- Agriculture Farming
- Livestock Farming
Project Reports
- Hydroponics
- Best Fertilizers
- Vertical Farming
- Sheep Farming
- Goat Farming
- Poultry Farming
- Fish Farming
- Pig Farming
- Dairy Farming
- Rabbit Farming
- Success Stories of Farmers
- Boost Fruit Yield
- District Wise Crop Production
- Schemes & Subsidies
- Agriculture Colleges
- Farm Insurance
- Disease Control And Management
Agriculture
Aquaculture
Horticulture
Agri Business
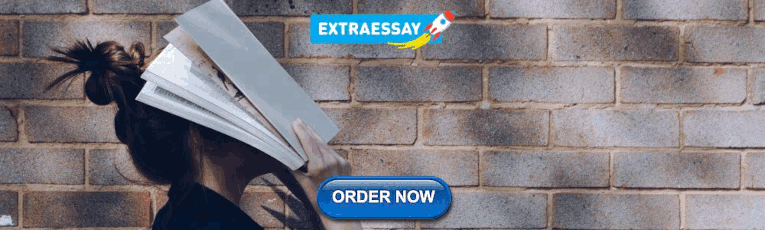
Dairy Processing Plant Project Report, Setup Cost, Profit
Table of contents, dairy processing plant project – milk procurement:, dairy processing plant project – milk processing:, dairy processing plant project – manufacturing of dairy products:, dairy processing plant project – dairy plant design and planning:, dairy processing plant project – dairy processing plant layout:, dairy processing plant project – bank loans and subsidies:, dairy processing plant project – bank security:, dairy processing plant project – cost and profits in dairy processing plant / economics of dairy processing plant, dairy processing plant project report – marketing of milk and dairy products, read: dairy farming faq., read: small scale dairy farming., introduction to dairy processing plant project:.
The following information is about Dairy Processing Plant Project Set up Cost and Profit .
Dairy processing around the world is growing rapidly to meet milk and dairy products for an ever-growing population. Dairy processing is an industry that involves harvesting or processing milk from milk-producing animals for human consumption. The structure of the dairy processing industry varies from country to country. Milk is sold directly to the public in developing countries, while in developing and major milk producing countries, most of the milk is sold on a wholesale basis. Milk is an easily digestible and highly nutritive human food that is consumed on a daily basis either directly or in any other dairy product forms. Dairy products contain different kinds of vitamins, proteins, minerals, fat, and sugar contents in liberal quantity. India stands third after America and Russia in the world milk production. Being one of the top milk producers, the distributions of milk across the population spread out in the nation are inadequate as there are limited milk Processing Plants. The distribution and supplying of processed milk are inadequate to reach children, expectant and nursing mothers across the nation. This can only be achieved by stepping up milk production and setting up dairy Processing Plants. To market milk and various dairy products; a scientific planning and layout must be set up for milk collection and processing at dairy Processing Plants. The general tendencies in the marketing of dairy products such as yogurt, soft cheeses, and creams that have short lifespan are located in urban regions and dairy products such as butter, cheese, and milk powders that have a longer shelf life are located in rural regions.
15% of total milk production across the nation is distributed under cooperatives and private dairy Processing Plants. These statistics exhibit a wide scope for young entrepreneurs to invest in the processing of milk and manufacture of dairy products for both domestic and export. Milk drawn from the cattle remains almost sterile with the milk temperature of about 37° C equal to the body temperature of the milch animal. The fresh milk will have a shelf life of about 2 to 3 hours and starts to sour. Milk is a perishable commodity gets easily contaminated from air, utensils, and other reasons; the milk should be sent to the dairy Processing Plant or milk collection centers at the earliest.
In almost all countries, most of the milk is produced in rural regions which are transported to the milk processing plant. In India, milk is collected both in the morning and evening and has to be transported twice in a day. Procurement of milk is carried out in various ways depending on the location and availability of collection centers or dairy Processing Plants. Milk is collected at the dairy Processing Plant by the following methods:
- Individuals: Those that are located near to the milk collection centers; the milk is brought by individual producers directly. The individuals carry the milk on their own transport and vessels to the Dairy plant.
- Contractor: Some contractors collect milk from individual milk producers. The contractor supplies milk to the dairy plant. In this process, the contractor has to collect and transport the milk, thereby the contractor buys milk at a cheaper rate from the individual milk produced and keeps his share of profit.
- Cooperative Organizations: To avoid the middlemen and contractors; some individual milk producers formed as a cooperative organization. Milk is collected at the cooperative organization brought by individual milk producers, the cooperative societies or organization is responsible to supply milk to the dairy plant. This method is beneficial to individual producers as they don’t need to share profits with contractors or middlemen.
- Milk Collection cum Chilling Centers: This method is currently more prevalent in Indian dairy operations in organized sections. The milk that arrives at the collection centers brought by individuals from the nearby rural regions is weighed and tested for fat content. The milk is stored in 40l cans and sent to the milk chilling center or dairy Processing Plant.
Milk is a nutritious food having a short shelf-life as it is a highly perishable commodity and an excellent medium for bacterial pathogens and micro-organisms growth. The shelf-life of milk can be extended for several days or weeks through milk processing that helps in reducing the number of pathogenic microorganisms. Following are the milk processing steps:
- Skimming: The raw milk during pasteurization undergoes milk skimming through common centrifugal separator application; the milk is passed through a clarifier or a separator which spins the milk through a series of conically shaped disks. The purpose of this process is to separate the debris, skim milk, and cream. Clarifier removes debris and any sediment present in the raw milk. The separator separates the heavier milk fat from the lighter milk at a temperature between 45° to 55° C to produce cream and skim milk.
- Fortifying: The skimmed milk may be added with Vitamins A and D at this stage. A peristaltic pump helps in dispensing the required amount of vitamin concentrate into the milk.
- Pasteurizing: This is an important process stage in milk processing. Heating every particle of the milk for a specified time duration at a specific temperature is termed as pasteurization. Usually it can be carried in two ways; first, the temperature can be 72°C for 15 to 17 sec time period or 63°C for 30 minutes. Pasteurization process helps in destroying bacteria and other microorganisms that may affect the milk shelf-life and also may affect consumer’s health.
- Homogenizing: In this process, the size of the remaining milk fat particles is reduced evenly. Homogenizing helps to prevent the milk fat from separating and floating to the surface. After going through pasteurization, the hot milk is pressurized to 2,500 to 3,000 psi by a multiple-cylinder piston pump and then compelled to pass through tiny sections in an adjustable valve. When the fat particles break down evenly into the proper size, to avoid harming its taste, the milk is quickly cooled to 4°C.
- Packaging: The final stage in the dairy Processing Plant is packing. The milk is packed in 500ml and 1000ml sealed packets. The packets are stamped with the date of packing. The milk packets are placed in transport containers and refrigerated. Transporting of milk packets to various retail outlets and distribution centers is carried out in refrigerated vehicles and are kept in refrigerated display cases.

