55 Process Improvement Case Studies & Project Results [2024]

Business leaders know that process improvement reduces costs and increases customer satisfaction. Therefore, businesses follow process improvement methodologies or deploy tools such as process modeling, process mining and RPA to discover, modify and automate their processes. However, it can be difficult for process experts and business analysts to understand the different process improvement approaches and the results they should expect.
Read our process improvement approaches guide for a categorization of process improvement approaches so you can rely on a framework to structure your process improvement initiatives. In this article, we share typical process improvement project results and case studies. Our aim is to provide benchmarks so business analysts and leaders can set targets for their own initiatives.
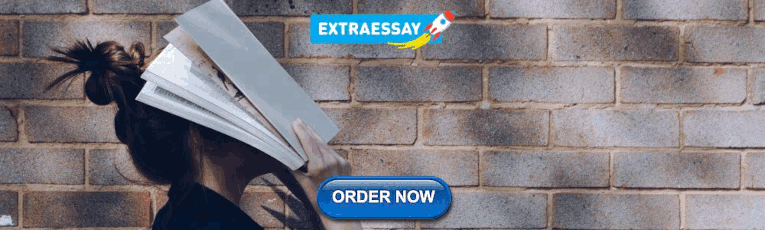
What are the typical project results?
Process improvement solutions help businesses define weaknesses and take action to solve these problems. In the case studies we collected, the most common project results that we came across are as follows:
1- Improved efficiency: Most businesses increase the efficiency of their processes by adapting process improvement methodologies. After defining their problems, companies eliminate unnecessary steps in processes, reduce their costs, and shorten process times. As a result, they achieve faster processes and higher quality output with fewer resources.
For example, in a process mining case study, a manufacturer leveraged IBM Process Mining to analyze the procure-to-pay processes. It is claimed that the manufacturer detected and managed deviations, mismatches and early payments, which lessened maverick buying and saved $60,000 in reworking cost. The firm improved purchase order and invoice processes by automating 75% of line creation and delivery activities. As a result, the company decreased the invoice registration and approval time.
2- Enhanced customer satisfaction: The increasing quality of output and faster processes can also reflect on customer satisfaction. Process improvement solutions help businesses reduce waiting time and focus on customer value. For example, it is claimed that by adopting the Kaizen methodology, Tata Steel has shortened its response time and delivered more on-time orders to its customers.
3- Harmonization of different teams/processes: For large companies, handling different processes simultaneously can be a big challenge. Teams should be informed about what others do, and processes need to work in sync to avoid problems. With process improvement solutions, businesses can have a full understanding of all their companies and align different processes successfully.
Here is an extended list of case studies which are collected from different resources. You can filter the list by the process improvement solution, service provider, industry, or process and investigate the achieved results.
Further Reading
If you want to learn more on process improvement, these articles can also interest you:
- Process Improvement: In-depth Guide for Businesses
- Lean Process Improvement Guide for Your Business
Check out comprehensive and constantly updated list of process mining case studies to process mining real-life examples and compare them to process improvement case studies.
If you want to manage and improve your processes, check out our data-driven and up-to-date list of vendors for:
- Workflow management software
- Business process management software
- Low-code/No-code development platform
- Onboarding software
- Process mining
- Business process automation software
If you still have questions about process improvement, we would like to help:

Cem has been the principal analyst at AIMultiple since 2017. AIMultiple informs hundreds of thousands of businesses (as per similarWeb) including 60% of Fortune 500 every month. Cem's work has been cited by leading global publications including Business Insider , Forbes, Washington Post , global firms like Deloitte , HPE, NGOs like World Economic Forum and supranational organizations like European Commission . You can see more reputable companies and media that referenced AIMultiple. Throughout his career, Cem served as a tech consultant, tech buyer and tech entrepreneur. He advised businesses on their enterprise software, automation, cloud, AI / ML and other technology related decisions at McKinsey & Company and Altman Solon for more than a decade. He also published a McKinsey report on digitalization. He led technology strategy and procurement of a telco while reporting to the CEO. He has also led commercial growth of deep tech company Hypatos that reached a 7 digit annual recurring revenue and a 9 digit valuation from 0 within 2 years. Cem's work in Hypatos was covered by leading technology publications like TechCrunch and Business Insider . Cem regularly speaks at international technology conferences. He graduated from Bogazici University as a computer engineer and holds an MBA from Columbia Business School.
To stay up-to-date on B2B tech & accelerate your enterprise:
Next to Read
What is process workflow & top 4 benefits & case studies in '24, business process design in '24: 7 best practices, how to implement process improvement in 6 steps in 2024.
Your email address will not be published. All fields are required.
Hi Cem, Thank you ver much for your interesting article. I am interested in getting a deeper look into some of the case studies: How exactly did they approach the problem? ….Would it be possible to get a closer look at the case studies? Thanks in advance. Adrian
Hi Adrian, please feel free to get in touch with us via [email protected] . Happy to discuss these in more detail once we know which types of case studies you are interested in
Related research
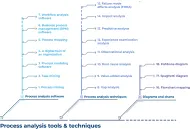
18 Best Process Analysis Tools & Techniques in 2024
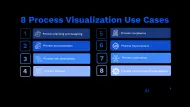
Process Visualization in '24: 8 Use Cases & 13 Best Techniques
- For Small Business
55 Process Improvement Case Studies & Project Results [2023]
- March 17, 2024
- by Terry Tolentino
Introduction
Process improvement is the practice of identifying, analyzing and improving upon existing business processes within an organization to optimize performance. It aims to reduce costs, enhance efficiency, eliminate redundancies, and deliver higher quality outputs. This is achieved by leveraging data and methods to understand root causes and implement targeted solutions.
Adopting process improvement enables organizations to:
- Reduce operational costs through waste and inefficiency elimination
- Improve productivity and output capacity with existing resources
- Streamline process workflows to boost speed and agility
- Standardize processes to minimize errors and defects
- Enhance customer experience and satisfaction
Some key process improvement methodologies and frameworks include:
Lean – Focuses on maximizing value and minimizing waste by removing non-value steps and optimizing flow. Key techniques include value stream mapping, 5S, JIT, etc.
Six Sigma – Follows a DMAIC (define, measure, analyze, improve, control) approach to reduce variations and defects by understanding root causes using statistical tools.
Kaizen – Involves continuous incremental improvements made by workers and cross-functional teams to enhance processes.
Business Process Management (BPM) – Leverages software tools and methods to discover, document, automate, and optimize end-to-end business processes.
Process Mining – Provides visibility into actual processes by extracting event logs from IT systems to create models and identify improvements.
Robotic Process Automation (RPA) – Automates repetitive and rules-based processes by deploying software bots that emulate human actions. Enables huge productivity gains.
This article examines 55 real-world process improvement case studies and their results across diverse companies and industries. The objective is to provide benchmarks and best practices for business leaders and process improvement teams undertaking such initiatives.
The Value of Process Improvement
Process improvement delivers immense value and competitive advantage to organizations. According to Gartner, BPM efforts have resulted in cost reductions of 15-25% and cycle time improvements of 20-40%.
McKinsey estimates that process excellence programs can potentially reduce costs by 20-40%, improve quality by 10-50%, and cut process times by 25-75%.
As per Forrester, RPA implementations yield an ROI of 200-300% with payback periods as short as 3-6 months.
The global business process management market size was valued at USD 14.9 billion in 2021, and is projected to grow at a CAGR of 14% from 2022 to 2030, per Grand View Research.
This underscores why over 80% of organizations are looking to optimize, automate, and transform their processes. The results make the investment highly worthwhile.
Key Process Improvement Results
Here are some typical outcomes organizations can achieve through process reengineering:
Productivity increase: 50-70% gains in productivity and output are common by optimizing human and technical resource usage.
Cost reduction: 25-60% reductions in operational costs by eliminating redundancies and waste.
Cycle time improvement: End-to-end process times shortened by 40-75% through workflow streamlining and automation.
Quality improvement: Error and defect rates reduced over 50-70% by minimizing process variations.
Revenue increase: 20-45% higher revenues enabled by faster and flawless customer order fulfilment.
Now let‘s examine 55 real-world examples of process improvement across industries:
Key Insights from the Case Studies
Analyzing these case studies reveals valuable patterns:
Manufacturing, financial services, and technology lead process improvement adoption, but benefits realized across sectors.
Production, supply chain, IT, finance processes improved the most. Customer services, HR, sales also optimized.
Lean Six Sigma, process mining, RPA, and BPM are the most popular and effective solutions.
Average efficiency gains of 50%, process costs reduced by 35%, process times shortened by 45%.
Process mining provides quick understanding of bottlenecks and pain points. More valuable for complex processes.
RPA and BPM rapidly automate repetitive and manual workflows for major productivity improvements.
Lean and Six Sigma drive a highly quantified approach to systematically eliminate waste and defects.
Kaizen and Agile facilitate continual improvement through small changes and team coordination.
Best Practices for Process Improvement Success
Here are some key tips for ensuring successful process improvement:
Secure Leadership Buy-in
- Engage executives early and outline the burning platform and expected benefits. Tie process improvement to strategic goals.
Define Scope and Prioritize
- Focus initial efforts on most critical processes with the biggest business impact.
Discover and Map Processes
- Understand current workflows using process mapping and mining. Identify pain points.
Measure and Baseline Metrics
- Quantify current process performance across time, cost, quality, and other KPIs before improvement.
Analyze Root Causes
- Dig deeper to uncover sources of bottlenecks, waste, variations etc. via cause-effect tools.
Redesign and Simplify Processes
- Eliminate non-value steps, minimize redundancies, standardize, and automate where possible.
Implement Changes Incrementally
- Test and iterate improvements through small pilot projects before enterprise-wide rollout.
Track Performance and Sustain Improvements
- Monitor key process metrics through automated dashboards for continuous improvement.
The outcomes from these case studies demonstrate the huge potential of process improvement to drive organizational excellence. While approaches differ, adopting a data-driven methodology tailored to your needs and backed by leadership commitment can enable you to replicate the success of these companies. The journey begins with discovering and mapping your processes to uncover improvement areas.
To learn more, explore these additional resources:
- McKinsey – The seven principles of improvement
- Forrester – The Total Economic ImpactTM Of Blue Prism
- Gartner – How to Get Started With Process Mining
Ready to optimize your business workflows? Our process improvement experts can guide you. Request a consultation .
The Lean Post / Articles / Lean Management Case Studies Library
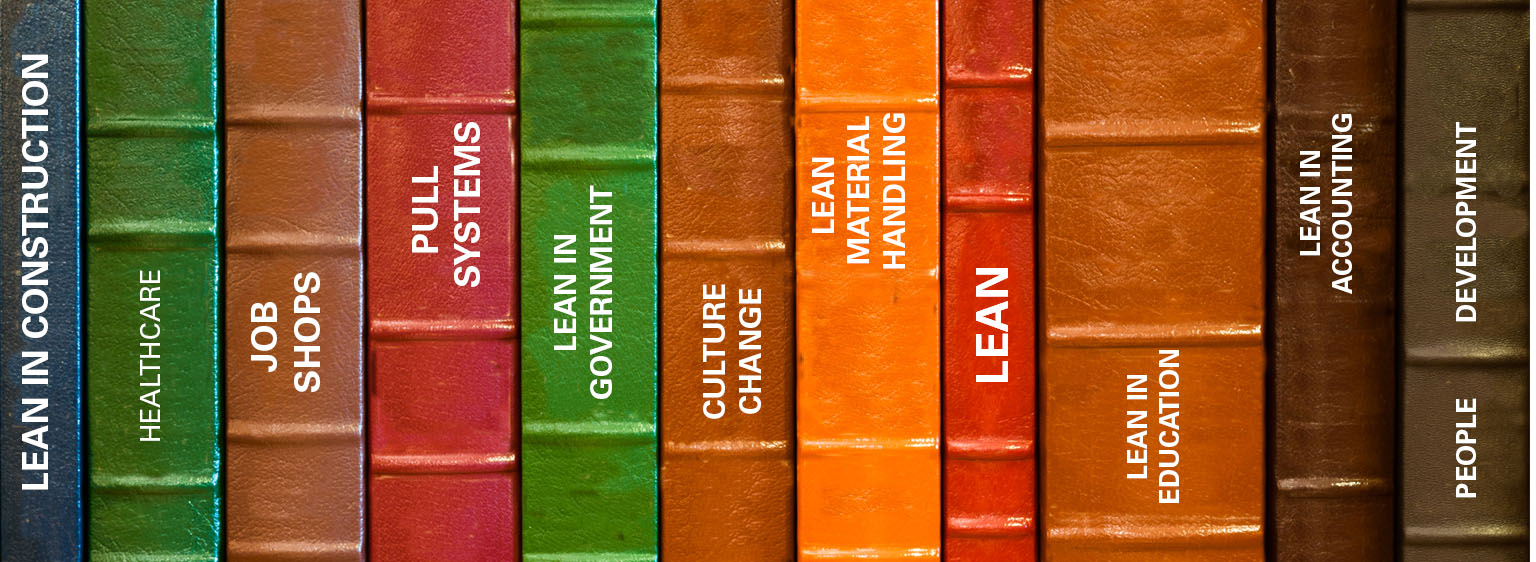
Lean Management Case Studies Library
By Chet Marchwinski
May 16, 2014
Learn how a variety of businesses and organizations used lean management principles to solve real business problems. We’ve arranged the examples in 16 categories to help you find the ones right for your environment.
Lean Management Examples from a Variety of Businesses
The following case studies of lean management principles in action show you how a variety of real businesses solved real business problems under diverse conditions.
We’ve arranged the stories in 16 categories to help you find the examples you need. There is some overlap. For instance, a “Lean Manufacturing” case study may also appear with “Privately Held Companies.”
Lean Manufacturing
- Logistics, Supply Chain, and Warehousing
- Lean Material Handling
- Job Shops (Low-volume, High-mix Manufacturing); Tool and Die
- Lean in Government
- Lean Healthcare
- Lean Accounting
- Lean Construction
- Lean in Office and Service Processes
- Lean in Education
Problem Solving
Pull Systems
Culture Change
People Development
Privately Held Companies
Maintenance
Many of the executives who took part in these transformations are interviewed in LEI’s Senior Executive Series on Lean Leadership . After reading the case studies, be sure to get their personal perspectives on leading change. (Feel free to link to this page, but please respect the copyrights of LEI and journalists by not copying the articles.)
Are you doing something new or notable in the practice of lean management? Let us share what you learned with the lean community. For more information, contact LEI’s Director of Communications Chet Marchwinski at cmarchwinski at lean dot org
Thrustmaster Turns Around
Learn how Thrustmaster of Texas successfully adopted lean thinking and practices to make sustainable improvements in a short period of time, and how other manufacturers of highly engineered, low-volume products can follow their lead using the Lean Transformation Framework.
Lean + Circular Principals = a New True North for Manufacturer
SunPower’s lean journey resembled most others until it defined a new mission, a new True North by combining lean principals with those of the “circular economy” to launch what it is calling a CLean Transformation.
Sustain Your Lean Business System with a “Golden Triangle” After a medical device maker took a hit to margins to fight off global competition, it rebuilt them by lifting its lean operating system to a higher level and keeping it there with a “golden triangle” of sustainability.
Followup Story:
Manufacturing Balancing Act: Pull Versus ERP
In this follow-up to “Sustain Your Lean Business System with a ‘Golden Triangle,’” a case study about Phase 2 Medical Manufacturing, the company needs warehouse space to keep pace with sales growth spurred by the lean transformation. Instead, it expands a pull system by connecting the plan-for-every-part database that underpins one-piece flow production with ERP, typically associated with big batch production.
Cultivating a Lean Problem-Solving Culture at O.C. Tanner If you are in the “appreciation business”, you have to live it in your own workplace. For O.C. Tanner that meant a lean transformation had to show the company appreciated and wanted people’s problem-solving ideas. Here’s a report on that effort, including what worked and what didn’t.
Lean Partnership with Dealer Network Helps Vermeer Reduce End-to-End Inventory on Top Sellers
A lean transformation had taken heavy-equipment manufacturer Vermeer away from batch manufacturing, but batch ordering by dealers was delaying how quickly they got equipment like brush chippers. Learn how it began converting its domestic industrial-line distribution network to lean replenishment, improving service to end customers and improving cash flow for Vermeer and its dealers.
Herman Miller’s Experiment in Excellence At Herman Miller, the lean management effort helps it build problem solvers as well as world-class office furniture. And as this case study shows, lean practices also helped it weather a brutal recession.
Build Your “House” of Production on a Stable Foundation Rigorous problem solving creates basic stability in a machining intensive facility.
A Journey to Value Streams: Reorganizing Into Five Groups Drives Lean Improvements and Customer Responsiveness An approach to creating a value -stream culture centered on autonomy, entrepreneurialism, and lean principles.
Change in Implementation Approach Opens the Door at EMCO to Greater Gains in Less Time A relatively quick, intensive project accelerates the rate of improvement and creates a showcase facility for spreading lean concepts.
Creating the Course and Tools for a Lean Accounting System A lean accounting implementation fills the frustrating disconnect between shop-floor improvements and financial statements.
For Athletic Shoe Company, the Soul of Lean Management Is Problem Solving After taking a lean tools approach to change, management re-organized the transformation around problem solving and process improvement to create a culture that engaged people while boosting performance.
Knife Company Hones Competitiveness by Bucking the Status Quo An iconic family-owned company turns to lean manufacturing to reduce costs by at least 30% to keep its U.S. operations open.
Lean Transformation Lives and Dies with Tools and Dies After a failed first try at just-in-time production , a company transforms tool maintenance, design, and fabrication to create a solid foundation for a second attempt.
Seasoned Lean Effort Avoids “Flavor-of-the-Month” Pitfall A look at how one company’s approach to what new tools it introduced, in what order, and how it prevented each new technique from being viewed as a “flavor of the month” fad.
Shifting to Value-Stream Managers: a Shop-Floor Revolution Leads to a Revolution in Plant Organization
Two years into a lean transformation, the low-hanging fruit has been plucked and progress has started to slow. Read how a Thomas & Betts plant recharged the transformation and reached higher levels of performance by using value-stream managers to span functional walls.
Using Plan-Do-Check-Act as a Strategy and Tactic for Helping Suppliers Improve
At Medtronic’s Neuromodulation business unit, the plan-do-check-act cycle is used on a strategic level to guide overall strategy for selecting and developing key suppliers as well as on a tactical level for guiding lean transformations at supplier facilities.
back to top
Logistics, Supply Chain, and Warehousing How a Retailer’s Distribution Center Exemplifies the Lean Precept “Respect for People,” and Reaps the Benefits
To make sure training engaged and resonated with people after previous attempts at a lean transformation faltered, LifeWay matched lean management tools and principles to its Bible-based culture and language.
Lean management case study series: Lean in Distribution: Go to Where the Action Is!
Starting with daily management walkabouts and standard work , this distributor had laid the groundwork for steady gains for years to come, just two years after its first kaizen workshop .
Putting Lean Principles in the Warehouse
Executives at Menlo Worldwide Logistics saw an opportunity to leapfrog the competition by embracing lean in its outsourced warehousing and receiving operations.
Lean Thinking Therapy Spreads Beyond the Shop
A company expands the lean transformation from the shop floor to international distribution, domestic shipping, and product development.
Sell One, Buy One, Make One: Transforming from Conventional to Lean Distribution
Large inventories to cover fluctuations in demand once characterized Toyota’s service parts distribution system — but no more. Here’s how one DC made the switch.
Material Handling
Following Four Steps to a Lean Material-Handling System Leads to a Leap in Performance
Creating the critical Plan for Every Part was one step in a methodical four-step implementation process to replace a traditional material-handling system.
Low-volume, High-mix Manufacturing; Tool and Die
The Backbone of Lean in the Back Shops
Sikorsky managers apply the lean concept of “every part, every interval” (EPEI) to level the mix in demand and create flow through a key manufacturing cell .
Landscape Forms Cultivates Lean to Fuel Growth Goals
With single-item orders 80% of the time, a low-volume, high-mix manufacturer decided single-piece flow cells were the best way decided the best way to add new products without having to constantly reconfigure production.
Lean Transformation Lives and Dies with Tools and Dies
After a failed first try at just-in-time production, a company transforms tool maintenance, design, and fabrication to create a solid foundation for a second attempt.
Canada Post Puts Its Stamp on a Lean Transformation
The “ inventory ” of mail already is paid for, so moving it faster doesn’t improve cash flow as in lean manufacturing. But Canada Post discovered that traditional batch-and-queue postal operations could benefit from lean principles.
Lean Thinking in Government: The State of Iowa
This story examines a kaizen event at a veterans home and more broadly at the lean effort in Iowa government.
Lean Thinking Helps City of Chula Vista with Budget Crunch
Goodrich Aerostructures’ Chula Vista plant introduces city government to lean thinking and practices so in order to maintain municipal services without resorting to further cuts in the workforce.
Using Lean Thinking to Reinvent City Government
Grand Rapids, MI, turns to lean principles to consolidate operations, eliminate wasted time and effort, and streamline to improve productivity while providing the quality of service that residents want.
Transforming Healthcare: What Matters Most? How the Cleveland Clinic Is Cultivating a Problem-Solving Mindset and Building a Culture of Improvement
The Cleveland Clinic reinvents its continuous improvement program to instill a problem-solving mindset and the skillset to solve everyday problems among the clinic’s thousands of caregivers.
View from the Hospital Floor: How to Build a Culture of Improvement One Unit at a Time
In order to do more and improve faster, the Cleveland Clinic is rolling out a methodology for building a “culture of improvement” across the 48,000-employee hospital system as this followup to the above story shows. Here’s how it works according to the people making the changes.
Dentist Drills Down to the Root Causes of Office Waste
Dentistry is a job shop that Dr. Sami Bahri is out to improve fundamentally for the benefit of patients through the application of lean principles.
Lean management case study series: Pediatric Hospital in Tough Market Pegs Growth to Lean Process Improvement
Lean improvement projects at Akron Children’s Hospital have saved millions of dollars, increased utilization of expensive assets, and reduced wait times for patients and their families.
Lean Design and Construction Project an Extension of Lean Commitment at Akron Children’s Hospital
Input from nurses, doctors, therapists, technicians, and patient parents heavily influenced design decisions..
“Pulling” Lean Through a Hospital
A thoughtful rollout of lean principles in the ER and eye-opening results created a “pull” for lean from other departments.
Best in Healthcare Getting Better with Lean
Mayo Clinic, Rochester, MN, stresses to doctors that the lean effort is aimed not at changing the moment of care, the touch moment between doctor and patient, but the 95% of the time when the patient is not in the doctor’s office
Fighting Cancer with Linear Accelerators and Accelerated Processes
Cross-functional team design and implement a lean process to dramatically increase the number of patients with brain and bone metastases receiving consultation, simulation, and first treatment on the same day without workarounds or expediting.
Massachusetts General Looks to Lean
A proton therapy treatment center, for many adults and children the best hope of beating cancer, applies lean principles to increase capacity.
New Facility, New Flow, and New Levels of Patient Care: The wait is over for patients at the Clearview Cancer Institute in Alabama
Physicians and staff have tirelessly reengineer processes and patient flow to eliminate as much waiting and waste as possible.
The Anatomy of Innovation
At a hospital in Pittsburgh, the emerging vision for the “hospital of the future” is described as giving the right patient, the right care, at the right time, in the right way, all the time.
Creating the Course and Tools for a Lean Accounting System
A lean accounting implementation fills the frustrating disconnect between shop-floor improvements and the financial statement.
Knife Company Hones Competitiveness by Bucking the Status Quo
An iconic family-owned company turns to lean manufacturing to reduce costs by at least 30% to keep its U.S. operations open.
Office and Service Processes
The “inventory” of mail already is paid for, so moving it faster doesn’t improve cash flow as in lean manufacturing. But Canada Post discovered that traditional batch-and-queue postal operations could benefit from lean principles.
Lean Landscapers
At an Atlanta landscaping company, lean practices are making inroads into a service industry in unusual yet fundamental ways.
LSG Sky Chefs Caters to New Market Realities
Business at airline caterer LSG Sky Chefs dropped 30% when airlines cut flights after the terrorist attacks on September 11, 2001. Sky Chefs responded with a rapid launch of a lean initiative.
leveraging Lean to Get the Oil Out
Aera Energy LLC, a California oil and gas company, relies on lean principles to improve key processes, including drilling new wells, repairing existing ones, and maximizing the number of barrels of crude pumped each day.
Columbus Public Schools Use Process Thinking to Improve Academic Achievement.
Columbus, OH, public schools, experiment with lean tools and process thinking to remove wasteful activities that don’t help them help students learn.
Lean Inroads into Alabama Academia
How the University of Alabama in Huntsville integrated lean concepts throughout its industrial engineering curriculum.
Linking Lean Thinking to the Classroom
Value-stream mapping is one of many activities included in the Ford Partnership for Advanced Studies (Ford PAS), an academic program designed to link high-school classroom learning to the skills needed in college and business.
Build Your “House” of Production on a Stable Foundation
Rigorous problem solving creates basic stability in a machining intensive facility.
For Athletic Shoe Company, the Soul of Lean Management Is Problem Solving
After talking a lean tools approach to change, management re-organized the transformation around problem solving and process improvement to create a culture that engaged people while boosting performance.
Toothbrush Plant Reverses Decay in Competitiveness
The rapid introduction of a lean system, beginning with just-in-time production and pull, helps a highly automated Midwest plant fight off overseas competition by reducing lead times and inventory while augmenting the plant’s advantage in service.
A Journey to Value Streams: Reorganizing Into Five Groups Drives Lean Improvements and Customer Responsiveness
An approach to creating a value-stream culture centered on autonomy, entrepreneurialism, and lean principles.
Making Lean Leaders — Ariens internship program develops lean and leadership skills
Besides making snow-blowers, mowers, and string trimmers, Ariens Co., of Brillion, WI, makes lean leaders.
Starting with daily management walkabouts and standard work, this 84-year-old, family-owned distributor laid the groundwork for steady gains for years to come, just two years after its first kaizen workshop.
Sustain Your Lean Business System with a “Golden Triangle”
After a medical device maker took a hit to margins to fight off global competition, it rebuilt them by lifting its lean operating system to a higher level and keeping it there with a “golden triangle” of sustainability. You’ll recognize two elements of the triangle right away: visual control and standardized work . The third, accountability management or a kamishibai system, is probably less well known but just as critical.
Cultivating a Lean Problem-Solving Culture at O.C. Tanner
If you are in the “appreciation business”, you have to live it in your own workplace. For O.C. Tanner that meant a lean transformation had to show the company appreciated and wanted people’s problem-solving ideas. Here’s a report on that effort, including what worked and what didn’t.
Lean Thinking in Aircraft Repair and Maintenance Takes Wing at FedEx Express
A major check that used to take 32,715 man-hours was cut to 21,535 hours in six months. That translated into a $2 million savings, which dovetailed with the company’s emphasis on reducing costs during the recession.
Construction
Input from nurses, doctors, therapists, technicians, and patient parents heavily influenced design decisions—from incorporating emergency room hallways that protect the privacy of abused children to the number of electrical outlets in each neonatal intensive care room.
Virtual Lean Learning Experience (VLX)
A continuing education service offering the latest in lean leadership and management.
Written by:
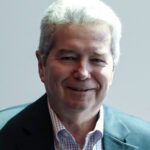
About Chet Marchwinski
Chet has been a humble, unwashed scribe of the lean continuous improvement movement since books by Taiichi Ohno and Shigeo Shingo first hit North America in the 1980s. At LEI, he contributes to content creation, marketing, public relations, and social media. Previously, he also wrote case studies on lean management implementations in…
Leave a Comment Cancel reply
Your email address will not be published. Required fields are marked *
Save my name, email, and website in this browser for the next time I comment.
Be the first to learn of new learning opportunities and the latest practical, actionable information. Subscribe to an LEI newsletter.
Join us on social, privacy overview.
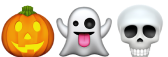
- Onsite training
3,000,000+ delegates
15,000+ clients
1,000+ locations
- KnowledgePass
- Log a ticket
01344203999 Available 24/7
Six Sigma Case Study: Everything You Need to Know
Explore the field of Six Sigma Case Studies in our comprehensive blog. From defining the methodology to real-world applications, our 'Six Sigma Case Study: Everything You Need to Know' blog sheds light on this powerful problem-solving tool. Uncover success stories and learn how Six Sigma can drive efficiency and quality improvements in various industries.

Exclusive 40% OFF
Training Outcomes Within Your Budget!
We ensure quality, budget-alignment, and timely delivery by our expert instructors.
Share this Resource
- Six Sigma Black Belt Upgrade
- Lean Six Sigma Green Belt
- Six Sigma Yellow Belt
- Six Sigma Black Belt
- Lean Six Sigma Black Belt
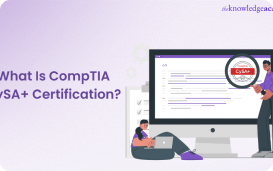
By analysing such case studies, one can gain insights into the successful application of Six Sigma in various industries and understand its impact on process improvement. Read this blog on Six Sigma Case Study to learn how real-world businesses have achieved remarkable process improvement and cost savings.
Table of Contents
1) Understanding Six Sigma Methodology
2) Six Sigma Case Study
a) Improving customer service
b) Improving delivery efficiency
3) Conclusion
Understanding Six Sigma Methodology
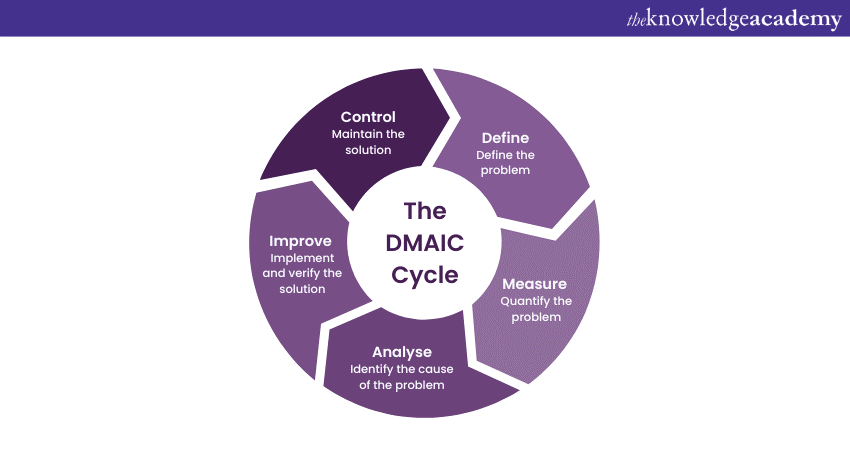
By applying statistical analysis and data-driven decision-making, Six Sigma helps organisations identify the root cause of problems and implement effective solutions. It emphasises the importance of process standardisation, continuous improvement, and customer satisfaction. With its focus on rigorous measurement and analysis, Six Sigma enables organisations to drive efficiency, reduce waste, and deliver exceptional products and services. The methodology follows a step-by-step process called Define, Measure, Analyse, Improve, and Control (DMAIC). These five phases are briefly explained below:
a) Define: The project goals and customer requirements are clearly defined in this phase.
b) Measure: In this phase, data is collected to understand the process's current state and identify improvement areas.
c) Analyse: This phase focuses on analysing data to determine the root cause of defects or variations.
d) Improve: This phase involves implementing solutions and making necessary changes to eliminate the identified issues.
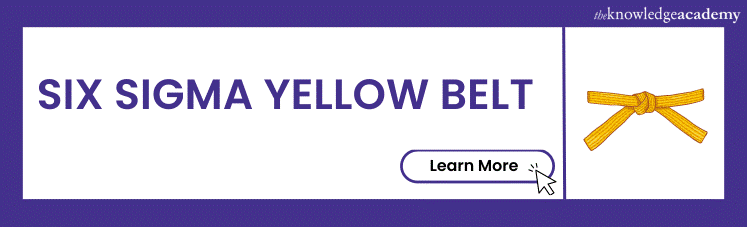
Six Sigma Case Study
In this section we discuss two Six Sigma Case Study that will help you understand and use it better.
Case Study 1: Improving customer service
This Six Sigma Case Study will focus on a telecommunications company facing significant customer service challenges. The issues included long wait times, frequent call transfers, unresolved issues, and many more. The company decided to apply Six Sigma methodologies to enhance customer satisfaction.
a) Define phase: Using the DMAIC approach, the team began by defining the problem: long wait times and inefficient call handling. They set a goal to reduce average wait time and increase first-call resolution rates.
b) Measure phase: In this phase, data was collected to analyse call volume, wait times, and reasons for call transfers. This helped identify bottlenecks and areas for improvement.
c) Analyse phase: During this phase, the team discovered that inadequate training and complex call routing were key contributors to the problems. They also found that certain product issues required better resolution protocols.
d) Improve phase: In this phase, targeted solutions were introduced and implemented to address these issues. The team revamped the training program, ensuring agents were well-trained and equipped to handle customer inquiries. They simplified call routing and introduced automated prompts for quicker issue resolution.
e) Control phase: Finally, monitoring systems were established in the control phase to track key metrics and ensure sustained improvements. Regular feedback loops were implemented to identify emerging challenges and make necessary adjustments.
The results were exceptional. Average wait times were reduced by 40%, and first-call resolution rates increased by 25%. Customer satisfaction scores improved significantly, leading to increased loyalty and positive word-of-mouth.
This Six Sigma Case Study highlights how Six Sigma methodologies can drive transformative improvements in customer service. By focusing on data analysis, process optimisation, and continuous monitoring, organisations can achieve outstanding outcomes and deliver exceptional customer experiences.
Understand the in-depth process of Six Sigma with our Six Sigma Yellow Belt Course . Join now!
Case Study 2: Improving delivery efficiency
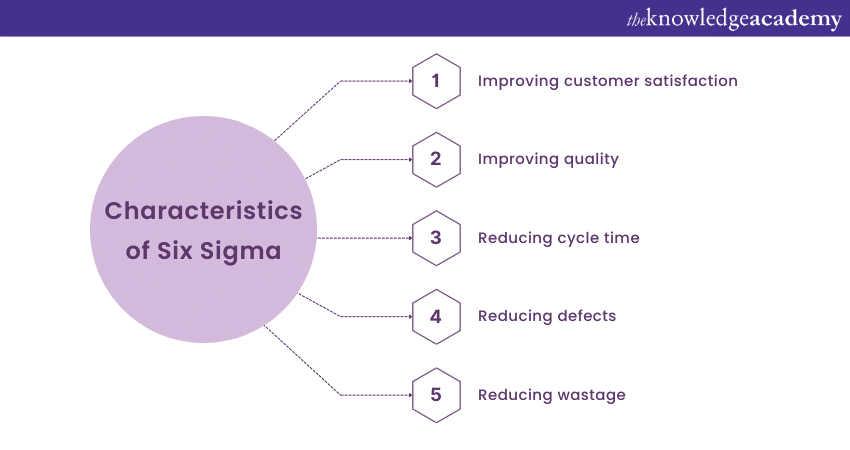
a) Define phase: The business used the Voice of the Customer (VoC) tool to understand customer needs and expectations. They identified prompt delivery, correct product selection, and a knowledgeable distribution team as crucial customer requirements.
b) Measure phase: The team collected data to evaluate the problem of slow delivery. They discovered that their Order Fulfillment Cycle Time (OFCT) was 46% longer than competitors, leading to customer dissatisfaction.
c) Analyse phase: The team brainstormed potential causes of slow delivery, including accuracy of sales plans, buffer stock issues, vendor delivery performance, and manufacturing schedule delays. They conducted a regression analysis, revealing that inadequate buffer stock for high-demand products was the main issue affecting delivery efficiency.
d) Improve phase: The distributor implemented a monthly demand review to ensure that in-demand products are readily available. They emphasised ordering and providing customers with the specific products they desired.
e) Control phase: The team developed plans to monitor sales of the top 20% of bestselling products, avoiding over or under-supply situations. They conducted annual reviews to identify any changes in demand and proactively adjust product offerings.
By applying Six Sigma Principles , the plumbing product distributor significantly improved its delivery efficiency, addressing the root cause of customer dissatisfaction. Prompt action, data-driven decision-making, and ongoing monitoring allowed them to meet customer expectations, enhance its reputation, and maintain a competitive edge in the industry. This case demonstrates the power of Lean Six Sigma in driving operational excellence and customer-centric improvements.
Take the next step in your professional development and boost your career by joining our Six Sigma Green Belt course .
Conclusion
We hope this blog gives you enough insights into the Six Sigma Case Study. This blog showcased the effectiveness of its methodology in driving transformative improvements. By applying DMAIC and using customer insights and data analysis, organisations have successfully resolved delivery inefficiencies, improving customer satisfaction and operational performance. The blog highlights how Six Sigma can be a powerful framework for organisations seeking excellence and exceptional value.
Learn the six-sigma methodology to achieve business objectives with our Six Sigma Certification Training today!
Frequently Asked Questions
Upcoming business improvement resources batches & dates.
Mon 15th Apr 2024
Sat 20th Apr 2024, Sun 21st Apr 2024
Mon 22nd Apr 2024
Mon 29th Apr 2024
Tue 7th May 2024
Mon 13th May 2024
Sat 18th May 2024, Sun 19th May 2024
Mon 20th May 2024
Tue 28th May 2024
Mon 3rd Jun 2024
Mon 10th Jun 2024
Mon 17th Jun 2024
Sat 22nd Jun 2024, Sun 23rd Jun 2024
Mon 24th Jun 2024
Mon 1st Jul 2024
Mon 8th Jul 2024
Mon 15th Jul 2024
Sat 20th Jul 2024, Sun 21st Jul 2024
Mon 22nd Jul 2024
Mon 29th Jul 2024
Mon 5th Aug 2024
Mon 12th Aug 2024
Sat 17th Aug 2024, Sun 18th Aug 2024
Mon 19th Aug 2024
Tue 27th Aug 2024
Mon 2nd Sep 2024
Mon 9th Sep 2024
Sat 14th Sep 2024, Sun 15th Sep 2024
Mon 16th Sep 2024
Mon 23rd Sep 2024
Mon 30th Sep 2024
Mon 7th Oct 2024
Sat 12th Oct 2024, Sun 13th Oct 2024
Mon 14th Oct 2024
Mon 21st Oct 2024
Mon 28th Oct 2024
Mon 4th Nov 2024
Sat 9th Nov 2024, Sun 10th Nov 2024
Mon 11th Nov 2024
Mon 18th Nov 2024
Mon 25th Nov 2024
Mon 2nd Dec 2024
Sat 7th Dec 2024, Sun 8th Dec 2024
Mon 9th Dec 2024
Mon 16th Dec 2024
Get A Quote
WHO WILL BE FUNDING THE COURSE?
My employer
By submitting your details you agree to be contacted in order to respond to your enquiry
- Business Analysis
- Lean Six Sigma Certification
Share this course
Our biggest spring sale.

