Hubs is now Protolabs Network. Find out more
You’ve come to the right place. Hubs is now Protolabs Network.
The same broad capabilities, exceptional quality and competitive pricing under a new brand.
Get instant quote
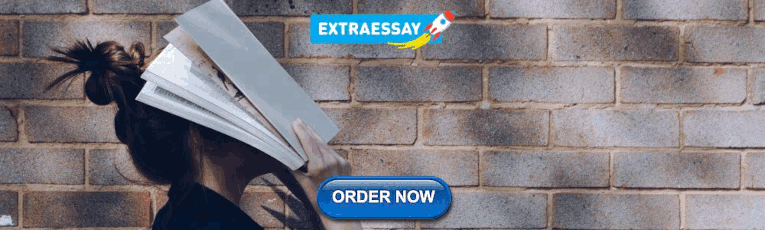
3D printing for aerospace and aviation
How does 3D printing accelerate innovation in the aerospace and aviation industry? In this article, we explain how 3D printing and additive manufacturing are commonly used in aerospace and how they improve prototyping and end-use part production for these industries.
3D printing is a clear fit for many prototyping and end-use applications within the aerospace and aviation industry. Parts produced via additive manufacturing can be stronger and lighter than those made using traditional manufacturing.
Aerospace was a very early adopter of 3D printing and still continues to contribute heavily to its development. Companies in this industry began using 3D printing in 1989, and in 2015, aerospace accounted for 16% of additive’s $4.9B global revenue.
In this article, we explore how 3D printing has made an impact on the aerospace industry. We go over design requirements for parts used in airplanes and give design recommendations for common and more niche aerospace and aviation applications. As well, we cover the best materials for 3D printing parts for this industry and examine one of our favorite case studies.
Implementing 3D printing in the aerospace design workflow
Designers and engineers creating new products in aerospace and aviation can implement 3D printing at all stages of the design workflow. Let’s break down all the major stages.
Design communication
Designs in the aerospace industry often begin as concept models showcasing a component of an aircraft. These are often also regularly used for aerodynamic testing, which is of critical importance for aerospace. SLA printing and Material Jetting are used to produce high detail and smooth scale models of aerospace designs. Accurate models allow design intention to be clearly communicated and showcase the overall form of a concept.
Validation
Prototyping using 3D printing is now commonplace in the aerospace industry. From a full-size landing gear enclosure printed rapidly with low-cost FDM, to a high-detail, full-color control board concept model, there is a 3D printing process suited to every prototyping need. Engineering materials for 3D printing also allow for full testing and validation of prototype performance.
Pre-production
One of the areas where 3D printing has been most disruptive and valuable is the production of low-cost rapid tooling for injection molding , thermoforming and jigs and fixtures . Within aerospace, this allows for tooling to be quickly manufactured at a low cost and then used to produce low to medium runs of parts. This validation mitigates the risk when investing in high-cost tooling at the production stage and can also provide production components for quantities up to 5,000 to 10,000 parts.
Production volumes in the aerospace industry can reach more than 70,000 parts per year, so 3D printing has predominantly been used in the past as a prototyping solution rather than the manufacturing of end-use parts.
Today, improvements in the size of industrial printers, the speed they are able to print at and the materials that are available all make 3D printing a viable option for more medium-sized production runs, particularly for high-end interior build-outs.
Customization
3D printing technologies significantly impact the aerospace industry when a substantial improvement in aircraft performance can justify the cost of highly complex one-off components.
The average corporate aircraft travel 75,000 miles per month and a single component that was designed and manufactured with 3D printing can reduce air drag by 2.1%, reducing fuel costs by 5.41%. And that’s just the impact of one 3D-printed part.
Parts can be tailored to a specific aircraft (custom, lightweight bracketry) or type of aircraft (cargo, passenger or even helicopter). 3D printing also provides part consolidation and topology optimization of many custom aerospace components.
How is 3D printing used in aerospace engineering?
Jigs & fixtures.
Big benefits exist for several more mundane 3D printing applications, including the production of jigs and fixtures . For each individual aircraft, companies have hundreds of fixtures, guides, templates and gauges 3D printed, generally with 60 to 90 percent reductions in cost and lead time compared to other manufacturing processes.
Surrogates are placeholder parts used throughout production that represent components that are later installed in final assemblies. Surrogates are mainly used for training. NASA and several Air Force bases commonly use surrogate parts on the production floor.
Mounting brackets
3D printing is commonly used to manufacture structural, low-volume metal brackets (with DMSL/SLM ) that mount complex life-saving systems to the interior wall of a plane.
High detail visual prototypes
3D printing with Material Jetting is able to produce multicolor designs with a surface finish comparable to injection molding. These visually appealing models allow designers to get a greater understanding of the form and fit of a part before making important production decisions.
This highly accurate method of prototyping is also ideal for aerodynamic testing and analysis, as the surface finish you get with 3D printing is often representative of a final part.
3D printing is used routinely to manufacture aerospace components that rely on aesthetics over function, such as door handles and light housings to control wheels and full interior dashboard designs.
How does 3D printing improve aerospace manufacturing?
Geometric design freedom.
Aerospace applications make use of advanced engineering materials and complex geometries in an attempt to reduce weight while improving performance. Aerospace parts frequently include internal channels for conformal cooling, internal features, thin walls and complex curved surfaces.
3D printing is capable of manufacturing such features and allows for the fabrication of highly complex and lightweight structures with high stability. This high degree of design freedom enables the topological optimization of the parts and the integration of functional features in a single component.
Also, certain 3D printing technologies, such as SLS , DMSL/SLM and Binder Jetting , are capable of small batch production at reasonable unit costs.
Consolidating assemblies into a single part
The design freedom you get with the 3D printing process also helps to consolidate multiple parts into a single component. This leads to weight savings (and thus cost reduction) and also reduces the amount of inventory kept at any time.
Surface finish
Having the right surface finishes is critical for the aerospace industry, and 3D-printed parts can be post-processed to a very high surface finish. Some technologies, such as Material Jetting , can produce parts with a smooth, injection-molding-like finish off the printer with little post-processing needed. High-performance metal parts produced with DMSL/SLM or low-cost metal parts produced with Binder Jetting can also be smoothed and polished (or even CNC machined) after printing to improve their accuracy and surface finish.
Part orientation
For functional parts that will bare load, part orientation in the build platform is very important. Due to the layer-by-layer nature of 3D printing, most parts will have anisotropic mechanical properties and will be weaker in the Z direction. This should be taken into consideration during the design process.
Support structures
Support structures are used in 3D printing to provide a solid base for depositing material above overhangs or at walls with steep angles (above 45 degrees). Support is also crucial in metal 3D printing, as it anchors the parts in the build plate and protects against warping.
The areas printed on supports will have a lower surface finish and some marks from the support removal. If this is suboptimal for your parts, there are processes that do not require support structures, such as SLS and Binder Jetting .
What are the best materials for 3D printing aerospace and aviation parts?
Check out this table for a more in-depth comparison of materials used to 3D print custom aerospace and aviation components.
3D printing in practice: Printing parts for satellites
Satellite designs include geometrically specific brackets that link the body of the satellite with reflectors and feeder facilities mounted at each end. Manufacturing these critical brackets comes with two distinct challenges.
These brackets must affix reflector and feeder facility components securely to the body of the satellite. As well, these brackets must be able to withstand the stress of insinuating against temperatures ranging from -170 to 100 degrees celsius. Very few materials can meet the requirements for the amount of stress these brackets endure.
Engineers at Airbus overcame these challenges by 3D printing these brackets using titanium. By opting to manufacture the brackets the additive way, the engineers at Airbus cut down on material waste, consolidated parts (making assembly easier and less labor-intensive), optimized part geometries and ended up with lighter-weight components. 3D printing helped reduce costs to produce parts and will save fuel over the life cycle of the satellites thanks to the lighter weight of the components.
More resources for engineers
What materials have the best repeatability.
Seeking consistency and predictability in your parts? Check out our guide on repeatability, which highlights the materials that will perform the same way time and time again.
Guide to designing for product scalability
How can you create a part or product that’s ready to move from prototype to production? Check out our article, which offers tips and tricks for designing with scalability in mind.
What is GD&T? How to reduce manufacturing errors and improve quality
What is Geometric Dimensioning and Tolerancing (GD&T) and how is it used? This article explores the basics of how and when to use GD&T to get the best results out of custom part manufacturing.
How do you design parts for MJF (Multi Jet Fusion) 3D printing?
Multi Jet Fusion (MJF) 3D printing can create highly accurate, complex industrial parts more efficiently - and potentially more cost-effectively - than other industrial 3D printing processes. This article covers how to design parts for MJF, common applications of the technology and key best practices.
What is design for manufacturability (DFM)?
Design for manufacturing (DFM) means taking a design-first approach to manufacturing. In this article, we look at the overall DFM process, the necessary steps for a successful outcome, examples of DFM done right and how to get the most out of your own processes.
3D printing STL files: A step-by-step guide
Learn how to avoid low quality 3D prints or unnecessarily large files by exporting your STL file in the correct resolution.
What’s the right resin for SLA? 3D printing materials compared
What are the different materials available for SLA 3D printing? This article compares the main printing resins, including standard, tough, durable, heat resistant, rubber-like, dental and castable, by material properties. Find the best material option for your application.
How to design parts for binder jetting 3D printing
A comprehensive guide on designing parts for Binder Jetting, covering the printing process, design specifications and material options.
What are the top STL file errors? Here's how to fix them
What are the most common STL file errors and how will they affect your ability to export models for 3D printing? Learn to identify the errors you may encounter when working with STL files and how to fix them so they don't delay your next 3D printing run.
What is CAD modeling? Comparing design software for 3D printing
What is CAD modeling and why is it an essential tool for digital manufacturing? Explore the types of CAD software available for bringing ideas into the physical world via digital 3D modeling. Find the right software tools for your application.
How to design parts for material jetting 3D printing
This article explains how to design Material Jetting 3D printed parts including technical design specifications, materials, limitations and an introduction into the post-processing options available.
Ready to transform your CAD file into a custom part? Upload your designs for a free, instant quote.

Chat To Team
01765 694 007
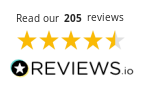
The Best Applications of 3D Printing In The Aerospace Industry
The best example of the application of Additive Manufacturing (AM) or 3D Printing is found in the Aerospace industry, which produces potentially lighter and stronger parts than traditional manufacturing parts .
The aerospace industry was a forerunner in 3D printing and contributed significantly to its development. Some aviation companies began using this technology in 1989, and 3D printing usage exploded over the next two decades. In 2015 , the aerospace industry accounted for around 16% of the $4.9 billion in global 3D printing sales.
This article explains how 3D printing in the aerospace industry is utilised for manufacturing and prototyping in the aircraft sector. Continue reading till the very end.
3D Printing of Large Aircraft Components
Rolls-Royce debuted the world’s most significant 3D printed engine component in 2016, preceded by successfully conducting the first-ever flight test run. This component was used in the Trent XWB-97 engine by Rolls-Royce, which was the result of coordination between the producers and the Department of Material Science and Engineering at the University of Sheffield. The equipment was a 1.5-meter-diameter titanium front section that housed 48 aerofoils. The old engine was replaced with Trent XwB-97 in the Airbus A380 after performing flight tests successfully.

Electron beam melting (EBM) technology was used to print the 3D component. This highlights 3D printing’s adaptability in the aerospace industry, extending beyond research and prototype to actual, polished industrial applications.
The Production Benefits of 3D Printing
Although some forms of additive manufacturing are still in their infancy, we’re seeing uptake for items that pose a more significant risk. Industry participants are now comfortable enough to venture beyond polymeric non-structural defense and aerospace parts into complex formation and critical components 3D printing applications . There are numerous advantages to employing 3D printing in the aerospace industry .
Freedom of Simplification
Although streamlining is a significant advantage, 3D printing also allows for complicated designs that are impossible to produce using traditional technologies such as injection moulding. This gives engineers complete design freedom to produce parts with the highest possible performance. It means you may utilise better design configurations, decrease tooling and fixture costs, and improve the durability and longevity of parts from a manufacturing standpoint.
Reduced Inventory Costs
Regardless of the certifications or requirements, this production method may produce customised parts worldwide using standard equipment and no part-specific tooling. For defense manufacturing , this implies having access to facilities close to crucial airbases or creating crucial components at the source, which also translates to lower inventory expenses.
Improved Aircraft Design
Improved airplane design is another benefit of 3D printing for the aerospace sector. Many advanced modifications cut the plane’s life-cycle cost by improving engine efficiency, lowering drag, and reducing mass. As 3D printing software becomes more advanced, engineers can now improve designs that benefit specifically from additive manufacturing technologies.
Enhanced Supply Chain
The development and construction of an airplane is a vast operation. 3D printing enhances manufacturing efficiency and reduces supply chain lead times by producing a wide range of components from a wide range of raw materials. It also addresses the aircraft demands characterised by extended lead times, production schedules, and long production delays that can last years.

Boeing launched the world’s 1st 3D printed metal satellite antenna in 2019. It has been experimenting with 3D printing since then. The antenna was designed for Spacecom, an Israeli company that recently launched the AMOS 17 satellite. Boeing used 3D printing to replace numerous parts in a large structure with a single 3D printed part, decreasing the antenna’s weight and labor hours.
Airbus has been employing additive manufacturing to manufacture and repair various parts for its aircraft for several years. By approving Materialise and EOS’s technologies, the European aerospace company is reaffirming its faith in 3D printing.
The two 3D printing companies have been approved to use selective laser cutting sintering (SLS) technology to produce certified parts. The parts will be created on an EOS P 770 3D printer and made of PA 2241 FR and EOS flame-retardant polyamide.
Airbus will use the SLS technique for the first time, marking a significant step forward for the industry, which is once again depending on additive manufacturing to improve its manufacturing technology.
Airbus made bio-inspired panels 15 percent lighter by employing 3D printing instead of traditional manufacturing methods. With this technology, complex internal support systems, such as lattices within the panels can also be created without incurring additional production expenses.
NASA & Made in Space
NASA collaborates with the San Francisco-based startup Made In Space on numerous fascinating initiatives that use additive manufacturing to advance space exploration in various ways. Because many of the parts required for space missions are made of aluminum, titanium, or steel, NASA is collaborating with various small entrepreneurs to produce metal printing technologies for the International Space Station.
Selective laser melting is the preferred metal 3D printing process for aircraft on Earth (SLM). In this procedure, the metal sample is injected from a hopper onto a construction plate, and each deposited layer is about the thickness of a single strand of human hair.
The powder is then selectively melted and fused using a laser. On the other hand, these systems are very massive and demand a lot of power. Furthermore, the powders are flammable, pose a respiratory issue, and would be challenging to handle in microgravity.
Preparing Aerospace For The Future With 3D Printing
Integrating 3D printing services and technology into existing workflows at crucial stages can speed up operations and provide designers and manufacturers more insight into new aircraft performance enhancements.
As one might think, this is a critical capability for the defense industry. Printers can be deployed anywhere, from Air Force bases to aircraft carriers, and facilities can be created near-critical airbases.
This capability could allow businesses to do something more than think and act globally…it could enable them to operate beyond Earth’s borders. Space exploration and also lunar and planetary colonisation may benefit from 3D printing.

