Quality management principles: The foundation for success
As the business world continues to navigate uncharted waters, companies and organizations of every size face unprecedented pressure. To thrive, they must consistently deliver exceptional quality and customer experience. That means striking a delicate balance: delivering excellence alongside the pursuit of operational efficiency.
To do this, they must be able to lean on a rock-solid foundation, with core principles for quality management built into their processes and culture at every level. These principles enable continual improvement for the benefit of the organization, its people, its stakeholders and its customers.
This article explores how quality managemen t principles can help businesses large and small to:
- Elevate their ambition
- Encourage people at every level of the organization to strive for excellence in their work
- Meet internationally recognized principles of quality management – such as those defined in ISO 9000
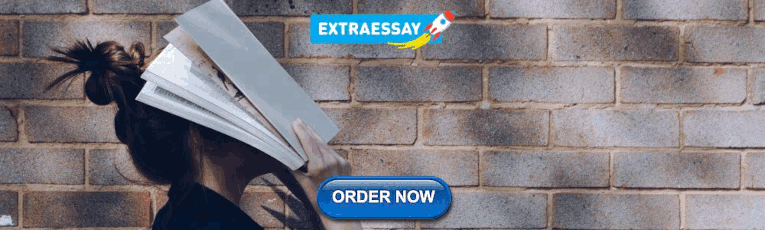
Table of contents
What are quality management principles.
Embedded at the core of any quality management system (QMS), quality management principles (or QMPs) are a set of universally applicable principles , distilled from years of theoretical development and practical application. Their structured approach provides guidance for organizations to define objectives, establish processes and develop systems to manage quality.
Adaptable and agile, they aren’t only applicable to particular industries, but instead offer broad applicability and relevance to any organization committed to process excellence. They are as beneficial to the manufacturing and services industries as to non-profit organizations, the public sector and government agencies.
The seven principles of quality management
Developed and updated by ISO/TC 176, ISO’s dedicated group of quality experts, the following core principles of quality management are designed to be used as a guiding foundation to support performance improvement for all organizations.
It is important to note that there is no priority order to the following list. The relevance of each quality principle will vary from one organization to another and can be expected to change or adjust over time, as the journey of an organization evolves.
- Customer focus : At the heart of quality management is the core aim of meeting customer requirements and striving to exceed the public’s expectations.
- Leadership : Successful leaders establish a unified sense of purpose and direction. They continuously create the optimal conditions in which employees flourish, gaining motivation and professional satisfaction in the pursuit of quality objectives.
- Engagement : Inspiring and empowering people at all levels is essential to the value delivery process.
- Process approach : A well-structured, coherent system is an effective container in which consistent and predictable results can be effectively and efficiently achieved.
- Improvement : A hallmark of successful organizations is a continuous dedication to improvement, from product or service quality to meeting or exceeding customers’ expectations. Such a commitment is an important driver of sustained growth.
- Evidence-based decision making : Reliable data analysis and informed, strategic decision making enhance the chances of achieving desired outcomes.
- Relationship management : The process of building strong, clear and mutually beneficial relationships with all stakeholders and interested parties lays the foundations of sustained success.
Sign up for email updates
Register to receive resources and updates on quality management and related standards.
Almost done! You are only one step away from joining the ISO subscriber list. Please confirm your subscription by clicking on the email we've just sent to you. You will not be registered until you confirm your subscription. If you can't find the email, kindly check your spam folder and/or the promotions tab (if you use Gmail).
To learn how your data will be used, please see our privacy notice .
Why are QMS principles important?
The cornerstones of building and sustaining excellence, QMPs are essential for several reasons:
- To establish a quality management culture. Driving quality mindsets empowers every member of the business to understand, value and contribute to the pursuit of quality.
- To foster consistency. Applying quality principles across an organization promotes consistency in product design, development and delivery. This builds customer trust and public engagement.
- To facilitate continuous improvement. Highlighting areas for ongoing improvement helps an organization stay relevant in an increasingly competitive global landscape.
- To promote customer orientation. Translating quality into increased loyalty and market growth turns satisfied customers into brand advocates.
- To encourage team engagement. Motivating people across all sectors to achieve their highest quality work results in greater workplace satisfaction, team spirit, productivity and staff retention.
- To reduce risks. Proactively identifying potential problems early limits the likelihood of costly mistakes, customer dissatisfaction and reputational damage.
- To support competitiveness. Cementing a quality foundation that strengthens an organization’s competitive positioning. This, ultimately, supports the delivery of high-quality products or services.
How should organizations embed QMS principles in their processes?
ISO’s quality management principles are set in place to help organizations develop high-quality products and services that are safe and effective. The QMS principles found in ISO 9000 have been designed to be adaptable and easily tailored to the unique blueprint and challenges of each organization. While the process of integration will differ, they are applicable to organizations of all sizes and types, across different cultures, locations and social conditions.
As the world’s top quality management standard, ISO 9001 describes the basic requirements of a quality management system. Its QMS requirements include a quality manual, quality objectives, organizational structure and responsibility, data management, internal processes, customer satisfaction, improvement opportunities, and quality instruments for measuring progress. It’s about building a solid foundation that allows all processes to come together to ensure quality across a whole organization.
Although adopting QMPs requires an investment of time, effort and discipline, the returns are substantial. They include enhanced performance, heightened customer satisfaction and market success. By committing to these principles, organizations establish a culture of quality that not only improves their products and services, but simultaneously enhances their customer base and safeguards their reputation.
In a world facing global supply chain issues, quality management is a cornerstone of success. It assures customers that even during times where external disruptions are possible, it is safe to invest their trust in a given product or service. The delivery of exceptional quality requires effective and empowered leadership, high employee engagement and satisfaction, enhanced relationship management and resilient decision making.
ISO 9001 Quality management systems
The road to excellence
By integrating established and recognized quality management principles in the very fabric of an organization, leaders are building a sturdy and resilient foundation that supports the development of high-quality outputs, integrity and reputational excellence.
As a long-established set of principles, QMPs hold timeless value. They serve as a trustworthy roadmap in a global marketplace beset with challenges, lighting the way for organizations committed to enhancing their quality management culture and achieving exceptional outcomes. Ultimately, though, they equip organizations with the agility to respond to customers’ needs, foster innovation, outpace the competition, and secure a leadership role in the market.
- Quality management principles: The foundation …
Quality Management Essay
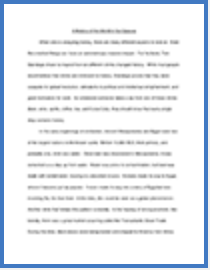
Measuring the Cost of Quality Management
CASE FOR QUALITY Measuring the Cost of Quality For Management by Gary Cokins T he quality movement has used the term cost of quality (COQ) for decades. But few organizations have actually adopted a reliable and repeatable method for measuring and reporting COQ and applied it to improve operations. Is the administrative effort just not worth the benefits, or is there a deeper problem with the methodology for measuring COQ? What COQ Should Do At an operational level, quality management
Definition Of Total Quality Management
Total Quality Management is the concept of processes and integration all of functions in an organization in order that to focus on quality control and approach to long-term success will continue improvement in all aspects but not short- term goal. TQM of business plan began in 1980 in the United States. It was popular until early 1990. Nowadays, in the small business to large business, including restaurant and fast food businesses that used system quality standards to manage the organization because
Productivity and Quality Management
Issue paper one: Productivity and Quality Management Executive Report Prepared by G.Y. Attanayake MBA/2003/1448 Course : MBA 501 Managing Business Operations Dr. Travis Perera and Mr. A.K.L Jayawardana July, 2003 POSTGRADUATE INSTITUTE OF MANAGEMENT University of Sri Jayewardenepura TABLE OF CONTENTS PAGE NO. EXECUTIVE SUMMERY 4 1.0 INTRODUCTION 5 1.1 MEASURING PRODUCTIVITY IN THE MANUFACTURING AND SERVICE SECTORS 1.1.1 Productivity Defined and Explained 5 1.1.1.1 Why Productivity
Quality And Total Quality Management
Quality is defined by meeting customers ' needs. Total quality management in the company through continuous improvement of the quality of its products, services and people. (Goetsch, 2010) Quality and total quality management, the main difference is that perception and activities. (Goetsch, 2010) Here are two of the main elements of the total amount as follows: 1) Education and training: all must be trained and the staff of the organization and educated so that they work hard to do a smart job.
Total Quality Management
Total Quality Management Total quality management is something that was introduced to us around the 1950s. By the 1980s this was something that had been implemented more into many different businesses and the movement began. A total quality management team is defined as the techniques an association uses to recover not only the quality of its company and services but also its production level. This technique involves a lot of joint effort and is used through-out an organization. Everyone is included
Quality Management System
Introduction Quality is a word which has been used for a very long time, lots of books have been written about it, and many of the world scientists have defined it in many different ways. In this research paper, I will emphasis on the Quality Management System, why is it important? What is it used for? What is the importance of having a Quality Management System? Many people think implementing QMS costs a lot and all the benefit is a piece of a paper which say that your company is certified in
Quality Management: Implementing Quality Systems
Implementing quality systems 01_Introduction A quality material, product, process, service or system is one that meets the needs of customers. Today, customers, including consumers, know what they want and can easily recognise ‘quality’. Businesses interact with a variety of customers e.g. • Internal e.g. staff who have their office cleaned, or use the canteen • Business e.g. suppliers of raw materials, stationery, transport, telecommunications • End users e.g. other firms, the government or
Quality Of Quality Assessment And Management
Quality Assessment and Management Healthcare facilities have a legal and moral obligation to provide the high quality patient care, (Huber, 2014). The Quality Management team’s goal will be to continually strive to improve the care their organization delivers. In order for this to be achieved their must goals and objectives to work towards. The success of these goals and objectives are dependent upon The Quality Management Structure of the organization. With proper implementation and management
Quality Of Quality Management Process
The Quality Management process is a set of procedures that are followed to ensure that deliverables that are produced by a team that comply with standards. The start of a Quality Management process involves setting quality levels, which agree with the customer. Quality Assurance along with Quality Control Process are measured and reported to the actual quality of deliverables. Part of the Quality Management Processes are quality issues are identified and resolved quickly. A Quality Management Process
The Quality Of Total Quality Management
Total quality management, also known as TQM, which is an umbrella methodology drawing on knowledge of the principles and practices of the behavioral sciences, the analysis of quantitative and non-quantitative data, economic theories, and process analysis to continually improve the quality of all processes. Three major contributors to the quality profession include: Walter A. Shewhart, W. Edwards Demings, and Joseph M. Juran, who taught the concepts of controlling the quality and managerial breakthrough
Popular Topics
- Questions And Answers Essay
- Race And Gender Essay
- Race Relation Essay
- Ralph Ellison Essay
- Rate Of Return Essay
- Reality Essay
- Reconstruction Era Essay
- Recruitment And Selection Essay
- Reflection Paper Essay
- Reflective Journal Essay
- Search Search Please fill out this field.
- What Is Total Quality Management?
- Understanding TQM
- Primary Principles
- How to Implement TQM
- Pros and Cons
- Industries Using TQM
The Bottom Line
- Business Essentials
What Is Total Quality Management (TQM) and Why Is It Important?
:max_bytes(150000):strip_icc():format(webp)/Group1805-3b9f749674f0434184ef75020339bd35.jpg)
Yarilet Perez is an experienced multimedia journalist and fact-checker with a Master of Science in Journalism. She has worked in multiple cities covering breaking news, politics, education, and more. Her expertise is in personal finance and investing, and real estate.
:max_bytes(150000):strip_icc():format(webp)/YariletPerez-d2289cb01c3c4f2aabf79ce6057e5078.jpg)
What Is Total Quality Management (TQM)?
Total quality management (TQM) is the continual process of detecting and reducing or eliminating errors in manufacturing. It streamlines supply chain management , improves the customer experience, and ensures that employees are up to speed with training. Total quality management aims to hold all parties involved in the production process accountable for the overall quality of the final product or service.
Key Takeaways
- Total quality management (TQM) is an ongoing process of detecting and reducing or eliminating errors.
- Total quality management is used to streamline supply chain management, improve customer service, and ensure that employees are properly trained.
- The focus is to improve the quality of an organization's outputs, including goods and services, through the continual improvement of internal practices.
- Total quality management aims to hold all parties involved in the production process accountable for the overall quality of the final product or service.
- There are often eight guiding principles to TQM that range from focusing on customers, continually improving, and adhering to processes.
Investopedia / Katie Kerpel
Understanding Total Quality Management (TQM)
Total quality management is a structured approach to overall organizational management. The focus of the process is to improve the quality of an organization's outputs, including goods and services, through the continual improvement of internal practices. The standards set as part of the TQM approach can reflect both internal priorities and any industry standards currently in place.
Industry standards can be defined at multiple levels and may include adherence to various laws and regulations governing the operation of a particular business. Industry standards can also include the production of items to an understood norm, even if the norm is not backed by official regulations. Acceptance sampling might be used to check the progress toward the TQM goal.
Example of Total Quality Management
Perhaps the most famous example of TQM is Toyota's implementation of the kanban system. A kanban is a physical signal that creates a chain reaction, resulting in a specific action. Toyota used this idea to implement its just-in-time (JIT) inventory process.
The company decided to keep just enough inventory on hand to fill customer orders as they were generated to make its assembly line more efficient. All parts of Toyota's assembly line are therefore assigned a physical card that has an associated inventory number.
The card is removed and moved up the supply chain right before a part is installed in a car, effectively requesting another of the same part. This allows the company to keep its inventory lean and not overstock unnecessary assets. Effective quality management resulted in better automobiles that could be produced at an affordable price.
History of Total Quality Management
TQM's history often dates back to the early 1900s when Walter A. Shewhart introduced modern quality control. Shewhart produced a landmark piece of industrial work entitled Economic Control of Quality of Manufactured Product in 1931. This exposition is considered one of the founding and basic principles of manufacturing quality control.
Further developments in Shewhart's work introduced new standards in quality management decades later. Joseph M. Juran published a book called What Is Total Quality Control? The Japanese Way . in 1954. The work was based on Juran's experience of being invited to Japan by Japanese scientists and engineers. Juran later co-authored Quality Planning and Analysis , another bestseller in TQM.
Another prominent figure in TQM history is W. Edwards Deming. Also posted in Japan after the Second World War, Deming became involved with the Union of Japanese Scientists and Engineers (JUSE). His career work included several TQM frameworks (Deming's 14 Points, Deming's Seven Deadly Diseases of Management, and The Deming Wheel).
The exact origin of the phrase total quality management is not known, but several parties mentioned above are credited for helping develop the general concept.
Primary Principles of Total Quality Management
TQM is considered a customer-focused process that focuses on consistently improving business operations management . It strives to ensure that all associated employees work toward the common goals of improving product or service quality, as well as improving the procedures that are in place for production. There are several guiding principles that define TQM.