We cannot process your enquiry without contacting you, please tick to confirm your consent to us for contacting you about your enquiry.
By submitting your details you agree to be contacted in order to respond to your enquiry.
We may not have the course you’re looking for. If you enquire or give us a call on 01344203999 and speak to our training experts, we may still be able to help with your training requirements.
Or select from our popular topics
- ITIL® Certification
- Scrum Certification
- Change Management Certification
- Business Analysis Courses
- Microsoft Azure Certification
- Microsoft Excel & Certification Course
- Microsoft Project
- Explore more courses
Press esc to close
Fill out your contact details below and our training experts will be in touch.
Fill out your contact details below
Thank you for your enquiry!
One of our training experts will be in touch shortly to go over your training requirements.
Back to Course Information
Fill out your contact details below so we can get in touch with you regarding your training requirements.
* WHO WILL BE FUNDING THE COURSE?
Preferred Contact Method
No preference
Back to course information
Fill out your training details below
Fill out your training details below so we have a better idea of what your training requirements are.
HOW MANY DELEGATES NEED TRAINING?
HOW DO YOU WANT THE COURSE DELIVERED?
Online Instructor-led
Online Self-paced
WHEN WOULD YOU LIKE TO TAKE THIS COURSE?
Next 2 - 4 months
WHAT IS YOUR REASON FOR ENQUIRING?
Looking for some information
Looking for a discount
I want to book but have questions
One of our training experts will be in touch shortly to go overy your training requirements.
Your privacy & cookies!
Like many websites we use cookies. We care about your data and experience, so to give you the best possible experience using our site, we store a very limited amount of your data. Continuing to use this site or clicking “Accept & close” means that you agree to our use of cookies. Learn more about our privacy policy and cookie policy cookie policy .
We use cookies that are essential for our site to work. Please visit our cookie policy for more information. To accept all cookies click 'Accept & close'.

The Complete Guide to Lean Process Improvement and How to Implement It
Last Updated on April 3, 2024 by Owen McGab Enaohwo
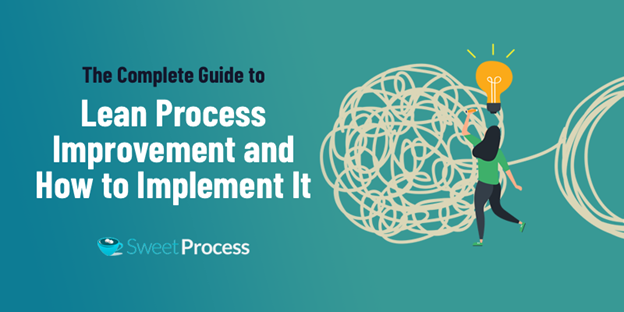
Featured Bonus Content: Download the FREE Lean Process Improvement Waste Reduction Checklist! Click Here To Download It.
Ask any business leader or read any article on why companies fail, and you’re likely to hear about poor cash management, bad market fit, hiring the wrong people, or weak leadership.
I nefficient processes are rarely cited as a reason why a company is falling behind or failing, even though they are usually the main reason why they do.
Ineffective processes are costing businesses a lot of money—almost a third of their income, if some studies are to be believed.
For example:
- Tech teams spend almost 30% of their time on finding data and menial tasks rather than conducting analysis.
- 64% of a sales rep’s counted hours are spent doing things that don’t contribute to the company’s bottom line.
- 50% companies also spend between $5 to $25 on manually processed invoices.
That’s a lot of company earnings going down the drain and something that lean process improvement can put a stop to.
In fact, the relevance of lean as a way of working became all too evident during the 2020-21 Covid pandemic as companies were forced to make do with less demand and uncertain supply chains.
Let’s take a closer look into what lean process improvement really means and how you can use it to keep your company a lean, mean machine.
The Complete Guide to Lean Process Improvement Chapter Index
Chapter 1: what is lean process improvement, chapter 2: how lean process improvement came about, chapter 3: the eight deadly wastes that lean process improvement eliminates, chapter 4: why lean sounds so familiar, chapter 5: types of lean process improvement methodologies, chapter 6: the three key anchors of an effective lean campaign, chapter 7: how to get started with lean process improvement, chapter 8: four cloud-based tools you can use to implement lean processes in your company, chapter 9: common misconceptions about lean process management, chapter 10: three lean process case studies.
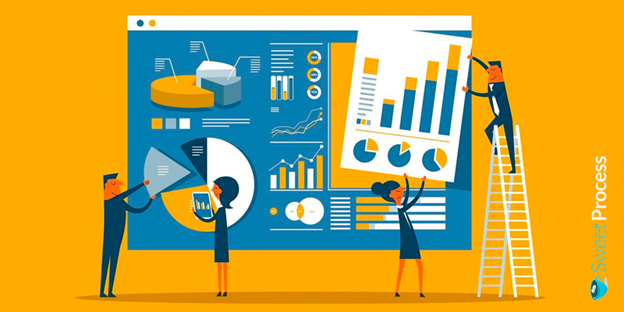
In lean process improvement , excess processes and steps are treated as burdens to be trimmed away.
Lean is best thought of as a philosophy rather than a hard and fast set of facts and techniques in a box. The objective here is to eliminate as much waste as possible to provide maximum value to the customer as efficiently and effectively as possible.
Lean process improvement starts with the customer: it first tries to define value, and then creates processes that best cater to it while keeping resource and time consumption down to a minimum.
Since consumer requirements and demands are constantly changing, lean process improvement treats all associated business processes as evolving entities rather than fixed constants. Managers must strive to continuously find ways to deliver greater value by reducing the number of steps required to do so.
Here’s an awesome video that showcases how lean process improvement works by using a house construction project as an example:
Even though process improvement has been part of business management for some time now, lean differs from other methods in one key way.
Standard business process management sees each department as part of a whole and optimizes them one at a time. Standard initiatives also treat process improvement as singular tasks that are carried out if necessary.
Lean process improvement techniques, on the other hand, see the entire value chain as a continuous flow, like a river. The departments are treated as tributaries feeding into the river, which ultimately leads to the market.
The emphasis here is to remove as many impediments as possible. In a true lean process, all actions have to add value to the final product. To this effect, a company committed to lean processes must strive to reduce costs, including labor, time, space and capital.
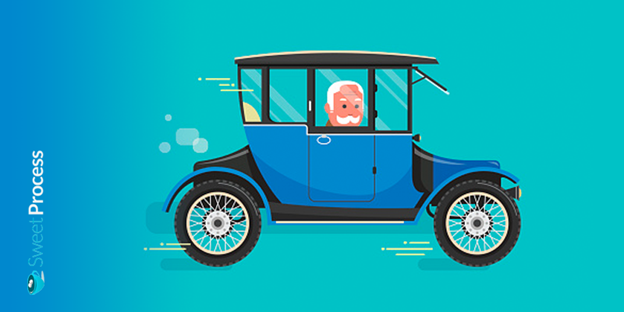
Lean philosophy owes its origins to a number of different methods, all spread out over the last century. While Ford and Toyota are generally considered the pioneers of lean manufacturing (and rightfully so), we can trace the idea back to mid-15th century Arsenal, Venice.
Established in 1104, the Arsenal was tasked with producing hundreds of ships for the Venetian Navy during its Mediterranean campaign. The shipbuilders came up with the idea of using interchangeable parts that could be used in different classes of ships, greatly speeding up the overall construction.
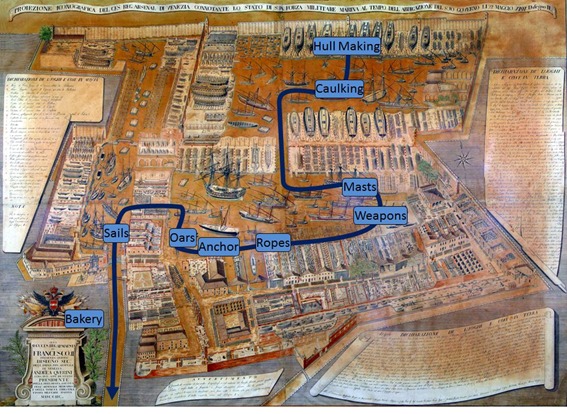
Galleys were assembled and then (literally) flowed along a channel where each department added its output. By the next century, the Venetian Arsenal had become so efficient at shipbuilding that it could finish an entire galley within an hour. Other countries soon began emulating their methods and flow-based production became common practice.
Although advanced for its time, the Venetian process was held back by the tools of its time. It wouldn’t be advanced further until the early 20th century when Henry Ford applied it to his automobile manufacturing efforts.
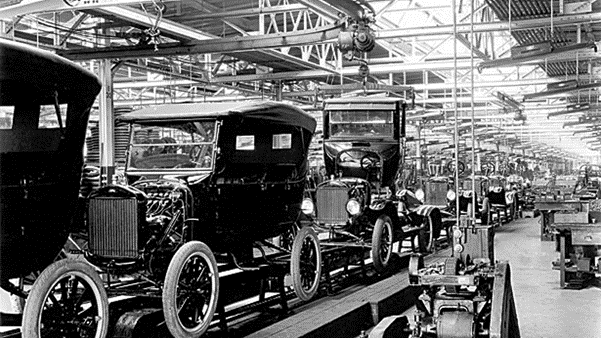
In 1913, Ford combined interchangeable parts with standard operating procedures, all working on a conveyor belt, which we now call an assembly line. Ford departed from the tradition of using general purpose machines, which created parts that had to be cut, grinded and hammered into place by technicians.
Instead, he came up with specialized machines that made perfectly fitting parts that could be put together with minimal revision. The machines were installed in strategic locations along the production line to bring down time and cost. Instead of the hours or even days it took for parts to reach the assembly lines before, Fords usually took a few minutes.
Even though Ford had revolutionized car manufacturing, his methods were limited to singular models with minimal optional features. He could also only make them in one color, hence his famous quote: “You can choose any color as long as it’s black.”
While Ford was busy revolutionizing the automobile industry, there was another silent movement in the works. Sakichi Toyoda , the son of a farmer and successful carpenter in Japan, had founded Toyoda Loom Works, which manufactured weaving machines.
A prolific inventor, Toyoda had come up with a loom that would automatically stop when a yarn would break. This was the first instance of industrial automation (or jidoka) that would define much of the 20th century.

