Information
- Author Services
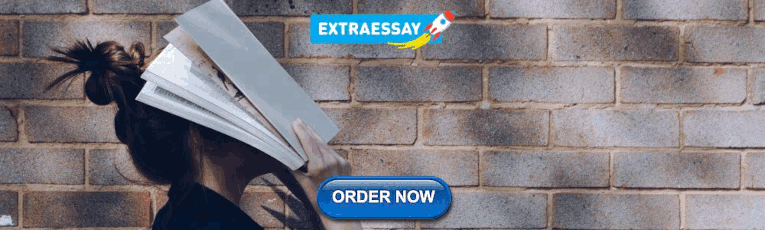
Initiatives
You are accessing a machine-readable page. In order to be human-readable, please install an RSS reader.
All articles published by MDPI are made immediately available worldwide under an open access license. No special permission is required to reuse all or part of the article published by MDPI, including figures and tables. For articles published under an open access Creative Common CC BY license, any part of the article may be reused without permission provided that the original article is clearly cited. For more information, please refer to https://www.mdpi.com/openaccess .
Feature papers represent the most advanced research with significant potential for high impact in the field. A Feature Paper should be a substantial original Article that involves several techniques or approaches, provides an outlook for future research directions and describes possible research applications.
Feature papers are submitted upon individual invitation or recommendation by the scientific editors and must receive positive feedback from the reviewers.
Editor’s Choice articles are based on recommendations by the scientific editors of MDPI journals from around the world. Editors select a small number of articles recently published in the journal that they believe will be particularly interesting to readers, or important in the respective research area. The aim is to provide a snapshot of some of the most exciting work published in the various research areas of the journal.
Original Submission Date Received: .
- Active Journals
- Find a Journal
- Proceedings Series
- For Authors
- For Reviewers
- For Editors
- For Librarians
- For Publishers
- For Societies
- For Conference Organizers
- Open Access Policy
- Institutional Open Access Program
- Special Issues Guidelines
- Editorial Process
- Research and Publication Ethics
- Article Processing Charges
- Testimonials
- Preprints.org
- SciProfiles
- Encyclopedia
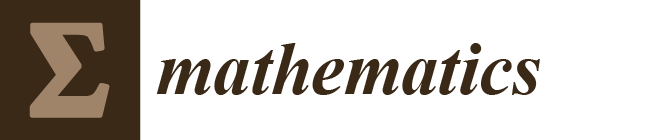
Journal Menu
- Mathematics Home
- Aims & Scope
- Editorial Board
- Reviewer Board
- Topical Advisory Panel
- Instructions for Authors
- Special Issues
- Sections & Collections
- Article Processing Charge
- Indexing & Archiving
- Editor’s Choice Articles
- Most Cited & Viewed
- Journal Statistics
- Journal History
- Journal Awards
- Society Collaborations
- Conferences
- Editorial Office
Journal Browser
- arrow_forward_ios Forthcoming issue arrow_forward_ios Current issue
- Vol. 12 (2024)
- Vol. 11 (2023)
- Vol. 10 (2022)
- Vol. 9 (2021)
- Vol. 8 (2020)
- Vol. 7 (2019)
- Vol. 6 (2018)
- Vol. 5 (2017)
- Vol. 4 (2016)
- Vol. 3 (2015)
- Vol. 2 (2014)
- Vol. 1 (2013)
Find support for a specific problem in the support section of our website.
Please let us know what you think of our products and services.
Visit our dedicated information section to learn more about MDPI.
Recent Advances in Finite Element Methods with Applications
- Print Special Issue Flyer
- Special Issue Editors
Special Issue Information
- Published Papers
A special issue of Mathematics (ISSN 2227-7390). This special issue belongs to the section " Engineering Mathematics ".
Deadline for manuscript submissions: 15 September 2024 | Viewed by 7687
Share This Special Issue
Special issue editor.