The Takeaways
The potential of 3D printing in the aerospace and defense business stretches far beyond the Earth’s atmosphere, whether it’s assisting an airline with a backlog of orders or making a tool out of lunar dust for the first settlers of Mars. As additive manufacturing establishes itself as a critical technology in aviation, it will be fascinating to see what new uses emerge.
One aspect is certain: future aircraft will be unable to take flight without the use of 3D printing.
New to 3D printing in education? Call us on 01765 694 007 to find out more about getting started, or request a sample below.
[maxbutton id=”1″]
Plastic 3D Printing Service
Fused Deposition Modeling
HP Multi Jet Fusion
Selective Laser Sintering
Stereolithography
Production Photopolymers
Nexa3D LSPc
Direct Metal Laser Sintering
Metal Binder Jetting
Vapor Smoothing 3D Prints
CNC Machining
CNC Milling
CNC Turning
Wire EDM Machining
Medical CNC
CNC Routing
Sheet Metal Fabrication
Sheet Cutting
Laser Cutting
Waterjet Cutting
Plasma Cutting
Tube Bending
Laser Tube Cutting
Laser Engraving
Custom Die Cutting
Plastic Injection Molding
Quick-Turn Molding
Prototype Molding
Bridge Molding
Production Molding
Overmolding
Insert Molding
Urethane and Silicone Casting
Plastic Extrusion
HDPE Injection Molding
Injection Molded Surface Finishes
Custom Plastic Fabrication
Micro Molding
Metal Injection Molding
Die Casting
Metal Stamping
Metal Extrusion
Custom Hydroforming
Assembly Services
Rapid Prototyping
High-Volume Production
Precision Grinding
Surface Grinding
Powder Coating
Aerospace and Defense
Consumer Products
Design Agencies
Electronics and Semiconductors
Hardware Startups
Medical and Dental
Supply Chain and Purchasing
All Technical Guides
Design Guides
eBooks Library
3D Printing Articles
Injection Molding Articles
Machining Articles
Sheet Cutting Articles
Xometry Production Guide
CAD Add-ins
Manufacturing Standards
Standard Sheet Thicknesses
Standard Tube and Pipe Sizes
Standard Threads
Standard Inserts
ITAR and Certifications
Case Studies
Supplier Community
Release Notes
Call: +1-800-983-1959
Email: [email protected]
Discover Xometry Teamspace
Meet An Account Rep
eProcurement Integrations
Bulk Upload for Production Quotes
Onboard Xometry As Your Vendor
How to Use the Xometry Instant Quoting Engine®
Test Drive Xometry
Tool Library and Tool Detail Pages
Part Revisions & Same-Suppliers for Repeat Orders
Xometry's Privacy and Security
Xometry’s Quality Assurance
Xometry’s Supplier Network
Xometry's Machine Learning
Xometry's Manufacturing Community
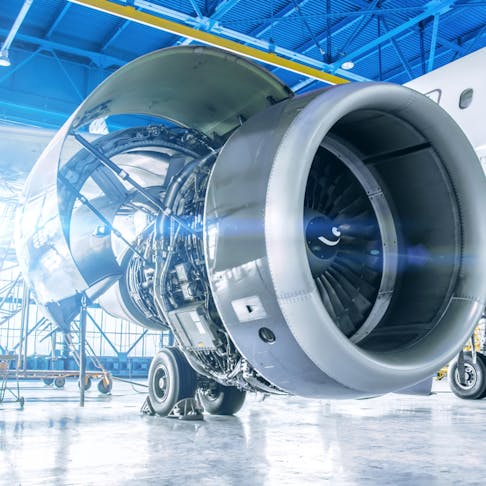
3D Printing in Aerospace: Materials, Processes, and Classifications
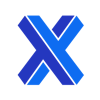
3D printing, also known as additive manufacturing, is highly valued in the aerospace industry. In an industry where weight or drag reduction can lead to huge cost savings, 3D printing has enabled aerospace manufacturers to create lighter and more fuel-efficient aircraft in a more cost-effective manner. The aerospace industry was one of the first industries to widely adopt 3D printing in the manufacture of key components, and the process has redefined the boundaries of design and manufacturing. Aerospace engineers were instrumental in the development of the 3D printing process, and the industry continues to reap the benefits today as 3D printing matures as a manufacturing process.
From jigs and prototype tooling to end-use parts like nozzles and control consoles, 3D printing in aerospace can be used to both aid the manufacturing process and satisfy particular applications within an aircraft. This article will discuss 3D printing in aerospace, the materials and processes used, and its different applications.
.css-2xf3ee{font-size:0.6em;margin-left:-2em;position:absolute;color:#22445F;} .css-14nvrlq{display:inline-block;line-height:1;height:1em;background-color:currentColor;-webkit-mask:url(https://assets.xometry.com/fontawesome-pro/v6/svgs/light/link.svg) no-repeat center/contain content-box;mask:url(https://assets.xometry.com/fontawesome-pro/v6/svgs/light/link.svg) no-repeat center/contain content-box;-webkit-mask:url(https://assets.xometry.com/fontawesome-pro/v6/svgs/light/link.svg) no-repeat center/contain content-box;aspect-ratio:640/512;vertical-align:-15%;}.css-14nvrlq:before{content:"";} What Is 3D Printing?
3D printing, also known as additive manufacturing, is a manufacturing process that creates parts layer by layer until the entire three-dimensional part is complete. It is the opposite of subtractive manufacturing processes like CNC (computer numerical control) machining where the material is removed from a workpiece to create parts. 3D printing can be used to manufacture trinkets, simple tools, and advanced components used in several industries such as aerospace, automotive, medical, machinery, and more. While 3D printing technology has existed since the 1980s, its use has exploded since the start of the 21st century as additive manufacturing has become a sound alternative to produce parts that require several processes to manufacture.
When Did the Aerospace Industry Start Using 3D Printing?
The aerospace industry was one of the first industries to implement 3D printing in 1989. Since the inception of 3D printing technology in the 1980s, the aerospace industry has been one of the largest contributors to the development of 3D printing processes and technology. Today, the industry remains one of the largest beneficiaries of the process and accounts for nearly 16% of the total revenue generated by the additive manufacturing industry.
How Did 3D Printing Start in the Aerospace Industry?
The origin of 3D printing in the aerospace industry dates back to the late 1980s. At the time, the largest benefactors of 3D printing were the US military and the defense industry. These two organizations widely used plastics as a cheaper alternative to metals to conduct testing and simulation of various aircraft systems and components.
3D printing was mainly used for prototyping and testing in the aerospace industry until the mid-2000s when it became possible to 3D print flame-retardant plastics through processes like selective laser sintering. As advancements in 3D printing continued throughout the first two decades of the 21st century, its use in aerospace applications expanded. Now it is used for applications throughout the aerospace component lifecycle, including: prototyping and validating designs, tools, jigs for aircraft maintenance, end-use parts in jet engines, and aircraft interiors.
What Kinds of Materials Are Used in 3D Printing for Aerospace Applications?
A number of different materials are used in aerospace industry applications. Common materials used are listed and described below:
1. Ceramics
2. carbon fiber .
Carbon fibers are long, exceptionally thin but strong strands of carbon atoms. Carbon fiber composites are ideal for aerospace applications since it is as strong as steel but lighter than aluminum. This allows manufacturers to improve aircraft performance by integrating 3D-printed carbon fiber parts into aircraft frames and structures. However, carbon fiber is expensive and difficult to produce, which limits the potential applications it can have in the aerospace industry.
Glass is an amorphous material that is made by the rapid quenching of a molten mixture of silica and other ingredients. Glass is a transparent and brittle material that has been used since ancient times. While it may often be associated with windows, 3D-printed glass is not used for windows in aircraft. Instead, glass-filled filaments and powders are often used to reinforce plastics and to make glass composites which are helpful in reducing aircraft weight.
Metals are naturally occurring ductile and lustrous materials that are excellent conductors of heat and electricity compared to other materials. Metals like aluminum and titanium are widely used in aircraft due to their corrosion resistance and high strength-to-weight ratios. 3D-printed metals are used in engine components, frames, structures, and electronics equipment. A major downside of metals is that they are heavy. Too much metal in an aircraft can adversely affect aircraft performance and fuel efficiency. Figure 1 is an example of a 3D printed turbine propeller:
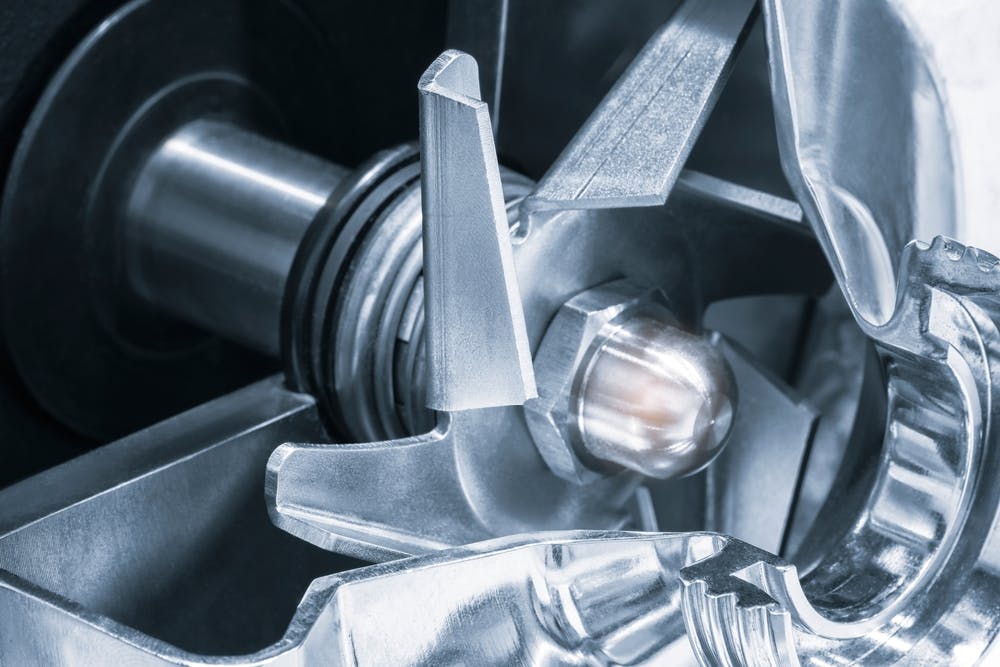
3D printed turbine propeller.
Image Credit: Shutterstock.com/Matveev Aleksandr
5. Polymers
Polymers are materials composed of repeating chains of molecules. Common examples of polymers in aerospace include synthetic thermoplastics like nylon and ABS (acrylonitrile butadiene styrene). These materials can be used to 3D-print interior components like seatback and wall panels or air ducts. Generally, polymers are great for aerospace applications since they are lightweight and durable. However, polymers are weak compared to metals and cannot be used for high load-bearing applications where metal is often preferred. For more information, see our guide on What Are Polymers .
6. Inconel®
Inconel® is a nickel-chromium-based superalloy valued for its strength at high temperatures and excellent creep and corrosion resistance. In 3D-printing aerospace applications, Inconel® is often used in jet turbine engines to make fuel nozzles. Inconel’s primary disadvantage is that it is an expensive material. For more information, see our guide on What is Inconel Metal .
7. Composites
Composite materials are composed of two or more constituent materials whose properties complement each other. Composite materials have structural benefits such as high strength and low weight, as well as increased wear resistance. Composite materials for 3D printing in aircraft lead to lighter and more structurally resilient aircraft since the desirable properties of different materials synergize. A downside of 3D-printed composite materials is that they are not biocompatible and can be expensive.
What Are the Steps in the 3D Printing Process in the Aerospace Industry?
3D printing can help validate part design and function and can be used for small-to-medium production volumes. The parts of the 3D printing process as it is used in the aerospace industry are listed and described below:
Aerospace designs commonly begin as concept models that showcase a particular aircraft component. Models are created in CAD software and then exported to a 3D-printer-friendly file format like .stl.
2. Preparation
Before a design can be fabricated by a 3D printer, certain preparation work must be completed to ensure desired print quality. The preparation methods will differ depending on part geometry, the type of 3D printing, and the printer being used. Part models must be configured and oriented in printers in a manner that ensures optimal quality. Additionally, some printers, like FDM (fused deposition modeling) and SLS (selective laser sintering) printers, require build trays to be heated before printing.
3. Printing
After 3D models are configured as desired and 3D printing systems are properly prepared according to the type of 3D printing and printing machine used, parts can be fabricated. Print times vary from a few minutes to several hours depending on the size of the part and the type of printing used.
4. Post-Processing
When 3D printing is completed, parts can be removed from the build tray. All 3D printed parts require some post-processing. However, parts printed by one method may require more post-processing than those produced by another method. For example, FDM printed parts often only require support material to be removed while DED (direct energy deposition) printed parts require additional machining processes to obtain desired dimensions.
Once post-processing is completed, the 3D printed part is tested and evaluated. If design modifications are needed, 3D printing enables designers to quickly create and test new designs. When a 3D-printed part’s intended function is satisfied, the part can be 3D printed for small-to-medium batch production or manufactured by more traditional methods.
What Are the Different Types of 3D Printing Used in the Aerospace Industry?
There are several different types of 3D printing that can be used in the aerospace industry. These are listed below:
1. Fused Deposition Modeling (FDM)
Fused deposition modeling (FDM) is a type of 3D printing that utilizes an extruded thermoplastic filament to make parts layer by layer. Molten plastic is extruded out of a nozzle onto a build tray. When the first layer cools, the following layer is deposited. This process repeats, layer by layer until the entire part is complete. FDM printing in aerospace is intended more for prototyping and design verification purposes than functional aircraft parts.
2. Stereolithography (SLA)
Stereolithography (SLA) is a 3D printing process that utilizes precisely placed photosensitive polymer resin that is cured by UV light to make parts layer by layer. SLA offers the highest resolution of any form of 3D printing and is often used to make cabin accessories like door knobs and seat back panels.
3. Selective Laser Sintering (SLS)
Selective laser sintering (SLS) is a 3D printing process that precisely sinters and fuses thermoplastic powders to form parts layer by layer. When a layer is completed, more powder is deposited, the build tray descends, and the process repeats. SLS is great for producing parts with complex geometries at high resolutions. SLS 3D printing in aerospace is commonly used for small-batch production of flexible airflow components like air ducts and heat-resistant parts like nozzle bezels.
4. Electron Beam Melting (EBM)
Electron beam melting (EBM) is a 3D printing process that uses electrically conductive metal powder and electron beams to manufacture parts layer by layer. The printing process must occur in a vacuum to prevent gas molecules from interfering with the energy emitted by the electron beam. The electron beam heats the metal powder to extremely high temperatures (1112-1292 °F) to melt and fuse it together to form parts. EBM can be used to make metal components like suspension wishbones.
5. Direct Energy Deposition (DED)
What are the different types of 3d printing machines used in the aerospace industry.
The different types of 3D printing machines used in the aerospace industry are described below:
1. Powder Bed Fusion (PBF) Machines
Powder bed fusion (PBF) machines are 3D printing machines that deposit powders and fuse them together through processes like SLS or EBM. The advantages of PBF machines include the ability to recycle unused powder for future printing processes, a wide selection of plastic and metal materials to choose from, and minimal support needed to produce parts. The disadvantages of PBF machines include the high power requirements to print parts, parts susceptible to thermal distortion, and slow printing time.
2. Fused Deposition Modeling (FDM) Machines
FDM machines are 3D printing machines that create parts by extruding plastic filaments layer by layer. FDM machines have several advantages including low cost, small footprint, and a wide variety of materials available for printing. However, FDM machines also have disadvantages. Parts printed by FDM are prone to warping and are weak in directions perpendicular to the print layers. Additionally, FDM machines are prone to nozzle clogging and frequently require bed calibration.
3. Stereolithography (SLA) Machines
SLA machines are 3D printing machines that manufacture parts by curing photosensitive polymers with a UV lamp. The advantages of SLA machines include the ability to print highly accurate and precise parts, the ability to save unused resin for future print jobs, and the ability to print complex and intricate patterns. However, the disadvantages of SLA machines include high upfront and maintenance costs and resins are not environmentally friendly.
4. Direct Energy Deposition (DED) Machines
Direct energy deposition (DED) machines are 3D printers that produce parts by using a focused heat source such as a laser, plasma arc, or electron beam that melts the powder or filament. The primary advantages of a DED printer are that it allows the grain structure of printed parts to be controlled and enables large parts to be made with little tooling. Disadvantages of DED machines include parts made with poor precision and the need for post-processing to obtain desired dimensions. Additionally, DED machines are expensive and can cost over $500,000 which can be a barrier for many organizations.
5. Binder Jetting (BJ) Machines
Binder jetting (BJ) machines are similar to PBF (powder bed fusion) machines, but deposit liquid binding agents onto metal or plastic powders to fuse them together rather than using a concentrated heat source to fuse the powders. The advantages of BJ machines include the ability to produce parts with few or no internal supports, the ability to produce parts with low surface roughness, and the ability to produce large parts. The disadvantages of BJ machines include difficulty in controlling accuracy and tolerances due to shrinkage and weak parts due to porous structures. While sintering as a post-process can make parts stronger, the additional process adds more cost.
What Types of Applications Are 3D-Printed Parts Used for in the Aircraft Industry?
Listed below are some examples of parts that can be manufactured by 3D printing for the aircraft industry:
1. Engine Components
The materials used for engine components must withstand high mechanical and thermal stresses. Parts like fuel nozzles can be made by 3D printing processes like EBM (electron beam melting) and DED (direct energy deposition). Not only is the production of nozzles using these processes more efficient, but the nozzles themselves are lighter than those made by traditional manufacturing methods. This offers significant positive benefits related to aircraft performance and environmental impact.
2. Structural Components
Structural components are interior and exterior components that help form and support the rigid body of an aircraft. Structural components like brackets and wishbones can be made by 3D printing processes like EBM and DED using titanium and titanium alloys, copper, and nickel alloys.
3. Maintenance and Repair
Maintenance and repair are routinely conducted on aircraft to ensure their safe use and long life. 3D printing methods like EBM and DED can be used to fabricate jigs, fixtures, and tools needed to conduct maintenance and repair on aircraft out of titanium, stainless steel, and copper, among other metals.
4. Interior Components
Interior components in aircraft include everything from avionics equipment to cabin accessories like door latches and light fixtures. SLA (stereolithography) and SLS (selective laser sintering) are two popular methods of 3D printing commonly used to fabricate interior components for aircraft.
5. Prototyping and Tooling
Prototyping and tooling refer to the processes related to designing and testing new design concepts and developing the related tooling. 3D printing is great for creating prototypes and tooling for the aerospace industry due to its ability to make complex parts on demand with little setup work required. This allows for rapid development and testing of new products like suspension wishbones and nozzle bezels.
What Are 3D Printed Aerospace Parts?
The following are mechanical aerospace parts that can all be made by 3D printing:
- Fuel nozzles
- Door latches
- Lighting fixtures
- Trim pieces
What Are the Advantages of 3D Printing Technology in the Aircraft Industry?
There are several advantages of 3D printing applications in the aircraft industry. They are described below:
- Reduced Weight: 3D printing can be used to replace metal parts with lighter plastic parts. Components produced by 3D printing will reduce the aircraft’s overall weight, which consequently reduces fuel consumption and improves the aircraft’s performance.
- Cost-Effectiveness: 3D-printed parts can be made in far fewer process steps than parts produced by traditional manufacturing processes. Additionally, the process is entirely automated. This helps reduce overall production costs and waste.
What Are the Disadvantages of 3D Printing Technology in the Aircraft Industry?
There are also several disadvantages of 3D printing in the aircraft industry . Some disadvantages are described below:
- Limited Materials Available: While many widely used plastics and metals are compatible with 3D printing, thousands of alloys and compounds are still incompatible. This fact limits the potential applications for which 3D printing can be used in the aerospace industry.
- Weak Part Structure: Some 3D printing methods, like FDM (fused deposition modeling) and SLS (selective laser sintering), produce parts with anisotropic properties (characteristics that differ depending on the direction of an applied load). This can be undesirable for certain load-bearing parts and limits the potential of various 3D printing applications for the aerospace industry.
Who Uses 3D Printing in the Aircraft Industry?
3D printing is used by R&D firms, aircraft manufacturers, and maintenance companies. 3D printing can be used for rapid prototyping of aerospace parts, and small-to-medium batch production of end-use aerospace components, jigs, fixtures, and tools for aircraft maintenance. For more information, see our guide on the Uses of 3D Printing in the Aircraft Industry .
What Applications for 3D Printing Technology in the Aviation Sector Might There Be in the Future?
3D printing is a process that continues to positively impact the aerospace industry. It is poised to reduce the negative environmental impact of the aerospace industry, bolster innovation within the industry, and improve both aircraft performance and manufacturing efficiency for years to come. 3D-printed wings and green aviation are just two examples of future 3D printing applications in aerospace.
This article presented 3D printing in aerospace, explained what it is, and discussed its various processes and classifications. To learn more about 3D printing in various industries, contact a Xometry representative .
Xometry provides a wide range of manufacturing capabilities, including 3D printing and other value-added services for all of your prototyping and production needs. Visit our website to learn more or to request a free, no-obligation quote .
Copyright and Trademark Notices
- Inconel® is a registered trademark of Special Metals Corporation.
The content appearing on this webpage is for informational purposes only. Xometry makes no representation or warranty of any kind, be it expressed or implied, as to the accuracy, completeness, or validity of the information. Any performance parameters, geometric tolerances, specific design features, quality and types of materials, or processes should not be inferred to represent what will be delivered by third-party suppliers or manufacturers through Xometry’s network. Buyers seeking quotes for parts are responsible for defining the specific requirements for those parts. Please refer to our terms and conditions for more information.
Airbus Gets on Board with 3D Printing

