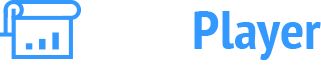
- My presentations
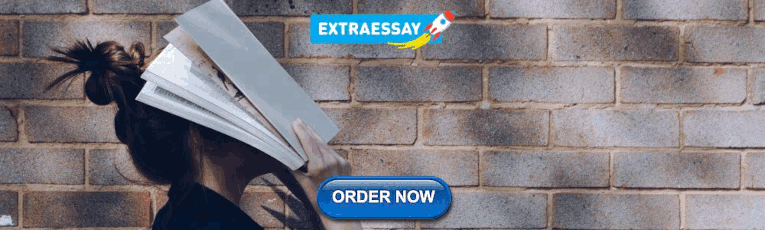
Auth with social network:
Download presentation
We think you have liked this presentation. If you wish to download it, please recommend it to your friends in any social system. Share buttons are a little bit lower. Thank you!
Presentation is loading. Please wait.
Basic Seven Tools of Quality
Published by Angel Cashmore Modified over 9 years ago
Similar presentations
Presentation on theme: "Basic Seven Tools of Quality"— Presentation transcript:
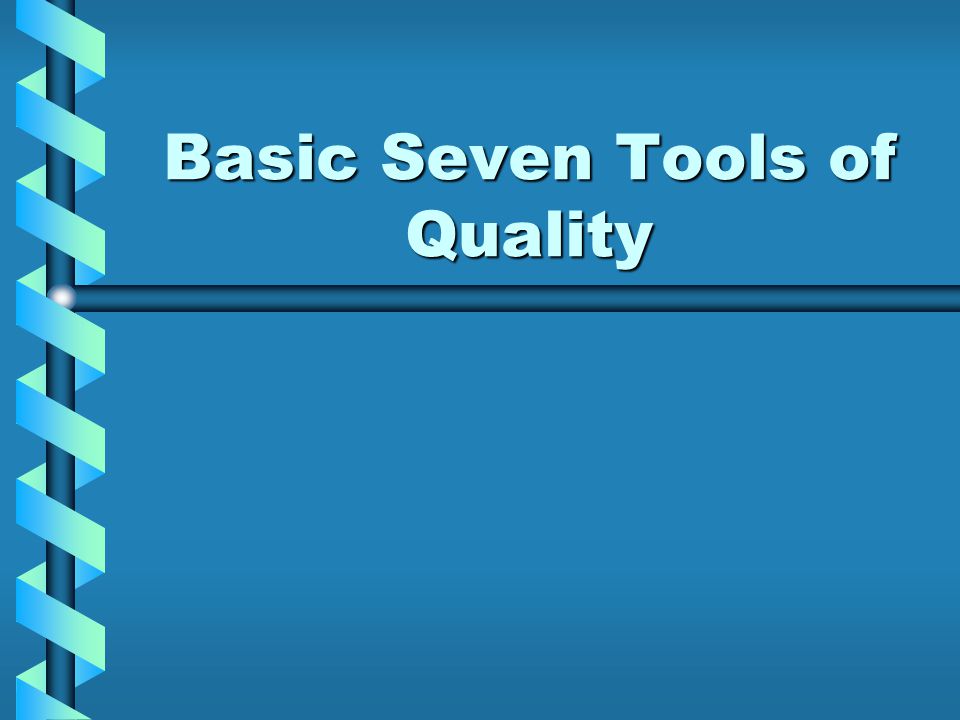
7 QC Tools.
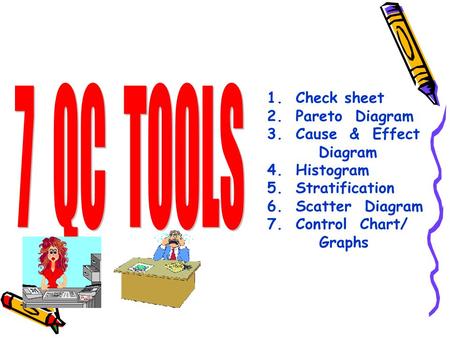
7 QC TOOLS 1. Check sheet 2. Pareto Diagram 3. Cause & Effect Diagram
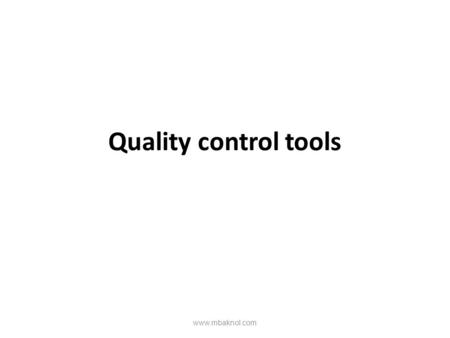
Quality control tools
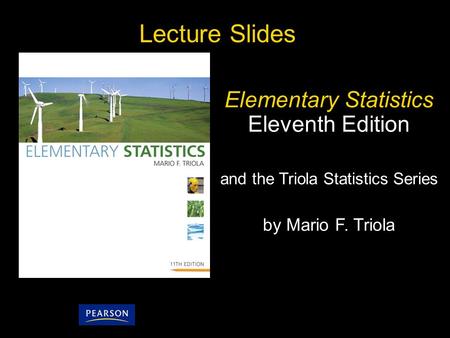
Copyright © 2010, 2007, 2004 Pearson Education, Inc. All Rights Reserved. Lecture Slides Elementary Statistics Eleventh Edition and the Triola.
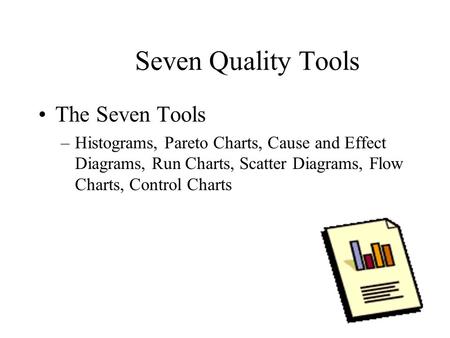
Seven Quality Tools The Seven Tools
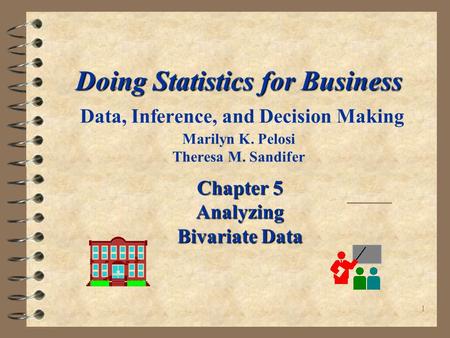
1 Doing Statistics for Business Doing Statistics for Business Data, Inference, and Decision Making Marilyn K. Pelosi Theresa M. Sandifer Chapter 5 Analyzing.
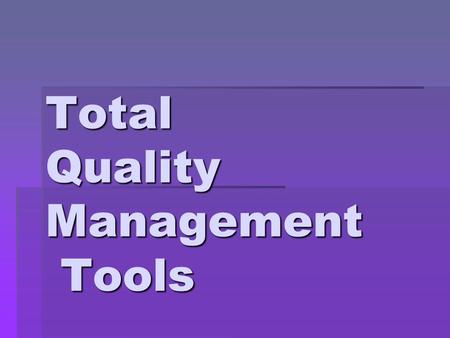
Total Quality Management Tools
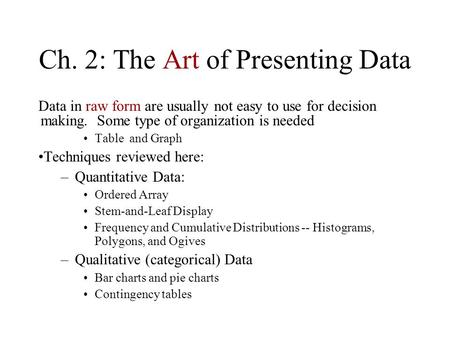
Ch. 2: The Art of Presenting Data Data in raw form are usually not easy to use for decision making. Some type of organization is needed Table and Graph.
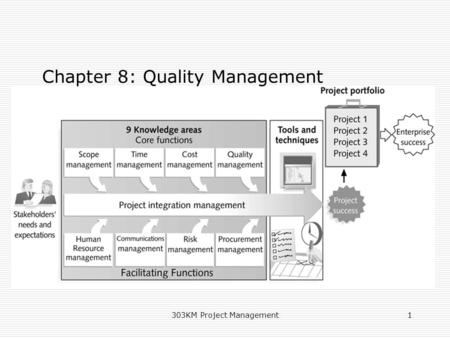
Chapter 8: Quality Management Project Quality Management
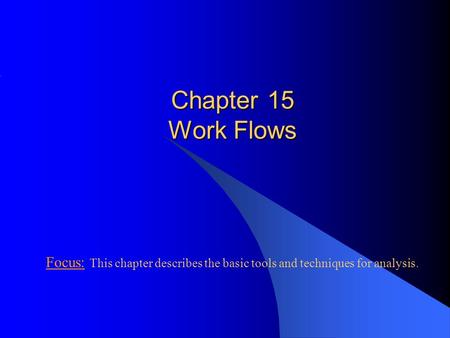
Chapter 15 Work Flows Focus: This chapter describes the basic tools and techniques for analysis.
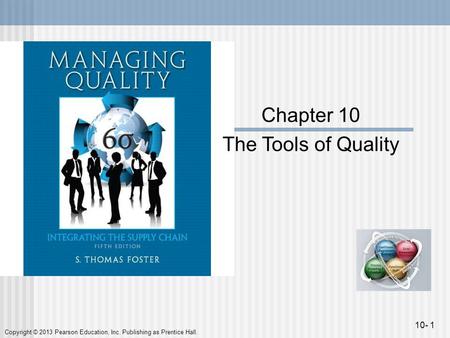
Chapter 10 The Tools of Quality.
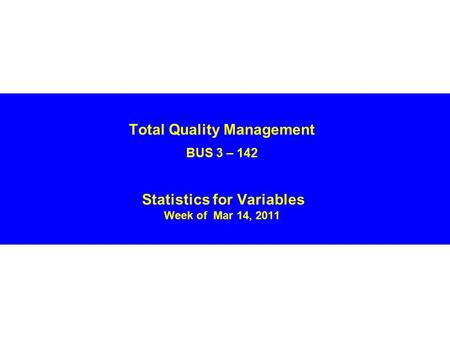
Total Quality Management BUS 3 – 142 Statistics for Variables Week of Mar 14, 2011.
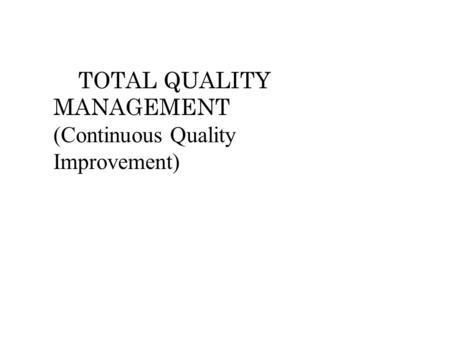
TOTAL QUALITY MANAGEMENT (Continuous Quality Improvement)
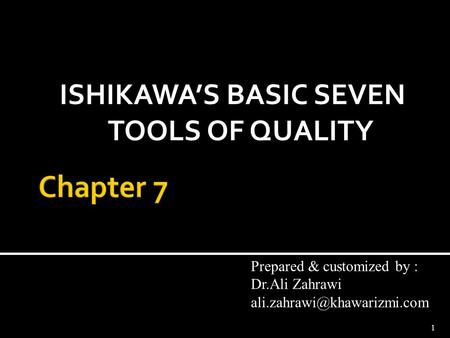
ISHIKAWA’S BASIC SEVEN TOOLS OF QUALITY
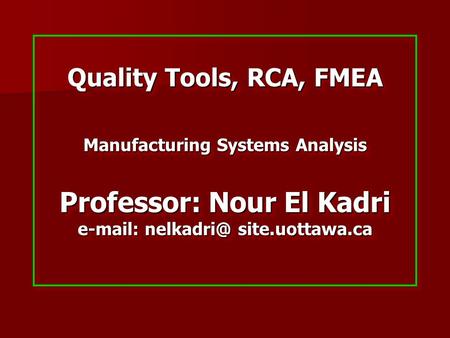
Quality Tools, RCA, FMEA Manufacturing Systems Analysis Professor: Nour El Kadri site.uottawa.ca.

2-3. In addition to the histogram, the frequency polygon, and the ogive, several other types of graphs are often used in statistics. They are the bar.
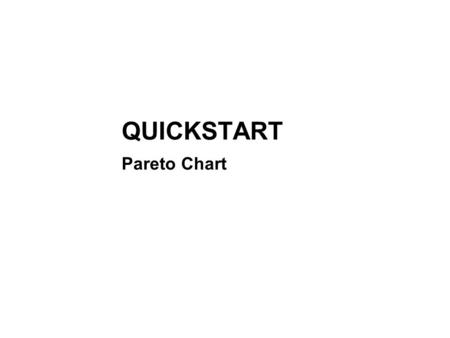
QUICKSTART Pareto Chart. Pareto Chart Understand what the Pareto law is Understand what a Pareto diagram is Provide Pareto analysis by level Provide examples.
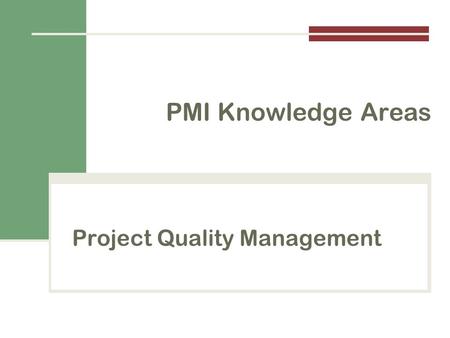
Project Quality Management
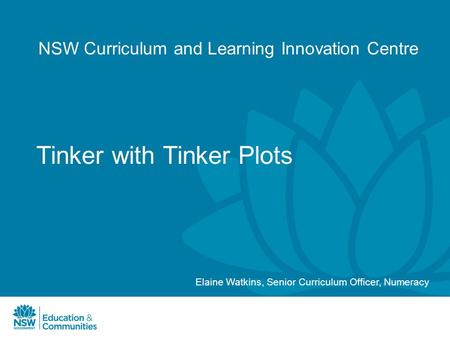
NSW Curriculum and Learning Innovation Centre Tinker with Tinker Plots Elaine Watkins, Senior Curriculum Officer, Numeracy.
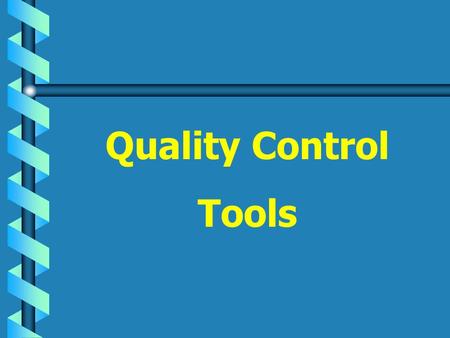
Quality Control Tools A committee for developing QC tools affiliated with JUSE was set up in April Their aim was to develop QC techniques for.
About project
© 2024 SlidePlayer.com Inc. All rights reserved.
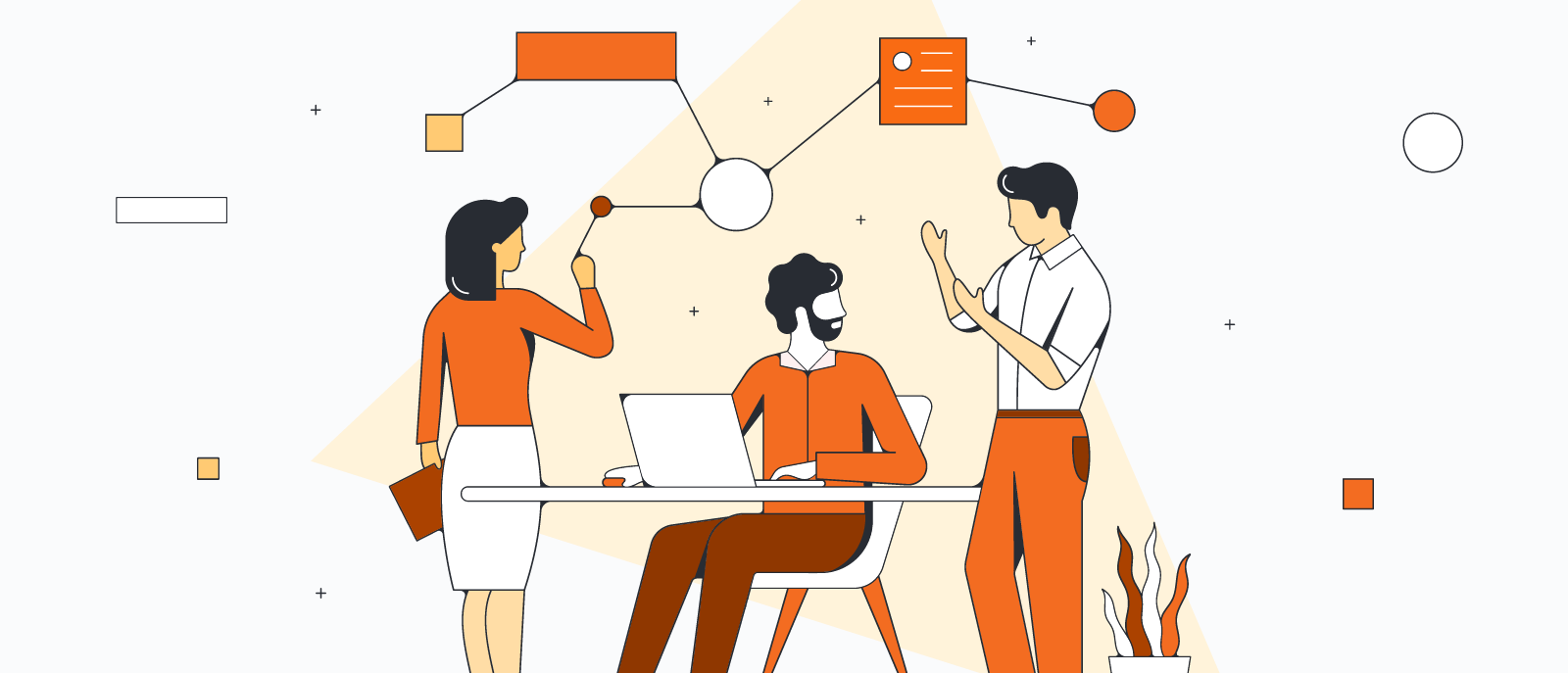
What are the 7 basic quality tools, and how can they change your business for the better?
Reading time: about 6 min
What are the 7 basic quality tools?
- Stratification
- Check sheet (tally sheet)
- Cause and effect diagram (fishbone or Ishikawa diagram)
- Pareto chart (80-20 rule)
- Scatter diagram
- Control chart (Shewhart chart)
The ability to identify and resolve quality-related issues quickly and efficiently is essential to anyone working in quality assurance or process improvement. But statistical quality control can quickly get complex and unwieldy for the average person, making training and quality assurance more difficult to scale.
Thankfully, engineers have discovered that most quality control problems can be solved by following a few key fundamentals. These fundamentals are called the seven basic tools of quality.
With these basic quality tools in your arsenal, you can easily manage the quality of your product or process, no matter what industry you serve.
Learn about these quality management tools and find templates to start using them quickly.
Where did the quality tools originate?
Kaoru Ishikawa, a Japanese professor of engineering, originally developed the seven quality tools (sometimes called the 7 QC tools) in the 1950s to help workers of various technical backgrounds implement effective quality control measures.
At the time, training programs in statistical quality control were complex and intimidating to workers with non-technical backgrounds. This made it difficult to standardize effective quality control across operations. Companies found that simplifying the training to user-friendly fundamentals—or seven quality tools—ensured better performance at scale
7 quality tools
1. stratification.
Stratification analysis is a quality assurance tool used to sort data, objects, and people into separate and distinct groups. Separating your data using stratification can help you determine its meaning, revealing patterns that might not otherwise be visible when it’s been lumped together.
Whether you’re looking at equipment, products, shifts, materials, or even days of the week, stratification analysis lets you make sense of your data before, during, and after its collection.
To get the most out of the stratification process, consider which information about your data’s sources may affect the end results of your data analysis. Make sure to set up your data collection so that that information is included.
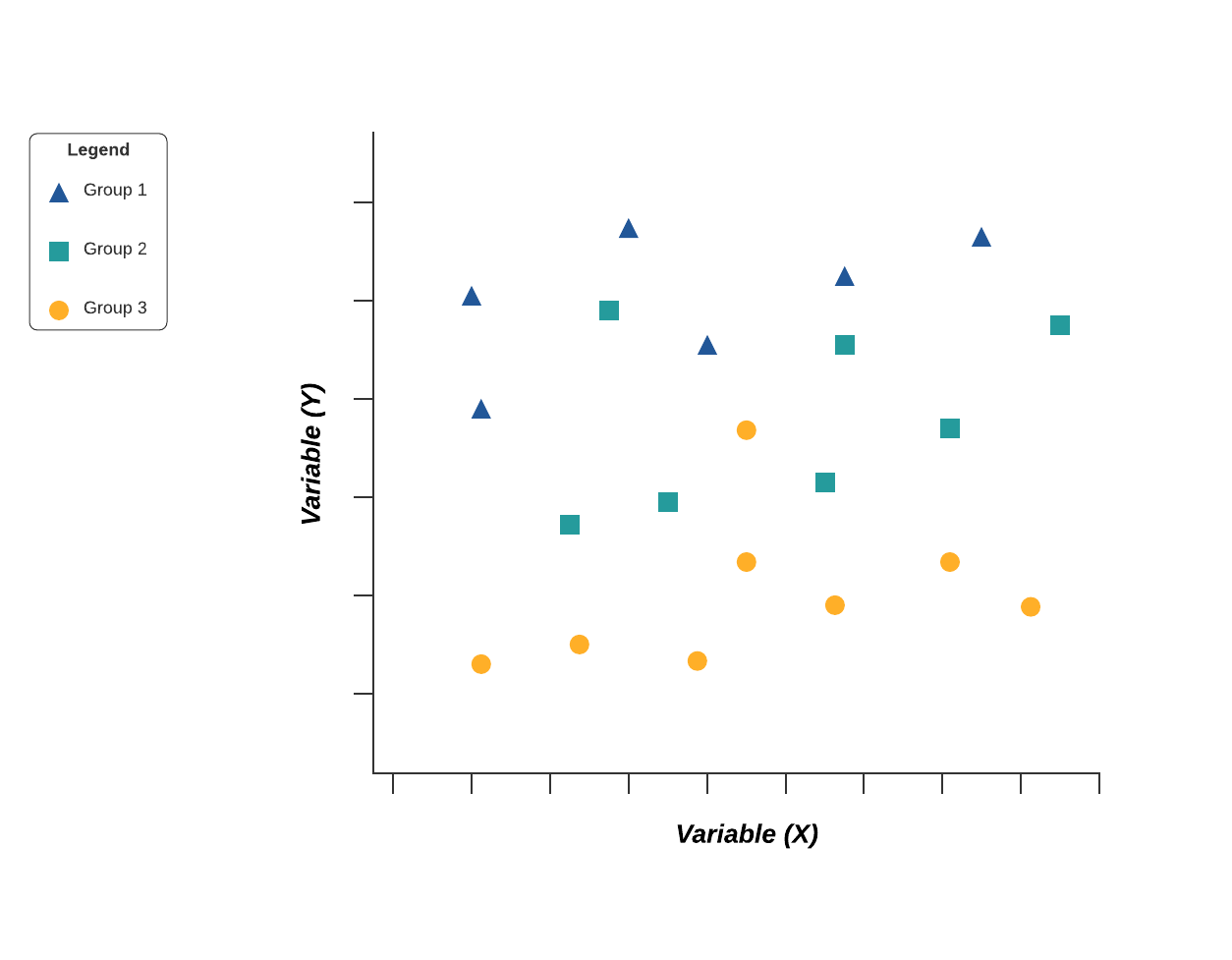
2. Histogram
Quality professionals are often tasked with analyzing and interpreting the behavior of different groups of data in an effort to manage quality. This is where quality control tools like the histogram come into play.
The histogram represents frequency distribution of data clearly and concisely amongst different groups of a sample, allowing you to quickly and easily identify areas of improvement within your processes. With a structure similar to a bar graph, each bar within a histogram represents a group, while the height of the bar represents the frequency of data within that group.
Histograms are particularly helpful when breaking down the frequency of your data into categories such as age, days of the week, physical measurements, or any other category that can be listed in chronological or numerical order.
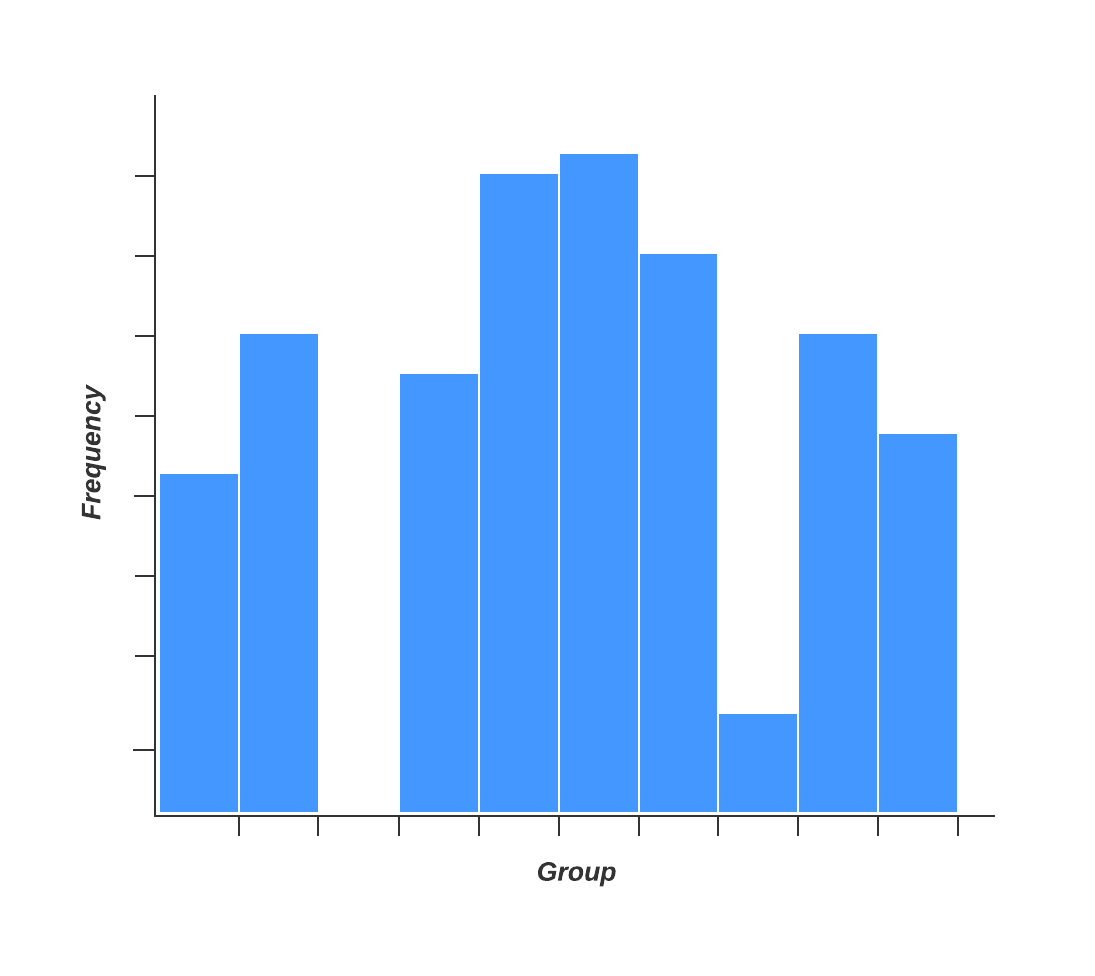
3. Check sheet (or tally sheet)
Check sheets can be used to collect quantitative or qualitative data. When used to collect quantitative data, they can be called a tally sheet. A check sheet collects data in the form of check or tally marks that indicate how many times a particular value has occurred, allowing you to quickly zero in on defects or errors within your process or product, defect patterns, and even causes of specific defects.
With its simple setup and easy-to-read graphics, check sheets make it easy to record preliminary frequency distribution data when measuring out processes. This particular graphic can be used as a preliminary data collection tool when creating histograms, bar graphs, and other quality tools.

