55 Process Improvement Case Studies & Project Results [2024]

Cem is the principal analyst at AIMultiple since 2017. AIMultiple informs hundreds of thousands of businesses (as per Similarweb) including 60% of Fortune 500 every month.
Cem's work focuses on how enterprises can leverage new technologies in AI, automation, cybersecurity(including network security, application security), data collection including web data collection and process intelligence.
![process improvement case study examples 55 Process Improvement Case Studies & Project Results [2024]](https://research.aimultiple.com/wp-content/uploads/2020/06/process-improvement-case-studies-382x215.png.webp)
Business leaders know that process improvement reduces costs and increases customer satisfaction. Therefore, businesses follow process improvement methodologies or deploy tools such as process modeling, process mining and RPA to discover, modify and automate their processes. However, it can be difficult for process experts and business analysts to understand the different process improvement approaches and the results they should expect.
Read our process improvement approaches guide for a categorization of process improvement approaches so you can rely on a framework to structure your process improvement initiatives. In this article, we share typical process improvement project results and case studies. Our aim is to provide benchmarks so business analysts and leaders can set targets for their own initiatives.
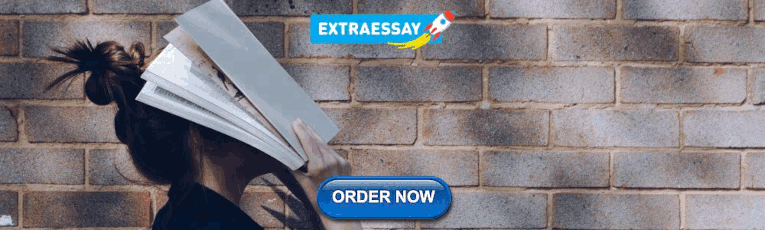
What are the typical project results?
Process improvement solutions help businesses define weaknesses and take action to solve these problems. In the case studies we collected, the most common project results that we came across are as follows:
1- Improved efficiency: Most businesses increase the efficiency of their processes by adapting process improvement methodologies. After defining their problems, companies eliminate unnecessary steps in processes, reduce their costs, and shorten process times. As a result, they achieve faster processes and higher quality output with fewer resources.
For example, in a process mining case study, a manufacturer leveraged a process mining software to analyze the procure-to-pay processes. It is claimed that the manufacturer could:
- Reduce maverick buying and saved $60,000 in reworking cost by detecting and managing deviations, mismatches and early payments.
- Improve purchase order and invoice processes by automating 75% of line creation and delivery activities. As a result, the company decreased the invoice registration and approval time.
2- Enhanced customer satisfaction: The increasing quality of output and faster processes can also reflect on customer satisfaction. Process improvement solutions help businesses reduce waiting time and focus on customer value. For example, it is claimed that by adopting the Kaizen methodology, Tata Steel has shortened its response time and delivered more on-time orders to its customers. 1
3- Harmonization of different teams/processes: For large companies, handling different processes simultaneously can be a big challenge. Teams should be informed about what others do, and processes need to work in sync to avoid problems. With process improvement solutions, businesses can have a full understanding of all their companies and align different processes successfully.
Here is an extended list of case studies which are collected from different resources. You can filter the list by the process improvement solution, service provider, industry, or process and investigate the achieved results.
Further Reading
If you want to learn more on process improvement, these articles can also interest you:
- Process Improvement: In-depth Guide for Businesses
- Lean Process Improvement Guide for Your Business
Check out comprehensive and constantly updated list of process mining case studies to process mining real-life examples and compare them to process improvement case studies.
If you want to manage and improve your processes, check out our data-driven and up-to-date list of vendors for:
- Workflow management software
- Business process management software
- Low-code/No-code development platform
- Onboarding software
- Process mining
- Business process automation software
If you still have questions about process improvement, we would like to help:
External Links
- 1. “ Process Improvement – A continuing initiative .” Tata Steel . 2008. Retrieved at May 17, 2024.

Cem's work has been cited by leading global publications including Business Insider, Forbes, Washington Post, global firms like Deloitte, HPE, NGOs like World Economic Forum and supranational organizations like European Commission. You can see more reputable companies and media that referenced AIMultiple.
Cem's hands-on enterprise software experience contributes to the insights that he generates. He oversees AIMultiple benchmarks in dynamic application security testing (DAST), data loss prevention (DLP), email marketing and web data collection. Other AIMultiple industry analysts and tech team support Cem in designing, running and evaluating benchmarks.
Throughout his career, Cem served as a tech consultant, tech buyer and tech entrepreneur. He advised enterprises on their technology decisions at McKinsey & Company and Altman Solon for more than a decade. He also published a McKinsey report on digitalization.
He led technology strategy and procurement of a telco while reporting to the CEO. He has also led commercial growth of deep tech company Hypatos that reached a 7 digit annual recurring revenue and a 9 digit valuation from 0 within 2 years. Cem's work in Hypatos was covered by leading technology publications like TechCrunch and Business Insider.
Cem regularly speaks at international technology conferences. He graduated from Bogazici University as a computer engineer and holds an MBA from Columbia Business School.
AIMultiple.com Traffic Analytics, Ranking & Audience , Similarweb. Why Microsoft, IBM, and Google Are Ramping up Efforts on AI Ethics , Business Insider. Microsoft invests $1 billion in OpenAI to pursue artificial intelligence that’s smarter than we are , Washington Post. Data management barriers to AI success , Deloitte. Empowering AI Leadership: AI C-Suite Toolkit , World Economic Forum. Science, Research and Innovation Performance of the EU , European Commission. Public-sector digitization: The trillion-dollar challenge , McKinsey & Company. Hypatos gets $11.8M for a deep learning approach to document processing , TechCrunch. We got an exclusive look at the pitch deck AI startup Hypatos used to raise $11 million , Business Insider.
To stay up-to-date on B2B tech & accelerate your enterprise:
Next to Read
What is process workflow & top 4 benefits & case studies in '24, how to implement process improvement in 6 steps in 2024, process improvement technology: 4 best tools to know in '24.
Your email address will not be published. All fields are required.
Hi Cem, Thank you ver much for your interesting article. I am interested in getting a deeper look into some of the case studies: How exactly did they approach the problem? ….Would it be possible to get a closer look at the case studies? Thanks in advance. Adrian
Hi Adrian, please feel free to get in touch with us via [email protected] . Happy to discuss these in more detail once we know which types of case studies you are interested in
Related research
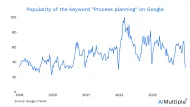
3 Steps to Follow for a Successful Process Planning in '24
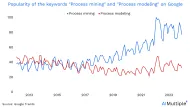
Process Mining vs Process Modeling in '24: 4 Best Practices

55 Process Improvement Case Studies & Project Results [2023]

Hi there! As a data analyst and AI professional, I wanted to share a comprehensive look at 55 process improvement case studies and their results. Optimizing business processes is essential for reducing costs, boosting quality, and improving customer satisfaction.
In this guide, we‘ll explore real-world examples of process improvement across industries. My goal is to provide you with detailed case studies so you can use them as benchmarks for your own projects. Let‘s dive in!
What Typical Results Should You Expect?
Before looking at individual cases, it‘s helpful to understand the most common benefits of process improvement:
- Increased Efficiency: Streamlining processes lets companies do more with less. For example, a manufacturer used process mining to cut invoice approval time and automated 75% of activities.
- Higher Quality: With smoother flows, there‘s less room for errors. A chemicals firm reduced defects by 70% after process optimization.
- Enhanced Customer Satisfaction: Faster throughput and fewer mistakes boost customer loyalty. An insurer‘s process work shortened response times and increased on-time case resolutions by 42%.
- Cost Savings: Eliminating waste and paperwork reduces expenses. A telecom achieved $2.3 million in annual savings through an RPA initiative.
Overview of 55 Process Improvement Case Studies

Manufacturing – Improving Production Processes
Manufacturers can leverage solutions like Lean Six Sigma to optimize production and supply chain processes.
For example, Lockheed Martin aimed to reduce its environmental footprint and costs. By focusing on eliminating non-value-added work, it decreased facility size by 33% and chemical storage to just 2% of original size. These lean initiatives saved enormously on real estate and hazardous waste expenditures.
Another manufacturing firm, 3M, recycled and reused waste materials rather than disposing them. This lean approach saved around $30 million annually in waste costs.
Across industries, remember that small efficiencies compound. 3M‘s CEO once stated: “Most of our products emerge from somebody’s idea about how to do something simpler, better, or cheaper.”
Healthcare – Boosting Patient Experience
In healthcare, accurate and timely processing of records is critical. Process improvement helps hospitals handle patient data more efficiently.
At University Hospitals Birmingham NHS Trust, automated self-check-in kiosks were implemented. This robotic process automation initiative reduced check-in time from 15 minutes to under 5 minutes. Patients could check-in quickly and accurately, improving their experience.
Meanwhile, BMC HealthNet Plan applied lean principles to claims processing. This increased claims processing accuracy from 93% to 99.7%. With fewer erroneous claims, patients received faster and more accurate service.
Banking – Accelerating Lending Decisions
Banks can struggle with long wait times for lending decisions. Process mining helps identify and eliminate inefficiencies in lending processes.
VTB Bank in Russia used process mining to cut application decision time from 14 days to 5 days. The percentage of timely handled loan applications also increased from 68% to 98%.
Another financial institution, BridgeLoan, reduced total loan processing time by 40% after process improvements. Applicants received faster decisions, improving customer satisfaction.
Across banking, optimizing processes around customer applications can significantly impact customer lifetime value.
Professional Services – Improving Delivery
Client work in professional services firms involves many interdependent processes. Consultancies like EY have applied RPA to coordinate projects better.
For EY, bots automated the process of reminding staff to book travel for upcoming client meetings. This initiative reduced manual effort by 50% while cutting airfare costs by 20% through early booking.
Meanwhile, enterprise giant Microsoft applied Six Sigma principles to sales and service processes. Fine-tuning these workflows reduced defects and enabled data-driven insights around optimal customer segmentation.
15 More Impactful Case Studies
Here are some additional examples that showcase process improvement results across sectors:
- Retail: Starbucks used lean principles to reduce customer waiting times in stores and speed up ordering.
- Energy: Synergy generated $2.3M in savings annually through RPA in its billing processes.
- Pharma: A global pharma optimized artwork management processes, improving coordination between countries.
- Construction: Afrisam implemented process mining for risk management, achieving real-time visibility.
- Food & Beverage: Kahiki Foods‘ lean program dropped production waste by 70% in months.
- Transport: Deutsche Bahn optimized rail freight through BPM, cutting logistical costs.
- Telecom: By mining processes, Nokia identified lead time improvements and training needs.
- Technology: Dell applied RPA in finance processes, saving $2M annually.
- Automotive: Mercedes Benz‘ kaizen approach reduced manufacturing time per vehicle by 10-20%.
- Aerospace: Lean initiatives helped Lockheed Martin consolidate facilities and slash chemical waste.
- Oil & Gas: Chevron‘s Six Sigma program targeted high-cost equipment failures, saving millions.
- Utilities : Alliander increased purchasing process efficiency with process mining.
- Insurance: Aegon‘s Lean Six Sigma initiative stopped £20M spend on external contractors.
- Media: The BBC sped up program preview creation through RPA bots.
- NGO: World Vision improved performance evaluation with optimized processes.
The data shows that process gains can have truly enterprise-wide benefits regardless of sector.
6 More In-Depth Case Studies
Let‘s look at a few case studies more closely to better understand how companies achieved process improvements:
1. AkzoNobel – Chemicals Company
- Initiative: Process mining to identify procurement inefficiencies
- Processes: P2P, AP, O2C
- Results: Cut manual work by 18%, improved supplier efficiency from 40% to 70%, reduced costs
AkzoNobel is a chemicals company that supplies paints, coatings and specialty chemicals globally. By using process mining, AkzoNobel analyzed its procure-to-pay, accounts payable and order-to-cash processes end-to-end.
Process mining revealed that 18% of activities required manual interventions. These bottlenecks caused delays and additional labor costs. In addition, only 40% of procurement engagements were happening through the preferred supplier program.
Leveraging these process insights, AkzoNobel automated more activities through RPA bots. It also expanded the preferred supplier program adoption to over 70%, increasing bargaining power and reducing maverick buying.
In total, the process optimization efforts reduced operational costs by millions annually while significantly improving efficiency.
2. Bancolombia – Financial Services Company
- Initiative: RPA implementation in back-office
- Processes: HR, accounting, customer service
- Results: Reduced labor and errors, improved compliance accuracy
Bancolombia is a leading Latin American financial services provider. It implemented RPA to eliminate repetitive and manual back-office processes across departments like HR, accounting, and customer service.
Over 200 bots now handle more than 50 processes across the company. This improved efficiency by automating tedious tasks such as data validation, report generation and file consolidations.
Interestingly, Bancolombia also used RPA bots to validate that allmanual processes were following proper compliance and control protocols. This boosted compliance accuracy across the back-office to over 97%.
By tapping into RPA, Bancolombia accelerated growth by managing higher transaction volumes without proportional headcount increases.
3. Mercedes Benz – Automotive Manufacturer
- Initiative: Kaizen and lean manufacturing
- Processes: Production
- Results: Reduced manufacturing time per vehicle by 10-20%, 3x increase in production flexibility
Mercedes Benz‘ Brazil factory was facing long manufacturing times and rigidity in responding to custom orders. By adopting kaizen principles, the company empowered shop floor teams to suggest process improvements. Hundreds of small optimizations were implemented – from changing factory layouts to modifying work sequences.
This lean approach reduced manufacturing time per vehicle by 10-20%. Previously, producing custom orders caused delays. But the flexibility tripled from producing 6 variants a day to over 18.
Kaizen and lean manufacturing helped Mercedes Benz shorten lead times and rapidly respond to changing customer demands.
4. Sberbank – Bank in Russia
- Initiative: Process mining for lending
- Processes: Mortgage operations
- Results: Time savings of 41 hours annually per employee
Sberbank is the largest bank in Russia, with millions of consumer and business loans. The bank used process mining technology to analyze processes around mortgage issuance and payments.
The analysis revealed over 400 variations within the core mortgage process. Many of these variations caused unnecessary delays due to additional verification steps.
By standardizing the process variants, Sberbank was able to eliminate numerous redundant checks. Staff productivity rose by 15 minutes per mortgage application, generating an extra 41 working hours annually for employees to focus on value-added work.
This showcases the value of process mining in discovering hidden inefficiencies within complex financial processes.
5. Telefonica 02 – Telecom Company
- Initiative: RPA adoption across GBS department
- Processes: Variety of back-office functions
- Results: Significant reduction in workload, improved speed and quality
Telefonica 02 is a leading UK telecom provider with over 25 million customers. In the Global Business Services (GBS) department, robotic process automation was adopted to handle repetitive back-office tasks.
RPA bots took over 15 critical processes including customer service logging, revenue tracking, dealership administration and commission payments. Bots worked 24/7 and reduced the time of repetitive tasks by half or more in many cases.
Across the department, RPA drove a 15-30% reduction in full-time staff workload. Employees could focus on higher value work. Customer service levels rose with faster response times. And with bots eliminating human error, quality and compliance also improved.
6. Coca-Cola – Food & Beverage Leader
- Initiative: Six Sigma to reduce product defects
- Processes: Production lines
- Results: Defect reductions of 10-15x on average
As a food and beverage leader, product quality is critical for Coca-Cola. By applying Six Sigma principles, the company aimed to minimize defects through process analysis and control.
Coca-Cola implemented Six Sigma statistical control methods like process mapping, root cause analysis, and continuous monitoring. This allowed each production line to identify and proactively eliminate causes of defects.
On average, the production lines achieved a 10-15x reduction in product defects through Six Sigma. And with fewer defects, customer satisfaction rose while waste declined.
These examples demonstrate that Six Sigma process excellence principles can deliver powerful benefits, even at massive global corporations.
Key Takeaways from 55 Process Improvement Case Studies
Let‘s recap the key learnings:
- Results : Efficiency gains, cost savings, higher customer satisfaction and quality are typical
- Methods : Process mining, RPA, Lean and Six Sigma prove valuable across industries
- ROI : Even minor improvements compound over years into major savings
- Mindset : Adopt continuous process excellence, not one-off initiatives
With the right approach, process improvements can benefit companies of any size and sector. The cases also illustrate how poor processes get magnified across large volumes.
Turn Insights into Action
I hope these real-world examples have provided you with ideas and benchmarks to drive process improvements in your organization. Here are my parting thoughts:
- Start small : Don‘t boil the ocean. Focus on high-impact areas first.
- Keep iterating : Process excellence is a journey, not a one-time project.
- Involve teams : Engage staff to identify issues and take ownership of solutions.
- Leverage data : Quantify inefficiencies and improvements to win over leadership.
Feel free to reach out if you need any help applying process improvement approaches like Lean Six Sigma or process mining. I‘m always happy to chat more and provide custom advice for your organization‘s needs.
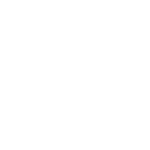
I am Paul Christiano, a fervent explorer at the intersection of artificial intelligence, machine learning, and their broader implications for society. Renowned as a leading figure in AI safety research, my passion lies in ensuring that the exponential powers of AI are harnessed for the greater good. Throughout my career, I've grappled with the challenges of aligning machine learning systems with human ethics and values. My work is driven by a belief that as AI becomes an even more integral part of our world, it's imperative to build systems that are transparent, trustworthy, and beneficial. I'm honored to be a part of the global effort to guide AI towards a future that prioritizes safety and the betterment of humanity.
Similar Posts
Predictive maintenance: what it is, why it matters, and how to do it right.
Equipment breakdowns are every operations manager‘s worst nightmare. The costs of unplanned downtime can completely derail…
The Explosive Rise of ChatGPT Plugins: Use Cases, Opportunities and Risks
ChatGPT by Anthropic has ignited a firestorm of interest in AI chatbots. Its impressive natural language…
Ultimate Guide to Virtual Reality (VR) in 2024: Types & Uses
Hello friend! As a data analyst and AI professional with expertise in emerging technologies, I‘m excited…
Intelligent Automation Tools: Key Features & Top Vendors [2023]
Hi there! With intelligent automation adoption accelerating, you‘re smart to be researching the key capabilities to…
Chat GPT-3 Introduction: The Complete Guide
ChatGPT-3 is a revolutionary artificial intelligence system from OpenAI that has transformed how humans interact with…
Top 6 AI Data Collection Challenges & Solutions in 2024
Hi there, as an experienced data analyst and AI consultant, I wanted to share some key…
- For Small Business
55 Process Improvement Case Studies & Project Results [2023]
- March 17, 2024
- by Terry Tolentino
Introduction
Process improvement is the practice of identifying, analyzing and improving upon existing business processes within an organization to optimize performance. It aims to reduce costs, enhance efficiency, eliminate redundancies, and deliver higher quality outputs. This is achieved by leveraging data and methods to understand root causes and implement targeted solutions.
Adopting process improvement enables organizations to:
- Reduce operational costs through waste and inefficiency elimination
- Improve productivity and output capacity with existing resources
- Streamline process workflows to boost speed and agility
- Standardize processes to minimize errors and defects
- Enhance customer experience and satisfaction
Some key process improvement methodologies and frameworks include:
Lean – Focuses on maximizing value and minimizing waste by removing non-value steps and optimizing flow. Key techniques include value stream mapping, 5S, JIT, etc.
Six Sigma – Follows a DMAIC (define, measure, analyze, improve, control) approach to reduce variations and defects by understanding root causes using statistical tools.
Kaizen – Involves continuous incremental improvements made by workers and cross-functional teams to enhance processes.
Business Process Management (BPM) – Leverages software tools and methods to discover, document, automate, and optimize end-to-end business processes.
Process Mining – Provides visibility into actual processes by extracting event logs from IT systems to create models and identify improvements.
Robotic Process Automation (RPA) – Automates repetitive and rules-based processes by deploying software bots that emulate human actions. Enables huge productivity gains.
This article examines 55 real-world process improvement case studies and their results across diverse companies and industries. The objective is to provide benchmarks and best practices for business leaders and process improvement teams undertaking such initiatives.
The Value of Process Improvement
Process improvement delivers immense value and competitive advantage to organizations. According to Gartner, BPM efforts have resulted in cost reductions of 15-25% and cycle time improvements of 20-40%.
McKinsey estimates that process excellence programs can potentially reduce costs by 20-40%, improve quality by 10-50%, and cut process times by 25-75%.
As per Forrester, RPA implementations yield an ROI of 200-300% with payback periods as short as 3-6 months.
The global business process management market size was valued at USD 14.9 billion in 2021, and is projected to grow at a CAGR of 14% from 2022 to 2030, per Grand View Research.
This underscores why over 80% of organizations are looking to optimize, automate, and transform their processes. The results make the investment highly worthwhile.
Key Process Improvement Results
Here are some typical outcomes organizations can achieve through process reengineering:
Productivity increase: 50-70% gains in productivity and output are common by optimizing human and technical resource usage.
Cost reduction: 25-60% reductions in operational costs by eliminating redundancies and waste.
Cycle time improvement: End-to-end process times shortened by 40-75% through workflow streamlining and automation.
Quality improvement: Error and defect rates reduced over 50-70% by minimizing process variations.
Revenue increase: 20-45% higher revenues enabled by faster and flawless customer order fulfilment.
Now let‘s examine 55 real-world examples of process improvement across industries:
Key Insights from the Case Studies
Analyzing these case studies reveals valuable patterns:
Manufacturing, financial services, and technology lead process improvement adoption, but benefits realized across sectors.
Production, supply chain, IT, finance processes improved the most. Customer services, HR, sales also optimized.
Lean Six Sigma, process mining, RPA, and BPM are the most popular and effective solutions.
Average efficiency gains of 50%, process costs reduced by 35%, process times shortened by 45%.
Process mining provides quick understanding of bottlenecks and pain points. More valuable for complex processes.
RPA and BPM rapidly automate repetitive and manual workflows for major productivity improvements.
Lean and Six Sigma drive a highly quantified approach to systematically eliminate waste and defects.
Kaizen and Agile facilitate continual improvement through small changes and team coordination.
Best Practices for Process Improvement Success
Here are some key tips for ensuring successful process improvement:
Secure Leadership Buy-in
- Engage executives early and outline the burning platform and expected benefits. Tie process improvement to strategic goals.
Define Scope and Prioritize
- Focus initial efforts on most critical processes with the biggest business impact.
Discover and Map Processes
- Understand current workflows using process mapping and mining. Identify pain points.
Measure and Baseline Metrics
- Quantify current process performance across time, cost, quality, and other KPIs before improvement.
Analyze Root Causes
- Dig deeper to uncover sources of bottlenecks, waste, variations etc. via cause-effect tools.
Redesign and Simplify Processes
- Eliminate non-value steps, minimize redundancies, standardize, and automate where possible.
Implement Changes Incrementally
- Test and iterate improvements through small pilot projects before enterprise-wide rollout.
Track Performance and Sustain Improvements
- Monitor key process metrics through automated dashboards for continuous improvement.
The outcomes from these case studies demonstrate the huge potential of process improvement to drive organizational excellence. While approaches differ, adopting a data-driven methodology tailored to your needs and backed by leadership commitment can enable you to replicate the success of these companies. The journey begins with discovering and mapping your processes to uncover improvement areas.
To learn more, explore these additional resources:
- McKinsey – The seven principles of improvement
- Forrester – The Total Economic ImpactTM Of Blue Prism
- Gartner – How to Get Started With Process Mining
Ready to optimize your business workflows? Our process improvement experts can guide you. Request a consultation .

