Academia.edu no longer supports Internet Explorer.
To browse Academia.edu and the wider internet faster and more securely, please take a few seconds to upgrade your browser .
Enter the email address you signed up with and we'll email you a reset link.
- We're Hiring!
- Help Center
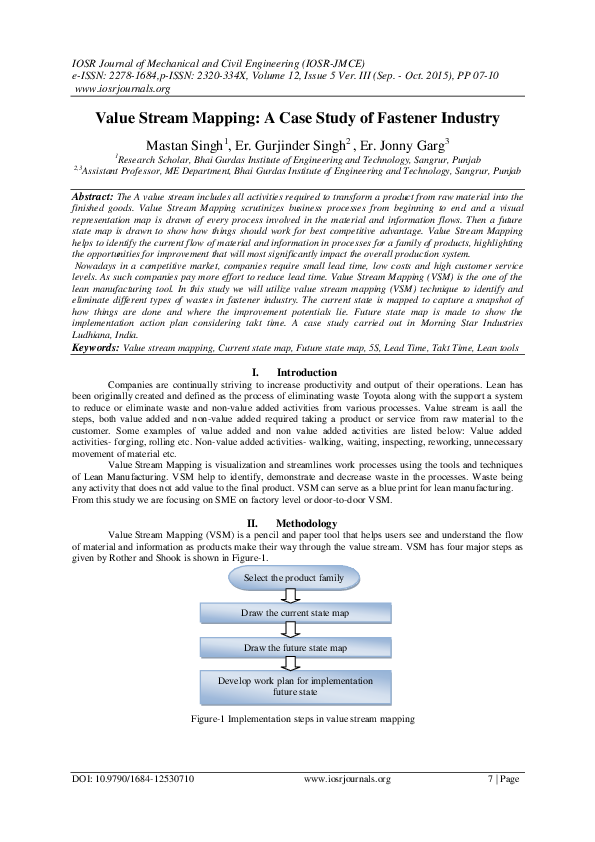
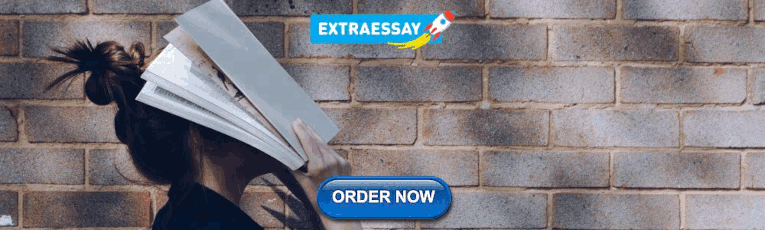
Value Stream Mapping: A Case Study of Automotive Industry

2014, International Journal of Research in Engineering and Technology
Related Papers
IOSR Journals
The A value stream includes all activities required to transform a product from raw material into the finished goods. Value Stream Mapping scrutinizes business processes from beginning to end and a visual representation map is drawn of every process involved in the material and information flows. Then a future state map is drawn to show how things should work for best competitive advantage. Value Stream Mapping helps to identify the current flow of material and information in processes for a family of products, highlighting the opportunities for improvement that will most significantly impact the overall production system. Nowadays in a competitive market, companies require small lead time, low costs and high customer service levels. As such companies pay more effort to reduce lead time. Value Stream Mapping (VSM) is the one of the lean manufacturing tool. In this study we will utilize value stream mapping (VSM) technique to identify and eliminate different types of wastes in fastener industry. The current state is mapped to capture a snapshot of how things are done and where the improvement potentials lie. Future state map is made to show the implementation action plan considering takt time. A case study carried out in Morning Star Industries Ludhiana, India.
