Hydroelectric Energy: The Power of Running Water
Hydroelectric energy is power made by moving water. “Hydro” comes from the Greek word for water.
Engineering, Geography, Social Studies, World History
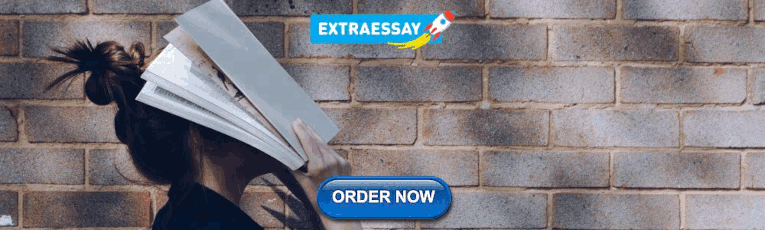
Loading ...

Hydroelectric energy is made by moving water. Hydro comes from the Greek word for water. Hydroelectric energy has been in use for thousands of years. Ancient Romans built turbines , which are wheels turned by flowing water. Roman turbines were not used for electricity , but for grinding grains to make flour and breads. Water mills provide another source of hydroelectric energy. Water mills, which were common until the Industrial Revolution , are large wheels usually located on the banks of moderately flowing rivers . Water mills generate energy that powers such diverse activities as grinding grain, cutting lumber , or creating hot fires to create steel . The first U.S. hydroelectric power plant was built on the Fox River in 1882 in Appleton, Wisconsin. This plant powered two paper mills and one home. Harnessing Hydroelectricity To harness energy from flowing water, the water must be controlled. A large reservoir is created, usually by damming a river to create an artificial lake, or reservoir. Water is channeled through tunnels in the dam. The energy of water flowing through the dam's tunnels causes turbines to turn. The turbines make generators move. Generators are machines that produce electricity. Engineers control the amount of water let through the dam. The process used to control this flow of water is called the intake system . When a lot of energy is needed, most of the tunnels to the turbines are open, and millions of gallons of water flow through them. When less energy is needed, engineers slow down the intake system by closing some of the tunnels. During floods , the intake system is helped by a spillway . A spillway is a structure that allows water to flow directly into the river or other body of water below the dam, bypassing all tunnels, turbines, and generators. Spillways prevent the dam and the community from being damaged. Spillways, which look like long ramps, are empty and dry most of the time. From Water Currents to Electrical Currents Large, fast-flowing rivers produce the most hydroelectricity. The Columbia River, which forms part of the border between the U.S. states of Washington and Oregon, is a big river that produces massive amounts of hydroelectric energy. The Bonneville Dam , one of many dams on the Columbia River, has 20 turbines and generates more than a million watts of power every year. Thats enough energy to power hundreds of thousands of homes and businesses. Hydroelectric power plants near waterfalls can create huge amounts of energy, too. Water crashing over the fall line is full of energy. A famous example of this is the hydroelectric plant at Niagara Falls, which spans the border between the United States and Canada. Hydroelectric energy generated by Niagara Falls is split between the U.S. state of New York and the Canadian province of Ontario. Engineers at Niagara Falls cannot turn the falls off, but they can severely limit the intake and control the amount of water rushing over the waterfall. The largest hydroelectric power plant in the world is the enormous Three Gorges Dam , which spans the Yangtze River in China. It is 185 meters (607 feet) tall and 115 meters (377 feet) thick at its base. It has 32 turbines and is able to generate more than two billion watts of power. Hydroelectric Energy and the Environment Hydroelectricity relies on water, which is a clean, renewable energy source. A renewable source of energy is one that will not run out. Renewable energy comes from natural sources, like wind , sunlight , rain, tides , and geothermal energy (the heat produced inside Earth). Nonrenewable energy sources include coal , oil , and natural gas . Water is renewable because the water cycle is continually recycling itself. Water evaporates , forms clouds , and then rains down on Earth, starting the cycle again.
Reservoirs created by dams can provide large, safe recreational space for a community. Boaters and water skiers can enjoy the lake. Many reservoirs are also stocked with fish. The area around a reservoir is often a protected natural space, allowing campers and hikers to enjoy the natural environment. Using water as a source of energy is generally a safe environmental choice. Its not perfect, though. Hydroelectric power plants require a dam and a reservoir. These artificial structures may be obstacles for fish trying to swim upstream . Some dams, including the Bonneville Dam, have installed fish ladders to help fish migrate . Fish ladders are a series of wide steps built on the side of the river and dam. The ladder allows fish to slowly swim upstream instead of being totally blocked by the dam. Dams flood river banks, destroying wetland habitat for thousands of organisms . Aquatic birds such as cranes and ducks are often at risk, as well as plants that depend on the marshy habitat of a riverbank. Operating the power plant may also raise the temperature of the water in the reservoir. Plants and animals near the dam have to adjust to this change or migrate elsewhere. The O'Shaughnessy Dam on the Tuolumne River in the U.S. state of California was one of the first hydroelectric energy projects to draw widespread criticism for its impact on the environment. The dam, constructed in 1913, flooded a region called Hetch Hetchy Valley, part of Yosemite National Park. (The lake created by the O'Shaughnessy Dam is called the Hetch Hetchy Reservoir.) Environmental coalitions opposed the dam, citing the destruction of the environment and the habitats it provided. However, the power plant provided affordable hydroelectric energy to the booming urban area around San Francisco. The Hetch Hetchy Reservoir is still a controversial project. Many people believe the O'Shaughnessy Dam should be destroyed and the valley returned to its native habitat. Others contend that destroying a source of energy for such a major urban area would reduce the quality of life for residents of the Bay Area . There are limits to the amount of hydroelectric energy a dam can provide. The most limiting factor is silt that builds up on the reservoir's bed. This silt is carried by the flowing river, but prevented from reaching its normal destination in a delta or river mouth by the dam. Hundreds of meters of silt build up on the bottom of the reservoir, reducing the amount of water in the facility. Less water means less powerful energy to flow through the systems turbines. Most dams must spend a considerable amount of money to avoid silt build-up, a process called siltation . Some power plants can only provide electricity for 20 or 30 years because of siltation. Hydroelectric Energy and People Billions of people depend on hydroelectricity every day. It powers homes, offices, factories, hospitals, and schools. Hydroelectric energy is usually one of the first methods a country uses to bring affordable electricity to rural areas . Hydroelectricity helps improve the hygiene , education, and employment opportunities available to a community. China and India, for instance, have built dozens of dams recently, as they have quickly industrialized. The United States depended on hydroelectric energy to bring electricity to many rural or poor areas. Most of this construction took place during the 1930s. Dams were a huge part of the New Deal , a series of government programs that put people to work and brought electricity to millions of its citizens during the Great Depression . The Bonneville Dam on the Columbia River, the Shasta Dam on the Sacramento River, and the Hoover Dam on the Colorado River are some dams constructed as part of the New Deal. The most famous hydroelectric power project of the New Deal is probably the Tennessee Valley Authority (TVA) . The TVA constructed a series of dams along the Tennessee River and its tributaries. Today, the TVA is the largest public power company in the U.S., providing affordable electricity for residents in the states of Alabama, Georgia, Kentucky, Mississippi, North Carolina, Tennessee, and Virginia. However, hydroelectricity often comes at a human cost. The huge dams required for hydroelectric energy projects create reservoirs that flood entire valleys. Homes, communities, and towns may be relocated as dam construction begins. Egypt began construction of the Aswan Dam complex on the Nile River in 1960. Engineers realized that ancient temples of Abu Simbel were going to be flooded by the reservoir, called Lake Nasser. These monuments were built directly into cliffs several stories tall. The Abu Simbel temples are a part of Egypt's cultural heritage and a major tourist destination. Rather than have the monuments flooded, the government of Egypt relocated the entire mountainside to an artificial hill nearby. Today, Abu Simbel sits above the Aswan Dam. China's massive Three Gorges Dam project brings safe, affordable electricity to millions of people. It allows hospitals, schools, and factories to work longer, more reliable hours. It also allows people to maintain healthier lifestyles by providing clean water. Construction of the dam directly benefited workers, too. More than a quarter of a million people have found work with the project. However, the project has forced more than a million people to relocate. Lifestyles were disrupted. Many families were relocated from rural towns on the banks of the Yangtze River to Chongqing, a major urban area with 31 million residents. Other people were relocated out of the province entirely.
Hoover Dam The Hoover Dam was built during the Great Depression, a period when most people had little money and jobs were very scarce. Building the dam seemed like an impossible task. Many people said it could not be built. Workers labored long, hard days for two years, building tunnels that are 15 meters (50 feet) wide, big enough to fit a commercial airplane without its wings. The Hoover Dam is 221 meters (726 feet) tall, 52 meters (171 feet) taller than the Washington Monument in the U.S. capital of Washington, D.C. Building the dam gave hope and dignity to many victims of the Great Depression. It gave people a job and a way to earn money. The Hoover Dam is still in use, providing power to 1.7 million people in Arizona, California, and Nevada. It is often considered an engineering milestone and is named for Herbert Hoover, the U.S. president who helped make the project happen.
Hydroelectric Nations Hydroelectric power provides almost all the energy for some nations. Norway, Brazil, and the Democratic Republic of Congo all get more than 90 percent of their electricity from hydroelectric power plants. Plans for a new hydroelectric plant in the Democratic Republic of Congo may link homes and businesses in Europe with the African power supply.
Washington's Energy The state of Washington is the largest consumer of hydroelectric power in the United States. The state used almost 58 million watts of hydroelectricity in 2009, more than double the next-largest state consumer, Oregon.
Articles & Profiles
Media credits.
The audio, illustrations, photos, and videos are credited beneath the media asset, except for promotional images, which generally link to another page that contains the media credit. The Rights Holder for media is the person or group credited.
Illustrators
Educator reviewer, last updated.
October 19, 2023
User Permissions
For information on user permissions, please read our Terms of Service. If you have questions about how to cite anything on our website in your project or classroom presentation, please contact your teacher. They will best know the preferred format. When you reach out to them, you will need the page title, URL, and the date you accessed the resource.
If a media asset is downloadable, a download button appears in the corner of the media viewer. If no button appears, you cannot download or save the media.
Text on this page is printable and can be used according to our Terms of Service .
Interactives
Any interactives on this page can only be played while you are visiting our website. You cannot download interactives.
Related Resources
- Previous Article
- Next Article
NOMENCLATURE
Introduction, methodology, results and discussion, conclusions and recommendations, data availability statement, design and analysis of a hydro-powered water turbine pump: a sustainable irrigation infrastructure.