- > Business Process Improvement Examples: 34 Actionable Ideas
Business Process Improvement Examples: 34 Actionable Ideas
Posted by Matt Banna
Aug 28, 2023 10:50:51 AM
When leaders consider implementing a structured business process improvement methodology , one of the challenges they often face is explaining to employees what types of opportunities to consider. Usually, there are some apparent needs that people attack immediately. Still, once those are addressed, it can be challenging to recognize the flaws in processes, especially ones you operate every day.
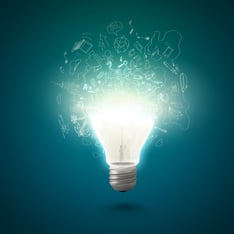
Quality Improvement
Product defects and errors affect profitability, cause dissatisfied customers, and hurt employee morale. That's why quality problems are usually the go-to target for improvement efforts. Some problems are easy to spot, but others take time to understand and uncover. Our customers have implemented quality improvements by:
- Using control charts to understand variation and detect trends
- Introducing process automation or mistake proofing ("poka yoke"), where possible, to eliminate the opportunity for error
- Calculating the financial impact of defects and rework
- Tracking customer complaints and reasons for support calls
- Applying the "5-whys" problem-solving technique to find the root cause of quality issues
When you think about quality improvement, remember that it isn't just the final products or services delivered to customers that can have errors. Internal processes and information must be free from defects as well.
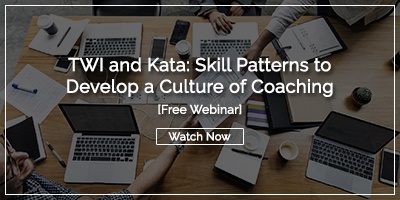
Cost Reduction
Keeping costs low is often considered to be the responsibility of the finance team and C-suite leaders, but chances are good that everyone in the organization can point to a way to reduce costs. Those closest to the work know what activities add to time and cost without any meaningful benefit. Common opportunities to reduce costs include:
- Limiting the purchase of perishable items except for immediate use
- Shifting from paper records or forms to electronic ones
- Frequently reviewing vendor contracts to ensure they meet current needs and conditions
- Reducing the inventory of products or raw materials
- Matching staffing to actual customer demand
Regardless of why the team undertakes an improvement project, most will have a positive impact on cost.
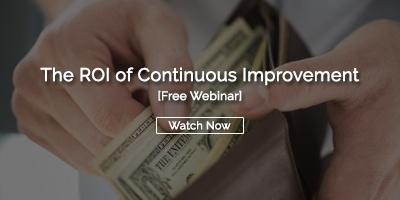
Revenue Generation
In the same way, everyone can contribute ideas about cost reduction; you don't have to be in sales or product development to have excellent ideas for increasing sales. Our customers have grown the top line by:
- Creating new bundles or products or services
- Addressing new markets or audiences
- Improving collections procedures
- Creative marketing to existing customers
- Making it easier to do business with the company
- Expanding partnerships to explore new channels
Our customers are often pleasantly surprised by the ideas that their teams come up with for increasing revenue when invited to do so.
Safety is a more significant challenge for some types of organizations than others, but every organization should pay attention to the safety of its workers and guests. This is one area where front-line workers can be extremely valuable; they see the risks firsthand. Process improvement examples that improve safety include:
- Employee awareness and training
- Workplace standardization and organization
- A well-documented and streamlined process for reporting hazards
- Automation that reduces safety or ergonomic risks
- A method for analyzing close calls or near misses
- Signage or other visual indicators of potential hazards
Customer Satisfaction
Every person in the organization has a role to play when it comes to customer satisfaction . Whether it is by creating products that maximize customer value, delivering support or services, insisting on excellent quality, or setting competitive prices, customer satisfaction is a team effort. Ideas for improving the customer experience include:
- Optimizing auto attendants to route customers to the help they need quickly
- Enhanced customer communications and content
- Implementing a structured approach to handling complains
- Skills-based contact center routing
- Transactional promoter score surveys
Your front-line employees know what your customers love and hate about working with your customers. Tap into this valuable resource to find areas for improvement.
Efficient companies practice operational excellence and get the most out of every resource. When organizations are inefficient, employees waste time and effort on tasks that don't add value, resources are wasted, and growth opportunities are missed. Ideas for improving productivity include:
- Eliminating duplicate work, like entering the same data into multiple systems
- Limiting meetings to those that are necessary and effective
- Streamlining approval processes
- Making sure that equipment and supplies are stored where they are needed
Process Improvement
All of the above examples represent ideas for improving business processes, but it is also wise to consider how you can improve your approach to improvement. Effective communications and documentation will help you accelerate the pace of positive change. You might think about the following:
- Frequently communicating strategic goals and annual objectives
- Deploying improvement management software
- Using digital wallboards to visualize work-in-progress
- Using daily huddle meetings to structure the day's improvement activities
- Measuring employee engagement and activity
- Improving cross-functional information sharing and collaboration
Improvement Techniques
Once your team is prolific at identifying opportunities for improvement, you'll want to ensure they know the most helpful techniques for implementing the ideas.
PDSA: PDSA is a structured cycle for improvement. The steps are:
Plan: Define the problem and identify possible solutions.
Do: Experiment by implementing one solution.
Study: Analyze the results of the experiment.
Act: If the experiment was successful, add it to the standard operation. If not, begin again.
The 5 Whys: The 5 whys is a problem-solving technique for finding the root cause of an issue. Simply stating a problem and then asking why five times or so will usually get to the bottom of the situation.
5S: 5S is a workplace organization technique for improving safety and efficiency. The steps are sort, set in order, shine, standardize, and sustain.
Catchball: Catchball is a technique borrowed from the Lean business methodology. Someone, usually a leader or manager, starts the "ball" rolling by sharing an idea and asking for feedback. Then, others add their thoughts and pass the idea up and down the layers of the origination until it is refined and a consensus is achieved.
A3 Problem Solving: A3 problem solving is a structured technique for defining and solving problems. On a single sheet of paper, the team determines the current state, identifies the desired state, selects performance measurements, develops an implementation plan, and tracks the results.
Business process improvement is critical for success in today's competitive landscape, but it doesn't have to be overwhelming. Small process changes implemented by employees can have a significant impact on results. Armed with process improvement software, a few problem-solving techniques, and the full support of leadership, your team will exceed all expectations.
Topics: Daily Improvement , Improvement Process
Add a Comment
Subscribe via email, recent posts.
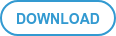
- Our Customers
Why KaiNexus
- Collaboration
- Standardization
- Customer Success Manager
- Lean Strategy
- Solutions Engineering
- Customer Marketing
- Configuration
- Continuous Enhancements
- Employee Driven
- Leader Driven
- Strategy Development
- Process Driven
- Daily Huddles
- Idea Generation
- Standard Work
- Visual Management
- Advanced ROI
- Notifications
- Universal Badges
- Case Studies
- Education Videos
Copyright © 2024 Privacy Policy
The Lean Post / Articles / Lean Management Case Studies Library
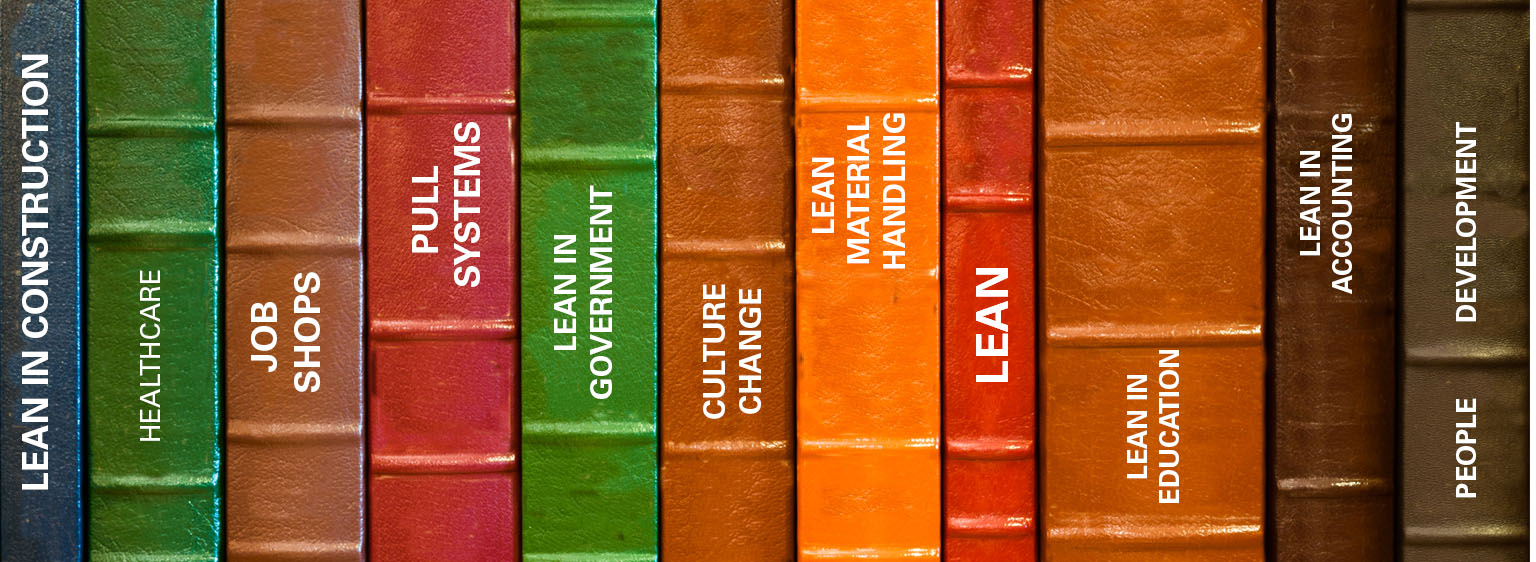
Lean Management Case Studies Library
By Chet Marchwinski
May 16, 2014
Learn how a variety of businesses and organizations used lean management principles to solve real business problems. We’ve arranged the examples in 16 categories to help you find the ones right for your environment.
Lean Management Examples from a Variety of Businesses
The following case studies of lean management principles in action show you how a variety of real businesses solved real business problems under diverse conditions.
We’ve arranged the stories in 16 categories to help you find the examples you need. There is some overlap. For instance, a “Lean Manufacturing” case study may also appear with “Privately Held Companies.”
Lean Manufacturing
- Logistics, Supply Chain, and Warehousing
- Lean Material Handling
- Job Shops (Low-volume, High-mix Manufacturing); Tool and Die
- Lean in Government
- Lean Healthcare
- Lean Accounting
- Lean Construction
- Lean in Office and Service Processes
- Lean in Education
Problem Solving
Pull Systems
Culture Change
People Development
Privately Held Companies
Maintenance
Many of the executives who took part in these transformations are interviewed in LEI’s Senior Executive Series on Lean Leadership . After reading the case studies, be sure to get their personal perspectives on leading change. (Feel free to link to this page, but please respect the copyrights of LEI and journalists by not copying the articles.)
Are you doing something new or notable in the practice of lean management? Let us share what you learned with the lean community. For more information, contact LEI’s Director of Communications Chet Marchwinski at cmarchwinski at lean dot org
Thrustmaster Turns Around
Learn how Thrustmaster of Texas successfully adopted lean thinking and practices to make sustainable improvements in a short period of time, and how other manufacturers of highly engineered, low-volume products can follow their lead using the Lean Transformation Framework.
Lean + Circular Principals = a New True North for Manufacturer
SunPower’s lean journey resembled most others until it defined a new mission, a new True North by combining lean principals with those of the “circular economy” to launch what it is calling a CLean Transformation.
Sustain Your Lean Business System with a “Golden Triangle” After a medical device maker took a hit to margins to fight off global competition, it rebuilt them by lifting its lean operating system to a higher level and keeping it there with a “golden triangle” of sustainability.
Followup Story:
Manufacturing Balancing Act: Pull Versus ERP
In this follow-up to “Sustain Your Lean Business System with a ‘Golden Triangle,’” a case study about Phase 2 Medical Manufacturing, the company needs warehouse space to keep pace with sales growth spurred by the lean transformation. Instead, it expands a pull system by connecting the plan-for-every-part database that underpins one-piece flow production with ERP, typically associated with big batch production.
Cultivating a Lean Problem-Solving Culture at O.C. Tanner If you are in the “appreciation business”, you have to live it in your own workplace. For O.C. Tanner that meant a lean transformation had to show the company appreciated and wanted people’s problem-solving ideas. Here’s a report on that effort, including what worked and what didn’t.
Lean Partnership with Dealer Network Helps Vermeer Reduce End-to-End Inventory on Top Sellers
A lean transformation had taken heavy-equipment manufacturer Vermeer away from batch manufacturing, but batch ordering by dealers was delaying how quickly they got equipment like brush chippers. Learn how it began converting its domestic industrial-line distribution network to lean replenishment, improving service to end customers and improving cash flow for Vermeer and its dealers.
Herman Miller’s Experiment in Excellence At Herman Miller, the lean management effort helps it build problem solvers as well as world-class office furniture. And as this case study shows, lean practices also helped it weather a brutal recession.
Build Your “House” of Production on a Stable Foundation Rigorous problem solving creates basic stability in a machining intensive facility.
A Journey to Value Streams: Reorganizing Into Five Groups Drives Lean Improvements and Customer Responsiveness An approach to creating a value -stream culture centered on autonomy, entrepreneurialism, and lean principles.
Change in Implementation Approach Opens the Door at EMCO to Greater Gains in Less Time A relatively quick, intensive project accelerates the rate of improvement and creates a showcase facility for spreading lean concepts.
Creating the Course and Tools for a Lean Accounting System A lean accounting implementation fills the frustrating disconnect between shop-floor improvements and financial statements.
For Athletic Shoe Company, the Soul of Lean Management Is Problem Solving After taking a lean tools approach to change, management re-organized the transformation around problem solving and process improvement to create a culture that engaged people while boosting performance.
Knife Company Hones Competitiveness by Bucking the Status Quo An iconic family-owned company turns to lean manufacturing to reduce costs by at least 30% to keep its U.S. operations open.
Lean Transformation Lives and Dies with Tools and Dies After a failed first try at just-in-time production , a company transforms tool maintenance, design, and fabrication to create a solid foundation for a second attempt.
Seasoned Lean Effort Avoids “Flavor-of-the-Month” Pitfall A look at how one company’s approach to what new tools it introduced, in what order, and how it prevented each new technique from being viewed as a “flavor of the month” fad.
Shifting to Value-Stream Managers: a Shop-Floor Revolution Leads to a Revolution in Plant Organization
Two years into a lean transformation, the low-hanging fruit has been plucked and progress has started to slow. Read how a Thomas & Betts plant recharged the transformation and reached higher levels of performance by using value-stream managers to span functional walls.
Using Plan-Do-Check-Act as a Strategy and Tactic for Helping Suppliers Improve
At Medtronic’s Neuromodulation business unit, the plan-do-check-act cycle is used on a strategic level to guide overall strategy for selecting and developing key suppliers as well as on a tactical level for guiding lean transformations at supplier facilities.
back to top
Logistics, Supply Chain, and Warehousing How a Retailer’s Distribution Center Exemplifies the Lean Precept “Respect for People,” and Reaps the Benefits
To make sure training engaged and resonated with people after previous attempts at a lean transformation faltered, LifeWay matched lean management tools and principles to its Bible-based culture and language.
Lean management case study series: Lean in Distribution: Go to Where the Action Is!
Starting with daily management walkabouts and standard work , this distributor had laid the groundwork for steady gains for years to come, just two years after its first kaizen workshop .
Putting Lean Principles in the Warehouse
Executives at Menlo Worldwide Logistics saw an opportunity to leapfrog the competition by embracing lean in its outsourced warehousing and receiving operations.
Lean Thinking Therapy Spreads Beyond the Shop
A company expands the lean transformation from the shop floor to international distribution, domestic shipping, and product development.
Sell One, Buy One, Make One: Transforming from Conventional to Lean Distribution
Large inventories to cover fluctuations in demand once characterized Toyota’s service parts distribution system — but no more. Here’s how one DC made the switch.
Material Handling
Following Four Steps to a Lean Material-Handling System Leads to a Leap in Performance
Creating the critical Plan for Every Part was one step in a methodical four-step implementation process to replace a traditional material-handling system.
Low-volume, High-mix Manufacturing; Tool and Die
The Backbone of Lean in the Back Shops
Sikorsky managers apply the lean concept of “every part, every interval” (EPEI) to level the mix in demand and create flow through a key manufacturing cell .
Landscape Forms Cultivates Lean to Fuel Growth Goals
With single-item orders 80% of the time, a low-volume, high-mix manufacturer decided single-piece flow cells were the best way decided the best way to add new products without having to constantly reconfigure production.
Lean Transformation Lives and Dies with Tools and Dies
After a failed first try at just-in-time production, a company transforms tool maintenance, design, and fabrication to create a solid foundation for a second attempt.
Canada Post Puts Its Stamp on a Lean Transformation
The “ inventory ” of mail already is paid for, so moving it faster doesn’t improve cash flow as in lean manufacturing. But Canada Post discovered that traditional batch-and-queue postal operations could benefit from lean principles.
Lean Thinking in Government: The State of Iowa
This story examines a kaizen event at a veterans home and more broadly at the lean effort in Iowa government.
Lean Thinking Helps City of Chula Vista with Budget Crunch
Goodrich Aerostructures’ Chula Vista plant introduces city government to lean thinking and practices so in order to maintain municipal services without resorting to further cuts in the workforce.
Using Lean Thinking to Reinvent City Government
Grand Rapids, MI, turns to lean principles to consolidate operations, eliminate wasted time and effort, and streamline to improve productivity while providing the quality of service that residents want.
Transforming Healthcare: What Matters Most? How the Cleveland Clinic Is Cultivating a Problem-Solving Mindset and Building a Culture of Improvement
The Cleveland Clinic reinvents its continuous improvement program to instill a problem-solving mindset and the skillset to solve everyday problems among the clinic’s thousands of caregivers.
View from the Hospital Floor: How to Build a Culture of Improvement One Unit at a Time
In order to do more and improve faster, the Cleveland Clinic is rolling out a methodology for building a “culture of improvement” across the 48,000-employee hospital system as this followup to the above story shows. Here’s how it works according to the people making the changes.
Dentist Drills Down to the Root Causes of Office Waste
Dentistry is a job shop that Dr. Sami Bahri is out to improve fundamentally for the benefit of patients through the application of lean principles.
Lean management case study series: Pediatric Hospital in Tough Market Pegs Growth to Lean Process Improvement
Lean improvement projects at Akron Children’s Hospital have saved millions of dollars, increased utilization of expensive assets, and reduced wait times for patients and their families.
Lean Design and Construction Project an Extension of Lean Commitment at Akron Children’s Hospital
Input from nurses, doctors, therapists, technicians, and patient parents heavily influenced design decisions..
“Pulling” Lean Through a Hospital
A thoughtful rollout of lean principles in the ER and eye-opening results created a “pull” for lean from other departments.
Best in Healthcare Getting Better with Lean
Mayo Clinic, Rochester, MN, stresses to doctors that the lean effort is aimed not at changing the moment of care, the touch moment between doctor and patient, but the 95% of the time when the patient is not in the doctor’s office
Fighting Cancer with Linear Accelerators and Accelerated Processes
Cross-functional team design and implement a lean process to dramatically increase the number of patients with brain and bone metastases receiving consultation, simulation, and first treatment on the same day without workarounds or expediting.
Massachusetts General Looks to Lean
A proton therapy treatment center, for many adults and children the best hope of beating cancer, applies lean principles to increase capacity.
New Facility, New Flow, and New Levels of Patient Care: The wait is over for patients at the Clearview Cancer Institute in Alabama
Physicians and staff have tirelessly reengineer processes and patient flow to eliminate as much waiting and waste as possible.
The Anatomy of Innovation
At a hospital in Pittsburgh, the emerging vision for the “hospital of the future” is described as giving the right patient, the right care, at the right time, in the right way, all the time.
Creating the Course and Tools for a Lean Accounting System
A lean accounting implementation fills the frustrating disconnect between shop-floor improvements and the financial statement.
Knife Company Hones Competitiveness by Bucking the Status Quo
An iconic family-owned company turns to lean manufacturing to reduce costs by at least 30% to keep its U.S. operations open.
Office and Service Processes
The “inventory” of mail already is paid for, so moving it faster doesn’t improve cash flow as in lean manufacturing. But Canada Post discovered that traditional batch-and-queue postal operations could benefit from lean principles.
Lean Landscapers
At an Atlanta landscaping company, lean practices are making inroads into a service industry in unusual yet fundamental ways.
LSG Sky Chefs Caters to New Market Realities
Business at airline caterer LSG Sky Chefs dropped 30% when airlines cut flights after the terrorist attacks on September 11, 2001. Sky Chefs responded with a rapid launch of a lean initiative.
leveraging Lean to Get the Oil Out
Aera Energy LLC, a California oil and gas company, relies on lean principles to improve key processes, including drilling new wells, repairing existing ones, and maximizing the number of barrels of crude pumped each day.
Columbus Public Schools Use Process Thinking to Improve Academic Achievement.
Columbus, OH, public schools, experiment with lean tools and process thinking to remove wasteful activities that don’t help them help students learn.
Lean Inroads into Alabama Academia
How the University of Alabama in Huntsville integrated lean concepts throughout its industrial engineering curriculum.
Linking Lean Thinking to the Classroom
Value-stream mapping is one of many activities included in the Ford Partnership for Advanced Studies (Ford PAS), an academic program designed to link high-school classroom learning to the skills needed in college and business.
Build Your “House” of Production on a Stable Foundation
Rigorous problem solving creates basic stability in a machining intensive facility.
For Athletic Shoe Company, the Soul of Lean Management Is Problem Solving
After talking a lean tools approach to change, management re-organized the transformation around problem solving and process improvement to create a culture that engaged people while boosting performance.
Toothbrush Plant Reverses Decay in Competitiveness
The rapid introduction of a lean system, beginning with just-in-time production and pull, helps a highly automated Midwest plant fight off overseas competition by reducing lead times and inventory while augmenting the plant’s advantage in service.
A Journey to Value Streams: Reorganizing Into Five Groups Drives Lean Improvements and Customer Responsiveness
An approach to creating a value-stream culture centered on autonomy, entrepreneurialism, and lean principles.
Making Lean Leaders — Ariens internship program develops lean and leadership skills
Besides making snow-blowers, mowers, and string trimmers, Ariens Co., of Brillion, WI, makes lean leaders.
Starting with daily management walkabouts and standard work, this 84-year-old, family-owned distributor laid the groundwork for steady gains for years to come, just two years after its first kaizen workshop.
Sustain Your Lean Business System with a “Golden Triangle”
After a medical device maker took a hit to margins to fight off global competition, it rebuilt them by lifting its lean operating system to a higher level and keeping it there with a “golden triangle” of sustainability. You’ll recognize two elements of the triangle right away: visual control and standardized work . The third, accountability management or a kamishibai system, is probably less well known but just as critical.
Cultivating a Lean Problem-Solving Culture at O.C. Tanner
If you are in the “appreciation business”, you have to live it in your own workplace. For O.C. Tanner that meant a lean transformation had to show the company appreciated and wanted people’s problem-solving ideas. Here’s a report on that effort, including what worked and what didn’t.
Lean Thinking in Aircraft Repair and Maintenance Takes Wing at FedEx Express
A major check that used to take 32,715 man-hours was cut to 21,535 hours in six months. That translated into a $2 million savings, which dovetailed with the company’s emphasis on reducing costs during the recession.
Construction
Input from nurses, doctors, therapists, technicians, and patient parents heavily influenced design decisions—from incorporating emergency room hallways that protect the privacy of abused children to the number of electrical outlets in each neonatal intensive care room.
Virtual Lean Learning Experience (VLX)
A continuing education service offering the latest in lean leadership and management.
Written by:
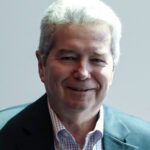
About Chet Marchwinski
Chet has been a humble, unwashed scribe of the lean continuous improvement movement since books by Taiichi Ohno and Shigeo Shingo first hit North America in the 1980s. At LEI, he contributes to content creation, marketing, public relations, and social media. Previously, he also wrote case studies on lean management implementations in…
Leave a Comment Cancel reply
Your email address will not be published. Required fields are marked *
Save my name, email, and website in this browser for the next time I comment.
Be the first to learn of new learning opportunities and the latest practical, actionable information. Subscribe to an LEI newsletter.
Join us on social, privacy overview.
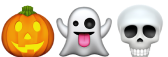
- Onsite training
3,000,000+ delegates
15,000+ clients
1,000+ locations
- KnowledgePass
- Log a ticket
01344203999 Available 24/7
Six Sigma Case Study: Everything You Need to Know
Explore the field of Six Sigma Case Studies in our comprehensive blog. From defining the methodology to real-world applications, our 'Six Sigma Case Study: Everything You Need to Know' blog sheds light on this powerful problem-solving tool. Uncover success stories and learn how Six Sigma can drive efficiency and quality improvements in various industries.

Exclusive 40% OFF
Training Outcomes Within Your Budget!
We ensure quality, budget-alignment, and timely delivery by our expert instructors.
Share this Resource
- Six Sigma Black Belt Upgrade
- Lean Six Sigma Green Belt
- Six Sigma Yellow Belt
- Six Sigma Black Belt
- Lean Six Sigma Black Belt
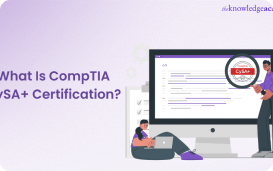
By analysing such case studies, one can gain insights into the successful application of Six Sigma in various industries and understand its impact on process improvement. Read this blog on Six Sigma Case Study to learn how real-world businesses have achieved remarkable process improvement and cost savings.
Table of Contents
1) Understanding Six Sigma Methodology
2) Six Sigma Case Study
a) Improving customer service
b) Improving delivery efficiency
3) Conclusion
Understanding Six Sigma Methodology
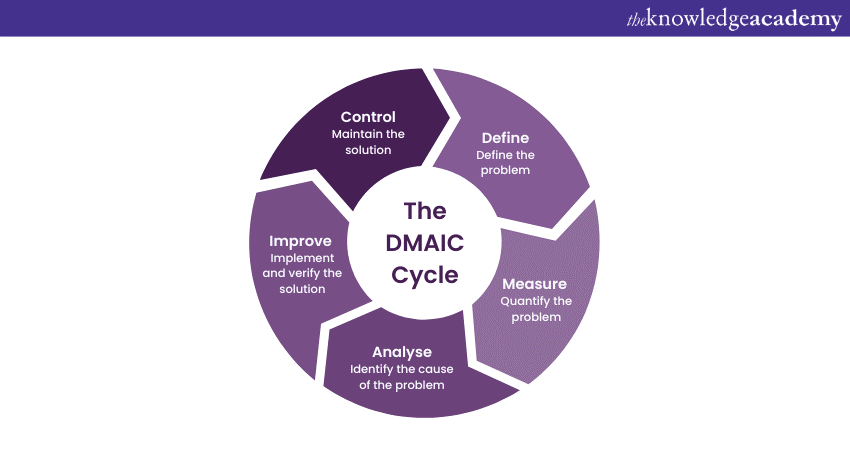
By applying statistical analysis and data-driven decision-making, Six Sigma helps organisations identify the root cause of problems and implement effective solutions. It emphasises the importance of process standardisation, continuous improvement, and customer satisfaction. With its focus on rigorous measurement and analysis, Six Sigma enables organisations to drive efficiency, reduce waste, and deliver exceptional products and services. The methodology follows a step-by-step process called Define, Measure, Analyse, Improve, and Control (DMAIC). These five phases are briefly explained below:
a) Define: The project goals and customer requirements are clearly defined in this phase.
b) Measure: In this phase, data is collected to understand the process's current state and identify improvement areas.
c) Analyse: This phase focuses on analysing data to determine the root cause of defects or variations.
d) Improve: This phase involves implementing solutions and making necessary changes to eliminate the identified issues.
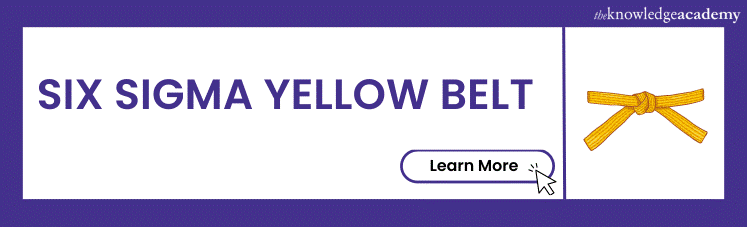
Six Sigma Case Study
In this section we discuss two Six Sigma Case Study that will help you understand and use it better.
Case Study 1: Improving customer service
This Six Sigma Case Study will focus on a telecommunications company facing significant customer service challenges. The issues included long wait times, frequent call transfers, unresolved issues, and many more. The company decided to apply Six Sigma methodologies to enhance customer satisfaction.
a) Define phase: Using the DMAIC approach, the team began by defining the problem: long wait times and inefficient call handling. They set a goal to reduce average wait time and increase first-call resolution rates.
b) Measure phase: In this phase, data was collected to analyse call volume, wait times, and reasons for call transfers. This helped identify bottlenecks and areas for improvement.
c) Analyse phase: During this phase, the team discovered that inadequate training and complex call routing were key contributors to the problems. They also found that certain product issues required better resolution protocols.
d) Improve phase: In this phase, targeted solutions were introduced and implemented to address these issues. The team revamped the training program, ensuring agents were well-trained and equipped to handle customer inquiries. They simplified call routing and introduced automated prompts for quicker issue resolution.
e) Control phase: Finally, monitoring systems were established in the control phase to track key metrics and ensure sustained improvements. Regular feedback loops were implemented to identify emerging challenges and make necessary adjustments.
The results were exceptional. Average wait times were reduced by 40%, and first-call resolution rates increased by 25%. Customer satisfaction scores improved significantly, leading to increased loyalty and positive word-of-mouth.
This Six Sigma Case Study highlights how Six Sigma methodologies can drive transformative improvements in customer service. By focusing on data analysis, process optimisation, and continuous monitoring, organisations can achieve outstanding outcomes and deliver exceptional customer experiences.
Understand the in-depth process of Six Sigma with our Six Sigma Yellow Belt Course . Join now!
Case Study 2: Improving delivery efficiency
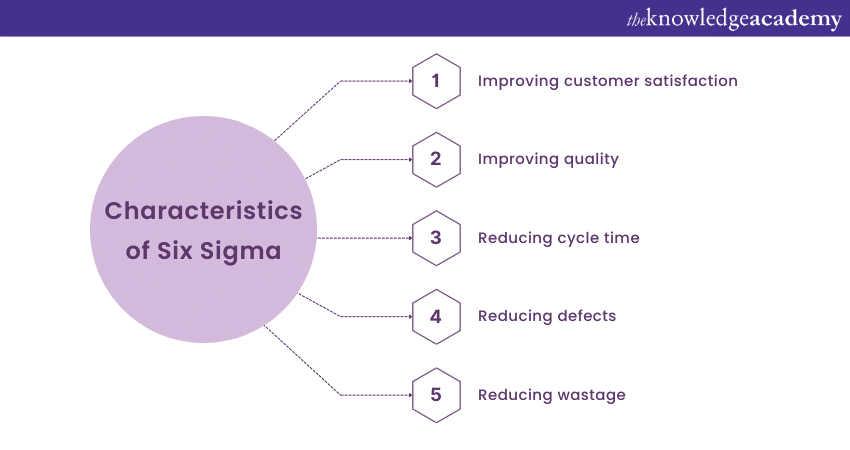
a) Define phase: The business used the Voice of the Customer (VoC) tool to understand customer needs and expectations. They identified prompt delivery, correct product selection, and a knowledgeable distribution team as crucial customer requirements.
b) Measure phase: The team collected data to evaluate the problem of slow delivery. They discovered that their Order Fulfillment Cycle Time (OFCT) was 46% longer than competitors, leading to customer dissatisfaction.
c) Analyse phase: The team brainstormed potential causes of slow delivery, including accuracy of sales plans, buffer stock issues, vendor delivery performance, and manufacturing schedule delays. They conducted a regression analysis, revealing that inadequate buffer stock for high-demand products was the main issue affecting delivery efficiency.
d) Improve phase: The distributor implemented a monthly demand review to ensure that in-demand products are readily available. They emphasised ordering and providing customers with the specific products they desired.
e) Control phase: The team developed plans to monitor sales of the top 20% of bestselling products, avoiding over or under-supply situations. They conducted annual reviews to identify any changes in demand and proactively adjust product offerings.
By applying Six Sigma Principles , the plumbing product distributor significantly improved its delivery efficiency, addressing the root cause of customer dissatisfaction. Prompt action, data-driven decision-making, and ongoing monitoring allowed them to meet customer expectations, enhance its reputation, and maintain a competitive edge in the industry. This case demonstrates the power of Lean Six Sigma in driving operational excellence and customer-centric improvements.
Take the next step in your professional development and boost your career by joining our Six Sigma Green Belt course .
Conclusion
We hope this blog gives you enough insights into the Six Sigma Case Study. This blog showcased the effectiveness of its methodology in driving transformative improvements. By applying DMAIC and using customer insights and data analysis, organisations have successfully resolved delivery inefficiencies, improving customer satisfaction and operational performance. The blog highlights how Six Sigma can be a powerful framework for organisations seeking excellence and exceptional value.
Learn the six-sigma methodology to achieve business objectives with our Six Sigma Certification Training today!
Frequently Asked Questions
Upcoming business improvement resources batches & dates.
Mon 3rd Jun 2024
Mon 10th Jun 2024
Mon 17th Jun 2024
Sat 22nd Jun 2024, Sun 23rd Jun 2024
Mon 24th Jun 2024
Mon 1st Jul 2024
Mon 8th Jul 2024
Mon 15th Jul 2024
Sat 20th Jul 2024, Sun 21st Jul 2024
Mon 22nd Jul 2024
Mon 29th Jul 2024
Mon 5th Aug 2024
Mon 12th Aug 2024
Sat 17th Aug 2024, Sun 18th Aug 2024
Mon 19th Aug 2024
Tue 27th Aug 2024
Mon 2nd Sep 2024
Mon 9th Sep 2024
Sat 14th Sep 2024, Sun 15th Sep 2024
Mon 16th Sep 2024
Mon 23rd Sep 2024
Mon 30th Sep 2024
Mon 7th Oct 2024
Sat 12th Oct 2024, Sun 13th Oct 2024
Mon 14th Oct 2024
Mon 21st Oct 2024
Mon 28th Oct 2024
Mon 4th Nov 2024
Sat 9th Nov 2024, Sun 10th Nov 2024
Mon 11th Nov 2024
Mon 18th Nov 2024
Mon 25th Nov 2024
Mon 2nd Dec 2024
Sat 7th Dec 2024, Sun 8th Dec 2024
Mon 9th Dec 2024
Mon 16th Dec 2024
Mon 6th Jan 2025
Mon 13th Jan 2025
Mon 20th Jan 2025
Mon 27th Jan 2025
Mon 3rd Feb 2025
Mon 10th Feb 2025
Mon 17th Feb 2025
Mon 24th Feb 2025
Mon 3rd Mar 2025
Mon 10th Mar 2025
Mon 17th Mar 2025
Mon 24th Mar 2025
Mon 31st Mar 2025
Mon 7th Apr 2025
Mon 14th Apr 2025
Tue 22nd Apr 2025
Mon 28th Apr 2025
Tue 6th May 2025
Mon 12th May 2025
Mon 19th May 2025
Tue 27th May 2025
Mon 2nd Jun 2025
Mon 9th Jun 2025
Mon 16th Jun 2025
Mon 23rd Jun 2025
Mon 30th Jun 2025
Mon 7th Jul 2025
Mon 14th Jul 2025
Mon 21st Jul 2025
Mon 28th Jul 2025
Mon 4th Aug 2025
Mon 11th Aug 2025
Mon 18th Aug 2025
Tue 26th Aug 2025
Mon 1st Sep 2025
Mon 8th Sep 2025
Mon 15th Sep 2025
Mon 22nd Sep 2025
Mon 29th Sep 2025
Mon 6th Oct 2025
Mon 13th Oct 2025
Mon 20th Oct 2025
Mon 27th Oct 2025
Mon 3rd Nov 2025
Mon 10th Nov 2025
Mon 17th Nov 2025
Mon 24th Nov 2025
Mon 1st Dec 2025
Mon 8th Dec 2025
Mon 15th Dec 2025
Get A Quote
WHO WILL BE FUNDING THE COURSE?
My employer
By submitting your details you agree to be contacted in order to respond to your enquiry
- Business Analysis
- Lean Six Sigma Certification
Share this course
Our biggest spring sale.