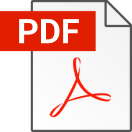
IOSR Journals publish within 3 days
Bus body manufacturing play a key role in automotive manufacturing, as vehicle manufacturers often sub contract such enterprise to complete bus manufacturing process. In a fiercely competitive global environment, the bus body manufacturing enterprises are constantly looking for ways of meet their customer requirements of delivery on time, cost and quality in order for them to survive. However, bus body manufacturing enterprises barely meet the customer demands in terms of delivering on time due to long cycle times on the production floor due to low labour utilization, material wastage and unorganized work flows. In this research, we critically looked at improving productivity such enterprises by considering a case study of one of the leading bus body manufacturing enterprises in Kenya. Value Stream Mapping was used as the main productivity improvement tool supported by line balancing techniques. The results from the improved value stream map indicated an increase in efficiency of 13.1% and a reduction the cycle time by 7 days, demonstrating the potential of these tools for improving productivity in bus body manufacturing.
ICSESD-2017
Pranav Charkha
International Journal of Scientific Research in Science and Technology IJSRST
Today, Lean manufacturing Tools and Techniques are widely used for eliminating various kinds of waste and increase profit of organization by making process more efficient. Lean is about doing additional with less: Less time, inventory, space, people, and money. Lean is about speed and obtaining it right the first time. The Lean manufacturing approach is meant to transform non-value added activity into value added activity. Lean manufacturing has its impact on the employees and also the customers alike. A lean organization understands customer value and focuses its key processes to continuously increase it. The ultimate goal is to produce perfect value to the customer through an ideal value creation methodology that has zero waste. This paper provides the literature survey on lean tools and lean implementation technique of implementing lean manufacturing.
Duong Huong
In Bangladesh a significant amount of foreign currency comes from the RMG sector. Garment industries in developing countries are more focused on sourcing of raw material and minimizing delivery cost than labor productivity because of the availability of cheap labor. Due to this, labor productivity is lower in developing countries than in the developed ones. So productivity improvement is one of the major concern in garments factories. This paper addresses the scope of value stream mapping (VSM) application in a selected garments factory of Bangladesh. The core idea behind the thesis work was to examine the existing condition of production system where there is no application of VSM technique and to analyze the scope of VSM technique application in the studied production line. The main objective of the research paper is to identify various wastes occurs in the production system. Additionally it tries to find out some areas for improvement and propose some improvement strategies. In this concern this case study has been conducted focusing cutting, finishing and on a particular production line of sewing section in a selected garments factory. During the investigation, attention has been concentrated how non-value adding activity hampers daily production rate and how to improve the productivity. Value adding, non-value adding (necessary and unnecessary) processes and different types of wastes have been identified by drawing the current state map for cutting, sewing and finishing sections. The study focuses on removing the big losses namely, breakdown losses, quality loss, small stops, startup rejects to improve the effectiveness of the production line. Some strategies are proposed for reducing these losses and improving the overall productivity. It is found that the non-value adding time has contributed significantly in total production lead time. Finally, a future state map has been proposed to the management that will be benefited for productivity improvement of the existing production system as well as to reduce the non-value adding time. 1. Introduction In Bangladesh, the Ready Made Garment (RMG) Industry has emerged as a major economic sector and has had its impact on the financial service sector, communication, transportation and on other related industries. 2 million workers in 4,000 factories, which is about one-fourth of the number of employees engaged in the manufacturing sector, constitute the real backbone of the country's economy [1]. Garment industries in developing countries are more focused on sourcing of raw material and minimizing delivery cost than labor productivity because of the availability of cheap labor. Due to this, labor productivity is lower in developing countries than in the developed ones. For example, labor is very cheap in Bangladesh but the productivity is low among other developing countries. Similarly, the cost of fabric is a major part of the garment so there seems to be great need for improvement in this sector. Even in developing countries the CAD and CAM system for fabric cutting has been implemented to save fabric. Now the worry is about labor productivity and making production flexible. The fashion industry is highly volatile and if the orders are not fulfilled on time, the fear for losing business is real. This