Butter Production: Raw milk after undergoing the process of filtration/clarification, skimming, and pasteurization are now ready to start the butter production process. Milk that is homogenized is not good for butter production, avoid the homogenization process. After skimming, the heavier milk fat that is separated is from raw milk is heat treated and cooled. This helps good whipping and churning. At the time of churning, culture inoculation can be processed for the ripening of the milk. This helps increase the content of diacetyl, which is the compound responsible for the flavor of butter. Butter made without culture is called sweet cream butter, butter that is flavor enhanced using culture is termed cultured butter or lactic. Both sweet cream and cultured butter have less storage life. To add flavor and storage life, salt is added at the recommended dosage. Butter which is ready can be stored in bulk quantities to be repacked into regular market quantity or according to market demand.
Cheese Production: Milk is heated while being stirred in the large cheese tank until it reaches the desired temperature. Add lactic acid bacteria along with rennet an enzyme to the milk. Stop stirring at this point, allowing the milk to settle down in a large vat. 30 to 45 minutes of resting leads to curdle of milk. The jellylike curdled milk is stirred in breaking it into smaller pieces. This allows separation of curd and water content. The smaller the pieces the harder the cheese will be. The curd is stirred while being heated up to 57° C. The cheese is collected in cheesecloth and pressed hard to remove whey or water content. The soft cheese collected is put into a saline bath for 30 minutes to 2 days depending on the cheese size. This processes any leftover moisture content and allows absorption of salt to make the cheese stable. The last process is ripening and fermentation, this makes the cheese dough formation of holes and the aroma.
Milk Powder Production: Milk that is not pasteurized is used for making milk powder. It can be of skim milk powder, fat filled milk powder or whole milk powder. Depending on the characteristics desired for the final powder product and the stability of the protein content in the milk, the milk is preheated in tubular heat chambers at a preheating or desired temperature. The heated milk, then passes through the evaporation chamber that increases the concentration of milk solids up to 50 percent. The concentrated milk is then fed into the drying chamber, spraying the concentrated milk over the hot air stream will allow the remaining water content to evaporate instantly, leaving tiny particles of powdered milk solids to fall at the bottom of the chamber. The milk powder is collected and packed at desirable quantity for market distribution.
Dairy Plant design and planning, young entrepreneurs should focus on this important section when starting their dairy Processing Plant project. As this include, the estimation of milk capacity, process scheduling, and appropriate plant layout in order to accomplish the target of taking care of raw milk and its byproducts at low cost and its well being. In any case, the dairy business and the plant design need to have proper planning to meet certain unique requirements and should be focused on them such as:
- Milk by nature is a perishable agriculture commodity with a few hours of shelf life. Raw milk has to chill and processed at the earliest before manufacturing the dairy products. Thus, TIME is the most essential factor and aspect to be considered for dairy plant design and planning.
- Milk provides nutritious and easily digestible, thus becoming an important commodity in every household of the general public. It is consumed by children, youngsters, elderly, pregnant and lactating women making the dairy industry an important part in the society.
- The dairy processing business needs to manage raw milk fluctuations in procurement. In the Flush season that is at the time of calving and abundant green fodder availability, milk is generated to the maximum. In dry seasons such as summer and end of calving season, milk generation will be at the lowest. Fluctuation of raw milk procurement depending on the season has to be considered at the time of dairy Processing Plant design and planning.
- Dairy processing plant hygiene and staff safety measures have to be considered.
- Water used in the dairy processing industry contains COD and BOD high values, proper effluent disposal of the dairy Processing Plant is essential.
- The dairy Processing Plant has to meet the Industrial Act, Pollution Control Act, Boiler Act, Labor Act, and additionally, has to meet HACCP and FSSAI guidelines.
Dairy processing plant efficiency and production depend on the dairy processing layout. Dairy plant layout is the most important part to start a dairy processing business. Proper planning with a proper layout not only increases efficiency and production, but also the quality of the products. Negligence in terms of improper dairy processing layout would put many lives at risk. A good dairy processing layout is of great importance to the quality production process. The layout emphasizes placing machinery at sufficient distance for staff easy movement while operating, cleaning, and monitoring the dairy Processing Plant. The common sections of a dairy Processing Plant layout include:
Reception: The first stage in the dairy processing layout is collecting milk from milk tankers and trucks. The milk is offloaded at the specially designed milk offloading section. The milk is pumped into the milk silos with flow meters checking the milk quantity.
Processing Rooms: Manufacturing of milk and dairy products such as cheese, butter and others is carried out in separate rooms. Manufacturing, packaging and storage rooms are included in the dairy processing layout. Cold rooms help to store the perishable products before dispatching to the market.
Laboratory: Labs help in quality assurance with timely analysis. They are placed with easy access to raw materials and product sampling for timely analysis. Labs placement should be located near to the manager’s office for easy supervision.
Administration Office: Placing of concerned departmental office rooms at the plant entrance aids the quick administration process. It will be accessible to vendors, visitors, and staff to facilitate the plant administration activities.
Utility Room: A good layout design will provide boiler, refrigeration system, compressed air and vacuum systems, power generators, and other are housed properly with sufficient space. For safety issues, the utilities are housed in different buildings.
Waste Handling Facility: The dairy processing layout will help in the proper handling of toxic waste and other bio waste produced in the dairy processing plant. Proper handling mechanisms will help protect contamination and environmental degradation.
Entrepreneurs can approach any financing PSU or Private bank for finance. New entrepreneurs should go through guidelines to claim incentives promoted by various State Governments for the promotion of Dairy product industry. There are various incentives depending upon the location of the dairy unit. Depending on states Agro Industry Policy, newcomers can take maximum advantage of these subsidies. To avail various subsidy schemes of government, it is recommended to take a bank loan. Along these lines, the entrepreneurs who are envious of benefiting subsidy should hold fast to the methods of finance, i.e. the quantum of bank loan and marginprescribed under the subsidy plan. The government of India has implemented the National Mission on Food Processing (NMFP) to be implemented through State / UT Governments during the 12th Five Year Plan (2012-17). Food Processing Industries can avail subsidy under this scheme. To implement this scheme in different states, GOI appointed State Nodal Agencies. For more information on schemes and state nodal offices, one can go through, Ministry of Food Processing Industries website.
The Loan issuing bank will take adequate security as per RBI guidelines. Entrepreneurs should plan projects accordingly to the fixed assets as security against bank loan. Banks will look into three aspects before issuing of loans, and they are primary security, collateral security, and hypothecation.
The primary security includes the land and building that are mortgaged to financing banks. Fixed assets such as the plant, machinery equipment, and other miscellaneous fixed assets shall have to be hypothecated to the bank.
The company or entrepreneur property or assets will be mortgaged when the value of the primary security will not be enough to cover the bank loan. The value of the primary assets along with the promoter’s immovable assets will be taken as collateral security by banks for extending loans.
Financing banks will take all stocks, inventories, and debtors as security against the loan and will hypothecate these assets.
Based on the type of milk procured and products proposed; different plant and machinery are required for dairy processing. All the plant and machinery are according to BIS specifications. A dairy Processing Plant for 10,000 liters capacity and section-wise machinery required with specifications are given below:
Reception Section of Dairy Processing Plant Project Report:
1. | Can Roller Conveyor (3 mtrs) | 1 No. |
2. | Can Tip Bar | 1 No. |
3. | S.S Weigh Bowl (500 lits) Electronic | 1 No. |
4. | S.S Dump Tank (1000 lits) | 1 No. |
5. | S.S Milk Pump (1.5 HP) | 1 No. |
6. | Disc Filter | 1 No. |
7. | S.S Can Scrubber 40 ltrs | 1 No. |
8. | Can Drip Saver (6 cans) | 1 No. |
9. | Laboratory Equipment: Milkoscan, Density meter, Milkotester, Cryoscope, HPLC, Emulsion quality analyzer, glassware, etc. | 1 set |
Process Section of Dairy Processing Plant Project:
1. | S.S Milk pump (2 HP) | 1 No. |
2. | S.S Milk Chiller, Cap (3 klph) | 1 No. |
3. | S.S Balance Tank with Float (100 lts) | 1 No. |
4. | S.S Flow Control Valve | 1 No. |
5. | S.S Simplex Filter | 1 No. |
6. | S.S Remote Control | 1 No. |
7. | Milk Pasteurizer (2.5 klph) | 1 No. |
8. | S.S Holding Coil (16 secs) | 1 No. |
9. | S.S Pipeline & Valves (interconnecting) | 1 Set |
10. | Flow Diversion Valve | 1 No. |
11. | Cream Separator (500 l/hr) | 1 No. |
12. | Cream Tank (1 kl) | 1 No. |
13. | Ghee Boiler (250 ltrs) | 1 No. |
14. | Ghee Settling Tank (250 ltrs) | 1 No. |
15. | Ghee Balance Tank & Pump | 1 Set |
16. | CIP Unit | 1 Set |
Storage and Packaging of Dairy Processing Plant Project:
1. | HMST- MS Outer (5 kl – single comp) | 1 No. |
2. | HMST- MS Outer (10 kl – single comp) | 1 No. |
3. | S.S Milk Pump (1hp) | 1 No. |
4. | S.S Overhead Tank (200 ltrs) | 1 No. |
5. | Packing Machine (5000 pph) | 2 No. |
6. | SS Pipes & Valves (interconnecting) | 1 Set |
7. | Pouch Packing Machine (stabilizer) | 1 No. |
8. | Spare S.S Pump (tanker filling) | 1 No. |
9. | G.I Pipeline (Driers for air & controls) | 1 Set |
Utilities of Dairy Processing Plant Project:
1. | Hot Water Generator | 1 No. |
2. | Water Softener | 1 No. |
3. | G.I Pipeline (water pump & valves) | 1 No. |
4. | Chimney (3 mtrs) | 1 No. |
5. | Makeup Water Tank (200 ltr) | 1 No. |
Refrigeration Section of Dairy Processing Plant Project:
1. | Refrigeration (storage equipment) | 1 Set |
Electricals of Dairy Processing Plant Project:
1. | Generator (63 kva) | 1 No. |
2. | Cables & Others | 1 Set |
3. | MCCB Control Panel Board | 1 No. |
Staff for Dairy Processing Plant Project:
1. | Plant Manager | 1 No. | 35,000/- | 35,000/- |
2. | Plant Operator | 1 No. | 27,500/- | 27,500/- |
3. | Marketing | 2 No. | 15,000/- | 30,000/- |
4. | Plant Supervisor | 1 No. | 16,000/- | 16,000/- |
5. | Mechanics | 2 No. | 15,000/- | 30,000/- |
6. | Driver (Delivery) | 1 No. | 7,500/- | 7,500/- |
7. | Lab Technicians | 2 No. | 14,500/- | 29,000/- |
8. | Labor | 8 No. | 6,000/- | 48,000/- |
9. | Accounts Staff | 2 No. | 7,500/- | 15,000/- |
10. | Watchman | 2 No. | 6,000/- | 12,000/- |
Capital Cost of Dairy Processing Plant Project:
1. | Site Development | 16.25 |
2. | Civil Works | 46.50 |
3. | Plant and Machinery equipment | 150.00 |
4. | Vehicles | 6.40 |
5. | Misc. Fixed Assets | 25.00 |
1. | Procured Milk Price (Avg) | 30.00 / ltr |
2. | Sale Price(Avg) Toned Milk (3% fat) | 34.00 / ltr |
3. | Sale Price(Avg) Cream (40% fat) | 120 / kg |
4. | Ghee | 290 / kg |
5. | Comm. And Transportation Charges | 1.5 / ltr |
6. | Electricity and Fuel | 0.60 / ltr |
7. | Pouches and Packing | 0.80 / ltr |
8. | Chemicals & Detergents | 0.25 / ltr |
9. | Maintenance & Repairs(% on Machinery Cost) | 5% |
10. | Insurance (% of Machinery Cost & Civil Structure) | 1.6% |
11. | Milk Distribution Cost | 1.25 / ltr |
12. | Advertising | 0.20 / ltr |
Income on Dairy Processing Plant Project:
Milk Procured(8,000/- ltr / day) | ||
Milk Processed(7,995 ltr / day) | ||
1. | Toned Milk (3% fat – 7,350 ltrs / day @ Rs.34 / ltr) | 2,49,900/- |
2. | Ghee (170 kg / day @ Rs.290 / kg) | 49,300/- |
3. | Cream (40% fat & 25% cream; 160 ltrs / day @ Rs.120 / kg) | 19,200/- |
The above cost figures in this project report are not actuals but are indicative to give an understanding to young entrepreneurs on investment and returns in the dairy processing business project. Dairy entrepreneurs should get quotations & estimations from vendors for specific designs of plant machinery equipment and their installations. It is recommended for entrepreneurs to enter into contract for maintenance and service after purchase.
The dairy unit should have a marketing department that will promote milk and dairy products by placing hoardings or billboards at strategic locations in the cities and retail centers. A detailed market survey of cities and retail outlets will help with distribution and advertising plans. The major competitors and their present offers are to be found out. Building or promoting dairy brand milk parlors and distribution retail outlets in major densely populated regions in the cities with door delivery of milk to consumers will be able to achieve higher growth in sales.
Dairy Processing Plant Project Report – Statutory / Government Approvals
The dairy Processing Plant must possess the following requirements licenses and permits from statutory agencies:
- License from the State Food and Drug Department.
- MMPO registration from the concerned state government.
- Plan approval from Gram Panchayat or Municipality.
- Registration – PF, ESI, and Labor laws.
- NOC from Fire and Safety Department.
- Clearance Certificate from Pollution Control Board
- Registration with Small Industries or District Industries Department.
- License from Factory Inspector for Boiler Installation.
- Local authority clearance for shops and establishment.
20 COMMENTS
Excellent useful information available on the site. One can down load and readjust the same as per own use
Very useful information for a start up. It provides most of the basic information that can be modified to suit any jurisdictional requirement.
The information is useful for a start up business in dairy milk processing plant. The work is commendable
Dear sir i am willing to start a Milk processing plant and automated milk collection system in uttar pradesh ( Ghazipur) Destrict please help me for providing a DPR on 10000/ltr/day plant
Very nice piece of information. Really a important guide for the new entrepreneurs to chalk out their business plan for successful implementation.
Thank you for detailed reports on multiple agro based industries. A good initiative, very helpful for new investors and project planners.
I would like to get in touch with you regarding a diary plant project in South, with an installed capacity of upto 1,00,000 liters per day processing. Please reach me at your convenience.
I got Excellent information to read this is helpful for my dairy business planning. I need the information for Machinery and Equipment suppliers & contacts
reg organic integrated agro project
Thank you for the excellent information. I would like to start this business.
Valuable information, highly cherished.
thank you for the great information.I would like this type of Business,
very informative
I am looking for a quotation for constructing a dairy processing plant. Please reach me on my email Id
We have plan to start dairy processing unit 3 Kl/hr . kindly to arrange DPR
GOOD PIECE OF INFORMATION. IF POSSIBLE, PLEASE GIVE US SOME KNOWLEDGE ON DISTRIBUTION CHANNELS AND MARKETING STRATEGIES USED BY THE KEY PLAYERS IN THE MARKET.
Very useful information for a start up company.
Absolutely productive information s through which,l will be able to approach for a milk plant as per my plan.
Sir, We have milk cooperative at Ghaghra, Gumla, Jharkhand. We would like to start milk chilling and processing unit. It is government sponsored. We need DPR, machines and entire set up. Let us know, if there are possibilities
Excellent information .I want to start 100000 litres milk processing plant per day with its byproducts..I need DPR and to know profitability details…
Very insightful business plan. We want a plan for 2000lts/ day milk collection center which we can develop into a processing plant. The infrastructure is already there so it the machinery and equipment. We would also appreciate if we can incorporate biscuit making machines with packing as an added enterprise.
LEAVE A REPLY Cancel reply
Save my name and email in this browser for the next time I comment.
Common Challenges in Strawberry Farming: A Beginners Guide
Maximizing yield in ridge gourd farming: best practices and tips , sustainable agriculture with crfs (controlled release fertilizers): a game-changer for..., organic farming vs. natural farming (zbnf): key principles and differences, strawberry nursery establishment and management, modi vision for indian agriculture, government support and policies for zbnf in india, deworming schedule for sheep: a beginners guide, ultimate guide to beans farming in kenya: from planting to..., ultimate guide to natural vegetable farming, natural farming for sustainable livestock management, dairy farm technology in india: the future of dairy husbandry, comprehensive guide to organic farming in villages, modern sheep farming technology: the future of sheep husbandry, goat farming technology: the future of goat husbandry, how to build a low-budget goat shed: cheap ideas and..., goat farming training programs in india: a beginner’s guide, types of pesticides used in agriculture: a beginner’s guide, economical aquaculture: a guide to low-budget fish farming, 15 common planting errors that can doom your fruit trees, borewell drilling cost, pump price, and pipe cost, polyhouse subsidy, cost, profit, project report, tractor subsidy, bank loan, eligibility, schemes, process, malabar neem project report details guide, cold storage project report, cost and subsidy, mushroom farming project report, cost and profit analysis.

