
- Sign up for free
- SafetyCulture
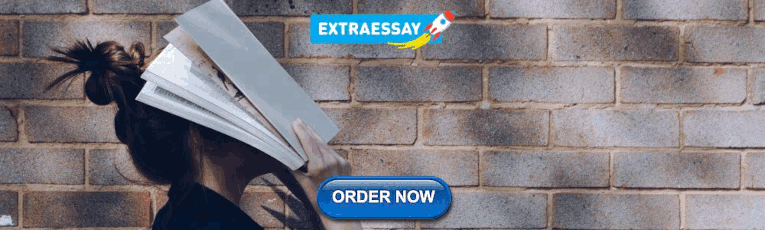
The 5 Whys: A Powerful Problem-Solving Tool
The 5 Whys can be used for everything from fixing a broken appliance to solving a complex business issue. This article discusses how you actually use it.
What is the 5 Whys Technique?
The 5 Whys is a problem-solving technique used to explore the cause-and-effect relationship that leads to a particular problem. The name derives from the method’s frequent utilization of the question “Why?” This repeating question is used to determine the root cause of a problem by repeating why the problem occurs five times. Each answer forms the basis for the next question.
It’s a simple but powerful technique that can help you get to the bottom of things in a thorough manner. It can be used for anything from figuring out why your car keeps breaking down to understanding why a project is behind schedule. It’s a great way to get clarity and find solutions fast.
When it comes to problem-solving, the 5 Whys is one of the simplest techniques around. But don’t let its simplicity fool you—it’s a powerful tool that can help you get to the root of any issue. The beauty of the 5 Whys is that it helps you get to the heart of the issue quickly and easily. And it’s a great tool for troubleshooting problems in your business. Here are some of its benefits:
- Identifies the root cause of the problem
- Helps you analyze and understand how one action can cause a chain of problems
- Gets you to the root cause quickly
- Does not use any complicated techniques for problem-solving
- Figures out the relationship between the various root causes
- Is very effective as a solution for simple problems
The 5 Whys technique was developed in the 1930s by Sakichi Toyoda, a mechanic who was always looking for ways to improve the efficiency of his work. He found that the best way to do this was to ask why his processes were failing. He would ask why five times until he got to the root of the problem. Simple as that!
The 5 whys is now a popular problem-solving technique that’s used in businesses all over the world. It’s simple yet amazingly effective at getting to the root of a problem.
How It Works
Let’s say you’ve got a problem. You know what it is, but you’re not sure how to fix it. This is where the 5 Whys come in.
Here’s how it works: you ask yourself why the problem happened, and then you ask yourself that question again and again until you get to the root of the issue.
The key is to ask why five times. Why did the problem happen? Why did the previous solution fail? And so on. This helps you get down to the root cause of the issue and find a solution that will actually work.
This is a great technique when you’re stuck and don’t know how to move forward. It can help you get clarity and come up with a solution that works for you.
Here’s a perfect example:
The customer refused to pay for the product. | |
Why? | The customer saw that there was damage to the product when it was opened. |
Why? | The product got damaged during the delivery. |
Why? | The product, which is made of glass, fell causing it to crack. |
Why? | There was no safety packaging for the product. |
Why? (Root Cause) | It was not properly inspected during the packaging process. |
Digitize the way you Work
- Get Started for Free
What are the 5 Whys in Six Sigma?
The 5 whys tools can be used in a variety of situations. It’s used in root cause analysis and Six Sigma to get to the root of a problem.
As we all know, Six Sigma is a process improvement methodology used in various industries to achieve near-perfection in their processes. Within that metholodogy, the 5 whys tool is used specifically for the DMAIC (Define, Measure, Analyze, Improve, and Control) framework.
As a result, it helps Six Sigma practitioners find the root cause of a problem by asking successive “why” questions.
When to Use this Method
This technique can be used when you’re trying to solve a specific problem understand why something went wrong. It can also be used to come up with new ideas or solutions.
The great thing about the 5 Whys is that it helps you get to the root of the problem, and it also encourages creativity and brainstorming. So if you’re facing a challenging problem, this is a technique you should try.
Limitations
The 5 Whys is a great tool for problem-solving, but it has some limitations. For example, it can be difficult to apply this technique to more complex problems. Aside from this, here are some of the constraints when using this method:
- This method is not recommended for complex problems as it may not lead to the main cause. This is because the 5 whys will lead to a single source, which may be a problem if there is a need for multiple solutions.
- It is reliant on the skills of the team facilitator. One wrong question or answer can lead to completely throwing off the questions, thus leading to a wrong root cause.
- The 5 whys method may not show all possible issues caused by the main problem.
How to Use the 5 Whys Method
Now that you know all about the 5 Whys method, let’s talk about how to use it. So how do you implement the 5 Whys tool? Here’s a quick and easy guide to get you started:
#1. Gather and Assemble a Team.
The first step is to create a team that is familiar with the problem or issue at hand. Familiarity with the issue is essential because this will determine the right questions to ask thus solving the problem correctly.
#2. Identify the Problem.
Next is to identify the problem at hand. Once you’ve done that, it’s time to discuss it with your team by writing down a brief statement or question of what the agreed issue needs to be solved. A team member can right down the statement while leaving enough space for why questions.
#3. Ask the 5 Whys.
Now is the time to ask the first why. The first question must pertain to why the problem occurred. The question must be based on facts and related to the issue. Keep going until you reach the root cause of the problem.
#4. Brainstorm Solutions to the Root Cause.
Once you’ve identified the root cause, you can start brainstorming solutions. It’s important to remember that not every solution will work, but the goal is to find a solution that will prevent the problem from happening again.
#5. Test the Solution.
So how do you know if the solution is effective? You need to test it. Modify the solution as needed and repeat the test until you’re satisfied that it’s working.
How Can SafetyCulture Help with Using 5 Whys?
The 5 Whys is a great tool for solving problems quickly and easily, and it can be used in situations wherein you need to find the cause of the problem. But how SafetyCulture (formerly iAuditor) can help you with using 5 Whys?
SafetyCulture is a powerful analytical tool and 5 whys software that can help you quickly and easily identify the root cause of any problem. Plus, the platform’s reporting and dashboard capabilities make it easy to share your findings with your team. Here are some other features that you can utilize when doing 5 whys analysis with SafetyCulture:
- Capture and report issues to gain better visibility and traceability, and get to the root cause using relevant insights and data for continuous improvement .
- Use the Heads Up feature to keep everyone in the loop during 5 Whys meetings. With this feature, you’ll never miss team meetings, ensure all agenda are addressed, and easily collect the additional necessary data to streamline the process.
- Assign actions to team members that are in charge of making sure that the 5 whys analysis progresses and that tasks are properly assigned through building workflows .
- Use various smart checklists and templates that you can customize based on your team’s needs.
- Integrate your tools to assess all kinds of data and monitor analytics in one place.
Featured Templates:
The 5 Whys Template
Can I use 5 Whys in any situation or problem that occur?
Yes and no. The great thing about 5 whys is that it can be used by anyone facing simple problems. However, for complex problems that require detailed solutions, using 5 whys may not be ideal.
Why are there only five "whys"?
The 5 Whys technique is based on the premise that the root cause of a problem can be found by asking why five times. With this method, you can get to the root of the issue and find appropriate solutions.
How do I know when I've reached the root cause?
There is no hard and fast rule for how many times you should ask why before you reach the root cause. However, if you find yourself going in circles or asking the same question multiple times, it’s likely that you haven’t yet reached the root cause.
How do you document 5 Whys?
There are various ways to document 5 whys. One way is to use a cause and effect diagram, also known as an Ishikawa diagram or fishbone diagram. This type of diagram can be used to brainstorm the possible causes of a problem. Another way to document 5 whys is to simply write down the question and answer for each step.
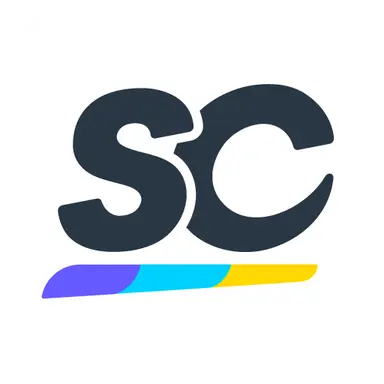
SafetyCulture Content Team
Related articles

- GRC Policy Management
Discover the key elements of Governance, Risk, and Compliance (GRC) policy management and how it helps organizations uphold transparency and accountability while mitigating risks and meeting standards.
- Find out more

- Construction Workflow
Learn what a construction workflow is, why it’s important, and how to create an efficient one for your team.

- Environmental Sustainability
Explore the importance of integrating environmental sustainability into an organization’s operations and some key strategies to implement.
Related pages
- Integrated Workplace Management System (IWMS)
- Construction Procurement Software
- Supply Chain Analytics Software
- Induction Software
- Construction Collaboration Software
- Workplace Efficiency
- Resistance to Change
- Operational Resilience Plan
- NDIS Audit Checklist
- Change Impact Assessment Template
- Environmental Aspects and Impacts Register
- 5 Whys Template
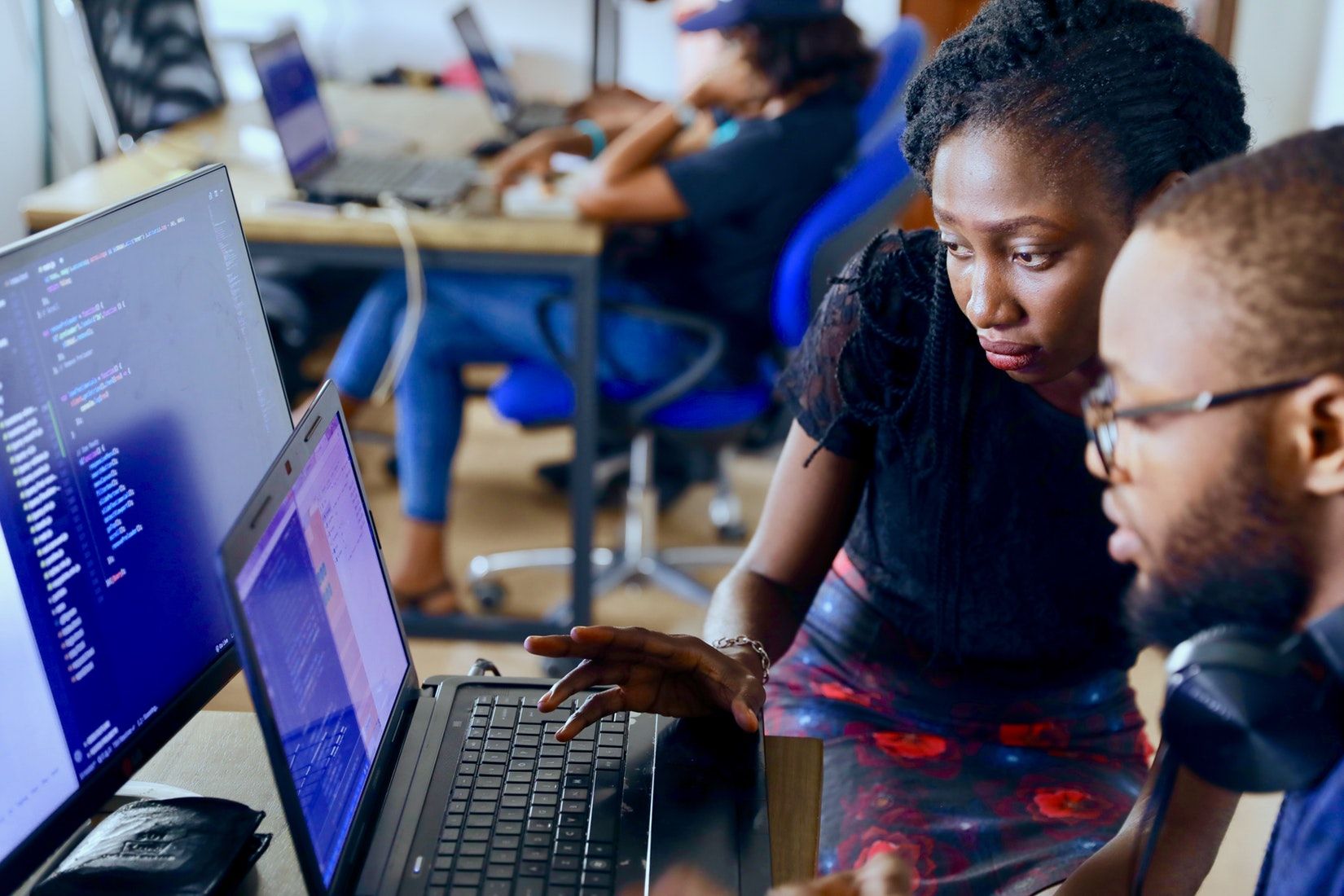
The 5 Whys Process We Use to Understand the Root of Any Problem
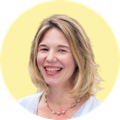
Former Director of People @ Buffer
Sometimes things don’t go according to plan. Tools break, wires get crossed, the best-laid plans fall apart.