Dear Colleagues,
The finite element method is an important tool used in applied sciences. In close association with computational mechanics, it has been increasingly applied across various fields, such as engineering, material sciences, environmental sciences, medicine, biology, as well as physics and chemistry, and so forth. The finite element method also motivates extensive research on mathematics, providing specific structures for the firm theoretical foundation.
This Special Issue, entitled “Recent Advances in Finite Element Methods with Applications”, aims to collect recent advances in the construction, theoretical analysis, implementation, and application of finite element methods. We invite investigators to contribute high-quality original research articles as well as review articles on recent advances in the following methods:
- finite element algorithms and mathematical theories for both classical and new model problems;
- applications of the method for real world problems, either on a specific problem or about the trend of a whole area, where finite element methods are used as research tools or as conceptual foundations;
- developments and principles of finite element software packages and platforms, as well as new techniques for a mid-way step, such as mesh generation.
Potential topics include, but are not limited to, Navier–Stokes equations, Magnetohydrodynamic equations, Boussinesq equations, Einstein equation, large deformation elasticity, computational biomechanics and biomathematics, medical engineering, mathematical theories of finite element methods, the interplay of finite element methods and machine learning, and so forth. The Special Issue is open to all kinds of finite element methods, and to advanced implementation approaches of the methods.
Dr. Shuo Zhang Guest Editor
Manuscripts should be submitted online at www.mdpi.com by registering and logging in to this website . Once you are registered, click here to go to the submission form . Manuscripts can be submitted until the deadline. All submissions that pass pre-check are peer-reviewed. Accepted papers will be published continuously in the journal (as soon as accepted) and will be listed together on the special issue website. Research articles, review articles as well as short communications are invited. For planned papers, a title and short abstract (about 100 words) can be sent to the Editorial Office for announcement on this website.
Submitted manuscripts should not have been published previously, nor be under consideration for publication elsewhere (except conference proceedings papers). All manuscripts are thoroughly refereed through a single-blind peer-review process. A guide for authors and other relevant information for submission of manuscripts is available on the Instructions for Authors page. Mathematics is an international peer-reviewed open access semimonthly journal published by MDPI.
Please visit the Instructions for Authors page before submitting a manuscript. The Article Processing Charge (APC) for publication in this open access journal is 2600 CHF (Swiss Francs). Submitted papers should be well formatted and use good English. Authors may use MDPI's English editing service prior to publication or during author revisions.
- Finite element methods
- Mixed finite element methods
- Spectral element method
- Discontinuous Galerkin methods
- Grid methods
- Meshfree methods
- Loubignac iteration
- Virtual element method
- Navier–Stokes equations
- Magnetohydrodynamic equations
- Boussinesq equations
- Large deformation elasticity
- Algorithms of FEM
- Applications of FEM
- Machine learning
- Implementation techniques of FEM
- Computational physics, chemistry and mechanics
- Computational biomechanics and biomathematics
- Material modeling
- Computational applied sciences
Published Papers (6 papers)
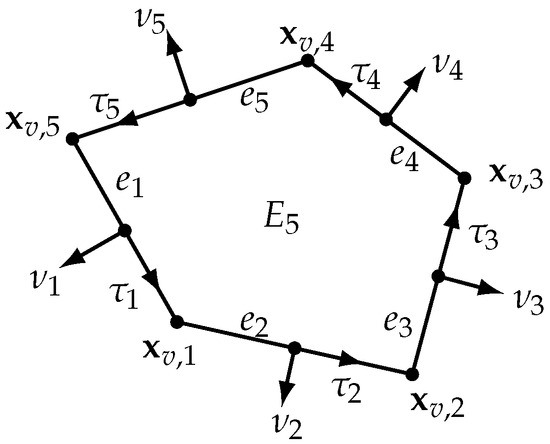
Further Information
Mdpi initiatives, follow mdpi.
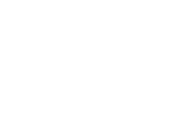
Subscribe to receive issue release notifications and newsletters from MDPI journals
finite element method Recently Published Documents
Total documents.
- Latest Documents
- Most Cited Documents
- Contributed Authors
- Related Sources
- Related Keywords
A reduced-order characteristic finite element method based on POD for optimal control problem governed by convection–diffusion equation
An infinite tube approach for the efficient modelling of collapse using the finite element method, a condensed generalized finite element method (cgfem) for interface problems, an extended finite element method implementation in comsol multiphysics: solid mechanics, uncertainty analysis in solid mechanics with uniform and triangular distributions using stochastic perturbation-based finite element method, convergence and supercloseness of a finite element method for a two-parameter singularly perturbed problem on shishkin triangular mesh, a c1 finite element method for axisymmetric lipid membranes in the presence of the gaussian energy, the optimal order convergence for the lowest order mixed finite element method of the biharmonic eigenvalue problem, a stabilizer-free weak galerkin finite element method for the stokes equations, local h1-norm error analysis of a mixed finite element method for a time-fractional biharmonic equation, export citation format, share document.
Help | Advanced Search
Mathematics > Numerical Analysis
Title: high-performance matrix-free unfitted finite element operator evaluation.
Abstract: Unfitted finite element methods, like CutFEM, have traditionally been implemented in a matrix-based fashion, where a sparse matrix is assembled and later applied to vectors while solving the resulting linear system. With the goal of increasing performance and enabling algorithms with polynomial spaces of higher degrees, this contribution chooses a more abstract approach by matrix-free evaluation of the operator action on vectors instead. The proposed method loops over cells and locally evaluates the cell, face, and interface integrals, including the contributions from cut cells and the different means of stabilization. The main challenge is the efficient numerical evaluation of terms in the weak form with unstructured quadrature points arising from the unfitted discretization in cells cut by the interface. We present design choices and performance optimizations for tensor-product elements and demonstrate the performance by means of benchmarks and application examples. We demonstrate a speedup of more than one order of magnitude for the operator evaluation of a discontinuous Galerkin discretization with polynomial degree three compared to a sparse matrix-vector product and develop performance models to quantify the performance properties over a wide range of polynomial degrees.
Submission history
Access paper:.
- Other Formats
Ancillary files ( details ) :
- ex_supplement.pdf
References & Citations
- Google Scholar
- Semantic Scholar
BibTeX formatted citation