When it comes to retrofitting aircraft, time is of the essence. But when newly designed elements in the cabin need to be integrated with existing components, spacer panels like those at the end of overhead compartments sometimes have to be adapted or redesigned. With tight retrofit timeframes to meet, Airbus was looking for a quick and smart solution to produce panels in small batches. Materialise’s aerospace manufacturing facility, with tailored post-production processes, provided the ideal solution.
The challenge
Produce small-batch custom parts to meet tight timeframes and quality requirements
When an airline updates the layout of its cabins, there are often gaps between the existing and new components. These need to be bridged with custom panels to create an attractive, seamlessly finished interior. With the clock ticking until the aircraft can be back in the skies generating revenue, finding a smart way to produce the new parts — which are typically needed in very limited quantities — is of the utmost importance.
Traditionally, new plastic parts are manufactured using custom-made injection molds. This process is relatively complex, especially as many of the components are highly specialized. With slow lead times and a high cost per part — given the limited numbers of parts needed for a typical retrofit — Airbus was keen to find a faster, more cost-effective solution for the spacer panels located alongside the overhead storage compartments in their commercial aircraft.
But cost and lead times, however crucial, are not the only consideration when dealing with the aerospace industry in general and commercial aircraft cabins in particular. As well as having to meet stringent quality requirements to be considered flight-ready, they also have to meet exacting aesthetic standards — Airbus had integrated 3D-printed parts in their A350 XWB airliner in the past, but never in places where they would be visible to passengers. This was a chance to take 3D printing across the next frontier and into the aircraft cabin.
The solution
Manufacturing for aerospace with tailored post-production finishing
Directly producing the spacer panels using 3D printing brought many crucial benefits for Airbus, the most obvious of which was lead time. For small-batch series and customized parts, aerospace 3D printing offers a drastically faster time-to-market than conventional manufacturing, as prior tool production is not required.
“ We think of this project as a great example of how we can serve the aerospace industry. It demonstrates how Materialise provides an end-to-end process that goes beyond the 3D print. ”
— erik de zeeuw, aerospace market manager at materialise.
Design optimization was another welcome benefit. Whereas internal structures like lattices add complexity and cost with the traditional injection mold techniques, 3D printing software could handle this with ease, making it possible to realize lightweight bionic panels and optimize the mass of the components.

In terms of finish, Materialise’s post-production processes ensured the 3D-printed parts met Airbus’ strict aesthetic requirements — once produced, the panels were then painted to Airbus cabin requirements, all using flame-retardant Airbus-approved materials.
Erik De Zeeuw, Aerospace Market Manager at Materialise, summarizes by saying, “We think of this project as a great example of how we can serve the aerospace industry. It demonstrates how Materialise provides an end-to-end process that goes beyond the 3D print. It’s about the strict quality process and incorporating every detail of the requirements from design to finishing.”

The foundation lies in a carefully honed quality management system, the results of which are evidenced by the number of certifications the Materialise manufacturing facility holds: ISO 9001 for quality management, ISO 14001 for environmental management, and the two critical ones for the aerospace industry quality management: EN9100 and EASA part 21.G, the latter of which is a Production Organization Approval (POA) from the civil aviation authority.
Flight-ready, aesthetically perfect panels that are 15% lighter
Working hand in hand with Airbus, we produced the company’s first-ever cabin-ready 3D-printed parts. Combining additive manufacturing and our post-production processes, the panels passed all Airbus Cabin Trim and Finish checks. And thanks to the design optimizations made possible by 3D printing, the spacer panels achieve full bionic design certification — Airbus’ first cabin parts to do so and a successful result of the company’s ongoing efforts to optimize part weight. Compared with the original design, intended for conventional production methods, the 3D-printed panels are 15% lighter.
Close collaboration between Materialise and Airbus was key to the success of this project. As Erik points out, “Our goal at Materialise is to be a trusted and reliable additive manufacturing supplier to Airbus. We do this by innovating together in design and production processes with our software and AM know-how, but also by seamlessly integrating Airbus’ own way of working.”
With this project, additive manufacturing showcases the enormous benefits it can offer to airlines with an unrivaled combination of affordability, quality and aesthetics, and fast lead times.
This case study in a few words
Certified additive manufacturing
Fused deposition modeling
Faster lead times
Optimized design
How we helped
Your additive manufacturing partner across the entire aerospace supply chain.
You might also like
- Shopping Cart
The Transformative Capabilities of 3D Printing in Aerospace
Aerospace engineers use Fused Deposition Modeling (FDM) Technology for prototyping, tooling and manufacturing. FDM can be used to build jigs, fixtures, check gauges and end-use parts in this industry.
Stratasys also offers PolyJet 3D printing for more precise prototyping that includes rigid, rubberlike and clear materials.
Case Studies
- Boom Supersonic
- Lockheed Martin
- Rocket Crafters
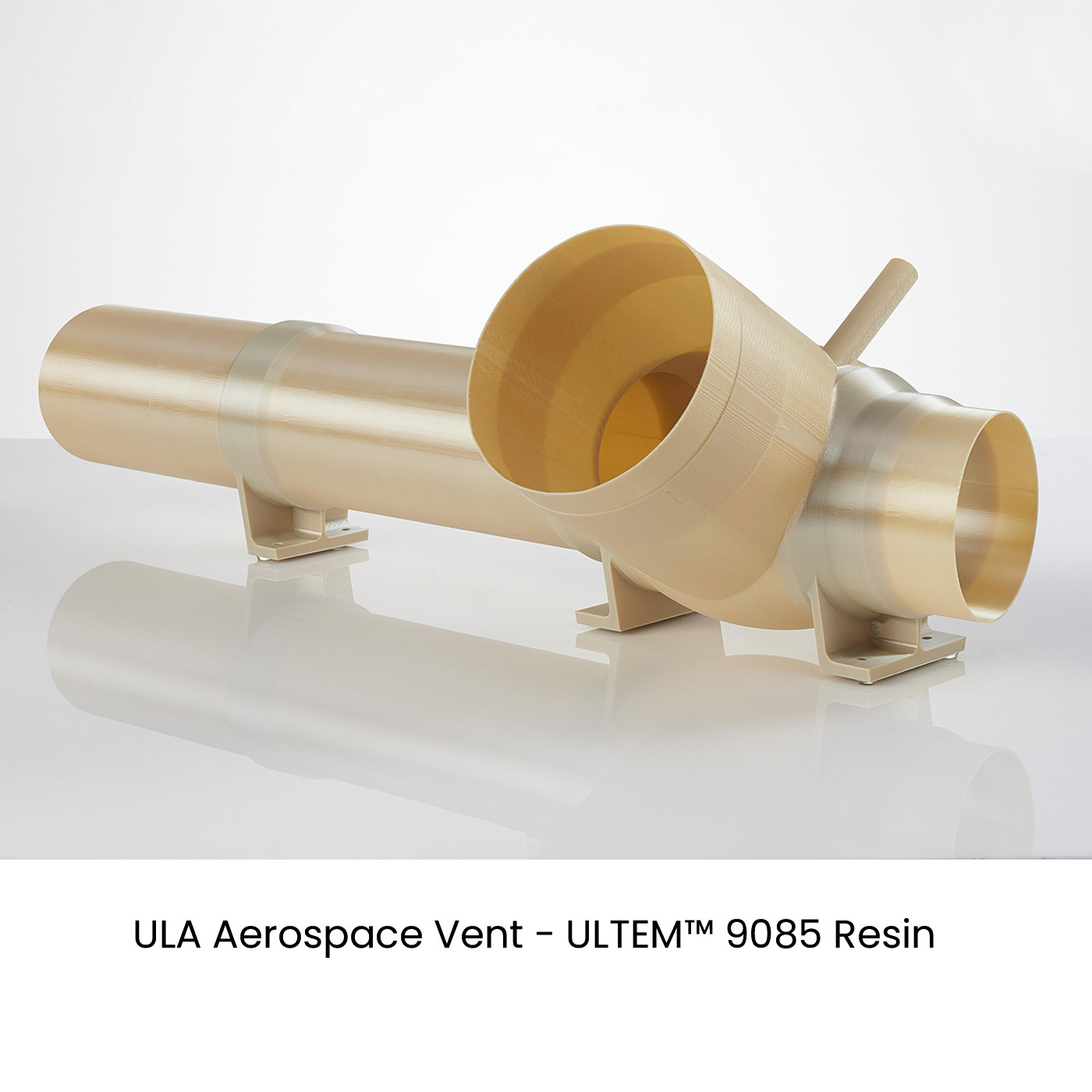
The aerospace industry has been at the forefront of embracing 3D printing and additive manufacturing, making it a trailblazer in the widespread use and application of these cutting-edge technologies. Due to its unique low-volume, high-mix production profile, aerospace is a very appropriate fit for additive manufacturing.
What sets Stratasys apart from other 3D printing providers is its comprehensive ecosystem of solutions, encompassing printers, materials, and contract part services. This all-encompassing approach allows Stratasys to cater to various prospects, even offering the option to experience additive manufacturing benefits through parts provided by Stratasys Direct Manufacturing.
Talk to a 3D printing expert

3D Printing in Aerospace Industry: Manufacturing Applications
Additive manufacturing finds extensive use in various aerospace applications, broadly categorized into three key stages of production:
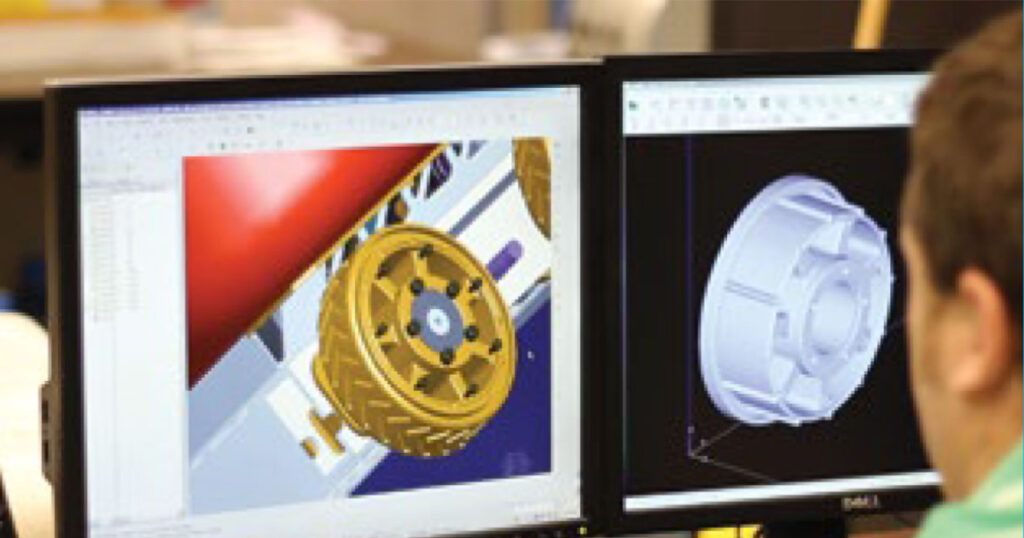
Engineering
3d printing for development and prototyping.
This phase involves the development of product concepts and prototypes using additive manufacturing in aerospace engineering.
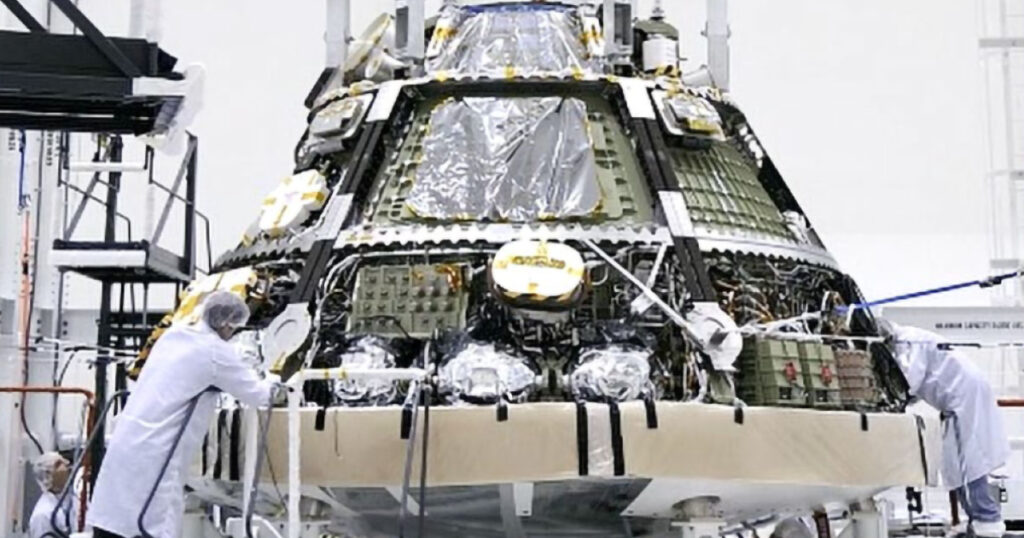
Additive Manufacturing for Aircraft Parts
Encompassing the process of manufacturing aircraft, sub-assemblies, and parts, including the use of diverse tooling and manufacturing aids.
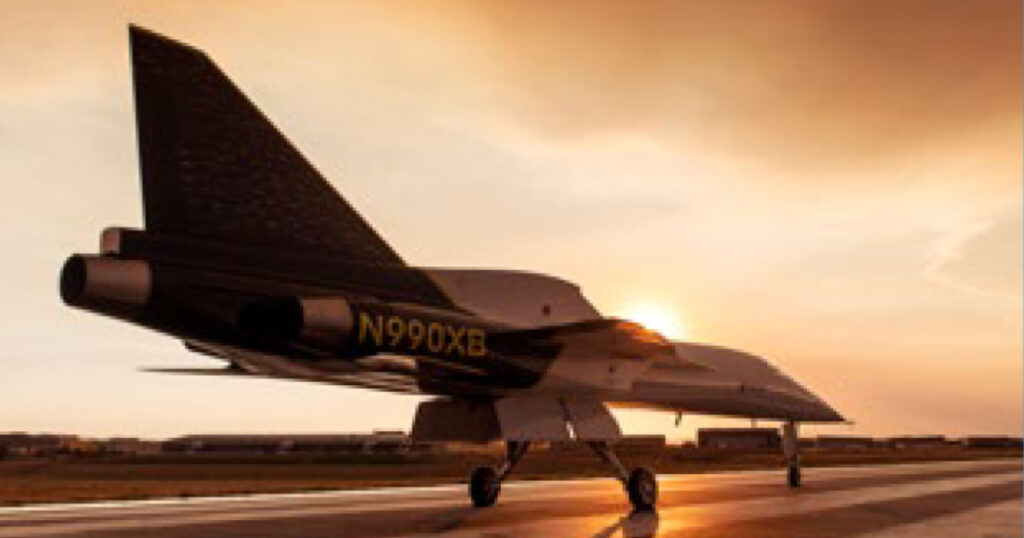
Flight Parts
The production of components for aerospace.
Focused on producing components that become integral parts of the aircraft, incorporating the advantages of 3D printing in the aerospace industry.
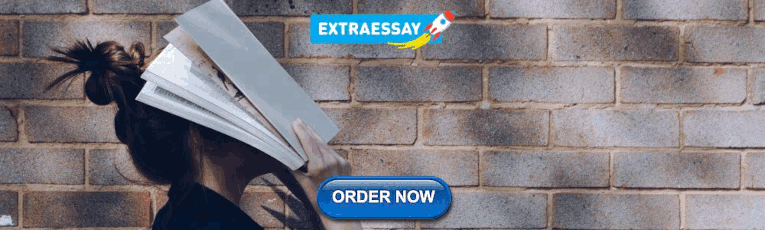
Benefits of 3D Printing in Aerospace
Additive manufacturing plays a pivotal role in addressing critical challenges faced by the aerospace industry, offering numerous advantages.