- Article contents
- Figures & tables
- Supplementary Data
- Open the PDF for in another window
- Guest Access
- Cite Icon Cite
- Permissions
- Search Site
Sanjay Poudel , Rosina Adhikari , Shashank Adhikari , Manjul Regmi , Hari Bahadur Dura; Design and analysis of a hydro-powered water turbine pump: a sustainable irrigation infrastructure. AQUA - Water Infrastructure, Ecosystems and Society 1 December 2021; 70 (8): 1231–1247. doi: https://doi.org/10.2166/aqua.2021.082
Download citation file:
- Ris (Zotero)
- Reference Manager
The agriculture sector of Nepal has been plagued by problems of poor irrigation networks and infrastructure. This has forced farmers to use fuel and electricity-based pumps, which are both expensive and unsustainable. The problems related to the distribution of power and fluctuating voltages add to the ineffectiveness of the electrical pumping system. So, as a better alternative for environment-friendly and inexpensive irrigation infrastructure, this paper proposes a design methodology of a community-operated hydro-powered pump called water turbine pump (WTP). Although introduced in the 1920s, this technology has been largely ignored nowadays. Moreover, there are insufficient literature and technical documentation to support the design decisions for developers. With an objective to induce momentum in the research and development of this technology, this work presents a well-defined methodology to design a WTP using a propeller turbine directly coupled with a centrifugal pump, in reference to a site located in Bardiya, Nepal. The WTP designed using this methodology could utilize a head of 3 m and a flow rate of 150 lps to deliver 14 lps of water to a height of 14.9 m, yielding a head ratio of 1:5, with an overall efficiency of 50.5%.
Water turbine pump (WTP) is a clean, renewable, and sustainable pumping solution for irrigation purposes.
This paper presents a detailed methodology for the design of WTP with a propeller turbine and centrifugal pump.
This paper aims to revive historical pumping technology by laying out a foundation stone in research and documentation of WTPs.
Graphical Abstract

At the eye of the impeller
At the inlet of runner or impeller
At the outlet of runner or impeller
In meridional direction
In the tangential direction
In the axial direction
Absolute velocity
Blade speed
Relative speed
Design head for turbine
Design flow rate for turbine
Delivery head of the pump
Delivery flow rate for turbine
Theoretical head for pump
Max possible speed for turbine
Rotation speed of turbine
Pfleiderer correction factor
Leading edge
Trailing edge
Nepal has 65% of its population engaged in agriculture, while this sector contributes only 27% of the GDP of the nation ( Government of Nepal 2021 ). It clearly shows the lack of commercialization in the agricultural sector of Nepal which is due to a massive share of smallholder farms. Here, 2.7 million smallholder farms account for 70% of the food produced with an average smallholder farm size of only 0.52 ha ( Raj & Hall 2020 ). Among many other problems leading to the low productivity of the smallholder farms, lack of irrigation facilities and poor distribution of irrigation networks are major ( JICA 2013 ).
In Nepal, only 54% of cultivated land is facilitated with irrigation out of which only one-third gets irrigated all year round ( WECS 2017 ). Even in the lower plains, where clusters of irrigation projects have been launched, the problem persists equally due to the lack of on-farm irrigation facilities and insufficient tertiary canals ( JICA 2013 ). A large number of smallholdings certainly pose great difficulty in expanding tertiary networks. So, plot to plot irrigation is practiced in most cases resulting in heavy loss of water ( JICA 2013 ). An alternative to this practice would be the deployment of on-farm pumping systems.
Pumped irrigation is ruled by fuel-based and electrical pumps worldwide and the case of Nepal is no different. However, these pumps turn out to be expensive for smallholders farmers in a long run because of the high operation and maintenance costs associated with each. They are also not an environment-friendly option, considering the emissions from fuels and the high energy intensity of electrical pumping. In addition, the problems related to the distribution of power and fluctuating voltages in Nepal add to the ineffectiveness of the electrical pumping system ( Pande et al. 2016 ). So, as a better alternative for environment-friendly and inexpensive irrigation infrastructure, this paper proposes the design methodology of a community-operated hydro-powered pump called water turbine pump (WTP). The WTP system requires much less civil works than expanding tertiary canal networks and can also work as an infrastructure for water supply in combination with a water treatment facility. However, this infrastructure may not be economically viable for individual farmers and rather is recommended to be installed and operated by a community or a governing body.
WTP consists of a turbine and a pump linked together in such a way that the rotational speed of the turbine is utilized by the pump to lift the water to a certain head. The combination of turbine and pump may vary according to the head and flow rate available for the turbine and the delivery conditions required for the site. WTPs are advantageous over their RE counterparts such as solar- and wind-powered pumps, as they: (i) can operate 24 hours a day, regardless of weather fluctuation, in a more controlled and predictable manner, (ii) have higher power to size ratio, leading to a compact size, and (iii) are mechanically simpler and more efficient ( Zambrano et al. 2019 ). Moreover, since there is no electromechanical or any other intermediate conversion involved, they are easy to fabricate at a local level, require less skilled manpower for operation and maintenance, and operate at zero cost.
The history of WTPs can be traced back to the 1920s when they were reported to be in use specifically in China where, by 1979, about 60,000 WTPs were irrigating 400,000 ha ( Fraenkel 1986 ). However, more recent documents on this technology are missing. In some documents, they have been classified according to the diameter of the propeller and the ratio of the installation head to the delivery head (head ratio). Series of models have ranged from 10 to 120 cm in rotor diameter and from 4:1 to 6:1 in head ratio. Some products with higher head ratios of 8:1, 10:1, 12:1, 18:1, and 20:1 have also been reported which seems very promising ( Tsutsui 1990 ). However, the available literature and documentation on WTPs are insufficient to support the design decisions. The research and development on this topic seem to have lagged significantly behind due to the takeover of fuel and electricity-based pumping systems. So, the main objective of this paper is to provide technical documentation on WTP technology. This paper is expected to (i) introduce the WTP technology to agriculture practitioners and infrastructure planners, (ii) provide a methodology of the hydraulic design of a WTP to engineers, and (iii) give a head start to the long-stagnant research and development of WTPs.
In this paper, we have presented a detailed methodology for the hydraulic design of WTP and evaluated the performance of each hydraulic component using Computational Fluid Dynamics (CFD). The CFD techniques used in this paper have been verified experimentally by other researchers. Finally, we have predicted the performance of the overall system.
The design methodology of a WTP is highly case-specific. Moreover, the mechanical power generated by the turbine and the power required by the pump require meticulous harmonization. So, a site was defined, and the hydropower resources were assessed. The types of the turbine and the pump were selected based on resource availability, deliverables, and their compatibility with each other. They were designed and their performances were evaluated using CFD. Finally, the system was modeled in SOLIDWORKS, and its characteristics were defined. An overview of the design methodology is depicted in Figure 1 .

Procedure for designing a WTP.
Site assessment
This paper focuses on the design of WTP for low head and high flow rate application, specifically in the plains (Terai region) of Nepal. The design is in reference to the specification of a canal network situated in Bethani, Thakurdwara VDC, Bardiya. The source stream is originated from the Karnali River and is one of the canals within the network of the Surya Patuwa irrigation plant. A fairly stable average annual flow of 1.5 m 3 /s flows through the canal. A total head of 3.3 m and a flow rate of 0.15 m 3 /s can be made available after simple civil construction. A basic layout of the installation site is presented in Figure 2 .

Possible layout of WTP installation at the site.
Considering that the efficiency of the canal lies in the range of 90–95% ( Harvey et al. 1993 ), the system was designed for (i) design head (H) = 3 m and (ii) flow rate (Q) = 0.15 m 3 /s.
Selection of turbine and pump
The selection of a turbine requires careful consideration of the head and flow rate available at the site. Propeller turbine is selected for this case, as (i) it is suitable for the low head (as low as 1 m) and high flowrate applications, (ii) it has a high specific speed that can run a centrifugal pump, and (iii) it is easier and cheaper to fabricate locally compared to its other counterparts ( Williamson et al. 2014 ). The selection of the pump, on the other hand, depends on its application. Here, a centrifugal pump was selected, as it provides a high flow rate ( Dixon & Hall 2013 ) as desired for flood irrigation purposes at the site.
In this case, the propeller turbine can be directly coupled with a centrifugal pump and can be installed directly into a canal drop or a weir on a canalized river where the head of 1 – 5 m is available. The resulting system leads to a compact configuration. However, in the case of the high head requirements, a reciprocating pump may be chosen.
Figure 3 shows the schematic diagram of the WTP installed in a canal drop.

Schematic diagram of Chinese WTP ( Fraenkel 1986 ).
Considering a reasonable efficiency of 85% ( JICA 2011 ), the theoretical power output of the propeller turbine was calculated to be 3,750 W. The head ratio of WTP was targeted in the range of 5:1–6:1 ( Tsutsui 1990 ). A design head (h) of 17 m and a delivery flow rate (q) of 16.4 lps were selected after iterations with several combinations, considering two criteria: (i) the value of head coefficient and flow coefficient shall be within the acceptable range of 0.7–1.3 and 0.05–0.2, respectively ( Tuzson 2000 ), and (ii) the theoretical power required to drive the pump shall be less than the theoretical power output from the propeller turbine.
Design of the propeller turbine
The propeller turbine design process involves the design of a runner, a guide ring, and a draft tube. The spiral casing could be omitted in this case because the value of H is less than 6 m ( Pai 2017 ). Alternatively, the turbine was designed to be installed into a rectangular channel or an open volute ( Susanto & Stamp 2012 ).
The design of the propeller turbine, presented in this paper, is mostly based on the design methodology for a low head propeller turbine (2–10 m) with output less than 5 KW, provided by Simpson & Williams (2011) . The methodology involves the following steps: (i) choosing the right rotational speed (N), (ii) sizing of the runner (diameter and hub-tip ratio), (iii) deciding the number of blades and pitch, (iv) calculating the blade parameters such as flow velocities and angles, and (v) designing the guide vanes and draft tube.
A value of N, less than N max , was selected such that the specific speed based on power ranged within 255–860 rpm ( Hothersall 2004 ).
The runner diameters were calculated using the statistical relationship provided by Siervo & Leva (1977) . A smaller hub-to-tip ratio (less than 0.5) would result in more twisted blades. Thus, for simplicity of manufacturing, a slightly larger than calculated hub-to-tip ratio was used ( Simpson & Williams 2011 ). Although the number of blades suggested was four ( Simpson & Williams 2011 ), the performances of the runners with four, five, and six blades were analyzed. The main parameters of the propeller turbine are summarized in Table 1 .
Turbine runner parameters
After calculating the sizing parameters, blades were designed. As long as the camber and twist of the blades are preserved, the performance of the propeller turbine does not vary significantly by using a constant thickness profile instead of an airfoil profile ( Demetriades et al. 1996 ). So, to simplify the manufacturing process, blades were designed with circular arcs and a constant thickness. The velocity components and blade parameters, shown in Figure 4 , were calculated for five spans distributed equally along the radius. The solidity (i.e. chord length of blade/blade pitch) at the hub of the runner was confined near 1 for minimum profile losses ( Chen & Engeda 2019 ). To incorporate the effect of the flow deviation, the angle of deviation was subtracted from the blade stagger angle. The angle of deviation was calculated using Carter's parameter for the circular arc camber line ( Hothersall 2004 ). The summary of spanwise values and other blade parameters is provided in the Supplementary Material.

Velocity diagram for propeller turbine blades.
For guide vanes, the radial configuration was chosen over axial, as it is more robust. The number of guide vanes was selected to fulfill two criteria: (i) the number of guide vanes shall be greater than the number of runner blades and (ii) their ratio shall not be an integer, to avoid stalling of the runner blades ( Kim 2015 ). Other basic dimensions of the guide vane were calculated as suggested by Nechleba (1957) and Zu-yan (2018) . They are summarized in Table 2 .
Guide vanes parameters
A simple conical draft tube with a divergence angle of 4° was designed. The length of the draft tube was selected to be 2.02 m such that: (i) the length is smaller than the maximum allowed suction head and (ii) the total head available to the runner would be maintained at 3 m. Care should be given to select the length of the draft tube because a length greater than the suction head leads to a destructive phenomenon called cavitation. The cavitation is caused by the loss in pressure that occurs downstream due to the conversion of pressurized flow to the free surface. Aerator tubes can also be employed to control this phenomenon ( Yamini et al. 2021 ). The detailed procedure of draft tube design can be found in Pai (2017) .
Design of the centrifugal pump
The design of the centrifugal pump is mostly based on the methodology given by Srinivasan (2008) and Gülich (2010) . The design process involves the following steps: (i) determining the inlet conditions (eye diameter, inlet diameter, inlet width, and velocities), (ii) determining the outlet conditions (outlet diameter and velocities), (iii) selecting the number of blades and the blade thickness, (iv) developing blade profile and flow passage, and (v) design of volute.
The rotational speed of the pump is equal to that of the turbine, i.e., 1,450 rpm. The specific speed of 19.63 rpm was obtained which led to the selection of radial configuration of the pump ( Girdhar & Moniz 2005 ). As the pump had low specific speed, the eye velocity (C 0 ) of 3 m/s was deemed suitable, as they provide good cavitation characteristics ( Srinivasan 2008 ). Using this eye velocity, the diameter of the eye (D 0 ) was calculated. The iterative procedure suggested by Srinivasan (2008) was then used to calculate the inlet blade angle ( β 1 ) and meridional velocity at the blade inlet (C m1 ). An angle of attack of 5° was added to β 1 for having shock-less entry at the blade ( Srinivasan 2008 ). For the determination of outlet conditions, first, the diameter of impeller (D 2 ) was to be selected. It was assumed in such a way that the flow coefficient obtained was within the acceptable range of 0.05–0.2 ( Tuzson 2000 ). Thus, the impeller diameter of 240 mm was selected, as it satisfied the flow coefficient criteria. It also resulted in a practical blade width at the outlet hence, making the manufacturing process easy. All the necessary calculations for the determination of inlet and outlet parameters were done using the Euler equation of turbomachinery and the velocity triangles. The velocity triangles at the impeller are shown in Figure 5 .