And on those occasions, it helps to know exactly what happened—so it doesn’t happen again.
Moments like these are when we at Buffer turn to a simple but remarkably effective process: The 5 Whys.
It’s just as it sounds: A discussion of the unexpected event or challenge that follows one train of thought to its logical conclusion by asking “Why?” five times to get to the root of what happened.
But it’s also a lot deeper than that, too. Let’s take a look at the origin and history of this unique process, and I’ll tell you a bit about how it works for us on our remote team at Buffer—and how it could work for you, too.
The origin of the 5 Whys
The 5 Whys technique was developed and fine-tuned within the Toyota Motor Corporation as a critical component of its problem-solving training.
Taiichi Ohno, the architect of the Toyota Production System in the 1950s, describes the method in his book Toyota Production System: Beyond Large-Scale Production as “the basis of Toyota’s scientific approach . . . by repeating why five times, the nature of the problem as well as its solution becomes clear.”
Ohno encouraged his team to dig into each problem that arose until they found the root cause. “Observe the production floor without preconceptions,” he would advise. “Ask ‘why’ five times about every matter.”
Here’s an example Toyota offers of a potential 5 Whys that might be used at one of their plants.
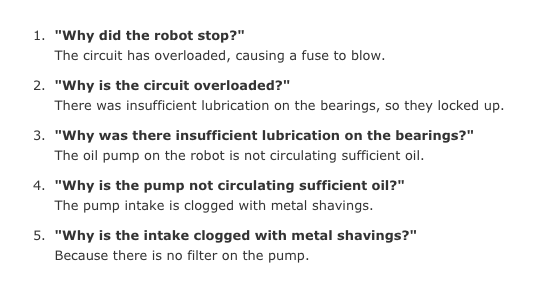
Today, the method is used far beyond Toyota, and it’s particularly popular in the world of lean development. A lot of what we know at Buffer in implementing the 5 Whys has come from The Lean Startup ‘s Eric Ries, who does an amazing job describing the 5 Why’s in these two posts.
How the 5 Whys process works
At our startup, we perform a “5 Whys” after something unexpected has occurred—and that means we perform them a lot! We keep a “5 Whys” folder in our team’s Dropbox Paper account, and the folder has 20+ notes files and counting (not to mention the 5 Whys docs that might not be categorized into the folder). ‘Fires’ of various sizes are inevitable—and probably the only constant in the life of a startup.
We’ve held these discussions in every facet of Buffer, from engineering to happiness to marketing and more, and the same process holds true no matter whether the problem is technical or more human-based. Here’s how Eric Ries explains:
“Five Whys involves holding meetings immediately following the resolution of problems the company is facing. These problems can be anything: development mistakes, site outages, marketing program failures, or even internal missed schedules. Any time something unexpected happens, we could do some root cause analysis.”
It’s important to note that the purpose of the 5 whys isn’t to place blame , but rather to uncover the root cause of why something unexpected occurred. Additionally, it helps a team create small, incremental steps so that the same issue doesn’t happen again (to anyone).
Tweet this ?
At Buffer, the habit of conducting 5 Whys originated from the engineering team. Here’s how our former CTO Sunil Sadasivan describes the changes that have resulted from making these a routine part of how we operate:
“What I really like about this is that it lets us worry about issues when they happen, and it helps us work towards ensuring they won’t happen again. At the same time, it lets us not have to worry about issues that haven’t happened. I now trust if something comes up that we didn’t foresee, we’ll conduct a 5 whys and learn from it. We let the 5 whys dictate what documentation we need in place or adjustments to make in our on-boarding process.”
Want to try it for yourself?
The 5 main steps to the the 5 Whys
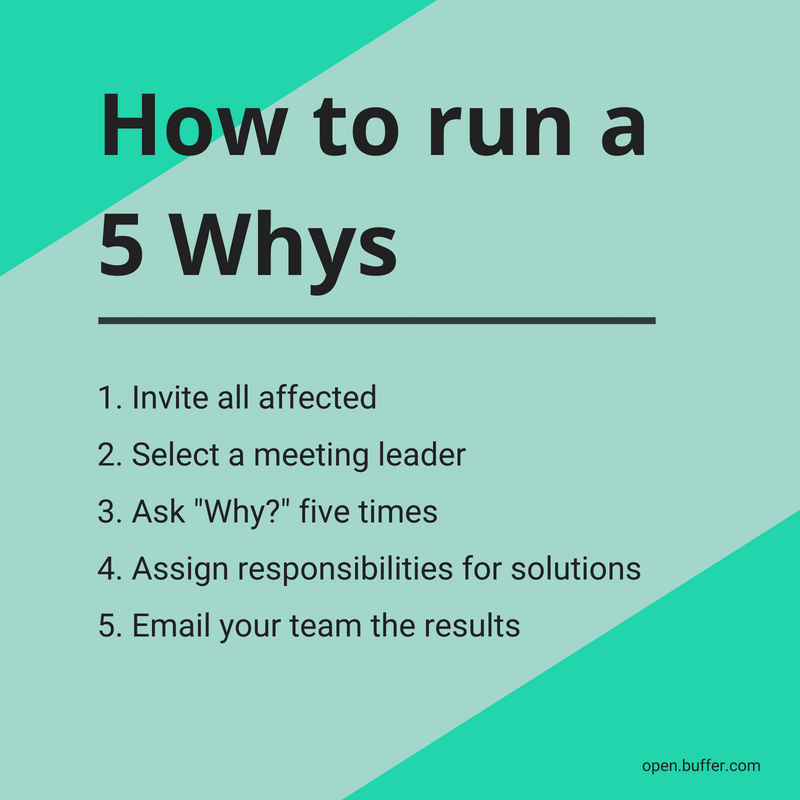
Step 1: Invite anyone affected by the issue
As soon as the problem or situation is identified (and all immediate concerns are dealt with), invite anyone at all on the team who was affected or noticed the issue to be involved in a 5 Whys meeting. As a remote team , we hold ours via Zoom.
Step 2: Select a 5 Whys master for the meeting
The 5 Whys master will lead the discussion, ask the 5 whys, and assign responsibility for the solutions the group comes up with. The rest of those involved will answer those questions and discuss.
In our experience, anyone can be a 5 Whys master — there are no special qualifications, and it doesn’t have to be the leader of the project or the originator of the issue. We’ve also found that it’s a good idea for the 5 Whys master to take notes for the meeting, unless he or she would like to assign someone else to this.
Step 3: Ask “why” five times
Dig at least five levels deep into the issue with five levels of “whys.” This seems like the simplest part but can in fact get a bit tricky! Getting the right question to start with, the first why, seems to be the key.
When we conduct our 5 Whys, it can feel natural and almost beneficial to go down all potential paths and be really comprehensive. However, this can widen the scope of how much learning and corrective actions need to occur. This is meant to be a ‘lean’ process in which picking one path allows us to perform just the amount of corrective actions needed to solve a problem.
We often have to tell ourselves we just need to pick one and go with it. If the same problem seems to occur again, then we can do another choosing the other route.
Together, we work through each of those five whys and discover actionable steps that have been or will be taken.
Step 4: Assign responsibility for solutions
At the end of the exercise, we go through each why question-and-answer pairing and come up with five related “corrective actions” that we all agree on. The master assigns responsibility for the solutions to various participants in the discussion.
Step 5: Email the whole team the results
After each 5 Whys process, someone involved in the meeting will write down what was discussed in the clearest, plainest language as possible. Then we add it to a Paper folder and—in one of the most important steps of the whole process—email the whole team with the results.
This makes sense to do, and not just for a company like Buffer that focuses on transparency. It’s super useful for everyone on your team to stay in the loop and understand any steps you’re taking as the result of a 5 Whys.
Eric Ries explains why the email is so important:
The advantage of sharing this information widely is that it gives everyone insight into the kinds of problems the team is facing, but also insight into how those problems are being tackled. And if the analysis is airtight, it makes it pretty easy for everyone to understand why the team is taking some time out to invest in problem prevention instead of new features. If, on the other hand, it ignites a firestorm – that’s good news too. Now you know you have a problem: either the analysis is not airtight, and you need to do it over again, or your company doesn’t understand why what you’re doing is important. Figure out which of these situations you’re in, and fix it.
