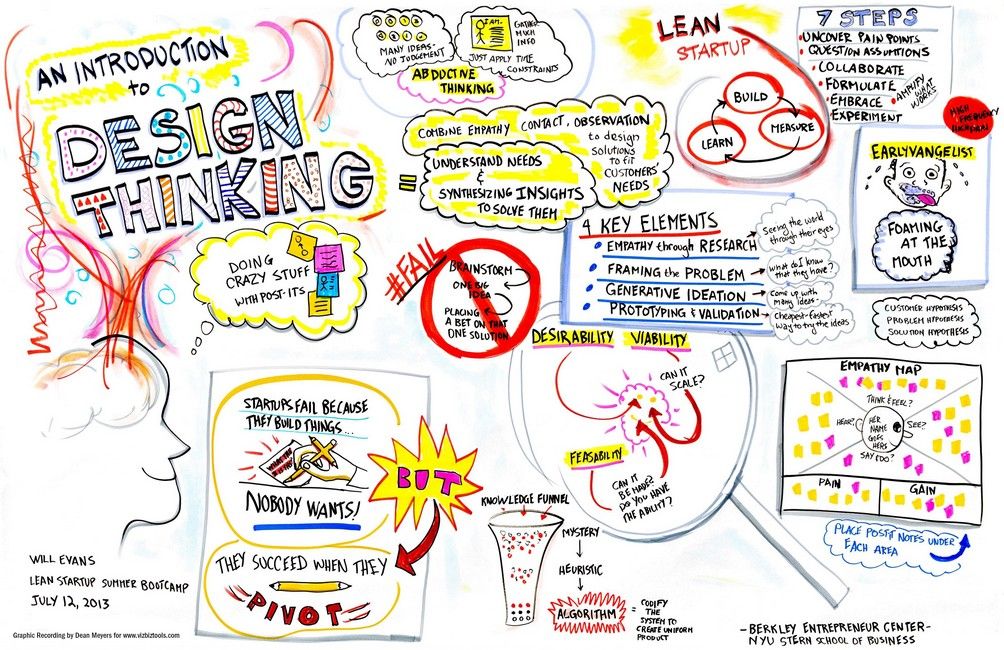
Here we see a more complex interpretation of the design thinking process and how it fits into the larger business sphere.
The Principles of Design Thinking
In the book, Design thinking: Understand, Improve Apply, Plattner and Meinel offer four underlying principles for design thinking:
- Human – all design is of a social nature
- Ambiguity – design thinking preserves and embraces ambiguity
- Re-design – all design processes are in fact re-design of existing processes
- Tangibility – the design process to make something tangible will facilitate communication of that design
It is also worth noting that design thinking functions independently of the design methods employed in any given design process. Design methods are the tools employed (such as interviews, user research , prototypes, etc.) and the assumption is that there are many paths that may be used (e.g. different sets of methods applied) to reach the same “best” result.
Visuals and Design Thinking
Firstly, it is important to acknowledge that design thinking is not about graphic design per se. However, designers are often used to communicating their thinking visually and drawings, sketches , prototypes, etc. are often used to convey the ideas created within a design thinking process.
In fact, ideas which are hard to express easily in words are often given shape in the form of visual metaphors. Design thinking thus easily incorporates abstract thought processes – something that scientific thinking may find more challenging to accommodate.

Visual representations of how those involved in the design process might be thinking about a problem.
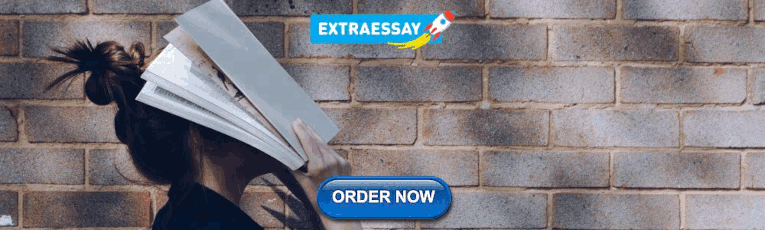
The Take Away
Design thinking is a process by which designers approach problem solving. It incorporates analytical, synthetic, divergent and convergent thinking to create a wide number of potential solutions and then narrow these down to a “best fit” solution. There are many ways to use a design thinking process to incorporate different methodologies to still reach the same end point. Designers must solve problems in order to add value through design.
Richard Buchanan’s original article "Wicked Problems in Design Thinking," was published in Design Issues , vol. 8, no. 2, Spring 1992.
Peter Rowe’s book from 1987 Design Thinking was published byCambridge: The MIT Press. ISBN 978-0-262-68067-7.
Herbert A Simon’s book from 1969 The Sciences of the Artificial . Was published by Cambridge: MIT Press.
Plattner, Hasso; Meinel, Christoph; Leifer, Larry J., eds. (2011). Design thinking: understand, improve, apply . Understanding innovation . Berlin; Heidelberg: Springer-Verlag. pp. xiv–xvi.doi:10.1007/978-3-642-13757-0. ISBN 3642137563.
This fascinating case study looks at how IBM plans to bring design thinking to large scale businesses - http://www.wired.com/2016/01/ibms-got-a-plan-to-bring-design-thinking-to-big-business/
See how Pepsi’s CEO, Indra Nooyi, implemented design thinking in her organization - https://hbr.org/2015/09/how-indra-nooyi-turned-design-thinking-into-strategy
Harvard Business Review examines design thinking and how it translates into action here - https://hbr.org/2015/09/design-for-action
Hero Image: Author/Copyright holder: Wikimedia Deutschland e. V. Copyright terms and licence: CC BY-SA 4.0
Creativity: Methods to Design Better Products and Services
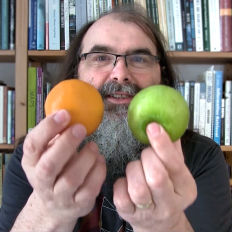
Get Weekly Design Insights
Topics in this article, what you should read next, what is design thinking and why is it so popular.
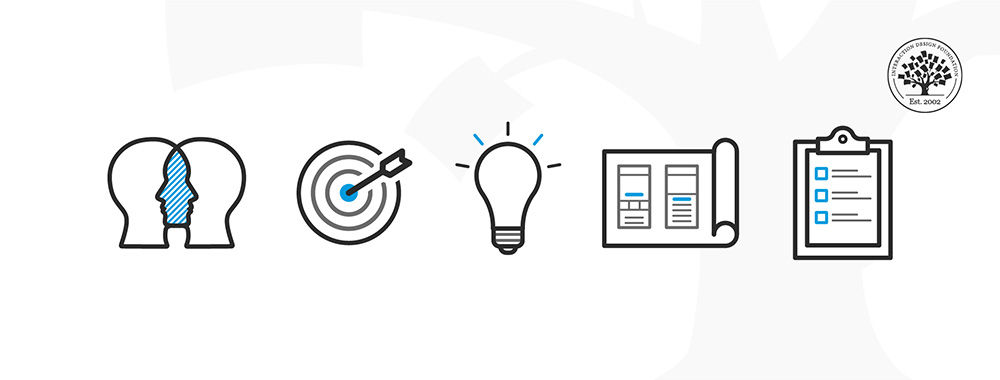
- 1.6k shares
Personas – A Simple Introduction
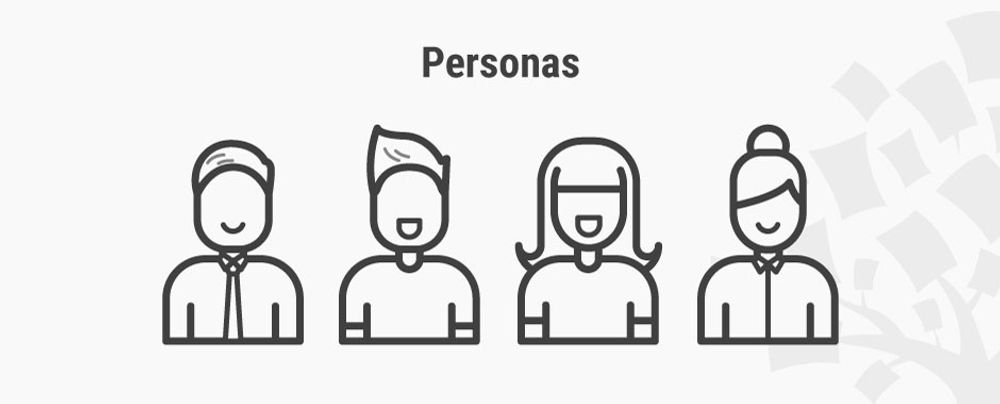
- 1.5k shares
Stage 2 in the Design Thinking Process: Define the Problem and Interpret the Results
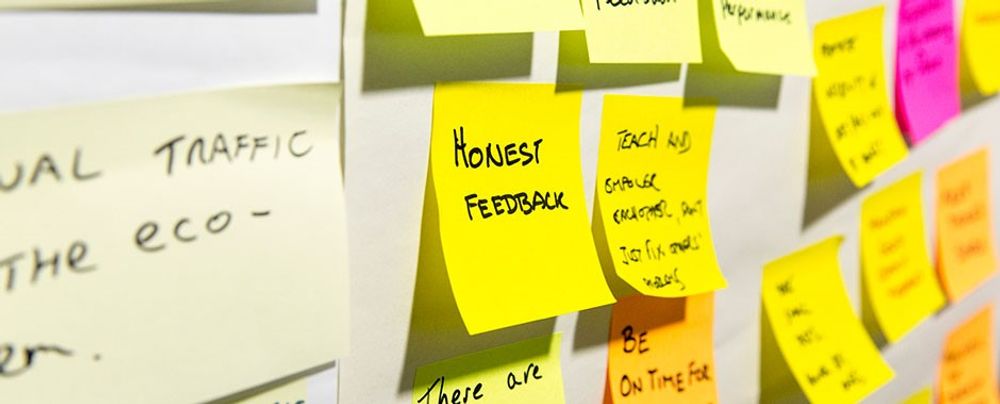
- 1.3k shares
What is Ideation – and How to Prepare for Ideation Sessions
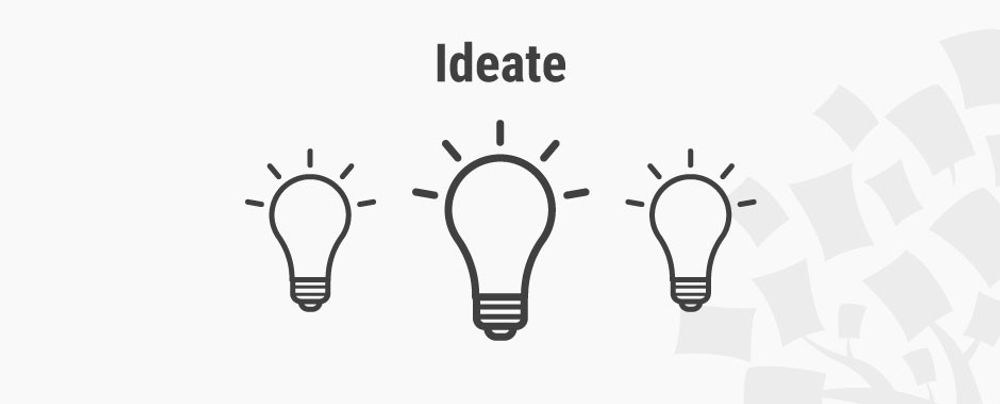
- 1.2k shares
Affinity Diagrams: How to Cluster Your Ideas and Reveal Insights
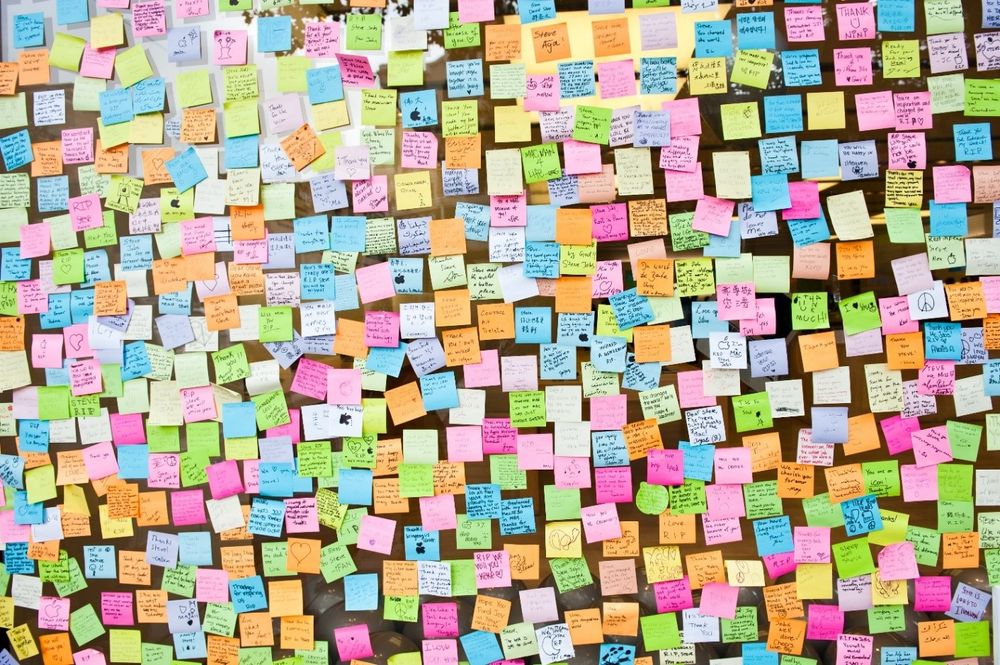
- 2 years ago
Stage 4 in the Design Thinking Process: Prototype
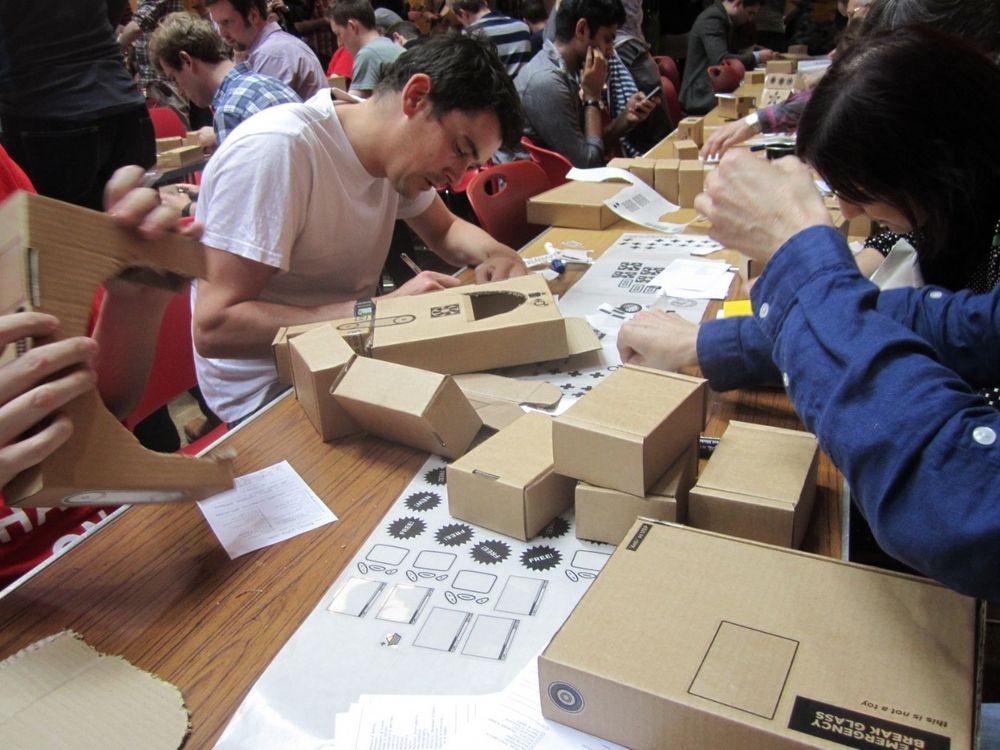
- 3 years ago
Stage 3 in the Design Thinking Process: Ideate
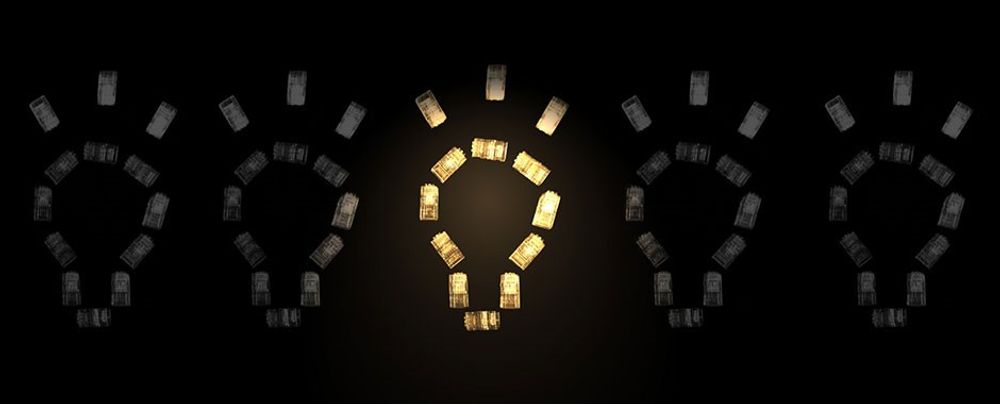
- 4 years ago
Stage 1 in the Design Thinking Process: Empathise with Your Users
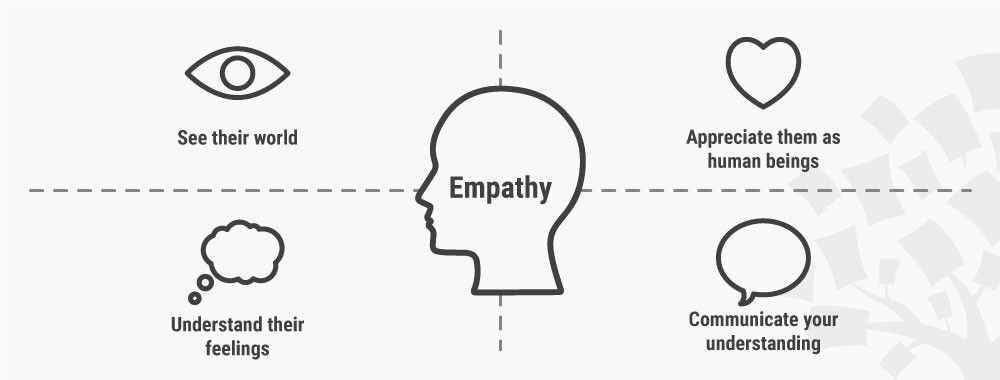
Empathy Map – Why and How to Use It
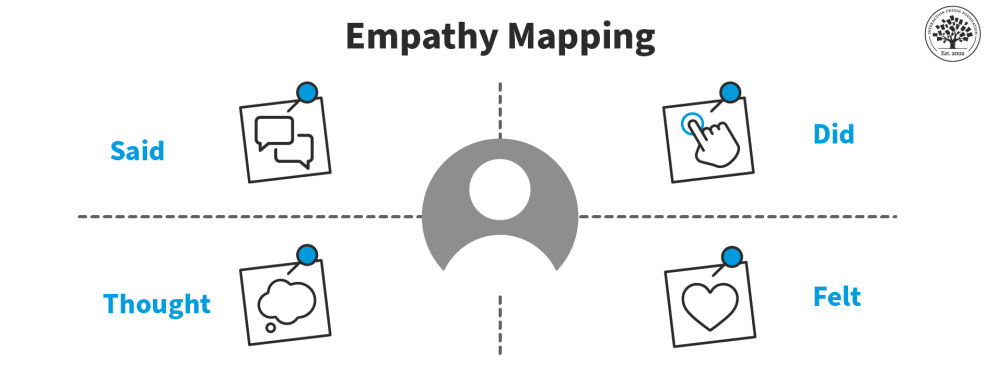
What Is Empathy and Why Is It So Important in Design Thinking?
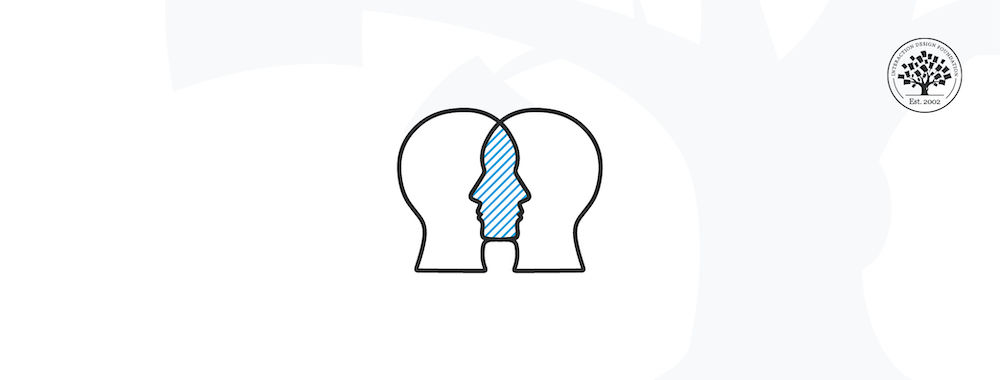
Open Access—Link to us!
We believe in Open Access and the democratization of knowledge . Unfortunately, world-class educational materials such as this page are normally hidden behind paywalls or in expensive textbooks.
If you want this to change , cite this article , link to us, or join us to help us democratize design knowledge !