4. Cause-and-effect diagram (also known as a fishbone or Ishikawa diagram)
Introduced by Kaoru Ishikawa, the fishbone diagram helps users identify the various factors (or causes) leading to an effect, usually depicted as a problem to be solved. Named for its resemblance to a fishbone, this quality management tool works by defining a quality-related problem on the right-hand side of the diagram, with individual root causes and sub-causes branching off to its left.
A fishbone diagram’s causes and subcauses are usually grouped into six main groups, including measurements, materials, personnel, environment, methods, and machines. These categories can help you identify the probable source of your problem while keeping your diagram structured and orderly.
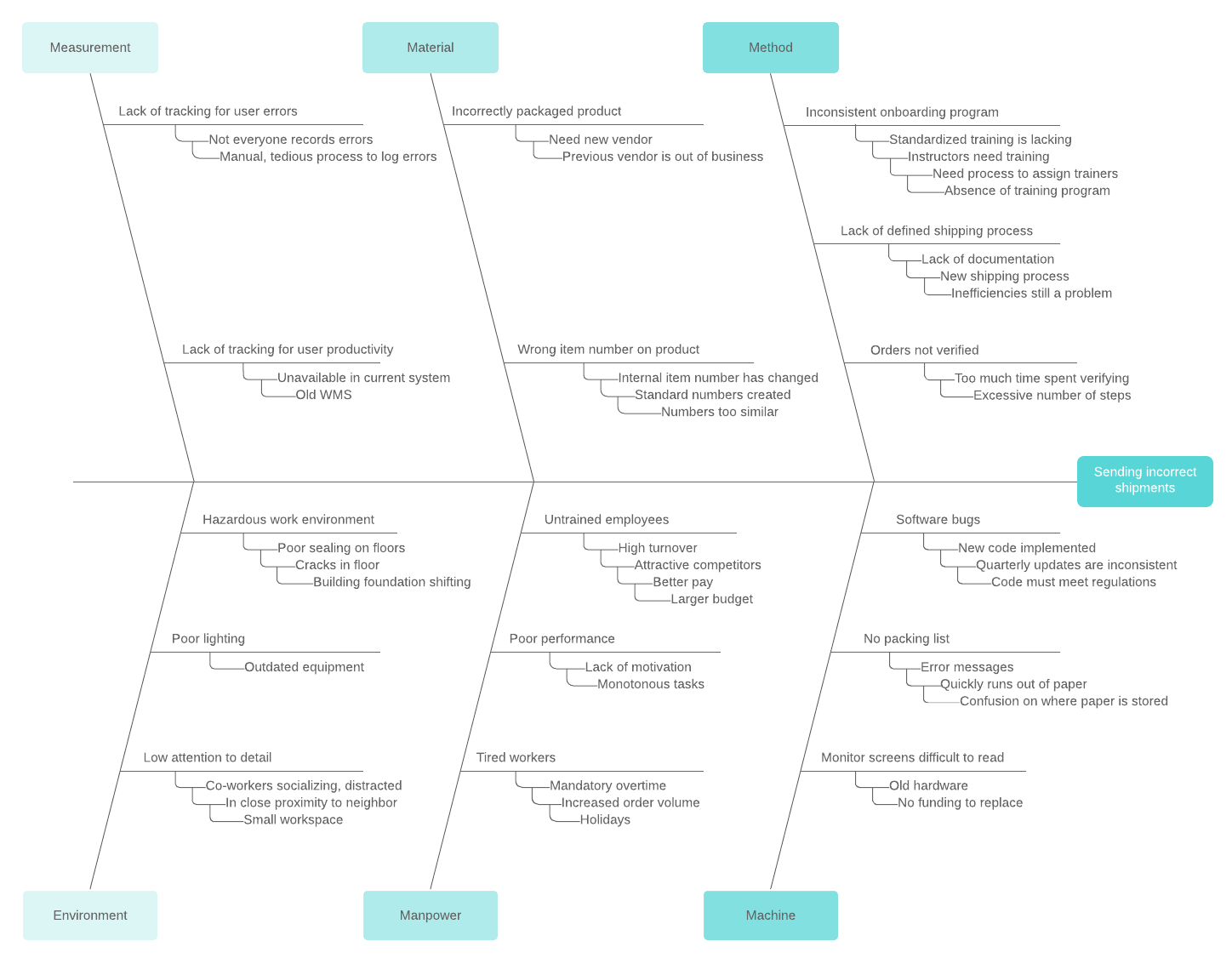
5. Pareto chart (80-20 rule)
As a quality control tool, the Pareto chart operates according to the 80-20 rule. This rule assumes that in any process, 80% of a process’s or system’s problems are caused by 20% of major factors, often referred to as the “vital few.” The remaining 20% of problems are caused by 80% of minor factors.
A combination of a bar and line graph, the Pareto chart depicts individual values in descending order using bars, while the cumulative total is represented by the line.
The goal of the Pareto chart is to highlight the relative importance of a variety of parameters, allowing you to identify and focus your efforts on the factors with the biggest impact on a specific part of a process or system.
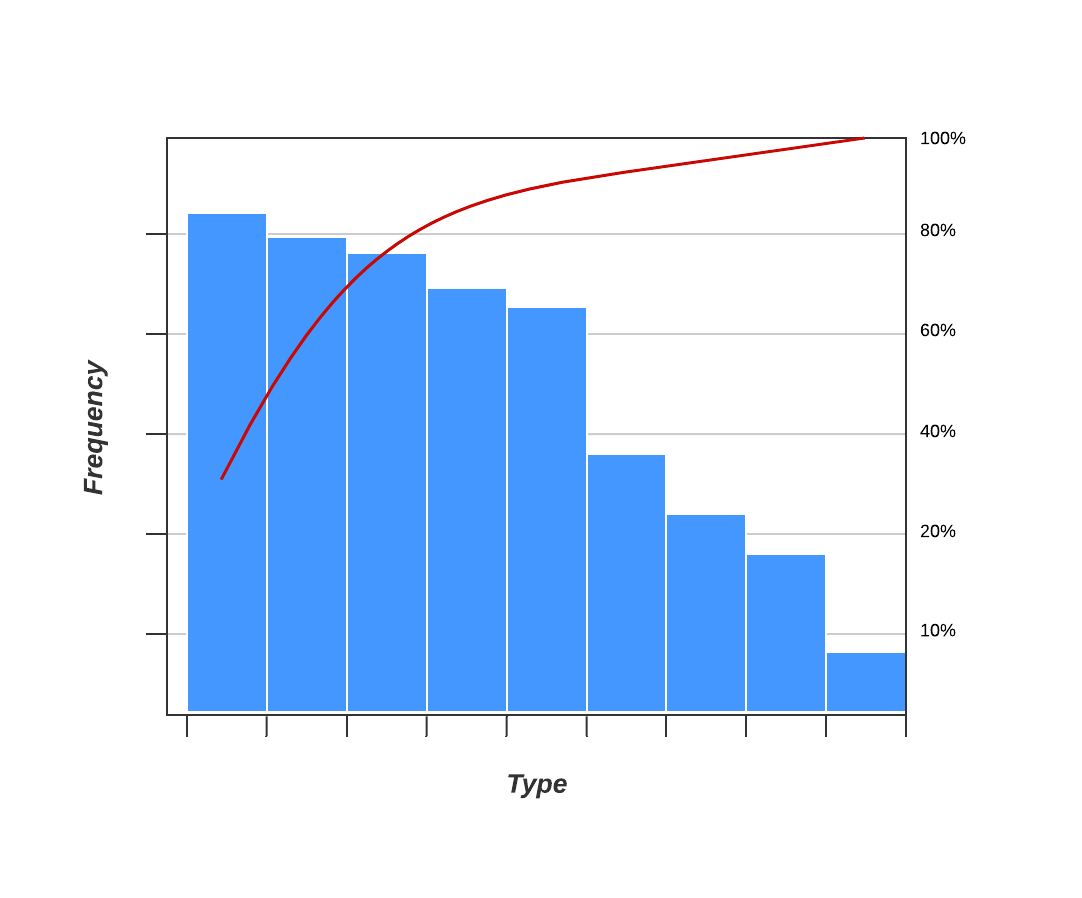
6. Scatter diagram
Out of the seven quality tools, the scatter diagram is most useful in depicting the relationship between two variables, which is ideal for quality assurance professionals trying to identify cause and effect relationships.
With dependent values on the diagram’s Y-axis and independent values on the X-axis, each dot represents a common intersection point. When joined, these dots can highlight the relationship between the two variables. The stronger the correlation in your diagram, the stronger the relationship between variables.
Scatter diagrams can prove useful as a quality control tool when used to define relationships between quality defects and possible causes such as environment, activity, personnel, and other variables. Once the relationship between a particular defect and its cause has been established, you can implement focused solutions with (hopefully) better outcomes.
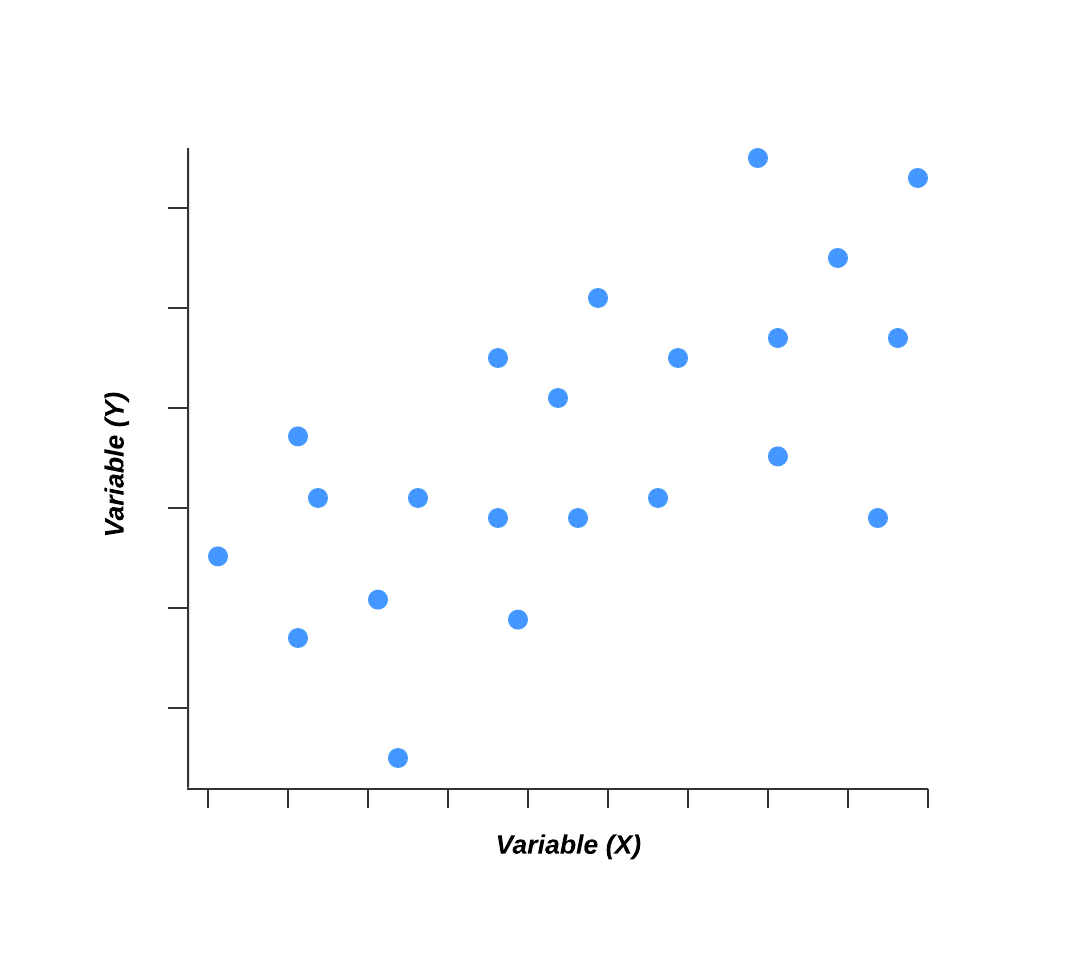
7. Control chart (also called a Shewhart chart)
Named after Walter A. Shewhart, this quality improvement tool can help quality assurance professionals determine whether or not a process is stable and predictable, making it easy for you to identify factors that might lead to variations or defects.
Control charts use a central line to depict an average or mean, as well as an upper and lower line to depict upper and lower control limits based on historical data. By comparing historical data to data collected from your current process, you can determine whether your current process is controlled or affected by specific variations.
Using a control chart can save your organization time and money by predicting process performance, particularly in terms of what your customer or organization expects in your final product.
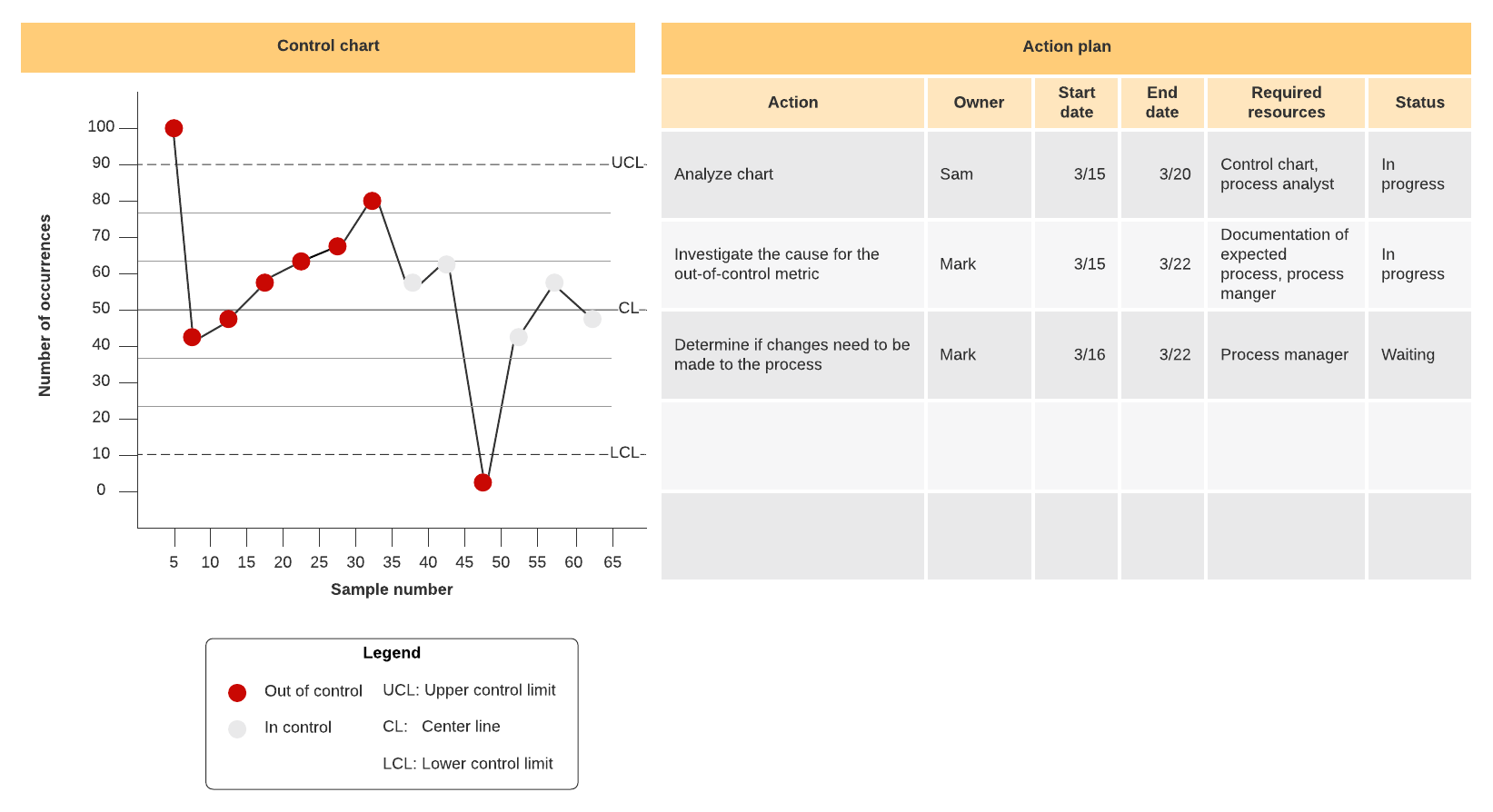
Bonus: Flowcharts
Some sources will swap out stratification to instead include flowcharts as one of the seven basic QC tools. Flowcharts are most commonly used to document organizational structures and process flows, making them ideal for identifying bottlenecks and unnecessary steps within your process or system.
Mapping out your current process can help you to more effectively pinpoint which activities are completed when and by whom, how processes flow from one department or task to another, and which steps can be eliminated to streamline your process.
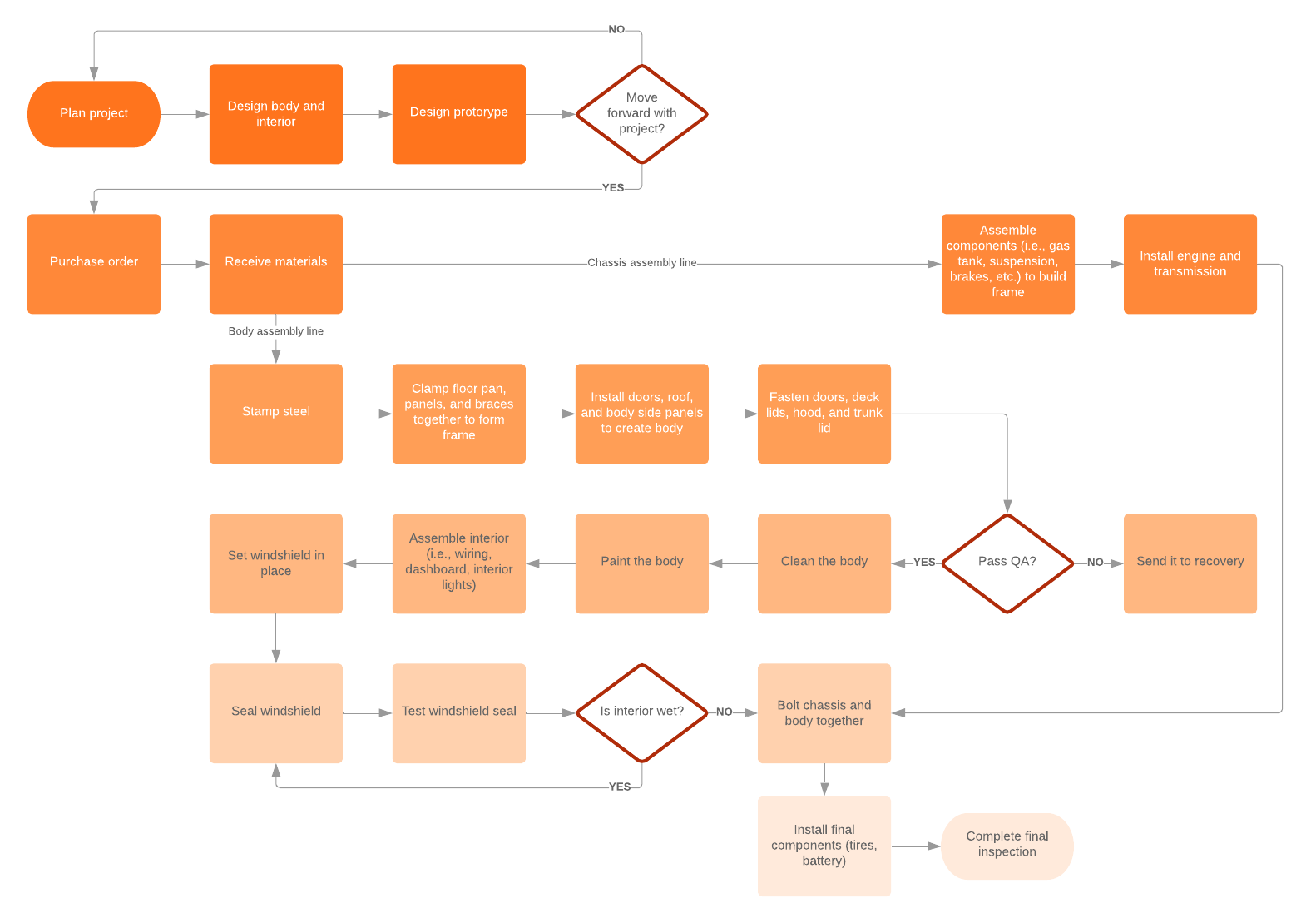
Learn how to create a process improvement plan in seven steps.
About Lucidchart
Lucidchart, a cloud-based intelligent diagramming application, is a core component of Lucid Software's Visual Collaboration Suite. This intuitive, cloud-based solution empowers teams to collaborate in real-time to build flowcharts, mockups, UML diagrams, customer journey maps, and more. Lucidchart propels teams forward to build the future faster. Lucid is proud to serve top businesses around the world, including customers such as Google, GE, and NBC Universal, and 99% of the Fortune 500. Lucid partners with industry leaders, including Google, Atlassian, and Microsoft. Since its founding, Lucid has received numerous awards for its products, business, and workplace culture. For more information, visit lucidchart.com.
Related articles
How to improve process visualization.
In this article we’ll talk about how to improve visualization, even if you are not a visual presentation expert.
Which process improvement methodology should you use?
Struggling to decide which process improvement methodology to use? Learn about the top approaches—Six Sigma, Lean, TQM, Just-in-time, and others—and the diagrams that can help you implement these techniques starting today.
Bring your bright ideas to life.
or continue with
By registering, you agree to our Terms of Service and you acknowledge that you have read and understand our Privacy Policy .
Quality Toolbox PowerPoint Template
A Collection of 25 Quality Management Tools and Techniques for Your Business! Professionally Designed Quality Assurance Charts and Diagrams Bring Your Plans to Life. This quality tools PowerPoint collection includes a huge range of introductions to common quality assurance techniques (e.g. Q7 and M7) and a wide selection of charts and analysis tools. All PowerPoint slides are professionally designed, slick, modern, and 100% editable. You can rely on this toolbox from the market leader to ensure long-term compliance with quality standards. Save Time - Download Now!
Instant Download:
- 100% Editable Powerpoint Slides / Graphics
- Outstanding Customer Support
- SSL Secure Payment
- Made in Germany
- Information
- Template (16:9)
Quality Assurance Methods and Tools for PowerPoint
This amazing quality tools PowerPoint toolbox contains 25 quality techniques for visualizing important measures of your quality assurance and presenting your results using our professionally designed slides.
Quality Management Tools and Techniques in PowerPoint
Quality management techniques are analysis tools used to build and maintain quality standards. The Elementary Quality Techniques Q7 and the Management Tools M7 have established themselves as pillars of quality management across all fields of business. These methods can be combined with each other and with other quality assurance procedures and strategies to provide reliable problem-solving strategies.
Create Your Quality Assurance Strategy
In addition to the 25 quality management tools, this template set provides you with clear information concerning how the Q7 and M7 can interact and be applied in practice. Clear overviews and well-designed charts of quality techniques allow you to easily set up and present your overall quality assurance strategy.
With the Quality Tools PowerPoint Set, You Can
- capitalize on twenty-five of the most important quality management tools
- expand and improve your quality assurance
- ensure you have the right tool for every quality management problem
This PowerPoint Template Includes:
- Introduction and definition of quality tools
- Overview of Q7 and M7
- Check sheet
- Quality control chart
- Pareto diagram
- Scatter diagram
- Brainstorming
- Cause and effect diagram
- Relations diagram
- Tree diagram
- Matrixdiagramm
- Matrix diagram
- Process decision program chart
- Affinity diagram
- Prioritization matrix
- Activity network plan
- House of quality
- Failure mode and effects analysis (FMEA)
- Frequency relevance analysis of problems (FRAP)
- Service blueprint
- Structural equation model (SEM)
- Statistical process control (SPC)
- Paired comparison analysis
- Value analysis
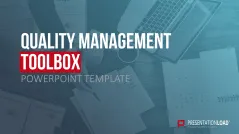
Infographics Bundle
Flat design – presentation people bundle, change management bundle, 150 strategy & management models, agile management bundle, gearwheel bundle, project charter, growth mindset, project canvas, artificial intelligence, gdpr: data protection powerpoint template, digital transformation, corporate services.
We’ll optimize your existing PowerPoint presentation and create slides in your corporate design.
New PowerPoint Templates
We are continually bringing you new PowerPoint templates on current business topics and in modern designs.
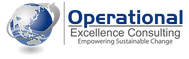
Aspect Ratio:
File Size: 16.0 MB
Number of Slides: 90
Terms of Usage
Training Presentation/Powerpoint:
Seven basic tools of quality.
Description The seven basic tools of quality is a designation given to a fixed set of graphical techniques identified as being most helpful in troubleshooting issues related to quality. They are called basic because they are suitable for people with little formal training in statistics and because they can be used to solve the vast majority of quality-related issues. The seven basic tools of quality or seven basic Quality Control (QC) tools as they are commonly called, are tools which arrange problem areas, put data into diagrams, surface problem areas and clearly bring up any hidden truth. These tools are not for experts alone but for the use of everyone in their daily work. A problem solving team's successes are dependent on the familiarity and ease with which these tools are used.
The Seve n Basic QC Tools are: 1. Check Sheet: Systematically collects and organizes data for analysis.
2. Histogram: Illustrates the distribution of a set of data.
3. Pareto Chart: Identifies and prioritizes the most significant factors contributing to a problem.
4. Cause-and-Effect Diagram (Fishbone/Ishikawa): Identifies potential causes of a problem for further analysis.
5. Scatter Diagram: Examines the relationship between two variables.
6. Control Chart: Monitors and maintains the stability of a process over time.
7. Stratification: Analyzes and categorizes data to identify patterns and variations. In this Seven Basic Tools of Quality PPT training presentation, you will be able to teach employees how to use the tools in their daily work or as part of the structured Plan-Do-Check-Act (PDCA) approach to problem solving. The basic tools can also be applied in A3 problem solving, 8D (Eight Disciplines) problem solving, Yellow Belt Lean Six Sigma projects, Green Belt Lean Six Sigma projects, Kaizen events, TPM Focused Improvement projects, etc.
Learning Objectives
To understand the seven basic tools for quality and process improvement.
To learn how to apply the seven basic tools of quality to problem solving or daily work.
PDCA Problem Solving
Stratification
Check Sheet
Control Chart
Pareto Chart
Cause & Effect Diagram
Scatter Diagram
You may also be interested in the following training presentations and frameworks (sold separately):
Introduction to Quality
Total Quality Management
Total Quality Process
PDCA Problem Solving Technique & Tools
Problem Solving & Visualization Tools
Root Cause Analysis
Seven Advanced Quality Tools
Reducing the Cost of Quality
8D Problem Solving Process
Advanced Product Quality Planning (APQP)
Failure Mode & Effects Analysis (FMEA)
Mistake-Proofing