Business Planning for a Milk Processing Plant: Key Steps and Checklist
By henry sheykin, get full bundle.
$169$99 | $59$39 | $39$29 | $15$9 | $25$15 | $15$9 | $15$9 | $15$9 | $19 |
Are you ready to embark on an exciting business venture in the milk processing industry? If so, you've come to the right place. In this blog post, we will provide you with a comprehensive checklist on how to write a business plan for a milk processing plant in 9 simple steps. But before we dive into the details, let's take a look at some fascinating statistics about this thriving industry.
Related Blogs
- 7 Mistakes to Avoid When Starting a Milk Processing Plant in the US?
- What Are The Top 9 Business Benefits Of Starting A Milk Processing Plant Business?
- What Are The Nine Best Ways To Boost A Milk Processing Plant Business?
- Milk Processing Plant Business Idea Description in 5 W’s and 1 H Format
- Buy or Acquire a Milk Processing Plant: Essential Checklist
- What Are The Reasons For The Failure Of Milk Processing Plant Businesses?
- Earnings of Milk Processing Plant Owners
- How to Open a Milk Processing Plant: A Detailed Checklist for Beginners
- 7 Primary KPIs for Effective Milk Processing Plant
- What Are the Main Costs of a Milk Processing Plant?
- Unleash your dairy dreams with our game-changing Pitch Deck! Join the revolution now!
- Effective Ways to Increase Profitability in Milk Processing
- The Complete Guide To Milk Processing Plant Business Financing And Raising Capital
- Strategies To Increase Your Milk Processing Plant Sales & Profitability
- How To Sell Milk Processing Plant Business in 9 Steps: Checklist
- Essential Startup Costs For A Milk Processing Plant
- What Are The Key Factors For Success In A Milk Processing Plant Business?
- Valuing a Dairy Plant Business? Tips!
- The No-Money Approach to Starting a Milk Processing Plant
According to recent data, the milk processing industry has experienced significant growth in the past decade. In fact, the global market for processed milk products is projected to reach $782.6 billion by 2026. This impressive growth can be attributed to the rising demand for organic and farm-fresh products, as well as the increasing popularity of dairy-based foods such as yoghurt, sour cream, and cheese.
If you're considering starting a milk processing plant to provide these high-quality products to your local community, now is definitely the perfect time to do so. By following our comprehensive checklist, you'll be well-prepared to navigate the challenges and opportunities that lie ahead.
So, without further ado, let's get started on the first step of writing a successful business plan for your milk processing plant - conducting market research and analyzing the milk processing industry.
Conduct Market Research And Analyze The Milk Processing Industry
Before starting a milk processing plant, it is crucial to conduct market research and analyze the milk processing industry. This step will provide valuable insights into the current state of the industry, potential market opportunities, and potential challenges.
- Identify market trends: Research the latest trends and developments in the milk processing industry. This includes analyzing consumer preferences for organic and farm-fresh products, as well as any emerging market segments.
- Assess market demand: Determine the potential demand for processed milk products in the target market. This can be done through surveys, interviews, or analyzing existing data. Understanding the demand will help determine the scale of production and potential sales volume.
- Analyze competitors: Identify existing milk processing plants in the area and analyze their products, pricing strategies, distribution channels, and customer base. This will help identify potential gaps in the market and competitive advantages for your own plant.
- Evaluate market barriers: Research any regulatory or legal barriers that may exist in the milk processing industry. This can include obtaining necessary permits and licenses, complying with food safety regulations, and adhering to labeling and packaging requirements.
Tips for conducting market research in the milk processing industry:
- Utilize online market research tools and databases to gather information about industry trends, market size, and consumer preferences.
- Attend industry trade shows and conferences to network with industry professionals and gather valuable insights.
- Engage with potential customers through focus groups or surveys to understand their preferences and buying habits.
- Consider hiring a market research firm to conduct a comprehensive analysis of the milk processing industry and market potential.
Conducting market research and analyzing the milk processing industry will provide a solid foundation for the business plan of your milk processing plant. It will help you make informed decisions regarding product offerings, target market, and marketing strategies, increasing the likelihood of success in this competitive industry.
| Milk Processing Plant Financial Model Get Template |
Define The Target Market And Identify The Potential Demand For Processed Milk Products
Defining the target market and identifying the potential demand for processed milk products is crucial for the success of your milk processing plant. By understanding who your target customers are and their consumption patterns, you can tailor your products and marketing strategies to meet their specific needs and preferences.
1. Conduct market research: Begin by conducting thorough market research to gain insights into the milk processing industry. Analyze consumer trends, preferences, and purchasing behavior related to dairy products. This will help you understand the demand for processed milk products and identify any gaps or opportunities in the market.
2. Identify target customers: Determine the specific target market segments for your milk processing plant. Consider factors such as age, income level, location, and lifestyle. For example, you may target health-conscious individuals, families seeking organic and farm-fresh products, or restaurants and delicatessens looking for high-quality dairy products. Clearly defining your target market will guide your product development and marketing strategies.
3. Assess market demand: Evaluate the potential demand for processed milk products in your target market. Identify the consumption patterns, volume of sales, and growth trends to gauge the market's potential. This information will help you forecast sales and make informed decisions regarding production capacity and product range.
- Consider surveying potential customers or conducting focus groups to understand their preferences and expectations for processed milk products.
- Stay updated with industry reports and publications to keep abreast of any shifts in consumer preferences or market dynamics that may impact the demand for your products.
- Take into account the seasonality of demand, as certain products like ice cream or flavored milk may experience higher sales during specific times of the year.
4. Analyze competition: Research and evaluate the competitors in the milk processing industry. Identify the key players, their market share, product offerings, pricing strategies, and distribution channels. This analysis will help you identify opportunities to differentiate your products and develop a competitive advantage.
By defining your target market and understanding the potential demand for processed milk products, you can effectively position your milk processing plant in the market and develop a comprehensive business plan to meet the needs of your customers.
Identify And Evaluate Potential Competitors In The Industry.
Identifying and evaluating potential competitors is a crucial step in developing a successful business plan for a milk processing plant. It allows you to gain insights into the existing players in the industry and understand how your plant can differentiate itself and capture market share. Here are some key considerations:
- Research Competitor Landscape: Begin by conducting thorough research on the milk processing industry and the competitors within your target market. Look for similar businesses in the area that are already producing and selling processed milk products. Study their products, pricing, distribution channels, and branding strategies to understand how they position themselves in the market.
- Identify Strengths and Weaknesses: Analyze the strengths and weaknesses of your potential competitors. This will help you identify areas where your milk processing plant can outperform or differentiate itself. Consider factors such as product quality, pricing, distribution reach, customer service, and brand reputation. Identifying gaps or areas for improvement can provide you with valuable insights for developing your own competitive advantage.
- Study Market Share and Growth Potential: Determine the market share held by the existing competitors and their growth trends. This information will help you gauge the level of competition and identify opportunities for market expansion. It will also give you a sense of the size of the market and its potential for growth.
- Assess Barriers to Entry: Evaluate the barriers to entry in the milk processing industry. These may include regulatory requirements, capital investment, access to raw milk supply, or established distribution channels. Understanding these barriers will give you a realistic idea of the challenges you may face and help you develop strategies to overcome them.
- Consider visiting your potential competitors' facilities to gain a firsthand experience of their operations and understand their production processes.
- Look for emerging trends in the industry, such as an increased demand for organic or plant-based milk products, and assess how your competitors are adapting to these changes.
- Keep an eye on new entrants in the market who may disrupt the industry or introduce innovative products or business models.
Determine The Necessary Production And Processing Equipment For The Plant.
When starting a milk processing plant, it is crucial to determine the necessary production and processing equipment to ensure smooth operations and high-quality products. The right equipment will enable efficient milk processing and packaging, ensuring the products meet customer expectations.
Here are some important factors to consider when determining the necessary production and processing equipment:
- Processing Capacity: Assess the volume of milk you plan to process on a daily basis to determine the necessary capacity of equipment. Consider factors such as anticipated growth, demand, and future expansion.
- Milk Quality and Safety: Invest in equipment that meets industry standards and regulations for milk processing and ensures the safety and quality of the final products. This includes pasteurization equipment, milk storage tanks, and packaging machines.
- Processing Methods: Depending on the products you plan to offer, consider the specific processing methods and equipment required. For example, cheese production may require cheese vats and curd cutters, while yogurt production may require yogurt fermenters and incubation tanks.
- Automation and Efficiency: Look for equipment that offers automation and efficiency features to streamline your production process. This can include automated filling and packaging machines, computerized control systems, and advanced filtration systems.
- Budget: Consider your budget constraints when selecting equipment. Balance the cost of purchasing and maintaining the equipment with the long-term benefits it will bring to your business.
- Consult with industry experts or equipment suppliers to understand the latest advancements and technologies in milk processing equipment.
- Consider the space available in your plant and ensure the equipment fits comfortably without causing any operational limitations.
- Take into account the maintenance requirements and availability of spare parts for the chosen equipment.
- Research the equipment suppliers thoroughly and choose reliable ones with a good track record in the industry.
By carefully determining the necessary production and processing equipment for your milk processing plant, you can ensure efficient operations, meet quality standards, and ultimately deliver high-quality products to your customers.
Assess The Availability And Cost Of Raw Milk Supply.
When starting a milk processing plant, it is essential to carefully assess the availability and cost of raw milk supply. The success of your business depends on securing a reliable and affordable source of raw milk. Here are some key considerations:
- Research local dairy farms and suppliers: Identify dairy farms in your area or nearby regions that have a consistent supply of high-quality raw milk. Visit these farms and establish relationships with the farmers to understand their production capabilities and determine if they align with your business needs.
- Evaluate milk production capacity: Determine the potential volume of raw milk that each dairy farm can provide on a regular basis. This evaluation will help you estimate the quantity of milk you can process and ensure that it meets your production requirements.