Focus on Customers
Under TQM, your customers define whether your products are high quality. Customer input is highly valued because it allows a company to better understand the needs and requirements in the manufacturing process. Customer surveys may reveal insufficient durability of goods. This input is then fed back into TQM systems to implement better raw material sourcing, manufacturing processes, and quality control procedures.
Commitment by Employees
Employees must buy into the processes and system if TQM is going to be successful. This includes clearly communicating across departments and leaders what goals, expectations, needs, and constraints are in place. A company adopting TQM principles must be willing to train employees and give them sufficient resources to complete tasks successfully and on time. TQM also strives to reduce attrition and maintain knowledgeable workers.
Improve Continuously
A company should gradually evolve and strive for incremental, small improvements as it learns more about its customers, processes, and competition. This concept of continuous improvement helps a company adapt to changing market expectations. It allows for greater adaptability to different products, markets, customers, or regions. Continuous improvement also drives and widens the competitive advantage that a company has built over related companies.
Adherence to Processes
TQM's systematic approach relies heavily on process flowcharts, TQM diagrams, visual action plans, and documented workflows . Every member engaged in the process must be aware and educated on their part of the process to ensure proper steps are taken at the right time of production. These processes are then continually analyzed to better understand deficiencies in the process.
Strategic and Systematic Approach
A company's processes and procedures should be a direct reflection of the organization's vision, mission , and long-term plan. TQM calls for a system approach to decision making that requires that a company dedicate itself to integrating quality as its core component and making the appropriate financial investments to make that happen.
Data Utilization
The systematic approach of TQM only works if feedback and input is given to evaluate how the process flow is moving. Management must continually rely on production, turnover, efficiency, and employee metrics to correlate the anticipated outcomes with the actual results. TQM relies heavily on documentation and planning, and only by utilizing and analyzing data can management understand if those plans are being met.
Integrate Systems
One way to utilize data is to integrate systems. TQM strategies believe systems should talk to each other, conveying useful information across departments and making smart decisions. When goods or inventory are used in one area, another department should have immediate access to that ERP information. TQM strives to allow everyone to be on the same page at the same time by linking data sources and sharing information across systems.
Communication
Data may transfer between departments freely, but there is a human element to coordinating processes and making sure an entire production line is operating efficiently. Effective communication plays a large part in TQM to motivate employees, educate members along a process, and avoid process errors whether it is normal day-to-day operations or large organizational changes.
Successful TQM requires a company-wide buy-in of every principle. The benefits of TQM quickly diminish if a company does not receive complete buy-in.
How to Implement Total Quality Management
TQM is a unique process. There is not a specific formula for implementing a system that suits every business and each type of industry. But you can create a checklist of issues that might suit your enterprise and proceed with them in chronological order. Some may suit your business while others will not. Select those that you think will provide an advantage.
- Identify your company’s existing culture, its core values, and its systems.
- Use this information to create a system that will serve as your master plan.
- Establish what your customers and clients want and what they expect from your business. Determine how to best meet these expectations and needs.
- Create a team of management and employees to guide and implement your goals and include these efforts in your daily business management process.
- Consistently gather feedback from both employees and customers to gauge your progress.
TQM is not a speedy process. Expect to dedicate an extended period of time to your efforts.
Advantages and Disadvantages of TQM
TQM results in a company making a product for less when it's implemented correctly. Companies that engage in TQM provide more consistent products that yield stronger customer loyalty when they emphasize quality and minimize waste.
As TQM touches every department across an organization, a company may reap substantial savings from materials sourcing, production, distribution, or back-office functions. Companies that successfully implement TQM can usually react more quickly to change and proactively plan ahead to avoid obsolescence.
A company must fully engage TQM principles to fully reap the benefits of TQM. This requires substantial buy-in from every department across an organization. This level of commitment is very difficult to achieve, requires substantial financial investment, and necessitates all levels of management to engage in TQM.
The conversion to TQM may be lengthy, and workers may feel resistant to change. A company may be required to replace processes, employees, equipment, or materials in favor of an untested, partially developed TQM plan. More skilled workers may decide to leave the company if they feel TQM processes don't appropriately utilize their skill sets.
Total Quality Management
Delivers stronger, higher quality products to customers
Results in lower company-wide costs
Minimizes waste throughout the entire production and sale process
Enables a company to become more adaptable
May require substantial financial investment to convert to TQM practices
Often requires conversion to TQM practices over a long period of time
May be met with resistance to change
Requires company-wide buy-in to be successful
Industries Using Total Quality Management
TQM originated in the manufacturing sector, but its principles can be applied to a variety of industries. It provides a cohesive vision for systemic change with a focus on long-term change rather than short-term goals. TQM is used in many industries with this in mind, including but not limited to manufacturing, banking and finance, and medicine.
These techniques can be applied to all departments within an individual organization. This helps ensure that all employees are working toward the goals set forth for the company and improving function in each area. Involved departments can include administration, marketing, production, and employee training.
What Does Total Quality Management Do?
TQM oversees all activities and tasks that are necessary to maintain a desired level of excellence within a business and its operations. This includes the determination of a quality policy, creating and implementing quality planning and assurance, and quality control and quality improvement measures.
What Are the Principles of TQM?
Various iterations of TQM have been developed, each with its own set of principles. Certain core elements persist nonetheless. These include good leadership, emphasis on quality, customer priority, error correction and improvement as an ongoing process, and job training.
What Is a TQM Diagram?
A TQM diagram is a visual depiction of the business and process layout. The diagram usually shows different processes or steps, allowing management to see a process, analyze weaknesses or risks in the flow, and strategically adjust how things are done.
Total quality management is the strategic framework that encourages everyone in an organization to focus on quality improvement. The theory holds that customer satisfaction will increase by being operationally excellent. Many principles drive TQM, but the overall purpose is to eliminate errors, streamline processes, and maximize efficiency.
Toyota. " Section 4. Plant Construction and Expansion Item 4. Development and Deployment of the Toyota Production System ."
American Society for Quality. " Walter A. Shewhart ."
American Society for Quality. " Joseph M. Juran ."
British Library. " W Edwards Deming ."
:max_bytes(150000):strip_icc():format(webp)/business-people-using-pen-tablet-notebook-are-planning-a-marketing-plan-to-improve-the-quality-of-their-sales-in-the-future--881542122-6767a39f655b4a018019715734dcfbe0.jpg)
- Terms of Service
- Editorial Policy
- Privacy Policy
- Your Privacy Choices
To read this content please select one of the options below:
Please note you do not have access to teaching notes, a literature review on total quality management (models, frameworks, and tools and techniques) in higher education.
The TQM Journal
ISSN : 1754-2731
Article publication date: 7 September 2021
Issue publication date: 24 November 2022
The purpose of this paper is to analyze the evolution of total quality management (TQM) models, frameworks, and tools and techniques in higher education (HE) over the last thirty years from 1991 till 2020, based on a literature review
Design/methodology/approach
30 articles from 52 journals were used to perform this detailed literature review. For the detailed analysis, the focus was only on articles related to TQM in higher education and specifically related to models, frameworks and tools and techniques. The study has investigated the growth of research articles, research streams, research methodologies, models and frameworks in the higher education sector and tools and techniques related to those.
This review addresses the progress and gaps in the application of TQM in HE, including the shift in global research in this area from the USA and Europe to Asia in recent years. The articles have been classified into four research methodologies and two research streams which have been reviewed in detail. The findings include reasons for multiple models/frameworks in HE proposed by researchers over the years and the importance of tools and techniques used in TQM implementation.
Originality/value
This study, which tries to bring a perspective to the main trends in TQM application to higher education wrt models, frameworks, tools and techniques over the last thirty years, is expected to add to the body of knowledge in this area and help future researchers to focus on the relevant areas identified in this paper.
- Higher education
- Tools and techniques
Jasti, N.V.K. , Venkateswaran, V. , Kota, S. and Sangwan, K.S. (2022), "A literature review on total quality management (models, frameworks, and tools and techniques) in higher education", The TQM Journal , Vol. 34 No. 5, pp. 1298-1319. https://doi.org/10.1108/TQM-04-2021-0113
Emerald Publishing Limited
Copyright © 2021, Emerald Publishing Limited
Related articles
We’re listening — tell us what you think, something didn’t work….
Report bugs here
All feedback is valuable
Please share your general feedback
Join us on our journey
Platform update page.
Visit emeraldpublishing.com/platformupdate to discover the latest news and updates
Questions & More Information
Answers to the most commonly asked questions here
- Call to +1 844 889-9952
The History & Evolution of Quality Management Quality
- What Is Quality Management?
- History of Quality Management Evolution
- Quality Management Key Principles
Quality Management Thinkers
- Quality Management Concepts
- Measuring the Quality
Measuring Quality of a Service
- Quality Management in the US and Japan
- Quality Practices in UAE
Works Cited
Quality Management was a natural offshoot of industrialization. Quality management became necessary to help reduce the quantity of defective products arising from production processes. Companies that managed to increase the quality of their products and to reduce defects in their finished products remained profitable. This report looks at the evolution of quality management as a field. It also explores the current methods and applications of quality management.
Definition of Quality
The definition of quality is evolutionary. This comes from the changes in industry affecting quality management approaches and quality management standards. One definition of quality is “freedom from defects” (Stephens 71). This definition applies to the level of workmanship. In this case, the aim of quality management is to eliminate defects through good workmanship. Another definition of quality is “product features” (Stephens 71). In this case, the quality of a product refers to the number of features the product possesses in relation to other products in its range. Taken together, the two definitions show that the current view of quality supersedes excellent workmanship to include the variety of product features.
Another definition of quality is “fitness for purpose” (Lal 1). This definition seeks to make quality a factor of product performance in the context of use. It advances the idea that a perfect product in the wrong context cannot meet the performance demands of that context. Therefore, despite freedom from defects and possession of superior features, a product may have a low quality rating for the specified application. These definitions show that the meaning of quality depends on usage. It is important to define the context before using any of the definitions of quality.
The History and Development of Quality Management
The history of quality management goes back to ancient Babylon. The Hammurabi building code imposed a death sentence on any mason who built a house that later collapsed and killed the occupants (Thomas 201). While the Hammurabi code did not have elaborate rules comparable to those in many cities today, it dealt with the fitness for purpose of any house. Later on, the Egyptians developed a process control system to handle the quarrying of stones for pyramid construction (Thomas 205). The stability of the pyramids depended on the uniformity of the stones used in their construction. This meant that process control was necessary to ensure each stone met its performance requirements.
During the middle ages, quality control became an important facet of shipbuilding because of the risks associated with sailing in poorly designed vessels. Ports with long ship building traditions used quality management to ensure that each ship was fit for its purpose. Quality management became more important during the industrial revolution because of the proliferation of industries. Manufacturers found it necessary to develop quality standards for various reasons. First, the profitability of the industries depended on the efficient utilization of raw materials (Mukherjee 48).
Industries needed raw materials in unprecedented quantities. The only way to make a profit was to use the raw materials efficiently. Secondly, quality controls made it possible for industries to predict the market value of their products (Mukherjee 52). Mass production led to the need for standardized prices. The only way to ensure that customers would purchase goods at the same price was if the manufacturers could produce the same quality of goods. Thirdly, quality became a source of competitive advantage (Dalic 26). Companies that built strong reputations as producers of high quality products gained a market advantage.
In the early years of the twentieth century, Fredrick Winslow Taylor wrote a book entitled, “Principles of Scientific Management” (Lal 22). This book, among other things, identified the need for quality inspections in manufacturing facilities. Taylor saw the need to employ a specialized quality inspector in each industry to ensure that all products released to the market met certain quality standards (Lal 22). His pioneering work led to the development of quality control systems in many industries. As mass production gained credence, quality control became critical for profitability. Each part produced on a production line needed to meet certain quality requirements before the assembly of the final product.
After the Second World War, quality philosophers such as Edward Deming, Joseph Muran, and Philip Krosby developed philosophical insights into quality control. Their insights took advantage of the statistical methods of quality measurement developed in the twenties for quality control. Kaoru Ishikawa synthesized their thoughts in the late sixties and based on his ideas, Japanese industries developed their quality management systems (Stephens 37). These systems gave Japan leadership in product quality management for many decades. Companies such as Toyota developed the Toyota System as its quality control adaptation (Stephens 76). Many Japanese companies practice lean manufacturing and have several other approaches to Total Quality Management (TQM).
Today, quality management uses computerized processes for speed and accuracy. Many manufacturers are aiming to establish non-defective production processes because of the high cost of handling defective products. The main area of contemporary research in quality management is product design. System design is more challenging than component design. Many manufacturers have attained very high quality levels in component design. The challenge is the overall product design. In the automotive sector, the strict quality requirements have been behind the massive recalls of automobiles because of defective system designs. This area requires the input of researchers and process engineers.
The Key Principles of Quality Management
Authors have no consensus regarding the number of fundamental concepts that comprise TQM. However, they all seem to capture the same concepts expressed in different ways. This report adopts the format of TQM principles in the ISO 9000 series. ISO 9000 series identifies eight principles of TQM.
The first principle of TQM according to the ISO 9000 series is customer focus (ISO 3). This principle encourages every organization to make its customers a central part of its operations. This comes from the understanding that the organization depends on its customers for survival. In this sense, the organization must strive to meet the current and future needs of its customers. This calls for the organization to conduct market research continually in order to uncover and meet customer needs and expectations. In addition, the business objectives of the organization should come from customer expectations. This ensures that everyone in the organization works towards meeting the needs of the customers.
The second principle of TQM is leadership (ISO 4). This principle encourages every organization to streamline its leadership function. The principle arose from the positive correlation between focused leadership and superior business performance. One of the goals of streamlining the leadership function is to eliminate miscommunication between different leadership levels in an organization. This principle also encourages leaders to motivate workers towards superior performance. Leaders are also supposed to set challenging goals for the organization. Challenging goals tend to motivate employees to strive towards excellence. Finally, this principle also requires leaders to avail all the resources that employees need to perform their tasks well.
Thirdly, ISO identifies the involvement of people as a principle of TQM (5). The fundamental focus of this principle is the appreciation of all people in the organization as valuable contributors to the objectives of the organization. This principle advocates for Theory Y leadership. It means that the leaders should ensure that everyone understands his or her role in the organization. It encourages leaders to help all employees to know what they contribute towards the organization and the importance of their contribution. This principle also encourages openness in information sharing. In addition, it encourages collective problem solving approaches. In summary, this principle encourages organizations to value and utilize their human resource.