Schematic diagram of impeller and velocity diagram.
Impeller blades with blade outlet angle ( β 2 ) of less than 90° produce backward curved vanes. These types of blades are mostly preferred in centrifugal pumps, as they provide higher efficiency with less secondary loss. According to Srinivasan (2008) , for a specific speed of less than 30 rpm, outlet blade angle must be less than 30° to obtain higher efficiency. Since the β 2 of 28° was obtained, therefore, the blades were backward-curved under the required criteria.
For a cast iron impeller, mechanical strength requirements are generally met when the thickness of the blade is 0.016–0.022 times the diameter of the impeller ( Gülich 2010 ). Since thicker blades can withstand high stresses and can be cast or welded easily, the blade thickness of 5 mm was considered to be appropriate. The leading edges (LEs) were filleted, and the trailing edges (TEs) were made as thin as possible. The main impeller parameters obtained are shown in Table 3 .
Pump impeller parameters

Meridional streamline for centrifugal impeller.

Mesh at (a) S1, (b) R1, and (c) S2.

Mesh at (a) r1 and (b) s1.

Boundary conditions for propeller turbine.

Boundary conditions for centrifugal pump.
The radial and axial velocities, from the LE of the blade to the TE of the blade, were assumed to vary linearly. The differential equation ( 4 ) was then integrated to obtain the streamline. MATLAB code was generated to develop the blade camber line, meridional streamline, and the varying blade width. The data generated were then used for the CAD modeling of the impeller in SOLIDWORKS.
Finally, the volute was designed using the constant velocity method, as it is easier to cast, economical to produce, and efficient in practice ( Srinivasan 2008 ). Assuming a constant flow velocity, the maximum throat area of volute at 360° was first calculated. The throat areas at different wrap angles were then calculated considering a directly proportional relationship between the throat area and the angle. A certain fillet was provided at the cutwater section, and the volute pipe area was increased with a 5° of angle of divergence after the volute made a full 360° wrap angle ( Gülich 2010 ).
All the design data along with codes are provided in the Supplementary Material.
CFD analysis
After obtaining all the design points, CFD tools were used to verify the performance of WTP. A single CFD setup for the entire system would be computationally complex. Thus, two different setups, one for the propeller turbine and another for the centrifugal pump, were generated. This paper uses the CFD methods that have been experimentally validated by other researchers for propeller turbines ( Vu et al. 2018 ) and centrifugal pumps ( Ding et al. 2019 ). The analysis was expected to verify the power delivered by the turbine, power requirement of the pump, and the head delivered by the pump.
The propeller turbine domain consisted of three subdomains namely: guide vane domain (S1), rotor domain (R1), and draft tube domain (S2). S1 and R1 were taken as a unit periodic segment of the guide vane and the rotor, respectively, to reduce the computational cost. The structured mesh was generated using Turbo-Grid software for S1 and R1, while the S2 subdomain was meshed using ANSYS Auto-mesh. The meshes generated for the domains are shown in Figure 7 . The number of elements in S1, R1, and S2 was obtained as 362,740, 2,308,278, and 93,060, respectively, after a grid-independent test. The boundary layer resolution around the guide vane and rotor blade had a y+ value in the range of 1–2.
The centrifugal pump domain consisted of two subdomains, namely: impeller domain (r1) and volute domain (s1). A unit periodic element of the impeller was used as the r1 subdomain, and a structured mesh was generated in Turbo-Grid. The subdomain s1 had unstructured mesh created in ANSYS Auto-mesh. The meshes generated for the domains are shown in Figure 8 . The number of elements in s1 and r1 was obtained as 653,058 and 1,737,491, respectively, after the grid independence test. The boundary layer resolution around the impeller blade had a y+ value in the range of 1 – 2.
ANSYS CFX solver was used for the analysis of both domains. In the case of the propeller turbine, a total pressure boundary condition of 29,341 Pa was applied at the inlet of S1, while an opening boundary condition with static pressure 0 Pa was applied at the outlet of S2 as shown in Figure 9 . Frozen rotor configuration was selected on the interface between S1 and R1, and R1 and S2, with specified pitch angles of 40 and 72°, and 72 and 360°, respectively. The advection scheme was set to a blend factor of 0.5, and the turbulence numeric was set to ‘High resolution’ with a physical time step of 2e-4. The RMS residual target was set to 1e-4. The models were solved for steady-state with the K− ω SST turbulence model.
For the centrifugal pump, a total pressure of 0 Pa was specified at the inlet of r1, while a mass flow rate of 16.4 kg/s was specified at the outlet of s1 as shown in Figure 10 . Frozen rotor configuration was selected on the interface with a specified pitch angle of 45 and 360°. The advection scheme was set to a blend factor of 0.5, and turbulence numeric was set to ‘Higher Order’ with a physical time step of 4.5e-5. The RMS residual target was set to 1e-5.
Effect of change in the number of blades of propeller turbine
Runners with four, five, and six blades were evaluated using CFD. Table 4 summarizes the results obtained by varying the number of blades from four to six.
Effect of different number of blades in turbine runner
Under the constant total head of 3 m, the flow rate in the turbine decreased with the increase in the number of blades due to the decrease in the annulus area of the runner. The power generated by the runner and the overall efficiency was observed to increase with the increase in the number of blades. However, the rotor efficiency was found to decrease because of increased losses due to blade friction.
Although four blades were considered optimal from the analytical calculation, the simulation results showed that the five-bladed turbine has matched the design point more accurately. The turbine with four blades would require a flow rate higher than available to achieve the full load condition, which means it will operate at partial load condition under the flow rate of 150 lps. Since the efficiency of the propeller turbine decreases at partial load conditions, five blades were chosen for the final design. Nevertheless, a runner with six blades could also be used, but the addition in the power would not be significant compared to the complication in fabrication it would add.
Velocity distribution at propeller runner
For an axial turbine, the meridional velocity (C m ) is equal to the axial velocity (C x ) and is supposed to be constant throughout the rotor. The value of C m obtained from CFD was plotted against meridional distance as well as radial span as shown in Figure 11(a) . The theoretically obtained value of meridional velocity was also plotted on the same chart. From the figure, it is clear that axial velocity computed from the simulation was almost constant throughout the runner and near about the analytical value (C m = C x = 5.03 m/s). The average value of computed streamwise and spanwise C m was obtained to be 5.24 and 5.08 m/s, respectively, with standard deviations of 0.16 and 0.4, respectively. The value of C m was obtained larger than calculated analytically at inner spans and smaller than expected at the hub and tip regions. It is because the boundary layer formed at the hub and tip constricts the area of flow increasing the axial velocity.

(a) Spanwise and streamwise meridional velocity distribution at R1. (b) Distribution of Cu.r in spanwise and streamwise direction at R1.
The free vortex theory applied for the runner design assumes that the angular momentum at the LE and the TE along the span is constant. Also, for the maximum efficiency of the rotor, it was expected that the tangential fluid velocity (C u ) at the TE be near about zero. Figure 11(b) shows the distribution of C u .r in the spanwise direction at LE and TE. Theoretically, C u .r was calculated to be 0.23 at LE and 0.02 at TE, whereas the average value of C u .r obtained from CFD was 0.32 and 0.16 at LE and TE with 0.078 and 0.076 standard deviations, respectively. The possible explanation for this difference is that since the fluid must overcome some frictional forces while flowing from LE to TE, the flow deviates less than the angle of the blade. It results in the value of C u being higher than assumed at TE. Similarly, due to the constant angle of attack at all spans of inlet because of flat blade guide vanes, spanwise distribution of C u .r could not be achieved as steady as assumed during calculation.
Effects of using constant thickness circular arc blades
For the simplicity of manufacturing, flat guide vanes and twisted runner blades with constant thickness were used instead of an airfoil, which is subjected to certain losses. Figure 12(a) shows the contour of total pressure around 50% of the radial span of the guide vane. The LE of the guide vane is observed to have resulted in a total pressure loss. The profile of the pressure contour suggests that the use of an airfoil cross-section could reduce the loss. Similarly, it can be observed in Figure 12(b) that the LE and TE of the propeller blade has undergone abrupt pressure change (rise at LE and fall at TE) in the direction of flow because of thinner LE and thicker TE. Furthermore, a small region of flow separation can be visualized at the immediate vicinity of the LE due to the use of circular arc camber ( Bian et al. 2018 ). The results also suggest that flow separation is likely to occur in blades with a slight change in an angle of attack of the fluid, i.e., at the off-design conditions. Thus, the off-design performance of the rotor is suspected to be poor.

Total pressure distribution (a) at mid-span of S1 and (b) at the hub of R1 (stationary frame).
Figure 13 shows the blade loading characteristics of the circular arc blade. The maximum pressure difference on the blade was observed to be around the maximum camber position at the mid-span. The abrupt changes in pressure at the LE and the TE were observed due to separation at LE and TE.

Blade loading chart of R1 blade at mid-span.
Variation of total pressure and velocity across centrifugal pump
Figure 14(a) and 14(b) show the pressure and velocity distribution in the pump. The total pressure rose when the water flowed from the LE to the TE. This is due to the energy imparted by the rotor to the water which causes the increase in the velocity as well as the static pressure of the water. In the case of the volute, the total pressure is mostly constant. However, due to the increasing cross-section area, the velocity decreases, as the velocity head is converted into the pressure head. A region of flow separation was also observed from the cutwater towards the outlet.

Total pressure and velocity distribution: (a) total pressure distribution and (b) velocity distribution.
Effect of change in flow rate at the inlet of impeller
The characteristics of the impeller were observed under different flow rates of 8, 12, 14, 16.4, and 19 lps by using CFD. Flow separation zones were observed in the suction side of the impeller blades at the flow rate of 8 lps. It is because, at the flow rate much lower than the design flow rate, the flow angle at the inlet is small to cause the flow to separate toward the suction side. As a result, the efficiency also decreases significantly. However, the separation was not detected for flow rates of greater than 8 lps. Figure 15(a) and 15(b) show velocity vectors at 8 and 16.4 lps, respectively.

Blade to blade view of velocity vectors at (a) 8 lps flow and (b) 16.4 lps flow.
Effect of change in flow rate at the volute cutwater
The effect of change in flow rate at the volute cutwater region was also studied using CFD. Figure 16 shows the velocity vectors in the cutwater region of the volute under different flow rates. It was observed that the flow separation starting from the cutwater toward the discharge side became prominent, as the flow rate increased. As the flow rate increases, the flow accelerates downstream. This leads to a decrease in the static pressure which causes backflow of fluid. Furthermore, the increase in velocity at the outlet causes the flow angle to decrease and deviate from the cutwater toward the discharge, resulting in the separation of flow from the cutwater toward the throat region ( Gülich 2010 ).

Flow at cutwater at different flow rates at (a) 14, (b) 16.4, and (c) 19 lps.
Characteristic curves of the centrifugal pump
At the design point, the pump could deliver a flow of 16.4 lps to a total head of 14.4 m and a static head of 13.5 m with an efficiency of 79%. At this condition, the pump required an input power of 2.92 KW. However, the power output from the turbine was insufficient to drive the pump at that point. To evaluate feasible operation range, the characteristic curves of the centrifugal pump were obtained by varying flow rates at the inlet of the pump. The characteristic curves of the centrifugal pump are shown in Figure 17(a) and 17(b) . Theoretically, the head provided by the pump should increase with the decrease in flow rate. After a certain point, the head must decrease even with the decrease in flow rate. The CFD results were observed to be less than the analytically calculated values with a maximum error of 7.5% between the two calculation methods. This deviation is due to the profile losses and the separation losses unaccounted by the analytical method.

(a) Head vs. flow characteristics. (b) Efficiency vs. flow characteristics of centrifugal pump.