- Assess milk quality standards: It is crucial to ensure that the raw milk you source meets all the necessary quality standards. Look for farms that prioritize hygiene, sanitation, and proper milking practices to maintain the freshness and purity of the milk. Consider conducting regular quality checks to maintain high product standards.
- Consider seasonal variations: Keep in mind that milk production can fluctuate throughout the year due to seasonal variations, such as changes in weather conditions or the reproductive cycles of cows. Plan accordingly and factor in potential seasonal variations in milk supply when assessing availability.
- Calculate the cost of raw milk: Analyze the pricing structures of different dairy farms and suppliers to determine the cost of raw milk. Consider factors such as transportation, quantity discounts, and any additional costs associated with the milk supply chain. This evaluation will help you estimate the financial implications of raw milk procurement.
- Establish long-term contracts: Consider entering into long-term contracts with dairy farmers to secure a consistent supply of raw milk. This can help build trust and ensure a stable partnership for your milk processing plant.
- Network with industry associations: Joining local or regional dairy industry associations can provide valuable insights into milk sourcing and connect you with potential suppliers. These associations often organize events and conferences where you can learn more about sourcing strategies and best practices.
Explore Potential Suppliers And Establish Partnerships.
When starting a milk processing plant, it is crucial to find reliable and high-quality suppliers for your raw milk. Exploring potential suppliers and establishing partnerships is an essential step in ensuring the success of your business.
One of the first things you should do is conduct thorough research to identify potential suppliers in your area or beyond. Look for suppliers who specialize in organic and farm-fresh raw milk to align with your business's mission of providing healthy and natural products. Consider factors such as the supplier's reputation, quality of their milk, and reliability of their deliveries.
Establishing partnerships with your chosen suppliers can bring numerous benefits to your milk processing plant. It can help you secure a consistent and reliable source of raw milk, negotiate better pricing and payment terms, and foster long-term relationships based on trust and mutual growth. Additionally, partnerships with suppliers who share your commitment to sustainability and ethical farming practices can enhance your brand's reputation.
Tips for exploring potential suppliers and establishing partnerships:
- Attend industry conferences and trade shows to meet suppliers face-to-face and learn about their products and practices.
- Visit potential supplier farms to assess their operations and ensure they meet your quality standards.
- Request samples of the raw milk from different suppliers and conduct taste tests to determine the flavor profile and quality of the milk.
- Request references from other businesses who have worked with the potential suppliers to get insights into their reliability and professionalism.
- Consider the logistics and transportation costs involved in sourcing raw milk from potential suppliers and choose ones that are cost-effective and conveniently located.
- Negotiate agreements and establish clear communication channels with your selected suppliers to ensure smooth operations and efficient collaborations.
By thoroughly exploring potential suppliers and establishing strong partnerships, you can ensure a consistent supply of high-quality raw milk for your milk processing plant. This will help you maintain the quality and integrity of your products, ultimately leading to customer satisfaction and business success.
Calculate The Initial Investment Required And Potential Sources Of Funding.
One of the most crucial steps in starting a milk processing plant is determining the initial investment required to set up the business and identifying potential sources of funding. This will help you understand the financial feasibility of your venture and plan accordingly.
To calculate the initial investment, you need to consider various factors such as:
- The cost of land or building for setting up the plant
- The cost of purchasing production and processing equipment
- The cost of raw milk supply and storage facilities
- The cost of packaging materials
- The cost of obtaining necessary licenses and certifications
- The cost of marketing and promotional activities
- The cost of recruiting and training employees
- The cost of utilities and other operational expenses
It is important to conduct thorough research and gather accurate cost estimates from multiple sources to ensure you have a realistic understanding of the financial requirements.
Once you have calculated the initial investment, the next step is to identify potential sources of funding. Here are some options to consider:
1. Self-Funding:
- Consider using your personal savings or assets to finance a portion of the investment. This will give you more control over the business and minimize the reliance on external funding.
2. Bank Loans:
- Approach banks or financial institutions to inquire about business loans specifically designed to support the establishment of milk processing plants. Prepare a comprehensive business plan and financial projections to increase the chances of securing a loan.
3. Government Grants and Subsidies:
- Research and explore available government grants and subsidies aimed at promoting agricultural and food processing industries. These funds can significantly reduce your initial investment burden.
4. Investor Funding:
- Consider attracting investors who are interested in your business idea and willing to provide financial support in exchange for equity or a share in profits. Prepare a compelling pitch and business plan to present to potential investors.
Remember, it is crucial to present a well-documented business plan, financial projections, and a solid return on investment (ROI) potential to attract potential sources of funding.
Study The Legal And Regulatory Requirements For Operating A Milk Processing Plant.
When starting a milk processing plant, it is essential to thoroughly study and understand the legal and regulatory requirements that govern the industry. This will ensure that your business operates in compliance with relevant laws and regulations, avoiding potential legal issues and penalties.
First and foremost, you should familiarize yourself with food safety regulations and standards that apply to milk processing plants. These regulations are in place to protect consumers and ensure the safety and quality of food products. It is crucial to adhere to guidelines for proper pasteurization techniques, sanitation practices, and product labeling.
You will need to obtain licenses and permits from the appropriate governmental authorities to operate a milk processing plant. These may include permits for food handling, dairy processing, and environmental compliance. Contact your local health department or agricultural department to inquire about the necessary permits and the application process.
Another important aspect to consider is packaging and labeling requirements for milk and milk products. Packaging should be designed to preserve the freshness and safety of the products, and labels must accurately reflect the contents and meet all necessary information and labeling requirements.
It is also essential to understand employment laws and regulations that apply to your milk processing plant. This includes laws related to employee health and safety, minimum wages, working hours, and other labor-related aspects. Complying with these regulations will contribute to creating a safe and respectful working environment.
Furthermore, it is crucial to be aware of the environmental regulations that apply to milk processing plants. Some of the key considerations include waste management practices, wastewater treatment, and energy conservation measures. Meeting these regulations will ensure that your business operates in an environmentally sustainable manner.
Tips for studying the legal and regulatory requirements:
- Consult with legal experts or industry professionals who specialize in food processing and dairy regulations for guidance and advice.
- Stay updated on any changes or updates to relevant laws and regulations to ensure ongoing compliance.
- Create a comprehensive checklist to ensure that all necessary permits, licenses, and certifications are obtained before commencing operations.
- Keep detailed records and documentation of your compliance efforts to demonstrate adherence to regulatory requirements.
Develop A Comprehensive Marketing And Sales Strategy.
Once you have completed the previous eight steps of writing a business plan for your milk processing plant, it's time to develop a comprehensive marketing and sales strategy. This step is crucial to ensure the success and profitability of your business.
Understand your target market: Before you can effectively market your products, it's essential to have a deep understanding of your target market. Identify who your potential customers are, their preferences, purchasing habits, and what drives their buying decisions. This knowledge will help you tailor your marketing messages to resonate with your target audience.
Create a brand identity: Your milk processing plant should have a strong brand identity that sets it apart from competitors. Develop a compelling brand story and create a unique brand name, logo, and packaging that conveys the values and quality of your organic and farm-fresh products. A cohesive and visually appealing brand identity will help attract customers and build brand loyalty.
Establish distribution channels: Determine the most effective distribution channels to reach your target market. This may include selling your products to local grocery stores, health food stores, delicatessens, and restaurants. Additionally, consider offering convenient delivery services to customers from the surrounding areas to expand your reach and convenience.
Tips for Developing a Marketing and Sales Strategy
- Invest in professional product photography to showcase the quality and freshness of your milk products.
- Utilize social media platforms and online advertising to raise brand awareness and reach a wider audience.
- Offer promotional discounts or special deals to attract new customers and encourage repeat purchases.
- Participate in local community events and farmer's markets to build connections and promote your brand.
- Build strong relationships with local grocery store buyers, restaurant owners, and other potential business partners to secure long-term partnerships.
Implement a comprehensive marketing plan: Develop a detailed marketing plan that outlines your strategies and tactics to promote your milk processing plant and products. This plan should include both online and offline marketing efforts, such as advertising campaigns, public relations, influencer partnerships, social media marketing, and content creation. Continuously evaluate and adjust your marketing strategies based on feedback and results to maximize your marketing impact.
Train your sales team: Invest in training your sales team to effectively sell your milk products. Provide them with in-depth product knowledge and customer service training to ensure they can confidently answer customers' questions and address any concerns. Incentivize your sales team to achieve sales targets and provide ongoing support and feedback to help them improve their performance.
Monitor and analyze performance: Regularly monitor and analyze the performance of your marketing and sales efforts. Track sales, customer feedback, and market trends to identify areas for improvement and success. Use this data to refine your strategies and make informed decisions to stay competitive in the milk processing industry.
By developing a comprehensive marketing and sales strategy, you can effectively promote your milk processing plant and products, attract customers, and drive sales. Remember to continuously adapt and evolve your strategies to meet the changing needs of your target market and ensure the long-term success of your business.
In conclusion, writing a business plan for a milk processing plant involves conducting thorough market research, identifying the target market and potential demand, evaluating competitors, determining production equipment and raw milk supply, establishing partnerships, calculating the initial investment, understanding legal requirements, and developing a comprehensive marketing strategy. By following these nine steps, entrepreneurs can create a solid foundation for starting a successful milk processing business and providing organic and farm-fresh products to local communities.
| Expert-built startup financial model templates |
Leave a comment
Your email address will not be published. Required fields are marked *
Please note, comments must be approved before they are published
JavaScript seems to be disabled in your browser. For the best experience on our site, be sure to turn on Javascript in your browser.
Tools for Developing a Business Plan for a Dairy Operation