Sustainability and Energy Conservation
3D printing enables the production of lighter parts by utilizing lightweight materials, such as polymers instead of metals. Optimized design methods, like generative and topological approaches, further contribute to reducing overall weight, resulting in lower fuel consumption for flight vehicles.
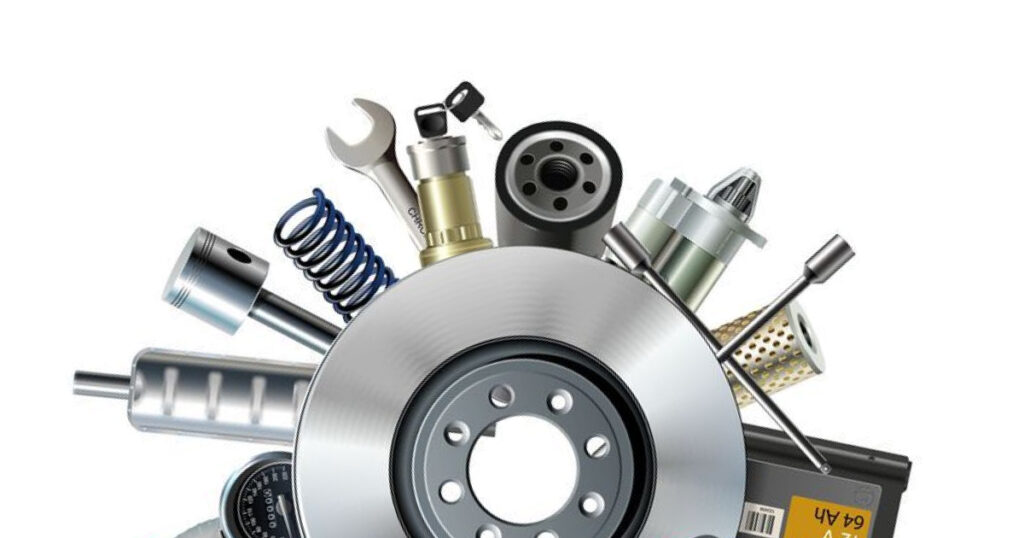
Spare Part Availability
Legacy aircraft programs, both in commercial and defense sectors, face increased costs as parts become obsolete and replacements are sought. Aerospace additive manufacturing services offer an efficient solution by enabling on-demand production of parts, eliminating the need for excessive inventory and addressing long-term use concerns.
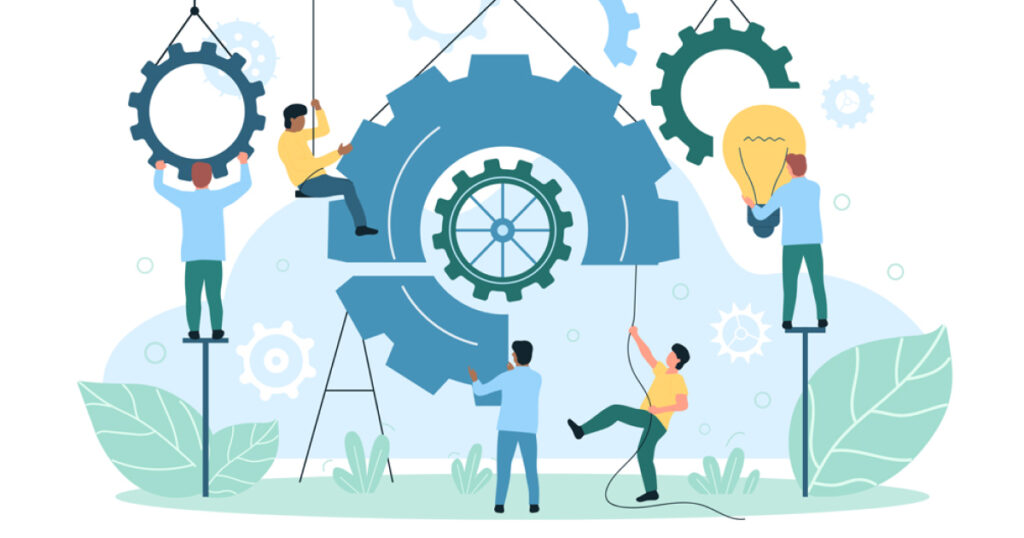
Speed of Innovation and Production
The aviation and defense industry has faced challenges in meeting projected timelines. The benefits of 3D printing in aerospace play a vital role in streamlining development programs, reducing cycle times, and accelerating time-to-market for new products.
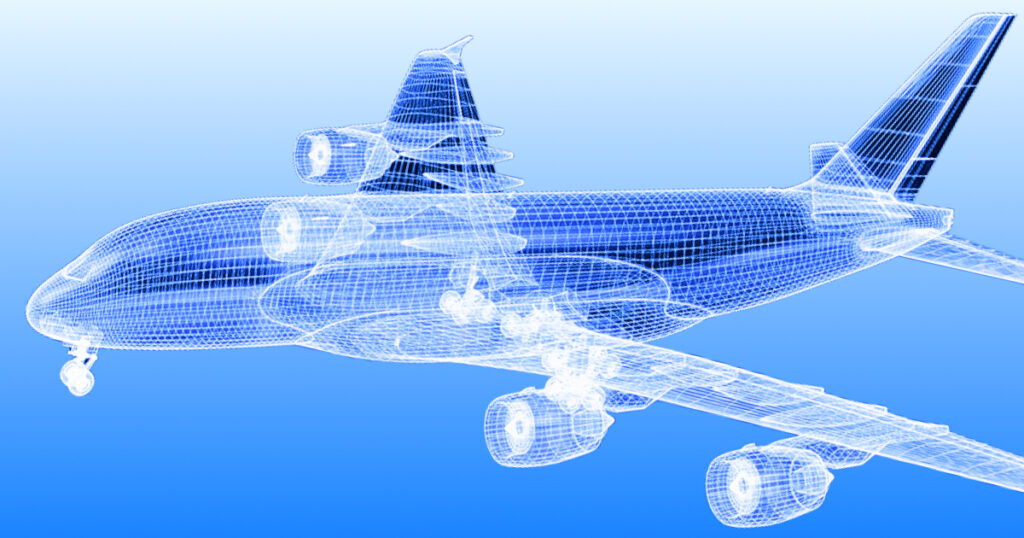
Durable and Lightweight Materials
Stratasys materials cater to a diverse range of aerospace application requirements. Engineering thermoplastics and carbon-filled materials address prototyping and strong tooling needs, while high-performance polymers like ULTEM™ resins meet rigorous physical and mechanical criteria for flight-worthy components. Antero 840CN03 fulfills specific low-outgassing and electrostatic dissipative requirements crucial for spacecraft.
Empowering Aerospace Manufacturing with Stratasys 3D Printers
Stratasys boasts a remarkable track record of manufacturing over 24 million parts in-house. The company is qualified to produce parts adhering to 26 Material Specifications and 46 Process Specifications, maintaining ISO9001 and AS9100 compliance for stringent quality control. Stratasys continues to lead the way in additive manufacturing innovations, making a lasting impact on the aerospace industry.
Subscribe to get the latest news and product updates from R&D
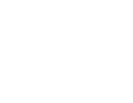
A TOP RESELLER OF
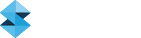
- Instant Quote
- 3D Printers & Systems
- 3D Printing Services & Consultation
- Shop Materials & Consumables
- Tech Support
- Material Specs & Docs
- About R&D
© 2023 R&D Technologies Inc. All rights reserved.

Ready to start your next project? Talk to our expert team today. Get on-demand production and rapid prototyping.
Interested in purchasing a 3D printer? We’ll help you find the perfect fit. Request a sales quote .
- 3D Printing Videos
- Company News
- Company Events
- Quoting Tool
- Material Specs and Docs
- 401-885-6400

Pioneering Advanced Manufacturing in High Volume: 3C Products Embrace Aerospace-Grade Titanium Alloy 3D Printing Technology

On July 12th, HONOR made a groundbreaking announcement at the HONOR Magic V2 and Full-scenario New Product Launch Event, introducing the HONOR Magic V2 as the first-ever 3C product to utilize cross-border aerospace processes and incorporate titanium 3D printing.
HONOR Magic V2, the new generation foldable screen smartphone, boasts a remarkable achievement in its design. Equipped with a 91% metal structure hinge, the device features a self-developed shielded strength steel upgrade. However, the true innovation lies in the adoption of aerospace-grade titanium alloy 3D printing technology. This groundbreaking use of titanium 3D printing allows the hinge to support an astonishing 400,000 folds.

The Luban Titanium Alloy Hinge, which was independently developed by HONOR, with several Chinese additive manufacturing companies, including HBD, also participating in the process. It is a key element of the HONOR Magic V2, plays a crucial role in achieving a remarkable thickness breakthrough of 9.90mm. By leveraging the advantages of titanium alloy technology, the axle cover within the hinge becomes lighter and thinner, resulting in reduced overall thickness and weight of the folding screen.
While electronic products typically rely on stainless steel or aluminum alloy for their metal structural components, these materials have their limitations. Stainless steel offers good gloss but lacks a weight advantage, while aluminum alloy is lightweight but compromises on hardness. Titanium alloy, on the other hand, strikes the perfect balance, offering superior strength while weighing only half as much as stainless steel of the same volume. Despite its benefits, the higher production costs and traditional processing difficulties have limited its use in the 3C industry. However, the emergence of metal 3D printing technology has addressed these challenges, making titanium alloy materials more accessible. This breakthrough has already seen widespread adoption in aerospace, medical, and other fields. Its application in the 3C industry, exemplified by the HONOR Magic V2, signifies a significant step forward.

The integration of metal 3D printing technology in the HONOR Magic V2 not only capitalizes on the inherent benefits of titanium alloy, such as lightweight and increased strength, but also enables further weight reduction and improved product integration through optimized lightweight, integrated, and thin-walled structural designs.
The significance of this achievement extends beyond the HONOR Magic V2. Reports have surfaced indicating that the next generation Apple Watch Ultra will also incorporate titanium 3D printing, partially replacing traditional CNC milling technology. This transition highlights the industry’s recognition of the immense potential offered by 3D metal printing in terms of enhanced product design and functionality. The growing trend of integrating 3D metal printing in various 3C products emphasizes its increasing importance in the consumer electronics industry.

0.025mm and a wall thickness of 0.2mm, HBD ensures that its products meet the lightweight, integration, and fine structural requirements of 3C product metal parts. With a steadfast commitment to excellence and craftsmanship, HBD focuses on the development of metal 3D printing equipment and processes, driving the advancement of 3C electronic consumer products and promoting the mass production application of metal 3D printing technology in the consumer electronics field.

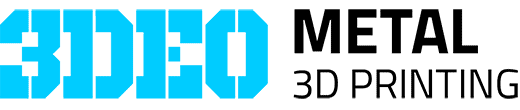
3DEO vs. Investment Casting in Aerospace
Intro to the problem.
As those who use investment cast parts in their products for the aerospace industry know, casting has always presented challenges: dimensional variation, post processing steps, non-destructive testing requirements, and uncertainty in material properties. For many, the final straw was the recent supply chain crisis that brought casting-centric production lines to a halt.
When it comes to casting, the selection of high quality domestic providers is shrinking as experts with relevant expertise retire. Meanwhile, overseas supply chains continue to struggle, and are forecast to be slower and more fragile for the foreseeable future, given the ongoing pandemic and geopolitical concerns. This is forcing many in the aerospace industry to take steps to address the uncertainty and significant delays they’re experiencing with cast parts: it’s making it difficult to keep promises to customers.
Even when parts are delivered on time, the value is just not as compelling as it used to be due to rising adjacent costs. When considering the total cost of the manufacturing process— including aforementioned required secondary operations, carrying costs and delays from overseas suppliers, NDT fallout due to poor quality, necessary rework, and line downtime—then casting is not the great deal the piece price quote alone would lead you to believe. Poor quality poses downstream uncertainty and reputational risk for your company, and many are finding that cast parts end up costing much more than they bargained (and budgeted) for.
Throughout the COVID-19 pandemic, 3DEO has heard from multiple customers about their intensifying challenges with investment casting, and we’ve learned a great deal about where we are uniquely able to help our customers. We’d like to highlight a few components we’ve begun producing hand-in-hand with our aerospace customers to get parts flying off their lines again.
NOTE: This case study is based on a US-based Tier 2 aerospace supplier’s success in migrating from a legacy investment cast supply chain to 3DEO’s metal 3D printing services.

The Challenge
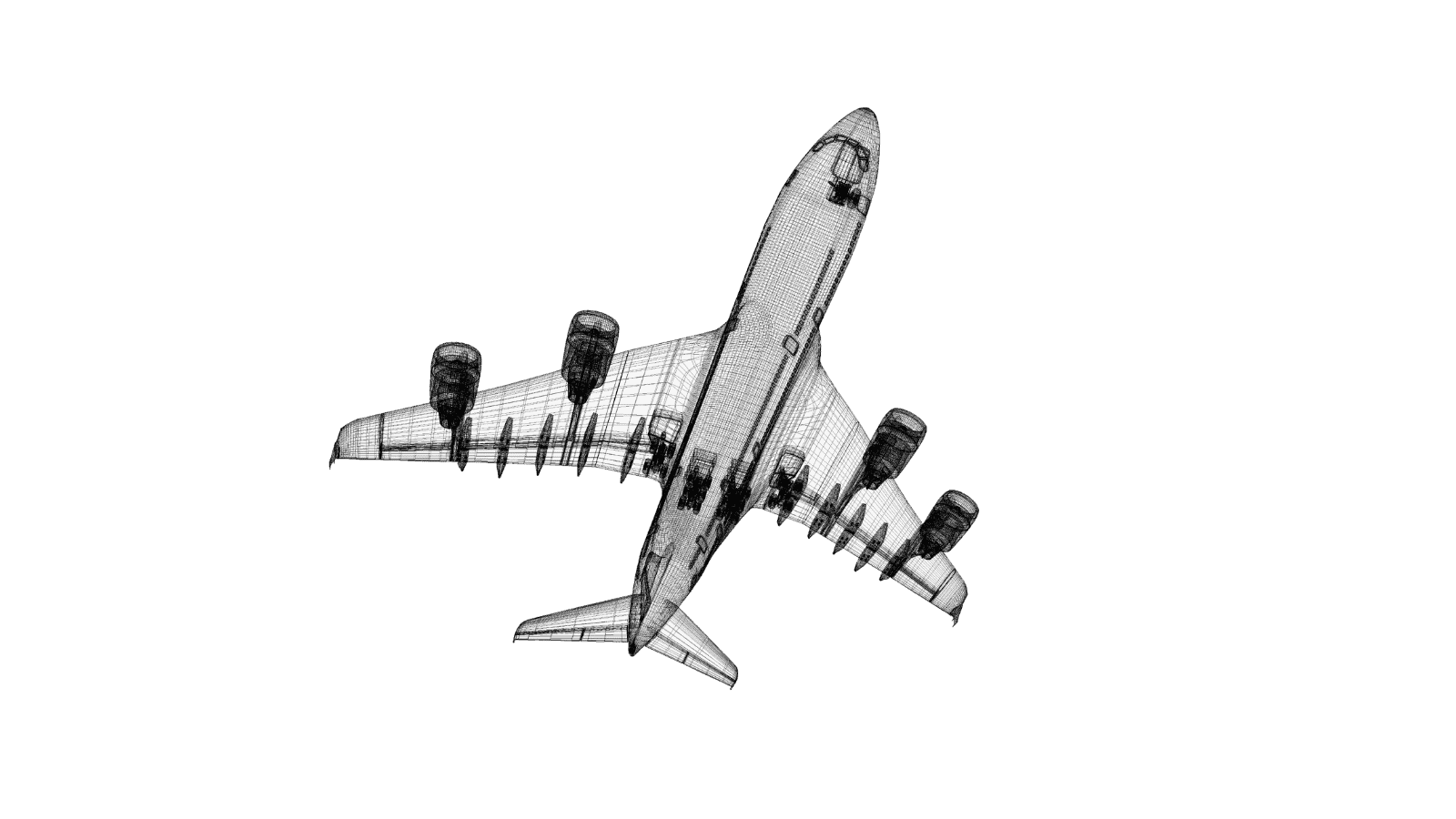
The challenges associated with this component are a combination of failings of the supply chain and fundamental limitations of the investment casting process.
Our customer, an aerospace tier 2 supplier, was unable to deliver subassemblies to their customer because their supplier was months behind schedule. The casting supplier saw this order as a relatively small proportion of their revenue for difficult-to-produce parts, and consequently had deprioritized them. The tier 2 supplier could not get commitments from their supplier to tighten delivery timelines, let alone ship parts.
Ultimately, the final customer, the aircraft manufacturer, was left in a challenging position sitting on over $12 million of incomplete product, awaiting subassemblies from the tier 2 supplier.
In addition to suppliers missing delivery timelines, a systemic challenge for this aerospace company was the poor quality of the investment cast parts themselves. According to this customer, the cast parts they receive from their vendors struggle with porosity:
And, this problem is not predictable—until the parts are radiographically or ultrasonically inspected, there’s no way to ensure casting quality. Recently, this manufacturer received a shipment of castings which nearly ALL failed NDT inspection, requiring rework. It was a lucky close call that they could even rework the components, as they previously had a failed run in 2019 that had to be scrapped entirely.
” We sectioned the samples you’ve provided and reviewed them side-by-side with the cast version of the same part; the castings look like swiss cheese by comparison. Engineering manager, Aerospace customer
While it will take time to execute, as a result of all these headaches the Director of Engineering for the product group that we’ve been working with is actively working to migrate parts away from casting to more reliable & timely firms that are using technologies that produce higher performing, more predictable parts. They tapped 3DEO to be just such a supplier.
The Solution
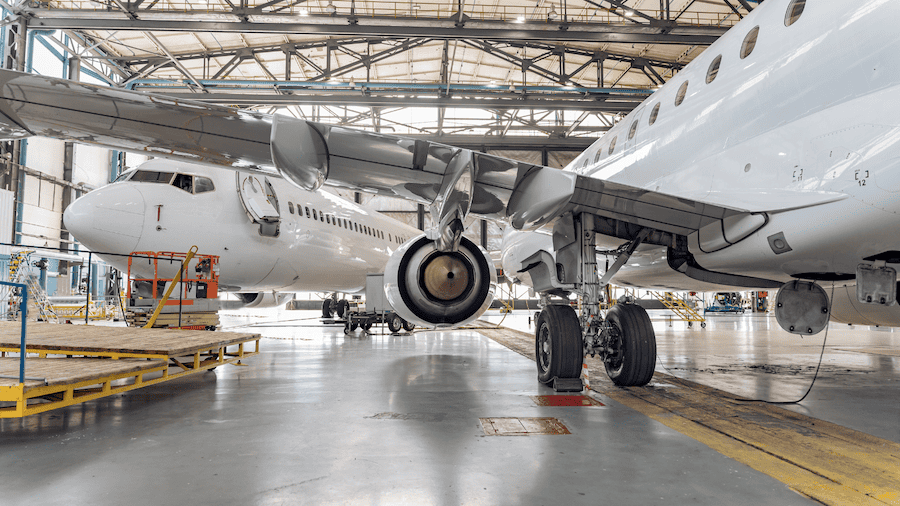
3DEO was able to help this customer solve its challenges with this part and get their subassemblies back in production—which was the beginning of a true partnership. This customer is leveraging 3DEO’s resources in a way that is creating long-term competitive advantage for the aerospace company, as they continue to bring additional components to be adapted from investment casting to additive manufacturing at scale. But what got the ball rolling?
To get started, 3DEO’s applications engineering team met with the customer’s engineering and procurement teams to fully understand the application in question and ensure 3DEO can deliver a working solution.
After reviewing the drawings and CAD designs, 3DEO immediately went to work on the first articles. Using its proprietary technology, 3DEO optimized the customer’s design for additive manufacturing in an effort to deliver a part closer to the final shape and eliminate post processing.
First articles were delivered in two weeks. One of 3DEO’s main advantages is that the sample parts are made on the same printers that produce production parts. As a result, any testing done on first articles remains valid for initial production runs. This dramatically accelerates launch cycles for new components.
Quality testing revealed that 3DEO’s material properties, dimensional tolerances, and surface finish were all superior to investment casting. Given the situation with the complete lack of parts from the investment casting supplier, the aerospace customer was able to seamlessly transition production to 3DEO.
” The 3DEO part surface finish looks great by comparison to the castings: no scratches, no pitting, and highly uniform. We regularly get castings that have to be reworked to meet customer aesthetic requirements. We have not rejected any parts yet that we’ve received from them. Engineer, Aerospace customer
Now, 3DEO is reviewing and qualifying other IC parts with this tier 2 supplier to help more of their product lines. A true manufacturing partnership is developing between the companies to ensure product is continually flowing with local manufacturing capability.
How 3DEO Added Value
- Supplied parts within two weeks when investment casting supplier was unable or unwilling to deliver parts
- Eliminated post processing due to tighter tolerances from 3DEO and reduced post machining of IC parts
- 3DEO’s high material density eliminated the “swiss cheese” associated with IC
- NDT fallout eliminated because they aren’t finding any parts with poor density – all parts delivered are usable by customer
Why customers choose 3DEO over Investment Casting
Flexible iterations (no mold to rework), quick turnaround to first parts, reliable delivery timelines, in-house design and engineering expertise.
3DEO is an award-winning design, engineering and manufacturing service firm specializing in complex metal 3D printed components produced in high volumes. 3DEO is driven by its commitment to help engineers to solve tough problems in novel ways that scale. For more on 3D metal printing aerospace read below:
We help companies at every stage of the product lifecycle from conceptual ideation to commercial production, through partnering with our customers on additive design manufacturing. And, our offering gives you parts that don’t just ‘look-like’ or ‘work-like’ the end part: 3DEO provides a unique production-ready additive platform where the first part is the real part.
A next-generation American manufacturing technology company, 3DEO is working with many aerospace companies today to replace MRO investment cast components. 3DEO strives to uphold high standards of quality in all that we do: we are ISO 9001 certified and currently certifying for AS9100.