In 1937, Sakichi Toyoda’s son, Kichiro Toyoda, founded the automotive division of Toyoda Loom Works, which we now know as Toyota Motors. Kichiro brought Ford’s assembly line to his father’s jidoka philosophy. But he went further.
Being obsessed with process refinement, he created kaizen ( continuous improvement ) workshops to eliminate muda , or waste, from the company processes. Toyoda identified seven types of muda that the company should look out for (more on this later).
Following the Second World War, the demand and resource crunch in Japan meant that Toyota couldn’t afford to have product defects corrected post purchase. The company began to aggressively push for eliminating product problems during production.
In the 1950s, Kichiro Toyoda stepped down as chief executive and was replaced by Taiizo Ishida who, with the help of Eiji Toyoda (Kichiro Toyoda’s cousin) and Taichi Ohno, reorganized the company. They introduced the just-in-time manufacturing method, which uses real demand to determine production rather than forecasts.
It took over a decade for Toyota to refine and implement its ideas across all its factories. Now known as the Toyota Production System (TPS), the techniques have been modified and used across a variety of industries like health, FMCG, IT, oil and gas, and more.
The word “lean” itself wouldn’t be coined until 1991, when it was first used in the book The Machine that Changed the World by Daniel T. Jones, James P. Womack, and Daniel Roos of MIT.
Even though focused heavily on TPS, lean isn’t restricted to it and can encompass any philosophy, technique, or technology that eliminates waste and promotes systemic efficiency.
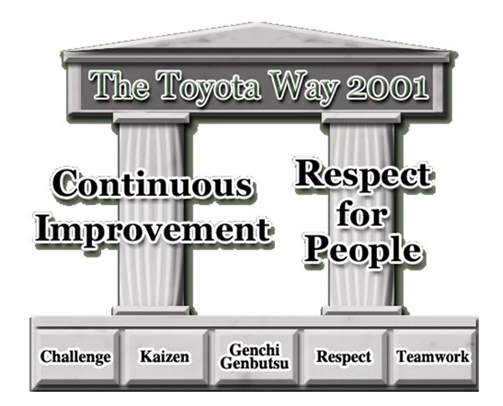
One criticism the book directed at TPS was that Toyota’s ideas were more concerned with economic progress and efficiency, with little regard for the people who enabled the processes. Toyota addressed these and more concerns in a new manifesto titled The Toyota Way 2001 which declared continuous improvement and respect for people as its two main pillars.
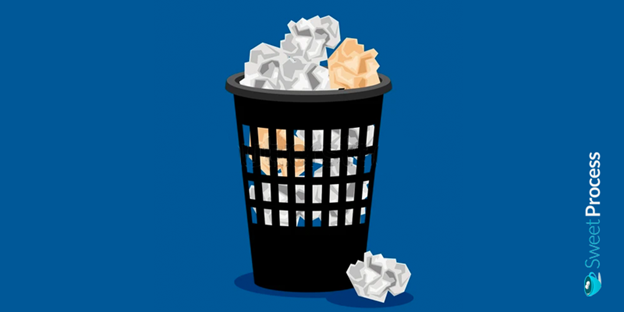
Waste reduction is what TPS or any lean system is built around. Three types of wastes are identified in Toyota philosophy:
- Muda : Pure, or lean, waste. Muda is any waste that can be quantified and uses up resources.
- Mura : Waste caused by unpredictable or chaotic processes that lead to uneven production.
- Muri : Waste due to overburdening either people, machines or processes.
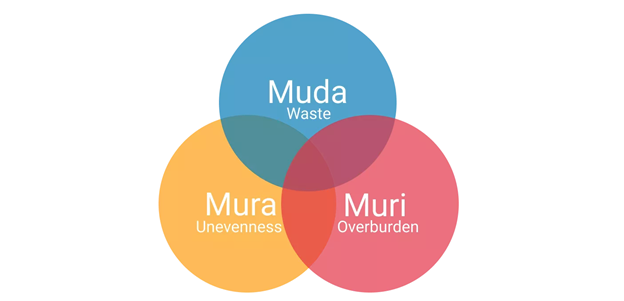
Even though Toyota has stuck with seven types of wastes , other methods have broken its categories down still further.
Muda distinguishes between necessary waste, or non-value adding processes that cannot be avoided, and pure waste, which are processes that can be safely eliminated. TPS identifies seven types of wastes , plus one that was added later:
Defects require significant resources and time to fix if they are discovered after the customer has purchased the product. A defective product may lead to complaints, expensive recalls, unpredictable inventory, and can damage your company’s reputation.
Reasons for defective products include poor design, bad material selection, improper documentation, lack of skilled workers, and large variety in inventory. Defects are best detected during the production process.
Defects can occur because of:
- Ineffective or incoherent processes.
- Too many product redesigns.
- Bad quality control.
- Lack of process and procedure documentation.
Overproduction
When a company over-produces unneeded items, they clog up the supply chain and cause downtimes. Overproduction also leads to inventory swells which can cost a lot to maintain and cause more work than needed. Since oversupply puts pressure on manufacturing, product defects may multiply and go unnoticed.
Overproduction is typically caused by:
- Not understanding market demand and poor forecasting.
- Not knowing how much surplus inventory the company can realistically keep.
- Having one manufacturing unit be more efficient/productive than its dependents down the value stream.
- Using inefficient production processes.
Overprocessing
A company’s overprocessing if its value delivery systems have more steps than needed. Compared to other errors, overprocessing is more subtle and can creep in unexpectedly.
The only way to avoid overprocessing is to have a thorough understanding of your customer’s demand. Working backward from your customer’s requirements can help you identify useful and wasteful processes.
Excessive processing can come in the form of:
- Manual invoicing when automation is available.
- Using items with precision or capacity not needed.
- Over-analyzing processes.
- Adding more features in a product than needed.
Moving stuff and people around costs money and time. Even the most trivial of movements can add up to significant volumes of work that amount to nothing, leading to waste. In lean philosophy, motion refers to any movements or actions carried out by people, equipment or machinery.
Process mapping can help you understand all aspects of work done within your company’s premises. Optimal facility layout can promote efficient movements that help shorten gaps between manufacturing and assembly areas.
Essentially, proper space utilization can help a company leverage its resources to the fullest, which is what reducing motion waste accomplishes.
Motion waste can be caused by:
- Inefficient workspace layout.
- Poor production planning.
- Long production processes.
- Shared resources.
- Lack of communication.
Transportation
While motion covers transportation as well, lean is a category in itself. Transportation waste can occur between production units, factories or facilities located between states and countries. Think of it as a macro-version of motion waste.
Transportation waste can cause excessive fuel consumption, lead time delays, poor supply chains and wasted man-hours. Value stream mapping can help overcome transportation errors by identifying routes that can be shortened or by moving facilities to more optimal locations.
Transportation errors can be caused by:
- Different production speeds between multiple facilities.
- Sending goods through high-traffic areas.
- Large order volumes that the company’s delivery systems cannot handle.
- Multiple storage locations.
Sufficient inventory is required to not only fulfill existing orders, but cater to expected ones as well. However, maintaining inventory comes with its own set of costs. From renting storage facilities to electricity, movement, and asset value depreciation all need to be factored in before deciding how much inventory is needed and at what levels it will be considered a waste.
Inventory waste can come in the form of parts waiting for assembly, excessive work in progress, or even products waiting to be shipped. Unwanted inventory can be an offshoot of overproduction or overprocessing and requires keen insight into customer demand, market dynamics and process efficiency to be eliminated.
Key reasons for excess inventory include:
- Excessive buffer stock to meet unrealistic forecasted demand.
- Needless features in products requiring more parts.
- Unpredictable transportation.
- Defective parts and/or products.
Idle time is time a company is paying for but not getting any output from. Suffice to say, waiting can quickly become very costly if left unchecked. Time-based wastes can happen either if people are waiting for parts to show up at their workstations, or if machines are sitting unused.
Waiting isn’t a problem in itself. It is a symptom of other systemic problems. It can occur because of:
- Poor transportation networks.
- Over- or under-production.
- Long or inefficient processes that don’t flow well.
Unused talent
Besides the seven traditional wastes that lean process management deals with, wasted talent was added later to account for unused skills. When employees possess skills that aren’t utilized, companies fail to harness their workforce’s full potential, leaving potential ideas and earnings on the table.
By leveraging each employee’s talents to the fullest, companies can find new ways to provide value, cut waste across the board and enable organization-wide growth.
Some symptoms of unused talent are:
- Excessive hierarchy, leading to a stifled work environment.
- Poor communication between management and workforce.
- Lack of or one-dimensional performance evaluation.
- On-ground staff not being incorporated into company decision making.
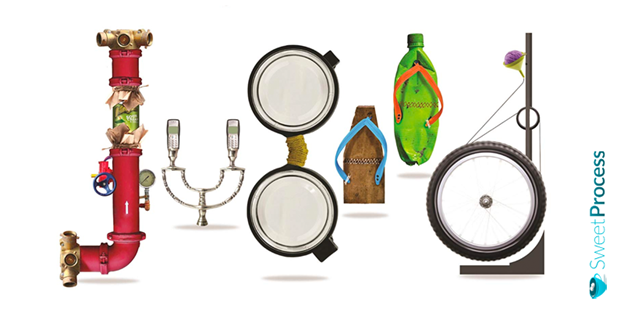
Toyota, Ford, et al. may have created a formalized structure in which to study and implement lean processes, but the idea itself is rather fundamental. Being scrappy and doing more with less is something cultures across the world expound and examples can be seen in our daily lives. Many such cultural artifacts have taken on lives of their own and have become informal problem-solving structures.
It’s important to note, however, that while such quick problem-solving methods are directed at the same goal that lean process improvement is, they both are fundamentally different.
While lean attempts continuous improvement through efficiency, informal problem-solving usually is more myopic and deals with the here and now with little regard for how the solutions may play out over time.
That being said, informal problem-solving still serves as a valid reference point to illustrate how effective lean can be. Some of the most popular such examples include:
Jugaad (India)
The word “jugaad” is a Hindi word that most Indians are well familiar with and refers to innovative solutions implemented with limited resources. Essentially, a jugaad is any solution that bends the rules, gets things done and almost always uses items that were never intended for the problem they are used to address.
Even though the philosophy of jugaad is commonplace in India, the COVID-19 pandemic really took it to the next level. People began to find novel ways to get through their day while maintaining social distancing.
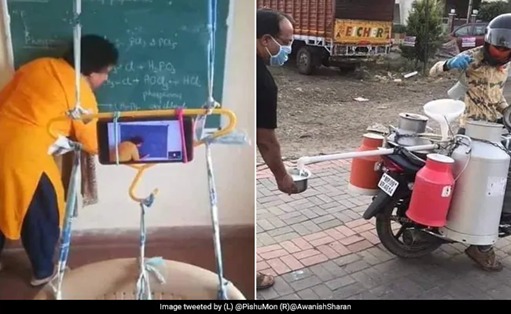
As it exemplifies resourcefulness and creativity, jugaad has jumped from being a simple streetsmart way of solving problems to a management principle. It has even been used to create highly resourceful and efficient enterprises.
The Dabbawalas, which is a social enterprise in Mumbai dedicated to helping people get fresh home-cooked meals at their workplace, is one such example. The service used a network of more than 5,000 children who delivered 200,000 food boxes per day without any IT infrastructure or fixed transportation methods. Forbes magazine awarded the Dabbawalas its Six Sigma certification in 2001 for their efficiency and accuracy.
Jury-rigging/Macgyvering (USA)
Jury-rigging started off as a verb in the navy during the late 18th century. When a ship was dismasted, a replacement mast was installed instead. Sometimes, items other than a mast, like a spar, or spinnaker pole, had to be used if a main mast wasn’t available. The term jury-rigged thus caught on as a verb for makeshift repairs or built using unorthodox methods.
Jury-rigging has become synonymous with creative problem solving using everyday items. Nowhere was this more visible than in the 80s television show MacGyver in which the protagonist used everyday items to create improvised but effective solutions.
So popular was the show and its fundamental premise that “macgyvering” became a part of the English lexicon, meaning simple, elegant solutions for complex problems using everyday resources.
One of the best examples of macgyvering happened before the show even went on air during the Apollo 13 mission . The doomed spacecraft made it back to Earth primarily because of ingenious improvisations that the engineers at NASA and the astronauts came up with.
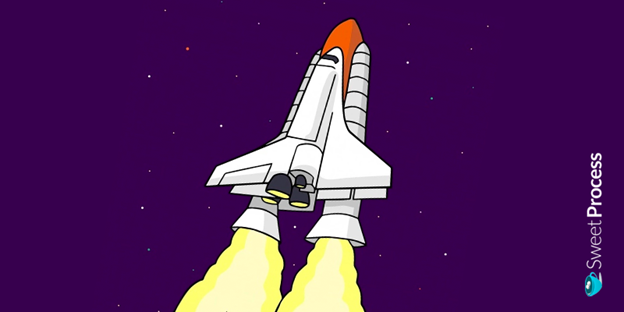
In one instance, when CO2 levels began to climb in the command module, the astronauts (under the instructions of the engineers at Houston) made a CO2 scrubber from duct tape, plastic bags, hoses and flight plan covers.
Life and productivity hacking has been an internet staple for over a decade now. “Hacking” essentially means using everyday items in creative new ways to get more value out of each resource. The idea quickly caught on and soon enough, we had thousands of hacks pouring in from all over the world.
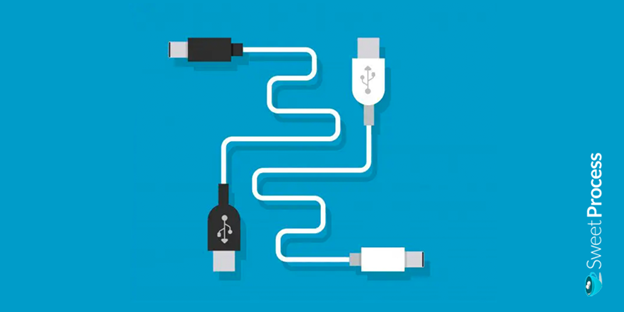
While quite clever and productive from a lean perspective, they work at the top of the funnel. Ideas such as these are what kaizen workshops attempt to come up with.
However, such solutions only make sense if they can be turned into procedures, policies and processes that consistently add value to a company’s supply chain in some meaningful way and can be built upon in the future.
Let’s take a look at some of the most popular lean process improvement models currently being utilized that you can use to turn your company’s ingenuity into productivity.
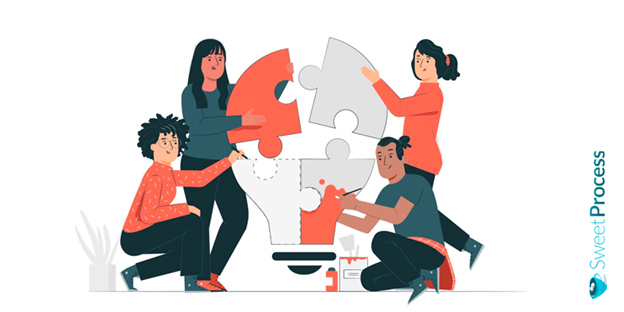
The Toyota Production System has led to a number of different productivity models over the years. While some are part of it but have evolved into separate process refinement tools, the TPS has also inspired new paradigms that have become very successful.
Just-in-Time (JIT)
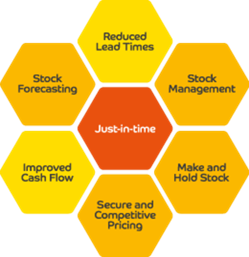
JIT applies the lean principle to inventory management. The core concept in JIT is to bring in raw materials from suppliers only when they are needed, thereby reducing warehousing and transportation costs.
The core objective of JIT is to promote efficient flow of raw materials, but it carries significant risk as well. A good example of JIT manufacturing is a company that makes bespoke custom shoes. Since the shoes are made after a customer places their order, the company can buy materials and parts from its suppliers post purchase.
Implementing JIT in mass manufacturing is a lot trickier though. Since only enough raw material to meet demand is to be stored, accurate sales forecasts and good vendor/client relationships become central to implementing JIT. While Toyota popularized the idea, the company still took over 20 years to perfect JIT.
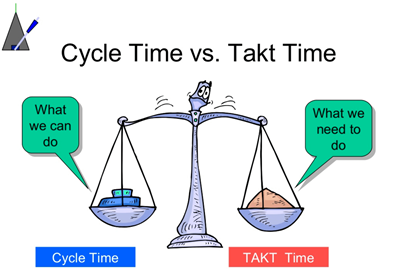
Closely related to JIT is takt time , which is a management tool used to measure the time interval between the start of production of one product and the start of production of the next. In Japanese, takt time is referred to as Takuto Taimu , which is borrowed from the German word Taktzeit , meaning cycle time.
Takt time is calculated by dividing the total time available for work divided by the number of products demanded. For example, let’s assume a customer places an order for 40 products in a week. If the company has a 40-hour work week, then it has one hour to complete each product.
Before settling on an ideal takt time, the company must also factor in machine downtime, transportation time, and process-related problems. If a company is providing parts to multiple assembly lines, then each line can have its own takt time depending on demand.
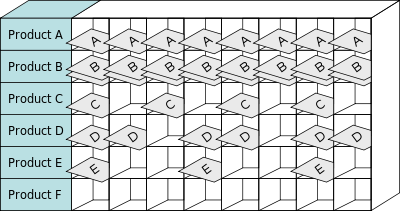
Heijunka means leveling in Japanese and refers to flattening the production curve to more manageable levels. A fundamental tenet of TPS and lean manufacturing, Heijunka primarily concerns with mura waste in lean. It attempts to remove uncertainty from production caused by a dynamic market, varying amounts of time taken to produce different parts, and human errors.
An example of Heijunka: let’s say a company consistently receives 400 orders from a customer every week. The weekly tally includes 100 items on Monday, 50 on Tuesday, 50 on Wednesday, 150 on Thursday and 50 on Friday.
While matching the daily production output to the orders may seem efficient, it also leads to uneven production throughout the week. The company may instead choose to produce 100 items every day Monday through Friday and meet its weekly production quota more evenly.
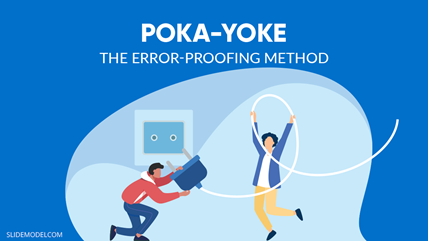
Another product of TPS, poka-yoke was coined in the 1960s by Toyota engineer Shiego Shingo. Initially, the term was boka-yoke, meaning fool or idiot-proofing, but was later changed to poka-yoke given the former’s derogatory implication.
Poka-yoke encourages people to learn from their mistakes in order to make successive attempts more efficient and productive. The product and production system are then redesigned to address those errors right at the start. In this sense, poka-yoke serves as a behavior-shaping constraint, and is central to TPS as it leads to better output at a faster rate.
A car with a manual transmission in which the clutch needs to be pressed before it can start to avoid any unwanted jumps or movement if it was in gear is an example of poka-yoke in action.
Likewise, microwaves and washing machines requiring the door to be closed before they can start, magnets in a grain processing plant and light curtains in factories that switch off dangerous machines when someone is near are all examples of poka-yoke .
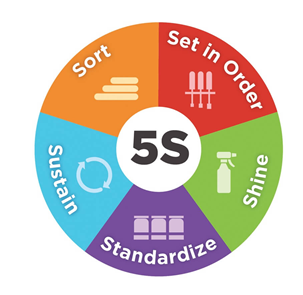
5S is a lean methodology that tries to create a safe, organized and uncluttered workspace. Its driving rationale is that an organized work environment leads to higher productivity and lower waste. The 5Ss’ stand for the five principles of organization, each of which starts with an S.
- Seiri : Which means to segregate needed tools and parts from unneeded ones.
- Seiton : Meaning to organize all the parts and tools for easy identification and use.
- Seiso : Means to clean up after a work is finished.
- Seiketsu : Which means to carry out seiri, seiton, and seiso every day to keep the workspace clean.
- Shitsuke : Meaning to strive to create a habit out of each of the four Ss’.
5S examples in the workspace include color-coding tools to make them easier to find, organizing all the tools in kits for easy reach, and floor labeling to direct workers to the right stations.
A Japanese term meaning “continuous improvement,” or “change for the better,” Kaizen is the core philosophy of TPS. Through Kaizen, a business can progressively become better and more efficient over time by learning from its mistakes, creating better processes and removing waste from its value chain.
Instead of going for massive, sweeping changes at one go, Kaizen focuses on small, incremental improvements that snowball into bigger refinements. The philosophy states that there is no end to perfection and that any process, no matter how efficient currently, can be improved upon. To this end, Kaizen requires top-to-bottom involvement, personnel discipline, teamwork, good morale and a commitment to quality.
Kaizen typically uses PDCA (plan-do-check-act) cycles to achieve its end. The company starts by planning the change process and letting everyone know how it will play out. The changes are then implemented and checked for results. If the outcome is satisfactory, the act stage turns the changes into standard practice.
Lean Six Sigma (DMEDI)
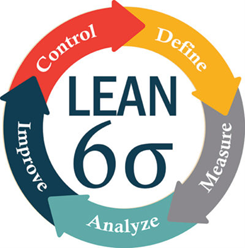
The above-mentioned lean process improvement methods are an integral part of the TPS. Six Sigma, on the other hand, offers a counter approach to lean. Instead of targeting waste as traditional lean process improvement does, Six Sigma is more concerned with removing process variations and reinforcing process control through data-driven methods.
The idea behind Six Sigma was developed by the American physicist and statistician Walter Shewhart who based it on the work of German mathematician Carl Fredrich Gauss. As per Shewhart, Six Sigma implies where a process needs to be improved.
The objective here is to bring an operation up to a six sigma level. Any operation that deviates three sigmas from the mean needs to be improved with one sigma being one standard deviation. A six sigma performance level can reduce defect rate to 3.4 errors per one million opportunities.
Over time, lean and six sigma have been combined to achieve even better results. Lean Six Sigma therefore uses the best of both methods and offers a greater variety of tools to clean up your processes.
Lean six sigma is also known as DMEDI, which stands for:
- Define : The problem is defined by identifying processes that deliver value to the client.
- Measure : Metrics required to measure the effectiveness of solutions are decided.
- Explore : Potential solutions are proposed and explored.
- Develop : The most viable solutions are developed and tested.
- Implement : Refined solutions are implemented.
Ford 8D Method
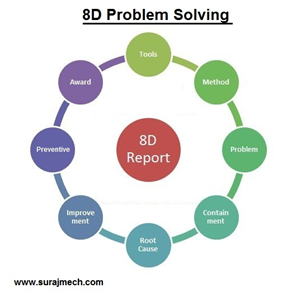
Ford’s 8D, or Eight Disciplines approach, has become a close contender to TPS and Six Sigma in its own right. The framework uses a set of eight steps to ensure continuous lean process improvement.
The eight steps are:
- Create a specific team for the problem : The team can span different departments and is usually disbanded once the problem is solved.
- Describe the problem : The team analyzes the problem and defines it as well as the scope of the solution.
- Take interim corrective action : While a long-term solution is found, a short-term work around is devised to keep the problem at bay.
- Analyze the root cause : The team then drills deep into the problem’s root cause(s). Tools such as the 5 Whys analysis, Fishbone diagram, Pareto charts, and failure mode and effects analysis (FMEA) can be used here.
- Come up with a permanent solution : Based on the root cause analysis, the team can then draw up prospective solutions to address the problem.
- Implement the solution : The team’s theories are put to the test as their planned solutions are implemented. Corrective actions can be taken if new insights are discovered.
- Prevent the problem’s recurrence : Part of the devised solution should be a strategy to preempt the problem should it occur again.
- Close the project and recognize the team’s contributions : Once the problem is suitably addressed, the team’s efforts are rewarded.
Obviously, lean process improvement has many dimensions, most of which won’t be useful to your organization. Let’s take a look at how you can implement these ideas.
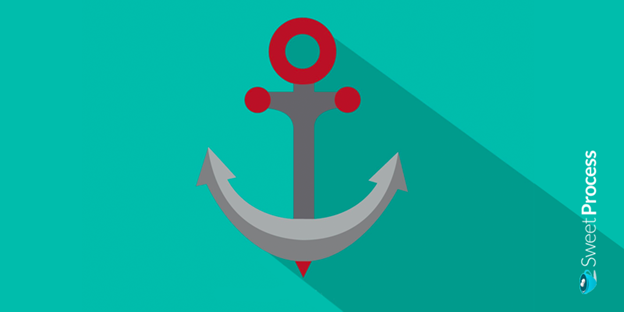
Statistical analysis of value chains and process development have resulted in a lot of data supporting lean process implementation. Even so, they really are only as good as the structures supporting them. The above sections only cover processes, which are one of three anchors that lean methods require.
No amount of clever planning and analysis can make up for poor stakeholder buy-in. Since lean requires constant review and refinement, employees have to get used to the idea of regular change, which is hard.
There are a few things you can do to get your team on-board with your plan:
Be honest from the start : The worst thing you can do is to try and convince your team members that your ideas are the best. Instead, simply share the data, along with your insights with them, and let them come to their own conclusions. If you did a good job building an accurate picture of the problem, most of your team members will agree with you.
Be empathetic : Any change will cause some upheaval downstream. Consequently, some people may be reassigned while others will have to be let go. We’re trying to trim the fat off, after all. But being blunt can have the opposite effect. Instead, try to present the solutions from the employee’s perspective.
Hire based on your company goals : While your processes may change over time, your goals are bound to remain the same. Hiring employees who share your core values and goals will help you get better buy-ins later on when implementing lean processes.
Communicate persistently : Any change initiative shouldn’t come off as a sudden move. Your staff members should always be aware of the problems that are cropping up and what you’re doing to address them.
Make your staff responsible for the change : If your own staff members come up with workable solutions, then you won’t need to convince them. This ties into better internal communications as well. The more informed your staff is, the better solutions they will be able to propose.
We’ve already discussed process analysis and improvement methods above. However, it is important to note that your processes are part of a flow and not discrete entities. Indeed, your entire organization is best looked at as one giant process which delivers value to the end customer.
Many opportunities to affect lean processes are borne out of new technologies and tools that allow for more efficient actions. For example, the advent of cloud-based productivity tools have enabled people to work remotely, making office spaces and associated IT infrastructure (partially) obsolete. These tools allow for companies to create the same value at a much lower cost making them ideal for lean process improvement.
Keeping your ears to the ground and looking out for new tools can help you lean-out your enterprise before your competitors. The best way is to stay up-to-date on all news regarding your industry and associated technologies.
Listening to your staff members and other stakeholders can also prove invaluable here. Chances are, someone has come across or is actively using tools that others in your company can also benefit from. Regular communication between management and staff can help you discover new tools and techniques regularly.
Check out our top five suggestions below:
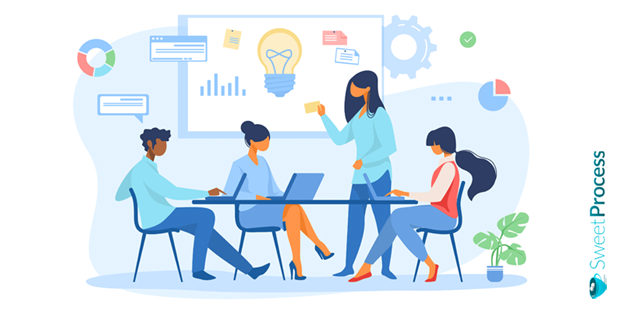
Since lean management has been written on at length, there are many opinions, tools, techniques and styles that you can opt for. But that’s what makes lean process improvement so challenging. It’s often hard for management to decide where to begin, which tools to use and which lean concepts to ignore. Here are some ideas to help you turn the ignition on your first lean project:
Start by documenting your processes
You can only improve upon your existing processes if you know where you’re going wrong, and where you have potential for improvement. Even though manual process documentation is the norm (and serves as a viable backup), we suggest you try cloud-based process management tools. These are far more flexible and allow for greater collaboration. Tools like SweetProcess can even turn processes into checklists that can be assigned and tracked by a manager.
Pick one process at a time
Even though lean concerns itself with organization-wide process flow, it’s best to restrict your focus to just one process . Doing so will help you gain a better understanding of how lean works and will keep things manageable.
Ideally, the process you choose should be one that:
- Has significant and continuous work-in-progress.
- Is failing to achieve takt time.
- Is unable to achieve a Six Sigma rating.
- Is proving to be unreliable.
- Is directly affecting consumer sentiment.
It is entirely possible that multiple company processes may check many of the boxes. In such a case, go with the most critical process. For example, if you identify problems in marketing and end-product transportation, then transportation should take precedence since it is required for order fulfillment.
Involve your on-ground staff in identifying problems, Kaizen opportunities and solution
This point can’t be stressed enough. Often, managers can end up with a theoretical understanding of the problem. In this case, making the frontline staff responsible for documenting problems and coming up with solutions can greatly speed up error correction.
Some ways to help you get everyone involved are:
Install suggestion boxes : Collect anonymous as well as signed feedback forms.
Employee surveys : Using emails and feedback forms to get feedback from employees is also a great way to gauge everyone’s mood and get them to share their ideas.
Encourage team meetings : Each team can have its own Kaizen workshops to identify opportunities to lean out its processes. Here’s a great video on how to conduct a Kaizen workshop.
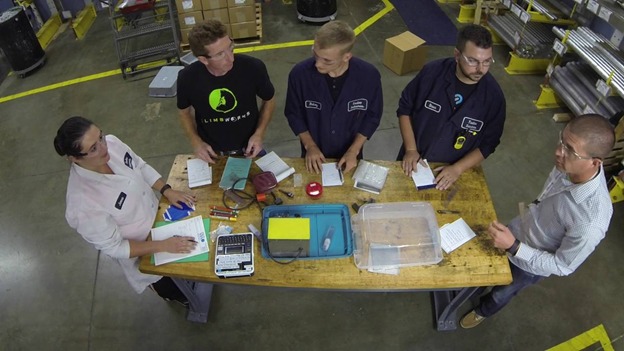
Reward great ideas : Recognizing the people who came up with the winning solution motivates each team member to do the same. Recognition can create a Kaizen culture where people start to think out of the box automatically, helping the company grow faster.
Arm them with the right tools : Modern cloud-based productivity and process documentation tools can make lean process implementation easier for everyone involved. Check out the section below for more on this.
In many ways, the latest crop of cloud-based productivity apps are the most lean thing to have happened to modern industry. They allow people to collaborate better, make distances irrelevant, enable better task tracking, and allow companies to keep all its information in one place.
Check out the following continuous improvement software that can help you launch and stay on top of your lean process improvement initiatives:
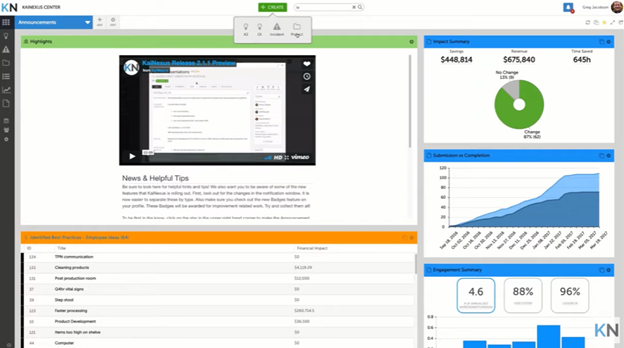
Features : Focuses on creating a Kaizen culture, highly flexible, software can be tailored to each company.
Price : Upon request
Free demo : Yes
Kainexus was founded by Dr. Gregory Jacobson and Matt Paliulis as undergrad students at Washington University. During his tenure at Baylor College of Medicine, Greg constantly came across processes that could be improved upon, but was frustrated by the lack of tools that could help him track his progress.
Greg and Matt thus started working together on a tool that could help healthcare companies improve their processes and so, Kainexus was born . At the core of Kainexus is the belief that every employee can help improve a company. Since it’s the onground employees who create outcomes, involving and empowering them helps the company grow.
The software is designed around maximum process visibility and collaboration. After login, you’re taken to a dashboard where you can manage all your activities. On the top is a notification bar that lets you know what everyone else is doing.
Kainexus makes lean process improvement a breeze. The software hits all the right notes as it focuses on creating a culture rather than just enforcing processes. It does so by involving as many people as possible. One of the main windows that managers can see in their dashboard is the engagement summary that reports how many people logged in, improvements contributed by each person and percentage of system used.
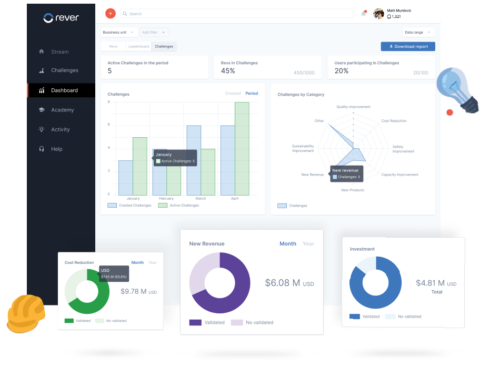
Features : Employee-centric design makes capturing new information easy, and the intuitive dashboard lets managers keep track of all Kaizen initiatives.
Price : Starts at $5 per person per month
Free trial : Yes
Reverscore presents itself as a frontline operations platform that empowers workers to create continuous improvement in their own specialized domains. In other words, the developers at Reverscore have taken an inverted pyramid approach to lean and Kaizen.
While the software allows management to keep a powerful, real-time track on all activities, the core emphasis is on helping employees do their best work and capture their experiences, much like IOT captures machine data.
Reverscore takes advantage of the fact that every worker today has a smartphone, which can enable them to share their ideas as well as track and report their progress in real time.
Employees can quickly take pictures or snapshots of events as they happen and share them with their team and manager through their software called Rever . The team can then discuss potential solutions and advise the employee on how to fix the problem. If found effective, the solution can be rolled out to other, similar departments.
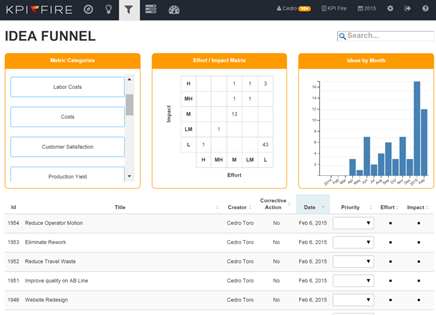
Features : KPI focused, makes tracking individual tasks easy, very minimalist design helps managers track progress better.
Price : Starts at $20 per feature per month
KPI Fire isn’t a Kaizen-based continuous improvement tool per se but it fits perfectly in any such project. The tool is designed to create and track KPIs, which is central to any lean process initiative.
KPI tracking is fundamental to lean in a few key ways. Firstly, since new initiatives often require new KPIs, it’s hard to know which ones are worth tracking and which ones you should ignore. KPI Fire can make quick work of this problem. Secondly, keeping track of KPIs is hard enough for employees to keep track of since it’s all too easy to get so caught up with day-to-day tasks that they don’t realize when they’ve gone astray. Again, a tool like KPI Fire can help them stay on track through completion.
To ensure no one is distracted (not even by the software), KPI Fire has a very simple interface that can be made to only show KPIs and their completion rate.
SweetProcess
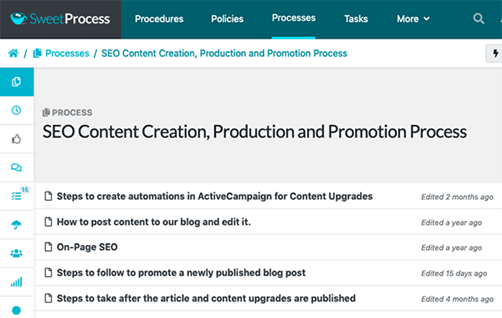
Features : Makes process documentation a breeze, each process can be turned into trackable checklists, powerful tracking features.
Price : $99/month for up to 20 members plus $5/month for every additional user
Free version : 14 days
Process improvement can only be done after process mapping . The more detailed your process documentation is, the more fine your refinements can be. While the above-mentioned tools can help you review your processes and even get everyone involved, their primary focus is on improvement.
SweetProcess is a process documentation tool that helps you get all your company’s process, procedure and policy know-how under one roof. All of these can also be organized, distributed and tracked by managers, team leaders, and employees through an intuitive interface.
Part of the reason why lean process improvement is so hard is that employees cannot capture real-time data or personal experiences on the fly. So, if an employee discovers new insight on the job that can add to the process, then they can edit the required checklists right there.
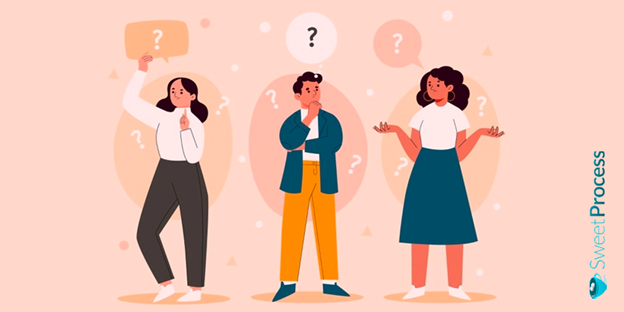
Leaning out your company processes can be interpreted in different ways by different stakeholders. More often than not, people feel they are being audited, or fear any changes that may happen as a result.
It is therefore vital to clear any misconceptions before you get started through a well-thought-out communication campaign. Consider the following.
It’s a one-time thing
Any improvement initiative runs the risk of looking like a “project.” And projects have start and end dates. It is therefore very easy for stakeholders to feel that your lean initiative is something they just have to get over with.
At the heart of lean thinking is the belief in continuous improvement. Even though each improvement does come in the form of small projects, they should in no way be treated as final. Each Kaizen project, if successful, should be built upon and improved further.
It’s all about cost-cutting
Lean process improvement does result in better savings as fewer resources required means less money spent, but that’s not its objective. Lean is primarily concerned with delivering better value to the end customer while reducing organization-wide waste. Bringing down operation costs is best looked at as a symptom rather than a goal here.
It only applies to manufacturing
Lean process thinking certainly has its roots in manufacturing, but since it’s primarily a philosophy, it can be used in virtually any industry. Even the tools can be applied with some modifications.
For instance, inventory waste in the case of marketing will be any assets and collateral that were developed but are sitting unused. Likewise, overproduction in software engineering will include any unnecessary product features. Software bugs can similarly be classified as defect waste.
It’s usually just a quick fix
Quick fixes have their place, and may even serve as a Kaizen inspiration, but they aren’t all there is to process improvement. If the improvement is time or location-specific and serves no value as an addition to the value chain, then it may be discarded.
The Apollo 13 example given earlier illustrates this point well. The astronauts had to make a crude CO2 scrubber out of things they had available. However, that doesn’t mean their method will become standard practice.
It standardizes work that takes away creativity
If anything, lean process improvement is all about enabling creativity which is foundational to Kaizen philosophy. The guiding principle is to turn great ideas into muscle memory, which is where standardization comes in.
An organization committed to lean processes will democratize ideation and encourage its workers to come up with unique solutions. However, that also means that most ideas won’t make it to the top.
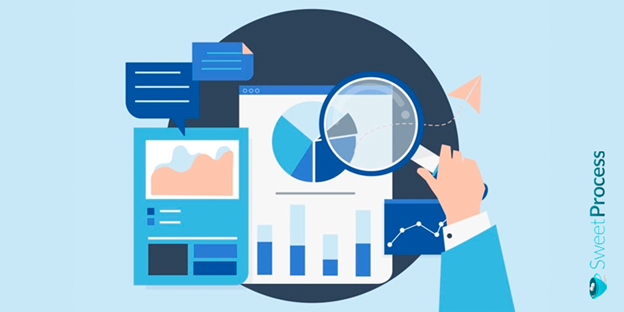
Organizations have come up with creative ways to make lean process management work for them. Here are three such examples that show how lean methods can help companies grow:
The Power of Streamlining Business Operations
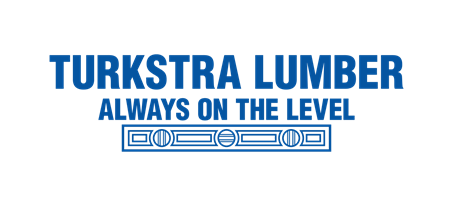
The Turkstra Lumber Company has been providing lumbering services to the Hamilton and Niagara regions since 1953. A family-owned business, the organization already had its processes and procedures down pat.
But Jamie Ramsden, business intelligence officer at Turkstra, saw the company could do a lot more by adopting some modern practices and streamlining its operations. The biggest pain point that Ramsden identified was that even though the company was working just fine, the operations weren’t as coordinated as they could have been.
A lean Six Sigma champion, Ramsden began exploring ways to implement modern lean methodologies to Turkstra’s management. Even though Excel Sheets proved to be helpful and the results were satisfactory, it proved to be a very top-down way of doing things with no feedback going back up.
Ramsden decided to use SweetProcess instead as he needed a tool that could enable more real-time collaboration and collect all their documentation in one place. His efforts paid off handsomely as his team now has perfect visibility into their day-to-day activities and can communicate seamlessly with each other.
Process Simplification Can Enhance Business Sales
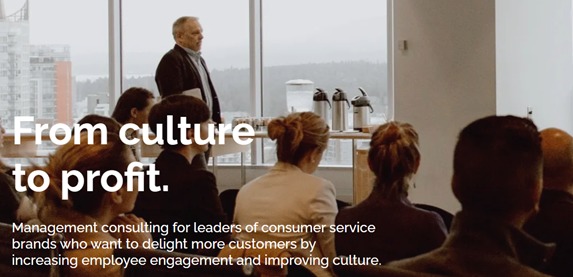
Processes in manufacturing are easy to understand since they are machine-driven. But how do you implement lean methods in a company that is almost entirely people-based? This was the challenge facing Rhys Green, CEO at TrailBlaze Partners, a business management consulting firm.
Mr. Green recalls one of TrailBlaze’s clients, 1-800-GOT-JUNK?, which helps remove unwanted material from people’s properties. 1-800-GOT-JUNK? had to deal with a lot of different people and the stuff they came across didn’t always fit in nice little boxes.
TrailBlaze experimented by first using plastic boxes, but then moved to reusable boxes to help simplify their loading and unloading process. But the most important change was cultural. The company simplified its customer-facing operations by making all interactions easier.
1-800-GOT-JUNK? went from a couple of million dollars a year business to over 100 million a year over the course of five years.
Transparency Promotes Efficiency
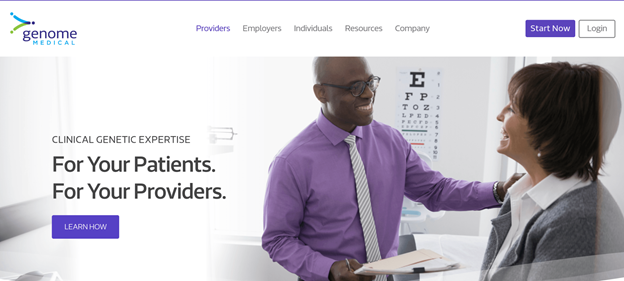
As the COO at Genome Medical, Kristin Ashcraft knows that their clients approach them for their commitment to quality, science-based healthcare. But she was also fully aware that trust in healthcare primarily comes from transparency.
Given the incredibly complex nature of genetic science, everyone from the customer to the team needs to have a clear understanding of what is required and what’s realistic. Ms. Ashcraft therefore focused heavily on increasing transparency throughout the company.
Not only did she build new processes by securing buy-ins from everyone involved, but also enhanced existing methods to create even better value for the end customer.
One of Ms. Ashcraft’s key goals was to ensure the company understood the before and after scenarios following a process overhaul. This was important to help the team members understand the importance of regular process reviews and improvements and, in turn, promote stakeholder buy-ins.
Many of the work cultures and methodologies becoming popular today are inspired by lean process improvement. BYOD, remote-working and shared office spaces are all examples that are firmly grounded in lean thinking. All of these try to remove waste from a company’s value creation process.
However, it is important to recognize the fact that what is now considered waste in lean was an important value-adding asset before new technologies made them irrelevant. This is why constant review of company processes in relation to new developments is so critical. As better methods and tools are proposed, tested and rolled out, older models will naturally become obsolete.
SweetProcess allows you to make just such a review of your existing processes. A cloud-based process documentation software, SweetProcess is designed around maximum collaboration and transparency. We offer a 14-day free trial , no credit cards required, so feel free to sign up and check it out.
Also, keeping track of available opportunities vis-à-vis your own goals and processes that can be hard, especially since you have to keep at it regularly. We’ve put together a questionnaire that you can use to help find process waste in your organization, while also helping you identify competitive and technological opportunities before your competitors.
Download our questionnaire here:
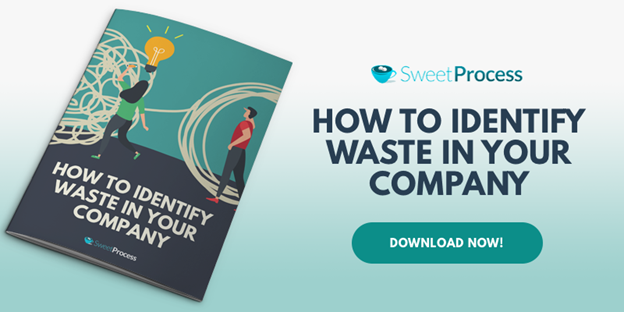
Related Posts:

Get Your Free Systemization Checklist

Leave a Reply Cancel reply
Your email address will not be published. Required fields are marked *