We cannot process your enquiry without contacting you, please tick to confirm your consent to us for contacting you about your enquiry.
By submitting your details you agree to be contacted in order to respond to your enquiry.
We may not have the course you’re looking for. If you enquire or give us a call on 01344203999 and speak to our training experts, we may still be able to help with your training requirements.
Or select from our popular topics
- ITIL® Certification
- Scrum Certification
- Change Management Certification
- Business Analysis Courses
- Microsoft Azure Certification
- Microsoft Excel Courses
- Microsoft Project
- Explore more courses
Press esc to close
Fill out your contact details below and our training experts will be in touch.
Fill out your contact details below
Thank you for your enquiry!
One of our training experts will be in touch shortly to go over your training requirements.
Back to Course Information
Fill out your contact details below so we can get in touch with you regarding your training requirements.
* WHO WILL BE FUNDING THE COURSE?
Preferred Contact Method
No preference
Back to course information
Fill out your training details below
Fill out your training details below so we have a better idea of what your training requirements are.
HOW MANY DELEGATES NEED TRAINING?
HOW DO YOU WANT THE COURSE DELIVERED?
Online Instructor-led
Online Self-paced
WHEN WOULD YOU LIKE TO TAKE THIS COURSE?
Next 2 - 4 months
WHAT IS YOUR REASON FOR ENQUIRING?
Looking for some information
Looking for a discount
I want to book but have questions
One of our training experts will be in touch shortly to go overy your training requirements.
Your privacy & cookies!
Like many websites we use cookies. We care about your data and experience, so to give you the best possible experience using our site, we store a very limited amount of your data. Continuing to use this site or clicking “Accept & close” means that you agree to our use of cookies. Learn more about our privacy policy and cookie policy cookie policy .
We use cookies that are essential for our site to work. Please visit our cookie policy for more information. To accept all cookies click 'Accept & close'.
Business process reengineering (BPR) is the radical redesign of core business processes to achieve dramatic improvements in performance, efficiency and effectiveness. BPR examples are not one-time projects, but rather examples of a continuous journey of innovation and change focused on optimizing end-to-end processes and eliminating redundancies. The purpose of BPR is to streamline workflows , eliminate unnecessary steps and improve resource utilization.
BPR involves business process redesign that challenges norms and methods within an organization. It typically focuses on achieving dramatic, transformative changes to existing processes. It should not be confused with business process management (BPM) , a more incremental approach to optimizing processes, or business process improvement (BPI), a broader term that encompasses any systematic effort to improve current processes. This blog outlines some BPR examples that benefit from a BPM methodology.
Background of business process reengineering
BPR emerged in the early 1990s as a management approach aimed at radically redesigning business operations to achieve business transformation. The methodology gained prominence with the publication of a 1990 article in the Harvard Business Review, “Reengineering Work: Don’t Automate, Obliterate,” by Michael Hammer, and the 1993 book by Hammer and James Champy, Reengineering the Corporation . An early case study of BPR was Ford Motor Company, which successfully implemented reengineering efforts in the 1990s to streamline its manufacturing processes and improve competitiveness.
Organizations of all sizes and industries implement business process reengineering. Step 1 is to define the goals of BPR, and subsequent steps include assessing the current state, identifying gaps and opportunities, and process mapping.
Successful implementation of BPR requires strong leadership, effective change management and a commitment to continuous improvement. Leaders, senior management, team members and stakeholders must champion the BPR initiative and provide the necessary resources, support and direction to enable new processes and meaningful change.
BPR examples: Use cases
Streamlining supply chain management.
Using BPR for supply chain optimization involves a meticulous reassessment and redesign of every step, including logistics, inventory management and procurement . A comprehensive supply chain overhaul might involve rethinking procurement strategies, implementing just-in-time inventory systems, optimizing production schedules or redesigning transportation and distribution networks. Technologies such as supply chain management software (SCM), enterprise resource planning (ERP) systems, and advanced analytics tools can be used to automate and optimize processes. For example, predictive analytics can be used to forecast demand and optimize inventory levels, while blockchain technology can enhance transparency and traceability in the supply chain.
- Improved efficiency
- Reduced cost
- Enhanced transparency
Customer relationship management (CRM)
BPR is a pivotal strategy for organizations that want to overhaul their customer relationship management (CRM) processes. Steps of business process reengineering for CRM include integrating customer data from disparate sources, using advanced analytics for insights, and optimizing service workflows to provide personalized experiences and shorter wait times.
BPR use cases for CRM might include:
- Implementing integrated CRM software to centralize customer data and enable real-time insights
- Adopting omnichannel communication strategies to provide seamless and consistent experiences across touchpoints
- Empowering frontline staff with training and resources to deliver exceptional service
Using BPR, companies can establish a comprehensive view of each customer, enabling anticipation of their needs, personalization of interactions and prompt issue resolution.
- 360-degree customer view
- Increased sales and retention
- Faster problem resolution
Digitizing administrative processes
Organizations are increasingly turning to BPR to digitize and automate administrative processes to reduce human errors. This transformation entails replacing manual, paper-based workflows with digital systems that use technologies like Robotic Process Automation (RPA) for routine tasks.
This might include streamlining payroll processes, digitizing HR operations or automating invoicing procedures. This can lead to can significant improvements in efficiency, accuracy and scalability and enable the organization to operate more effectively.
- Reduced processing times
- Reduced errors
- Increased adaptability
Improving product development processes
BPR plays a crucial role in optimizing product development processes, from ideation to market launch. This comprehensive overhaul involves evaluating and redesigning workflows, fostering cross-functional collaboration and innovating by using advanced technologies. This can involve implementing cross-functional teams to encourage communication and knowledge sharing, adopting agile methodologies to promote iterative development and rapid prototyping, and by using technology such as product lifecycle management (PLM) software to streamline documentation and version control.
BPR initiatives such as these enable organizations to reduce product development cycle times, respond more quickly to market demands, and deliver innovative products that meet customer needs.
- Faster time-to-market
- Enhanced innovation
- Higher product quality
Updating technology infrastructure
In an era of rapid technological advancement, BPR serves as a vital strategy for organizations that need to update and modernize their technology infrastructure. This transformation involves migrating to cloud-based solutions, adopting emerging technologies like artificial intelligence (AI) and machine learning (ML) , and integrating disparate systems for improved data management and analysis, which enables more informed decision making. Embracing new technologies helps organizations improve performance, cybersecurity and scalability and positioning themselves for long-term success.
- Enhanced performance
- Improved security
- Increased innovation
Reducing staff redundancy
In response to changing market dynamics and organizational needs, many companies turn to BPR to restructure their workforce and reduce redundancy. These strategic initiatives can involve streamlining organizational hierarchies, consolidating departments and outsourcing non-core functions. Optimizing workforce allocation and eliminating redundant roles allows organizations to reduce costs, enhance operational efficiency and focus resources on key priorities.
- Cost savings
- Increased efficiency
- Focus on core competencies
Cutting costs across operations
BPR is a powerful tool to systematically identify inefficiencies, redundancies and waste within business operations. This enables organizations to streamline processes and cut costs.
BPR focuses on redesigning processes to eliminate non-value-added activities, optimize resource allocation, and enhance operational efficiency. This might entail automating repetitive tasks, reorganizing workflows for minimizing bottlenecks, renegotiating contracts with suppliers to secure better terms, or by using technology to improve collaboration and communication. This can enable significant cost savings and improve profitability.
- Lower costs
- Enhanced competitiveness
Improving output quality
BPR can enhance the quality of output across various business processes, from manufacturing to service delivery. BPR initiatives generally boost key performance indicators (KPIs).
Steps for improving output quality involve implementing quality control measures, fostering a culture of continuous improvement, and using customer feedback and other metrics to drive innovation.
Technology can also be used to automate processes. When employees are freed from distracting processes, they can increase their focus on consistently delivering high-quality products and services. This builds customer trust and loyalty and supports the organization’s long-term success.
- Higher customer satisfaction
- Enhanced brand image
Human resource (HR) process optimization
BPR is crucial for optimizing human resources (HR) processes. Initiatives might include automating the onboarding process with easy-to-use portals, streamlining workflows, creating self-service portals and apps, using AI for talent acquisition , and implementing a data-driven approach to performance management.
Fostering employee engagement can also help attract, develop and retain top talent. Aligning HR processes with organizational goals and values can enhance workforce productivity, satisfaction and business performance.
- Faster recruitment cycles
- Improved employee engagement
- Strategic talent allocation
BPR examples: Case studies
The following case study examples demonstrate a mix of BPR methodologies and use cases working together to yield client benefits.
Bouygues becomes the AI standard bearer in French telecom
Bouygues Telecom , a leading French communications service provider, was plagued by legacy systems that struggled to keep up with an enormous volume of support calls. The result? Frustrated customers were left stranded in call lines and Bouygues at risk of being replaced by its competitors. Thankfully, Bouygues had partnered with IBM previously in one of our first pre- IBM watsonx™ AI deployments. This phase 1 engagement laid the groundwork perfectly for AI’s injection into the telecom’s call center during phase 2.
Today, Bouygues greets over 800,000 calls a month with IBM watsonx Assistant™, and IBM watsonx Orchestrate™ helps alleviate the repetitive tasks that agents previously had to handle manually, freeing them for higher-value work. In all, agents’ pre-and-post-call workloads were reduced by 30%. 1 In addition, 8 million customer-agent conversations—which were, in the past, only partially analyzed—have now been summarized with consistent accuracy for the creation of actionable insights.
Taken together, these technologies have made Bouygues a disruptor in the world of customer care, yielding a USD 5 million projected reduction in yearly operational costs and placing them at the forefront of AI technology. 1
Finance of America promotes lifetime loyalty via customer-centric transformation
By co-creating with IBM, mortgage lender Finance of America was able to recenter their operations around their customers, driving value for both them and the prospective home buyers they serve.
To accomplish this goal, FOA iterated quickly on both new strategies and features that would prioritize customer service and retention. From IBM-facilitated design thinking workshops came roadmaps for a consistent brand experience across channels, simplifying the work of their agents and streamlining the application process for their customers.
As a result of this transformation, FOA is projected to double their customer base in just three years. In the same time frame, they aim to increase revenue by over 50% and income by over 80%. Now, Finance of America is primed to deliver enhanced services—such as debt advisory—that will help promote lifetime customer loyalty. 2
BPR examples and IBM
Business process reengineering (BPR) with IBM takes a critical look at core processes to spot and redesign areas that need improvement. By stepping back, strategists can analyze areas like supply chain, customer experience and finance operations. BPR services experts can embed emerging technologies and overhaul existing processes to improve the business holistically. They can help you build new processes with intelligent workflows that drive profitability, weed out redundancies, and prioritize cost saving.
1. IBM Wow Story: Bouygues Becomes the AI Standard-Bearer in French Telecom. Last updated 10 November 2023.
2. IBM Wow Story: Finance of America Promotes Lifetime Loyalty via Customer-Centric Transformation. Last updated 23 February 2024.
More from Business transformation
Attention new clients: exciting financial incentives for vmware cloud foundation on ibm cloud.
4 min read - New client specials: Get up to 50% off when you commit to a 1- or 3-year term contract on new VCF-as-a-Service offerings, plus an additional value of up to USD 200K in credits through 30 June 2025 when you migrate your VMware workloads to IBM Cloud®.1 Low starting prices: On-demand VCF-as-a-Service deployments begin under USD 200 per month.2 The IBM Cloud benefit: See the potential for a 201%3 return on investment (ROI) over 3 years with reduced downtime, cost and…
IBM Partner Plus Day: Celebrating our collaborative journey with the IBM Ecosystem
4 min read - Today we kicked off IBM Think 2024 in Boston with Partner Plus Day, a full day dedicated to our partners who are driving client innovation, business growth and scaling the adoption of transformative technology such as generative AI. It is also the perfect opportunity to reflect on the progress and success of the IBM Ecosystem, more than a year after we introduced Partner Plus, the program that embodies our new era of partner-first collaboration. Our partners have generated remarkable business…
How will quantum impact the biotech industry?
5 min read - The physics of atoms and the technology behind treating disease might sound like disparate fields. However, in the past few decades, advances in artificial intelligence, sensing, simulation and more have driven enormous impacts within the biotech industry. Quantum computing provides an opportunity to extend these advancements with computational speedups and/or accuracy in each of those areas. Now is the time for enterprises, commercial organizations and research institutions to begin exploring how to use quantum to solve problems in their respective domains. As a Partner in IBM’s Quantum practice, I've had the pleasure of working…
IBM Newsletters
- Product overview
- All features
- App integrations
CAPABILITIES
- project icon Project management
- Project views
- Custom fields
- Status updates
- goal icon Goals and reporting
- Reporting dashboards
- workflow icon Workflows and automation
- portfolio icon Resource management
- Time tracking
- my-task icon Admin and security
- Admin console
- asana-intelligence icon Asana Intelligence
- list icon Personal
- premium icon Starter
- briefcase icon Advanced
- Goal management
- Organizational planning
- Campaign management
- Creative production
- Content calendars
- Marketing strategic planning
- Resource planning
- Project intake
- Product launches
- Employee onboarding
- View all uses arrow-right icon
- Project plans
- Team goals & objectives
- Team continuity
- Meeting agenda
- View all templates arrow-right icon
- Work management resources Discover best practices, watch webinars, get insights
- What's new Learn about the latest and greatest from Asana
- Customer stories See how the world's best organizations drive work innovation with Asana
- Help Center Get lots of tips, tricks, and advice to get the most from Asana
- Asana Academy Sign up for interactive courses and webinars to learn Asana
- Developers Learn more about building apps on the Asana platform
- Community programs Connect with and learn from Asana customers around the world
- Events Find out about upcoming events near you
- Partners Learn more about our partner programs
- Support Need help? Contact the Asana support team
- Asana for nonprofits Get more information on our nonprofit discount program, and apply.
Featured Reads
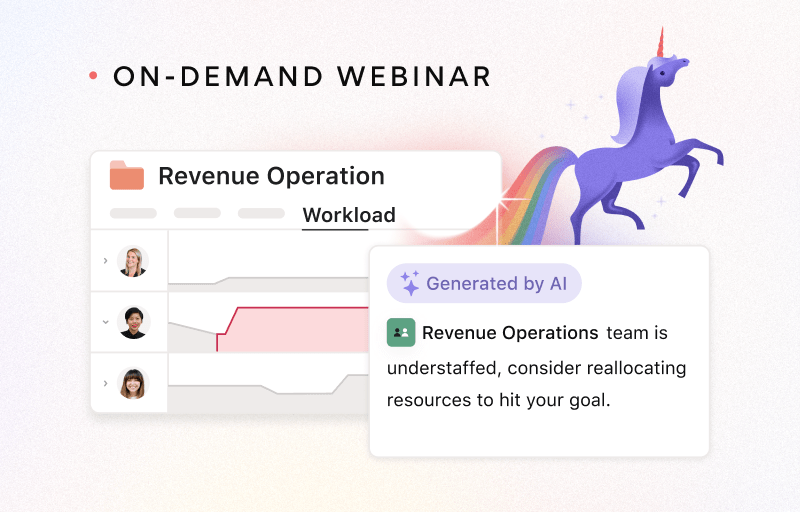
- Project management |
- 7 types of process improvement methodol ...
7 types of process improvement methodologies you should know about
Business process improvements are methodologies in which a team evaluates their current processes and adapts them in order to increase profitability. This article highlights seven different process improvements your team can use to reduce inefficiencies and increase profit.
If businesses decided to consistently stay the same over time, many of them would collapse. Innovation requires change, and if businesses don’t change to meet customer demands, they won’t achieve much growth.
This is why many organizations use some form of process improvement methodology to adapt their processes to customer demands.
What is process improvement?
Business process improvements are methodologies in which a team evaluates their current processes and adapts them with the intent to increase productivity, streamline workflows, adapt to changing business needs, or increase profitability.
7 types of process improvement methodologies
There are seven different business process improvement methodologies your team can use to help reduce inefficiencies. In most cases, the methodology you choose depends on why you want to improve your processes and what you’re looking to improve.
1. Six Sigma methodology
Six Sigma is often used in manufacturing, mainly because it helps minimize defects and inconsistencies. The goal here is to optimize for consistency, which in the end leads to customer satisfaction.
There are two main processes used in Six Sigma: DMAIC for existing processes and DMADV for new processes. Since this article focuses specifically on improvements to existing processes, let’s dive into the DMAIC process.
What is the DMAIC process?
DMAIC is a Six Sigma process used to optimize existing processes. DMAIC stands for:
Define the opportunity for improvement.
Measure the performance of your existing processes.
Analyze the process to find defects and root causes.
Improve processes by addressing root causes.
Control any improved processes and assess future process performance to correct deviations.
The bulk of the DMAIC process improvement happens during the analysis stage. During the analysis stage of DMAIC, teams use a fishbone diagram, or an Ishikawa diagram , to visualize the possible causes of a product defect. The head of the fishbone diagram states the initial problem—then as you follow along the spine of the fish, each rib lists different categories of issues that can lead to the initial problem. This type of visual analysis is a good way to identify the different issues one root cause can create.
2. Total Quality Management (TQM)
Total quality management (TQM) is a customer-focused method that involves continuous improvement over time. This technique is often used in supply chain management and customer satisfaction projects.
TQM relies heavily on data-driven decisions and performance metrics. During the problem solving process, you use success metrics to decide how you can improve a process.
Here some key features of TQM:
Customer-focus: The end goal of TQM is always to benefit the end customer. If your team is focused on improving quality, ask yourself how that process change may affect how end consumers experience your product.
Full-team involvement: Unlike other process improvement methodologies TQM involves the entire team—not just production. As a result, you may end up looking for ways to optimize more business-centric processes, such as sales and marketing, to benefit the end consumer.
Continuous improvement: Continuous improvement in business is the idea of making small changes with the goal of continually optimizing processes. There's a lot of variability when it comes to business, and continuous improvement helps your team adapt when outside circumstances change.
Data-driven decision making : In order to apply continuous process improvement, you must continually collect data to analyze how processes are performing. This data can help identify where there may be inefficiencies and where to focus improvement initiatives.
Process-focused: The main goal of implementing TQM is to improve processes. Other process improvement methods like Six Sigma work to minimize the amount of defects, while TQM works to decrease inefficiencies.
3. Lean manufacturing
This form of process improvement goes by many names, with lean manufacturing being the most common. It may also be referred to as Lean production or just-in-time production. Defined by James P. Womack, Daniel Jones, and Daniel Roos in the book "The Machine That Changed the World," Lean highlights five main principles based off of the authors' experiences at Toyota manufacturing.
The 5 principles of lean
Identify value
Value stream mapping
Create flow
Establish pull
Continuous improvement
4. Continuous improvement (kaizen)
The Japanese philosophy of kaizen guides the continuous improvement model . Kaizen was born from the idea that life should be continuously improved so we can lead more satisfying and fulfilling lives.
This same concept can be applied to business—because as long as you are continuously improving, your business can become more successful. The goal of continuous improvement is to optimize for activities that generate value and to get rid of any waste.
There are three types of waste that kaizen aims to remove:
Muda (wastefulness) : Practices that consume resources but don’t add value.
Mura (unevenness): Overproduction that leaves behind waste, like excess product.
Muri (overburden): Too much strain on resources, such as worn out machinery or overworked employees.
5. Plan Do Check Act (PDCA)
The PDCA cycle is an interactive form of problem solving. It's used to improve processes and implement change. PDCA was created by Walter Shewhart when he applied the scientific method to economic quality control. Later, the idea was developed even further by W. Edwards Deming, who expanded on Shewhart's idea and used the scientific method for process improvement in addition to quality control.
There are four main steps to the PDCA cycle:
Plan : Decide on the problem you would like to solve, and create a plan to solve it.
Do: Test and implement the plan at a small scale.
Check: Review how the actions in the Do stage performed.
Act: After reviewing the results of the test, decide whether or not you want to implement the change at a larger scale.
PDCA is an improvement cycle. This means that these steps can be repeated until your team reaches the desired result.
6. 5 Whys analysis
The 5 Whys analysis is a process improvement technique used to identify the root cause of a problem. It's a really simple process in theory: you gather a group of stakeholders who were involved in a failure, and one person asks: "Why did this go wrong?" Repeat this question approximately five times, until you get to the root cause of an issue. The 5 Whys analysis aims to identify the issues within a process, but not human error.
Here's an example:
Problem: There was an increase in customer complaints regarding damaged products.
"Why did this happen?" Because packaging was not sufficient enough to protect the products.
"Why was the packaging not sufficient enough to protect the products?" Because the team testing packaging did not test past a certain level of stress.
"Why did the team not test the packaging further?" Because current standard processes indicated that the testing indicated was sufficient.
"Why did the current standard process indicate that this testing was sufficient?" Because this process was created for a previous product, and not this current product that is coming back damaged.
"Why wasn’t there a new process for the new product?" Because the project template for launching new products doesn’t include stress testing the new packaging.
You can see from this example that the team asked “Why” until they identified the process error that needs to be fixed—in this case, adding a “stress test new packaging” step into their product launch template . When working with stakeholders in processes like this, it's important to identify the issues, and co-create next steps together so that your production can improve.
7. Business process management (BPM)
Business process management, or BPM , is the act of analyzing and improving business processes. Much like any organic being, businesses grow and shift over time. Your team may have implemented processes that worked when your team was small, but as you grow those processes may not scale in a way that allows your team to be as efficient as possible.
Most of the time, BPM helps teams identify bottlenecks, ways to automate manual work, and strategies to improve inefficiencies. There are five main steps to business process management.
Analyze: Look at your current processes and map them from beginning to end. This is commonly known as process mapping.
Model: Draft out what you want the process to look like. Ideally, you'll have found any inefficiencies in the first step, and you can draft how you would like to solve them in this stage.
Implement : Put your model to action. During this stage, it's important to establish key success metrics so you can gauge whether or not the changes made were successful.
Monitor: Decide whether or not your project is successful. Are the success metrics you identified in step three improving?
Optimize: As the process evolves, continue looking for inefficiencies in your process and continuously optimize as you go.
Manage process improvements to increase productivity
As a team lead, one of the most valuable things you can bring to your team are clearer processes and better workflows . When used effectively, process improvement increases your team's productivity and decreases inefficiencies.
To increase clarity and improve processes, try work management. Work management tools like Asana can help you take your team’s productivity to the next level by standardizing processes, streamlining workflows, and keeping your team in sync.
Related resources
What is a flowchart? Symbols and types explained
What are story points? Six easy steps to estimate work in Agile
How to choose project management software for your team
7 steps to complete a social media audit (with template)
- Leadership Team
- Our Approach
- PMO Services
- Program & Project Managers
- PM Training & Development
- Case Studies
- Our Culture
- Employee Benefits
- Job Opportunities
- Benefits Realization Management Diagnostic
- Project Management Maturity Guide
- Guide to Agile Project Management
- PM Maturity Assessment
- Project Management as a Service (PMaaS) and Why It’s the Future
About PM Solutions
PM Solutions is a project management consulting firm that helps PMO, project, and business leaders apply project and portfolio management practices that drive performance and operational efficiency.
- Co-Founder & Co-CEO J. Kent Crawford
- Co-Founder & Co-CEO Deborah Bigelow Crawford
- President, PM Solutions & PM College Bruce Miller
- Vice President, Client Success, Eric Foss
- Managing Director, HR & Administration, Karen Alfonsi
- Director, Marketing and Communications, Carrie Capili
With our approach , companies can expect high-value, high-impact solutions, and measurable, sustainable results.
- PMO Deployment, Operation, and Enhancement
- Project Management as a Service (PMaaS)
- Project Review & Recovery
- Project Portfolio Management (PPM)
- Project Management Maturity Advancement
- Organizational Change Management
- Project Management Methodology Implementation
- Demand Management
- Project Management Mentors
- Resource Management
- Vendor Management
Project & Program Managers
We can provide you with highly experienced program and project managers ; experts to help guide, lead, and support high-visibility initiatives.
PM Training & Development
PM College® provides corporate project management training and competency programs for clients around the world.
By Project Initiatives
- Cost Reduction Initiatives (1)
- Data Center Consolidation (1)
- High-risk Capital Initiatives (1)
- Infrastructure Program Management (0)
- Manufacturing Facility Operations (1)
- Mentoring (11)
- Methodology (4)
- New Product Development (1)
- Organizational Change (6)
- PMO Assessment (4)
- PMO Deployment (4)
- Process Improvement (7)
- Program & Portfolio Management (10)
- Project Audits (1)
- Project Management Training (7)
- Regulatory Compliance (1)
- Resource Management (1)
- Strategy Execution (1)
- Systems Integration Deployment (0)
- Troubled Project Recovery (3)
- Vendor Management (2)
By Industry
- Automotive (1)
- Energy & Utilities (7)
- Financial Services (2)
- Human Resources (1)
- Information Technology (5)
- Insurance (5)
- Manufacturing (6)
- Pharma/Biotech (2)
- Professional Services (2)
- Research and Development (1)
- Retail & Merchandise (1)
- Security (1)
- Benefits Realization (4)
- Change Management (6)
- IT Project Management (4)
- Outsourcing Project Management (4)
- Performance & Value Measurement (12)
- Project Management Maturity (23)
- Project Management Methodology (12)
- Project Management Office (58)
- Project Management Training (31)
- Project Management Trends (50)
- Project Manager Competency (18)
- Project Portfolio Management (11)
- Project Recovery (9)
- Resource Management (5)
- Strategy & Governance (14)
- Articles (46)
- Brochures (3)
- eNewsletters (19)
- Research (46)
- Webinars (24)
- White Papers (36)
- contact us get in touch call: 800.983.0388
Home » Case Studies » Process Improvement
Pm solutions has a proven experience in providing solutions to a broad range of markets. our project management case studies cover a wide variety of needs across a number of industries., more process improvement case studies, ontario power generation achieves project excellence through the establishment of an enterprise project management office.
"We have really changed public perception, and as a result, increased our credibility in OPG’s ability to execute projects. “- Mike Martelli, Chief Projects Officer, OPG Read More »
- Energy & Utilities
- PMO Assessment
- Process Improvement
- Program & Portfolio Management
PM Governance Combined with Agile Tools Improves Delivery and Quality of Financial Services Programs
Changing state and federal regulatory compliance challenges caused this company to reinvent its custom-built storefront and home office systems. The IT and PMO teams were geared more for operational maintenance rather than for the complexities of developing new systems. This resulted in an overwhelming workload and schedule overrun measured in years. A years-overdue project was brought to Operational Pilot, saving millions in development time. Read More »
- Financial Services
- Methodology
Transformative Leadership Sets Financial Services Enterprise PMO on Fast Track to Strategic Value
For this privately held financial services company, a compelling journey of business transformation started with a good read. Read More »
- PMO Deployment
- Project Management Training
- Strategy Execution
Pharmaceutical Company’s Internal PM Certification Program Brings More Predictable Project Outcomes
An internal PM certification program was rapidly developed and implemented. During the first three years, over 400 participants attended more than 30 courses. Team members, project managers, and sponsors gained a good understanding of project management and the techniques needed to achieve more consistent project delivery. The program’s ability to remain intact after an acquisition validated the program’s value to the larger company globally. Read More »
- Pharma/Biotech
Accident Fund’s Award-Winning PMO Puts Processes Before Tools in Implementing Project Portfolio Management
PM Solutions used its PPM Maturity and Project Management Maturity Models to develop an improvement roadmap that included a number of specific recommendations from a project management governance perspective. Established PPM processes that helped eliminate approximately 100 non-value-adding projects, led to the successful implementation of a PPM tool, and won the company national acclaim – all in under three years. Read More »
Mentoring Brings an Enhanced Focus on Accountability to Merchants Insurance Group
PM Solutions led a targeted mentoring program for the client's project leads to provide one-on-one advice and coaching on how to apply consistent project management practices within the confines of their actual projects. Value Delivered: Improved on-time project delivery to 80% resulting in one program booking $100,000 of business in the first three days, and another program realizing 758% revenue growth in the first two months of introduction. Read More »
Wireless Warehouse Initiative Transforms Materials Management Operations and Improves Delivery Speed by 66%
For a world-wide provider of turbine-driven gas compression, oil pumping and power generation packages: PM Solutions provided a senior-level project manager to lead the implementation of a warehouse radio frequency (RF) solution, being responsible for overseeing requirements gathering, systems design, procurement and installation of the necessary hardware and software, and coordinating user acceptance testing. Value Delivered: Thanks to a retooling of the materials management system incorporating RF automation, the company’s warehouse accelerated delivery speed of parts by 66%, creating a significant reduction in overall time to market. This complex automation project came in on time and more than 18% under budget. Read More »
- Information Technology
- eNewsletters
- White Papers
- PMO of the Year Award
Connect with Us
The project management experts®.
PM Solutions is a project management services firm helping organizations apply project management and PMO practices to improve business performance.
Toll-free (US): 800.983.0388 International: +1.484.450.0100 [email protected]
285 Wilmington-West Chester Pike Chadds Ford, PA 19317 USA
© 2012-2024 Project Management Solutions, Inc. All Rights Reserved. Privacy & Terms
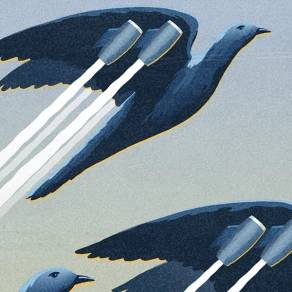
Related Expertise: Culture and Change Management , Business Strategy , Corporate Strategy
Five Case Studies of Transformation Excellence
November 03, 2014 By Lars Fæste , Jim Hemerling , Perry Keenan , and Martin Reeves
In a business environment characterized by greater volatility and more frequent disruptions, companies face a clear imperative: they must transform or fall behind. Yet most transformation efforts are highly complex initiatives that take years to implement. As a result, most fall short of their intended targets—in value, timing, or both. Based on client experience, The Boston Consulting Group has developed an approach to transformation that flips the odds in a company’s favor. What does that look like in the real world? Here are five company examples that show successful transformations, across a range of industries and locations.
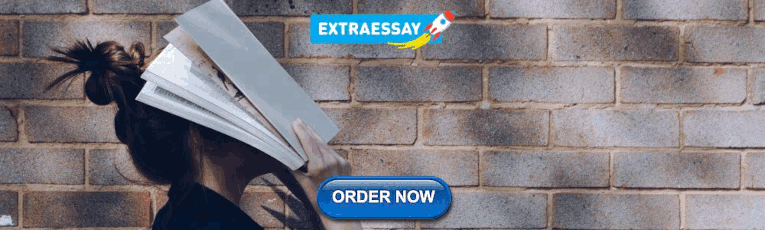
VF’s Growth Transformation Creates Strong Value for Investors
Value creation is a powerful lens for identifying the initiatives that will have the greatest impact on a company’s transformation agenda and for understanding the potential value of the overall program for shareholders.
VF offers a compelling example of a company using a sharp focus on value creation to chart its transformation course. In the early 2000s, VF was a good company with strong management but limited organic growth. Its “jeanswear” and intimate-apparel businesses, although responsible for 80 percent of the company’s revenues, were mature, low-gross-margin segments. And the company’s cost-cutting initiatives were delivering diminishing returns. VF’s top line was essentially flat, at about $5 billion in annual revenues, with an unclear path to future growth. VF’s value creation had been driven by cost discipline and manufacturing efficiency, yet, to the frustration of management, VF had a lower valuation multiple than most of its peers.
With BCG’s help, VF assessed its options and identified key levers to drive stronger and more-sustainable value creation. The result was a multiyear transformation comprising four components:
- A Strong Commitment to Value Creation as the Company’s Focus. Initially, VF cut back its growth guidance to signal to investors that it would not pursue growth opportunities at the expense of profitability. And as a sign of management’s commitment to balanced value creation, the company increased its dividend by 90 percent.
- Relentless Cost Management. VF built on its long-known operational excellence to develop an operating model focused on leveraging scale and synergies across its businesses through initiatives in sourcing, supply chain processes, and offshoring.
- A Major Transformation of the Portfolio. To help fund its journey, VF divested product lines worth about $1 billion in revenues, including its namesake intimate-apparel business. It used those resources to acquire nearly $2 billion worth of higher-growth, higher-margin brands, such as Vans, Nautica, and Reef. Overall, this shifted the balance of its portfolio from 70 percent low-growth heritage brands to 65 percent higher-growth lifestyle brands.
- The Creation of a High-Performance Culture. VF has created an ownership mind-set in its management ranks. More than 200 managers across all key businesses and regions received training in the underlying principles of value creation, and the performance of every brand and business is assessed in terms of its value contribution. In addition, VF strengthened its management bench through a dedicated talent-management program and selective high-profile hires. (For an illustration of VF’s transformation roadmap, see the exhibit.)
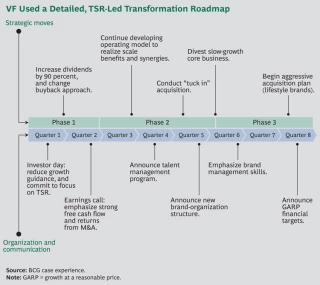
The results of VF’s TSR-led transformation are apparent. 1 1 For a detailed description of the VF journey, see the 2013 Value Creators Report, Unlocking New Sources of Value Creation , BCG report, September 2013. Notes: 1 For a detailed description of the VF journey, see the 2013 Value Creators Report, Unlocking New Sources of Value Creation , BCG report, September 2013. The company’s revenues have grown from $7 billion in 2008 to more than $11 billion in 2013 (and revenues are projected to top $17 billion by 2017). At the same time, profitability has improved substantially, highlighted by a gross margin of 48 percent as of mid-2014. The company’s stock price quadrupled from $15 per share in 2005 to more than $65 per share in September 2014, while paying about 2 percent a year in dividends. As a result, the company has ranked in the top quintile of the S&P 500 in terms of TSR over the past ten years.
A Consumer-Packaged-Goods Company Uses Several Levers to Fund Its Transformation Journey
A leading consumer-packaged-goods (CPG) player was struggling to respond to challenging market dynamics, particularly in the value-based segments and at the price points where it was strongest. The near- and medium-term forecasts looked even worse, with likely contractions in sales volume and potentially even in revenues. A comprehensive transformation effort was needed.
To fund the journey, the company looked at several cost-reduction initiatives, including logistics. Previously, the company had worked with a large number of logistics providers, causing it to miss out on scale efficiencies.
To improve, it bundled all transportation spending, across the entire network (both inbound to production facilities and out-bound to its various distribution channels), and opened it to bidding through a request-for-proposal process. As a result, the company was able to save 10 percent on logistics in the first 12 months—a very fast gain for what is essentially a commodity service.
Similarly, the company addressed its marketing-agency spending. A benchmark analysis revealed that the company had been paying rates well above the market average and getting fewer hours per full-time equivalent each year than the market standard. By getting both rates and hours in line, the company managed to save more than 10 percent on its agency spending—and those savings were immediately reinvested to enable the launch of what became a highly successful brand.
Next, the company pivoted to growth mode in order to win in the medium term. The measure with the biggest impact was pricing. The company operates in a category that is highly segmented across product lines and highly localized. Products that sell well in one region often do poorly in a neighboring state. Accordingly, it sought to de-average its pricing approach across locations, brands, and pack sizes, driving a 2 percent increase in EBIT.
Similarly, it analyzed trade promotion effectiveness by gathering and compiling data on the roughly 150,000 promotions that the company had run across channels, locations, brands, and pack sizes. The result was a 2 terabyte database tracking the historical performance of all promotions.
Using that information, the company could make smarter decisions about which promotions should be scrapped, which should be tweaked, and which should merit a greater push. The result was another 2 percent increase in EBIT. Critically, this was a clear capability that the company built up internally, with the objective of continually strengthening its trade-promotion performance over time, and that has continued to pay annual dividends.
Finally, the company launched a significant initiative in targeted distribution. Before the transformation, the company’s distributors made decisions regarding product stocking in independent retail locations that were largely intuitive. To improve its distribution, the company leveraged big data to analyze historical sales performance for segments, brands, and individual SKUs within a roughly ten-mile radius of that retail location. On the basis of that analysis, the company was able to identify the five SKUs likely to sell best that were currently not in a particular store. The company put this tool on a mobile platform and is in the process of rolling it out to the distributor base. (Currently, approximately 60 percent of distributors, representing about 80 percent of sales volume, are rolling it out.) Without any changes to the product lineup, that measure has driven a 4 percent jump in gross sales.
Throughout the process, management had a strong change-management effort in place. For example, senior leaders communicated the goals of the transformation to employees through town hall meetings. Cognizant of how stressful transformations can be for employees—particularly during the early efforts to fund the journey, which often emphasize cost reductions—the company aggressively talked about how those savings were being reinvested into the business to drive growth (for example, investments into the most effective trade promotions and the brands that showed the greatest sales-growth potential).
In the aggregate, the transformation led to a much stronger EBIT performance, with increases of nearly $100 million in fiscal 2013 and far more anticipated in 2014 and 2015. The company’s premium products now make up a much bigger part of the portfolio. And the company is better positioned to compete in its market.
A Leading Bank Uses a Lean Approach to Transform Its Target Operating Model
A leading bank in Europe is in the process of a multiyear transformation of its operating model. Prior to this effort, a benchmarking analysis found that the bank was lagging behind its peers in several aspects. Branch employees handled fewer customers and sold fewer new products, and back-office processing times for new products were slow. Customer feedback was poor, and rework rates were high, especially at the interface between the front and back offices. Activities that could have been managed centrally were handled at local levels, increasing complexity and cost. Harmonization across borders—albeit a challenge given that the bank operates in many countries—was limited. However, the benchmark also highlighted many strengths that provided a basis for further improvement, such as common platforms and efficient product-administration processes.
To address the gaps, the company set the design principles for a target operating model for its operations and launched a lean program to get there. Using an end-to-end process approach, all the bank’s activities were broken down into roughly 250 processes, covering everything that a customer could potentially experience. Each process was then optimized from end to end using lean tools. This approach breaks down silos and increases collaboration and transparency across both functions and organization layers.
Employees from different functions took an active role in the process improvements, participating in employee workshops in which they analyzed processes from the perspective of the customer. For a mortgage, the process was broken down into discrete steps, from the moment the customer walks into a branch or goes to the company website, until the house has changed owners. In the front office, the system was improved to strengthen management, including clear performance targets, preparation of branch managers for coaching roles, and training in root-cause problem solving. This new way of working and approaching problems has directly boosted both productivity and morale.
The bank is making sizable gains in performance as the program rolls through the organization. For example, front-office processing time for a mortgage has decreased by 33 percent and the bank can get a final answer to customers 36 percent faster. The call centers had a significant increase in first-call resolution. Even more important, customer satisfaction scores are increasing, and rework rates have been halved. For each process the bank revamps, it achieves a consistent 15 to 25 percent increase in productivity.
And the bank isn’t done yet. It is focusing on permanently embedding a change mind-set into the organization so that continuous improvement becomes the norm. This change capability will be essential as the bank continues on its transformation journey.
A German Health Insurer Transforms Itself to Better Serve Customers
Barmer GEK, Germany’s largest public health insurer, has a successful history spanning 130 years and has been named one of the top 100 brands in Germany. When its new CEO, Dr. Christoph Straub, took office in 2011, he quickly realized the need for action despite the company’s relatively good financial health. The company was still dealing with the postmerger integration of Barmer and GEK in 2010 and needed to adapt to a fast-changing and increasingly competitive market. It was losing ground to competitors in both market share and key financial benchmarks. Barmer GEK was suffering from overhead structures that kept it from delivering market-leading customer service and being cost efficient, even as competitors were improving their service offerings in a market where prices are fixed. Facing this fundamental challenge, Barmer GEK decided to launch a major transformation effort.
The goal of the transformation was to fundamentally improve the customer experience, with customer satisfaction as a benchmark of success. At the same time, Barmer GEK needed to improve its cost position and make tough choices to align its operations to better meet customer needs. As part of the first step in the transformation, the company launched a delayering program that streamlined management layers, leading to significant savings and notable side benefits including enhanced accountability, better decision making, and an increased customer focus. Delayering laid the path to win in the medium term through fundamental changes to the company’s business and operating model in order to set up the company for long-term success.
The company launched ambitious efforts to change the way things were traditionally done:
- A Better Client-Service Model. Barmer GEK is reducing the number of its branches by 50 percent, while transitioning to larger and more attractive service centers throughout Germany. More than 90 percent of customers will still be able to reach a service center within 20 minutes. To reach rural areas, mobile branches that can visit homes were created.
- Improved Customer Access. Because Barmer GEK wanted to make it easier for customers to access the company, it invested significantly in online services and full-service call centers. This led to a direct reduction in the number of customers who need to visit branches while maintaining high levels of customer satisfaction.
- Organization Simplification. A pillar of Barmer GEK’s transformation is the centralization and specialization of claim processing. By moving from 80 regional hubs to 40 specialized processing centers, the company is now using specialized administrators—who are more effective and efficient than under the old staffing model—and increased sharing of best practices.
Although Barmer GEK has strategically reduced its workforce in some areas—through proven concepts such as specialization and centralization of core processes—it has invested heavily in areas that are aligned with delivering value to the customer, increasing the number of customer-facing employees across the board. These changes have made Barmer GEK competitive on cost, with expected annual savings exceeding €300 million, as the company continues on its journey to deliver exceptional value to customers. Beyond being described in the German press as a “bold move,” the transformation has laid the groundwork for the successful future of the company.
Nokia’s Leader-Driven Transformation Reinvents the Company (Again)
We all remember Nokia as the company that once dominated the mobile-phone industry but subsequently had to exit that business. What is easily forgotten is that Nokia has radically and successfully reinvented itself several times in its 150-year history. This makes Nokia a prime example of a “serial transformer.”
In 2014, Nokia embarked on perhaps the most radical transformation in its history. During that year, Nokia had to make a radical choice: continue massively investing in its mobile-device business (its largest) or reinvent itself. The device business had been moving toward a difficult stalemate, generating dissatisfactory results and requiring increasing amounts of capital, which Nokia no longer had. At the same time, the company was in a 50-50 joint venture with Siemens—called Nokia Siemens Networks (NSN)—that sold networking equipment. NSN had been undergoing a massive turnaround and cost-reduction program, steadily improving its results.
When Microsoft expressed interest in taking over Nokia’s device business, Nokia chairman Risto Siilasmaa took the initiative. Over the course of six months, he and the executive team evaluated several alternatives and shaped a deal that would radically change Nokia’s trajectory: selling the mobile business to Microsoft. In parallel, Nokia CFO Timo Ihamuotila orchestrated another deal to buy out Siemens from the NSN joint venture, giving Nokia 100 percent control over the unit and forming the cash-generating core of the new Nokia. These deals have proved essential for Nokia to fund the journey. They were well-timed, well-executed moves at the right terms.
Right after these radical announcements, Nokia embarked on a strategy-led design period to win in the medium term with new people and a new organization, with Risto Siilasmaa as chairman and interim CEO. Nokia set up a new portfolio strategy, corporate structure, capital structure, robust business plans, and management team with president and CEO Rajeev Suri in charge. Nokia focused on delivering excellent operational results across its portfolio of three businesses while planning its next move: a leading position in technologies for a world in which everyone and everything will be connected.
Nokia’s share price has steadily climbed. Its enterprise value has grown 12-fold since bottoming out in July 2012. The company has returned billions of dollars of cash to its shareholders and is once again the most valuable company in Finland. The next few years will demonstrate how this chapter in Nokia’s 150-year history of serial transformation will again reinvent the company.

Managing Director & Senior Partner
San Francisco - Bay Area

Managing Director & Senior Partner, Chairman of the BCG Henderson Institute
ABOUT BOSTON CONSULTING GROUP
Boston Consulting Group partners with leaders in business and society to tackle their most important challenges and capture their greatest opportunities. BCG was the pioneer in business strategy when it was founded in 1963. Today, we work closely with clients to embrace a transformational approach aimed at benefiting all stakeholders—empowering organizations to grow, build sustainable competitive advantage, and drive positive societal impact.
Our diverse, global teams bring deep industry and functional expertise and a range of perspectives that question the status quo and spark change. BCG delivers solutions through leading-edge management consulting, technology and design, and corporate and digital ventures. We work in a uniquely collaborative model across the firm and throughout all levels of the client organization, fueled by the goal of helping our clients thrive and enabling them to make the world a better place.
© Boston Consulting Group 2024. All rights reserved.
For information or permission to reprint, please contact BCG at [email protected] . To find the latest BCG content and register to receive e-alerts on this topic or others, please visit bcg.com . Follow Boston Consulting Group on Facebook and X (formerly Twitter) .
Subscribe to our Business Transformation E-Alert.

- Get started
11 Ideas for Process Improvement: Examples & Tips

You’re running business processes on a daily basis, and so, it’s easy to fall into the mentality of “It’s how we’ve always done it.” By implementing ideas for process improvement, you can dramatically increase your business’ efficiency, save costs, and reduce mistakes.