3DEO accelerates customer innovation through its combination of unique additive manufacturing technology and professional services.
- Early-stage design for additive manufacturing
- Component functionality optimization
- Transition from prototyping to production
- Production at scale
- 3D metal printing aerospace
3DEO is an indirect supplier to:
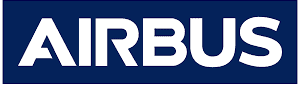
De-Risking the Supply Chain
Customer’s investment casting supply chain.
Long cycle times

3DEO’s Supply Chain
Short cycle times, first articles within weeks

- Quality Policy
- Request Sample Parts
- Request a Quote
- Intelligent Layering®
- Quality Production
- Press Releases
- Case Studies
- Technical Guides & White Papers
3D Printing Materials
- 17-4PH Stainless Steel
- 316L Stainless Steel
- Pure Copper
©2022 3DEO, All Rights Reserved | Terms & Conditions | Privacy Policy
- Technical Guides & White Papers

- Consumables for Composite Printers
- Spare parts for Composite Printers
- Consumables & Spares for Markforged Metal Printers
- Rent a 3D Printer
- Markforged FX10 New
- Markforged FX20
- Metal X System
In-field additive manufacturing solutions

- X7 Field Edition

- Digital Source
- The EIGER Fleet
- EIGER Simulation New
- EIGER Inspection
- EIGER Software Offline
- Test EIGER now
- Support Centre
Discover the materials used in Markforged 3D printers for high-strength components for industrial applications.
- Precise PLA
- Smooth TPU 95A
- ULTEM™ 9085 Filament
- Nylon White
- Carbon-Fibre
- HSHT-Fiberglass
- 17-4 Stainless Steel
- A2 Tool Steel
- D2 Tool Steel
- H13 Tool Steel
- Inconel 625

Order Markforged Filaments, Consumables, Spare Parts & 3D Printers online
- Applications
- 3D Print Stronger than Aluminium
- Why you need a 3D printer
- Composites Design Guide
- Webinars and Customer Talks
- Introduction to 3D Printing
- Guides for Metal 3D Printing
- Guides for Plastic 3D Printing
- Tips and Tricks
- Markforged University
- Guide to AM on the Production-Line
- The Economics of 3D Printing
Composite Design Guide
3d printing vs. cnc machining.
- View all Guides
- Get in touch
- Your contacts
- Fairs and Events
- Company – Mark3D UK
- Careers at Mark3D UK
- REQUEST A SAMPLE PART
ISS Aerospace Manufacture Resiliently with Markforged and Mark3D

The Company in Focus: ISS Aerospace
ISS Aerospace was established in the UK in 2015 to build on a decade of experience with professional UAV platforms by the company‘s founder, Ryan Kempley. Since that time they have designed, built and operated UAS systems for missions all over the world, achieving numerous world firsts.
The company provides a range of services including commercial and military off-the-shelf UAVs, custom design and engineering, training, and technical support. Their experienced team of engineers and technicians work closely with clients to understand their specific requirements, and to develop UAV solutions that meet their needs.
ISS Aerospace has a strong focus on research and development, continuously improving its products and services to remain at the forefront of the UAV industry.
At a glance:
- Weeks long lead times reduced to hours
Resilience to supply chain disruption
Outsourcing costs eliminated
Manufacturing costs significantly reduced
Robust, quality components
Rapid iterative development
Comprehensive support from Mark3D
Download the full Case Study to discover how ISS Aerospace achieved all of the above!
Fill out our secure form to download the case study PDF.
- Company name *
- Your Name * First Last
- Address * ZIP / Postal Code
- I´ve read the privacy policy and accept it.
- Name This field is for validation purposes and should be left unchanged.
Leading aerospace companies are protecting themselves from supply chain instability using Markforged industrial 3D printers.

The ISS Aerospace Markforged 3D Printer Farm In Action
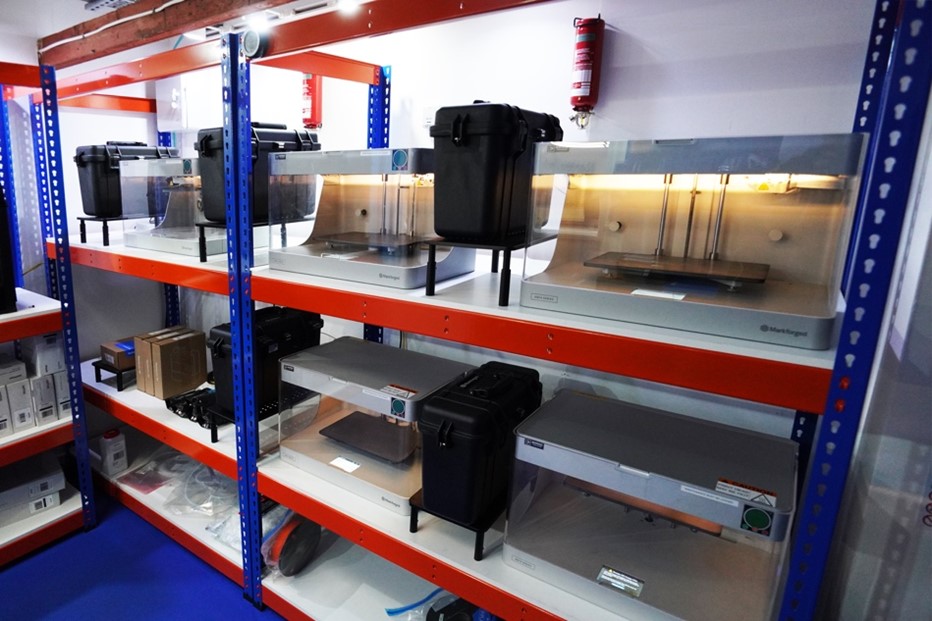
Learn more about 3D printing continuous fibres!
Which continuous fibre is suitable for which applications? How do I design correctly for filament 3D printing? What do users say and where can I find more information? – This is the right place for you! The guides below can tell you everything you need to know.

DfAM – How do you design your part best for 3D printing with composites? In this guide you will get valuable tips for design and material selection.

3D printing in production
This free guide serves as a source of information for engineers and contractors who want to integrate a 3D printer into their manufacturing process.

Primetall Case Study
In this practical case study from Primetall, 3D printing was used to print custom fixtures. It was practically “drilled around the corner”.

The two production technologies each have various benefits and drawbacks, and this article identifys the applications which best benefit from one or the other.
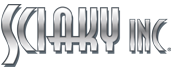
- Arc Welding
- News & Events
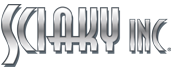
- What is EBAM?
- EBAM Systems
- Contract EBAM Services
- Applications & Industries
- Closed Loop Control
- Wire vs. Powder Metal 3D Printing
- Directed Energy Deposition
- Customer Service & Training
- Electron Beam Welders
- Large Chamber Systems
- Medium Chamber Systems
- Small Chamber Systems
- Internal & External EB Gun Options
- In-Stock Systems
- EB Welding Services
- Retrofits & Upgrades
- Spare Parts
- Electron Beam Welding
- Metal 3D Printing
- EBAM Customer Service & Training
- EB Welding Customer Support
- Sciaky Arc Welders
- Resistance Welders (Spot/Seam)
- Press Releases
- Certificates & NAICS Codes
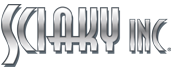
- EBAM Technology
Electron Beam Additive Manufacturing (EBAM ® )
- Aerospace Case Study Lockheed Martin
- 1+877-450-2518
- Get a quote
Lockheed Martin Space Systems Advances Development of 3D-Printing for Critical Parts with EBAM ®
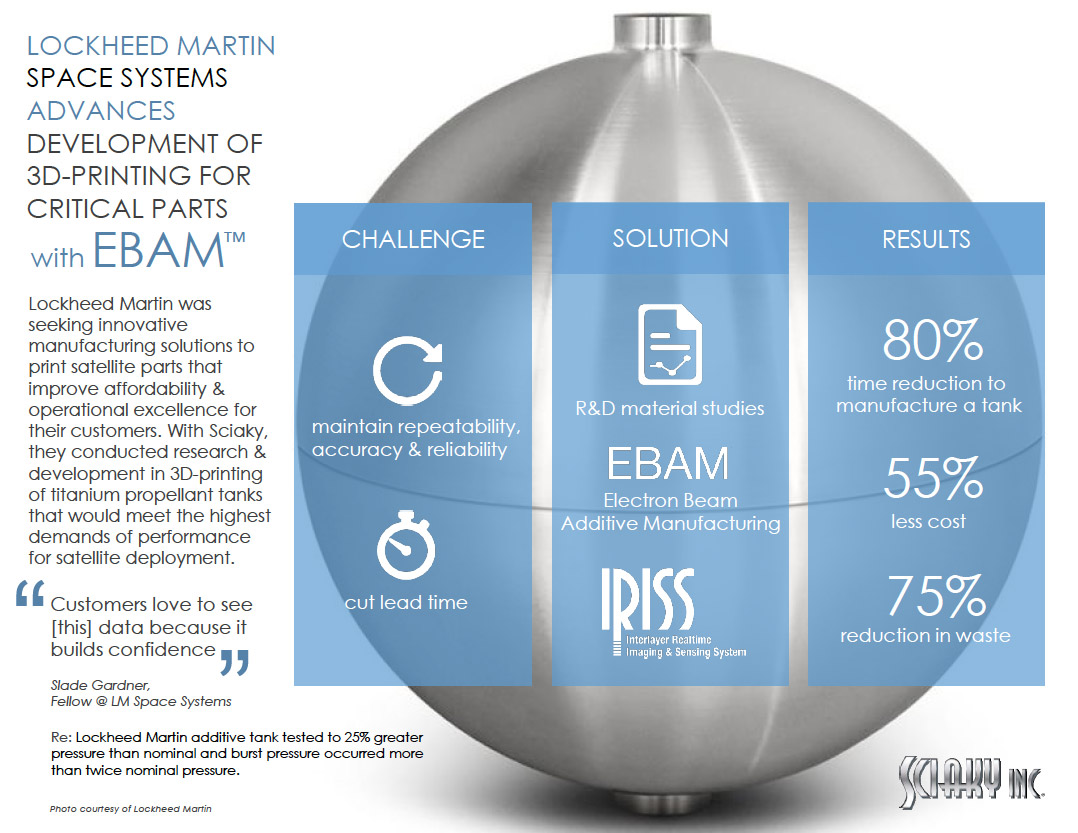
Click Here to Download this Infographic
Lockheed Martin was seeking innovative manufacturing solutions to print satellite parts that improve affordability and operational excellence for their customers.
With Sciaky, they conducted research and development in 3D-printing of titanium propellant tanks that would meet the highest demands of performance for satellite deployment.
"Customers love to see [this] data because it builds confidence" - Slade Gardner, Fellow @ LM Space Systems
Re: Lockheed Martin additive tank tested to 25% greater pressure than nominal and burst pressure occurred more than twice nominal pressure.
Click for more info or call Sciaky now: 1+877-450-2518
Latest News:
- Sciaky, Inc. Announces the EBAM- 53 Machine for Laboratory and Research Facilities
Affiliations:
- AmericaMakes
- Association of the US Army
- The American Welding Institute
- Center for Innovative Materials
- Additive Manufacturing Users Group
- The Alliance for the Development of Additive Processing Technologies
- National Defense Industrial Assoc.
- The Welding Institute Ltd.
- Michigan Aerospace Manufacturers Association
- International Titanium Association
Made in America. Deployed Globally.
Sciaky is based in Chicago, IL, USA. Its welding systems and EBAM ® industrial 3d printing machines are distributed internationally and found in manufacturing plants and advanced research and development facilities around the world. Contact a sales rep in your area by clicking here .
- United States
- United Kingdom
- Switzerland
- South Korea
- About Sciaky
- Media Coverage
Sciaky Global Headquarters Sciaky, Inc. 4915 W 67th St. Chicago, IL 60638
Phone: +1-877-450-2518 Fax: +1-708-594-9213
A Phillips Service Industries Company
FIND A SALES REP

Click or call Sciaky now: +1-877-450-2518
- Privacy Policy
Select your language
3D Printing in Aerospace and Defense – Thematic Intelligence

All the vital news, analysis, and commentary curated by our industry experts.