Photo Credit Free-Photos from Pixabay
For ag professionals or producers who want to develop a business plan for the dairy operation, this library of resources provides tools that may be useful.
The site includes a Business Plan Template, Business Planning Factsheets, a Case Farm example to show how a finished product may look, and a set of Financial Resource Documents. These documents are a collection of sample reports that show the type of financial information to include in a plan. There is also a folder of Financial Tools at the site that includes both Excel spreadsheets and fillable PDF forms that can be used to create these financial reports.
You may also be interested in ...

Milk Production Records for Management Control

Feeding Records for Management Control

Using QuickBooks to Manage Your Farm Business: Instructor-Guided

Using Quickbooks to Manage Your Farm Business

Standard Operating Procedures for Dairy Farms

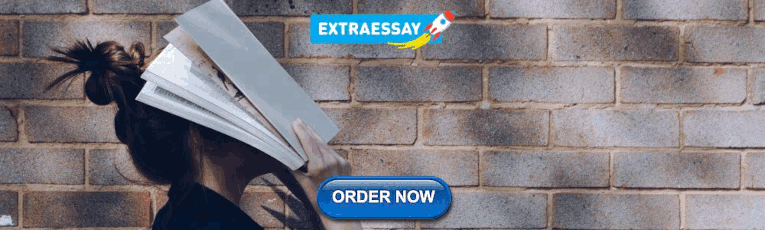
Heifer Economics

Dairy Sense: Unlocking Added Potential

Dairy Heifer Cost Variation

The Seven Steps of Action Planning

Dairy Risk-Management Education: Using Milk Futures to Lock in Profitability
Personalize your experience with penn state extension and stay informed of the latest in agriculture..
Academia.edu no longer supports Internet Explorer.
To browse Academia.edu and the wider internet faster and more securely, please take a few seconds to upgrade your browser .
Enter the email address you signed up with and we'll email you a reset link.
- We're Hiring!
- Help Center
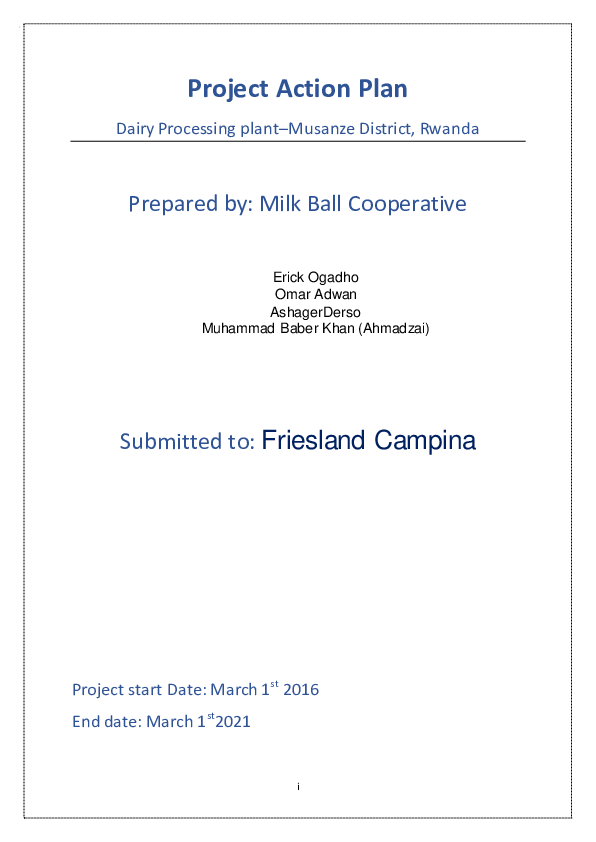
Project Action Plan Dairy Processing plant-Musanze District, Rwanda Prepared by: Milk Ball Cooperative

2016, Dairy Processing plant
Milk Ball Cooperative, is a dairy cooperative of Musanze district´s dairy chain in Rwanda, is providing an investment business idea on Dairy processing plant in Musanze district, to Friesland Campina. Currently, Friesland Campina has shown an interest in establishing a dairy processing plant in Musanze district Rwanda. It aims at achieving this by linking existing and new smallholder dairy producers to expanding market demand in Rwanda and within the region, driven by improved quality, reduced transaction costs, and increased investment all along the dairy value chain. This document gives an overview of the structure of Milk Ball Cooperative, its activities, credentials, and strategies. Milk Ball cooperative will work with smallholder dairy producer in Rwanda in procurement of adequate amount of quality milk for the Friesland Campina proposed dairy processing plant. In addition, this document gives the details of the requirements of the proposed Dairy processing plant business idea and an insight of the Rwandan dairy value chain. Also; it gives the projections of the cash flow over the project period of 5 years and the expected payback period. The estimated cost of the project implementation is 8.86 million Euros. After five years of duration, Friesland Campina will have a functional dairy processing plant. All the data included in this project study is based on data gathered from secondary sources and on certain assumptions.
Related Papers
Nathaniel Makoni
A study of the dairy sector in six East African countries was followed by a dairy expert consultation in Uganda in April 2014. The objective of the initiative was to explore possibilities to improve coordination among development agencies, investors and other value chain stakeholders and governments, and for creating synergy within and between the different countries. This report describes outcomes of both study and consultation and is intended to serve as a reference document for all stakeholders. It includes recommendations and priority actions that should enable stakeholders to capitalize on the opportunities in the East African dairy sector and clarify the roles of various partners in this endeavour (donors, public sector, and private sector). Study and consultation were initiated by the Inter-Agency Donor Group (IADG) on pro-poor livestock research and development. Keywords: dairy, dairy value chain, milk, livestock, cattle, donor collaboration, East Africa, Kenya, Ethiopia, Ta...
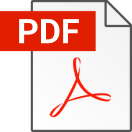
Eduardo Fuentes
Gebreyohannes Berhane
The potential for dairy production in Alamata is significant but yet untapped. Market oriented smallholder dairy development in Alamata has an opportunity for growth because of growing urban population, location of the town on the main Addis Ababa-Mekelle highway. In 2005, Improving Productivity and Market Success of Ethiopian farmers' project introduced participatory market-oriented dairy development through value chain approach. Prior to the intervention, gaps in the value chain were identified through rapid diagnostic survey, and the interventions were designed on the basis of a district level participatory market oriented value chain development planning approach involving the key stakeholders. The interventions encompassed i) capacity building of women and men famers and public staff extension workers ii) feed improvement and utilization through introduction of improved forages, crop residue treatment and stale feeding, iii) breed improvement through selection of local cattle (Senga) breed and cross breeding using exotic bull (Jersey and/or Holstein Frisian) and use of artificial insemination (AI) iv) introduction of better yielding indigenous (Begait breed) heifers v) provision of credit and vi) formation of milk marketing cooperatives. Multitude of methods and approaches were employed to monitor and document the intervention processes and outcomes such as PRA, stakeholder workshops, community level focus group discussions, household survey, etc. The results indicate: i) milk yield per cow and the culture of milk selling and milk supply to market increased ii) households, particularly women, obtained additional income from milk sales and their livelihoods improved iii) both the approaches and technologies diffused to adjacent kebeles and neighboring woredas. Overall participatory market-oriented smallholder dairy development with value chain approach was effective in the pilot learning woreda (PLW). The challenges to ensuring sustainability and scaling up/out of the experiences were insufficient response for the high demands of farmers for input supply (better yielding heifers, improved forage seeds), inefficient AI and bull service and weak animal health service by the public extension and ineffective organizational setup and leadership experience both within the dairy cooperatives and the cooperative department of the woreda office of agriculture and rural development (WoARD).
Asian Journal of Agriculture and Rural Development
EUGENE KARENZI
Journal of Asynchronous Learning Network
John Kabasa
The AgShare Phase I Program, conducted at Makerere University, Kampala, Uganda, was formed to create open education resources for teaching and community development through action research. The study was conducted by an interdisciplinary team of investigators from fields of veterinary medicine and agri-business. Two master of science students conducted dairy value chain action research that produced case materials used to create open education resources (OER) course modules (milk hygiene and marketing modules) and design interventions that would improve milk production, quality, and safety; reduce milk spoilage; increase price per liter of milk received by farmers; and support on-farm processing of yogurt and other dairy products. This research was used in partial fulfillment of the requirement for the master’s degree in Livestock Development, Planning, and Management (MLD) and the master’s degree in Agri-business Management (M Agbus Mgt) by these students. The conceptual design, im...
Journal of Asynchronous Learning Networks
Harinder Makkar
Siemen Van Berkum
California Center for Cooperative Development, Davis, …
Justin Ellerby
Loading Preview
Sorry, preview is currently unavailable. You can download the paper by clicking the button above.
- We're Hiring!
- Help Center
- Find new research papers in:
- Health Sciences
- Earth Sciences
- Cognitive Science
- Mathematics
- Computer Science
- Academia ©2024

DESIGNING A PROCESS LINE
- Medium text
In the dairy, raw milk passes through several stages of treatment in various types of processing equipment before reaching the consumer in the form of a finished, refined product. Production usually takes place continuously in a closed process, where the main components are connected by a system of pipes. The type of treatment involved and the design of the process depend on the end product. The process described in this chapter is general milk pasteurization. This process is the basic operation in market milk processing, and also constitutes an important pre-treatment stage in a chain of dairy processes such as cheesemaking and cultured milk production. The aim is to present some of the considerations which the plant designer has to face when planning a whole milk pasteurization plant.
Process design considerations
There are many aspects to be considered when a process line is designed. They can vary and be extremely complex, which places considerable demands on those responsible for the preliminary planning. Project engineering always involves a compromise between different requirements such as:
- Product-related – concerning the raw material, its treatment and the quality of the end product
- Process-related – concerning plant capacity, selection of components and their compatibility, degree of process control, availability of heating and cooling media, cleaning of processing equipment, etc.
- Economic – that the total cost of production to meet the stipulated quality standards is as low as possible
- Legal – legislation stipulating process parameters as well as choice of components and system solutions
The process illustrated in Figure 7.1 deals with heat treatment – pasteurization – of whole milk, e.g. market milk for sale to consumers.