- Customer Favourites
7 Quality Tools
Powerpoint Templates
Icon Bundle
Kpi Dashboard
Professional
Business Plans
Swot Analysis
Gantt Chart
Business Proposal
Marketing Plan
Project Management
Business Case
Business Model
Cyber Security
Business PPT
Digital Marketing
Digital Transformation
Human Resources
Product Management
Artificial Intelligence
Company Profile
Acknowledgement PPT
PPT Presentation
Reports Brochures
One Page Pitch
Interview PPT
All Categories
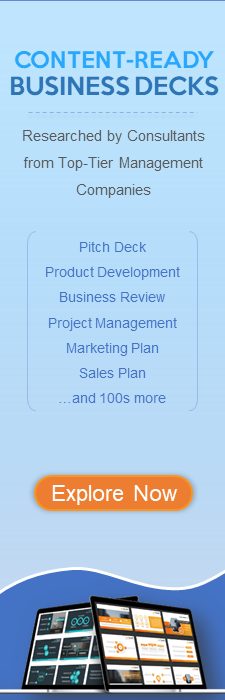
- You're currently reading page 1

Stages // require(['jquery'], function ($) { $(document).ready(function () { //removes paginator if items are less than selected items per page var paginator = $("#limiter :selected").text(); var itemsPerPage = parseInt(paginator); var itemsCount = $(".products.list.items.product-items.sli_container").children().length; if (itemsCount ? ’Stages’ here means the number of divisions or graphic elements in the slide. For example, if you want a 4 piece puzzle slide, you can search for the word ‘puzzles’ and then select 4 ‘Stages’ here. We have categorized all our content according to the number of ‘Stages’ to make it easier for you to refine the results.
Category // require(['jquery'], function ($) { $(document).ready(function () { //removes paginator if items are less than selected items per page var paginator = $("#limiter :selected").text(); var itemsperpage = parseint(paginator); var itemscount = $(".products.list.items.product-items.sli_container").children().length; if (itemscount.
- Business Slides (75)
- Circular (13)
- Complete Decks (27)
- Concepts 1 (2)
- Data and Statistics (3)
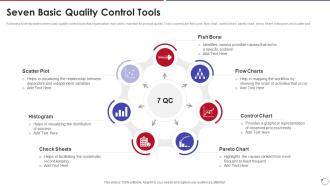
7 Basic Tools of Quality for Process Improvement