Bibliographic and Citation Tools
Code, data and media associated with this article, recommenders and search tools.
- Institution
arXivLabs: experimental projects with community collaborators
arXivLabs is a framework that allows collaborators to develop and share new arXiv features directly on our website.
Both individuals and organizations that work with arXivLabs have embraced and accepted our values of openness, community, excellence, and user data privacy. arXiv is committed to these values and only works with partners that adhere to them.
Have an idea for a project that will add value for arXiv's community? Learn more about arXivLabs .
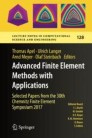
Advanced Finite Element Methods with Applications
Selected Papers from the 30th Chemnitz Finite Element Symposium 2017
- © 2019
- Thomas Apel 0 ,
- Ulrich Langer 1 ,
- Arnd Meyer 2 ,
- Olaf Steinbach 3
Institut für Mathematik & Computergestützte Simulation, Universität der Bundeswehr München, Neubiberg, Germany
You can also search for this editor in PubMed Google Scholar
Institute for Computational Mathematics, Johannes Kepler University Linz, Linz, Austria
Fakultät für mathematik, tu chemnitz, chemnitz, germany, institut für angewandte mathematik, technische universität graz, graz, austria.
- Features overview papers and original research articles from participants of the 30th Chemnitz Finite Element Symposium
- The Symposium itself already has a 40-year tradition
- Offers readers insights into the latest results
Part of the book series: Lecture Notes in Computational Science and Engineering (LNCSE, volume 128)
Included in the following conference series:
- FEM: Chemnitz Fine Element Symposium
Conference proceedings info: FEM 2017.
18k Accesses
39 Citations
This is a preview of subscription content, log in via an institution to check access.
Access this book
- Available as EPUB and PDF
- Read on any device
- Instant download
- Own it forever
- Compact, lightweight edition
- Dispatched in 3 to 5 business days
- Free shipping worldwide - see info
- Durable hardcover edition
Tax calculation will be finalised at checkout
Other ways to access
Licence this eBook for your library
Institutional subscriptions
Table of contents (19 chapters)
Front matter, superconvergent graded meshes for an elliptic dirichlet control problem.
- Thomas Apel, Mariano Mateos, Johannes Pfefferer, Arnd Rösch
Explicit and Implicit Reconstructions of the Potential in Dual Mixed hp -Finite Element Methods
- Lothar Banz, Jan Petsche, Andreas Schröder
Two Stabilized Three-Field Formulations for the Biharmonic Problem
Analysis of the hp -version of a first order system least squares method for the helmholtz equation.
- Maximilian Bernkopf, Jens Markus Melenk
Numerical Study of Goal-Oriented Error Control for Stabilized Finite Element Methods
- Marius Paul Bruchhäuser, Kristina Schwegler, Markus Bause
Uniform Exponential Stability of Galerkin Approximations for a Damped Wave System
- Herbert Egger, Thomas Kugler
Adaptive Algorithm Based on Functional-Type A Posteriori Error Estimate for Reissner-Mindlin Plates
- Maxim Frolov, Olga Chistiakova
Wavelet Boundary Element Methods: Adaptivity and Goal-Oriented Error Estimation
- Helmut Harbrecht, Manuela Moor
Comparison Analysis of Two Numerical Methods for Fractional Diffusion Problems Based on the Best Rational Approximations of t γ on [0, 1]
- Stanislav Harizanov, Raytcho Lazarov, Svetozar Margenov, Pencho Marinov, Joseph Pasciak
A Three-Level Extension of the GDSW Overlapping Schwarz Preconditioner in Two Dimensions
- Alexander Heinlein, Axel Klawonn, Oliver Rheinbach, Friederike Röver
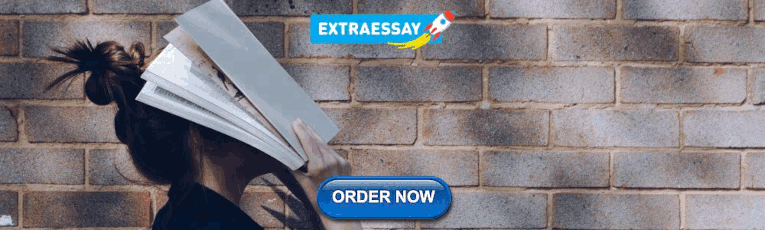
A Parallel Multigrid Solver for Multi-Patch Isogeometric Analysis
- Christoph Hofer, Stefan Takacs
On a Renewed Approach to A Posteriori Error Bounds for Approximate Solutions of Reaction-Diffusion Equations
- Vadim G. Korneev
Space-Time Finite Element Methods for Parabolic Evolution Problems with Variable Coefficients
- Ulrich Langer, Martin Neumüller, Andreas Schafelner
ACA Improvement by Surface Segmentation
- Sergej Rjasanow, Steffen Weißer
First Order Error Correction for Trimmed Quadrature in Isogeometric Analysis
- Felix Scholz, Angelos Mantzaflaris, Bert Jüttler
A Space–Time Finite Element Method for the Linear Bidomain Equations
- Olaf Steinbach, Huidong Yang
A Stabilized Space–Time Finite Element Method for the Wave Equation
- Olaf Steinbach, Marco Zank
An Optimal Order CG-DG Space-Time Discretization Method for Parabolic Problems
- Igor Voulis
A Framework for Efficient Hierarchic Plate and Shell Elements
- Michael Weise
- Finite element methods
- Isogeometric analysis
- Parallel implementation
- Fast solvers
- Fractional derivatives
- Computational mechanics
About this book
Finite element methods are the most popular methods for solving partial differential equations numerically, and despite having a history of more than 50 years, there is still active research on their analysis, application and extension. This book features overview papers and original research articles from participants of the 30th Chemnitz Finite Element Symposium, which itself has a 40-year history. Covering topics including numerical methods for equations with fractional partial derivatives; isogeometric analysis and other novel discretization methods, like space-time finite elements and boundary elements; analysis of a posteriori error estimates and adaptive methods; enhancement of efficient solvers of the resulting systems of equations, discretization methods for partial differential equations on surfaces; and methods adapted to applications in solid and fluid mechanics, it offers readers insights into the latest results.
Editors and Affiliations
Institut für mathematik & computergestützte simulation, universität der bundeswehr münchen, neubiberg, germany.
Thomas Apel
Ulrich Langer
Olaf Steinbach
Bibliographic Information
Book Title : Advanced Finite Element Methods with Applications
Book Subtitle : Selected Papers from the 30th Chemnitz Finite Element Symposium 2017
Editors : Thomas Apel, Ulrich Langer, Arnd Meyer, Olaf Steinbach
Series Title : Lecture Notes in Computational Science and Engineering
DOI : https://doi.org/10.1007/978-3-030-14244-5
Publisher : Springer Cham
eBook Packages : Mathematics and Statistics , Mathematics and Statistics (R0)
Copyright Information : Springer Nature Switzerland AG 2019
Hardcover ISBN : 978-3-030-14243-8 Published: 29 June 2019
Softcover ISBN : 978-3-030-14246-9 Published: 14 August 2020
eBook ISBN : 978-3-030-14244-5 Published: 28 June 2019
Series ISSN : 1439-7358
Series E-ISSN : 2197-7100
Edition Number : 1
Number of Pages : XXII, 428
Number of Illustrations : 27 b/w illustrations, 76 illustrations in colour
Topics : Computational Mathematics and Numerical Analysis , Theoretical, Mathematical and Computational Physics , Mathematical and Computational Engineering
- Publish with us
Policies and ethics
- Find a journal
- Track your research
Academia.edu no longer supports Internet Explorer.
To browse Academia.edu and the wider internet faster and more securely, please take a few seconds to upgrade your browser .
- We're Hiring!
- Help Center
Finite Element Methods
- Most Cited Papers
- Most Downloaded Papers
- Newest Papers
- Save to Library
- Last »
- Computational Mechanics Follow Following
- Finite Element Analysis (Engineering) Follow Following
- Mechanical Engineering Follow Following
- Fracture Mechanics Follow Following
- Structural Engineering Follow Following
- Earthquake Engineering Follow Following
- Structural Dynamics Follow Following
- Composite Materials and Structures Follow Following
- Biomechanics Follow Following
- Finite Element Simulations Follow Following
Enter the email address you signed up with and we'll email you a reset link.
- Academia.edu Publishing
- We're Hiring!
- Help Center
- Find new research papers in:
- Health Sciences
- Earth Sciences
- Cognitive Science
- Mathematics
- Computer Science
- Academia ©2024
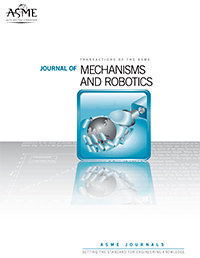
- Previous Article
- Next Article
1 Introduction
2 dynamic model of flexible continuum manipulator, 3 experimental setup of tendon-driven flexible continuum manipulator, 4 model validation results and discussion, 5 conclusions, acknowledgment, conflict of interest, data availability statement, nomenclature, appendix a: derivation of shape functions, appendix b: global assembled mass matrix, finite element method-based dynamic modeling framework for flexible continuum manipulators.
Contributed by Mechanisms and Robotics Committee of ASME for publication in the J ournal of M echanisms and R obotics .
- Split-Screen
- Article contents
- Figures & tables
- Supplementary Data
- Peer Review
- Open the PDF for in another window
- Cite Icon Cite
- Permissions
- Search Site
Modassir Firdaus, M., Dilip Paranjape, O., and Vadali, M. (March 5, 2024). "Finite Element Method-Based Dynamic Modeling Framework for Flexible Continuum Manipulators." ASME. J. Mechanisms Robotics . October 2024; 16(10): 101013. https://doi.org/10.1115/1.4064669
Download citation file:
- Ris (Zotero)
- Reference Manager
Flexible continuum manipulators (FCMs) are gaining importance because of their maneuverability and pliability in confined and complex spaces, where rigid link manipulators underperform. However, the dynamic behavior and control of the FCM are quite challenging due to its complex nonlinear behavior. In this study, a finite element-based dynamic model framework is derived that accounts for the geometric nonlinearities and inertial effects. An experimental setup of tendon-driven FCM, consisting of a flexible backbone, is developed to validate the model. The modal analysis of the model is in agreement with the analytical solutions, with less than 10% error. The model is also validated for various loading conditions on the tip-actuated tendon-driven FCM. The steady-state tip position predictions are within 15 % of the ground truth.

