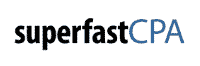
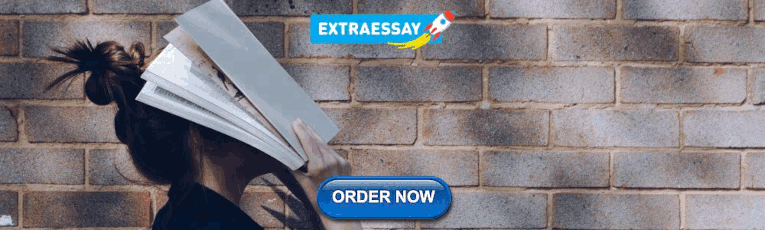
What is Cost Assignment?
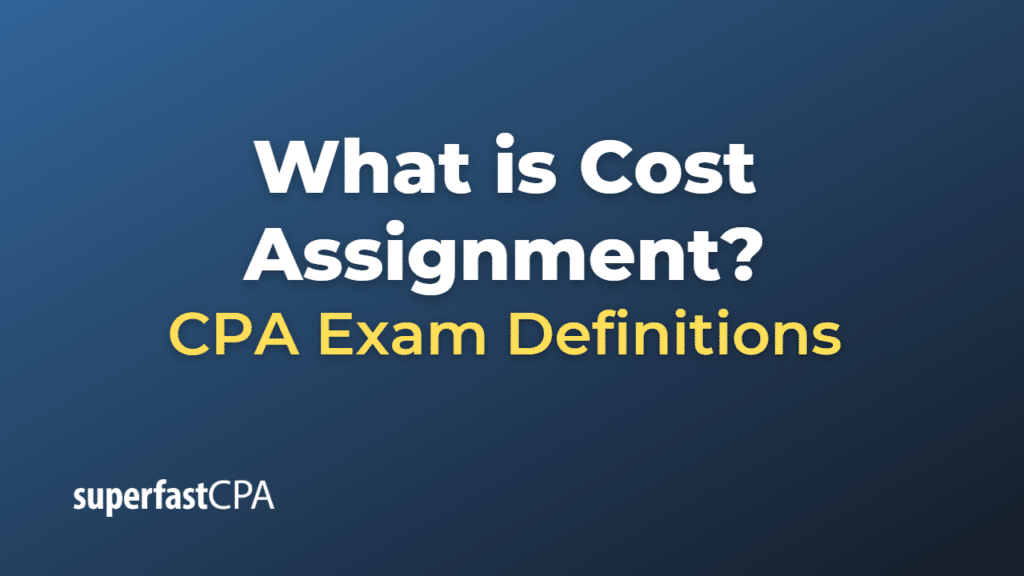
Share This...
Cost assignment.
Cost assignment is the process of associating costs with cost objects, such as products, services, departments, or projects. It encompasses the identification, measurement, and allocation of both direct and indirect costs to ensure a comprehensive understanding of the resources consumed by various cost objects within an organization. Cost assignment is a crucial aspect of cost accounting and management accounting, as it helps organizations make informed decisions about pricing, resource allocation, budgeting, and performance evaluation.
There are two main components of cost assignment:
- Direct cost assignment: Direct costs are those costs that can be specifically traced or identified with a particular cost object. Examples of direct costs include direct materials, such as raw materials used in manufacturing a product, and direct labor, such as the wages paid to workers directly involved in producing a product or providing a service. Direct cost assignment involves linking these costs directly to the relevant cost objects, typically through invoices, timesheets, or other documentation.
- Indirect cost assignment (Cost allocation): Indirect costs, also known as overhead or shared costs, are those costs that cannot be directly traced to a specific cost object or are not economically feasible to trace directly. Examples of indirect costs include rent, utilities, depreciation, insurance, and administrative expenses. Since indirect costs cannot be assigned directly to cost objects, organizations use various cost allocation methods to distribute these costs in a systematic and rational manner. Some common cost allocation methods include direct allocation, step-down allocation, reciprocal allocation, and activity-based costing (ABC).
In summary, cost assignment is the process of associating both direct and indirect costs with cost objects, such as products, services, departments, or projects. It plays a critical role in cost accounting and management accounting by providing organizations with the necessary information to make informed decisions about pricing, resource allocation, budgeting, and performance evaluation.
Example of Cost Assignment
Let’s consider an example of cost assignment at a bakery called “BreadHeaven” that produces two types of bread: white bread and whole wheat bread.
BreadHeaven incurs various direct and indirect costs to produce the bread. Here’s how the company would assign these costs to the two types of bread:
- Direct cost assignment:
Direct costs can be specifically traced to each type of bread. In this case, the direct costs include:
- Direct materials: BreadHeaven purchases flour, yeast, salt, and other ingredients required to make the bread. The cost of these ingredients can be directly traced to each type of bread.
- Direct labor: BreadHeaven employs bakers who are directly involved in making the bread. The wages paid to these bakers can be directly traced to each type of bread based on the time spent working on each bread type.
For example, if BreadHeaven spent $2,000 on direct materials and $1,500 on direct labor for white bread, and $3,000 on direct materials and $2,500 on direct labor for whole wheat bread, these costs would be directly assigned to each bread type.
- Indirect cost assignment (Cost allocation):
Indirect costs, such as rent, utilities, equipment maintenance, and administrative expenses, cannot be directly traced to each type of bread. BreadHeaven uses a cost allocation method to assign these costs to the two types of bread.