- > Business Process Improvement Examples: 34 Actionable Ideas
Business Process Improvement Examples: 34 Actionable Ideas
Posted by Matt Banna
Aug 28, 2023 10:50:51 AM
When leaders consider implementing a structured business process improvement methodology , one of the challenges they often face is explaining to employees what types of opportunities to consider. Usually, there are some apparent needs that people attack immediately. Still, once those are addressed, it can be challenging to recognize the flaws in processes, especially ones you operate every day.
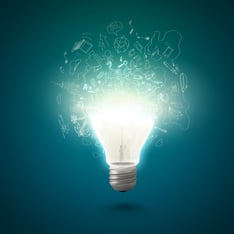
Quality Improvement
Product defects and errors affect profitability, cause dissatisfied customers, and hurt employee morale. That's why quality problems are usually the go-to target for improvement efforts. Some problems are easy to spot, but others take time to understand and uncover. Our customers have implemented quality improvements by:
- Using control charts to understand variation and detect trends
- Introducing process automation or mistake proofing ("poka yoke"), where possible, to eliminate the opportunity for error
- Calculating the financial impact of defects and rework
- Tracking customer complaints and reasons for support calls
- Applying the "5-whys" problem-solving technique to find the root cause of quality issues
When you think about quality improvement, remember that it isn't just the final products or services delivered to customers that can have errors. Internal processes and information must be free from defects as well.
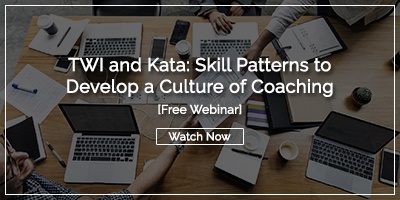
Cost Reduction
Keeping costs low is often considered to be the responsibility of the finance team and C-suite leaders, but chances are good that everyone in the organization can point to a way to reduce costs. Those closest to the work know what activities add to time and cost without any meaningful benefit. Common opportunities to reduce costs include:
- Limiting the purchase of perishable items except for immediate use
- Shifting from paper records or forms to electronic ones
- Frequently reviewing vendor contracts to ensure they meet current needs and conditions
- Reducing the inventory of products or raw materials
- Matching staffing to actual customer demand
Regardless of why the team undertakes an improvement project, most will have a positive impact on cost.
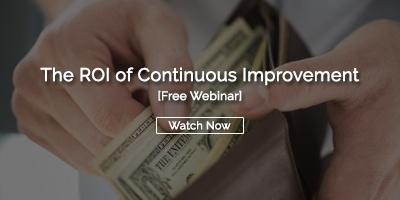
Revenue Generation
In the same way, everyone can contribute ideas about cost reduction; you don't have to be in sales or product development to have excellent ideas for increasing sales. Our customers have grown the top line by:
- Creating new bundles or products or services
- Addressing new markets or audiences
- Improving collections procedures
- Creative marketing to existing customers
- Making it easier to do business with the company
- Expanding partnerships to explore new channels
Our customers are often pleasantly surprised by the ideas that their teams come up with for increasing revenue when invited to do so.
Safety is a more significant challenge for some types of organizations than others, but every organization should pay attention to the safety of its workers and guests. This is one area where front-line workers can be extremely valuable; they see the risks firsthand. Process improvement examples that improve safety include:
- Employee awareness and training
- Workplace standardization and organization
- A well-documented and streamlined process for reporting hazards
- Automation that reduces safety or ergonomic risks
- A method for analyzing close calls or near misses
- Signage or other visual indicators of potential hazards
Customer Satisfaction
Every person in the organization has a role to play when it comes to customer satisfaction . Whether it is by creating products that maximize customer value, delivering support or services, insisting on excellent quality, or setting competitive prices, customer satisfaction is a team effort. Ideas for improving the customer experience include:
- Optimizing auto attendants to route customers to the help they need quickly
- Enhanced customer communications and content
- Implementing a structured approach to handling complains
- Skills-based contact center routing
- Transactional promoter score surveys
Your front-line employees know what your customers love and hate about working with your customers. Tap into this valuable resource to find areas for improvement.
Efficient companies practice operational excellence and get the most out of every resource. When organizations are inefficient, employees waste time and effort on tasks that don't add value, resources are wasted, and growth opportunities are missed. Ideas for improving productivity include:
- Eliminating duplicate work, like entering the same data into multiple systems
- Limiting meetings to those that are necessary and effective
- Streamlining approval processes
- Making sure that equipment and supplies are stored where they are needed
Process Improvement
All of the above examples represent ideas for improving business processes, but it is also wise to consider how you can improve your approach to improvement. Effective communications and documentation will help you accelerate the pace of positive change. You might think about the following:
- Frequently communicating strategic goals and annual objectives
- Deploying improvement management software
- Using digital wallboards to visualize work-in-progress
- Using daily huddle meetings to structure the day's improvement activities
- Measuring employee engagement and activity
- Improving cross-functional information sharing and collaboration
Improvement Techniques
Once your team is prolific at identifying opportunities for improvement, you'll want to ensure they know the most helpful techniques for implementing the ideas.
PDSA: PDSA is a structured cycle for improvement. The steps are:
Plan: Define the problem and identify possible solutions.
Do: Experiment by implementing one solution.
Study: Analyze the results of the experiment.
Act: If the experiment was successful, add it to the standard operation. If not, begin again.
The 5 Whys: The 5 whys is a problem-solving technique for finding the root cause of an issue. Simply stating a problem and then asking why five times or so will usually get to the bottom of the situation.
5S: 5S is a workplace organization technique for improving safety and efficiency. The steps are sort, set in order, shine, standardize, and sustain.
Catchball: Catchball is a technique borrowed from the Lean business methodology. Someone, usually a leader or manager, starts the "ball" rolling by sharing an idea and asking for feedback. Then, others add their thoughts and pass the idea up and down the layers of the origination until it is refined and a consensus is achieved.
A3 Problem Solving: A3 problem solving is a structured technique for defining and solving problems. On a single sheet of paper, the team determines the current state, identifies the desired state, selects performance measurements, develops an implementation plan, and tracks the results.
Business process improvement is critical for success in today's competitive landscape, but it doesn't have to be overwhelming. Small process changes implemented by employees can have a significant impact on results. Armed with process improvement software, a few problem-solving techniques, and the full support of leadership, your team will exceed all expectations.
Topics: Daily Improvement , Improvement Process
Add a Comment
Subscribe via email, recent posts.
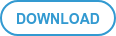
- Our Customers
Why KaiNexus
- Collaboration
- Standardization
- Customer Success Manager
- Lean Strategy
- Solutions Engineering
- Customer Marketing
- Configuration
- Continuous Enhancements
- Employee Driven
- Leader Driven
- Strategy Development
- Process Driven
- Daily Huddles
- Idea Generation
- Standard Work
- Visual Management
- Advanced ROI
- Notifications
- Universal Badges
- Case Studies
- Education Videos
Copyright © 2024 Privacy Policy
- Leadership Team
- Our Approach
- PMO Services
- Program & Project Managers
- PM Training & Development
- Case Studies
- Our Culture
- Employee Benefits
- Job Opportunities
- Benefits Realization Management Diagnostic
- Project Management Maturity Guide
- Guide to Agile Project Management
- PM Maturity Assessment
- Project Management as a Service (PMaaS) and Why It’s the Future
About PM Solutions
PM Solutions is a project management consulting firm that helps PMO, project, and business leaders apply project and portfolio management practices that drive performance and operational efficiency.
- Co-Founder & Co-CEO J. Kent Crawford
- Co-Founder & Co-CEO Deborah Bigelow Crawford
- President, PM Solutions & PM College Bruce Miller
- Vice President, Client Success, Eric Foss
- Managing Director, HR & Administration, Karen Alfonsi
- Director, Marketing and Communications, Carrie Capili
With our approach , companies can expect high-value, high-impact solutions, and measurable, sustainable results.
- PMO Deployment, Operation, and Enhancement
- Project Management as a Service (PMaaS)
- Project Review & Recovery
- Project Portfolio Management (PPM)
- Project Management Maturity Advancement
- Organizational Change Management
- Project Management Methodology Implementation
- Demand Management
- Project Management Mentors
- Resource Management
- Vendor Management
Project & Program Managers
We can provide you with highly experienced program and project managers ; experts to help guide, lead, and support high-visibility initiatives.
PM Training & Development
PM College® provides corporate project management training and competency programs for clients around the world.
By Project Initiatives
- Cost Reduction Initiatives (1)
- Data Center Consolidation (1)
- High-risk Capital Initiatives (1)
- Infrastructure Program Management (0)
- Manufacturing Facility Operations (1)
- Mentoring (11)
- Methodology (4)
- New Product Development (1)
- Organizational Change (6)
- PMO Assessment (4)
- PMO Deployment (4)
- Process Improvement (7)
- Program & Portfolio Management (10)
- Project Audits (1)
- Project Management Training (7)
- Regulatory Compliance (1)
- Resource Management (1)
- Strategy Execution (1)
- Systems Integration Deployment (0)
- Troubled Project Recovery (3)
- Vendor Management (2)
By Industry
- Automotive (1)
- Energy & Utilities (7)
- Financial Services (2)
- Human Resources (1)
- Information Technology (5)
- Insurance (5)
- Manufacturing (6)
- Pharma/Biotech (2)
- Professional Services (2)
- Research and Development (1)
- Retail & Merchandise (1)
- Security (1)
- Benefits Realization (4)
- Change Management (6)
- IT Project Management (4)
- Outsourcing Project Management (4)
- Performance & Value Measurement (12)
- Project Management Maturity (23)
- Project Management Methodology (12)
- Project Management Office (58)
- Project Management Training (31)
- Project Management Trends (50)
- Project Manager Competency (18)
- Project Portfolio Management (11)
- Project Recovery (9)
- Resource Management (5)
- Strategy & Governance (14)
- Articles (46)
- Brochures (3)
- eNewsletters (19)
- Research (44)
- Webinars (24)
- White Papers (35)
- contact us get in touch call: 800.983.0388
Home » Case Studies » Process Improvement
Pm solutions has a proven experience in providing solutions to a broad range of markets. our project management case studies cover a wide variety of needs across a number of industries., more process improvement case studies, ontario power generation achieves project excellence through the establishment of an enterprise project management office.
"We have really changed public perception, and as a result, increased our credibility in OPG’s ability to execute projects. “- Mike Martelli, Chief Projects Officer, OPG Read More »
- Energy & Utilities
- PMO Assessment
- Process Improvement
- Program & Portfolio Management
PM Governance Combined with Agile Tools Improves Delivery and Quality of Financial Services Programs
Changing state and federal regulatory compliance challenges caused this company to reinvent its custom-built storefront and home office systems. The IT and PMO teams were geared more for operational maintenance rather than for the complexities of developing new systems. This resulted in an overwhelming workload and schedule overrun measured in years. A years-overdue project was brought to Operational Pilot, saving millions in development time. Read More »
- Financial Services
- Methodology
Transformative Leadership Sets Financial Services Enterprise PMO on Fast Track to Strategic Value
For this privately held financial services company, a compelling journey of business transformation started with a good read. Read More »
- PMO Deployment
- Project Management Training
- Strategy Execution
Pharmaceutical Company’s Internal PM Certification Program Brings More Predictable Project Outcomes
An internal PM certification program was rapidly developed and implemented. During the first three years, over 400 participants attended more than 30 courses. Team members, project managers, and sponsors gained a good understanding of project management and the techniques needed to achieve more consistent project delivery. The program’s ability to remain intact after an acquisition validated the program’s value to the larger company globally. Read More »
- Pharma/Biotech
Accident Fund’s Award-Winning PMO Puts Processes Before Tools in Implementing Project Portfolio Management
PM Solutions used its PPM Maturity and Project Management Maturity Models to develop an improvement roadmap that included a number of specific recommendations from a project management governance perspective. Established PPM processes that helped eliminate approximately 100 non-value-adding projects, led to the successful implementation of a PPM tool, and won the company national acclaim – all in under three years. Read More »
Mentoring Brings an Enhanced Focus on Accountability to Merchants Insurance Group
PM Solutions led a targeted mentoring program for the client's project leads to provide one-on-one advice and coaching on how to apply consistent project management practices within the confines of their actual projects. Value Delivered: Improved on-time project delivery to 80% resulting in one program booking $100,000 of business in the first three days, and another program realizing 758% revenue growth in the first two months of introduction. Read More »
Wireless Warehouse Initiative Transforms Materials Management Operations and Improves Delivery Speed by 66%
For a world-wide provider of turbine-driven gas compression, oil pumping and power generation packages: PM Solutions provided a senior-level project manager to lead the implementation of a warehouse radio frequency (RF) solution, being responsible for overseeing requirements gathering, systems design, procurement and installation of the necessary hardware and software, and coordinating user acceptance testing. Value Delivered: Thanks to a retooling of the materials management system incorporating RF automation, the company’s warehouse accelerated delivery speed of parts by 66%, creating a significant reduction in overall time to market. This complex automation project came in on time and more than 18% under budget. Read More »
- Information Technology
- eNewsletters
- White Papers
- PMO of the Year Award
Connect with Us
The project management experts®.
PM Solutions is a project management services firm helping organizations apply project management and PMO practices to improve business performance.
Toll-free (US): 800.983.0388 International: +1.484.450.0100 [email protected]
285 Wilmington-West Chester Pike Chadds Ford, PA 19317 USA
© 2012-2024 Project Management Solutions, Inc. All Rights Reserved. Privacy & Terms
.css-s5s6ko{margin-right:42px;color:#F5F4F3;}@media (max-width: 1120px){.css-s5s6ko{margin-right:12px;}} Join us: Learn how to build a trusted AI strategy to support your company's intelligent transformation, featuring Forrester .css-1ixh9fn{display:inline-block;}@media (max-width: 480px){.css-1ixh9fn{display:block;margin-top:12px;}} .css-1uaoevr-heading-6{font-size:14px;line-height:24px;font-weight:500;-webkit-text-decoration:underline;text-decoration:underline;color:#F5F4F3;}.css-1uaoevr-heading-6:hover{color:#F5F4F3;} .css-ora5nu-heading-6{display:-webkit-box;display:-webkit-flex;display:-ms-flexbox;display:flex;-webkit-align-items:center;-webkit-box-align:center;-ms-flex-align:center;align-items:center;-webkit-box-pack:start;-ms-flex-pack:start;-webkit-justify-content:flex-start;justify-content:flex-start;color:#0D0E10;-webkit-transition:all 0.3s;transition:all 0.3s;position:relative;font-size:16px;line-height:28px;padding:0;font-size:14px;line-height:24px;font-weight:500;-webkit-text-decoration:underline;text-decoration:underline;color:#F5F4F3;}.css-ora5nu-heading-6:hover{border-bottom:0;color:#CD4848;}.css-ora5nu-heading-6:hover path{fill:#CD4848;}.css-ora5nu-heading-6:hover div{border-color:#CD4848;}.css-ora5nu-heading-6:hover div:before{border-left-color:#CD4848;}.css-ora5nu-heading-6:active{border-bottom:0;background-color:#EBE8E8;color:#0D0E10;}.css-ora5nu-heading-6:active path{fill:#0D0E10;}.css-ora5nu-heading-6:active div{border-color:#0D0E10;}.css-ora5nu-heading-6:active div:before{border-left-color:#0D0E10;}.css-ora5nu-heading-6:hover{color:#F5F4F3;} Register now .css-1k6cidy{width:11px;height:11px;margin-left:8px;}.css-1k6cidy path{fill:currentColor;}
- Project management |
- 7 types of process improvement methodol ...
7 types of process improvement methodologies you should know about
Business process improvements are methodologies in which a team evaluates their current processes and adapts them in order to increase profitability. This article highlights seven different process improvements your team can use to reduce inefficiencies and increase profit.
If businesses decided to consistently stay the same over time, many of them would collapse. Innovation requires change, and if businesses don’t change to meet customer demands, they won’t achieve much growth.
This is why many organizations use some form of process improvement methodology to adapt their processes to customer demands.
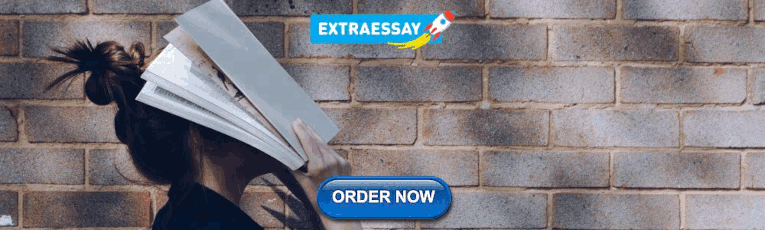
What is process improvement?
Business process improvements are methodologies in which a team evaluates their current processes and adapts them with the intent to increase productivity, streamline workflows, adapt to changing business needs, or increase profitability.
7 types of process improvement methodologies
There are seven different business process improvement methodologies your team can use to help reduce inefficiencies. In most cases, the methodology you choose depends on why you want to improve your processes and what you’re looking to improve.
1. Six Sigma methodology
Six Sigma is often used in manufacturing, mainly because it helps minimize defects and inconsistencies. The goal here is to optimize for consistency, which in the end leads to customer satisfaction.
There are two main processes used in Six Sigma: DMAIC for existing processes and DMADV for new processes. Since this article focuses specifically on improvements to existing processes, let’s dive into the DMAIC process.
What is the DMAIC process?
DMAIC is a Six Sigma process used to optimize existing processes. DMAIC stands for:
Define the opportunity for improvement.
Measure the performance of your existing processes.
Analyze the process to find defects and root causes.
Improve processes by addressing root causes.
Control any improved processes and assess future process performance to correct deviations.
The bulk of the DMAIC process improvement happens during the analysis stage. During the analysis stage of DMAIC, teams use a fishbone diagram, or an Ishikawa diagram , to visualize the possible causes of a product defect. The head of the fishbone diagram states the initial problem—then as you follow along the spine of the fish, each rib lists different categories of issues that can lead to the initial problem. This type of visual analysis is a good way to identify the different issues one root cause can create.
2. Total Quality Management (TQM)
Total quality management (TQM) is a customer-focused method that involves continuous improvement over time. This technique is often used in supply chain management and customer satisfaction projects.
TQM relies heavily on data-driven decisions and performance metrics. During the problem solving process, you use success metrics to decide how you can improve a process.
Here some key features of TQM:
Customer-focus: The end goal of TQM is always to benefit the end customer. If your team is focused on improving quality, ask yourself how that process change may affect how end consumers experience your product.
Full-team involvement: Unlike other process improvement methodologies TQM involves the entire team—not just production. As a result, you may end up looking for ways to optimize more business-centric processes, such as sales and marketing, to benefit the end consumer.
Continuous improvement: Continuous improvement in business is the idea of making small changes with the goal of continually optimizing processes. There's a lot of variability when it comes to business, and continuous improvement helps your team adapt when outside circumstances change.
Data-driven decision making : In order to apply continuous process improvement, you must continually collect data to analyze how processes are performing. This data can help identify where there may be inefficiencies and where to focus improvement initiatives.
Process-focused: The main goal of implementing TQM is to improve processes. Other process improvement methods like Six Sigma work to minimize the amount of defects, while TQM works to decrease inefficiencies.
3. Lean manufacturing
This form of process improvement goes by many names, with lean manufacturing being the most common. It may also be referred to as Lean production or just-in-time production. Defined by James P. Womack, Daniel Jones, and Daniel Roos in the book "The Machine That Changed the World," Lean highlights five main principles based off of the authors' experiences at Toyota manufacturing.
The 5 principles of lean
Identify value
Value stream mapping
Create flow
Establish pull
Continuous improvement
4. Continuous improvement (kaizen)
The Japanese philosophy of kaizen guides the continuous improvement model . Kaizen was born from the idea that life should be continuously improved so we can lead more satisfying and fulfilling lives.
This same concept can be applied to business—because as long as you are continuously improving, your business can become more successful. The goal of continuous improvement is to optimize for activities that generate value and to get rid of any waste.
There are three types of waste that kaizen aims to remove:
Muda (wastefulness) : Practices that consume resources but don’t add value.
Mura (unevenness): Overproduction that leaves behind waste, like excess product.
Muri (overburden): Too much strain on resources, such as worn out machinery or overworked employees.
5. Plan Do Check Act (PDCA)
The PDCA cycle is an interactive form of problem solving. It's used to improve processes and implement change. PDCA was created by Walter Shewhart when he applied the scientific method to economic quality control. Later, the idea was developed even further by W. Edwards Deming, who expanded on Shewhart's idea and used the scientific method for process improvement in addition to quality control.
There are four main steps to the PDCA cycle:
Plan : Decide on the problem you would like to solve, and create a plan to solve it.
Do: Test and implement the plan at a small scale.
Check: Review how the actions in the Do stage performed.
Act: After reviewing the results of the test, decide whether or not you want to implement the change at a larger scale.
PDCA is an improvement cycle. This means that these steps can be repeated until your team reaches the desired result.
6. 5 Whys analysis
The 5 Whys analysis is a process improvement technique used to identify the root cause of a problem. It's a really simple process in theory: you gather a group of stakeholders who were involved in a failure, and one person asks: "Why did this go wrong?" Repeat this question approximately five times, until you get to the root cause of an issue. The 5 Whys analysis aims to identify the issues within a process, but not human error.
Here's an example:
Problem: There was an increase in customer complaints regarding damaged products.
"Why did this happen?" Because packaging was not sufficient enough to protect the products.
"Why was the packaging not sufficient enough to protect the products?" Because the team testing packaging did not test past a certain level of stress.
"Why did the team not test the packaging further?" Because current standard processes indicated that the testing indicated was sufficient.
"Why did the current standard process indicate that this testing was sufficient?" Because this process was created for a previous product, and not this current product that is coming back damaged.
"Why wasn’t there a new process for the new product?" Because the project template for launching new products doesn’t include stress testing the new packaging.
You can see from this example that the team asked “Why” until they identified the process error that needs to be fixed—in this case, adding a “stress test new packaging” step into their product launch template . When working with stakeholders in processes like this, it's important to identify the issues, and co-create next steps together so that your production can improve.
7. Business process management (BPM)
Business process management, or BPM , is the act of analyzing and improving business processes. Much like any organic being, businesses grow and shift over time. Your team may have implemented processes that worked when your team was small, but as you grow those processes may not scale in a way that allows your team to be as efficient as possible.
Most of the time, BPM helps teams identify bottlenecks, ways to automate manual work, and strategies to improve inefficiencies. There are five main steps to business process management.
Analyze: Look at your current processes and map them from beginning to end. This is commonly known as process mapping.
Model: Draft out what you want the process to look like. Ideally, you'll have found any inefficiencies in the first step, and you can draft how you would like to solve them in this stage.
Implement : Put your model to action. During this stage, it's important to establish key success metrics so you can gauge whether or not the changes made were successful.
Monitor: Decide whether or not your project is successful. Are the success metrics you identified in step three improving?
Optimize: As the process evolves, continue looking for inefficiencies in your process and continuously optimize as you go.
Manage process improvements to increase productivity
As a team lead, one of the most valuable things you can bring to your team are clearer processes and better workflows . When used effectively, process improvement increases your team's productivity and decreases inefficiencies.
To increase clarity and improve processes, try work management. Work management tools like Asana can help you take your team’s productivity to the next level by standardizing processes, streamlining workflows, and keeping your team in sync.
Related resources
Critical path method: How to use CPM for project management
15 project management interview questions, answers, and tips
Unmanaged business goals don’t work. Here’s what does.
How Asana uses work management to drive product development
Continuous Improvement 101 & 201: Models, Processes, and Plans
By Kate Eby | January 4, 2020 (updated September 21, 2023)
- Share on Facebook
- Share on LinkedIn
Link copied
Small daily efforts can reduce waste and raise the quality of output. Use the following tips, examples, and improvement plan templates to implement changes in your organization. Experts share case studies and advice to help you get started.
In this article, you’ll find principles of continuous improvement , examples , case studies , and plan templates .
What Is Continuous Improvement?
In continuous improvement (CI) , teams attempt to make products and processes better by reducing waste or improving quality. The continuous improvement process can include small incremental changes over time or breakthrough changes that occur all at once.
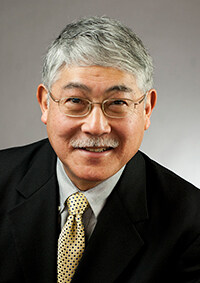
Marshall Ariza, a Principal Consultant at Firefly Consulting , explains, “Continuous improvement is a generic term used to describe Lean, Six Sigma, and the Theory of Constraints. It’s a discipline of how to look at a situation or activity to help the people who do the work perform the tasks faster and at a higher quality, meaning with more predictable outcomes.”
Searching for problems, sketching out solutions, and iterating on improvements are at the heart of many formal methodologies — the name may change, but it’s all continuous improvement.
Ideally, entire organizations — regardless of role or department — should practice continuous improvement as part of their daily routine. With its emphasis on lowering costs and raising efficiency, continuous improvement is a pillar of Lean management and therefore, can help companies in all industries gain a competitive advantage. Continuous improvement may sound like just another generic management theory, but when done correctly, it can be powerful and transformative.
Continuous Process Improvement
Continuous process improvement (CPI) is another term for continuous improvement. Both terms describe regular efforts to change software, tools, methods, and processes. These changes can improve products, delight customers, and result in larger profits.
Continuous Process Improvement Steps
The basic continuous process improvement model includes the four steps of the PDCA cycle: plan, do, check, act. Although other improvement models have steps with different names, the PDCA activities still form the core of these improvement frameworks.
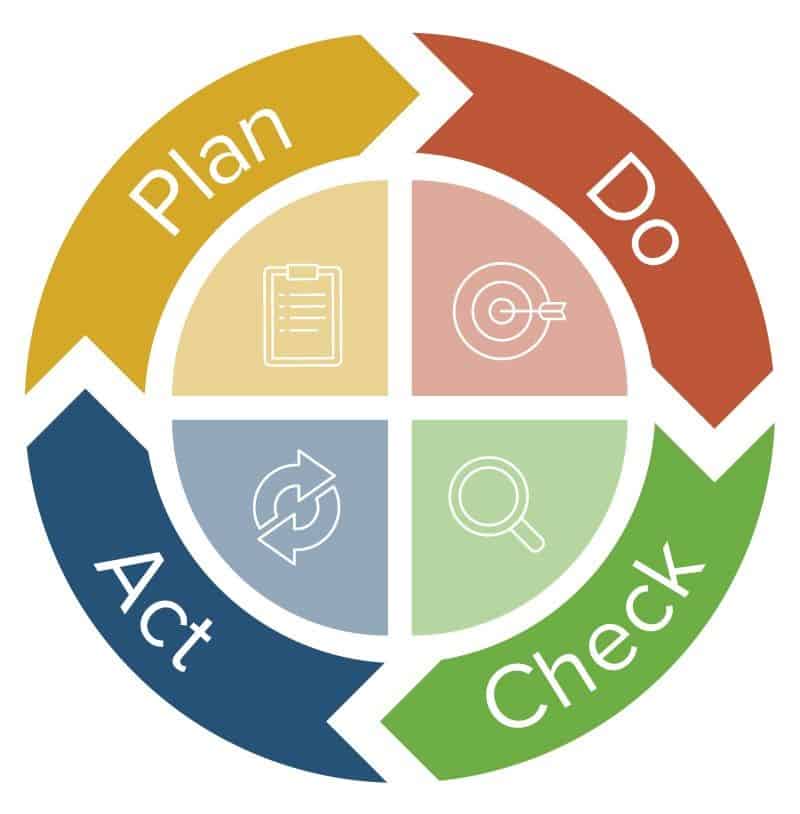
- Plan: Identify problems or a goal.
- Do: Formulate a theory or solution. Establish metrics. Implement a solution.
- Check: Track the efficacy of the solution and adjust solutions, as necessary. Watch for new problems or areas of focus.
- Act: Apply the learnings from the previous steps on a wider scale or restart the cycle to find new goals or implement improved solutions.
PDCA is a simple, repeatable system for addressing problems and testing solutions. The PDCA cycle, also known as the Deming cycle , gave root to other continuous improvement models, such as Six Sigma and the DMAIC cycle. Learn more about PDCA by reading “ A Quality Principle: Everything You Need to Know about Total Quality Management .”
Continuous or Continual Improvement?
Although continuous improvement and continual improvement are sometimes used interchangeably, they have distinct meanings:
- Continual Improvement: Some quality practitioners believe that continual improvement refers to assorted efforts in different departments using a variety of methods. Not everyone who works in quality management systems recognizes the term continual.
- Continuous Improvement: The same quality pundits consider continuous improvement to refer to specific efforts within continual improvement. The ISO 9000 Technical Committee 176 debated the choice of words in the 1990s and decided against “continuous” because it implies an impossible activity wherein improvements would be made minute to minute. However, other practitioners think that continuous improvement means that everyone in an organization works toward making improvements daily. The term may also be associated with statistical process control. However, use of the term may vary by industry. For instance, ISO 14000, the environmental management standard, uses the term “continual” to refer to separate, ongoing improvement projects.
Kaizen Continuous Improvement
According to Ariza, “Continuous improvement is a take-off of Kaizen, or ‘do a little bit all the time.’ Keep making gradual improvements, reviewing them, and asking yourself every day, ‘How can we make this better?’ You will get those changes and improvements.”
As a continuous improvement approach, Kaizen helps organizations to enhance output quality, lower costs, raise morale, and empower employees. More of a philosophy than a methodology, Kaizen is less structured than Six Sigma. However, Kaizen does use visual tools such as value stream mapping and Kanban boards to track process flows. To learn more about Kaizen, read “ Definitive Guide to Lean Project Management .”
Lean Continuous Improvement
Continuous improvement is a key part of Lean and Agile management. Lean methods help teams to eliminate waste and simplify workflows. Lean was first used in manufacturing, but is now used by many other industries as well.
Built on Kaizen, Lean continuous improvement shares the principles of creating big shifts from small changes and encouraging employees to offer new ideas. Lean continuous improvement creates process refinements by helping teams explore new ways of working. Learn more about this methodology by reading “ The Indispensable Guide to Lean Process Improvement with Templates and Case Studies .”
Six Sigma Continuous Improvement
Six Sigma is a formal method of continuous improvement that removes variability and raises the likelihood of creating the results teams want. Most widely used in the form of Lean Six Sigma , the method uses the DMAIC cycle.
Analogous to PDCA, DMAIC stands for define, measure, analyze, improve, and control. In Six Sigma initiatives, trained Six Sigma practitioners support organizations in their data-driven improvement projects. The results-based, competitive-improvement framework for operational excellence is an offshoot of Six Sigma. The methodology uses the Continuous Improvement Maturity Model (CIMM) to gauge an organization’s progress in using Lean Six Sigma methods. Learn more about this framework by reading “ Operational Excellence: Key Principles and How to Implement Them .” Six Sigma employs many of the analytical tools used in quality management, such as business process mapping, fishbone diagrams, SIPOC, and more.
Continuous Improvement Case Studies