Published: January 17, 2024 Report Code: GDDEF-TR-S089-TH
- Share on Twitter
- Share on LinkedIn
- Share on Facebook
- Share on Threads
- Share via Email
- Report Overview
- Key Players
Table of Contents
3d printing in aerospace and defense thematic report overview.
The 3D printing industry has made its mark on the manufacturing world and become an essential part of the defense industrial supply chain. The software segment of the industry will deliver the fastest growth as companies prioritize adopting workflow automation tools. This is because automation enables companies to reduce the time and cost of the production cycle, facilitating 3D printing’s transition into mass manufacturing. This growth reflects the potential and hope encapsulated in this technology.
The 3D Printing in Aerospace and Defense thematic intelligence report gives you an in-depth insight into the 3D printing market and the impact it will have on the aerospace and defense industry. It further entails a deep-dive analysis of the industry, including real-life use case studies that showcase the impact of 3D printing on aerospace and defense. The report identifies the key market trends that will shape 3D printing over the coming years and gives an insight into the market players and the competitive landscape within the theme.
3D Printing in Aerospace and Defense – Key Trends
The primary trends that will shape the 3D printing theme over the next 12 to 24 months are classified into technology trends, macroeconomic trends, and regulatory trends.
- Technology trends: The key technology trends impacting the 3D printing theme are the increased use of binder jetting technologies, increasing speed of 3D printing machines, software developments, adoption of workflow automation, and traceability and repeatability, among others.
- Macroeconomic trends: ESG adoption, a spike in M&A activity, 3D printing of tools and spare parts for specific repairs, and education of current and future engineers regarding the value of 3D printing are a few of the key macroeconomic trends expected to drive the market.
- Regulatory trends: Standardization for 3D printing, use of encryption for safeguarding intellectual property, and tackling questions about product liability are part of the regulatory trends impacting the 3D printing market.
3D Printing in Aerospace and Defense – Industry Analysis
3D printing became popular during the COVID-19 pandemic for providing replacement parts and alleviating supply chain disruption. However, the slow post-COVID-19 recovery, coupled with the economic shock of the Russia-Ukraine war, has been challenging for the 3D printing industry to navigate through. The macroeconomic and environmental forces shaping the manufacturing landscape will have just as significant an impact on the 3D printing industry’s growth as technological advances.
The 3D Printing in Aerospace and Defense industry analysis also covers:
3D Printing Market, 2019-2030

Buy the Full Report for More Insights into 3D Printing in Aerospace and Defense Market
Download a Free Report Sample
3D Printing in Aerospace and Defense - Value Chain Analysis
The 3D printing value chain consists of hardware, materials, software, and services.
Hardware: The hardware value chain can be further segmented into metal printers, polymer and ceramic printers, bioprinters, and post-processing machines. Metal printing will be an area of keen interest in the industry over the coming years. In 2022, the launch of new machines, notably by HP, and significant M&A activity by Desktop Metal and Markforged led to growing competition. The polymers, ceramics, and bioprinting sectors are equally competitive as well. In addition, post-processing, which occurs at the end of the 3D printing process, has become increasingly significant. A rising number of organizations consider 3D printing as an industrial-grade manufacturing alternative with accompanying industrial volumes.
3D Printing Value Chain Analysis

Buy the Full Report for More Insights into the 3D Printing Value Chain
Leading Aerospace and Defense Companies
A few leading aerospace and defense companies making their mark within the 3D printing theme are:
- AI Space Factory
- ArianeGroup
Leading Public Companies
The leading listed players associated with the 3D printing theme are:
Leading Private Companies
The leading private companies associated with the 3D printing theme are:
Buy the Full Report to Know More about the Leading Aerospace and Defense, Public, and Private Companies in the 3D Printing Theme
3D Sector Scorecard
At GlobalData, we use a scorecard approach to predict tomorrow’s leading companies within each sector. Our power sector scorecard has three screens: A thematic screen, a valuation screen, and a risk screen.
- The thematic screen ranks companies based on overall leadership in the 10 themes that matter most to their industry, generating a leading indicator of future performance.
- The valuation screen ranks our universe of companies within a sector based on selected valuation metrics.
- The risk screen ranks companies within a particular sector based on overall investment risk.
3D Sector Scorecard – Thematic Screen

Buy the Full Report to Know More about the 3D Sector Scorecards
• Highlights from the range of different sustainability programs currently being undertaken by various defense and aerospace companies.
Key Highlights
- Scientific overview of 3D printing
- Studies of emerging technological trends and their broader impact on the market.
- Analysis of the various military and civilian hypersonic technologies programs currently under development, their history, and projections on future development initiatives.
Reasons to Buy
- Determine potential investment companies based on trend analysis and market projections.
- Gaining an understanding of the market challenges and opportunities surrounding the 3D printing theme.
- Understand how spending on 3D printing will fit into the overall market and which spending areas are being prioritized.
- 1. Executive Summary
- 3.1. The seven types of 3D printing technology
- 3.2. The cost of 3D printing
- 4.1. Technology trends
- 4.2. Macroeconomic trends
- 4.3. Regulatory trends
- 4.4. Aerospace and defense trends
- 5.1. Market size and growth forecasts
- 5.2. Use cases
- 5.3. Timeline
- 6.1. M&A trends
- 6.2. Patent trends
- 6.3. Company filing trends
- 6.4. Hiring trends
- 6.5. Social media trends
- 7.1. Hardware
- 7.2. Materials
- 7.3. Software
- 7.4. Services
- 8.1. Aerospace and defense companies
- 8.2. Militaries
- 8.3. Public companies
- 8.4. Private companies
- 9.1. 3D sector scorecard
- 10. Glossary
- 11. Further Reading
- 12. Our Thematic Research Methodology
- 13. About GlobalData
- 14. Contact Us
Frequently asked questions
The key technology trends impacting the 3D printing theme are the increased use of binder jetting technologies, increasing speed of 3D printing machines, software developments, adoption of workflow automation, and traceability and repeatability, among others.
ESG adoption, a spike in M&A activity, 3D printing of tools and spare parts for specific repairs, and education of current and future engineers regarding the value of 3D printing are a few of the key macroeconomic trends expected to drive the market.
Standardization for 3D printing, the use of encryption for safeguarding intellectual property, and tackling questions about product liability are part of the regulatory trends impacting the 3D printing market.
The key components of the 3D printing value chain are hardware, materials, software, and services.

- Currency Conversion is for Indicative purpose only. All orders are processed in US Dollars only.
- USD - US Dollar
- AUD — Australian Dollar
- BRL — Brazilian Real
- CNY — Yuan Renminbi
- GBP — Pound Sterling
- INR — Indian Rupee
- JPY — Japanese Yen
- ZAR — South African Rand
- USD — US Dollar
- RUB — Russian Ruble
Can be used by individual purchaser only
Can be shared by unlimited users within one corporate location e.g. a regional office
Can be shared globally by unlimited users within the purchasing corporation e.g. all employees of a single company
Undecided about purchasing this report?
Get in touch to find out about multi-purchase discounts.
[email protected] Tel +44 20 7947 2745
Every customer’s requirement is unique. With over 220,000 construction projects tracked, we can create a tailored dataset for you based on the types of projects you are looking for. Please get in touch with your specific requirements and we can send you a quote.
Sample Report
3D Printing in Aerospace and Defense – Thematic Intelligence was curated by the best experts in the industry and we are confident about its unique quality. However, we want you to make the most beneficial decision for your business, so we offer free sample pages to help you:
- Assess the relevance of the report
- Evaluate the quality of the report
- Justify the cost
Download your copy of the sample report and make an informed decision about whether the full report will provide you with the insights and information you need.
Below is a sample report to understand what you are buying

“The GlobalData platform is our go-to tool for intelligence services. GlobalData provides an easy way to access comprehensive intelligence data around multiple sectors, which essentially makes it a one-for-all intelligence platform, for tendering and approaching customers.
GlobalData is very customer orientated, with a high degree of personalised services, which benefits everyday use. The highly detailed project intelligence and forecast reports can be utilised across multiple departments and workflow scopes, from operational to strategic level, and often support strategic decisions. GlobalData Analytics and visualisation solutions has contributed positively when preparing management presentations and strategic papers.”
“COVID-19 has caused significant interference to our business and the COVID-19 intelligence from GlobalData has helped us reach better decisions around strategy. These two highlights have helped enormously to understand the projections into the future concerning our business units, we also utilise the project database to source new projects for Liebherr-Werk to use as an additional source to pitch for new business.”
Your daily news has saved me a lot of time and keeps me up-to-date with what is happening in the market, I like that you almost always have a link to the source origin. We also use your market data in our Strategic Business Process to support our business decisions. By having everything in one place on the Intelligence Center it has saved me a lot of time versus looking on different sources, the alert function also helps with this.
Having used several other market research companies, I find that GlobalData manages to provide that ‘difficult-to-get’ market data that others can’t, as well as very diverse and complete consumer surveys.
Our experience with GlobalData has been very good, from the platform itself to the people. I find that the analysts and the account team have a high level of customer focus and responsiveness and therefore I can always rely on. The platform is more holistic than other providers. It is convenient and almost like a one stop shop. The pricing suite is highly competitive and value for our organisation.
I like reports that inform new segments such as the analysis on generation Z, millennials, the impact of COVID 19 to our banking customers and their new channel habits. Secondly the specialist insight on affluent sector significantly increases our understanding about this group of customers. The combination of those give us depth and breadth of the evolving market.
I’m in the business of answering and helping people make decisions so with the intelligence center I can do that, effectively and efficiently. I can share quickly key insights that answer and satisfy our country stakeholders by giving them many quality studies and primary research about competitive landscape beyond the outlook of our bank. It helps me be seen as an advisory partner and that makes a big difference. A big benefit of our subscription is that no one holds the whole data and because it allows so many people, so many different parts of our organisation have access, it enables all teams to have the same level of knowledge and decision support.
“I know that I can always rely on Globaldata’s work when I’m searching for the right consumer and market insights. I use Globaldata insights to understand the changing market & consumer landscape and help create better taste & wellbeing solutions for our customers in food, beverage and healthcare industries.
Globaldata has the right data and the reports are of very high quality compared to your competitors. Globaldata not only has overall market sizes & consumer insights on food & beverages but also provides insights at the ingredient & flavour level. That is key for B2B companies like Givaudan. This way we understand our customers’ business and also gain insight to our unique industry”
GlobalData provides a great range of information and reports on various sectors that is highly relevant, timely, easy to access and utilise. The reports and data dashboards help engagement with clients; they provide valuable industry and market insights that can enrich client conversations and can help in the shaping of value propositions. Moreover, using GlobalData products has helped increase my knowledge of the finance sector, the players within it, and the general threats and opportunities.
I find the consumer surveys that are carried out to be extremely beneficial and not something I have seen anywhere else. They provided an insightful view of why and which consumers take (or don’t) particular financial products. This can help shape conversations with clients to ensure they make the right strategic decisions for their business.
One of the challenges I have found is that data in the payments space is often piecemeal. With GD all of the data I need is in one place, but it also comes with additional market reports that provide useful extra context and information. Having the ability to set-up alerts on relevant movements in the industry, be it competitors or customers, and have them emailed directly to me, ensures I get early sight of industry activity and don’t have to search for news.
Related reports

Every Company Report we produce is powered by the GlobalData Intelligence Center.
Subscribing to our intelligence platform means you can monitor developments at 3D Printing in Aerospace and Defense – Thematic Intelligence in real time.
- Access a live 3D Printing in Aerospace and Defense – Thematic Intelligence dashboard for 12 months, with up-to-the-minute insights.
- Fuel your decision making with real-time deal coverage and media activity.
- Turn insights on financials, deals, products and pipelines into powerful agents of commercial advantage.
- Media Coverage
- Register your printer

- Powder sieve
- Atex vacum cleaner
- Sandblaster
- Sandblaster SLS
- Dedicated powder tools
- PA12 Smooth
- PA12 Industrial
- Flexa Black
- Flexa Bright
- Polipropylen (PP)
- PA11 Carbon Fiber
- Flexa Performance
- PBT Optimal
- HP Used (profile only)
As SLS 3D printing is getting more popular, we share our insights, tips, and tricks for you to use.
With a four-figure installation worldwide of Sinterit's 3D printers, here you can find some of our client's stories.
Grasp the basic knowledge about SLS. Your journey starts here.
Check the latest webinars about our products, SLS technology and more
Download special ebooks about SLS 3D printing technology
Get to know how much it costs if you decode to choose the Sinterit SLS 3D printing solutions
Check all technical details, FAQ
Case Studies
Our customers stories with the 3D printer in the background

Sinterit SLS 3D printing in SAE Aero Design
The SLS 3D printing technology from Sinterit was one of the components of the success that the SAE Aero Design Student Association from Warsaw University of Technology achieved in prestigious competitions in the United States.
Browse resources by industry
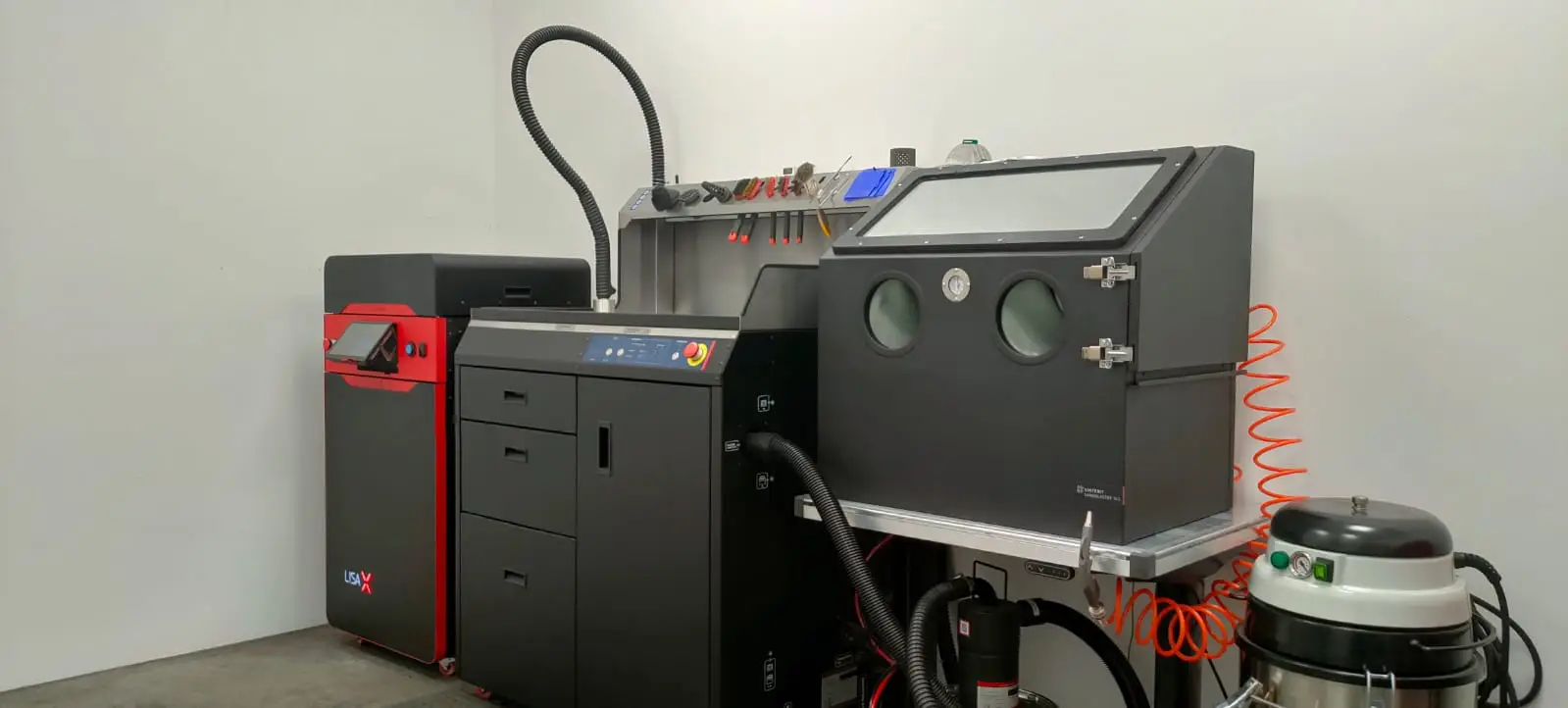
- Consumer Products
- Industrial Products