For a substantial period of time, the advancements in manipulator design have been centrally focused on the replication of human-like motion. Rigid-linked manipulators exhibit satisfactory performance characteristics, such as accuracy and payload capacity, in open environments. However, their limitations become apparent in scenarios requiring maneuverability in confined and complex spaces, such as minimally invasive surgical procedures [ 1 – 4 ] and inspections of inaccessible areas [ 5 ]. In these applications, flexible continuum manipulators (FCMs) are advantageous. Flexible manipulator designs involve several rigid links interconnected with actuatable joints, hence are also called discrete manipulators [ 6 ]. However, flexible continuum manipulators, sometimes referred to as continuum manipulators, don’t consist of rigid links with discrete joints. Rather, they bend continuously along the length [ 7 ].
Multiple designs of continuum manipulators have been proposed in the literature. Some of them have co-axially sliding pre-curved flexible backbones [ 8 – 10 ], while others use pneumatically actuated soft materials for manipulation [ 11 , 12 ]. Some more recent designs have a flexible backbone with actuated tendons [ 13 – 15 ]. In this study, a flexible backbone-based tendon-driven continuum manipulator is used. A set of tendons runs parallel to the axial direction of the tendon-driven FCM backbone through multiple intermediate disks. The kinematics of such an FCM is closely related to the bending behavior of the backbone [ 16 ]. Furthermore, the dynamics are accompanied by mass, stiffness, and damping of the material used as the backbone [ 17 ].
Most kinematic models assume constant curvature and approximate the robot’s shape with a series of mutually tangent circular arcs, defined by three essential parameters: radius of curvature, arc angle, and bending plane [ 2 , 15 , 18 – 21 ]. However, under extreme loading conditions, the constant curvature assumption is not applicable and requires variable curvature kinematic frameworks in tandem with elasticity theories tailored for slender objects, as extensively examined in previous investigations [ 22 ]. The prevailing methodology for dynamic modeling has centered around the classical Bernoulli–Euler beam theory, notable for its assumption of small deflections. Some have turned to the planar large-deflection Bernoulli–Euler elastica theory for manipulators exhibiting substantial deflections [ 17 , 23 ]. Some others have used more complex Cosserat rod theory in pursuit of precision, accuracy, and using closed-form solutions from these theories [ 24 , 25 ]. However, in scenarios with multiple loading conditions and large deflections introducing geometric nonlinearities, such as a tendon-drive FCM, these methods lead to multiple solutions or unsolvable governing equations. Godage et al. [ 26 ] introduced a lumped parameter analysis for the dynamics of FCMs, although it doesn’t account for geometric nonlinearities. Rone et al. devised a dynamic model grounded in the virtual power principle, circumventing inertial effects [ 27 , 28 ]. This model falls between high-fidelity finite element method (FEM) models and computationally economical lumped parameter models. Xu and Simaan [ 29 ] presented a static behavior analysis of continuum robots with multiple flexible backbones, utilizing elliptical integrals with geometric compatibility and static equilibrium constraints. Ehsani-Seresht and Hashemi-Pour Moosavi formulated a dynamic model using the Euler–Lagrange approach for an extensible, flexible backbone continuum robot, incorporating external forces and cable friction [ 30 ]. These models do not account for large deflections or geometric nonlinearities, resulting in less precise control of the tip. Further, most of these do not provide a comprehensive framework to handle the complex loading interactions between the FCM and tendons.
In this paper, an FEM-based framework for tendon-driven FCM is discussed that accounts for geometric nonlinearities and inertial effects of the FCM to predict its behavior. Geometric nonlinearities significantly affect the stiffness matrix of FCM under large deflection. Therefore, when the model does not account for geometric nonlinearities, it cannot accurately represent the deflection [ 31 ]. The dynamics of FCMs share similarities with drill strings used in directional drilling [ 32 ], as both are slender and akin to Euler–Bernoulli beams. Employing the virtual work principle, Feng et al. [ 33 ] developed an FEM-based six degrees-of-freedom (DOF) dynamic model to elucidate large displacement of drill strings. A strategy similar to Feng et al. [ 33 ] is employed in this work. The dynamic model of the FCM is derived using the virtual work principle. Free vibration analysis is done for modal validation. FEM-based natural frequencies are compared with analytical frequencies. In addition, the modulus of elasticity of the backbone material of FCM is identified. The damping of FCM is approximated as a lumped damping model. The equations of motion (EOM), a set of second-order ordinary differential equations (ODEs), are suitable for the control design for the FCM. The model is computationally efficient as it only deals with ODEs; thus, it may be useful in designing the observer in real-time to control tendon-driven FCM. An experimental validation of tendon-driven planar FCM is developed to validate the model.
The remainder of the paper is organized as follows: Sec. 2 provides a detailed formulation of the model. In Sec. 3 , we explain the experimental setup used for parameter estimation and validation of the FEM dynamic model. Section 4 presents a comparison of FEM-based modes with analytical modes and experimental validation. Finally, concluding remarks on the research are provided in Sec. 5 .
This section presents the dynamic model of tendon-drive FCM. The approach is based on the FEM for its ability to reasonably approximate the analytical solutions of a higher-order differential equation. Furthermore, it facilitates the application of comprehensive and realistic external boundary conditions and enables control design. The dynamic behavior of FCM is dominated by axial and bending deformations under loading conditions. Therefore, shear and torsion deformations are not significant compared to axial and bending deformations [ 34 ]. In this case, a one-dimensional discretization is a suitable choice [ 35 ]. Therefore, FCM is discretized in the axial direction, with each discrete element having six degrees-of-freedom. The principle of virtual work is applied to derive the elemental dynamic equations. Subsequently, the dynamic equations in local coordinates are transformed to the global coordinates using Rodrigues rotation formula [ 36 ]. The model developed for FCM is verified by performing free vibration analysis. The FEM-based natural frequencies are obtained and compared with analytical solutions to verify the mass and stiffness matrix. The schematic of FCM is shown in Fig. 1 , which consists of a flexible backbone with one end rigidly attached and the other one a disk with two actuating tendons. When the tension is applied to the tendons, FCM goes under a bent state.

Schematic of an FCM that has a natural state with equal tension in the tendons, a bent state due to the difference in the tension
2.1 Discretization of Flexible Continuum Manipulator.