Put it all together and the process looks like this:
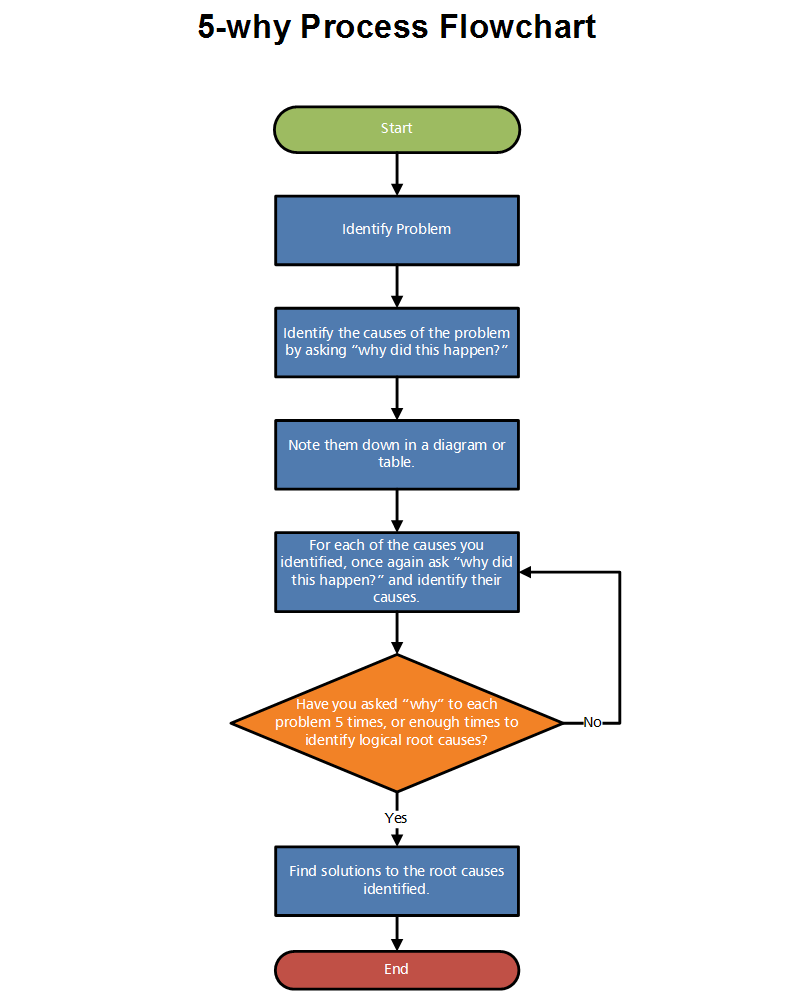
Some real-life 5 Whys examples
To take the 5 Whys from theoretical to actual, here’s a look at a few moments in Buffer’s history that have called for a 5 Whys meeting.
In early 2014, we had a brief systemwide outage. Here’s a look at the 5 Whys the team conducted:
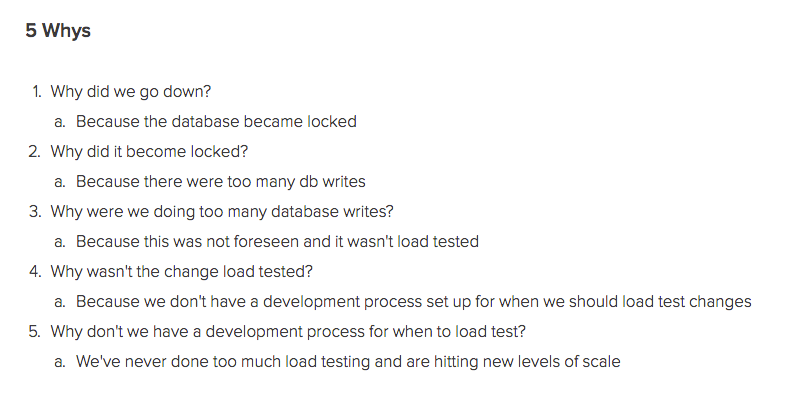
And the corrective actions that resulted:
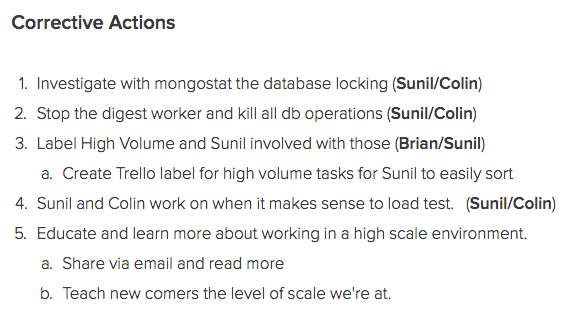
Here’s an example from the customer happiness world. One of our Happiness Heroes wanted to understand how he might have handled a customer’s problem better, so he performed a modified 5 Whys as a reflection and shared it with the team.
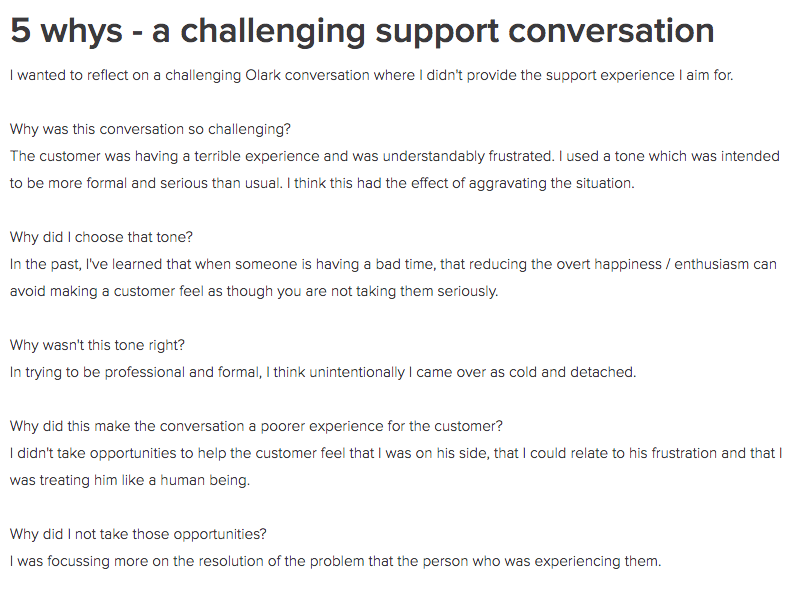
I have learned so much from viewing these examples and being part of 5 Whys processes. It’s been great to develop a habit of reflecting anytime something unexpected happens and taking incremental steps so that we change what happens the next time around.
The 5 Whys in daily life
Although the 5 Whys is most widely used for manufacturing/development use, I’ve found that it is also quite applicable to daily life in any situation where one might seek deeper understanding—of a problem, a challenge or even a motivation behind an action.
This quick graphic from Start of Happiness provides a great example:
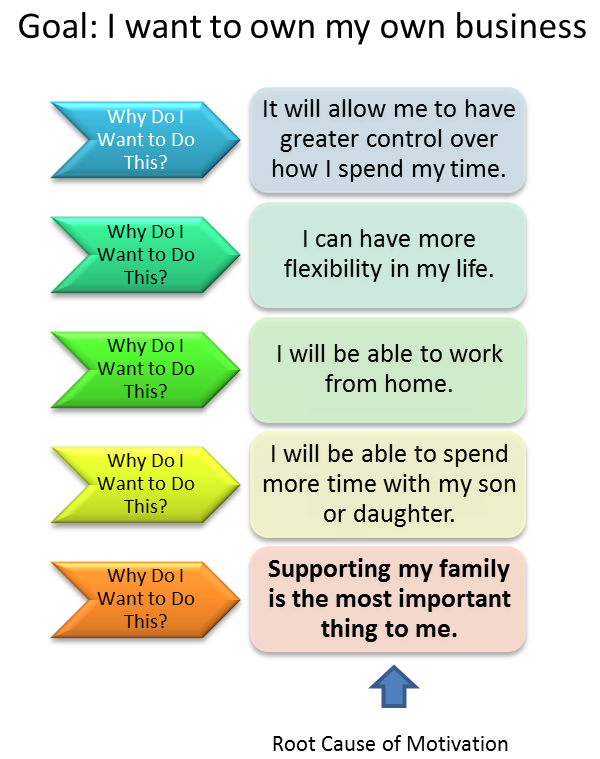
Ever since learning about the 5 Whys, I find myself asking “why?” a lot more often.
Over to you
What sort of process do you use to get to the root of unexpected situations or challenges in your work or life? Have you ever tried the 5 Whys?
I’d love to hear your insights in the comments!
P.S. If you liked this post, you might enjoy our Open blog newsletter . Receive each new post delivered right to your inbox! Sign up here .
Try Buffer for free
140,000+ small businesses like yours use Buffer to build their brand on social media every month
Related Articles
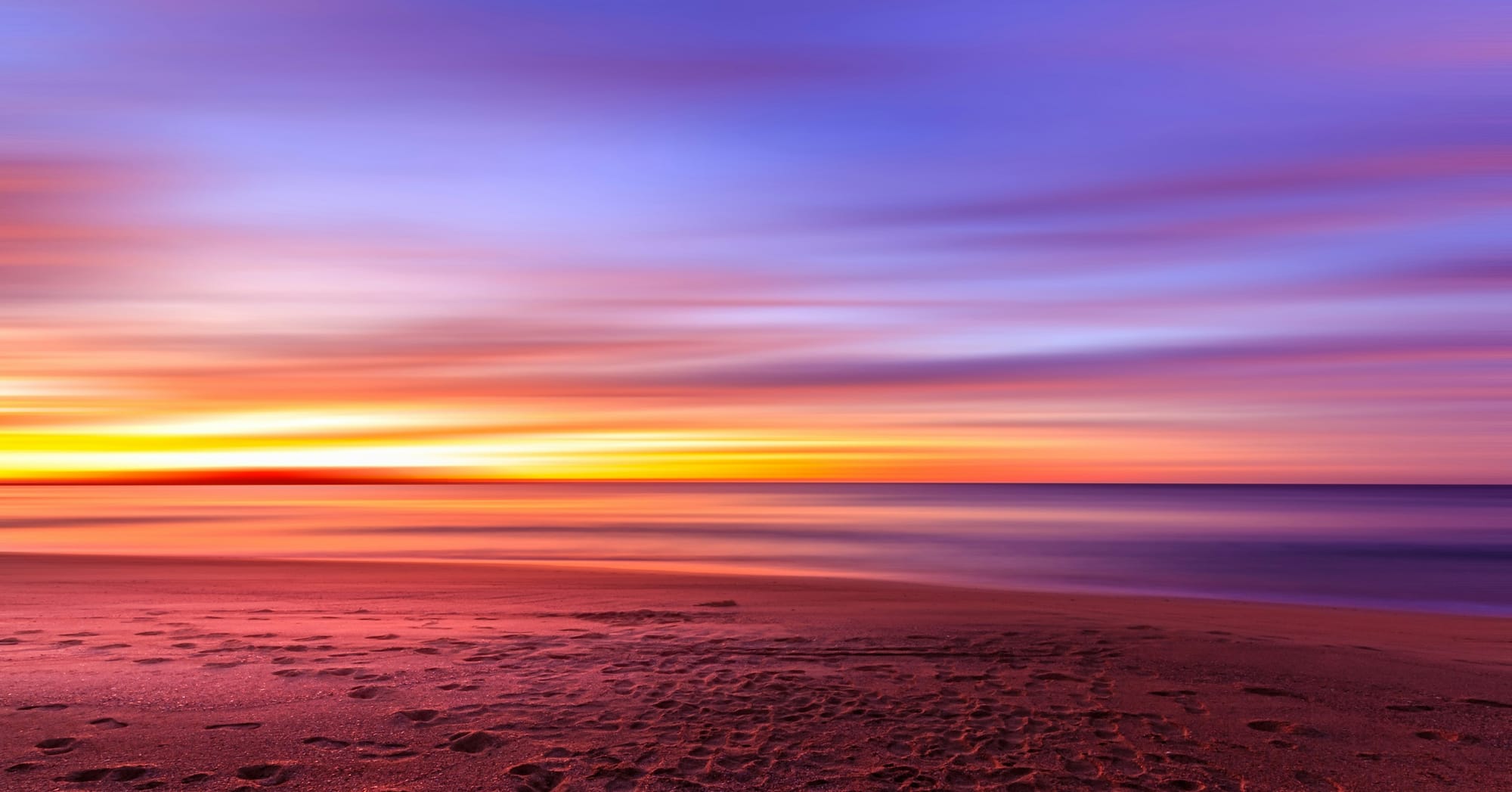