Suppose the total indirect costs for the month are $6,000. BreadHeaven decides to use the number of loaves produced as the allocation base , as it believes that indirect costs are driven by the production volume. During the month, the bakery produces 3,000 loaves of white bread and 2,000 loaves of whole wheat bread, totaling 5,000 loaves.
The allocation rate per loaf is:
Allocation Rate = Total Indirect Costs / Total Loaves Allocation Rate = $6,000 / 5,000 loaves = $1.20 per loaf
BreadHeaven allocates the indirect costs to each type of bread using the allocation rate and the number of loaves produced:
- White bread: 3,000 loaves × $1.20 per loaf = $3,600
- Whole wheat bread: 2,000 loaves × $1.20 per loaf = $2,400
After completing the cost assignment, BreadHeaven can determine the total costs for each type of bread:
- White bread: $2,000 (direct materials) + $1,500 (direct labor) + $3,600 (indirect costs) = $7,100
- Whole wheat bread: $3,000 (direct materials) + $2,500 (direct labor) + $2,400 (indirect costs) = $7,900
By assigning both direct and indirect costs to each type of bread, BreadHeaven gains a better understanding of the full cost of producing each bread type, which can inform pricing decisions, resource allocation, and performance evaluation.
Other Posts You'll Like...
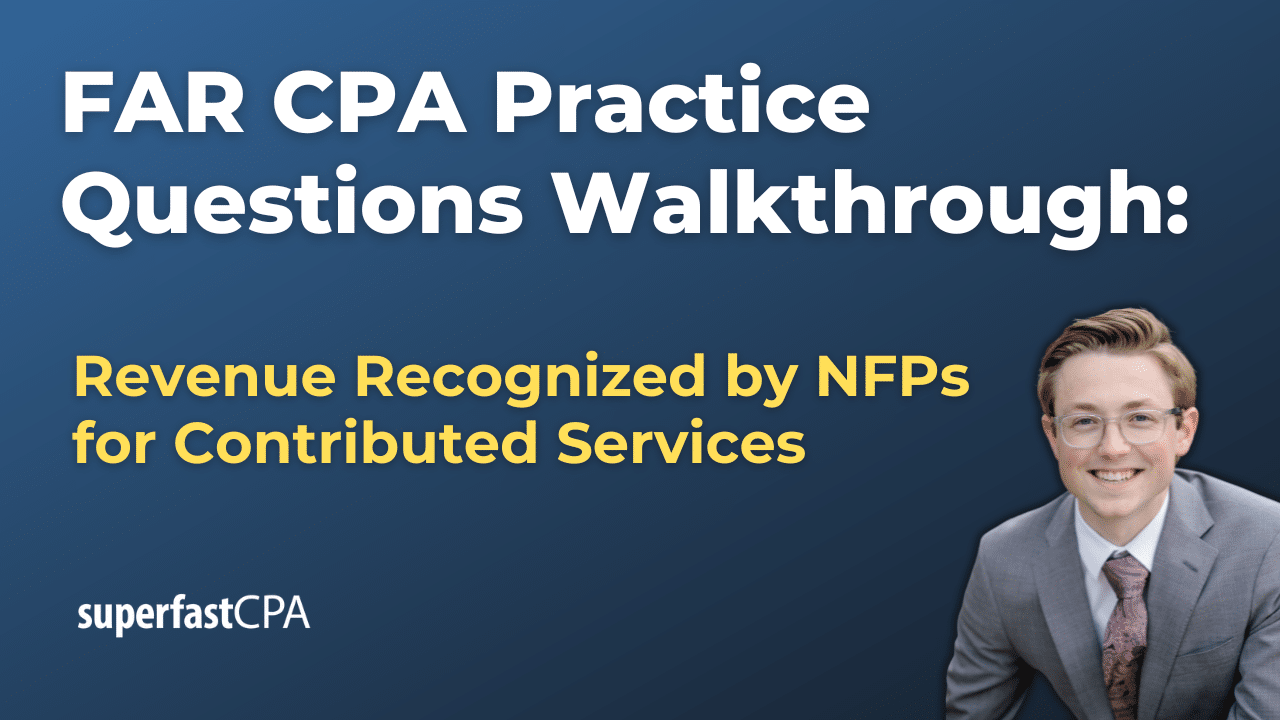
FAR CPA Practice Questions: Revenue Recognized by NFPs for Contributed Services
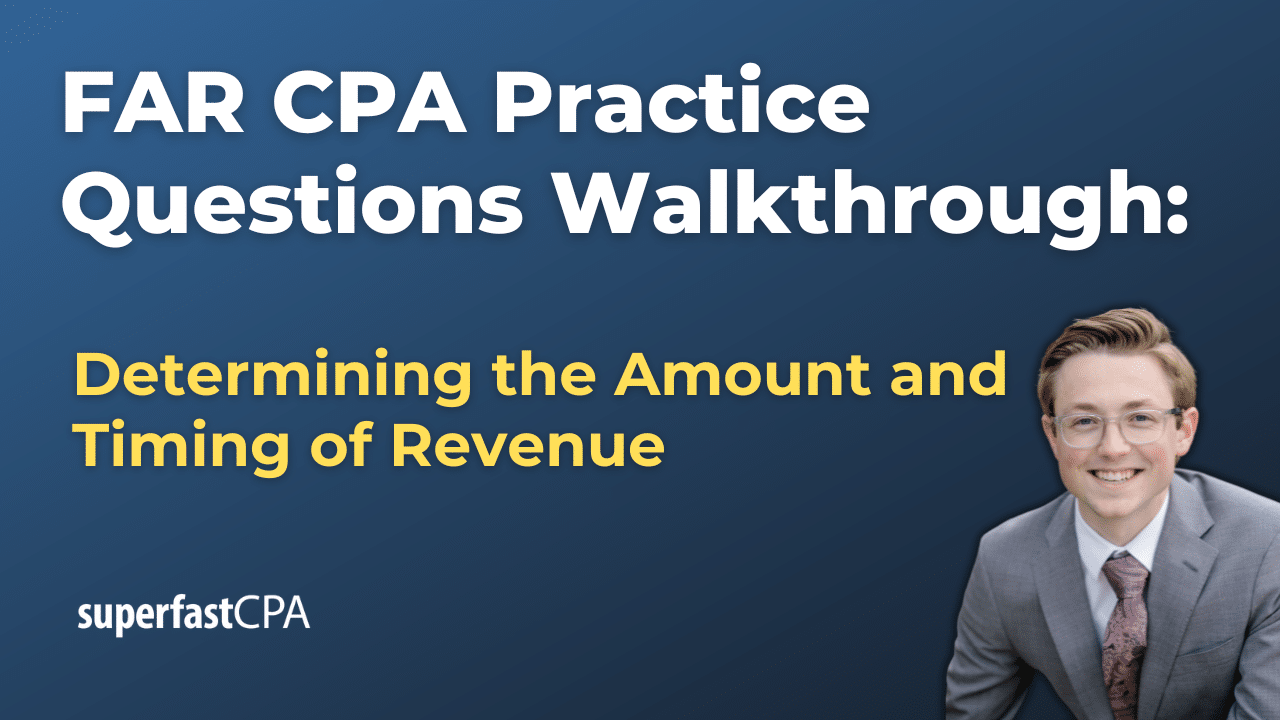
FAR CPA Practice Questions: Determining the Amount and Timing of Revenue
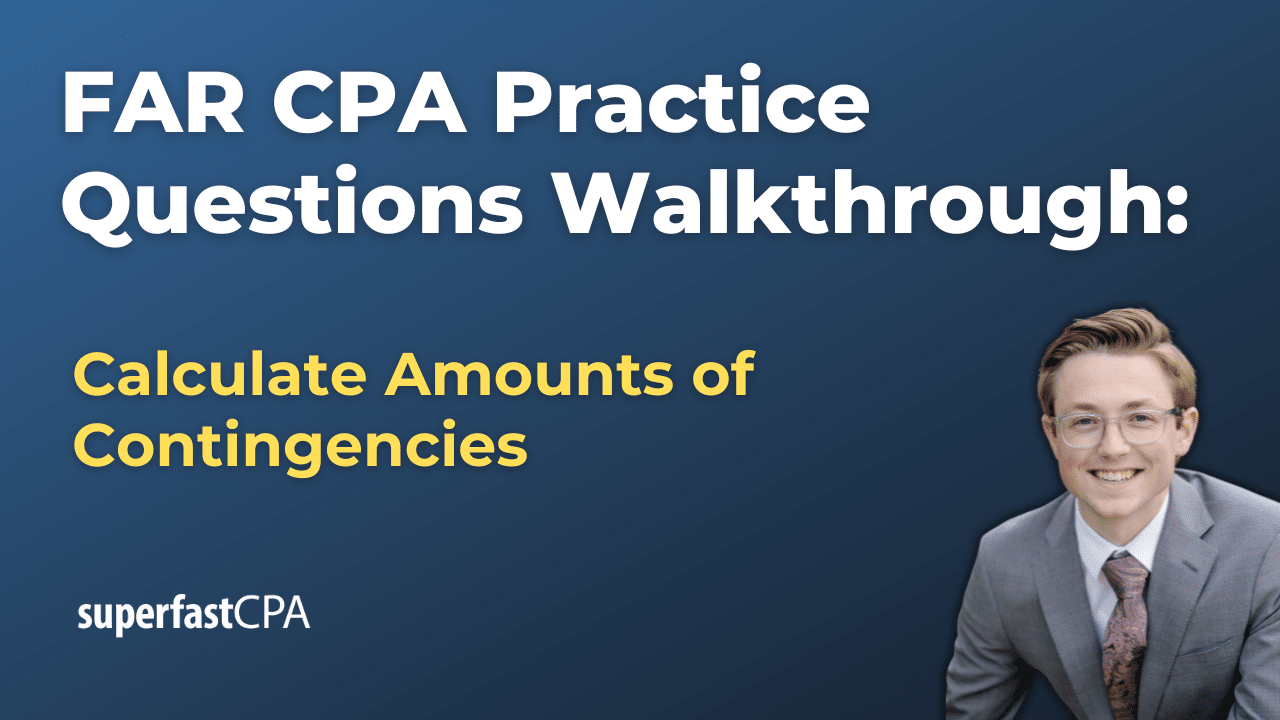
FAR CPA Practice Questions: Calculate Amounts of Contingencies
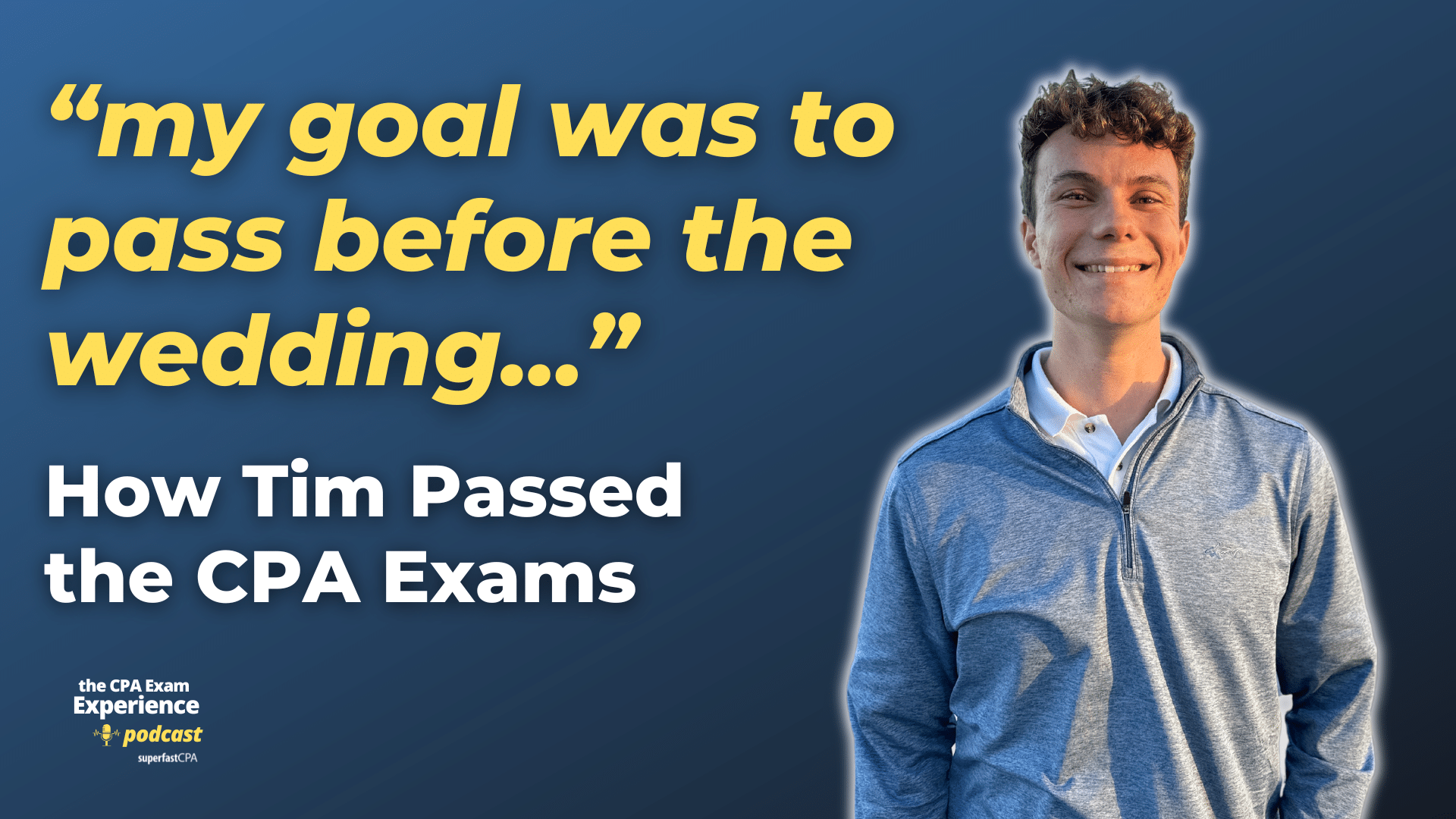
How Tim Passed the CPA Exams While Being Extremely Busy
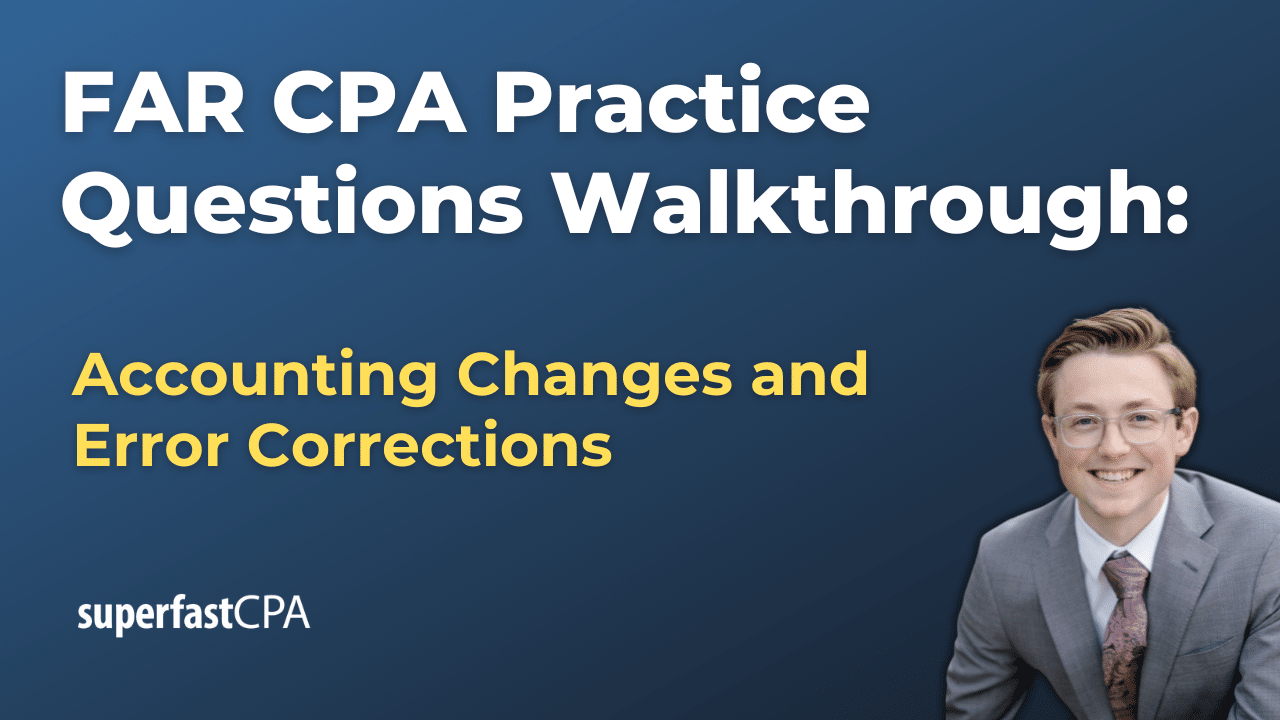
FAR CPA Practice Questions: Accounting Changes and Error Corrections
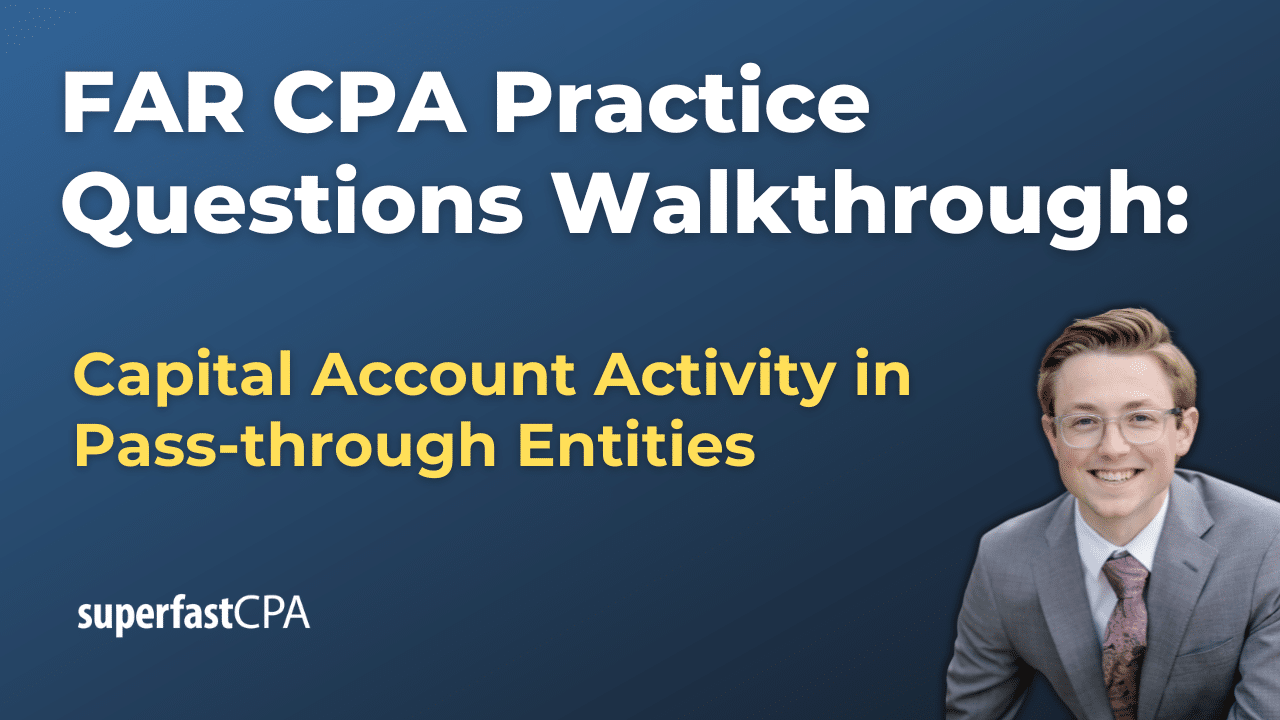
FAR CPA Practice Questions: Capital Account Activity in Pass-through Entities
Helpful links.
- Learn to Study "Strategically"
- How to Pass a Failed CPA Exam
- Samples of SFCPA Study Tools
- SuperfastCPA Podcast
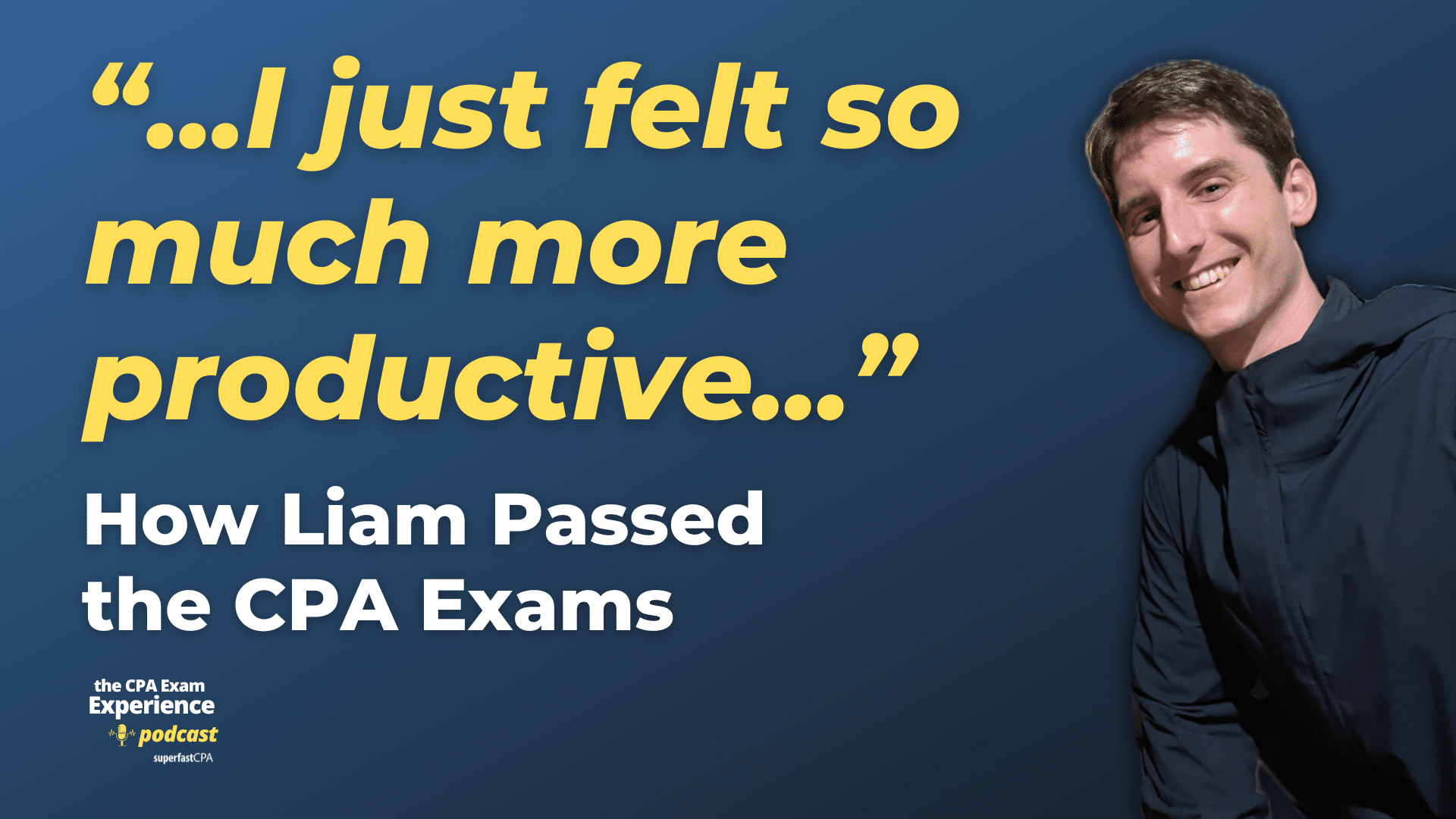
How Liam Passed His CPA Exams by Tweaking His Study Process
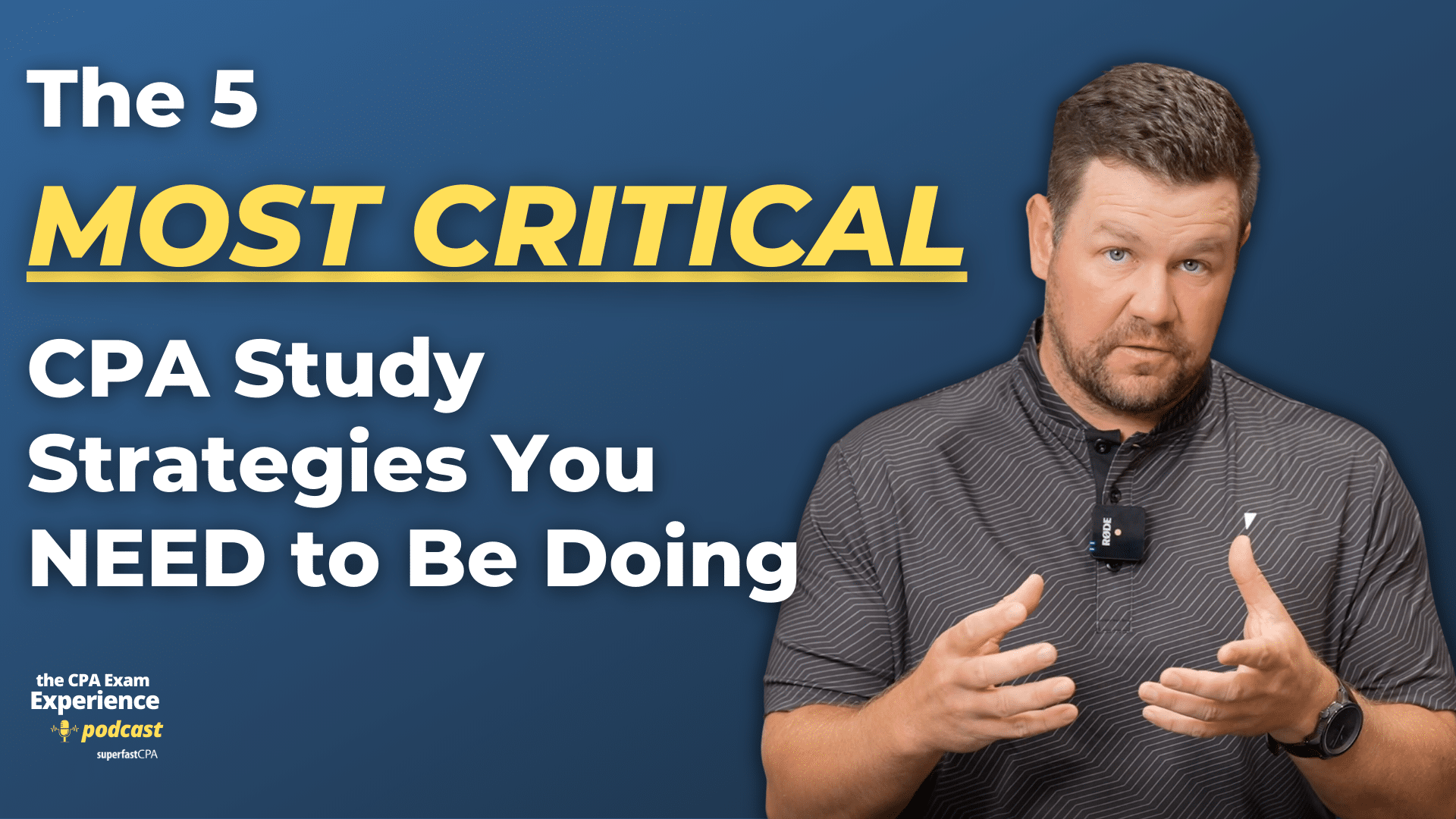
The 5 Critical CPA Exam Study Strategies You Need to Be Doing
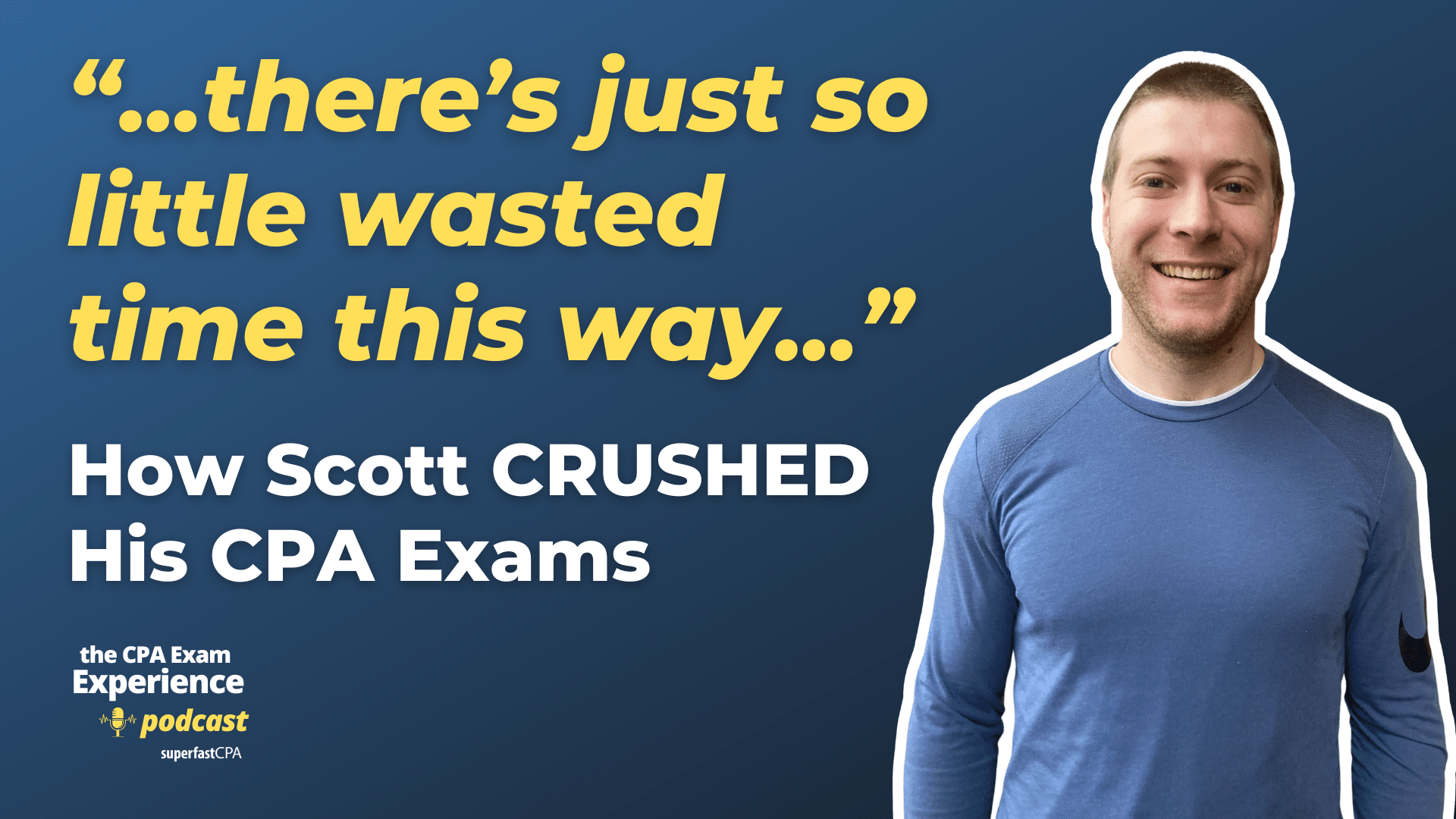
Scoring in the High 90s While Working Full-Time? How Scott Passed His CPA Exams
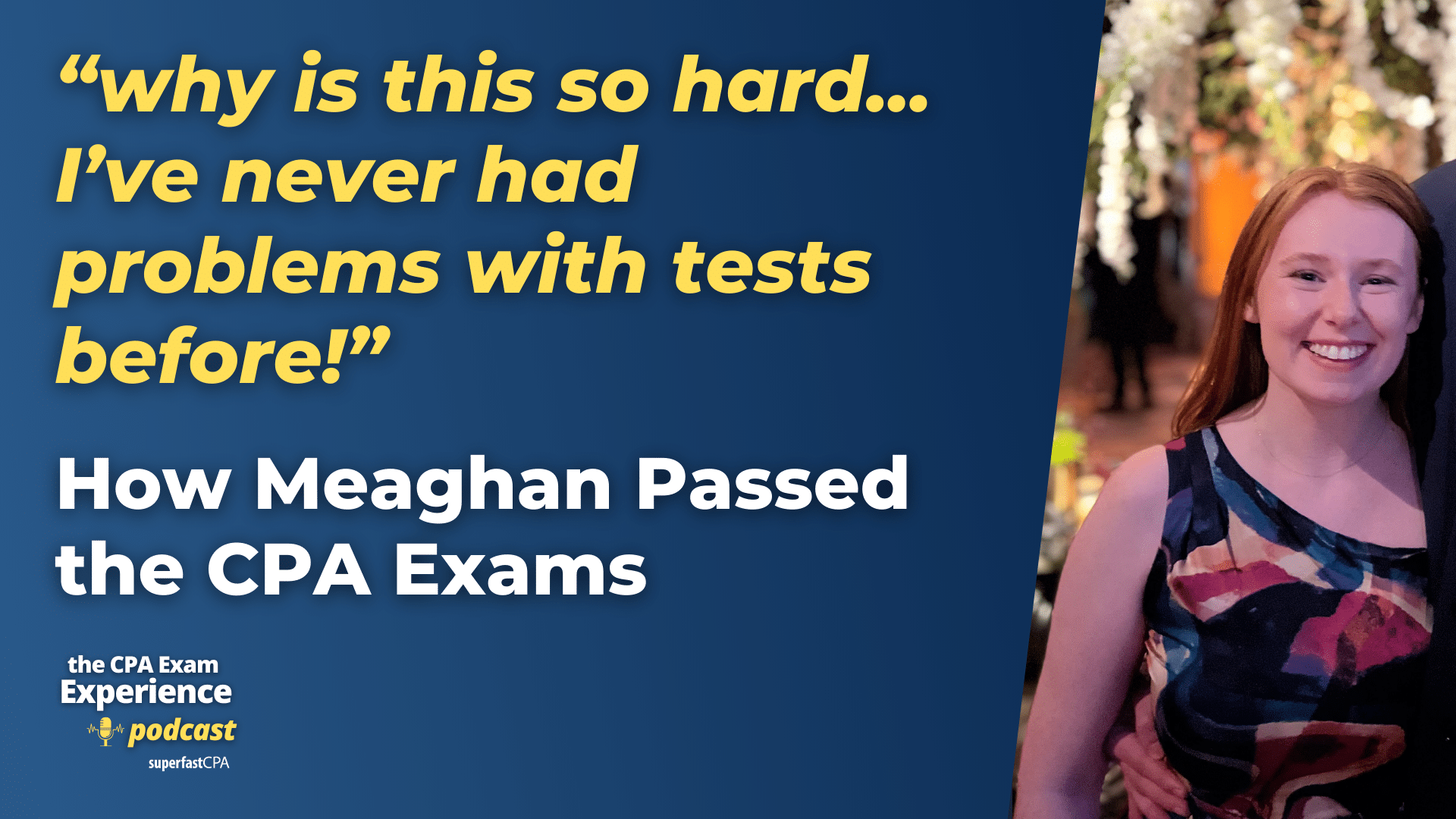
How Studying from Her Phone Helped Meaghan Pass the CPA Exams
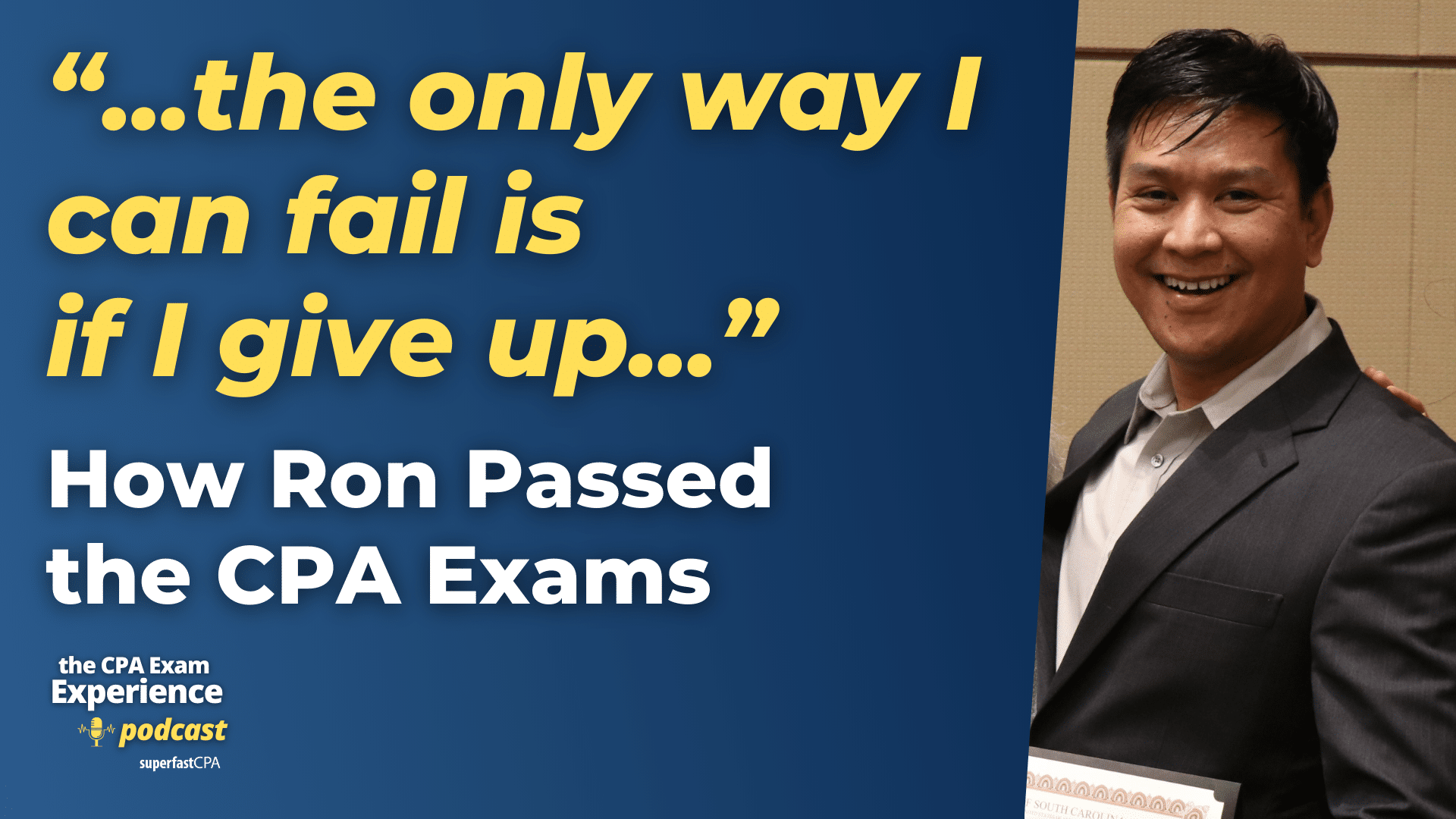
How Ron Passed His CPA Exams by Going All In
Want to pass as fast as possible, ( and avoid failing sections), watch one of our free "study hacks" trainings for a free walkthrough of the superfastcpa study methods that have helped so many candidates pass their sections faster and avoid failing scores....
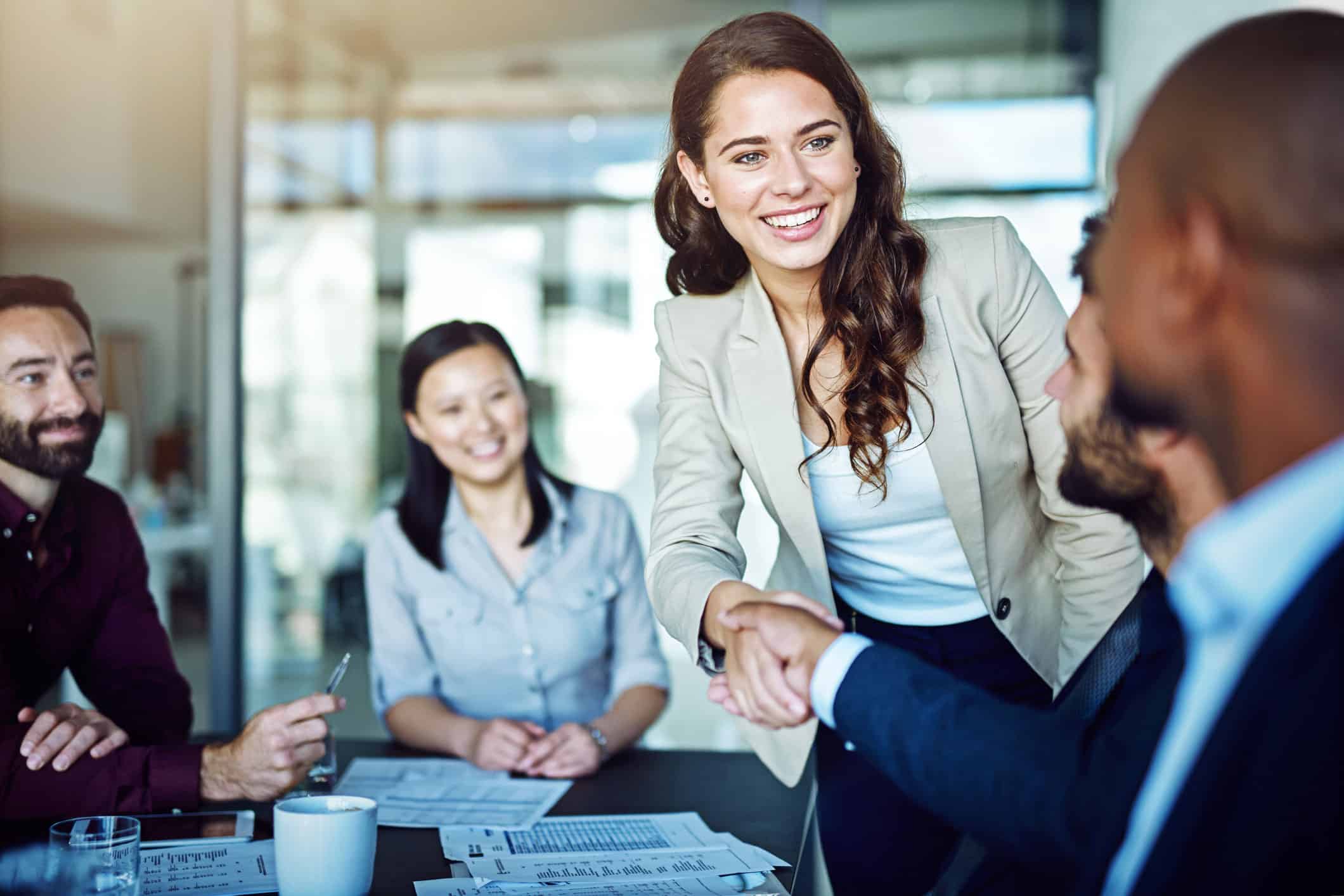
Make Your Study Process Easier and more effective with SuperfastCPA
Take Your CPA Exams with Confidence
- Free "Study Hacks" Training
- SuperfastCPA PRO Course
- SuperfastCPA Review Notes
- SuperfastCPA Audio Notes
- SuperfastCPA Quizzes
Get Started
- Free "Study Hacks Training"
- Read Reviews of SuperfastCPA
- Busy Candidate's Guide to Passing
- Subscribe to the Podcast
- Purchase Now
- Nate's Story
- Interviews with SFCPA Customers
- Our Study Methods
- SuperfastCPA Reviews
- CPA Score Release Dates
- The "Best" CPA Review Course
- Do You Really Need the CPA License?
- 7 Habits of Successful Candidates
- "Deep Work" & CPA Study
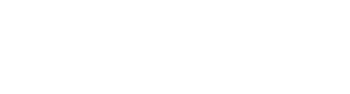
Activity-Based Costing (ABC)