Knowing process improvement methodologies is a great place to start because it provides you with a way to execute upon a process improvement plan. In this article, we will look at process improvement ideas for work and see how automation solutions can help put them in action.
1. What is Process Improvement?
2. What are the Benefits of Process Improvement?
3. What are Ideas for Process Improvement?
4. What are Process Improvement Examples?
5. What are Process Improvement Techniques?
6. Closing Thoughts
What is Process Improvement?
Process improvement is the act of identifying, analysing, and enhancing existing business processes. The goal is to optimise performance and improve upon standards that will result in better quality and user experiences for end users/customers.
Business process improvement makes it possible to:
- Generate better quality projects
- Reduce the consequences of human/manual errors
- Eliminate and remove waste
- Expedite process and project completion
- Limit friction
By reducing waste, streamlining steps, and minimising errors, everyone that interacts within and outside of the business gets to benefit.
What are the Benefits of Process Improvement?
Speaking of benefits, let’s outline what you stand to gain by putting in practice the upcoming ideas for process improvement:
1. Increased Productivity
Business process improvement tends to entail the deployment of automation software to streamline processes. As a result, companies get to benefit from greater productivity.
In fact, research showed that workers spend an average of 520 hours annually taking care of repetitive tasks that could instead be automated.
2. Enhanced Customer Satisfaction
The goal of any business is to satisfy and add value to its customers’ lives. With process improvement, customers get to gain from better customer service, as well as improved product quality. As a result, customer satisfaction increases.
3. Improved Employee Satisfaction
Along with happy customers comes happier employees as they no longer have to waste time on manual, repetitive, and monotonous tasks. Instead, they can allocate their efforts towards creative, strategic, and greater value add responsibilities.
4. Reduced Risk
Process improvement with automation can lead to greater internal control, visibility, and transparency. This means that companies are able to reduce their risks associated with security, safety, compliance and more.
What are Ideas for Process Improvement?
Now you may be wondering, how can you get started with process improvement to reap the aforementioned benefits and more?
We’re going to share a few ideas for process improvement. With these ideas in mind, consider your own business’ functions to see what project improvement ideas are most fitting and relevant.
Along with this list, keep in mind that process improvement is especially useful for finance functions, such as reconciliations, regulatory reporting, revenue management, expense analytics, and more.
1. Tracking Time and Analysis
At the heart of every process your business runs sits the people that do the work. Oftentimes, procrastination will cause business processes to be thwarted or result in added waste.
With the rise of remote workers and the distaste for micromanagement, time tracking and analysis software can be of service.
Such software is able to provide screenshots as proof of work, automatically generated timesheets, and time reports that help managers and stakeholders understand where employees’ time is being spent.
2. Team Performance Monitoring
While time tracking can offer immediate benefits and improvement opportunities, it’s also useful to monitor team performance. To quantify performance, you can use project status tracking to figure out where bottlenecks may exist.
To overcome bottlenecks, automation solutions can be used to streamline processes and offer each responsible party with greater visibility into what’s needed of them at any given time.
3. Project Management Process
Most business processes are repetitive by nature. As such, it’s effective to designate a project management process so that every key stage is clearly broken down into its phases.
This also helps to ensure that every individual who is involved in a part of the process is aware of what they have to do. Automation software is useful for this too because you get to visualise processes, map them out, and assign roles and responsibilities by doing so.
4. Communication
As with any good relationship, including business relationships, communication is the primary foundation. With poor communication between departments and colleagues, processes can get stuck and important details may fall through the cracks.
By improving communication and collaboration (as with automation software and tools), you can work smoother and better.
5. Eliminate Waste
A primary method to improve processes is to identify and eliminate waste that stem from inefficient processes.
To begin identifying waste, you should look out for: excess processing, reporting, overproduction, unused inventory, defects, stuck products, unnecessary moving of product, ineffective motion of people, and underutilised or non-utilised talent.
6. Reduce Costs
Like eliminating waste, it’s also possible to improve processes by reducing costs. Cost reduction can be found by removing unnecessary or duplicate tasks, automating manual tasks, and reviewing the flow of processes to ensure that the order of tasks are designed as best as can be.
7. Improve Process Visualisation
Another idea to improve processes is to start by visualising processes to gain a deep understanding of processes.
Process visualisation makes it possible to see the various steps, the people involved, and the time it takes to run through each step. By visualising the process, you can identify inefficiencies, bottlenecks, or issues.
8. Revenue Generation
Like cutting costs, you can also aim your process improvement efforts to generate increased revenue.
To do so, you can explore ideas like: creating new services or products, expanding your markets, marketing to existing customers creatively, expanding partnerships, and improving relationships within the business.
9. Quality Improvement
Another go-to method for process improvement is to focus on bettering the quality of services and goods. Automating processes is a great way to reduce mistakes and thereby increase the output’s quality. Another method to identify inefficiencies is to practise the “5 Whys” to find the root cause of any quality defects.
10. Efficiency
A focus on efficiency means that you’ll look to eliminate redundant work, reduce meetings to those that are necessary, ensure supplies are provided as required, and streamline approval processes.
11. Review and Optimise
As you execute upon your ideas for process improvement, remember that continual process improvement is the name of the game. As such, you can constantly review and optimise processes.
With automation software, this becomes easier to do because you’ll be able to access up-to-date insights and recognise where process improvement possibilities lie.
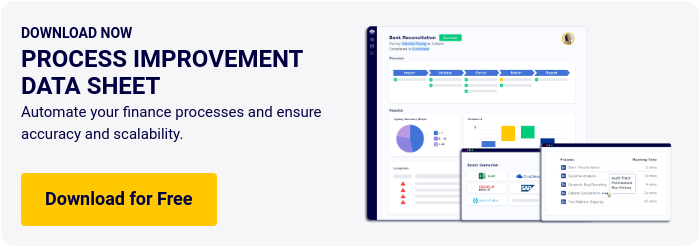
What are Process Improvement Examples?
Ideas for process improvement can be best understood by reviewing some examples. Here’s a look at what’s possible:
1. Data Accuracy:
Mistakes are commonly occurring due to data inaccuracy and manual data entry errors. Correcting these mistakes can save time, money, and damage in the short and long-term. Automation software can collect, connect, and standardise data needs in less time with greater accuracy.
2. Extra Processing
Time is wasted having to re-enter data, create reports, budget, and scan paper documentation. This leads to bottlenecks and delays.
3. Waiting Time
System downtime and managerial approval is another way that processes get stuck in limbo. With automation software, processes flow smoothly plus the data can be stored securely in the cloud so available remotely if needed. If they hit any snags, the necessary people are notified to keep the process moving along.
4. Overproduction:
A key issue in many businesses is overproduction. Whether it be in terms of products or paperwork, overproduction leads to waste and extra unnecessary costs.
What are Process Improvement Techniques?
There’s a long list of process improvement methodologies to try when you’re seeking to make your business run more efficiently.
To get a general overview, here’s a quick summary of popular process improvement techniques:
PDSA stands for: Plan, Do, Study, and Act. It entails defining the problem and ideating solutions, implementing the chosen solution, analysing its effectiveness, and then adding the change as part of the standard procedure for work.
5S is a process improvement technique for better safety and efficiency. It covers a series of steps including: Sort, Set in Order, Shine, Standardise, Sustain.
3. The 5 Whys
To find the root cause of an inefficiency, ask “Why” five times in a row to get to the bottom of it.

Closing Thoughts
Once you have these ideas for process improvement in mind, it’s time to get to making your business run better. Process improvement is intended to be a recurring activity. With that said, once you implement an improvement, be sure to monitor the outcome to make sure that your desired results are the reality.
Automation software can be your holy grail to achieve process improvement on multiple levels. From helping you visualise existing processes to managing manual and error-prone tasks and analysing outcomes, automation bridges the gap between existing processing and your to-be processes.
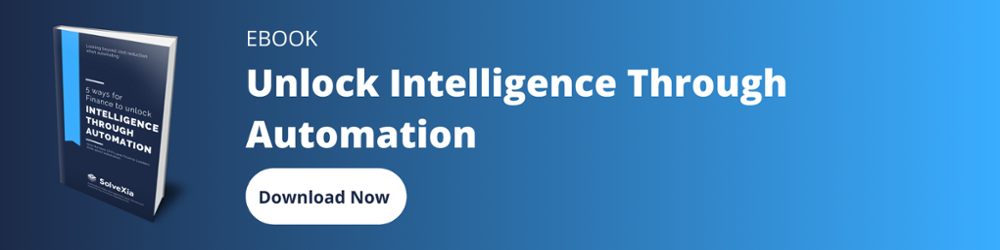
Related Posts
Our top guides, our top guide, popular posts, free up time and reduce errors, intelligent reconciliation solution, intelligent rebate management solution, recommended for you.
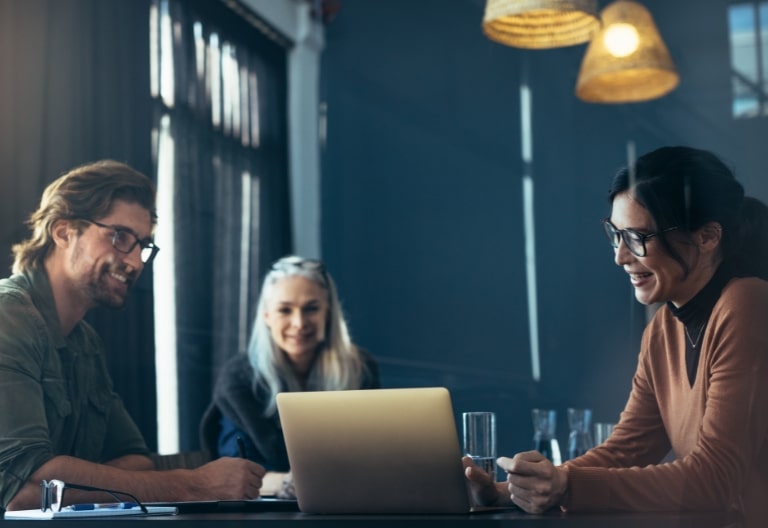
Request a Demo
Book a 30-minute call to see how our intelligent software can give you more insights and control over your data and reporting.
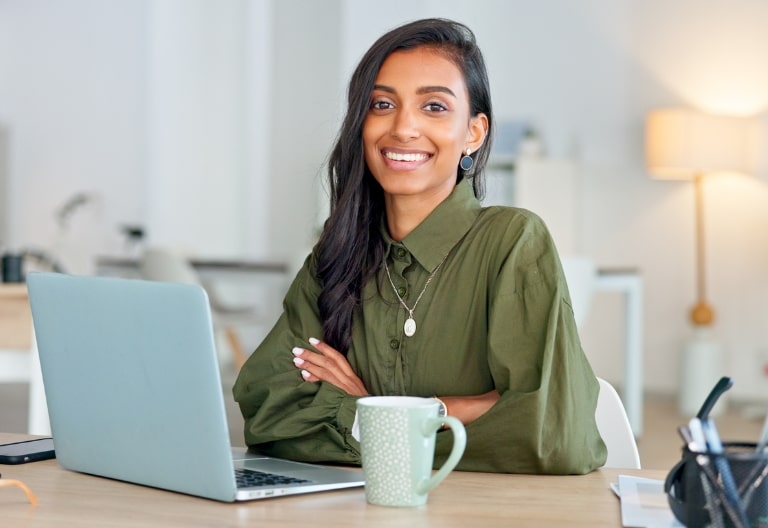
Reconciliation Data Sheet
Download our data sheet to learn how to automate your reconciliations for increased accuracy, speed and control.
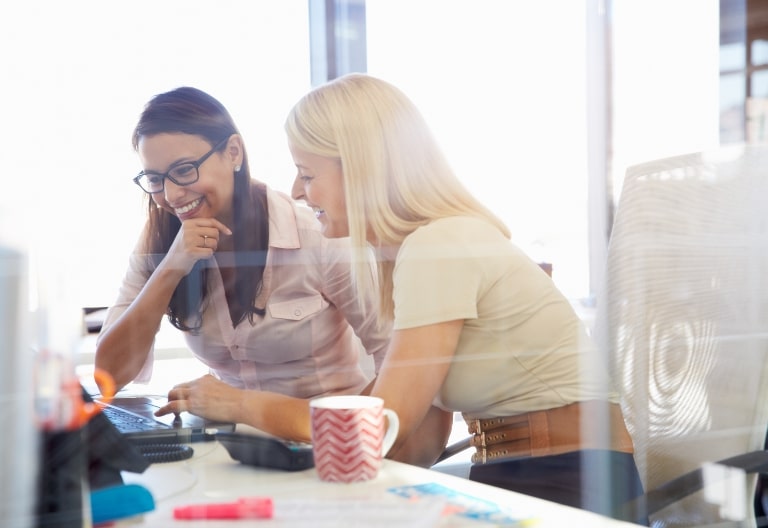
Regulatory Reporting Data Sheet
Download our data sheet to learn how you can prepare, validate and submit regulatory returns 10x faster with automation.
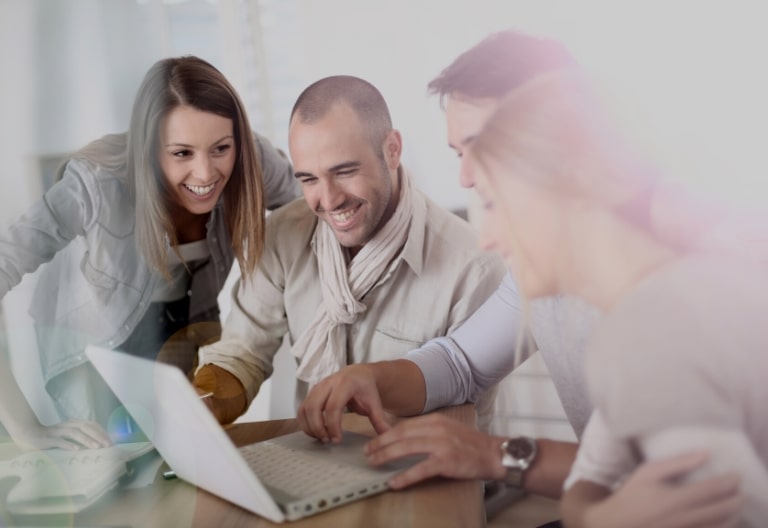
Financial Automation Data Sheet
Download our data sheet to learn how you can run your processes up to 100x faster and with 98% fewer errors.
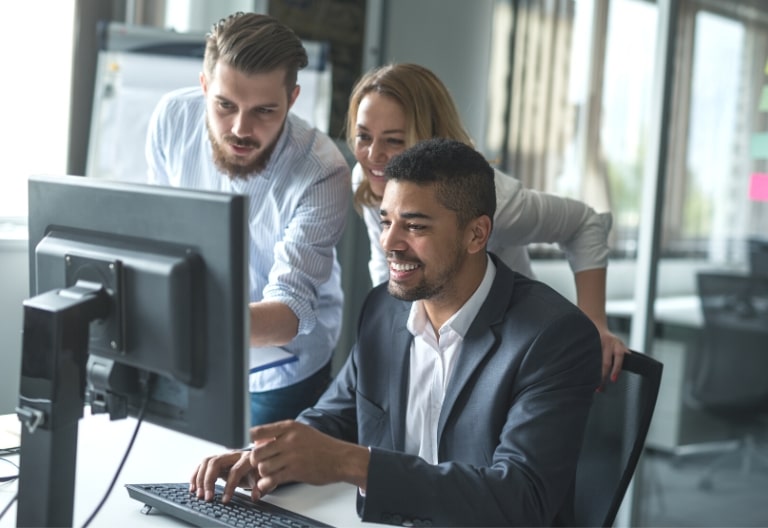
Rebate Management Data Sheet
Download our data sheet to learn how you can manage complex vendor and customer rebates and commission reporting at scale.
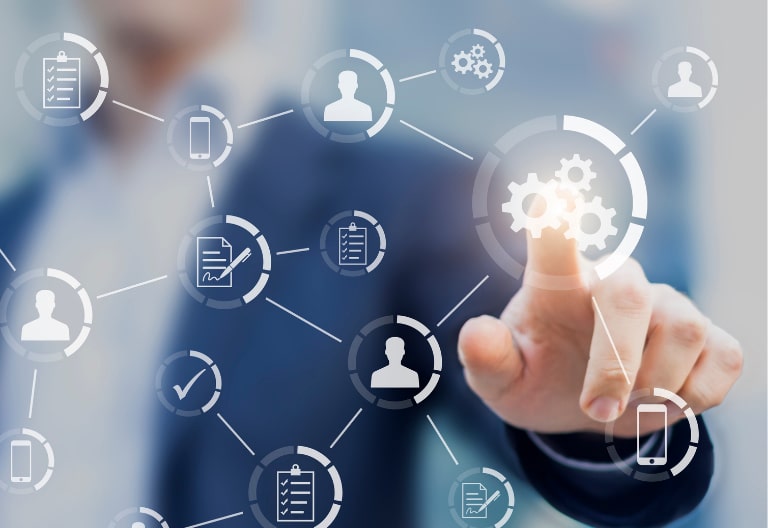
Top 10 Automation Challenges for CFOs
Learn how you can avoid and overcome the biggest challenges facing CFOs who want to automate.
Latest Blog Posts
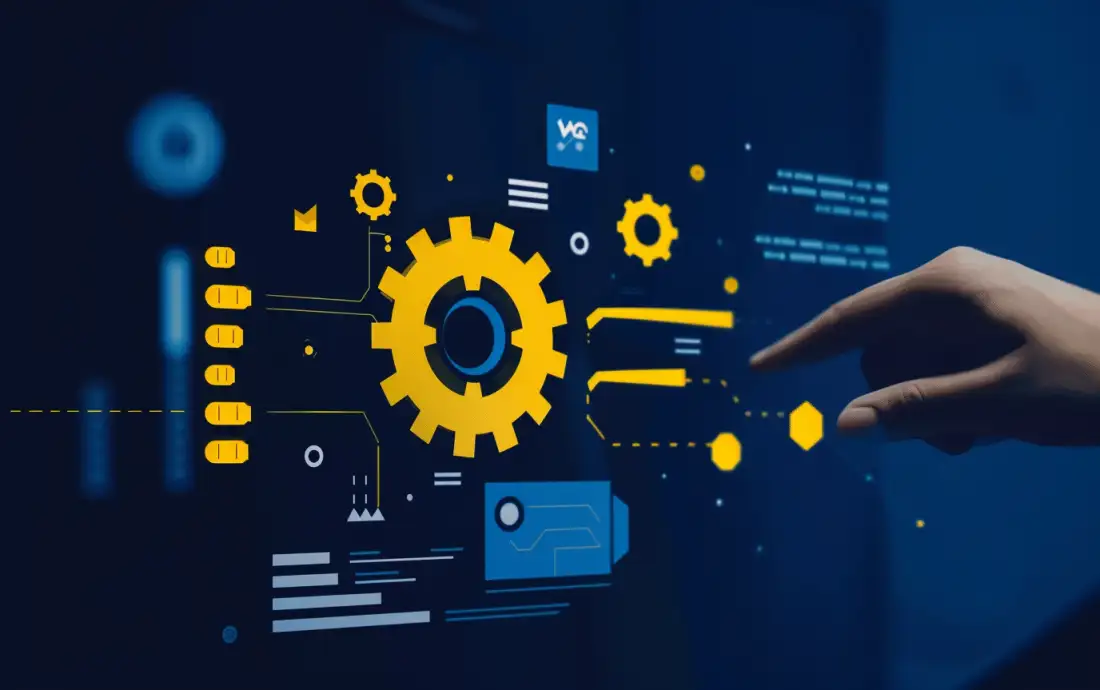
Best Business Process Modelling Tools for 2024
Business process modelling tools help a business and CFOs reach its goals by realising, measuring, and monitoring how operations function.
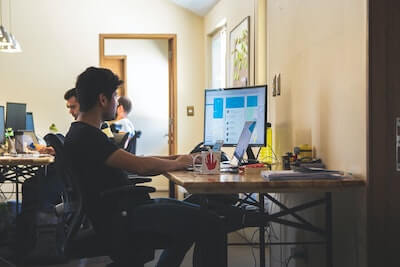
Best Workflow Approval Software
When choosing the right workflow approval software for your business, there are many aspect to consider. Find out here.
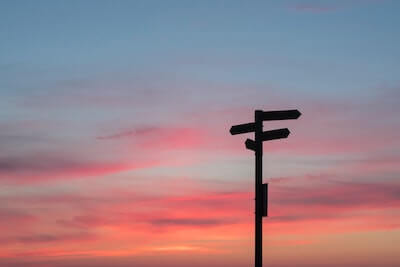
7 Models of Change Management Every CFO Must Know
There are various models of change that every CFO should know to run their business. See the breakdown of 7 change management.
We use essential cookies to make Venngage work. By clicking “Accept All Cookies”, you agree to the storing of cookies on your device to enhance site navigation, analyze site usage, and assist in our marketing efforts.
Manage Cookies
Cookies and similar technologies collect certain information about how you’re using our website. Some of them are essential, and without them you wouldn’t be able to use Venngage. But others are optional, and you get to choose whether we use them or not.
Strictly Necessary Cookies
These cookies are always on, as they’re essential for making Venngage work, and making it safe. Without these cookies, services you’ve asked for can’t be provided.
Show cookie providers
- Google Login
Functionality Cookies
These cookies help us provide enhanced functionality and personalisation, and remember your settings. They may be set by us or by third party providers.
Performance Cookies
These cookies help us analyze how many people are using Venngage, where they come from and how they're using it. If you opt out of these cookies, we can’t get feedback to make Venngage better for you and all our users.
- Google Analytics
Targeting Cookies
These cookies are set by our advertising partners to track your activity and show you relevant Venngage ads on other sites as you browse the internet.
- Google Tag Manager
- Infographics
- Daily Infographics
- Popular Templates
- Accessibility
- Graphic Design
- Graphs and Charts
- Data Visualization
- Human Resources