Japan is known worldwide for its quality products and services. One of the many reasons for this is its excellent quality management. How did it become so? Japan has Dr. Kaoru Ishikawa to thank for that.
Postwar Japan underwent a major quality revolution. Companies were focused on training their employees in statistical quality control. But soon they realized that the complexity of the subject itself could intimidate most of the workers; so they wanted more basic tools.
Dr. Kaoru Ishikawa, a member of the Japanese Union of Scientists and Engineers (JUSE), took it to his hands to make quality control easier for everyone – even those with little knowledge of statistics – to understand. He introduced the 7 basic tools of quality. They were soon adopted by most companies and became the foundation of Japan’s astonishing industrial resurgence after World War 2.
This post will describe the 7 basic quality tools, how to use them and give you access to templates that you can use right away.
Quality Tools: What Are They?
How can teams and organizations use the 7 basic quality tools, cause and effect diagram, scatter diagram, check sheets.
- Control chart
- Pareto chart
The 7 basic tools of quality, sometimes also referred to as 7 QC tools – represent a fixed set of graphical tools used for troubleshooting issues that are related to quality.
They are called basic quality tools because they can be easily learned by anyone even without any formal training in statistics. Dr. Kaoru Ishikawa played the leading role in the development and advocacy of using the 7 quality tools in organizations for problem-solving and process improvement.
The 7 basic quality tools include;
- Cause-and-effect diagram
- Scatter diagram
- Check sheet
The 7 quality tools were first emphasized by Kaoru Ishikawa a professor of engineering at the University of Tokyo, who is also known as the father of “Quality Circles” for the role he played in launching Japan’s quality movement in the 1960s. During this time, companies were focused on training their employees in statistical quality control realized that the complexity of the subject could intimidate most of the workers; hence they opted for simpler methods that are easy to learn and use. 7 basic tools of quality were thus incorporated company-wide.
Quality tools are used to collect data, analyze data, identify root causes, and measure results in problem-solving and process improvement. The use of these tools helps people involved easily generate new ideas, solve problems, and do proper planning.
- Structured approach: They provide a systematic approach to problem-solving and process improvement, ensuring that efforts are well-organized and focused.
- Data-driven decision making: The tools enable data collection, analysis, and visualization, empowering teams to make informed decisions based on evidence.
- Improved communication and collaboration: Visual representations and structured tools facilitate effective communication and collaboration among team members, leading to shared understanding and alignment.
- Problem identification and prioritization: The tools help identify and prioritize problems or improvement opportunities, enabling teams to allocate resources efficiently and address critical issues first.
- Continuous improvement: By using these tools, teams can establish a culture of continuous improvement, as they provide a framework for ongoing monitoring, analysis, and refinement of processes.
7 Basic Quality Tools Explained with Templates
The 7 quality tools can be applied across any industry. They help teams and individuals analyze and interpret the data they gather and derive maximum information from it.
Flowcharts are perhaps the most popular out of the 7 quality tools. This tool is used to visualize the sequence of steps in a process, event, workflow, system, etc. In addition to showing the process as a whole, a flowchart also highlights the relationship between steps and the process boundaries (start and end).
Flowcharts use a standard set of symbols, and it’s important to standardize the use of these symbols so anyone can understand and use them easily. Here’s a roundup of all the key flowchart symbols .
- To build a common understanding of a process.
- To analyze processes and discover areas of issues, inefficiencies, blockers, etc.
- To standardize processes by leading everyone to follow the same steps.
Real-world examples of usage
- Documenting and analyzing the steps involved in a customer order fulfillment process.
- Mapping out the workflow of a software development lifecycle.
- Visualizing the process flow of patient admissions in a hospital.
Enhances process understanding, highlights bottlenecks or inefficiencies, and supports process optimization and standardization efforts.
How to use a flowchart
- Gather a team of employees involved in carrying out the process for analyzing it.
- List down the steps involved in the process from its start to end.
- If you are using an online tool like Creately , you can first write down the process steps and rearrange them later on the canvas as you identify the flow.
- Identify the sequence of steps; when representing the flow with your flowchart, show it from left to write or from top to bottom.
- Connect the shapes with arrows to indicate the flow.
Who can use it?
- Process improvement teams mapping and documenting existing processes for analysis.
- Business analysts or consultants analyzing workflow and process optimization opportunities.
- Software developers or system designers documenting the flow of information or interactions in a system.
To learn more about flowcharts, refer to our Ultimate Flowchart Tutorial .
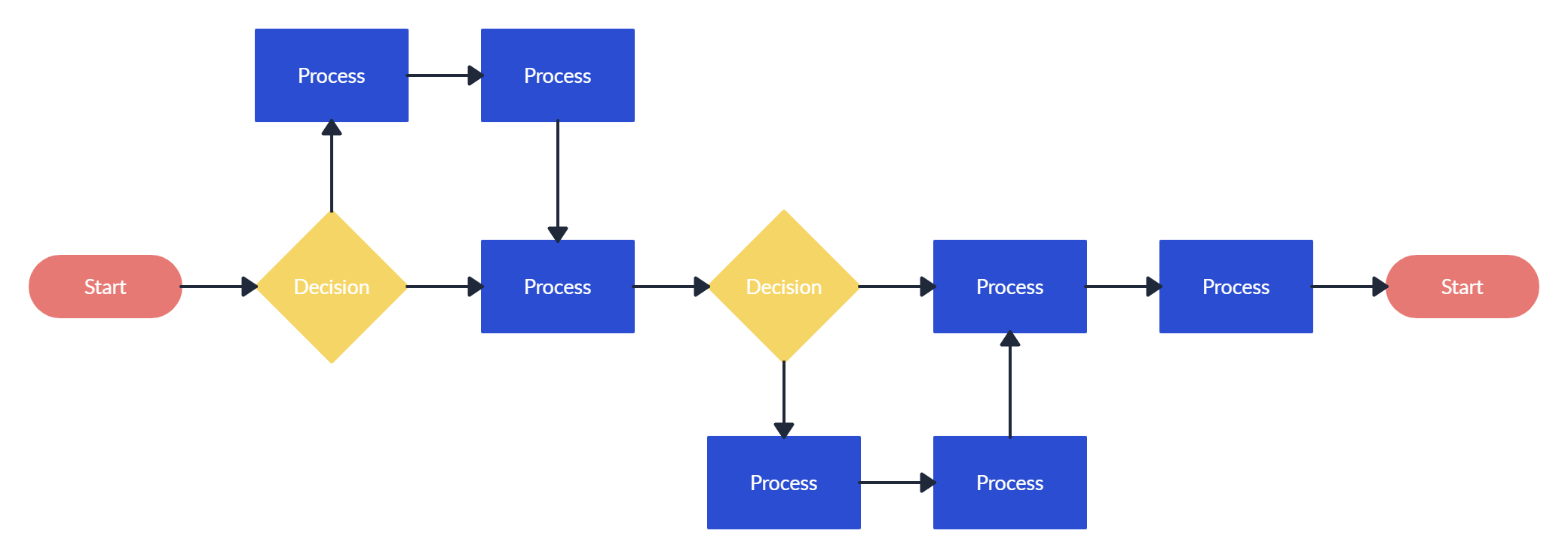
A histogram is a type of bar chart that visualizes the distribution of numerical data. It groups numbers into ranges and the height of the bar indicates how many fall into each range.
It’s a powerful quality planning and control tool that helps you understand preventive and corrective actions.
- To easily interpret a large amount of data and identify patterns.
- To make predictions of process performance.
- To identify the different causes of a quality problem.
- Analyzing the distribution of call wait times in a call center.
- Assessing the distribution of product weights in a manufacturing process.
- Examining the variation in delivery times for an e-commerce business.
Provides insights into process performance and variation, enabling teams to target areas for improvement and make data-driven decisions.
How to make a histogram
- Collect data for analysis. Record occurrences of specific ranges using a tally chart.
- Analyze the data at hand and split the data into intervals or bins.
- Count how many values fall into each bin.
- On the graph, indicate the frequency of occurrences for each bin with the area (height) of the bar.
- Process engineers or data analysts examining process performance metrics.
- Financial analysts analyzing expenditure patterns or budget variances.
- Supply chain managers assessing supplier performance or delivery times.
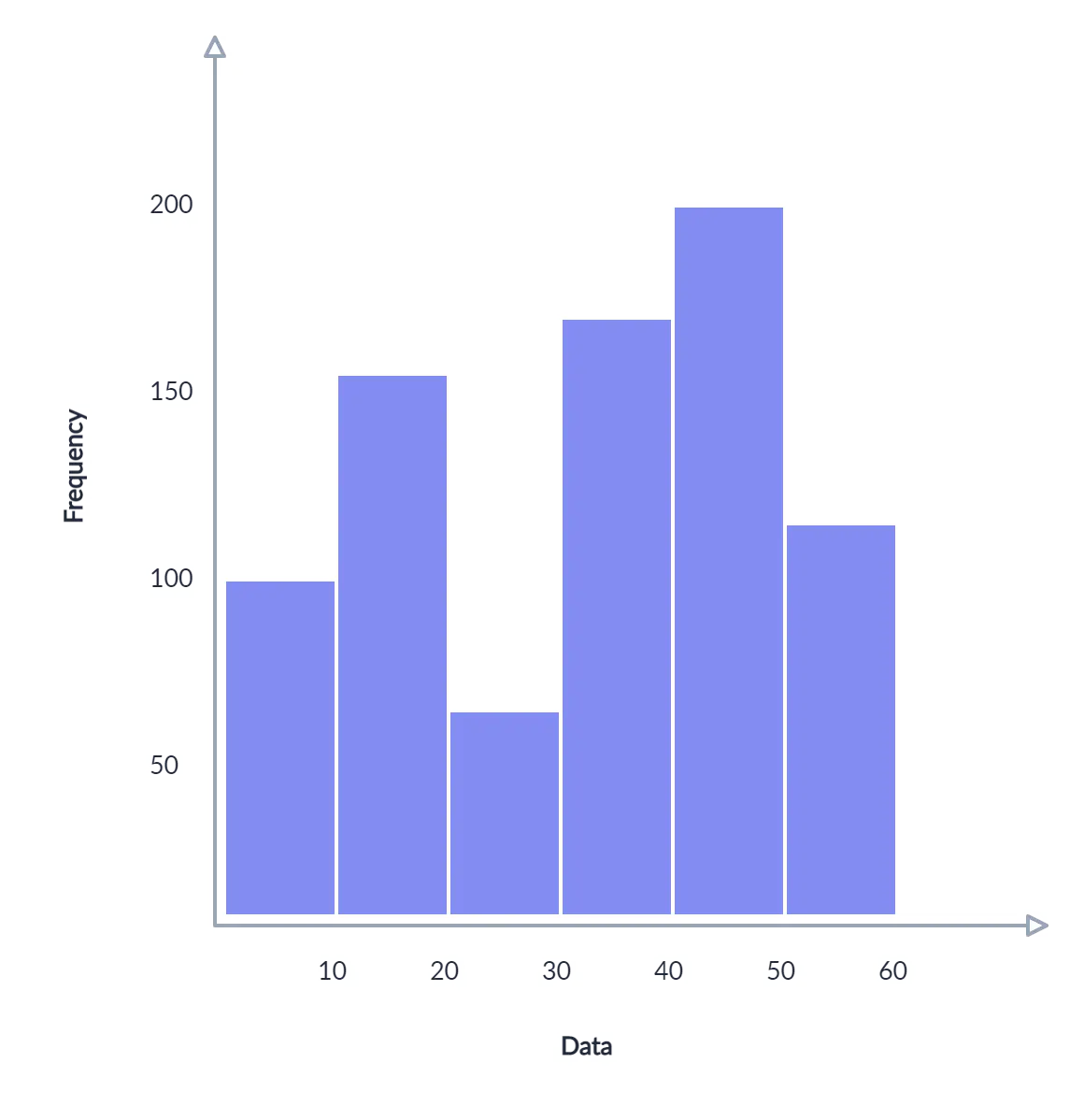
Here’s a useful article to learn more about using a histogram for quality improvement in more detail.
This tool is devised by Kaoru Ishikawa himself and is also known as the fishbone diagram (for it’s shaped like the skeleton of a fish) and Ishikawa diagram.
They are used for identifying the various factors (causes) leading to an issue (effect). It ultimately helps discover the root cause of the problem allowing you to find the correct solution effectively.
- Problem-solving; finding root causes of a problem.
- Uncovering the relationships between different causes leading to a problem.
- During group brainstorming sessions to gather different perspectives on the matter.
- Investigating the potential causes of low employee morale or high turnover rates.
- Analyzing the factors contributing to product defects in a manufacturing process.
- Identifying the root causes of customer complaints in a service industry.
Enhances problem-solving by systematically identifying and organizing possible causes, allowing teams to address root causes rather than symptoms.
How to use the cause and effect diagram
- Identify the problem area that needs to be analyzed and write it down at the head of the diagram.
- Identify the main causes of the problem. These are the labels for the main branches of the fishbone diagram. These main categories can include methods, material, machinery, people, policies, procedures, etc.
- Identify plausible sub-causes of the main causes and attach them as sub-branches to the main branches.
- Referring to the diagram you have created, do a deeper investigation of the major and minor causes.
- Once you have identified the root cause, create an action plan outlining your strategy to overcome the problem.
- Cross-functional improvement teams working on complex problems or process improvement projects.
- Quality engineers investigating the root causes of quality issues.
- Product designers or engineers seeking to understand the factors affecting product performance.
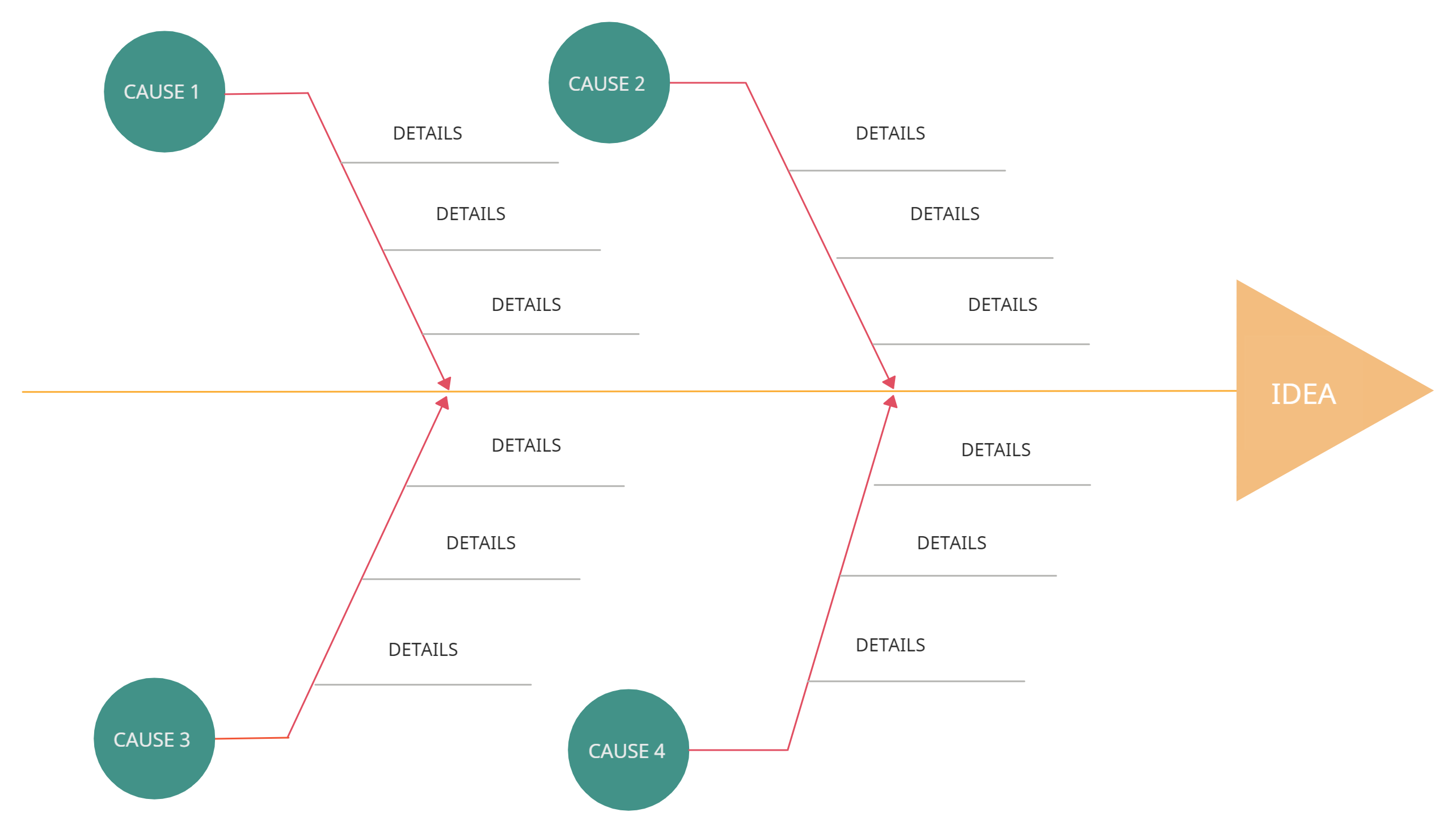
The scatter diagram (scatter charts, scatter plots, scattergrams, scatter graphs) is a chart that helps you identify how two variables are related.
The scatter diagram shows the values of the two variables plotted along the two axes of the graph. The pattern of the resulting points will reveal the correlation.
- To validate the relationship between causes and effects.
- To understand the causes of poor performance.
- To understand the influence of the independent variable over the dependent variable.
- Exploring the relationship between advertising expenditure and sales revenue.
- Analyzing the correlation between employee training hours and performance metrics.
- Investigating the connection between temperature and product quality in a production line.
Helps identify correlations or patterns between variables, facilitating the understanding of cause-and-effect relationships and aiding in decision-making.
How to make a scatter diagram
- Start with collecting data needed for validation. Understand the cause and effect relationship between the two variables.
- Identify dependent and independent variables. The dependent variable plotted along the vertical axis is called the measures parameter. The independent variable plotted along the horizontal axis is called the control parameter.
- Draw the graph based on the collected data. Add horizontal axis and vertical axis name and draw the trend line.
- Based on the trend line, analyze the diagram to understand the correlation which can be categorized as Strong, Moderate and No Relation.
- Data analysts exploring relationships between variables in research or analytics projects.
- Manufacturing engineers investigating the correlation between process parameters and product quality.
- Sales or marketing teams analyzing the relationship between marketing efforts and sales performance.
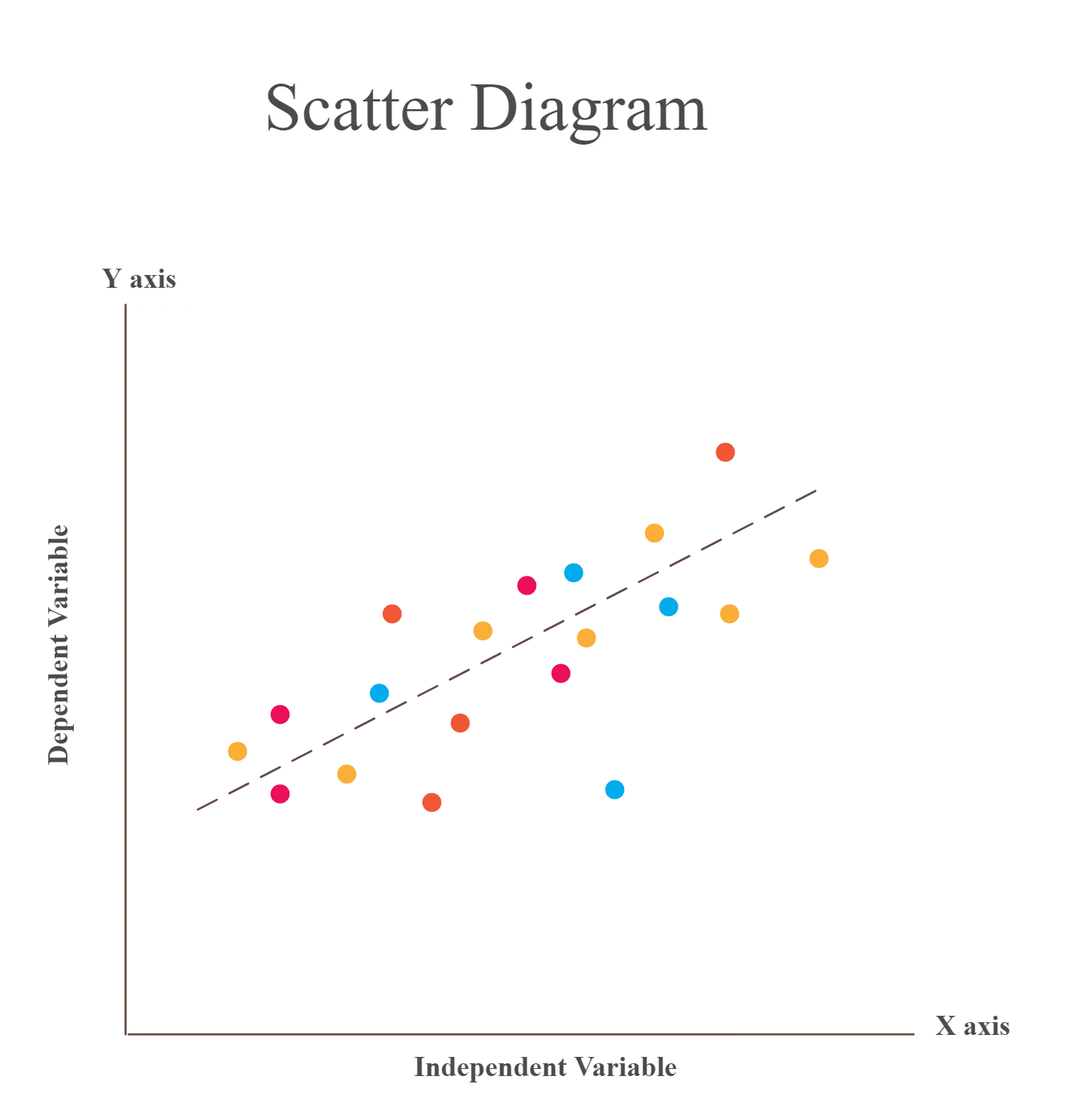
Check sheets provide a systematic way to collect, record and present quantitative and qualitative data about quality problems. A check sheet used to collect quantitative data is known as a tally sheet.
It is one of the most popular QC tools and it makes data gathering much simpler.
- To check the shape of the probability distribution of a process
- To quantify defects by type, by location or by cause
- To keep track of the completion of steps in a multistep procedure (as a checklist )
- Tracking the number of defects or errors in a manufacturing process.
- Recording customer complaints or inquiries to identify common issues.
- Monitoring the frequency of equipment breakdowns or maintenance needs.
Provides a structured approach for data collection, making it easier to identify trends, patterns, and areas for improvement.
How to make a checksheet
- Identify the needed information.
- Why do you need to collect the data?
- What type of information should you collect?
- Where should you collect the data from?
- Who should collect the data?
- When should you collect the data?
- How should you measure the data?
- How much data is essential?
Construct your sheet based on the title, source information and content information (refer to the example below).
Test the sheets. Make sure that all the rows and columns in it are required and relevant and that the sheet is easy to refer to and use. Test it with other collectors and make adjustments based on feedback.
- Quality inspectors or auditors who need to collect data on defects or issues.
- Process operators or technicians responsible for tracking process parameters or measurements.
- Customer service representatives who record customer complaints or inquiries.
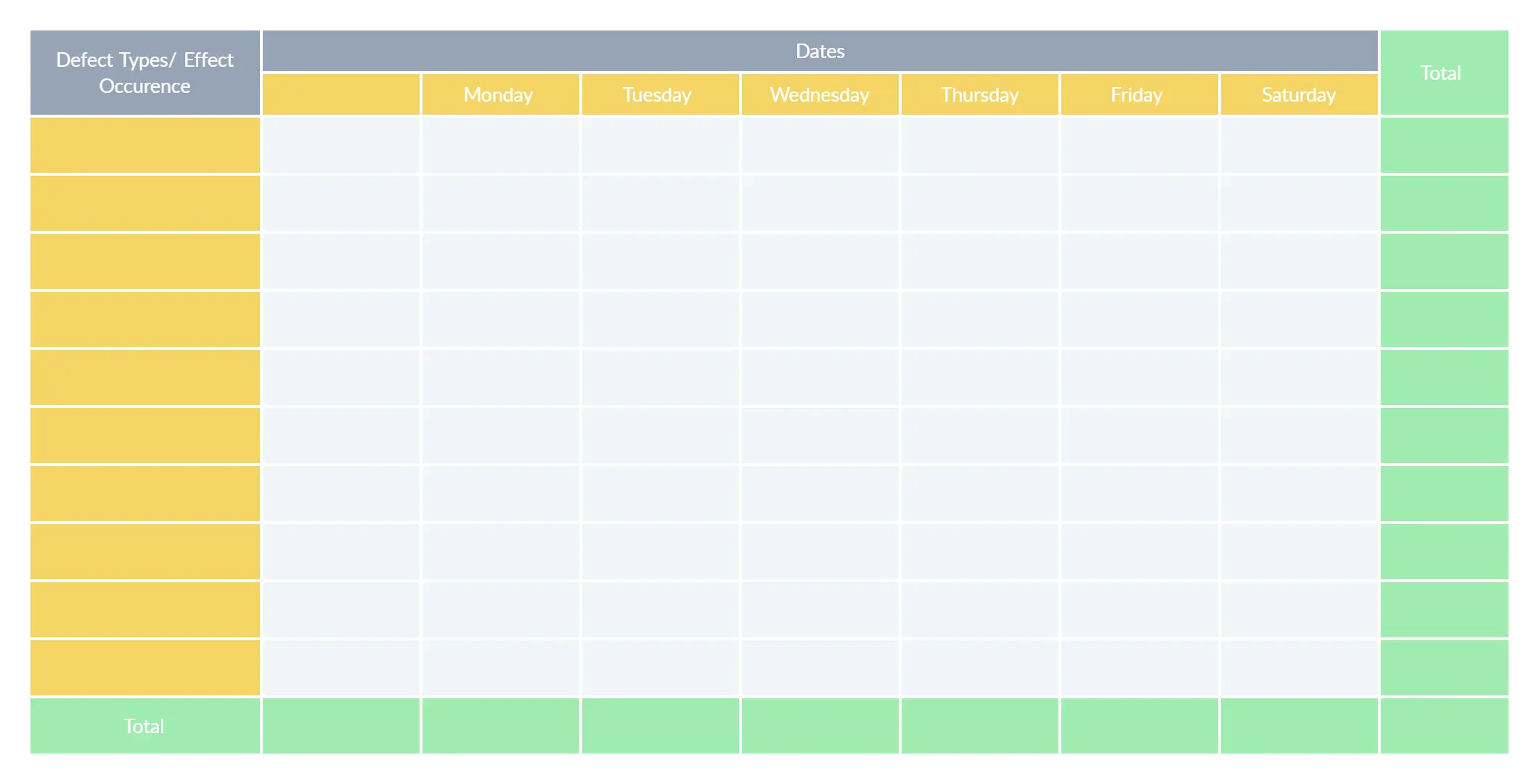
Control Chart
The control chart is a type of run chart used to observe and study process variation resulting from a common or special cause over a period of time.
The chart helps measure the variations and visualize it to show whether the change is within an acceptable limit or not. It helps track metrics such as defects, cost per unit, production time, inventory on hand , etc.
Control charts are generally used in manufacturing, process improvement methodologies like Six Sigma and stock trading algorithms.
- To determine whether a process is stable.
- To monitor processes and learn how to improve poor performance.
- To recognize abnormal changes in a process.
- Monitoring the variation in product dimensions during a manufacturing process.
- Tracking the number of customer complaints received per day.
- Monitoring the average response time of a customer support team.
Enables real-time monitoring of process stability, early detection of deviations or abnormalities, and prompt corrective actions to maintain consistent quality.
How to create a control chart
- Gather data on the characteristic of interest.
- Calculate mean and upper/lower control limits.
- Create a graph and plot the collected data.
- Add lines representing the mean and control limits to the graph.
- Look for patterns, trends, or points beyond control limits.
- Determine if the process is in control or out of control.
- Investigate and address causes of out-of-control points.
- Regularly update the chart with new data and analyze for ongoing improvement.
- Production supervisors or operators monitoring process performance on the shop floor.
- Quality control or assurance personnel tracking variation in product quality over time.
- Service managers observing customer satisfaction levels and service performance metrics.
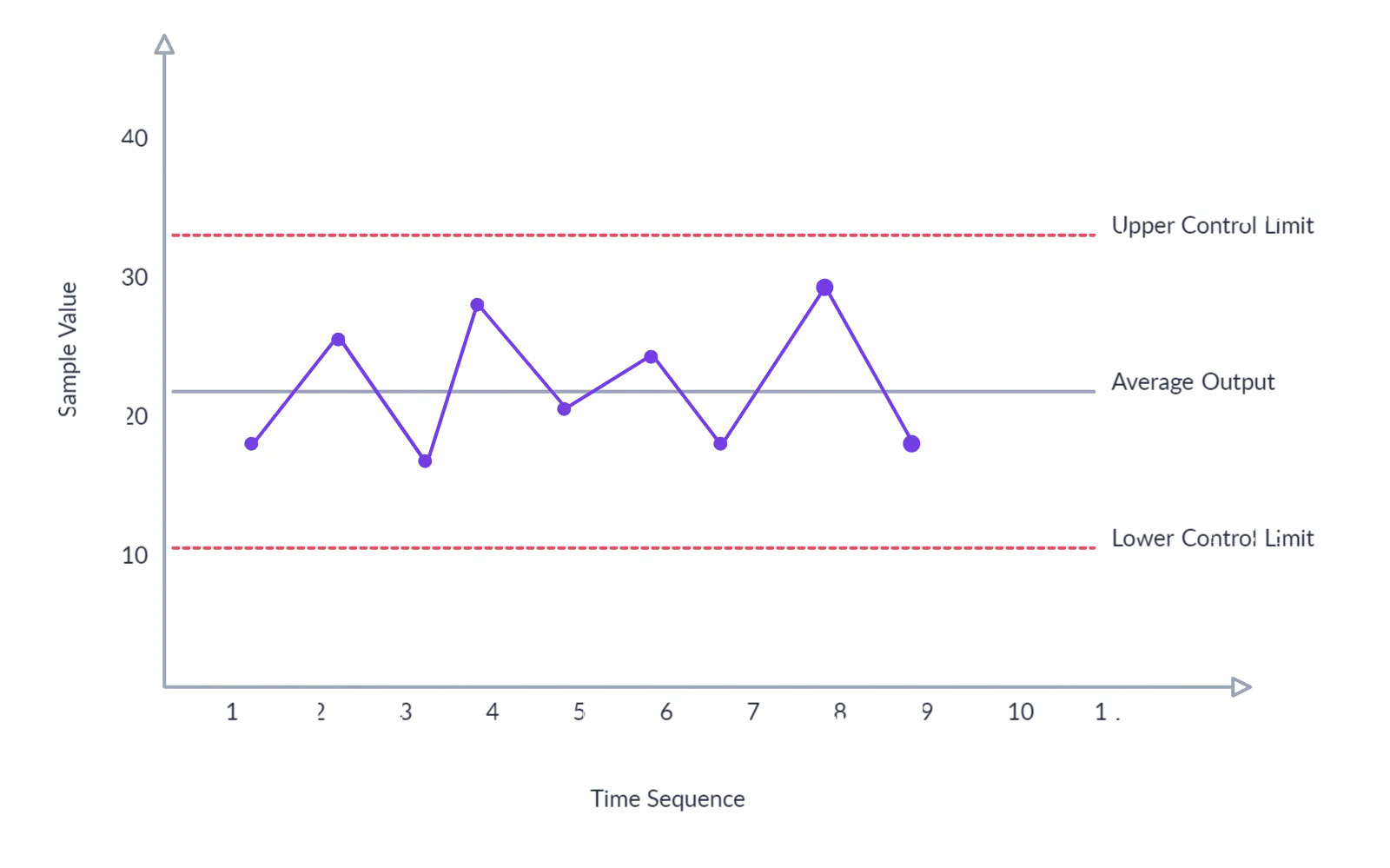
Pareto Chart
The Pareto chart is a combination of a bar graph and a line graph. It helps identify the facts needed to set priorities.
The Pareto chart organizes and presents information in such a way that makes it easier to understand the relative importance of various problems or causes of problems. It comes in the shape of a vertical bar chart and displays the defects in order (from the highest to the lowest) while the line graph shows the cumulative percentage of the defect.
- To identify the relative importance of the causes of a problem.
- To help teams identify the causes that will have the highest impact when solved.
- To easily calculate the impact of a defect on the production.
- Analyzing customer feedback to identify the most common product or service issues.
- Prioritizing improvement efforts based on the frequency of quality incidents.
- Identifying the major causes of delays in project management.
Helps focus improvement efforts on the most significant factors or problems, leading to effective allocation of resources and improved outcomes.
How to create a Pareto chart
- Select the problem for investigation. Also, select a method and time for collecting information. If necessary create a check sheet for recording information.
- Once you have collected the data, go through them and sort them out to calculate the cumulative percentage.
- Draw the graph, bars, cumulative percentage line and add labels (refer to the example below).
- Analyze the chart to identify the vital few problems from the trivial many by using the 80/20 rule . Plan further actions to eliminate the identified defects by finding their root causes.
- Quality managers or improvement teams looking to prioritize improvement initiatives.
- Project managers seeking to identify and address the most critical project risks.
- Sales or marketing teams analyzing customer feedback or product issues.