Written by True Tamplin, BSc, CEPF®
Reviewed by subject matter experts.
Updated on June 08, 2023
Get Any Financial Question Answered
Table of contents, activity-based costing (abc) - definition.
An activity-based costing system (also known as ABC System ) is a two-stage procedure for assigning overhead costs to products, which focuses on the major activities performed in the production process.
Activity-based costing is a costing method that identifies activities in an organization and assigns the cost of each activity to all products and services according to the actual consumption by each.
Moreover, Activity-Based Costing (ABC) has been developed as a more modern absorption costing method to overcome the problems of under-costing and over-costing and to produce more accurate product costs.
Explanation of Activity-Based Costing
Activity based Costing (ABC) is a systematic, cause & effect method of assigning the cost of activities to products, services, customers or any cost object.
ABC is based on the principle that “products consume activities”. Traditional cost systems allocate costs based on direct labor, material cost, revenue or other simplistic methods.
As a result, traditional systems tend to over-cost high volume products, services and customers and under-cost low volume.
Activity based costing should not be treated as an alternative to job costing or process costing but as one of the best tools for refining a costing system which provides a better measurement of the non-uniformity in the use of an organization’s overhead resources for job, products and services.
Activity-based costing incorporates in its costing system the basic and vital role of different activities. ABC System refined costing system by focusing on individual activities as the fundamental cost objects.
An activity is an event, task or unit of work with a specified purpose e.g., designing products, setting up machines, operating machines and distributing products.
In traditional absorption costing, overheads are first assigned or related to cost centers, (production and service centers) and then to cost objects i.e., products or services.
But in Activity-based costing system, overheads are related or assigned to activities or grouped into cost pools before they are related to cost objects i.e., products or services.
Thus, the activity based system system uses activities instead of functional departments (Cost Centers) for absorbing overheads.
The basic feature of functional departments is that they tend to include a series of different activities causing different costs that behave in different ways.
Further, the activities also tend to run across functions.
For example, the procurement or purchase of materials is made on the basis of a requisition note sent by a manufacturing department or stores.
The purchase requisition note is not raised in the purchasing department where most of the costs relating to procurement or purchase are incurred.
Activity costs tend to behave in a similar manner to each other i.e., they have the same cost driver or the factor causing a change in the cost of an activity.
Thus, it is believed that activity-based costing helps in presenting a more realistic picture of the behavior of costs.
Difference Between Traditional Costing and Activity-Based Costing
The basic distinction between traditional cost accounting and ABC is as follows:
Traditional cost accounting techniques allocate costs to products based on attributes of a single unit.
Typical attributes include the number of direct labor hours required to manufacture a unit, purchase cost of merchandise resold or the number of days occupied.
Allocations, therefore, vary directly with the ‘volume of units produced, cost of merchandise sold or days occupied by the customer.
In contrast, Activity based costing (ABC) systems focus on activities required to produce each product or provide each service based on each product’s or service’s consumption of the activities.
Using ABC, overhead costs are traced to products and services by identifying the resources, activities and their costs and quantities to produce output.
A unit or output (a driver) is used to calculate the cost of each activity consumed during any given period of time.
An activity based costing system can be viewed in two different ways:
- The cost assignment view provides information about resources, activities and cost objects.
- The process view provides operational (often non-financial) information about cost drivers, activities and performance.
Factors Prompting the Development of Activity-Based Costing System
Activity based costing System has developed basically on account of the limitations of the traditional absorption costing system.
The basic factors which have prompted the development of Activity based costing (ABC System) may be summarized as follows:
- The traditional methods applied for absorbing overheads lay emphasis on the calculation and application of overhead recovery rates which are acceptable for the valuation of stocks for the purposes of routine financial reporting . The management is not able to find these different traditional methods of costing that may be helpful in making some hard decisions which may affect the product strategies.
- The rapid development of automated production has led to growing overhead costs. According to an estimate, the normal overhead rate which was 200% to 300% of direct costs about 15 years ago, has gone up to 500% to 800%.
- The ever increasing and severe market competition due to globalization has increased the necessity of more accurate product costs in order to avoid the disadvantages of under-costing and over-costing.
- There has been an increase in the tendency towards product diversification to secure economies of scope and increased market share requiring the ascertainment of more accurate product costs under the conditions of the fast-changing cost structure.
Importance/Advantages of Activity-Based Costing
Activity-based costing does not only apply to manufacture organizations: it is also appropriate for service organizations such as financial institutions , medical care providers and government units.
In fact, some banking companies have been applying the concept for years under another name - unit costing.
Unit costing is used to calculate the cost of banking services by determining the cost and consumption of each unit of output of functions required to deliver the service.
A major advantage of using Activity based costing (ABC) is that it avoids or minimizes distortions in product costing that result from arbitrary allocations of indirect costs.
Unlike more traditional line-item budgets which cannot be tied to specific outputs, ABC generates useful information on how money is being spent, if a department is being cost-effective, and how to benchmark (or compare oneself against others) for quality improvements.
Activity Based Costing also provides a clear metric for improvement. It encourages management to evaluate the efficiency and cost-effectiveness of program activities.
Some ABC systems rank activities by the degree to which they add value to the organization or its outputs.
This helps managers identify what activities are really value- added—those that will best accomplish a mission, deliver a service, or meet customer demand —thus improving decision-making through better information, and helping to eliminate waste by encouraging employees to look at all costs.
That is why an essential aspect of any ABC endeavor is to get a clear picture of the activities a business area performs.
When employees understand the activities they perform, they can better understand the costs involved.
Important Terms in Activity-Based Costing
The operation of the ABC System involves the use of the following terms:
- Cost Object: It indicates an item for which cost is calculated using the Activity-based costing System. For Example, a service, a customer or a product.
- Cost Driver: A cost driver is any factor or force that causes a change in the cost of an activity.
Cost driver may be divided into two parts:
(a) Resource Cost Driver and
(b) Activity Cost Driver.
The quantity measure of the resources used/consumed by an activity is called Resource Cost Driver. It is used to assign the cost of a resource to an activity or cost pool.
An activity cost driver is Really a measure of frequency and Strength of Demand, set on tasks by cost items.
It’s utilized to assign activity costs to cost objects. The price drivers for various company purposes i.e., manufacturing, promotion, research and development, etc., have been provided below:

Steps to Follow in Activity-Based Costing
Activity Based Costing requires accountants to follow these steps.
- Step 1: Identify the activities that consume resources.
- Step 2: Assign costs to activities.
- Step 3: Identify the cost driver associated with each activity. A cost driver is a factor that causes, or "drives" an activity's cost.
- Step 4: Compute a cost rate per cost driver unit.
- Step 5: Assign costs to products by multiplying the cost driver rate times the volume of cost drivers consumed by the product.
Need or Objects of Activities-Based Costing
ABC System is needed by an organization for the purpose of accurate product costing in cases where:
- Production overhead costs are high in comparison to the various direct costs;
- The product range of the organization is highly diverse;
- Overhead resources used by various products are very different in amounts;
- Volume or quantity of production is not a primary driving force for the consumption of overhead resources.
Limitations of ABC System
The ABC System suffers from the following limitations:
- This system is more time-consuming due to the fact that the number of activities to which the overhead resources of an organization have to be related, is very large.
- It involves a high cost of operation and can be used only by large organizations. It is not suitable for small scale units.
- In some cases, the establishment of cause and effect relationship between Cost Driver and Costs may not be a simple affair.
Jumbo Auto Ltd. produces three products ‘P’, ‘Q’ and ‘R’ for which the standard costs and quantities per unit are as follows:

Production overhead split by departments:

Department ‘A’ is labor intensive while Department ‘B’ is machine intensive. Total labor hours in Department A = 55,000 Total machine hours in Department B = 1,50,000 Production overhead split by activity:

You are required to:
(i). Prepare Product Cost Statement under traditional Absorption Costing and Activity-based Costing Method.
(ii). Compare the results under two methods:
Traditional Absorption Costing
Calculation of overhead absorption rates : Department ‘A’ = $5,50,000 / 55,000 Labor hours = $10 per labor hour.
Department ‘B’ = $7,50,000 / 1,50,000 Machine Hours = $5 per machine hour.

Activity-based Costing
Calculation of Cost Driver Rates:
(i). Receiving/Inspecting = $7,00,000 / 2,500 (No. of batches received/inspected) = $280 per requisition .
(ii). Production Scheduling/Machine Sets-up = $6,00,000 / 400 (No. of batches for scheduling) = $1,500 per set-up

Note: Calculation of Overhead per unit.
Receiving: Product P = ($280 x 600) / 5,000 = $33.60 Product Q = ($280 x 900) / 15,000 = $16.80 Product R = ($280 x 1,000) / 22,500 = $12.44
Production Scheduling: Product P = ($1,500 x 140) / 5,000 = $42.00 Product Q = ($1,500 x 110) / 15,000 = $11.00 Product R = ($1,500 x 150) / 22,500 = $10.00
Comparison of Results Under Both Costing Methods
From the above analysis, it is clear that the Traditional Absorption Costing Method and Activity-based Costing Method show different cost results.
Under the traditional absorption costing method, Product ‘R’ is more expensive while under activity-based costing method, product ‘P’ is more expensive.
If we assume that Activity-Based Costing is more accurate (which may or may not be possible), under traditional absorption costing method, product ‘R’ would be over-priced while product ‘P’ would be underpriced as a result of which sales for product ‘R’ would be less and sales for product ‘P’ would be more leading to a loss to the company.
Activity-Based Costing (ABC) FAQs
What are the different types of cost drivers under abc.
Explicit cost driver- explicit cost drivers are those which are included in the accounting records of an organization at the time of preparing Financial Statements. These include items such as salaries, raw material consumption etc. Implicit cost drivers- Implicit cost drivers are not recorded in the accounting records of an organization during the preparation of Financial Statements. These include factors such as machine hours, labor hours etc.
What is a cost pool under ABC?
A cost pool consists of one or more similar activities that can't be identified easily with specific products, services, departments etc. Cost pools are used to account for the common costs of the organization.
What is a cost element under ABC?
A cost element refers to an account which receives and accumulates costs over a period of time. It also includes the revenue accounts that receive and accumulate revenues over a period of time.
What is a service level in ABC?
A service level measures the number of requests that are processed by an organization within a set time frame. Generally, the higher the number of services within the predetermined time period, the more efficient is the organization.
What is Activity-Based Costing (ABC)?
Activity-Based Costing (ABC) is a method of cost accounting that assigns costs to products and services based on the activities that produce them, rather than allocating overhead costs using traditional methods such as direct labor hours or machine hours.

About the Author
True Tamplin, BSc, CEPF®
True Tamplin is a published author, public speaker, CEO of UpDigital, and founder of Finance Strategists.
True is a Certified Educator in Personal Finance (CEPF®), author of The Handy Financial Ratios Guide , a member of the Society for Advancing Business Editing and Writing, contributes to his financial education site, Finance Strategists, and has spoken to various financial communities such as the CFA Institute, as well as university students like his Alma mater, Biola University , where he received a bachelor of science in business and data analytics.
To learn more about True, visit his personal website or view his author profiles on Amazon , Nasdaq and Forbes .
Related Topics
- Activity-Based Costing (ABC) Principles, History & Steps
- Computation of Unit Cost Under Activity-Based Costing
Ask a Financial Professional Any Question
We use cookies to ensure that we give you the best experience on our website. If you continue to use this site we will assume that you are happy with it.
Fact Checked
At Finance Strategists, we partner with financial experts to ensure the accuracy of our financial content.
Our team of reviewers are established professionals with decades of experience in areas of personal finance and hold many advanced degrees and certifications.
They regularly contribute to top tier financial publications, such as The Wall Street Journal, U.S. News & World Report, Reuters, Morning Star, Yahoo Finance, Bloomberg, Marketwatch, Investopedia, TheStreet.com, Motley Fool, CNBC, and many others.
This team of experts helps Finance Strategists maintain the highest level of accuracy and professionalism possible.
Why You Can Trust Finance Strategists
Finance Strategists is a leading financial education organization that connects people with financial professionals, priding itself on providing accurate and reliable financial information to millions of readers each year.
We follow strict ethical journalism practices, which includes presenting unbiased information and citing reliable, attributed resources.
Our goal is to deliver the most understandable and comprehensive explanations of financial topics using simple writing complemented by helpful graphics and animation videos.
Our writing and editorial staff are a team of experts holding advanced financial designations and have written for most major financial media publications. Our work has been directly cited by organizations including Entrepreneur, Business Insider, Investopedia, Forbes, CNBC, and many others.
Our mission is to empower readers with the most factual and reliable financial information possible to help them make informed decisions for their individual needs.
How It Works
Step 1 of 3, ask any financial question.
Ask a question about your financial situation providing as much detail as possible. Your information is kept secure and not shared unless you specify.