- Beginner Guides
Blog Human Resources How to Create a Process Improvement Plan [20+ Templates Included]
How to Create a Process Improvement Plan [20+ Templates Included]
Written by: Jennifer Gaskin Jun 12, 2023
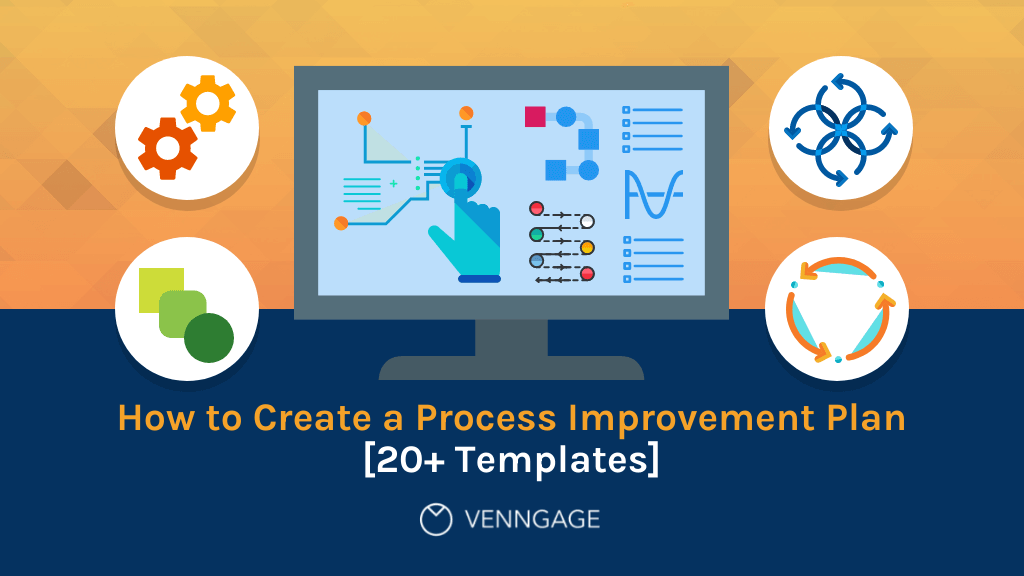
A process improvement plan is a comprehensive and actionable document that outlines the necessary steps to enhance the efficiency, effectiveness and overall performance of processes and procedures within your company. It serves as a roadmap to identify areas of improvement, address bottlenecks, streamline workflows and optimize resource utilization.
By creating a process improvement plan , companies can proactively drive positive change, foster continuous improvement and achieve higher levels of operational excellence.
Many aspects of process improvement can benefit from visual communication tools like infographics, presentations, mind maps and more. Venngage simplifies process improvement for Learning and Development teams with user-friendly plan templates for efficient implementation and management.
Click to jump ahead:
How do you create a process improvement plan?
What are the most common types of process improvement plans, what is an example of process improvement, types of process improvement plan & examples, what are the benefits of establishing a process improvement plan, process improvement plan faq.
A well-designed process improvement plan can streamline operations, enhance efficiency and drive organizational growth. To help you navigate this crucial endeavor, here are ten essential steps to create a process improvement plan that yields measurable results:
- Identify the Goals: Define the specific objectives you aim to achieve through process improvement. For example, reducing customer wait times by 20% or decreasing production errors by 15%.
- Analyze Current Processes: Thoroughly evaluate existing workflows to identify bottlenecks, inefficiencies and areas of improvement. For instance, examine how information flows between departments or how inventory is managed.
- Gather Stakeholder Input: Engage employees, managers and other relevant stakeholders to gather insights and perspectives on process challenges. Example: Conduct interviews or surveys, or integrate a cloud contact center solution to collect feedback on pain points and potential solutions.
- Prioritize Improvement Areas: Based on the analysis and stakeholder input, prioritize the areas that require immediate attention. This might involve identifying high-impact processes that, when improved, will have a significant positive effect on the organization.
- Set Measurable Objectives: Establish specific and measurable objectives that align with the identified improvement areas. These objectives should be quantifiable and time-bound. For example, reduce customer complaints by 25% within six months.
- Develop Action Plans: Create detailed action plans for each improvement area, outlining the steps, responsibilities and timelines for implementing changes. For instance, assign a cross-functional team to streamline the order fulfillment process and develop a timeline for completing the necessary changes. Consider having action plan templates in place so there you team has a framework for how to accomplish processes.
- Implement Changes: Execute the action plans while closely monitoring progress and ensuring adherence to the established timelines. Example: Introduce new software to automate manual data entry tasks and track key performance indicators.
- Measure Results: Regularly measure and evaluate the impact of the implemented changes against the set objectives. This may involve tracking metrics like cost savings, productivity improvements, or customer satisfaction ratings.
- Adjust and Refine: Based on the results, identify any gaps or areas that need further improvement. Adjust the action plans accordingly, making iterative refinements to continuously optimize processes.
- Communicate & Engage : Keep all stakeholders informed about the progress of the process improvement initiatives and encourage their ongoing involvement. Share success stories and celebrate achievements to sustain motivation and engagement.
By adhering to these useful guidelines, you will forge a formidable process enhancement blueprint that propels transformative growth within your organization. Keep in mind that process improvement is an ever-evolving odyssey and constant scrutiny and fine-tuning will safeguard perpetual triumph in fine-tuning your operations.
Process Improvement Plan Case Study
Following the steps we outlined earlier, let’s explore a hypothetical process improvement plan for a doctor’s office that constantly gets complaints from patients about how many forms they have to fill out.
Process Improvement Plan: Reducing Patient Form Burden in a Doctor’s Office
- Identify the Goals: The goal is to streamline the patient intake process and reduce the number of forms patients have to fill out, resulting in improved patient satisfaction and reduced administrative burden.
- Analyze Current Processes: Evaluate the existing patient intake process to identify the number and types of forms patients are required to complete, as well as any redundancies or inefficiencies in the process.
- Gather Stakeholder Input: Engage with patients, front desk staff and healthcare providers to understand their perspectives on form-related challenges and potential solutions. Conduct surveys or hold focus group discussions to gather feedback.
- Prioritize Improvement Areas: Identify key areas where form reduction can have the most significant impact on patient experience and administrative efficiency. For example, focus on eliminating redundant information across forms or consolidating multiple forms into a single comprehensive document.
- Set Measurable Objectives: Establish specific objectives, such as reducing the number of forms by 50% within three months, minimizing the time patients spend filling out forms by 25% or achieving a patient satisfaction rating of 80% regarding the form intake process.
- Develop Action Plans: Create action plans to streamline the patient intake process and minimize form requirements. Examples of actions may include:
- Conduct a thorough review of existing forms and identify areas of overlap or duplication.
- Consult with legal and compliance teams to ensure necessary information is captured while minimizing redundancies.
- Explore the possibility of implementing electronic forms or online pre-registration to expedite the process.
- Train front desk staff on the new streamlined process and educate them on assisting patients in completing forms efficiently.
- Implement Changes: Execute the action plans by implementing the agreed-upon improvements. This could involve revising and consolidating forms, implementing electronic forms or online pre-registration systems and providing staff training on the revised process.
- Measure Results: Regularly measure and evaluate the impact of the implemented changes against the set objectives. Track metrics such as the number of forms eliminated, time saved for patients and patient satisfaction ratings related to the revised intake process.
- Adjust and Refine: Based on the results and ongoing feedback, identify any areas that require further improvement. Refine the process by addressing any remaining pain points or bottlenecks to ensure a seamless and efficient patient intake experience.
- Communicate and Engage: Maintain open communication with patients, staff and healthcare providers throughout the process improvement journey. Inform patients about the changes and improvements made to the form intake process and encourage their feedback and suggestions for further enhancements.
By implementing this process improvement plan, the doctor’s office can minimize the burden on patients by reducing the number of forms they need to fill out, resulting in improved patient satisfaction and streamlined administrative processes. Remember that continuous evaluation and refinement are essential to adapt to evolving patient needs and ensure ongoing improvements in the patient intake experience.
You can customize this process improvement plan template to reflect the example above:
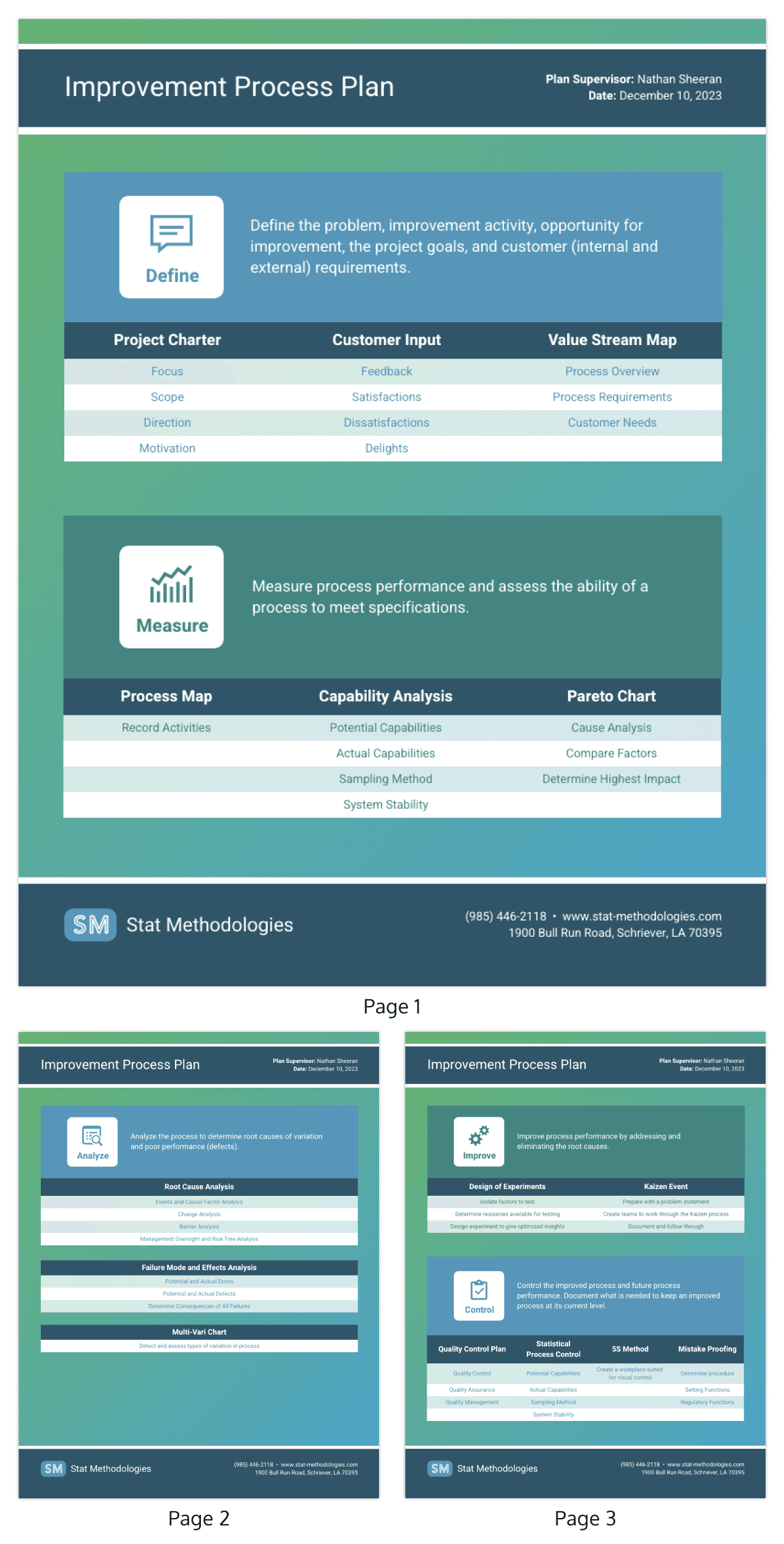
There are found major methods of process improvement that you may consider integrating into your process improvement plans. Some of these methods are used in the largest companies in the world.
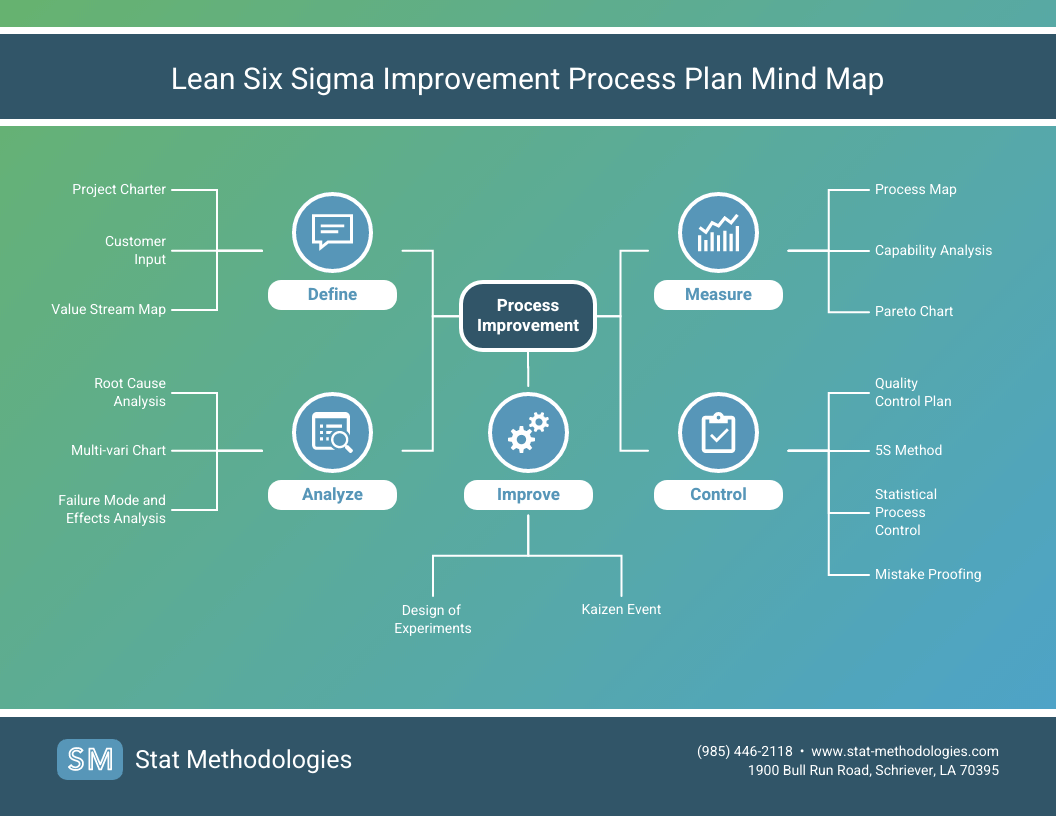
A quality control method developed by a Motorola engineer, Six Sigma has become a global phenomenon and Six Sigma certification is highly sought-after in many industries. Six Sigma outlines five steps for improving existing business practices, abbreviated to DMAIC:
Here’s how a process improvement plan should be when using the Six Sigma method:
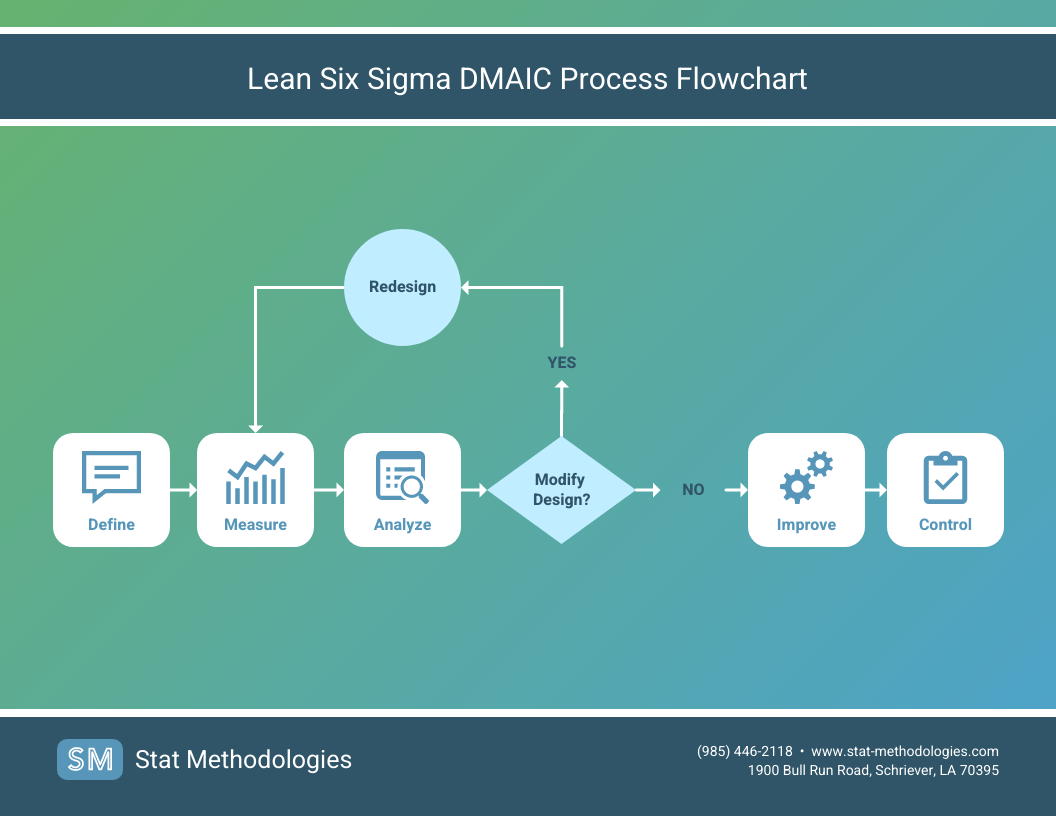
Lean & Lean Six Sigma
Lean traditionally is used by manufacturing companies, but the principles are useful across all industries and as its name suggests, Lean process improvement plans focus on reducing waste. In particular, Lean aims to eliminate any activities that do not add value to the end user of the good or service. The steps are:
- Identify value
- Map value stream
- Create flow
- Establish pull
- Seek perfection
Lean Six Sigma is the hybrid of the two methods, helping organizations improve processes through DMAIC while also eliminating waste.
Total quality management (TQM)
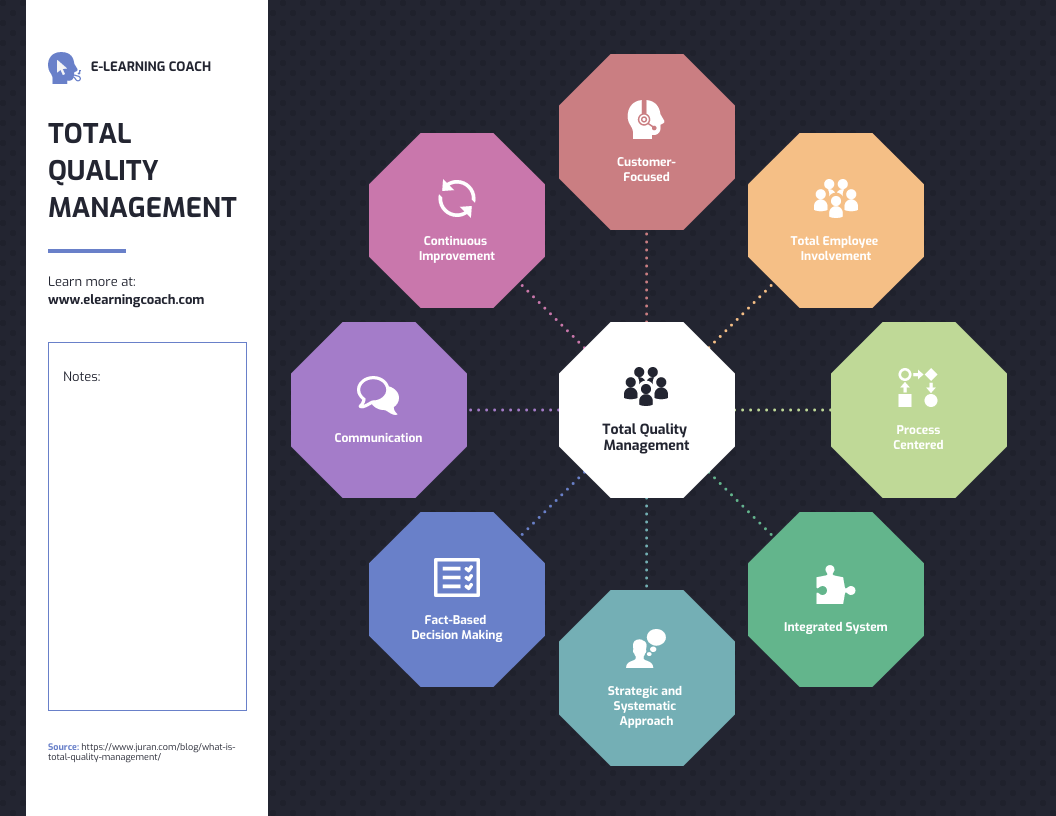
Total quality management (TQM) had its heyday in the 1980s and early 1990s before the advent of Lean and Six Sigma, but its main objectives are still valid today. TQM process development plans focus primarily on quality control, ensuring that the company’s output is of the highest possible quality and determining ways to make output even better.
TQM doesn’t have steps as most other process improvement methods do. Rather, it focuses on principles that should guide an organization with a TQM mindset:
- Customer-focused
- Total employee involvement
- Process-centric
- Full team integration
- Strategic and systemic
- Data-driven decisions
- Constant communication
Plan-Do-Check-Act (PDCA)
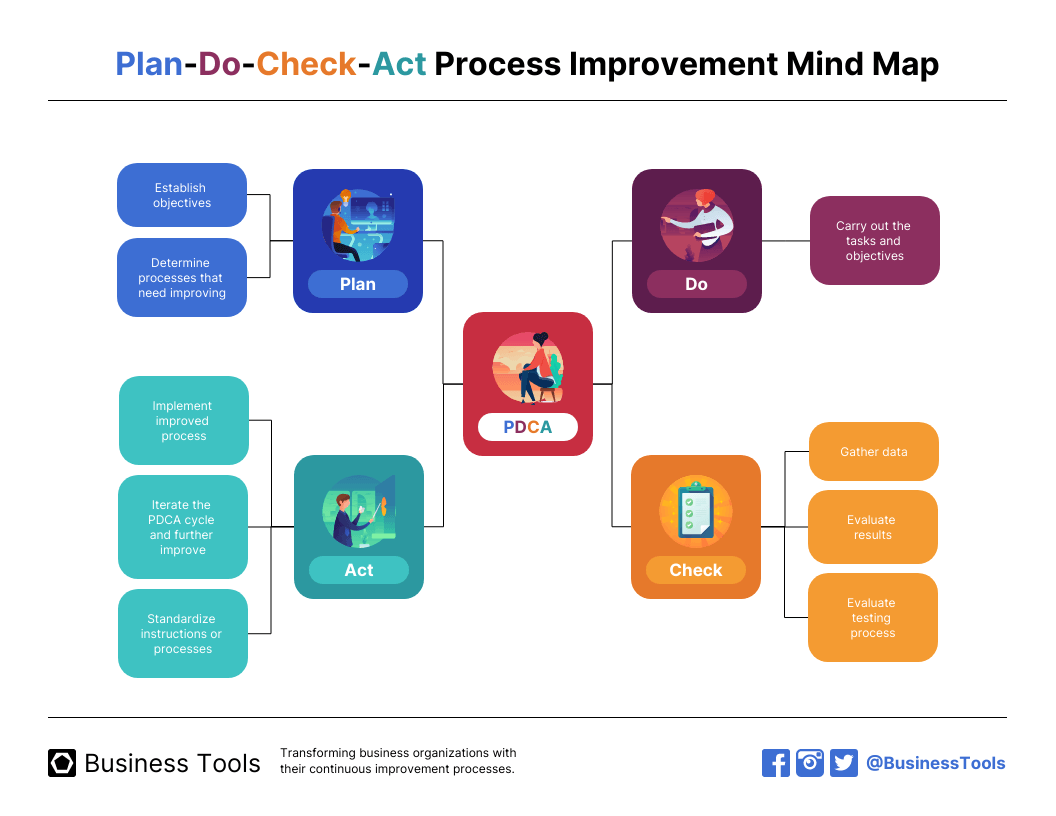
Plan-Do-Check-Act (PDCA) is a continuous change management cycle that was first established by engineer and management consultant W. Edwards Deming in the 1950s. Back then it was called a Deming Wheel , which was later modified by Japanese engineers to arrive at its current definition.
The steps involved in PDCA are obvious:
As the name suggests, process improvement refers to the task of identifying, analyzing and improving existing business processes that are often outdated or no longer efficient enough.
While the term is most often used in a business context, it can refer to any decision or actions that aim to improve a process, be it as simple as finding a shorter route on your drive to work or as complex as improving the whole customer service process of a corporation.
Back to its business context, process improvement could target wasteful spending, poor office design, IT system downtime, employee disengagement and many other issues that can doom an organization.
Process improvement can’t be effective without proper process documentation policies in place. If you haven’t documented your company’s processes yet, we can help with that. Check out these process documentation templates to get you started.
There’s more than one type of process improvement plan, which we’ll explore more in detail . In addition to the example we shared above, a process improvement plan can also consist of 6 steps:
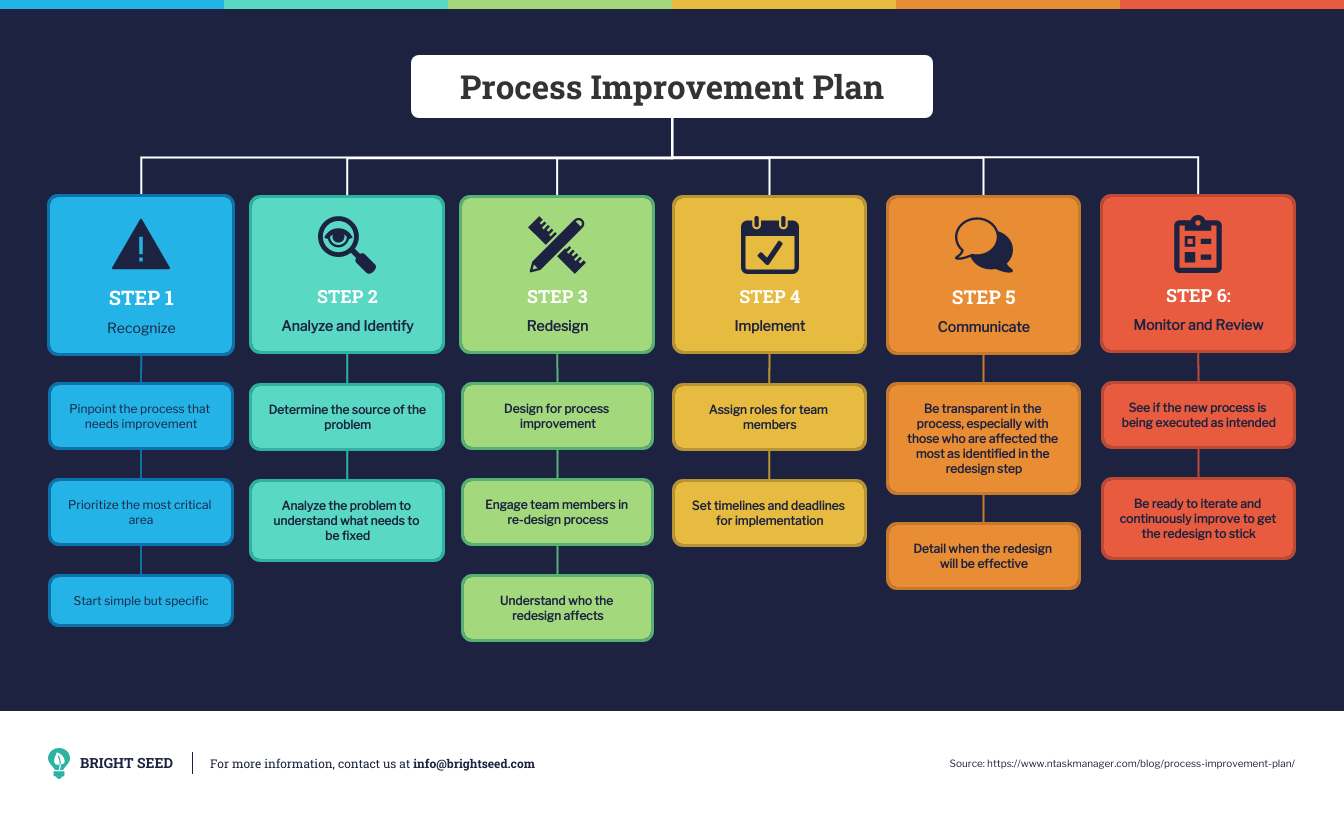
Or 4 steps, like this one which is developed using the Plan-Do-Check-Act (PDCA) model:
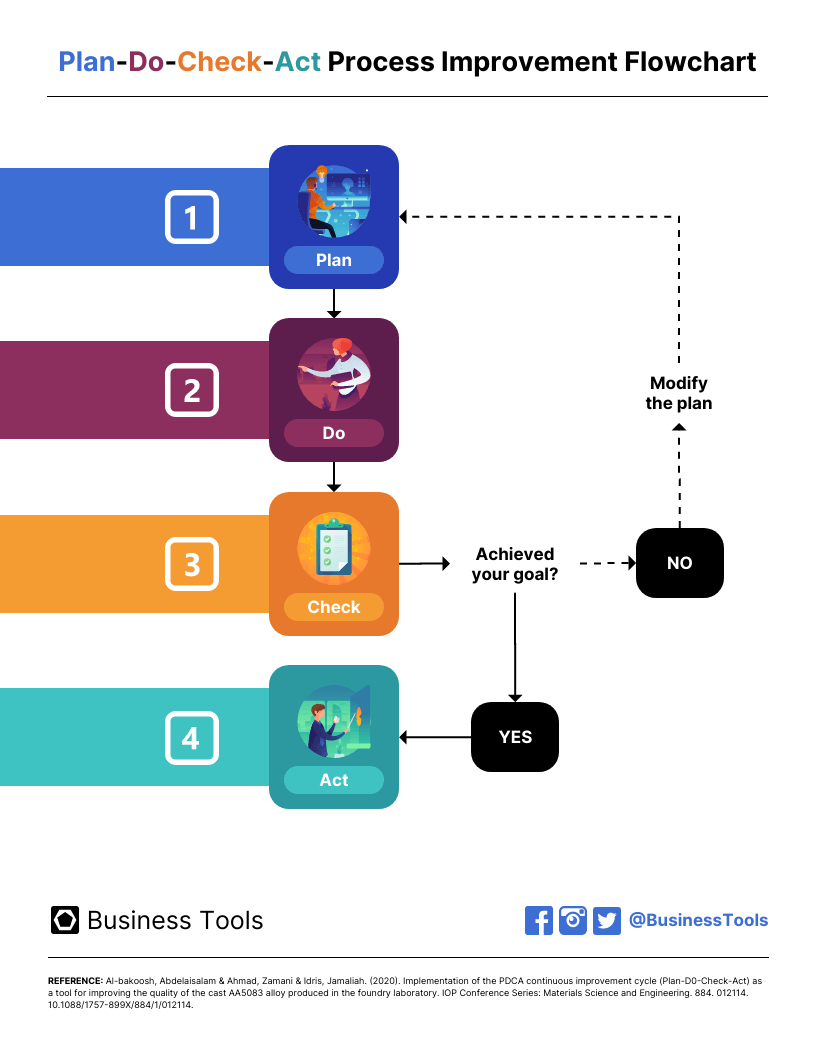
These steps are, of course, quite simplified and some process improvement plans will require months or years of changes to procedures, hiring practices, training, systems, software and more.
For example, a process improvement plan for a company lacking a specific skill set in its employees can mean hiring new staff and training the existing one. In cases like this, other tools like individual development plans can be useful.
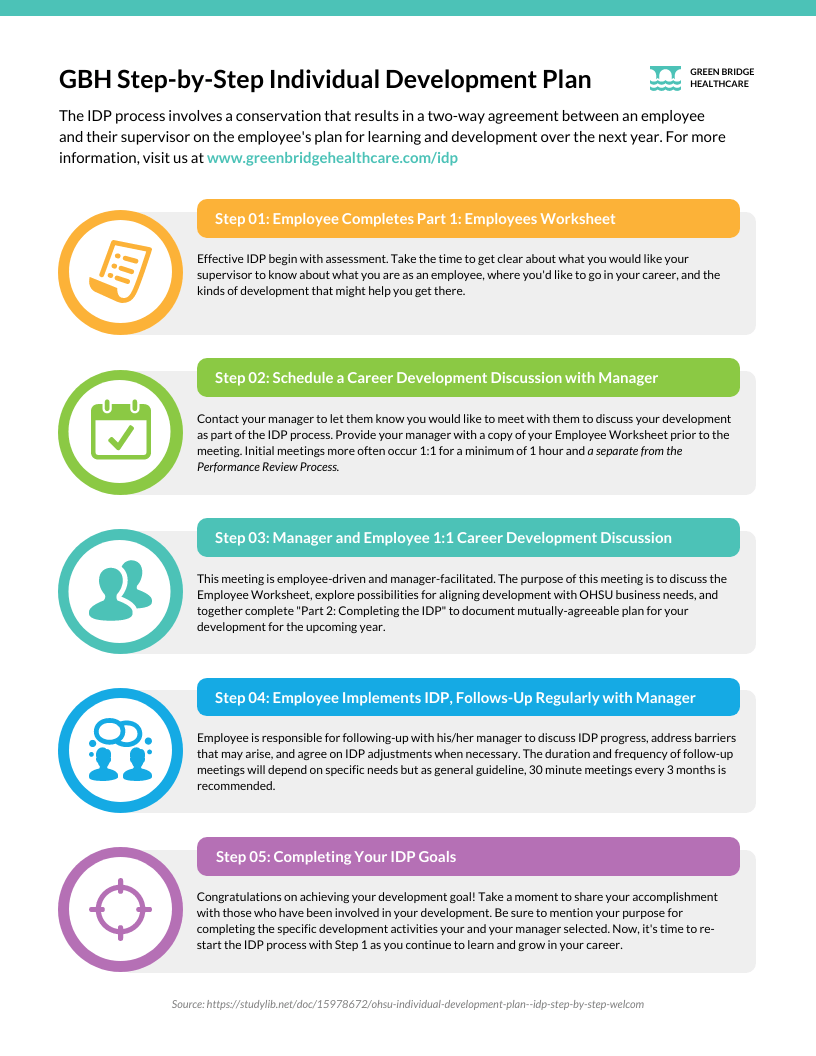
This individual development plan designed for healthcare workers is a good example of how process improvement plans can branch off into other areas.
And once the new process is in place, it’s important to communicate it to the team effectively. That could be through a process infographic , timeline , mind map or other types of visual communication .
Customize this project communication plan to help streamline communication channels between teams working on the same project:
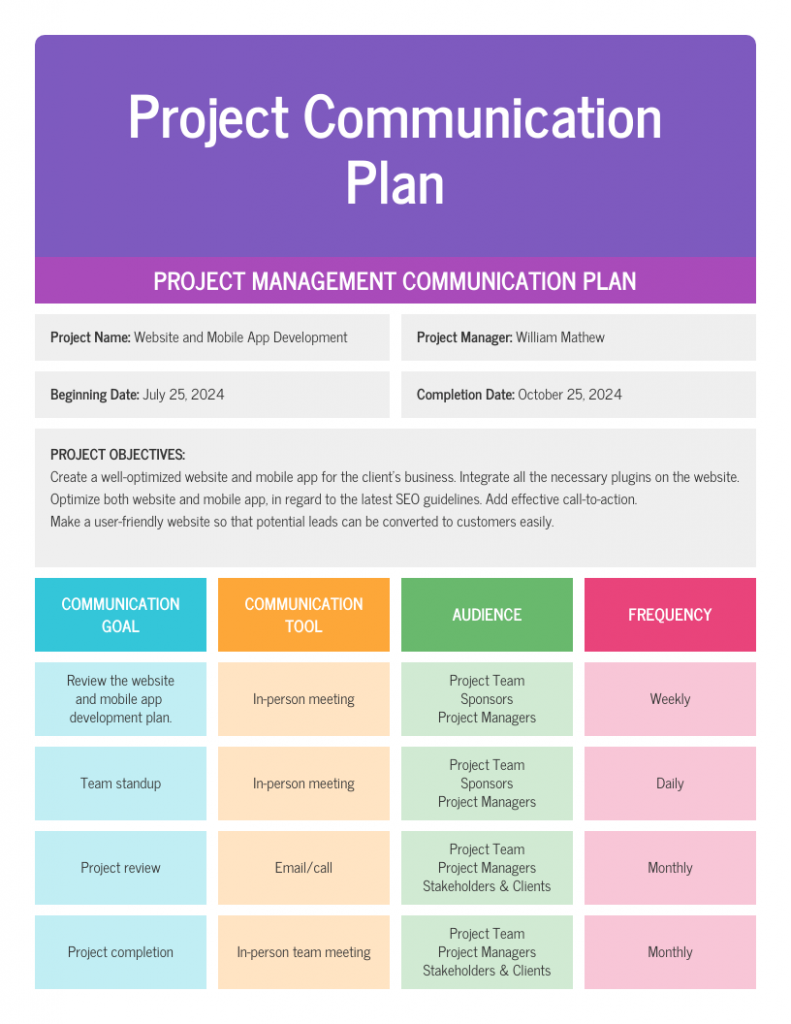
Another example of a process improvement plan, this nursing care plan is used in a healthcare setting only. It could be used to illustrate a new plan aimed at addressing gaps in communication and patient care. But you can use the process suggested in this plan and apply it to any industry.