The fourth TQM principle is the use of the process approach (ISO 5). This principle underscores the fact that when an organization uses the process approach to manage its activities, it achieves its goals more efficiently. The use of the process approach ensures that the organization posts predictable results. Once the organization establishes a process for handling a certain issue, it focuses on streamlining the process in order to improve its overall performance. An organization needs to analyze how various processes interact in order to find avenues for improving performance. In addition, the organization must analyze the impact of each process on its stakeholders such as customers, shareholders and its employees.
The fifth TQM principle according to the ISO 9000 series is the use of a system approach to management (ISO 6). The goal of this principle is to break down management silos in the organization. Each organization that does not use a system approach in its management creates an environment that can lead to the emergence of fiefdoms. This can create artificial blockages in the operations of the organization that can reduce overall organizational efficiency. This model also makes it easy for the organization to measure its performance.
The ISO 9000 series identifies continual improvement as a TQM principle (ISO 8). Unlike static improvement processes, continual improvement as espoused by TQM makes finding and eliminating bottlenecks an on-going process in an organization. The ability to implement this principle is what separates regular organizations from dynamic ones. The main advantage of this principle is that it gives the organization the ability to take advantage of emerging opportunities effectively. It makes change a normal process of organizational life. This principle encourages the organization to make continuous improvements in its products, processes, and systems (ISO 8). The effective implementation of this principle is what leads to organizational growth.
The seventh principle of TQM according to the ISO 9000 series is the use of facts in decision-making (ISO 9). This principle encourages every organization to institutionalize the use of logical decision-making processes. The advantage of a fact-based approach to decision making is that each person in the organization can appreciate and anticipate the decisions that the organization will take in any situation. This makes it easy for people to step in for others whenever the need arises. To implement this principle, each organization needs to ensure that every person has access to the information he or she needs to make good decisions. In addition, the organization must always ensure that the information is accurate.
Finally, the ISO 9000 series identified mutually beneficial supplier relationships as the eighth TQM principle. The basic assumption behind this principle is that each organization and its suppliers are mutually dependent. This means that each of them should identify mutually beneficial arrangements. Good supplier relationships give organizations the ability to take advantage of emergent opportunities. Organizations that seek to implement this principle should plan joint improvement programs with their suppliers, alongside other cooperative ventures. In the same breath, each organization should identify its key suppliers and work towards deepening their relations.
The emergence of quality management as an academic discipline as well as its adoption in industry relied on the work of the champions of TQM. These champions were scholars and philosophers in the field of quality management. The notable champions of TQM were Edward Deming, Joseph M. Juran, A. V. Feigenbaum, Kaoru Ishikawa, and Philip Crosby.
Edward Deming was a statistician who came up with fourteen key principles for quality improvement. Deming was philosophically opposed to the use of management by objectives. He helped to bring to the fore the need to add quality management to the essential role of supervisors. He encouraged organizations to bring down management silos and other organizational barriers in order to turn the workforce into a cooperative team.
Apart from the fourteen principles, Deming also identified barriers to the effective deployment of quality management. The list he made included lack of purpose, and emphasis on short-term profits (Lal 33). A comparison of Deming’s fourteen principles and those espoused by ISO shows that Deming had captured the essence of TQM, but had too many specifics in his list of principles. Each of them can comfortably fit within the eight TQM principles of the ISO 9000 series.
The second champion of TQM was Joseph M. Juran. Juran first came to the limelight when he proposed the application of the Pareto principle to the quality management. This approach defined his philosophy and forms part of his quality management legacy. Juran also developed the quality trilogy, which comprised quality planning, quality control, and quality improvement (Stephens 14). Part of Juran’s discomfort with the quality management approaches of his time was that they focused on the quality of the finished product instead of focusing on the entire planning process. By the time quality checks came into play, it was already too late. At best, quality control processes could only identify defective products, rather than stop the production of defective products from the onset.
The third champion of quality control was Armand Vallin Feigenbaum. Feigenbaum was the one who developed the concept of Total Quality Control, which later evolved into TQM. He contributed to quality control in several ways. First, he developed Total Quality Control, which was the precursor to TQM, and is the foundation of the present day practice of quality management. Secondly, Feigenbaum developed the concept of the hidden plant. The hidden plant refers to all the activities that an organization undertakes to revise poor quality work (Bender and Krasnick 14).
When Feigenbaum looked at all the hidden efforts, he concluded that these activities were significant enough to form a hidden plant within the factory. Thirdly, Feigenbaum developed the concept of quality accountability (Bender and Krasnick 15). Essentially, he tried to find ways of making people accountable for quality in the organization. This approach can help an organization to eliminate quality lapses in processes where no one is accountable. Feigenbaum also developed the concept of quality costs by showing that the production of poor quality goods and services costs the organization time and money (Thomas 28).
The fourth champion of quality control was Kaoru Ishikawa. Ishikawa developed the philosophies of Juran and Deming by finding ways of applying them to Japanese companies. Ishikawa conceptualized quality circles and then trained organizations on how to use quality circles (Bender and Krasnick 66). The essential quality principles propagated by Ishikawa were as follows. First Ishikawa believed in continuous improvement of processes, products, and systems (Lal 14). He encouraged organizations to implement continuous improvement mechanisms in their production processes. Secondly, Ishikawa believed that organizations needed to worry about quality at every stage of production. This was in response to the prevailing practice where quality inspections took place at the end of the production process.
Finally, the fifth champion of quality management was Philip Crosby. Crosby developed four main precepts. Crosby defined quality as conformance to requirements (Mukherjee 34). In this case, the requirements meant product and customer requirements. Secondly, Crosby believed that prevention was the only way of attaining high quality production standards (Mukherjee 38). This meant that it was important to do something in the right way during the first attempt. This eliminates the costs associated with revisions. Thirdly, Crosby popularized the notion that the standard all quality management processes should aim for is to have no defects (Bender and Krasnick 72). This is an absolute standard. Finally, Crosby postulated that the price of quality was the cost of quality failure (Bender and Krasnick 72).
Quality Management Approaches
The measurement of the quality of services is different from the measurement of the quality of manufactured goods. This difference arises from the nature of goods and services. Customers can assess the quality of a product after picking it off a shelf, and can predict with reasonable accuracy how any other copy of the same product will perform. When it comes to services, it is impossible for a customer to predict whether the quality of services received from a company will be satisfactory at a different time. The reason for this is that customers access services on demand, while they access manufactured products in advance. In this regard, the measurement of the quality of manufactured products differs from the measurement of the quality of services.
Measuring the Quality of a Manufactured Product
Based on the definitions of quality discussed in the previous section, it is possible to deduce the essential factors to consider when measuring the quality of manufactured products. The first approach of measuring the quality of manufactured products is by examining how the finished product compares to the design specifications. This measure is useful when using the no-defects approach to quality management. In this case, the basis for product testing is the ideal performance standards set during the design phase. The second approach to the testing of the quality of manufactured products is checking whether the product is fit for purpose. The idea in this case is to determine whether the product meets the functional requirements and customer expectations (Martin 19).
This measure is ideal for testing products that are new in the market. Such products require performance testing to ensure that they meet market needs. Another approach for measuring the quality of manufactured goods is by using statistical techniques (Mukherjee 65). The methods used in statistical measurement of quality include checking the degree of conformity of a batch of products to design standards against the number of defective products in the same batch. This means that an organization uses measures that indicate the percentage of defective products in relation to non-defective products. This approach is useful for measuring changes in production quality in numerical terms. However, knowing the number of defective products as a statistical expression is only the first step in instituting quality control measures.
Measuring the quality of a service is not as easy as measuring the quality of a product. The reason for this is that services expire at the point of consumption and are not available for review later. However, each organization can use customer feedback as a means of measuring the quality of services offered by the organization. A company can also measure the quality of the services offered statistically by reviewing the feedback it gets from its customers.
A company needs to collect reviews from its customers. Usually, organizations have places where customers can give their feedback in the form of complaints, or compliments. By counting the number of complaints received per unit number of customers, a company can establish whether the services it renders meet the desired criteria. This approach requires care because not every customer provides feedback to the organization. In fact, a large number of unhappy customers do not give feedback (BSI 1). A company may not even realize that it has lost business to its competitors.
A second way of measuring the quality of services is by examining the number of customers who use the company’s services. This means that it is important to keep track of the number of customers who seek services from a company, and the number of repeat customers. If the company realizes that it is serving an increasing number of customers per given time, then it can tell whether its services have the appropriate quality dimensions. A reduction in the number of clients can mean that there are quality lapses in the provision of services. It is important to note that number alone cannot be a good indicator of the quality of services offered. The company may have other competitive advantages that lead to high customer numbers, such as a convenient business location.
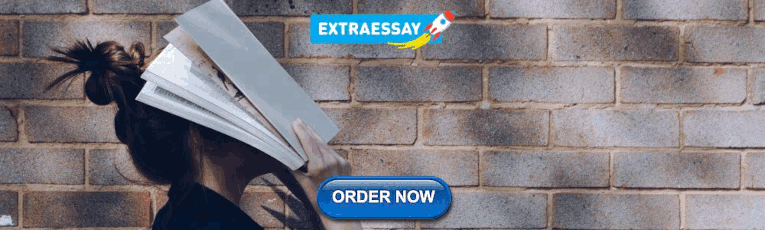
Quality Management in the US and Japanese Firms from the Fifties
Quality management in Japan took off earlier than in the US. After the Second World War, Japan decided to focus on industrial growth as its national priority. Initially, Japanese products were not competitive in the global market because of low quality workmanship. The work of thinkers like Kaoru Ishikawa made Japan change its attitude towards quality management. Ishikawa, among other quality management promoters influenced the Japanese industry by introducing quality management thinking and practices in the country. During the same period, the US was a world leader in manufacturing. The country had well developed industries and stable industrial models. However, quality management was not a priority for many companies in the US. Manufacturers were happy with their production processes and were not keen to improve the prevailing methods. This went on until the seventies.
The energy crisis of the late seventies made the world aware of quality improvements in Japan. The country had made the production of fuel-efficient cars a central priority in its automobile industry. The result was that when people started looking for efficient cars, Japanese cars proved their worth. In addition to automobiles, Japanese machinery started making their way to shops in the US. Companies such as Fuji and Sony became household names in the US because of their ability to produce goods that rivaled the quality of products made in the US.
The eighties saw the reemergence of the US as a production powerhouse. The US proved to be innovative in its product design processes. In addition, management consultants, working with quality management specialists started training companies in the US on quality control. Companies in the US that took quality control seriously soon became competitive against Japanese companies. In some cases, Japanese companies opened branches in the US to handle the local market. Companies based in the US did the same in Japan to benefit from the Japanese quality culture. The result was a general increase in quality standards in the two countries.
Today, TQM is a standardized process found in both the US and Japan. Different companies have different adaptations for use in their context. The rising power in the world right now is China. China is becoming a strong partner to many countries because of its huge manufacturing capabilities. China is suffering from quality control problems partly because of its history. China is competitive because of the low labor costs in the country. Based on Japan’s history, China can catch up with the US and Japan in the coming years if it adopts quality control as a central tenet of industrial growth.
Examples of Quality Practices in UAE Organizations
Many organizations in the UAE use TQM principles to run their affairs. Two of these organizations are Mashreq and the Dubai Customs. Mashreq is an ISO certified banking institution. Mashreq obtained an ISO 9000 certification in regards to its service quality. Mashreq identified four main customer needs in its efforts towards achieving ISO 9000 certification. First, the company realized that it is vital for it to achieve a superior level of reliability, efficiency, and effectiveness in its services (BSI 1).
The UAE is an important financial hub for the Middle East. Competition in the financial services sector is very stiff. A lackadaisical performance is a recipe for disaster for any financial services provider. In this regard, Mashreq set for itself challenging goals in regards to the quality of services that its clients can expect. Secondly, Mashreq made a commitment to ensure that it would improve its processes, systems, and services continually, while at the same time ensuring that staff morale remained high (BSI 2). This goal was consistent with the principles of TQM. The third commitment that Mashreq made towards quality improvement was to demonstrate an ongoing commitment towards its customers.
This commitment was very similar to one of the principles of TQM that encourages organizations to focus on their customers. The fourth commitment Mashreq made was to benchmark its services with international players (BSI 2). This commitment showed that Mashreq realized that the UAE is becoming an international financial hub. The organization also hoped that setting high goals would motivate its staff members to engage in their work with greater focus. The main issue in Mashreq’s ISO 9000 certification was that the organization demonstrated its commitment to TQM, and continual process improvement. The organization has put systems in place to aid it to improve its processes, systems, and products.
The second organization that is practicing TQM is Dubai Customs. Dubai Customs is a very busy organization by virtue of Dubai’s role as a transport hub of the UAE, the Arab countries, and beyond. The emirate is also becoming a critical connection point for international flights. The management of Dubai Customs acted on the need to reduce and eventually eliminate all quality concerns in regards to the services offered by the organization. The managers were alive to the fact that dissatisfied customers tend to go away without talking to anyone. On the other hand, it is possible to win back customers who voice their complaints.
The managers of Dubai Customs chose to invite quality assessors from LRQA to conduct a quality assessment. This decision shows that the organization was ready to risk its reputation for the benefit of its customers. It also demonstrates that the organization was confident about its systems.
The certification process took five months. This period was shorter than normal because of the commitment of the organization to TQM. The certification project had several aspects, which included gap analysis, internal audits, external audits, and the eventual certification (Lloyds Register 2). The certification project aimed at ensuring that Dubai Customs achieved the ISO 10002 certification for the handling of complaints. Handling of complaints is a very critical aspect of service quality.
The objective was to ensure that Dubai Customs would handle at least three quarters of all complaints within a week. By the end of the certification project period, the time had reduced to two and a half days. The project also included an audit of the actual complaint management system. The auditors assessed the effectiveness of the actions generated from complaint resolution processes, against the needs of the clients of the organization. This helped the organization to find a way of measuring the quality of the solutions it gave to its customers.
Bender, Douglas A and Carla Krasnick. A Total Quality Management Process Improvement Model. New York: Diane Publishing, 1993. Print.
BSI. Using BSI ISO 9001 to Demonstrate Mashreq’s Commitment Towards its Customers. Dubai: BSI Group, 2013. Print.
Dalic, Tomislaw. Globalisation of Marketing Strategies in Light of Segmentation and Cultural Diversity. Norderstedt: GRIN Verlag, 2007. Print.
ISO. Quality Management Principles. Geneva: ISO Central Secretariat, 2012. Print.
Lal, H. Total Quality Management: A Practical Approach. New Delhi: New Age International, 2004. Print.
Lloyds Register. LRQA Business Assurance Approach Helps Dubai Customs Improve Customer Satisfaction. Dubai: Lloyds Register, 2013. Print.
Martin, Roger L. The Design of Business: Why Design Thinking Is the Next Competitive Advantage. Boston, MA: Harvard Business Press, 2009. Print.