Privacy Settings
Our digital services use necessary tracking technologies, including third-party cookies, for security, functionality, and to uphold user rights. Optional cookies offer enhanced features, and analytics.
Experience the full potential of our site that remembers your preferences and supports secure sign-in.
Governs the storage of data necessary for maintaining website security, user authentication, and fraud prevention mechanisms.
Enhanced Functionality
Saves your settings and preferences, like your location, for a more personalized experience.
Referral Program
We use cookies to enable our referral program, giving you and your friends discounts.
Error Reporting
We share user ID with Bugsnag and NewRelic to help us track errors and fix issues.
Optimize your experience by allowing us to monitor site usage. You’ll enjoy a smoother, more personalized journey without compromising your privacy.
Analytics Storage
Collects anonymous data on how you navigate and interact, helping us make informed improvements.
Differentiates real visitors from automated bots, ensuring accurate usage data and improving your website experience.
Lets us tailor your digital ads to match your interests, making them more relevant and useful to you.
Advertising Storage
Stores information for better-targeted advertising, enhancing your online ad experience.
Personalization Storage
Permits storing data to personalize content and ads across Google services based on user behavior, enhancing overall user experience.
Advertising Personalization
Allows for content and ad personalization across Google services based on user behavior. This consent enhances user experiences.
Enables personalizing ads based on user data and interactions, allowing for more relevant advertising experiences across Google services.
Receive more relevant advertisements by sharing your interests and behavior with our trusted advertising partners.
Enables better ad targeting and measurement on Meta platforms, making ads you see more relevant.
Allows for improved ad effectiveness and measurement through Meta’s Conversions API, ensuring privacy-compliant data sharing.
LinkedIn Insights
Tracks conversions, retargeting, and web analytics for LinkedIn ad campaigns, enhancing ad relevance and performance.
LinkedIn CAPI
Enhances LinkedIn advertising through server-side event tracking, offering more accurate measurement and personalization.
Google Ads Tag
Tracks ad performance and user engagement, helping deliver ads that are most useful to you.
Share Knowledge, Get Respect!
or copy link
Cite according to academic standards
Simply copy and paste the text below into your bibliographic reference list, onto your blog, or anywhere else. You can also just hyperlink to this article.
New to UX Design? We’re giving you a free ebook!

Download our free ebook The Basics of User Experience Design to learn about core concepts of UX design.
In 9 chapters, we’ll cover: conducting user interviews, design thinking, interaction design, mobile UX design, usability, UX research, and many more!
New to UX Design? We’re Giving You a Free ebook!
Welcome to E4C.
Sign Into Your Account
Forgot Password?
Remember Me
Don't have an account? Sign Up
Home » Articles » How 3D printing helps solve big problems in design for global development
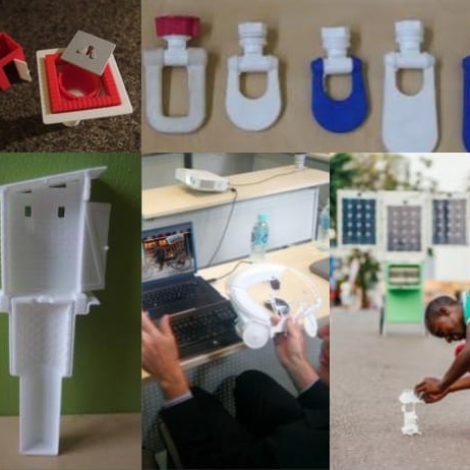
How 3D printing helps solve big problems in design for global development
High expectations have been heaped on the role of 3D printers, but their place in global development can still seem limited. They have seen mixed results in the manufacture of prosthetic limbs , and they are doing really interesting, albeit peripheral, work in aid delivery to disaster areas. One group even offers a guide to printing corn shellers . These applications suggest an important future for the technology in underserved communities. But for designers and engineers wondering how to use these machines to enhance their work now, Catapult Design has some ideas. Noel Wilson, Catapult’s Creative Director, share examples of their work.
Catapult Design is a non-profit firm based in Denver, Colorado (USA) that works with socially driven clients around the world. In our work 3D printers are a powerful prototyping & communication tool. We don’t see it as a scalable manufacturing method, yet. Alongside generative software, it will definitely help us all manufacture products that are smarter, stronger, lighter, healthier in the long run. But for now Catapult Design focuses on using 3D printing to support concepts on their path to manufacturing, or to communicate design intent. We are excited about associated additive manufacturing potentials, present and future, but we have yet to see it compete in terms of scalability or manufacturing efficiency with other processes. 3D printing can produce some forms that no other process can, and out of a broad range of exciting materials.