This creative design process infographic would be an ideal way to share with a creative team a proposed new method of taking clients through the design process. Consider color-coding new or revised steps if creating a piece like this to share a revised company process.

Customize this action plan mind map once you’ve settled on a new process so that team members see steps involved in their tasks but also keep the main objectives in mind.
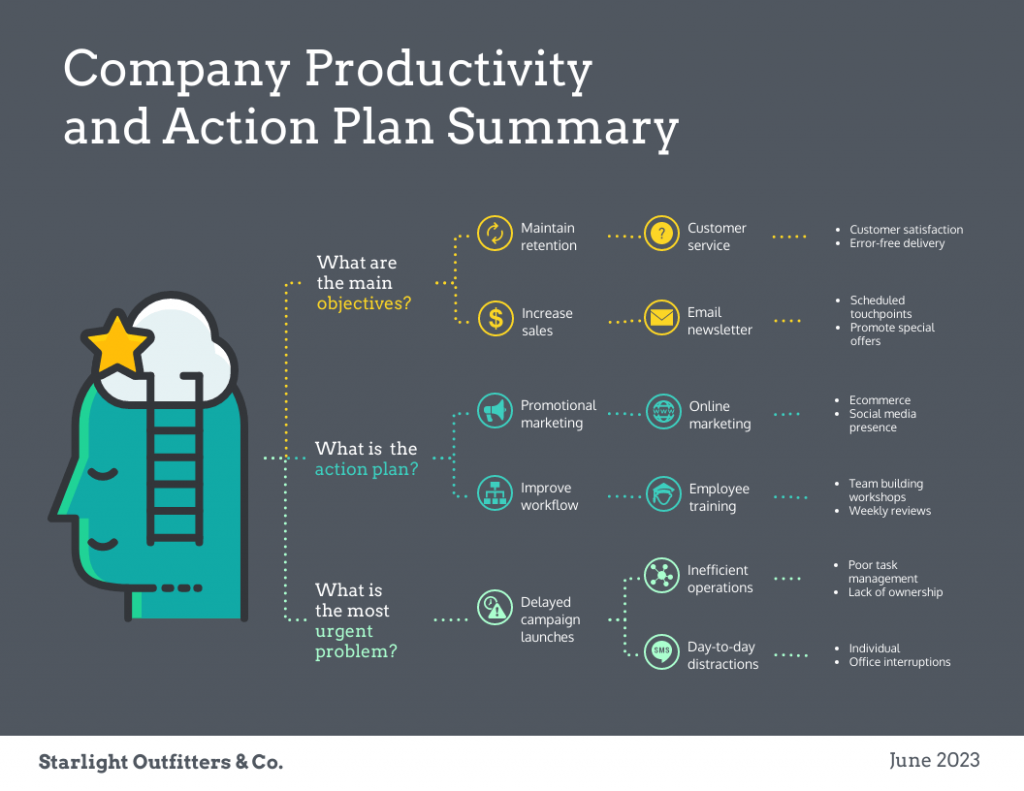
Process improvement plans are useful for organizations of all types and their output can include simple verbal instructions. But most companies benefit from creating charts, presentations and infographics to communicate a variety of aspects surrounding the plan.
Check out these process improvement plan templates that may help your organization.
Process improvement plan development examples
Developing a process improvement plan is complicated, but visual tools like infographics can make it easier for your team to grasp the steps involved.
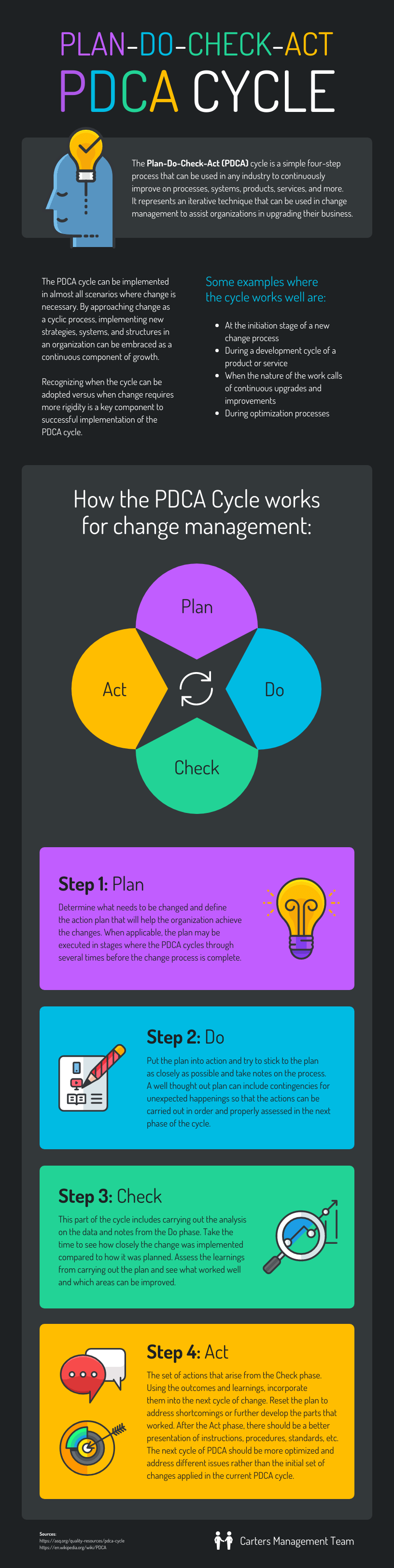
Help your management team and employees understand the steps involved in the plan-do-check-act (PDCA) cycle with this infographic. Customize it for your needs by outlining specific actions they need to take in the bottom section.
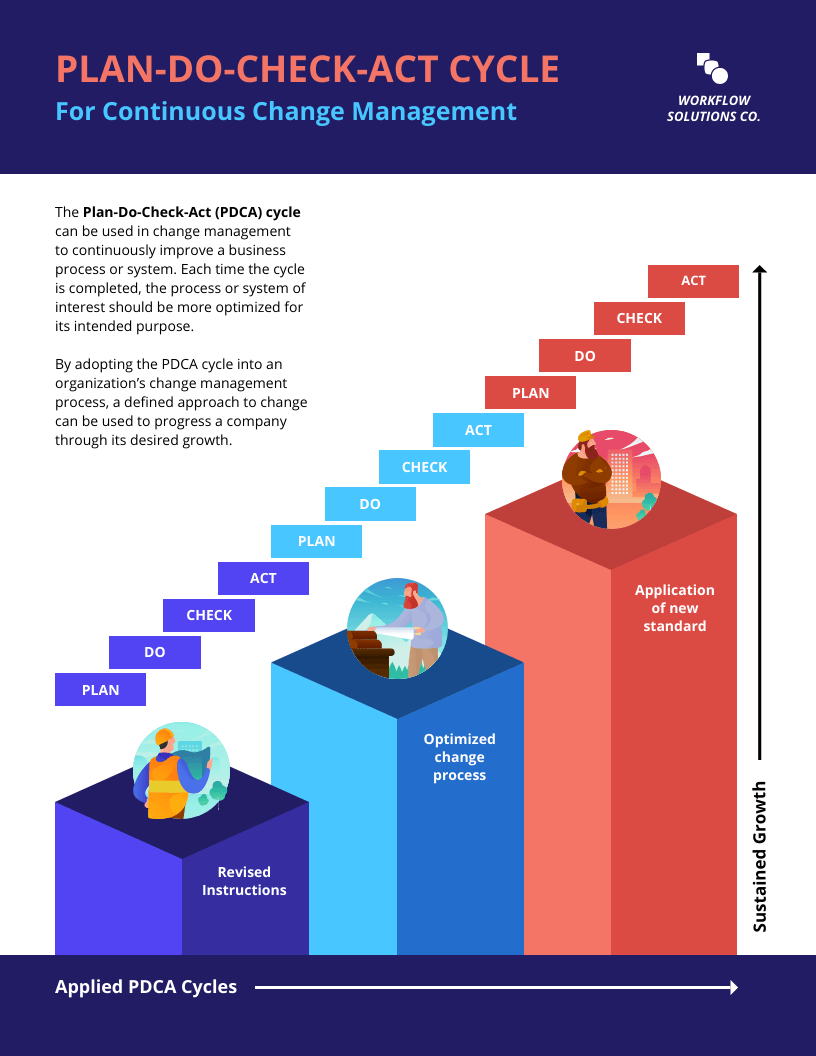
This PDCA cycle infographic is ideal for companies that are implementing improvement plans across their organization.
Revised process examples
Once you’ve settled on a new way of doing things, explaining the new process clearly to employees (and sometimes customers) is critical. Process and timeline infographics are helpful, as they allow people to visualize the new steps.
Here’s an example of a process improvement plan to revise customer support process, built based on the PDCA concept:
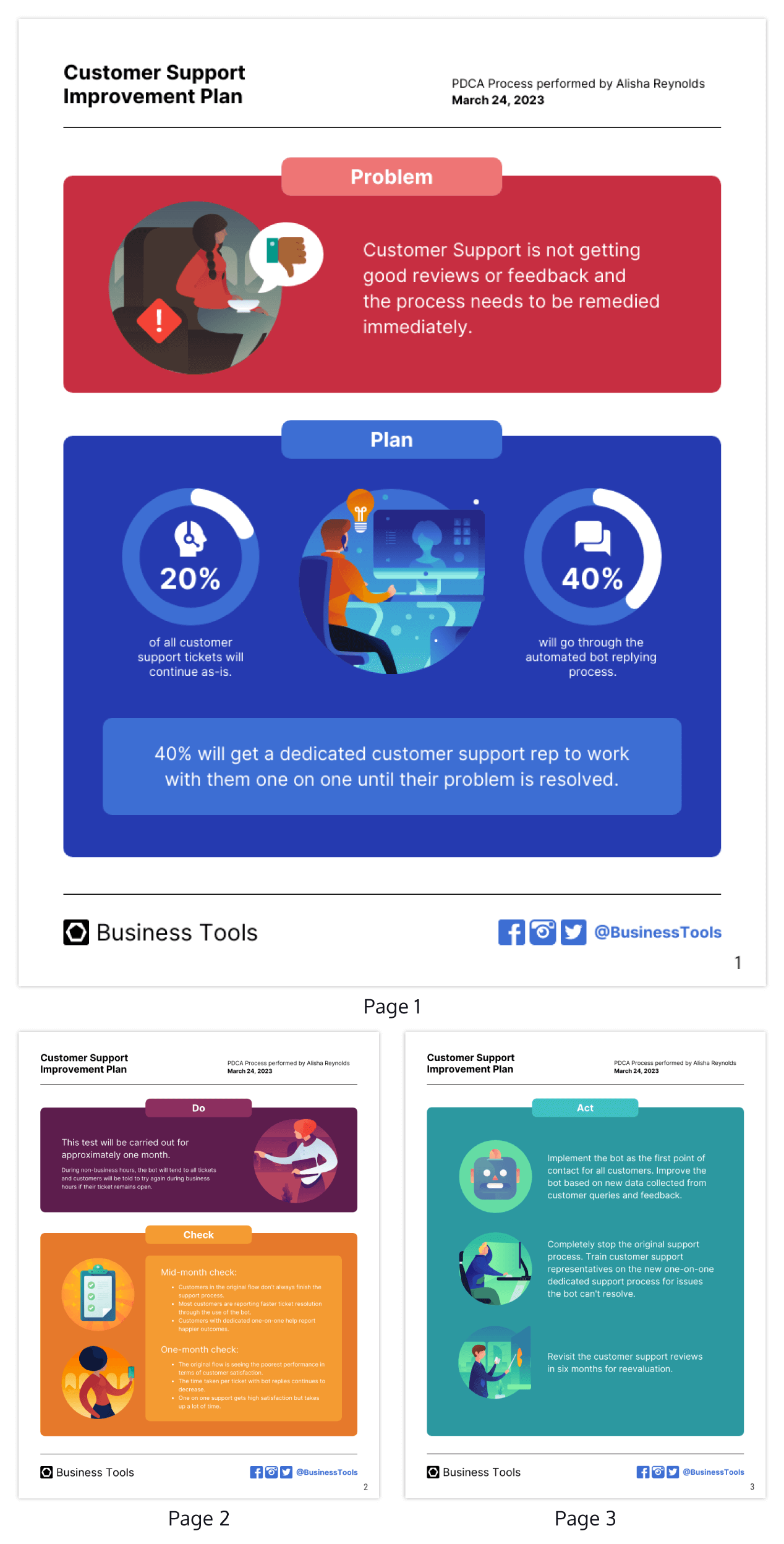
Customize this project management process infographic for the new process you and your teammates are creating. Quickly change out icons for ones that apply to your business and use My Brand Kit to ensure the design aligns with your corporate identity.
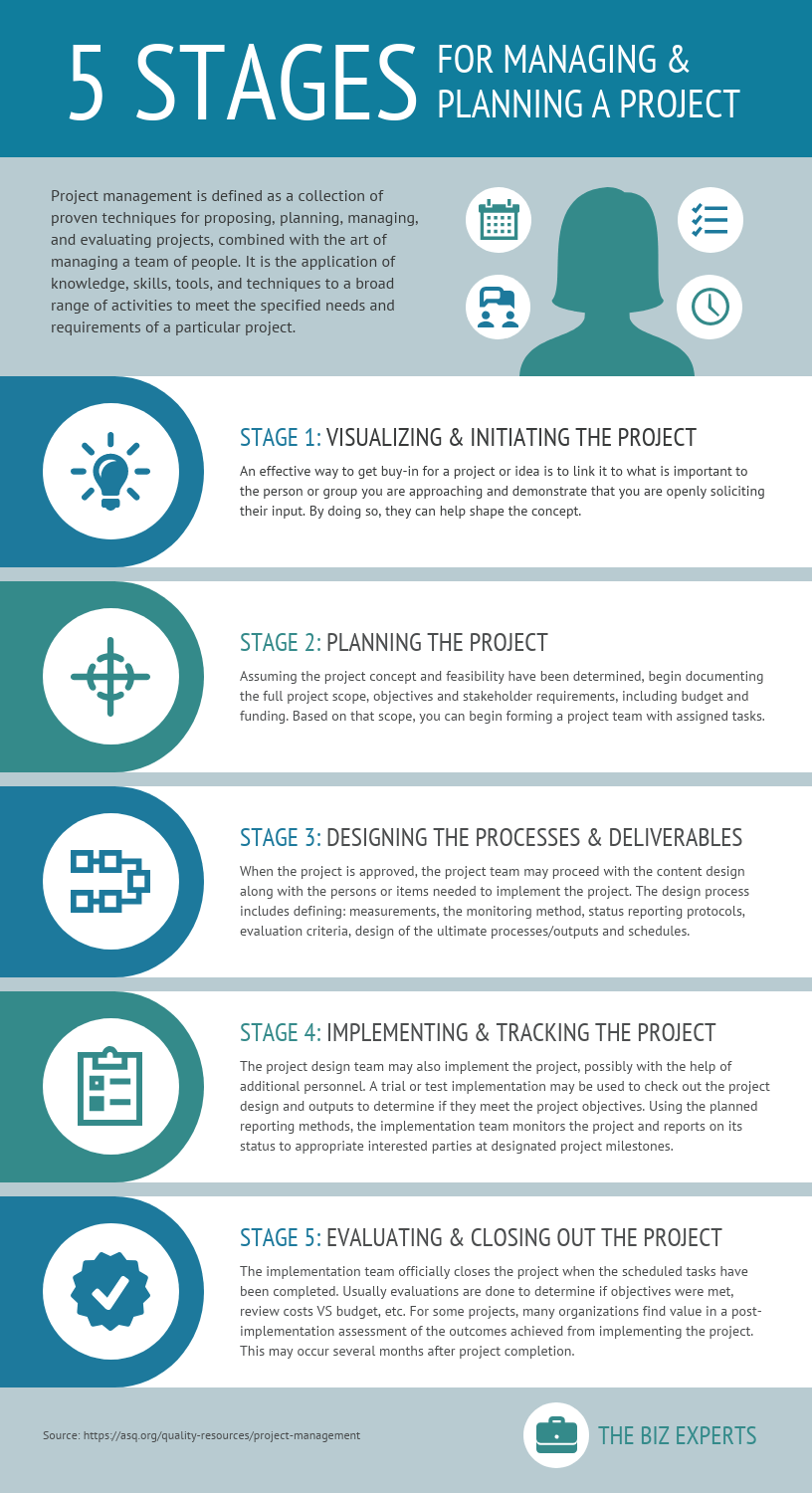
Use this colorful process infographic for a new process that has several steps. Lengthen or shorten as needed to cover all the steps in your revised process. Or use a template like this to create a process improvement action plan as you begin your work.
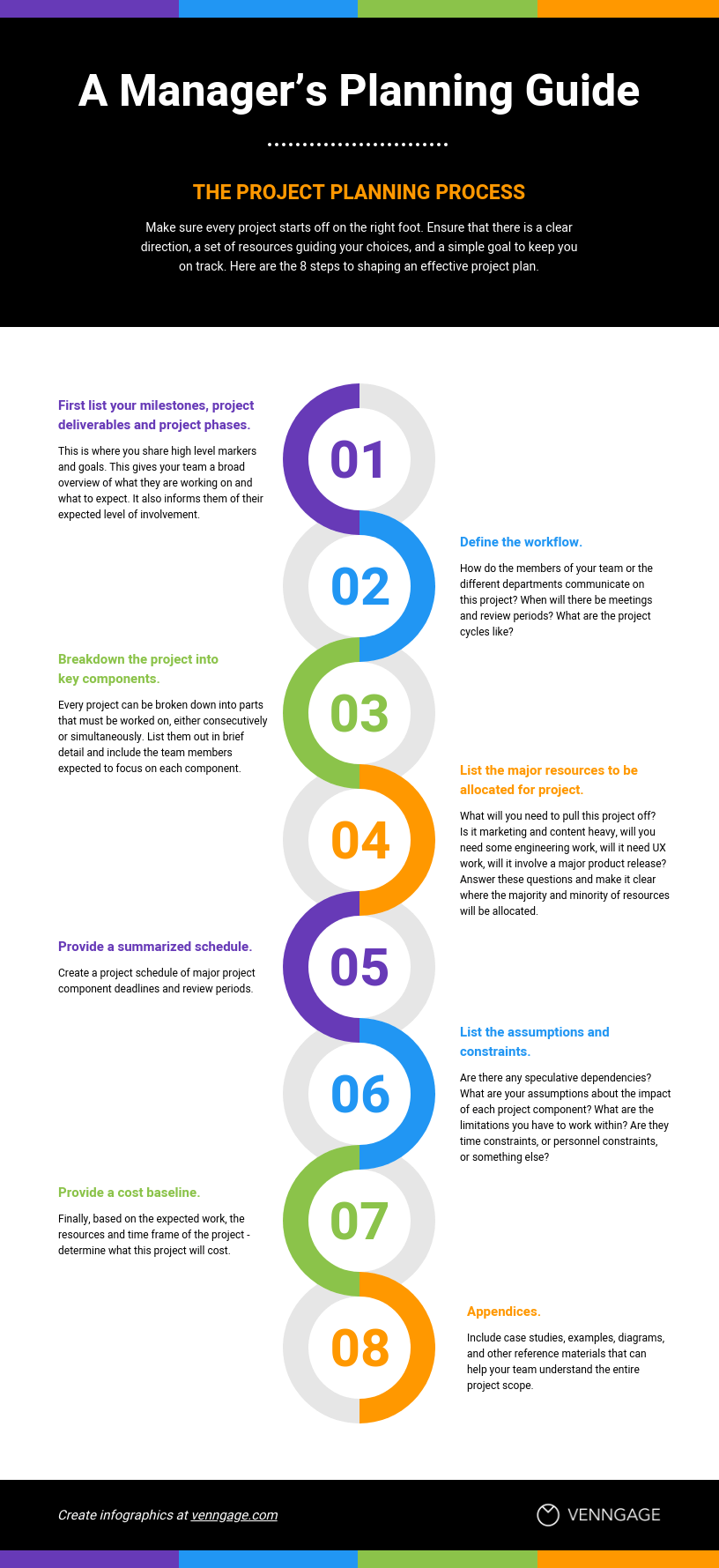
Revised policy examples
Process development plans can easily spill over into a variety of business areas and it’s often necessary to craft new policies and procedures on the way to your new process. Infographics and other tools can help you spread the word and document these new policies.
If your new process will require added documentation that needs to be signed by an employee or their supervisor, customize this procedure infographic that explores how to submit expense claims. Change the title, content and illustrations for your needs.
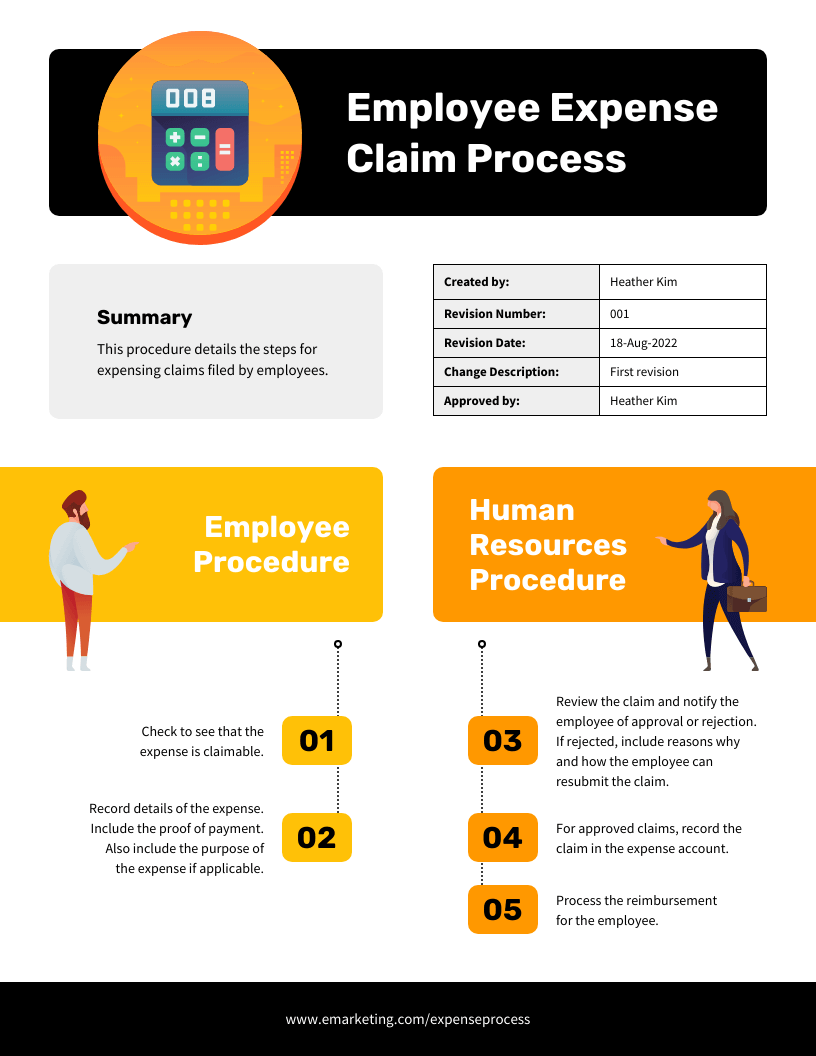
Perhaps your process improvement plan revealed that nobody in your organization is prepared for a disaster or emergency. The output of your process improvement team could be a business continuity plan like this one.
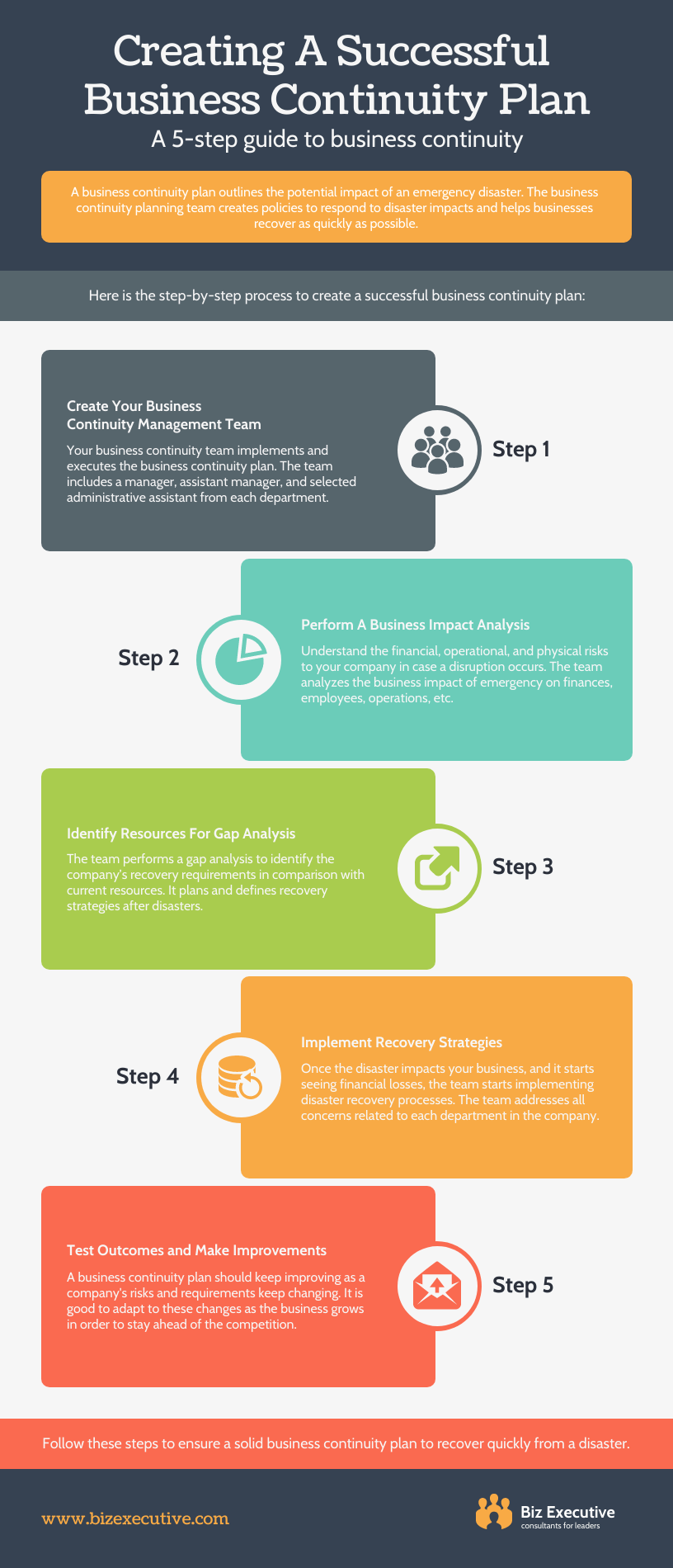
Employee development examples
The success of your new process will depend entirely on your team’s ability to execute it and many organizations find that a major reason why their current processes aren’t working is that team members lack certain skills. So, employee development is often involved in executing a revised plan.
Help team members visualize the skills they need to develop by working with them to create a mind map like this one.
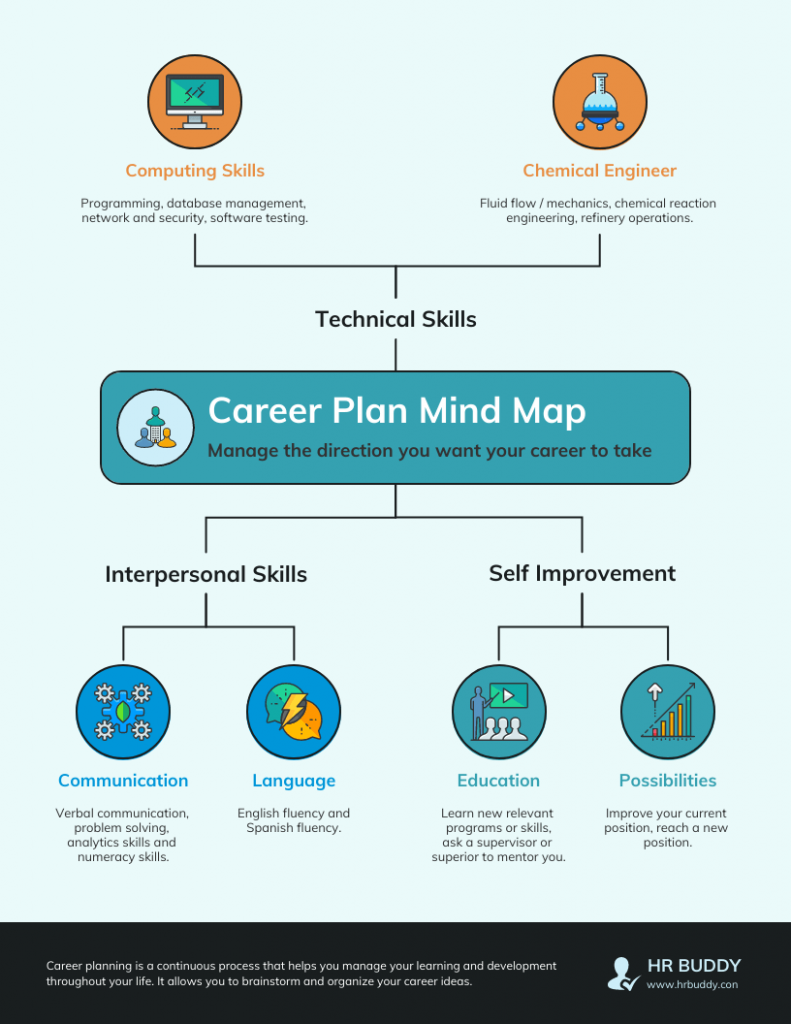
Customize this career planning infographic for team members as you work with them to help them build the necessary skills. While this example is about career planning in general, it’s easy to customize with specifics for your employees.
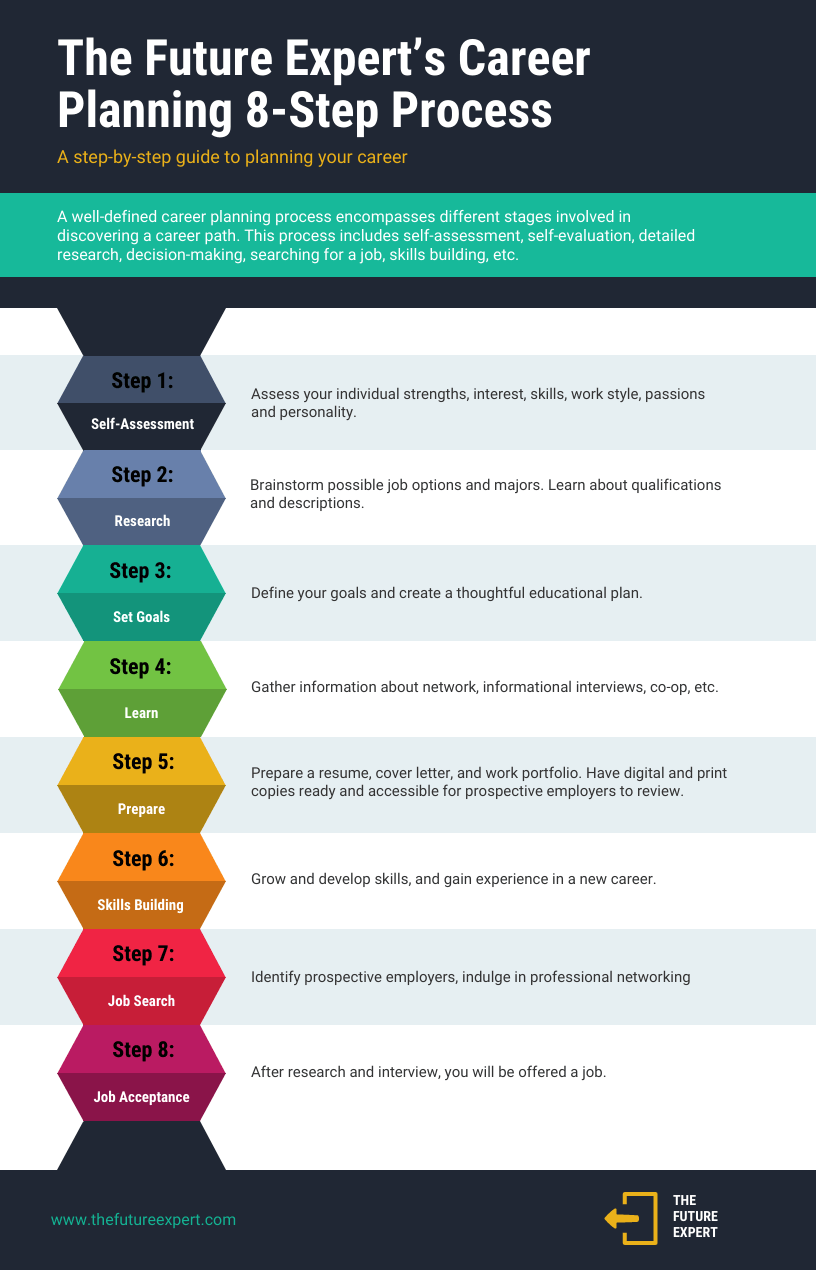
Change management examples
Humans by nature are resistant to change and your organization may find it challenging to implement a new process. These change management plans may help you communicate and motivate your team.
Follow the steps in this change management process infographic to break through your team’s stubborn adherence to old, inefficient processes.
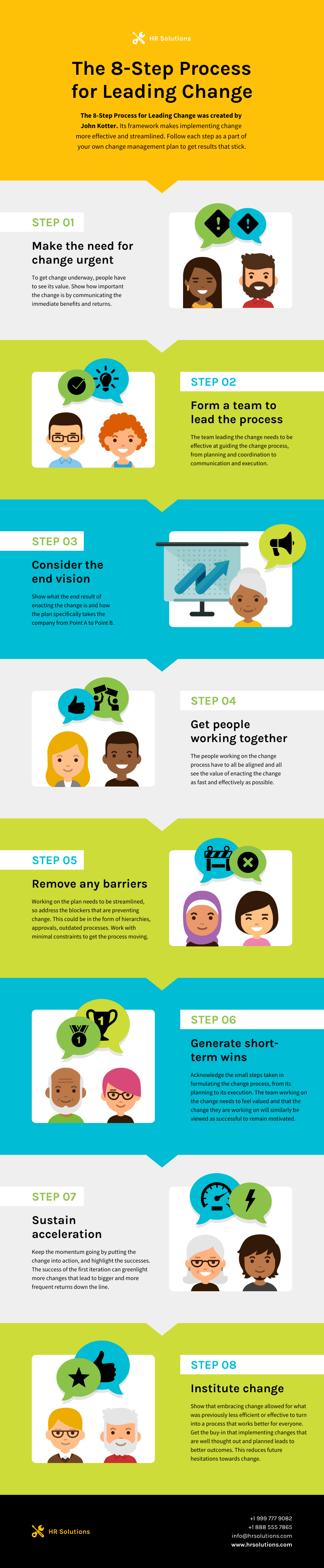
Update this planning process infographic to help get your team on the side of change. Employees who feel they are involved in steering the company in the right direction will feel a strong sense of ownership in the entire process improvement operation.
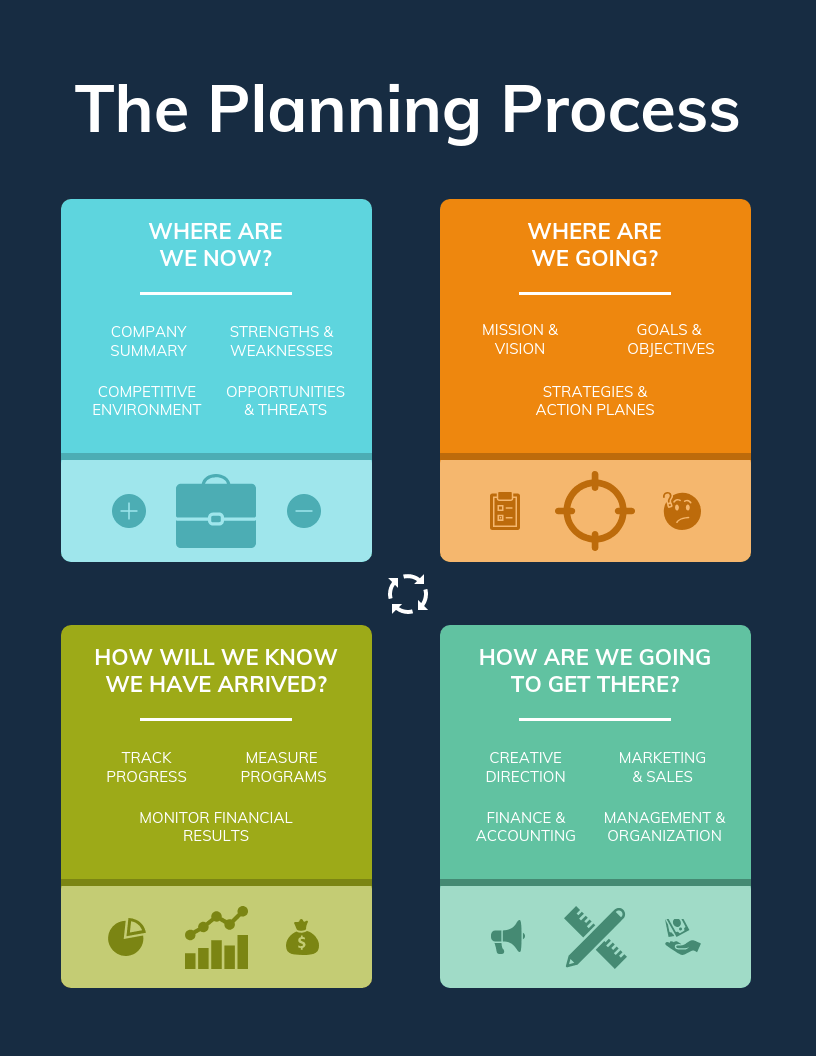
There are many benefits of diving into a process improvement plan in your organization and the most obvious and important is to improve your company’s overall efficiency. Doing so can make the business more profitable in the long run. But that’s not where the benefits end.
The biggest benefits of a process improvement plan include:
- Employee satisfaction : More productive workers make a company more money over time, but they also gain a sense of accomplishment and self-improvement.
- Customer satisfaction : Many process improvement plans target tasks that are customer- or client-facing and making sure your customers are satisfied is crucial for any organization.
- Agility : The business landscape is constantly changing, so putting a process improvement strategy into place will equip your organization to handle future disruption.
- Safety : Efficient processes are helpful to reducing workplace accidents and repetitive stress injuries and examining the physical activities employees are doing as part of their jobs can help make them safer overall.
- Modernization : Organizations that resist technology are likely not long for the world and process improvement plans are ideal for adapting new technologies to your company’s workflows.
- Innovation : In any company, there are things you do because that’s the way you’ve always done them. But breaking those processes down to see how they function is one of the best ways to spark a new idea and create innovation in your organization.
Do you have more questions about creating a process improvement plan for your organization? We’ve got answers.
How do you propose a process improvement plan?
Communication is a critical part of process improvement. If people don’t know or understand why change is needed, it’s unlikely they’ll embrace any new processes. Proposing a process improvement plan requires an individual or small group who will own the plan’s development from start to finish and can be evangelists for the plan across the organization.
What are the contents of a process improvement plan?
In general, process improvement plans must include a definition of the process, an explanation of its steps, an identification of the ways in which it falls short, a proposed new process and a mechanism for monitoring the revised steps.
How do you find areas of process improvement?
If you knew exactly why your organization wasn’t as successful, you’d fix it right away. But finding areas of process improvement means keeping your ear to the ground and observing the organization in an objective way. Common areas of process improvement include authority overlap, constantly missed deadlines, poor quality control, physical safety issues, fixing errors rather than preventing them, employee and customer dissatisfaction and excess spending.
Enhance productivity and eliminate frustration with process improvement plans
Identifying where your company is failing in the processes used across the organization is not an easy task, as it requires dispassionate examination of how you may be falling short. But visual communication tools like infographics, mind maps and process illustrations can help communicate issues to your team and get everyone moving in the right direction.
Interested in visualizing your process improvement plans and gaining buy-in from stakeholders? Start by registering for a FREE Venngage account and choose a suitable process improvement plan to customize. Our templates are professional-looking, fully customizable and really easy to edit, even if you don’t have design experience.
Discover popular designs
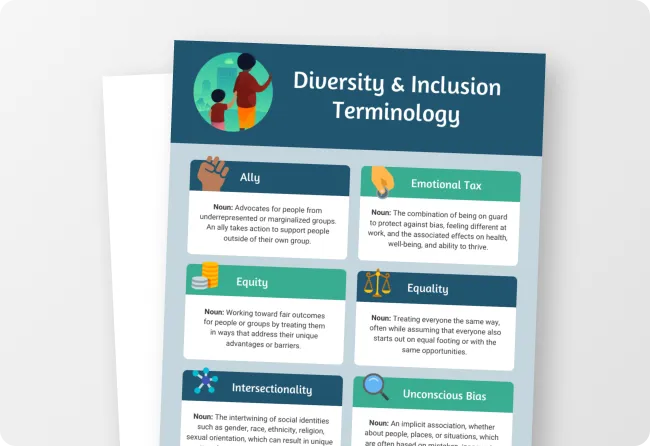
Infographic maker
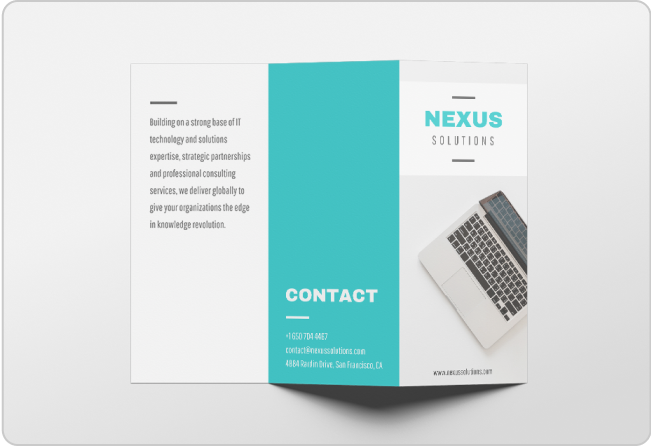
Brochure maker
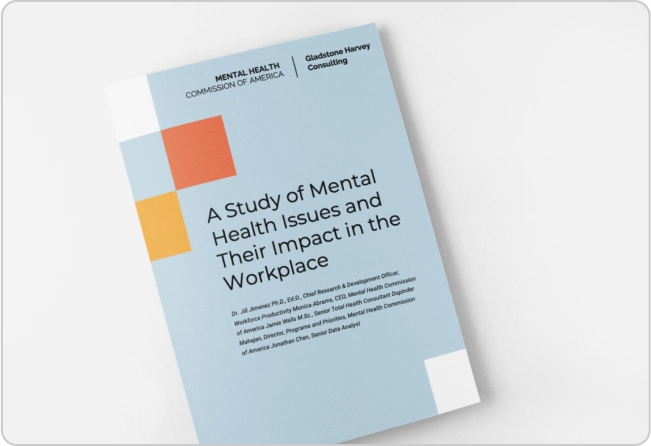
White paper online
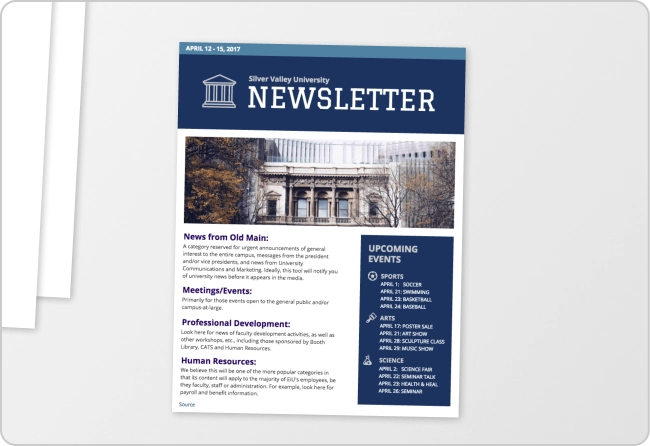
Newsletter creator
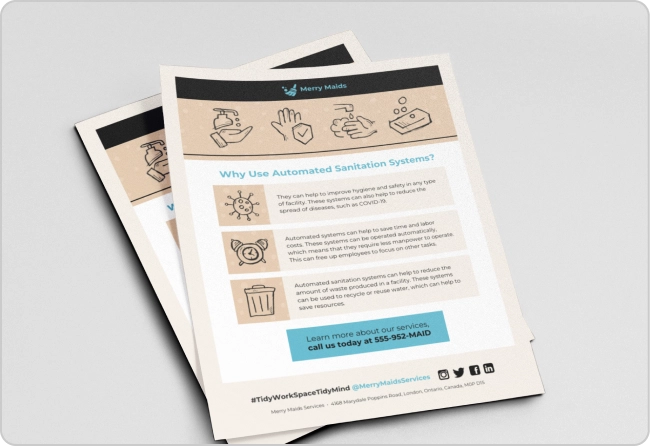
Flyer maker
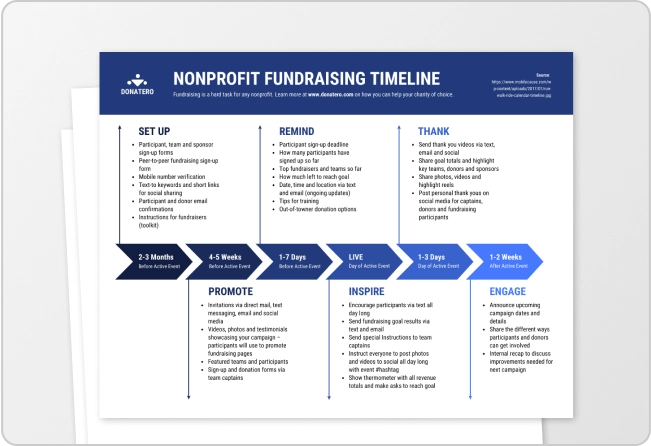
Timeline maker
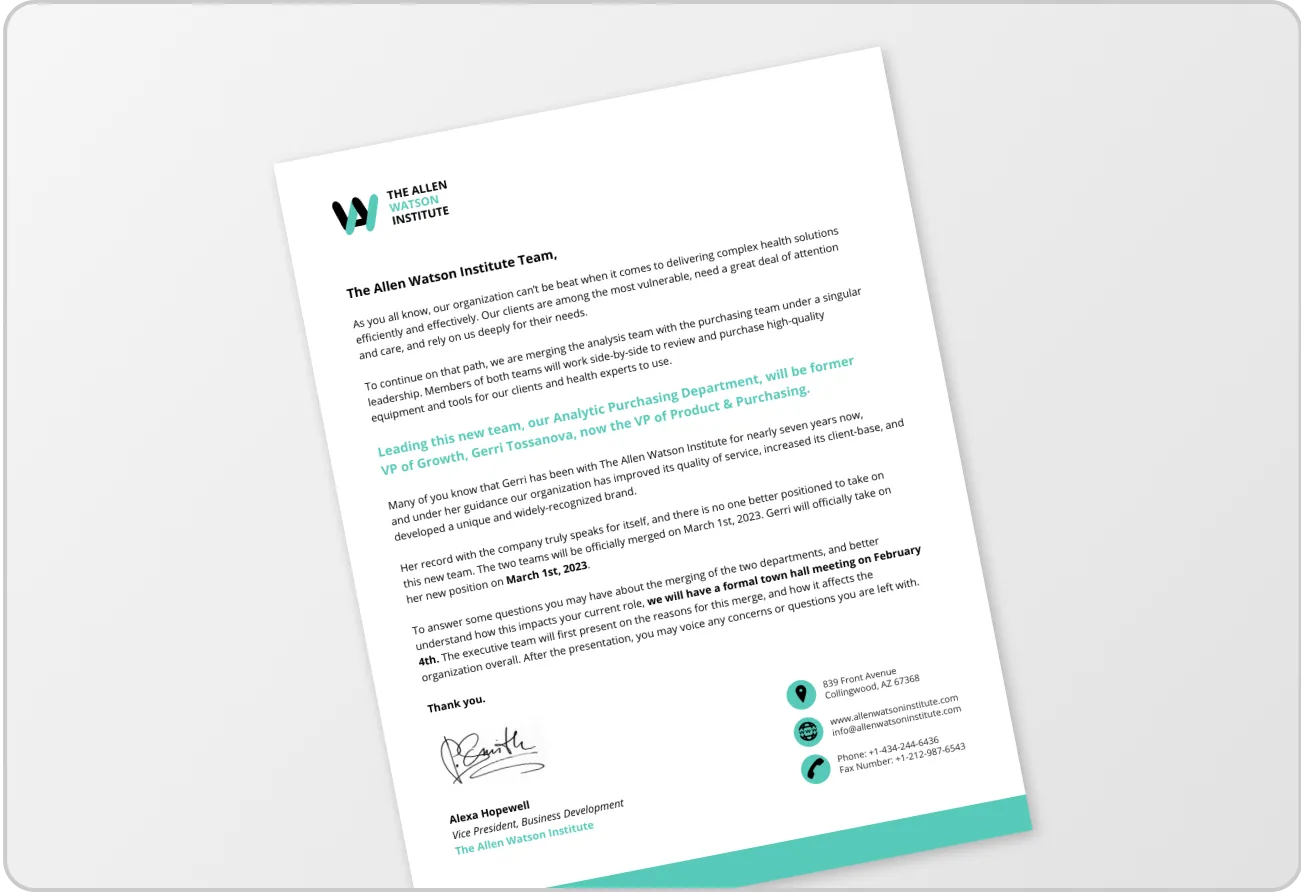
Letterhead maker
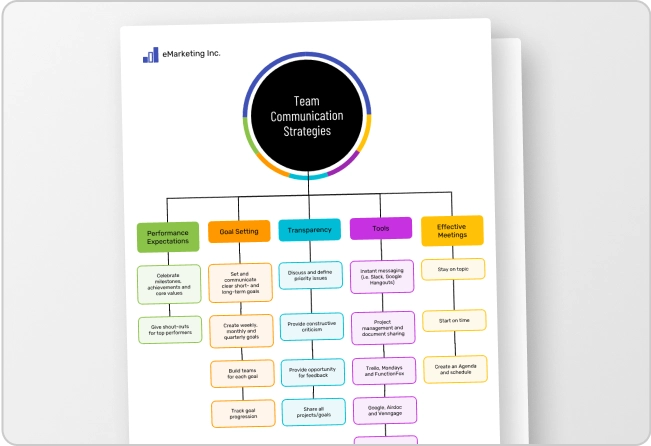
Mind map maker
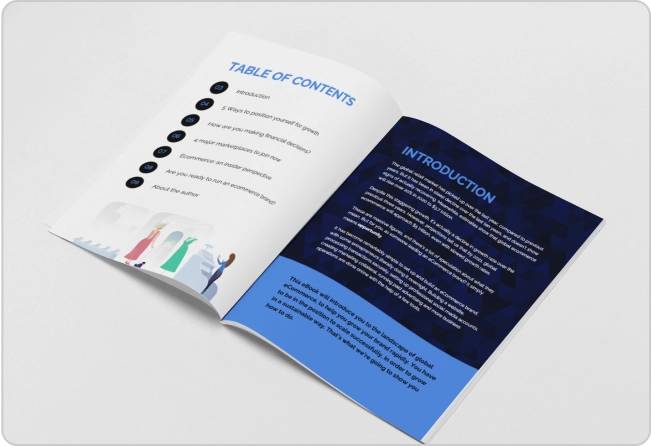
Ebook maker