Section view of WTP assembly.
Although a 16.4 lps flow rate was selected as the design point, it could be observed from the CFD simulation results that the flow rate of 14 lps could be delivered at the best efficiency point. The efficiency at 14 lps was observed to be 81%, whereas at 16.4 lps, the efficiency was 79%. The increase in efficiency at a lower flow rate is because of the low magnitude of frictional losses subsequently due to the lower flow rates. At 14 lps, the input power required to operate the pump was found to be 2.62 kW which is less than the power output of the turbine. The total head of 15.5 m and the static head of 14.9 m were obtained at this discharge rate.
Characteristics of WTP
The section view of WTP assembly is shown in Figure 18 . The pump, at the design point, required input power of 2.92 KW, but the turbine could only generate an output power of 2.77 KW, which was insufficient to run the pump. However, at the best efficiency point of 14 lps, the pump only required an input power of 2.62 KW. Thus, a WTP working under the head of 3 m and the flow rate of 150 lps, which could pump 14 lps of water to the height of 14.9 m at its best efficiency point, was obtained. The individual efficiencies of the turbine and the pump were obtained as 63 and 81%, respectively, with an overall efficiency of 50.5% assuming 1% mechanical losses at bearing. The head ratio of 1:5 could be obtained from the design.
In conclusion, this paper presented a methodology that could be used to design a WTP for low head and high flow rate applications, in the case of an irrigation canal network at Bardiya, Nepal. This technology is expected to be a reliable, economic, and environment-friendly alternative for irrigation infrastructure, over fuel, electricity, and other RE-based pumping systems.
To sum up, a WTP was designed using the methodology presented in this paper, and the design was verified using experimentally validated CFD methods. It could utilize the head of 3 m and the flow rate of 150 lps to deliver 14 lps of water to a height of 14.9 m, yielding a head ratio of 1:5 at its best efficiency point. The individual efficiencies of the turbine system and the pump system were obtained as 63 and 81%, respectively, with an overall efficiency of 50.5%, considering 1% mechanical losses at bearing.
The scope of this paper was limited to the hydraulic design of WTP components for given site specifications. This topic has wide prospects to be deployed in irrigation systems and/or water supply systems. Further research and development are required to strengthen its potential, all of which could not be covered in this project due to time and resource constraints. To the researchers willing to investigate this topic further, off-design characteristics of WTP can be analyzed with experimental validation. Furthermore, combinations of various kinds of pumps and turbines can be tested.
All relevant data are included in the paper or its Supplementary Information.
Supplementary data
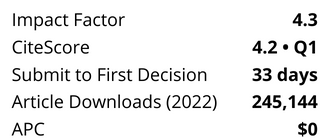
Affiliations
- ISSN 2709-8028 EISSN 2709-8036
- Open Access
- Collections
- Subscriptions
- Subscribe to Open
- Editorial Services
- Rights and Permissions
- Sign Up for Our Mailing List
- IWA Publishing
- Republic – Export Building, Units 1.04 & 1.05
- 1 Clove Crescent
- London, E14 2BA, UK
- Telephone: +44 208 054 8208
- Fax: +44 207 654 5555
- IWAPublishing.com
- IWA-network.org
- IWA-connect.org
- Cookie Policy
- Terms & Conditions
- Get Adobe Acrobat Reader
- ©Copyright 2024 IWA Publishing
This Feature Is Available To Subscribers Only
Sign In or Create an Account
Accessibility Links
- Skip to content
- Skip to search IOPscience
- Skip to Journals list
- Accessibility help
- Accessibility Help
Click here to close this panel.
Purpose-led Publishing is a coalition of three not-for-profit publishers in the field of physical sciences: AIP Publishing, the American Physical Society and IOP Publishing.
Together, as publishers that will always put purpose above profit, we have defined a set of industry standards that underpin high-quality, ethical scholarly communications.
We are proudly declaring that science is our only shareholder.
Experimental investigation of Archimedes Screw Hydro Turbine rotation with and without deflector
Y Setiawan 1 , E S Wijianti 1 , B S Wibowo 1 , S Saparin 1 and P Prayitnoadi 1
Published under licence by IOP Publishing Ltd IOP Conference Series: Earth and Environmental Science , Volume 926 , 3rd International Conference on Green Energy and Environment 2021 (The 3rd ICoGEE 2021) 29th-30th September, Bangka Belitung, Indonesia Citation Y Setiawan et al 2021 IOP Conf. Ser.: Earth Environ. Sci. 926 012013 DOI 10.1088/1755-1315/926/1/012013
Article metrics
702 Total downloads
Share this article
Author e-mails.
Author affiliations
1 Mechanical Engineering Department, Faculty of Engineering, Universitas Bangka Belitung, Indonesia
Buy this article in print
The Archimedes screw water turbine (AST) is a device that works mechanically to produce electrical energy with an energy source that comes from the flow of water. Archimedes screw hydro turbines operate at low head and flow rates and can generate electricity at micro levels. This type of turbine is very suitable for use in small waters such as irrigation and rivers. The research was conducted by building a prototype of a small-scale Archimedes screw hydro turbine with and without deflector. The purpose of this research is to compare the rotation produced by the two turbines and whether the installation of a deflector can improve turbine performance. The turbine is constructed with a screw length of 1 m, outer diameter is 30 cm, the number of blades 15, and each has a pitch distance is 13 cm. Turbine angle variations are 30°, 35°, and 40°. The results showed that the best rotor rotation was produced by the screw without deflector at an angle of 30°. This shows that the addition of a deflector reduces the resulting screw rotation.
Export citation and abstract BibTeX RIS
Content from this work may be used under the terms of the Creative Commons Attribution 3.0 licence . Any further distribution of this work must maintain attribution to the author(s) and the title of the work, journal citation and DOI.
- Election 2024
- Entertainment
- Newsletters
- Photography
- Personal Finance
- AP Investigations
- AP Buyline Personal Finance
- AP Buyline Shopping
- Press Releases
- Israel-Hamas War
- Russia-Ukraine War
- Global elections
- Asia Pacific
- Latin America
- Middle East
- Election Results
- Delegate Tracker
- AP & Elections
- Auto Racing
- 2024 Paris Olympic Games
- Movie reviews
- Book reviews
- Personal finance
- Financial Markets
- Business Highlights
- Financial wellness
- Artificial Intelligence
- Social Media
New industry readies for launch as researchers hone offshore wind turbines that float
Researchers are racing to create large wind turbines and floating platforms, bringing energy from offshore wind closer to reality. (AP Video: Robert Bukaty)
FILE - The University of Maine’s first prototype of an offshore wind turbine is seen in this Sept. 20, 2013 file photo, near Castine Maine. (AP Photo/Robert F. Bukaty, files)
- Copy Link copied
Habib Dagher, director of the advanced composites center, center, works with research assistants Ryan Thornton, left, and Mitchell Kelley, at the University of Maine, Wednesday, March 27, 2024, at the University of Maine, in Orono, Maine. (AP Photo/Robert F. Bukaty)
A 13-foot-tall wind turbine is tested for stability in a wave pool, Wednesday, March 27, 2024, at the University of Maine, in Orono, Maine. The waves simulate worst possible conditions for an offshore wind turbine on a 1:70 scale. (AP Photo/Robert F. Bukaty)
A computer graphic shows stability tests on a 13-foot-tall wind turbine in a wave pool, Wednesday, March 27, 2024, at the University of Maine, in Orono, Maine. (AP Photo/Robert F. Bukaty)
A 13-foot-tall wind turbine floats in a wave pool, Wednesday, March 27, 2024, at the University of Maine, in Orono, Maine. At UMaine more than 50 engineers comprise the largest floating offshore wind team in the U.S.(AP Photo/Robert F. Bukaty)
Anthony Viselli, manager of offshore model testing and structure design, left, and Habib Dagher, director of the advanced composites center, examine used anchor cables used for securing floating offshore wind turbines to the ocean floor, Wednesday, March 27, 2024, at the University of Maine, in Orono, Maine. (AP Photo/Robert F. Bukaty)
A bank of powerful fans and 16 mechanical paddles are used to simulate in a pool the worst conditions at sea, Wednesday, March 27, 2024, at the University of Maine, in Orono, Maine. (AP Photo/Robert F. Bukaty)
A figure represents a human standing on a vertical column used to stabilize a floating wind turbine in the wave pool, Wednesday, March 27, 2024, at the University of Maine, in Orono, Maine. (AP Photo/Robert F. Bukaty)
ORONO, Maine (AP) — As waves grew and gusts increased, a wind turbine bobbed gently, its blades spinning with a gentle woosh. The tempest reached a crescendo with little drama other than splashing water.
The uneventful outcome is exactly what engineers aimed for.
The demonstration featuring a 13-foot-tall (4-meter-tall) floating wind turbine in an indoor pool aimed to ensure it can withstand the strain of powerful water and wind when much larger versions are deployed in the ocean.
It’s the University of Maine’s contribution to a worldwide race to improve floating machines to tap wind that blows across deeper waters offshore, too deep to attach turbines to the seabed with permanent pilings.
In the next decade, UMaine researchers said, they envision turbine platforms floating in the ocean beyond the horizon, stretching more than 700 feet (210 meters) skyward and anchored with mooring lines.
“These structures are massive,” said Anthony Viselli, chief engineer for offshore wind technology at the university’s Advanced Composites Center, after the demonstration wrapped up. “These would be some of the largest moving structures that humankind has endeavored to create. And there would be many of them.”
As the technology advances, dozens of designs are being promoted by experts who see floating wind turbines as a way to address climate change by shifting away from burning fossil fuels.
Floating turbines are the only way some countries and U.S. states can capture offshore wind energy on a large scale. In the U.S. alone, 2.8 terawatts of wind energy potential blows over ocean waters too deep for traditional turbines that affix to the ocean floor, according to the National Renewable Energy Laboratory . That’s enough to power 350 million homes — more than double the number of existing homes in the U.S.
The first floating wind farm started operating off Scotland’s coast in 2017. In the United States, the Department of Interior two weeks ago proposed the first floating wind energy auctions for the Gulf of Maine, following lease auctions for the West Coast that began in 2022 . The nearly 1 million acres up for auction off the New England coast could generate enough clean wind energy to power more than 5 million local homes, the department said.
UMaine is home to the nation’s largest team of engineers dedicated to floating offshore wind. Other big players include Equinor, which has installed a demonstration floating project of the coast of Norway; global company Principle Power, which has installed small-scale projects off Scotland and Portugal; and SBM Offshore, which has a demonstration project off France.
Floating offshore wind is still a nascent industry, however, making it expensive.
The Norwegian company Equinor postponed its Trollvind floating initiative , citing technology availability, rising costs and a strained timetable to deliver on the original concept.
Danish wind energy developer Ørsted decided to focus its efforts on fixed-bottom turbines, foregoing deeper offshore regions including Japan, Norway, Spain, Portugal and the U.S. West Coast. “We care a lot about affordability of renewable power, and floating wind is a lot more expensive than bottom-fixed,” said CEO Mads Nipper.
But others are moving forward.
Gazelle Wind Power is developing a modular platform system to make manufacture and assembly cost-effective and efficient.
“This is a global problem and this is an ideal solution in order to deliver power to shore,” said Gazelle Wind Power CEO Jon Salazar.
UMaine launched its first floating prototype a decade ago and became a surprise global leader after a study showed that the Gulf of Maine had the wind energy potential of 156 nuclear power plants, due to fast, consistent wind.
The state could meet all its home heating needs and power every car — if they were all electric vehicles — by tapping just 3% of that water. That improves the odds of successfully sharing the resource with fishermen, recreational boaters, the military and, of course, marine life . Indeed, the federal government’s lease proposal spares Maine’s key lobstering grounds from development, removing a potential obstacle.
Trailblazers in offshore wind are benefiting from work done by the oil industry, which engineered floating oil and gas rigs, said Habib Dagher, director of the Advanced Composites Center.
The university’s wind wave basin, which looks something like a swimming pool with wave and wind generators that can mimic ocean conditions up to a 500-year storm, takes that work to the next level.
On a recent day, the semi-submersible floating turbine was tethered to the bottom of the basin. Its 1:70 scale represented a real turbine standing about 800 feet (240 meters) tall atop a platform in the ocean. The goal is to have industrial scale turbines of 15 to 20 megawatts each, Dagher said.
Size and efficiency are keys to profitability. Larger wind turbines mean fewer are needed, reducing construction, installation and maintenance costs, Viselli said. With greater size and efficiency, developers envision only about 50 turbines needed to produce about the same amount of electricity as a nuclear power plant.
Full-size turbines generate peak power starting at about 20 mph (32 kph). In powerful storms, they shut down automatically to avoid stressing the equipment or breaking. The mooring lines tethered to the ocean floor are made of rope nearly thick as a telephone pole and under heavy tension. That makes them safer for marine mammals.
For all the turbine technology, the platforms developed by UMaine can be built locally with concrete, a simple material that’s readily available. The university already has partners around the world interested in licensing its technology. The state of Maine plans to develop a port facility in the Searsport area to build the floating bases and attach turbines before sending them into the Gulf of Maine.
A brand new industry means some experiments in design will succeed and some will fail. And there is work to ensure that wind farms are good neighbors, overcoming objections from others using the ocean.
“We’re going to have some problems and we have to figure out how to roll up our sleeves and solve these problems,” Dagher said. “And I think we have no choice as a society but to do that.”
McDermott reported from Providence, Rhode Island.
The Associated Press’ climate and environmental coverage receives financial support from multiple private foundations. AP is solely responsible for all content. Find AP’s standards for working with philanthropies, a list of supporters and funded coverage areas at AP.org .