- Aerospace / Automotive / Traction
- Prototyping
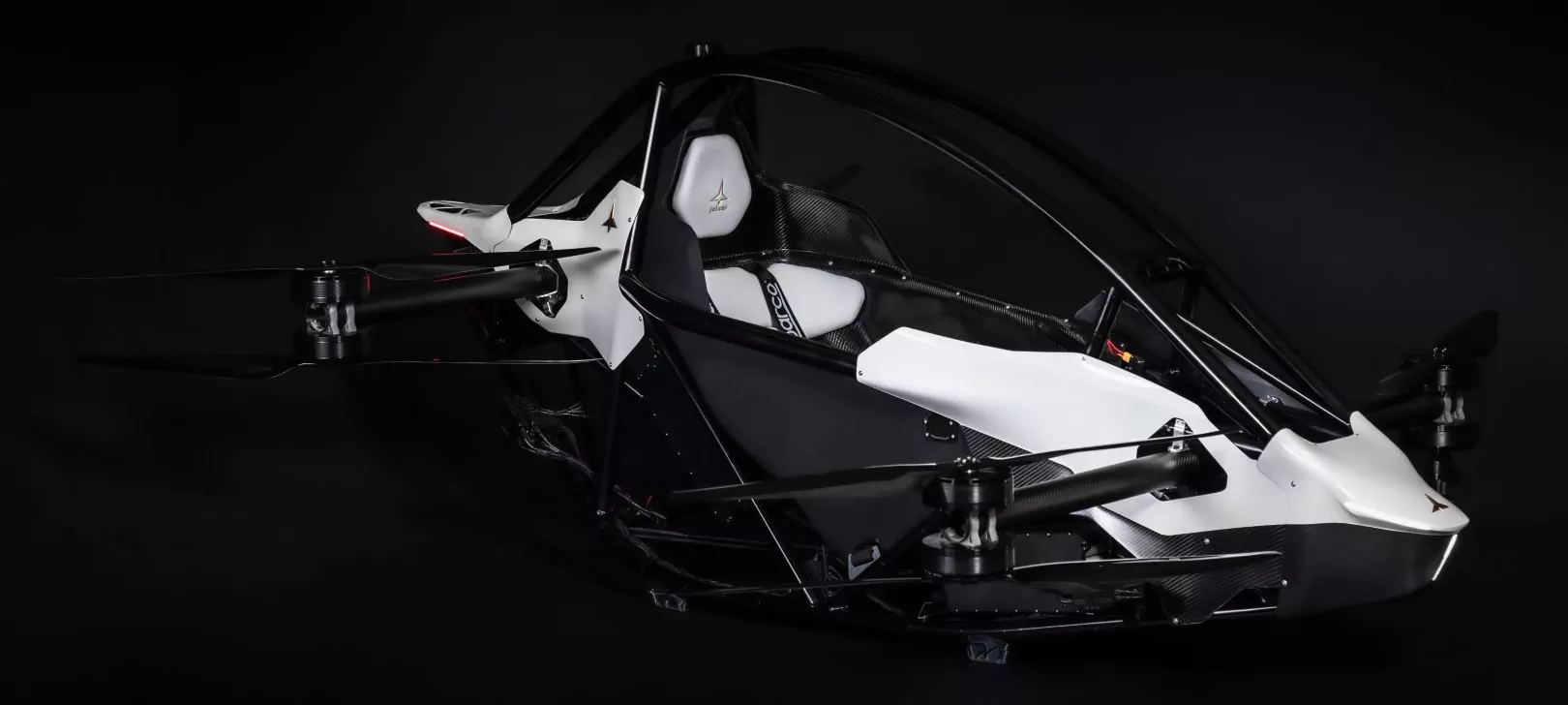
- Electronics
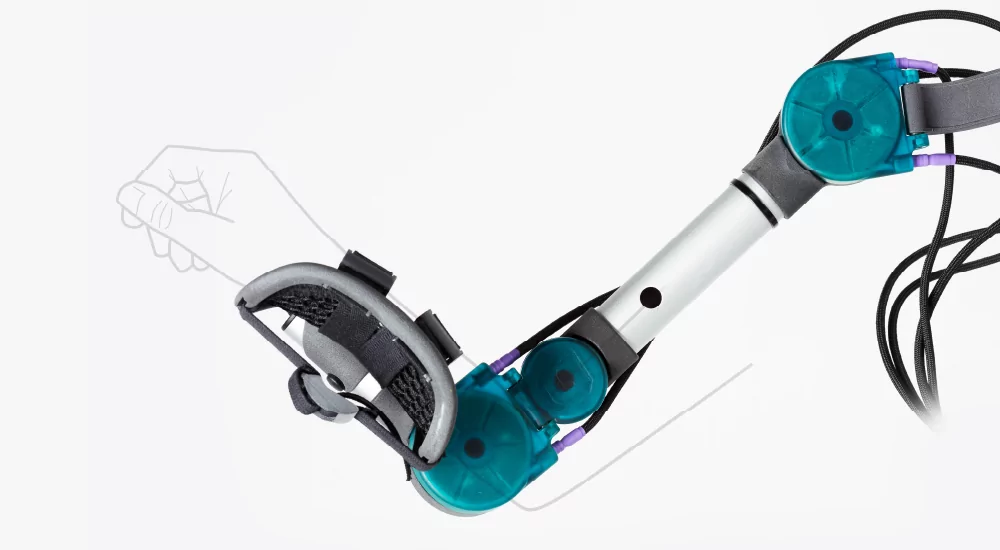
- End-Use Part
- Healthcare / Medical

- Government/Military

- Replacement parts

Maurice Briggs
Director at lazerthrust.
Sinterit LISA is the most accessible means to produce precise constraint-free solutions to modern problems. The technology does what it says on the tin and the team at Sinterit is dedicated to working with their customers to achieve their objectives.
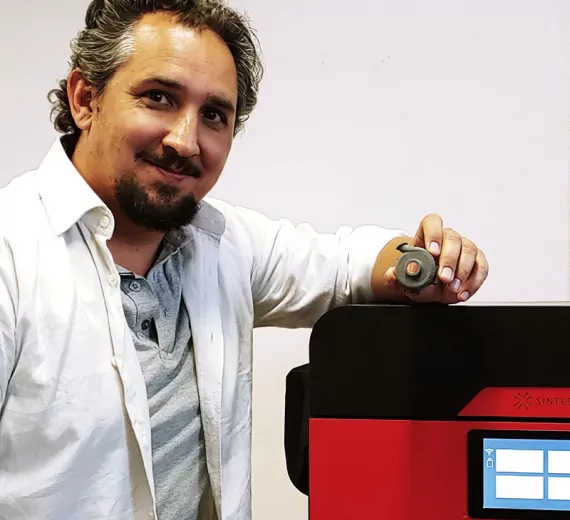
Joshua Rosen
Eca medical.
One of the main benefits of SLS is the ability to print complex geometry in quick succession to do rapid prototyping.
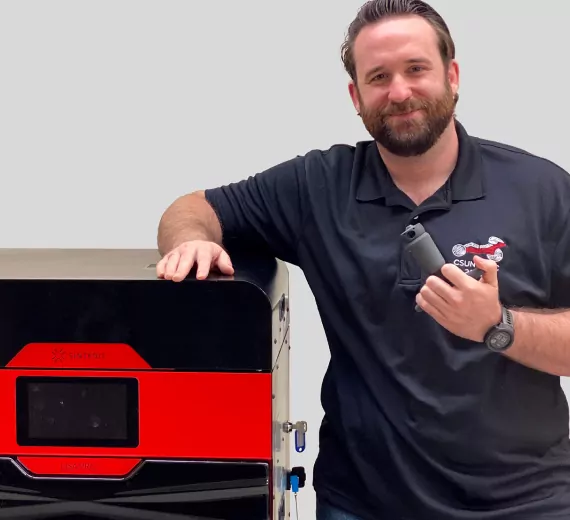
Lluís Llenas
The FFF and SLA parts are a good choice to get a physical impression of the designs and to assemble rough prototypes. But when it comes to producing reliable prototypes to be verified in our fatigue tests or to send functional samples to our customers for validation, SLS is the only acceptable choice.
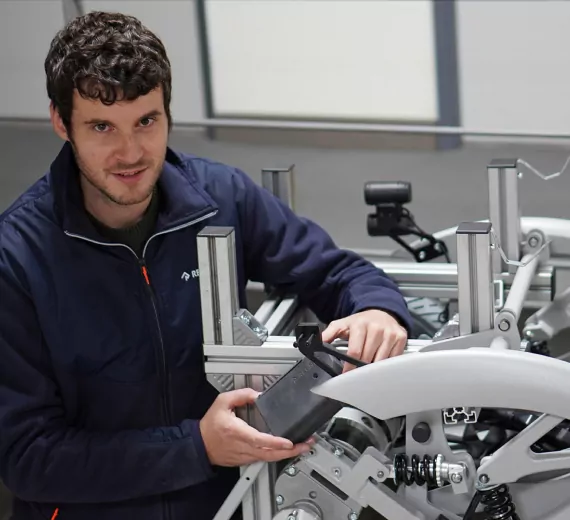
Sean Higgins
Nabson inc..
In order to keep up with our production demand, we have been operating the Lisa PRO almost 7 days a week for the past couple of months, without incident, and produced over 1500 sleeves.

Tell us, how we can help you with your project.

Get a free sample box
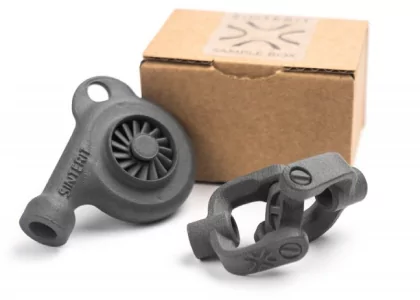
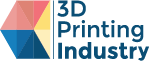
- Case Studies
- Medical & Dental
- Executive Interview Series
- Applications
- 3D Platforms
- Electronics
- Stock Market
- Entertainment
- Art & Sculpture
- 3DP Applications
- Construction
- Post Processing
- 3D Software
- Laser Cutters
- Consumer Products
- Legal and Regulatory
- Open source
- Uncategorized
- On demand manufacturing
- 3D Printing
- Market Insights
- Crowd Funding
- 3D Printers
- 3D Printing News Digest
- 3D Scanners
- Kickstarter, etc
Mantle 3D printers reduce tooling lead times by 50%, new customers announced
US-based metal 3D printer manufacturer Mantle has expanded the reach of its 3D printing technology, including the P-200 metal 3D printer, with three new customers. These new customers include Spectru…
Velo3D technology cuts lead-time of Upwing Energy’s gas-compressor module
US-based natural gas service provider Upwing Energy has leveraged technology from metal 3D printer manufacturer Velo3D to 3D print its Subsurface Compressor System (SCS) compressor module. By using Ve…
Evolve Additive Solutions launches program for 3D printing at high volume
Evolve Additive Solutions, a Minnesota-based 3D printer manufacturer, has launched a Production Assessment Program. “This is an exciting time in the growth of Evolve,” said Joe Allison, CE…
HP’s digital manufacturing offering ‘opening new markets’ to 3D printing service providers
Multinational printing firm HP has published a series of use cases that reflect how its 3D printers for manufacturing are increasingly ‘opening new markets’ to service bureaus. For those making …
3D printed marine parts validated after successful tests on-board Endeavour oil tanker
3D printing service provider 3D Metalforge has successfully tested three different 3D printed parts on board ConocoPhillips Polar Tankers’ Endeavour oil tanker. As part of a pioneering project, 3D Met…
Enel’s Geyser project deploys 3D printing for geothermal plant replacement parts
Subscribe to our YouTube channel for the latest 3D printing video shorts, reviews and webinar replays. Italian renewable energy company Enel Green Power has developed replacement technical c…
Customized production in the packaging industry with Stratasys 3D printing
Marchesini Group S.p.A., an Italian manufacturer of automated packaging machinery, has adopted an entirely customized production business model using Stratasys 3D printing technology. Located within …
3D printing used to protect bus drivers at Seattle Children’s Hospital
Californian rapid prototyping service provider GoProto and design and engineering specialist Function Foundry, have collaborated to help protect high-risk bus drivers at Seattle Children’s Hospital us…
Additive Manufacturer Green Trade Association commissions first research project
Global trade group Additive Manufacturer Green Trade Association (AMGTA) has announced a systematic review into the environmental sustainability of metal 3D printing. The organization’s first literary…
HİDROMEK reduces costs of machinery end-use parts with LOOP PRO 3D Printer
HİDROMEK, a manufacturer of construction machinery based in Turkey, is using the LOOP PRO 3D printer to produce end-use parts for its agricultural vehicles. Seeking to reduce its downtimes and avoid …
3D Printing News Briefs, June 16, 2022: Lawsuit, Software, & Aerospace Case Studies

Share this Article
First up in today’s 3D Printing News Briefs, we’ll share the latest update in the Continuous Composites lawsuit against Markforged. Next, nTopology has released an advanced lattice generation tool. Finally, on to aerospace news, as BigRep shared a case study about how its technology helped overcome COVID-19 supply chain challenges and Objectify Technologies shared one about redesigning a hydraulic block manifold for 3D printing.
Markforged Challenges Lawsuit by Continuous Composites

A composite part being 3D printed via Continuous Composites’ ‘CF3D’ technology. Image via Continuous Composites.
Last year, Continuous Composites sued Markforged , alleging that the metal and carbon fiber 3D printer manufacturer infringed upon patents that are related to its own Continuous Fiber 3D printing (CF3D). The case revolves around US patents ‘ 9,511,543 ,’ ‘ 9,987,798 ,’ ‘ 10,744,708 ,’ and ‘ 10,759,109 ,’ which Continuous Composites says are part of a larger family of patents, revolving around its core technology, from before Markforged was founded. This fall, Markforged filed a motion to dismiss the case, in which Continuous Composites is seeking financial compensation and an injunction preventing the Massachusetts company from violating the patents in the future.
Now, Markforged has called for the case to be thrown out , and barring this, has requested a trial by jury, stating that patent 9,511,543 covers “something different from the conventional slicing techniques,” and that the patent covers a 3D printing method that directs curable liquid material to a nozzle—but Continuous Composites doesn’t use this kind of material, so it’s not liable for patent infringement in this case. In addition, Markforged asked how it can infringe on the other three patents, because they all “fail to comply with one or more of the conditions for patentability.” So it seems like this case won’t be over anytime soon.
nTopology Releases Advanced Lattice Generation Tool
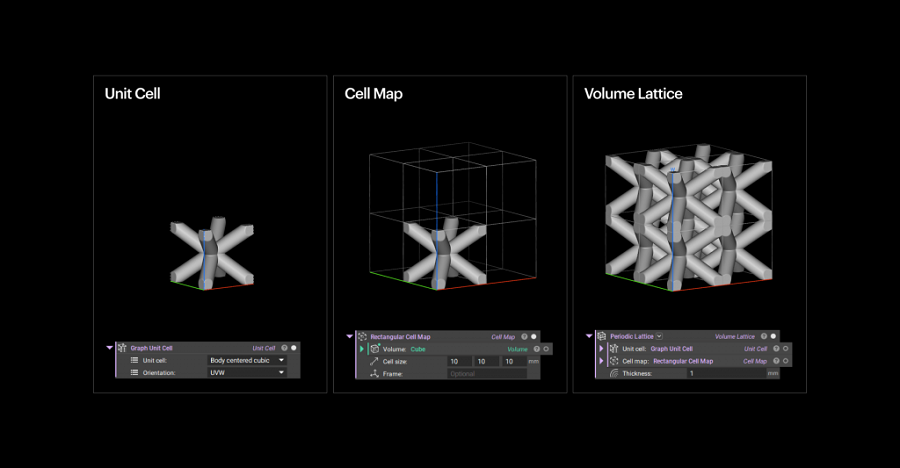
The new tools separate the lattice generation process into three fundamental components: unit cell, cell map, and lattice parameters.
Engineering software provider nTopology has announced the release of its 3rd generation lattice generation tool , which it says is faster and offers more control over complex lattice structures. The goal was to make it easier than ever for new nTop users to access the lattice tools, which is why the lattice generation process has been separated into three main steps: selecting a unit cell, defining the cell map, and controlling the parameters of the lattice. For existing users of the software, nTopology wanted to streamline the transition to its new latticing technology, which includes 37 blocks that have been in development for nearly two years; visit the updated Lattices tab to find three new blocks that will enable you to transition over your current workflows.
Some of the key features of this new release including super-fast lattice generation, and by super-fast, nTopology means a performance increase of 50% to the fastest lattice generation tools on the market. Users can also enjoy more control over creating lattices with new tools for streamlining design and optimization. These new tools include lattice warping, a unified latticing workflow, filter beam utilities, and the ability to create surface lattices, which enables the design of conformal rib grids to increase body stiffness in organic and complex shapes.
BigRep Overcame COVID Supply Chain Issues by 3D Printing Molds
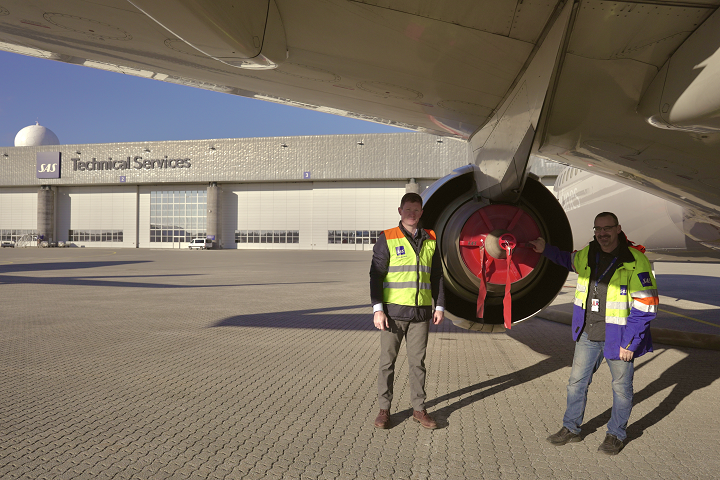
CNE’s Nathan Brown and Jason Deadman from SAS
During the height of the COVID-19 pandemic, 62% of passenger planes were grounded, which isn’t great for their engines, as they need to be protected from the elements when parked for a long period of time. Due to supply chain shortages, Scandinavian Airlines ( SAS ) didn’t have enough off-the-shelf engine covers and exhaust plugs on-site, and turned to CNE Engineering , a local specialized supplier that uses large-format 3D printers by BigRep , for help creating parts for aircraft maintenance . To 3D print molds for producing the castable urethane parts, CNE used the BigRep ONE, with its cubic meter build volume, for the main piece, and the BigRep STUDIO for smaller features like removable mold inserts. BigRep’s bio-based PLX was used to print the outer shells, while HI-TEMP CF was used for the center core and the inserts were printed using TPU. Large-format 3D printing helped CNE meet the SAS’s fast timing requirements during a time that traditional supply chains were unable to do so.
“This case study is a shining example of how BigRep’s large-format 3D printers are already changing the game in aerospace MRO,” said Peter Smeets, BigRep’s Chairman of the Board and Managing Director of 360 Aircraft Finance. “We believe this is only the beginning and that 3D printed solutions will become the gold standard for custom, cost-effective manufacturing free from traditional supply chain issues.”
You can read the full case study here .
Objectify Technologies Redesigned Aerospace Manifold for AM
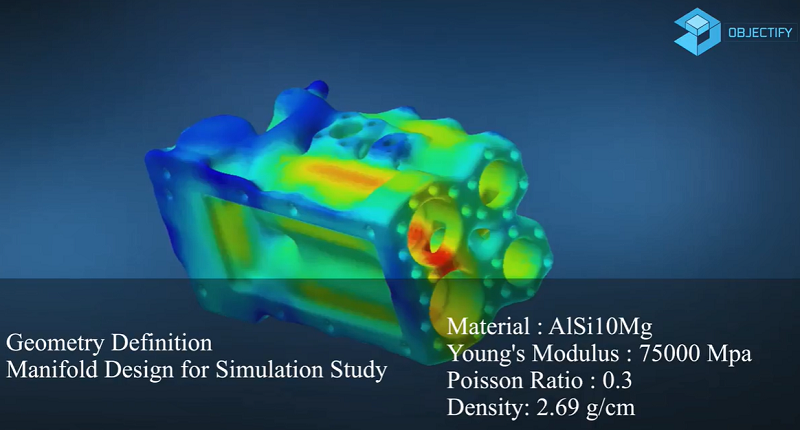
Finally, Objectify Technologies worked with an aerospace customer to redesign a hydraulic block manifold for 3D printing, as the technology enables the fabrication of internal features and passages. In the aerospace industry, this kind of manifold is used to regulate fluid flow, which helps control power transfer between actuators, pumps, and other components of a hydraulic system. Using traditional manufacturing to create these typically requires specialized tooling because of the necessary complex drilling, and unfortunately, it can often lead to abrupt, angled junctions forming between flow paths, which causes flow separation and even stagnation. Using 3D printing to create the hydraulic block manifold out of an aluminum alloy allowed Objectify to reduce the weight of the component, while maintaining its robustness, improving flow paths, and considering loading constraints.
In redesigning the manifold, Objectify used Rhino and MSC Apex to modify and optimize the design, Materialise Magics to prepare the data, and Simufact Additive to simulate the build. The company replaced unnecessary drill channels with simpler designs, which allowed critical areas to be modified and internal channels redesigned for 3D printing. The first design was printed and subjected to stress tests, and the final hydraulic block manifold had a 30% reduced weight, up to 60% improved flow efficiency, and was printed in one piece.
Subscribe to Our Email Newsletter
Stay up-to-date on all the latest news from the 3D printing industry and receive information and offers from third party vendors.
- Enter your email address *
- Email This field is for validation purposes and should be left unchanged.
Recent News
3D Printing Webinar and Event Roundup: June 2, 2024
3D Printing News Briefs, June 1, 2024: Sustainability, Cementitious Materials, & More
3D Printed Art
3D Printed Food
3D Printed Guns
You May Also Like
3d printing webinar and event roundup: may 26, 2024.
In the weekly 3D Printing Webinar and Event Roundup, ASTM’s AMCOE concludes its professional certificate course, while Solid Print3D will offer a masterclass on Form 4 materials. If you’re in...
Twente Additive Manufacturing: A Construction 3D Printer for Every Task
The additive construction (AC) sector is currently bustling, though not every bit of activity necessarily means it’s thriving. Startups in the space are in the process of getting off the...
3D Printing Webinar and Event Roundup: May 19, 2024
This week, Stratasys continues its advanced training and starts its Experience Stratasys tour across the United States. ASTM’s AMCOE continues its professional certificate course, and SPE is offering a workshop...
SPEE3D Releases Expeditionary Manufacturing Unit for Cold Spray 3D Printing
SPEE3D, the Australian original equipment manufacturer (OEM) of cold spray additive manufacturing (CSAM) systems, has released an end-to-end deployable production unit for metal parts. The new product, called the Expeditionary...
Print Services
Upload your 3D Models and get them printed quickly and efficiently.