Translational Research Support and Services for Scientists, Scholars, and Community Members
- Team Science
- Research Design & Analysis
- Informatics
- Clinical Studies & Trials
- Recruitment & Retention Support
- Community and Stakeholder Engagement
- Research Process Improvement
- T.5 Capacity in Medical Devices
- Biomedical and Health Data Sciences Collaborative (BHDSC)
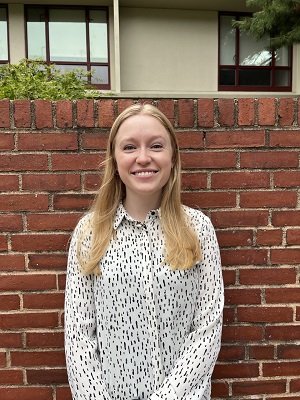
Meet our staff
Education, training, and mentorship for new and seasoned researchers.
- Clinical and Translational Science Graduate Program
- T32 Fellowship Programs
- K Scholar Programs
- Junior Faculty Research Career Development Forum
- Professional Education
- Mentor Training
- Blue Star Investigator Certificate Program
May 16, 1:00PM | Seminars & Workshops
May 20, 11:00am | seminars & workshops.
- Small Grants to Advance Translational Science (S-GATS)
- Open Opportunities
- Upcoming Opportunities
- Past Opportunities
- Career Development Awards
- Other Funding Sources
- Grant Writing Assistance
- Informatics Voucher Program
Since 2009, we’ve awarded 93 grants for innovative, interdisciplinary research through our Pilot Studies Program .
Tracking our progress towards acceleration, innovation and collaboration
- By The Numbers
- Success Stories
- Publications Referencing Tufts CTSI
- Beyond the Numbers
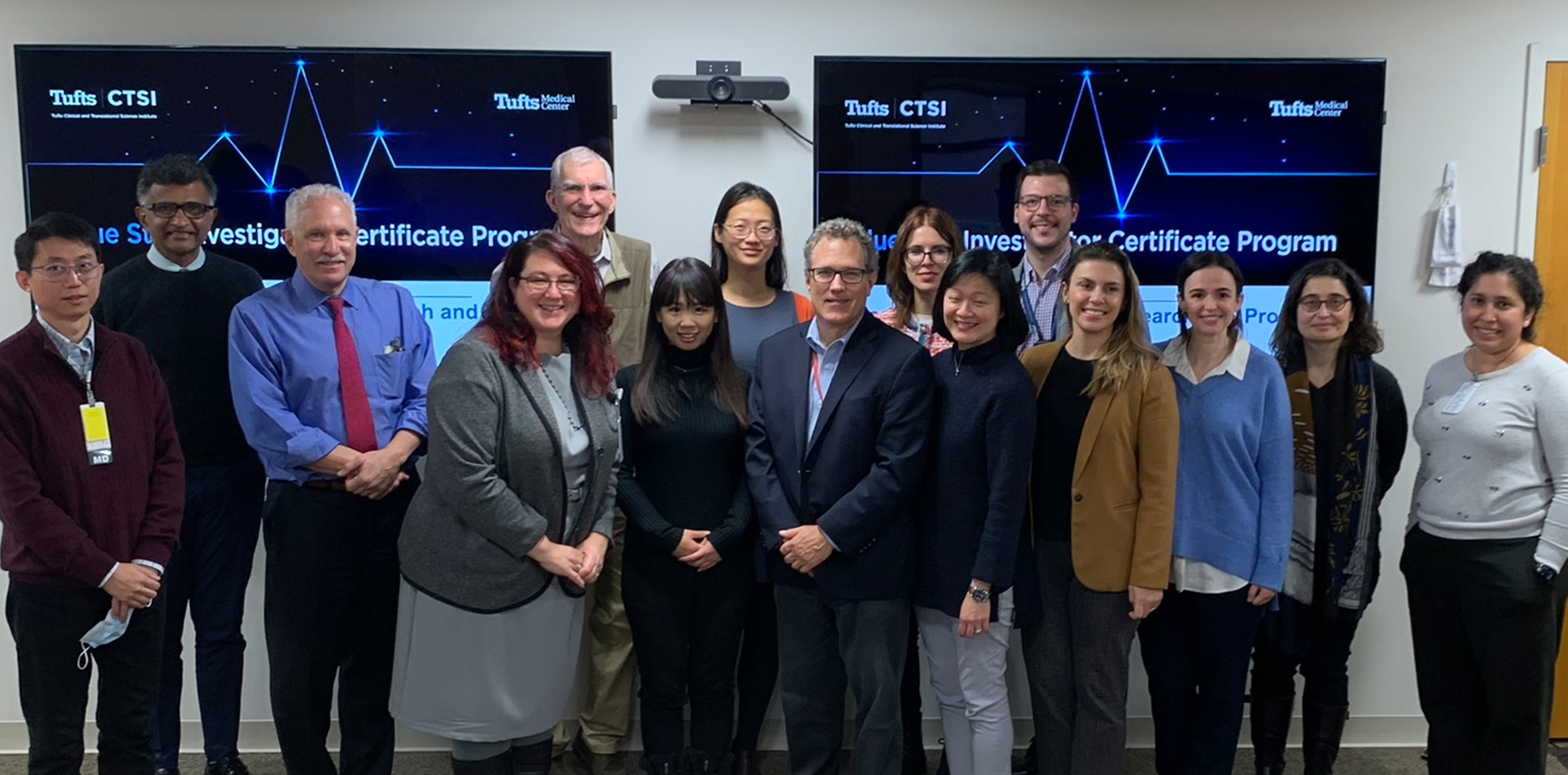
Featured Success Story
Building a culture and community of collaboration, what powers us, our partners.
- Commitment to Anti-Racism
- What is Translational Science?
- Broadly Engaged Team Science
- Annual Reports
- Academic Appointments
- How to Cite Tufts CTSI
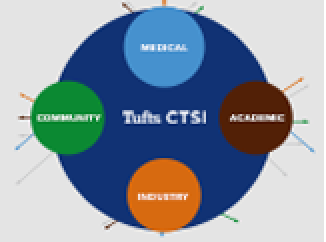
Research Process Improvement Case Studies
Rethinking recruitment: two case studies on how to improve clinical recruitment rates.
Staff from the Center for Research Process Improvement at Tufts Clinical and Translational Science Institute (Tufts CTSI) often use a continuous quality improvement framework to problem solve when they approach a researcher or project facing operational challenges. They recently partnered with Tufts CTSI’s Recruitment and Retention Support Unit and Multi-site Clinical Research Center to rethink the process for providing consultations to researchers. This new cross-functional team meets with study teams to understand the barriers and facilitators to recruitment and how they can select recruitment strategies using a data-informed approach.
The new process is highlighted in two case studies: The first case study highlights how they use quality improvement tools to prioritize recruitment strategies with study teams. The second case study outlines how using clinical trial metric dashboards can help teams to make data-informed decisions. Both case studies are examples of the importance of focusing on the science of science, as well as the science itself.
Further quality improvement tools and examples are highlighted in the research process improvement toolkit .
Case Study 1 Case Study 2
Case Study 1: Optimize Clinical Trial Recruitment Using Quality Improvement Tools
One of the most challenging aspects of conducting clinical research is recruiting and retaining participants. Even a well-designed study won’t succeed if it lacks a robust recruitment and retention plan. Tufts Clinical and Translational Science Institute’s (Tufts CTSI) Center for Research Process Improvement, Recruitment and Retention Support Unit, and Multi-site Clinical Research Center have been partnering with research study teams to explore how using quality improvement (QI) tools can help study teams to think strategically about their recruitment plans and enhance their overall recruitment approach.
Recently, Tufts CTSI worked with two study teams who were actively recruiting specific populations for two clinical trials. With both study teams, we used key driver diagrams and prioritization matrix tools to understand contributors to successful participant recruitment and to prioritize actions to improve recruitment rates. Prior to completing the key driver diagram, we needed to understand the barriers and facilitators to recruitment with each team. We worked with them to complete a list of all barriers and facilitators and catalogued each on a comprehensive spreadsheet.
Key Driver Diagrams
A key driver diagram is used to visualize the drivers, or conditions, that could affect achieving a project’s goal such as recruiting the needed number of participants. It shows the relationships between different drivers and how they influence reaching the goal. The diagram also lists actions or operational changes that may impact the drivers. The change ideas in this case are different recruitment strategies the study team could use to improve their accrual rates.
We met with both study teams to understand their recruitment approaches, desired study populations, and the overall recruitment environment, using the information to draft key driver diagrams for each study. The barriers and facilitators we collected from the study teams were also used to inform the key driver diagram. Although each driver diagram was specific to its respective project, both diagrams included similar conditions and actions that could lead to improved participant recruitment. See Figure 1 for a generic key driver diagram that can be adapted for other clinical studies planning to recruit participants.
Figure 1. Recruitment Key Driver Diagram
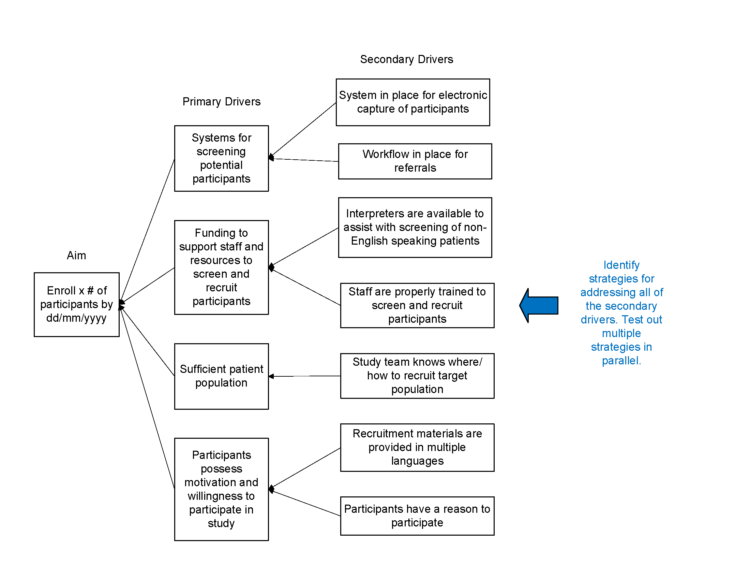
Open larger image view .
Description of Recruitment Key Driver Diagram.
Prioritization Matrix
A prioritization matrix is a tool that helps compare actions in order to decide which actions, or change strategies, have the greatest priority, the most impact, or are the easiest to accomplish. Using a prioritization matrix can help a group of stakeholders achieve consensus in strategy prioritization and avoid or resolve disagreements.
Using the results of the key driver diagram, the study team reviewed the list of possible actions or changes to the existing recruitment process. Next, we helped the team sort the change strategies in a prioritization matrix based on the potential impact of the strategy to increase recruitment and the level and effort required to implement the strategy. After sorting all the strategies into the matrix, the team began implementing those strategies that had high impact but required low effort. See Figure 2 for a blank prioritization matrix you can use for your own research study.
Figure 2. Prioritization Matrix
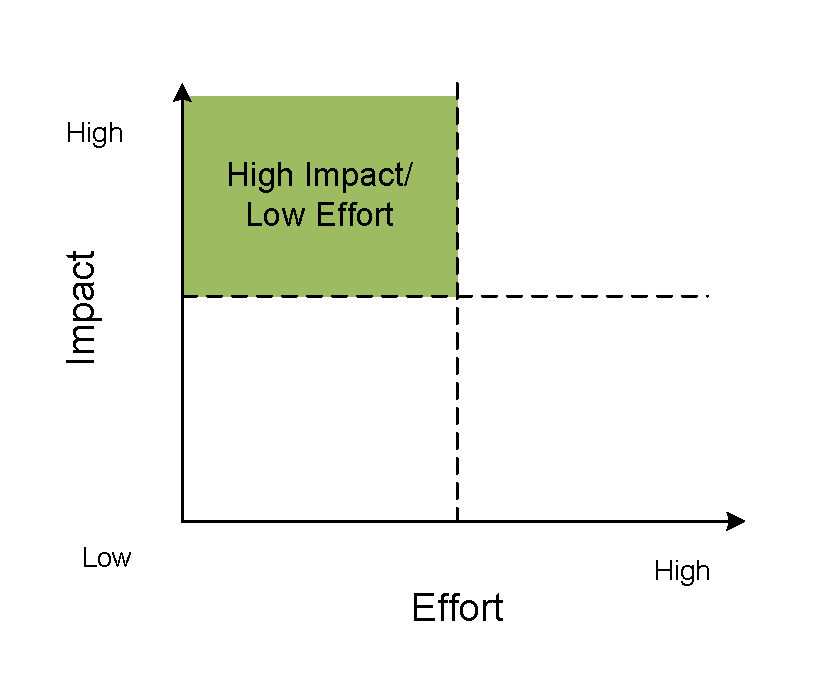
Open larger image view.
Description of Prioritization Matrix.
Key Takeaways
The driver diagram and prioritization matrix are tools to help study teams organize their thinking and planning around improving participant recruitment. Deploying a key driver diagram helps teams systematically identify effective changes and develop a stronger recruitment plan. The prioritization matrix helps teams avoid feeling overwhelmed by the numerous strategies they could use to improve recruitment and ensures the team is focused on the strategies that are both impactful and feasible to implement.
If you have questions on how to use one of these tools and apply them to your research project, please contact Senior Project Manager Alyssa Cabrera, MPH .
Case Study 2: Using Clinical Trial Metric Dashboard Data to Improve Study Operations
Investigators are often keenly aware that industry sponsors collect clinical trial metrics on the research studies and sites they activate for trial participation, but sponsors rarely share these data, trends, and benchmarks with investigators. As a result, investigators may find it helpful to collect their own “in house” metrics. Metric dashboards, which can easily be developed in Excel, provide a study team with an opportunity to reflect on these data and brainstorm solutions for improving key trial performance metrics. Investigators who have access to a clinical trial management system (CTMS) can work with their data teams to see if key metrics can be easily exported from the CTMS or from a custom report.
Recently, a team from Tufts Clinical and Translational Science Institute’s Center for Research Process Improvement, Recruitment and Retention Support Unit, and Multi-site Clinical Research Center partnered with two study teams on collecting key study metrics. Our staff met with each of the teams to help decide which performance measures, and what level of performance, would be most useful for the team’s management of the study. One team prioritized tracking the study visit completion rate; the other team prioritized tracking the screen fail rate. Each team was able to make informed study management decisions based upon the metric results and implement improvements in key operational areas. For example, one team tracked the financial costs of supplying recruitment materials to external research sites. After seeing that few participants were recruited from these sites, and that the recruitment costs were high, the team decided that the external site recruitment strategy was not worth the investment.
If you are new to using clinical trial metrics to manage your research studies, check out the newly-developed resource, Collecting and Using Clinical Trial Metrics to Improve Trial Performance . You can download operational guidelines for key metrics, access a dashboard template, and learn about three key metrics and their importance to study success. Example pages are displayed below.
Figure 1. Example Pages
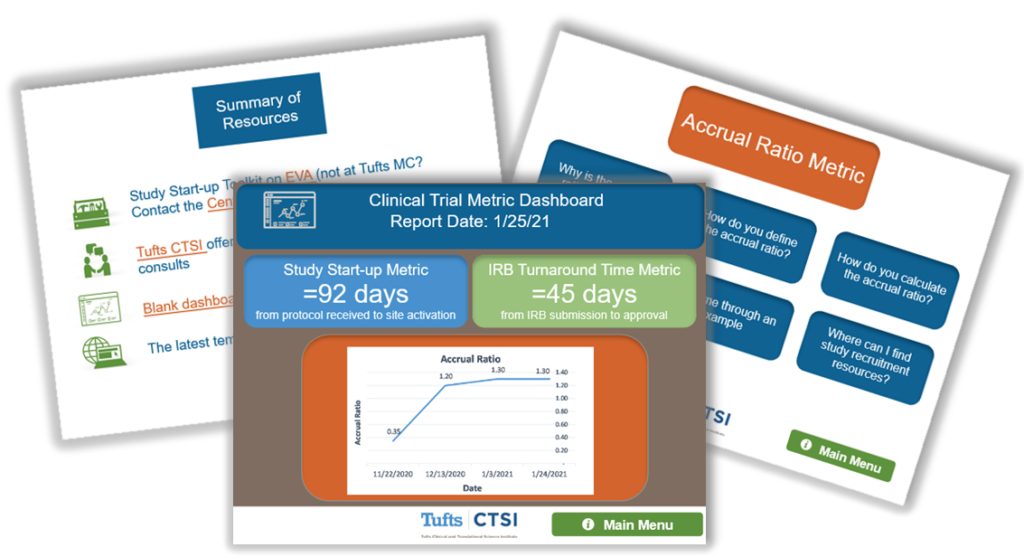
Description of image.
If you have any questions about how you might use clinical trial metrics in your research studies, or how to use these resources, please contact Senior Project Manager Alyssa Cabrera, MPH .

- SUGGESTED TOPICS
- The Magazine
- Newsletters
- Managing Yourself
- Managing Teams
- Work-life Balance
- The Big Idea
- Data & Visuals
- Reading Lists
- Case Selections
- HBR Learning
- Topic Feeds
- Account Settings
- Email Preferences
Creating a Culture of Continuous Improvement
- Aravind Chandrasekaran
- John S. Toussaint

How one Wisconsin health system did it.
A number of health systems have scored impressive gains in improving outcomes and patient satisfaction and lower costs by applying the Toyota Production System (TPS) to redesign “lean” clinical and administrative processes, eliminating waste and boosting quality. But in all too many cases, when the leader who championed TPS left his or her organization, these efforts began slipping. The authors know this firsthand: This happened at Wisconsin-based ThedaCare. When one of the authors (John Toussaint) left in 2008, its performance in terms of quality (as measured by the Centers for Medicare & Medicaid Services’s metrics for Next Generation accountable care organizations) fell from best in the nation to middle of the pack. Through the authors’ research in health care and other industries, they’ve identified a set of practices that can stop this collapse and sustain a culture of continuous improvement after the departure of a leader who was passionate about TPS. They include the following: incorporating TPS in succession planning for the CEO and board members, instilling lean behaviors in managers at all levels, creating your own success stories, and establishing a TPS operating system.
A number of health systems have scored impressive gains in improving outcomes and patient satisfaction and lower costs by applying the Toyota Production System (TPS) to redesign “lean” clinical and administrative processes, eliminating waste and boosting quality. But in all too many cases, when the leader who championed TPS left his or her organization, these efforts began slipping. We know this firsthand: This happened at Wisconsin-based ThedaCare . When one of us (John Toussaint) left in 2008, its performance in terms of quality (as measured by the Centers for Medicare & Medicaid Services’s metrics for Next Generation accountable care organizations) fell from best in the nation to middle of the pack.

- Aravind Chandrasekaran is an associate professor of operations and academic director of Master of Business Operational Excellence (MBOE) at the Ohio State University’s Fisher College of Business.
- John S. Toussaint M.D., is the founder and executive chairman of Catalysis, a nonprofit educational institute, and an adjunct professor at Ohio State University’s Fisher College of Business. He is the former CEO of a health care system and coaches teams on Toyota Production System principles.
Partner Center
- Change Management
- Strategic Planning
- GE Work-Out
- Business Process Improvement
- Team Effectiveness
- Executive Coaching
- Strategy Development/Implementation
- Process Re-engineering
- Supply-Chain Management/Supplier Development
- Cost-Reduction
- Product-Yield Increase
- Cycle-Time Reduction/Productivity
- Non-Value-Added Work Elimination
- Organizational Integration
- Global Standardization
- Client List
- Testimonials
- Case Studies
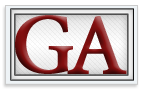
Gagnon Associates
Management & Organizational Consulting