means that time is very important driver for success. The Company that delivers goods with a shorter lead time is the market winner. This can be achieved greatly by adopting lean manufacturing system which is more than a cost reduction program. It aims at eliminating wastes which could be in the form of excess production and inventory, redundant movement of material, waiting and delays, over processing, excess worker motion, rework and corrections. Part of lean manufacturing is assessing operations and processes or products that add cost rather than value. Each step of the manufacturing process is examined to determine if it adds value to the product. If it does not add value, the process could be assigned to a subcontractor or outsourcing company in order to focus the workforce on value-added operations of its core business. This is known as value stream which is a set of processes required to transform raw materials into finished goods that customer's value. In this research work, the scope of one of the most important Lean Manufacturing tool called " Value Stream Mapping " will be evaluated in a selected garments factory
IAEME PUBLICATION
IAEME Publication
Purpose: The purpose of this paper is to implement lean to determine and eliminate various wastes with the help of Value Stream Mapping. It aims at representing a Current and Future State Maps to give overview of improved areas in waste and resource management in Indian Manufacturing Firm. By the detailed study processes involved in industry, the existing stages have been mapped with the help of Value Stream Mapping. After which improvement related areas are identified like cycle time, production lead time etc. Considering the current processes of the industries operations Current State map is developed to show how actual production is taking place at the industry before implementing any lean procedure. A Future State Map is finally developed considering the lean behavior to reduce the waste production and to increase its productivity. After a thorough comparison between Current and Future State Map of the Indian Manufacturing Firm a 78.8% decrease production lead time was investigated, followed by 28.4% reduction in cycle time. Also a significant decrease in WIP and manpower requirements was observed. This case study presents VSM as a robust tool for implementing lean and to give proper insight to industry managers and researchers to know techniques of improving lean implementation.
International Journal of Engineering Research and General Science
Chowdhury Rahman , Mostafizur Rahman Sobuj
In Bangladesh a significant amount of foreign currency comes from the RMG sector. Garment industries in developing countries are more focused on sourcing of raw material and minimizing delivery cost than labor productivity because of the availability of cheap labor. Due to this, labor productivity is lower in developing countries than in the developed ones. So productivity improvement is one of the major concern in garments factories. This paper addresses the scope of value stream mapping (VSM) application in a selected garments factory of Bangladesh. The core idea behind the thesis work was to examine the existing condition of production system where there is no application of VSM technique and to analyze the scope of VSM technique application in the studied production line. The main objective of the research paper is to identify various wastes occurs in the production system. Additionally it tries to find out some areas for improvement and propose some improvement strategies. In this concern this case study has been conducted focusing cutting, finishing and on a particular production line of sewing section in a selected garments factory. During the investigation, attention has been concentrated how non- value adding activity hampers daily production rate and how to improve the productivity. Value adding, non-value adding (necessary and unnecessary) processes and different types of wastes have been identified by drawing the current state map for cutting, sewing and finishing sections. The study focuses on removing the big losses namely, breakdown losses, quality loss, small stops, startup rejects to improve the effectiveness of the production line. Some strategies are proposed for reducing these losses and improving the overall productivity. It is found that the non-value adding time has contributed significantly in total production lead time. Finally, a future state map has been proposed to the management that will be benefited for productivity improvement of the existing production system as well as to reduce the non-value adding time.
International Journal of Productivity and Quality Management
Rajarajanramji Mohanraj
International Journal of Latest Technology in Engineering, Management & Applied Science -IJLTEMAS (www.ijltemas.in)
For any Company's economy, the industry cost, production time, total quality management and waste reduction have great impact. The investments consumed by the company by eradicating non value added production work and time are very important. Focusing on these points Lean Manufacturing tools, a Japanese strategy, is implemented in this work. An apparel industry was studied and the bottleneck areas were identified through Value Stream Mapping (VSM). The bottleneck areas were identified and eliminated by implementing line balancing and parallel working section. The implementation of kaizen resulted in reduction of cycle time by 48.7%.