Nine years ago, we decided to launch a new free product alongside Buffer. We called it Pablo, and it was a huge hit in our community. Within just seven months of its launch, half a million photos were created using Pablo. Similarly, we had the initial ideas for Stories Creator and Remix many years ago now. All three of these tools have been an important part of Buffer’s story. They’ve taught us lessons and helped us connect with a wider audience. In Pablo’s case, the idea for this tool happene
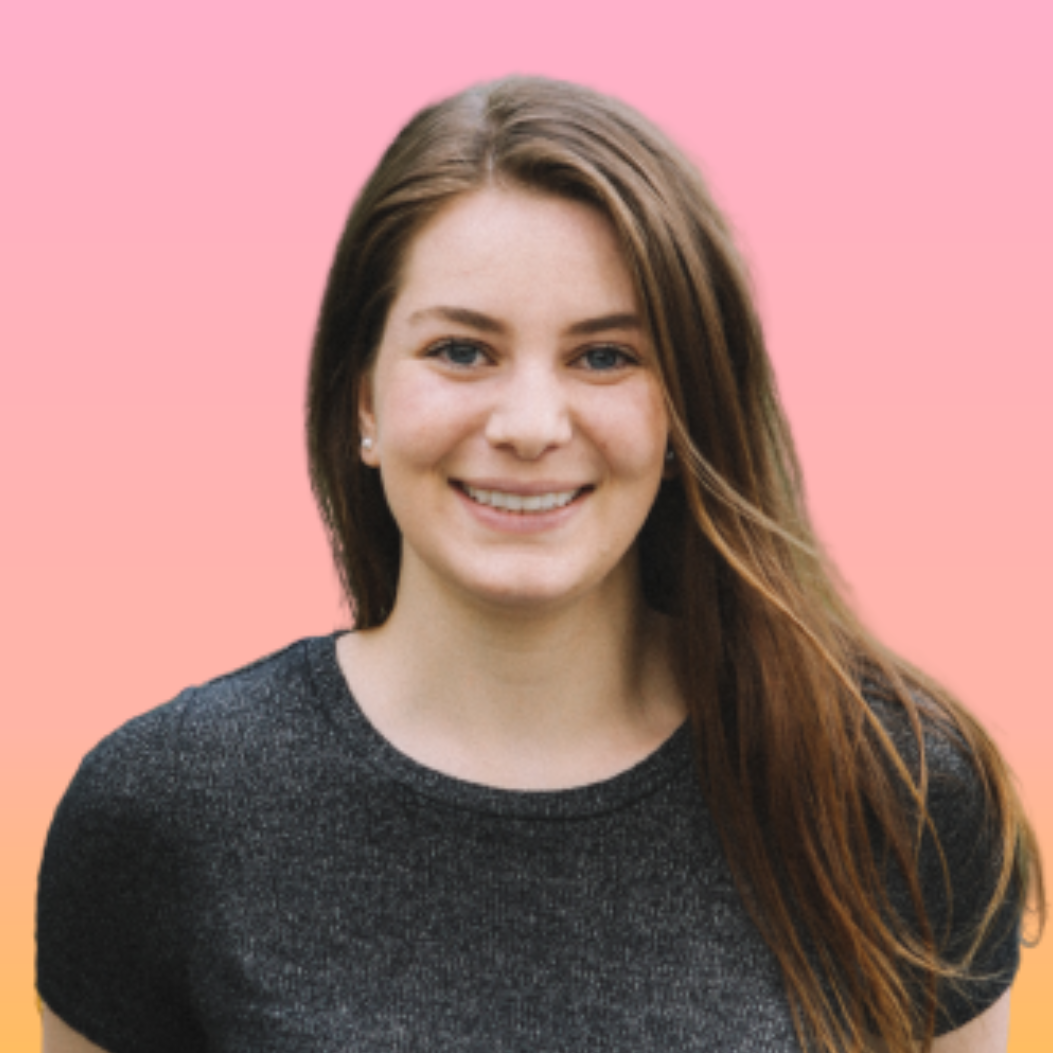
If you use Buffer, you might have experienced us having more downtime than usual recently. We want to start with an apology for not sharing more transparently along the way what’s been happening. We’ve been caught up in the work and haven’t invested enough in communicating with our community, and we’re so sorry about this misstep. We know some of our customers have had a frustrating time using Buffer recently and we need to do better by you. This past August and September were the months we’ve
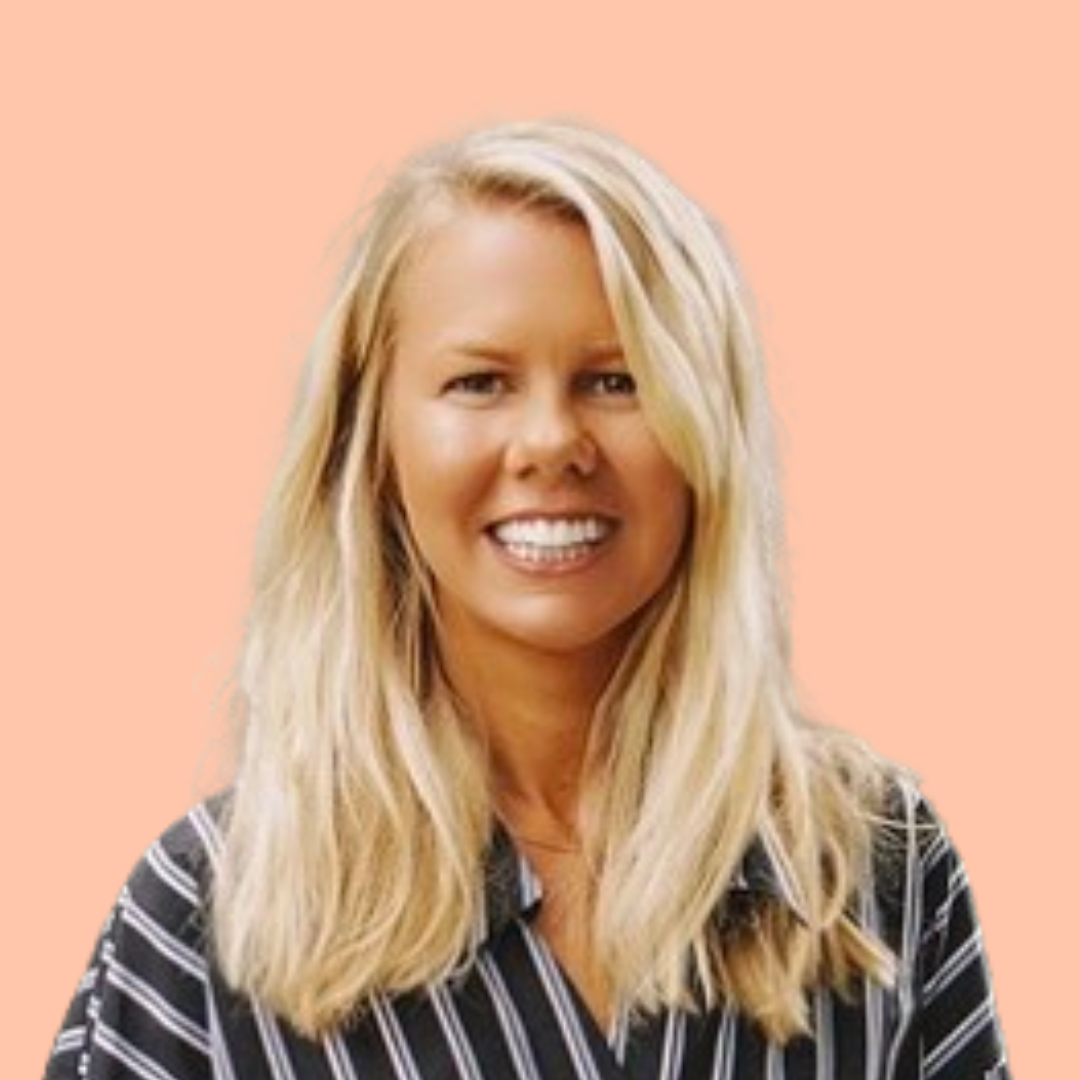
As part of our commitment to transparency and building in public, Buffer engineer Joe Birch shares how we’re doing this for our own GraphQL API via the use of GitHub Actions.
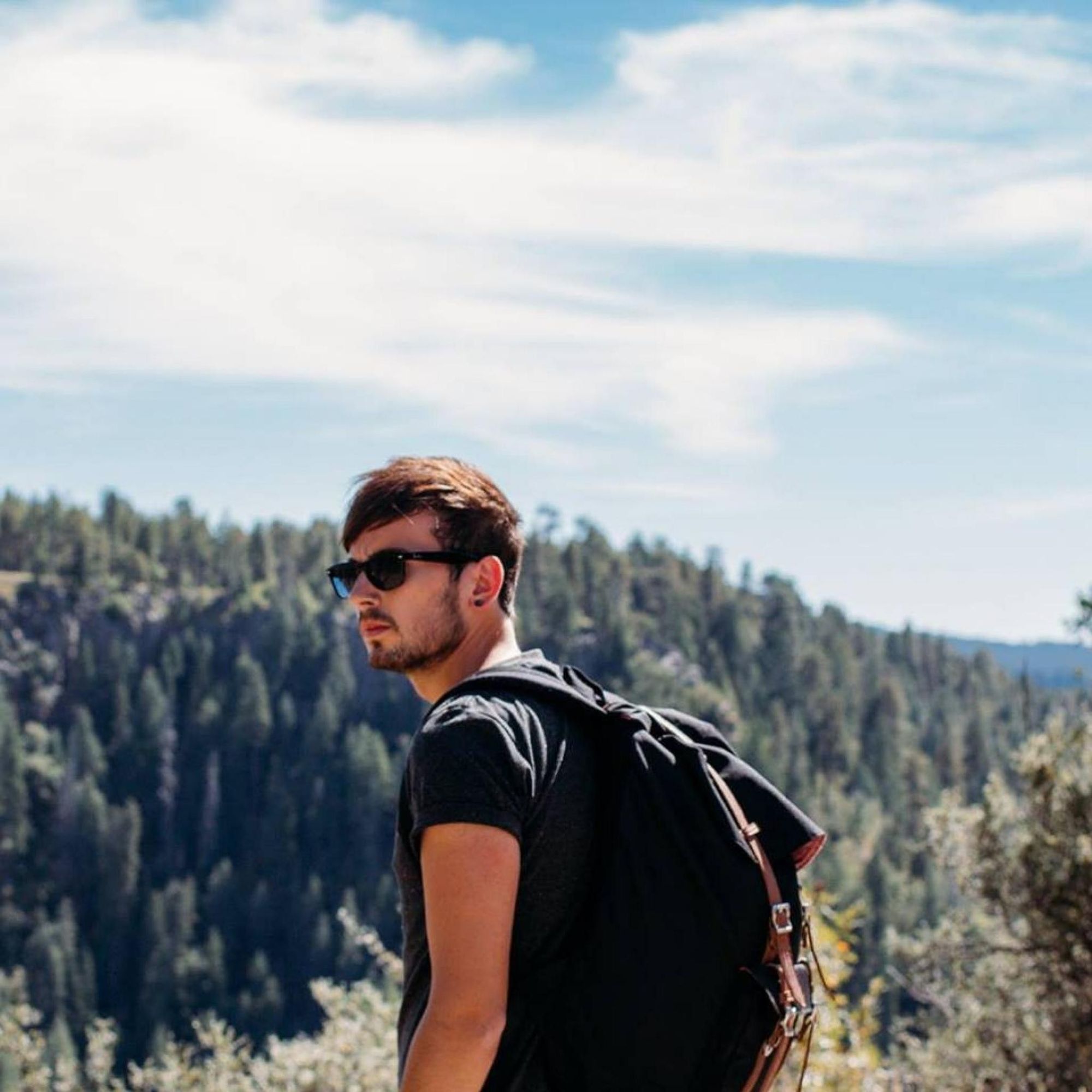
140,000+ people like you use Buffer to build their brand on social media every month
Copyright © 2024 Buffer | Privacy | Terms | Security
- Social Media Marketing
- Instagram Marketing
- Social Analytics
- News and Trends
- Best apps and tools
- Inside Buffer
- Remote Work
- Transparency
- Blog & podcasts
- Best Time to Post on Social Media
- Social Media Blog
- Social Media Glossary
- About Buffer
- Our culture

- RCA 101 – 5-Why Analysis (Free Training)
- RCA201 – Basic Failure Analysis
- RCA 301 – PROACT® RCA Certification
- RCA401 – RCA Train The Trainer
- Other Trainings
- 5 Whys Root Cause Analysis Template
- RCA Template
- Chronic Failure Calculator
Root Cause Analysis with 5 Whys Technique (With Examples)
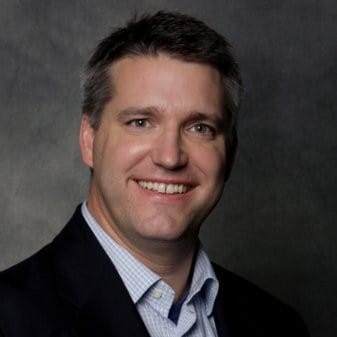
By Sebastian Traeger
Updated: April 23, 2024
Reading Time: 7 minutes
What Is the 5 Whys Technique?