Mukherjee, P N. Total Quality Management. New Delhi: PHI Learning Pvt. Ltd, 2006. Print.
Stephens, Kenneth S. Juran, Quality, and a Century of Improvement. Milwaulee, WI: ASQ Quality Press, 2005. Print.
Thomas, Anne. Strategies for Branding Success. New York: eBooklt.com, 2011. Print.
Cite this paper
Select style
- Chicago (A-D)
- Chicago (N-B)
BusinessEssay. (2022, December 18). The History & Evolution of Quality Management Quality. https://business-essay.com/quality-management-evolution-and-modern-methods/
"The History & Evolution of Quality Management Quality." BusinessEssay , 18 Dec. 2022, business-essay.com/quality-management-evolution-and-modern-methods/.
BusinessEssay . (2022) 'The History & Evolution of Quality Management Quality'. 18 December.
BusinessEssay . 2022. "The History & Evolution of Quality Management Quality." December 18, 2022. https://business-essay.com/quality-management-evolution-and-modern-methods/.
1. BusinessEssay . "The History & Evolution of Quality Management Quality." December 18, 2022. https://business-essay.com/quality-management-evolution-and-modern-methods/.
Bibliography
BusinessEssay . "The History & Evolution of Quality Management Quality." December 18, 2022. https://business-essay.com/quality-management-evolution-and-modern-methods/.
- Strategic Leadership Role in Change Management
- Procter and Gamble Company: Development Issues
- Enterprise Resource and Material Requirements Planning in the UAE
- Managing Information System
- Quality Management Issues: Theory and Practice
- Innovation and Organizational Culture
- The Management and Organizational Dynamics
- Cultural Diversity and Group Relations in the Workplace
- Dubai Customs’ Quality Management and Innovation
- Abu Dhabi National Oil Company: Program Governance
- Undergraduate
- High School
- Architecture
- American History
- Asian History
- Antique Literature
- American Literature
- Asian Literature
- Classic English Literature
- World Literature
- Creative Writing
- Linguistics
- Criminal Justice
- Legal Issues
- Anthropology
- Archaeology
- Political Science
- World Affairs
- African-American Studies
- East European Studies
- Latin-American Studies
- Native-American Studies
- West European Studies
- Family and Consumer Science
- Social Issues
- Women and Gender Studies
- Social Work
- Natural Sciences
- Pharmacology
- Earth science
- Agriculture
- Agricultural Studies
- Computer Science
- IT Management
- Mathematics
- Investments
- Engineering and Technology
- Engineering
- Aeronautics
- Medicine and Health
- Alternative Medicine
- Communications and Media
- Advertising
- Communication Strategies
- Public Relations
- Educational Theories
- Teacher's Career
- Chicago/Turabian
- Company Analysis
- Education Theories
- Shakespeare
- Canadian Studies
- Food Safety
- Relation of Global Warming and Extreme Weather Condition
- Movie Review
- Admission Essay
- Annotated Bibliography
- Application Essay
- Article Critique
- Article Review
- Article Writing
- Book Review
- Business Plan
- Business Proposal
- Capstone Project
- Cover Letter
- Creative Essay
- Dissertation
- Dissertation - Abstract
- Dissertation - Conclusion
- Dissertation - Discussion
- Dissertation - Hypothesis
- Dissertation - Introduction
- Dissertation - Literature
- Dissertation - Methodology
- Dissertation - Results
- GCSE Coursework
- Grant Proposal
- Marketing Plan
- Multiple Choice Quiz
- Personal Statement
- Power Point Presentation
- Power Point Presentation With Speaker Notes
- Questionnaire
- Reaction Paper
- Research Paper
- Research Proposal
- SWOT analysis
- Thesis Paper
- Online Quiz
- Literature Review
- Movie Analysis
- Statistics problem
- Math Problem
- All papers examples
- How It Works
- Money Back Policy
- Terms of Use
- Privacy Policy
- We Are Hiring
Quality Management, Essay Example
Pages: 4
Words: 1229
Hire a Writer for Custom Essay
Use 10% Off Discount: "custom10" in 1 Click 👇
You are free to use it as an inspiration or a source for your own work.
Introduction
Quality management is the act of overseeing all tasks and activities that are needed in the maintenance of the desired levels of excellence. This includes creation and implementation of quality assurance and planning, as well as quality improvement and control. It can also be referred to as TQM (total quality management).
Methods of quality improvement
There are several methods of improving quality. This includes process improvement, product improvement and people based improvement. Below, we shall discuss some of the quality management methods and techniques which drive and incorporate quality improvement.
The ISO 9000 family standards are standards designed help an organization in ensuring that the needs of stake holders and customers are met. These standards have been published by the International Organization for Standardization and are implemented through the National Standards bodies while at the same time meeting the regulatory and statutory requirements. The ISO 9000 deals with quality management systems fundamentals, which includes the eight principals of management on which the standards of the family are based. It deals with the requirements which an organization that is wishing to meet the standards have to fulfill (Robert, 1993) .
Total quality management (TQM). This is a strategy of management that is used to embed quality awareness in the processes of an organization. It functions in the premise that the processes and the products is the main responsibility of all those who are involved with the consumption or creation of the services or the products that are offered by the organization. It capitalizes in the involvement of workforce, suppliers, customers and management for the purpose of meeting and exceeding the expectations of the customers (Adam, 1998).
Quality management/ project management strategies
The strategies most organizations use are:
Mistake-Proofing
This is a great strategy for companies that focus in high-volume production. As a company grows and becomes large in terms of production, it gets more prone to human errors. Mistake-proofing components of production and manufacturing, high-volume output is ensured and there will be guarantee that the produced product will be 100% up to standard.
This strategy should be used when the company is experiencing a boost in its production and sales volumes as many companies get exposed to error in production in such situations.
The major advantage of this strategy is that it minimizes the production of faulty products and hence reduces the quality cost.
A disadvantage with this strategy Is that it a tedious process and require a lot of time to completely ensure that all systems are in place for production of standard products (Gray & Morain, 2000).
Continuous Improvement
Change cannot be simply be embraced for the sake of it. A company would rather go for something that can be easier to improve. In view of this, it is a universal idea that common sense should guide in the company’s continuous improvement. One should over time analyze each element of production and identify areas which need improvement. Employees should be encouraged to give feedback as they are at a better position to do that (Langley, A. and van Alphen, 1993).
This is a strategy suits companies when they are advancing from infancy or its initial stages.
An advantage with this strategy is that it makes the company stay with up to date systems of operation hence ensuring that wastage due to usage of obsolete technology is minimized completely.
A disadvantage with this strategy is that: in circumstances whereby there are many ways of advancing systems it might be complicated in choosing the more appropriate and economical one as different systems work differently (Gray & Morain, 2000).
Employee Monitoring
The company’s workforce should be trained regularly. Tools for the job should be available and proper training on use of these tools should be given. Classes for training on new methods of work or new skills to reinforce ones performance should be given priority and encouraged by the management. The employees in the front line always impact the company’s bottom line; hence it is crucial to ensure that they are performing well. With this strategy, smart delegation is crucial and a management team that is well equipped.
This strategy suits the company in all its stages as employees are a great contributing factor in every stage of business survival.
A major advantage of this strategy is that it boosts employee morale and this reflects to better output. The needs of the employees are catered for hence they work efficiently and are satisfied with work and working conditions.
A disadvantage of this strategy is that it is a costly process which will need the company to dedicate its funds and time.
Strategies in quality management are often at best described by 4 classes of quality cost which are: internal failure, external failure, prevention costs and appraisal or inspection.
Quality cost- can also be referred to as cost of poor quality and it sometimes accounts to 20-30% of total sales. This is the cost of not performing tasks in the right way at the first time.
Types of Quality cost
In this context the producer incurs external failure costs when non-conforming or defective products are retailed to the consumer, who afterwards finds out the defect in the good. Such examples can be: transportation costs to return the product, replacement and warranty returns, if the consumer sues the company it might have to part with legal fees and sales lost as a result of spoiled name and reputation and customer confidence. The company incurs internal failure costs when it decides to engage itself in activities dealing with non-conforming products before the consumer buys them. Such costs may be: rework and scrap costs. These activities may lead to use of overtime, downgrading costs and in the end result to losses. Internal failures are can be rarely be seen by the customers in ordinary circumstances. These internal failures push up the unit costs of production and hence affect customers as they are forced to pay higher rates for the conforming products they buy (Robert, 1993) .
Appraisal or Inspection costs come about when the company checks, tests, confirms and finally measures the product conformance to customer expectations. Such costs are: maintaining quality control costs or upkeep of the quality assurance department.
Prevention costs come by when an organization engages in regulation on production on non-conforming products (Langley & van Alphen, 1993).
Though researchers have tried to study the issue of quality management, it has not been exhaustively done as there is need for more. This paper is an addition to the already done researchers.
To build a standard for future use of groups of the quality initiative one needs to fully understand the dynamic nature of all the aspects of the environment in which businesses operate and how variables influence their performance.
In order to have an impact on the employees of organizations they must be involved in drafting of all future standards that affect them (Robert, 1993) .
Barriers in establishing a future standard may be: technology, management styles, available resources in the organization to fully implement the standard proposed and the unwillingness of various individual to effect change.
Adam, J. F., (1998). “Understanding Evolutionary Processes in Non- Manufacturing Industries: Empirical Insights from the Shakeout in Pharmaceutical Wholesaling,” Evolutionary Economics 8, pp. 231–270.
Gray, R. & Morain, M., (2000) Total Quality Management that suits Employees . South Australian Commission, Adelaide.
Langley, A. & van Alphen, M. (eds) (1993) Proc. 2nd National Workshop on the Management and Risk Assessment American Society . Atlanta, Georgia.
Robert, S., (1993). The New GE: How Jack Welch Revived an American Institution. Homewood, IL: Irwin Business One.
Stuck with your Essay?
Get in touch with one of our experts for instant help!
Labor Demographics, Essay Example
The I.T Architecture, Essay Example
Time is precious
don’t waste it!
Plagiarism-free guarantee
Privacy guarantee
Secure checkout
Money back guarantee
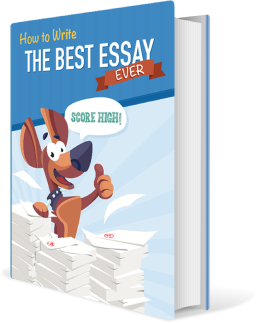
Related Essay Samples & Examples
Voting as a civic responsibility, essay example.
Pages: 1
Words: 287
Utilitarianism and Its Applications, Essay Example
Words: 356
The Age-Related Changes of the Older Person, Essay Example
Pages: 2
Words: 448
The Problems ESOL Teachers Face, Essay Example
Pages: 8
Words: 2293
Should English Be the Primary Language? Essay Example
Words: 999
The Term “Social Construction of Reality”, Essay Example
Words: 371
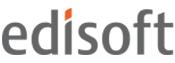
What is Quality Management?

What Are the Different Quality Management Methods?
What is a quality management system, what does the quality management system do, what is the role of a quality management system, what is the difference between quality control and inventory control, why is a quality management system needed, who needs a quality management system, what are the key components of a quality management system, what are the benefits of a quality management system, what are the benefits of a quality management system with erp, what are the features and functionality of a quality management system, what are the key types of quality management systems, what is the difference between a qms and an erp system, what are the benefits of a qms integrated with erp, how do you choose the right quality management system, get a fully integrated qms and erp solution with optiproerp and sap business one.
Quality management is used by organizations to ensure a product or service is consistent and meets certain standards. It is made up of four segments: quality planning, quality control, quality assurance, and quality improvements.
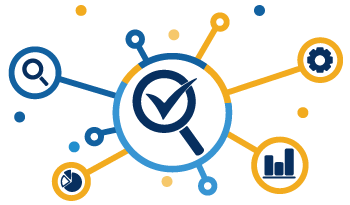
There are four main quality management methods as noted below. Each has its own advantages and disadvantages, and the right method depends on the organization’s structure, needs, and overall goals.
Standardized Systems
The federal government sets up standards, such as ISO certifications, that some organizations must follow according to the type of goods they produce (such as baby car seats.) Some businesses may not be required to use standards but do so anyway, as it helps their reputation or it aligns with their company’s objectives.
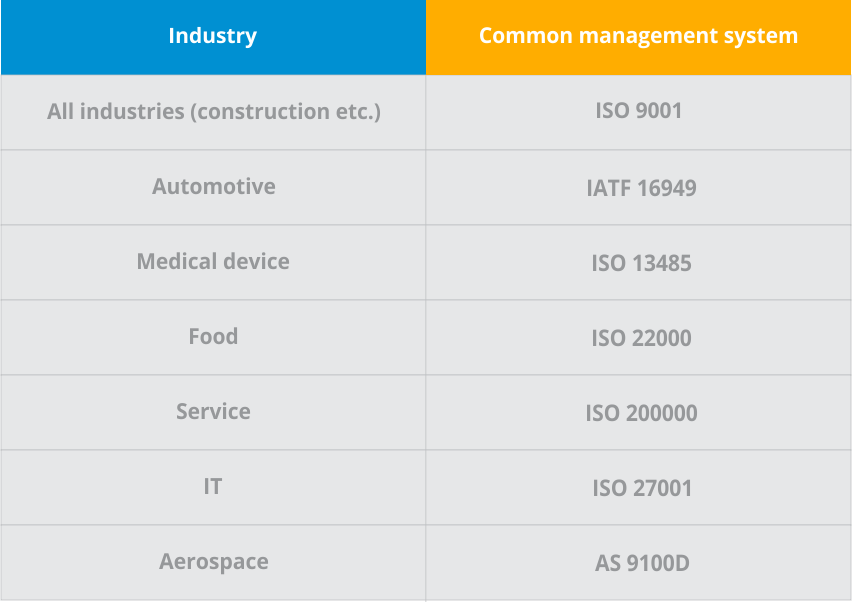
Total Quality Management (TQM)
When a company uses TQM, they want to improve quality across the organization. It takes into consideration the company’s overall quality goals and then looks at every process and other factors that affect quality to make positive change.
Six Sigma is a very structured and data-driven method for quality management. Its focus is to define, measure, analyze, improve, and control. It is often used by large product manufacturers and requires intense training.
Continuous Quality Improvement (CQI)
This method is just as the name indicates, it’s continuous. There is always room for improvement, and the business seeks to perfect its quality. CQI considers teams and individuals and how they impact quality. It includes Plan, Do, Check, and Act as its approach to quality, with people over processes being the focus.