What’s Your Favorite Out of the 7 Basic Quality Tools?
You can use these 7 basic quality tools individually or together to effectively investigate processes and identify areas for improvement. According to Ishikawa, it’s important that all employees learn how to use these tools to ensure the achievement of excellent performance throughout the organization.
Got anything to add to our guide? Let us know in the comments section below.
Join over thousands of organizations that use Creately to brainstorm, plan, analyze, and execute their projects successfully.
FAQs about 7 Basic Quality Tools
Quality problems in an organization can manifest in various forms and affect different areas of operations.
- Product defects: Products may have defects or non-conformities that deviate from quality specifications, leading to customer dissatisfaction, returns, or warranty claims.
- Service errors: Service errors can occur when services do not meet customer expectations, such as incorrect billing, delays in delivery, or inadequate customer support.
- Process inefficiencies: Inefficient processes can lead to delays, errors, or rework, resulting in increased costs, decreased productivity, and customer dissatisfaction.
- Poor design or innovation: Inadequate product design or lack of innovation can lead to products that do not meet customer needs, lack competitive features, or have usability issues.
- Supplier quality issues: Poor quality materials or components from suppliers can affect the overall quality of the final product or service.
- Ineffective quality management systems: Inadequate quality management systems, such as lack of quality standards, processes, or documentation, can contribute to quality problems throughout the organization.
The basic quality improvement steps typically follow a systematic approach to identify, analyze, implement, and monitor improvements in processes or products.
- Clearly articulate the problem or identify the area for improvement.
- Collect relevant data and information related to the problem.
- Analyze the collected data to identify patterns, root causes, and opportunities for improvement.
- Brainstorm and generate potential improvement ideas or solutions.
- Assess the feasibility, impact, and effectiveness of the generated improvement ideas.
- Develop an action plan to implement the chosen solution.
- Continuously monitor and measure the results of the implemented solution.
- Based on the monitoring results, evaluate the effectiveness of the implemented solution.
- Once the improvement is successful, document the new processes, best practices, or standard operating procedures (SOPs).
- Iterate through the steps to continuously improve processes and products.
More Related Articles
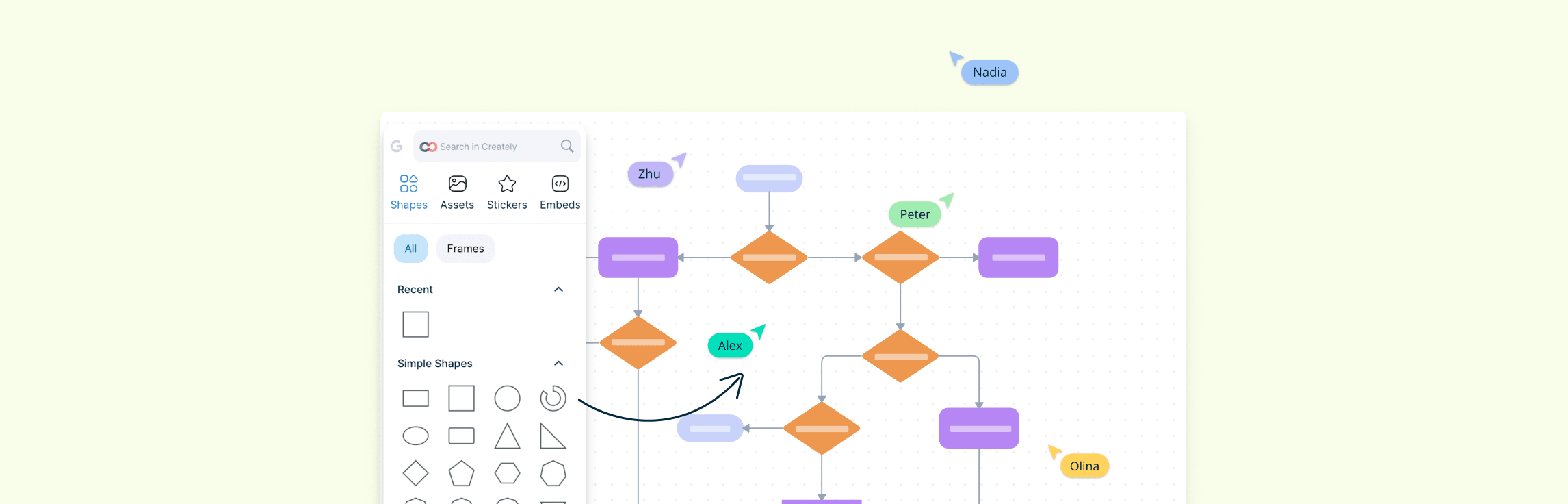
Amanda Athuraliya is the communication specialist/content writer at Creately, online diagramming and collaboration tool. She is an avid reader, a budding writer and a passionate researcher who loves to write about all kinds of topics.
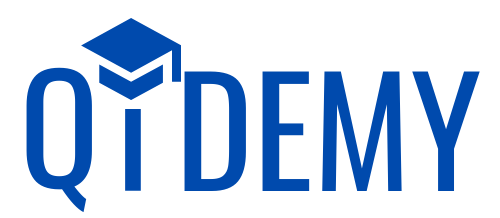
What are 7 QC Tools? | Free Downloadable Templates
- Post author: Manish Singla
- Post published: April 9, 2022
- Post category: Quality 101
- Post comments: 0 Comments
As a quality engineer, you know that using the right tools is critical to success. In this article, we’ll discuss seven of the most important quality control tools i.e. 7 QC Tools, and how they can help your business.
We’ll also explore some of the benefits of each tool and how to use them effectively.
By understanding these tools and incorporating them into your quality control process, you can ensure that your products are consistently high-quality.
Let’s get started!
Table of Contents
Origin of 7 QC Tools
The 7QC tools are said to have been developed by Kaoru Ishikawa in postwar Japan, inspired by Benkei’s seven famous weapons.
Benkei was a Japanese warrior monk who armed himself with seven weapons and was on a personal quest to take 1,000 swords from samurai warriors who he considered arrogant and undeserving.
In 1950, Dr. W. Edwards Deming gave a series of lectures to a group of Japanese scientists and engineers in which he made his first public appearance outside the United States.
Unfortunately, most people were intimidated by the subject’s complexity, so Ishikawa concentrated on only a few tools that would suffice for most quality-related concerns.
#1 Checksheet
Checksheet is a data collection tool. It is an analytical tool used to collect, record, and present data for the objective of conducting analysis.
Checksheet is used to collect both quantitative and qualitative data.
When a Check-sheet is used for collecting Quantitative data it is generally called a Tally Sheet .
Data Collection is the primary step for any improvement identification or problem analysis.
Types of the checksheets are majorly based on the type and purpose of data collected.
Following are the types of checksheets:
- Classification Checksheet
- Defect Location CheckSheet
- Frequency Checksheet
- Measurement Scale Checksheet

To read about Checksheets in more detail, check our article on Checksheet.
What is Checksheet? | Free Template
#2 Histogram
A histogram is a graphical tool used for representing data as frequency distribution.
It groups data into continuous number ranges and each range corresponds to a vertical bar i.e. the height of each bar shows how many cases fall into each range.
Each bar indicates the number of observations that lie in-between the range of values, known as class or bin.
A histogram is a two-axis chart. Its Y-Axis displays the frequency and the X-Axis displays the number range. One of the distinguishing features of a Histogram is that there are no gaps between the range bars.
The histogram can be classified into different types based on the shape of the frequency distribution of the data. We can categorize histograms into 5 types based on their shapes. They are listed below:
- Bell Shaped Histogram
- Skewed Right Histogram
- Skewed Left Histogram
- Uniform Histogram
- Bimodal Histogram
- Multimodal Histogram
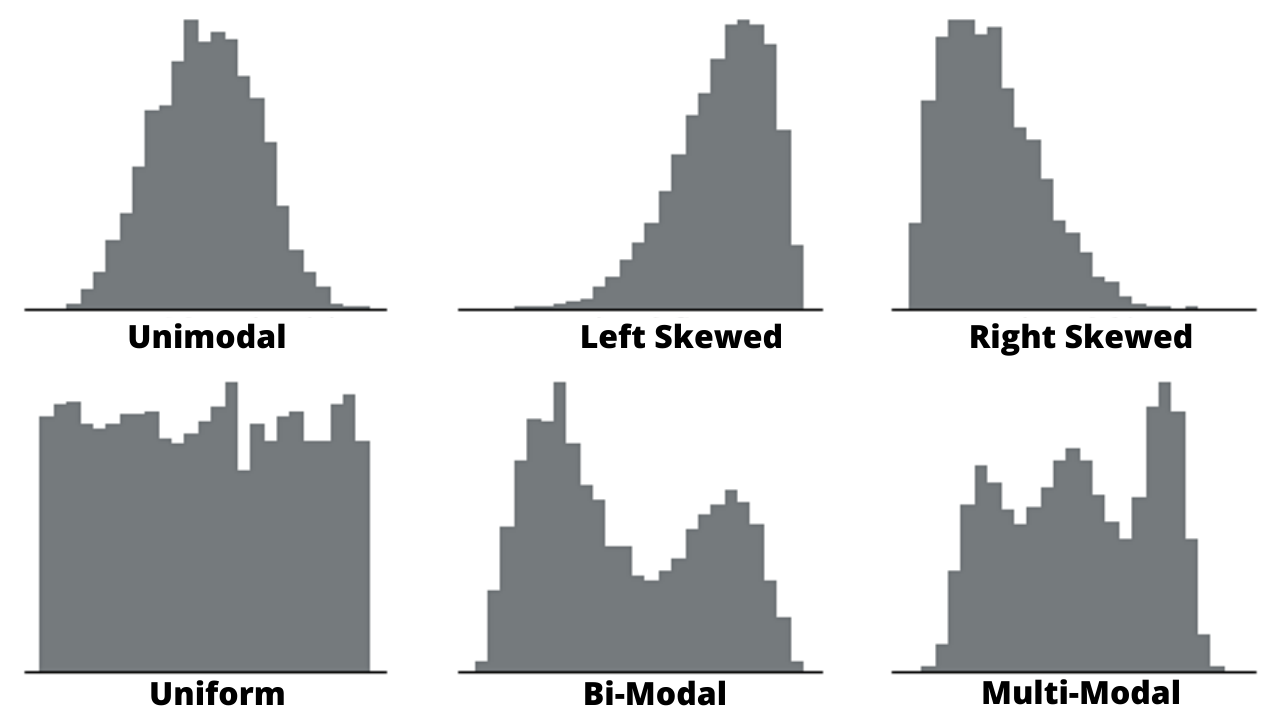
To read about Histogram in more detail, check our article on Histogram.
What is Histogram?
#3 Scatter Diagram
A scatter diagram or scatter plot is a mathematical diagram that plots pairs of data on an X-Y graph in order to reveal the relationship between the data sets .
In other words, scatter diagrams help us understand how one set of data affects another.
They are commonly used in scientific and statistical analysis , as well as in business and marketing to visualize the relationships between different factors.
For example, scatter diagrams can be used to study the correlation between two variables – such as price and demand – or to investigate how a change in one variable affects the other.
There are many different types of scatter plots, but all share the same basic features: an X-axis (horizontal) and a Y-axis (vertical) , as well as a series of points that represent the data. The type of scatter plot will vary depending on what information you want to glean from the data.
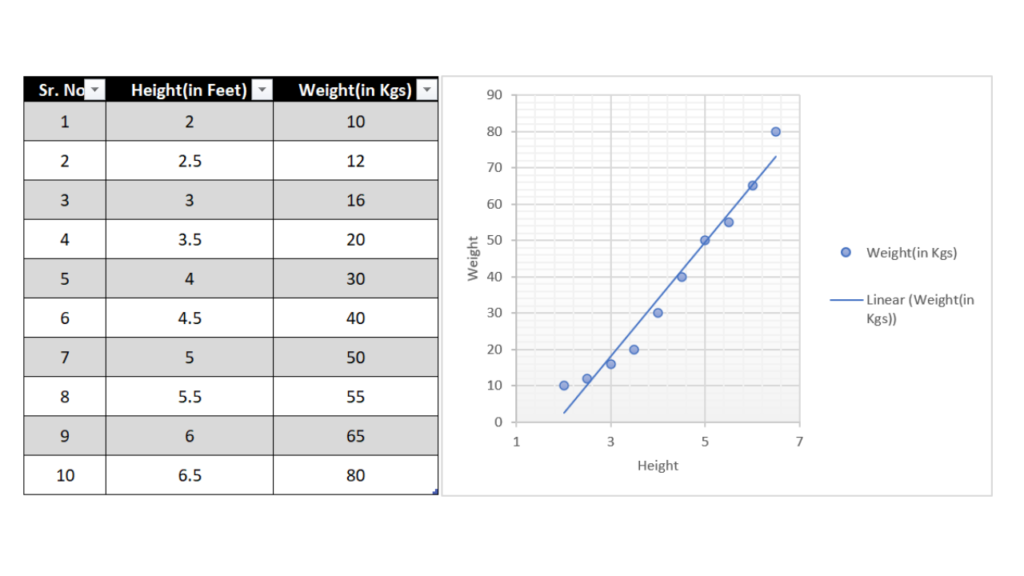
There are several advantages of scatter diagrams:
- They allow you to visualize the relationship between two variables.
- They can help you identify outliers in your data.
- They can help you identify patterns in your data .
- They can help you understand how the variables are related to each other .
- They can help you determine the direction of the relationship between the two variables.
To read about scatter diagrams in more detail, check our article on Histogram.
What is Scatter Diagram?
#4 Fishbone Diagram
A Fishbone diagram is a graphical tool used for organizing potential causes of a problem in a logical manner. The fishbone diagram identifies many possible causes for an effect or problem.
It can be used to structure a brainstorming session. It immediately sorts ideas into useful categories. It is mostly used in conjunction with other problem-solving techniques, such as 5 Why root cause analysis.
It is called a fishbone diagram because of its shape . Its shape looks like a fishbone and hence the name fishbone diagram.
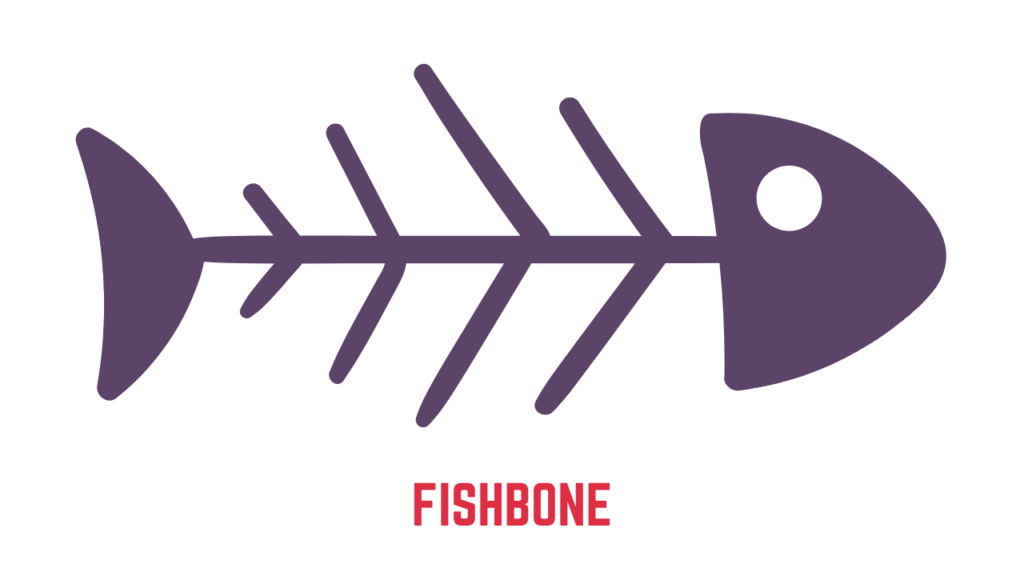
There are a number of advantages to using fishbone diagrams:
- They help to identify the root causes of problems.
- They are an effective way of organizing and visualizing data.
- They can be used to generate hypotheses about problems.
- Help prioritize relevant causes, so underlying root causes are addressed first.
To read about Fishbone Diagram in more detail, check our article on the Fishbone diagram.
What is Fishbone Diagram?
#5 Pareto Charts
A Pareto chart is a graphical tool used to display the relative proportions of occurrence of different values. It is named after economist Vilfredo Pareto, who observed that 80% of Italy’s land was owned by 20% of its population.
The Pareto principle, also known as the 80/20 rule , has been popularized in business and quality management as a way to focus on those activities that will yield the most results . The theory behind the principle is that a relatively small number of causes (the vital few) produce the majority of effects (the trivial many).
In other words, you can achieve a lot with a little effort if you focus on the right things . When applied to quality improvement, the Pareto principle can help you prioritize actions and allocate resources to achieve the greatest impact.
The bars are arranged with the longest on the left and the shortest on the right so they visually depict what percentage occurs more often than others. A Pareto chart can be used to find what factors are more important so that you can focus on them.
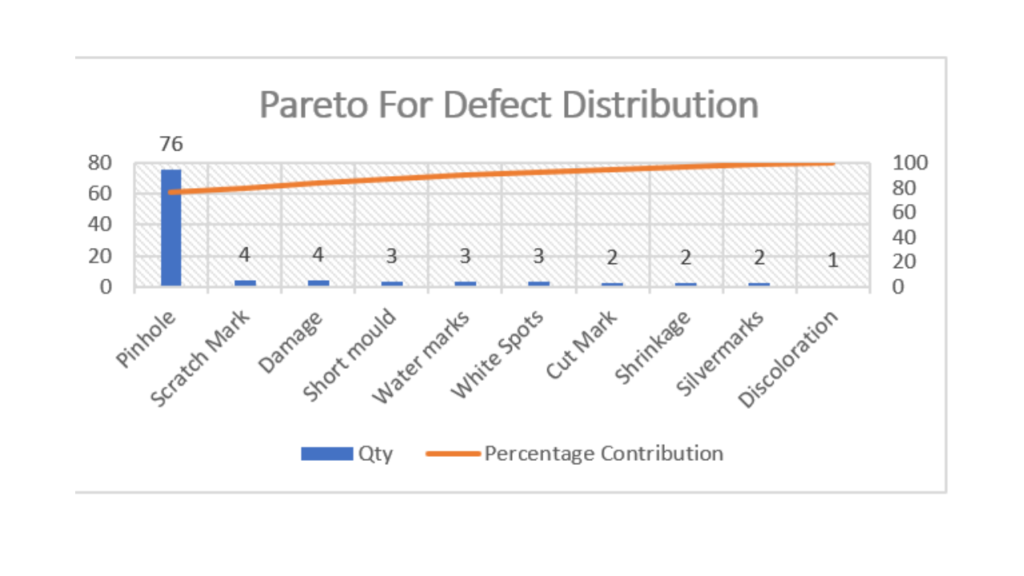
Pareto Charts offer multiple benefits :
- One of the advantages of the Pareto chart is that it helps to identify the main cause of defects or problems. Defects are ranked in order of their severity.
- The Pareto chart helps to determine the cumulative impact of the defect. In other words, it helps to identify the overall impact of all the defects.
- Another advantage of the Pareto chart is that it is simple and easy to use. It helps to prioritize the defects, and it can be used to determine the corrective action for the highest priority defects.
- The Pareto principle or 80-20 rule states that 80% of the effects come from 20% of the causes. This principle can be applied to many areas of life, and it is particularly useful for problem-solving. The Pareto chart is based on this principle, and it can be used to identify the problems that have the biggest impact.
To read about Pareto Charts in more detail, check our article on Pareto Charts.
What is Pareto Chart?
#6 Stratification
Stratification is a quality control tool for sorting data, things, and people into separate and distinct categories. Stratifying your data can help you figure out what it means, revealing patterns that might otherwise be undetectable when it’s grouped together.
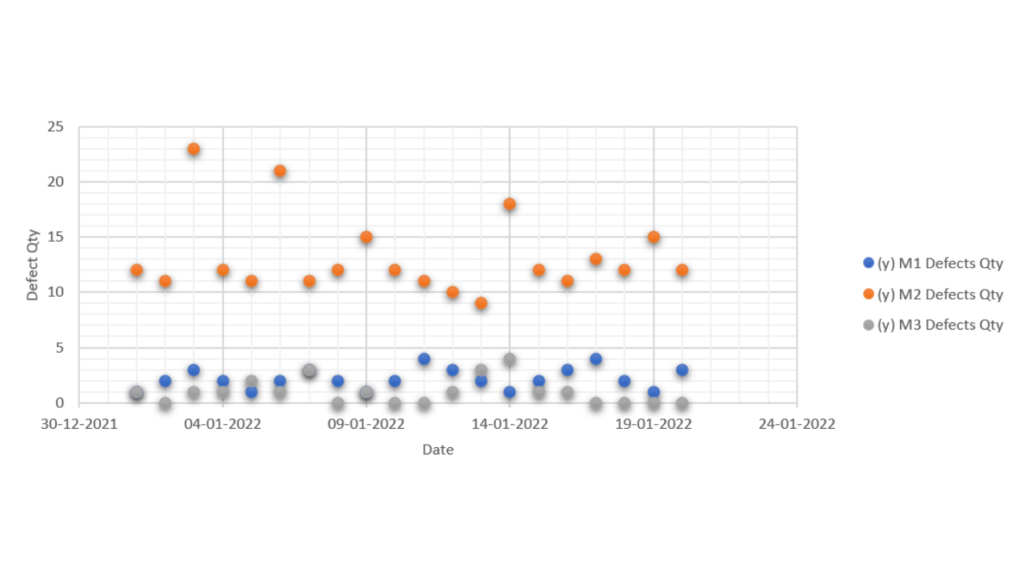
To read about stratification in more detail, check our article on Stratification.
What is Stratification?
#7 Control Charts
Control Charts are graphical tools used to monitor and control a process. There are different types of Control Charts, but all aim to help identify and correct process problems.
Control charts can be used in many industries, such as healthcare, manufacturing, and as part of various methodologies such as TQM, Six Sigma, Kanban, and project management.
Control charts are used to study how a process changes over time and to identify when and how the process goes out of control. Control charts can help you to improve the quality of your product or service and to ensure that your process is running smoothly.
There are many benefits to using control charts, including:
- they help to identify problems in a process
- they help to determine the cause of the problem
- they help to find the appropriate corrective action
- they help to track the progress of the corrective action
- They help to prevent future problems.
To read about Control Charts in more detail, check our article on Control Charts.
What are Control Charts?
How to use 7 QC Tools?
Each of the 7 QC Tools provides its own unique benefits that can help improve the quality of products. Here is a description of how each tool can be used:
– Control Chart : The Control Chart can be used to track and measure the variability of a process.
The Control Chart can help operators identify and track special causes of variation, which can help improve the quality of products.
– Pareto Chart : The Pareto Chart can be used to identify and prioritize the most important causes of defects. The Pareto Chart can help operators focus on the most important problems and improve the quality of products.
– Histogram : The Histogram can be used to track and measure the distribution of data. The Histogram can help operators identify and track special causes of variation, which can help improve the quality of products.
– Scatter Diagram : The Scatter Diagram can be used to identify and track the relationship between two variables. The Scatter Diagram can help operators identify and track special causes of variation, which can help improve the quality of products.
– Check Sheet : The Check Sheet can be used to track and measure the characteristics of a process.
– Flowchart : The Flowchart can be used to map and understand the flow of a process.
– Cause and Effect Diagram : The Cause and Effect Diagram can be used to identify and track the relationships between causes and effects.
New 7 QC Tools
In 1976, the Union of Japanese Scientists and Engineers (JUSE) saw the need for tools to promote innovation, communicate information, and successfully plan major projects.
A team researched and developed the seven new quality control tools, to be used along with the 7 basic quality tools.
Often called the seven management and planning (MP) tools , or simply the seven management tools.
The seven new tools, listed in an order that moves from abstract analysis to detailed planning, are:
- Affinity Diagram
- Relations Diagram
- Tree Diagram
- Matrix Diagram
- Arrows Diagram
- Process Decision Program Chart
- Prioritization Matrix- Matrix Data Analysis
Affinity Diagram
An affinity diagram is a tool that is used for organizing and sorting data. It is used to identify the similarities and differences between a group of items.
The affinity diagram is also known as the KJ Method, named after Japanese quality control experts Jiro Kawakita and Kaoru Johansson.
The method was developed in the early 1960s. The affinity diagram is used to identify the cause-and-effect relationships between different items.
Relationship Diagram
A relationship diagram is a tool that is used to identify the relationships between different items.
It is also known as the Ishikawa diagram, named after quality control expert Kaoru Ishikawa. The diagram was developed in the early 1960s.
It helps Find Solutions by Clarifying Relationships with Complex Interrelated Causes. To allow a team to systematically identify, analyze, and classify the cause and effect relationships that exist among all critical issues.
- Useful at the planning stage for obtaining perspective on the overall situation.
- Facilitates consensus among team
- Assists to develop and change people’s thinking
- Enables priorities to be identified accurately
Tree Diagrams
A tree diagram is a graphical tool used to represent the hierarchical relationships between items in a data set.
Also known as a “decision tree,” a tree diagram can be used to evaluate various scenarios and determine the optimal course of action.
Tree diagrams are commonly used in project management, business decision-making, risk assessment, and event planning.
Matrix Diagram
Matrix diagrams are used to help identify and understand the relationships between elements of a system.
In quality control, matrix diagrams can be used to identify and understand the relationships between various quality characteristics and the causes that affect them.
Consists of a two-dimensional array to determine the location and nature of the problem Discovers key ideas by relationships represented by the cells in the matrix.
- It helps incorporate data while working on different ideas based on extensive experience
- Clarifies relationships among different elements
- Makes the overall structure of the problem immediately obvious
- Combined with two to four types of diagrams, the location of the problem is clearer.
Arrow Diagram
Arrow Diagram is used for Working Out Optimal Schedules and Controlling Them Effectively.
- The arrow diagram shows relationships among tasks needed to implement a plan.
- Allows overall tasks to be viewed and potential snags to be identified before work starts. This leads to discovery of possible improvements
- Makes it easy to monitor the progress of work
- Deals promptly with changes to the plan
- Improves communication among team
Process Decisions Program Charts (PDPC)
PDPCs are used for planning the activities needed to solve problems when information is incomplete or the situation is fluid and hard to forecast.
Examples include planning an R & D project, mapping out countermeasures against long-term chronic problems, and planning a sales campaign.
A PDPC consists of a series of steps linked in sequence. Its goal is to depict the events and contingencies likely to occur when progressing from a starting point to one or more final outcomes
Prioritization Matrix
This technique quantifies, arranges data, and presents it in Matrix form.
It involves finding indicators that differentiate and attempt to clarify a large amount of information.
Prioritization Matrix is used by teams to narrow down options through a systematic approach of comparing choices by selecting, weighting, and applying criteria.
Benefits of 7 QC Tools
The 7 QC Tools have been shown to provide a number of benefits, including:
- Improved product quality
- Increased efficiency
- Reduced manufacturing costs
- Reduced waste and scrap
- Improved customer satisfaction
- Improved safety and health
Each of the 7 QC Tools provides its own unique benefits that can help improve the quality of products.
Hope this article was helpful. If yes do comment and share with your peers.
Keep improving!
- www.asq.org
- https://www.lucidchart.com/
You Might Also Like
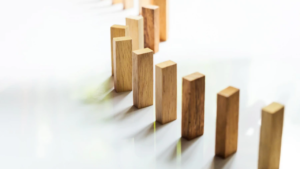
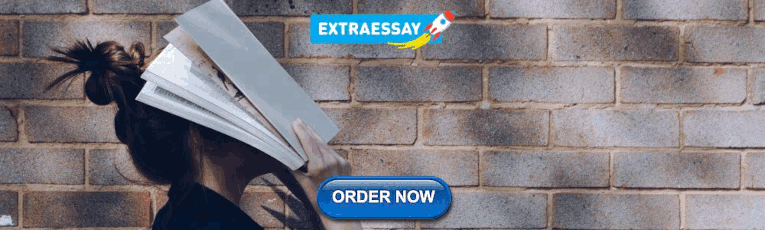
What is Fishbone Diagram? | Free Downloadable Template
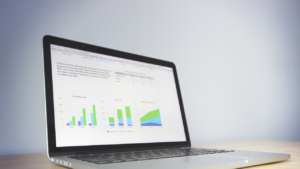
What is a Scatter Diagram? | Free Excel Template
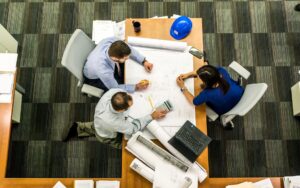
The benefits of implementing Total Quality Management (TQM) approach
Leave a reply cancel reply.
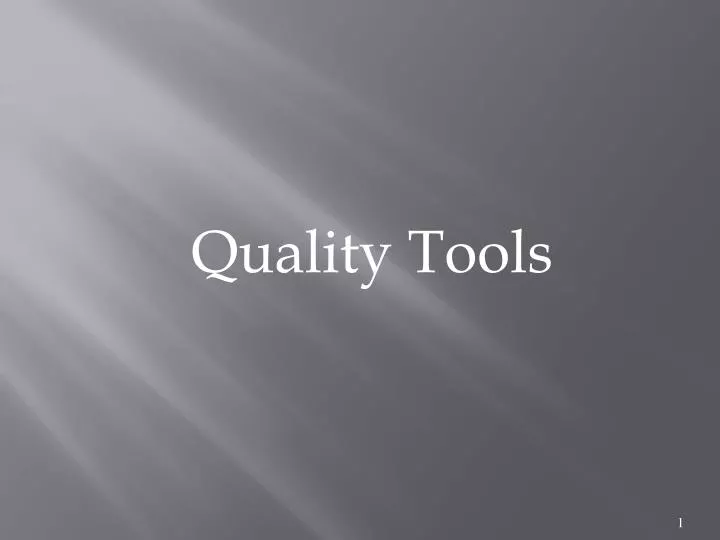
Quality Tools
Nov 08, 2014
560 likes | 807 Views
Quality Tools. Key Contributors to Quality Management. Key Contributors to Quality Management. Total Quality Management. A philosophy that involves everyone in an organization in a continual effort to improve quality and achieve customer satisfaction. Process Improvement.
Share Presentation
- process improvement
- quality tools
- control phase
- process improvement cycle
- stable operations stable ops