Take the Quiz: Find the Best State for You »
What's the best state for you ».
New Industry Readies for Launch as Researchers Hone Offshore Wind Turbines That Float
Researchers around the world are racing to create large wind turbines and floating platforms as upcoming lease auctions bring offshore wind closer to reality

Robert F. Bukaty
FILE - The University of Maine's first prototype of an offshore wind turbine is seen in this Sept. 20, 2013 file photo, near Castine Maine. (AP Photo/Robert F. Bukaty, files)
ORONO, Maine (AP) — As waves grew and gusts increased, a wind turbine bobbed gently, its blades spinning with a gentle woosh. The tempest reached a crescendo with little drama other than splashing water.
The uneventful outcome is exactly what engineers aimed for.
The demonstration featuring a 13-foot-tall (4-meter-tall) floating wind turbine in an indoor pool aimed to ensure it can withstand the strain of powerful water and wind when much larger versions are deployed in the ocean.
It’s the University of Maine’s contribution to a worldwide race to improve floating machines to tap wind that blows across deeper waters offshore, too deep to attach turbines to the seabed with permanent pilings.
In the next decade, UMaine researchers said, they envision turbine platforms floating in the ocean beyond the horizon, stretching more than 700 feet (210 meters) skyward and anchored with mooring lines.
“These structures are massive,” said Anthony Viselli, chief engineer for offshore wind technology at the university’s Advanced Composites Center, after the demonstration wrapped up. “These would be some of the largest moving structures that humankind has endeavored to create. And there would be many of them.”
As the technology advances, dozens of designs are being promoted by experts who see floating wind turbines as a way to address climate change by shifting away from burning fossil fuels.
Floating turbines are the only way some countries and U.S. states can capture offshore wind energy on a large scale. In the U.S. alone, 2.8 terawatts of wind energy potential blows over ocean waters too deep for traditional turbines that affix to the ocean floor, according to the National Renewable Energy Laboratory . That’s enough to power 350 million homes — more than double the number of existing homes in the U.S.
The first floating wind farm started operating off Scotland’s coast in 2017. In the United States, the Department of Interior two weeks ago proposed the first floating wind energy auctions for the Gulf of Maine, following lease auctions for the West Coast that began in 2022 . The nearly 1 million acres up for auction off the New England coast could generate enough clean wind energy to power more than 5 million local homes, the department said.
UMaine is home to the nation's largest team of engineers dedicated to floating offshore wind. Other big players include Equinor, which has installed a demonstration floating project of the coast of Norway; global company Principle Power, which has installed small-scale projects off Scotland and Portugal; and SBM Offshore, which has a demonstration project off France.
Floating offshore wind is still a nascent industry, however, making it expensive.
The Norwegian company Equinor postponed its Trollvind floating initiative , citing technology availability, rising costs and a strained timetable to deliver on the original concept.
Danish wind energy developer Ørsted decided to focus its efforts on fixed-bottom turbines, foregoing deeper offshore regions including Japan, Norway, Spain, Portugal and the U.S. West Coast. “We care a lot about affordability of renewable power, and floating wind is a lot more expensive than bottom-fixed,” said CEO Mads Nipper.
But others are moving forward.
Gazelle Wind Power is developing a modular platform system to make manufacture and assembly cost-effective and efficient.
“This is a global problem and this is an ideal solution in order to deliver power to shore,” said Gazelle Wind Power CEO Jon Salazar.
UMaine launched its first floating prototype a decade ago and became a surprise global leader after a study showed that the Gulf of Maine had the wind energy potential of 156 nuclear power plants, due to fast, consistent wind.
The state could meet all its home heating needs and power every car — if they were all electric vehicles — by tapping just 3% of that water. That improves the odds of successfully sharing the resource with fishermen, recreational boaters, the military and, of course, marine life . Indeed, the federal government’s lease proposal spares Maine’s key lobstering grounds from development, removing a potential obstacle.
Trailblazers in offshore wind are benefiting from work done by the oil industry, which engineered floating oil and gas rigs, said Habib Dagher, director of the Advanced Composites Center.
The university's wind wave basin, which looks something like a swimming pool with wave and wind generators that can mimic ocean conditions up to a 500-year storm, takes that work to the next level.
On a recent day, the semi-submersible floating turbine was tethered to the bottom of the basin. Its 1:70 scale represented a real turbine standing about 800 feet (240 meters) tall atop a platform in the ocean. The goal is to have industrial scale turbines of 15 to 20 megawatts each, Dagher said.
Size and efficiency are keys to profitability. Larger wind turbines mean fewer are needed, reducing construction, installation and maintenance costs, Viselli said. With greater size and efficiency, developers envision only about 50 turbines needed to produce about the same amount of electricity as a nuclear power plant.
Full-size turbines generate peak power starting at about 20 mph (32 kph). In powerful storms, they shut down automatically to avoid stressing the equipment or breaking. The mooring lines tethered to the ocean floor are made of rope nearly thick as a telephone pole and under heavy tension. That makes them safer for marine mammals.
For all the turbine technology, the platforms developed by UMaine can be built locally with concrete, a simple material that's readily available. The university already has partners around the world interested in licensing its technology. The state of Maine plans to develop a port facility in the Searsport area to build the floating bases and attach turbines before sending them into the Gulf of Maine.
A brand new industry means some experiments in design will succeed and some will fail. And there is work to ensure that wind farms are good neighbors, overcoming objections from others using the ocean.
“We’re going to have some problems and we have to figure out how to roll up our sleeves and solve these problems,” Dagher said. “And I think we have no choice as a society but to do that.”
McDermott reported from Providence, Rhode Island.
The Associated Press’ climate and environmental coverage receives financial support from multiple private foundations. AP is solely responsible for all content. Find AP’s standards for working with philanthropies, a list of supporters and funded coverage areas at AP.org .
Copyright 2024 The Associated Press . All rights reserved. This material may not be published, broadcast, rewritten or redistributed.
Photos You Should See - May 2024

Tags: Associated Press , business , electric vehicles , world news , Maine , education
America 2024

Subscribe to our daily newsletter to get investing advice, rankings and stock market news.
See a newsletter example .
You May Also Like
The 10 worst presidents.
U.S. News Staff Feb. 23, 2024

Cartoons on President Donald Trump
Feb. 1, 2017, at 1:24 p.m.

Photos: Obama Behind the Scenes
April 8, 2022

Photos: Who Supports Joe Biden?
March 11, 2020
Key Moments From Cohen Cross-Examination
Laura Mannweiler May 16, 2024

Brown v. Board in Pictures
Lauren Camera and Avi Gupta May 16, 2024
Privilege Claim Signals Fed-Up Biden
Aneeta Mathur-Ashton May 16, 2024