- 3DPrinting Business Directory
Site Sponsor
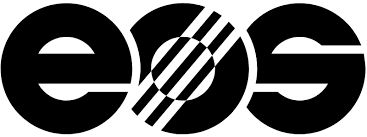
Additive Manufacturing Strategies
Networking & Intelligence Summit, February 4-6, 2025
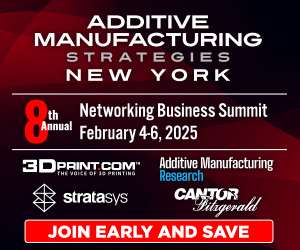
3D Printing jobs around the world.
- I would like to also register for free and access proprietary industry data from SmarTech and 3DPrint.com
- Comments This field is for validation purposes and should be left unchanged.
3D Printing Guides
- Desktop 3D Printer Buyer’s Guide
- 3D Scanner Buyer's Guide
- Metal 3D Printer Guide
- Industrial Polymer 3D Printer Guide
- The 3D Systems Zone
- The HP Zone
- Desktop Metal Zone
- Bioprinting Zone
- The Space Zone
- 3D Printing Stocks Zone
Register to view and download proprietary industry data from AM Research and 3DPrint.com Questions? Contact [email protected]
Already have an account?
- First name *
- Last name *
- Password * Enter Password Confirm Password
- I agree to receive the 3DPrint.com Daily newsletter and promotional email correspondence.
- Create a Business
- 3D Printing
- Additive Manufacturing
What Metal 3D printing is used for: Case studies
- What is a CNC machine?
- What is metalworking: forming, cutting and joining
- What is CNC routing?
- The First look at Laser Cutting and Engraving - 2021 guide
- A Brief Guide to Casting Metals
- 8 Ways machining takes Jewelry making to a whole new level
- What is 3D Printing – Detailed Guide on Additive Manufacturing
- Must-read article for newcomers to 3D printing
- Why 3D Printing is the Best Thing since the X-Ray
- Express guide of FDM 3D printing materials
- A quick guide to exotic FDM printing materials
- What is Resin 3D printing - Introductory Guide [2021 update]
- Why every industry needs SLS 3D printing
- What is Material Jetting?
- The Whole Tooth about 3D Printing in Dentistry
- CNC vs 3D Printing – a comparative guide
- What is metal 3D printing?
- How to use 3D printing for Jewelry
- What is Injection Molding?
- Rotomolding vs Injection Molding
- A Closer Look at Reaction Injection Molding
- TOP 12 CNC routers for Small Business and Hobby [2021 Update]
- Ideas for Laser Cutting & Engraving Projects you can Sell
- 3D Printed Plant Pots & Accessories: does plastic mix well with greens?
- Introduction to 3D Printing custom miniatures
- 8 TOP Laser Cutters and Engravers for Home Shop
- Make your own 3D Printed Cookie Cutters – with or without a printer
- Easy ways to 3D print Topographic maps and Landscape models
Share with friends:
The application of metal 3D printing is widespread and continues to rapidly evolve. Numerous industries now use 3D printing to support additive manufacturing for enhanced and more efficient production. EY’s Global 3D printing Report states that the top three industrial applications of metal 3D printing are mechanical and plant engineering, electronics, and automotive and aerospace. In addition, metal 3D printing has proven utility in the medical fields, such as for manufacturing prosthetics and implants . Here, we explore the most exciting applications of metal 3D printing to demonstrate how this innovative technology could be useful to you.
- Metal 3D printing for mechanical engineering
Metal 3D printing for Aerospace
- Metal 3D printing in Healthcare
3D printing for mechanical engineering
Additive manufacturing provides countless opportunities for designers and engineers to create more complex types of structures.
1. Industrial repair by Siemens
German Siemens has leveraged the power of 3D printing to dramatically shorten lead times for mechanical repairs. For instance, the replacement of burner tips in gas turbines is both a time-consuming and cost-intensive process. The entire repairing process can take up to nine months, and the cost of spare burner tips is excessive. The application of 3D printing has helped Siemens extend the operation of turbines, while concurrently improving burner tip design. The process involves removing the worn-out burner tip, metal printing a new tip, and then welding it back into place. Ultimately, additive manufacturing reduces repair time by as much as 90% – from up to 44 weeks to just 4 weeks.
2. Blades for gas-turbine engines
Mechanical and plant engineering, as well as automotive industry, have intensively used metal 3D printing for creating fully functional prototypes, parts, and tools. Companies such as General Electric (GE), in it’s Aviation subdivision and avio S.p.A. utilize 3D printing for manufacturing turbine blades for gas-turbine engines. Moreover, GE has developed the world’s largest laser-powered 3D printer for metal . It is reported that this printer will be able to create parts that fit inside a 1 cubic-meter space. Vice president and general manager of GE Additive, Mohammad Ehteshami, claims that this machine will be capable of 3D printing jet engine structural components suitable for manufacturers in the power, automotive, oil and gas industries.
3. Increase in performance of hydraulics
A quite unusual application of metal 3D printing was recently described in the Metal Additive Manufacturing magazine . With the help of Selective Laser Melting, engineers were able to increase the performance of hydraulics by optimizing the functionality of the internal channel geometry. It was written that the dimensions of the 3D printed part were 80 x 80 x 50 mm and weighed less than 1 kilogram. Overall, the mass of the part was significantly reduced, while at the same time its performance increased. For instance, a test pressure (1400 bar) of the part revealed no plastic deformation or liquid leakage. These benefits came at no additional expense associated with post-processing.
The popularity of 3D printing in the creation of aircraft parts continues to grow rapidly because energy costs and waste during production are significantly reduced. The finished 3D print can also be much lighter compared to the original parts, thus resulting in reducing the weight of planes and leading to fuel saving.
1. Fuel nozzles for jet engines
GE Aviation uses metal 3D printing for manufacturing fuel nozzles for Boeing and Airbus planes. These new designs integrated approximately 20 details of the traditionally manufactured part into a single one, resulting in savings of about $1.6 million per flight.
2. Structural components for Dreamliners
Boeing now orders 3D printed parts of titanium alloy for production of its new 787 Dreamliner. These bone-like structures reduce weight and increases overall performance. Boeing reports that the usage of metal 3D printing can reduce the cost of each Dreamliner by $2 - $3 million, and are considered to be the first printed structural components that bear the stress of an airframe in flight.
3. Space X and NASA
NASA has successfully tested a jet engine containing 3D printed parts. The device withstood the same stress as a regular rocket engine where fuel is burned at temperatures greater than 6,000 ℉ . Meanwhile, Elon Musk’s SpaceX also uses additive manufacturing for producing rocket ship parts at a reduced cost and improved performance.
Metal 3D printing in healthcare
Additive manufacturing has also proven to be beneficial for medical purposes. Both healthcare and dental industry actively deploy metal 3D printing for creating hips, knees, shoulder implants, shoe insoles, hearing aids, and prosthetics. Presently, medical implants are very commonly manufactured using 3D printing. It is reported that customized products provide superior comfort that contributes to a faster patient recovery. Risks of implant reject, as well as costs, are similarly reduced. Metal 3D printing has also improved the dental industry . In particular, 3D printing has emerged as a powerful technology in the field of orthodontics. Dental technicians, and their patients, are now reaping the benefits resulting from 3D fabrication that is replacing manual and time-consuming processes. Ultimately, this is making treatments more efficient and also much more affordable.
3D Print with Metal
- Sign up for free
By using this Service, you agree to our Terms and that you have read our Privacy Policy , including our Cookie use .
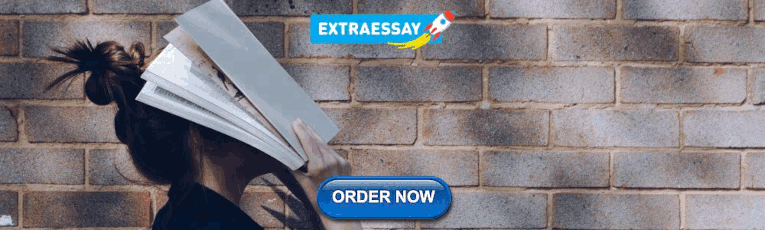
IMAGES
VIDEO
COMMENTS
As well, we cover the best materials for 3D printing parts for this industry and examine one of our favorite case studies. Implementing 3D printing in the aerospace design workflow Designers and engineers creating new products in aerospace and aviation can implement 3D printing at all stages of the design workflow.
Additive manufacturing, also called 3D printing, has many applications in the aerospace industry, from design to manufacturing and beyond. The aerospace industry was one of the earliest commercial adopters of 3D printing, or additive manufacturing, when it was invented. Indeed, many OEMs, suppliers, and government agencies have used 3D printing ...
Aerospace, Case Studies, Explainers, Formlabs / By 5ms / June 23, 2022 October 27, 2022. The best example of the application of Additive Manufacturing (AM) or 3D Printing is found in the Aerospace industry, which produces potentially lighter and stronger parts than traditional manufacturing parts. The aerospace industry was a forerunner in 3D ...
Now, the team is seeing efficiencies in tool production using 3D printing. "We now regularly produce customized, low- volume tools within 24 hours of an engineer's request, and at a fraction of the cost of an aluminum tool," says Chris Botting, Materials, Processes and Additive Manufacturing Engineer, Marshall Aerospace and Defence Group.
3D Printed End-Use, Replacement, and Custom Parts for Aerospace. A large library of proprietary, high-performance materials to produce parts that are up to the challenge of extreme environments. Stop waiting and overpaying for tooling. Gain flexibility and take on more non-traditional jobs by 3D printing parts directly in house.
Project Highlights: A leading aerospace company was looking for 3D design and printing services to eliminate errors associated with the paper-based design and 2D printing using model-based design (MBD). The in-house team of 3D engineers, guided by a senior executive, understood the business requirements and aerospace standards and methodologies.
In 2015, the aerospace and defense industries contributed approximately 16% of 3D printing to $4.9+ billion in global revenues. In this review, additive manufacturing technology and 3DP technology and their uses in the aircraft industry were described precisely. Types of printers used in 3D printing technology and types of printing done by ...
Metal 3D printing has emerged as a game-changer in the aerospace industry, enabling the creation of complex, lightweight, and high-performance components. These case studies demonstrate how this ...
Stereolithography (SLA) is a 3D printing process that utilizes precisely placed photosensitive polymer resin that is cured by UV light to make parts layer by layer. SLA offers the highest resolution of any form of 3D printing and is often used to make cabin accessories like door knobs and seat back panels. 3.
In terms of finish, Materialise's post-production processes ensured the 3D-printed parts met Airbus' strict aesthetic requirements — once produced, the panels were then painted to Airbus cabin requirements, all using flame-retardant Airbus-approved materials. Erik De Zeeuw, Aerospace Market Manager at Materialise, summarizes by saying ...
The aerospace industry has been at the forefront of embracing 3D printing and additive manufacturing, making it a trailblazer in the widespread use and application of these cutting-edge technologies. Due to its unique low-volume, high-mix production profile, aerospace is a very appropriate fit for additive manufacturing.
Today's metal 3D printers unlock designs impossible with conventional methods, offering unparalleled precision and complexity. Blending groundbreaking innovation and expertise, AddUp is leading the evolution of metal additive manufacturing. Explore 29 innovative real-world case studies of 3D printing applications in aerospace, medical, and ...
The 3D printing technologies have been transforming all industries by producing three-dimensional objects based on the commands given by software programs. Aerospace is one of the industries that adopted 3D printing technology early. But the new 3D printing applications and use cases in the aerospace industry is being created regularly.
Equipped with a 91% metal structure hinge, the device features a self-developed shielded strength steel upgrade. However, the true innovation lies in the adoption of aerospace-grade titanium alloy 3D printing technology. This groundbreaking use of titanium 3D printing allows the hinge to support an astonishing 400,000 folds. Image via honor.com
NOTE: This case study is based on a US-based Tier 2 aerospace supplier's success in migrating from a legacy investment cast supply chain to 3DEO's metal 3D printing services. The Challenge The challenges associated with this component are a combination of failings of the supply chain and fundamental limitations of the investment casting ...
Download the full Case Study to discover how ISS Aerospace achieved all of the above! Fill out our secure form to download the case study PDF. Company name * Your Name * First Last. Email * Phone * ... In this practical case study from Primetall, 3D printing was used to print custom fixtures. It was practically "drilled around the corner".
With Sciaky, they conducted research and development in 3D-printing of titanium propellant tanks that would meet the highest demands of performance for satellite deployment. Re: Lockheed Martin additive tank tested to 25% greater pressure than nominal and burst pressure occurred more than twice nominal pressure.
The 3D Printing in Aerospace and Defense thematic intelligence report gives you an in-depth insight into the 3D printing market and the impact it will have on the aerospace and defense industry. It further entails a deep-dive analysis of the industry, including real-life use case studies that showcase the impact of 3D printing on aerospace and defense. The primary trends that will shape the 3D ...
As SLS 3D printing is getting more popular, we share our insights, tips, and tricks for you to use. Case Studies. With a four-figure installation worldwide of Sinterit's 3D printers, here you can find some of our client's stories. SLS Technology. Grasp the basic knowledge about SLS. Your journey starts here. Webinars
Mantle 3D printers reduce tooling lead times by 50%, new customers announced. Alex Tyrer-Jones February 13th 2024 - 7:29pm. US-based metal 3D printer manufacturer Mantle has expanded the reach of ...
Finally, on to aerospace news, as BigRep shared a case study about how its technology helped overcome COVID-19 supply chain challenges and Objectify Technologies shared one about redesigning a ...
The application of metal 3D printing is widespread and continues to rapidly evolve. Numerous industries now use 3D printing to support additive manufacturing for enhanced and more efficient production. EY's Global 3D printing Report states that the top three industrial applications of metal 3D printing are mechanical and plant engineering, electronics, and automotive and aerospace.
Aerospace (27) Transportation (21) Medical (9) Energy (2) Technologies. Fused Deposition Modeling (64) Selective Laser Sintering (34) PolyJet (25) Stereolithography (24) Multi Jet Fusion (11) Injection Molding (7) Programmable Photopolymerization (5) ... 3D Printing Automotive Fixtures Case Study January 17, 2020.