Giles Johnston is a chartered engineer who consults with businesses to improve their operational processes, and the author of Effective SOPs . He and Firefly Consulting’s Marshall Ariza offer the following case studies of how real companies used continuous improvement processes:
- CCC Win: Johnston worked with a team who had never performed formal business process or continuous improvement work. The tool of choice: a cause, concern, and countermeasure (CCC) exercise . To begin, they sketched out their current workflow and pulled it apart. That’s a bit stupid . That doesn’t work. That only works half of the time. Only half of our customers do this . “Within a couple of hours, they had 40 legitimate concerns about their process, which they then converted into an action plan. The countermeasures became action steps in their plan,” Johnston says,
- Maintenance Walkthrough: Johnson walked through a plant with an engineer. “Just tell me everything that gets up your back,” he told the employee. He listed everything the man told him, and together they flipped the list around to draft an action plan. The engineer’s reaction: “I didn’t think it could be that easy.”
- Continuous Improvement Bingo Win: CI bingo is an ice-breaking tool to start discussions about improvement. Johnston shares an example of a team that, while playing bingo, half in jest, suggested their invoices could be prettier . When the invoices were formatted, and a logo added, the accounting team noticed that customers were paying bills faster. A quick survey of those customers revealed that customers lost the plain invoices on cluttered desks. Customers could now find the colorful sheets.
- Great Product, Poor Company Culture: Ariza describes a client whose customers said something to the effect of: We love your product, but we hate dealing with the company . “As a CEO or COO, how do you deal with that?” he asks. “That’s how continuous improvement helped. The organization could dig deeper to discover where the problem stood, whether with the approach of customer service, the voicemail setup, or something else. Frame the problem, frame the solution, and set up objectives and parameters. Then use this information for a project charter. Follow those steps for each pain point, and you end up with a series of projects to execute against.”
Additional Continuous Improvement Methodologies
Concepts similar to continuous improvement include business process improvement , which focuses on process improvement to create better deliverables, and business process management , which focuses on managing and automating processes. The following list includes other CI-based approaches that businesses and nonprofits use today:
- TQM: Total quality management (TQM) is the first methodology in the modern era to express continuous improvement principles. TQM was superseded by Six Sigma.
- Reengineering: In reengineering, organizations enact major shifts in culture and methodologies to support their principal customers.
- JIT: Just-in-time (JIT) is a foundational aspect of Kanban in which production lines obtain inventory as they consume it. For JIT to function properly, the line must remove waste, such as those found in time and processes, thereby improving quality.
- Lean Thinking: Lean thinking , also called lean management , removes unnecessary layers of management to bring all parts of an organization closer to essential activities. Use this methodology to rigorously analyze all processes and eliminate efforts that do not add value.
- ISO 9000: A quality certification standard, ISO 9000 focuses on documenting processes and, less explicitly, on improving them. The most recent version, ISO 9000-2015, includes a provision for continuous improvement.
- Theory of Constraints (TOC): This methodology analyzes processes to detect and leverage bottlenecks. Since bottlenecks will always appear, TOC provides a vehicle for implementing continuous improvement.
- Standard Work: A standard work initiative documents the best practices for all processes and tasks. It eliminates waste and adds to employee safety because all employees perform tasks in a consistent and optimal manner.
8 Principles of Continuous Improvement
The principles of continuous improvement include making small step-by-step changes, empowering employees, reflecting and repeating, and creating measurable and repeatable changes. These values apply regardless of the methods or tools you use to implement continuous improvement.
- Improvement Is Built on Small Changes: Monumental cultural shifts or game-changing research can be scary, and they aren’t necessary.
- Step-by-Step Changes Are Pocketbook-Friendly: Change doesn’t have to be expensive.
- Employee Ideas Matter: Ideas for change should come from the people who do the work daily.
- Enhancements Must Be Measurable and Repeatable: Everyone needs to know what success looks like so they can continue to see quality results.
- Focus on Improving, Not on Deploying Tools: Formal improvement methods can be helpful, but any good idea is beneficial to continuous improvement.
- Involvement Generates a Sense of Ownership: Improvements also generate gravitational pull and momentum — when teams know that management listens to their ideas, see their ideas implemented, and reap the benefits of those changes, they begin to look for ways to make changes.
- Look Within for Answers: As the saying goes, the grass is always greener on the other side — another company’s approach might seem objectively superior to your own. And while other companies’ approaches may very well work for them, remember that their organization is different from yours. It’s important to examine your own processes and find ways to improve those.
- Continuous Improvement Is Iterative: As the word “continuous” implies, to succeed over time, teams must regularly reflect on processes.
Continuous Improvement Example
What does the continuous improvement process really look like? Firefly Consulting’s Marshall Ariza offers an example from everyday home life that looks at how making small changes can have big results in efficiency and the quality of the end product.
Suppose you wake up on a Saturday morning and decide to make an omelette. Maybe you have eggs, and maybe you don’t. You rummage around in the refrigerator for onions and cheese. You look through the cabinets for a can of chilis but have to run to the basement to get a can. When you’re ready to chop vegetables, you forget where you keep the cutting board. When you’re ready to whisk the eggs, you look for the whisk in a drawer, only to find it in the dishwasher. When you’ve whisked the eggs, you realize you haven’t heated the butter in the pan. And on it goes, right to your rummaging around for the spatula to turn the omelette, and running to get a plate before the eggs burn.
Ariza explains: “You’ve been busy the whole time, but then you ask yourself: How would they do it on a cooking show on PBS? Before they start to cook, the vegetables are all cut up. All the utensils they need are in grabbing space. Looking for items and forgetting steps wastes time. So, if you compare the time from start to finish that you took to what they take on the show, you’ll see there’s a huge difference.”
“That’s what we do in continuous improvement. To start the conversation, we help people see wasted activity. Then, we help them put together a new process that takes out the guesswork and gets things systematized. Continuous improvement gets rid of the non-value added activities that don’t contribute to the desired outcome,” says Ariza.
What Is Continuous Quality Improvement (CQI)?
Continuous quality improvement is a tool that helps all members of a team work together to improve processes and products. In CQI, leaders encourage employees to share ideas, and everyone tries to make improvements daily.
In their report card on CQI , Blumenthal and Kilo referred to the CQI movement as “the effort to import into healthcare lessons that other industries learned years ago about improving product quality in order to meet their customers’ needs and expectations.”
To learn more about CQI, read “ Where Data Serves People: Benefits of the Continuous Quality Improvement Approach .”
Managing Continuous Improvement
Start continuous improvement by identifying where problems usually occur. Trouble spots show up in tasks, workflows, or even workspaces. But not every problem needs an improvement program.
The pursuit of continuous improvement may be formal or adaptive: formal continuous improvement endeavors follow frameworks such as Six Sigma and recognized analysis tools to achieve measurable results. By contrast, adaptive continuous improvement uses a mix of analytical tools. In engineering and other settings, continuous process improvement regularly reviews and updates processes to align them with an organization’s evolving business goals.
Ariza describes continuous improvement efforts as two parts. “First, you learn to see what you’re dealing with and break it down into tasks that add to valued outcome versus those things you’re doing that don’t, such as rework or not using time efficiently. Second, you let the people who do those tasks make the changes. That’s what CI is at its heart. They’re the ones who understand best what’s going on. So, they are best equipped to know what will be a workable solution or what’s not very practical.”
Formal continuous improvement actions leverage methodologies such as DMAIC from Six Sigma and start from the impetus of C-level stakeholders. Some pundits believe that formal programs with measurable financial outcomes signal management’s commitment to ongoing improvement and are one way to systematize CI. When pursuing formal programs, consider teaching your team analysis techniques.
Resistance to Continuous Improvement
Despite the benefits of continuous improvement, teams sometimes shy away from the process. The thought of a full-on Agile or Six Sigma exercise, complete with statistical analysis, can intimidate managers. Employees may assume that management expects more work on top of an already full schedule.
“When you’ve been through the tunnel and have gotten to the light, you understand that you can save so much time and make life easier. Why wouldn’t you want to do continuous improvement? But if you’ve never experienced that and you’re crushed with work, it just seems like something else you have to do,” explains Johnston.
He adds that sometimes, cynicism reigns. “A lot of people feel they’ve heard it all before, with all the lofty intentions from management, and nothing happens. I sometimes see managers that tell people to do continuous improvement and then not give them any clue how to do it. They don’t have the tools or a good approach, and they don’t have the ability to coach and facilitate their staff, but they expect results. I can see a lot of people being frustrated.”
Ariza agrees. “The point is to have a goal, as opposed to just floating the idea of improvement without metrics. You need some metrics. How long to get there? How much energy and effort? What is that worth? Putting a value around projects is the contribution of Six Sigma. You prioritize projects, and define what success looks like so you can celebrate it.”
Concern, Cause, Countermeasure and CI Bingo
Johnston emphasizes how light and easy continuous improvement can be. “When most people engage with it, they realize that CI doesn’t require much effort. Just sharing a few basic tools, such as PDCA, gets a lot of results without having to train people in any methodologies. If you have a good manager who provides the appropriate thinking process, the results you can get with little output are stunning.”
One simple tool is the CCC exercise , which stands for concern, cause, and countermeasure. CCC is used in lean manufacturing and can reveal solutions without requiring complex problem solving skills. As Johnston explains, “CCC focuses on capturing people’s gripes about what’s wrong with the business. Sometimes it’s worth it just to get nagging and complaints out in the open. When that’s done, employees can look at what’s causing these issues by asking good why questions. CCC is a really fast way to create an action plan.”
Likewise, continuous improvement bingo can start the conversation about change to gather specific goals, especially when improvement requests are vague. A workshop leader lists the areas for improvement at the top and team members list possible types of improvements down the side. Then, the team matches changes to functional areas.
“What I find fascinating is the confidence it builds from taking small improvement steps,” says Johnston. “As people get more confident, what might have seemed a big step two weeks ago is now a tiny step, and people take on bigger and bigger challenges because they learn stuff, get more skills, and gain confidence. If you do it right, people get the feeling of winning and contributing to something more meaningful than just banging parts out or delivering a service. Maslow’s Hierarchy comes to mind when he says that people can do more with their minds than just delivering the service. They can contribute in other ways.”
Continuous Improvement Methodology Choices
In choosing a quality improvement methodology, consider the culture of the organization and whether improvement is already baked into its strategy. Some companies can easily systemize continuous improvement principles.
Some practitioners suggest that when small, daily changes are not possible or when the concept is new, organizations may choose rapid improvement events. Rapid improvement events last from one to five days and usually focus on one topic. Participants leave with an action plan and discrete action items. Giles Johnston’s work with CCC sheets (detailed earlier in this article) is an example of a type of continuous improvement event.
When organizations need to ensure consistent improvement efforts, the control piece in Six Sigma DMAIC may be the answer. According to Ariza, “Control is a revolutionary piece of the sequential roadmap. It’s a backstop in the improvement process that says you need metrics to measure if you’re slipping.” For this reason, and because it demands the endorsement of management and a group effort to implement quality programs, Six Sigma has largely superseded TQM and merged with Lean to offer the best of all approaches.
Further, as discussed in International Journal of Productivity and Quality Management , many CI initiatives fail because companies made insufficient effort to mesh their continuous improvement methods with their management and quality management systems.
Continuous Improvement Benefits
“With continuous improvement, you’re generally going to reduce costs. It helps eliminate rework, pinpoint and eliminate the cause of errors, and also helps you understand the dynamics of how work gets done,” says Ariza.
He explains that although you may be highly engaged in doing something, the activities may not contribute to your final result. By dissecting the activities, you can eliminate those activities that don’t contribute to a positive outcome and find ways to finish work in less time at a reduced cost. Continuous improvement offers the following benefits to help companies stay competitive in an ever-changing competitive landscape:
- Streamline workflows
- Reduce overhead
- Improve product quality
- Increase efficiency and productivity
- Decrease project costs
- Reduce waste
- Raise employee satisfaction
- Build teamwork
- Improve customer satisfaction
- Improve organizational alignment, from the front lines to the executive suite
- Increase engagement in improvement by promoting a sense of ownership and accountability for improvement
- Shorten time to share knowledge and ideas
- Raise skill level throughout a team
Continuous Improvement Tools
Continuous improvement tools help teams learn which processes to improve. The tools show teams where their strengths and weaknesses lie, and can also help keep everyone looking for and making positive changes beyond individual projects.
Use these CI tools as you embark on your continuous improvement journey:
- Benchmarking: This tool encourages you to evaluate current processes and outcomes and compare those results with competitor and industry standards for excellence.
- CCC Worksheet: Working through concerns, causes, and countermeasures provides an easy way to air complaints, identify problem sources, and determine solutions. CCC worksheets may alleviate employee fears over the complexity of a continuous improvement program. Download the CCC worksheet below .
- Business Process or Value Stream Mapping: Although process mapping software is available, teams can simply sketch their processes on paper, a flip chart, or a whiteboard. Mapping offers an easy way to gain an overview of end-to-end operations.
Then, develop and maintain quality with these tools:
- Kanban: A Kanban board helps you visualize workflow and spot bottlenecks. Use it as an initial analysis tool and then continue using it as a work management tool.
- Kaizen Event: A lean management tool, a Kaizen event is a short project, usually lasting about five days, that focuses on one area of improvement. Our Kaizen Event Checklist describes everything you need to get started.
- 5 Whys: The 5 Whys is a tool widely used in continuous improvement and quality circles. Begin by asking why a problem exists, and then ask Why? for each answer until the root cause appears. Download a 5 Whys template .
- 5S: Used originally in manufacturing and now for rapid improvement, 5S suggests the five tips that yield the most improvement: sort, set up, shine, standardize, and sustain.
- The Wastes: Originating in Kaizen and Lean Manufacturing, the three types of waste define activities that do not produce added value: muda , the process wastes; mura , the waste of unevenness; and muri , the waste of overburden. Filter your activities through the lens of the Wastes.
- RADAR Matrix: Discussed in “ Quality Improvement Methodologies – PDCA Cycle, RADAR Matrix, DMAIC and DFSS, ” RADAR matrix is an operational excellence tool used in the EFQM Excellence Model. The acronym RADAR stands for results, approach, deploy, assess, and refine. The tool takes the results an organization aims for, and plans and deploys approaches to attain the goals, and then assesses and iterates improvements.
- Hoshin Kanri: Translated in English as policy development , Hoshin Kanri ensures that all procedures and processes in an organization ultimately align with policies and strategies.
After improvements are made, record and monitor results with the following tools:
- A3 Reports: Lean and Agile organizations use A3 to provide an overview of lessons learned after a PDCA cycle. They usually contain context, details about the current problem, potential solutions, and a proposed plan.
- Gemba Walks: In a gemba walk, executives and management walk through a specific operational area to observe processes and learn about employee concerns. The exercise is a focus on action, not just on goals. It forces you to ask, Where do I want to go, and what needs to happen to get there?
Continuous Quality Improvement Plan
A CI plan outlines how to make products or processes better. The plan lists what the company will improve, the improvements themselves, and how to measure them. A formal plan can list the methodologies and tools the team will use to research gaps, discover solutions, and track success.
Continuous Improvement Plan Templates
Hundreds of templates exist for preparing and planning your improvement initiatives, but we’ve selected the best options to help you get started. Download the following free templates and customize them to suit your CI plan requirements.
CCC Template
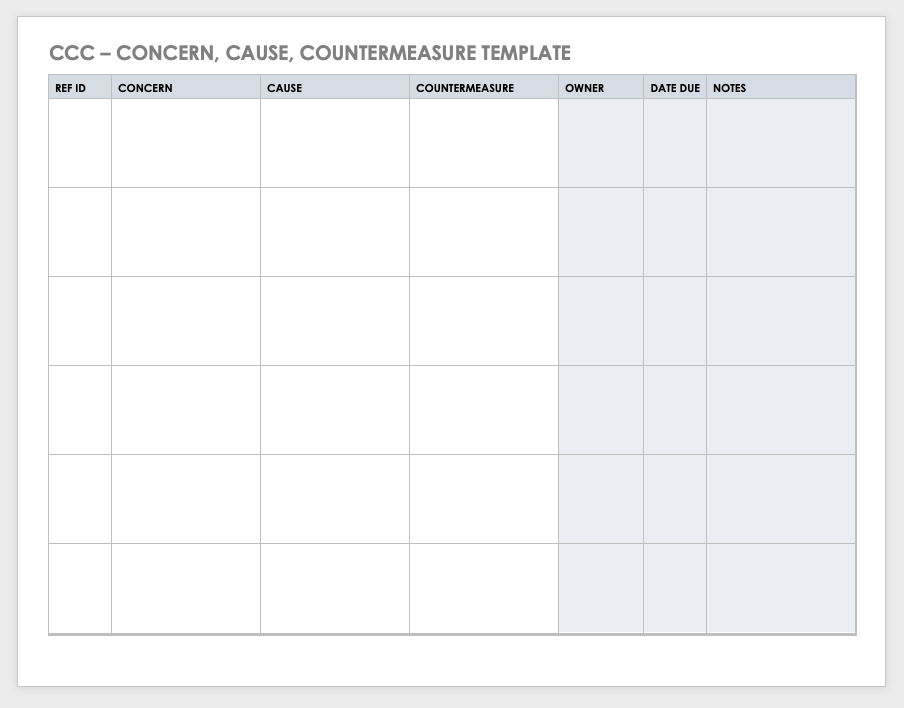
Giles Johnston drafted this concern, cause, and countermeasure template. Use it as a way to break the “improvement” ice with reluctant staff or with those who have little experience with formal improvement endeavors. Pass out sheets or gather around a table to list problems and concerns, consider the root causes of issues, and brainstorm solutions.
Download CCC Template
Excel | Word | PDF
Continuous Improvement Bingo Template
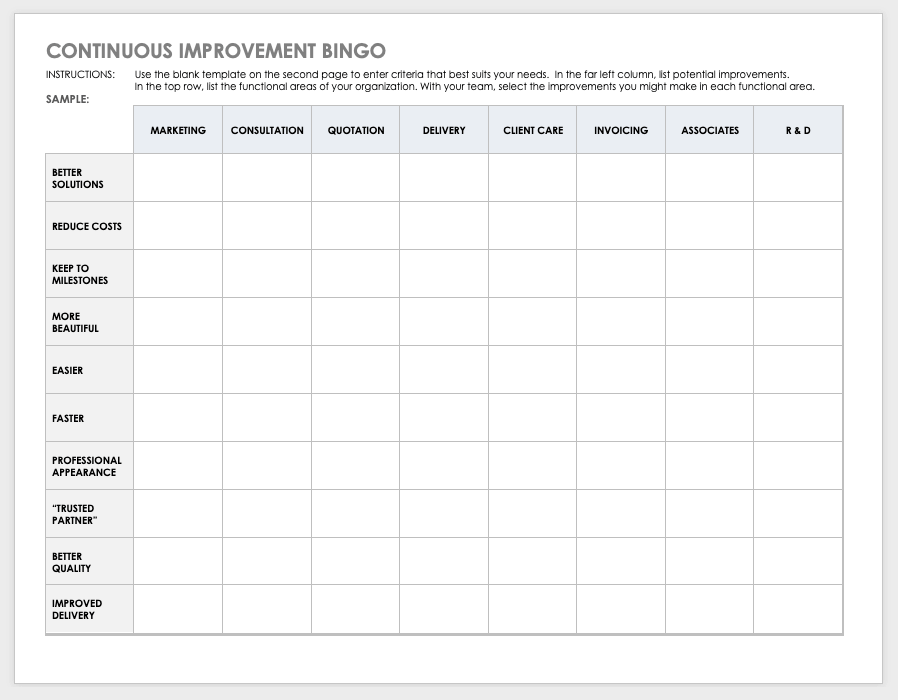
Another simple tool for starting the CI discussion, Johnston’s continuous improvement bingo card lists qualitative goals in the first column and functional areas in the top row. For each functional area, staff will suggest a goal. This template includes an example and a blank worksheet where you can add your organization’s own goals and areas for improvement.
Download Continuous Improvement Bingo Template
Excel | Word | PDF
Long Continuous Improvement Plan Template
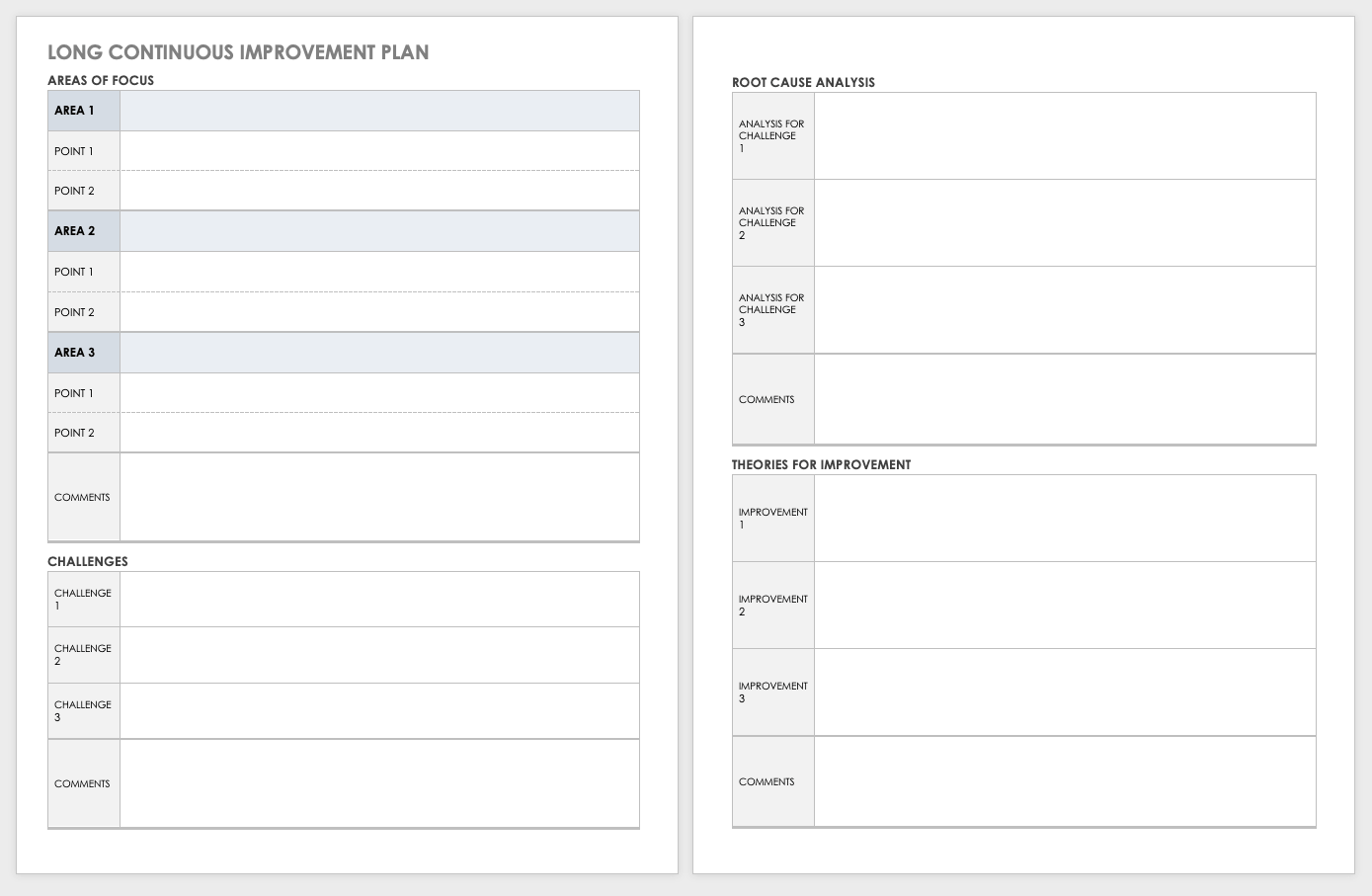
When your team knows where it needs to improve, the origin of problems, and potential remedies, you must capture that information in a continuous improvement plan. In this plan template, you can specify the focus area, the problem in each, the root causes, and the hypothesized solution.
Download Long Continuous Improvement Plan Template
Excel | Word | PDF
Monitor and Manage Continuous Improvement with Real-Time Work Management in Smartsheet
Empower your people to go above and beyond with a flexible platform designed to match the needs of your team — and adapt as those needs change.
The Smartsheet platform makes it easy to plan, capture, manage, and report on work from anywhere, helping your team be more effective and get more done. Report on key metrics and get real-time visibility into work as it happens with roll-up reports, dashboards, and automated workflows built to keep your team connected and informed.
When teams have clarity into the work getting done, there’s no telling how much more they can accomplish in the same amount of time. Try Smartsheet for free, today.
Discover why over 90% of Fortune 100 companies trust Smartsheet to get work done.
We use essential cookies to make Venngage work. By clicking “Accept All Cookies”, you agree to the storing of cookies on your device to enhance site navigation, analyze site usage, and assist in our marketing efforts.
Manage Cookies
Cookies and similar technologies collect certain information about how you’re using our website. Some of them are essential, and without them you wouldn’t be able to use Venngage. But others are optional, and you get to choose whether we use them or not.
Strictly Necessary Cookies
These cookies are always on, as they’re essential for making Venngage work, and making it safe. Without these cookies, services you’ve asked for can’t be provided.
Show cookie providers
- Google Login
Functionality Cookies
These cookies help us provide enhanced functionality and personalisation, and remember your settings. They may be set by us or by third party providers.
Performance Cookies
These cookies help us analyze how many people are using Venngage, where they come from and how they're using it. If you opt out of these cookies, we can’t get feedback to make Venngage better for you and all our users.
- Google Analytics
Targeting Cookies
These cookies are set by our advertising partners to track your activity and show you relevant Venngage ads on other sites as you browse the internet.
- Google Tag Manager
- Infographics
- Daily Infographics
- Graphic Design
- Graphs and Charts
- Data Visualization
- Human Resources
- Training and Development
- Beginner Guides
Blog Human Resources
How to Create a Process Improvement Plan [20+ Templates Included]
By Jennifer Gaskin , Jun 12, 2023
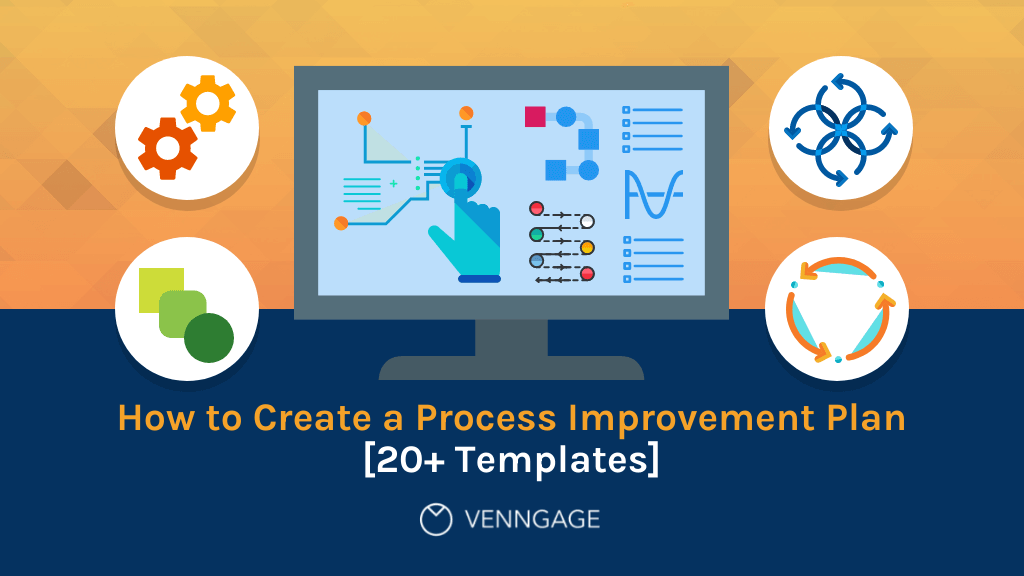
A process improvement plan is a comprehensive and actionable document that outlines the necessary steps to enhance the efficiency, effectiveness and overall performance of processes and procedures within your company. It serves as a roadmap to identify areas of improvement, address bottlenecks, streamline workflows and optimize resource utilization.
By creating a process improvement plan , companies can proactively drive positive change, foster continuous improvement and achieve higher levels of operational excellence.
Many aspects of process improvement can benefit from visual communication tools like infographics, presentations, mind maps and more. Venngage simplifies process improvement for Learning and Development teams with user-friendly plan templates for efficient implementation and management.
Click to jump ahead:
How do you create a process improvement plan?
What are the most common types of process improvement plans, what is an example of process improvement, types of process improvement plan & examples, what are the benefits of establishing a process improvement plan, process improvement plan faq.
A well-designed process improvement plan can streamline operations, enhance efficiency and drive organizational growth. To help you navigate this crucial endeavor, here are ten essential steps to create a process improvement plan that yields measurable results:
- Identify the Goals: Define the specific objectives you aim to achieve through process improvement. For example, reducing customer wait times by 20% or decreasing production errors by 15%.
- Analyze Current Processes: Thoroughly evaluate existing workflows to identify bottlenecks, inefficiencies and areas of improvement. For instance, examine how information flows between departments or how inventory is managed.
- Gather Stakeholder Input: Engage employees, managers and other relevant stakeholders to gather insights and perspectives on process challenges. Example: Conduct interviews or surveys, or integrate a cloud contact center solution to collect feedback on pain points and potential solutions.
- Prioritize Improvement Areas: Based on the analysis and stakeholder input, prioritize the areas that require immediate attention. This might involve identifying high-impact processes that, when improved, will have a significant positive effect on the organization.
- Set Measurable Objectives: Establish specific and measurable objectives that align with the identified improvement areas. These objectives should be quantifiable and time-bound. For example, reduce customer complaints by 25% within six months.
- Develop Action Plans: Create detailed action plans for each improvement area, outlining the steps, responsibilities and timelines for implementing changes. For instance, assign a cross-functional team to streamline the order fulfillment process and develop a timeline for completing the necessary changes. Consider having action plan templates in place so there you team has a framework for how to accomplish processes.
- Implement Changes: Execute the action plans while closely monitoring progress and ensuring adherence to the established timelines. Example: Introduce new software to automate manual data entry tasks and track key performance indicators.
- Measure Results: Regularly measure and evaluate the impact of the implemented changes against the set objectives. This may involve tracking metrics like cost savings, productivity improvements, or customer satisfaction ratings.
- Adjust and Refine: Based on the results, identify any gaps or areas that need further improvement. Adjust the action plans accordingly, making iterative refinements to continuously optimize processes.
- Communicate & Engage : Keep all stakeholders informed about the progress of the process improvement initiatives and encourage their ongoing involvement. Share success stories and celebrate achievements to sustain motivation and engagement.
By adhering to these useful guidelines, you will forge a formidable process enhancement blueprint that propels transformative growth within your organization. Keep in mind that process improvement is an ever-evolving odyssey and constant scrutiny and fine-tuning will safeguard perpetual triumph in fine-tuning your operations.
Process Improvement Plan Case Study
Following the steps we outlined earlier, let’s explore a hypothetical process improvement plan for a doctor’s office that constantly gets complaints from patients about how many forms they have to fill out.
Process Improvement Plan: Reducing Patient Form Burden in a Doctor’s Office
- Identify the Goals: The goal is to streamline the patient intake process and reduce the number of forms patients have to fill out, resulting in improved patient satisfaction and reduced administrative burden.
- Analyze Current Processes: Evaluate the existing patient intake process to identify the number and types of forms patients are required to complete, as well as any redundancies or inefficiencies in the process.
- Gather Stakeholder Input: Engage with patients, front desk staff and healthcare providers to understand their perspectives on form-related challenges and potential solutions. Conduct surveys or hold focus group discussions to gather feedback.
- Prioritize Improvement Areas: Identify key areas where form reduction can have the most significant impact on patient experience and administrative efficiency. For example, focus on eliminating redundant information across forms or consolidating multiple forms into a single comprehensive document.
- Set Measurable Objectives: Establish specific objectives, such as reducing the number of forms by 50% within three months, minimizing the time patients spend filling out forms by 25% or achieving a patient satisfaction rating of 80% regarding the form intake process.
- Develop Action Plans: Create action plans to streamline the patient intake process and minimize form requirements. Examples of actions may include:
- Conduct a thorough review of existing forms and identify areas of overlap or duplication.
- Consult with legal and compliance teams to ensure necessary information is captured while minimizing redundancies.
- Explore the possibility of implementing electronic forms or online pre-registration to expedite the process.
- Train front desk staff on the new streamlined process and educate them on assisting patients in completing forms efficiently.
- Implement Changes: Execute the action plans by implementing the agreed-upon improvements. This could involve revising and consolidating forms, implementing electronic forms or online pre-registration systems and providing staff training on the revised process.
- Measure Results: Regularly measure and evaluate the impact of the implemented changes against the set objectives. Track metrics such as the number of forms eliminated, time saved for patients and patient satisfaction ratings related to the revised intake process.
- Adjust and Refine: Based on the results and ongoing feedback, identify any areas that require further improvement. Refine the process by addressing any remaining pain points or bottlenecks to ensure a seamless and efficient patient intake experience.
- Communicate and Engage: Maintain open communication with patients, staff and healthcare providers throughout the process improvement journey. Inform patients about the changes and improvements made to the form intake process and encourage their feedback and suggestions for further enhancements.
By implementing this process improvement plan, the doctor’s office can minimize the burden on patients by reducing the number of forms they need to fill out, resulting in improved patient satisfaction and streamlined administrative processes. Remember that continuous evaluation and refinement are essential to adapt to evolving patient needs and ensure ongoing improvements in the patient intake experience.
You can customize this process improvement plan template to reflect the example above:
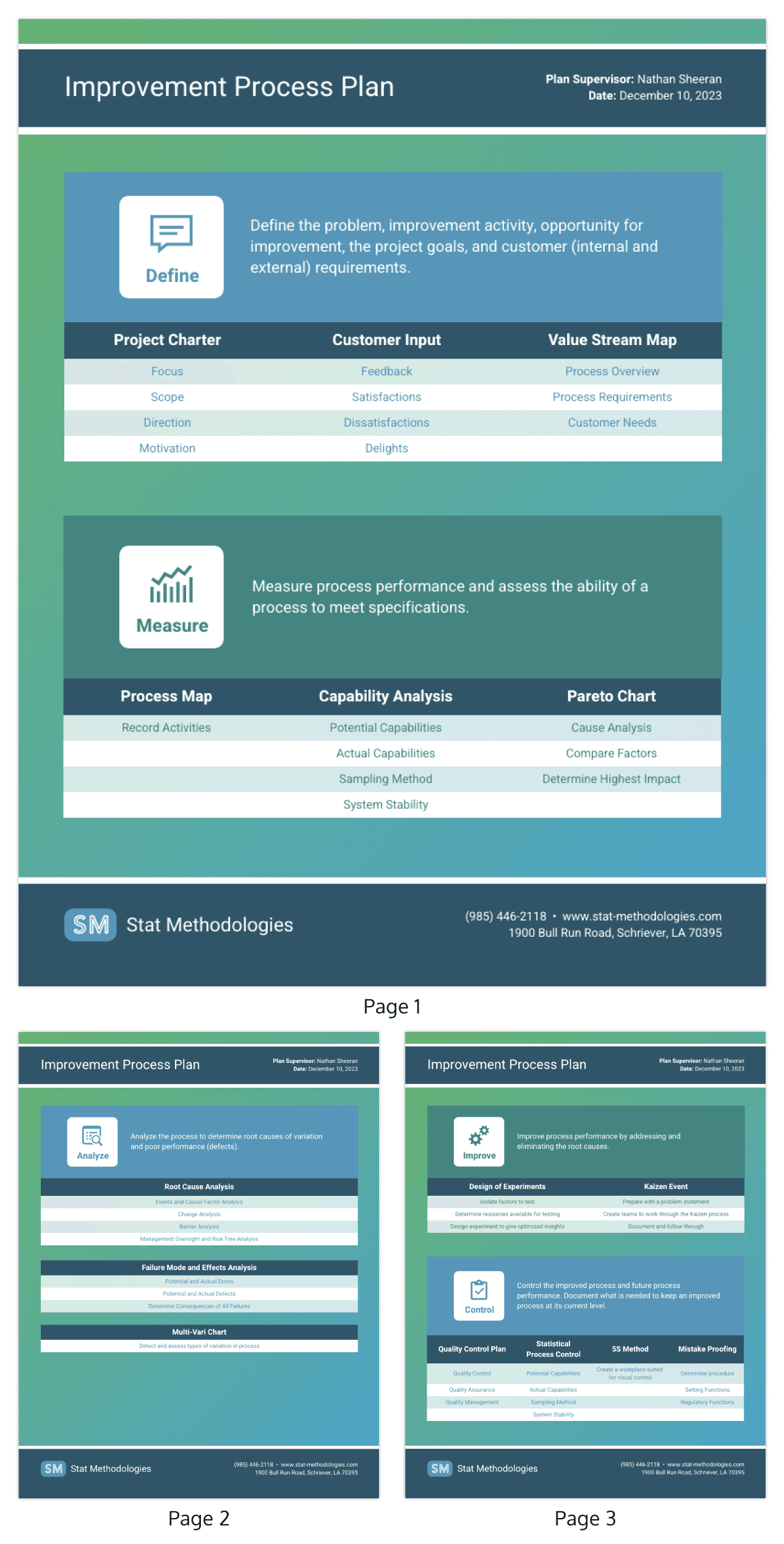
There are found major methods of process improvement that you may consider integrating into your process improvement plans. Some of these methods are used in the largest companies in the world.
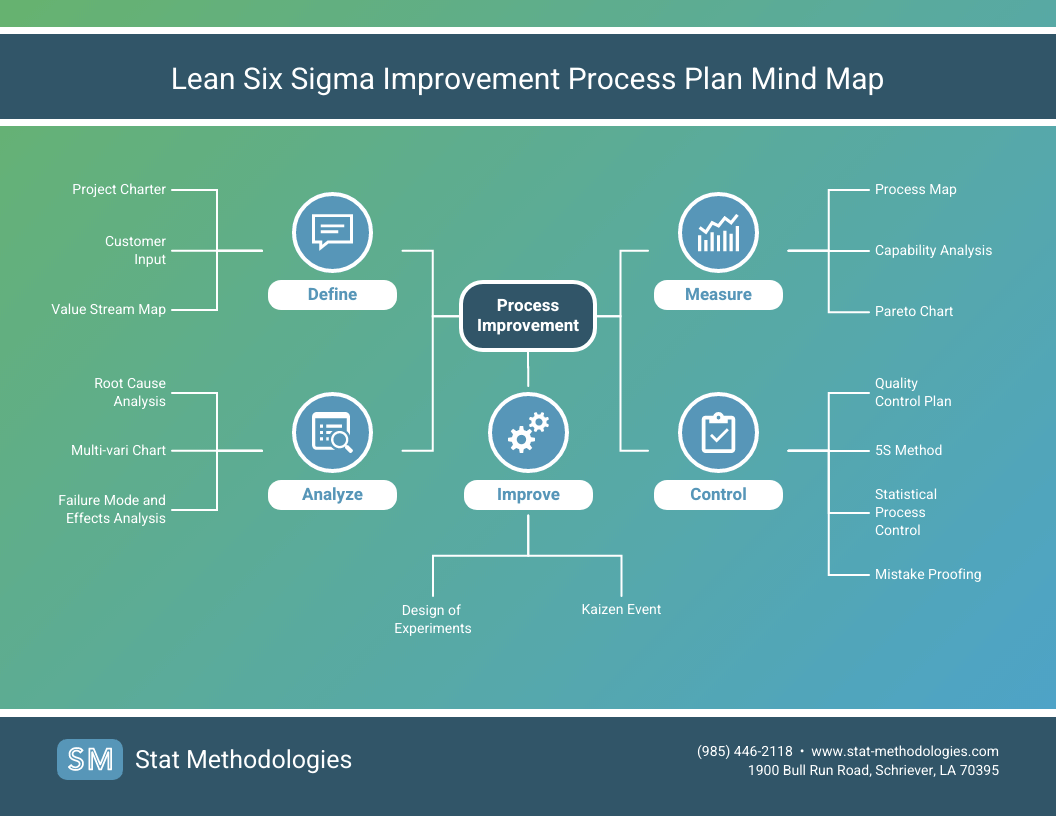
A quality control method developed by a Motorola engineer, Six Sigma has become a global phenomenon and Six Sigma certification is highly sought-after in many industries. Six Sigma outlines five steps for improving existing business practices, abbreviated to DMAIC:
Here’s how a process improvement plan should be when using the Six Sigma method:
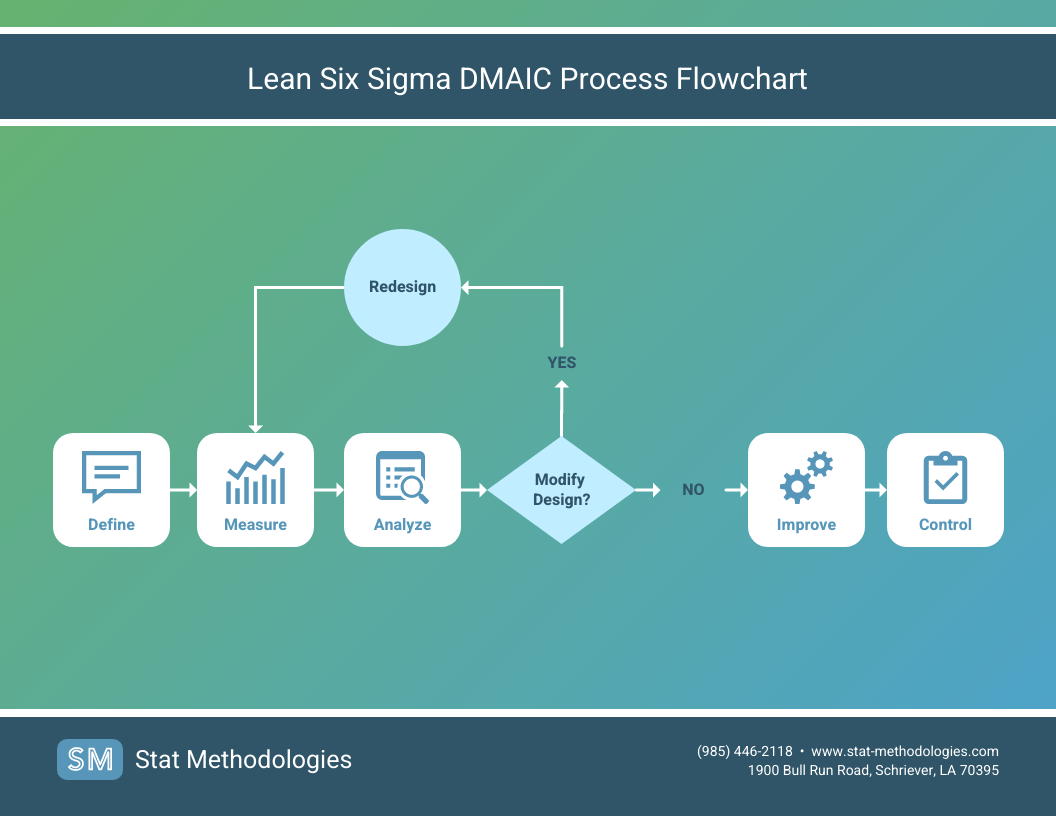
Lean & Lean Six Sigma
Lean traditionally is used by manufacturing companies, but the principles are useful across all industries and as its name suggests, Lean process improvement plans focus on reducing waste. In particular, Lean aims to eliminate any activities that do not add value to the end user of the good or service. The steps are:
- Identify value
- Map value stream
- Create flow
- Establish pull
- Seek perfection
Lean Six Sigma is the hybrid of the two methods, helping organizations improve processes through DMAIC while also eliminating waste.
Total quality management (TQM)
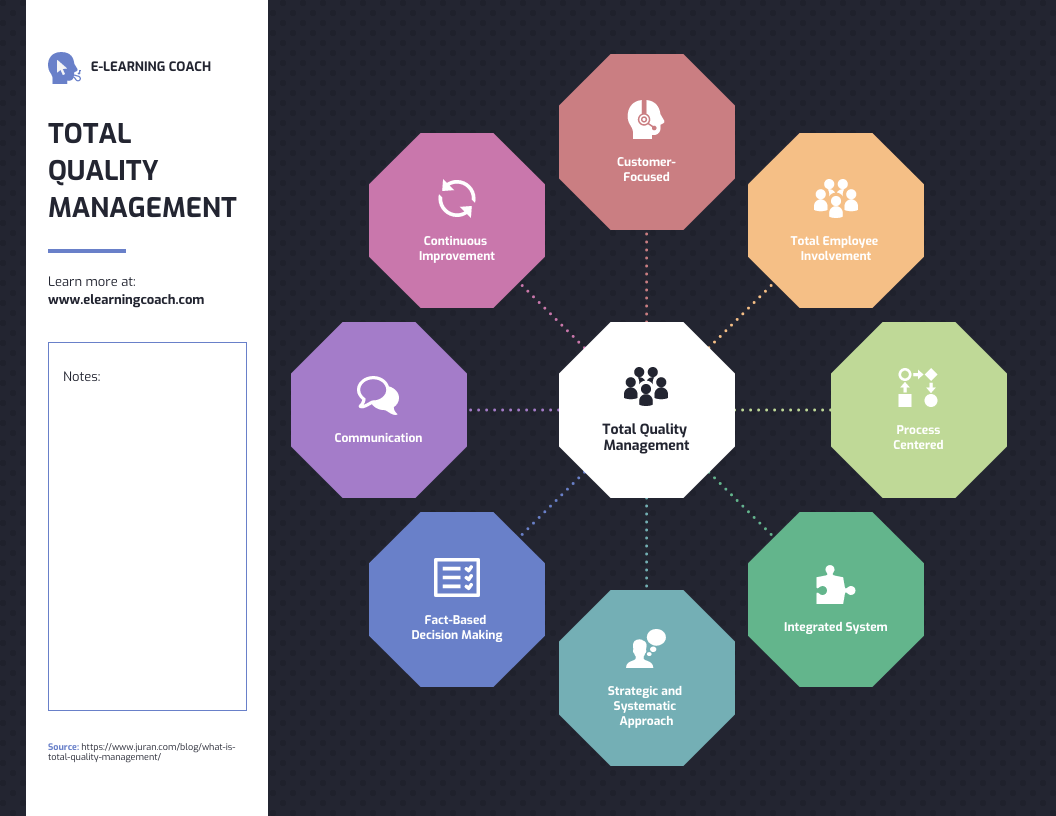
Total quality management (TQM) had its heyday in the 1980s and early 1990s before the advent of Lean and Six Sigma, but its main objectives are still valid today. TQM process development plans focus primarily on quality control, ensuring that the company’s output is of the highest possible quality and determining ways to make output even better.
TQM doesn’t have steps as most other process improvement methods do. Rather, it focuses on principles that should guide an organization with a TQM mindset:
- Customer-focused
- Total employee involvement
- Process-centric
- Full team integration
- Strategic and systemic
- Data-driven decisions
- Constant communication
Plan-Do-Check-Act (PDCA)
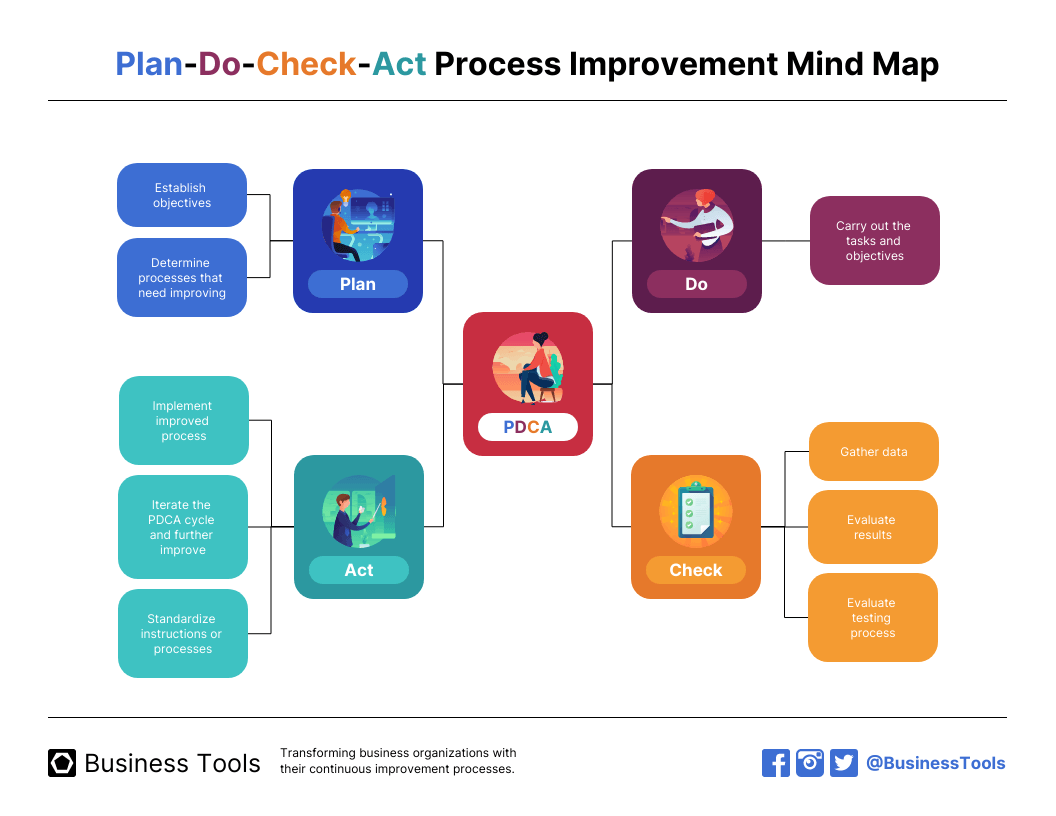
Plan-Do-Check-Act (PDCA) is a continuous change management cycle that was first established by engineer and management consultant W. Edwards Deming in the 1950s. Back then it was called a Deming Wheel , which was later modified by Japanese engineers to arrive at its current definition.
The steps involved in PDCA are obvious:
As the name suggests, process improvement refers to the task of identifying, analyzing and improving existing business processes that are often outdated or no longer efficient enough.
While the term is most often used in a business context, it can refer to any decision or actions that aim to improve a process, be it as simple as finding a shorter route on your drive to work or as complex as improving the whole customer service process of a corporation.
Back to its business context, process improvement could target wasteful spending, poor office design, IT system downtime, employee disengagement and many other issues that can doom an organization.
Process improvement can’t be effective without proper process documentation policies in place. If you haven’t documented your company’s processes yet, we can help with that. Check out these process documentation templates to get you started.
There’s more than one type of process improvement plan, which we’ll explore more in detail . In addition to the example we shared above, a process improvement plan can also consist of 6 steps:
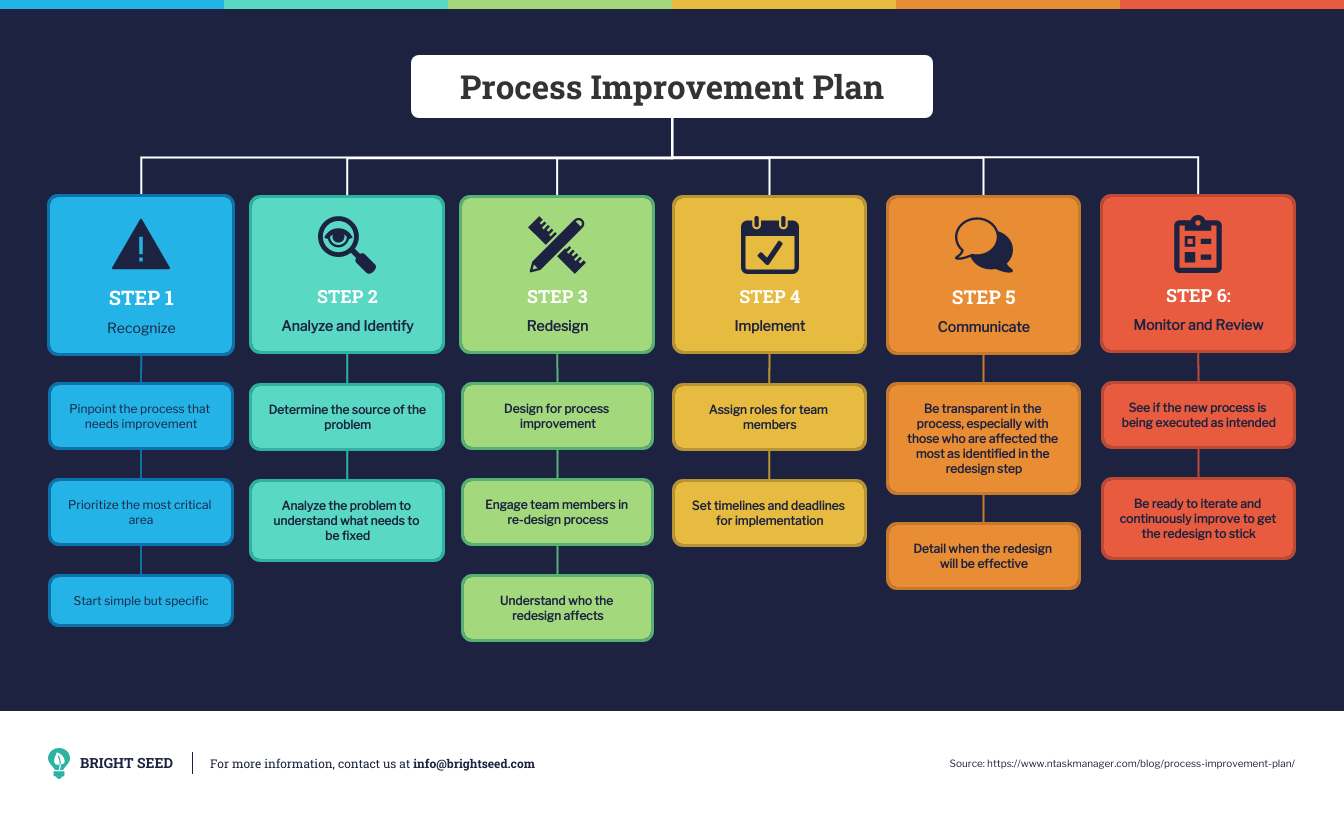
Or 4 steps, like this one which is developed using the Plan-Do-Check-Act (PDCA) model:
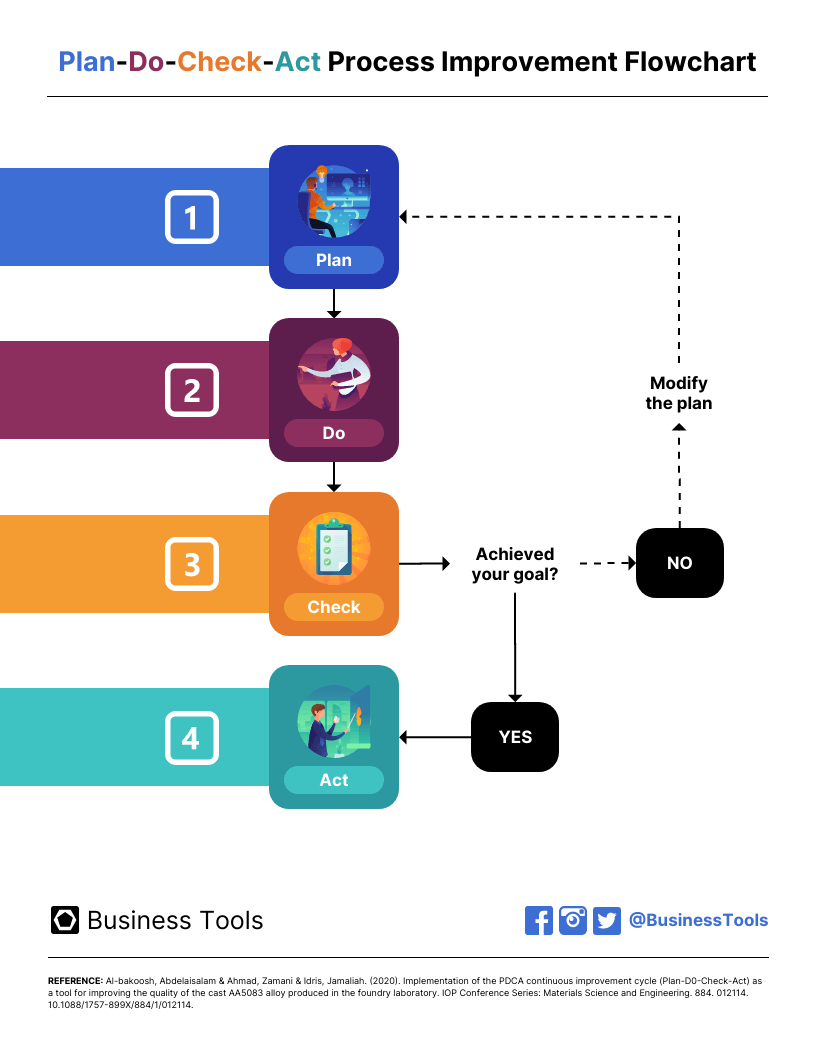
These steps are, of course, quite simplified and some process improvement plans will require months or years of changes to procedures, hiring practices, training, systems, software and more.
For example, a process improvement plan for a company lacking a specific skill set in its employees can mean hiring new staff and training the existing one. In cases like this, other tools like individual development plans can be useful.
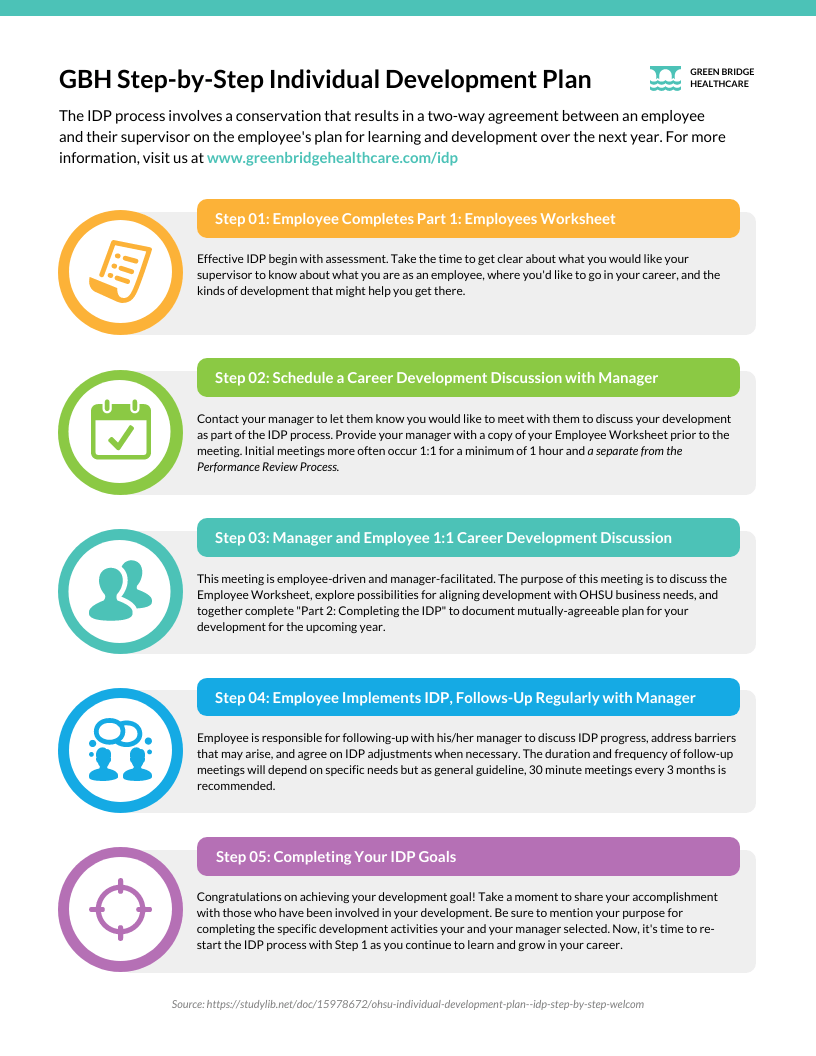
This individual development plan designed for healthcare workers is a good example of how process improvement plans can branch off into other areas.
And once the new process is in place, it’s important to communicate it to the team effectively. That could be through a process infographic , timeline , mind map or other types of visual communication .
Customize this project communication plan to help streamline communication channels between teams working on the same project:
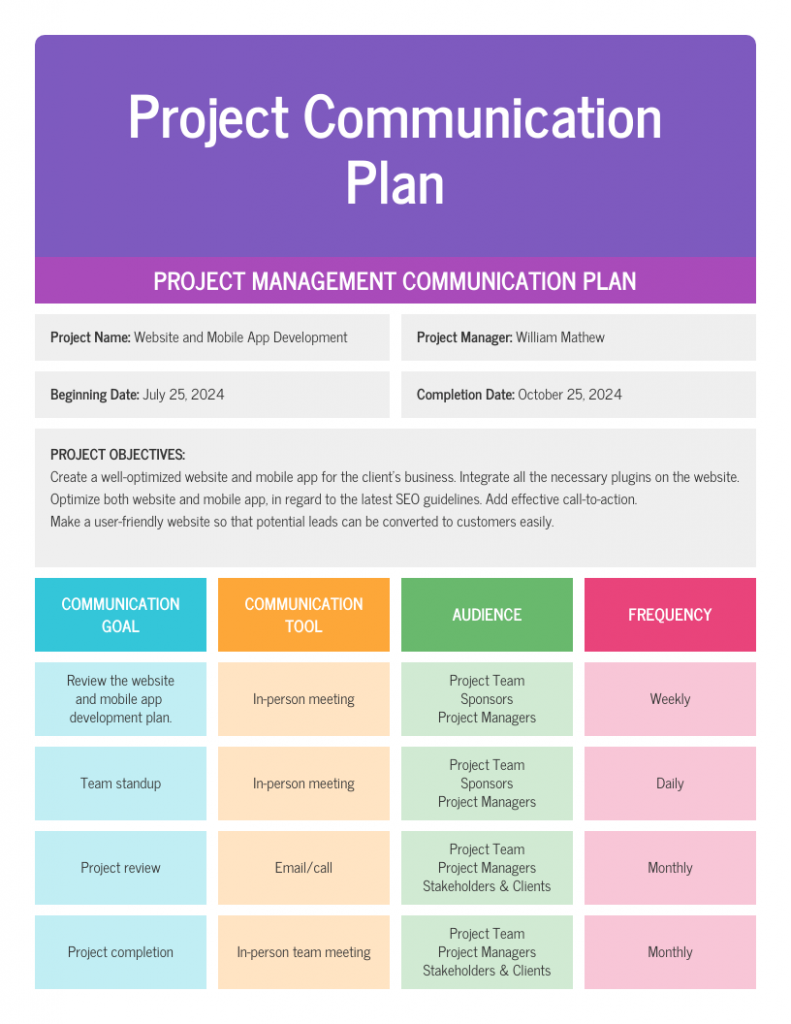
Another example of a process improvement plan, this nursing care plan is used in a healthcare setting only. It could be used to illustrate a new plan aimed at addressing gaps in communication and patient care. But you can use the process suggested in this plan and apply it to any industry.