International Journal of Engineering Research and Technology (IJERT)
IJERT Journal
https://www.ijert.org/lead-time-reduction-in-windmill-control-panel-manufacturing https://www.ijert.org/research/lead-time-reduction-in-windmill-control-panel-manufacturing-IJERTCONV7IS06072.pdf The prime purpose is to reduce the lead time of windmill control panel manufacturing by implementing lean manufacturing by the use of lean tools to achieve the takt time in electrical control panel assembly line. The ''lean'' approach has been applied more frequently in automobile assembly and machine tool building then in electrical control panel manufacturing company. The lean system was developed with reduced non value added activities so that greatly reduces the seven Mudas. People work with a greater confidence, with greater ease, and with greater peace than the typical manufacturing facility. Value stream mapping and line balancing was the main tool used to identify the opportunities for various lean techniques. We described a simulation model that was developed to contrast the ''current'' and ''Future'' scenarios in detail, in order to illustrate the potential benefits such as reduced production lead-time and lower work-in-process inventory. Work instructions is displayed in all the assembly stations also improved the performance of the line workers.
RELATED PAPERS
Dr. N D Chauhan
American Journal of Engineering and Technology Management
mauton gbededo
bagus kurniawan
International Journal of Trend in Scientific Research and Development (IJTSRD)
Kiran Kumar G K
Ritesh Bhat
International Journal of Lean Enterprise Research
Prof. Vikas Kumar
international journal for research in applied science and engineering technology ijraset
IJRASET Publication
International Journal of …
Dr. Farzad Tahriri
Praveen Saraswat
Pratik Kikani
IJRAME Journal
Asia Pacific Journal of Multidisciplinary Research
Research and Statistics Center
Tonny Rosado
IEEE Access
deepthi m r
Azhar Sohail
International Journal of Production Economics
Fawaz Abdulmalek
AK'Aphisak Kraart
IJESMR Journal
THE IJES Editor
RSIS International
MIMBAR : Jurnal Sosial dan Pembangunan
Ajeng Pratiwi
Jurnal Teknologi
Jafri Rohani
African Journal of …
Yusof Ismail
Grey Systems: Theory and Application
Robisom Calado
ijetrm journal
Ijetrm Journal
Muhammad Farid Shaari
Antony Pearce
2021 IEEE 8th International Conference on Industrial Engineering and Applications
Nattapong Kongprasert
International Journal of Recent Technology and Engineering
Prof. Shiva Prasad H C
IJSTE - International Journal of Science Technology and Engineering
RELATED TOPICS
- We're Hiring!
- Help Center
- Find new research papers in:
- Health Sciences
- Earth Sciences
- Cognitive Science
- Mathematics
- Computer Science
- Academia ©2024
Value stream mapping and lean simulation: a case study in automotive company
- ORIGINAL ARTICLE
- Published: 19 October 2015
- Volume 85 , pages 547–555, ( 2016 )
Cite this article
- P. F. Andrade 1 ,
- V. G. Pereira 1 &
- E. G. Del Conte 1
1907 Accesses
42 Citations
Explore all metrics
This work aims at applying the concepts of value stream mapping (VSM) in an auto-parts company in the ABC region of Sao Paulo. By mapping the current state of art, it was possible to identify the waste present in an assembly line of clutch discs. The future state was suggested with improvements for elimination of waste and reduction of lead time, which went from 60.5 to 4.14 days. Simulations were made using current and future states to support the suggested improvements, and reduction of 7 % in total production time was verified, as well as 10 % increase in the use of work positions. The results showed that VSM combined with simulation is a good alternative in the decision-making for change in production process.
This is a preview of subscription content, log in via an institution to check access.
Access this article
Price includes VAT (Russian Federation)
Instant access to the full article PDF.