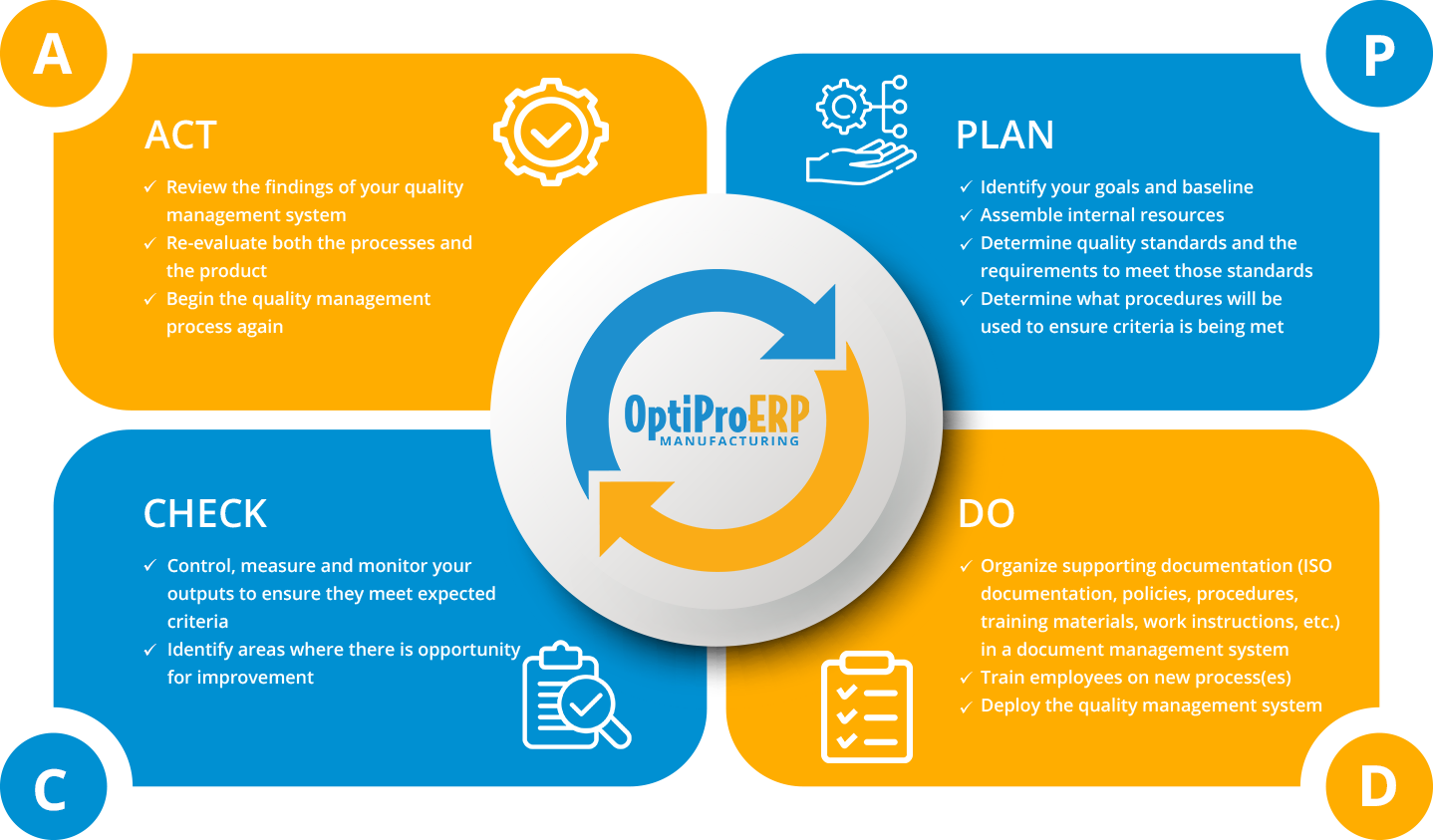
A Quality Management System (QMS) is a scheme of processes with the goal of making sure products are manufactured without any quality issues. It checks before, during, and after production to be sure all components and the final product meet industry and government regulations.
A quality management system can be handled manually, or with a software solution. It is broken down into two sections: quality assurance and quality control. Quality assurance is the act of carrying out inspections along the manufacturing process. Quality control includes inspections that help ensure customer expectations and industry standards are met – for example, by receiving feedback from customers, or conducting an inspection on the plant floor. Quality assurance is making sure your quality levels are met as the products are made, and quality control tests products after they are manufactured.
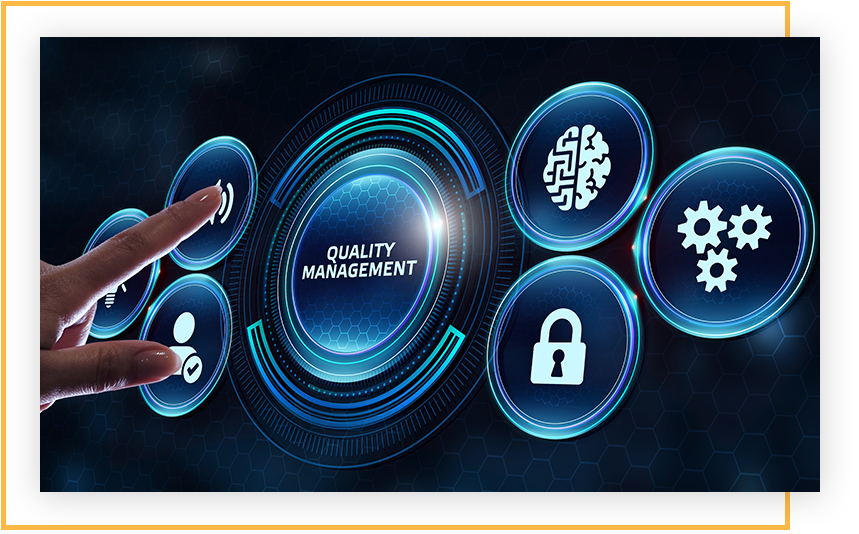
A quality management system should review products and their components throughout the production lifecycle, from receiving raw materials, to components in the WIP stage, to shipping the finished goods. The system will review how many products are made and determine if any were faulty. It should keep track of vendor products to ensure they meet quality standards – and if they don’t, they can be promptly returned. The system has inspection plans that examine people, products, and equipment.
A good quality management system will track any errors, keep an audit trail, find ways to correct any immediate problems, and fix anything needed to prevent future issues. It should be able to evaluate suppliers’ ability to deliver using key performance indicators (KPIs). A quality management system should keep track of any changes to policies and procedures as well as provide reports on anything related to the quality management process.
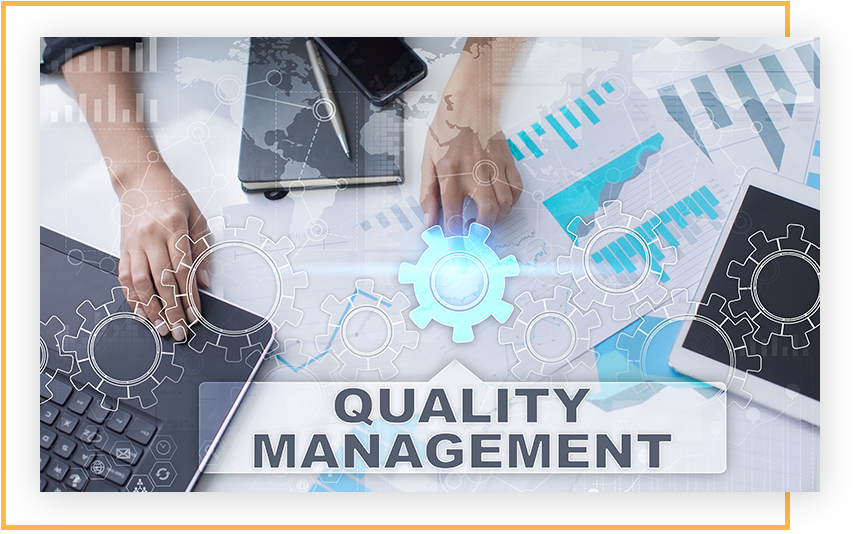
A quality management system’s role is to maintain the integrity of the company’s products so as to maintain a good reputation with customers. It’s a proactive measure to keep quality levels high and to ensure they meet or surpass regulatory, industrial, and customer standards.
QMS has the important role of providing manufacturers with a structure for tracking everything related to quality. When a good quality management system is in place, manufacturers feel more confident about their products. It helps them to define problems and inspect issues. In this way, manufacturers better control their processes, collect data, and analyze costs, problems, performance, etc.
Quality control is in place to ensure that standards are met by measuring quality levels and output. Quality control helps to keep manufacturers compliant with industry and regulatory standards by measuring metrics against the standards set. It plays an important role in maintaining a business’s reputation.
Inventory control helps to maintain optimized levels of materials and products on hand for manufacturers to minimize waste and identify damaged inventory at the source. Inventory control keeps processes streamlined and locates any problem areas. By identifying problems and keeping quality stock readily available, inventory control supports the quality control process.
A quality management system is needed to ensure manufacturers’ products consistently meet customer expectations. It provides an audit trail of all quality-related actions, which is helpful for your defense in case of litigation. A quality management system keeps track of customer feedback, issues, suppliers, documentation, risks, training records, equipment used, audits, and inspections.
The importance of Quality Management System resides in its potential to identify production issues, eliminate unnecessary steps in the process, and close gaps in performance, which in turn improves processes for lean manufacturing. Quality management systems are important to comply with ISO standards and develop a corporate culture geared toward quality.
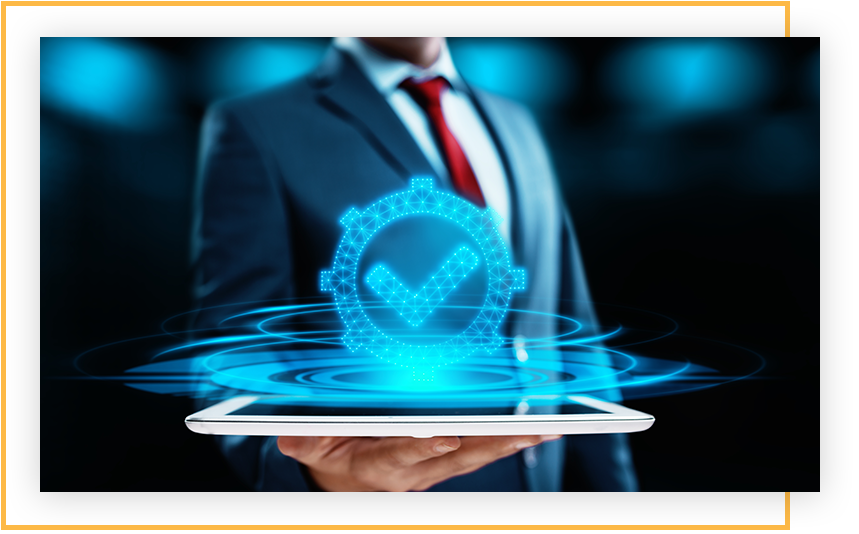
All manufacturers need a quality management system to make sure their products meet customers’ expectations. A quality management system also helps ensure responsibilities, schedules, relationships, contracts, and agreements are on par with industry standards.
A quality management system is important for manufacturers to manage their processes, keep all quality-related information in a central place, and document the controls in place, all with a view to improving collaboration between teams. It also helps to keep companies audit-ready, improves profits by eliminating errors and waste, lowers costs, increases performance, notifies suppliers quickly if their products are faulty, and maintains a culture of quality.
The key components of a quality management system are as follows:
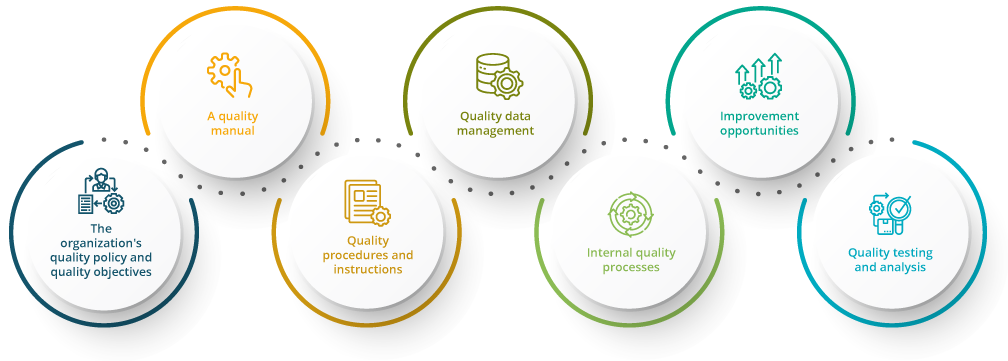
There are many benefits to using a quality management system. Below is a list of the most significant benefits.
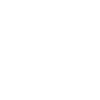
Greater Efficiency
With a quality management system, you gain control over processes to make them more streamlined and efficient.
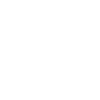
Increased Profitability
A quality management system helps to increase profitability by increasing the number of satisfied customers and making improvements to operations that help lower costs.
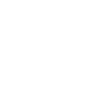
Improve Quality
Improve processes to reduce errors, remove substandard raw materials, incorporate controls, and increase accountability.
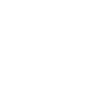
Reduce Costs
Eliminate costs associated with scrapped finished goods and reworked goods.
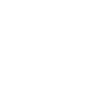
Meet Compliance Standards
With strict controls in place, manufacturers can meet both government and industry standards.
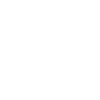
Enhanced Reputation
By consistently providing quality products, manufacturers gain a solid reputation that retains existing customers and attracts new ones.
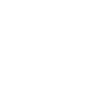
Better Collaboration
With coordinated processes and a single source of quality data, businesses with a good quality management system break down data silos and enjoy greater collaboration.
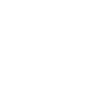
Greater Customer Satisfaction
Manufacturers with a quality management system produce high-quality products that satisfy customers.
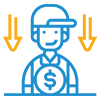
Reduce IT Needs
With an ERP system, the operations of every department in your organization are integrated into one system. Thus, IT doesn’t have multiple systems to maintain, which results in lower costs.
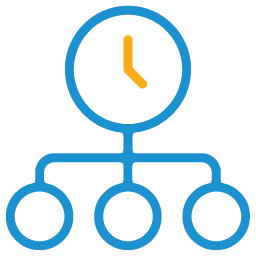
Since everyone is working from one system, data entry is simplified and errors are reduced. Everything resides in a single database so users have the latest information, updated in real time. All of this allows employees to work more efficiently.
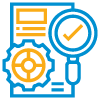
Improve Accuracy
Gain better accuracy by eliminating manual data entry and automating processes. Not having to re-enter data into separate systems also reduces mistakes.