Step 2 of 3
Our team will connect you with a vetted, trusted professional.
Someone on our team will connect you with a financial professional in our network holding the correct designation and expertise.

Step 3 of 3
Get your questions answered and book a free call if necessary.
A financial professional will offer guidance based on the information provided and offer a no-obligation call to better understand your situation.

Where Should We Send Your Answer?
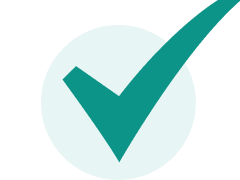
Just a Few More Details
We need just a bit more info from you to direct your question to the right person.
Tell Us More About Yourself
Is there any other context you can provide.
Pro tip: Professionals are more likely to answer questions when background and context is given. The more details you provide, the faster and more thorough reply you'll receive.
What is your age?
Are you married, do you own your home.
- Owned outright
- Owned with a mortgage
Do you have any children under 18?
- Yes, 3 or more
What is the approximate value of your cash savings and other investments?
- $50k - $250k
- $250k - $1m
Pro tip: A portfolio often becomes more complicated when it has more investable assets. Please answer this question to help us connect you with the right professional.
Would you prefer to work with a financial professional remotely or in-person?
- I would prefer remote (video call, etc.)
- I would prefer in-person
- I don't mind, either are fine
What's your zip code?
- I'm not in the U.S.
Submit to get your question answered.
A financial professional will be in touch to help you shortly.
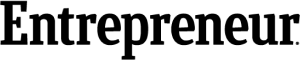
Part 1: Tell Us More About Yourself
Do you own a business, which activity is most important to you during retirement.
- Giving back / charity
- Spending time with family and friends
- Pursuing hobbies
Part 2: Your Current Nest Egg
Part 3: confidence going into retirement, how comfortable are you with investing.
- Very comfortable
- Somewhat comfortable
- Not comfortable at all
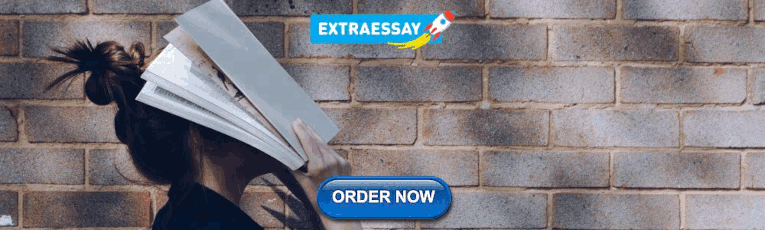
How confident are you in your long term financial plan?
- Very confident
- Somewhat confident
- Not confident / I don't have a plan
What is your risk tolerance?
How much are you saving for retirement each month.
- None currently
- Minimal: $50 - $200
- Steady Saver: $200 - $500
- Serious Planner: $500 - $1,000
- Aggressive Saver: $1,000+
How much will you need each month during retirement?
- Bare Necessities: $1,500 - $2,500
- Moderate Comfort: $2,500 - $3,500
- Comfortable Lifestyle: $3,500 - $5,500
- Affluent Living: $5,500 - $8,000
- Luxury Lifestyle: $8,000+
Part 4: Getting Your Retirement Ready
What is your current financial priority.
- Getting out of debt
- Growing my wealth
- Protecting my wealth
Do you already work with a financial advisor?
Which of these is most important for your financial advisor to have.
- Tax planning expertise
- Investment management expertise
- Estate planning expertise
- None of the above
Where should we send your answer?
Submit to get your retirement-readiness report., get in touch with, great the financial professional will get back to you soon., where should we send the downloadable file, great hit “submit” and an advisor will send you the guide shortly., create a free account and ask any financial question, learn at your own pace with our free courses.
Take self-paced courses to master the fundamentals of finance and connect with like-minded individuals.
Get Started
To ensure one vote per person, please include the following info, great thank you for voting., get in touch with a financial advisor, submit your info below and someone will get back to you shortly..
- Search Search Please fill out this field.
What Is Activity-Based Costing (ABC)?
How activity-based costing (abc) works, requirements for activity-based costing (abc), benefits of activity-based costing (abc), what are the five levels of activity in abc costing, what does activity-based costing seek to identify, how do you calculate abc costing, the bottom line.
- Corporate Finance
Activity-Based Costing (ABC): Method and Advantages Defined with Example
:max_bytes(150000):strip_icc():format(webp)/wk_headshot_aug_2018_02__william_kenton-5bfc261446e0fb005118afc9.jpg)
Activity-based costing (ABC) is a costing method that assigns overhead and indirect costs to related products and services. This cost accounting method recognizes the relationship between costs, overhead activities, and manufactured products, assigning indirect costs to products less arbitrarily than traditional costing methods. However, some indirect costs—such as management and office staff salaries—are difficult to assign to a product.
Key Takeaways
- Activity-based costing (ABC) is a method of assigning overhead and indirect costs—such as salaries and utilities—to products and services.
- This system of cost accounting is based on "activities"; an activity is any event, unit of work, or task with a specific goal.
- All activities are cost drivers: Purchase orders and machine setups are examples of activities.
- The cost driver rate, which is the cost pool total divided by the cost driver total, is used to calculate the amount of overhead and indirect costs related to a particular activity.
- ABC is used to get a better grasp on costs, allowing companies to form a more appropriate pricing strategy.
Investopedia / Theresa Chiechi
Activity-based costing (ABC) is mostly used in the manufacturing industry. It enhances the reliability of cost data, hence producing nearly true costs and better classifying the costs incurred by the company during its production process.
This costing system is used in target costing, product costing, product line profitability analysis, customer profitability analysis, and service pricing. Activity-based costing is used to get a better grasp on costs, allowing companies to form a more appropriate pricing strategy.
The formula for activity-based costing is the cost pool total divided by the cost driver, which yields the cost driver rate. The cost driver rate is used in activity-based costing to calculate the amount of overhead and indirect costs related to a particular activity.
The ABC calculation is as follows:
- Identify all the activities required to create the product.
- Divide the activities into cost pools, which include all the individual costs related to an activity. Calculate the total overhead of each cost pool.
- Assign each cost pool activity cost drivers, such as hours or units.
- Calculate the cost driver rate by dividing the total overhead in each cost pool by the total cost drivers.
- Multiply the cost driver rate by the number of cost drivers.
As an activity-based costing example, consider Company ABC, which has a $50,000 per year electricity bill. The number of labor hours has a direct impact on the electric bill. For the year, there were 2,500 labor hours worked; in this example, this is the cost driver. Calculating the cost driver rate is done by dividing the $50,000 a year electric bill by the 2,500 hours, yielding a cost driver rate of $20. For Product XYZ, the company uses electricity for 10 hours. The overhead costs for the product are $200, or $20 times 10.
Activity-based costing benefits the costing process by expanding the number of cost pools that can be used to analyze overhead costs and by making indirect costs traceable to certain activities.
The ABC system of cost accounting is based on activities, which are any events, units of work, or tasks with a specific goal—such as setting up machines for production, designing products, distributing finished goods, or operating machines. Activities consume overhead resources and are considered cost objects.
Under the ABC system, an activity can also be considered as any transaction or event that is a cost driver. A cost driver, also known as an activity driver, is used to refer to an allocation base. Examples of cost drivers include machine setups, maintenance requests, consumed power, purchase orders, quality inspections, or production orders.
There are two categories of activity measures: transaction drivers, which involve counting how many times an activity occurs, and duration drivers, which measure how long an activity takes to complete.
Unlike traditional cost measurement systems that depend on volume count, such as machine hours and/or direct labor hours, to allocate indirect or overhead costs to products, the ABC system classifies five broad levels of activity that are, to a certain extent, unrelated to how many units are produced. These levels include batch-level activity , unit-level activity, customer-level activity, organization-sustaining activity, and product-level activity.
Activity-based costing (ABC) enhances the costing process in three ways. First, it expands the number of cost pools that can be used to assemble overhead costs. Instead of accumulating all costs in one company-wide pool, it pools costs by activity.
Second, it creates new bases for assigning overhead costs to items, so costs are allocated based on the activities that generate costs, instead of on volume measures—such as machine hours or direct labor costs.
Finally, ABC alters the nature of several indirect costs, making costs previously considered indirect—such as depreciation , utilities, or salaries—traceable to certain activities. Alternatively, ABC transfers overhead costs from high-volume products to low-volume products, raising the unit cost of low-volume products.
There are five levels of activity in ABC costing: unit-level activities, batch-level activities, product-level activities, customer-level activities, and organization-sustaining activities. Unit-level activities are performed each time a unit is produced. (For example, providing power for a piece of equipment is a unit-level cost.) Batch-level activities are performed each time a batch is processed, regardless of the number of units in the batch. Coordinating shipments to customers is an example of a batch-level activity.
Product-level activities are related to specific products; product-level activities must be carried out regardless of how many units of product are made and sold. (For example, designing a product is a product-level activity.) Customer-level activities relate to specific customers. An example of a customer-level activity is general technical product support. The final level of activity, organization-sustaining activity, refers to activities that must be completed regardless of the products being produced, how many batches are run, or how many units are made.
The goal of ABC costing is to optimize business activities and processes to enhance efficiency and reduce costs. It seeks to identify the highest cost drivers: the activities and processes that consume the most of a company's resources.
ABC costing is calculated by finding the total cost pool and dividing it by the cost driver. The cost pool is an aggregate of all the costs associated with performing a particular business task, such as making a particular product. Cost drivers are labor hours, machine hours, and customer contacts.
Activity-based costing (ABC) is a costing method that directly ties all overhead and indirect costs to specific products and services.
Activity-based costing recognizes the relationships between costs, overhead activities (all events, tasks, or units of work with a specific purpose), and manufactured products. The goal of activity-based costing is to understand a company's true costs and reduce inefficiencies by identifying the highest cost drivers: the activities and processes that consume most of a company's resources.
Chartered Global Management Accountant. " Activity-Based Costing (ABC) ."
:max_bytes(150000):strip_icc():format(webp)/GettyImages-1324728773-07aaf43a0181415daeef37612645701a.jpg)
- Terms of Service
- Editorial Policy
- Privacy Policy
- Your Privacy Choices