Kim Tees Up Shift in New Jersey Politics
Louis Jacobson May 16, 2024

New Home Construction Holds Steady
Tim Smart May 16, 2024

Who Is Prime Minister Robert Fico?
Laura Mannweiler May 15, 2024

New industry readies for launch as researchers hone offshore wind turbines that float
O RONO, Maine (AP) — As waves grew and gusts increased, a wind turbine bobbed gently, its blades spinning with a gentle woosh. The tempest reached a crescendo with little drama other than splashing water.
The uneventful outcome is exactly what engineers aimed for.
The demonstration featuring a 13-foot-tall (4-meter-tall) floating wind turbine in an indoor pool aimed to ensure it can withstand the strain of powerful water and wind when much larger versions are deployed in the ocean.
It’s the University of Maine’s contribution to a worldwide race to improve floating machines to tap wind that blows across deeper waters offshore, too deep to attach turbines to the seabed with permanent pilings.
In the next decade, UMaine researchers said, they envision turbine platforms floating in the ocean beyond the horizon, stretching more than 700 feet (210 meters) skyward and anchored with mooring lines.
“These structures are massive,” said Anthony Viselli, chief engineer for offshore wind technology at the university’s Advanced Composites Center, after the demonstration wrapped up. “These would be some of the largest moving structures that humankind has endeavored to create. And there would be many of them.”
As the technology advances, dozens of designs are being promoted by experts who see floating wind turbines as a way to address climate change by shifting away from burning fossil fuels.
Floating turbines are the only way some countries and U.S. states can capture offshore wind energy on a large scale. In the U.S. alone, 2.8 terawatts of wind energy potential blows over ocean waters too deep for traditional turbines that affix to the ocean floor, according to the National Renewable Energy Laboratory . That’s enough to power 350 million homes — more than double the number of existing homes in the U.S.
The first floating wind farm started operating off Scotland’s coast in 2017. In the United States, the Department of Interior two weeks ago proposed the first floating wind energy auctions for the Gulf of Maine, following lease auctions for the West Coast that began in 2022 . The nearly 1 million acres up for auction off the New England coast could generate enough clean wind energy to power more than 5 million local homes, the department said.
UMaine is home to the nation's largest team of engineers dedicated to floating offshore wind. Other big players include Equinor, which has installed a demonstration floating project of the coast of Norway; global company Principle Power, which has installed small-scale projects off Scotland and Portugal; and SBM Offshore, which has a demonstration project off France.
Floating offshore wind is still a nascent industry, however, making it expensive.
The Norwegian company Equinor postponed its Trollvind floating initiative , citing technology availability, rising costs and a strained timetable to deliver on the original concept.
Danish wind energy developer Ørsted decided to focus its efforts on fixed-bottom turbines, foregoing deeper offshore regions including Japan, Norway, Spain, Portugal and the U.S. West Coast. “We care a lot about affordability of renewable power, and floating wind is a lot more expensive than bottom-fixed,” said CEO Mads Nipper.
But others are moving forward.
Gazelle Wind Power is developing a modular platform system to make manufacture and assembly cost-effective and efficient.
“This is a global problem and this is an ideal solution in order to deliver power to shore,” said Gazelle Wind Power CEO Jon Salazar.
UMaine launched its first floating prototype a decade ago and became a surprise global leader after a study showed that the Gulf of Maine had the wind energy potential of 156 nuclear power plants, due to fast, consistent wind.
The state could meet all its home heating needs and power every car — if they were all electric vehicles — by tapping just 3% of that water. That improves the odds of successfully sharing the resource with fishermen, recreational boaters, the military and, of course, marine life . Indeed, the federal government’s lease proposal spares Maine’s key lobstering grounds from development, removing a potential obstacle.
Trailblazers in offshore wind are benefiting from work done by the oil industry, which engineered floating oil and gas rigs, said Habib Dagher, director of the Advanced Composites Center.
The university's wind wave basin, which looks something like a swimming pool with wave and wind generators that can mimic ocean conditions up to a 500-year storm, takes that work to the next level.
On a recent day, the semi-submersible floating turbine was tethered to the bottom of the basin. Its 1:70 scale represented a real turbine standing about 800 feet (240 meters) tall atop a platform in the ocean. The goal is to have industrial scale turbines of 15 to 20 megawatts each, Dagher said.
Size and efficiency are keys to profitability. Larger wind turbines mean fewer are needed, reducing construction, installation and maintenance costs, Viselli said. With greater size and efficiency, developers envision only about 50 turbines needed to produce about the same amount of electricity as a nuclear power plant.
Full-size turbines generate peak power starting at about 20 mph (32 kph). In powerful storms, they shut down automatically to avoid stressing the equipment or breaking. The mooring lines tethered to the ocean floor are made of rope nearly thick as a telephone pole and under heavy tension. That makes them safer for marine mammals.
For all the turbine technology, the platforms developed by UMaine can be built locally with concrete, a simple material that's readily available. The university already has partners around the world interested in licensing its technology. The state of Maine plans to develop a port facility in the Searsport area to build the floating bases and attach turbines before sending them into the Gulf of Maine.
A brand new industry means some experiments in design will succeed and some will fail. And there is work to ensure that wind farms are good neighbors, overcoming objections from others using the ocean.
“We’re going to have some problems and we have to figure out how to roll up our sleeves and solve these problems,” Dagher said. “And I think we have no choice as a society but to do that.”
McDermott reported from Providence, Rhode Island.
The Associated Press’ climate and environmental coverage receives financial support from multiple private foundations. AP is solely responsible for all content. Find AP’s standards for working with philanthropies, a list of supporters and funded coverage areas at AP.org .
David Sharp And Jennifer Mcdermott, The Associated Press
A study on flow fields and performance of water wheel turbine using experimental and numerical analyses
- Published: 10 January 2018
- Volume 61 , pages 464–474, ( 2018 )
Cite this article
- Manh Hung Nguyen 1 ,
- Haechang Jeong 1 &
- Changjo Yang 2
429 Accesses
14 Citations
Explore all metrics
In this paper, an analysis of the performance and flow fields of water wheel turbines for tidal energy extraction is carried out using experimental and numerical methods. The purpose of this work is to develop a water turbine suitable for sites, where fast and shallow surface flows are available, such as rivers or tidal currents. For both methods, the water wheel turbine is tested over a range of tip speed ratios with a differing number of rotor blades, ranging between three and twelve. The results indicate that the numerical simulation shows agreement with the experiment in most cases. Also, the water wheel turbine operates effectively at a range of small tip-speed ratios, where the highest turbine efficiency is produced. Under the same working conditions, the turbines using between six and nine blades generate a greater efficiency and cause lesser reverse flows than others when submerged in water. In contrast, the 3-bladed turbine is the least efficient design as it produces the lowest amount of energy and causes intense vibrations and noises. These noises are a result of a collision between the incoming flow of the channel and the wheel blades during the experimentation, especially at high load conditions. By adding more blades, the torque generated is improved considerably; however, the upstream and downstream depths of the turbine, in this case, are also elevated significantly. Furthermore, in the inlet region, the 3-bladed and 6-bladed turbines have a smaller shock loss and a lower resistance to the main flow from the inlet than the others. Meanwhile, it is found that the flow in the outlet region on the turbines with between nine and twelve blades is in the opposite direction to the wheel’s rotation, significantly obstructing the main flow from the inlet.
This is a preview of subscription content, log in via an institution to check access.
Access this article
Price includes VAT (Russian Federation)
Instant access to the full article PDF.
Rent this article via DeepDyve
Institutional subscriptions
Similar content being viewed by others
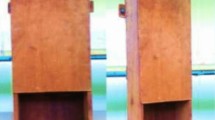
Experimental study of an oscillating water column wave energy converter based on regular waves
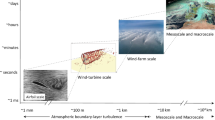
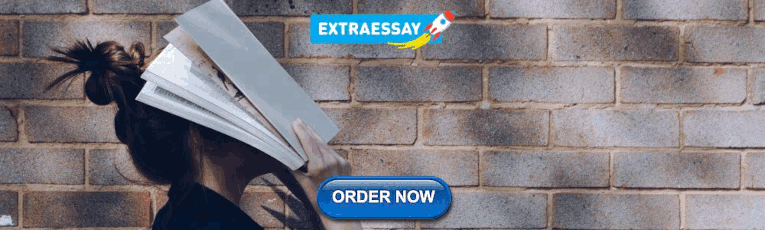
Wind-Turbine and Wind-Farm Flows: A Review
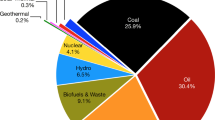
Principle Parameters and Environmental Impacts that Affect the Performance of Wind Turbine: An Overview
Müller G. Water wheel as a power source. Http://hmf.enseeiht.fr/travaux/CD0708/beiere/3/html/bi/3/fichiers/Muller_histo.pdf, 2004
Google Scholar
Müller G, Kauppert K. Performance characteristics of water wheels. J Hydraul Res, 2004, 42: 451–460
Article Google Scholar
Jones Z. Domestic electricity generation using waterwheels on moored barge. Dissertation for the Master’s Degree. Edinburgh: Heriot Watt University, 2005
Capecchi D. Over and undershot waterwheels in the 18th Century: Science-technology controversy. Adv Hist Stud, 2013, 02: 131–139
Quaranta E, Revelli R. Performance characteristics, power losses and mechanical power estimation for a breastshot water wheel. Energy, 2015, 87: 315–325
Denny M. The efficiency of overshot and undershot waterwheels. Eur J Phys, 2004, 25: 193–202
Article MathSciNet MATH Google Scholar
Müller G, Denchfield S, Schelmerdine R. Stream wheels for applications in shallow and deep water. In: Proceedings of 32nd IAHR Congress, 2007. 291–100
Nguyen M H, Hoang A D, Yang C J. A parametric study about blade shapes and blade numbers of water wheel type tidal turbine by numerical method. J Korean Soc Marine Environ & Safety, 2016, 22: 296–303
Yelguntwar P, Bhange P, Lilhare Y, et al. Design, fabrication and testing of a waterwheel for power generation in an open channel flow. Intl J Eng and Advanced Tech, 2014, 2: 1–7
Turnock S R, Müller G, Nicholls-Lee R F, et al. Development of a floating tidal energy system suitable for use in shallow water. In: Proceedings of the 7th European Wave and Tidal Energy Conference, 2007. 822–831
Gandhi J R, Jha H, Jha S N, et al. Renewable energy based floating power generator (rivers and canals). Int J Eng Res & Appl, 2016, 6: 49–52
Batten W M J, Weichbrodt F, Müller G, et al. Design and stability of a floating free stream energy converter. In: Proceedings of the 34th World Congress of the International Association for Hydro-Environment Research and Engineering, 2011. 624–630
Sam A A. Water wheel CFD simulation. Dissertation for the Master’s Degree. Lund University, 2010
Nishi Y, Inagaki T, Li Y, et al. Study on an undershot cross-flow water turbine. J Therm Sci, 2014, 23: 239–245
Nishi Y, Inagaki T, Li Y, et al. Research on the flow field of undershot cross-flow water turbines using experiments and numerical analysis. In: Proceedings of IOP Conference Series: Earth and Environmental Science, 2014. 22–31
James A S. Hydrostatic pressure converters for the exploitation of very low head hydropower potential. Dissertation for the Doctoral Degree. Southampton: University of Southampton, 2009
Paudel S, Linton N, Zanke U C E, et al. Experimental investigation on the effect of channel width on flexible rubber blade water wheel performance. Renew Energ, 2013, 52: 1–7
Müller G, Jenkins R, Batten W M J. Potential, performance limits and environmental effects of floating water mills. In: Proceedings of River Flow, 2010. 192–198
Bresse J A C. Water wheels or hydraulic motors. Honolulu: University Press of the Pacific, 2003
Müller G, Kauppert K. Die wasserräder als hydraulische kraftmaschinen. Bautechnik, 2003, 80: 181–189
Mehmood N, Liang Z, Khan J. Diffuser augmented horizontal axis tidal current turbines. Res J Applied Sci Eng & Tech, 2012, 18: 3522–3532
Nguyen M H, Hoang A D, Yang C J. Evaluation of vane tidal turbine’s performance and comparison of efficiency among six-bladed, eight-bladed and twelve-bladed types. In: Proceedings of the 38th KOSME Spring Conference, 2014. 134–135
Download references
Author information
Authors and affiliations.
Graduate School, Division of Marine Engineering, Mokpo National Maritime University, Mokpo, 58628, Republic of Korea
Manh Hung Nguyen & Haechang Jeong
Department of Marine Engineering, Mokpo National Maritime University, Mokpo, 58628, Republic of Korea
Changjo Yang
You can also search for this author in PubMed Google Scholar
Corresponding author
Correspondence to Changjo Yang .
Rights and permissions
Reprints and permissions
About this article
Nguyen, M.H., Jeong, H. & Yang, C. A study on flow fields and performance of water wheel turbine using experimental and numerical analyses. Sci. China Technol. Sci. 61 , 464–474 (2018). https://doi.org/10.1007/s11431-017-9146-9
Download citation
Received : 13 January 2017
Accepted : 11 September 2017
Published : 10 January 2018
Issue Date : March 2018
DOI : https://doi.org/10.1007/s11431-017-9146-9
Share this article
Anyone you share the following link with will be able to read this content:
Sorry, a shareable link is not currently available for this article.
Provided by the Springer Nature SharedIt content-sharing initiative
- water wheel
- tidal energy
- tip speed ratio
- the number of blades
- Find a journal
- Publish with us
- Track your research