Generalized block chart of the milk pasteurization process.
Some legal requirements
In most countries where milk is processed into various products, certain requirements are determined by law to protect consumers against infection by pathogenic microorganisms. The wording and recommendations may vary, but the combination below covers the most commonly stated requirements:
- Heat treatment The milk must be heat treated in such a way that all pathogenic microorganisms are killed. A minimum temperature/holding time of 72 °C for 15 seconds must be achieved.
- Recording The heating temperature must be automatically recorded and the transcript saved for a prescribed period of time.
- Clarification prior to heat treatment As milk often contains solid matter such as dirt particles, leucocytes (white blood corpuscles) and somatic cells (of udder tissue), it must be clarified. Since pasteurization is less likely to be effective if bacteria are hidden in lumps and particles in the milk, clarification must take place before heating. Milk can be clarified in a filter or, more effectively, in a centrifugal clarifier.
- Preventing reinfection Heat exchangers are calculated so that a higher pressure should be maintained in the pasteurized milk flow compared to the unpasteurized milk and service media. If a leakage should occur in the heat exchanger, pasteurized milk must flow into the unpasteurized milk or cooling medium, and not in the opposite direction. In order to ensure this, a booster pump to create a pressure differential is often required and in certain countries it is mandatory.
In the event of temperature drop in the pasteurized product due to a temporary shortage of heating medium, the plant must be provided with a flow diversion valve to divert the insufficiently heated milk back to the balance tank.
- Automatic temperature control
- Recording thermometer
- Automatic safety device preventing insufficient heating
- Adequate safety system preventing the mixture of pasteurized or sterilized milk with incompletely heated milk
- Automatic recording device for the safety system referred to in the preceding intent
- Heat treatment
- Clarification prior to heat treatment
- Preventing reinfection
Equipment required
The following equipment is required for a remote controlled process:
- Silo tanks for storing the raw milk.
- Plate heat exchanger for heating and cooling, a holding tube and a hot water unit.
- Centrifugal clarifier (as only whole milk is to be treated, a centrifugal separator is not needed in this example).
- Intermediate storage tank for temporary storage of processed milk.
- Pipes and fittings for connecting main components and pneumatically operated valves for controlling and distributing the product flow and cleaning fluids.
- Pumps for transportation of milk through the entire milk treatment plant.
- Control equipment for control of capacity, pasteurization temperature and valve positions.
- Various service systems: – Water supply – Steam production – Refrigeration for coolant – Compressed air for pneumatically operated units – Electric power – Drain and waste water.
Most of the service systems are described in Chapter 6.11. Service media requirements are calculated after the plant design is agreed upon. Thus, the temperature programme for pasteurization must be known, as well as the specifications for all other areas where heating and cooling are needed (cold storage, cleaning systems, etc.), before the number and power of electrically operated machines, number of pneumatically operated units, working hours of the plant, etc. can be determined. Such calculations are not presented in this book.
Choice of equipment Silo tanks
The number and size of silo tanks are determined by the raw milk delivery schedules and volume of each delivery. In order to operate the plant continuously without stoppages due to lack of raw material, a sufficient supply of raw milk must be available. Preferably, the milk should have been stored for at least one hour before being processed, as natural degassing of the milk takes place during that period of time. Short periods of agitation are acceptable, but agitation is not really needed until about 5 – 10 minutes before the silo is to be emptied, to equalize the overall quality. This avoids interference with the natural degassing process.
- Heat exchanger
The main aim of pasteurizing milk is to destroy pathogenic microorganisms. To achieve this, the milk is normally heated to not less than 72 °C for at least 15 seconds and then cooled rapidly. These parameters are stipulated by law in many countries. The plate heat exchanger is most common for market milk pasteurization purposes. Tubular heat exchangers can be used when long running times are essential. Scraped-surface heat exchangers are used for viscous products. When the relevant parameters are known, the size (dimensioning) of the heat exchanger can be calculated. In the present example, the parameters are:
- Plant capacity, l/h 20 000
- Temperature programme, °C 4 – 72 – 4
- Regenerative effect, % 90 – 94
- Temperature of the heating medium, °C 74 – 75
- Temperature of the coolant, °C +2
The demand for service media (steam, water and ice water) is also calculated, as this substantially influences the choice of valves for steam regulation and ice water feed. In plate heat exchangers, the connection plates between the sections are provided with inlets and outlets for product and service media. The inlet and outlet connections can be oriented either vertically or horizontally. The ends of the plate heat exchanger (frame and pressure plate) can likewise be fitted with inlets and outlets. When long running time is essential the tubular heat exchanger is an alternative to the plate heat exchanger. Dimensioning data for the heat exchanger are given in Chapter 6.1.
Hot water heating systems
Hot water or saturated steam at atmospheric pressure can be used as the heating medium in pasteurizers. Hot steam, however, is not used because of the high differential temperature. The most commonly used heating medium is therefore hot water, typically about 2 – 3 °C higher than the required temperature of the product. Steam is delivered from the steam boiler at a pressure of 600 – 700 kPa (6 – 7 bar). This steam is used to heat water, which in turn heats the product to pasteurization temperature. The water heater in Figure 7.2 is a closed system consisting of a specially designed, compact and simple cassette-type plate heat exchanger (3) equipped with a steam regulating valve (2) and a steam trap (4). The service water is circulated by the centrifugal pump (5) via the heater (3) and the heating section of the pasteurizer. The function of the expansion vessel (7) is to compensate for the increase in the volume of the water that takes place when it is heated. The system also includes pressure and temperature indicators as well as safety and ventilation valves (8).

Principle of the hot water system connected to a pasteurizer.
- Steam shut-off valve
- Steam regulating valve
- Centrifugal pump
- Water regulating valve
- Expansion vessel
- Safety and ventilation valves
- TI Temperature indicator
- PI Pressure indicator
Temperature control
A constant pasteurization temperature is maintained by a temperature controller acting on the steam regulating valve (2) in Figure 7.2. Any tendency for the product temperature to drop is immediately detected by a sensor in the product line before the holding tube. The sensor then changes the signal to the controller, which opens the steam-regulating valve to supply more steam to the water. This increases the temperature of the circulating water and stops the temperature drop in the product.
The length and size of the externally located holding tube are calculated according to the known holding time and hourly capacity of the plant and the pipe dimension, typically the same as for the pipes feeding the pasteurization plant. Dimensioning data for the holding tube are given in Chapter 6.1. Typically, the holding tube is covered by a stainless steel hood to prevent people from being burnt when touching it and from radiation as well.
Pasteurization control
It is essential that the milk has been properly pasteurized before it leaves the plate heat exchanger. If the temperature drops below 72 °C, the unpasteurized milk must be kept apart from the already pasteurized product. To accomplish this, a temperature transmitter and flow diversion valve are fitted in the pipe downstream of the holding tube. Valve (3) in Figure 7.3 returns unpasteurized milk to the balance tank if the temperature transmitter detects that the milk passing it has not been sufficiently heated.

Automatic temperature control loop.
- TT Temperature transmitter
- Holding tube
- Booster pump
- Diversion valve
Pasteurizer cooling system
As already noted, the product is cooled mainly by regenerative heat exchange. The maximum practical efficiency of regeneration is about 94 – 95%, which means that the lowest temperature obtained by regenerative cooling is about 8 – 9 °C. Chilling the milk to 4 °C for storage therefore requires a cooling medium with a temperature of about 2 °C. Ice water can only be used if the final temperature is above 3 – 4 °C. For lower temperatures, it is necessary to use brine or alcohol solutions, to avoid the risk of freezing cooling media. The coolant is circulated from the dairy refrigeration plant to the point of use, as shown in Figure 7.4. The flow of coolant to the pasteurizer cooling section is controlled to maintain a constant product outlet temperature. This is done by a regulating circuit consisting of a temperature transmitter in the outgoing product line, a temperature controller in the control panel and a regulating valve in the coolant supply line. The position of the regulating valve is altered by the controller in response to signals from the transmitter. The signal from the transmitter is directly proportional to the temperature of the product leaving the pasteurizer. This signal is often connected to a temperature recorder in the control panel and recorded on a graph, together with the pasteurization temperature and the position of the flow diversion valve.

Cooling system for pasteurizer.
Booster pump to prevent reinfection
Care must be taken to avoid any risk of contamination of the pasteurized product by unpasteurized product or cooling medium. If any leakage should occur in the pasteurizer, it must be in the direction from pasteurized product to unpasteurized product or cooling medium.
This means that the pasteurized product must be under higher pressure than the medium on the other side of the heat exchanger plates. In Figure 7.3, a booster pump (2) is therefore installed in the product line, either after the holding section or before the heating section. The latter position minimizes the operating temperature of the pump and prolongs its life. The pump increases the pressure and maintains a positive differential pressure on the pasteurized product side, throughout the regenerative and cooling sections of the pasteurizer. Installation of a booster pump is specified in the legal requirements for pasteurization in some countries.
The complete pasteurizer
A modern milk pasteurizer, complete with equipment for operation, supervision and control of the process, is made using matching components, forming a sophisticated process unit, as in Figure 7.5.