This creative design process infographic would be an ideal way to share with a creative team a proposed new method of taking clients through the design process. Consider color-coding new or revised steps if creating a piece like this to share a revised company process.

Customize this action plan mind map once you’ve settled on a new process so that team members see steps involved in their tasks but also keep the main objectives in mind.
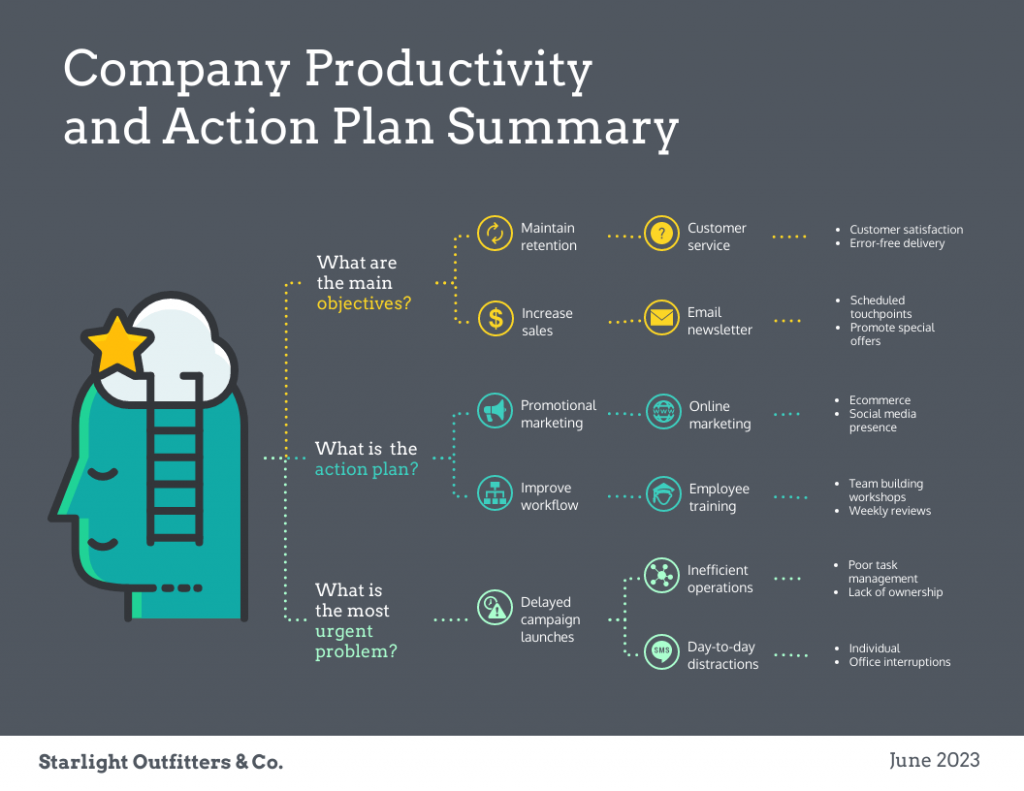
Process improvement plans are useful for organizations of all types and their output can include simple verbal instructions. But most companies benefit from creating charts, presentations and infographics to communicate a variety of aspects surrounding the plan.
Check out these process improvement plan templates that may help your organization.
Process improvement plan development examples
Developing a process improvement plan is complicated, but visual tools like infographics can make it easier for your team to grasp the steps involved.
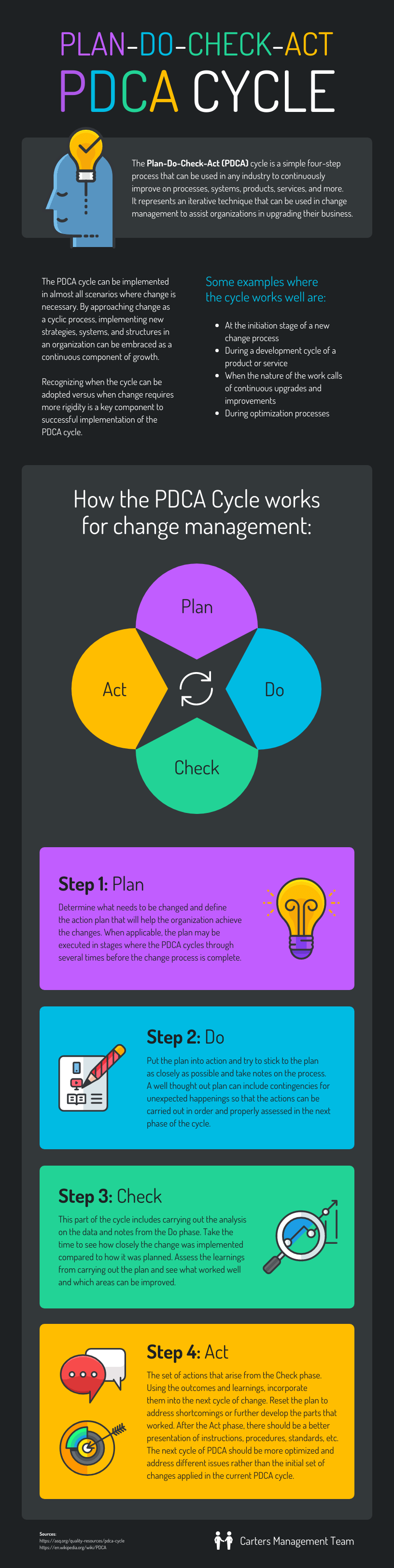
Help your management team and employees understand the steps involved in the plan-do-check-act (PDCA) cycle with this infographic. Customize it for your needs by outlining specific actions they need to take in the bottom section.
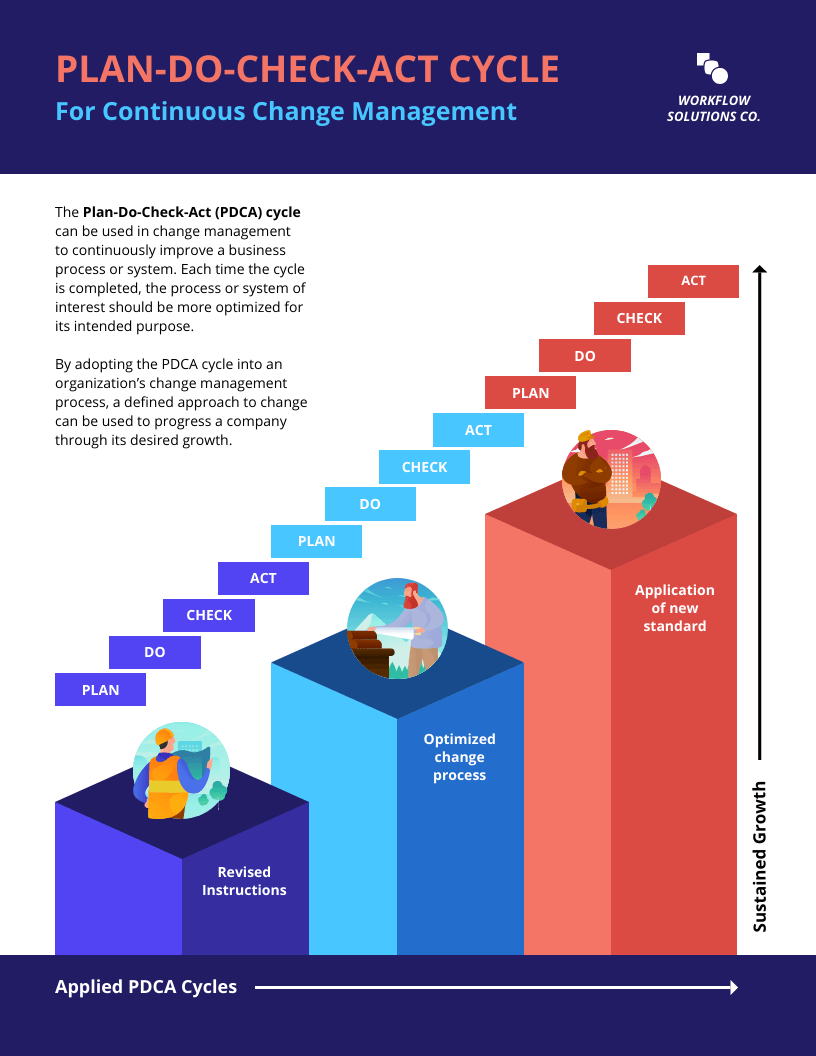
This PDCA cycle infographic is ideal for companies that are implementing improvement plans across their organization.
Revised process examples
Once you’ve settled on a new way of doing things, explaining the new process clearly to employees (and sometimes customers) is critical. Process and timeline infographics are helpful, as they allow people to visualize the new steps.
Here’s an example of a process improvement plan to revise customer support process, built based on the PDCA concept:
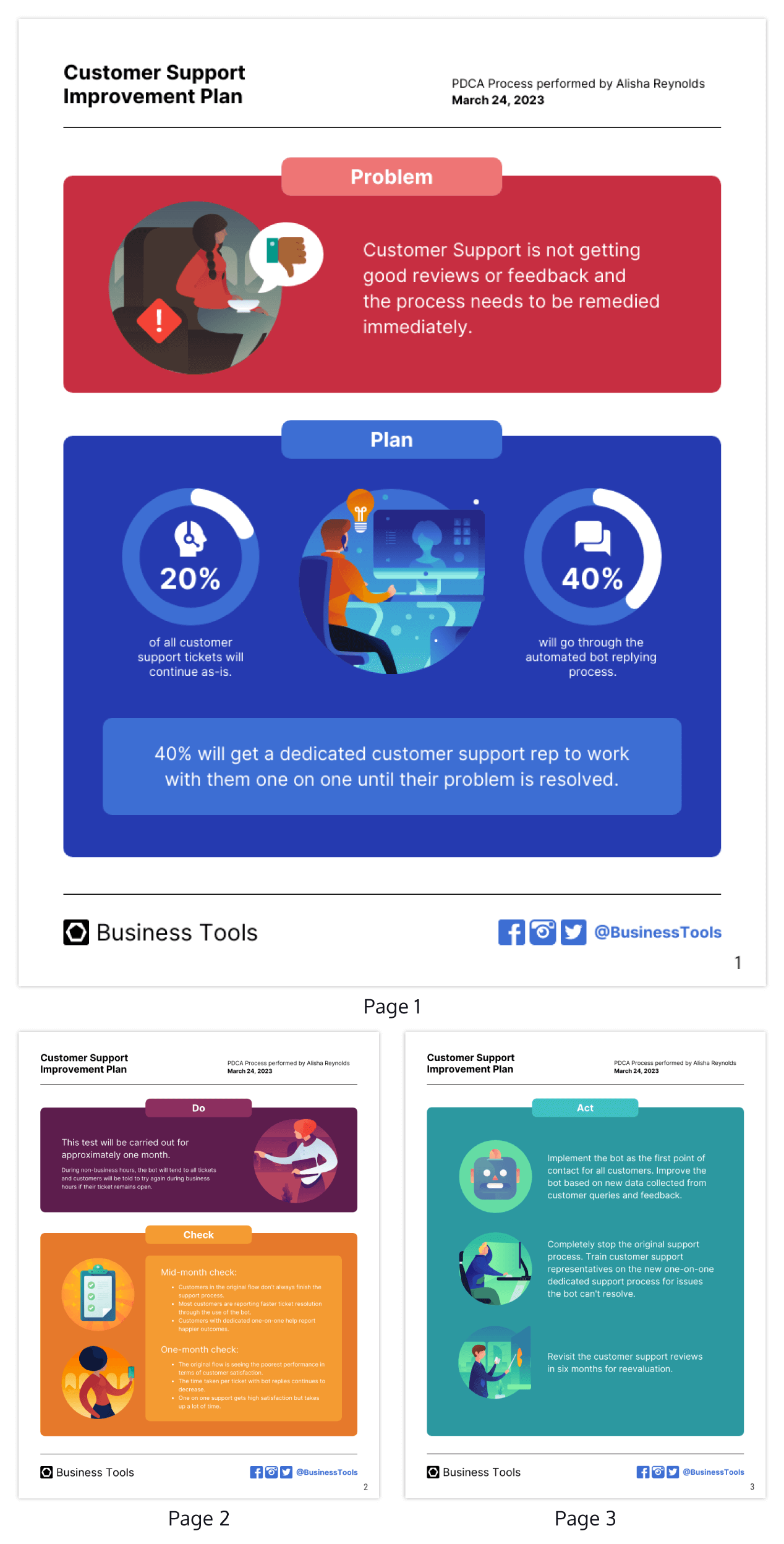
Customize this project management process infographic for the new process you and your teammates are creating. Quickly change out icons for ones that apply to your business and use My Brand Kit to ensure the design aligns with your corporate identity.
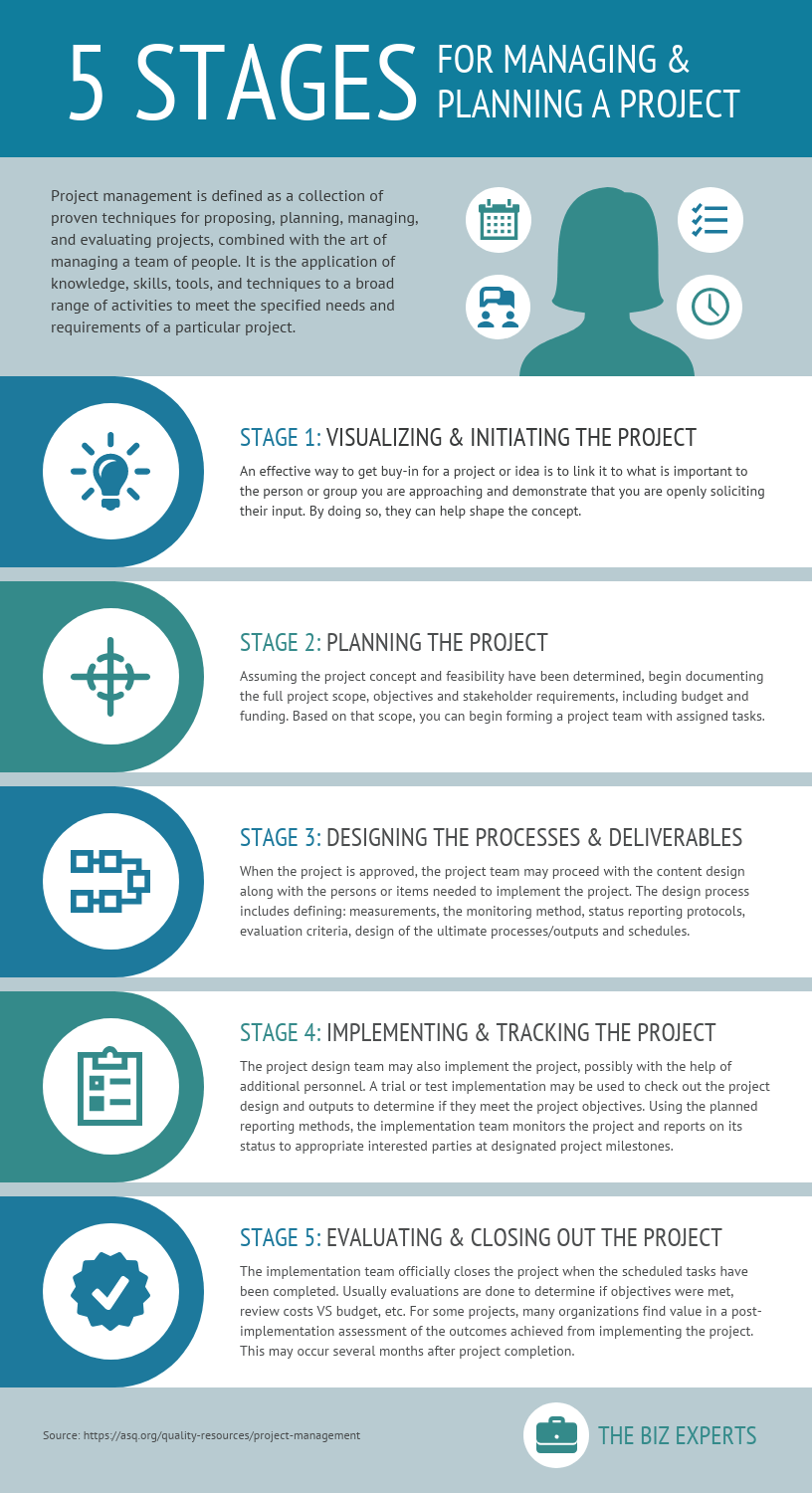
Use this colorful process infographic for a new process that has several steps. Lengthen or shorten as needed to cover all the steps in your revised process. Or use a template like this to create a process improvement action plan as you begin your work.
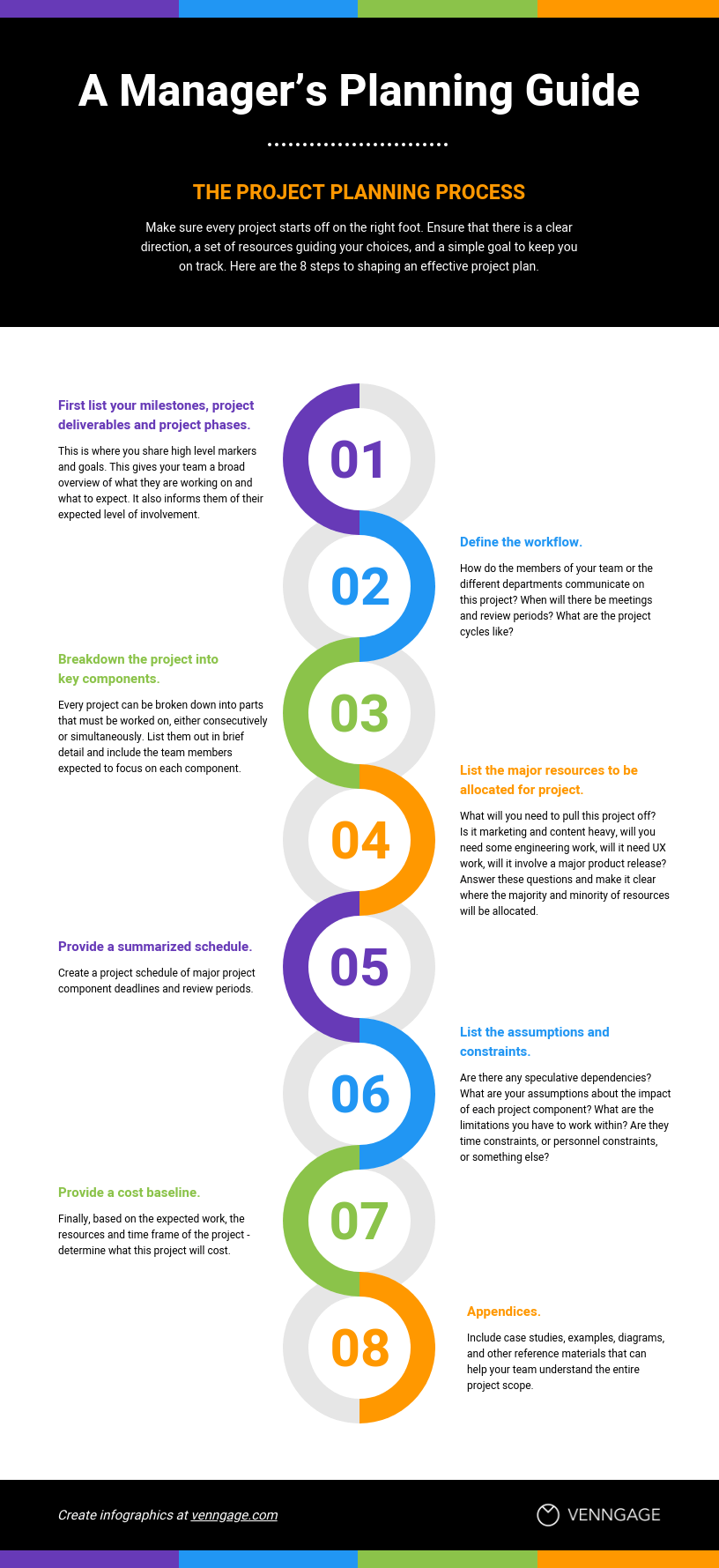
Revised policy examples
Process development plans can easily spill over into a variety of business areas and it’s often necessary to craft new policies and procedures on the way to your new process. Infographics and other tools can help you spread the word and document these new policies.
If your new process will require added documentation that needs to be signed by an employee or their supervisor, customize this procedure infographic that explores how to submit expense claims. Change the title, content and illustrations for your needs.
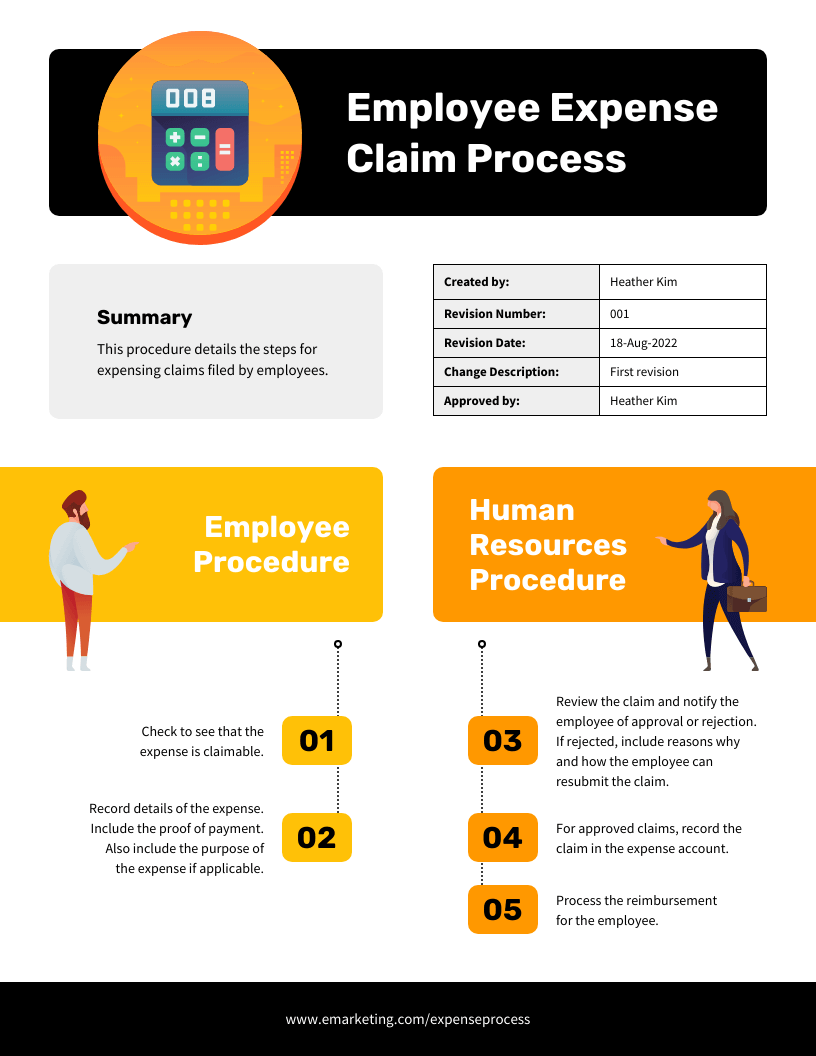
Perhaps your process improvement plan revealed that nobody in your organization is prepared for a disaster or emergency. The output of your process improvement team could be a business continuity plan like this one.
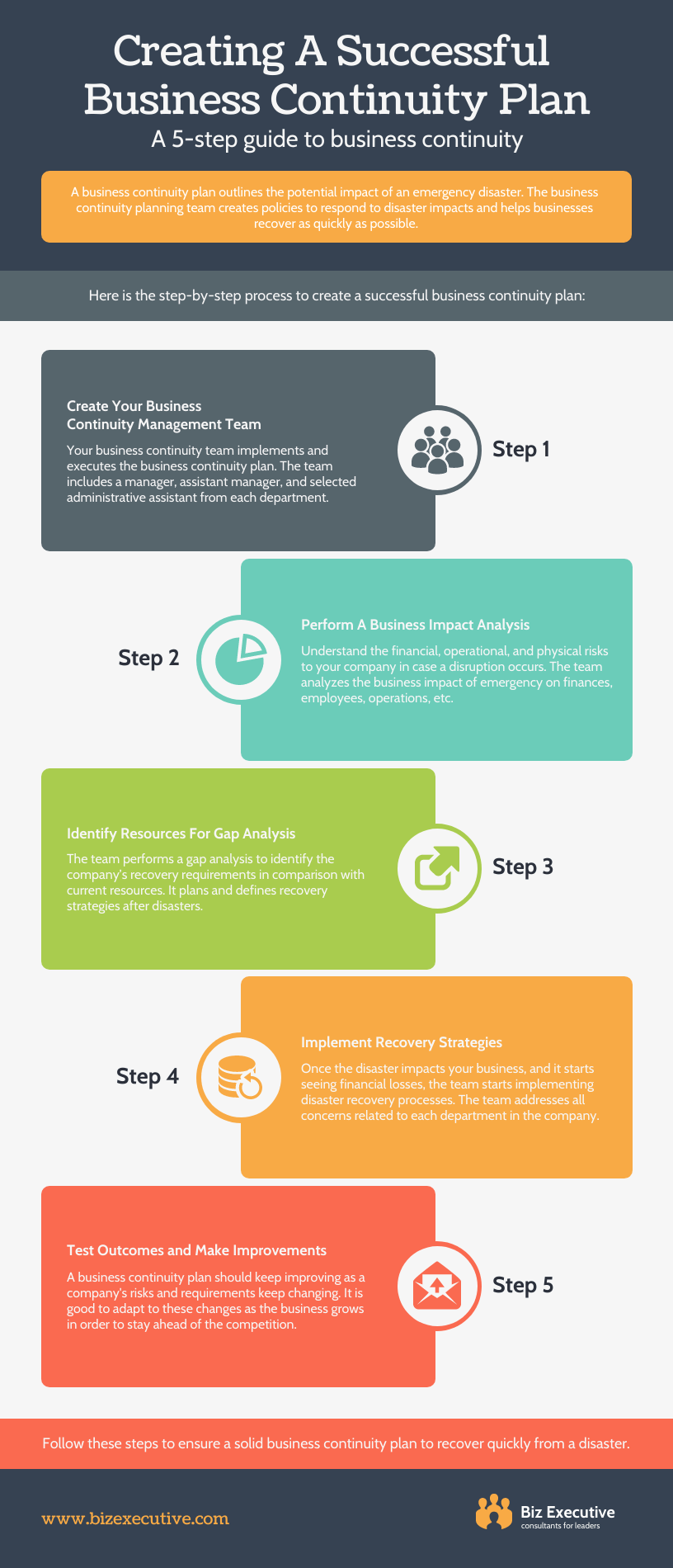
Employee development examples
The success of your new process will depend entirely on your team’s ability to execute it and many organizations find that a major reason why their current processes aren’t working is that team members lack certain skills. So, employee development is often involved in executing a revised plan.
Help team members visualize the skills they need to develop by working with them to create a mind map like this one.
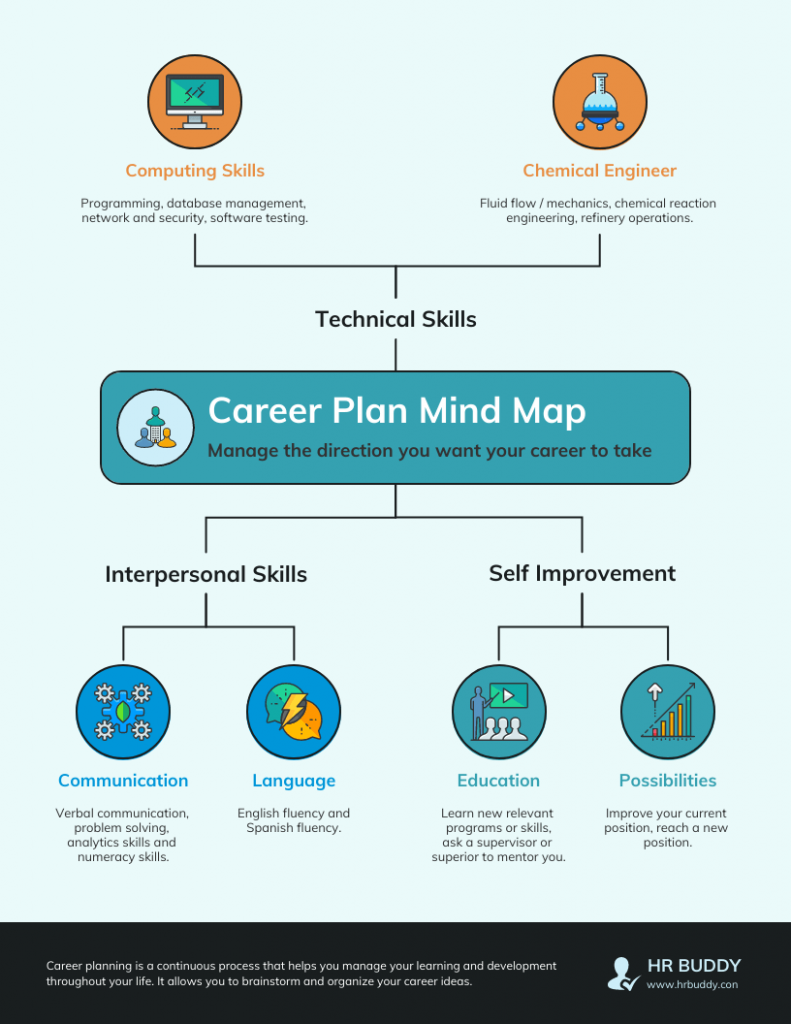
Customize this career planning infographic for team members as you work with them to help them build the necessary skills. While this example is about career planning in general, it’s easy to customize with specifics for your employees.
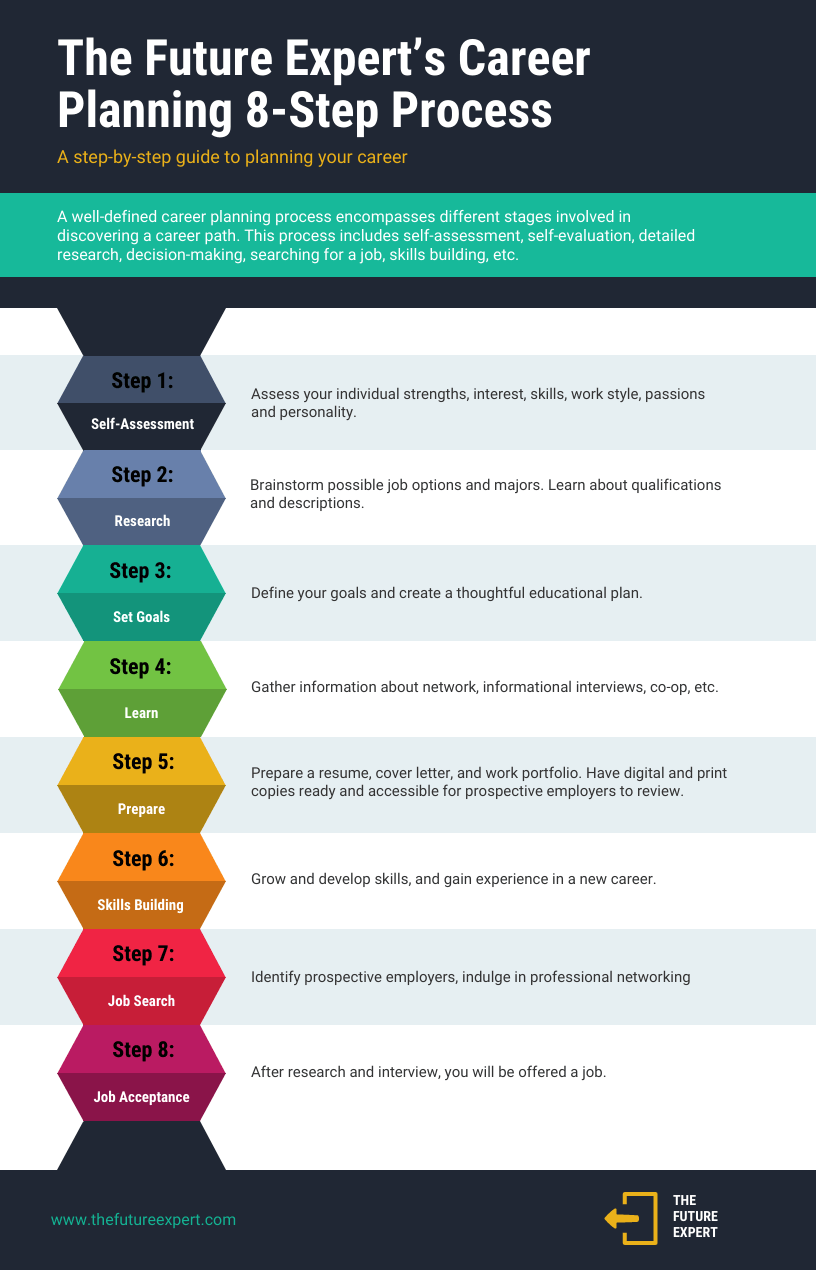
Change management examples
Humans by nature are resistant to change and your organization may find it challenging to implement a new process. These change management plans may help you communicate and motivate your team.
Follow the steps in this change management process infographic to break through your team’s stubborn adherence to old, inefficient processes.
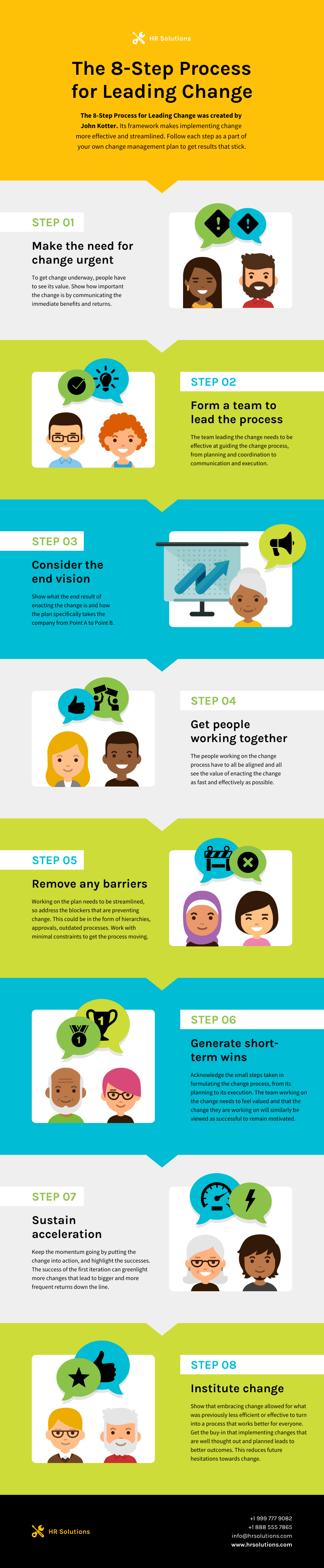
Update this planning process infographic to help get your team on the side of change. Employees who feel they are involved in steering the company in the right direction will feel a strong sense of ownership in the entire process improvement operation.
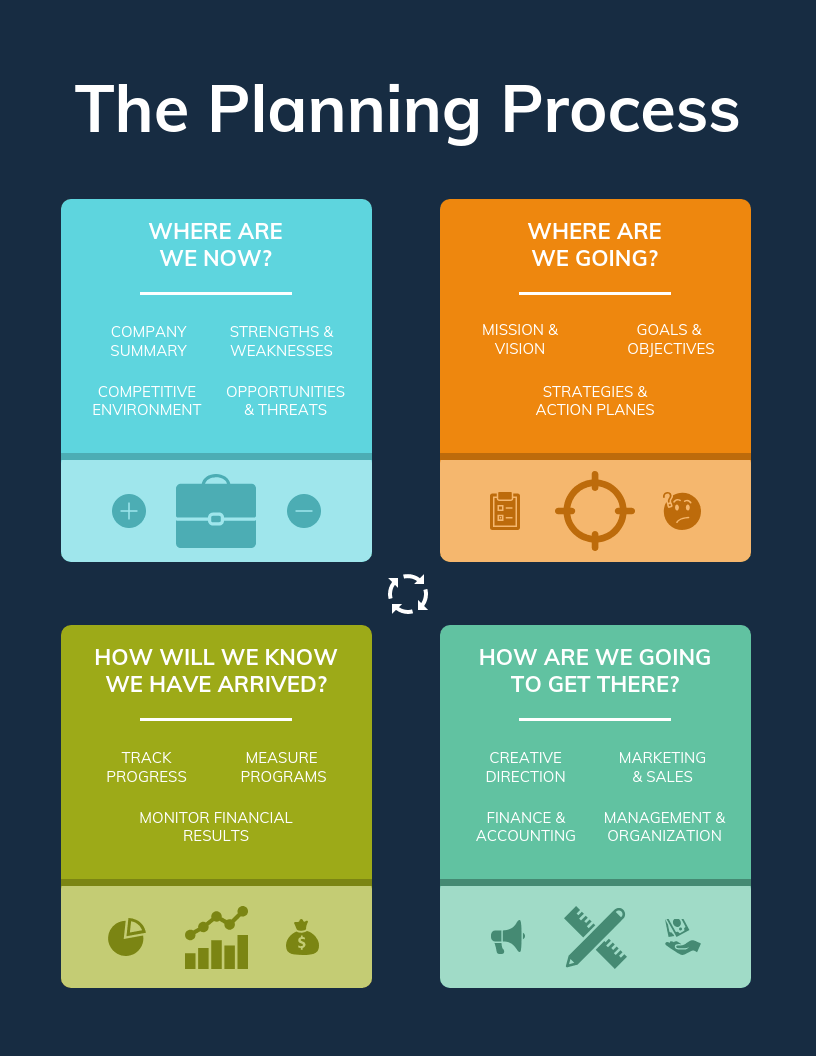
There are many benefits of diving into a process improvement plan in your organization and the most obvious and important is to improve your company’s overall efficiency. Doing so can make the business more profitable in the long run. But that’s not where the benefits end.
The biggest benefits of a process improvement plan include:
- Employee satisfaction : More productive workers make a company more money over time, but they also gain a sense of accomplishment and self-improvement.
- Customer satisfaction : Many process improvement plans target tasks that are customer- or client-facing and making sure your customers are satisfied is crucial for any organization.
- Agility : The business landscape is constantly changing, so putting a process improvement strategy into place will equip your organization to handle future disruption.
- Safety : Efficient processes are helpful to reducing workplace accidents and repetitive stress injuries and examining the physical activities employees are doing as part of their jobs can help make them safer overall.
- Modernization : Organizations that resist technology are likely not long for the world and process improvement plans are ideal for adapting new technologies to your company’s workflows.
- Innovation : In any company, there are things you do because that’s the way you’ve always done them. But breaking those processes down to see how they function is one of the best ways to spark a new idea and create innovation in your organization.
Do you have more questions about creating a process improvement plan for your organization? We’ve got answers.
How do you propose a process improvement plan?
Communication is a critical part of process improvement. If people don’t know or understand why change is needed, it’s unlikely they’ll embrace any new processes. Proposing a process improvement plan requires an individual or small group who will own the plan’s development from start to finish and can be evangelists for the plan across the organization.
What are the contents of a process improvement plan?
In general, process improvement plans must include a definition of the process, an explanation of its steps, an identification of the ways in which it falls short, a proposed new process and a mechanism for monitoring the revised steps.
How do you find areas of process improvement?
If you knew exactly why your organization wasn’t as successful, you’d fix it right away. But finding areas of process improvement means keeping your ear to the ground and observing the organization in an objective way. Common areas of process improvement include authority overlap, constantly missed deadlines, poor quality control, physical safety issues, fixing errors rather than preventing them, employee and customer dissatisfaction and excess spending.
Enhance productivity and eliminate frustration with process improvement plans
Identifying where your company is failing in the processes used across the organization is not an easy task, as it requires dispassionate examination of how you may be falling short. But visual communication tools like infographics, mind maps and process illustrations can help communicate issues to your team and get everyone moving in the right direction.
Interested in visualizing your process improvement plans and gaining buy-in from stakeholders? Start by registering for a FREE Venngage account and choose a suitable process improvement plan to customize. Our templates are professional-looking, fully customizable and really easy to edit, even if you don’t have design experience.
- Change Management
- Strategic Planning
- GE Work-Out
- Business Process Improvement
- Team Effectiveness
- Executive Coaching
- Strategy Development/Implementation
- Process Re-engineering
- Supply-Chain Management/Supplier Development
- Cost-Reduction
- Product-Yield Increase
- Cycle-Time Reduction/Productivity
- Non-Value-Added Work Elimination
- Organizational Integration
- Global Standardization
- Client List
- Testimonials
- Case Studies
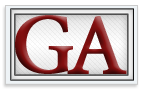
Gagnon Associates
Management & Organizational Consulting