Cost of living help and a future made in Australia
Investing in a future made in australia.
Investing in a Future Made in Australia and the skills to make it a reality
Print or save page
On this page
Attracting investment in key industries
Making Australians the beneficiaries of change
A Future Made in Australia is about creating new jobs and opportunities for every part of our country by maximising the economic and industrial benefits of the move to net zero and securing Australia’s place in a changing global economic and strategic landscape.
The Government’s $22.7 billion Future Made in Australia package will help facilitate the private sector investment required for Australia to be an indispensable part of the global economy.
For more information refer to the Future Made in Australia fact sheet [PDF 438KB]
Better deploying capital in priority areas
The Future Made in Australia package will realise Australia’s potential to become a renewable energy superpower, value‑add to our resources and strengthen economic security by better attracting and enabling investment in priority areas. The Government will create a Future Made in Australia Act and establish a National Interest Framework that identifies priority industries and ensures investments associated with them are responsible and targeted.
The Framework will have a focus on industries that contribute to the net zero transformation where Australia has a comparative advantage, and where Australia has national interest imperatives related to economic resilience and security.
Strengthening and streamlining approvals
This Budget provides a faster pathway to better decisions on environmental, energy, planning, cultural heritage and foreign investment approvals.
This includes:
- $134.2 million to better prioritise approvals for renewable energy projects of national significance, and support faster decisions on environment, cultural heritage and planning approvals.
- Working with the states and territories through the Energy and Climate Change Ministerial Council to accelerate electricity grid connections.
- $20.7 million to improve engagement with communities impacted by the energy transition and accelerate the delivery of key energy projects.
- $15.7 million to strengthen scrutiny of high‑risk foreign investment proposals, enhance monitoring and enforcement activities and support faster decisions.
The Government will also encourage foreign investment by providing refunds of 75 per cent of application fees for unsuccessful competitive bids.
Promoting sustainable finance
The Government is committing $17.3 million to mobilise private sector investment in sustainable activities. This includes extending Australia’s sustainable finance taxonomy to the agriculture sector and developing a labelling regime for financial products marketed as sustainable.
The Government will also examine opportunities to improve data quality and provide $1.3 million to develop and issue guidance for best practice transition plans.
Making Australia a renewable energy superpower
Powering australia with cheaper, cleaner, more reliable energy.
Australia’s potential to produce abundant renewable energy is a powerful source of comparative advantage. To realise this, the Government is unlocking more than $65 billion of investment in renewable capacity through the Capacity Investment Scheme by 2030.
This Budget helps Australians benefit from cheaper, cleaner energy sooner by investing $27.7 million to integrate consumer energy resources like batteries and solar into the grid.
The New Vehicle Efficiency Standard will save Australians around $95 billion at the bowser by 2050 and reduce transport emissions.
Unlocking investment in net zero industries and jobs
This Budget accelerates growth of new industries by establishing the $1.7 billion Future Made in Australia Innovation Fund and delivering a 10‑year extension of funding to the Australian Renewable Energy Agency. It also delivers the $44.4 million Energy Industry Jobs Plan and $134.2 million for skills and employment support in key regions.
The Future Made in Australia package establishes time‑limited incentives to invest in new industries. The Hydrogen Production Tax Incentive will make Australia’s pipeline of hydrogen projects commercial sooner, at an estimated cost of $6.7 billion over the decade. This Budget also expands the Hydrogen Headstart program by $1.3 billion.
Boosting demand for Australia’s green exports
The Government is making it easier for businesses and trading partners to source low‑emissions products by building better markets and product standards for green products.
This Budget provides $32.2 million to fast‑track the initial phase of the Guarantee of Origin scheme, focused on renewable hydrogen, and bring forward the expansion of the scheme to accredit the emissions content of green metals and low‑carbon liquid fuels. The Government is also working closely with trading partners to identify opportunities to drive greater supply chain transparency and better market recognition of high environmental, social and governance standards in the critical minerals sector.
Realising the opportunities of the net zero transformation
Australia is committed to reaching net zero greenhouse gas emissions by 2050 and is developing six sector plans covering:
- electricity and energy
- agriculture and land
- the built environment.
This Budget continues investment in effective emissions abatement, including through $63.8 million to support emissions reduction efforts in the agriculture and land sector.
The Government is also investing $399 million to establish the Net Zero Economy Authority and support the economy‑wide net zero transformation. This Budget also invests an additional $48 million in reforms to the Australian Carbon Credit Unit scheme and $20.7 million to improve community engagement.
Strengthening resources and economic security
Backing a strong resources sector.
The Government is investing $8.8 billion over the decade to add more value to our resources and strengthen critical minerals supply chains. This Budget establishes a production tax incentive for processing and refining critical minerals at an estimated cost of $7 billion over the decade. It commits up to $1.2 billion in strategic critical minerals projects through the Critical Minerals Facility and the Northern Australia Infrastructure Facility, and pre‑feasibility studies for common user precincts.
This is in addition to $566.1 million to support Geoscience Australia to map all of Australia’s critical minerals, strategic materials, groundwater and other resources essential for the transition to net zero.
Manufacturing clean energy technologies
The Government is committing $1.5 billion to manufacturing clean energy technologies, including the $1 billion Solar Sunshot and $523.2 million Battery Breakthrough Initiative. These investments will be delivered by ARENA.
Strengthening supply chains
To support the delivery of the 82 per cent renewable energy target, the Government has formed the National Renewable Energy Supply Chain Action Plan with states and territories. The Government will invest an additional $14.3 million working with trade partners to support global rules on unfair trade practices and to negotiate benchmarks for trade in high quality critical minerals.
Digital, science and innovation
Investing in new technologies and capabilities.
The Government is investing $466.4 million to partner with PsiQuantum and the Queensland Government to build the world’s first commercial‑scale quantum computer in Brisbane.
The Government will undertake a strategic examination of Australia’s research and development (R&D) system with $38.2 million invested in a range of science, technology, engineering, and maths programs.
The Government is providing $448.7 million to partner with the United States in the Landsat Next satellite program to provide access to critical data to monitor the earth’s climate, agricultural production, and natural disasters.
Modernising and digitising industries
This Budget commits $288.1 million to support Australia’s Digital ID System. A National Robotics Strategy will also be released to promote the responsible production and adoption of robotics and automation technologies for advanced manufacturing in Australia.
Reforming tertiary education
The Government is committing $1.6 billion over 5 years, and an additional $2.7 billion from 2028–29 to 2034–35 to reform the tertiary education system and deliver Australia's future workforce.
This includes $1.1 billion for reforms to university funding and tertiary system governance.
Over $500 million will be provided for skills and training in priority industries and to support women’s participation in these sectors.
The Government will set a tertiary attainment target of 80 per cent of the working‑age population by 2050.
Supporting students on placements
The Government will establish Commonwealth Prac Payments (CPP) for students undertaking mandatory placements. From 1 July 2025, the payment will provide more than 73,000 eligible students, including teachers, nurses, midwives and social workers with $319.50 per week during their placements.
Felicity is a full‑time student receiving Youth Allowance, living by herself. She is studying a Bachelor of Nursing and must stop paid work during her mandatory prac placement. During her prac, Felicity receives $712.05 per week from the Government including: $319.50 of CPP, $285.55 of Youth Allowance (YA), $103.50 of Commonwealth Rent Assistance (CRA) and $3.50 of Energy Supplement.
Felicity receives $351.55 a week more than she would have in 2023 before indexation and the changes to YA, CRA and CPP in the current and 2023–24 Budget
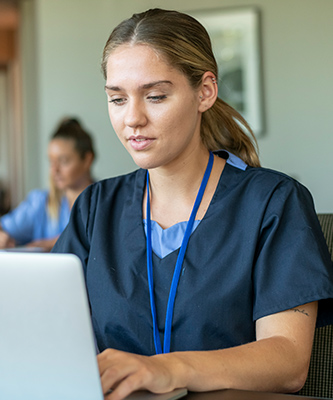
Broadening access to university
From January 2026, needs‑based funding will provide per student funding contributions for under‑represented students. The Government will also provide $350.3 million to fully fund university enabling courses and increase pathways for prospective students to university.
Skills pipeline for priority industries
Skills and training for Future Made in Australia industries
The Government will expand eligibility to the New Energy Apprenticeships Program to include work in the clean energy sector, including in construction and advanced manufacturing. This will provide access to $10,000 incentive payments and support our target of 10,000 new energy apprentices.
The Government will commit $30 million to turbocharge the VET teaching workforce for clean energy courses and $50 million to upgrade and expand clean energy training facilities.
The Government will invest $55.6 million to establish the Building Women’s Careers program to support women’s participation in key industries including clean energy and advanced manufacturing.
Supporting apprentices and building the construction workforce
The $5,000 support payments to apprentices in priority occupations will be maintained for another 12 months to 1 July 2025, up from $3,000 in the absence of any changes. Employers of these apprentices will receive a $5,000 hiring incentive, up from $4,000 in the absence of changes. This will provide certainty to apprentices while the Strategic Review of the Apprenticeship Incentive System is underway.
The Government will also invest $88.8 million to deliver 20,000 new fee‑free TAFE places including pre‑apprenticeships in courses relevant to the construction sector. The Government will provide $1.8 million to deliver streamlined skills assessments for around 1,900 migrants from comparable countries to work in Australia’s housing construction industry.
Strengthening our defence industry capability
An integrated and focused approach to defending Australia
The Government is investing an additional $50.3 billion over ten years to implement the 2024 National Defence Strategy to meet Australia’s strategic needs.
Overall funding for Defence will reach $765 billion over the decade. Defence’s Integrated Investment Program has been rebuilt to create a focused Australian Defence Force, accelerate delivery of priority capabilities, and provide certainty to grow Australia’s defence industry. This includes funding for the Royal Australian Navy’s surface combatant fleet and establishing a guided weapons and explosive ordnance manufacturing capability earlier.
The Government is reforming Defence’s budget to support the National Defence Strategy and delivery of priority capabilities.
Developing defence industry and skills
Industry development grants funding of $165.7 million will also help businesses to scale up and deliver the Sovereign Defence Industrial Priorities, which include continuous naval shipbuilding and sustainment, and development and integration of autonomous systems.
The Government is providing $101.8 million to attract and retain the skilled industrial workforce to support Australian shipbuilding and delivery of conventionally armed, nuclear powered submarines. This includes a pilot apprenticeship program in shipbuilding trades and technologies.
Investing in civil maritime capabilities
The Government is providing $123.8 million to maintain and enhance civil maritime security capabilities. This includes $71.2 million to increase the Australian Border Force’s on‑water response and aerial surveillance capabilities.
Securing Australia’s place in the world
Strengthening relationships and simplifying trade
A stable, prosperous and resilient Pacific region
The Government is delivering over $2 billion in development assistance to the Pacific in 2024–25. This includes the Australia‑Tuvalu Falepili Union.
Investing in our relationship with Southeast Asia
Following the launch of Australia’s Southeast Asia Economic Strategy to 2040, the Government is committing $505.9 million to deepen ties with the region.
Australia recently celebrated 50 years of partnership with the Association of Southeast Asian Nations (ASEAN). At the ASEAN‑Australia Special Summit, the Government announced a range of new and expanded initiatives, including a $2 billion Southeast Asia Investment Financing Facility to boost Australian trade and investment.
Simplifying trade
The Government will abolish 457 nuisance tariffs from 1 July 2024, streamlining $8.5 billion in annual trade and eliminating tariffs on goods such as toothbrushes, fridges, dishwashers, clothing and sanitary products.
The Government will provide $29.9 million to coordinate trade simplification and deliver the Digital Trade Accelerator program, and $10.9 million to enhance the Go Global Toolkit to support exporters.
The Government is expanding the Australia‑India Business Exchange, diversifying trade and helping more Australian businesses build commercial ties with India and across South Asia. There will be $2 million to support Australian agricultural exporters entering the Chinese markets.
Support for small businesses
Helping small businesses
This Budget’s Small Business Statement reaffirms the Government’s commitment to deliver a better deal for small businesses, with $641.4 million in targeted support.
For more information refer to the small business fact sheet [PDF 0.98MB]
Improving cash flow
The Government is providing $290 million to extend the $20,000 instant asset write‑off for 12 months. There will be $25.3 million to improve payment times to small businesses and $23.3 million to increase eInvoicing adoption.
Easing cost pressures and reducing the administrative burden
This Budget provides $3.5 billion of energy bill relief, including rebates of $325 to around one million small businesses.
The Government is reducing the administrative burden for small business by abolishing 457 nuisance tariffs and delivering $10 million to provide additional support for small business employers administering the Paid Parental Leave scheme.
Supporting confidence and resilience in the small business sector
This Budget invests a further $10.8 million in tailored, free and confidential financial and mental wellbeing supports for small business owners.
The Government is providing $20.5 million to the Fair Work Ombudsman to help small businesses understand and comply with recent workplace relations changes.
There will be $3 million to implement the Government’s response to the Review of the Franchising Code of Conduct, including remaking and enhancing the Code, and an additional $2.6 million to support more small businesses through alternative dispute resolution.
A more resilient Australia
Preparing for the future
The Government is preparing Australia for future droughts and heightened risk of natural disasters.
Disaster resilience and preparedness
The Government will provide $138.7 million to improve Australia’s response and resilience to natural hazards and disasters. Support includes: funding for the National Emergency Management Agency to supply communities with vital goods, equipment, and temporary accommodation during an emergency, aerial firefighting capability, and mental health support. This is in addition to the $11.4 billion previously committed for Disaster Recovery Funding Arrangements for the states and territories.
The Government is establishing a pilot program for Australia’s Strategic Fleet. These vessels will improve Australia’s capacity to respond and support communities and supply chains during crises.
Preparing for drought and climate change
This Budget provides $174.6 million from the National Water Grid Fund to deliver new water infrastructure projects that will enhance water security, boost agricultural production and help drought proof regional communities.
The Government will provide $519.1 million from its Future Drought Fund to help farmers and rural communities manage the impacts of climate change and prepare for future droughts.
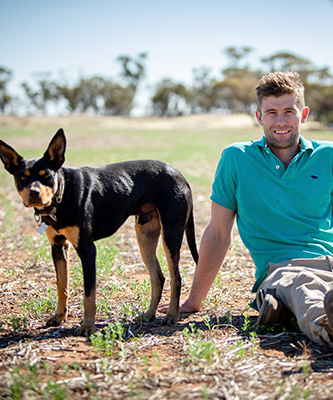
This investment will build the drought resilience of more farmers like Victorian cropper Ed Rickard.
The Fund supported Ed in developing a better farm business plan, which identified his need for weather stations and soil moisture probes. It also helped him implement a succession plan that ensured his farm’s long-term viability.
Back to top