Rent this article via DeepDyve
Institutional subscriptions
Similar content being viewed by others
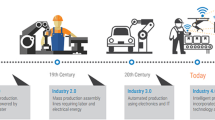
Literature review of Industry 4.0 and related technologies
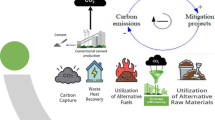
Carbon emissions mitigation methods for cement industry using a systems dynamics model
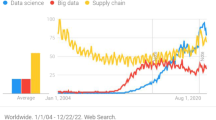
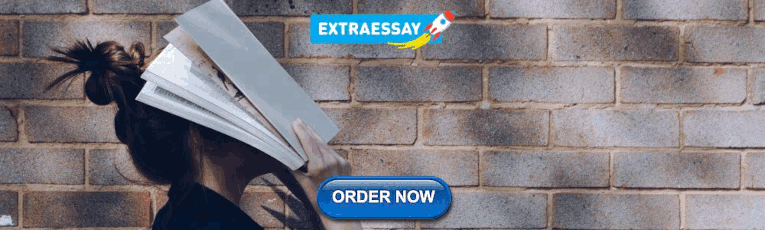
Data science and big data analytics: a systematic review of methodologies used in the supply chain and logistics research
Liker JK (2005) O Modelo Toyota: 14 principios de gestão do maior fabricante do mundo. Bookman, Porto Alegre
Google Scholar
Rother M, Shook J (2003) Aprendendo a Enxergar: mapeando o fluxo de valor para agregar valor e eliminar o desperdício. Lean Institute Brasil, São Paulo
Lustosa L, Mesquita MA, Quelhas O, Oliveira R (2008) Planejamento e controle da Produção. Elsevier, Rio de Janeiro
Nash MA, Poling SR (2008) Mapping the total value stream. CRC Press, New York
Abdulmalek FA, Rajgopal J (2007) Analyzing the benefits of lean manufacturing and value stream mapping via simulation: a process sector case study. Int J Prod Econ 107:223–236
Article Google Scholar
Anand G, Kodali R (2009) Simulation model for the design of lean manufacturing systems—a case study. Int J Product and Qual Manag 4(5–6):691–714
Womack Jp, Jones DT (2003) A Mentalidade Enxuta nas empresas: elimine o desperdício e crie riqueza 9th ed. Campus, Rio de Janeiro
Shank JK, Govindarajan V (1993) Strategic cost management: the new tool for competitive advantage. The Free Press, New York
Belokar Rm, Kumar V; Kharb SS (2012) An application of value stream mapping in automotive industry: a case study. International Journal of Innovative Technology and Exploring Engineering (IJITEE) Vol 1 No 2.
Rajakumar S, Arunachalan VP, Selladurai V (2005) Simulation of workflow balancing in assembly shopfloor operations. J Manuf Technol Manag 16(3):265–281
Mönch L (2007) Simulation-based benchmarking of production control schemes for complex manufacturing systems. Control Eng Pract 15(11):1381–1393
Freitas Filho PJ (2008) Introdução à modelagem e simulação de sistemas com aplicações em arena 2. Visual Books, Florianópolis
Donatelli A, Harris G (2004) Combining value stream mapping and discrete event simulation, in Proceedings of the Huntsville Simulation Conference. Society for Modeling and Simulation International, San Diego, CA
McDonald T, VAN Aken EM, Rentes AF (2002) Utilizing simulation to enhance value stream mapping: a manufacturing case application. Int J Logist: Res and Appl 5(2):213–232
Mohamed AS, Khaled SE, Aziz EE (2011) Value stream map simulator using ExtendSim. Proceedings of the World Congress on Engineering, London
Rajenthirakumar D et al. (2012) Lean manufacturing: a study of application in a customary atmosphere. International Journal of Lean Thinking. pp. 20–35.
Lian YH, Landeghem HV (2002) An application of simulation and value stream mapping in lean manufacturing. In: Proceedings 14th European Simulation Symposium, pp 1–8.
Ohno T (1988) Just-in-time for today and tomorrow. Productivity Press.
Download references
Author information
Authors and affiliations.
Centro de Engenharia, Modelagem e Ciências Sociais Aplicadas (CECS), Universidade Federal do ABC, Santo André, Brazil
P. F. Andrade, V. G. Pereira & E. G. Del Conte
You can also search for this author in PubMed Google Scholar
Corresponding author
Correspondence to E. G. Del Conte .