Finite element discretization of the FCM
2.2 Equations of Motion in Local Coordinates Frame.
2.3 transformation of equations of motion from local to global coordinates..
A simple experimental setup is built to validate the FEM dynamic model. A schematic of the experimental setup is shown in Fig. 3 . The setup consists of a single-disk tendon-driven FCM (Sec. 3.1 ), sensors, an actuator, a real-time controller, and data acquisition (DAQ) as the main components. These are integrated into a single system using aluminum extrusions and a mechanical breadboard, as shown in Fig. 4 . Initially, the FCM is in its natural state, as shown in Fig. 1 . As the actuator rotates, one of the tendons is pulled while the other loosens, thus bending the backbone. The bending increases as the tension increases. The tension is recorded through the load cells mounted on the tendons, as shown in Fig. 3 .

Schematic of the single-disk tendon-driven planar FCM

Experimental setup of tendon-driven FCM: ( a ) front view, ( b ) a magnified view of the backbone with markers, ( c ) a rear view with motor, and ( d ) control hardware and DAQ
3.1 Design of Single-Disk Tendon-Driven Flexible Continuum Manipulator.
A single-disk FCM with a nylon-66 rod of radius “ r ” 3.25 (mm) and length “ L ” 300 (mm) is used as the backbone. The density of nylon 66 is 1030 kg / m 3 , and the Poisson’s ratio is 0.4. A disk of diameter “ D d ” is rigidly connected to the tip of the backbone. Two steel actuating tendons with a diameter of 0.7 mm are crimped diametrically opposite to the disk. The attachment points of the tendons are on a circle of diameter “ D p ” 2.5 (mm) (pitch circle diameter) shown in Fig. 3 . Other ends of the tendons are connected to the driving pulley of the motor (Fig. 4(d) ). These tendons are routed from front to back of the setup through pulleys mounted on the top of the aluminum frame as in Fig. 4(c) . One end of the FCM is fixed with the structure of the experimental setup, and a load is applied on the other through the actuating tendons.
Tension in the actuating tendons, generated using a Nema-23 (120 kg-cm) hybrid servo motor, provides a bending moment at the free end of the FCM. The tension is measured using Futek LCM 300 load cells mounted on each actuating tendon, as shown in Fig. 4 . The measurements are logged using NI9637 and connected to a real-time controller (SbRio 9629), which also controls the rotation angle of the motor. An accelerometer (Dytran-3055D5) is mounted at the free end to measure the acceleration of the tip. Visual markers at equal distances along the backbone provide ground truth position information through a Kinect vision sensor. The Kinect is mounted in front of the backbone as shown in Fig. 4(a) .
3.2 Estimation of Modulus of Elasticity.
Accurate material properties of the backbone are needed to compute the mass and stiffness matrices. Among these, the modulus of elasticity is vital as it can significantly impact the model predictions. The modulus of elasticity of nylon-66 is highly uncertain and varies from 0.210 GPa to 3.77 GPa [ 38 ] depending on the manufacturing quality. Thus, it needs to be estimated for the specific backbone used in the current setup. Simple free vibration experiments are conducted to estimate the transverse natural frequency of the backbone. A miniature-size accelerometer (Dytran 3225F7) is mounted on the free end, and the other end is fixed, as shown in Fig. 5 . Figure 6 shows the response of tip acceleration when it is released from an initial condition. The fast Fourier transformation (FFT) of acceleration response is shown in Fig. 7 . The peak of Fig. 7 is the transverse fundamental frequency and is estimated to be 54.7 rad/s over ten experiments. A modulus of elasticity of 0.7 GPa resulted in a transverse fundamental frequency of 54.56 rad/s from the FEM dynamic model.

Setup for estimation of modulus of elasticity

Zero input acceleration of the tip

FFT spectrum of acceleration in Fig. 6
3.3 Estimation of Damping.
Rayleigh’s damping model is one of the most popular methods to estimate the damping of various systems as a function of the mass and stiffness matrices. However, it requires the identification of at least two harmonics of the system. However, only the first fundamental frequency was observed for the current setup, as can be seen from the earlier experiments in Figs. 6 and 7 . Therefore, a lumped damping model is an alternative method used in the current work.
In this model, the entire tendon-driven FCM, including the sensors, is considered a single mass-spring-damper system. The backbone is assumed to be made up of a single material and is considered isotropic; thus, stiffness and damping are assumed to be invariant with direction. Let m e q v be the total mass of the system, k e q v be the total stiffness, and C e q v be the total damping. The tip acceleration in the transverse direction under impulse response is shown in Fig. 8 . The acceleration response is exponentially decaying, similar to the second-order response of a simple spring-mass-damper system [ 39 ]. The exponentially decaying curve fitting to the peak of acceleration response, as shown in Fig. 8 , provides the value of the damping ratio of the lumped spring-mass-damper system. FFT of acceleration gives the natural frequencies of the FCM. Figure 9 clearly shows a single peak, meaning the first natural frequency at 5.7 Hz. The value of fundamental natural frequency ω and damping ratio ζ is calculated for nine different experiments and tabulated in Table 1 . The average value of damping ratio ζ a v g = 0.114 Ns / m results in equivalent damping of C e q v = 0.1506 Ns / m . This is used to estimate the damping matrix [ C ] in Eq. (15) .

Tip acceleration for an impulse excitation used to estimate the damping ratio of FCM

FFT spectrum of acceleration of FCM in Fig. 8
Estimation of fundamental frequency and damping ratio
- The damping coefficient of each element is equal because all elements are dimensionally equivalent. c i = c e ; i = 1 , 2 , … . n where n is the number of elements.
- The damping coefficient of an element is the same for all DOF and decoupled. The damping matrix of an element will have only diagonal elements and given by c x = c y = c z = c θ x = c θ y = c θ z = c e [ c e ] = [ c e 0 0 0 0 0 0 c e 0 0 0 0 0 0 c e 0 0 0 0 0 0 c e 0 0 0 0 0 0 c e 0 0 0 0 0 0 c e ] (16)
- Element damping is proportional to product of C e q v and number of elements given by c e ∝ n C e q v c e = η n C e q v (17) where η is the proportionality constant and is referred to as the correction factor for elemental damping. c e = η L l e C e q v c e = λ L C e q v (18) where λ = η l e is the damping tuning factor. The value of the damping tuning factor λ is iteratively found by comparing the predicted and experimental tip positions under actuation. In the current study, the tip position when one of the actuating tendons touches the backbone during bending is used for iterative estimation of λ . It was found to be 1 for nylon-66.
Finally, the elemental damping matrices from Eq. (17) are transformed and assembled into global damping matrix [ C ] similar to mass and stiffness matrices.
The model is validated in two phases. First, modal analysis is carried out to compare the predicted natural frequencies to the analytical solutions of an Euler–Bernoulli beam. Subsequently, the model is validated against experiments under various loading conditions using the setup discussed in Sec. 3 .
4.1 Modal Analysis.
The natural frequencies of the first three modes in transverse, axial, and torsional directions predicted by the model are compared with the analytical solution based on Euler–Bernoulli beam theory [ 40 ] and are documented in Table 2 . The error between analytical and predictions is less than 10 % . Figure 10 shows the mode shape at the first three natural frequencies. As the backbone cross section is circular and symmetric about the Y and Z axes, the lateral and transverse modes are the same.