'Forever chemicals' found to rain down on all five Great Lakes
Perfluoroalkyl and polyfluoroalkyl substances, also known as PFAS or "forever chemicals," have become persistent pollutants in the air, water and soil. Because they are so stable, they can be transported throughout the water cycle, making their way into drinking water sources and precipitation. According to findings published in ACS' Environmental Science & Technology , precipitation introduces similar amounts of PFAS into each of the Great Lakes; however, the lakes eliminate the chemicals at different rates.
Consuming PFAS has been linked to negative health outcomes. And in April 2024, the U.S. Environmental Protection Agency (EPA) designated two forever chemicals -- PFOS and PFOA -- as hazardous substances, placing limits on their concentrations in drinking water. The Great Lakes are a major freshwater source for both the U.S. and Canada, and the EPA reports that the surrounding basin area is home to roughly 10% and 30% of each country's population, respectively. Previous studies demonstrated that these lakes contain PFAS. But Marta Venier at Indiana University and colleagues from the U.S. and Canada wanted to understand where the compounds come from and where they go.
Between 2021 and 2022, 207 precipitation samples and 60 air samples were taken from five sites surrounding the Great Lakes in the U.S.: Chicago; Cleveland; Sturgeon Point, N.Y.; Eagle Harbor, Mich.; and Sleeping Bear Dunes, Mich. During the same period, 87 different water samples were collected from the five Great Lakes. The team analyzed all the samples for 41 types of PFAS and found:
- In precipitation samples, PFAS concentrations largely remained the same across sites, suggesting that the compounds are present at similar levels regardless of population density.
- In air samples, Cleveland had the highest median concentration of PFAS and Sleeping Bear Dunes the lowest, suggesting a strong connection between population density and airborne PFAS.
- In the lake water samples, the highest concentration of PFAS were in Lake Ontario, followed by Lake Michigan, Lake Erie, Lake Huron and Lake Superior.
- The concentration of PFOS and PFOA in lake water decreased compared to data from previous studies as far back as 2005, but the concentration of a replacement PFAS known as PFBA remained high, suggesting that further regulation efforts may be needed.
The team calculated that airborne deposition from precipitation is primarily how PFAS get into the lakes, while they're removed by sedimentation, attaching to particles as they settle to the lakebed or flowing out through connecting channels. Overall, their calculations showed that the northernmost lakes (Superior, Michigan and Huron) are generally accumulating PFAS. Further south, Lake Ontario is generally eliminating the compounds and levels in Lake Erie remain at a steady state. The researchers say that this work could help inform future actions and policies aimed at mitigating PFAS' presence in the Great Lakes.
The authors acknowledge funding from the Great Lakes Restoration Initiative from the U.S. Environmental Protection Agency's Great Lakes National Program Office.
- Nature of Water
- Nuclear Energy
- Environmental Issues
- Great Lakes
- Precipitation (meteorology)
- Evaporation from plants
- Lake effect snow
- Water resources
- Surface runoff
- Infiltration (hydrology)
Story Source:
Materials provided by American Chemical Society . Note: Content may be edited for style and length.
Journal Reference :
- Chunjie Xia, Staci L. Capozzi, Kevin A. Romanak, Daniel C. Lehman, Alice Dove, Violeta Richardson, Tracie Greenberg, Daryl McGoldrick, Marta Venier. The Ins and Outs of Per- and Polyfluoroalkyl Substances in the Great Lakes: The Role of Atmospheric Deposition . Environmental Science & Technology , 2024; DOI: 10.1021/acs.est.3c10098
Cite This Page :
Explore More
- Otters Use Tools to Survive a Changing World
- Monogamy in Mice: Newly Evolved Type of Cell
- Sustainable Electronics, Doped With Air
- Male Vs Female Brain Structure
- Breeding 'Carbon Gobbling' Plants
- Why Do We Overindulge?
- Jelly Sea Creatures and Underwater Robotics
- Teeth of Sabre-Toothed Tigers
- Robotic 'SuperLimbs' Could Help Moonwalkers
- Solving Quantum Many-Body Problems
Trending Topics
Strange & offbeat.
- Grundfos USA
- Research & insights
Waste less energy
Are you aware of how much energy goes to waste when water is leaking from your network?
Whether you are dealing with small leaks or large pipe bursts, paying to transport water through your system only to have it leaked leads to unnecessary expenses. And with rising energy prices, this hidden financial impact of pipe breaks can easily become significant.
Not to mention the impact leaks can have on your public image. With today’s large focus on sustainability, it is essential to keep your water and energy consumption as low as possible, and preferably eliminate any waste.
How large is the hidden cost of your water loss?
If 1 m 3 of non-revenue water requires 1 kWh for transportation and 1 kWh costs about €0.5, a yearly water loss of 1,000,000 m 3 equals about €500,000 in unnecessary energy expenses.
Solution: Automatic monitoring and proactive asset management
To reduce energy waste, it is essential that pipe breaks are dealt with in a timely manner or, even better, prevented from happening at all. Increasing your focus on long-term planning can help you decrease leakage.
You can learn more about how to detect and locate leaks here and how to reduce your pipe burst rate through asset management here.
Explore more benefits
Find leaks quickly and efficiently, reduce the impact of pipe bursts, take charge of your assets, simplify complexity, want to know more about grundfos utility analytics.

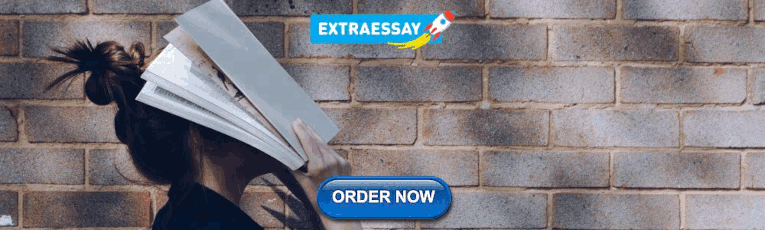
COMMENTS
Other and emerging alternative energy technology. Yen-Hsiung Kiang, in Fuel Property Estimation and Combustion Process Characterization, 2018. 10.7.1 Water Turbine. Water turbine is used to convert energy contained in water, potential energy or kinetic energy, into mechanical or electrical energy.. There are two types of water turbine, the reaction water turbine and the impulse water turbine.
Kaplan turbine and electrical generator cut-away view. The runner of the small water turbine. A water turbine is a rotary machine that converts kinetic energy and potential energy of water into mechanical work.. Water turbines were developed in the 19th century and were widely used for industrial power prior to electrical grids.Now, they are mostly used for electric power generation.
Hydroelectric energy is made by moving water. Hydro comes from the Greek word for water. Hydroelectric energy has been in use for thousands of years. Ancient Romans built turbines, which are wheels turned by flowing water.Roman turbines were not used for electricity, but for grinding grains to make flour and breads. Water mills provide another source of hydroelectric energy.
Abstract. The energy crisis of the modern era may be overcome by hydrokinetic energy, the most readily and free source of energy available, to provide basic electricity needs to remote and urban areas at a low cost. The kinetic energy of flowing water at low speed could be extracted effectively by designing an appropriate design of the blade, as the turbine's performance is dependent upon ...
Turbine energy recovery is a process energy saving technology, and understanding turbine efficiency has important operational and economic benefits for the operator of a power plant. There are three main areas of research into turbine energy efficiency: the structural performance of the turbine itself, the configuration of the recovery device and the regulation of operating conditions.
The efficiency of a hydraulic turbine varies with water flow as shown in Fig. 4, and for most types of hydraulic turbines, the efficiency is very close to the peak for a wide range of flows . The head loss in a through a pipe is propositional to the square of water inflow and can be calculated by Δ H = kQ 2 , where k is a constant.
In-pipe water turbines have begun to gain interest for harvesting power on a small scale from pipe networks. However, few studies have addressed the feasibility of installing spherical lift-based helical-bladed turbines in a water supply network. ... This research explored the potential of in-pipe turbines to be installed in main pipelines. A ...
Hydropower is one of the most sustainable and desirable renewable energy sources. Gravitational water vortex hydro turbine (GWVHT) systems are one of the most suitable and sustainable renewable power generation devices for remote and rural areas, particularly in developing countries, owing to their small scales and low costs. There are various GWVHT systems with different configurations and ...
Water supply pipelines and canals may possess a bulky amount of excess hydro energy. The renewable and clean feature of hydropower production with the lower cost, with shorter time of construction, and with contribution of small private sectors for investment on local projects are of major concerns. However, high expenses associated with the use of turbines in small hydropower plants have ...
In their research, the turbine efficiency in the channel was higher than the turbine efficiency in a free flow case, and the maximum efficiency was obtained at a high tip speed ratio (TSR). ... (2017) Performance study of ducted nozzle Savonius water turbine, comparison with conventional Savonius turbine. Energy 134:566-584. https://doi.org ...
River Current Turbine is an energy conversion technology that could be used in harnessing kinetic energy of a stream of flowing river water for the generation of electricity.
Tiny, very low-headed storage of flowing water is a possible location for screw turbines such as rivers, irrigation systems, water delivery systems, drinking water systems, drainage systems, cooling systems, and even desalination plants, with almost nil to 6.5 m head and a flow rate of 6.5 m 3 /s and less being the most popular sites .
Water turbine pump (WTP) is a clean, renewable, and sustainable pumping solution for irrigation purposes. This paper presents a detailed methodology for the design of WTP with a propeller turbine and centrifugal pump. This paper aims to revive historical pumping technology by laying out a foundation stone in research and documentation of WTPs.
In this research, the purpose is studying the fa ctors that. effect on the efficiency of water turbines by using the relation between. cross-section area and v elocity. And also, by using the ...
The use of microturbines in irrigation applications represents a great opportunity for increasing sustainable energy generation. Irrigation systems have water flow that can be used to generate electricity based on microturbines that are acceptably configure such, that efficiency in crop irrigation is not affected. This research validates this use of microturbines through a system designed ...
1. Introduction. The water power is considered as one of the renewable energy resources which has a large potential in changing the fossil energy of generating electricity [1].The Pelton turbine (or Pelton wheel turbine) is a type of turbine that commonly used in hydroelectric plants and in various energy recovery applications [1].It can be also described as an impulse type water turbine.
The research was conducted by building a prototype of a small-scale Archimedes screw hydro turbine with and without deflector. The purpose of this research is to compare the rotation produced by the two turbines and whether the installation of a deflector can improve turbine performance. The turbine is constructed with a screw length of 1 m ...
Updated 4:21 AM PDT, May 14, 2024. ORONO, Maine (AP) — As waves grew and gusts increased, a wind turbine bobbed gently, its blades spinning with a gentle woosh. The tempest reached a crescendo with little drama other than splashing water. The uneventful outcome is exactly what engineers aimed for. The demonstration featuring a 13-foot-tall (4 ...
The demonstration featuring a 13-foot-tall (4-meter-tall) floating wind turbine in an indoor pool aimed to ensure it can withstand the strain of powerful water and wind when much larger versions ...
The demonstration featuring a 13-foot-tall (4-meter-tall) floating wind turbine in an indoor pool aimed to ensure it can withstand the strain of powerful water and wind when much larger versions ...
This Special Issue titled "CFD Modelling and Simulation of Water Turbines" aims to present recent novel research trends based on advanced CFD techniques for water turbines. The following topics, among others, will be included in this Issue: CFD numerical methods (i.e., URANS, LES, hybrid, DNS, etc.) applied to simulation of water turbines
The purpose of this work is to develop a water turbine suitable for sites, where fast and shallow surface flows are available, such as rivers or tidal currents. ... et al. Research on the flow field of undershot cross-flow water turbines using experiments and numerical analysis. In: Proceedings of IOP Conference Series: Earth and Environmental ...
This Budget accelerates growth of new industries by establishing the $1.7 billion Future Made in Australia Innovation Fund and delivering a 10‑year extension of funding to the Australian Renewable Energy Agency. It also delivers the $44.4 million Energy Industry Jobs Plan and $134.2 million for skills and employment support in key regions.
Perfluoroalkyl and polyfluoroalkyl substances, also known as PFAS or 'forever chemicals,' have become persistent pollutants in the air, water and soil. Because they are so stable, they can be ...
Solution: Automatic monitoring and proactive asset management. To reduce energy waste, it is essential that pipe breaks are dealt with in a timely manner or, even better, prevented from happening at all. Increasing your focus on long-term planning can help you decrease leakage. You can learn more about how to detect and locate leaks here and ...
The following formula is used to express the rotational kinetic energy of unit water area behind the inducer, so as to illustrate the relationship between tangential velocity and kinetic energy: ... Jinfeng Zhang, Shuyu Gao, Xinyan Song, and Rui Zhu. 2024. "Research on Energy Loss of Optimization of Inducer-Impeller Axial Fit Dimensions Based ...