Rights and permissions
Reprints and permissions
About this article
Andrade, P.F., Pereira, V.G. & Del Conte, E.G. Value stream mapping and lean simulation: a case study in automotive company. Int J Adv Manuf Technol 85 , 547–555 (2016). https://doi.org/10.1007/s00170-015-7972-7
Download citation
Received : 11 July 2015
Accepted : 12 October 2015
Published : 19 October 2015
Issue Date : July 2016
DOI : https://doi.org/10.1007/s00170-015-7972-7
Share this article
Anyone you share the following link with will be able to read this content:
Sorry, a shareable link is not currently available for this article.
Provided by the Springer Nature SharedIt content-sharing initiative
- Value stream mapping
- Lean production
- Find a journal
- Publish with us
- Track your research
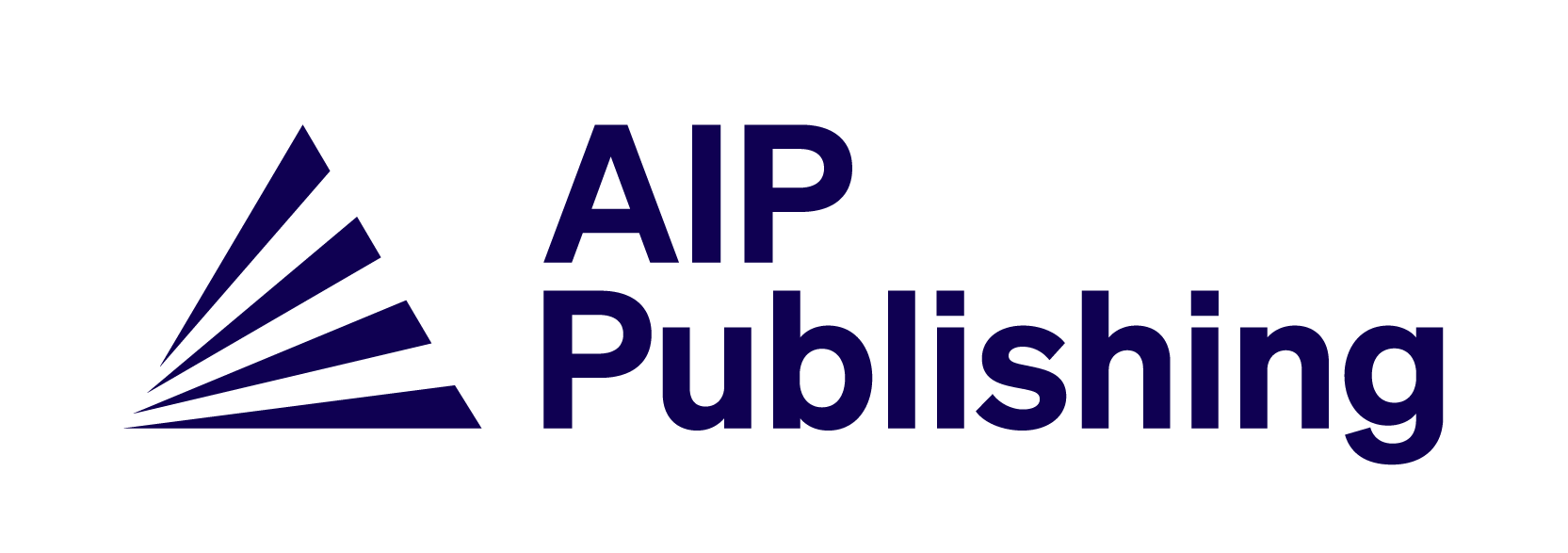
- Previous Article
- Next Article
Value stream mapping: A case study of lock industry
- Article contents
- Figures & tables
- Supplementary Data
- Peer Review
- Reprints and Permissions
- Cite Icon Cite
- Search Site
Pradip A. Parab , Vinay A. Shirodkar; Value stream mapping: A case study of lock industry. AIP Conf. Proc. 3 September 2019; 2148 (1): 030041. https://doi.org/10.1063/1.5123963
Download citation file:
- Ris (Zotero)
- Reference Manager
Value Stream Mapping (VSM) is a useful tool to see hidden wastes and sources of these wastes in a manufacturing facility, primarily for discerning between activities that adds value to the process and activities that do not. It is one of the key lean tools used to identify opportunities for eliminating non-value adding activities, reducing production lead time and lowering work-in-process (WIP) inventory. This paper demonstrates a case study of VSM application at a special purpose lock manufacturing facility. A current state map is drawn to document how processes are operated on production floor. Through aggressive application of process improvement techniques, a future state map is developed to design a lean process flow by eliminating wasteful activities. In a major overhaul of activities, the existing process layout riddled with excessive inter-station travels was changed to an effective and cost efficient product layout. In addition, lean tools like 3G, Kaizen and 5S were implemented for better utilization of manufacturing facilities. The outcome was seen in the drastic reduction achieved in production lead time and WIP inventory. Production lead time and WIP inventory decreased by 62.74% and 66.09% respectively. Furthermore, rejection levels and unwanted travels were drastically reduced.