The complete pasteurizer plant consists of:
Balance tank
Flow controller.
- Regenerative preheating sections
Centrifugal clarifier
- Heating section
- Hot water heating system
- Regenerative cooling sections
- Cooling sections
- Flow diversion valve
- Control panel
- A Temperature transmitter
- B Pressure gauge
The float-controlled inlet valve regulates the flow of milk and maintains a constant level in the balance tank. If the supply of milk is interrupted, the level will begin to drop. As the pasteurizer must be full at all times during operation to prevent the product from burning on to the plates, the balance tank is often fitted with a low-level electrode which transmits a signal as soon as the level reaches the minimum point. This signal actuates the flow diversion valve, which returns the product to the balance tank. The milk is replaced by water and the pasteurizer shuts down when circulation has continued for a pre-determined time.
The feed pump supplies the pasteurizer with milk from the balance tank, which provides a constant head.
The flow controller maintains the flow through the pasteurizer at the correct value. This guarantees stable temperature control and a constant length of the holding time for the required pasteurization effect. Often the flow controller is located after the first regenerative section.
Regenerative pre-heating
The cold untreated milk is pumped through the first section in the pasteurizer, the pre-heating section. Here, it is regeneratively heated with pasteurized milk, which is cooled at the same time. If the milk is to be treated at a temperature between the inlet and outlet temperatures of the regenerative section, for example clarification at 55 °C, the regenerative section is divided into two sections. The first section is dimensioned so that the milk leaves at the required temperature of 55 °C. After being clarified, the milk returns to the pasteurizer, which completes the regenerative pre-heating in the second section.
Pasteurization
Final heating to pasteurization temperature with hot water, normally of a temperature 2 – 3 °C higher than the pasteurization temperature (Δ t = 2 – 3 °C), takes place in the heating section. The hot milk continues to an external tubular holding cell. After the holding cell, the temperature of the milk is checked by a sensor in the line. It transmits a continuous signal to the temperature controller in the control panel. The same signal is also transmitted to a recording instrument which records the pasteurization temperature.
Flow diversion
A sensor after the holding cell transmits a signal to the temperature monitor. As soon as this signal falls below a pre-set value, corresponding to a specified minimum temperature, the monitor switches the flow diversion valve to divert the flow. In many plants, the position of the flow diversion valve is recorded together with the pasteurization temperature. For the location of the flow diversion valve, various solutions are available to satisfy local regulations and recommendations. Below are three alternatives which are commonly utilized:
- The flow diversion valve is situated just after the holding cell. Where a booster pump is installed, the valve is located before the pump. If the temperature drops under the pre-set level, the valve diverts the flow to the balance tank and the pump stops. The flow in the regenerative and cooling sections thus comes to a standstill (even when no booster pump is integrated). After a short while, without temperature increase, the heat exchanger is emptied, cleaned and sanitized. When satisfactory heating is possible, the plant is restarted.
- The flow diversion valve is located after the cooling section of the plant. Following a temperature drop, the flow is diverted to the balance tank and the plant is emptied of product, cleaned and sanitized. The plant is then ready for restart when the temperature conditions are acceptable again.
- The flow diversion valve is located between the holding cell and the booster pump. If the temperature drops, the valve diverts the flow. The booster pump is not stopped, but other valves around the heat exchanger will automatically be positioned so that the milk in the regenerative and cooling sections will be circulated to maintain the right pressure in the plant. This also preserves a proper temperature balance. When the heating conditions are acceptable, the process can be resumed without intermediate cleaning.
After the holding section, the milk is returned to the regenerative section(s) for cooling. Here the pasteurized milk transfers its heat to the cold incoming milk. The outgoing pasteurized milk is then chilled with cold water, ice water, a glycol solution or some other refrigerant, depending on the required temperature. The temperature of the chilled milk is normally recorded, together with the pasteurization temperature and the position of the flow diversion valve. The graph consequently shows three curves.
As the milk in the present example is not going to be separated into skim milk and cream, a centrifugal clarifier is shown in Figure 7.6. Some dairies specify centrifugal clarification of cold (<6 °C) raw milk immediately after arrival at the dairy, especially when the milk is going to be stored until the next day. However, clarification at about 55 °C is much more efficient, because the viscosity of the milk is lower at that temperature. The milk feeding the clarifier is therefore taken from the first regenerative heating section at 55 °C.

Bowl of a centrifugal clarifier.
Design of piping system
In the example in this chapter, 20 000 litres of milk per hour have to pass through pipes, fittings and processing equipment during production. The product velocity through the pipes is determined by the size of the passage, i.e. the inside diameter of the pipe. The larger the diameter, the lower the product velocity. For a flow rate of 20 000 litres per hour, the product velocity in a 76 mm (3") pipe will be 1.25 m/s. The velocity will be 2.75 m/s if a 51 mm (2") pipe is selected. Higher velocities result in greater friction in the liquid itself and between the liquid and the pipe wall. Consequently, there is more mechanical treatment of the product. For each product, there is an upper velocity limit that should not be exceeded if quality demands are to be met. For milk, this velocity is about 3 m/s.
It might then seem reasonable to choose a larger pipe size than the minimum required by velocity considerations. But larger pipes mean larger components and greatly increased costs. The diameter nearest the limit is therefore chosen. In our case, this is 2.5" (63.5 mm), which corresponds to a velocity of 1.75 m/s, as shown in Figure 7.7.

Product velocity and flow rate graph.
Laminar and turbulent flows
Laminar flow is a type of flow in which the particles maintain a continuous, steady motion along parallel paths. This type of flow occurs, for example, in straight, round pipes or between parallel walls at low velocities. On the other hand, in turbulent flow the particles have an irregular motion and intermix intensively with each other. The length of a line represents the mean velocity of the particles at various points in the section through the passage, as illustrated in Figure 7.8. In laminar flow, the velocity is greatest at the centre of the passage. Due to the friction between the layers, the velocity slows progressively towards the walls, where it is zero. In turbulent flow, the layers intermix and therefore the velocity of the liquid is roughly the same in the central part of the passage, but drops rapidly towards the walls. On the walls, a very thin laminar layer of the liquid has zero instantaneous velocity. To obtain laminar flow in a round pipe, the diameter must be small, the velocity low and the viscosity of the liquid high.

Velocity profile diagrams for laminar and turbulent flows.
Flow resistance
Every component in the line offers resistance to the flow when a liquid is forced through a pipe system. In straight pipes, the resistance is due to friction between the liquid and the walls. In bends, additional friction occurs from the liquid having to change direction. In the same way, friction, changes of direction and changes of section result in resistance in fittings, valves and processing equipment. The magnitude of this resistance is relative to the velocity of the liquid in the system. The resistance of each component in the line can be obtained from the resistance coefficient given by the manufacturer. The total resistance of the line can then be calculated by multiplying the sum of the coefficients by the square of the flow velocity and dividing the result by 2 g (g = the acceleration due to gravity = 9.81 m/s 2 ). Example: The product velocity in a pipe system is 1.75 m/s (pipe diameter 2.5" and flow rate 20 000 litres/hour). The sum of the resistance coefficients amounts to 190. The flow resistance will be:

Flow resistance is expressed in terms of the liquid column, or head, needed to compensate for the loss of pressure due to the resistance. This way of reckoning dates back to the original application of pumping, which was to lift water from a low level to a higher level, e.g. from a mine shaft to ground level. The performance of the pump was judged by the height to which it could lift the water. In our case, the total resistance in the pipe system is equivalent to the work done by a pump lifting a liquid 30 metres vertically. This also means that a column of water 30 metres high would exert enough pressure to overcome the flow resistance, as illustrated in Figure 7.9.

Process line illustrating the example with a 30-metre head between tank and process.
Pressure drop
The flow resistance of a liquid in a component results in a loss of pressure. If the pressure is measured with a pressure gauge (Figure 7.10) before and after the component, the pressure will be lower on the discharge side. The component, for instance a shut-off valve, causes a pressure drop in the line. This pressure drop (measured in terms of head) is equivalent to the resistance in the component. The magnitude depends on the velocity, i.e. the flow rate and the size of the pipes.

Pressure drop can be shown by pressure gauges in the process line.
The pressure drop of a component is often stated as the loss of head in metres for different flow rates instead of the resistance coefficient. The graph in Figure 7.11 covers flow rates from 5 000 litres/hour for the smallest pipe diameter, 1.5" (38 mm), to 200 000 litres/hour for the largest, 4" (101.6 mm) shut-off valve. For a flow rate of 20 000 litres/hour and a pipe size of 2.5" (63.5 mm), a velocity of 1.75 m/s, the graph indicates a pressure drop, or loss of head, of 0.4 metre over the fully open valve.
The pressure drop over each of the components in the line for a given flow rate can be determined in the same way. When added together, these values give the total pressure drop for the system. Every component in the line should be dimensioned to cause the lowest possible pressure drop. A pressure drop involves an increase in flow velocity, either in the form of turbulence or by local acceleration through passages. Higher velocities result in increased friction at the surfaces of the pipe and other equipment and greater forces in bends, etc. This increases the mechanical treatment of the product.
In the case of milk, this may lead to breakage of the fat globules, exposing the released fat to attack by lipase enzymes. Eventually, the resulting high content of free fatty acids adversely affects the flavour of the milk. This problem is aggravated if air is present during the mechanical treatment of the product. This can occur if air is sucked in through leaking unions. For other products, such as yoghurt, the treatment of the product must be particularly gentle. The greatest care must be taken in the selection of components as well as in the dimensioning and design of the process line. The size of the pipes in a system must be such that the velocity of the liquid does not exceed the critical value for the product (3 m/s for milk, or slower for some other dairy products). The number of valves in the line should be kept to a minimum and the pressure drops across them should be as low as possible. They should also be placed so that unnecessary changes of direction are avoided.

Pressure-drop graph for a shut-off valve.
Process control equipment
To ensure trouble-free operation of the process and achieve the desired product quality, it is necessary to control quantities such as liquid levels, flows, temperatures, pressures, concentrations and pH values at certain pre-determined levels. The equipment for measuring and controlling these parameters is called instrumentation, which includes various types of sensors, transmitters, actuators and control equipment. A sensor is an element which measures an actual quantity. A transmitter converts the signal from the sensor to a standardized signal. This value is also known as the measured value. Sometimes sensors and transmitters are combined in one measuring device, also called a transmitter, for example a pressure transmitter. Design and functionality vary according to requirements. Examples of measuring devices are temperature, level, pressure and conductivity transmitters. A regulating device is basically an adjusting mechanism, such as a regulating valve or a pump with variable speed, fitted in a process line. The setting of the regulating device, valve plug position or motor speed, determines the amount of the regulated process parameters. A regulator calculates the difference between the measured value and the set value and, based on that difference, adjusts the signal to the regulating device. The regulator setting is correct if the two values are the same. If the measured value changes, the signal from the transmitter changes accordingly. When the measured value does not equal the set value, the regulator adjusts the signal to the regulating device. As a result, the position of the regulating device is adjusted (valve position or speed) to match. The transmitter immediately senses the change in process parameters and transmits this information to the regulator. This cycle of comparison and correction, the control loop, is repeated until the set and measured values match. A control loop is illustrated in Figure 7.12.

Control loop for pressure control, consisting of a transmitter, a regulator and a regulating valve.
Transmitters
Transmitters in control systems vary considerably in design and function. Some transmitters react directly to changes in the measured value. In the pressure transmitter in Figure 7.13, the pressure of the product on a membrane is transferred to the sensor and a transmitter, which gives an electrical signal directly proportional to the product pressure. Most transmitters, however, operate indirectly. They measure the changes in a physical quantity, which has a constant relation to the process parameters to be controlled. This type of transmitter was shown previously in connection with the transport of liquid through the line, where a required flow rate is maintained by controlling the pressure of the product at the pump outlet. The above-mentioned pressure transmitter can also be used to measure the level in a tank. Installed in the bottom of a tank, it senses the static pressure of the liquid column above the diaphragm. This pressure is proportional to the height of the liquid. A signal is transmitted to an instrument, which indicates the level. Many types of transmitters utilize the fact that the electrical resistance of metals varies with temperature in a characteristic manner. One such transmitter is the common temperature transmitter, Figure 7.14.
A wire of platinum is mounted in a protective tube, which is inserted in the line so that it is heated by the liquid. Table 7.1 shows the resistance values of a platinum wire at various temperatures.
Variations in resistance with temperature according to a given characteristic
Resistance Ω | Temperature °C |
---|---|
100.00 | 0 |
103.90 | 10 |
107.79 | 20 |
111.67 | 30 |
115.54 | 40 |
119.40 | 50 |
123.24 | 60 |
130.89 | 80 |
138.50 | 100 |
The resistance can be measured by connecting the metal wire to an electrical circuit. Any change in the resistance will correspond to a given change in temperature, and the temperature of the product can therefore be determined. The transmitters described above are those most often used in dairies. There are, however, many other types available on the market.