First three non-dimensionalized: ( a ) transverse, ( b ) axial, and ( c ) torsional mode shapes
Modal analysis comparisons
4.2 Experimental Validation.
The angular displacement of the motor generates tension in actuating tendons that apply load at the tip of the FCM. For various angular displacements, the positions and tensions are recorded. The tension at the final state of the FCM is considered as steady-state tension. For experimental validation, the steady-state tension is fed as loading at the tip of FCM in Eq. (15) . Predicted tip positions are compared with measured ones.
Figures 11 and 12 , show the initial tendon tension up to the buckling limit of the backbone of the FCM. This tension is defined as pre-tension. The pre-tension is very small since the backbone material has a small buckling limit. The initial pose with 0 deg angular displacement of the driving pulley is the natural state. The thick patch like plot is load cell raw measurements, while the line plot inside the thick patch is the moving average of raw measurements. The tension in the tendon is recorded for several poses (bending) of FCM with different angular displacements of the driving pulley. Initially, the motor provides angular displacement, which causes a change in actuating tendon length. The motor holds at the final rotated angle for some time and returns to the initial angle. Whole measurements of tension are divided into five sections, as shown in Fig. 13 . The first section is the initial neutral state. The second section is the transient state reaching toward a steady-state. The third section is steady-state. The fourth section is the transient state reaching toward the natural state. The fifth section is back to the neutral state. Measurements of RHS and LHS load cells are shown for four different angular displacement inputs by motor Ω = − 15 deg , 15 deg , − 30 deg , and 30 deg in Figs. 13 – 20 .

Tension in RHS tendon in the natural state ( 0 deg angular displacement)

Tension in LHS tendon in the natural state ( 0 deg angular displacement)

Tension in RHS tendon for angular displacement from 0 deg (natural state) to − 15 deg (steady-state) and back to 0 deg

Tension in LHS tendon for angular displacement from 0 deg (natural state) to − 15 deg (steady-state) and back to 0 deg

Tension in RHS tendon for angular displacement from 0 deg (natural state) to 15 deg (steady-state) and back to 0 deg

Tension in LHS tendon for angular displacement from 0 deg (natural state) to 15 deg (steady-state) and back to 0 deg

Tension in RHS tendon for angular displacement from 0 deg (natural state) to − 30 deg (steady-state) and back to 0 deg

Tension in LHS tendon for angular displacement from 0 deg (natural state) to − 30 deg (steady-state) and back to 0 deg

Tension in RHS tendon for angular displacement from 0 deg (natural state) to 30 deg (steady-state) and back to 0 deg

Tension in LHS tendon for angular displacement from 0 deg (natural state) to 30 deg (steady-state) and back to 0 deg
The RHS tendon goes under tension for negative angular displacement of the motor while the LHS tendon slacks. Figures 13 and 14 show the tension in RHS and LHS tendon respectively for 15 deg rotation of the motor. Tension in the RHS tendon increases in a transient state, while in the LHS tendon, it decreases to zero. The LHS tendon goes under tension for the positive angular displacement, while the RHS tendon slakes as in Figs. 15 and 16 . For ± 30 deg rotation of the motor, the tension in RHS and LHS tendons are shown in Figs. 17 – 20 . When the motor rotates ± 30 deg , one of the tendons touches the backbone. This state is considered constrained in this study. Therefore, the maximum angular displacement input is ± 30 deg . Using multiple disks through the length of the FCM will resolve this issue in further studies. The bending of the backbone is directly proportional to the angular displacement of the motor. The coordinates of the markers are recorded using a Kinect Vision Sensor shown in Fig. 4(a) for different bendings of FCM. Three experiments are done to record the tension in actuating tendons for the same motor angular displacement inputs. The average of steady-state tension is shown in Fig. 21 . The coordinates of the tip marker are used for steady-state validation of the proposed FEM dynamic model in the upcoming section. Validation of transient response will be done in upcoming studies.

Steady-state average tension in RHS and LHS tendons for various angular displacements
The tendon tension measured at different angular inputs of the driving motor pulley is fed as input load M θ y and F x in the force vector [ F ] of Eq. (15) to predict the tip coordinate of FCM. The input moment is tendon tension multiplied by disk pitch radius 0.5 D p . Figure 22 shows the predicted response of tendon-driven planar FCM. U T and V T are the X and Y coordinates of the tip of the FCM in the global frame. Experimental values of U T and V T of the tip are recorded for multiple experiments for different driving pulley angular inputs Ω . The average of all experimental values of U T and V T for each Ω is taken as the final experimental value of U T and V T .

Predicted deflection of the backbone under applied tendon tension
Figures 23 and 24 , show the experimental and predicted values of U T and V T respectively. The percentage error between actual and predicted U T and V T is presented in Figs. 25 and 26 . The overall percentage error in U T is within 1 % for different values of Ω . However, there is a significant fluctuation in the percentage error of U T for − 10 deg < Ω < 10 deg compared to other values of Ω . The percentage error in V T is within 15 % for Ω < − 10 deg and Ω > 10 deg . The percentage error in V T for Ω > 10 deg decreases with Ω . The region for − 10 deg < Ω < 10 deg is highly uncertain because of uncertainty in sensor readings and permanent deformation in the backbone. The region for Ω > 10 deg is named a biased region due to initial bending. Since the value of V T is small, that is around or less than ± 10 (mm) shown in Fig. 24 . Therefore, the percentage error in V T fluctuates up to 40 % . For Ω > 10 deg , the percentage error is high due to permanent bending in the backbone of FCM. In an experimental setup, the permanent deformation in the backbone is on the side of negative Ω . Thus the tendon tension (LHS tendon tension) measured for negative Ω is less than that of (RHS tendon tension) for positive Ω . Therefore, the predicted V T is greater than experimental V T as in Fig. 24 for Ω > 10 deg . However, the predicted value of V T converges to the experimental value as Ω increases. Thus, the percentage error of V T decreases from 40 % to 6 % for Ω > 10 deg .