3D printing it is not solving big problems all by itself. But it is definitely helping us to achieve greater levels of detail, speed, and depth in our work.
Miniature water transport prototype models
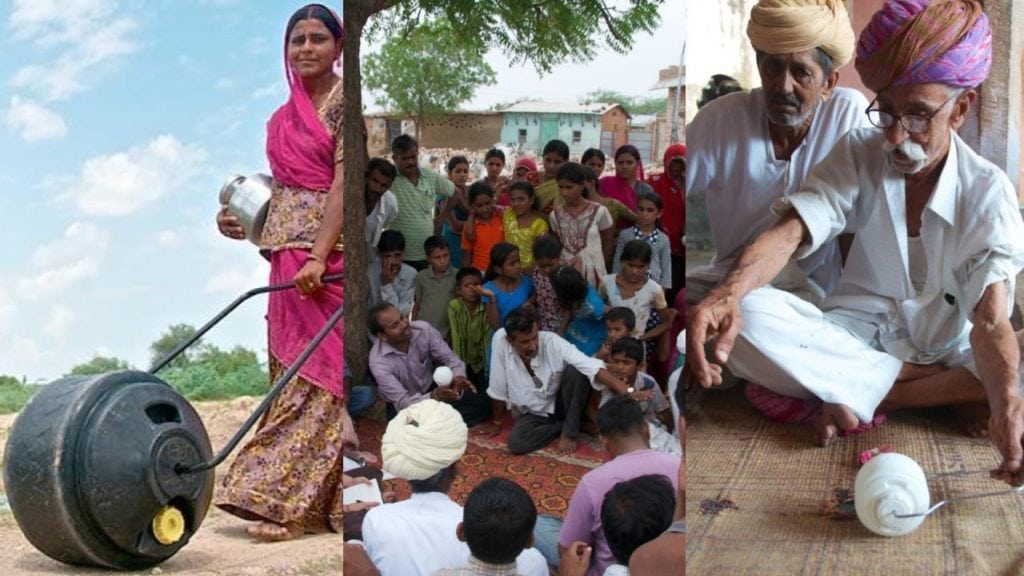
Catapult Design worked with Wello water to help them redesign their rolling water barrel for the Indian market. Their intention was to ease drudgery in water transport and improve water management in the home. After months of research in Rajasthan, we started to develop concepts with our partners and target customers. After a few rounds of rough prototyping with existing barrels and containers, we were able to create refined miniature models of our design concepts. The models encouraged deeper discussion with community focus groups, which led to further refinement of the design. Wello is now manufacturing the redesigned product and there are at least 10,000 Wello Waterwheels in circulation, with 50,000 more expected in the next two years.
Latrine construction training aids
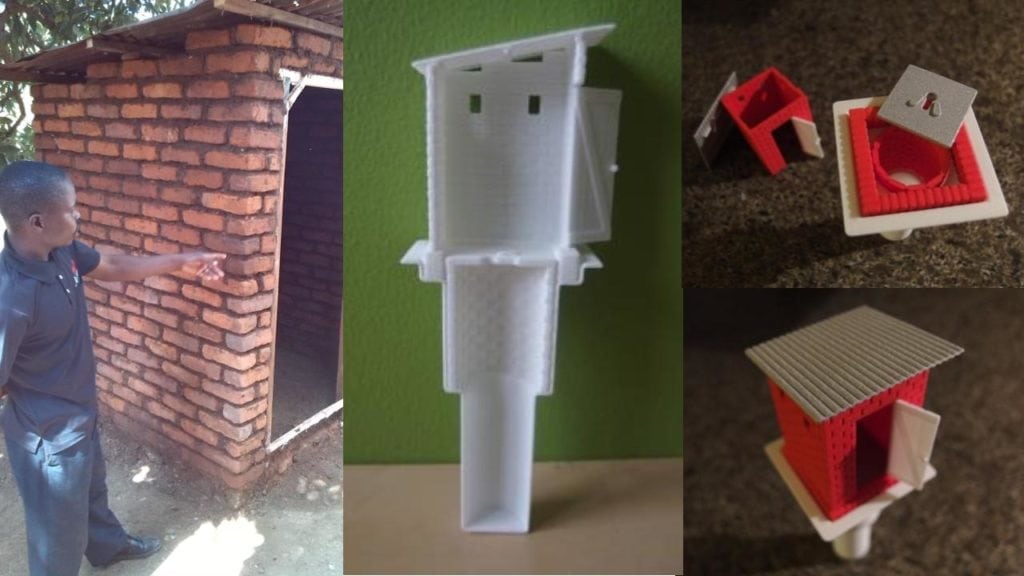
We worked with Abt Associates to help them train latrine construction workers in Malawi. They were teaching the workers to use techniques that require less concrete. Abt needed a training tool as a visual aid for the workers. We created this cross-section model and loose assembly model to allow Abt to experiment with training methods and to see if both or either model were effective in communicating the construction techniques.
Pedicab prototype models
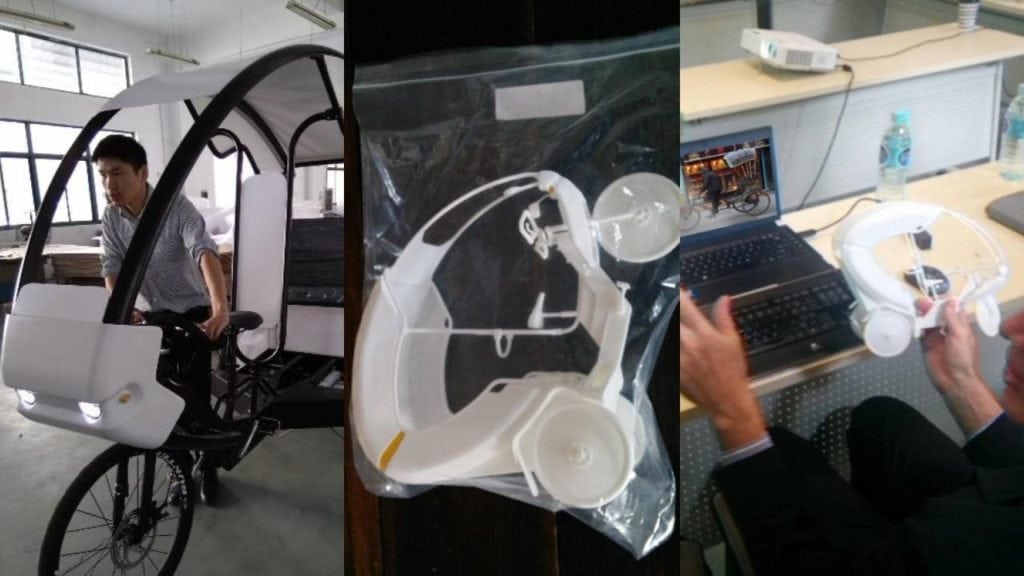
Catapult Design worked with the Asian Development Bank (ADB) to create a modern pedicab for South Asian cities. Their goal is to provide a sustainable transport option that governments might be willing to procure. The new designs could bolster a complex rickshaw industry in Southeast Asia where rickshaw bans and restrictions are threatening people’s livelihoods. We had several design reviews and brainstorms with industry experts, clients, manufacturers and designers, and used printed models of the pedicab design to work through details and make decisions. We are now assembling 60 of these pedicabs in Nepal, in both Kathmandu and Lumbini, to run a pilot with local rickshaw drivers.
Prototyping and small-scale manufacture of water taps
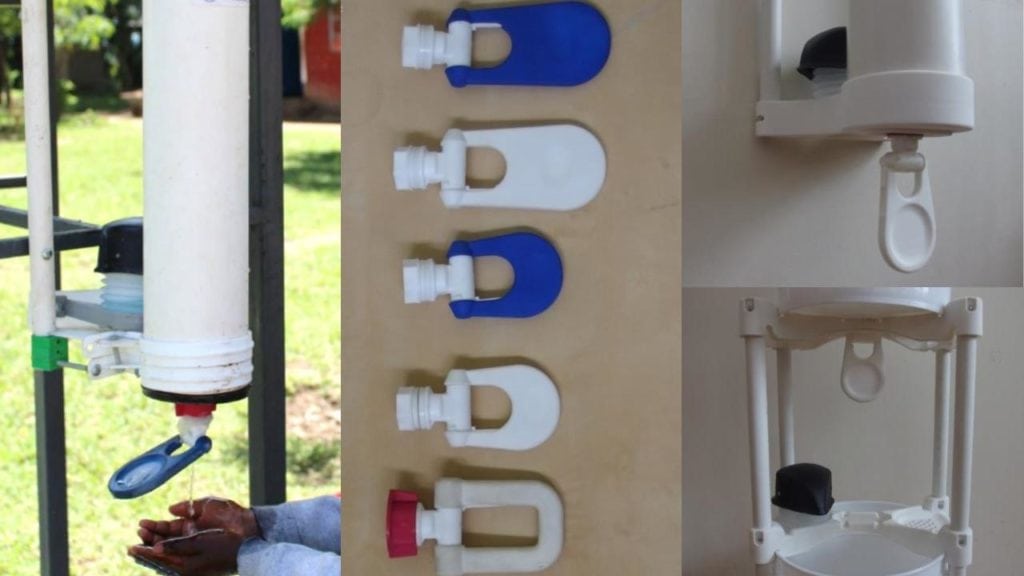
We worked with Innovations in Poverty Action (IPA) to help them design hand-washing hardware for Kenyan households, clinics, and primary schools that are off of the plumbing grid. IPA was researching the impact hand-washing behavior change could have on disease rates in children. After a lot of rough prototyping, we honed in on a tap design and then were able to explore variations of it until we reached a design that fit everyone’s needs. IPA also needed to conduct a pilot of several hundred units to test the designs, but didn’t have the money to commit to tooling. We were able to 3D print 200 taps that snapped onto the body of existing polypropylene beer brewing taps. The result was functional taps for the pilot.
Prototyping a soap foamer and a mold for manufacturing its parts
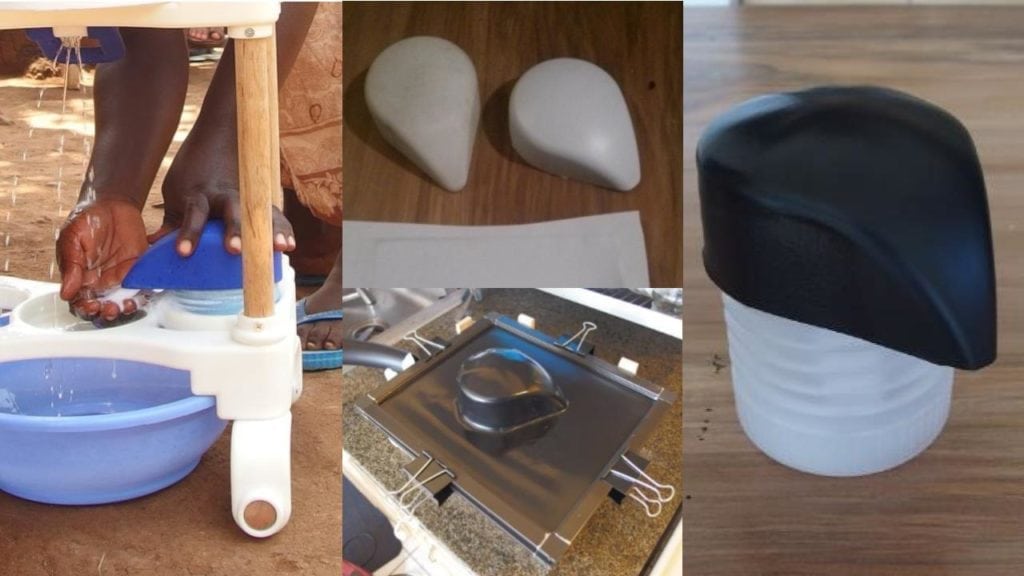
Apart from a tap, we also developed a soap foamer for IPA. Again, we needed to help IPA get to their pilot stage without committing to tooling. Once we had prototyped and tested the concept, we found existing working components that we could repurpose (in this case a simple bug dusting device). We still needed to create custom covers to channel the foam onto the users’ hands. So we 3D printed the first few, creating tough prototypes for initial testing. But then when it came to creating 200 or more for the pilot, the cost of printing these covers was too high. Our solution was to vacuum form them. To do this, we 3D printed the mold, filled it with plaster, and then formed more than 200 covers over it. IPA have since completed their pilot and we are now applying for further project funding to make design revisions, conduct further testing, and then take it to manufacture with a fabrication partner. This time we hope to have a tooling budget.