The Basics of a Cost Accounting System
When starting a business, one of the most critical tasks is to develop a cost accounting system. Cost accounting is recording, classifying, and summarizing expenses to calculate a business’s costs and profits.
A cost accounting system is essential for managing a business’s finances and making informed decisions about where to allocate resources. A cost accounting system is necessary for companies as it allows for accurate financial planning and management.
This article will discuss the basics of a cost accounting system and provide tips on creating one.
What Is Cost Accounting?
Cost accounting is recording, classifying, and summarizing the costs associated with a business operation. Cost accounting allows businesses to track and manage their expenses to make informed decisions about allocating resources and achieving desired outcomes.
By understanding where companies spend their money and how they impact business performance, cost accountants can help managers make sound financial decisions.
When performed correctly, cost accounting can provide a clear view of an organization’s financial health and help identify areas of improvement . By tracking spending across departments and products, for example, managers can identify areas where they can achieve efficiencies and clarify the costs associated with specific activities or products.
As a result of these benefits, cost accounting is an essential tool for any business seeking to improve its financial stability and performance.
What is a Cost Accounting System ?
A cost accounting system is a way of recording, classifying, and summarizing expenses to understand where to spend the money and how to improve it. Cost accounting systems help businesses of all sizes to manage their finances, identify areas for improvement, and make strategic decisions about where to allocate resources.
Cost accounting systems also help provide accurate information about spending patterns and performance. They should allow managers to track the costs of products and services, identify which departments are spending too much or too little money, and make informed decisions about where to allocate resources.
The core elements of a cost accounting system are:
A way to identify and track the sources of costs (e.g., materials, labor, overhead)
A way to determine the total price of an item or batch of objects (e.g., product costing)
A way to account for changes in prices over time (e.g., budgeting and forecasting)
A means to compare actual results against expectations (e.g., costing performance analysis)
Cost Accounting System vs. Financial Accounting System
The two systems of accounting: the Cost Accounting System and the Financial Accounting System, play an essential role in managing a company’s financial data. Although both methods have distinct purposes, specific areas overlap, making it difficult to differentiate between them.
Cost Accounting is mainly used for internal decision-making by management and product cost analysis. It calculates the materials, labor, overhead, and other associated expenses related to production processes.
The system requires detailed records of all components in manufacturing or producing any item or service. It helps managers better understand the total cost of production and make informed decisions about pricing strategies and budgeting.
Financial Accounting, on the other hand, is primarily concerned with reporting external financial information to shareholders, creditors, and the government. Financial Accounting statements follow Generally Accepted Accounting Principles (GAAP).
These statements include a company’s balance sheet, income, and cash flow statement. They provide an overview of all revenues earned and expenses incurred by a business during a specific period. As such, they provide quantitative evidence that helps assess a company’s performance and profitability from an outside perspective.
Ultimately, Cost Accounting Systems and Financial Accounting systems play essential roles within any organization. Understanding their differences can help them make more informed decisions about managing their finances effectively.
Why Are Cost Accounting Systems Important?
Cost accounting systems are essential for businesses to track the costs associated with their operations.
Cost accounting systems allow companies to monitor and control expenses easily, accurately measure the performance and profitability of different activities, identify waste areas, and make informed decisions on allocating resources.
1. Monitor & Control Expenses
A cost accounting system provides an accurate record of all business expenses incurred, making it easy to keep track of spending and develop strategies for controlling them.
It helps ensure that money is being spent efficiently and enables companies to make better-informed decisions about cutting costs or increasing revenues.
2. Measure Performance & Profitability
Cost accounting systems provide detailed information about the profitability of each activity within a company’s operations. This information is essential for measuring performance, setting goals and objectives, and understanding the return on investment (ROI) associated with different activities.
3. Identify Waste
Cost accounting systems help to identify areas of waste or inefficiency within a business. Cost accounting systems enable firms to take corrective action and streamline operations for greater efficiency by pinpointing where resources are being misused or misallocated.
4. Allocate Resources
Cost accounting systems provide data about where companies should allocate their resources for the best results. It helps businesses make informed decisions about allocating resources such as personnel, materials, equipment, and other assets efficiently to maximize productivity and profitability.
In conclusion, cost accounting systems are essential because they provide businesses with the information needed to monitor and control expenses, accurately measure performance and profitability, identify waste areas, and make informed decisions about allocating resources.
Companies that invest in cost accounting systems can better understand their operations and make sound strategic decisions for the future.
Main Types of Cost Accounting Systems: Job Order Costing and Process Costing
The two most common accounting systems are job order costing and process costing. They are both critical, but they have different strengths and weaknesses.
Job order costing is better when the goal is to track the costs of producing a specific good or service. It’s also suitable for monitoring inventory changes and detecting cost overages or underruns.
Process costing is better when the goal is to understand how much it costs to produce a product or service. One can use it to find areas where efficiency can be improved and determine whether a proposed project is feasible.
Job Order Costing – Cost Accounting System
Job order costing is a management tool that helps managers identify, assign, and track the costs associated with producing goods and services.
The method helps improve decision-making by providing information about the quantities and prices of individual jobs. Job order costing helps in various industries, including manufacturing, service businesses, and advertising.
There are two main types of job order costing: direct job order costing and indirect job order costing. Direct job order costing involves assigning resources (such as labor hours) to specific jobs on an assembly line, while indirect job order costing involves setting resources (such as materials) to products instead of to particular jobs.
Both methods provide information about how they spent on each product, which can help managers make better decisions about where to allocate resources next.
The basic steps of job order costing are as follows:
Allocate resources among competing demands by creating jobs or tasks.
Track the costs associated with each assignment or position.
Calculate the total cost of goods and services produced by combining the costs for all jobs or tasks.
Make decisions based on the total price of goods and services paid.
Adjust resources as needed to ensure the total cost of goods and services.
Advantages of Job Order Costing
Job order costing is a method used in business to track the costs associated with producing a product or service. This method is more accurate and efficient than traditional methods, such as a production line.
There are several advantages to using job order costing.
It allows for more accurate financial forecasting and planning. By tracking the costs of each production stage, businesses can better predict how much they will need to spend to produce a product or service. This information can help companies make tough investment decisions, such as creating a new product line or hiring additional staff.
Improves efficiency by reducing the amount of time needed to complete tasks. Businesses can minimize waste and ensure they meet the products on time by knowing exactly how much it will cost to produce a product or service at each stage.
A better understanding of expenses. Job order costing helps businesses to understand where their expenses are coming from and allows them to make more informed decisions about where to allocate resources.
Easier decision-making. By knowing what parts of a project are most expensive, businesses can make easier decisions about whether or not they want to invest in those areas.
Disadvantages of Job Costing
The disadvantages of job costing are as follows:
It can be challenging to compare the costs of different jobs due to the varying nature of the work.
Job costing can be time-consuming and complex, which could lead to errors or inaccuracies in reporting.
Determining the actual cost of a job can be challenging, as factors such as variable and indirect costs can be challenging.
It can be challenging to forecast future costs, which could lead to inaccurate forecasts and wasted resources.
Job costing can be resource-intensive, so it could cause a bottleneck in decision-making if not used effectively.
The risks associated with job costing data are also high, including data theft and fraud, loss of confidentiality, and misinterpretation of data.
These drawbacks highlight why it is essential for businesses to carefully consider whether or not job costing is the best tool for their needs before investing resources in developing and implementing the system.
Process Costing – Cost Accounting System
Process costing is a type of costing that estimates the total cost of executing a process. The primary purpose of process costing is to help manage and optimize the execution of a process by estimating the total costs associated with performing the steps in that process.
Process costing can help to estimate the following costs: Direct materials, direct labor, and overhead costs.
One of the most critical aspects of process costing is determining which should include cost categories in an estimate. One should consider many factors when making this decision. It depends on the product, how often to perform the process, and how much variation there is in performance.
But, one of the most important factors to consider when performing process costing is how much variation there is in the output from one batch to another. Many factors, such as variations in raw materials, manufacturing processes, or human error, can cause variability.
By incorporating variability into your cost estimates, you can account for the fact that not every batch will produce the same results.
Advantages of Process Costing
The following are the advantages of using a process costing for decision-making:
It can help identify and reduce waste and inefficiencies in a circle.
It can help managers make better decisions about resource allocation.
It can help identify a need for improvement in the process.
It can provide an overall picture of how much it costs to produce an item or service.
It is a valuable tool for benchmarking against other methods and industries.
It can allow managers to make informed decisions about pricing and other business decisions related to the production process.
Disadvantages of Process Costing
Process costing is a popular tool for managing and tracking the resources used in production. However, there are several disadvantages to using process costing:
It can take time to estimate the resources required for specific processes properly.
It can be challenging to compare the costs of different processes.
It can take time to measure the effectiveness of process improvements .
The costs of various process steps may vary significantly from one company to another.
Process costing may only be suitable for some businesses.
Traditional Vs. Activity-Based Costing
Activity-based costing (ABC) is a method of cost analysis used to determine the costs associated with different activities within a business. It differs from traditional costing techniques because ABC assigns costs to actions rather than products or services.
Activity-based costing helps provide more accurate information on which decisions are from, allowing businesses to better understand the actual price of their products and services.
Traditional costing systems assign overhead costs such as utilities, rent, and insurance to product units without considering any additional details about the activity involved in producing these items. Others criticize this system for being too simple and needing more points for assigning certain costs to particular products.
Moreover, under traditional methods, all resources are treated equally, regardless of their actual usage or the value they provide to the product.
In contrast, activity-based costing assigns costs based on activities and resources used in producing a product or service. The method identifies all activities performed during production and assigns associated overhead costs to products based on their usage of those activities. It allows companies to accurately give overhead costs, resulting in more detailed cost analysis and improved decision-making.
Activity-based costing also helps identify non-value-added activities, which can be eliminated from a business’s processes, leading to increased efficiency and cost savings. Additionally, ABC provides an understanding of how changes in resource usage affect a company’s overall expenses. By examining cost assignments under different scenarios, businesses can make better decisions on how to allocate resources.
Overall, activity-based costing is a more complex and accurate system than traditional cost analysis methods. It provides valuable insight into resource utilization and cost assignment, allowing businesses to make better products and resource allocation decisions. Incorporating ABC into their operations can improve efficiency, reduce costs, and ultimately increase profitability.
Parts of a Cost Accounting System
A cost accounting system is a valuable tool for managing business finances . It allows businesses to track expenses and profits and make informed decisions about where to allocate resources.
A well-designed cost accounting system should include the following five parts: an input measurement basis, inventory valuation method, cost accumulation method, cost flow assumption, and recording interval capability.
Input Measurement Basis
The input measurement basis is part of a cost accounting system that helps to identify and quantify the inputs used in a manufacturing process. Inputs can be physical items like raw materials, parts, or finished products; or intangible items like information technology resources, labor, or management time.
By quantifying the input costs associated with a particular process step, managers can better understand the financial impact of changes to their manufacturing operations. Input measurement basis also plays a vital role in effective costing; a process managers use to identify the total cost of producing a good or service.
2. Inventory valuation method
The objective of inventory valuation is to determine the fair value of an inventory. It is done by estimating the current market value of the list and comparing it to its carrying value.
If the carrying value is greater than the market value, then there is an overstock situation, and companies should do something about it (i.e., reduce stock levels, lower prices, etc.).
If the carrying value is less than the market value, there is a shortage situation, and they should take action (i.e., increase production, increase prices, etc.).
Businesses can use several methods to value their inventory, including the first-in, first-out (FIFO), last-in, last-out (LIFO), and average cost. Each has advantages and disadvantages; businesses typically choose one or more depending on their circumstances.
3. Cost Accumulation Method
The cost accumulation method records, tracks, and summarizes the costs associated with a particular project or undertaking. This method can help ensure accurate financial reporting and facilitate decision-making about allocating resources across different areas of the project.
The cost accumulation method relies on specific accounting records and reports detailing each cost incurred and the total costs. They can use the information to make informed decisions about where to allocate funds to reach project goals.
The main advantages of using the CAM include its ability to help businesses make informed decisions about allocating resources and forecasting future cash flow needs.
Additionally, the CAM can help companies identify spending patterns that may indicate potential problems. However, the main disadvantage of using the CAM is that it can be time-consuming to maintain and can be challenging to apply to complex business models.
4. Cost Flow Assumption
A cost flow assumption is a fundamental costing principle that states the costs associated with producing a good or allocating services to its various stages of production to reflect the relative proportions of ownership and responsibility for those costs.
This assumption is used with other cost accounting principles, such as standard costing , to create a complete picture of how a company spends its money.
The cost flow assumption is from two fundamental assumptions: first, that the costs incurred in producing an asset are proportional to the amount of time and resources used to create that investment, and second, that the expenses incurred during production are homogeneous throughout the production process.
In practice, these assumptions may only sometimes be accurate, but they provide a framework for allocating costs across different stages of production.
5. Recording Interval Capability
Recording interval capability is a critical part of any cost accounting system. The purpose of the recording interval is to ensure that all costs incurred during a particular period are appropriately accounted for and tracked.
By establishing an accurate recording interval, businesses can ensure that they accurately track their expenses and make informed decisions about where to allocate resources.
There are a few considerations that must be taken into account when setting the recording interval.
First, the gap should be long enough to encompass all of the costs associated with a particular project but not so long as to become cumbersome or impractical to maintain.
Next, the interval should be wide enough to capture expenses, such as direct materials, labor, and overhead costs.
Lastly, one should adjust the recording interval periodically as new information becomes available to reflect updated costing information.
What Are The Cost Accounting Principles?
Matching principle.
The Matching principle is a fundamental principle of cost accounting that states that revenues should match expenses. Following the matching principle, businesses can better understand and manage their costs.
This principle is crucial because it allows companies to identify and correct mistakes early in budgeting. Additionally, by matching expenses to revenue, businesses can more accurately track their progress and make informed decisions regarding future expenditures.
Principle of Conservatism
The Principle of conservatism is a cost accounting system that guides businesses in allocating costs between current and future periods. The regulation states that companies should give expenses based on the assumption that prices will be the same in future periods as in the present.
This principle helps decide which costs to include in financial reports and can also guide businesses in their decision-making about investing money and managing resources.
What Are Some Of The Most Popular Cost Accounting Systems?
From a business standpoint, accounting information is vital to making informed decisions and ensuring compliance with laws and regulations. Many businesses use cost accounting systems to track spending and income to ensure accuracy.
Here are some of the most popular cost accounting systems:
1. General ledger (GL) system
A general ledger system is one of the most popular cost accounting systems. It helps businesses account for revenue and costs , which can help companies to make better business decisions.
A general ledger system consists of several components: a receivable ledger, a payable ledger, and a balance sheet.
The receivable ledger tracks the number of money companies have received from customers.
The payable ledger tracks the money companies have paid to their suppliers. The balance sheet measures how much money businesses own (assets) and how much they owe (liabilities).
General ledger systems are vital because they help businesses track their financial status over time. This information can help companies to make better business decisions and avoid financial problems.
2. Accounts payable (AP) system
An Accounts Payable (AP) system is one of the most popular cost accounting systems. AP systems track and record all payments due to vendors and other creditors. They can use this calculation to calculate the financial status of a business and make decisions about how to spend money.
AP systems are helpful for businesses of all sizes. They can be used in companies that manufacture products, provide services, or manage finances. The main advantage of using an AP system is that it easily tracks payments and liabilities. This information can help companies avoid problems with billing, collections, and debt management.
Another benefit of using an AP system is that it can help businesses track expenses. This information can help companies identify areas where they may be spending too much money and change their budgeting process.
3. Production scheduling
Production scheduling is one of the most popular cost accounting systems. It is a planning and control system that aims to optimize the production process by assigning tasks to workers in a way that makes the most sense from a production standpoint. Companies can use production schedules in various industries, including manufacturing, agriculture, and service.
There are several factors to consider when using production scheduling: throughput, lead time, cycle time, capacity utilization, and inventory levels. Throughput is the amount of product produced per hour. Lead time is the time it takes for a product to leave the production line. Cycle time is how long it takes for products to go through the entire production process from start to finish. Capacity utilization is the percentage of maximum possible output achieved. Lastly, inventory levels are how much product is currently on hand.
The Basics Of Cost Accounting System – Conclusion
A cost accounting system is a vital tool for any business. It allows companies to track expenses and profits, making it easier to manage finances and stay competitive.
A reasonable cost accounting system should be simple and provide accurate information, so businesses can make informed decisions about allocating resources and improving their bottom line. Understanding cost accounting basics is vital to creating a successful system.
It includes understanding accounts, transactions, costs, and profit/loss. While it can be daunting to set up and maintain, the benefits are clear: accurate financial reporting, improved decision-making, and improved control over expenses.
The Basics Of Cost Accounting System – Recommended Reading
Cost Accounting Systems Expert
Manufacturing Cost Accounting Assessment (benjaminwann.com)
Depreciation In Cost Accounting: What Is It And Why Does It Matter? (benjaminwann.com)
Is Cost Accounting GAAP? (benjaminwann.com)
Cost Accounting: Definition and Types With Examples (investopedia.com)
Cost Accounting Defined: What It Is & Why It Matters | NetSuite
Each article on AccountingProfessor.org is hand-edited for several dimensions by Benjamin Wann . My site utilizes a unique process that leverages AI and human subject matter expertise to create the best content possible.
For more great content, checkout my YouTube channel!
- Accounting Career (85)
- Accounting Defined (110)
- Accrual Accounting (2)
- Activity Based Costing (6)
- Actual Costing (21)
- All Posts (1)
- Artificial Intelligence (AI) (16)
- Best Practices; staying in business (5)
- Bookkeeping (52)
- Books To Read (10)
- Budgeting (15)
- Business Advice (4)
- Business Aquisition (3)
- Business Brokerage (6)
- Business Partnering (4)
- Business Processes (1)
- Business Strategy (11)
- Buying a Business (26)
- Canadian Manufacturing (11)
- Consulting (3)
- Controller (35)
- Cost Accounting (102)
- Cost Reduction (2)
- Culture (4)
- Depreciation (3)
- Globalization (3)
- Intelligent Costing (2)
- Inventory Accounting (46)
- Investing (3)
- Leadership (71)
- Management Accounting (10)
- Manufacturing Advantages (4)
- Manufacturing Challenges (20)
- Manufacturing Cooperation (3)
- Manufacturing Digitization (10)
- Manufacturing Excellence (97)
- Manufacturing Systems (6)
- Manufacturing Trade Agreements (1)
- Networking (2)
- Office Fun (3)
- Overhead Allocation (8)
- Process Improvement (19)
- Product Cost (2)
- Public Accounting (7)
- Questions To Ask (47)
- Quotes Explained (5)
- Recommended Solutions (1)
- Risk Analysis (6)
- Selling a Business (34)
- Small Business Advice & Insights (91)
- Small Business Tips (10)
- Smb Defined (1)
- Software (2)
- Standard Cost (75)
- Strategy Execution (66)
- Supply Chain (13)
- Teamwork (2)
- Technological advances (3)
- Uncategorized (1)
- Working Capital (3)
- Writing Strengths (1)
Meet The Author
Related Posts