Case Study: Business Process Improvement
This Case Study illustrates how Gagnon Associates used its Business Process Improvement capability to optimize a client’s new-product development process:
The Company
A formerly high-flying, enviably profitable surgical products division of a major health care company. Makers of state-of-the-art, reusable and disposable devices for the rapidly-growing, least-invasive surgery market.
The Problem
Declining profits due to increased costs associated with a lack of discipline and lack of customer focus in screening new product ideas, initiating new-product development projects and managing the new-product life cycle in the post-introduction phase.
The Approach
Management enlists Gagnon Associates consulting support to lead the effort to: a) assess new-product screening, new-product development, and post-product introduction processes and related issues, and b) reengineer these interrelated processes for improved efficiency/effectiveness.
Four “boundaryless,” client teams are created, including representatives from finance, R&D, marketing, sales, purchasing and other functions. Three teams focus on one each of three previously mentioned processes. The fourth team analyzes a recent unsatisfactory surgical pump introduction for additional insights into deficiencies in the new-product introduction process.
Over three days of an intense, highly-interactive, four-day intervention, teams work both independently and in close coordination, as needed, to: a) define existing process deficiencies, b) reengineer processes, and c) address key process interrelationships. Throughout, Gagnon Associates catalyzes and facilitates the process by providing online, work-group leadership as well as “just-in-time” training and coaching on underlying process reengineering tools and techniques.
The Results
Teams completely reengineer new-product screening and new-product development processes and develop a more formal process for managing the post-introduction phases of the product life-cycle. On the fourth day of the engagement, the division’s management team reviews and approves the newly reengineered processes in an interactive forum, attended by all team members and moderated by Gagnon Associates consulting staff .
Management is so pleased with the newly redesigned processes that it commits to testing approximately 120 new product development projects currently in the pipeline against the new model and estimates that, as a result, some 40 to 50 resource-draining projects of questionable value to the customer will be eliminated.
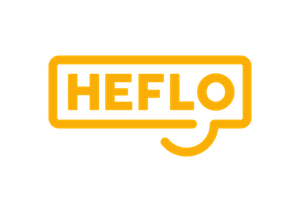
Business Process Reengineering Examples – Understand and Learn from them
Do you know what business process reengineering is?
I t’s the radical reconsideration of a business process to achieve dramatic improvement in cost, quality, service and speed performance. Business process reengineering is the analysis and redesign of company processes. Check out some business process reengineering examples below.
You should observe some points when implementing business process reengineering, such as:
- A change of focus from management to the customer
- Managers must give power to their team’s
- Focus on results
- It’s not positive to score points, but to lead and teach
- Simple and optimized processes are better than complicated and intricate processes
- If a process continually doesn’t work, it’s time to come up with a new one, looking to the future.
- Always identify goals and purposes
- Keep the company mission in mind
Only by following these recommendations will business process reengineering work as expected.
Now that you understand what Business Process Reengineering is, let’s look at some examples and case studies.
Also see: What is process reengineering methodology?
Business process reengineering examples: BPR that works
There’s nothing better than tried and true BPR examples to really understand the subject. With this in mind, we’ve separated some business process reengineering examples that have been successful.
Business process reengineering examples : Fast food company
An example of business process reengineering that we can cite is that of a fast food company.
Completely redesigning the delivery of products can give you unexpected results. In this type of restaurant, the process goes like all others, the customer orders, the order goes to the kitchen, which prepares the meal and then delivers to the consumer.
Business process analysts realized that it would be more advantageous if the meal portions were previously prepared in a separate center, and delivered to the restaurants daily.
When the customer orders, staff place everything together and deliver it. This is a complete change in the process, resulting in greater control, fewer accidents, greater employee satisfaction, and increased ability to focus on customer needs, all without losing quality.
CURIOSITY : The next time you go to a hamburger fastfood restaurant, note that your cup is always placed in the center of the tray, reducing the risk of it falling over.
To relax before you check out the next Business Process Reengineering case study, watch this fun video:
Business process reengineering examples : company selling commemorative cards
In a company that offers products such as Christmas, anniversary, commemorative cards, etc., renewing the stock and changing the design of the cards is constantly fundamental.
On average, it takes three months for new items to reach the shelves. Across market research , it’s possible to realize that there would ideally be new products every month.
At first glance, it’s easy to say that the delay was at the production stage. When analyzing and mapping the process, it’s verified that the creation stage was the most time consuming.
Oftentimes the creative team receives the concept and several employees begin to perform the same task (duplicate actions), or an idea takes days to get off the paper. With this information, we can redesign the process completely, defining a cross-functional team from concept and creation, with incredible results in speed, costs and effectiveness.
This is an example of business process reengineering that shows the importance of studying the process and then modifying it.
Also see: Process mapping examples.
Process reengineering is about finding new solutions to old processes, check out this video because, often, we’re unable to see obvious process change solutions:
Business process reengineering examples : Creation, application and proofreading
One of the most distressing tasks for teachers and students, whether in universities or schools, is test creation, their use by students and subsequent marking.
One of the great problems teachers face is the student’s writing, which is often unintelligible, brought on by the students’ weariness to write by hand.
The solution? The application of evidence through electronic forms in notebooks where students can type, as well as having access to other tools that assist in their answers, such as spreadsheets.
To prevent students from querying improperly, these devices don’t have a wi-fi or internet enabled connection. They’re simple (and low-cost) devices in which the students upload the tests via pen-drive and then the teacher collects them. The teacher then connects the data to a system that helps them correct the tests (without needing to interpret the writing), share comments with students, access performance statistics, and access a database of questions that helps to develop the tests.
See this infographic that summarizes the steps of Business Process Reengineering in a schematic way:
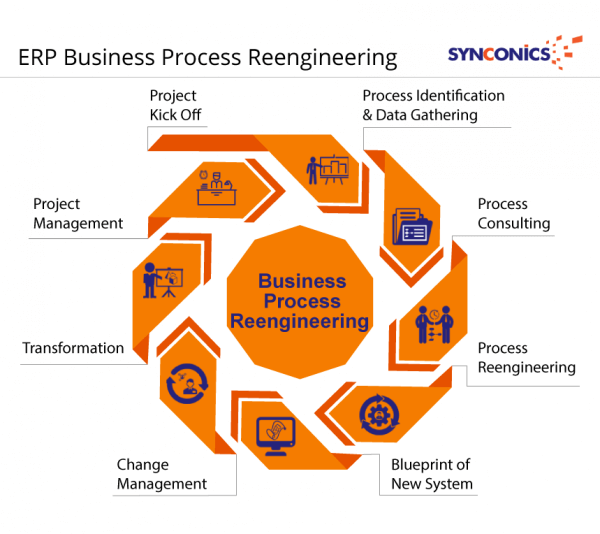
Business process reengineering examples : Creative Quartets
The process of creation in advertising agencies is divided, in brief, into 6 stages:
- The customer service team interviews the customer and passes the information to the planning team
- The planning team makes the necessary studies. Then develops strategy and delivers the request for the creation of pieces for the creative pair (editor and designer)
- After developing the requested pieces the creative pair alongside the planning and customer service teams carry out a presentation meeting. Eventual adjustments are then made to the campaign
- Customer service presents the campaign to the customer, often in conjunction with the creative pairing and planning team. Then receives customer feedback
- The process resumes, if the client requests adjustments or disapproves of the campaign
You should’ve noticed that these processes have four agents: the creative pair, a customer service professional, and a planning agent.
Conflicts between creation, planning and customer service are very common. Customer service complain of deadlines and not understanding the scope as much as the others. Creatives and planning, defend their points of view and claim that they’re doing the correct work and that customer service must convince clients of this.
To end this conflict in teamwork , an agency has developed creative quartets in which the 4 professionals work in their area of expertise, but divide a table and everyone are jointly abreast of all steps from the process, from the initial briefing to receiving customer feedback.
With this closeness, it became easier for each one to understand the difficulties of the others, generating a synergy that made this process much more productive and agile, becoming an example of successful process reengineering.
Know more: Definition of process management
Check out this schematic chart with important information on Business Process Reengineering:
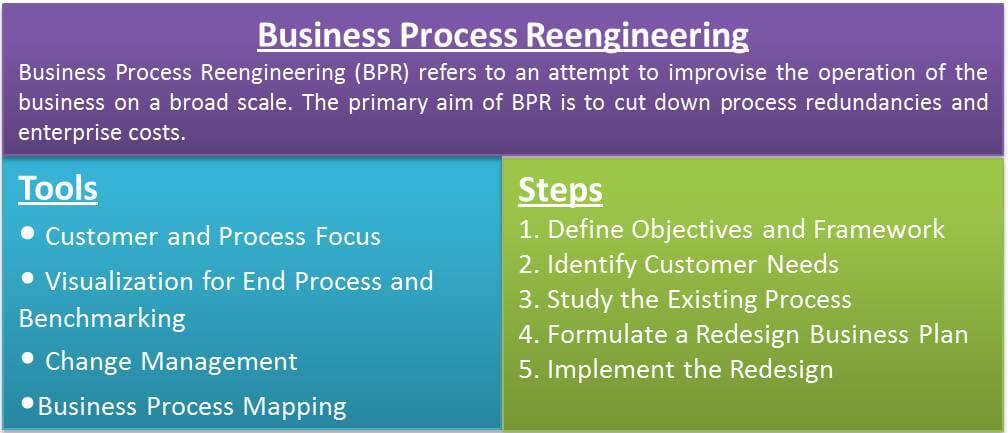
Business process reengineering examples : Cereal products
The process of transforming food into cereal products begins on the farm with the harvest. This is followed by primary processing, packing and transportation to the processing plants (depending on the grain).
This large company analyzed its process and discovered a serious logistical problem. It lost almost 20% of the grains harvested during transportation from farms to the factories, located near the biggest consumption centers, due to the precariousness of the roads.
After a study, this Business Process Reengineering case came to the conclusion that it would be more profitable to move the factories nearer to the farms. Afterwards, they transport final products to large centers with much fewer losses.
The old factory sheds were transformed into distribution centers, helping to reduce the impact of the initial investment, they already had docks and other ready-made logistics infrastructure.
Know more: Watch this video with more in-depth details on what is Business Process Reengineering, take advantage of it now:
Business process reengineering examples : Non-integrated system
It might also be that your company has a disconnected system. This forces each team member or customer to go through several departments and people to solve a problem.
People lose information, they constantly repeat data, which frustrates everyone. You can solve this by a general change in the company’s system. Integrate systems with effective software that makes all information clear and available.
These are just a few business process reengineering examples, and how BPR can help companies with problems. Business Process Reengineering case studies, like these, are key to being inspired and provoking thoughts of innovative solutions for your business.
It’s important to remember that you shouldn’t make changes before mapping and modeling processes. For this, HEFLO is the best tool in the market, which allows you to understand exactly what your company needs.
Now that you’ve read about Business Process Reengineering examples, also check out examples of how to reduce costs in your company and get onto it now!
3 Comments . Leave new
Nice article. Well explained these terms and infographics really help me to understand this concept.
Thank you very much.
Good article. How can this be applied in small (tiny) organizations, mainly in trading businesses?
Leave a Reply Cancel reply
Your email address will not be published. Required fields are marked *
Post Comment
- Business Management
- Process Automation
- Process Documentation
- Process Improvement
- Process Mapping
- Process Modeling
- Process Optimization
25 Operational Excellence Examples for Peak Business Performance
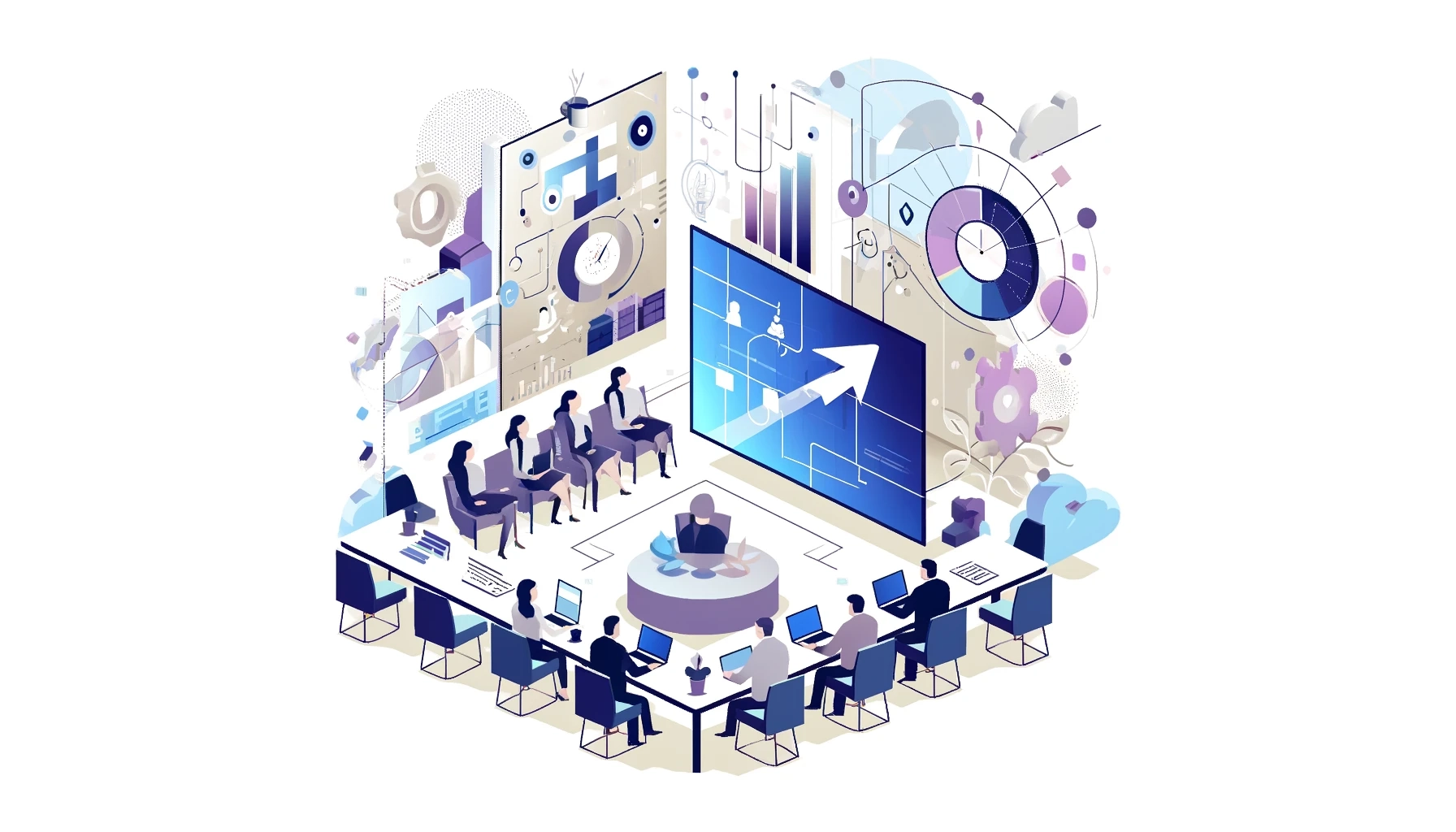
Turn your texts, PPTs, PDFs or URLs to video - in minutes.
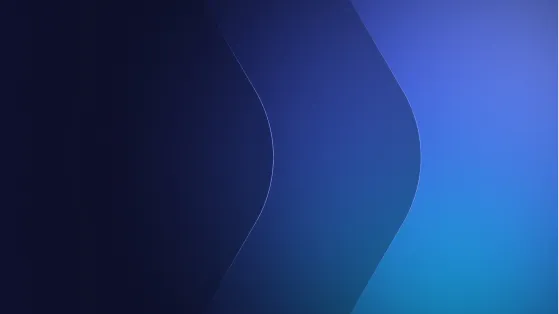
Operational excellence (also known as OpEx) is the reason why some businesses rocket past the competition while others are still revving their engines at the starting line.
But what does your executive team really mean when they say they want to "achieve operational excellence"?
Excellence means great performance... constantly. No easy feat.
This business philosophy drives organizations to find iteratively efficient ways of doing things. The result is a happy customer, workforce, and bottom line — simply put, business success.
Joseph F. Paris Jr., founder of the Operational Excellence Society, says, " When implemented well, OpEx creates an environment where leadership and employees collaborate to improve operations [...] A collaborative approach drives value for customers and anticipates and resolves issues pre-emptively. "
Let's show you some examples of operational excellence and how other businesses use it.
Example 1: Continuous improvement
Toyota's Kaizen approach is one of the most popular operational excellence examples. It involves employees at all levels working together to achieve regular, incremental improvements in the manufacturing process.
The term "Kaizen" in Japanese means "change for the better" or "continuous improvement." This philosophy focuses on continually improving processes in manufacturing, engineering, business management, and other areas to boost operational performance.
Kaizen is literally applied every day in Toyota's factories. With every employee tasked to produce Kaizen inspired optimizations, it's operational excellence is inevitable. Here's a short clip that shows it in practice:
Example 2: Focus on process
Intel implements a rigorous process-oriented approach in its chip manufacturing. The company combines standardized processes with Six Sigma and significantly improves operational excellence. Basically, it systematically optimizes each step to enhance efficiency, reduce waste, and ensure consistent quality outcomes.
Check out this behind-the-scenes tour at one of Intel's factories in the U.S:
Example 3: Cost reduction
By using Synthesia , an AI video maker, Modern Canada dramatically reduces the costs of producing training and operational videos from thousands of dollars per video to significantly less.
According to this case study, the company generated 100 videos in six months, 90% faster, while saving +$6,000 per video.
How companies can cut down costs using operational excellence examples like this one:
- Implement automation and AI tools to streamline processes and reduce labor costs.
- Outsource functions like IT support, human resources, and payroll.
- Regularly review and negotiate supplier contracts to secure better pricing or terms.
- Shrink utility costs with energy-efficient workplace technologies and practices.
- Support remote work wherever possible.
Example 4: Customer satisfaction ratings
Amazon is at the top of the list in this category of operational excellence examples. The giant retailer tracks customer feedback and satisfaction through its star rating system and detailed customer reviews. This system influences product offerings and seller standards by forcing sellers to constantly enhance their business processes, improve customer fulfillment, and drive overall operational excellence.
Here's how you can make the most of customer satisfaction ratings at your company:
- Incorporate real-time feedback on services and products.
- Use feedback to make immediate adjustments to operations.
- Identify specific areas or demographics where satisfaction is low.
- Tailor operational improvements for the segments that show low satisfaction.
- Set clear metrics that connect customer happiness ratings to individual and team performance goals.
- Promote a culture of customer-centric operational excellence.
Example 5: Lean manufacturing
With a smooth "just-in-time" (JIT) inventory system Dell minimizes stock levels and reduces waste while ensuring components are available for assembly exactly when needed. This system directly serves lean manufacturing, allowing the company to create more value for customers with fewer resources because:
- It keeps only the necessary materials on hand, reducing storage costs and increasing operational excellence.
- Goods arrive just when needed, making the production process quicker and more flexible.
- Less money is locked up in unused inventory, allowing funds to be used for other business needs.
- Any issues with inventory need to be fixed immediately to avoid slowing down production, leading to ongoing improvements in product quality.
Example 6: Create value for customers
This is one of the unique examples of operational excellence because it involves creating value for customers by first obsessing over employee training.
While taking great care of its employees, Heineken adds value to the end user and ensures better service and product quality. Its continuous improvement efforts led the company to use AI to scale training video production . This shift allowed it to make employee resources more engaging and accessible.
Since using AI to achieve operational excellence, Heineken has trained 70,000 employees in multiple languages in supply chain processes. Here's how they did it and what their Global TPM Manager of Customer Service and Logistics says about it:
Example 7: Agility
Netflix has rapidly adapted to changes in consumer behavior, from DVD rentals to streaming services. It continuously evolves its content offerings using real-time data to match what worldwide viewers want.
This service powered by analytics keeps content interesting and audiences engaged. Netflix digitized its interactions with 151 million subscribers, and algorithmic recommendations trigger 80% of the content these people watch. The result is a retention rate enhanced by 79% .
Example 8: Customer focus
As a "customer-obsessed company that focuses on delivering a WOW experience," Zappos empowers its customer service reps to go to great lengths to satisfy customers. Their dedication to operational excellence principles allowed the company to grow a loyal customer base through exceptional service. Now, the entire internet talks about Zappos "going to extremes for customers."
To truly satisfy its customers, Zappos first pleases its customer service reps. While most call centers have a 30-45% turnover rate, at Zappos, it's only 18-20%. These stats show that the company retains 10-25% more employees than the average call center.
Example 9: Learning
As a global leader in science and innovation, DuPont creates in-house training videos for its Operational Excellence Program. The company is committed to continual learning and skill development across its international workforce.
DuPont turned to AI videos to scale training production more effectively. This decision allowed it to create video learning resources 80% faster and with +$10,000 savings per video compared to third-party vendors.
Example 10: Science
The science-based technology company 3M encourages its researchers to spend 15% of their time on projects of their choice. This approach fosters innovation and has led to the development of Post-it Notes, a product now available in any stationary store worldwide. The company's innovation mindset made it to the Harvard Business Review publication.
Example 11: Create comprehensive transparency
Patagonia offers complete transparency about its supply chain and the environmental impact of its products, building trust and loyalty. As proof, Patagonia's brand awareness is at 57% in the U.S., and 79% of its customers are loyal to the brand.
The company has a solid Supply Chain Environmental Responsibility Program and focuses on material traceability to map out all the entities in its supply chain. This level of transparency is a powerful operational excellence strategy example.
Example 12: Standardization
The Canadian international real estate investment trust Northwest Healthcare Properties has a special approach to using video for training. By creating consistent, scalable, and easily updated training content with AI, it ensures a standardized learning experience across the organization. This standardization drives business processes and is critical during transformative changes.
Example 13: Decision-making
There's no list of operational excellence examples that won't include Google! The tech giant uses data-driven decision-making processes and operational excellence tools to inform its product development, ensuring decisions rely on data analysis and metrics.
By examining a lot of information and numbers to make smart choices about new products, Google can be more sure that its products will be useful and that people will like them.
Example 14: Respect every individual
The SAS Institute maintains high employee satisfaction by respecting personal work-life balance and providing a supportive work environment. The entire organization lives and breathes by the principle that "satisfied employees mean satisfied customers." By taking care of its most important asset, the employees, the Institute achieves organizational excellence much more easily.
Example 15: Empower employees
At Southwest Airlines, employees can make in-the-moment decisions that enhance customer service. Empowering the staff creates a sense of ownership. They feel responsible and take the initiative to solve problems creatively. Plus, happy staff means happy customers—when the team feels free to personalize their approach, they can deliver above-average service.
Forbes called Southwest Airlines "the world's most profitable airline ever." You can read its story here .
Example 16: Seek perfection
The story of the late Steve Jobs spending 30 minutes debating the shade of grey that Apple should use for the in-store bathroom signs is internet-famous.
The company prioritizes designing beautiful and functional products even today, believing this sparks user creativity. This commitment to aesthetics and high performance drives their continuous pursuit of innovation, pushing them to create even better products.
Example 17: Assure quality at the source
L. L. Bean ensures quality from the start of the manufacturing process. It implements strict operational excellence methodologies to minimize defects and customer returns. This approach helps maintain its reputation for high-quality products that customers trust and rely on.
Example 18: Leadership
Following Satya Nadella's vision, Microsoft emphasizes a growth mindset. Leaders at all levels are encouraged to see challenges as opportunities to learn and grow. This mindset excites everyone to learn new skills and contribute to the company's success. It's a win-win — employees feel empowered, and Microsoft keeps innovating.
Example 19: Think systematically
IKEA systematically designs its operations, from product design to in-store customer experience and follow-up services. This ensures ongoing process improvement, efficiency, and a unified process flow throughout the production cycle and customer journey. Moreover, this way of thinking at every business step helps eliminate unnecessary procedures.
Example 20: Employee feedback
The #1 AI CRM, Salesforce, regularly solicits employee feedback through internal platforms and town hall meetings. The company uses this feedback to influence its policies and culture. That's how its workplace meets employees' needs and goals, creating a friendly and welcoming environment that encourages new ideas and growth.
Example 22: Lead
Indra Nooyi, former CEO of PepsiCo, led the company to pivot towards healthier products in response to changing consumer tastes and health trends. This leadership move helped PepsiCo stay relevant and competitive as more people began choosing healthier options.
Example 23: Create repeatable processes
FedEx has optimized repeatable package routing and delivery processes, ensuring fast, reliable service worldwide. Their consistently efficient processes for package delivery pay off in high client satisfaction worldwide. In 2023, the company won the "Logistics Provider of the Year" award.
Example 24: Commitment to quality
When you say Rolex, you say quality. The company adheres to stringent aesthetic guidelines and quality control processes in manufacturing watches, ensuring its reputation for reliability and excellence. That's why they've been around for over 100 years (since 1905!). It takes a whole year to make one Rolex, and they say you can recognize it from 20 feet away:
Example 25: Establish key performance indicators (KPIs)
Coca-Cola uses KPIs to measure everything from sales performance to environmental impact, helping to align its operations with strategic goals. Thanks to these thorough and specific KPIs, all parts of the company work effectively towards common objectives, promoting efficiency and accountability across the organization.
Power your operational excellence with AI videos
Imagine replacing lengthy emails and yawn-inducing manuals with engaging, crystal-clear videos that even the busiest bee on your team can understand in a snap.
Yes, videos help you streamline operations, enhance training, and communicate complex processes with incredible ease.
And no, they don't have to blow your budget. On the contrary! Creating AI videos can save you money, time, and even personnel, replacing traditional crew-led video production. It's so easy you can do it yourself in hours instead of days or weeks.
Use this free AI video generator and see what it's like to turn text into video in minutes!
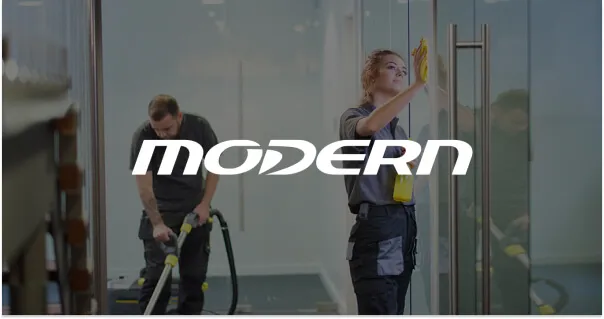
You might also like
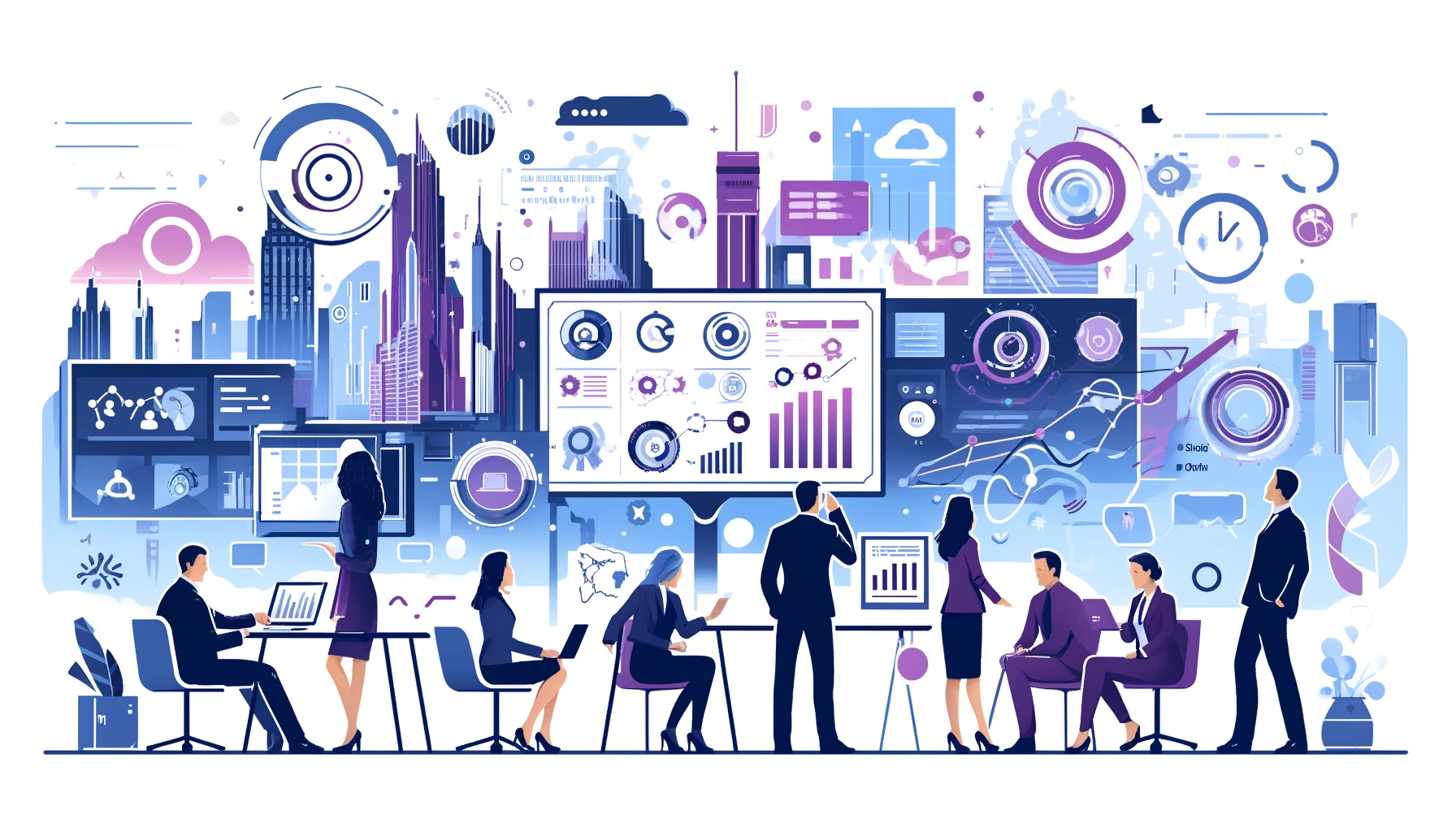
6 Must-Know Sales Enablement Trends & Stats for 2024
Discover the latest AI-powered sales enablement trends & stats for 2024. Elevate your sales strategy with insights on sales enablement trends.
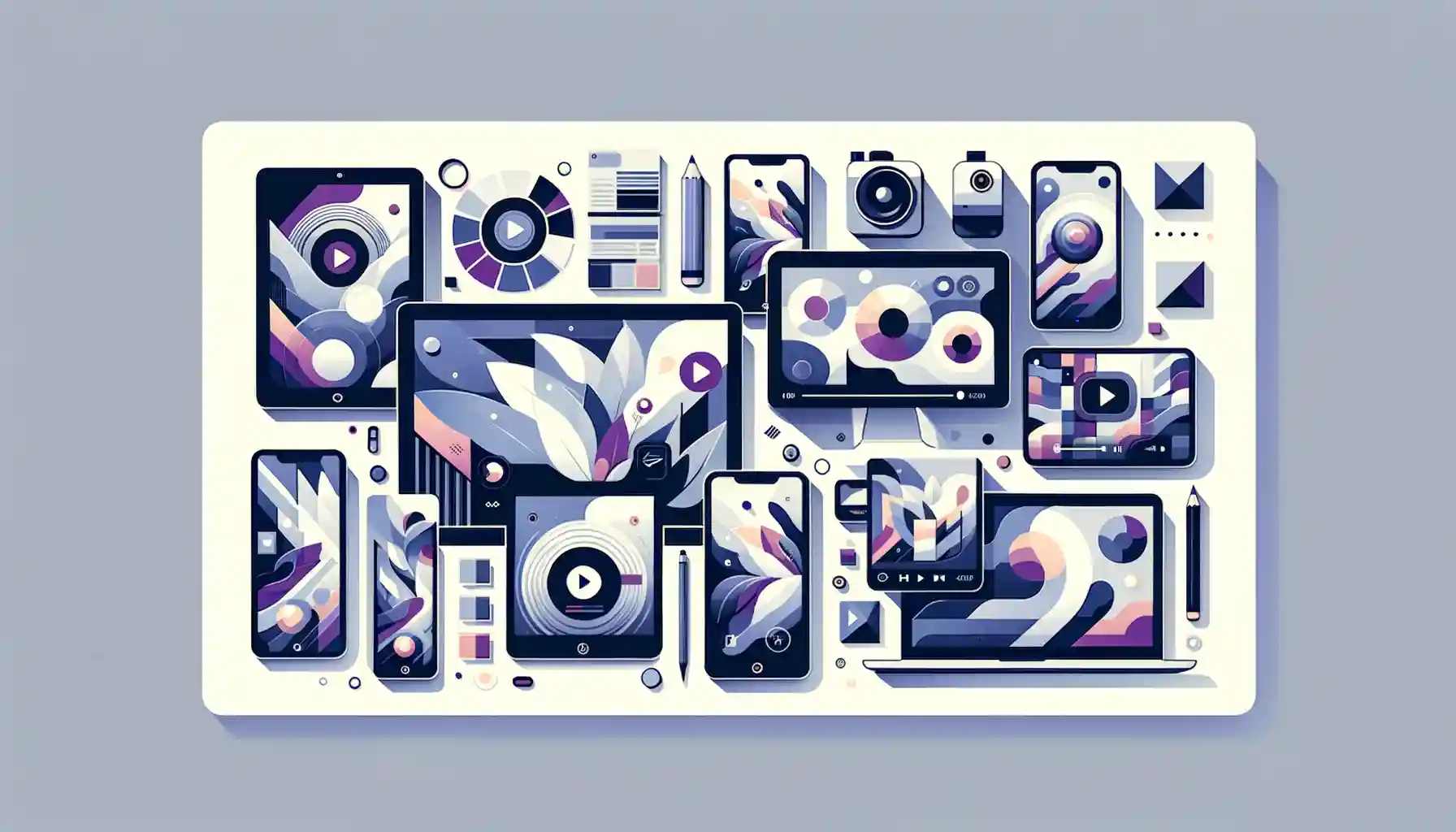
12 Brilliant examples of brand videos
Explore these 12 brilliant brand videos to get inspired by. Learn how to create impactful brand videos that resonate with your audience and drive sales.
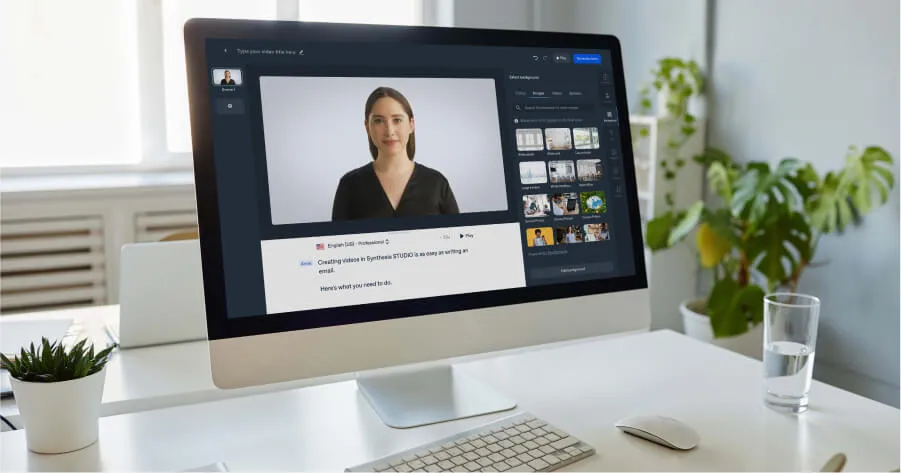
How To Create Effective Video SOPs
SOPs don't have to be boring and dull. Here we show you a better way of presenting these documents - in video.
Discover 25 operational excellence examples for peak business performance, including continuous improvement and lean manufacturing.
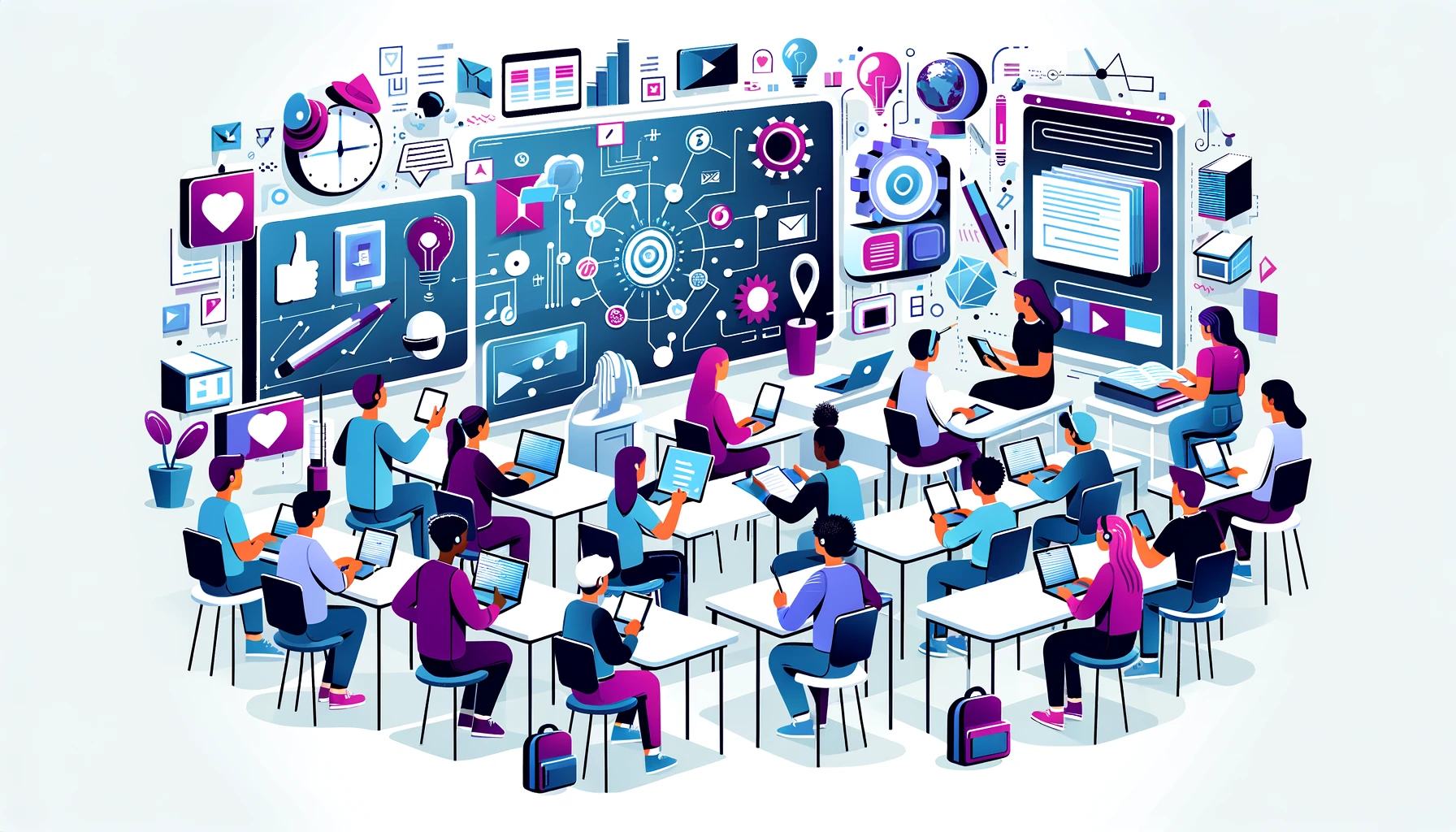
11 Most Important Education Trends for 2024 and Beyond
Discover the top 11 education trends for 2024 & beyond, including AI personalization, gamification, AR experiences, & more. Stay ahead with the latest trends!
Frequently asked questions
Ready to try our ai video platform.
Create an account and get started using Synthesia, with full access to all 160+ avatars and 130+ languages.
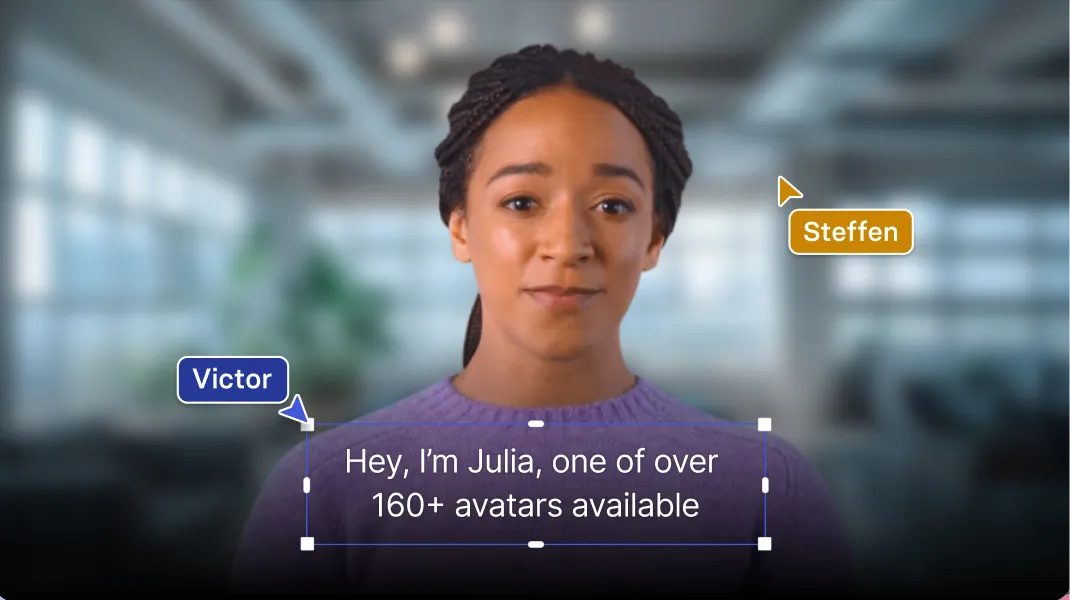
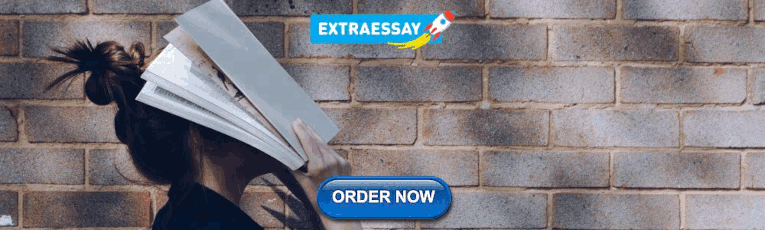
IMAGES
VIDEO
COMMENTS
Process improvement solutions help businesses define weaknesses and take action to solve these problems. In the case studies we collected, the most common project results that we came across are as follows: 1- Improved efficiency: Most businesses increase the efficiency of their processes by adapting process improvement methodologies.
An insurer's process work shortened response times and increased on-time case resolutions by 42%. Cost Savings: Eliminating waste and paperwork reduces expenses. A telecom achieved $2.3 million in annual savings through an RPA initiative. Overview of 55 Process Improvement Case Studies. Here is a high-level snapshot of the case studies we ...
The global business process management market size was valued at USD 14.9 billion in 2021, and is projected to grow at a CAGR of 14% from 2022 to 2030, per Grand View Research. This underscores why over 80% of organizations are looking to optimize, automate, and transform their processes. The results make the investment highly worthwhile.
PDSA: PDSA is a structured cycle for improvement. The steps are: Plan: Define the problem and identify possible solutions. Do: Experiment by implementing one solution. Study: Analyze the results of the experiment. Act: If the experiment was successful, add it to the standard operation. If not, begin again.
Lean Management Examples from a Variety of Businesses. The following case studies of lean management principles in action show you how a variety of real businesses solved real business problems under diverse conditions. ... management re-organized the transformation around problem solving and process improvement to create a culture that engaged ...
Six Sigma Case Study is a data-driven methodology widely used in organisations to improve process efficiency and quality. It helps reduce process defects and variations, enhancing customer satisfaction and increasing profitability. It provides a real-world example of how its methodology was applied to identify and solve a problem, showcasing ...
case study:Performance anagement and Lean rocess mprovement Results Washington. 22. A publication of the. Ash Center for Democratic Governance and Innovation Harvard Kennedy School 79 John F. Kennedy Street Cambridge, ma 02138 616-495-0557 www.ash.harvard.edu This paper is copyrighted by the author. It cannot be reproduced or reused without ...
The following case study examples demonstrate a mix of BPR methodologies and use cases working together to yield client benefits. Bouygues becomes the AI standard bearer in French telecom Bouygues Telecom , a leading French communications service provider, was plagued by legacy systems that struggled to keep up with an enormous volume of ...
7 types of process improvement methodologies. There are seven different business process improvement methodologies your team can use to help reduce inefficiencies. In most cases, the methodology you choose depends on why you want to improve your processes and what you're looking to improve. 1. Six Sigma methodology.
CASE STUDY. This case study evaluates the process and methodologies used in certifying the win/loss review process as a Six Sigma Black Belt project at Microsoft Corporation. It shares the insights gained from a process improvement perspective but does not cover broader benefits and results, such as improvements in win rates or revenue performance.
PM Solutions led a targeted mentoring program for the client's project leads to provide one-on-one advice and coaching on how to apply consistent project management practices within the confines of their actual projects. Value Delivered: Improved on-time project delivery to 80% resulting in one program booking $100,000 of business in the first ...
Five Case Studies of Transformation Excellence. November 03, 2014 By Lars Fæste , Jim Hemerling , Perry Keenan, and Martin Reeves. In a business environment characterized by greater volatility and more frequent disruptions, companies face a clear imperative: they must transform or fall behind. Yet most transformation efforts are highly complex ...
With process improvement, customers get to gain from better customer service, as well as improved product quality. As a result, customer satisfaction increases. 3. Improved Employee Satisfaction. Along with happy customers comes happier employees as they no longer have to waste time on manual, repetitive, and monotonous tasks.
Process Improvement Plan Case Study. Following the steps we outlined earlier, let's explore a hypothetical process improvement plan for a doctor's office that constantly gets complaints from patients about how many forms they have to fill out. Process Improvement Plan: Reducing Patient Form Burden in a Doctor's Office. Identify the Goals:
The second case study outlines how using clinical trial metric dashboards can help teams to make data-informed decisions. Both case studies are examples of the importance of focusing on the science of science, as well as the science itself. Further quality improvement tools and examples are highlighted in the research process improvement ...
Creating a Culture of Continuous Improvement. by. Aravind Chandrasekaran. and. John S. Toussaint. May 24, 2019. michellealbert/Getty Images. Summary. A number of health systems have scored ...
Case Study: Business Process Improvement. This Case Study illustrates how Gagnon Associates used its Business Process Improvement capability to optimize a client's new-product development process: The Company. A formerly high-flying, enviably profitable surgical products division of a major health care company.
Using Exploratory Data Analysis to Improve the Fresh Foods Ordering Process in Retail Stores. This case study presents a real-world example of how the thought processes of data scientists can contribute to quality practice. See how explorative data analysis and basic statistics helped a grocery chain reduce inefficiencies in its retail ...
Business process reengineering examples: company selling commemorative cards. In a company that offers products such as Christmas, anniversary, commemorative cards, etc., renewing the stock and changing the design of the cards is constantly fundamental. On average, it takes three months for new items to reach the shelves.
Abstract and Figures. This thesis is a case study for a Roofing company based in Phoenix Arizona. The topic of the thesis is Business Process Improvement and overviews the popular methods such as ...
Example 1: Continuous improvement. ... According to this case study, the company generated 100 videos in six months, 90% faster, while saving +$6,000 per video. ... This ensures ongoing process improvement, efficiency, and a unified process flow throughout the production cycle and customer journey. Moreover, this way of thinking at every ...
MDIC Case for Quality: CAPA Process Improvement 3 To enable such a paradigm shift, the team applied a "design thinking" approach to redefine the CAPA process. Further, leveraging principles of agile development, the team rapidly refined and tested the proposed solution. The result is the Risk-Based Improvement Framework presented in this paper.
Jonathan Kraft, Manager of Open Standards Benchmarking at APQC, explains the five use cases for the Process Classification Framework (PCF)®, the world's most widely-used process framework, including process discovery and standardization, process improvement, technology implementation, benchmarking, and content management. Watch the video.
CAHPS ® surveys play an important role as a quality improvement (QI) tool for healthcare organizations that use the standardized data to:. Identify relative strengths and weaknesses in their performance. Determine where they need to improve. Track their progress over time. Supporting and assessing the use of CAHPS surveys for QI purposes is one of the key objectives for the CAHPS grants.