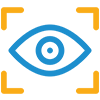
Increase Visibility
An ERP system works across the company so you have visibility into all departments. Sales can see what is happening with manufacturing, and procurement can see when inventory is running low. Everyone can work smarter and more efficiently. It also allows users to drill down into data to examine things closely. By having a greater quantity of data, better insight into company operations is achieved.
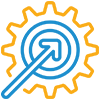
Simpler to Upgrade
When you only have one system to upgrade, it is much simpler than having multiple systems that may not integrate, or if they do, it is usually problematic when one or more needs to be upgraded. With ERP, all data is in a single database so it is easy to back up and incorporate back in once an upgrade is complete.
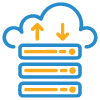
Greater Data Integrity
Due to increased accuracy and connectivity between departments, ERP provides greater data integrity. Since everything is stored in a single database and updated in real-time, you can count on the information being correct.
A good quality management system should include the following functionality:
End-to-end Quality Control
The system should be set up to quickly identify and resolve issues in receiving, production, and shipping., work center tracking, know how much was produced per work center and if there were any quality problems., material review board, this function tracks raw materials, work in progress, and finished goods to help procurement get the best deals and to quickly return supplies that are defective., mobile data collection, capture quality control information from anywhere using mobile devices, or the web., return to vendor, see when received goods are faulty so you can get them back to the supplier quickly., inspection plans, use quality control inspection plans, checklists, and tests to check people, products, and equipment., nc and capa, be able to track and keep an audit trail of non-conformances as well as corrective and preventative action processes., aql and rql sampling, carry out 100% inspection or sampling routines for accepted quality levels (aql) and rejectable quality levels (rql) throughout processes., traceability and recall reporting, implement forward and backward tracing of all movements of a serial or lot number., vendor performance evaluation, use kpis to report on how well vendors are performing., document control, document internal controls, security, and quality measures, as well as document searches and retrievals for audits or inspections., change management, receive multi-level notifications and historical tags with automated changes to policies, procedures, and more..
Startup companies often use a manual method for quality management which can become difficult to sustain as they grow. There are also stand-alone quality management systems, as well as ERP systems that include quality management as a module.
When a quality management system is part of a manufacturing ERP system , it can fully manage and streamline your quality management and compliance processes throughout your supply chain, from purchasing and receiving to production and shipping.
A quality management system manages only the quality control and assurance processes within a company. An ERP system, by contrast, has modules that handle departmental operations and work together with the quality management module. The whole organization can collaborate to ensure products and processes are of the highest quality.
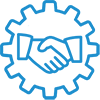
End to End Quality Control
When a quality management system is integrated with ERP, it allows the whole organization to be quality-focused. Capturing and coordinating information accurately ensures you’re continually meeting quality and regulatory standards. ERP helps to unify processes, better coordinate workflows, and improve the sharing of data to break down silos.
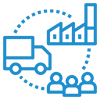
Supply Chain Optimization
A QMS in ERP lets you streamline post-inspection processes to quickly determine when received goods are faulty. You can set up automated audits and checks of incoming raw materials to ensure they meet the agreed-upon quality standards. It also analyzes supplier performance to make better decisions and reduce costs. ERP that is integrated with shipping, barcode, and RFID technology lets manufacturers track the movement of goods across the supply chain.
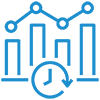
Real-time Data
Improve the speed and accuracy of data collection and quality management. Capture and evaluate inspection and QC test results from the shop floor or warehouse in real-time and have visibility from anywhere at any time. Being able to stop production due to a quality issue before or early into production instead of further down the line provides big cost savings and reduces frustrations.
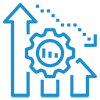
Reduce Complexity
Manage processes, data collection, along with preventive and corrective actions easily in one system. With real-time tracking and insights, manufacturers can manage complex supply chains to ensure the quality of goods always meets the standards set.
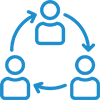
Staff Collaboration
ERP provides a single system to fully manage and streamline your quality management and compliance processes throughout your supply chain, from purchasing and receiving to production and shipping. Quality is important across the organization and with ERP software, staff can easily collaborate, as they are all working with the same information from a single database.
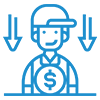
Lower IT Costs
ERP cuts down on IT costs, since there is only one platform to maintain instead of multiple disparate solutions. When it is time to upgrade, it can be very challenging if there are many stand-alone systems integrated together. Data must be backed up from each system before the upgrade. Afterward, trying to get them all to work together again can be very time-consuming.
There are lots of options out there for QMS and ERP systems, so how do you choose the right one? Below are some of the key criteria to consider.
Industry Experience
Does the company have much experience in your industry? What other companies similar to yours have they worked with? Can they provide references? Can they speak knowledgeably about the quality requirements your company must meet? You’ll want to feel confident that not only can the software meet your needs, but that the people who will be providing the installation and training have industry knowledge.
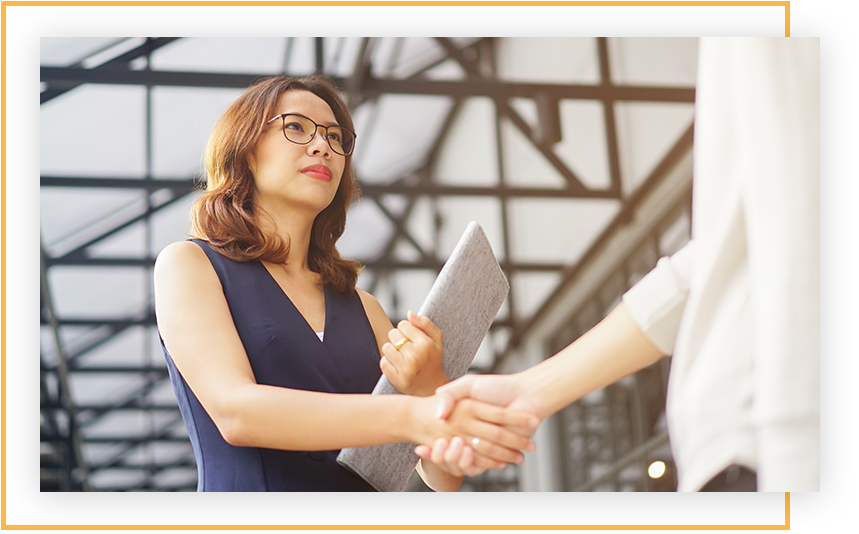
Functionality Needs
You’ll want to understand what the software can do to determine if it will meet the needs of your business. For instance:
- Does it provide the quality compliance requirements necessary for your industry?
- If needed, can it easily integrate with your other system(s)?
- Does it track all non-conformances and provide a full audit trail?
- Does it offer Correct and Preventative Action management or CAPA that gets to the root cause analysis of a problem and helps you take corrective actions?
- Does it provide AQL (Acceptable Quality Limit) and RQL (Rejectable Quality Level) sampling throughout processes?
- Does it provide Document Control to record all of your quality activities?
- Does it display KPIs to help you understand how well suppliers are performing?
- Does it collect data from anywhere using mobile devices or the web?
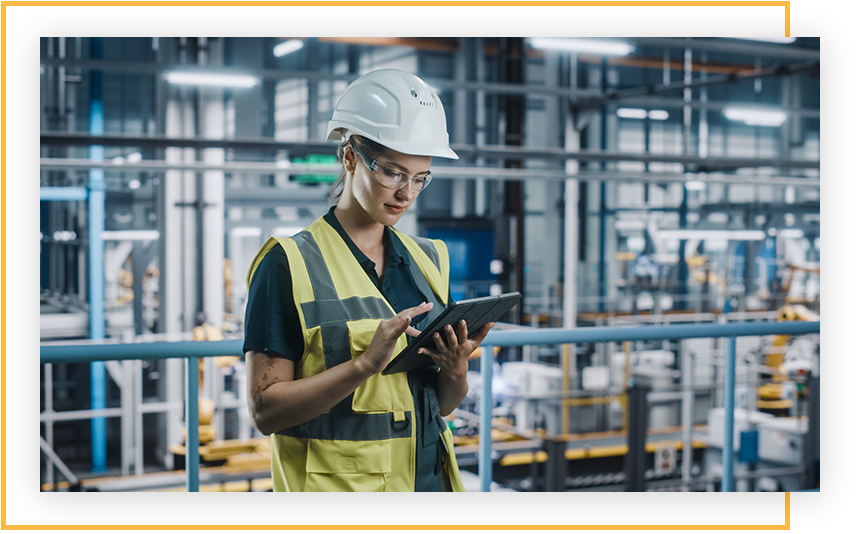
It’s important to have good visibility of key quality events in real-time to resolve issues proactively. You’ll want to be able to see what is happening across the business so you can truly understand issues. You should be able to monitor vendor performance and employees to see if they are compliant or if they need additional training.
OptiProERP is a complete manufacturing ERP solution embedded into SAP Business One. It provides business and manufacturing functionality, including robust quality management features . OptiProERP is mobile-friendly and cloud-based. It provides demand forecasting, IoT integration, machine learning, and AI. OptiProERP also includes e-commerce and warehouse management modules.
Manufacturing ERP Resources

Achieve Manufacturing Excellence with Cloud ERP: A Guide for Small and Midsize Manufacturers
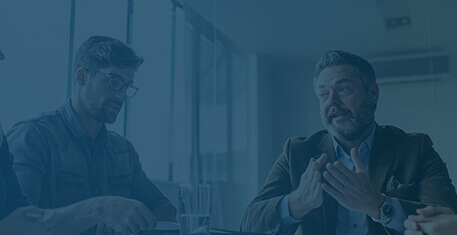
60-Second ERP Guides
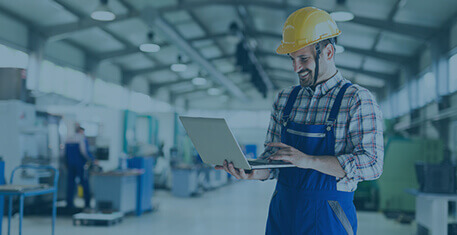
A Roadmap for ERP Selection in Today’s Digital World
See optiproerp’s best-of-breed solution in action.

About OptiProERP
OptiProERP is a leading global provider of industry-specific ERP solutions for manufacturers and distributors. Backed by deep industry expertise and driven by a commitment to customer service, OptiProERP delivers best-in-class, end-to-end industry solutions built on the market-leading platform for small and midsize enterprises, SAP Business One.
OptiProERP, as part of eWorkplace Manufacturing, is SAP’s strategic industry partner for manufacturing and distribution and its first OEM partner as part of SAP’s global PartnerEdge Program.
Ready to learn more? Request a personalized demo now!
Request a Personalized Demo
Ready to see more? Request a personalized demo now!
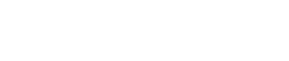
- Privacy Policy
- Terms of Use
© 2024 OptiProERP Software ®
We want to hear from you!
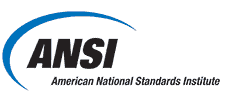
Understanding & Improving Quality Control in Manufacturing
In the dynamic landscape of modern manufacturing, where efficiency, reliability, and customer satisfaction reign supreme, quality control emerges as the linchpin that safeguards against defects, optimizes processes, and ensures the delivery of products that meet or exceed expectations.
The Importance of Quality Control
Quality control serves as the bedrock upon which the reputation and success of manufacturing enterprises are built. By meticulously monitoring every stage of the production process, from raw material acquisition to final product inspection, quality control mitigates the risk of defects, minimizes waste, and upholds the integrity of the brand. Beyond mere compliance with standards, it fosters trust and confidence among consumers, driving loyalty and repeat business while safeguarding against costly recalls and reputational damage.
Quality Control vs. Quality Assurance
While often used interchangeably, quality control and quality assurance are distinct yet complementary concepts within the broader framework of quality management. Quality control focuses on the identification and rectification of defects in the finished product, employing techniques such as statistical process control, inspection, and testing to ensure adherence to predefined standards. In contrast, quality assurance encompasses the proactive measures implemented throughout the production process to prevent defects from occurring in the first place. It involves the establishment of robust processes, procedures, and protocols aimed at continuously improving product quality and operational efficiency, thereby minimizing the need for corrective action downstream.
Improving Quality Control
Enhancing quality control necessitates a multifaceted approach that addresses both systemic issues and individual processes within the manufacturing ecosystem. Key strategies to improve quality control include:
- Embracing a Culture of Quality: Cultivate a corporate culture that prioritizes quality at every level of the organization, from the shop floor to the C-suite. Instill a sense of ownership and accountability among employees, empowering them to identify and address quality concerns proactively.
- Implementing Robust Process Controls: Standardize processes, procedures, and workflows to minimize variability and enhance predictability. Utilize tools such as process mapping, flowcharts, and control plans to identify potential sources of variation and establish effective controls to mitigate risks.
- Leveraging Technology: Embrace cutting-edge technologies such as automation, artificial intelligence, and data analytics to streamline quality control processes and enhance accuracy. Deploy advanced inspection systems, sensor-based monitoring devices, solenoid valves for precise control of fluid flow, and predictive analytics platforms to detect deviations in real-time and preemptively address quality issues before they escalate.
- Continuous Training and Development: Invest in the ongoing training and development of employees to ensure they possess the requisite skills and knowledge to perform their roles effectively. Provide comprehensive training programs on quality control principles, methodologies, and tools, and encourage continuous learning and skill enhancement through workshops, seminars, and certifications.
By embracing these strategies and fostering a culture of continuous improvement, manufacturers can elevate the effectiveness of their quality control efforts, drive operational excellence, and position themselves as leaders in their respective industries. In doing so, they not only enhance customer satisfaction and loyalty but also bolster their competitiveness and long-term viability in an increasingly demanding marketplace.
Contributing Author: Larry Rayhon, Senior Director of Product Engineering, Marotta Controls
Larry Rayhon is Senior Director of Product Engineering at Marotta Controls . For nearly 30 years, Rayhon has contributed to the success of key programs for customers and has recently taken the roll in leading all operations for Marotta’s power and actuation business unit. Joining Marotta in 1988, he spent 10 years leading the development group and transitioning many key programs from development to production.
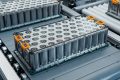
Leave a Reply Cancel reply
Your email address will not be published. Required fields are marked *
This site uses Akismet to reduce spam. Learn how your comment data is processed .
Total Quality Management Implementation Exploratory Essay
A framework for tqm to achieve business excellence, total quality management from theory to practice: a case study, critical implementation issues in total quality management, achieving the organizational change necessary for successful tqm.
Total Quality Management (TQM) is a set of quality and management tools employed in order to increase the performance of a business by reducing losses and increasing turnover. It aims at continually improving the quality of delivery of goods, services and all the functions of a business venture. This includes the interaction between all the sections of a firm as well as the individual sections themselves.