Example of the 5 whys technique, how to conduct a 5 whys analysis in 5 steps, when to use a 5 whys analysis, using 5 whys template, tips for mastering the 5 whys technique, frequently asked questions about 5 whys.
With over two decades in business – spanning strategy consulting, tech startups and executive leadership – I am committed to helping your organization thrive.
At Reliability, we’re on a mission to help enhance strategic decision-making and operational excellence through the power of Root Cause Analysis, and I hope this article will be helpful!
Our goal is to help you better understand 5 whys techniques by offering insights and practical tips based on years of experience. Whether you’re new to doing RCAs or a seasoned pro, we trust this will be useful in your journey towards working hard and working smart.
The 5 Whys Technique is like peeling an onion – it helps you uncover the underlying reasons behind a problem, layer by layer. By repeatedly asking “why” at least five times, this method digs deep to reveal the root cause of an issue. It’s a simple yet powerful problem-solving approach that aims to get to the heart of the matter rather than just addressing surface-level symptoms.
5 Whys Technique: A method that involves iteratively asking “why” five times to unveil the fundamental cause of a problem.
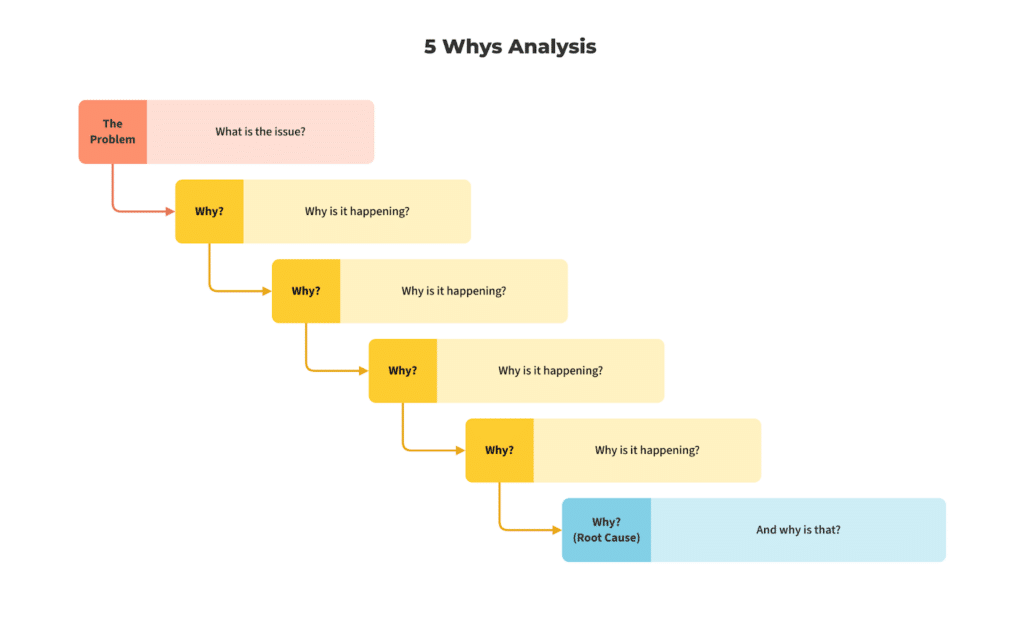
In essence, the 5 Whys Technique is not just about fixing what’s broken on the surface; it’s about understanding and addressing the deeper issues that lead to problems in the first place.
The 5 Whys Technique is like a detective, uncovering the truth behind recurring problems. Let’s take a look at how this method works in two different scenarios.
Case Study: Manufacturing Defects
Imagine a company that keeps encountering the same manufacturing defects despite various attempts to fix them. By using the 5 Whys Technique, they discovered that the defects were not caused by faulty machinery, as previously assumed, but rather by human error due to unclear operating instructions. This realization led to improved training procedures and clear work guidelines, ultimately eliminating the defects.
Application in Service Industry
Now, consider a service industry struggling with frequent customer complaints and service failures. Through the 5 Whys Technique, it was revealed that these issues stemmed from inadequate staffing levels during peak hours. By addressing this root cause, such as hiring additional staff or adjusting schedules, the service quality can significantly improve, leading to higher customer satisfaction.
These examples illustrate how the 5 Whys Technique can be applied across different sectors to identify and address underlying issues effectively.
Step 1: Identify the Problem
Before diving into a 5 Whys analysis, it’s crucial to clearly identify the problem or issue at hand . This step sets the stage for the entire process and ensures that the focus remains on addressing the right concern. Take the time to gather relevant data, observe patterns, and consult with team members or stakeholders to gain a comprehensive understanding of the problem.
Step 2: Ask ‘Why’ Five Times
Once the problem is clearly defined, it’s time to start peeling back the layers. The process involves asking “why” five times, not necessarily limited to five questions but enough to delve deeper into the underlying causes of the problem . Each “why” serves as a gateway to uncovering additional factors contributing to the issue. This iterative approach helps in identifying not just one cause, but multiple interconnected elements that may be at play.
By consistently probing deeper with each “why,” you can reveal hidden complexities and nuances that may have been overlooked initially. This method allows for a more thorough understanding of the situation, paving the way for effective solutions that address root causes rather than surface-level symptoms.
This structured approach encourages critical thinking and enables teams to move beyond quick fixes towards sustainable improvements.
The 5 Whys Technique is a versatile problem-solving approach that can be applied in various scenarios to uncover root causes and drive continuous improvement. Here are two key situations where the 5 Whys Analysis can be particularly beneficial:
Recurring Issues
- The 5 Whys Technique is especially useful when dealing with recurring issues. Whether it’s a manufacturing defect that keeps resurfacing or a persistent customer complaint in the service industry, this method helps identify the underlying reasons behind these repetitive problems. By repeatedly asking “why,” it becomes possible to trace the issue back to its root cause, allowing for targeted solutions that prevent reoccurrence.
Process Improvement
- Organizations constantly strive to enhance their processes and workflows for increased efficiency and quality. When seeking to improve existing procedures, the 5 Whys Technique serves as a valuable tool. By systematically analyzing the factors contributing to inefficiencies or bottlenecks, teams can gain insights into how processes can be optimized at their core. This method enables organizations to make informed decisions about process improvements based on a deep understanding of the underlying issues.
In both cases, the 5 Whys Analysis offers a structured yet flexible approach to delve into complex problems, making it an indispensable tool for driving meaningful change and progress within organizations.
When it comes to conducting a 5 Whys analysis, utilizing a structured template can greatly facilitate the process and ensure a comprehensive investigation into the root cause identification. Using RCA software such as EasyRCA can benefit the team by streamlining your 5-why process. Here’s how organizations can benefit from using a template:

Benefits of Using a Template
- Streamlined Process: A well-designed 5 Whys template provides a clear framework for conducting the analysis, guiding teams through the iterative questioning process. This streamlines the investigation, making it easier to navigate and ensuring that no crucial aspects are overlooked.
- Thorough Investigation: By following a predefined template, teams are prompted to explore various facets of the problem systematically. This ensures that all relevant factors are considered, leading to a more thorough and insightful investigation into the underlying causes.
- Consistent Approach: Templates offer a standardized approach to conducting 5 Whys analyses within an organization. This consistency promotes uniformity in problem-solving methods across different teams or departments, enhancing overall efficiency and effectiveness.
Customizing the Template
Organizations have the flexibility to customize 5 Whys templates according to their specific needs and industry requirements. This adaptability allows for tailoring the template to address unique challenges and incorporate industry-specific considerations. Customization may include:
- Adding Industry-Specific Prompts: Tailoring the template by incorporating prompts or questions relevant to particular industries or types of issues being analyzed.
- Incorporating Visual Aids: Enhancing the template with visual aids such as flow charts or diagrams can help teams better understand and communicate complex causal relationships.
- Iterative Refinement: Regularly reviewing and refining the template based on feedback and evolving organizational needs ensures that it remains aligned with current processes and challenges.
Customizing the template empowers organizations to harness the full potential of the 5 Whys Technique in addressing diverse problems while aligning with their unique operational contexts.
Encouraging Open Communication
In mastering the 5 Whys Technique as a problem-solving method, creating an environment that fosters open communication is paramount. When team members feel comfortable expressing their perspectives and insights, it leads to a more comprehensive exploration of the underlying causes of a problem. Encouraging open communication allows for diverse viewpoints to be considered, providing a holistic understanding of the issue at hand.
By promoting an atmosphere where individuals are empowered to voice their observations and concerns, the 5 Whys analysis can benefit from a rich tapestry of ideas and experiences. This inclusive approach not only enhances the depth of the analysis but also cultivates a sense of ownership and collective responsibility for addressing root causes within the team or organization.
Continuous Improvement Mindset
A key aspect of mastering the 5 Whys Technique is embracing a continuous improvement mindset. Rather than viewing problems as isolated incidents, this approach encourages teams to see them as opportunities for growth and development. By instilling a culture of continuous improvement, organizations can leverage the insights gained from 5 Whys analyzes to drive positive change across various aspects of their operations.