Case Study: Business Process Improvement
This Case Study illustrates how Gagnon Associates used its Business Process Improvement capability to optimize a client’s new-product development process:
The Company
A formerly high-flying, enviably profitable surgical products division of a major health care company. Makers of state-of-the-art, reusable and disposable devices for the rapidly-growing, least-invasive surgery market.
The Problem
Declining profits due to increased costs associated with a lack of discipline and lack of customer focus in screening new product ideas, initiating new-product development projects and managing the new-product life cycle in the post-introduction phase.
The Approach
Management enlists Gagnon Associates consulting support to lead the effort to: a) assess new-product screening, new-product development, and post-product introduction processes and related issues, and b) reengineer these interrelated processes for improved efficiency/effectiveness.
Four “boundaryless,” client teams are created, including representatives from finance, R&D, marketing, sales, purchasing and other functions. Three teams focus on one each of three previously mentioned processes. The fourth team analyzes a recent unsatisfactory surgical pump introduction for additional insights into deficiencies in the new-product introduction process.
Over three days of an intense, highly-interactive, four-day intervention, teams work both independently and in close coordination, as needed, to: a) define existing process deficiencies, b) reengineer processes, and c) address key process interrelationships. Throughout, Gagnon Associates catalyzes and facilitates the process by providing online, work-group leadership as well as “just-in-time” training and coaching on underlying process reengineering tools and techniques.
The Results
Teams completely reengineer new-product screening and new-product development processes and develop a more formal process for managing the post-introduction phases of the product life-cycle. On the fourth day of the engagement, the division’s management team reviews and approves the newly reengineered processes in an interactive forum, attended by all team members and moderated by Gagnon Associates consulting staff .
Management is so pleased with the newly redesigned processes that it commits to testing approximately 120 new product development projects currently in the pipeline against the new model and estimates that, as a result, some 40 to 50 resource-draining projects of questionable value to the customer will be eliminated.

An official website of the United States government
The .gov means it’s official. Federal government websites often end in .gov or .mil. Before sharing sensitive information, make sure you’re on a federal government site.
The site is secure. The https:// ensures that you are connecting to the official website and that any information you provide is encrypted and transmitted securely.
- Publications
- Account settings
Preview improvements coming to the PMC website in October 2024. Learn More or Try it out now .
- Advanced Search
- Journal List
- Int J Environ Res Public Health

Applying Lean in Process Innovation in Healthcare: The Case of Hip Fracture
Manuel francisco morales-contreras.
1 Department of Management, ICADE, Universidad Pontificia Comillas, ICADE, 28015 Madrid, Spain
Pedro Chana-Valero
2 Fundación San Juan de Dios, Centro de CC de la Salud San Rafael, Universidad Nebrija, 28036 Madrid, Spain; se.ajirben@anahcp (P.C.-V.); se.ajirben@agicrage (E.G.G.)
Manuel F. Suárez-Barraza
3 International Business Department, School of Business and Economy, Universidad de las Américas Puebla (UDLAP), Puebla 72810, Mexico; [email protected]
Andrés Saldaña Díaz
4 Hospital San Juan de Dios León, 24010 León, Spain; moc.liamg@zaidlasna
Elena García García
Academic literature and practitioners acknowledge that there is a need to improve efficiency and service quality in the healthcare industry. In Spain, osteoporotic fractures represent a great cost in socio-economic and morbi-mortality terms, hip fracture being the surgical pathology with the second highest consumption of resources. The research questions that govern this study concern the use of Lean principles to identify waste, and an evaluation of the application of an innovative approach in the hip fracture surgery process. A research design based on a case study and action research was developed. Findings relate to (i) the identification of the main types of waste or muda (being the most frequent delay, transportation, over-processing and defects); (ii) the analysis of existing processes based on a Lean approach (identifying opportunities for improvement as a reduction of the number of steps and participants, improving communication, automation, standardization, etc.); and (iii) the application of an innovative process based on the Lean approach and action research in the healthcare industry. This research provides insights for academia, practitioners, management, and society: waste identification and process redesign helps to continue the improvement of operations, increase efficiency, reduce costs, and enhance services, providing benefits to patients, families, hospital employees, and the healthcare system.
1. Introduction
Among the high-risk industries, healthcare is the most poorly managed of all and is very late in coming to recognize the importance of the system factors that underlie adverse events [ 1 ], making a healthcare system analysis and support for patients and staff an absolute priority [ 2 ]. Overtreatment, undertreatment, overdiagnosis, underdiagnosis, uncontrolled costs and budgets, and medical treatment errors have been reported in health systems across the developed world [ 3 ]. Medical error can be defined as a deviation from the process of care that may or may not cause harm to the patient [ 4 ]. In the USA, medical errors are the third cause of death after cancer and heart disease. In Spain, it is estimated that medical errors were involved in 25.9% of court verdicts, 98.5% of them resulted in compensation awards [ 5 ], leading to an increase in healthcare costs. But not only medical errors impact patient experience and lack of efficiency in healthcare; other examples are: delays, long waiting times, waiting lists for service delivery, lack or excess of capacity, lack or excess of inventory, patients going to the hospital several times until a service is provided, unsatisfied patients, etc. The management of a healthcare organization needs to be able to make decisions on the value delivered to patients and relatives, so patient value must be the key to making responsible decisions as a health system. Porter defines patient value as the patient-relevant medical outcome divided by cost [ 3 ].
Funding and efficiency in the health sector becomes a priority issue in the context of an ageing population [ 6 ]. To address the crisis, the NHS (National Health Service, UK) has turned to the use of different “quality improvement” methodologies, often discovered outside the health sector, Lean management systems being one of them [ 7 ].
The term Lean applied to production or management systems was used for the first time by Womack et al. [ 8 ] It was derived from the Toyota Production System, which was oriented to the continuous improvement of quality, productivity, and efficiency, as well as to the reduction of costs and delivery times within the Japanese automotive industry [ 8 , 9 , 10 , 11 , 12 ]. Lean is doing more with less and refers to a methodology that pursues the identification and elimination of waste ( Muda in Japanese) [ 8 ]. Waste is defined as any activity that does not add any value from the customer perspective, thus reducing the efficiency of a process and increasing its costs [ 9 , 11 ]. Literature states that seven types of waste could be found in any process: defects, movements, process, inventory, overproduction, transportation, and time [ 8 , 9 , 11 , 12 ].
Although Lean management systems were originated within the manufacturing sector, there is a growing interest for its implementation in service companies [ 13 ]. There are many opportunities of finding waste in the service sector as the processes tend to be slow, and tend to include high values of work in process (or customers waiting), which has an impact on the costs, service quality, and customer satisfaction [ 14 ].
Lean practices, with the aim of improving medical care processes, can help to achieve more reliable healthcare systems by addressing the three steps for reducing system errors in healthcare, proposed by Makary et al., in 2016 [ 15 ]: making errors more visible (facilitate a culture of speaking up), responding to error (support clinician needs), and making errors less frequent (foster culture of safety). Lean has been implemented in different areas in healthcare as intensive care units, X-Ray, cardiology surgery, oncology, mental health units, and clinical laboratories [ 7 , 16 , 17 , 18 , 19 , 20 ]. A national survey in the United States found that 70% of hospitals used Lean healthcare or related methodologies to deal with both quality and cost issues [ 21 ]. Gonzalez-Aleu et al. in 2018 analysed the critical success factors when implementing continuous improvement projects in hospitals [ 22 ]. But there is not enough evidence to address its sustainability in broad healthcare adoption as well as its impact in quality healthcare [ 7 ] and achieve both effectiveness and efficiency improvements [ 18 ]. Thus, it remains a “challenge for academics and practitioners to evaluate Lean healthcare under a more critical perspective” [ 17 ].
Hip fracture is one of the leading pathologies in terms of resource consumption [ 23 ], with a progressive increase in the estimate of new cases per year [ 24 ] and a high-risk patient profile. Applying Lean to this scenario, with the aim of identifying barriers, sensitized with the patient’s needs and mapping the experience of the different actors involved, can improve quality of care and increase the efficiency of processes, helping managers and staff address more complex issues and deepen our understanding of how Lean works in healthcare [ 25 ].
The main research questions that govern the study are:
- RQ1. → What types of waste or muda could be identified around a hip fracture surgery process?
- RQ2. → How a process innovation methodology using Lean techniques is applied in healthcare, in particular in a hip fracture surgery processes?
With the aim of answering these research questions, we decided to conduct a methodology based on a case study and action research, by involving the research team in the process evaluation and redesign. The article is structured as follows: (i) an introduction; (ii) a literature review and theoretical framework; (iii) a description of the research methodology; (iv) the case study results; (v) discussion; and (vi) conclusion.
2. Theoretical Framework
Hip fractures are potentially catastrophic (deadly) events with adverse outcomes including alteration in function, institutionalization, and death [ 26 ]. Mortality rates have increased in ageing patients who live alone and who have poor pre-fracture mental status and mobility [ 26 , 27 , 28 ], other associated factors being: white race, osteoporosis, previous hip fracture, level of physical functioning, medication use, and hormonal and dietary factors [ 29 ]. Osteoporosis fractures are the fourth leading cause of chronic disease morbidity. Over 2 million women and 750,000 men are estimated to suffer osteoporosis at the level of the femoral neck, with an expected prevalence of 24.2% in women between 70 and 80 years old. The cost to the Spanish healthcare system related to osteoporosis fractures amounted to 4.2 billion euros in 2017 and is expected to increase to 5.5 billion in 2030 [ 30 ].
More than 500,000 acute hip fractures will occur annually by 2040; each year at least 300,000 old people are hospitalized by hip fractures [ 24 ]. The number of geriatric hip fractures is expected to rise annually all over the world related to the elderly population ages, which will significantly increase care costs for healthcare systems, patients, relatives, and societies. The incidence of this complication for the elderly in the United States is expected to grow to half a million by 2040, with a worldwide incidence of geriatric hip fractures reaching up to 4.5 million by 2050 [ 31 , 32 , 33 ]. In Spain, hip fractures are the second highest obstetric and surgical condition in resource consumption after colorectal and anal cancer regarding the average costs of the Diagnosis Related Groups (DRG) [ 23 ], with an estimation of 263,351 new hip fractures in women and 84,213 in men between 2010 and 2020, with an existing tendency to increase in older age groups (>80 years) [ 34 ]. In the 2018 National Registry of Hip Fractures (RNFC) report, the overall profile, of the 11,431 patients included from the 72 participating hospitals, described a profile of patients with an average age greater than 87 years, usually living at home, with 76% being women [ 35 ].
Looking for efficiency in the process at hand, with a mortality rate within the first year at 20–33% (that may persist beyond 5 years) is a priority, as is relying on value-based healthcare models [ 31 , 32 ]. In the first three months after surgery, older adults have an eight times higher risks of dying of a hip fracture compared with people who have not suffered from it, continuing the risk of death still in the first ten years [ 36 ]. Related to functional outcomes, which directly impact the patient´s social dimension, it is important to describe functional outcomes such as the inability to walk independently (40% of hip fractures patients), the situation of vulnerability, needing assistance to perform daily tasks (60%) and patients who become totally dependent requiring a nursing home one year after fracture.
Social impact is relevant, according to a study published in the British Medical Journal, which detected 80% of women over 75 years who would prefer to die rather than experience the loss of independence and living in a nursing home after hip fracture discharge [ 37 ].
According to Bradeanu et al., health and social care for hip fractures in the elderly in one year amounts to two billion euros in the UK, where the annual incidence was 79,243 euros in 2019, expecting to increase to 104,000 cases by 2025. Dementia incidence will reach 75.6 million in 2030 and 135.46 in 2050 in the whole population, but doubles every five years among people aged 65 to 90. They also highlight the social impact that both pathologies together have on the caregivers, including depression, a higher risk of developing anxiety, and more hours per day spent helping patients. Furthermore, hip fractures are associated with the development of disability, depression, and cardiovascular diseases in the elderly, with additional cost for society [ 36 ].
Therefore, with an increasing incidence and associated poor clinical outcomes, it is relevant to evaluate the impact of hip fractures in the elderly not only on the healthcare system but also in terms of the social impact that is generated by patients as well as by their relatives, the society and the environment [ 32 ]. Living in changing times regarding healthcare, political agendas, budgetary limitations, and new leaderships contributes to demanding from professionals the provision of greater value with fewer resources, promoting a bigger impact on patients and other stakeholders [ 38 ].
Nowadays, patients are increasingly demanding immediate, high-quality, and individualized care to their specific needs. To meet these demands, strategies are needed to combine sustainable quality improvement with increased efficiency [ 39 ]. Improving and ensuring effectiveness of clinical procedures is necessary, but so is improving healthcare performance using appropriate indicators: what works, for whom, and in which circumstances? This must be addressed to not leave anyone behind [ 40 , 41 ].
In a progressive ageing population scenario, indicators that measure the social value of interventions are becoming key indicators to be analyzed in a process of quality continuous improvement. It is important to detect key performance indicators during the process analysis so that, once improvements have been implemented, they can be measured; because collecting data is not enough, they must be used to improve healthcare [ 40 ].
Despite being the focus on which to work, currently the most important indicators to measure the performance of the health care process are the length of hospital stay (LOS), i.e., the number of days comprised between the date of a patient admission and the discharge date [ 42 ], as well as the intra-hospital, 30-day, and year-round survival. Exploring Lean healthcare on patient flow, the main outcomes categorized related to the utilization of services and access to services [ 21 , 43 ] are the length of stay, mean waiting time to see a doctor, mean waiting time to get treatment, median time for daily treatment, median waiting time to see a professional (nurse preparation), and the median process time of being discharged. Therefore, LOS and shorter waiting times after Lean healthcare intervention were the most common measures related to process outcomes. Related to the hip fracture care pathway, usual measurements are time to surgery, duration of surgery, detection of complications, hospital cost, allogenic transfusion rate, thirty-day readmission, and in-hospital mortality [ 44 , 45 ].
The provision of quality health services depends on an adequate and efficient execution of each of the processes in which not only clinical activities exist, but also in which a series of non-clinical support activities are executed by different types of resources, which varies from one organization to another. These processes are highly complex and dynamic, and it is becoming increasingly common to design them ad hoc with a multi-disciplinary character but, seeking a balance in the improvement of processes between the generation of impact on patient´s quality of life on the one hand and the need to reduce costs, reduce waiting times, and to improve the productivity of each resource on the other, is not an easy task [ 46 ].
In 2012, the European Commission proposed a new cooperation framework for innovation in the field of active and healthy ageing, adopting the “Quadruple Helix” innovation model, which aims to generate shared value involving and benefiting civil society, private companies, academia, and the public sector, thus creating a powerful innovation ecosystem [ 47 ]. Designing strategies to implement effective solutions according to this model requires the use of specific tools that can trigger improvements in the management and handling of risks, including psychosocial risk management and, subsequently, better well-being [ 48 ]. A useful method is the “design thinking” or user-centred design, proposed by the Stanford University Institute of Design, which establishes five unavoidable phases in the process of designing a digital solution, so that it is finally adopted by the target audience: empathizing, defining, devising, prototyping, and evaluating [ 47 ].
A more sceptical and scientifically rigorous approach to the development, evaluation, and dissemination of quality improvement methodologies is required, combined with the demand of more robust evidence for the methods and approaches that they use, in those areas of knowledge where a mix of theoretical, empirical, and experimental evidence is used to enable guidance and planning for their application [ 49 ].
Strategies focused on the improvement of care quality, waiting times, resource consumption, etc., with the aim of assuring sustainable high-quality care, are needed. For instance, innovative methods such as design thinking combined with Lean. Lean has proved to be a method that has become, in the past decade, one of the most commonly used as a quality improvement approach in healthcare settings to improve delivery of care [ 25 , 50 ], guaranteeing the improvement of the effectiveness and efficiency of health care delivery, and providing an impetus for establishing the best practice within an organization [ 42 ].
The Lean methodology approach was developed in the car manufacturing industry, and was later adopted in the healthcare field with the aim of improving quality of care and the efficiency of processes [ 25 , 39 , 51 ]. The first authors to carry out research on Lean in health were Young et al. in 2004, and Spear in 2005 [ 52 , 53 ]. Both argue that carrying out Kaizen and Lean Thinking efforts in health systems can help eliminate errors, delays, inadequate processes, duplications, and all kinds of MUDA in the activities of health services. Another pioneering research work on the subject was that of Kollberg and Dahlgaard et al., in 2007, who emphasize in their article that continuous improvement techniques help to significantly improve the performance of processes and services in health systems (specifically in Sweden in this case) [ 54 ]. Drotz and Poksinska also confirm the benefits of implementing Lean and Kaizen in health organizations because it generates positive effects on the positions and roles of medical personnel, moving from a bureaucratic style to an approach of agile processes and teamwork [ 20 ]. On the other hand, authors such as Bortolotti et al. have found 14 specific factors that increase the ability of employees to solve problems when using Kaizen in health systems [ 55 ]. The clarity of goals, the degree of the difficulty of objectives, the autonomy of the work teams, and the support of the top managers are critical to the success of the application of Kaizen according to these researchers.
On the other hand, Ortíz-Barrios and Alfaro-Saiz (2020) carried out a literature review of the application of process improvement in emergency processes in health hospitals [ 56 ]. The selected papers were categorized considering the leading ED problems and publication year. Two hundred and three (203) papers distributed in 120 journals were found to meet the inclusion criteria. In Latin America, Brazilian authors such as Coehlo et al. (2015) present a case study of process improvement, in which the performance improvement of the total workspace was 75% and the reduction in waiting for patient care went from 2 h to 30 min [ 57 ]. Coelho et al. (2015) also point out that Lean and Kaizen’s efforts can eliminate at least three hours a day of overtime in hospitals in Brazil. Curatolo et al., in 2014, also performed a literature review indicating that a Lean approach with a high-methodological maturity level that includes the 11 characteristic activities of process innovation or Business Process Improvement has never been reported [ 58 ]. Considering this, the paper suggests a meta model for a high-methodological maturity-level Lean method based on the characteristic activities of Business Process Improvement. Finally, Meyer et al. present the successful application of Lean Six Sigma, a set of quality improvement (QI) tools, to streamline their processes and uncover the root causes of program inefficiencies. All this for a hospital that performs treatments for cancer patients by Tobacco [ 59 ].
Godley et al. affirmed that quality improvement studies improving timeliness in healthcare are essential for reducing delays in care and for improving quality [ 60 ]. In 2018, Woodnutt et al. carried out a systematic literature review on the Lean sustainable method in NHS hospitals, finding that waiting times were the most common area in which Lean practices could have an effect [ 7 ]. In the management of patients undergoing hip replacement surgery, recent studies applying Lean methodology in combination with other strategies improved quality and at the same time reduced costs, resource consumption, and waiting times [ 42 , 44 ]. Moreover, interventions aimed at improving pre-fracture function and post-fracture social support could increase health perception following hip fracture [ 61 ] and there is evidence that psychological and social factors, particularly social support, influence recovery and post-fracture quality of life [ 62 ].
Therefore, Lean methodology, with the aim of identifying fundamental areas of delay and inefficiency throughout the process, has not been fully implemented to hip fracture care individually or combined with other methodologies [ 44 ], such as design thinking. This would enable the mapping of the patient’s experience (journey map) during hospital admission and subsequent discharge from the perspective of what he/she sees, hears, and feels at each phase of the process [ 63 ].
Lean methodology is used to increase value in healthcare, but it is seen that the determination of value is variable. It is not easily quantified under evaluation of healthcare-related services, maybe because much of this value is not based on clinical outcomes but on social ones, which are difficult to describe, capture, and translate into a decision-maker´s language, usually financial [ 38 ]. There is no standardized way to capture the social value inherent in healthcare programs, but we must work to obtain not only the direct and indirect costs, but also to determine the impacts they are creating.
Lean and Kaizen are focused on improving processes towards an ideal state, with the focus always on adding value to the client (patients), identifying waste (tasks that do not benefit or add value), reducing costs, and improving the work of professionals [ 7 , 48 ]. The origins of business process innovation could be traced back to the seminal works of Harrington [ 64 ] and Davenport and Short [ 65 ]. Davenport and Short defined processes as “a set of logically-related tasks performed to achieve a defined business outcome”, and they stated that a company should redesign such processes when they prove to be inefficient or ineffective [ 65 ]. Their research proposed a methodology consisting on five steps: (i) Develop the business vision and process objectives; (ii) Identify the processes to be redesigned; (iii) Understand and measure the performance of existing processes; (iv) Identify IT levers; and (v) Design and build a process prototype and implement improvements (Davenport and Short, 1990). Harrington defined business process innovation as “a systematic methodology developed to help significant advances in the way its business processes operate”. His model is composed of five stages: (i) Organising for quality; (ii) Understand the process; (iii) Rationalise processes; (iv) Implement, measure, and monitor, and (v) Continuous Improvement [ 64 ]. The literature also presents different approaches for business process improvement (Hammer and Champy [ 66 ]; Elzinga et al., [ 67 ]; Lee and Chuah [ 68 ]; Gardner [ 69 ]; Alange and Steiber [ 70 ]; Page [ 71 ]; and [ 72 ], among others).
The next section describes the methodology of this research paper, including a justification for the selected business improvement process framework.
3. Methodology
The objective of this research is to develop and apply a process of innovation methodology based on Lean principles in the healthcare industry, in particular in hip fracture processes. In order to pursue the objective, a research design based on a case study and action research (AR) was developed.
A qualitative case study methodology is appropriate when there is an interest in knowing the “how” and “why” of a phenomenon and it is focused in contemporary events [ 73 ]. Theory built from cases is likely “to have important strengths like novelty, testability, and empirical validity, which arise from the intimate linkage with empirical evidence” [ 74 ], and it is also likely to be interesting, accurate and testable, as they use a wide range of data sources such as interviews, documentation, quantitative data, and direct observations [ 75 ].
Greenwood and Levin defined AR as “the research in which the validity and value of the research results are tested through collaborative insider-professional researcher knowledge generation and application processes in projects of social change that aim to increase fairness, wellness, and self-determination”. AR allows collaboration between professional researchers and community and organizational stakeholders in “defining the objectives, constructing the research questions, learning research skills, pooling knowledge and efforts, conducting the research, interpreting the results, and applying what is learned to produce positive social change” [ 76 ]. An AR methodology aims at simultaneously generating an action and building knowledge related to this action; thus, the results are both the action or intervention and the research itself [ 77 , 78 ]. Empirical AR is carried out, as the researchers document a current phenomenon, follow the process and share the results. It is also a participatory research, as the researchers maintain active and close contact with agents within the organization, as both are part of the research team [ 77 ]. AR is research in action, participative, concurrent with action and consisting of a sequence of events with a focus on problem solving [ 78 ].
Alfaro and Avella in 2013 proposed to conduct a preliminary stage in AR which consists of the identification of the problem or opportunity that the research team pretends to study; this should be done as a teamwork activity among researchers and practitioners [ 77 ]. Once the study topic has been identified, the six main steps in AR are data gathering, data feedback, data analysis, action planning, implementation, and evaluation [ 78 ].
A private general medical surgical hospital has been chosen as a case study. It is located in a +120,000 habitants city in the North of Spain, in a sparsely populated region. This study focuses on optimization and improvement in the design of hip fracture surgery processes in the above-mentioned hospital. The justification for the case study lies in the fact that the hospital is located in a region with a clear aging population and consequently there is a high prevalence of hip fracture cases. The hospital decided to start offering the service “hip fracture surgery” in 2019; thus, operating rooms were assigned, and professionals were hired for this purpose. Before 2019, this service was only provided in particular and punctual cases; since 2019 the demand forecast is 150 surgeries per year.
The case study hospital has a long trajectory of working according to high quality standards (as it is certified ISO 9001 and EFQM 500+). Moreover, it shows a strong commitment towards continuous improvement, as the new service “hip fracture surgery” implies high values of LOS of patients, as well as high resource consumption. This justifies the interest, both for the hospital and for the Public Health system, in studying, analysing, and proposing improvements in the process with the aim of improving the quality of the services provided, the efficiency of the operations, and the experience of the patients and their quality of life once they have left the hospital facilities.
In this research, AR is ensured by the collaboration of researchers (expert in Lean, process innovation, and healthcare) with hospital management and professionals (doctors, nurses, technicians), who jointly defined the research objectives, conducted the research, analysed and discussed the results, and planned for action implementation and the next steps.
The research team decided to use the framework based on process innovation by Suárez-Barraza et al. (2019) [ 72 ]. The main justification for this is that the selected model is based on Kaizen and Lean management systems [ 8 , 9 ] with a gradual and continuous improvement focus. On the other hand, other models are closer to engineering and are more appropriate for manufacturing operations, and are more oriented to breakthrough or radical innovation. Lean management systems originated in Toyota’s automotive factories, and they are used today in countless companies and organizations, both in manufacturing and services, having begun to be used in the healthcare sector in recent years [ 16 , 19 , 20 ]. Lean management systems seek to analyse production processes with the aim of identifying the activities that add value to the customer, and then minimizing or eliminating all the activities that do not add any value, called waste ( muda , in Japanese).
The process innovation framework consists of the following stages [ 72 ], as shown in Figure 1 : (1) process selection and understanding the process, (2) mapping the process, (3) process measurement, (4) process analysis, (5) process redesign [ 72 ].