Experimental and predicted tip coordinates along the X -axis in global frame

Experimental and predicted tip coordinates along the Y -axis in global frame

Error in experimental and simulation tip in the global x coordinate

Error in experimental and simulation tip in the global y coordinate
This study presented an FEM-based dynamic model for tendon-driven flexible continuum manipulators. The model, derived using the principle of virtual work, captures the geometric nonlinearities and inertial effects of FCMs. An experimental setup of tendon-driven FCM is designed to validate the model. A detailed discussion estimation of the stiffness and damping matrices is provided. The model is first validated using the modal analysis, wherein the predicted natural frequencies are compared to the analytical natural frequencies. The prediction error was within 10 % of the analytical solution. Subsequently, the model is experimentally validated for the steady-state behavior of the FCM at various actuating tensions. The percentage error in the predicted tip positions under steady-state varied from 1 % to 15 % of the ground truth. The proposed FEM dynamic modal for tendon-driven FCM with the damping modal is a good fit with the actual system. Future studies will focus on validating the FEM dynamic model for transient response and using the model to develop tip position control.
The authors thank and acknowledge the support of the Gujarat Council on Science and Technology for their financial support under Grant No. GUJCOST/2020-21/875. The authors also thank the Indian Institute of Technology Gandhinagar for continuous support. Special thanks to Professor Jayaprakash K R (NOW Lab, Indian Institute of Technology, Gandhinagar) and Professor Shanmuganathan Raman (Associate Professor, Electrical Engineering & Computer Science and Engineering, Indian Institute of Technology, Gandhinagar) for lending measurement equipment. The authors thank Mr. Pushan Pravin Patel, Ms. Kshitija Anam, and Mr. Sresth Tosniwal for helping develop the experimental setup.
There are no conflicts of interest.
No data, models, or code were generated or used for this paper.
radius of the backbone
length of the backbone
displacement vector of any point of an element
damping of single element
internal force in backbone due to initial displacement
internal force developed in the backbone due to subsequent displacement
total internal force developed in the backbone
displacement in the direction of u i -axis
displacement in the direction of v i -axis
displacement in the direction of w i -axis
displacement vector of an element
tip coordinate along the global X direction
tip coordinate along the global Y direction
front disk diameter
pitch circle diameter of the disk
force in the axial direction
force in the transverse direction
force in the lateral direction
bending moment in the Y direction
bending moment in the Z direction
torsion in the X direction
frame attached to the i th node of i th element
global inertial frame
matrix of physical properties of the manipulator
shape function matrix
mass matrix of the manipulator per unit length
elemental mass matrix
elemental stiffness matrix
elemental force vector
global mass matrix of the whole system in the global inertial frame
global stiffness matrix of the whole system in the global inertial frame
global damping matrix of the whole system in the global inertial frame
strain matrix
axial strain in X
torsional strain in X
global angle of rotation about the X -axis
global angle of rotation about the Y -axis
global angle of rotation about the Z -axis
angle of rotation about the u i -axis
angle of rotation about the v i -axis
angle of rotation about the w i -axis
bending curvature in X
bending curvature in Z
driving motor pulley rotated angle
A.1 Axial Shape Functions
A.2 torsional shape functions, a.3 transverse shape functions, a.4 lateral shape functions, a.5 shape functions for θ z, a.6 shape functions for θ y, get email alerts, related articles, related proceedings papers, related chapters, affiliations.
- Accepted Manuscripts
- ASME Journal Media
- About the Journal
- Editorial Board
- Information for Authors
- Call for Papers
- Rights and Permission
- Online ISSN 1942-4310
- Print ISSN 1942-4302
ASME Journals
- About ASME Journals
- Submit a Paper
- Title History
ASME Conference Proceedings
- About ASME Conference Publications and Proceedings
- Conference Proceedings Author Guidelines
ASME eBooks
- About ASME eBooks
- ASME Press Advisory & Oversight Committee
- Book Proposal Guidelines
- Frequently Asked Questions
- Publication Permissions & Reprints
- ASME Membership
Opportunities
- Faculty Positions
- ASME Community
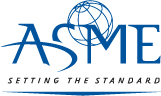
- Accessibility
- Privacy Statement
- Terms of Use
- Get Adobe Acrobat Reader
This Feature Is Available To Subscribers Only
Sign In or Create an Account
Subscribe to the PwC Newsletter
Join the community, edit social preview.