Fostering a mindset focused on continuous improvement entails actively seeking feedback, evaluating processes, and implementing iterative enhancements based on the findings. It involves an ongoing commitment to learning from past experiences and leveraging that knowledge to proactively address potential issues before they escalate. Embracing this mindset ensures that the 5 Whys Technique becomes ingrained in the organizational ethos, leading to sustained progress and resilience in problem-solving efforts.
As we wrap up our exploration of the 5 Whys Technique, let’s address some common questions that may arise regarding this powerful problem-solving method.
What is the primary goal of the 5 Whys Technique?
The primary goal of the 5 Whys Technique is to uncover the root cause of a problem by iteratively asking “why” at least five times. This approach aims to move beyond surface-level symptoms and address the underlying issues that lead to recurring problems.
Is the 5 Whys Technique limited to specific industries or sectors?
No, the 5 Whys Technique is versatile and can be applied across various industries and sectors. Whether it’s manufacturing, healthcare, service, or technology, this method offers a structured yet flexible approach to identifying root causes and driving continuous improvement.
How does the 5 Whys Technique contribute to continuous improvement?
By delving into the fundamental reasons behind problems, the 5 Whys Technique provides organizations with valuable insights for driving continuous improvement. It not only helps in resolving immediate issues but also fosters a culture of ongoing enhancement and development within an organization.
Can the 5 Whys Technique be used for complex problems with multiple contributing factors?
Yes, while initially designed as a simple and straightforward method, the 5 Whys Technique can certainly be applied to complex problems with multiple interconnected factors. By systematically probing deeper into each layer of causality, this technique enables a comprehensive understanding of intricate issues.
I hope you found this guide to 5 whys technique insightful and actionable! Stay tuned for more thought-provoking articles as we continue to share our knowledge. Success is rooted in a thorough understanding and consistent application, and we hope this article was a step in unlocking the full potential of Root Cause Analysis for your organization.
Reliability runs initiatives such as an online learning center focused on the proprietary PROACT® RCA methodology and EasyRCA.com software. For additional resources, visit Reliability Resources .
- Root Cause Analysis /
Recent Posts
How to Perform Root Cause Investigations?
Post-Incident Analysis for Enhanced Reliability
How To Conduct Incident Analysis?
The Role of Artificial Intelligence in Reliability Engineering
Root Cause Analysis Software
Our RCA software mobilizes your team to complete standardized RCA’s while giving you the enterprise-wide data you need to increase asset performance and keep your team safe.
Root Cause Analysis Training
[email protected]
Tel: 1 (800) 457-0645
Share article with friends:

Guide: 5 Whys
Author: Daniel Croft
Daniel Croft is an experienced continuous improvement manager with a Lean Six Sigma Black Belt and a Bachelor's degree in Business Management. With more than ten years of experience applying his skills across various industries, Daniel specializes in optimizing processes and improving efficiency. His approach combines practical experience with a deep understanding of business fundamentals to drive meaningful change.
5 Whys is a problem-solving technique used to get to the root cause of problems by asking the question of Why multiple times, but often 5 times giving it the name “5 Whys”. This allows people to address the root cause of issues instead of the symptoms of the root causes which is often what is seen as the problem.
Like a doctor diagnosing an issue such as neck pain, a painkiller will only address the symptoms of the neck pain and not the root cause of the pain. By getting to the root cause you can ensure a long-term fix to the root cause of the neck pain which could be caused by seating positions and not taking painkillers which is a short-term fix.
What is the 5 Whys?
The 5 Whys is a root cause analysis problem-solving technique that aims to identify the root cause of a problem by repeatedly asking the question “Why?” five times or until the core issue is unveiled. Developed within the Toyota Production System , it’s one of fundamental tools in the Lean Six Sigma methodology.
Here’s how it works:
- Begin with a clear and concise problem statement.
- Ask “Why?” the problem occurred. Document the answer.
- If this answer doesn’t identify the root cause, ask “Why?” again and document the subsequent answer.
- Continue this process until you’ve either asked “Why?” five times or the root cause has been identified.

Lets go through an example, let’s say a machine stopped working:
- Why? – The machine’s fuse blew.
- Why? – The machine was overloaded.
- Why? – There wasn’t adequate training on machine capacity.
- Why? – Training materials were outdated.
- Why? – There’s no review process for updating training materials.
In this case, the root cause is the lack of a review process for training materials, and addressing this will prevent similar issues in the future. Only treating the symptom in this situation would have been to change the fuse, for it then to regularly blow and cause additional downtime.
This is a good example where a machine stopping working’s root cause is cause by an issue what would not be obvious is first glace at the symptom of the problem and provides a clear example that root cause analysis is important to ensure that solutions are not jumped to before a through root cause analysis is conducted.

Want exclusive templates, tools and guides?
Join our email list below and for the next 28 days, we will send you exclusive tools, templates and guides unavailable on the website. We developed a short and simple 28-day program designed to develop your ability to implement Lean and Six Sigma methods daily.
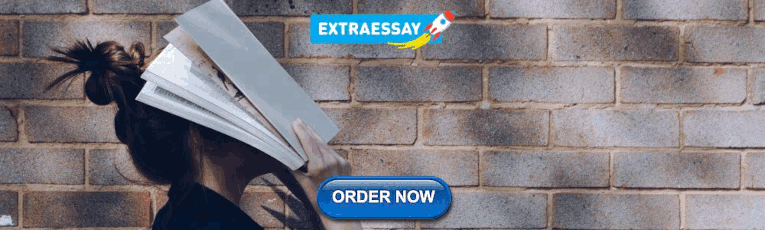
Why is the 5 Whys Important?
Understanding the 5 Whys is important because identifying symptoms of a problem is not the same as uncovering its root cause. If you only address symptoms this provides only temporary solution to the problem. However, understanding and resolving the root cause can prevent the issue from reoccurring.
The 5 Whys Problem-Solving technique is also useful for:
- Problem Prevention: By identifying the root cause of the problem, businesses can implement long-term solutions, leading to more robust systems and processes and prevent the problem reoccurring.
- Cost-Efficiency: Addressing root causes is often more cost-effective in the long run as it prevents recurrence and the associated costs of repeated problem-solving which usually involves the same people constantly firefighting the same issues such as repeated machine breakdowns.
- Improved Processes: Regular use of the 5 Whys to identify the root causes of problems can highlight weaknesses in processes, leading to continuous improvement and optimization processes.
- Empowerment: The use of 5 Whys by individuals a positive culture that promotes a deeper understanding of systems and processes, empowering teams to take ownership and responsibility in addressing issues.
How to Conduct a 5 Whys Root Cause Analysis?
Step 1: define the problem.
This is an important step as if the problem is not defined effectively it could result in focusing in the wrong problem. A good method for this could be to use the 5W1H Is/Is Not Problem solving technique to gain a common understanding of that the problem is.
When stating the problem you are going to conduct a 5 Whys on it is important to be specific about the issue and avoid ambiguous descriptions. Additionally, where data and information is available this should be collected and used as evidence that points to the actual problem rather than opinions of the problem.
Step 2: Ask the First “Why?”
Now you have a clear problem definition you should ask the question “Why did that happen?” This should be done to understand the problem without making assumptions and should be done with supporting facts and data that backs up the initial answer to the question.
Step 3: Continue to Ask Why?
Now you should have an answer to the first why. This should form the next step and ask why did that happen. This ensures you dont settle for the inisital surface-level answer or symptoms of the real problem and pushes you to understand the underlying issues.
When you continue to ask why you should:
- Continuously question the previous answer
- Challenge answer that seem like assumptions and lack evidence to support them to avoid going down the wrong route.
Step 4: Continue the Process
- Keep the questioning focused on the problem
- If you feel the questioning is going off track revert back to what the initial problem definition.
- Ensure each answer provided logically leads to the next “Why?”
- The 5 Whys process then concludes when further questions leads to no further valuable answers are given or the when the root cause of the issues becomes clear.
Step 5 Implement Solutions
Once you have identified the root cause the you need to address it by implementing a solution to prevent the problem reoccuring.
This should be a case of developing an actionable solution that address the root cause of the issue and not preventing the symptoms as addressing the symptom will likely cause the issue to reappear elsewhere.
Make sure you test the solutions to ensure they are effective in addressing the root cause, you should then continue to monitor the process over time to confirm the problem did not reappear in the same place or elsewhere.
If the problem does not re appear congratulations you have solved the problem!
An Example of 5 Whys Analysis
Below is a good example of a 5 Whys analysis done in a situation where there was a production downtime.

To summarize, the 5 Whys process is an effective problem-solving tool that can assist businesses in identifying the root cause of a problem and developing effective solutions. Teams can delve deep into underlying issues and develop targeted solutions that address the root cause of the problem by asking “why” multiple times.
The five steps of the 5 Whys process – defining the problem, asking “why” once, asking “why” more times, developing a solution, implementing the solution, provide a clear framework for problem-solving and can help ensure that the problem is effectively resolved. The 5 Whys process encourages teams to think critically and systematically, resulting in long-term solutions that are effective, targeted, and sustainable.
- Benjamin, S.J., Marathamuthu, M.S. and Murugaiah, U., 2015. The use of 5-WHYs technique to eliminate OEE’s speed loss in a manufacturing firm. Journal of Quality in Maintenance Engineering , 21 (4), pp.419-435.
A: The 5 Whys technique is a problem-solving method that involves asking “why” multiple times to uncover the root cause of a problem or issue.
A: The 5 Whys technique involves repeatedly asking “why” to identify the underlying cause of a problem. After asking “why” five times or until the root cause is revealed, you can develop effective solutions to address the issue.
A: The primary purpose of the 5 Whys technique is to identify and address the root cause of a problem. It helps organizations and individuals go beyond surface-level symptoms and understand the deeper issues affecting their processes or systems.
A: The 5 Whys technique is best used when you encounter a problem or issue that needs to be resolved. It is particularly useful for complex problems, recurring issues, or situations where multiple factors contribute to the problem.
A: Yes, the 5 Whys technique can be applied to any industry or field. It is commonly used in manufacturing, engineering, healthcare, software development, project management, and various other sectors.
A: While the technique is called the “5 Whys,” the number of “whys” you need to ask may vary. The goal is to keep asking “why” until you reach the root cause of the problem, which may require more or fewer than five iterations.
A: Yes, there are a few limitations to consider when using the 5 Whys technique. It relies on the skill and knowledge of the people involved, and it may oversimplify complex problems. Additionally, it assumes a linear cause-and-effect relationship, which may not always be accurate.
A: Yes, the 5 Whys technique can be used in a group setting. In fact, involving multiple perspectives can enhance the effectiveness of the technique and lead to more comprehensive problem-solving.

Daniel Croft
Hi im Daniel continuous improvement manager with a Black Belt in Lean Six Sigma and over 10 years of real-world experience across a range sectors, I have a passion for optimizing processes and creating a culture of efficiency. I wanted to create Learn Lean Siigma to be a platform dedicated to Lean Six Sigma and process improvement insights and provide all the guides, tools, techniques and templates I looked for in one place as someone new to the world of Lean Six Sigma and Continuous improvement.
Download Template

Free Lean Six Sigma Templates
Improve your Lean Six Sigma projects with our free templates. They're designed to make implementation and management easier, helping you achieve better results.
Was this helpful?