Learning how to economize a cart design through a printed model
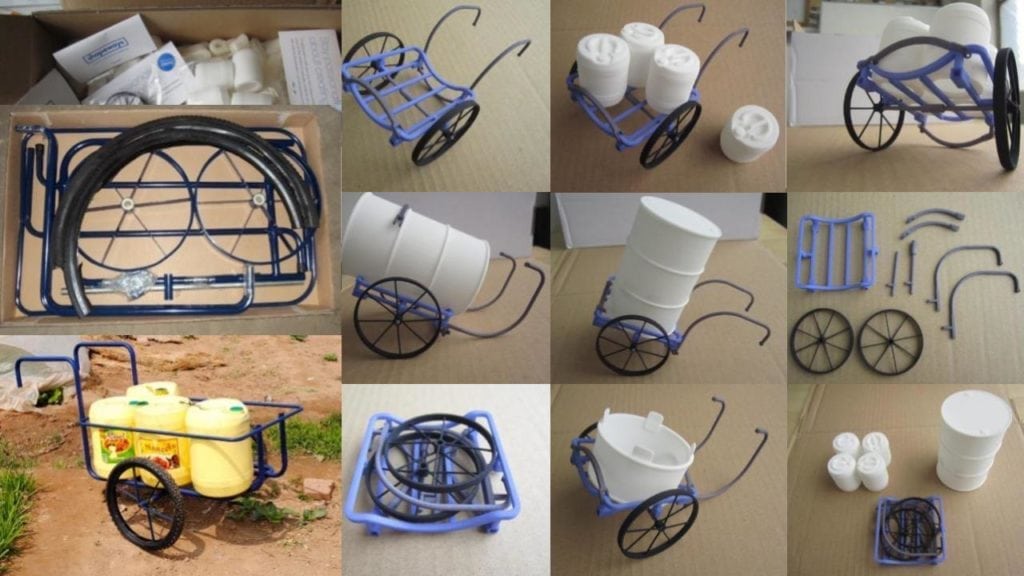
We helped Anza to design a flat-packed handcart to transport water and other goods in Northern Tanzania. It was important for us to understand the flat-packing, the assembly, and the modularity of the carts, so we 3D printed a model. The model allowed us to play with the design concept to get the size of the package down to its minimum, and the design of the cart to its most useful, and modular state. The 3D print also helped in communicating the design to the client and fabrication partners. Anza produced around 1000 of these carts in China and tested them in the Mount Kilimanjaro area.
3D prints with digital models communicate a Wi-Fi kiosk concept to engineers
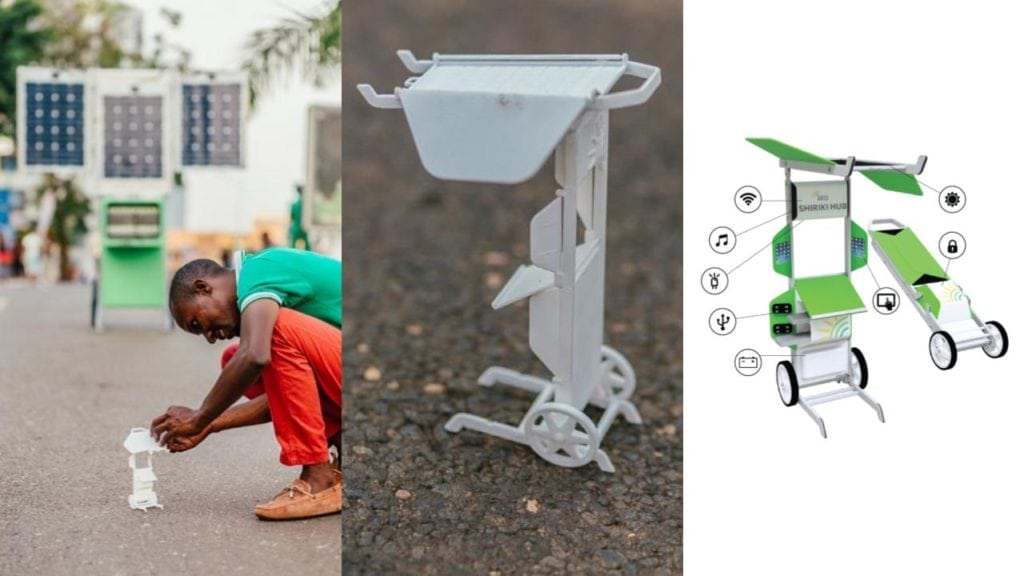
Catapult Design helped African Renewable Energy Distribution (ARED) to redesign their phone charging kiosk for Rwandan communities and refugee camps. ARED’s goal was to provide access to energy, information and entertainment through the combination of a mobile battery, server, Wi-Fi, and speakers. They wanted the kiosks to be super durable, minimal and modern. It was our job to visit Rwanda, conduct research with the existing cart vendors, prototype concepts with ARED, and then refine the concept to hand over to a German engineering and manufacturing partner called Tech Solute. We used a combination of scaled 3D-printed prototypes and annotated 3D models (IGES/STEP and Sketch Fab platform) to communicate the design to the engineering partners, who then translated it into a fully functional prototype. ARED is currently testing several prototypes in Rwanda, and will refine the design further at the end of the year to scale production into the hundreds.
All of the models shown here use selective laser sintering (SLS) 3D printing, but we also use Stereolithography (SLA) and fuel deposition modeling (FDM) at times for lower-fidelity prototyping.
We also sometimes use 3D printing purely to expose people to modern additive fabrication possibilities and techniques. We have 3D printed trophies, schwag and toys to showcase 3D printing capabilities and advocate exploration with these exciting processes.
We continue to use 3D printing in a multitude of ways, and look forward to advancing our methods in parallel to the capabilities of the technology. 3D-printed metals, printing multiple materials at once (including circuitry), and printing lattices that can grow biomaterials are just three areas with which we are excited to experiment in the future.
Share This Article
Leave a Reply
You must be logged in to post a comment.
Suggested Articles
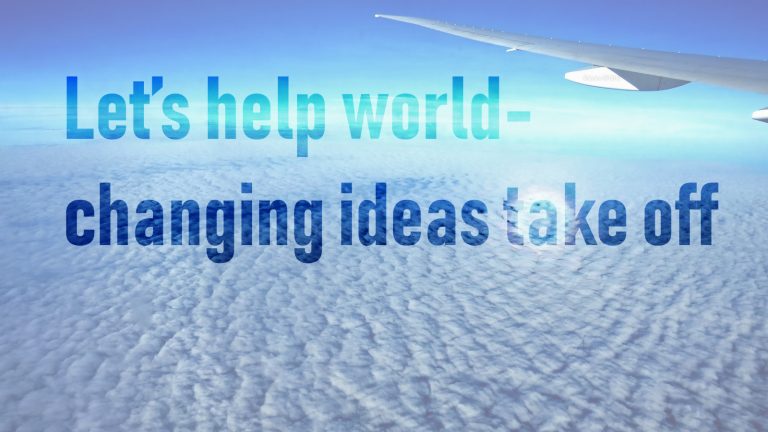
Let’s solve the big problems and support bolder technology design...
Inventors are solving the myriad problems that arise from global poverty, but there is not enough focus on the big issues. Global development experts observed a dichotomy between...
Read Full Article
Join a global community of changemakers.
Solving Real-World Problems with 3D Printing
In today's blog we're going to look at 3 interesting ways that 3D printing can be used in education to solve real-world problems. Each example looks at a particular global challenge, before we explain how we envisage students taking on the challenges with the use of 3D technologies. Although each example is different, they all have one thing in common - breaking down the silos between schools and the wider community.
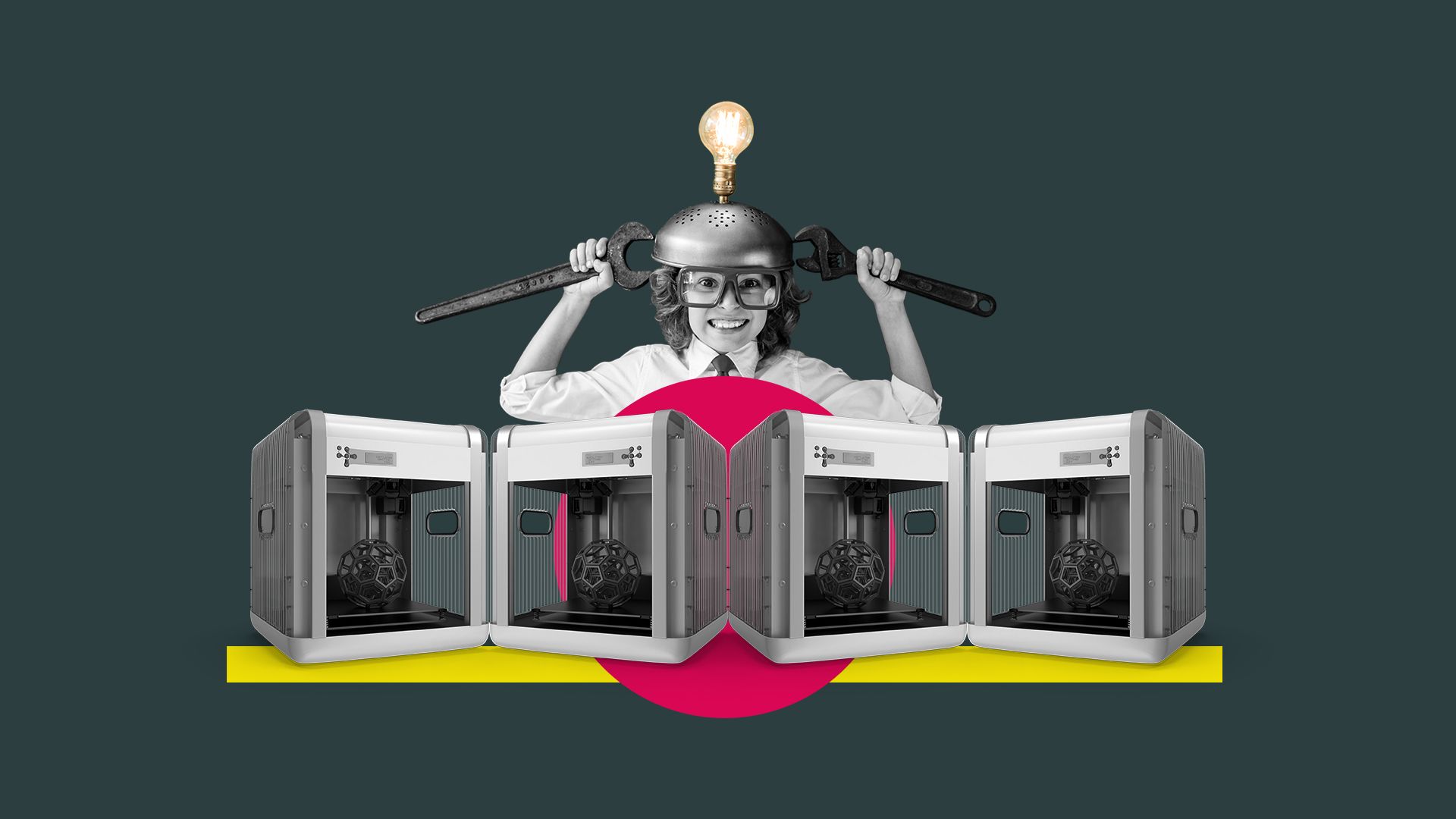
7th February 2021 • News
Example 1: Assistive Technology
Current assistive technology solutions can be expensive, undesirable and not customised to the needs of individuals.