Add a new code entry for this paper
Remove a code repository from this paper, mark the official implementation from paper authors, add a new evaluation result row, remove a task, add a method, remove a method, edit datasets, a moving mesh finite element method for bernoulli free boundary problems.
5 Apr 2024 · Jinye Shen , Heng Dai , Weizhang Huang · Edit social preview
A moving mesh finite element method is studied for the numerical solution of Bernoulli free boundary problems. The method is based on the pseudo-transient continuation with which a moving boundary problem is constructed and its steady-state solution is taken as the solution of the underlying Bernoulli free boundary problem. The moving boundary problem is solved in a split manner at each time step: the moving boundary is updated with the Euler scheme, the interior mesh points are moved using a moving mesh method, and the corresponding initial-boundary value problem is solved using the linear finite element method. The method can take full advantages of both the pseudo-transient continuation and the moving mesh method. Particularly, it is able to move the mesh, free of tangling, to fit the varying domain for a variety of geometries no matter if they are convex or concave. Moreover, it is convergent towards steady state for a broad class of free boundary problems and initial guesses of the free boundary. Numerical examples for Bernoulli free boundary problems with constant and non-constant Bernoulli conditions and for nonlinear free boundary problems are presented to demonstrate the accuracy and robustness of the method and its ability to deal with various geometries and nonlinearities.
Code Edit Add Remove Mark official
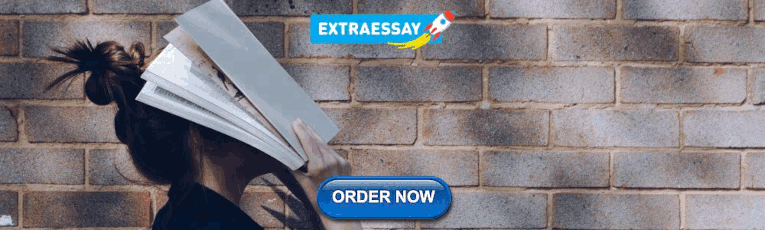
IMAGES
VIDEO
COMMENTS
Abstract. The finite element method (FEM) is a numerical analy sis technique for obtaining approximate. solutions to a wide variety of engineering problems. A finite element model of a pro blem ...
In a paper published in 1960 , R.W. Clough coined the phrase Finite Element Method, and this unassuming and right-to-the-point phrase was an instant hit, bringing out the essence of the method. With his deep insights and profound vision into Courant's variational approach, J.H. Argyris developed the energy method for engineering structures ...
9 mixed methods Dual mixed method Instead of integrating by parts in the second equation, we can formally integrate by parts in the ˙rst equation of (9.14). To make this well-de˙ned, we set div„Ω":=. 2 2„Ω" : div 2 2„Ω". Ł endowed with the graph norm k k2 div„Ω". := k k2 2„Ω" ‚kdiv k.
An International Journal for Innovations in Computational Methodology and Application. The aim of this journal is to provide ideas and information involving the use of the finite element method and its variants, both in scientific inquiry and in professional practice. The scope is intentionally broad, encompassing use of the finite element ...
I. (1941-1965) The birth of the finite element method The origin of the finite element method as a numerical modeling paradigm may be traced back to in early 1940's. In 1941, A. Hrennikoff, a Russian-Canadian structural engineer at the University of British Columbia, published a paper in ASME Journal of Applied Mechanics on his membrane
The objective of this paper is to design an experimental research using the finite element method. In this respect, an orthogonal cutting pattern will be established using this method. This involves determining the type, the method and technique of FEA application used, the material and the constitutive model of the material to be processed ...
technology for the current and future eras of FEM research. Note that this paper may not strictly follow the chronological order of FEM developments, because often time these develop-ments were interwoven across dierent time periods. 1 (1941-1965) The Birth of the Finite Element Method The origin of the FEM as a numerical modeling paradigm
This paper presents an advanced approach for structural topology optimization by incorporating fatigue crack propagation analysis. The extended finite element method (X-FEM) is employed to model ...
The finite element method also motivates extensive research on mathematics, providing specific structures for the firm theoretical foundation. This Special Issue, entitled "Recent Advances in Finite Element Methods with Applications", aims to collect recent advances in the construction, theoretical analysis, implementation, and application ...
The current study utilises Finite Element Analysis (FEA) to probe the combined effects of creep behaviour, fatigue failure, and random vibration on the longevity of solder joints within electronic ...
This is achieved by enriching the polynomial approximation space of the classical finite element method. The GEFM/XFEM has shown its potential in a variety of applications that involve non-smooth solutions near interfaces: Among them are the simulation of cracks, shear bands, dislocations, solidification, and multi-field problems.
The purpose of this primer is to provide the basics of the finite element method, primarily illustrated through a classical model problem, linearized elasticity. The topics covered are: † Weighted residual methods and Galerkin's approximations, † A model problem for one-dimensional linear elastostatics, † Weak formulations in one ...
2. Algorithm for solving shape optimization on multiple overlapping domains. In this section, we present the algorithm for solving PDE constrained shape optimization problems using the MultiMesh Finite Element Method (FEM). In this paper, we consider shape optimization problems of the form. (2.1) min J(u; )
In this paper, a two-level finite element method for Oseen viscoelastic fluid flow obeying an Oldroyd-B type constitutive law is presented. With the newly proposed algorithm, solving a large system of the constitutive equations will not be much more complex than the solution of one linearized equation.
Throughout its history, the finite element method has been applied in various ways and in various domains, from structural mechanics to electromagnetism, from thermal flow to fluid-structure interaction. This Special Issue is dedicated to exploring the recent advances in various applications of the finite element method and related methods.
Show abstract. ... For this to be achieved finite element analysis (FEA) can be used. (1) The FEA or the finite element method (FEM) is a numerical tool for solving problems in engineering and ...
A reduced-order characteristic finite element method based on POD for optimal control problem governed by convection-diffusion equation. Computer Methods in Applied Mechanics and Engineering . 10.1016/j.cma.2021.114538 . 2022 . Vol 391 . pp. 114538. Author (s): Junpeng Song . Hongxing Rui.
Unfitted finite element methods, like CutFEM, have traditionally been implemented in a matrix-based fashion, where a sparse matrix is assembled and later applied to vectors while solving the resulting linear system. With the goal of increasing performance and enabling algorithms with polynomial spaces of higher degrees, this contribution chooses a more abstract approach by matrix-free ...
In practical applications, the lowest-order Galerkin-mixed method is the most popular one, where the linear Lagrange element is used for the concentration and the lowest-order Raviart-Thomas element, the lowest-order Nédélec edge element and piece-wise constant discontinuous Galerkin element are used for the velocity, vorticity and pressure ...
This book collects nineteen papers and original research articles from participants of the 30th Chemnitz Finite Element Symposium. It offers readers insights into the latest results of research on finite element methods, their analysis, application and extension.
A FINITE ELEMENT METHOD FOR TIME FRACTIONAL 455 where 0 <α<1 and Ω is the bounded open domain inRd,d=1,2,3and ∂Ω is the boundary of Ω.Here Δ = ∂ 2 ∂x 2 1 + ∂ ∂x2 + ∂2 ∂x2 3 denotes the Lapla-cian operator with respect to the x variable, R 0 D α t u(t,x) denotes the left Riemann-Liouville fractional derivative with respect to the time variable t defined by
The Finite Element method is commonly used to build numerical models to simulate the human hearing system behavior, ... we will use a simplified geometries previously used by our research group in other works. 22-25. ... In this paper, a semi-automatic algorithm to build, from Micro-CT images, a numerical model of the human auditory system was ...
In this paper a robust three-dimensional (3D) finite element (FE) anisotropy model is introduced based on a particular scalar potential formulation. The specific 3D FE model is suitable for the accurate evaluation of the peak flux density... more. Download. by Themistoklis D. Kefalas. 92.
This paper presents the implementation of the eXtended Finite Element Method (XFEM) in the general-purpose commercial software package COMSOL Multiphysics for multi-field thermo-hydro-mechanical problems in discontinuous porous media. To this end, an exclusive enrichment strategy is proposed in compliance with the COMSOL modeling structure.
The Finite Element Method: 1D. (Example worked out on board) Suppose uh(x) can be written as linear combination of Vh elements: uh(x) = X uivi(x) vi2Vh. The discrete form becomes: find coefficients ui 2 R such that.
The deformation of an aluminum plate, called in this paper, a support plate, which is part of a bending plastic deformation device, is studied in this paper using the Finite Elements Method ...
Abstract. Flexible continuum manipulators (FCMs) are gaining importance because of their maneuverability and pliability in confined and complex spaces, where rigid link manipulators underperform. However, the dynamic behavior and control of the FCM are quite challenging due to its complex nonlinear behavior. In this study, a finite element-based dynamic model framework is derived that accounts ...
The finite element method (FEM), or finite element analysis (FEA), is a computational technique used to obtain approximate solutions of boundary value problems in engineering. Boundary value problems are also called field problems. The field is the domain of interest and most often represents a physical structure.
The paper introduces a finite element method for an Eulerian formulation of partial differential equations governing the transport and diffusion of a scalar quantity in a time-dependent domain. The method follows the idea from Lehrenfeld & Olshanskii [ESAIM: M2AN, 53(2): 585-614, 2019] of a solution extension to realise the Eulearian time ...
A moving mesh finite element method is studied for the numerical solution of Bernoulli free boundary problems. The method is based on the pseudo-transient continuation with which a moving boundary problem is constructed and its steady-state solution is taken as the solution of the underlying Bernoulli free boundary problem. The moving boundary ...