Presentation Transcript
Key Contributors to Quality Management
Total Quality Management A philosophy that involves everyone in an organization in a continual effort to improve quality and achieve customer satisfaction
Process Improvement • A systematic approach to improving a process • Overview of the approach • process mapping • analyze the process • redesign the process
Plan Act Do Study The PDSA Cycle
Select a process Document Study/document Evaluate Seek ways to Improve it Implement the Improved process Design an Improved process The Process Improvement Cycle
Process Improvement Tools • There are a number of tools that can be used for problem solving and process improvement • Tools aid in data collection and interpretation, and provide the basis for decision making
Seven Basic Quality Tools • Check sheets • Flowcharts • Scatter diagrams • Histograms • Pareto analysis • Control charts • Cause-and-effect diagrams
Check Sheet Monday • Billing Errors • Wrong Account • Wrong Amount • A/R Errors • Wrong Account • Wrong Amount
Flowchart Process Process Process? OK? OK Process Identify value added steps, rework loops, flow loops, etc.
The Operations FunctionInputsTransformed into Outputs Inputs Labor Personnel Capital Machines Money Resources Raw Material Components Energy Facilities Management Arts & Sciences Managerial Talent Technical Expertise
The Operations FunctionInputs Transformed into Outputs Inputs Labor Personnel Capital Machines Money Resources Raw Material Components Energy Facilities Management Arts & Sciences Managerial Talent Technical Expertise Process The firm transforms inputs to outputs (operations, finance, marketing)
The Operations FunctionInputs Transformed into Outputs Inputs Labor Personnel Capital Machines Money Resources Raw Material Components Energy Facilities Management Arts & Sciences Managerial Talent Technical Expertise Process The firm transforms inputs to outputs (operations, finance, marketing) Outputs
The Operations FunctionInputs Transformed into Outputs Inputs Labor Personnel Capital Machines Money Resources Raw Material Components Energy Facilities Management Arts & Sciences Managerial Talent Technical Expertise Process The firm transforms inputs to outputs (operations, finance, marketing) Outputs Clients, customers
Example Processes • Insurance • Banks • Retail • Golf Course • School Discuss operations for two companies / organizations that you are familiar with. Use one or more of the seven quality tools for one of the companies.
Scatter Diagram Variable B Variable A
Histogram frequency A B C D E
Number of defects Offcenter Smeared print Missing label Other Loose Pareto Analysis 80% of the problems may be attributed to 20% of the causes.
1020 UCL 1010 1000 990 LCL 980 970 0 1 2 3 4 5 6 7 8 9 10 11 12 13 14 15 Control Chart
UCL UCL UCL LCL LCL Additional improvements made to the process LCL Process centered and stable Process not centered and not stable Tracking Improvements
Methods Materials Cause Cause Cause Cause Effect Cause Cause Environment Cause Cause Cause Cause Cause Cause People Equipment Cause-and-Effect Diagram
What is Six Sigma? • Appropriate Metric – 3.4 million defects per million opportunities • Robust Methodology – Tools plus implementation methods to make success more likely • Philosophy – Cost-focused, data-driven
What is Six Sigma?Key Concepts • Critical to Quality: What attributes are most important to the customer? (CTQ, CTC, CTD) • Defect: Failing to deliver what the customer wants / expects (DPMO) • Variation: The level of unpredictability the customer experiences
What is Six Sigma?Key Concepts • Process Capability: What your process can deliver – consistently • Stable Operations:Stable ops are predictable • Design for Six Sigma:Designing to meet customer needs and process capability
DMADV - DMAIC Existing Processes New Processes
Define Phase - Tools • Project Charter • Stakeholder Analysis • Affinity Diagram • SIPOC • Voice of the Customer • CT Tree • Kano Model • SWOT Analysis • Cause-and-Effect Diagrams • Supplier Segmentation • Project Management
Charter • Problem statement • Business case • Goals, milestones, success criteria, & deliverables • Project scope / boundaries • Roles & responsibilities • Stakeholder support / approval needed
Business Case
Define Outputs • Once completed, the Define Phase should answer the following questions: 1) Who is the customer? 2) What matters? 3) What is the scope? 4) What defect am I trying to reduce? 5) What are the improvement targets?
The Measure Phase • Purpose • To collect current performance of the process identified in the Define phase • This data is used to determine sources of variation and serve as a benchmark to validate improvements
Measure - Key Concepts • Measurement • Variation • Exists naturally in any process and is the reason Six Sigma projects are undertaken • Data • Data Collection Plan • Measurement System Analysis • Ensures measurement techniques are reproducible and repeatable
Data Collection Plan • What data will be collected? • Why is it needed? • Who is responsible? • How will it be collected? • When will it be collected? • Where will it be collected?
Measurement System Analysis • After Data Collection Plan is complete, it needs to be verified before actual data is collected • MSA is performed on a regular basis • MSA ends when a high level of confidence is reached that the data collected accurately depicts the variation in the process
Analyze Phase • The analyze phase allows the Project Team to target improvement opportunities by taking a closer look at the data.
Analyze Phase • Capability Analysis - establishing current performance level • Graphical Analysis - a visual indication of performance using graphs • Root Cause Analysis – developing a hypothesis about the causes of variation • Root Cause Verification – verifying that the planned action will generate the desired improvement
Elements of Improve Phase • Generate Improvement Alternatives • Create a “Should Be” Process Map • Conduct FMEA • Perform Cost/Benefit Analysis • Pilot • Validate Improvement
Control PhaseWhy is it important? • The Control Phase begins as the project team tries to eliminate errors by “Mistake Proofing” their improvement alternative. • Mistake Proofing attempts to eliminate the opportunities for error.
Control PhaseWhy is it important? • Mistake Proofing tries to make it impossible for an operation to be performed incorrectly, and/or correct errors before they are passed to the next worker, where they might become a defect.
Control Phase #2 • During the Control Phase the Project team will: 1) Develop a plan to make sure the measurement system will remain relevant over the long term. 2) Establish Control Charts the process owner will use to manage the process. 3) Create a Reaction Plan to address situations that might cause the process to move out of control.
Control Phase #3 • The Control Phase ends when: 1) Standard Operating Procedures have been updated. 2) Process Operators, the people who do the job, have been trained for the new process. • Once completed, the Control Phase should sustain the gains the project made while implementing ongoing process controls.
Control Phase #4 • When is a project complete? 1) When other Black Belts can see the ongoing controls work 2) When the customer sees the results 3) When the business sees the money.
Stakeholder Analysis
SIPOC Example
SWOT Analysis
Quality Awards Baldrige Award
Malcolm Baldrige National Quality Award (1 of 2) • Began in 1987 • Recognizes achievements of excellent organizations and provide examples to others • may give two awards in each category • manufacturing • small business • service • health care • education
Malcolm Baldrige National Quality Award (2 of 2) • Establishes criteria for evaluating quality efforts • Provides guidance for other American companies
2007 MBNQA Categories and Scoring System 1.0 Leadership 120 2.0 Strategic Planning 85 3.0 Customer and Market Focus 85 4.0 Measurement, Analysis, & Knowledge Management 90 5.0 Workforce Focus 85 6.0 Process Management 85 7.0 Results 450
- More by User
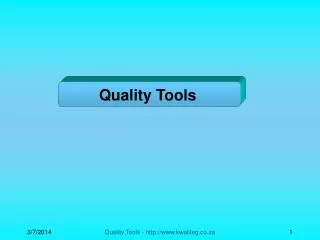
Quality Tools Table of Contents Quality techniques 7 Basic Quality techniques Histograms Pareto Charts Run Charts Scatter Diagrams Control Charts Flow Charts Cause and Effect Diagrams New techniques Other Tools Introduction
554 views • 19 slides
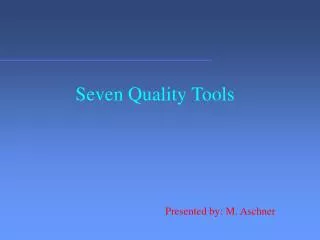
Seven Quality Tools
Seven Quality Tools. Presented by: M. Aschner. Objective. Present an overview of Seven Quality Tools Address purpose and applications Highlight benefits. The Deming Chain Improve Quality Decrease Costs Improve Productivity Decrease Price Increase Market Stay in Business
1.11k views • 39 slides
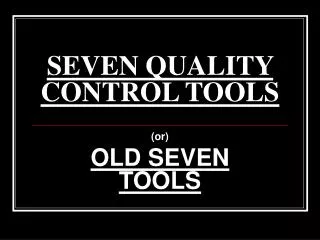
SEVEN QUALITY CONTROL TOOLS
SEVEN QUALITY CONTROL TOOLS. (or) OLD SEVEN TOOLS. Dr.Kaoru Ishikawa, Professor at Tokyo University & Father of Q C in Japan. CAUSE ANALYSIS TOOLS are Cause and Effect diagram, Pareto analysis & Scatter diagram . EVALUATION AND DECISION MAKING TOOLS are decision matrix and multivoting.
1.82k views • 38 slides
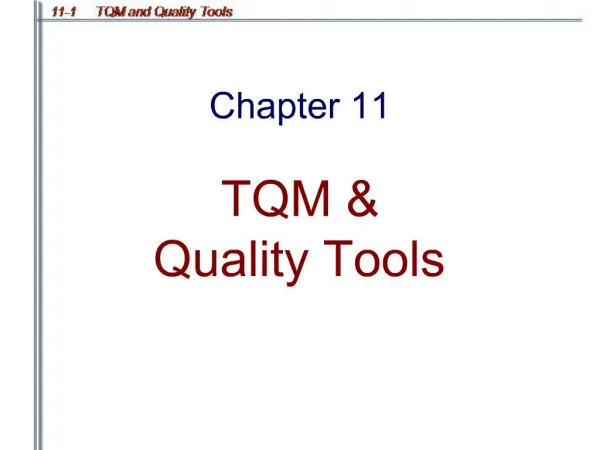
TQM Quality Tools
Total Quality Management. A philosophy that involves everyone in an organization in a continual effort to improve quality and achieve customer satisfaction.. Find out what the customer wantsDesign a product or service that meets or exceeds customer wantsDesign processes that facilitates doing the
983 views • 22 slides
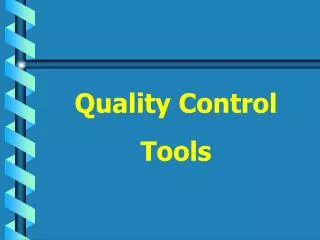
Quality Control Tools
Quality Control Tools. Introduction.
616 views • 12 slides
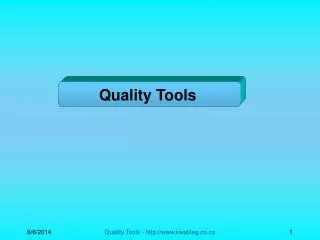
Quality Tools. Table of Contents. Quality techniques 7 Basic Quality techniques Histograms Pareto Charts Run Charts Scatter Diagrams Control Charts Flow Charts Cause and Effect Diagrams New techniques Other Tools. Introduction.
505 views • 19 slides
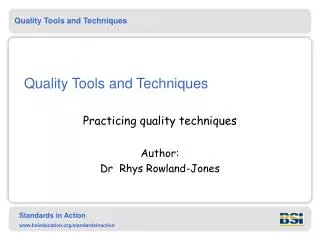
Quality Tools and Techniques
Quality Tools and Techniques. Practicing quality techniques Author: Dr Rhys Rowland-Jones. Session plan. Demonstrate the differing types of quality tools/techniques attributed to the Japanese. Illustrate the applicability of tools and techniques of quality improvement.
649 views • 22 slides
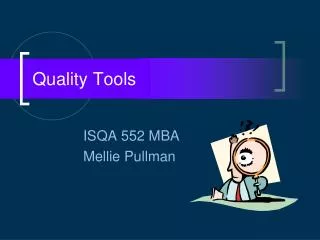
Quality Tools. ISQA 552 MBA Mellie Pullman. Quality Specifications. Design quality : Inherent value of the product in the marketplace Dimensions include: Performance, Features, Reliability, Durability, Serviceability, Response, Aesthetics, and Reputation.
815 views • 42 slides
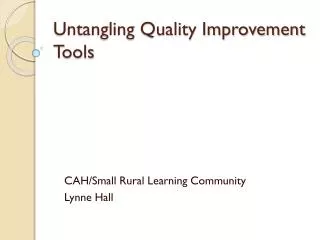
Untangling Quality Improvement Tools
Untangling Quality Improvement Tools. CAH/Small Rural Learning Community Lynne Hall. s2. Histograms. Flow Charts. Run Charts. Check sheets. Scatter Diagrams. Cause and Effect Diagrams. Force Field Analysis. Bar Charts. Pareto Charts. Nominal Group Technique. Root Cause Analysis.
926 views • 63 slides
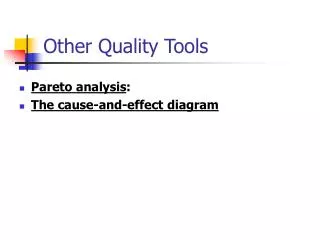
Other Quality Tools
Pareto analysis : The cause-and-effect diagram. Other Quality Tools . Pareto Analysis a simple method for separating the major causes (the 'vital few) of a problem, from the minor ones ('trivial many')
321 views • 13 slides
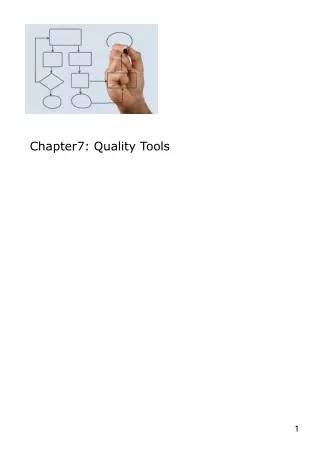
Chapter7: Quality Tools
Chapter7: Quality Tools. QC TOOLS. Tools for Problem Solving & ANALYSIS.
281 views • 12 slides
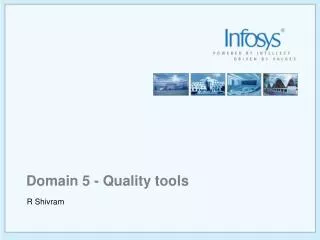
Domain 5 - Quality tools
Domain 5 - Quality tools. R Shivram. Flow. Definition & Types of tools Tools for ideas and information Questions. Definition. A vehicle that assist in performing a task. They can be used in Defining a mission, vision, goals, and objectives Defining Do and Check processes
607 views • 36 slides
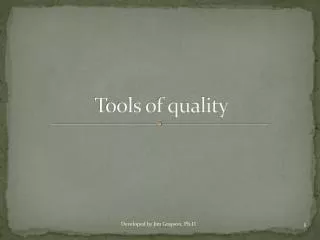
Tools of quality
Tools of quality. 7 QC Tools: The Lean Six Sigma Pocket Toolbook. Flowchart [p. 33-41] Check Sheet [p. 78-81] Histogram [p. 111-113] Pareto [p. 142-144] Cause-and-Effect [p. 146-147] Scatter [p. 154-155] Control Chart [p. 122-135]. Pareto Diagram. Cause and Effect Diagram.
467 views • 35 slides
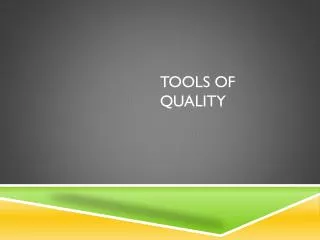
Tools of quality. 7 QC Tools: The Lean Six Sigma Pocket Toolbook. Flowchart [p. 116] Check Sheet [p. 95] Histogram [p. 129] Pareto [p. 178] Cause-and-Effect [p. 49] Scatter [p. 228] Control Chart [p. 75]. Pareto Diagram. Cause and Effect Diagram.
441 views • 30 slides
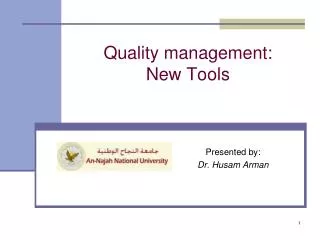
Quality management: New Tools
Quality management: New Tools. Presented by: Dr. Husam Arman. New Quality Tools. Affinity Diagrams Interrelationship Diagrams Tree Diagrams. Affinity Diagrams. Organizes a large amount of verbal data related to a broad problem or subject Ideas, opinions, facts
351 views • 14 slides
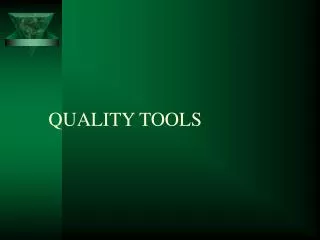
QUALITY TOOLS
QUALITY TOOLS. Table of Contents. Quality techniques 7 Basic Quality techniques Histograms Pareto Charts Run Charts Scatter Diagrams Control Charts Flow Charts Cause and Effect Diagrams New techniques Other Tools. Introduction.
702 views • 41 slides
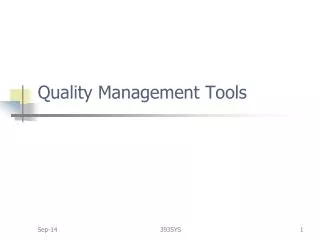
Quality Management Tools
Quality Management Tools. 1 Modern Quality Management. Modern quality management requires customer satisfaction prefers prevention to inspection recognizes management responsibility for quality Noteworthy quality experts include Deming, Juran, Crosby, Ishikawa, Taguchi, and Feigenbaum
1.09k views • 28 slides
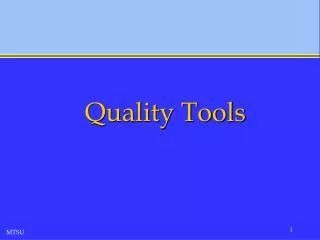
Quality Tools. Plan. Act. Do. Study. The PDSA Cycle. Select a process. Document. Study/document. Evaluate. Seek ways to Improve it. Implement the Improved process. Design an Improved process. The Process Improvement Cycle. Process Improvement Tools.
1.52k views • 124 slides
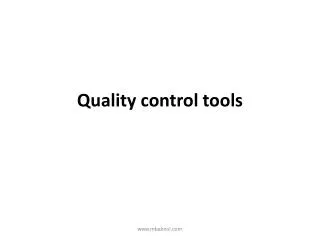
Quality control tools
Quality control tools. Introduction.
412 views • 21 slides
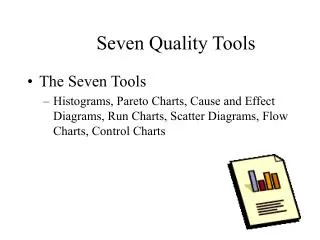
Seven Quality Tools. The Seven Tools Histograms, Pareto Charts, Cause and Effect Diagrams, Run Charts, Scatter Diagrams, Flow Charts, Control Charts. Ishikawa’s Basic Tools of Quality.
469 views • 28 slides
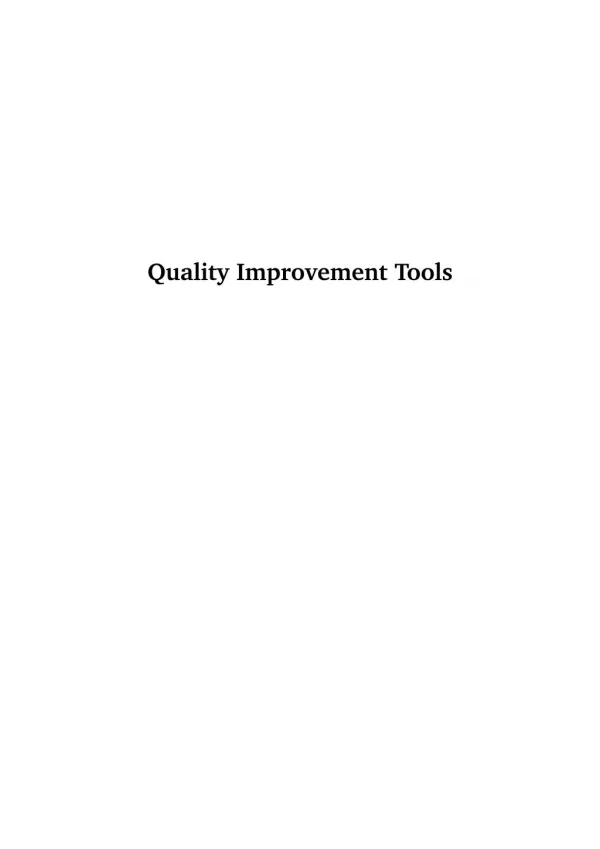
Quality Improvement Tools
The purpose of this guidance is to bestow you a brief knowledge regarding quality tools in order to provide the root causes of the quality problem which are related to manufacturing of mechanical seals, which are adopted by carbon steel flanges manufacturers. The modes of the defects on the production line are investigated via direct observation on the production line plus statistical tools such as Histogram, Check sheets, Pareto Analysis, Cause & Effect Diagram, etc. All these tools are used in enhancing the procedure by continuous monitoring via inspection of the samples. The work displays utility of quality tools in order to find out the root causes of the issues as well as eliminates them.
268 views • 4 slides
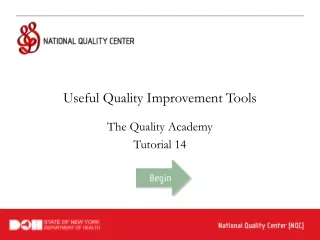
Useful Quality Improvement Tools
Useful Quality Improvement Tools. The Quality Academy Tutorial 14. Learning Objectives: You Will Learn About…. Tools for understanding processes (e.g., flowcharts) Tools to analyze and display data (e.g., run charts, histograms) Tools to organize ideas (e.g., cause-and-effect diagrams).
556 views • 41 slides
Home Collections Strategy / Business Plan Tqm Quality Tools PowerPoint Presentation
Quality Tools PowerPoint Presentation & Google Slides