Generally, the objective of TQM is to achieve an overall efficiency that is higher than the individual productivity from the components, such as design, planning, production, customer service approaches, and staff participation. Customer satisfaction and incessant improvement are the fundamental beliefs of the TQM strategy.
TQM cannot function effectively without the necessary changes being taken on the structure and functioning of the organization by its top management. Such changes include adherence to quality in planning, control and improvement, these can be achieved through numerous channels, for example, continuous improvement can be achieved by undertaking work-based training on a regular basis.
Quality management is involved with the prevention of problems happening by putting in place attitudes and controls that may make such prevention a success.
The core aspect of quality is to get it right the first time, and to meet the needs of the customer every time, by engaging everyone in the firm. TQM is therefore a conception of management that utilizes the resources and opportunities in an organization in the way possible through continuous improvement.
Elements of TQM
The implementation of a TQM is influenced by a range of indicators, both financial and non-financial. These affect the various aspects of TQM such as a reduction in defect frequencies, increased client satisfaction, increased output, and reduced order cycle time.
Fiscal indicators of a TQM include market share, profits, defect percentage, performance and stock turnover etc, while the non-fiscal indicators are customer satisfaction, innovation, skill improvement, reliability, and talent development, among others.
These parameters are vital to adjust the infrastructure, (firm and systems), reward and acknowledgment system or hygiene aspects (human components) in place to set up and nourish the TQM characteristics.
TQM elements are grouped into three main categories: Technologies (tools), Organization (systems), and People, these affect the financial and non-financial performance of the organization.
Technologies and Tools
Measures of technology and tools include benchmarking, data management, continuous improvement, problem solving, and continuous improvement, among others. Of these, TQM studies suggest that the most important is continuous improvement.
Organization (systems)
Organizational aspects of a TQM strategy include culture, organizational structure, communication, shared vision, and performance management. Again, TQM studies suggest that culture is the most important factor in achieving a TQM.
Factors relating to people include leadership, management responsibility, empowerment, training and education, and team learning. Team learning is the most vital TQM element among these.
An efficient application of the TQM elements results into increased productivity of the organization indicated by financial performances such as increased stock turnover, increased market share and profits, and a reduction in defect rates and non-financial performances.
Non-financial performances include customer satisfaction, delivery reliability, innovation, reduced order cycle time, and workflow improvement as some of the non-financial performances.
The mentioned elements of TQM have been successfully by Apple, the company has encouraged innovation and continues to a market leader in the smartphone and PC market.
Apart from technology, Apple has a clear sense of the customer needs and continues to ensure that customer satisfaction is its core aim. This has enabled it to attain the position of the world’s second largest company despite being in danger going out of business a few years ago.
Manufacturing firms across the world are currently spending a substantial amount of time and money to improve the quality of their products, this has been brought by an increase in the expectation of consumers and has led to an increase in the quality of goods supplied in domestic markets.
A number of manufacturers have acted on these challenges by trying to employ some approaches of quality improvement procedure on a systems-wide basis. These approaches differ to some level but they share a fundamental set of features that represent the core of any quality improvement method.
The process of ‘total quality’ commonly includes:
- Plainly defining the notion of quality and coming up with its measurement standards;
- Carrying out quality training for the whole organization;
- Coming up with meaningful parameters of quality for both the work processes and for each employee;
- Coming up with a system to take corrective measures whenever there are problems with product quality;
- Implementing efficient management practices to increase employee participation; and
- Establishing an organizational culture and reward scheme that enforces the principle that quality should be everyone’s core concern.
When a firm implements a quality improvement process, it commonly does so with the help of an external party. The first part of this process involves quality training, explaining the standards and expectations, establishing parameters for quality improvement, and establishing procedures to do away with threats to quality after their identification.
The second part is the implementation phase since the organization starts the use of training, standards, taking corrective measures and management practices to continuing daily processes. To achieve success in a quality improvement process, an organization needs to institutionalize the process into the firm’s practice, many organizations struggle or fail to realize their goals in this area, hence failure in quality improvement.
In order to improve a firm’s products, it must require, motivate, and effect change in all of its sectors. For management to start a TQM, the procedure is comparatively straightforward. The first step is for the organization to underline the reason for quality improvement; the second stage is to come up with a strategy for the quality improvement.
Thirdly-, management needs to employ a quality improvement process that is in tow with the firm’s needs. The quality improvement process can be developed internally or contracted from external sources and in order to ensure that the plan is successful, the management must note the following
- Leadership must lead by example;
- The more rapid and complicated the changes are, the greater the help needed;
- Managers must give continuous feedback to their seniors;
- Messages given to staff must be devoid of any ambiguities;
- The management and workers must show openness when handling problems; and
- Meetings and paperwork must be minimized so that management has ample time to exhibit quality conduct to their workforce.
Failure to implement sound TQM policies can lead to a decline in performance by an organization, this has been proved by a number of companies.
For example, Enron, a US energy company that was a market leader and was named ‘America’s Most Innovative Company’ for six years and with revenues of more than $100 billion in 2001, however, the company wound up operations in 2006 as a result of accounting frauds that were planned and executed by its managers, a fraud that became to be known as the Enron scandal.
The main idea of the article under consideration is whether the Total Quality Management (TQM) is an opportunity to improve business or it is a strategy which provides only theoretical knowledge and may never be use in practice.
TQM key principles may be failing only in case when the company managers failed to apply those in complex or did not understand the main idea of those. The main points which each company should remember if it wants to apply TQM principles are the lessons.
In order to achieve the results promised by the proponents of the TQM approach, it is important to have knowledge of the key TQM principles, these are: efficient top management and commitment, client satisfaction, staff participation and motivation, continuous improvement, collaboration with suppliers, and recognition of the importance of quality in realizing TQM goals.
For a successful implementation of TQM, the organization needs to have the following lessons:
- It is important that organizations clearly understand the meaning and implications of TQM before implementing it. Before implementing a TQM, the management needs to identify its targets and the mode of implementation;
- Establish a culture that can sustain and support the implementation of a TQM. Many firms succeed in committing to total quality by employing the principles mentioned earlier, but fail in cultivating a culture that promotes quality improvement;
- TQM implementation should be matched with the firm’s strategic priorities, competitiveness, and objectives;
- Take note of the most important things- time and effort. Management should target achievable, practical, and real goals instead of trying to cover many elements at a time;
- TQM implementation should be aligned to the needs of the individual organizations and these are normally unique to each organization;
- Take a holistic approach as TQM is a complex process that requires an effective strategy to succeed. TQM is so wide and incorporates many disciplines and an approach that encourages interaction between these disciplines must be adopted;
- Remember that the term ‘Total Quality Management’ communicates the concept of quality improvement activities with stress on the word ‘total’ and a wide definition of ‘quality’;
- There is need to understand that TQM is not a solution for all aspects of quality, the organization must understand the extent to which this strategy will improve quality and improve productivity.
The TQM strategy is a good advisor in the company management. A manager should just correctly understand TQM principles and properly apply those. It is also important to remember that the principles should be integratable. Those who fail to understand the main principles of the TQM framework and the lessons are unable to use this strategy. Even if they try, they are not sure to succeed with it.
There are a lot of examples when a company managed to succeed with the help of the TQM and its principles. For example, the Coca Cola Company strongly commits leadership, focuses on customers, involves and empowers employees, provides continuous improvements in different spheres, increases and supports partnerships, and considers quality as a strategic point in planning business.
With the help of the TQM use the company is a leader in the beverage drinks production all over the world.
Implementation of a TQM is one of the most challenging tasks in an organization. It is not rare to find organizations failing in their attempts to improve the quality of goods and services, these failed companies are being pushed out of the market. Companies are using quality to gain a competitive advantage over the others.
Often, the reason for the failure of implementation of TQM is in the fact that their approach bears little similarity to the conventions. An example of such cause of failure is in the development of standards, standards are usually control-oriented methods controlled by the top-level management with little involvement of the employees.
The management uses these standards to control their staff. Training changes to a corrective activity whenever the set standards are not followed. Conceptual weakness is one of the main mistakes provided by the companies which want to apply TQM principles. The failure to understand properly control-oriented methods, training and motivation results in bad consequences for the company implementation.
Another type for failure is s design failure, this occurs when the TQM concept is convincing but the plan and/or implementation is not carried out in the right manner. When TQM systems are not designed with the organizational needs in mind, chances of failure are higher. Design failures are an earlier warning that the implementation will fail too.
The third form of failure is an implementation failure. This occurs when the concept and design are convincing, but the change agent and/or the top-level management do not comprehend the intricacy of organizational change and innovation required. Similarly, it may be caused by the failure to allocate funds for supporting the realization of the TQM strategy.
The main failures mentioned above should be considered by any company which desires to apply TQM principles in practice. Before considering TQM principles the managers of the company should check the most commonly occurred mistakes. It is obvious that it is impossible to run a successful business without standards and control. Furthermore, motivation should be properly stated.
Employees should be encouraged to do something new. The communication should not be organized from top to bottom only. One of the most frequently occurred failures connected with the TQM applying is an implementation failure. The main reason is when conceptual and design elements are correct, but the organizational and cultural change is not understood in a proper way.
One of the best examples of failure to understand the implantation of the TQM principles and the organizational change may be considered via the Boeing Company. It failed to provide the organizational change properly which made it possible for the Airbus Company come to the fore.
This company lost its market share in 2006 because the organizational and cultural changes were not properly considered and the company had to review its positions to return to the previous positions.
The TQM Approach of Asset Management
This approach recognizes that apart buildings, land, machines or funds in the bank, an organization’s assets include its workforce, customers, community, corporate culture, etc. A sound management of these assets will increase the productivity. An example is Delta Airline’s that supports its employees to give satisfactory services to customers and this has led to an excellent financial record.
- Chicago (A-D)
- Chicago (N-B)
IvyPanda. (2023, December 12). Total Quality Management Implementation. https://ivypanda.com/essays/total-quality-management-implementation/
"Total Quality Management Implementation." IvyPanda , 12 Dec. 2023, ivypanda.com/essays/total-quality-management-implementation/.
IvyPanda . (2023) 'Total Quality Management Implementation'. 12 December.
IvyPanda . 2023. "Total Quality Management Implementation." December 12, 2023. https://ivypanda.com/essays/total-quality-management-implementation/.
1. IvyPanda . "Total Quality Management Implementation." December 12, 2023. https://ivypanda.com/essays/total-quality-management-implementation/.
Bibliography
IvyPanda . "Total Quality Management Implementation." December 12, 2023. https://ivypanda.com/essays/total-quality-management-implementation/.
- Commitment of Top Management in TQM
- Total Quality Management (TQM) Implementation: The Case of ADNOC
- Total Quality Management (TQM) as a Significant Issue in the Contemporary Strategic Management
- Implementation of Total Quality Management (TQM): Toyota Case Study
- TQM in Dubai Metro System
- Comparing TQM with ISO Standards
- Comparing a TQM Implementation in Toyota Motor Company and Emirates Airlines
- Understanding the Obstacles to TQM Success
- Total Quality Management: Advantages and Disadvantages
- Total Quality Management: Origins and Evolution of the Term
- Improved Work Environment for Employees Working at a Production Plant
- Emergency Management in Organizations
- The Novelty of Teams
- Organization Learning and Information Technology Management
- A Process for Practicing Design Innovation
What caused Dubai floods? Experts cite climate change, not cloud seeding
- Medium Text
DID CLOUD SEEDING CAUSE THE STORM?
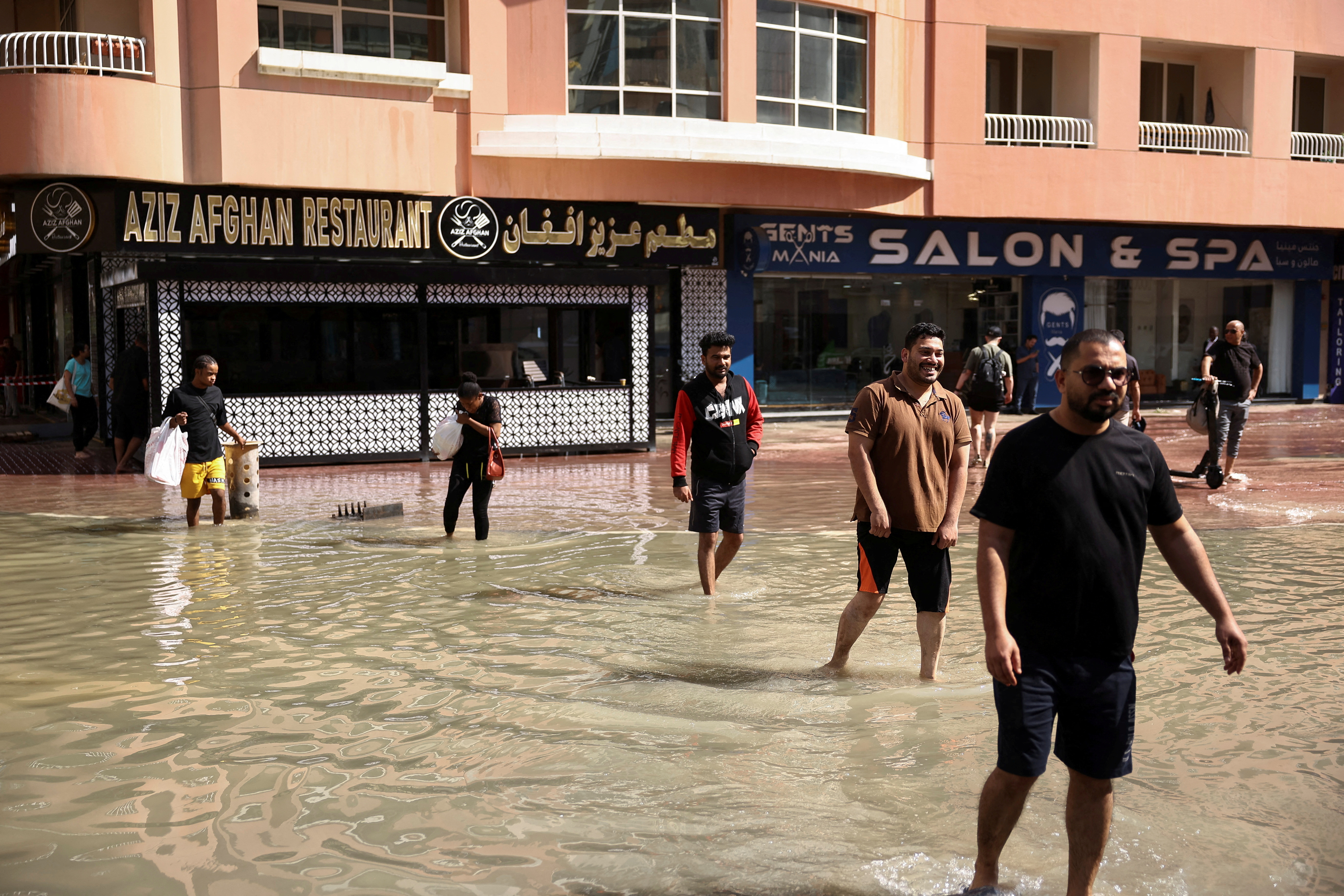
CAN'T CREATE CLOUDS FROM NOTHING
Sign up here.