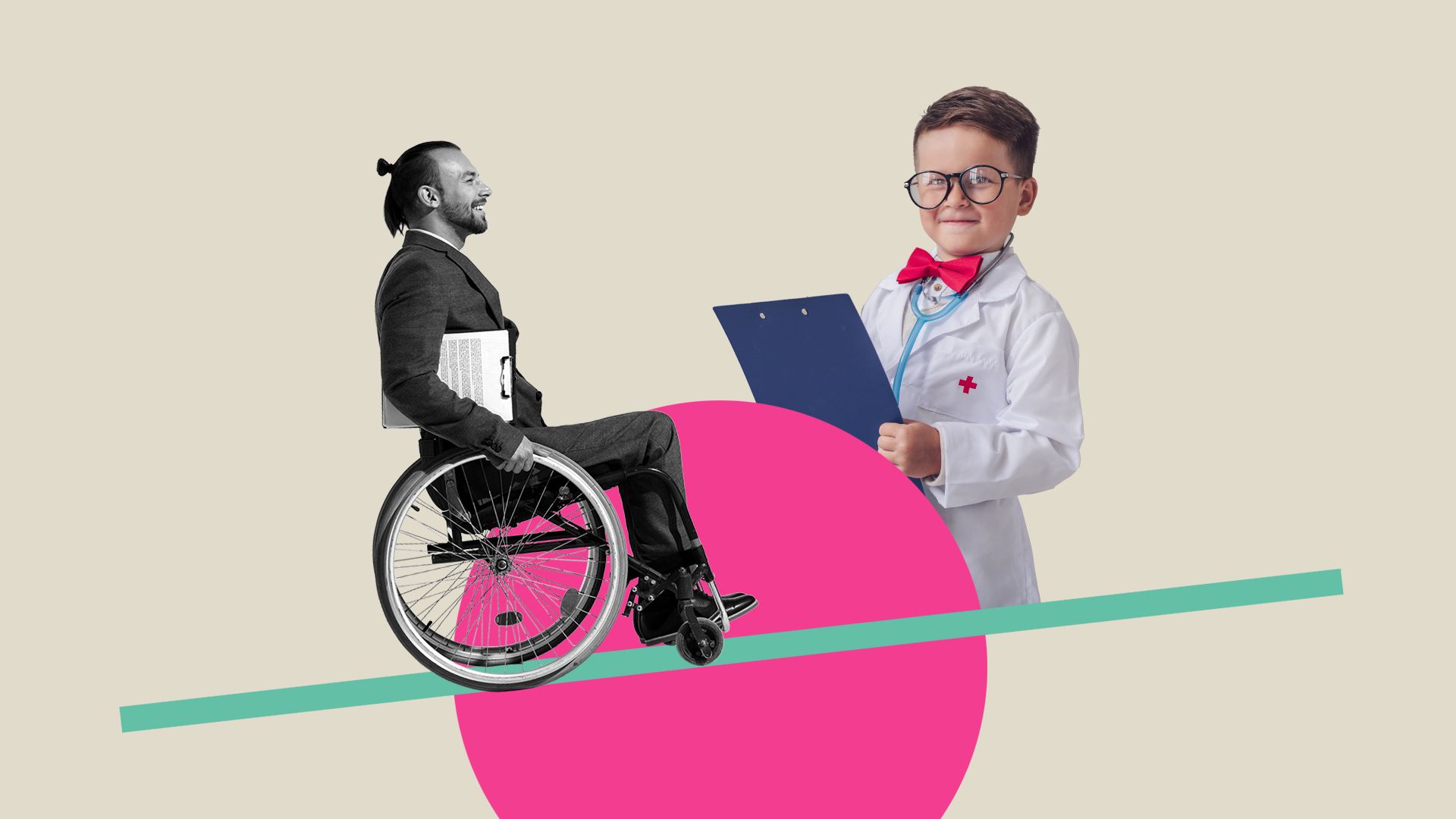
If you’ve been following PrintLab for some time, you’ll know that assistive technology is one of the key themes we incorporate into our learning platform. The obvious benefits of students designing assistive devices for people with disabilities are that they have the opportunity to go through an amazing, empathetic journey of creative problem solving – all whilst improving the life of another person or people. But what is the wider impact of this? Let’s take a look at a hypothetical scenario…
Last year we launched the make:able 3D printing and assistive technology challenge in collaboration with Autodesk and partners. The brief is to ‘design and make a product or prototype that improves the day-to-day life of someone who struggles with mobility in their hands’ and to date we’ve had an astounding 17,000 student registrations across 500 schools in 70+ countries. Due to the school disruptions from the pandemic, we might not see all 17,000 students participate but imagine if even 10,000 students entered and worked in teams of 4. If you do the math, that’s 2500 low-cost, customised assistive devices. And then if you take it further and make these designs open source and shared on platforms like Makers Making Change so they can be downloaded, adjusted and manufactured, you can begin to understand just how many lives can be supported in programs like this.
Example 2: Circular Product Design
Plastic packaging and products continue to use up finite resources and clog up the Earth’s oceans – destroying wildlife and marine environments.
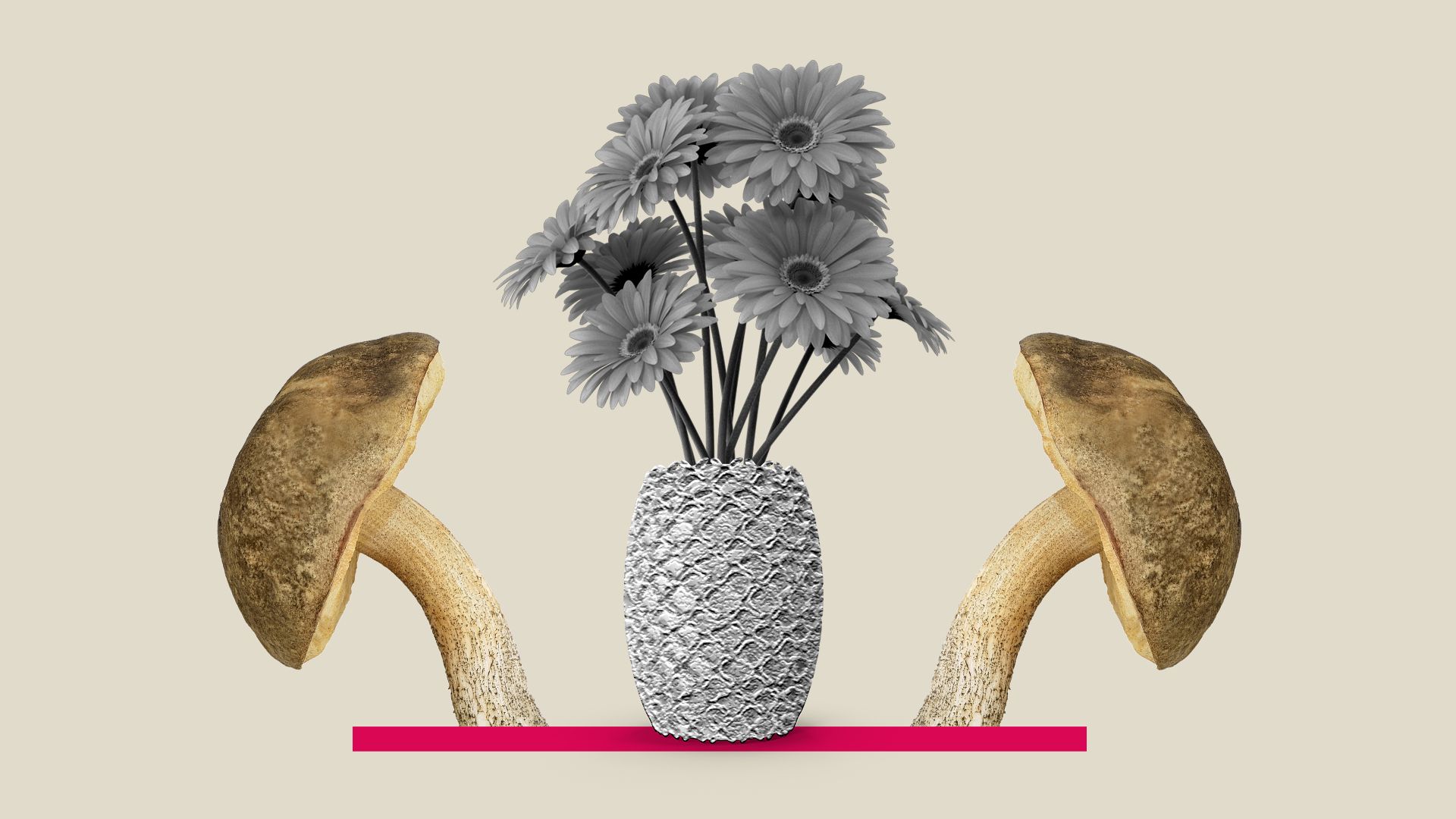
There’s no doubt that plastics are fantastic in the way they look, feel and function, but predictions such as ‘there will be more plastic in our oceans that fish by 2050’ means that we really need to rethink the way we design and manufacture products. There’s a huge wave of innovators looking at how we can make better use of the plastic we produce through reuse, repair, recycling and remanufacturing initiatives. However, there’s also need to explore alternatives to plastics, especially for products that don’t require their specific properties.
One particular area of interest that we’ll be exploring at PrintLab is the use of mycelium (the thread-like part of a mushroom) to grow a range of products – from packaging to homeware. By combining mycelium with an organic substrate such as agricultural waste inside a mould, ‘polystyrene-like’ products can be created with fantastic properties such as flame resistance. The best thing is that once the products are no longer required, they can be composted at home or within the local community, providing nutrients back to the Earth. And if you combine this process with the freedom of design that reusable 3D printed moulds offer, the applications are endless! You can check out some amazing examples from Grown.bio here .
So where does this fit into education? In our opinion, education should be a playground for exploration and experimentation in fields such as sustainability. Imagine a school growing their own mushrooms and using the mycelium to produce homeware that is then sold throughout the local community. Now imagine this scaled up across networks of schools around the world who all share valuable data and research with an open-source mentality. This type of innovation from young students will surely drive awareness through social proof and send a wave of influence to designers and manufacturers around the world.
As a final note on plastics, we’re also excited to see how the 3D printing industry responds to this global challenge. We are already seeing companies like Filamentive who offer premium 3D printing materials made from recycled post-industrial waste where possible. And there’s a whole lot of experimentation going on with organic pastes, where viscous materials are mixed and extruded through desktop machines.
Example 3: Manufacturing Hubs
Emerging technologies such as 3D printing can be expensive and inaccessible for small businesses.
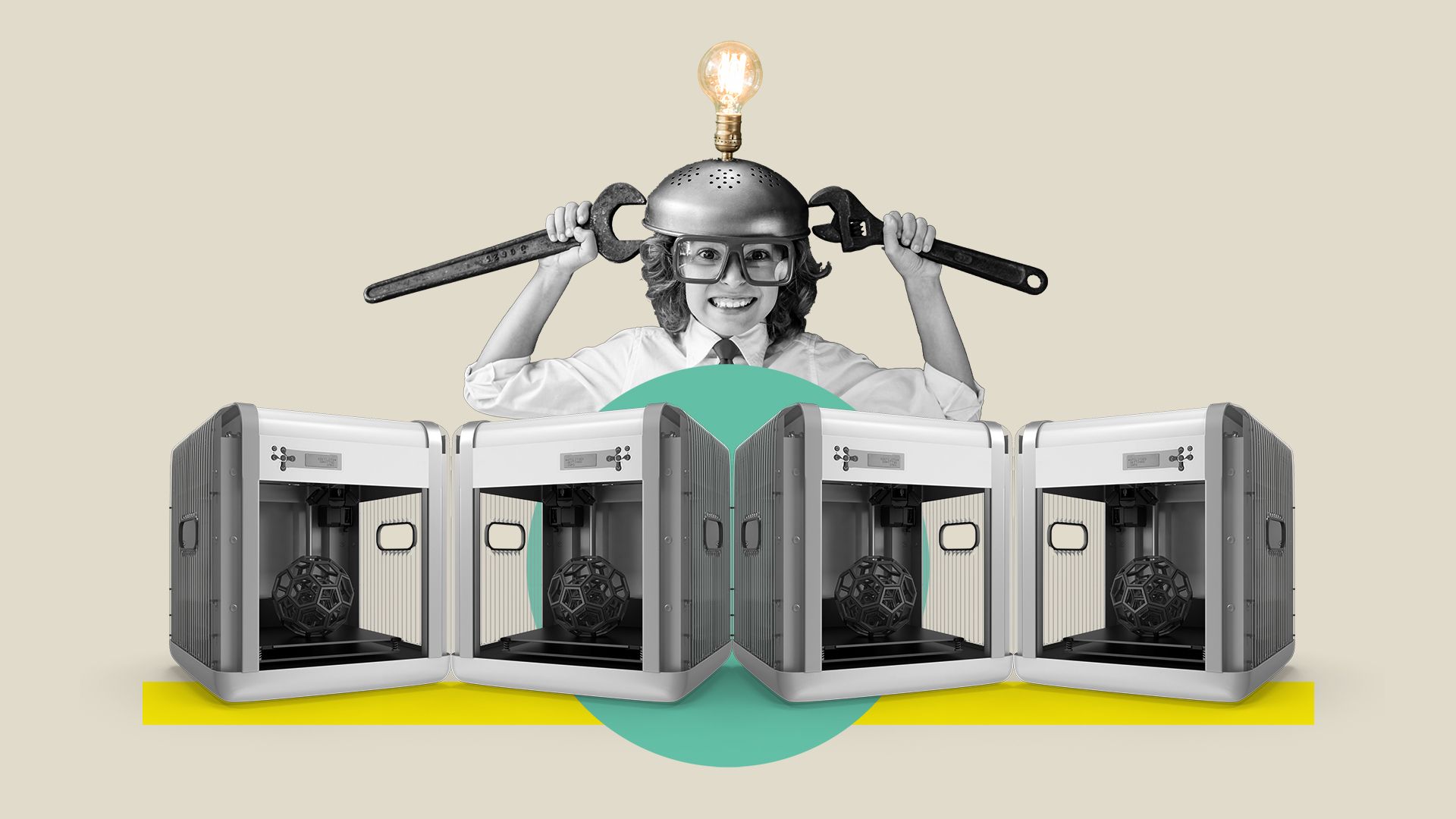
Our final example is more of a vision and it might seem like wishful thinking but if we don’t spark discussions about topics, they’d never come to fruition! The vision is based on governments providing funding to schools to purchase a broad range of additive manufacturing hardware (including high-end industrial machines), in view of supporting them to become manufacturing hubs that serve local businesses. For small businesses, this means easy, local and affordable access to equipment that can grow their brands. And for schools, it means that students can become an integral part of the daily operations where they can gain valuable entrepreneurial and technical skills. There’s always been a call for stronger links between industry and education and initiatives like this are sure to help close the widening skills gap of the present. We can even imagine creative businesses coming to one of these hubs to be upskilled by students themselves.