Admirable Quality Tools Template PowerPoint Presentation
About the template:, features of the template:.
- 100% customizable slides and easy to download.
- Slides are available in different nodes & colors.
- The slide contained in 4:3 and 16:9 format.
- Easy to change the slide colors quickly.
- Eye-grabbing design slide for the presentation.
- The excellent visuals of this slide will make your presentation eye-catching.
- Quality Tools
- Quality Management
- Quality Control Tools
- Total Quality Management
- Quality Diagram
- Quality Design
- Quality Infographics

297+ Templates

1100+ Templates

Team / Teamwork
348+ Templates

Strategy / Business Plan
6673+ Templates

55+ Templates

493+ Templates

413+ Templates

72+ Templates

685+ Templates

13+ Templates
You May Also Like These PowerPoint Templates

NTRS - NASA Technical Reports Server
Available downloads, related records.
- Open access
- Published: 31 May 2024
Freely available, online videos to support neurological physiotherapists and students in task-specific training skill acquisition: a scoping review
- Nicola C.M. Towersey 1 ,
- Kelvin Sasse 1 ,
- Verna Stavric 1 ,
- Gemma Alder 1 &
- Nicola L. Saywell 1
BMC Medical Education volume 24 , Article number: 603 ( 2024 ) Cite this article
78 Accesses
Metrics details
Videos to support learning of clinical skills are effective; however, little is known about the scope and educational quality of the content of freely available online videos demonstrating task-specific training (TST). This review aimed to determine the extent, characteristics of freely available online videos, and whether the content is suitable to guide skill acquisition of task-specific training for neurological physiotherapists and students.
A scoping review was conducted. Google video and YouTube were searched in December 2022. Videos that met our eligibility criteria and were explicitly designed for (TST) skill acquisition were included in the report.
Ten videos met the inclusion criteria and were difficult to find amongst the range of videos available. Most were presented by physiotherapists or occupational therapists, originated from the USA, featured stroke as the condition of the person being treated, and involved a range of interventions (upper limb, constraint induced movement therapy, balance, bicycling). Most videos were created by universities or private practices and only two used people with a neurological condition as the participant. When the content of videos and their presentation (instruction and/or demonstration), was assessed against each key component of TST (practice structure, specificity, repetition, modification, progression, feedback), five of the videos were rated very suitable and five moderately suitable to guide skill acquisition. Most videos failed to demonstrate and provide instruction on each key component of TST and were missing at least one component, with feedback most frequently omitted.
Conclusions
There are many freely available online videos which could be described as demonstrating TST; very few are suitable to guide skill acquisition. The development of a standardised and validated assessment tool, that is easy to use and assesses the content of TST videos is required to support learners to critically evaluate the educational quality of video content. Guidelines based on sound teaching theory and practice are required to assist creators of online videos to provide suitable resources that meet the learning needs of neurological physiotherapists and students.
Peer Review reports
Task-specific training (TST) is a common rehabilitation strategy used and taught by a wide range of allied health professionals including physiotherapists, occupational therapists, speech language therapists and academic institutions. It involves goal directed practice, repetition, progressive challenge, and positive reinforcement to optimise motor learning [ 1 ]. TST has been shown to be effective at inducing cortical reorganization, decreasing disability and improving functional outcomes for people with neurological conditions such as stroke, Parkinson’s disease, spinal cord injury and cerebral palsy [ 2 , 3 , 4 , 5 , 6 , 7 , 8 ]. TST is referred to in the literature by a range of terms, including ‘repetitive functional task practice’, ‘repetitive task practice’ [ 3 ], ‘task-orientated therapy’ [ 1 ] and ‘task-related training’ [ 9 ]. For this review, it will be referred to as task-specific training (TST).
The widespread use of the internet has extended traditional education by enabling users to search for, watch, and share a large variety of freely available online videos to supplement their learning. The use of online videos has grown in popularity over the past decade with ease of access and low cost making them one of the most frequently used self-learning resources for health professionals and students [ 10 , 11 , 12 ]. Videos have been shown to significantly improve learning outcomes [ 13 ], however, mechanisms for controlling the content within online videos are limited. The results of internet searches are determined by an algorithm using likes, views, and popularity rather than an assessment of whether the content is suitable to guide skill acquisition [ 14 , 15 ] and previous studies have found online videos often omit key learning points and are of variable educational quality [ 14 , 16 , 17 , 18 ].
Freely available online videos may be useful to guide skill acquisition and reinforce learning for neurological physiotherapists and students. However, there is a need to evaluate the quality of the content of these videos to ensure that they are based on best practice. To our knowledge, there has been no research exploring the extent, characteristics, and educational quality of freely available online videos for the skill acquisition of TST. In this scoping review, our aim was to determine the extent, characteristics, and whether the content of freely available online videos is suitable to guide skill acquisition of TST.
A scoping review was conducted and carried out according to the Preferred Reporting Items for Systematic Review and meta-analysis for scoping reviews (PRISMA- ScR), adapting the five stages suggested by Arksey and O’Malley and the Joanna Briggs Institute (JBI) for evidence synthesis [ 21 , 22 , 23 ]. An a priori protocol was developed to guide this review prior to undertaking it.
Identifying relevant videos
A detailed search plan outlining the search terms, sources, eligibility criteria, and delimiters was established based on suggestions by Godin et al. [ 24 ], and in consultation with a senior librarian. The JBI; Population, Concept and Context (PCC) elements were used to formulate a combination of search terms to maintain transparency, ensure organised search methods, and reduce the risk of bias [ 23 ]. The population included neurological physiotherapy, the condition of interest or intended audience, were left open. The concept was the demonstration and instruction of TST that a novice could use for skill acquisition. The context included rehabilitation. Refer to Table 1 for the initial search terms.
The inclusion criteria included videos with the stated purpose to teach TST and included an element of physical skill demonstration and instruction. Videos had to be freely available online via a device with internet capabilities, in English, without subscription requirements to access, and within the scope of neurological physiotherapy practice [ 25 ]. There were no restrictions on the rehabilitation setting, date of upload, duration of video, or country of origin (Table 2 ).
A pilot search was carried out as suggested by the JBI guidelines [ 23 ] and following discussion between authors; search terms and the eligibility criteria were refined to reduce ambiguity regarding the definition of TST, and the level of instruction required for the video. For this review, TST included practice of meaningful tasks. Tasks were considered part-task if they were linked to a whole-task reconstruction; virtual reality involving the upper limb was considered part-task as it lacked the manipulation of physical objects and were included. Instructions needed to be provided during TST with sufficient detail to allow a novice to apply it. These could have been in the form of subtitles, voice-over, or directly to the camera.
Google video search engine and YouTube were searched due to their high use, free access and relevancy ordered results [ 26 ]. YouTube has 2,562 million active users, while Google is the dominant global search engine, with an 84.08% worldwide market share [ 26 , 27 ]. Internet Protocol (IP) addresses and being logged into Google accounts have been found to contribute 11.7% to variation in results [ 19 ]. Therefore, searches were performed with personalised search off, in Google Chrome incognito browser, with relevancy sorting on, to improve the consistency of the search results. To reduce the effect of algorithmic searching, all preliminary searches were conducted on the Firefox search engine, with official searches performed in Google incognito, from the same IP address, on a single day in Auckland, New Zealand.
The searches were conducted from Auckland, New Zealand (NZ), on the 16th of December 2022 by KS. The complete search strategy used in Google video search engine and YouTube is in Appendix 1 . Ten searches were conducted on each search engine with the first 10 pages of each search (representing 100 results) screened for relevance. This number was chosen to capture a wide range of the most relevant results, while still being feasible to screen [ 24 ]. Potentially relevant videos were bookmarked in a folder named after the search engine and in a subfolder with the search terms used [ 24 ]. If a video was embedded within a website, it was followed to its source and then bookmarked, to reduce duplicates.
Finally, a series of YouTube channels were hand searched to identify missed videos. Consistency was maintained by the same reviewer (KS), using the same IP address, applying the same method as the primary searches, on a single day (22nd December 2022).
Video selection
Videos were selected using the following process. Duplicates were removed and KS screened all the videos against the eligibility criteria. A second reviewer (NT) independently cross-checked 20% of videos, to check for consistency and appropriate application of the selection criteria. Any discrepancies were referred to NLS to be resolved by consensus.
Data charting
Data charting was used to synthesise and interpret the data [ 21 ]. KS and NT independently viewed the selected videos and summarised the data in a Microsoft (MS) Excel spreadsheet, based on the JBI guidelines [ 22 , 23 ]. The data extracted for this review were the video title, upload date, duration, number of views, likes/ dislikes, the presenter(s), the participant(s), source, country of origin, intervention, the key components of TST (practice structure, specificity, repetition, modification, progression, feedback) and how they were presented (instruction and/or demonstration).
Summarising and reporting results
To address the extent and characteristics of the selected videos, we identified trends using data analysing tools and pivot tables in MS Excel and presented the data descriptively.
Scoring of videos
The suitability of videos to guide skill acquisition was assessed using a pragmatic scoring system developed for this scoping review. Although previous studies have developed scoring systems to evaluate online material [ 28 , 29 ], none were appropriate for the purpose of this study. The scoring system was developed after reviewing pertinent literature [ 30 , 31 ] and seeking expert opinion. It evaluated video content against the agreed key components of TST for motor learning (practice structure, specificity, repetition, modification, progression, feedback) and whether demonstration and instruction were provided on each component. Videos were scored from 0 to 2 for each of the six TST components for a total possible score of 12. Components scored 2 if both demonstration and instruction were provided, 1 if they provided either one, or 0 for a missing component. Those videos scoring 0–4 were considered unsuitable, 5–8 moderately suitable and 9–12 very suitable to guide skill acquisition. Data analysis was conducted by KS, and NT and NSW, physiotherapists with extensive clinical and teaching experience in neurological physiotherapy.
Identification and selection of material
Google Video and YouTube searches resulted in 2,000 videos. After initial screening of titles and thumbnails, 179 were bookmarked as potentially relevant. Hand-searching YouTube channels identified an additional 12 videos, resulting in 191 videos being manually inputted into a MS Excel spreadsheet.
All 191 videos were screened against the eligibility criteria by KS, with NT cross-checking 20% between January 11th, 2023, and January 13th, 2023. The agreement between reviewers was high (95%), exceeding the PRISMA-ScR guidelines requirements of 70–80% agreement [ 22 ]. A third reviewer (NLS) adjudicated any discrepancies (7%) with reference to the definition of TST and the inclusion criteria. Of the181 rejected videos, seven were duplicates, four were unavailable in English, 74 did not meet our definition for TST, 47 did not explicitly state that the purpose of the video was to teach TST, six had no skills demonstration in the video and 43 did not have sufficient instruction to allow a novice to repeat. Only ten videos fulfilled the eligibility criteria (0.4% of videos identified, 5% of videos bookmarked) and were included in the review, as represented in Fig. 1 .
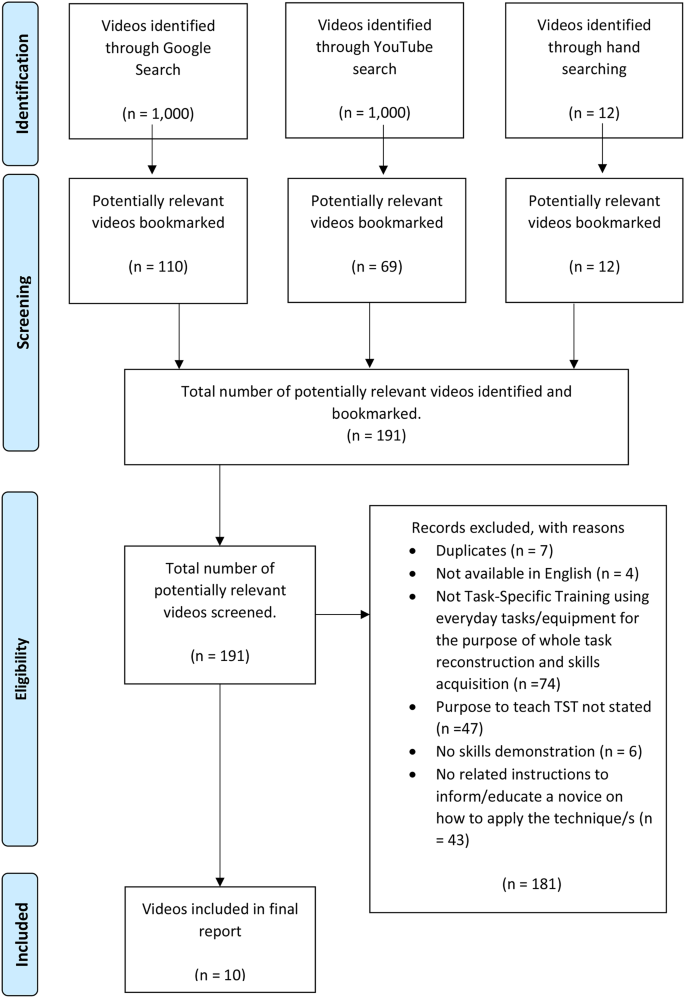
PRISMA flow diagram
Description of included videos
Videos had been uploaded to the platform a median of 30 months prior to our search date (range: 7–79 months). The median length of videos was 5.32 min (range: 3–20 min), with a median of 1386.5 views (range: 181–21950). The median number of likes for a video was 11.5 (range: 2–581), and the number of dislikes for all videos was 0. Occupational therapists were presenters in five of the videos, physiotherapists in two and the professional status of the presenter was unidentified in three videos. The focus of most videos was stroke rehabilitation (9) with cerebral palsy rehabilitation presented in one. Only two of the videos included people with the selected condition as participants. Seven videos were uploaded by universities, two by clinicians in a private practice and one by an unidentified contributor. Most videos were created in the United States of America (USA) with one each from Australia and India. A range of interventions were presented including upper limb training (7), bicycle training (1), constraint induced movement therapy (1), and balance training (1). A summary of the characteristics of the included videos is provided in Table 3 .
Only 10 videos explicitly stated that the purpose of the video was to teach TST and therefore had their content assessed for its suitability to guide skill acquisition. The videos were assessed in relation to the key components of TST (practice structure, specificity, repetition, modification, progression, feedback) and how they were presented (with instruction and/or demonstration). All videos included demonstration and instruction about manipulating practice structure to promote motor learning. Specificity was demonstrated in all videos using physical objects relevant to the task, while only three videos provided instruction in addition to demonstration. Nine of the videos provided demonstration and instruction on the use of repetition, with one video providing instruction only. Five videos provided demonstration and instruction on how to modify the activity, three provided instructions only and two failed to provide modification. Seven videos provided demonstration and instruction on progressions, with two videos providing instruction only, and one failing to demonstrate or provide instruction on any form of progression. None of the videos demonstrated the provision of feedback to promote motor learning and only one video provided instruction on how to provide feedback. The scores for videos ranged from 6 to 9/12 with five videos being considered moderately suitable and five very suitable to guide skill acquisition. Only one video included all the key components of TST and none of the videos provided demonstration and instruction on each component. A breakdown of the TST components and suitability scores is detailed in Table 4 .
This review was the first, to our knowledge, to examine the extent, characteristics, and suitability of freely available online videos that guide skill acquisition of TST for neurological physiotherapists and students. Despite a wide and comprehensive search strategy, only ten videos met the eligibility criteria. This suggests that despite over 2000 videos being available, there is a lack of suitable material to address the skill acquisition of TST for neurological physiotherapists and students.
This review highlights a fundamental problem when searching for educational videos online. Namely, it is difficult to find the few suitable videos amongst the array of videos of variable educational quality. It is unlikely that everyday internet users would be prepared to screen so many videos to find those ones related to TST which provide adequate information for training skill acquisition. Several authors have suggested mechanisms to improve the identification of educational videos. The use of a domain based ranking system, that ranks videos from trusted sources (universities or health organisations) higher up in the search results may make identification easier [ 32 ]. The use of inbuilt educational filters, with a strict criterion for labelling content as educational, might also improve identification [ 32 , 33 ]. In addition, organisations with an interest in educating physiotherapists could identify and disseminate existing online videos that are suitable to guide skill acquisition.
During our review of the characteristics of videos, we noticed that physiotherapists and occupational therapists created the majority of TST videos using a range of interventions, mainly featuring the upper limb, and the condition of stroke. None of the videos demonstrated the use of TST during walking, which would be particularly useful for neurological physiotherapists and students, as this is often their focus in rehabilitation. People with a neurological condition used as participants were found in only two of the videos. One of the strengths of video is that it can depict authentic, real-world experiences of people with neurological conditions during rehabilitation sessions. The lack of involvement of people who have real impairments means subtleties in using TST skills for people with a neurological condition will be overlooked. Time constraints and ethical considerations may have been factors in the reduced involvement of people with neurological conditions, however, overcoming these issues to include people with real impairments would enhance the learning experience.
The suitability of videos to guide skill acquisition was assessed in relation to the key components of TST and how they were presented (with demonstration and/ or instructions) and were found to be variable. None of the videos provided demonstration and instruction for each component of TST, and only one video included all the key components. The use of instruction and demonstration has been found to optimise skill acquisition [ 34 , 35 ], therefore, its omission would impact users’ understanding of the components and their ability to perform TST effectively. Feedback was omitted in all but one video, which was concerning as feedback is essential for motor learning and an integral component of TST [ 36 , 37 ]. These results support the findings of previous studies, which found videos created for health professions to be of low educational quality and missing key information. Videos on surface anatomy omitted key aspects related to upper and lower limb anatomy, such as vessels, nerves, cubital fossa, wrists, and hands [ 28 ]. Videos by physiotherapists on shoulder joint mobilisation techniques failed to describe or illustrate vital aspects of techniques such as patient and therapist position, force of application and dosage [ 17 ]. Online videos have also frequently been found to contain inaccurate, contradictory, or misleading information [ 28 , 32 , 38 , 39 ] with no reference to sources or evidence; this is in part due to the lack of peer review processes to monitor quality [ 38 ]. This highlights, that users need to critically evaluate the content of videos, and that improvements need to be made before they can be recommended as a valuable learning resource.
It has been suggested that the quality of video content for education can be filtered by evaluating variables such as the uploading source, video duration or the subjective estimation by viewers, expressed as likes/dislikes. The uploading source in particular has been found to be valuable for discriminating and predicting the quality of video content. Those uploaded by professionals, professional associations, and credible health care organisations are often of higher quality and are more suitable for education than those uploaded by individuals [ 38 , 40 , 41 , 42 , 43 ]. In contrast, video duration and the likes/dislikes ratio were found to be unreliable as a predictor of quality [ 14 , 40 , 42 , 43 ]. These results are consistent with the findings from our study which found that the videos sourced from educational institutions or private clinics were more suitable to guide skill acquisition. Neurological physiotherapists and students should consider the source of online videos to assist them to assess the educational quality of video resources.
This review highlights the importance of evaluating the content within freely available online videos. There are several tools available for assessing the quality, flow, and user friendliness of websites [ 44 ], evaluating health information on the internet, and the credibility of websites [ 45 ]. Although these tools are somewhat useful, they do not assess the content of the video in sufficient detail to help users determine if they are a suitable learning resource to guide skill acquisition. The development of content specific quality tools is required to assist learners to critically evaluate the quality of video content. In addition, guidelines based on sound teaching theory and practice are required to assist creators of online videos to create high quality resources that meet the needs of neurological physiotherapists and students.
This study was the first, to our knowledge, to examine the extent, characteristics of freely available online videos, and whether the content is suitable to guide skill acquisition of TST for neurological physiotherapists and students. Previous studies [ 38 , 39 ] have evaluated the quality of online videos using various gross assessment tools [ 44 , 45 , 46 ]. However, these tools do not evaluate the video content; our study assessed whether the content of freely available online TST videos is suitable to guide skill acquisition. This review has identified difficulties neurological physiotherapists and students face in sourcing relevant videos of good educational quality without subscriptions to specialised domains. Attempts were made throughout the searches to reduce the impacts of search engine personalisation; and consistent reporting of the search strategy and methods, maintained rigour and transparency.
Limitations
The criteria used to evaluate the suitability of the video content for skill acquisition was developed by the authors, was subjective, and may have been affected by observer bias. To reduce the risk of bias, two authors (KS, NT) assessed each video independently. The use of American spelling was used as it resulted in the most search results however, it may have influenced the identification of videos and resulted in the higher prevalence of videos from the USA. Forty-seven videos were excluded as they did not fit our inclusion criteria of explicitly stating that the purpose was the teach. It is acknowledged that some of these videos may have been videos teaching TST.