Process innovation framework.
Data analysis and collection
We selected the 2019 and 2020 years for observation because we wanted to know the details of the complete process related to hip fracture. Data and statistics were collected during 2019 and 2020. The field work and analytical phase occurred from November 2019 to March 2020. We combined the statistical analysis of the hip fracture patient’s dataset attended over 2019 and 2020 with process innovation and Lean healthcare analysis, including user experience ones. In this case, the study combined administrative data, experts’ point of view, and an observational process review.
4. Case Study: Hip Fracture Surgery Description
In this section we present a general description of the hospital case study, as well as a summary of descriptive statistics about the hip fracture surgery process in 2019 and 2020.
The special features that make the case study relevant are related to the aging of the population, the depopulation of this region, social isolation, and the lack of rural doctors and health care centers. The importance of the management of patient´s admission after hip fracture and discharge is undeniable. The case study hospital counts with over 300 beds, and provides medical services in close to 40 disciplines, which include traumatology, geriatrics, and cardiology, among others.
The hospital, immersed in a process of continuous quality improvement, analyzed the 2019 data and consequently took some actions oriented to improve them. Actions consisted of standardizing the medical-surgical process, consolidating an orthogeriatrics team, and carrying out an exhaustive follow-up. According to the data described below, a high impact was achieved, resulting in a reduction in average stays and mortality. The research described in this paper comes as the next step in this process of continuous improvement at the case study hospital, and consists of the analysis with Lean methodology with the aim of detecting potential points of improvement, within the real possibilities of the process at hand.
Hip fracture surgery at the hospital provides a service to 150 hip interventions annually as mentioned above in the case study justification in the Methodology section ( Section 3 ).
A descriptive statistical analysis has been carried out to describe the population:
Total patient population . We reviewed 148 clinical record histories in 2019, from 39 men and 109 women. In 2020, we reviewed 106 clinical records, from 26 men and 80 women.
Age . Related to age, in 2019, the average age was 86.5 years, the minimum being 68.5 years and the maximum being 99.9 years. In 2020, the average was 85.5 years, the minimum being 66 years and the maximum being 101 years. By gender, in 2019 women/men average ages were 87/85 years, and in 2020 women/men average ages were 87/81 years.
In-hospital mortality . In 2019, in-hospital mortality was about 6.77% of admissions or 8.78% of patients (13 patients). Discharge due to death occurs at different times, on average two weeks after admission, although half of the deaths occur before 9 days. Moreover, 30 days after discharge, the mortality rate is 1.35% (2 patients). In 2020, in-hospital mortality was reduced to 3.7%.
Total hospitalization time. Total hospitalization time refers to the total process cycle time, from patient arrival to the hospital to the moment when the patient is discharged and leaves the hospital. In 2019, half of patients (median value for cycle times) were discharged within 11.9 days, the average being 15.9 days; 25% of patients were discharged at 16 days or more. In 2020, the LOS median value was 9 days, the average being 9.41 days (40.97% less than 2019 data).
Presurgical time . The average presurgical time (from patient admission to surgery) was approximately 4 days in 2019, half of patients underwent surgery in 3.16 days or less. During 2020, presurgical time was 3.15 days.
Post-surgical average stay. The average length of stay after surgery in 2019 was 10.12 days. A length of stay after surgery of more than 20 days could be considered exceptional. On the other hand, during 2020, the average post-surgical time was reduced to 5.25 days, a reduction of approximately 50%.
A summary of the descriptive statistics is shown in Table 1 below:
Summary of descriptive statistical analysis.
5. Applying Lean in Process Innovation in Hip Fracture: Results
5.1. process selection and understanding the process.
The quality management system at the case study hospital has been built based on the analysis and understanding of the different needs and expectations of all the involved stakeholders (patients, society, suppliers, collaborators, finance clients) with the aim of providing them with the highest level of satisfaction. The system classifies internal processes in strategic processes, care processes, and support processes. Appendix A Figure A1 presents a detailed map of all of them.
Strategic processes refer to external relations of the hospital, to the management and planning, and to the continuous improvement.
Care processes refer to health attention, psychological attention, and social attention. Health attention consists of all the processes oriented to provide a health service to the patients, involving health operational steps (such as emergency, admissions, external medical consultations, hospitalization, surgery, rehabilitation), but also to diagnosis support (laboratory, image, other tests), clinical support (pharmacy, sterilization, blood reserves, nutrition, and dietetics) and care support (patient care, social work, volunteering, spiritual and religious care, bioethics, and patient safety). Psychological attention consists of all the processes oriented to provide a psychological rehabilitation service. Social attention consists of all the processes oriented to provide a service to homeless patients.
Support processes refer to information technologies, procurement and logistics, human resources, administration, and other processes.
5.2. Mapping the Process
The research team conducting this project is formed by the paper authors, two of them being experts in healthcare processes (in particular, in hip fracture) and two of them being experts in Lean management and innovation process methodologies. Collaboration with hospital management and hospital professionals (technicians, nurses, doctors) has been necessary in this research; in particular, the collaboration of a traumatologist doctor who is in charge of hip fracture surgery. Mapping the process refers to the documentation of the present situation and to the identification of flow.
Documenting the present situation must be done as it is in reality and not under ideal conditions. This has been conducted in two steps: first, the experts in hip fracture wrote the flow or sequence of activities from the first to the last step, i.e., from the first moment a patient enters the hospital until the moment the same patient leaves the facilities of the mentioned hospital. Second, a mixed team (expert in hip fracture and expert in Lean implementation) visited the hospital and followed the process from the first to the last activity, taking notes and pictures, asking questions to the different participants in the process activities, and walking the distances all along the path.
The results of these two steps are the design of a block diagram (which provides a general description of the sequence of the process) and, based on it, the detailed process mapping using flow diagrams. Figure 2 shows a block diagram, which is the first step in the process analysis. The flow diagram of the hip fracture process uses symbols according to the American National Standard Institute (ANSI). Figure 3 presents an excerpt of a flow diagram of the process. This first excerpt contains only 7 activities of a total of 236. The complete flow diagram can be found in Appendix B Figure A2 . The flow diagram was built on 23 pages that can be seen in Appendix B , showing that the hip care process map is a complex process in its current situation.

Block diagram.

Flow diagram (partial) showing the existing process.
5.3. Process Measurements
Measuring the existing process implies identifying different indicators related to the process with the aim of quantifying them. Process redesign will propose some initiatives oriented to improve the values of the proposed metrics. The indicators that we consider are:
The total number of activities resulted in 236.
The number of participants is 18 (*).
They are grouped in different areas (see detail in Table 2 ).
Detail of areas and participants in hip fracture surgery processes.
Note (*): It is important to acknowledge that the traumatologist doctor also acts as the surgeon.
- (iii) Process cycle times. This refers to the total process time, from patient arrival at the hospital to the moment that the patient is discharged and leaves the hospital (also known as total hospitalization times or LOS). Total process cycle times in 2020 are reported above in the case study description, the average being 9.41 days (40.97% less than 2019 data), the median being 9 days, the standard deviation being 4.17, the minimum being 0 days, and the maximum value being 32 days.
5.4. Process Analysis
The process analysis is carried out in two steps:
Analysis of hip fracture process activities.
- Defects: errors or defects when performing a task, producing a service or making a product.
- Overprocessing: repeating tasks or activities during the process.
- Overproduction: producing more than necessary.
- Movement: unnecessary or inadequate movement of personnel to execute a task (related to ergonomics or efficiency of movements).
- Transportation: carrying out or moving materials or patients from one location to a different location where a new task will be performed. This also refers to the transportation of employees.
- Inventory: excess of materials or goods which are cumulated in case they are needed.
- Delay: additional waiting time when the process stops more than usual.
- Unused Talent: underused qualified workers (it could also be—but not in this case—a bad attitude from employees affecting the process results).
Our analysis shows that 60 opportunities for potential muda have been identified in 54 activities (i.e., 6 activities present 2 types of muda ). Table 4 shows a summary of the different types of Muda . Appendix C Table A1 provides the details of all of them.
Summary of the different types of Muda: ( a ) Data, ( b ) Pareto chart.
5.5. Process Redesign
AR is involved in the teamwork activities carried out between researchers and practitioners. Process measurements and analysis have been conducted by the research team (based on its experience in Lean, process innovation, and healthcare) with the collaboration of the hospital director, hospital employees (nurses, technicians), and mainly by the active support and involvement of a traumatologist doctor who is also in charge of hip fracture surgery at the hospital.
After process analysis has been conducted by the research team in collaboration with hospital professionals (management, doctors, nurses), process redesign will consist of the proposal and implementation of some initiatives oriented to enhance value creation from the patient point of view, i.e., reducing waste, increasing efficiency, improving patient experience, and improving the values of the process metrics. Table 5 below summarizes a list of actions that have been proposed for further implementation, identifying the type of muda that could be impacted by them:
List of proposals.
As a next step, beyond the scope of this research paper, the authors suggest that an implementation plan could be designed, scheduled, executed, and evaluated. A new multidisciplinary team (involving researchers and hospital professionals) could be formed with the aim of guaranteeing that expected results are confirmed.
6. Discussion
The results of the care activity of the case study hospital are similar in average age to those found in the national hip fracture registry in Spain, with an average age of 87 years [ 35 ]. The average LOS of this registry is 10 days, slightly higher than the LOS of the analysed hospital.
The research questions that govern this study are (i) to try to identify the types of waste or muda , and (ii) to evaluate the application of a process innovation approach in healthcare, in particular in the hip fracture surgery process.
This research allowed us to identify 60 muda opportunities along the hip fracture surgery process, which is composed of 236 activities and where 18 participants interact. It is relevant to point out that 18 participants does not refer to 18 people, but to 18 job positions, each of them being performed by 1 or more people. For instance, one position is a nurse; if the patient stays at the hospital for 2 weeks, there will be different people working as nurses to take care of him (the nursing team is composed of more than 10 employees per shift, morning, evening, and night, 24 h a day).
The following different types of muda have been identified along the process: defects, overprocessing, overproduction, movement, transportation, inventory, delay, and unused talent. Some of them occur punctually, but others (we consider them as critical muda ) are more repetitive all along the process; these are the ones that we are going to discuss. Although three types of muda represent 72% of the total (enough for critical muda discussion), we also decided to consider the fourth type (which only represents 10% of the total).
Delay is the most frequent waste in the hip fracture surgery process. Delay represents 33% of all cases, the most common being as follows: (i) the patient needs to wait because the clinical process requires it (for instance, the patient needs to be stabilized—pulse, temperature, blood pressure, etc.—before being transferred to the next stage); (ii) the patient needs to wait because of a lack of available resources (no available hospital porter for transfer) or because all resources are busy (for example, X-Ray is being provided to a different patient; (iii) delays produced because an employee has forgotten or neglected a task, or presents a bad attitude. Type (i) is normal; type (ii) needs to be minimized (better resource planning); type (iii) needs to be eradicated. Communication between employees patients is crucial in each case because, even if the delay cannot be avoided, the patient experience could be positive if there is a clear explanation and justification for it.
Transportation is the second type of waste. In general, transportation refers to transferring the patient from one location to a different location, and, although frequent, it is not very relevant, as distances within the hospital are not big. When referring to transportation of employees (doctors, nurses, porters, etc.) there is evidence of inefficiency (repeated distances are walked to supervise, take care, provide service etc., to patients). Spaghetti charts and cause-and-effect analyses could be used to study this type of muda in detail.
Overprocessing waste could happen when (i) some tasks need to be repeated; (ii) the process is not well- or properly defined; or (iii) lack of resources or when employees perform tasks that are not supposed to be carried out by them. Waste reduction could be achieved by different means such as automation (e.g., when initiating the hip fracture process the system automatically requests a bed, avoiding the need to phone or call a floor supervisor), process standardization with poka-yokes or checklists (e.g., to avoid repeating blood tests or X-Rays), better planning (e.g., to avoid repeating the pre-surgery preparation); or better maintenance planning (e.g., reliable maintenance plans avoid equipment and machinery failures).
Defect refers to waste when the results of an activity are not right, i.e., when an error is produced. Errors could be clinical, or cause by service, attention, etc. Causes of errors could be diverse, but if clinical errors are excluded, many are related to miscommunication (too many participants in the process), a lack of a standardized processes (every employee adopts his/her own criteria to execute an activity or to take a decision), or to an excessive workload (attention and concentration decrease). A leaner process with less participants, standardized processes (process defines, trained employees, checklists, and poka-yokes) and a planned workload will reduce waste opportunities.
An inventory of materials is necessary at many stages in the process: labels, paper and bracelets in admissions; and X-Ray plates, medicines, and medical goods in emergency areas, rooms, UCEs, and operating rooms. Every supervisor is responsible for inventory management (inventory levels, keeping control, placing the orders). No specific method (economic order quantity, fixed period ordering, first in first out, etc.), nor software is used, but a manual control is carried out according to his/her own criteria. Lack or excess of an inventory has been reported, an excess of it being more frequent due to the fact that healthcare deals with patient lives and risks should be minimized. There is a pharmacy inside the hospital, in case of any material need.
Movement waste in this process deals mainly with patient manipulation to be transferred from a stretcher to accommodate a mattress, the handling of X-Rays, electrode tests, blood test sampling, or movement inside the operating room. Process standardization according to different patient types (weight, volume, health condition) would help to minimize this muda .
Different types of muda according to the literature [ 8 , 9 , 11 , 12 ] have been identified in the process, being delay the most frequent. This agrees with Godley et al. [ 60 ] and Woodnutt [ 7 ], who identified delay and waiting times as the relevant types of waste that should be addressed with the aim of optimizing processes. The literature shows different examples of authors who have studied the different types of muda in the same way. In the educational sector, Doman indicates that with process innovation efforts, the graduate and graduate management processes can be improved [ 79 ]. Walters et al. identified specific areas of internal production waste including defects and waiting, and in the process of our investigation, identified a significant shift in process efficiency due to resource allocation [ 80 ] focusing on 1040 financial norms. In fact, Ann Douglas et al. similarly identified the 8 types of muda in Higher Education [ 81 ] and Suárez-Barraza et al. also identified three new types of muda in the 21st century such as unnecessary emails, excess work meetings, and technological distractors [ 82 ]; processes in hospitals cannot be free of these three new types of muda either.
Finally, Coelho et al. present evidence of process innovation in health processes, for example, they reduced the cancer outpatient chemotherapy process cycle time from 2 h to 30 min [ 57 ].
Close collaboration between clinical staff, hospital management, and researchers allowed the collection of precise data, as well as information sharing, which is very valuable for the process analysis and redesign. A new process design presents the following advantages, which are aligned with the literature [ 31 , 42 , 44 , 60 ]:
For patients, a reduction of LOS, potential errors, and, as a consequence, an improvement in patient satisfaction and experience. Quality improvement impacts directly on the quality of life of the patient, including both psychological and social aspects related to the social isolation in which the patient returns after discharge.
For hospital management, an increase in efficiency and better planning, thus a cost reduction, a capacity increase, and, as a consequence, a potential increase of activity.
For hospital employees, waste reduction (times, overprocessing, potential errors, etc.) and standardized processes will reduce the workload, stress and fatigue, increasing their satisfaction, thus, their motivation and commitment.
The above-mentioned findings justify the selection of this process innovation framework, as it has a clear focus on waste identification and Lean operations redesign [ 72 ]. The identification of changes in the analyzed process with the proposed methodology involves a second phase of analysis and reflection with the orthogeriatric team to go in depth into the findings, and to identify those that can really undergo an improvement process.
7. Conclusions
The research examines the identification of waste or muda in a hip fracture surgery process in healthcare. Eight types of muda have been identified, the most frequent being delay, transportation, overprocessing, and defects, and actions based on them for improvement have been proposed.
The application of a process innovation approach has also been examined in this research, the result being that, although innovative, this approach is appropriate for the healthcare sector, as it is appropriate in any other service industry. Applying the process innovation methodology represents an effort of the Kaizen philosophy in critical processes in the health sector. In fact, it allows crystallizing redesigns and changes to eliminate muda from the activities of health processes. In our case study, all the proposals will lower the muda percentage by at least 30% for all hip process activities in the current situation.
This research is innovative on the implementation of the technical approach, and its contributions on the implementation side can be summarized by a set of proposals that have been done including: process standardization, reduction of the number of participants in the process, techniques to improve communication, automation initiatives, training, implementation of inventory management techniques, the implementation of some tools (such as 5 s, checklists, or poka-yokes), including new performance indicators, as well as patient satisfaction measurement systems, among others.
This research is also innovative on the action-research process itself, as it brings the following contributions: (1) although not common, we succeeded in obtaining a formal collaboration among clinical personnel (doctors, nurses, etc.), service managers, and researchers to carry out a joint research project; (2) a research team (expert in Lean and process innovation, as well as in healthcare) entering the hospital and visiting the whole detailed process overcoming potential problems or communication barriers; (3) the advantages of documenting and recording observations and results (the power of direct observation in the gemba , the Japanese word for “place”); (4) fruitful discussions among specialists, experts, managers, and researchers towards sharing knowledge and ideas aiming at process improvement; (5) the adaptation of a process innovation approach within the healthcare sector, which is different from other service industries due to different needs, priorities, and vocabulary, as well as differences between private or public hospitals.
When the average stay data is adjusted to normal [ 35 ], it can be complex to introduce improvements that contribute to the sustainability of the service and increase the impact on the patient. Therefore, an exhaustive analysis of each one of the mudas found before their implantation is necessary.
This research also offers some practical implications for healthcare managers:
- (i) the identification of all different types of muda all along the hip fracture surgery process provides hospital managers with an opportunity for continuous improvement, by trying to eliminate or minimize them;
- (ii) some initiatives have been proposed to redesign the process, which allows the management to take action towards gaining efficiency and service quality, which in turn impacts on operating costs and patient satisfaction;
- (iii) the observation and the analysis have been carried out by researchers, but a basic training and a checklist (an audit tool) would help employees to carry out this assessment any time they need in the future.
Finally, some limitations of the research are: (i) the data cannot be generalized due to its qualitative nature; (ii) the findings refer to the specific context of hip fracture surgery in a case study in Spain; (iii) process redesign initiatives have been proposed for implementation, but have not been evaluated yet. Future studies could be carried out with the objective of evaluating the effectiveness of the implemented actions and their outcome, as well as by using data analysis techniques to better understand the variability of data dispersion. Other future areas for research could be initiated using several years of data history in the case study, and by using a larger sample of hospitals, as well as other geographical areas.
Acknowledgments
Hospital management and personnel that kindly participated and collaborated with the research team.
Main Process s at case study hospital.

Source: Hospital Quality Management System.

Hip Fracture Process Flowcharts.
Analysis of different types of muda .
Author Contributions
All authors made a proportional contribution. Conceptualization, M.F.M.-C., E.G.G.; methodology, M.F.M.-C., M.F.S.-B.; validation, P.C.-V., M.F.S.-B.; formal analysis, M.F.M.-C., M.F.S.-B.; investigation, M.F.M.-C., P.C.-V., A.S.D., E.G.G.; resources, A.S.D.; data curation, M.F.M.-C., P.C.-V., A.S.D., E.G.G.; writing—original draft preparation, M.F.M.-C., P.C.-V., M.F.S.-B., E.G.G.; writing—review and editing, M.F.M.-C., P.C.-V., E.G.G.; visualization, M.F.M.-C., P.C.-V., E.G.G.; supervision, M.F.M.-C., E.G.G.; project administration, E.G.G. All authors have read and agreed to the published version of the manuscript.
This research received no external funding.
Conflicts of Interest
The authors declare no conflict of interest.
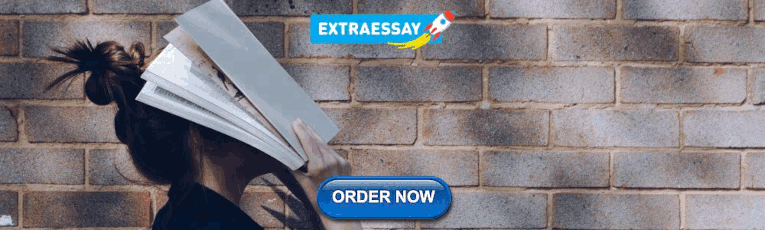
IMAGES
VIDEO
COMMENTS
Explore our sortable list of 55 process improvement case studies with a detailed guide about types of process improvement solutions & typical project results ... For example, in a process mining case study, a manufacturer leveraged IBM Process Mining to analyze the procure-to-pay processes. It is claimed that the manufacturer detected and ...
Overview of 55 Process Improvement Case Studies. Here is a high-level snapshot of the case studies we'll explore: Now let's look at some specific examples… Manufacturing - Improving Production Processes. Manufacturers can leverage solutions like Lean Six Sigma to optimize production and supply chain processes.
Now let's examine 55 real-world examples of process improvement across industries: Key Insights from the Case Studies. Analyzing these case studies reveals valuable patterns: Manufacturing, financial services, and technology lead process improvement adoption, but benefits realized across sectors.
This case study is one of three highlighting successes identified as part of the Operational Excellence in Government Project . The purpose of the case studies is to elevate and document the successes, and in doing so to provide a greater amount of detail than is typically available about such efforts . The case studies explain the
CASE STUDY. This case study evaluates the process and methodologies used in certifying the win/loss review process as a Six Sigma Black Belt project at Microsoft Corporation. It shares the insights gained from a process improvement perspective but does not cover broader benefits and results, such as improvements in win rates or revenue performance.
Lean Management Examples from a Variety of Businesses. The following case studies of lean management principles in action show you how a variety of real businesses solved real business problems under diverse conditions. ... management re-organized the transformation around problem solving and process improvement to create a culture that engaged ...
Six Sigma Case Study is a data-driven methodology widely used in organisations to improve process efficiency and quality. It helps reduce process defects and variations, enhancing customer satisfaction and increasing profitability. It provides a real-world example of how its methodology was applied to identify and solve a problem, showcasing ...
Features: Makes process documentation a breeze, each process can be turned into trackable checklists, powerful tracking features. Price: $99/month for up to 20 members plus $5/month for every additional user. Free version: 14 days. Process improvement can only be done after process mapping.
PDSA: PDSA is a structured cycle for improvement. The steps are: Plan: Define the problem and identify possible solutions. Do: Experiment by implementing one solution. Study: Analyze the results of the experiment. Act: If the experiment was successful, add it to the standard operation. If not, begin again.
PM Solutions led a targeted mentoring program for the client's project leads to provide one-on-one advice and coaching on how to apply consistent project management practices within the confines of their actual projects. Value Delivered: Improved on-time project delivery to 80% resulting in one program booking $100,000 of business in the first ...
7 types of process improvement methodologies. There are seven different business process improvement methodologies your team can use to help reduce inefficiencies. In most cases, the methodology you choose depends on why you want to improve your processes and what you're looking to improve. 1. Six Sigma methodology.
Five Case Studies of Transformation Excellence. November 03, 2014 By Lars Fæste , Jim Hemerling , Perry Keenan, and Martin Reeves. In a business environment characterized by greater volatility and more frequent disruptions, companies face a clear imperative: they must transform or fall behind. Yet most transformation efforts are highly complex ...
Small daily efforts can reduce waste and raise the quality of output. Use the following tips, examples, and improvement plan templates to implement changes in your organization. Experts share case studies and advice to help you get started. In this article, you'll find principles of continuous improvement, examples, case studies, and plan ...
Process Improvement Plan Case Study. Following the steps we outlined earlier, let's explore a hypothetical process improvement plan for a doctor's office that constantly gets complaints from patients about how many forms they have to fill out. Process Improvement Plan: Reducing Patient Form Burden in a Doctor's Office. Identify the Goals:
Search more than 1,000 examples of case studies sharing quality solutions to real-world problems. Find more case studies Featured Case Studies Classic Case Studies ... Imagine if every organization could have the luxury of a 3,000 square-foot room with tools purely dedicated for process improvement, innovation, and brainstorming. ...
Jonathan Kraft, Manager of Open Standards Benchmarking at APQC, explains the five use cases for the Process Classification Framework (PCF)®, the world's most widely-used process framework, including process discovery and standardization, process improvement, technology implementation, benchmarking, and content management. Watch the video.
This article presents a proposed methodological approach aimed at realising a commitment to broad participation, collaboration and consensus-building in process improvement in healthcare. Our case study shows that it is possible to deploy the approach successfully to specify process improvements in an area of pressing need during the COVID-19 ...
Case Study: Business Process Improvement. This Case Study illustrates how Gagnon Associates used its Business Process Improvement capability to optimize a client's new-product development process: The Company. A formerly high-flying, enviably profitable surgical products division of a major health care company.
The purpose of this paper is to present a framework and case examples of a Research Process Improvement Program implemented at Tufts CTSI. To promote research process improvement, we developed online training seminars, workshops, and in‐person consultation models to describe core process improvement principles and methods, demonstrate the use ...
3. Methodology. The objective of this research is to develop and apply a process of innovation methodology based on Lean principles in the healthcare industry, in particular in hip fracture processes. In order to pursue the objective, a research design based on a case study and action research (AR) was developed.
Abstract and Figures. This thesis is a case study for a Roofing company based in Phoenix Arizona. The topic of the thesis is Business Process Improvement and overviews the popular methods such as ...
The case study also demonstrated that even smaller business units and its processes affected the overall value chain in a major way and the importance to analyse the process interdependencies between organisational units. KEY WORDS: Lean Construction, Organisational Process Improvement, Process
Case Studies of Quality Improvement Initiatives. Over a five-year period the CAHPS RAND Team prepared a series of case studies of quality improvement initiatives undertaken by health plans and health care organizations. The studies provide practical examples of efforts to improve performance on various aspects of patients' experience of health ...