We hope you enjoyed reading about some of our visions for 3D printing in education and if you ever have any questions or are interested in collaborating with us, feel free to reach out at [email protected] .
Enter Your Code
Access Code:
Whats a code?
A code is a combination of letters and numbers that gives you access to PrintLab’s Student Portal. If your school or organisation is signed up to PrintLab Classroom, simply ask them for the code and enter it above. If you’re an educator and not sure where to find your code, click here .
I need help
For any support queries or general questions, please email [email protected] and we’ll be happy to help!

- Education & Teaching
- Schools & Teaching

Enjoy fast, free delivery, exclusive deals, and award-winning movies & TV shows with Prime Try Prime and start saving today with fast, free delivery
Amazon Prime includes:
Fast, FREE Delivery is available to Prime members. To join, select "Try Amazon Prime and start saving today with Fast, FREE Delivery" below the Add to Cart button.
- Cardmembers earn 5% Back at Amazon.com with a Prime Credit Card.
- Unlimited Free Two-Day Delivery
- Streaming of thousands of movies and TV shows with limited ads on Prime Video.
- A Kindle book to borrow for free each month - with no due dates
- Listen to over 2 million songs and hundreds of playlists
- Unlimited photo storage with anywhere access
Important: Your credit card will NOT be charged when you start your free trial or if you cancel during the trial period. If you're happy with Amazon Prime, do nothing. At the end of the free trial, your membership will automatically upgrade to a monthly membership.

Download the free Kindle app and start reading Kindle books instantly on your smartphone, tablet, or computer - no Kindle device required .
Read instantly on your browser with Kindle for Web.
Using your mobile phone camera - scan the code below and download the Kindle app.

Image Unavailable

- To view this video download Flash Player

Problem-Solving through 3D Printing & 3D Design: STEAM Project Guide & Curriculum Paperback – April 16, 2017
Purchase options and add-ons.
- Activity 1: Explore a Collection of Public Models
- Activity 2: Meet Your 3D Printer
- Activity 3: Get Oriented with a Slicer
- Activity 4: Optimize Your Slicer
- Activity 1: Explore the TinkerCAD Tutorials
- Activity 2: Create a First Prototype
- Activity 3: Iterate Your Design
- Activity 1: Compare Traditional and Digital Clay
- Activity 2: Improve Your Animal
- Activity 3: Import Models into TinkerCAD
- Activity 4: Export Models from TinkerCAD for 3D Printing
- Activity 1: Create a Cookie Cutter Using a Single Line
- Activity 2: Create a Cookie Cutter Using Multiple Lines
- Activity 3: Trace a Cookie Cutter
- Activity 4: Import and Extrude Line Drawings in TinkerCAD
- Activity 1: Break Three Dimensions Into Two
- Activity 2: Create the Front and Profile Views
- Activity 3: Modify Parts for Interconnectivity
- Activity 1: Create Common Gears
- Activity 2: Assemble Gears into a Functional Device
- Activity 3: Modify Print Settings for Functional Parts
- Activity 1: Badge / Medallion
- Activity 2: Bookmarks
- Activity 3: Bracelets
- Activity 4: Light Box
- Activity 5: Marble Roller Coaster
- Activity 6: Construction Set
- Activity 7: Minecraft Export
- Print length 46 pages
- Language English
- Publication date April 16, 2017
- Dimensions 8.5 x 0.11 x 11 inches
- ISBN-10 1537562029
- ISBN-13 978-1537562025
- See all details

Product details
- Publisher : CreateSpace Independent Publishing Platform (April 16, 2017)
- Language : English
- Paperback : 46 pages
- ISBN-10 : 1537562029
- ISBN-13 : 978-1537562025
- Item Weight : 6.1 ounces
- Dimensions : 8.5 x 0.11 x 11 inches
- #1,234 in STEM Education
Customer reviews
Customer Reviews, including Product Star Ratings help customers to learn more about the product and decide whether it is the right product for them.
To calculate the overall star rating and percentage breakdown by star, we don’t use a simple average. Instead, our system considers things like how recent a review is and if the reviewer bought the item on Amazon. It also analyzed reviews to verify trustworthiness.
No customer reviews
- Amazon Newsletter
- About Amazon
- Accessibility
- Sustainability
- Press Center
- Investor Relations
- Amazon Devices
- Amazon Science
- Sell on Amazon
- Sell apps on Amazon
- Supply to Amazon
- Protect & Build Your Brand
- Become an Affiliate
- Become a Delivery Driver
- Start a Package Delivery Business
- Advertise Your Products
- Self-Publish with Us
- Become an Amazon Hub Partner
- › See More Ways to Make Money
- Amazon Visa
- Amazon Store Card
- Amazon Secured Card
- Amazon Business Card
- Shop with Points
- Credit Card Marketplace
- Reload Your Balance
- Amazon Currency Converter
- Your Account
- Your Orders
- Shipping Rates & Policies
- Amazon Prime
- Returns & Replacements
- Manage Your Content and Devices
- Recalls and Product Safety Alerts
- Conditions of Use
- Privacy Notice
- Consumer Health Data Privacy Disclosure
- Your Ads Privacy Choices
How to solve problems with design thinking
May 18, 2023 Is it time to throw out the standard playbook when it comes to problem solving? Uniquely challenging times call for unique approaches, write Michael Birshan , Ben Sheppard , and coauthors in a recent article , and design thinking offers a much-needed fresh perspective for leaders navigating volatility. Design thinking is a systemic, intuitive, customer-focused problem-solving approach that can create significant value and boost organizational resilience. The proof is in the pudding: From 2013 to 2018, companies that embraced the business value of design had TSR that were 56 percentage points higher than that of their industry peers. Check out these insights to understand how to use design thinking to unleash the power of creativity in strategy and problem solving.
Designing out of difficult times
What is design thinking?
The power of design thinking
Leading by design
Author Talks: Don Norman designs a better world
Are you asking enough from your design leaders?
Tapping into the business value of design
Redesigning the design department
Author Talks: Design your future
A design-led approach to embracing an ecosystem strategy
More than a feeling: Ten design practices to deliver business value
MORE FROM MCKINSEY
How design helps incumbents build new businesses
Featured Topics
Featured series.
A series of random questions answered by Harvard experts.
Explore the Gazette
Read the latest.
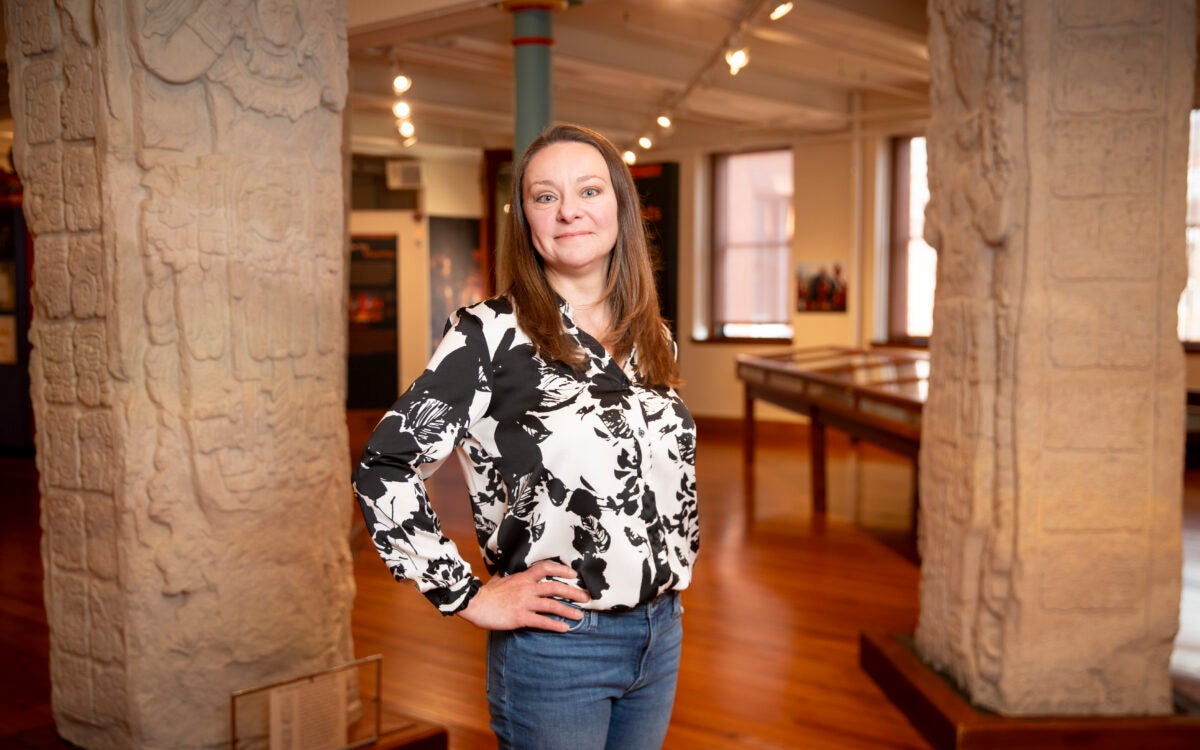
‘I haven’t really had a proper weekend in a long time’
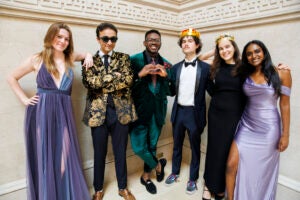
Party like it’s 2020
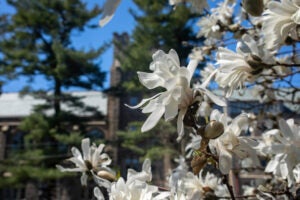
Study of Psychedelics in Society and Culture announces funding recipients
‘you can solve anything’.
Priyanka Pillai wants to take on big problems — and has learned how good design can help
Christina Pazzanese
Harvard Staff Writer
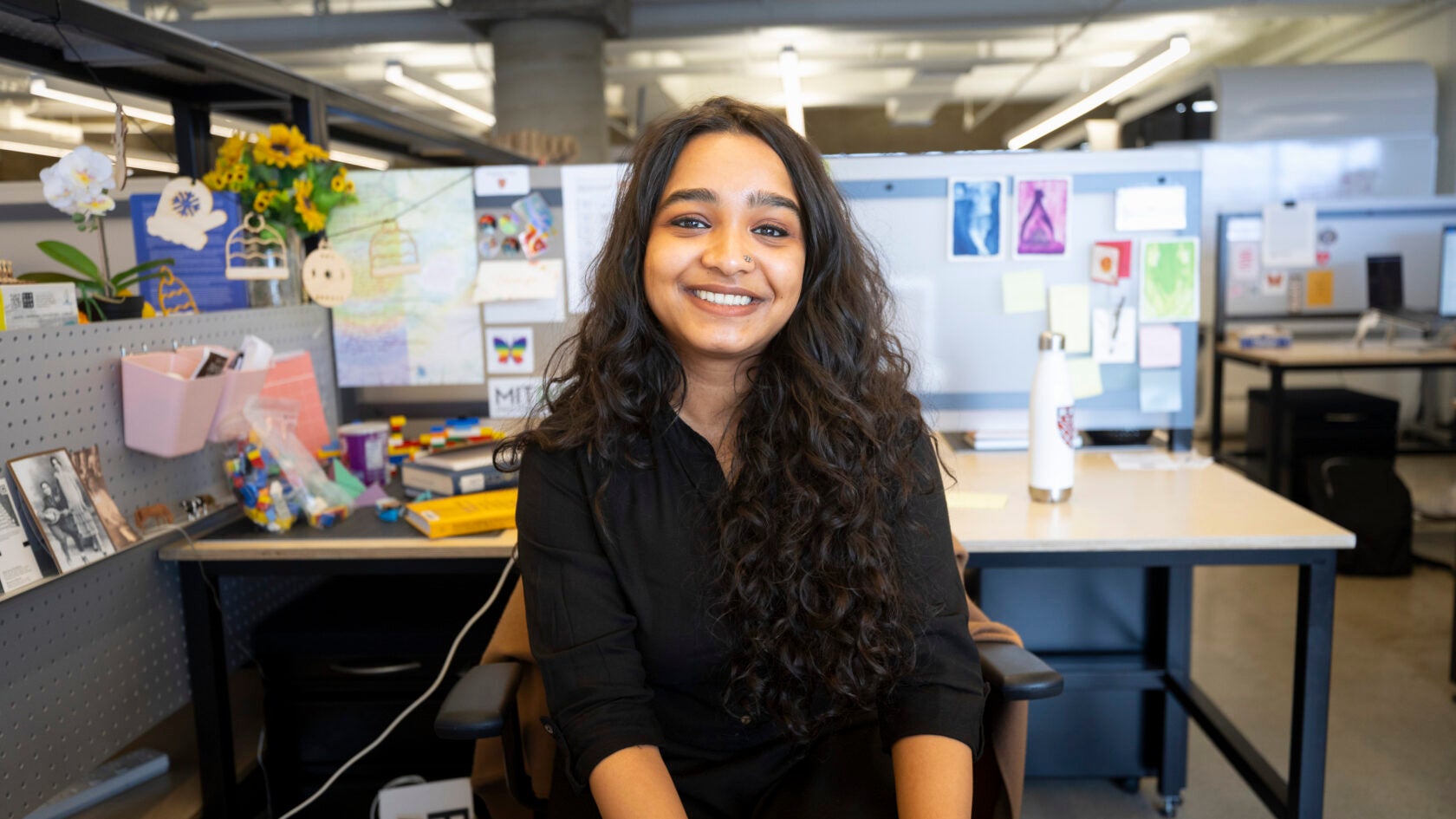
Niles Singer/Harvard Staff Photographer
Part of the Commencement 2024 series
A collection of stories covering Harvard University’s 373rd Commencement.