Service-Based Inventory Models: Accounting Methods for Hybrid Product-Service Offerings Where Inventory Components Are Part of Ongoing Service Delivery
In today’s business landscape, the lines between products and services are increasingly blurred. Many organizations have adopted hybrid offerings that seamlessly integrate physical goods and

AI-Driven Inventory Obsolescence Prediction: Leveraging Machine Learning for More Accurate Inventory Write-Down and Obsolescence Forecasting
In today’s dynamic and competitive business landscape, effective inventory management has become a critical priority for organizations across various industries. One of the significant challenges

Inventory Accounting for Perishable Goods in the Last-Mile Economy: Addressing Valuation Challenges for Time-Sensitive Inventory in Rapid Delivery Models
The rise of e-commerce and the growing demand for fast, convenient delivery have given birth to the last-mile economy, where businesses compete to deliver products
Subscribe to discover my secrets to success. Get 3 valuable downloads, free exclusive tips, offers, and discounts that we only share with my email subscribers.
Social media.

Quick links
- Terms of Service
Other Pages
Contact indo.
- 302-981-1733
- [email protected]
© Accounting Professor 2023. All rights reserved
Discover more from accounting professor.org.
Subscribe now to keep reading and get access to the full archive.
Type your email…
Continue reading
All Subjects
Managerial Accounting
Study guides for every class, that actually explain what's on your next test, cost assignment, from class:.
Cost assignment is the process of allocating costs to specific cost objects, such as products, services, or activities, based on the consumption or usage of resources. It is a fundamental concept in managerial accounting that is crucial for understanding and managing costs in organizations, particularly in the context of job order costing and process costing.
congrats on reading the definition of Cost Assignment . now let's actually learn it.
5 Must Know Facts For Your Next Test
- Cost assignment is a critical step in both job order costing and process costing, as it determines the total cost of a specific product or service.
- In job order costing, costs are assigned to individual jobs or batches based on the specific resources consumed, while in process costing, costs are assigned to production departments or processes.
- The choice of cost assignment method can significantly impact the reported costs and profitability of a product or service, making it an important consideration in managerial decision-making.
- Accurate cost assignment is essential for pricing decisions, performance evaluation, and cost control, as it provides managers with a clear understanding of the costs associated with different products or services.
- The use of cost drivers, such as direct labor hours or machine hours, is a common approach to allocating indirect costs to cost objects in both job order costing and process costing.
Review Questions
- In job order costing, cost assignment involves directly tracing the materials, labor, and overhead costs to individual jobs or batches based on the specific resources consumed. This allows for the calculation of the total cost of each unique job or batch. In process costing, cost assignment involves allocating costs to production departments or processes based on the resources consumed within each stage of the production process. This enables the calculation of the average cost per unit produced within a given time period.
- Accurate cost assignment is crucial for making informed managerial decisions, such as pricing, product mix, and resource allocation. Inaccurate cost assignment can lead to mispricing, poor performance evaluation, and suboptimal decision-making. By understanding the true costs associated with different products or services, managers can make more informed decisions that maximize profitability and efficiency. Additionally, cost assignment data is essential for cost control and continuous improvement efforts, as it provides insights into the drivers of costs and opportunities for cost reduction.
- The choice of cost assignment method, such as the use of direct costs versus indirect cost allocation, can significantly impact the reported costs and profitability of a product or service. For example, if a company underestimates the indirect costs associated with a particular product, it may price that product too low, leading to lower reported profitability. Conversely, if a company overestimates the indirect costs associated with a product, it may price that product too high, potentially making it less competitive in the market. The choice of cost assignment method, including the selection of appropriate cost drivers, can have far-reaching implications for a company's financial performance and strategic decision-making.
Related terms
Costs that can be directly traced to a specific cost object, such as the materials and labor used to manufacture a product.
Costs that cannot be directly traced to a specific cost object and are typically allocated using a cost driver, such as overhead expenses.
The process of assigning indirect costs to cost objects using a reasonable basis, such as a cost driver.
" Cost Assignment " also found in:
Subjects ( 2 ).
- Cost Accounting
- Strategic Cost Management
© 2024 Fiveable Inc. All rights reserved.
Ap® and sat® are trademarks registered by the college board, which is not affiliated with, and does not endorse this website..
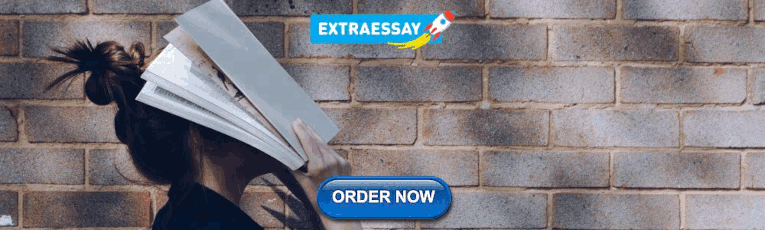
IMAGES
VIDEO
COMMENTS
What is Cost Assignment? Cost assignment is the allocation of costs to the activities or objects that triggered the incurrence of the costs. The concept is heavily used in activity-based costing, where overhead costs are traced back to the actions causing the overhead to be incurred. The cost assignment is based on one or more cost drivers.. Cost assignments are associated with direct costs ...
Cost Assignment. Cost assignment is the process of associating costs with cost objects, such as products, services, departments, or projects. It encompasses the identification, measurement, and allocation of both direct and indirect costs to ensure a comprehensive understanding of the resources consumed by various cost objects within an organization.
Cost Allocation or cost assignment is the process of identifying and assigning costs to the various cost objects. These cost objects could be those for which the company needs to find out the cost separately. A few examples of cost objects can be a product, customer, project, department, and so on. The need for cost allocation arises because ...
An activity-based costing system (also known as ABC System) is a two-stage procedure for assigning overhead costs to products, which focuses on the major activities performed in the production process. Activity-based costing is a costing method that identifies activities in an organization and assigns the cost of each activity to all products ...
Cost assignment is a management accounting process in a manufacturing setting that allocates costs across products, services, and departments. The process is essential in determining the profitability of each product, guiding pricing strategies, and identifying efficiency improvements. ... Levels of Sophistication in Cost Systems. Cost systems ...
Cost allocation is the process of identifying, accumulating, and assigning costs to costs objects such as departments, products, programs, or a branch of a company. It involves identifying the cost objects in a company, identifying the costs incurred by the cost objects, and then assigning the costs to the cost objects based on specific criteria.
Cost Accumulation is the process of collecting all costs information about the business with the help of the cost accounting system. It is a process of collection of all relevant data regarding the various costs incurred by the company at various stages of production. ... Cost Assignment is mainly useful for an activity-based costing method ...
Activity-based costing (ABC) is a method of assigning overhead and indirect costs—such as salaries and utilities—to products and services. This system of cost accounting is based on ...
Cost Accounting System vs. Financial Accounting System. The two systems of accounting: ... By examining cost assignments under different scenarios, businesses can make better decisions on how to allocate resources. Overall, activity-based costing is a more complex and accurate system than traditional cost analysis methods. It provides valuable ...
Cost assignment is the process of allocating costs to specific cost objects, such as products, services, or activities, based on the consumption or usage of resources. It is a fundamental concept in managerial accounting that is crucial for understanding and managing costs in organizations, particularly in the context of job order costing and process costing.