Sign in via your Institution
Citing articles via, publish with us - request a quote.
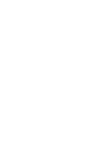
Sign up for alerts
- Online ISSN 1551-7616
- Print ISSN 0094-243X
- For Researchers
- For Librarians
- For Advertisers
- Our Publishing Partners
- Physics Today
- Conference Proceedings
- Special Topics
pubs.aip.org
- Privacy Policy
- Terms of Use
Connect with AIP Publishing
This feature is available to subscribers only.
Sign In or Create an Account
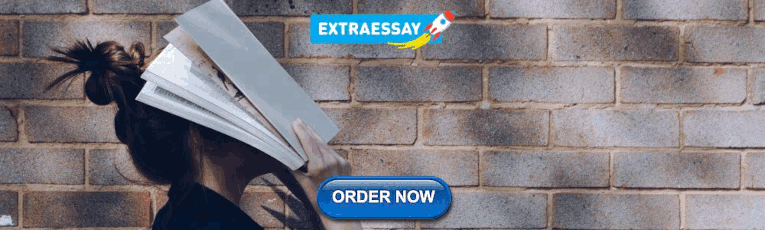
IMAGES
VIDEO
COMMENTS
PDF | On Jan 1, 2022, Jagdeep Singh and others published Productivity improvement using value stream mapping and simulation - case studies | Find, read and cite all the research you need on ...
mapping in automotive industry. Value Stream mapping aim is identified waste in terms of non-value added activities. Current State Map is prepared to give details about the existing position and identify various problem areas. Future State Map is made to show the implementation action plan. A case study carried out in Lear Corporation Halol ...
techniques called Value Stream Mapping (VSM) to improve the processes in an automotive industry. 2. Literature review Palak P. Sheth, Vivek A. Deshpande, Hiren R. Kardani(2014) in their work on value stream mapping in an automotive firm, executed the VSM method effectively in the industry. The case study was basically
Value Stream Map-ping provides the clarity and step-by-step guidance that is sorely needed to help Lean practitioners and leaders in the ofice. The experience and relevance they provide will make this the latest well-thumbed and often-referenced guide to enterprise value stream mapping.".
Value Stream Mapping: A Case Study Of Fastener Industry DOI: 10.9790/1684-12530710 www.iosrjournals.org 8 | Page In order to draw value stream map following strategies applied: 1. Obtained information from company 2. Conducted time studies 3. Data collected from shop floor observation. 4. E-draw Max version 7.9.4 software is used to draw ...
This paper presents a case study that describes the use of Value Stream Mapping (VSM) in the production of steel pipes. Relevant data from this process were collected and analyzed at the start of the project. An initial process was mapped, associated waste was identified, and then future processes were mapped.