Growing up in India, Priyanka Pillai witnessed the immense and varied struggles many impoverished people faced in their daily lives, such as getting prenatal care and protecting children from labor exploitation.
As an undergraduate in Bangalore studying industrial design, she wondered whether good design could help ease at least parts of these and other challenges. She came to Harvard Graduate School of Design two years ago and got her answer, discovering she could take on big problems “that you don’t even realize … could be tackled with design.”
Pillai wanted to do something to help address the refugee crisis in Uganda for her independent design engineering project. Those projects span two semesters and call for students seeking a master’s in design engineering (a joint GSD and John A. Paulson School of Engineering and Applied Sciences program) to identify complex, real-world problems and develop solution prototypes.
“For the first time, I truly felt like I was doing work that was very in touch with what GSD wants people to do, which is working with communities.”
Conducting fieldwork in Uganda, Pillai saw the difficulties that South Sudanese refugees were having reuniting with their families. The plight of those fleeing the ongoing civil war in the northeast African nation has become one of the largest refugee crises in the world, with more than half a million living in Uganda alone, mostly in camps.
More than 60 percent are children separated from parents who are looking for them, Pillai said, and need multiple layers of support. While non-governmental organizations (NGOs) are providing some assistance, much more help is needed.
“One thing that really stood out was agency. There’s currently a lack of agency when it comes to finding their family members on their own,” said Pillai, who graduates later this month. Many refugees use informal, ad hoc methods such as phone calls, WhatsApp, and photo sharing to try to find relatives.
“The second part, which is extremely critical, is that we need to move from a Western-centric way of finding a family member,” such as cataloguing names, ages, and date of separation done by NGOs, because it doesn’t capture vernacularor local geography, vital details that may speed up reunification, she said, noting that learning more about how to design for “the Indian context” and the Global South more generally was a key reason she came to Harvard.
“A lot of cultural nuances were missing in connection to the data to find missing family members,” she said. “And that’s the kind of solution that we’re moving toward.”
Given the ubiquity of cellphones there, Pillai and classmate Julius Stein designed and built an online platform for refugees to enter information about themselves using text, photos, and audio. The platform generates a series of questions that can lead to possible matches while minimizing the risk of exploitation by malign actors.
“For the first time, I truly felt like I was doing work that was very in touch with what GSD wants people to do, which is working with communities,” she said. “It was just a life-changing experience.”
Earlier this month, one startup Pillai is involved in, Alba, won an Ingenuity Award as part of the Harvard President’s Innovation Challenge. The team designed a special wipe so the visually impaired can better detect when their menstrual period has begun without relying on outside assistance.
In 2023, Pillai was part of a student project that won gold in the Spark International Design awards. The design team created Felt, a haptic armband that turns sound and visual clues into movement. The device assists people who are deaf blind to independently catch emotional nuances or subtexts in conversations, which often get lost in Braille or other translations.
During her time in the program, Pillai also jumped at the opportunity to take courses at the Harvard Kennedy School, Harvard Law School, and Harvard Graduate School of Education to learn more about things such as accessibility, ethical design, and negotiation.
“I knew that I was limiting myself because I didn’t know all these different things,” she said.
When not focused on her own studies, Pillai has been a teaching fellow for a design studio at GSD and at SEAS for a course led by her IDEP adviser, Krzysztof Gajos, Gordon McKay Professor of Computer Science.
“I love teaching,” she said. “It’s one of my favorite experiences.”
Reflecting on her time at GSD, Pillai has been deeply inspired by the faculty and her fellow students. This group from many different backgrounds with different interests and perspectives, working in many different disciplines, has been like a “dream” design studio where she’s been able to share and borrow ideas and practices from others and see how other fields look at things such as collaboration, sustainability and accessibility. It has been intellectually liberating to experience such fearlessness, she said, after years of feeling so “constrained” in her prior practice, which had been “rooted in ‘realistic goals.’”
“People tackling very huge issues that you don’t even realize 1) is a problem that could be tackled with design, and 2), they’re almost your age and they’re doing it somehow. That was very important to see,” she said.
“People really think that you can solve anything.”
Share this article
Also in this series:.
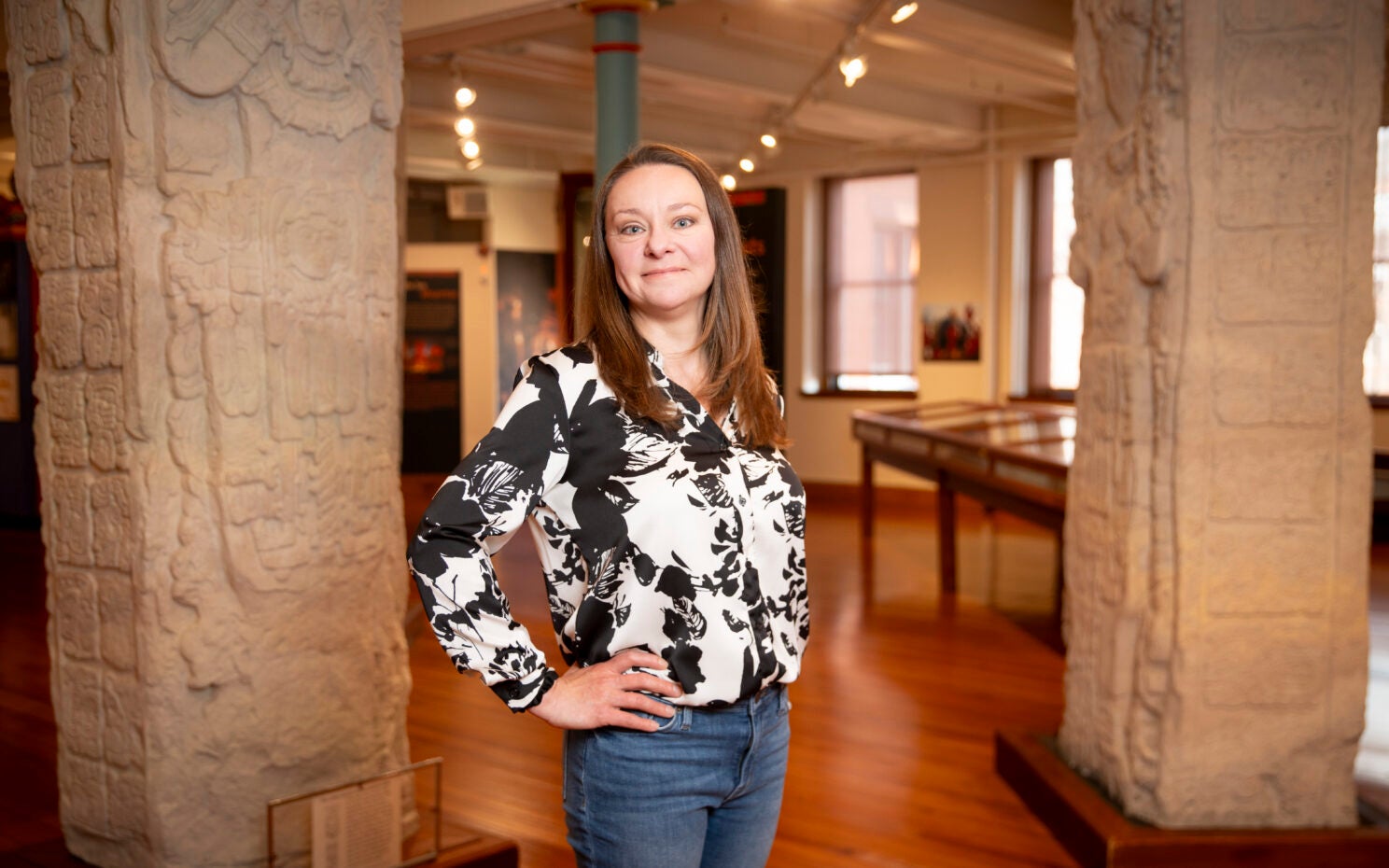
Longtime supporter of grads Kathy Hanley caps 13-year quest with a Commencement of her own
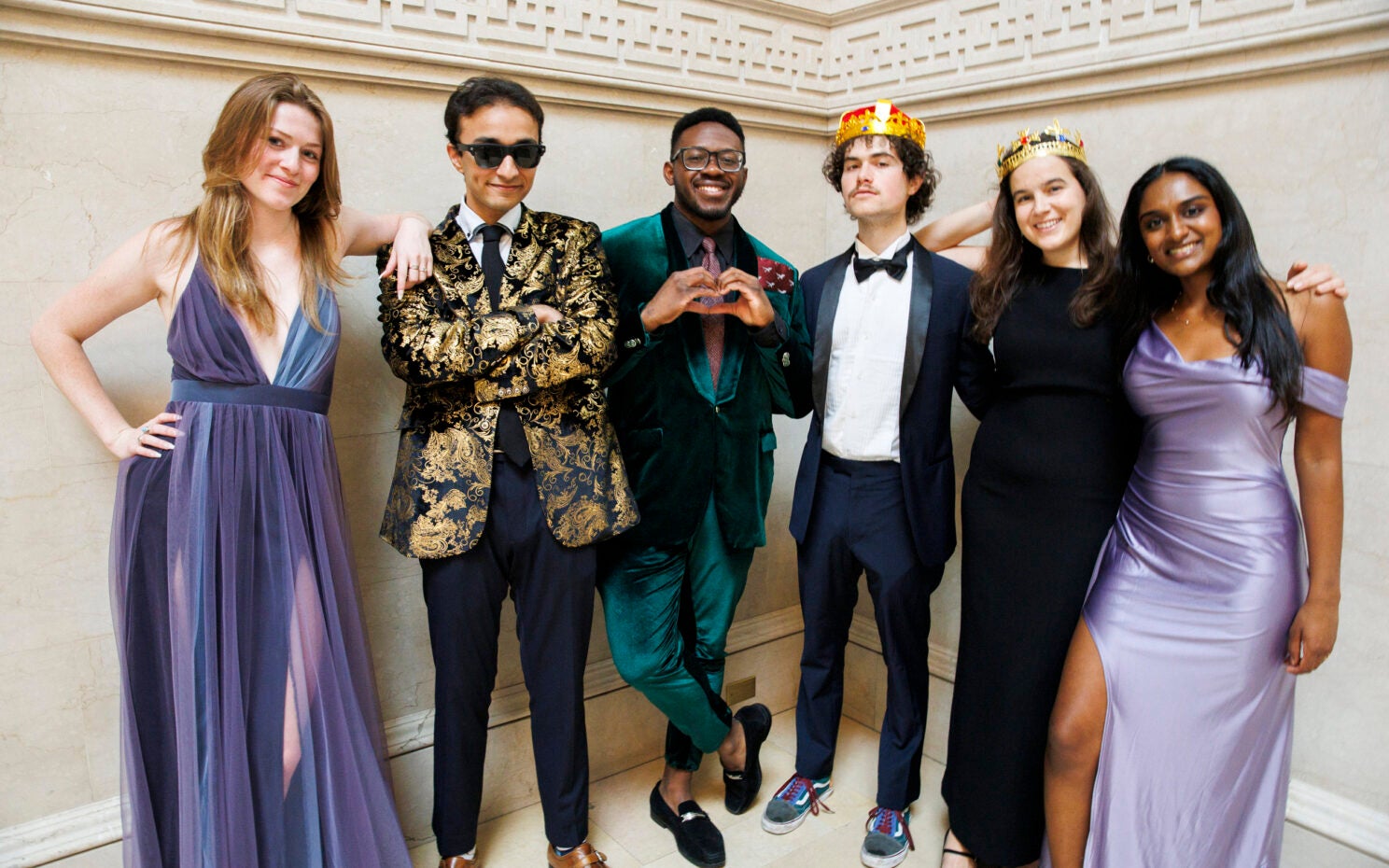
Class of ’24 gets a do-over on high school prom that pandemic took away

‘I was frustrated, infuriated, because women are just as capable’
Experiences in Uganda and U.S. fuel Ananda Birungi’s passion for empowering others, especially women and girls
You might like

Three major events, including Psychedelics Bootcamp 2024, to be hosted over summer
Epic science inside a cubic millimeter of brain
Researchers publish largest-ever dataset of neural connections
Pop star on one continent, college student on another
Model and musician Kazuma Mitchell managed to (mostly) avoid the spotlight while at Harvard
Finding right mix on campus speech policies
Legal, political scholars discuss balancing personal safety, constitutional rights, academic freedom amid roiling protests, cultural shifts
To read this content please select one of the options below:
Please note you do not have access to teaching notes, topological optimization in 3d-magnetostatics: development of adjoint methods using the equations of magnetic moments.