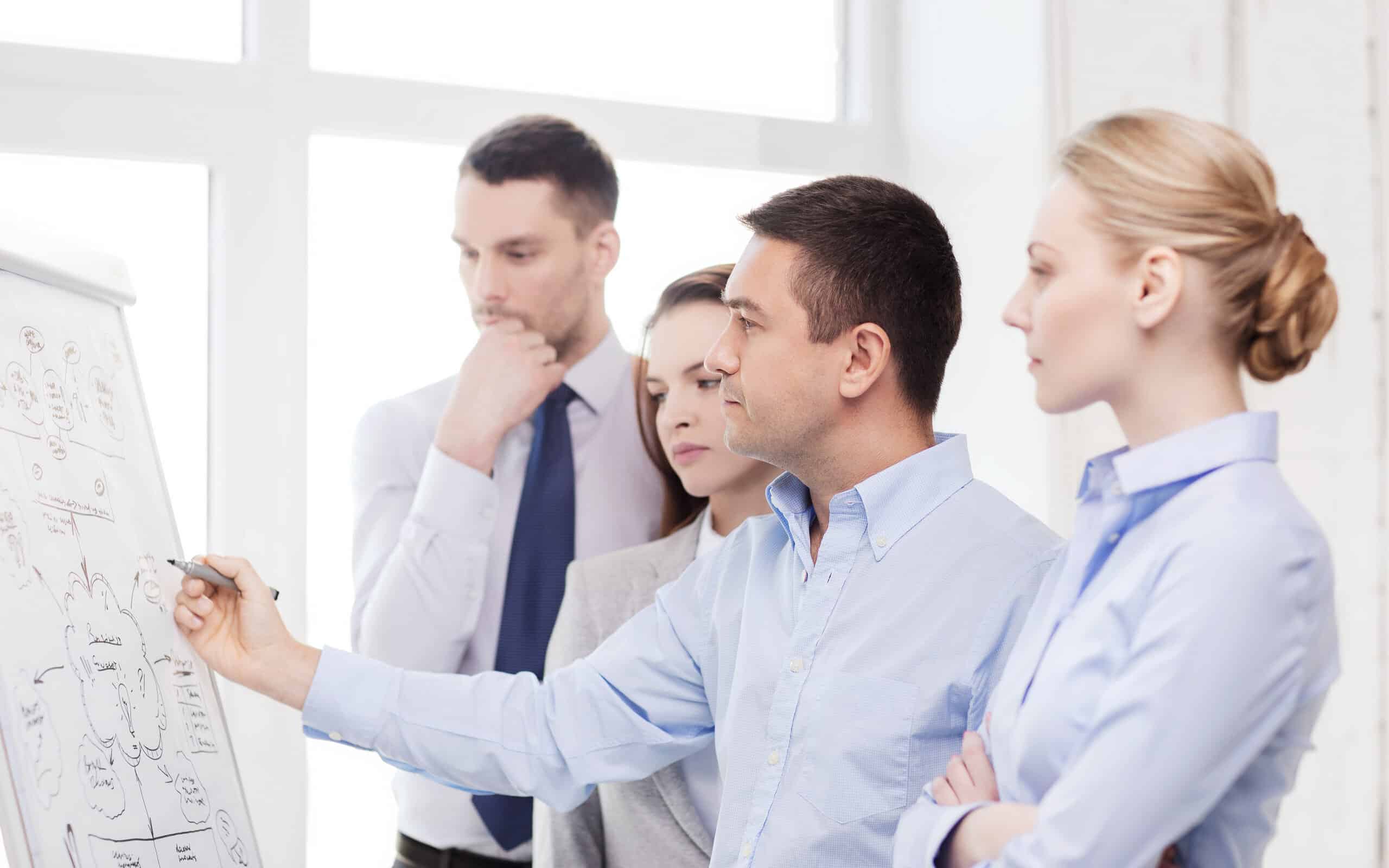
The Simple Yet Powerful 5 Whys Method for Effective Problem-Solving
Updated: May 16, 2023 by Lori Kinney
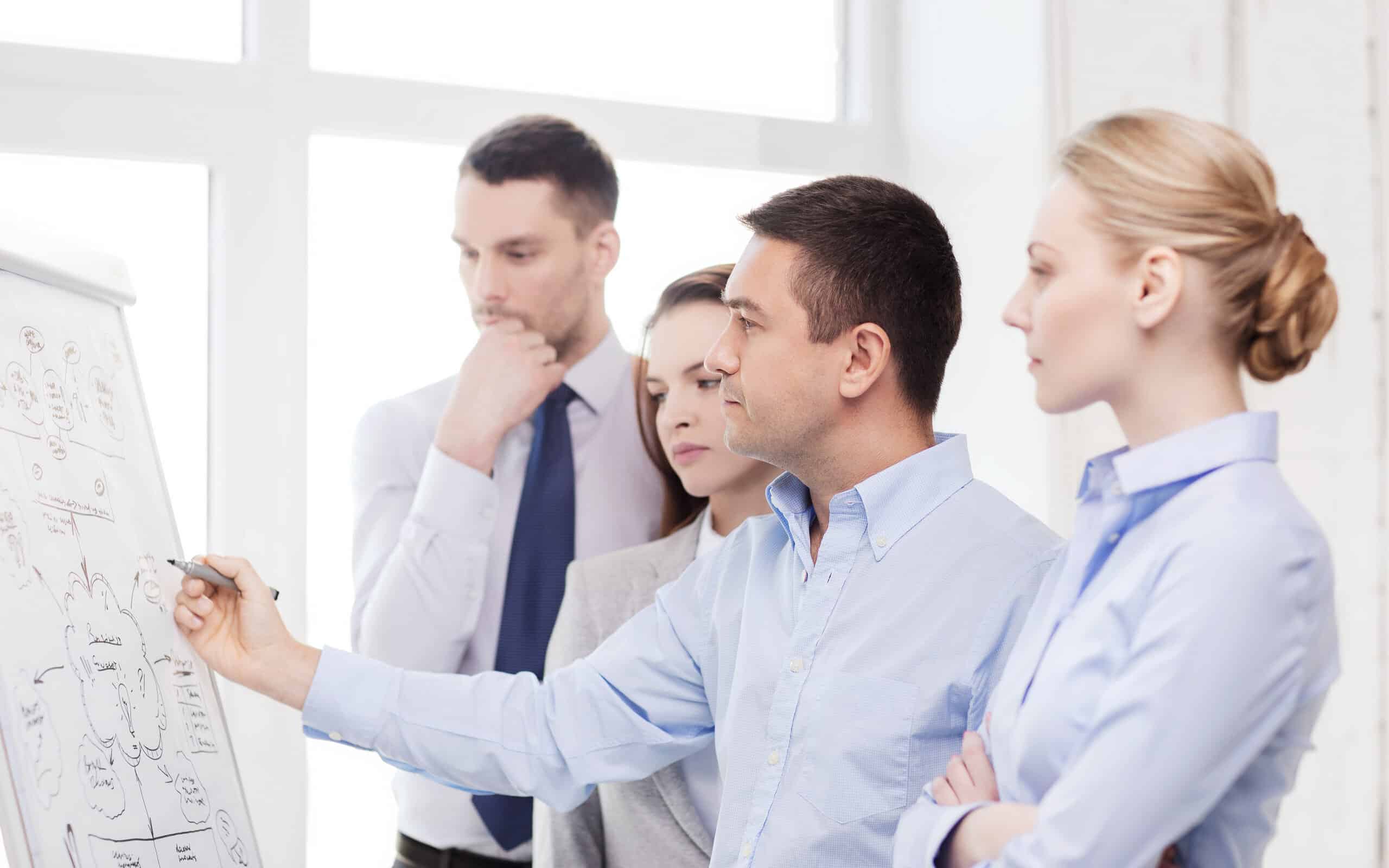
As a child, you were always asking your parents “Why this?” “Why that?” “Why can’t I do this?” “Why can’t I do that?” Little did you know that you were preparing yourself to be a problem-solver looking for root causes when you would grow up.
This article will discuss what is the 5 Why method of looking for a problem’s root cause, how to correctly ask the questions, and what benefits and best practices there might be to help you do a better job of improving your processes.
Overview: What are the 5 Whys?
The 5 Whys technique was developed in the 1930s by Sakichi Toyoda, the Japanese industrialist, inventor, and founder of Toyota Industries. The 5 Whys technique is an iterative, team-driven process that interrogates the problem by asking Why(?) a number of times, usually 5, thus driving the search to uncover the root cause of a problem.
Rather than using the phrase “solutions” once the root cause is found, the 5 Whys uses the term “countermeasures.” A countermeasure is action-oriented and seeks to prevent the problem from happening again, whereas a solution may just seek to deal with the symptoms.
Here is the 5 Why technique in a nutshell:
First, you must have a defined problem. Put together a team to address the problem. Then:
- List: Using a white board, flip chart, butcher paper, or other visual display, list five potential reasons for your problem.
- Evaluate: Using data, subject matter experts, or experience, evaluate each of the five potential reasons.
- Select: Select the one reason that seems to be the most likely potential cause.
- List again: Now list five potential reasons for the potential cause that you selected.
- Evaluate again: Evaluate those five new potential reasons.
- Select again: Again, select the one reason that seems to have the most potential as a root cause.
Repeat the process of list, evaluate, and select as many times as needed until you feel that the root cause has been uncovered. The
Unfortunately, many organizations don’t do the 5 Whys the correct way. Often, they:
- Look at the problem
- Offer one potential cause
- Ask “Why?” for that one cause
- And continue one at a time
In the end, you will have only explored five potential causes. Doing it with the list, evaluate, and select approach, you will have assessed 25 potential causes by listing five for each iteration.
3 benefits of the 5 Whys
This technique has been around since the 1930s. It has been shown to work and can be successfully applied to many situations.
1. It is a simple yet powerful tool
With just the use of a flip chart and a few markers, a group of people can usually get to the root cause of a problem relatively quickly.
2. A sking “why” 5 times focuses the team on getting to the root cause
Using this approach in a disciplined fashion will get you to focus on the causes and prevent you from jumping to conclusions as to the solution.
3. Helps engage the people who deal with the problem
Getting input from the people who deal with the problem and making them part of the solution can result in better buy-in and engagement.
Why are the 5 Whys important to understand?
While the 5 Why technique is simple, you must understand the proper mechanics of the method so that you get the best results possible.
It encourages collaborative problem-solving
Getting the team to collaboratively work together is not only important for the 5 Why problem solving session but for any future activities that would improve the process.
You want to focus on improvement, not blame
Do not allow such causes as “ human error,” “employee attitude,” “communication,” and other generic and ill-defined reasons to be used as the root cause.
Understand the importance of having support from leadership
Hopefully, in the end, the team will come up with a number of countermeasures that will remove the root cause(s) of a problem. It will usually fall upon leadership to provide the resources to make the change. Avoid future frustration by having management on board with this technique from the beginning.
An example of the 5 Whys in use
An example is in order.
You are on your way home from work, and your car stops:
- Why did your car stop? Because it ran out of gas.
- Why did it run out of gas? Because I didn’t buy any gas on my way to work.
- Why didn’t you buy any gas this morning? Because I didn’t have any money.
- Why didn’t you have any money? Because I lost it all last night in a poker game.