Pressure transmitter
- Reference pressure
- Capillary pipe
- Process pressure

Resistance type temperature transmitter

The regulator in Figure 7.15 is the brain of the temperature control system and the controller is available in many different forms. According to a previous definition, a regulator is a device that continuously compares the measured value with a reference or pre-set (set point) value. Any differential causes the regulator to transmit a corrective signal to the regulating unit, which then adjusts its setting accordingly. The corrective process continues until the measured value and the set point value coincide again. The regulator may be a local electronic regulator or built into the control system as a software regulator. On electronic controllers there is a knob for setting the required set point, which is indicated by an indicator on a scale. The measured value, the output from the transmitter, can be read on the scale at all times. There is also a scale showing the output signal to the regulating device. Nowadays, most regulators are based on software in the control system. The regulator is displayed on the operator station as a graphical representation of the electronic regulator, with process value, set point and output signal. These parameters are sometimes also displayed as trend curves, which can assist the operator when working with the regulating system. Some regulators have a switch function, which can be used to produce a signal at a given maximum or minimum value. This signal can be used to perform a change in the process. An example is to re-circulate the flow of a pasteurizer if the temperature at the outlet of the heat exchanger holding section drops below 72 ºC. The switch is set to operate at this temperature and as soon as the temperature drops under this value it will close the solenoid valve controlling the air supply to the flow diversion valve, thereby forcing the pasteurizer to re-circulate the product.
The regulating device

Regulating valve.
A pneumatic regulating valve, shown in Figure 7.16, is built around a body with a seat for the plug, which is attached to the lower end of the regulating stem. The stem is operated between the open and closed positions by differential pressure between the upper and lower sides of the piston. When the pressure is higher on the lower side, the piston moves upwards, lifting the plug from its seat. A higher pressure on top of the piston closes the valve. Actuation is essentially as follows: a pneumatic signal from a controller is supplied to a proportioning device, a positioner, at the top of the valve. The positioner ensures that the position of the plug, in relation to the seat, always is proportional to the regulating signal. When the signal corresponds to the pre-set value, the positioner balances the pressures on either side of the piston so that the position of the plug remains constant. In this balanced condition the pressure drop over the valve is exactly what is required, and the measured value registered by the transmitter coincides with the pre-set value. If the product pressure drops, the transmitter reduces its signal to the regulator. As the measured value now no longer coincides with the pre-set value, the regulator reacts by increasing its signal to the valve actuator. The positioner then increases the pressure on the upper side of the piston, moving the plug towards the seat. The resulting increase in the valve flow resistance increases the product pressure and the reverse cycle of operations is initiated, retarding the downward movement of the piston. When the pressure in the line has reached the pre-set value, the positioner again holds the valve piston in balance.
Do you want to continue reading?
Please enter your details to continue reading the rest of the book of 480 pages essential dairy processing knowledge. Please note that entering your e-mail address here does not mean that you subscribe to any newsletters.
You can also:
Your first visit?
Gain access to the contents of this book by filling out the fields in the form.
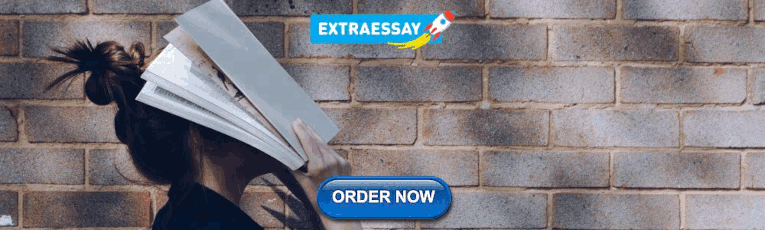
IMAGES
VIDEO
COMMENTS
The total covered area depends on the processes involved, products manufactured, the quantity of milk handled and the equipment chosen product manufacturing. About 4000 sq.ft. area of building is required for handling 10000 liters of milk. The essential sections of a milk processing plant are given in below.
business plan for dairy and dairy processing farm purpose: for finacial lease loan request project name: ***** dairy and dairy processing farm project promoter: ***** project location: agaro town oromia regional state, ethiopia phone: 09***** submitted to: development bank of ethiopia agaro, ethiopia february, 2024 table of contents contents page i. excutive summary iii 1.
This dairy farm business plan demonstrates one path forward for the next generation of Missouri's dairy farmers. This path involves producing milk in Missouri with a 3,500-cow single site dairy, a capital and labor efficient scale. This dairy plan gives Missouri dairy producers a vision of a new scale and style of dairying common in growing ...
Business plan; Project proposal format; New Microsoft Word Document (4) - Copy; ... , 3 Milk Processing plant 400, 4 Refrigerated Vehicle 800, 5 Milking Equipment 220, 6 Office Furniture and Equipment 25, 7 Dairy Heifers 900, 8 Pre-Production Expense 32, Total 2,587, 9 Working Capital 1,471,128. 10 Total Investment Cost 4,058,624. ...
An on-farm processer may transport milk through a pipe from the bulk tank to the plant. A small dairy plant may need a small bulk milk pick-up truck and tank to travel to one or two producers and pick up purchased milk. Work with your inspector to determine the best way to meet your transportation needs.
The following information is about Dairy Processing Plant Project Set up Cost and Profit. Dairy processing around the world is growing rapidly to meet milk and dairy products for an ever-growing population. Dairy processing is an industry that involves harvesting or processing milk from milk-producing animals for human consumption.
these processing plants into major milk producing regions, and the result is a business that is built on extremely narrow profit margins. Small-scale milk processing in Kansas could create many viable marketing opportunities, but barriers to enter into these specialty markets are significant.
Milk Processing Plant Business Idea Description in 5 W's and 1 H Format. According to recent data, the milk processing industry has experienced significant growth in the past decade. In fact, the global market for processed milk products is projected to reach $782.6 billion by 2026.
Bill Thompson Food Manufacturing Administrator Tennessee Department of Agriculture 440 Hogan Road Nashville, TN 37220 Phone: (615) 837-5534 Fax: (615) 837-5335 Email: [email protected]. Eric C. Goan Director Center for Food Processing Extension Specialist Dairy Processing The University of Tennessee Department of Food Science & Technology ...
Resources and tools to develop a business plan. For ag professionals or producers who want to develop a business plan for the dairy operation, this library of resources provides tools that may be useful. The site includes a Business Plan Template, Business Planning Factsheets, a Case Farm example to show how a finished product may look, and a ...
The annual milk production in Tanzania is currently estimated at 1,150 million liters, mainly produced by smallholder farmers of which about 813 million liters (70%) come from indigenous cattle and 337 million liters (30%) from improved dairy cattle. Over 90.5 % of the marketed milk is traded through traditional informal markets; approximately ...
Strategic business planning. is simply a process to help you explicitly develop a . long-term plan. for your business. In many cases, the day-to-day grind of operating a dairy makes it difficult to think about long-term goals unless we make a concerted effort to do so. But this is critical to the sustainability of the business.
%PDF-1.7 %µµµµ 1 0 obj >/Metadata 1511 0 R/ViewerPreferences 1512 0 R>> endobj 2 0 obj > endobj 3 0 obj >/ExtGState >/XObject >/ProcSet[/PDF/Text/ImageB/ImageC ...
This document provides a proposal for a dairy farm and milk processing plant project in Addis Ababa, Ethiopia. The project will be located in Akaki Kaliti woreda and owned by Worku Abuhay. It will require 20,000 square meters of land and an initial investment of 150 million Ethiopian birr to establish dairy farming operations, milk processing facilities, and oilseed processing. The project ...
established a dairy processing plant in August 2013 after receiving a loan worth 2.4 million Birr ($104,575 USD) from the Commercial Bank of Ethiopia, which enabled Hirut to purchase ... BUSINESS PLAN DEVELOPMENT The SAFE team worked with Rut & Hirut to create a business plan which outlines the company's vision, mission and strategic
Diary & milk processing project proposal - Free download as Word Doc (.doc), PDF File (.pdf), Text File (.txt) or read online for free. The document is a loan appraisal report for Misale Dairy Farming & Processing PLC, which plans to establish a dairy farm and milk processing plant in Ethiopia. Key points include: - The project will be located 103km from Addis Ababa and will have year-round ...
Milk Ball cooperative will work with smallholder dairy producer in Rwanda in procurement of adequate amount of quality milk for the Friesland Campina proposed dairy processing plant. In addition, this document gives the details of the requirements of the proposed Dairy processing plant business idea and an insight of the Rwandan dairy value chain.
ABOUT MELKAM ENDALE DAIRY FARM AND MILK PROCESSING Melkam Endale Dairy Farm and Milk Processing (MEDFMP) began as a dairy farm on 2.7 hectares outside Addis Ababa. When founder Melkam Endale decided to turn the business into a commercial dairy processor in 2017, it became clear that MEDFMP would need to find additional sources of raw milk ...
This business plan proposes establishing a dairy farm and dairy processing facility in Agaro Town, Ethiopia. The plan requests financial lease funding and outlines a project to establish a 60,000 square meter farm with infrastructure to house 35 dairy cows and produce milk and milk products. It presents market analysis showing demand for dairy in the region. The plan estimates total initial ...
In the dairy, raw milk passes through several stages of treatment in various types of processing equipment before reaching the consumer in the form of a finished, refined product. Production usually takes place continuously in a closed process, where the main components are connected by a system of pipes. The type of treatment involved and the ...
Dairy Plan Phase-I (NDP-I) in February, 2012 with a total investment of about Rs.2242 crore to be implemented from 2011-12 to 2016-17. ... The milk processing plant shall have the following essential facilities. i) Raw Milk Reception Dock (RMRD) - consisting of can conveyor, can washer, weighing balance, dump tank etc.
This proposal is for a dairy farm and milk processing plant in Akaki woreda Town, Ethiopia. The project will require 20,000 square meters of land and a startup capital of 150 million Ethiopian birr to establish dairy farming operations, a milk processing facility, and produce dairy products. It is expected to employ 320 people and be an important source of income for the regional government ...
This document provides a business plan for Tahir Kasim's proposed dairy farm in Agaro, Ethiopia. The plan outlines that the farm will have 8 crossbreed cows producing an average of 26,880 liters of milk per year to sell locally. The target customers are local cafes and consumers in Agaro town. The financial projections estimate that the dairy farm will be profitable and have positive cash ...