COMPEL - The international journal for computation and mathematics in electrical and electronic engineering
ISSN : 0332-1649
Article publication date: 17 May 2024
The purpose of this paper is mainly to develop the adjoint method within the method of magnetic moment (MMM) and thus, to provide an efficient new way to solve topology optimization problems in magnetostatic to design 3D-magnetic circuits.
Design/methodology/approach
First, the MMM is recalled and the optimization design problem is reformulated as a partial derivative equation-constrained optimization problem where the constraint is the Maxwell equation in magnetostatic. From the Karush–Khun–Tucker optimality conditions, a new problem is derived which depends on a Lagrangian parameter. This problem is called the adjoint problem and the Lagrangian parameter is called the adjoint parameter. Thus, solving the direct and the adjoint problems, the values of the objective function as well as its gradient can be efficiently obtained. To obtain a topology optimization code, a semi isotropic material with penalization (SIMP) relaxed-penalization approach associated with an optimization based on gradient descent steps has been developed and used.
In this paper, the authors provide theoretical results which make it possible to compute the gradient via the continuous adjoint of the MMMs. A code was developed and it was validated by comparing it with a finite difference method. Thus, a topology optimization code associating this adjoint based gradient computations and SIMP penalization technique was developed and its efficiency was shown by solving a 3D design problem in magnetostatic.
Research limitations/implications
This research is limited to the design of systems in magnetostatic using the linearity of the materials. The simple examples, the authors provided, are just done to validate our theoretical results and some extensions of our topology optimization code have to be done to solve more interesting design cases.
Originality/value
The problem of design is a 3D magnetic circuit. The 2D optimization problems are well known and several methods of resolution have been introduced, but rare are the problems using the adjoint method in 3D. Moreover, the association with the MMMs has never been treated yet. The authors show in this paper that this association could provide gains in CPU time.
- Optimization
- Sensitivity analysis
- Numerical methods
- Method of magnetic moments
- Volume integral method
Acknowledgements
Funding : This work was supported by ANR – French Research National Agency (ANR-21-CE05-0001-01).
Michel, S. , Messine, F. and Poirier, J.-R. (2024), "Topological optimization in 3D-magnetostatics: development of adjoint methods using the equations of magnetic moments", COMPEL - The international journal for computation and mathematics in electrical and electronic engineering , Vol. ahead-of-print No. ahead-of-print. https://doi.org/10.1108/COMPEL-10-2023-0533
Emerald Publishing Limited
Copyright © 2024, Emerald Publishing Limited
Related articles
We’re listening — tell us what you think, something didn’t work….
Report bugs here
All feedback is valuable
Please share your general feedback
Join us on our journey
Platform update page.
Visit emeraldpublishing.com/platformupdate to discover the latest news and updates
Questions & More Information
Answers to the most commonly asked questions here
Novel quantum algorithm proposed for high-quality solutions to combinatorial optimization problems
C ombinatorial optimization problems (COPs) have applications in many different fields such as logistics, supply chain management, machine learning, material design and drug discovery, among others, for finding the optimal solution to complex problems. These problems are usually very computationally intensive using classical computers and thus solving COPs using quantum computers has attracted significant attention from both academia and industry.
Quantum computers take advantage of the quantum property of superposition, using specialized qubits, that can exist in an infinite yet contained number of states of 0 or 1 or any combination of the two, to quickly solve large problems. However, when COPs involve constraints, conventional quantum algorithms like adiabatic quantum annealing struggle to obtain a near-optimal solution within the operation time of quantum computers.
Recent advances in quantum technology have led to devices such as quantum annealers and gate-type quantum devices that provide suitable platforms for solving COPs. Unfortunately, they are susceptible to noise, which limits their applicability to quantum algorithms with low computational costs.
To address this challenge, Assistant Professor Tatsuhiko Shirai and Professor Nozomu Togawa from the Department of Computer Science and Communications Engineering at Waseda University in Japan have recently developed a post-processing variationally scheduled quantum algorithm (pVSQA). Their study was published in the journal IEEE Transactions on Quantum Engineering .
"The two main methods for solving COPs with quantum devices are variational scheduling and post-processing. Our algorithm combines variational scheduling with a post-processing method that transforms infeasible solutions into feasible ones, allowing us to achieve near-optimal solutions for constrained COPs on both quantum annealers and gate-based quantum computers," explains Dr. Shirai.
The innovative pVSQA algorithm uses a quantum device to first generate a variational quantum state via quantum computation. This is then used to generate a probability distribution function which consists of all the feasible and infeasible solutions that are within the constraints of the COP.
Next, the post-processing method transforms the infeasible solutions into feasible ones, leaving the probability distribution with only feasible solutions. A classical computer is then used to calculate an energy expectation value of the cost function using this new probability distribution. Repeating this calculation results in a near-optimal solution.
The researchers analyzed the performance of this algorithm using both a simulator and real quantum devices such as a quantum annealer and a gate-type quantum device. The experiments revealed that pVSQA achieves a near-optimal performance within a predetermined time on the simulator and outperforms conventional quantum algorithms without post-processing on real quantum devices.
Dr. Shirai said, "Drastic social transformations are urgently needed to address various social issues. Examples include the realization of a carbon-neutral society to solve climate change issues and the realization of sustainable development goals to address issues such as increased energy demand and food shortage.
"Efficiently solving combinatorial optimization problems is at the heart of achieving these transformations. Our new method will play a significant role in realizing these long-term social transformations."
In conclusion, this study marks a significant step forward for using quantum computers for solving COPs, holding promise for addressing complex real-world problems across various domains.
More information: Tatsuhiko Shirai et al, Post-Processing Variationally Scheduled Quantum Algorithm for Constrained Combinatorial Optimization Problems, IEEE Transactions on Quantum Engineering (2024). DOI: 10.1109/TQE.2024.3376721
Provided by Waseda University
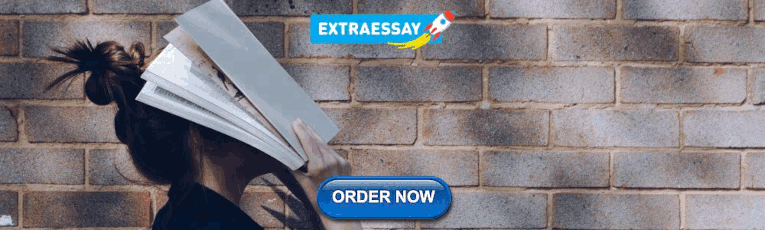
IMAGES
VIDEO
COMMENTS
Whether you are participating in a hackathon, a contest, or a project-based learning activity, 3D design can help you showcase your skills, creativity, and problem-solving abilities. However, 3D ...
The simplicity and precision lay the groundwork for more complex 3D models ensuring a smoother process for problem solving endeavours. The key software that Twenty20 Engineering uses for 2D CAD are, AutoCAD and Draftsight. We also use the 2D draughting tools within SolidWorks and SMAP3D, depending on the nature of the project and industry sector.
2. Project: Invent an object that solves a problem in your morning routine: The project for this class is to design a single function object to solve a problem that you observe in real life. Product design is this way of intervening in the physical world, so that you can make improvements and we've all complained about how something works ...
Problem-solving and Critical Thinking: Developing problem-solving and critical thinking skills will help you overcome challenges that arise during the 3D design process. It involves troubleshooting issues, optimizing resources, and finding creative solutions to achieve desired outcomes.
A great way to begin a 3D printing unit is to start a design challenge using a 3D printer. Design Challenge 101 (a quick refresher) A design challenge is an open-ended project that encourages students to ask questions, take the initiative, and think creatively. With a design challenge, teachers can engage students in problem-solving ...
See how members of the Design Girls Team at Brookwood School use 3D printing to solve problems for people in their community.For more videos, activities and ...
At Makers Empire we see lots of great examples of teachers integrating 3D design and printing into different curriculum areas. Here are our top ten design challenge ideas for integrating mathematics with 3D design. 1. Use Makers Empire's Blocker Module to create shapes and designs that have specific perimeters.
Designers are spending a lot less time ideating with 2D mediums in favour of working with immersive technology. 3D sketching has enabled a faster and more creative design pipeline. Designers are creating more unique and compelling designs through the use of Gravity Sketch at the early stages of their process. Max. January 11, 2021.
How students can work together in teams to design and create 3D-printed projects, promoting communication, teamwork, and problem-solving abilities. Additionally, discover how the skills acquired through 3D modeling and printing, such as digital literacy and design thinking, prepare students for future careers in fields such as engineering ...
Table of contents. What are the 5 Stages of the Design Thinking Process. Stage 1: Empathize—Research Your Users' Needs. Stage 2: Define—State Your Users' Needs and Problems. Stage 3: Ideate—Challenge Assumptions and Create Ideas. Stage 4: Prototype—Start to Create Solutions. Stage 5: Test—Try Your Solutions Out.
Step 2: Class discussion to identify and define a problem (5 minutes) Step 3: Brainstorm possible ideas for solving the problem (5 minutes) Step 4: Design a solution for the problem using Makers Empire (30 minutes) Step 5: Students share their designed solutions and give each other feedback. (10 minutes) Use the provided Fairy Tale worksheet ...
Tomorrow's innovators are made today. At Autodesk, we empower innovators everywhere to take the problems of today and turn them into something amazing. Start Tinkering Join Class. 3D design Design for problem solving created by Isaac Albenio with Tinkercad.
This chapter explores the use of Prototype Problem-Solving Activities and 3D printing (PPSA) as a curricular tool to develop mathematical understanding, creativity, and technological literacy. ... Students in this study used augmented reality and 3D software to design and present ideas for urban development. Students and the public expressed ...
In solving descriptive geometry (DG) problems, board (i.e., hand drawing) methods are frequently used, despite this discipline is still very important to enhance spatial vision. These methods are very different from CAD tools which are used in the field of design. CAD facilitates the realization of geometric constructions and transformations (i.e., rotation, translation, copying, scaling ...
Using TRIZ in 3D graphics can have many benefits, such as enabling you to solve design problems faster and easier, improve the quality and efficiency of your 3D graphics, and enhance your ...
The term "Design Thinking" dates back to the 1987 book by Peter Rowe; "Design Thinking." In that book he describes the way that architects and urban planners would approach design problems. However, the idea that there was a specific pattern of problem solving in "design thought" came much earlier in Herbert A Simon's book, "The Science of the Artificial" which was published ...
It was important for us to understand the flat-packing, the assembly, and the modularity of the carts, so we 3D printed a model. The model allowed us to play with the design concept to get the size of the package down to its minimum, and the design of the cart to its most useful, and modular state. The 3D print also helped in communicating the ...
Solving Real-World Problems with 3D Printing. In today's blog we're going to look at 3 interesting ways that 3D printing can be used in education to solve real-world problems. Each example looks at a particular global challenge, before we explain how we envisage students taking on the challenges with the use of 3D technologies.
3D printing can do much more than create action figures! Based on successful programming in schools, libraries, and community centers, this guide explores free and flexible projects integrating science, technology, engineering, art, and mathematics.
The proof is in the pudding: From 2013 to 2018, companies that embraced the business value of design had TSR that were 56 percentage points higher than that of their industry peers. Check out these insights to understand how to use design thinking to unleash the power of creativity in strategy and problem solving. Designing out of difficult times.
3. Prototype and test. 4. Present and communicate. 5. Showcase your personality. 6. Update and improve. If you want to showcase your 3D design skills and impress potential clients or employers ...
1. Introduction. In this paper, we focus on solving the 3D-PP using deep reinforcement learning (DRL), which has received widespread attention due to its efficiency to solve advanced real-world challenges. 3D-PP is a classical and important combinatorial optimization problem, which has a wide range of applications in the cutting and packing industry, e.g., when cutting wood or foam rubber into ...
As an undergraduate in Bangalore studying industrial design, she wondered whether good design could help ease at least parts of these and other challenges. She came to Harvard Graduate School of Design two years ago and got her answer, discovering she could take on big problems "that you don't even realize … could be tackled with design.".
The problem of design is a 3D magnetic circuit. The 2D optimization problems are well known and several methods of resolution have been introduced, but rare are the problems using the adjoint method in 3D. Moreover, the association with the MMMs has never been treated yet.
Combinatorial optimization problems (COPs) have applications in many different fields such as logistics, supply chain management, machine learning, material design and drug discovery, among others ...