This example should illustrate the importance of digging down beneath the most proximate cause of the problem. Failure to determine the root cause assures that you will be treating the symptoms of the problem instead of its cause, in which case, the disease will return — that is, you will continue to have the same problems over and over again.
Also note that the actual numbers of whys is not important as long as you get to the root cause. One might also ask, “Why did you lose all your money in the poker game last night?”
Here’s another example. The Washington Monument was disintegrating:
- Why? Use of harsh chemicals
- Why? To clean pigeon poop
- Why so many pigeons? They eat spiders and there are a lot of spiders at monument
- Why so many spiders? They eat gnats and lots of gnats at monument
- Why so many gnats? They are attracted to the light at dusk.
Countermeasure: Turn on the lights at a later time.
3 best practices when thinking about the 5 Whys
Doing the 5 Whys is simple, but not easy. Keep the team on task and take advantage of the team members’ knowledge, experience, and enthusiasm.
1. Don’t try to do this alone; use a group of people involved in the process
Five heads are better than one. Select a diverse group of team members to get the widest perspective.
2. Focus on counter measures rather than solutions
The solution to a headache is to take two aspirin. The countermeasure to a headache is to find out what is causing it and remove it.
3. Be open and respectful of everyone’s input and participation
Everyone’s idea has value. You never know who might hold the hidden gem. Listen and be respectful so people will feel comfortable offering their ideas — you’ll also have better buy-in once you find the root cause.
Frequently Asked Questions (FAQ) about the 5 Whys
Can i ask more than 5 whys .
Yes. You can ask more than five or less than five. The key is, how many questions does it take to get to what appears to be the root cause.
Can I use the computer to do the 5 Why exercise?
It’s recommended that you use something more tactile like flip charts. This way, you can tear them off and hang them on the wall for everyone to see. The more visual you make the work, the better.
Should my manager run the 5 Why session or someone else?
Since the manager often has a stake in the outcome of the process, it might be best to use a neutral facilitator who can help keep the team on task, ask the right questions, and not get defensive when the potential causes are mentioned.
The 5 Whys wrapped up
The 5 Whys is an iterative, team-based approach to asking questions about the potential causes of a problem. Once the problem is defined, the potential causes should be listed, evaluated, and selected, and then repeated as many times as necessary to get to the root cause.
Once the root cause(s) is identified, the team should recommend specific, action-oriented countermeasures to mitigate or eliminate the root cause of the problem. Remember, don’t just address the symptoms; you must find the underlying cause, otherwise the problem will resurface sometime in the future.
Join 65,000 Black Belts and Register For The Industry Leading ISIXSIGMA Newsletter Today
About the author.
Lori Kinney
Table of Contents
What is the 5 Whys framework?
Use the 5 whys to transform your problem-solving approach.
The 5 Whys framework is a problem-solving technique used to identify the root cause of a problem . It’s a simple but powerful way to uncover the underlying reasons behind a problem by asking the question “why” repeatedly. By doing so, you can delve beyond the symptoms and surface-level causes of a problem and reach the fundamental cause that is contributing to the issue. And by addressing the root cause, you have a better chance of implementing effective solutions and preventing the problem from recurring.
Dive into the 5 Whys: Origins, basics, and benefits
Let's demystify the 5 Whys and discover:
What is it?
How does it help identify the root cause of problems?
How does it lead to more effective resolutions?
We'll highlight the benefits that it brings to the table after we provide you with the origins.
Origins of the 5 Whys: From Toyota to today
The 5 Whys technique, a cornerstone in the Toyota Production System, was initially employed to zero in on the root cause of manufacturing issues. The ultimate aim of the approach was to eliminate waste, increase efficiency, and improve quality in manufacturing processes.
With applications beyond the realm of manufacturing, many different industries have adopted the 5 Whys technique over time, demonstrating its powerful ability to drill down to the heart of problems.
Potential of the 5 Whys: Benefits and impact
Incorporating the 5 Whys technique into your problem-solving arsenal brings many benefits, including enhanced efficiency and amplified productivity. It also fosters a proactive problem-solving attitude within your team.
Using the 5 Whys approach is especially beneficial as it hones in on the root cause of issue, which helps prevent its recurrence in the future. By taking corrective actions at the source, businesses can avoid repeatedly dealing with the same issue.
Mastering the 5 Whys: Step-by-step guide
Embarking on a 5 Whys journey is akin to mining for gold — digging through layers to unearth the precious nugget — the root cause of your problem.
Here's your step-by-step guide to ensure a successful excavation with the 5 Whys template .
Step 1: State your problem
Your journey with the 5 Whys begins by clearly stating your problem. This crucial first step lays the groundwork for the entire analysis.
Step 2: Ask your first Why?
Now it's time to get to work. With your problem defined, pose your first "Why" question. The question should address the problem you've just stated.
Step 3: Probe deeper with more Whys
Don't stop there! Keep probing with more "Why" questions. Each question should be a response to the previous answer. Per the classic technique, you'll typically ask five times. Remember, the goal is to dig deeper into the root cause.
Step 4: Unearth the root cause
You'll know you've hit the root cause when your "Why" questions no longer produce meaningful responses. More than likely, you’ve found the core issue that, if addressed, will prevent the problem from recurring.
Step 5: Develop and implement your solution
It's time to take action with the root cause in your sights. Develop a solution that tackles the root cause directly rather than just dealing with surface-level symptoms. And remember, the proof is in the pudding. Implement your solution and observe the effects.
5 Whys in action: Real-world applications and examples
To truly appreciate the 5 Whys, you have to see it in action. We'll explore how the 5 Whys technique is used for root cause analysis in UX Design by delving into a detailed example, demonstrating how to navigate user experience challenges.
UX Design case study: Navigating user experience challenges
Let's take a hypothetical scenario where we encounter a UX Design problem that'll benefit from using the 5 Whys method.
Initial problem : Our latest app design needs to improve user navigation.
Application of the 5 Whys method:
Why is navigation difficult? Users need help finding the search function.
Why are users having trouble finding the search function? The search function needs to be more easily visible.
Why isn't the search function easily visual? Because it's located within a menu, not on the main screen.
Why is it placed on a menu? We wanted to keep the main screen uncluttered.
Why'd we want to keep the main screen uncluttered? It'd enhance the user experience.
Solution implemented: We added a prominent search bar on the app's main screen.
Outcome: user complaints about navigational difficulties were reduced by 50%, leading to an increase in app usage and user satisfaction
Software development: Debugging with precision
For developers, the 5 Whys is a powerful tool for debugging. Let's walk through a hypothetical situation where code goes rogue.
Problem statement:
A recently launched app crashes whenever users try to sign up.
Question: Why does the app crash when users try to sign up?
Answer: Because there's an unhandled exception in the sign-up module
Second Why?
Q: Why is there an unhandled exception in the sign-up module?
A: Because it doesn't handle a case where a new user's email is already in the database.
Q: Why doesn't it handle the case where a new user's email is already in the database?
A: Because there's a missing condition, check for duplicate emails in the code.
By identifying and fixing these common missteps and pitfalls, you'll enhance your usage of the 5 Whys technique. This'll lead to precise root cause detection and practical solutions that address the issues.
Amplifying the 5 Whys with Fishbone Diagrams
You can amplify the 5 Whys by pairing it with a fishbone diagram , also known as the Ishikawa Diagram. This combination enhances problem-solving by mapping cause-and-effect relationships, aiding understanding and decision-making in complex projects.
To combine these methodologies, start by creating a fishbone diagram and map the different categories related to the main problem and their potential causes. For each potential cause, use the 5 Whys technique to explore the underlying reasons and identify the root cause for each branch on the diagram. The 5 Whys analysis will help you to challenge assumptions and discover the fundamental reasons driving each cause in a structured manner.
Miro has easy-to-customize fishbone diagram templates that can help you get started.
Perfecting your 5 Whys approach
To fully harness the power of the 5 Whys, it's crucial to adopt best practices and dodge common pitfalls.
Follow these best practices to perfect your use of the 5 Whys:
Be consistent
Consistency in the 5 Whys lies in persistent probing. Don't stop at initial reasons — repeatedly maintain your Why inquiries. This diligent uncovering of layers helps reveal the root cause.
Beware of assumptions
Assumptions can compromise the 5 Whys effectiveness. Stay on path and validate each Why with data. This grounding ensures your conclusions are fact-based, not assumption-driven.
Keep the big picture in mind
It's crucial to zero in on the problem, but don't let this tunnel vision distract you from the broader perspective. Effective solutions shouldn't only tackle the immediate problem, but they should also seamlessly blend with your overarching objectives and strategies.
Discover more
5 whys: examples, explanations, and how to find the causes of problems, what is root cause analysis, what is a cause and analysis diagram, get on board in seconds, plans and pricing.
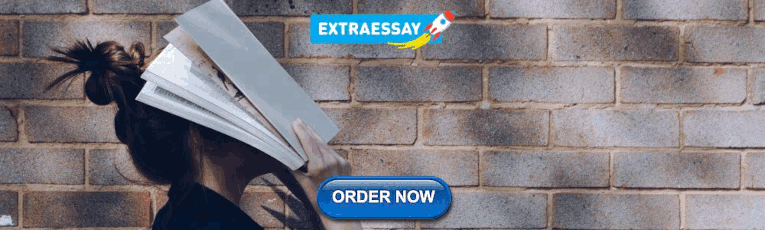
IMAGES
VIDEO
COMMENTS
The 5 Whys strategy is a simple, effective tool for uncovering the root of a problem. You can use it in troubleshooting, problem-solving, and quality-improvement initiatives. Start with a problem and ask why it is occurring.
Within that metholodogy, the 5 whys tool is used specifically for the DMAIC (Define, Measure, Analyze, Improve, and Control) framework. As a result, it helps Six Sigma practitioners find the root cause of a problem by asking successive “why” questions.
The 5 Whys strategy is a simple, effective tool for uncovering the root of a problem. You can use it in troubleshooting, problem-solving, and quality-improvement initiatives. Start with a problem and ask why it is occurring.
An in-depth look at the 5 Whys, a simple problem-solving exercise designed to unearth the root of any problem or unexpected situation.
The 5 Whys Technique is like peeling an onion – it helps you uncover the underlying reasons behind a problem, layer by layer. By repeatedly asking “why” at least five times, this method digs deep to reveal the root cause of an issue.
The 5 Whys is a root cause analysis problem-solving technique that aims to identify the root cause of a problem by repeatedly asking the question “Why?” five times or until the core issue is unveiled. Developed within the Toyota Production System, it’s one of fundamental tools in the Lean Six Sigma methodology. Here’s how it works:
The 5 Whys is a powerful, easy-to-use technique for getting at the root of a problem. It empowers you and your team to understand why a problem persists and to decide on a path forward.
While there are many RCA problem-solving techniques, one popular and easy technique is the 5 Whys method. Performing a 5 Whys analysis is one of the most efficient ways to both discover the root cause of a problem and ensure that steps are taken to prevent it from happening again.
The 5 Whys is an iterative, team-based approach to asking questions about the potential causes of a problem. Once the problem is defined, the potential causes should be listed, evaluated, and selected, and then repeated as many times as necessary to get to the root cause.
How does it help identify the root cause of problems? How does it lead to more effective resolutions? We'll highlight the benefits that it brings to the table after we provide you with the origins. Origins of the 5 Whys: From Toyota to today.