Value Stream Mapping: A Case Study of Fastener Industry. IOSR Journals. The A value stream includes all activities required to transform a product from raw material into the finished goods. Value Stream Mapping scrutinizes business processes from beginning to end and a visual representation map is drawn of every process involved in the material ...
This study provides an up-to-date, review of value stream mapping. A systematic methodology is presented in this paper for selecting product family and processes for improvements. A current state map is developed after critical observations, calculations, and analysis for identifying wastes in current system.
ORIGINAL ARTICLE. Value stream mapping and lean simulation: a case study in automotive company. P. F. Andrade1&V. G. Pereira1&E. G. Del Conte1. Received: 11 July 2015/Accepted: 12 October 2015/Published online: 19 October 2015 # Springer-Verlag London 2015. Abstract This work aims at applying the concepts of value streammapping(VSM)inanauto ...
Modelling and Simulation the Value Stream Mapping - Case Study. The case study carried out under this article aims to highlight the importance of combining simple Lean Production tools with software with software in testing, testing, and designing alternative solutions for the needs of digitization of business processes in the future. Expand.
This paper explores the concept of Value Stream Analysis and Mapping (VSA/M) as applied to Product Development (PD) efforts. Value Stream Analysis and Mapping is a method of business process improvement. The application of VSA/M began in the manufacturing community. PD efforts provide a different setting for the use of VSA/M. Site
View PDF; Download full issue; Search ScienceDirect ... Production efficiency improvement in batch production system using value stream mapping and simulation: a case study of the roasted and ground coffee industry, In Production planning and control, 2014, Volume: 25 Issue: 5 Pages: 425-446, ISSN: 0953-7287. ... Learning to see: value-stream ...
This article describes the application of value stream mapping to analyze and redesign the way of managing the materials procurement stage of a project. A framework based on integrated definition (IDEF) methodology, the stream analysis approach, activity-based costing, and discrete event simulation is presented.
Mapping the value stream always starts with the customer demand. To create Current Value stream map these following step are followed-. Step I- Calculate takt time: Takt time for this process is 4.83 min. Step II- Understand Customer Demand: Customer demand is monthly or daily demand of customer as per need.
View PDF; Download full issue; Search ScienceDirect. Procedia Engineering. Volume 41, 2012, Pages 1727-1734. Production Flow Analysis through Value Stream Mapping: A Lean Manufacturing Process Case Study ... 2007, Analyzing the benefits of lean manufacturing and value stream mapping via simulation: A process sector case study, Int. J ...
This thesis proposes to use Value Stream Mapping as an implementation technique for SMEs. This technique is tested in a company as a case study. By applying the Value Stream Mapping tool to a specific process within this company, substantial improvement potential is revealed.
DOI: 10.5505/PAJES.2016.59251 Corpus ID: 115526410; Value stream mapping and simulation for lean manufacturing: A case study in furniture industry @article{Goren2017ValueSM, title={Value stream mapping and simulation for lean manufacturing: A case study in furniture industry}, author={Hacer Guner Goren}, journal={Pamukkale University Journal of Engineering Sciences}, year={2017}, volume={23 ...
Value Stream Mapping as a Lean Construction Tool - a Case Study. Abstract— Low productivity is the chronic problem in construction industry. One way to increase the productivity is to reduce non-value adding activities. Productivity improvements achieve higher cost savings with minimal investment. This paper describes the concepts of value ...
Value Stream Mapping (VSM) is a popular and easy tool for visualizing production processes in enterprise. It allows one to eliminate or reduce waste, i.e., activities that do not create added value for the customer. The versatility of this tool allows it to be used in industry. There are theoretical, methodological, and practical aspects encountered by practitioners in developing Value Stream ...
Value Stream Mapping (VSM) is a useful tool to see hidden wastes and sources of these wastes in a manufacturing facility, primarily for discerning between activities that adds value to the process and activities that do not. It is one of the key lean tools used to identify opportunities for eliminating non-value adding activities, reducing ...