There are very few suitable online videos that are freely available and specifically designed to support neurological physiotherapists and students in the skill acquisition of TST. The development of a standardised and validated assessment tool, that is easy to use and assesses the content of TST videos is required to support learners to critically evaluate the educational quality of video content. Guidelines based on sound teaching theory and practice are required to assist creators of online videos to provide suitable resources that meet the needs of neurological physiotherapists and students.
Data availability
The datasets used and/or analysed during the current study are available from the corresponding author on reasonable request.
Abbreviations
- Task-specific training
United States of America
Constraint Induced Movement Therapy
Joanna Briggs Institute
New Zealand
Internet protocol
Population, Concept, Context
Winstein CJ, Wolf SL, Dromerick AW, Lane CJ, Nelsen MA, Lewthwaite R, et al. Effect of a Task-oriented Rehabilitation Program on Upper Extremity Recovery following Motor Stroke: the ICARE Randomized Clinical Trial. JAMA. 2016;315(6):571–81.
Article Google Scholar
English C, Hillier SL, Lynch EA. Circuit class therapy for improving mobility after stroke. Cochrane Database Syst Rev. 2017;6(6):Cd007513.
Google Scholar
French B, Thomas LH, Coupe J, McMahon NE, Connell L, Harrison J, et al. Repetitive task training for improving functional ability after stroke. Cochrane Database Syst Rev. 2016;11(11):Cd006073.
Hornby TG, Reisman DS, Ward IG, Scheets PL, Miller A, Haddad D, et al. Clinical Practice Guideline to improve locomotor function following chronic stroke, incomplete spinal cord Injury, and Brain Injury. J Neurol Phys Ther. 2020;44(1):49–100.
Kwakkel G, Veerbeek JM, van Wegen EE, Wolf SL. Constraint-induced movement therapy after stroke. Lancet Neurol. 2015;14(2):224–34.
Lin SH, Dionne TP. Interventions to Improve Movement and Functional outcomes in Adult Stroke Rehabilitation: review and evidence Summary. J Participat Med. 2018;10(1).
Ni M, Hazzard JB, Signorile JF, Luca C. Exercise guidelines for Gait function in Parkinson’s Disease: a systematic review and Meta-analysis. Neurorehabil Neural Repair. 2018;32(10):872–86.
Sakzewski L, Gordon A, Eliasson A-C. The state of the evidence for intensive Upper Limb Therapy approaches for Children with Unilateral Cerebral Palsy. J Child Neurol. 2014;29(8):1077–90.
Bayona NA, Bitensky J, Salter K, Teasell R. The role of task-specific training in rehabilitation therapies. Top Stroke Rehabil. 2005;12(3):58–65.
Pearson Education. Beyond Millennials: The Next Generation of Learners. 2018.
Rapp AK, Healy MG, Charlton ME, Keith JN, Rosenbaum ME, Kapadia MR. YouTube is the most frequently used Educational Video Source for Surgical Preparation. J Surg Educ. 2016;73(6):1072–6.
Ventola CL. Social media and health care professionals: benefits, risks, and best practices. P t. 2014;39(7):491–520.
Noetel M, Griffith S, Delaney O, Sanders T, Parker P, del Pozo Cruz B, et al. Video improves learning in higher education: a systematic review. Rev Educ Res. 2021;91(2):204–36.
Frongia G, Mehrabi A, Fonouni H, Rennert H, Golriz M, Günther P. YouTube as a potential training resource for laparoscopic fundoplication. J Surg Educ. 2016;73(6):1066–71.
Srinivasa K, Chen Y, Henning MA. The role of online videos in teaching procedural skills to post-graduate medical learners: a systematic narrative review. Med Teach. 2020;42(6):689–97.
Derakhshan A, Lee L, Bhama P, Barbarite E, Shaye D. Assessing the educational quality of ‘YouTube’ videos for facelifts. Am J Otolaryngol. 2019;40(2):156–9.
Shah S, Patel R, Patel N, Patel I. Low educational quality and trustworthiness of YouTube videos by physiotherapists on shoulder joint mobilization techniques: a descriptive study. J Man Manip Ther. 2022;30(6):334–41.
Küçükakkaş O, İnce B. Can YouTube be used as an educational tool in lymphedema rehabilitation? Arch Physiother. 2022;12(1):5.
Hannák A, Sapiezynski P, Kakhki AM, Krishnamurthy B, Lazer D, Mislove A et al. Measuring personalization of web search. Proceedings of the 22nd international conference on World Wide Web. 2013.
Bianchi T. Worldwide desktop market share of leading search engines from January 2015 to December 2022: Statista; 2023 January 6 Available from: https://www.statista.com/statistics/216573/worldwide-market-share-of-search-engines/ .
Arksey H, O’Malley L. Scoping studies: towards a methodological framework. Int J Soc Res Methodol. 2005;8(1):19–32.
Tricco AC, Lillie E, Zarin W, O’Brien KK, Colquhoun H, Levac D, et al. PRISMA Extension for scoping reviews (PRISMA-ScR): Checklist and Explanation. Ann Intern Med. 2018;169(7):467–73.
Peters MDJ, Marnie C, Tricco AC, Pollock D, Munn Z, Alexander L, et al. Updated methodological guidance for the conduct of scoping reviews. JBI Evid Synth. 2020;18(10):2119–26.
Godin K, Stapleton J, Kirkpatrick SI, Hanning RM, Leatherdale ST. Applying systematic review search methods to the grey literature: a case study examining guidelines for school-based breakfast programs in Canada. Syst Reviews. 2015;4(1):138.
Lennon S. Physical Management in Neurological Rehabilitation. 2 ed2004.
Bianchi T. Global search engine desktop market share 2022: Statista; 2023, January 6 Available from: https://www.statista.com/statistics/216573/worldwide-market-share-of-search-engines/ .
Kemp SD. 2022: Global Overview Report: Data Reportal - Global Digital Insights; 2022, May 4 Available from: https://datareportal.com/reports/digital-2022-global-overview-report .
Azer SA. Can “YouTube” help students in learning surface anatomy? Surg Radiol Anat. 2012;34(5):465–8.
Murugiah K, Vallakati A, Rajput K, Sood A, Challa NR. YouTube as a source of information on cardiopulmonary resuscitation. Resuscitation. 2011;82(3):332–4.
Hubbard IJ, Parsons MW, Neilson C, Carey LM. Task-specific training: evidence for and translation to clinical practice. Occup Ther Int. 2009;16(3–4):175–89.
Kleim JA, Jones TA. Principles of experience-dependent neural plasticity: implications for rehabilitation after brain damage. J Speech Lang Hear Res. 2008;51(1):S225–39.
Sunderland N, Camm CF, Glover K, Watts A, Warwick G. A quality assessment of respiratory auscultation material on YouTube. Clin Med (Lond). 2014;14(4):391–5.
Camm CF, Sunderland N, Camm AJ. A quality assessment of cardiac auscultation material on YouTube. Clin Cardiol. 2013;36(2):77–81.
Preston E, Ada L, Dean CM, Stanton R, Waddington G, Canning C. The Physiotherapy eSkills Training Online resource improves performance of practical skills: a controlled trial. BMC Med Educ. 2012;12:119.
Dong C, Goh PS. Twelve tips for the effective use of videos in medical education. Med Teach. 2015;37(2):140–5.
Levin MF, Demers M. Motor learning in neurological rehabilitation. Disabil Rehabil. 2021;43(24):3445–53.
Maier M, Ballester BR, Verschure P. Principles of Neurorehabilitation after Stroke based on Motor Learning and Brain plasticity mechanisms. Front Syst Neurosci. 2019;13:74.
Madathil KC, Rivera-Rodriguez AJ, Greenstein JS, Gramopadhye AK. Healthcare information on YouTube: a systematic review. Health Inf J. 2015;21(3):173–94.
Erdem MN, Karaca S. Evaluating the Accuracy and Quality of the information in kyphosis videos Shared on YouTube. Spine (Phila Pa 1976). 2018;43(22):E1334–9.
Lee JS, Seo HS, Hong TH. YouTube as a potential training method for laparoscopic cholecystectomy. Ann Surg Treat Res. 2015;89(2):92–7.
Lee H, Choi A, Jang Y, Lee JI. YouTube as a learning tool for four shoulder tests. Prim Health Care Res Dev. 2018;20:e70.
Ajumobi AB, Malakouti M, Bullen A, Ahaneku H, Lunsford TN. YouTube™ as a source of Instructional Videos on Bowel Preparation: a content analysis. J Cancer Educ. 2016;31(4):755–9.
Desai T, Shariff A, Dhingra V, Minhas D, Eure M, Kats M. Is content really king? An objective analysis of the public’s response to medical videos on YouTube. PLoS ONE. 2013;8(12):e82469.
Bernard A, Langille M, Hughes S, Rose C, Leddin D, Veldhuyzen van Zanten S. A systematic review of patient inflammatory bowel disease information resources on the world wide web. Am J Gastroenterol. 2007;102(9):2070–7.
Silberg WM, Lundberg GD, Musacchio RA. Assessing, controlling, and assuring the quality of medical information on the internet: Caveant Lector et viewor–let the reader and viewer beware. JAMA. 1997;277(15):1244–5.
Team HON. Health On the Net 2020 updated March 2020; cited 2023 May 13. Available from: https://www.hon.ch/en/ .
Download references
Acknowledgements
Melanie Grant (Senior librarian) contributed to the design of the search strategy.
Kelvin Sasse was funded as part of a student summer scholarship funded by the School of Clinical Sciences, Physiotherapy Department, Auckland University of Technology. Auckland, New Zealand.
Author information
Authors and affiliations.
School of Clinical Sciences, Department of Physiotherapy, Health and Rehabilitation Research Institute, Auckland University of Technology, Northshore Campus, Private Bag 92006, Auckland, 1142, New Zealand
Nicola C.M. Towersey, Kelvin Sasse, Verna Stavric, Gemma Alder & Nicola L. Saywell
You can also search for this author in PubMed Google Scholar
Contributions
NT, NLS, GA and VS conceived and designed the study and contributed to manuscript preparation. KS collected, collated, analysed the data, and contributed to the writing of the manuscript. NT, NLS, GA and VS also contributed to data collection and analysis. All authors read and approved the final manuscript.
Corresponding author
Correspondence to Nicola C.M. Towersey .
Ethics declarations
Ethics approval and consent to participate.
Not applicable.
Consent for publication
Competing interests.
The authors declare no competing interests.
Additional information
Publisher’s note.
Springer Nature remains neutral with regard to jurisdictional claims in published maps and institutional affiliations.
Electronic supplementary material
Below is the link to the electronic supplementary material.
Supplementary Material 1
Rights and permissions.
Open Access This article is licensed under a Creative Commons Attribution 4.0 International License, which permits use, sharing, adaptation, distribution and reproduction in any medium or format, as long as you give appropriate credit to the original author(s) and the source, provide a link to the Creative Commons licence, and indicate if changes were made. The images or other third party material in this article are included in the article’s Creative Commons licence, unless indicated otherwise in a credit line to the material. If material is not included in the article’s Creative Commons licence and your intended use is not permitted by statutory regulation or exceeds the permitted use, you will need to obtain permission directly from the copyright holder. To view a copy of this licence, visit http://creativecommons.org/licenses/by/4.0/ . The Creative Commons Public Domain Dedication waiver ( http://creativecommons.org/publicdomain/zero/1.0/ ) applies to the data made available in this article, unless otherwise stated in a credit line to the data.
Reprints and permissions
About this article
Cite this article.
Towersey, N., Sasse, K., Stavric, V. et al. Freely available, online videos to support neurological physiotherapists and students in task-specific training skill acquisition: a scoping review. BMC Med Educ 24 , 603 (2024). https://doi.org/10.1186/s12909-024-05545-5
Download citation
Received : 21 June 2023
Accepted : 09 May 2024
Published : 31 May 2024
DOI : https://doi.org/10.1186/s12909-024-05545-5
Share this article
Anyone you share the following link with will be able to read this content:
Sorry, a shareable link is not currently available for this article.
Provided by the Springer Nature SharedIt content-sharing initiative
- Search engine
- Neurological rehabilitation
- Physiotherapy
BMC Medical Education
ISSN: 1472-6920
- Submission enquiries: [email protected]
- General enquiries: [email protected]
A new AI era begins
Introducing the fastest, most intelligent Windows PCs ever. Windows 11 Copilot+ PCs give you lightning speed, unique Copilot+ PC experiences, and more at a price that outperforms.
The best Windows yet
When there’s a lot to do, let Windows 11 help you get it done.
Meet Windows 11
Learn how to use the new features of Windows 11 and see what makes it the best Windows yet.
Upgrade your experience
Learn how to get Windows 11 on your current PC 4 , or purchase a new PC that can run Windows 11.
Need help transferring files, resetting a password, or upgrading to Windows 11? Explore the Windows support page for helpful articles on all things Windows. Have a specific issue you’re troubleshooting? Ask your question in the Microsoft Community.
Meet Copilot in Windows
Find the information and ideas you need to power your ingenuity. Copilot in Windows 6 is an AI feature that allows you to get answers fast and ask follow-up questions, get AI-generated graphics based on your ideas, and kickstart your creativity while you work. Get to know Copilot in Windows, your new intelligent assistant.
Sync your PC & phone
Microsoft Phone Link makes it possible to make calls, reply to texts, and check your phone’s notifications from your PC 5 .
Find the right fit
Explore a selection of new PCs, or get help selecting the best computer for your unique needs.
Better together
Discover the Windows 11 experiences built to bring your favorite Microsoft tools to life.
Microsoft Store
The apps you need. The shows you love. Find them fast in the new Microsoft Store. 1 2
Microsoft Edge
Make the most of your time online with the browser built for Windows.
Microsoft 365
Maximize your productivity with easy-to-use Windows 11 multitasking tools built to work with the Microsoft apps you use every day. 3
Looking for more?
Get help with your transition to Windows 11, and make the most of your Windows experience.
Get Windows 11
Intuitive. Easy. Faster than ever. Experience all Windows has to offer. 4
Get Microsoft news and updates
Subscribe to our newsletter to get the latest news, feature updates, how-to tips, deals and more for Windows and other Microsoft products.
Become an insider
Register with the Windows Insider Program and start engaging with engineers to help shape the future of Windows.
- 1 Screens simulated. Features and app availability may vary by region.
- 2 Some apps shown coming later. Certain apps only available through Microsoft Store app in Windows 11.
- 3 Microsoft 365 subscription sold separately.
- 4 Windows 11 upgrade is available for eligible PCs that meet minimum device specifications . Upgrade timing may vary by device. Internet service fees may apply. Features and app availability may vary by region. Certain features require specific hardware (see Windows 11 specifications ).
- 5 Phone Link experience comes preinstalled on your PC with Windows 10 (running Windows 10, May 2019 Update at the least) or Windows 11. To experience the full functionality, Android phones must be running Android 7.0 or later. Phone Link for iOS requires iPhone with iOS 14 or higher, Windows 11 device, Bluetooth connection and the latest version of the Phone Link app. Not available for iPad (iPadOS) or MacOS. Device compatibility may vary. Regional restrictions may apply.
- 6 Copilot in Windows (in preview) is available in select global markets and will roll out starting in summer 2024 to Windows 11 PCs in the European Economic Area. Copilot in Windows 10 functionality is limited and has specific system requirements . Learn More .
Follow Microsoft Windows
Share this page
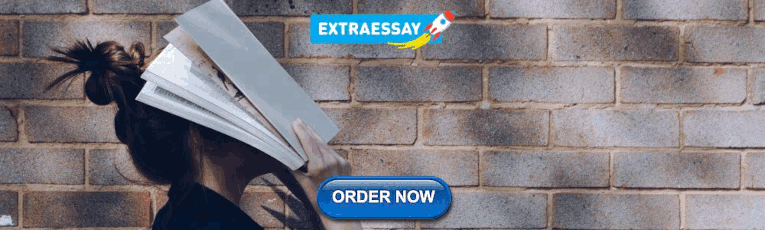
IMAGES
VIDEO
COMMENTS
Quality Glossary Definition: Seven tools of quality "The Old Seven." "The First Seven." "The Basic Seven." Quality pros have many names for these seven basic tools of quality, first emphasized by Kaoru Ishikawa, a professor of engineering at Tokyo University and the father of "quality circles."Start your quality journey by mastering these tools, and you'll have a name for them too: indispensable.
Farah Amreen. This document discusses various quality tools including check sheets, histograms, Pareto charts, cause and effect diagrams, control charts, scatter diagrams, and flow charts. It provides examples and definitions of each tool. Check sheets are used to systematically record data and a sample check sheet on garment defects is shown.
Saahil Walia. The 7 Quality Control (QC) Tools are fundamental instruments in quality management, offering structured methodologies to analyze and improve processes. These tools include histograms, control charts, Pareto diagrams, cause and effect, and stratification to enable efficient data interpretation and decision-making.
This document discusses quality tools and techniques, specifically focusing on the 7 basic tools of quality: histograms, Pareto charts, cause-and-effect diagrams, scatter diagrams, control charts, flow charts, and check sheets. Examples are provided for each tool to demonstrate how they are used. The tools are used to analyze processes ...
The Basic Seven (B7) Tools of Quality. The Basic Seven (B7) Tools of Quality. A PowerPoint Training Presentation By Keith H. Cooper "As much as 95% of quality related problems in the factory can be solved with seven fundamental quantitative tools." - Kaoru Ishikawa. What are the Basic Seven Tools of Quality?. Fishbone Diagrams
30 Summary This presentation provided learning material for each of Ishikawa's seven basic tools of quality. Each tool was clearly defined with definitions, a step-by-step process and an example of how the tool can be used. As seen through the presentation, these tools are rather simple and effective.
Identify the loopholes. Solve quality related complex issues and more. Get access to this ready-made quality PPT templates to apply these tools. This deck comprises of tools such as cause & effect diagram, check sheet, control charts, histogram, pareto chart, scatter diagram, and stratification. Use one or more quality tool to troubleshoot the ...
Stratification. Histogram. Check sheet (tally sheet) Cause and effect diagram (fishbone or Ishikawa diagram) Pareto chart (80-20 rule) Scatter diagram. Control chart (Shewhart chart) The ability to identify and resolve quality-related issues quickly and efficiently is essential to anyone working in quality assurance or process improvement.
Grab our presentation template to depict the 7 Quality Control Tools and how they are crucial for identifying issues, analyzing data, and finding solutions in quality management. 100% compatible with MS PowerPoint and Google Slides, this deck features visuals that can be used to ensure accurate and faster interpretation of content.
This quality tools PowerPoint collection includes a huge range of introductions to common quality assurance techniques (e.g. Q7 and M7) and a wide selection of charts and analysis tools. All PowerPoint slides are professionally designed, slick, modern, and 100% editable. You can rely on this toolbox from the market leader to ensure long-term ...
The seven basic tools of quality tools are tools which arrange problem areas, put data into diagrams, surface problem areas and clearly bring up any hidden truth. A problem solving team's successes are dependent on the familiarity and ease with which these tools are used. In this Seven Basic Tools of Quality PPT training presentation, you will be able to teach employees how to use the tools in ...
4.0/5.0 - 2207 ratings Verified by LiveChat May. 2024 EXCELLENT SERVICE. 7 Quality Tools found in: Collection Of Quality Control Seven Basic Quality Control Tools, 7 qc tools powerpoint presentation slides, 7 tools for total quality management ppt powerpoint guide, Seven basic tools of quality..
Presentation Transcript. SEVEN QUALITY CONTROL TOOLS (or) OLD SEVEN TOOLS. Dr.Kaoru Ishikawa, Professor at Tokyo University & Father of Q C in Japan. • CAUSE ANALYSIS TOOLS are Cause and Effect diagram, Pareto analysis & Scatter diagram. • EVALUATION AND DECISION MAKING TOOLS are decision matrix and multivoting.
manju3426. This presentation discusses quality control tools including check sheets, flow charts, histograms, cause and effect diagrams, Pareto charts, scatter diagrams, and control charts. It provides examples and guidelines for when and how to use each tool, as well as their benefits. The seven tools are effective for problem solving, process ...
How Can Teams and Organizations Use the 7 Basic Quality Tools? Quality tools are used to collect data, analyze data, identify root causes, and measure results in problem-solving and process improvement. The use of these tools helps people involved easily generate new ideas, solve problems, and do proper planning.
A team researched and developed the seven new quality control tools, to be used along with the 7 basic quality tools. Often called the seven management and planning (MP) tools, or simply the seven management tools. The seven new tools, listed in an order that moves from abstract analysis to detailed planning, are: Affinity Diagram.
The different quality management tools used to identify the problem depend on the needs of the company. It is vital to identify the cause of the problem in order to ensure the quality of products or services. Task #3: Perform quality checks. Traditionally, the pen and paper method was used to perform quality checks.
This is a quality management tools ppt powerpoint guide. This is a seven stage process. The stages in this process are control chart, flow chart, cause effect diagram, pareto chart, the 7 quality tools, for process improvement, check sheet, histogram, scatter plot. Slide 1 of 7.
7 Features to Enhance Presentation's Quality. In this 7 QC Tools PPT, we have added a few features that you have never thought of. Easily accessible on every platform, whether it is Microsoft PowerPoint, Google Slides, or Apple Keynote. Available in two different layouts that are blue and multi-colored. You have an option to pick yours.
Seven Quality Tools. Seven Quality Tools. Presented by: M. Aschner. Objective. Present an overview of Seven Quality Tools Address purpose and applications Highlight benefits. The Deming Chain Improve Quality Decrease Costs Improve Productivity Decrease Price Increase Market Stay in Business. 1.11k views • 39 slides
Download this excellent Best Quality Tools PowerPoint Presentation to construct an inspiring presentation. This template is a 100% easy-to-use and versatile template. As a result, you can generate a meaningful impact among your audiences, teammates, and colleagues.
The Seven Basic Tools of Quality. Sep 17, 2011 • Download as PPT, PDF •. 107 likes • 79,079 views. Tim McMahon. Explanation of the seven basic tools used to solve a variety of quality-related issues. They are suitable for people with little formal training in statistics. Education Technology. 1 of 73. Download now.
Item 2b - Students Driving Curriculum Quality for Sustainability: Criteria & Tools.
2022 Quality Payment Program: Doctors and Clinicians Performance Information on the Medicare.gov Compare Tool ... Lisa Trapani, RoseComm. May 2024. 1. Disclaimers This presentation was prepared as a tool to assist providers and isn't intended to grant rights or impose obligations. Although every reasonable effort has been made to assure the ...
12-12:30 pm -- Lunch, Welcome Remarks, and Presentation on "A Decade of CESTA Data" 12:30-3:30 pm -- DH Research Fellows' Showcase 12:30 - 1:50 PM : The Meaning and Measurement of Place with presentations from: Matt Randolph (PhD Candidate in History): "Bringing AI to Archibald Grimké's Archive: A Case Study of Artificial Intelligence for Histories of Race and Slavery" This digital project ...
This presentation will focus on recent advances achieved through the project, including integration of multiple air quality datasets in a prototype data fusion system in Google Earth Engine, the quantification of uncertainties associated with our data fusion approach, and the development of user interfaces and visualization tools to convey air ...
Videos to support learning of clinical skills are effective; however, little is known about the scope and educational quality of the content of freely available online videos demonstrating task-specific training (TST). This review aimed to determine the extent, characteristics of freely available online videos, and whether the content is suitable to guide skill acquisition of task-specific ...
5 Phone Link experience comes preinstalled on your PC with Windows 10 (running Windows 10, May 2019 Update at the least) or Windows 11. To experience the full functionality, Android phones must be running Android 7.0 or later. Phone Link for iOS requires iPhone with iOS 14 or higher, Windows 11 device, Bluetooth connection and the latest ...