Reporting by Alexander Cornwell; editing by Maha El Dahan and Alexandra Hudson
Our Standards: The Thomson Reuters Trust Principles. New Tab , opens new tab
China General Nuclear Power Group (CGN) has secured its first yuan-denominated trade finance to import Chinese PV modules for a solar plant in Brazil, official media said on Friday.
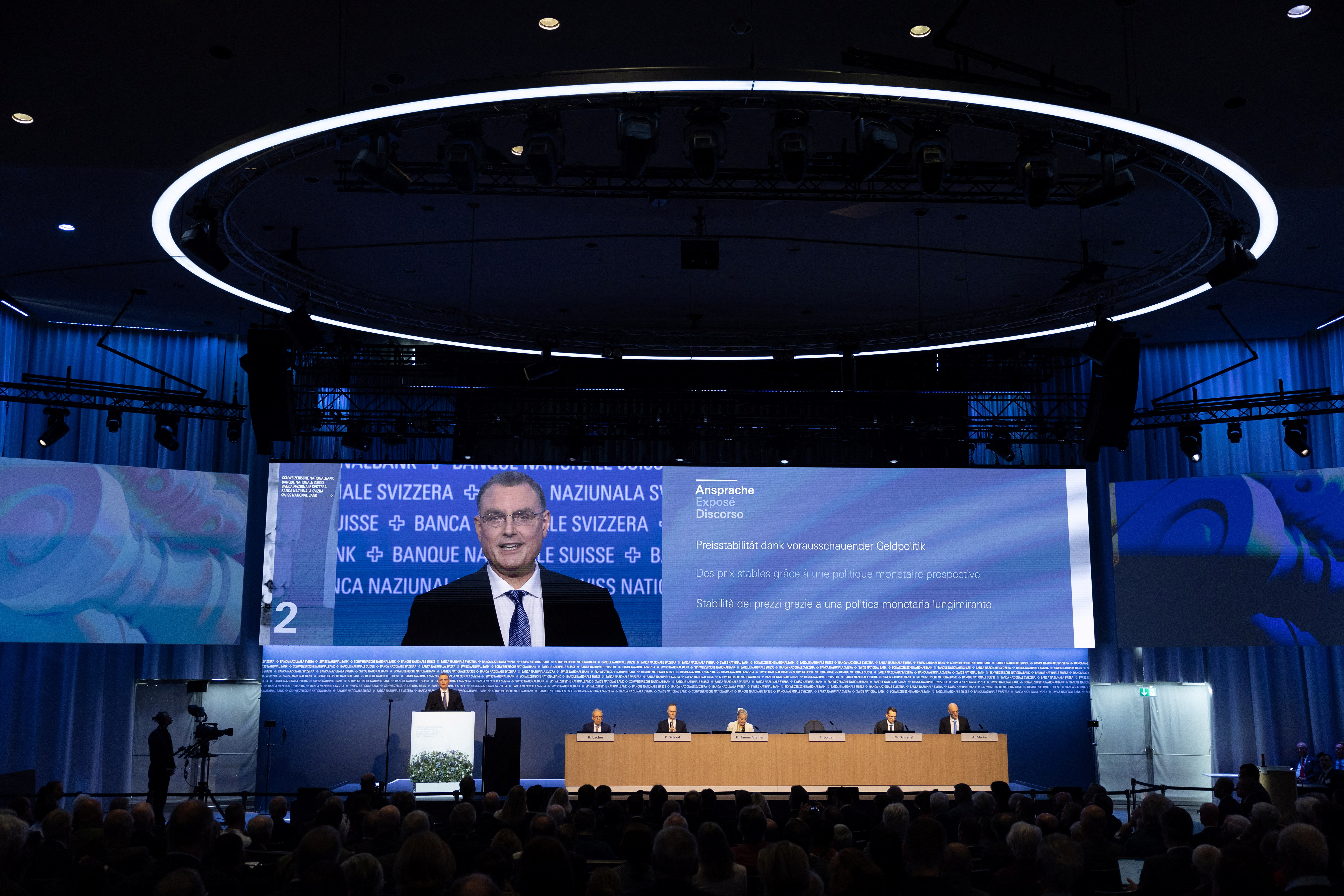
World Chevron
A British man has been charged over alleged hostile state activity intended to benefit Russia, including by allegedly recruiting others for an arson attack on a Ukrainian-linked commercial property in London.
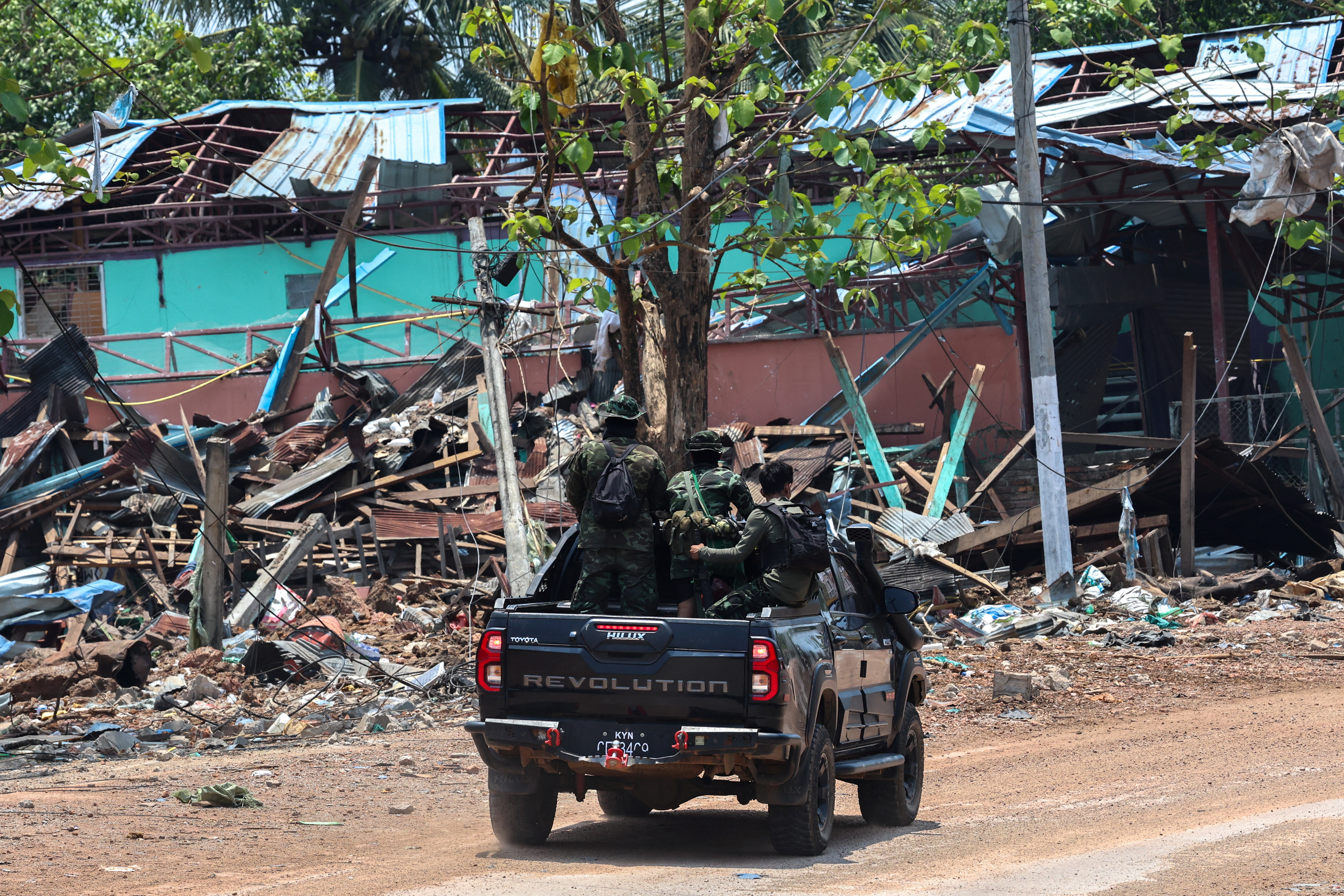
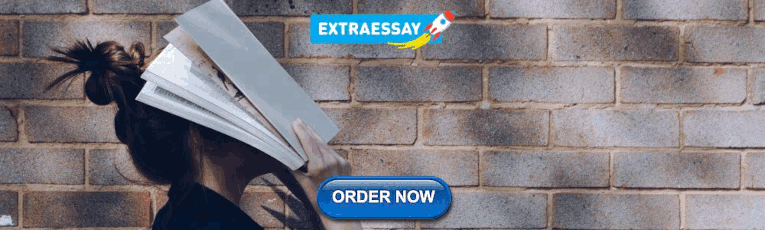
IMAGES
VIDEO
COMMENTS
Introduction. Quality management activities in organizations are undertaken to ensure that quality in its products is achieved and maintained within an unacceptable budget 1.It is an activity that is closely dependent on the feedback from the organization's clients, thus the quality management concept involves establishing channels for relaying customer feedback for which it requires that ...
40) identifies quality management as an approach whose main focus is to improve, not only quality but performance as well in an effort towards meeting or even exceeding the expectations of the customers. Generally, quality assurance entails four major aspects, which include quality assurance, quality control, quality planning in addition to ...
Quality management systems come in various guises, but they all share the same set of characteristics. They aim to identify potential hazards early in the process and to improve them over time. Determining which is the right QMS for you can be a complicated process and depends on your company's unique needs and objectives.
Quality management serves as a cornerstone for many enterprises, extending beyond the pursuit of superior product or service quality. It encompasses a holistic approach, incorporating quality planning, quality control, quality assurance, and quality improvement. The focus extends not only to the final output but also to the methodologies ...
Quality Glossary Definition: Total quality management. A core definition of total quality management (TQM) describes a management approach to long-term success through customer satisfaction. In a TQM effort, all members of an organization participate in improving processes, products, services, and the culture in which they work.
Total quality management is a complex notion covering human, product, and technological process as the basic dimensions leading to constant improvement of the quality of services and products. We will write. a custom essay specifically for you by our professional experts.
What are quality management principles? Embedded at the core of any quality management system (QMS), quality management principles (or QMPs) are a set of universally applicable principles, distilled from years of theoretical development and practical application.Their structured approach provides guidance for organizations to define objectives, establish processes and develop systems to manage ...
6.1. General conclusions. Quality 2030 consists of five collectively designed themes for future QM research and practice: (a) systems perspectives applied, (b) stability in change, (c) models for smart self-organising, (d) integrating sustainable development, and (e) higher purpose as QM booster.
Introduction. This paper is to provide a general understanding of Total Quality Management, a concept that is. aimed at ensuring quality with continuous improvement. It takes Oakland's "Total ...
Quality management is about making organisations perform for their stakeholders - from improving products, services, systems and processes, to making sure that the whole organisation is fit and effective. Managing quality means constantly pursuing excellence: making sure that what your organisation does is fit for purpose, and not only stays ...
Total Quality Management is the concept of processes and integration all of functions in an organization in order that to focus on quality control and approach to long-term success will continue improvement in all aspects but not short- term goal. TQM of business plan began in 1980 in the United States. It was popular until early 1990.
Total Quality Management - TQM: Total Quality Management (TQM) is the continuous process of reducing or eliminating errors in manufacturing, streamlining supply chain management , improving the ...
The purpose of this paper is to analyze the evolution of total quality management (TQM) models, frameworks, and tools and techniques in higher education (HE) over the last thirty years from 1991 till 2020, based on a literature review,30 articles from 52 journals were used to perform this detailed literature review. For the detailed analysis ...
Quality Management was a natural offshoot of industrialization. Quality management became necessary to help reduce the quantity of defective products arising from production processes. Companies that managed to increase the quality of their products and to reduce defects in their finished products remained profitable.
The Importance Of Quality Management. With the development of science and technology and the needs of market competition, more and more companies begin to pay attention to quality management. In the process of enterprises' development, the quality is the key to success or failure of any companies (Mile, 2004).
1) Quality of design. Quality of design measure the functionality of a product or services. It is the decision of designer to include or exclude certain production features. The customer really measures quality through appearance, operation and reliability. 2) Quality of performance.
The elements of quality management include focus on the customer, strategy, teamwork, continual commitment and a scientific approach. Other elements are continuous improvement, training and education, control and obsession with quality (Hakes, 1991). We will write a custom essay on your topic. 809 writers online. Learn More.
Quality management is the act of overseeing all tasks and activities that are needed in the maintenance of the desired levels of excellence. This includes creation and implementation of quality assurance and planning, as well as quality improvement and control. It can also be referred to as TQM (total quality management).
A Quality Management System (QMS) is a scheme of processes with the goal of making sure products are manufactured without any quality issues. It checks before, during, and after production to be sure all components and the final product meet industry and government regulations. A quality management system can be handled manually, or with a ...
Full Citation. "Partial quality management: An essay.". A serious gap is emerging between what is espoused as total quality management and what is actually being implemented. Examples of actual implementation failures are given. In addition to affecting the offending firms, these gaps threaten the viability of the quality management ...
Quality Management Essay. Executive Summary This report shows the use of Quality management techniques that are essential in the growth of performance in the field of manufacturing and services in business firms. Effective quality management can underpin organizational success. It is a field that is relatively new and growing market as it ...
The Quality Management Systems stipulated in the various standards gives the management framework that enables a company to institute necessary control measures to tackle risks, evaluate, and assess progress of the company. We will write a custom essay on your topic.
What Is Total Quality Management Management Essay. Total Quality Management is an essential tool that makes an improvement reaction to firms and companies. It is a technique of managing the future outcomes, and it does consist more features than just ensuring product and service quality, as it is a technique of running people and business ...
Key strategies to improve quality control include: Embracing a Culture of Quality: Cultivate a corporate culture that prioritizes quality at every level of the organization, from the shop floor to the C-suite. Instill a sense of ownership and accountability among employees, empowering them to identify and address quality concerns proactively.
Total Quality Management (TQM) is a set of quality and management tools employed in order to increase the performance of a business by reducing losses and increasing turnover. It aims at continually improving the quality of delivery of goods, services and all the functions of a business venture. This includes the interaction between all the ...
A storm hit the United Arab Emirates and Oman this week bringing record rainfall that flooded highways, inundated houses, grid-locked traffic and trapped people in their homes.